MOSOLF Special Vehicles GmbH è un'azienda leader nella produzione di veicoli per uso speciale con sede a Kippenheim, in Germania. L'azienda, che conta quasi 50 dipendenti, produce annualmente circa 1000 veicoli per uso speciale e di emergenza. La sua clientela include forze dell'ordine statali e federali tedesche, settore della difesa, organizzazioni per il controllo dei disastri e il soccorso tecnico, comuni e clienti industriali, che richiedono tutti veicoli altamente personalizzati e con prestazioni elevate.
Nel settore automobilistico, i componenti vengono realizzati principalmente con processi di produzione di massa, come lo stampaggio a iniezione, economicamente vantaggiosi per volumi di centinaia di migliaia di unità. Tuttavia, la clientela di MOSOLF necessita di una vasta gamma di parti personalizzate in volumi ridotti, per cui il costo delle attrezzature rende economicamente impraticabili i metodi di produzione tradizionali. In questo contesto, la stampa 3D rappresenta una soluzione ottimale per l'azienda.
"Secondo le mie stime, attualmente un mezzo di polizia su tre [in Germania] contiene parti realizzate mediante produzione additiva. Utilizziamo così tanto la stampa 3D che non c'è veicolo che lasci il nostro stabilimento senza una parte prodotta con questa tecnologia. Attualmente stampiamo in 3D circa 5000 parti all'anno, ma la tendenza è in crescita, il che significa che su ogni veicolo sono presenti almeno tre parti realizzate con questa tecnologia."
Carsten Busam, responsabile della pianificazione di progetto presso MOSOLF Special Vehicles GmbH
Continua a leggere per scoprire come MOSOLF utilizza la stampa 3D a sinterizzazione laser selettiva (SLS) con la serie Fuse per produrre un'ampia gamma di parti per utilizzo finale per furgoni della polizia e altri veicoli per uso speciale e di emergenza.
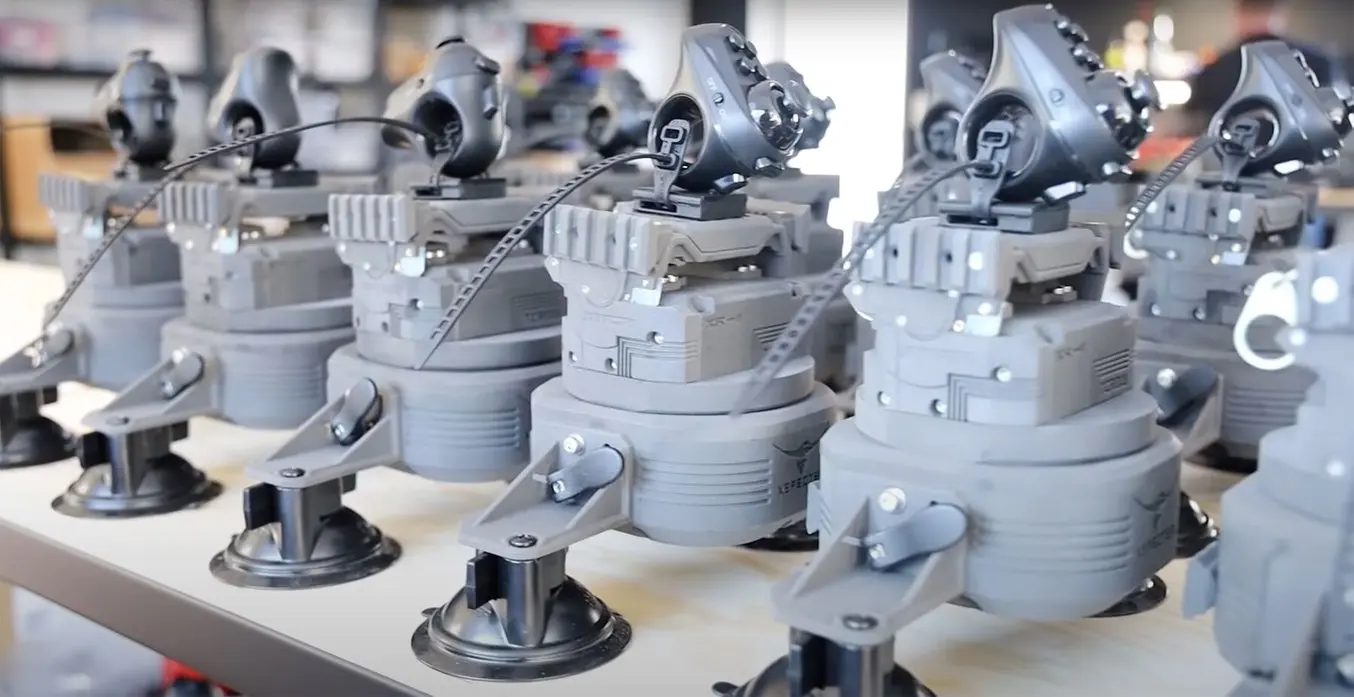
Produzione SLS per utilizzo finale
La stampa 3D per utilizzo finale non è solamente possibile, ma ora, grazie all'ecosistema SLS Fuse, è anche più economica, agile e scalabile che mai. Confronta i metodi di produzione, valuta i prezzi all'ingrosso della polvere e scopri le esperienze di 15 aziende che già utilizzano la serie Fuse.
Soluzioni personalizzate per soddisfare le esigenze dei 17 corpi di polizia tedeschi
"La nostra sfida più grande è la varietà", ha affermato Busam. Ogni stato e divisione delle forze di polizia acquista vari tipi di veicoli, ognuno dei quali può richiedere componenti personalizzati in base alla sua funzione specifica. Anche i componenti da integrare possono variare: ad esempio, i diversi corpi di polizia utilizzano sistemi radio o di segnalazione di aziende diverse. Di conseguenza, ogni veicolo necessita di un'ampia gamma di parti personalizzate.
"Realizziamo veicoli per 17 corpi di polizia in Germania, ciascuno con la propria visione di ergonomia e utilizzo. Di conseguenza, le quantità sono di solito relativamente elevate per il design di base, ma se si considera il grado di personalizzazione, tornano a essere ridotte", ha detto Busam.
Il team di MOSOLF lavora su veicoli prodotti in serie, ossia automobili, camion e furgoni già disponibili in commercio, che vengono adattati per rispondere a specifiche esigenze. Il team deve trovare la collocazione ideale per ogni caratteristica richiesta, garantendo che sia ergonomica, robusta ed esteticamente adeguata. Nel caso dei modelli più vecchi, era un'operazione più semplice poiché c'erano più spazi vuoti in cui installare i componenti, come nel cruscotto o nella console. I modelli più recenti, invece, hanno rappresentato una sfida maggiore.
"Gli interni dei veicoli hanno sempre più schermi e sempre meno spazi dedicati alla manutenzione. Sebbene siano presenti vani per alloggiare oggetti o ricaricare smartphone, è difficile riuscire a trovare spazi per l'installazione di tutti i comandi. Questo è particolarmente vero nei veicoli non identificabili, dove è importante che non si capisca che si tratta di mezzi della polizia", ha affermato Busam.
MOSOLF ha iniziato a utilizzare la stampa 3D nel 2016, in seguito alla richiesta della polizia bavarese di installare nuove radio digitali su tutta la flotta di veicoli e motocicli.
"Abbiamo dovuto sviluppare soluzioni personalizzate per ciascun mezzo. Se avessimo realizzato tutte le parti in lamiera, il processo sarebbe stato lungo o le soluzioni avrebbero avuto un aspetto meno gradevole. Ecco perché abbiamo iniziato a utilizzare la stampa 3D."
