500 parti in due giorni: come la stampa 3D ha contribuito alle prove di trapanatura per Airbus
Una delle sfide principali nella produzione manifatturiera avanzata è assicurarsi che strutture complesse come robot, assemblaggi assistiti digitalmente e tecnologie di lavorazione meccanica vengano montate correttamente. Con sede nella Factory 2050, una fabbrica da 43 milioni di sterline, presso l'Advanced Manufacturing Research Centre (AMRC), l'Integrated Manufacturing Group è un gruppo di ricerca che lavora con partner industriali per unire tecnologie all'avanguardia e sviluppare sistemi integrati.
Di recente si sono occupati di un progetto per Airbus, il più grande produttore aerospaziale in Europa, che riguardava trapanatura ad alta tolleranza e lavorazione meccanica di componenti in fibra di carbonio, alluminio e titanio.
Dati i rigidi requisiti aerospaziali, era fondamentale evitare la contaminazione incrociata dei fori durante queste prove. Poco dopo l'avvio del progetto, il team si è reso conto che la soluzione pianificata non sarebbe stata sufficiente per risolvere il problema, con il rischio di dover affrontare settimane di ritardi nel caso in cui avessero dovuto lavorare o creare le parti di ricambio tramite stampaggio a iniezione.
Scopri da George Sleath, un ingegnere di progetto presso l'Integrated Manufacturing Group, come il team ha utilizzato la stampa 3D per creare rapidamente 500 tappi per foratura ad alta precisione, riducendo i tempi di produzione da diverse settimane a soli tre giorni.
Sleath e il team di ingegneri hanno lavorato con la postazione di produzione additiva a libero accesso dell'AMRC per creare le parti di cui avevano bisogno. Leggi il nostro caso di studio per scoprire come il libero accesso alla stampa 3D può aiutare centinaia di ingegneri all'interno della struttura.