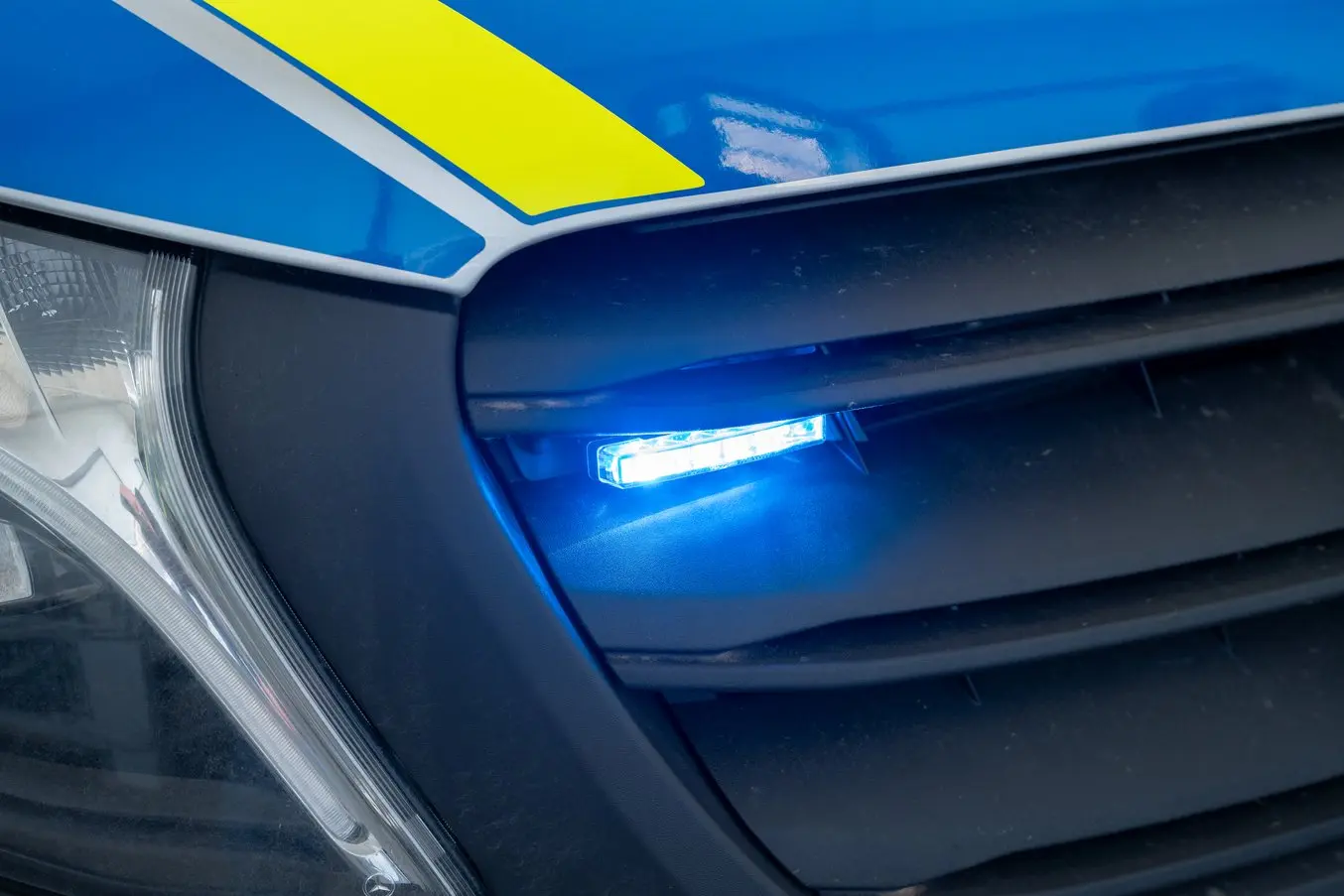
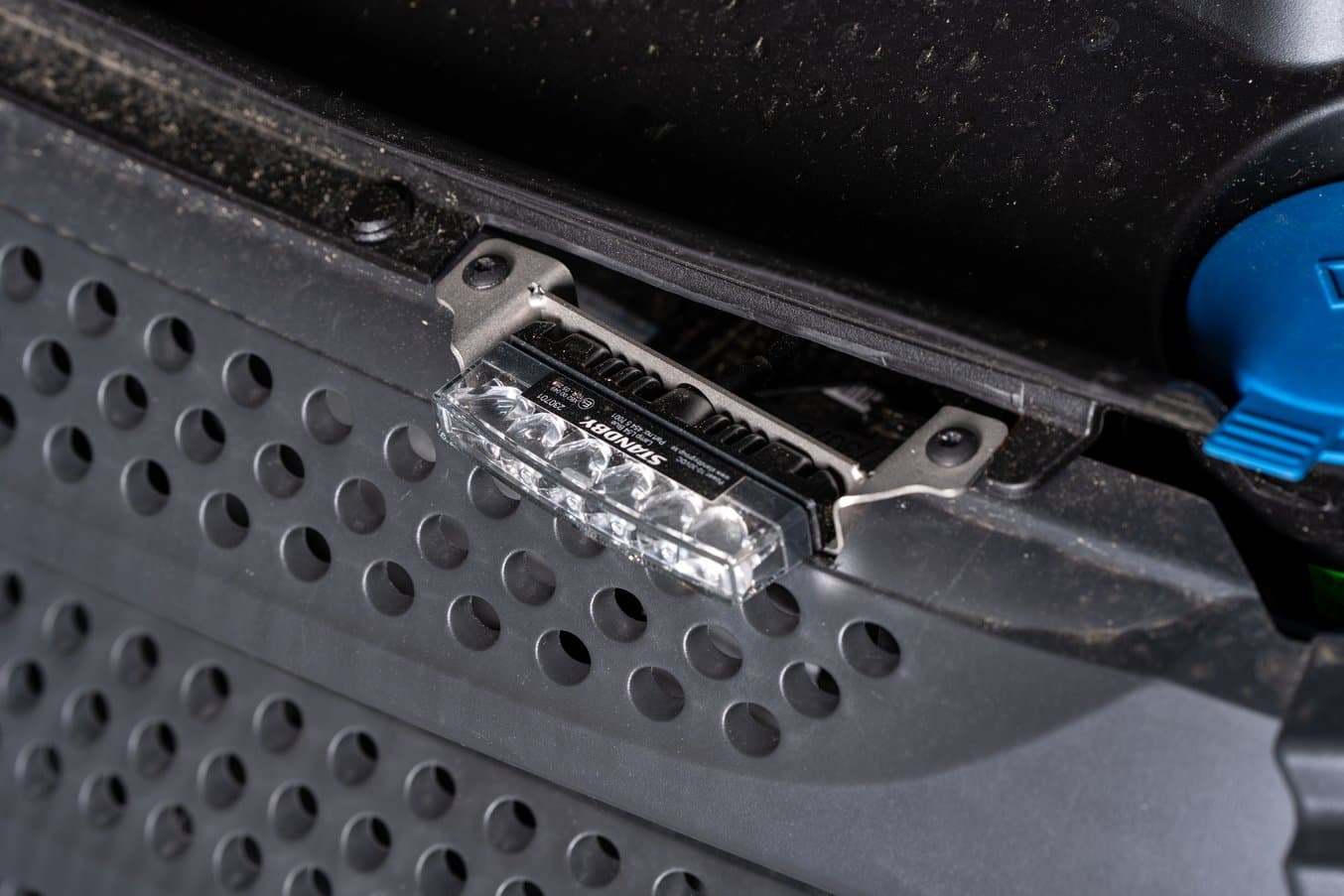
Attacco personalizzato per le luci lampeggianti a LED anteriori dei furgoni della polizia. In passato, il team produceva questi componenti tramite formatura della lamiera.
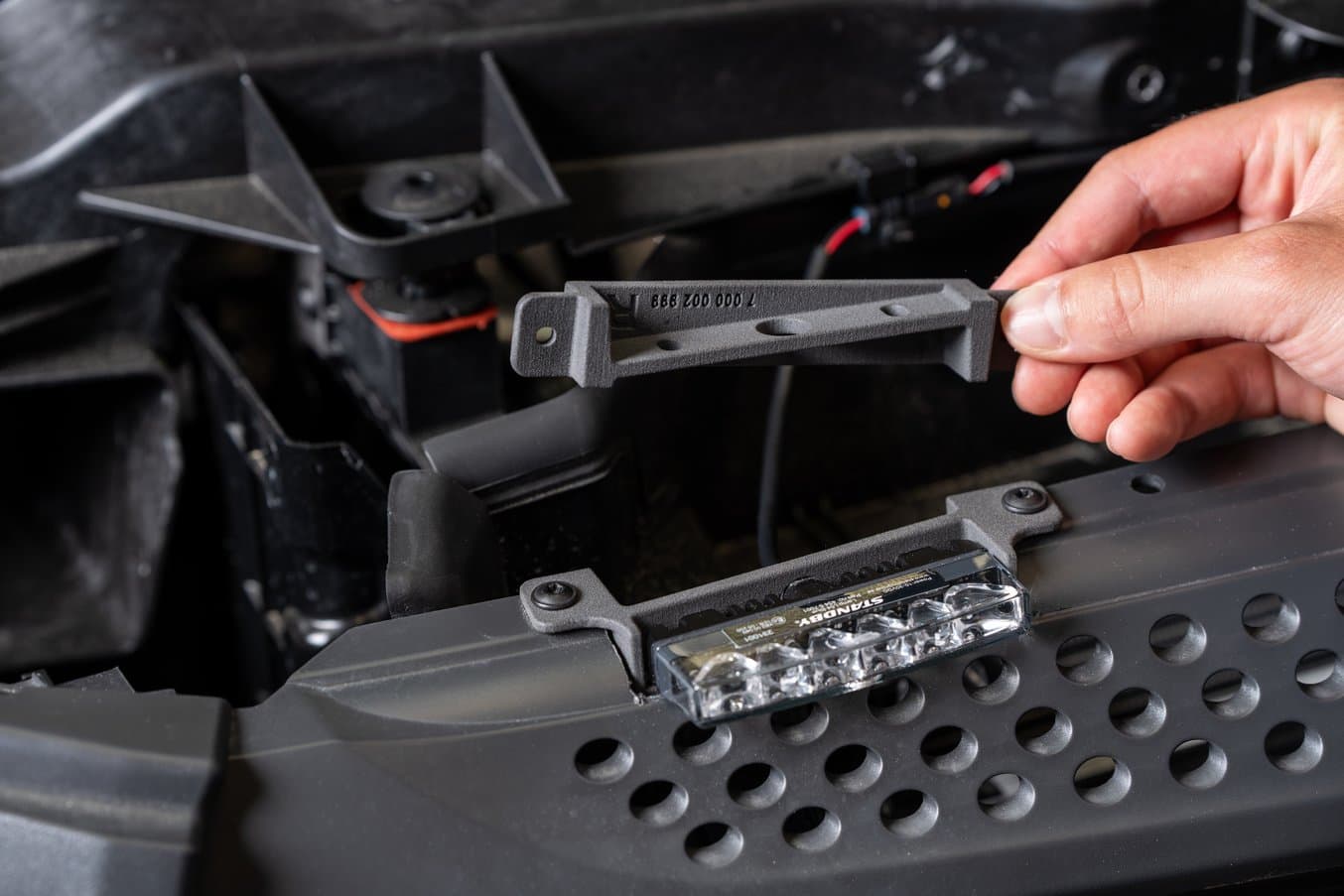
La stampa 3D SLS offre una soluzione sostanzialmente più rapida, semplice ed economica.
Inizialmente, il team produceva le parti con la stampa 3D a modellazione a deposizione fusa (FDM), che in quel momento era la tecnologia più accessibile e adatta alle necessità dell'azienda. Tuttavia, i limiti di questa tecnologia sono emersi presto: non permetteva di incrementare la produzione a volumi sufficienti per soddisfare l'ordine e le parti non raggiungevano la qualità industriale richiesta.
La stampa 3D SLS sarebbe stata la soluzione ideale, ma il costo degli apparecchi, che si aggirava intorno ai 200 000 €, li rendeva inaccessibili per le piccole imprese. Con il lancio della serie Fuse di Formlabs, la situazione è cambiata.
"La stampa SLS è perfetta per MOSOLF, poiché garantisce qualità eccellente, accuratezza elevata, alte prestazioni dei materiali e la possibilità di produrre molti componenti contemporaneamente. È anche conveniente dal punto di vista economico, poiché l'intero sistema è estremamente accessibile", ha affermato Gerhard Duda, AD e fondatore di 3D-WERK Black Forest GmbH, partner di Formlabs che ha collaborato fin dall'inizio con il team di MOSOLF per individuare le soluzioni migliori per le applicazioni dell'azienda.
"L'ecosistema Fuse era perfetto per noi perché è il più facile da gestire in termini di gestione e workflow", ha aggiunto Busam.
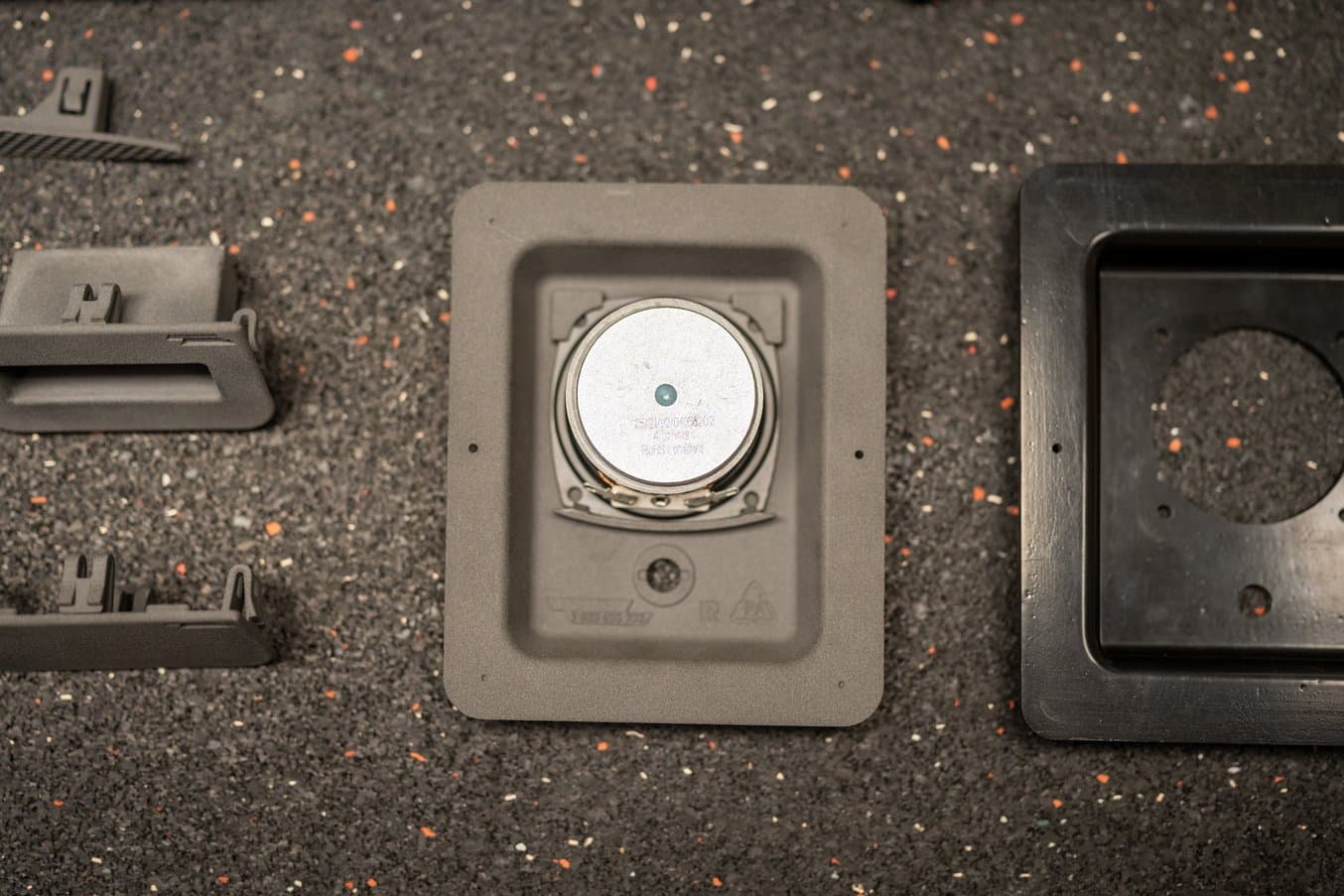
Questo coperchio per altoparlante è stato progettato per ridurre i costi di pre-installazione del 70%. Il corpo dell'altoparlante si collega direttamente all'inserto, eliminando la necessità di saldature o fissaggi meccanici.