Testare diversi metodi per evitare la contaminazione incrociata
"Uno dei requisiti principali del processo di trapanatura era evitare le contaminazioni nei fori. Ossia, dopo aver eseguito una foratura, prima di passare al foro successivo, dovevamo coprire il buco, in modo da evitare che qualsiasi scheggia o residuo generato durante la seconda trapanatura non lo contaminasse. Quando ci siamo resi conto di aver bisogno di un tappo particolare per questa funzione, avevamo a disposizione poco tempo per trovare una soluzione", racconta Sleath.
Gli ingegneri hanno prima provato a usare un pezzo di alluminio con un piccolo O-ring, ma non era sufficiente. Di conseguenza, l'intero progetto veniva rallentato perciò, dato il tempo limitato disponibile per terminare i test, questa soluzione non era accettabile.
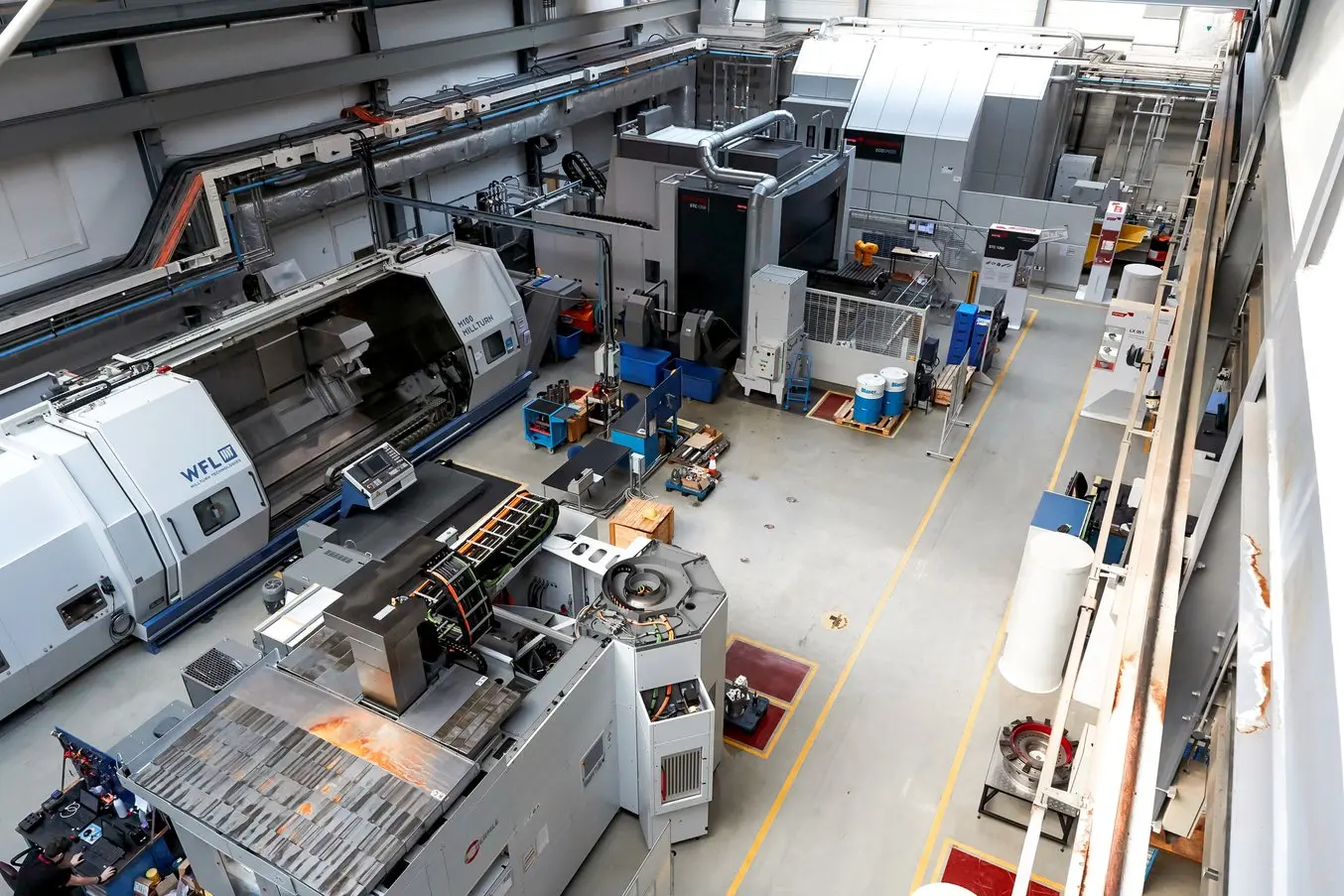
Il team quindi creò un nuovo design: un piccolo disco sul cui bordo c'era una canale di taglio per un O-ring. La parte aveva dei requisiti di tolleranza relativamente stretti; se il taglio fosse stato troppo grande e l'anello fosse sprofondato nel lato della parte, avrebbe sigillato la plastica invece dell'O-ring. L'intervallo di tolleranza accettabile era metà dello spessore dell'O-ring, ossia circa mezzo millimetro.
La varietà delle parti comportava anche ulteriori complicazioni per la produzione. "Dovevamo avere a disposizione delle varianti, perché i fori erano di più dimensioni, e quindi avevamo bisogno di coperchi protettivi diversi. Dal punto di vista della progettazione virtuale, non ci vuole molto tempo per cambiare una dimensione, ma se devi stampare a iniezione le parti, hai bisogno di uno stampo nuovo ogni volta", spiega Sleath.