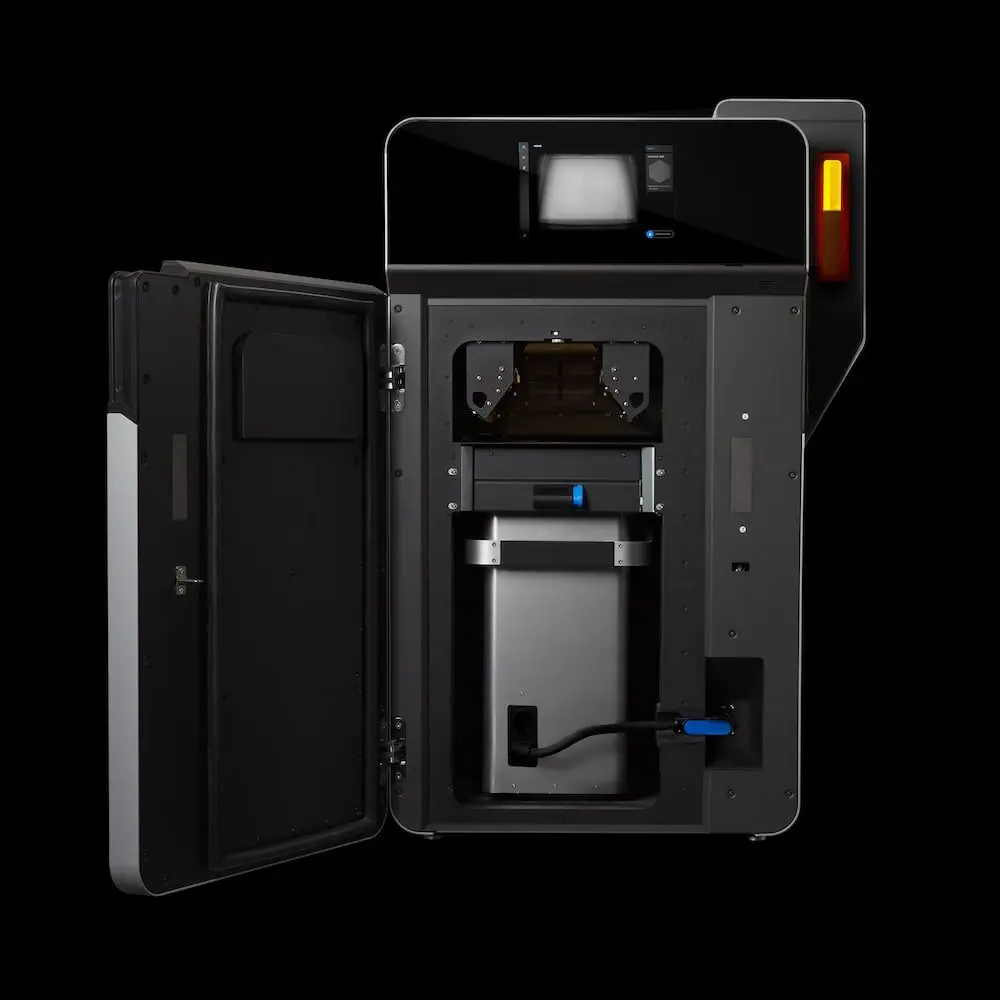
Produzione rapida di parti SLS ad alte prestazioni con la nuova Fuse 1+ 30W
Guarda la nostra dimostrazione di prodotto per un'introduzione alla Fuse 1+ 30W e alla stampa 3D SLS svolta dagli esperti di Formlabs.
Parti per utilizzo finale personalizzate entro 24 ore con la stampa 3D SLS
Il principale vantaggio della produzione additiva rispetto ai tradizionali metodi di produzione di massa, come stampaggio a iniezione, termoformatura o formatura della lamiera, è che permette di produrre parti per utilizzo finale personalizzate o in volumi ridotti senza necessità di attrezzature costose.
"Utilizziamo la tecnologia SLS e in particolare la Fuse 1+ 30W per diversi componenti, dai design più piccoli e semplici alla complessa console installata sui veicoli. Abbiamo adottato ampiamente questa tecnologia e la Fuse 1+ 30W soddisfa circa l'80% delle nostre esigenze", ha dichiarato Tiberiu Morariu, responsabile di prototipazione, design e ideazione tecnica presso MOSOLF.
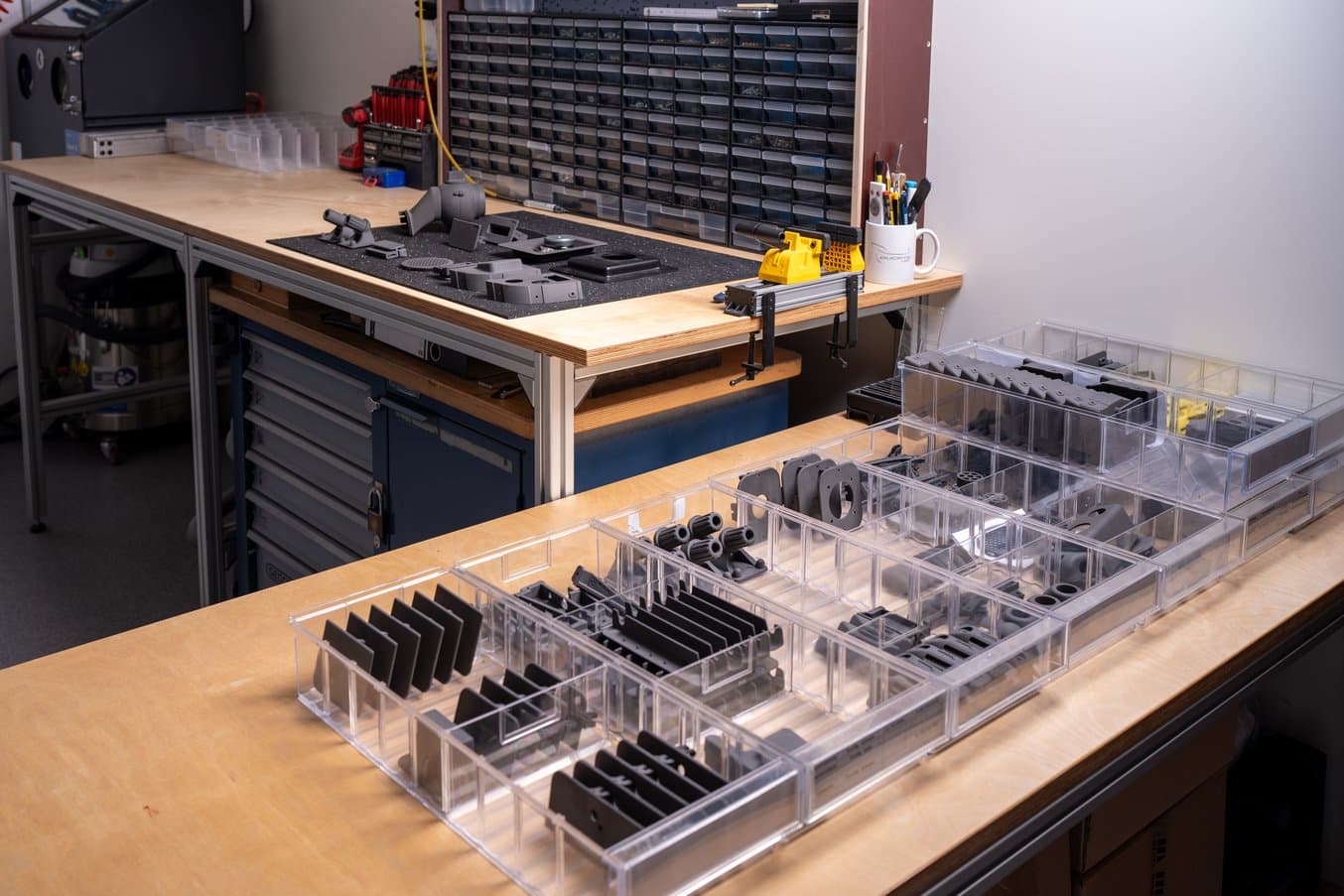
Il team di MOSOLF utilizza la stampa 3D SLS per produrre decine di design personalizzati, dai piccoli coperchi e involucri ai grandi assemblaggi in più parti e componenti del cruscotto.