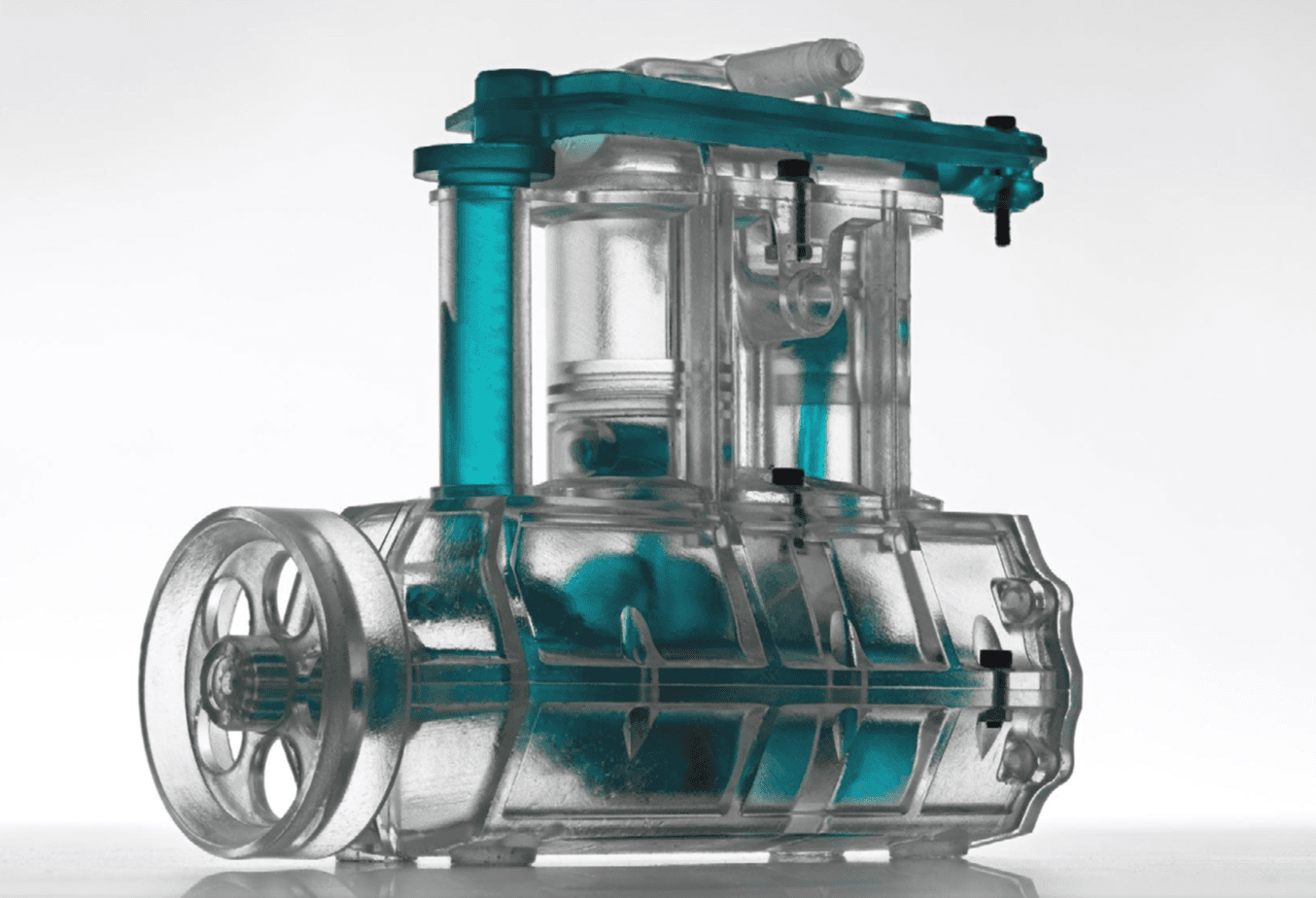
Aggiustaggio in campo ingegneristico
Scarica il nostro whitepaper per scoprire di più sulla tolleranza e l'aggiustaggio nella progettazione per la stampa 3D di assemblaggi funzionali.
Scarica il whitepaperStampa 3D di 500 coperchi protettivi in due giorni
Al team servivano circa 500 di questi piccoli coperchi protettivi nell'arco di dieci giorni, e perciò l'unica opzione di produzione disponibile era la stampa 3D.