"I requisiti possono variare non solo tra uno stato e l'altro, ma anche tra una stazione di polizia e l'altra. La stampa 3D consente di adattarsi più facilmente a queste differenze. È possibile modificare velocemente il design nel passaggio da un veicolo all'altro. Anche se il veicolo e la forma sono gli stessi, i sistemi installati possono essere molto diversi", ha spiegato Morariu.
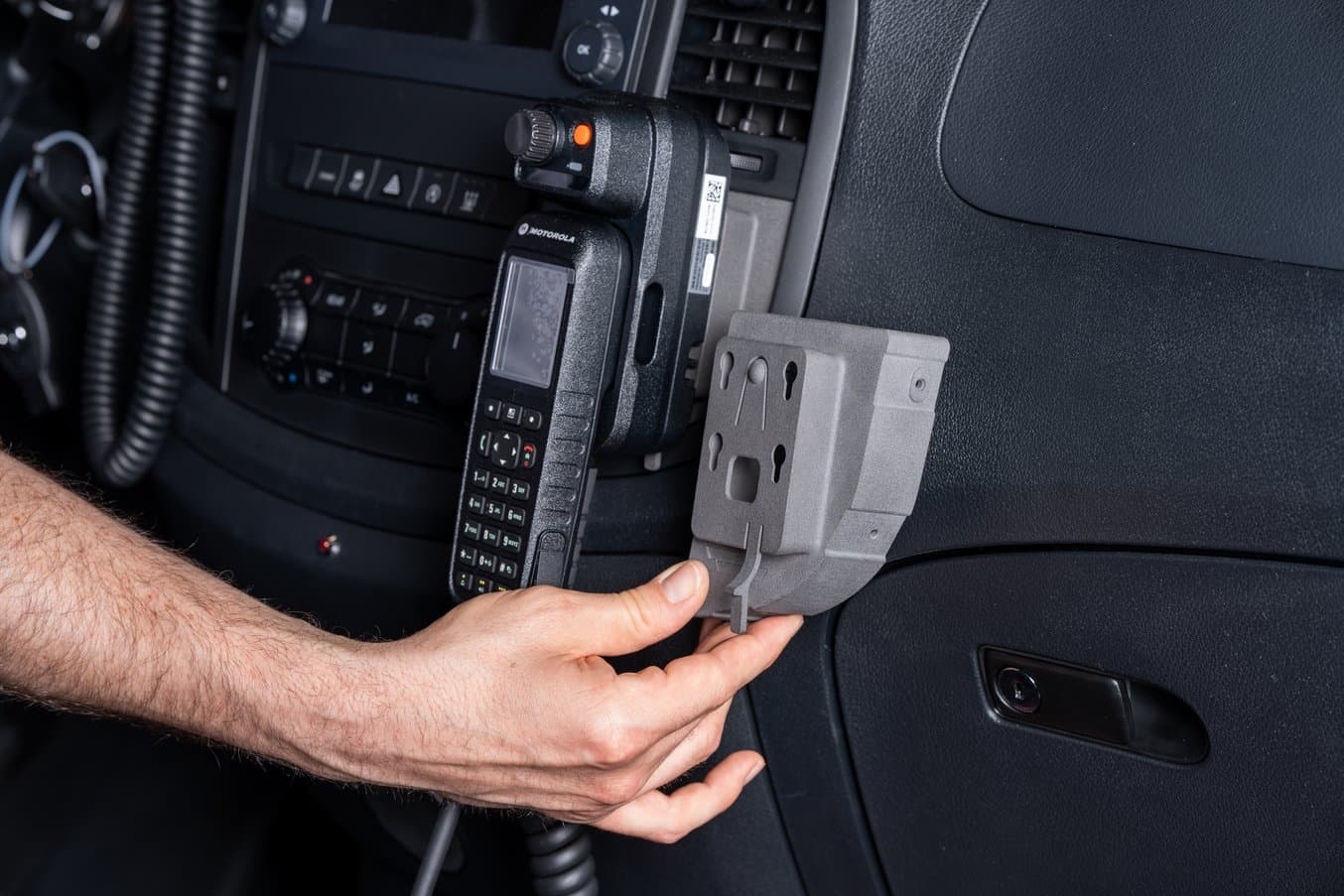
L'attacco per la radio rappresenta un eccellente esempio di personalizzazione. Sebbene l'attacco alla console sia identico per tutti i furgoni Mercedes, l'assemblaggio complessivo può essere facilmente modificato utilizzando diversi supporti per radio provenienti da varie aziende.
Questa versatilità semplifica e accelera notevolmente il processo di prototipazione e produzione, poiché sia i prototipi che le parti per utilizzo finale possono essere realizzati con lo stesso apparecchio.
"Per un designer, non c'è nulla di più gratificante che concepire un'idea, disegnarla e poterla avere tra le mani già il giorno successivo", ha affermato Morariu.
"La stampa 3D ha avuto un impatto significativo sulla produzione in-house, poiché ha accelerato notevolmente i tempi in molte aree. I metodi tradizionali richiedono dalle quattro alle sei settimane per la consegna, soprattutto se le parti devono essere rivestite. Al contrario, con la stampa 3D possiamo produrre le parti in una sola notte. Senza la stampa 3D, i nostri processi produttivi sarebbero probabilmente molto più lunghi e complessi, poiché dovremmo produrre e adattare ogni parte più volte."
Carsten Busam, responsabile della pianificazione di progetto presso MOSOLF Special Vehicles GmbH
Stampa 3D SLS | Formatura della lamiera | Termoformatura | Stampaggio a iniezione | |
---|---|---|---|---|
Tempo dal design al prototipo alla parte in serie | 1-2 settimane | 6-8 settimane | 6-8 settimane | 6-8 settimane |
Tempo di realizzazione per parti per utilizzo finale | 1-2 giorni | 6-8 settimane | 6-8 settimane | 6-8 settimane |
Altri fattori | Nessuna attrezzatura richiesta Personalizzazione semplice Libertà di design Aspetto estetico straordinario | Richiede l'uso di attrezzature Libertà di design limitata Più difficile da personalizzare Aspetto estetico non soddisfacente | Richiede l'uso di attrezzature Libertà di design limitata Più difficile da personalizzare | Richiede attrezzature costose Nessuna possibilità di personalizzazione Meno libertà di design |
"Al giorno d'oggi i veicoli sono sempre più curati dal punto di vista estetico, con interni meno standard e spazi per riporre gli oggetti sempre più dinamici e sofisticati. La stampa 3D riveste un ruolo fondamentale nel design e nell'ergonomia dei veicoli, poiché offre risultati che altre tecnologie, come la termoformatura o la formatura della lamiera, non sempre riescono a garantire. Inoltre, la stampa 3D permette di risolvere in modo ottimale il montaggio sul veicolo, anche con forme complesse. Grazie alla stampa 3D, posso progettare con maggiore libertà, sviluppare appieno la mia creatività nel design e nelle forme."
Tiberiu Morariu, responsabile di prototipazione, design e ideazione tecnica presso MOSOLF Special Vehicles GmbH
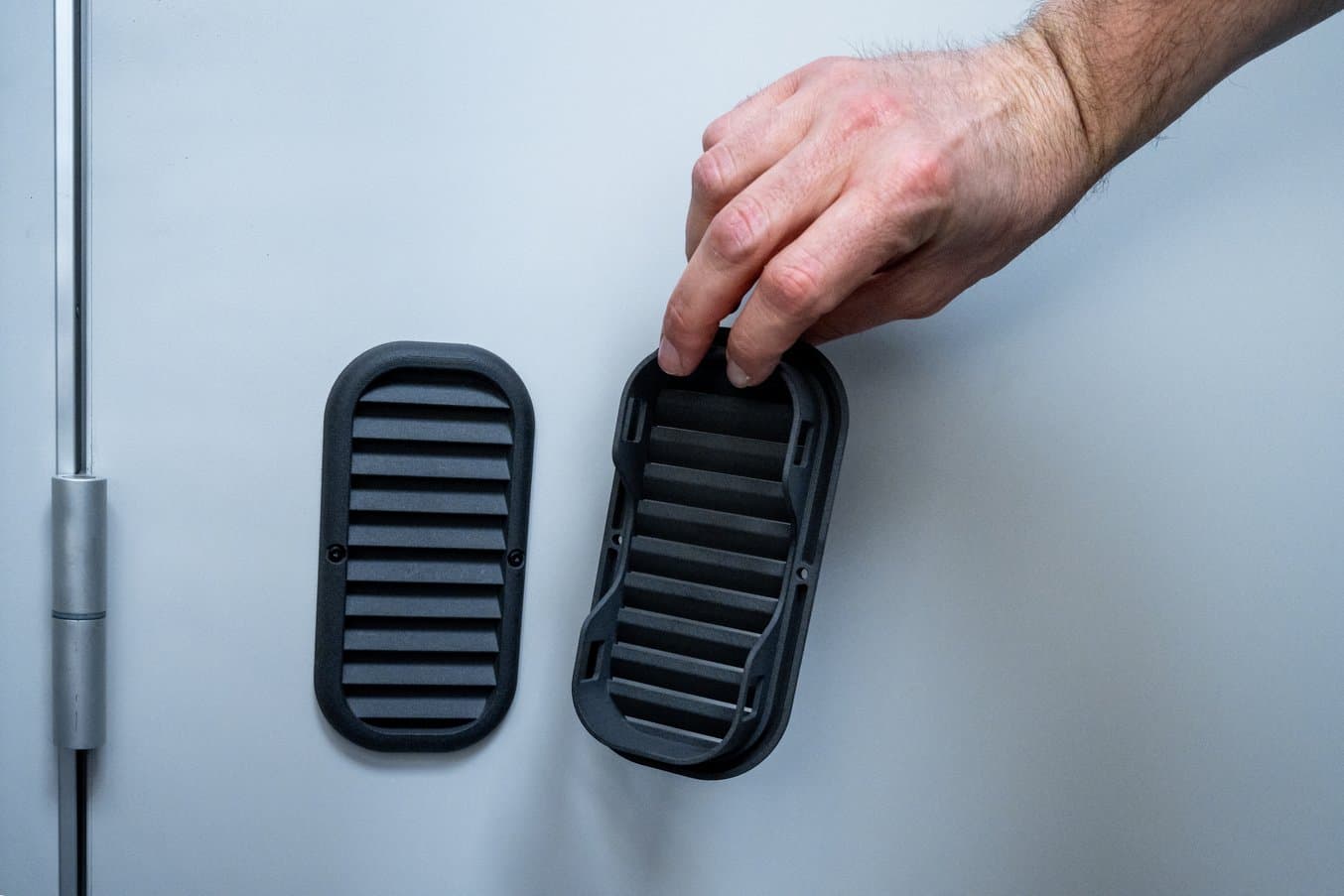
Questa presa d'aria è una valvola unidirezionale che divide il vano nero da quello bianco in un veicolo specializzato per le indagini sugli incendi dolosi. Si tratta di un assemblaggio dal design relativamente complesso, composto da tre componenti avvitati tra loro. Inizialmente, il team ha tentato di produrla tramite stampa 3D FDM, ma ha riscontrato difficoltà dovute alla forma circolare e alle pareti sottili, perciò è passato alla stampa 3D SLS, che offre una maggiore libertà di design.
Uno dei principali vantaggi della stampa 3D SLS è che i team di ingegneria conoscono bene le proprietà meccaniche dei materiali disponibili, come il nylon, che è ampiamente utilizzato nel settore automobilistico per la produzione di parti interne ed esterne. Il team di MOSOLF ha una buona conoscenza delle prestazioni di una parte in nylon realizzata con la stampa 3D SLS, quindi può progettare tenendo conto della funzionalità e persino sostituire alcune parti in metallo originali.
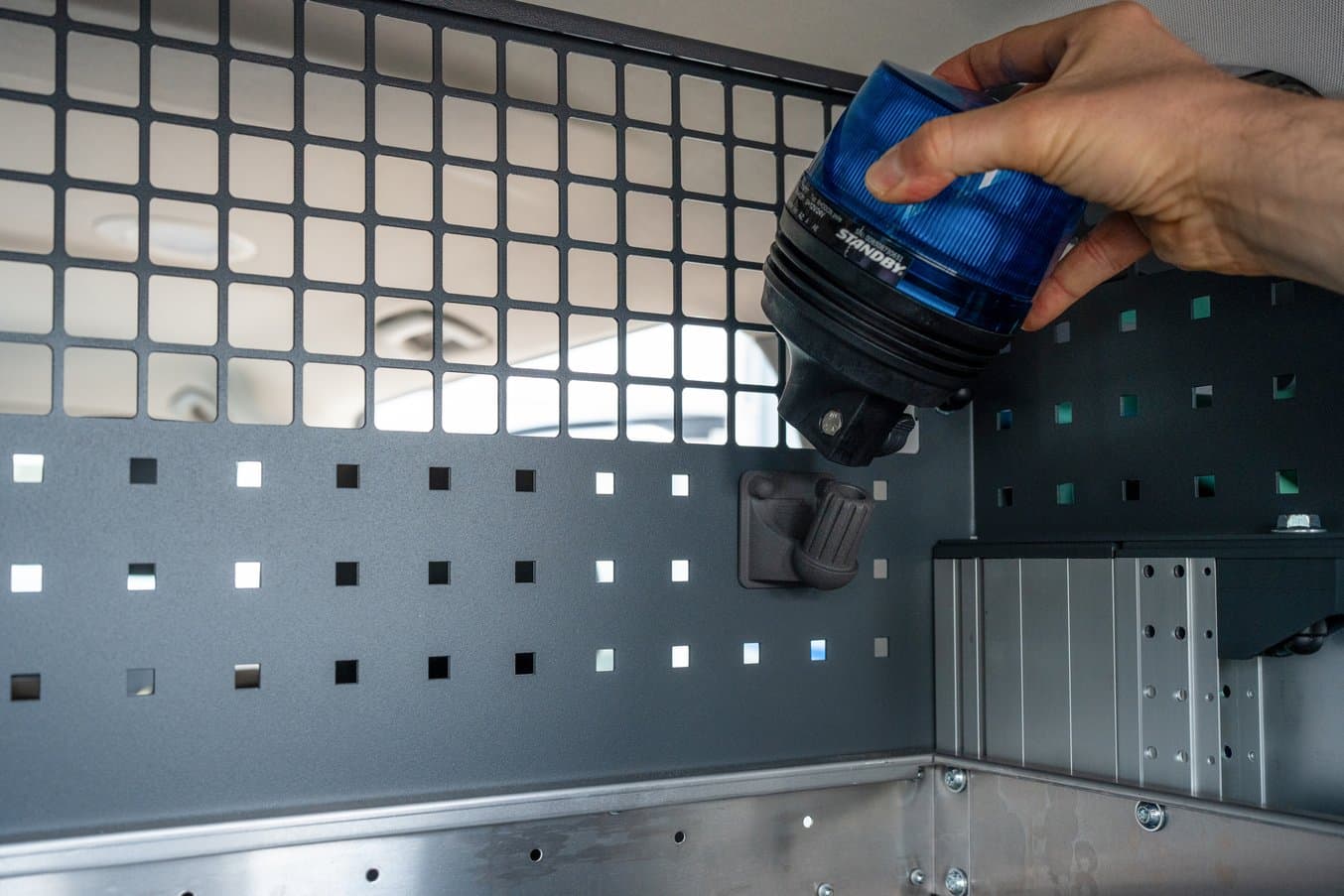
Attacco a clip nel vano bagagli per una luce di emergenza rimovibile.
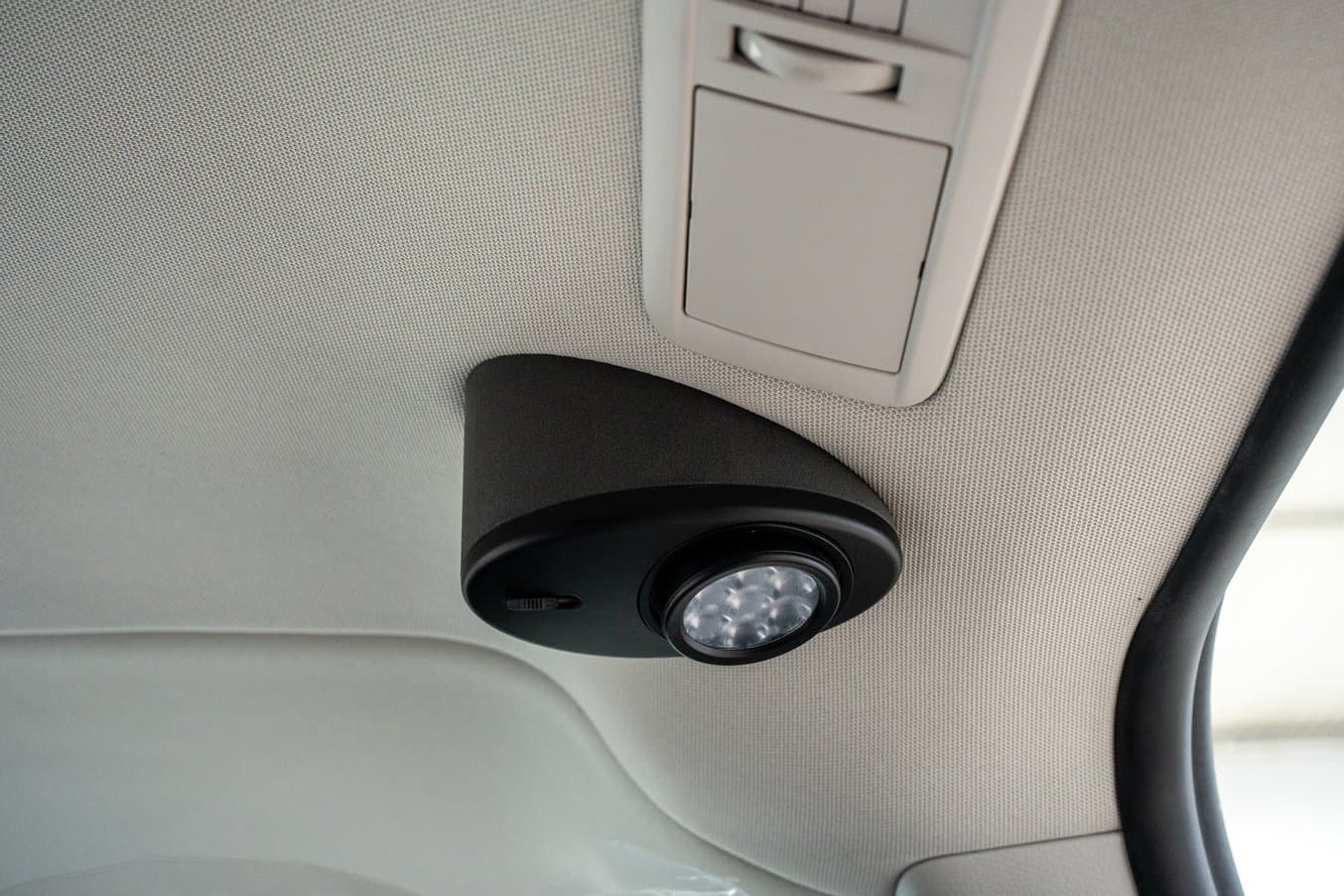
Alloggiamento e attacco per una luce da applicare al cielo del veicolo.
"L'ecosistema Fuse offre un materiale perfetto: pronto all'uso, presente sul mercato da molto tempo e testato in modo approfondito", ha affermato Duda.
Oltre alla resistenza, uno dei criteri più importanti per le applicazioni nel settore automobilistico è la resistenza alle alte temperature. L'acido polilattico (PLA) per la stampa FDM è un materiale da escludere a causa della sua temperatura di distorsione termica di soli 50 °C a 0,45 MPa. L'acrilonitrile-butadiene-stirene (ABS) ha una temperatura di distorsione termica di 90 °C a 0,45 MPa, che è migliore ma spesso insufficiente per molte applicazioni. Al contrario, la Nylon 12 Powder di Formlabs, con una temperatura di distorsione termica di 171 °C a 0,45 MPa, offre una resistenza alle alte temperature significativamente superiore, riducendo il rischio che parti funzionali, come il supporto di una radio, si danneggino in caso di surriscaldamento, ad esempio quando l'auto resta parcheggiata a lungo sotto il sole.
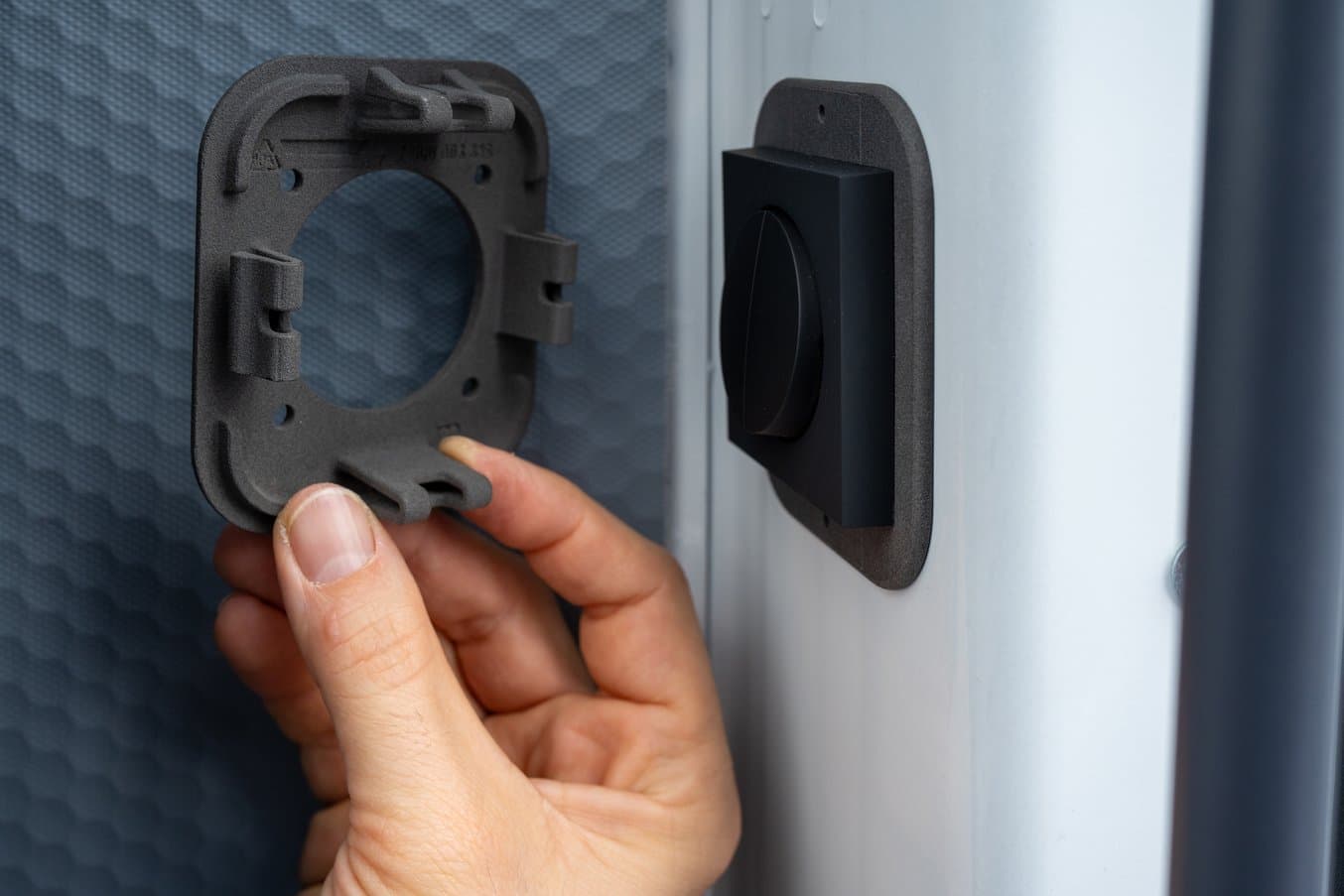
Alloggiamento per presa elettrica.
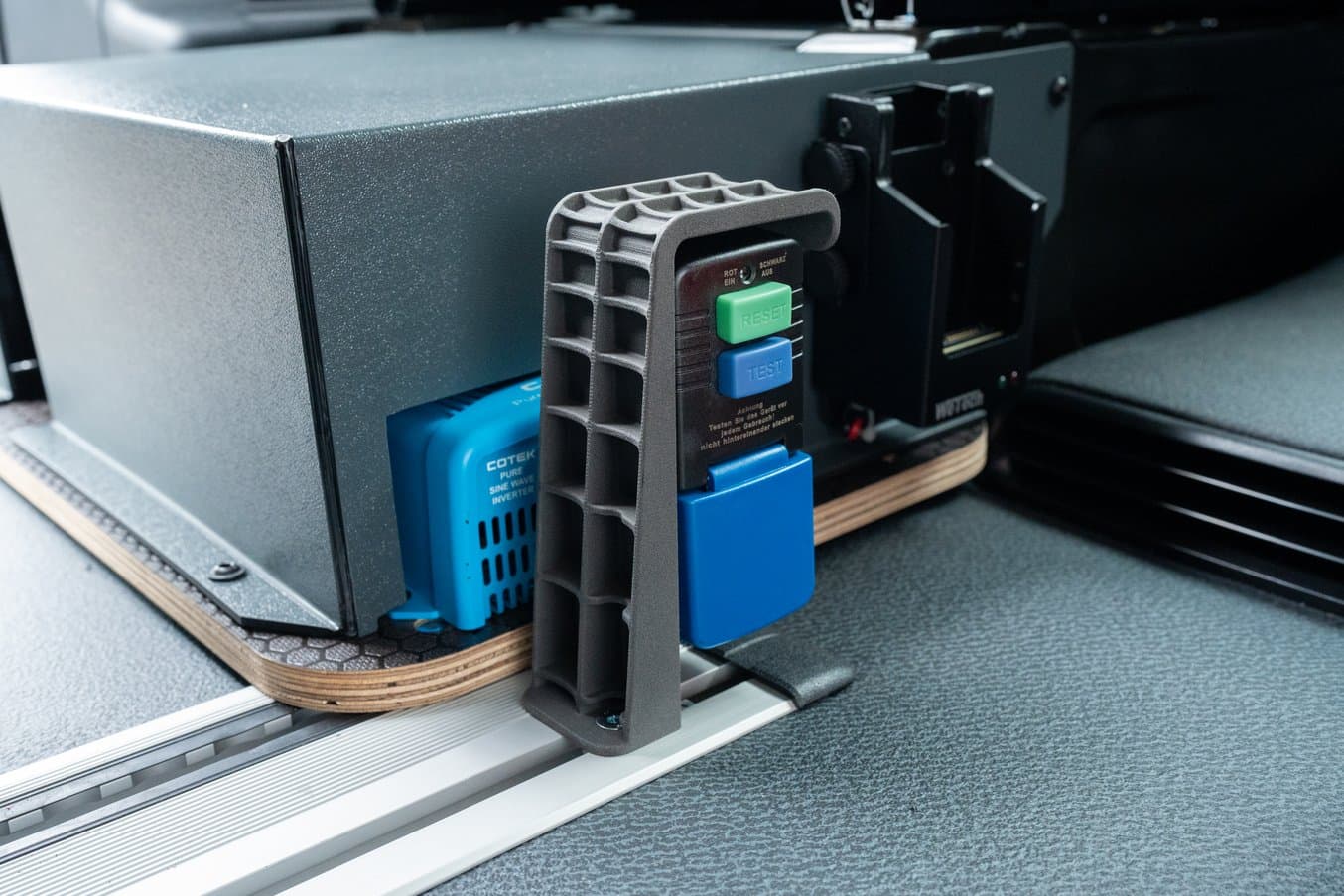
Coperchio protettivo per evitare danni accidentali durante gli spostamenti all'interno del veicolo.
In alcuni casi, i veicoli vengono noleggiati dalle forze di polizia o di emergenza e poi venduti alla popolazione civile o ad altri dipartimenti una volta terminato il loro utilizzo. Per questo motivo, il team di MOSOLF deve adattare questi veicoli senza danneggiare o modificare nulla in modo permanente, così da facilitare il ripristino dello stato originale al termine del loro ciclo di vita. La produzione additiva facilita questa operazione: invece di modificare in modo permanente i componenti esistenti, il team li sostituisce con parti stampate in 3D che possono essere sostituite in un secondo momento.
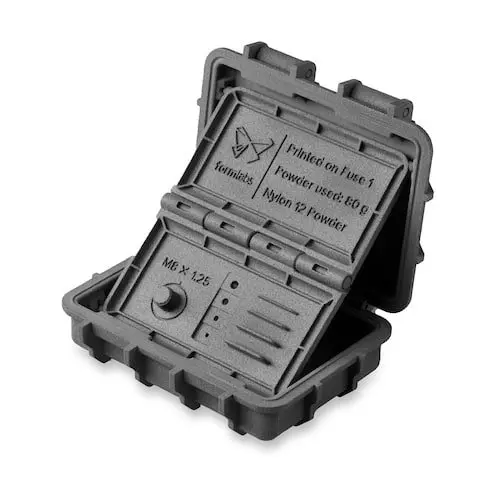
Richiedi un campione SLS gratuito
Guarda e tocca con mano la qualità di Formlabs. Saremo lieti di inviare presso la tua azienda una parte SLS stampata con la Fuse 1+ 30W come campione gratuito.
Verso un futuro in cui i veicoli della polizia conterranno sempre più componenti stampati in 3D
Sulla base del successo ottenuto con la stampa 3D SLS, i team di MOSOLF e 3D-WERK stanno ora valutando come impiegare altri materiali e altre stampanti per sostituire un numero ancora maggiore di parti nei veicoli per uso speciale.
"Nonostante anni di esperienza nel campo della produzione additiva, mi capita ancora oggi di rimanere stupito di fronte a prodotti che abbiamo progettato e stampato noi stessi, grazie alle funzionalità e alle possibilità offerte dalla stampa 3D", ha dichiarato Michael Ringwald, amministratore delegato di MOSOLF.