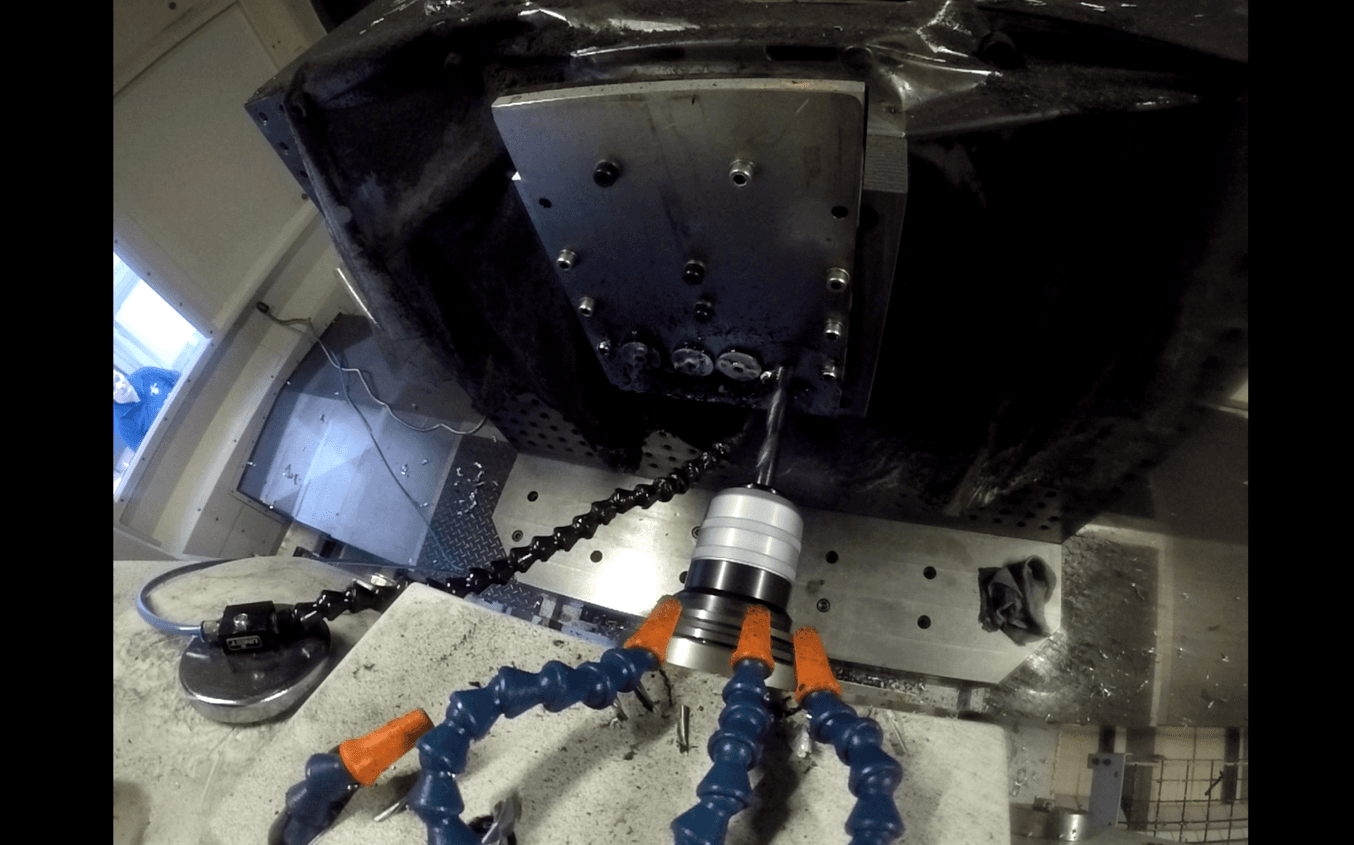
Non sapendo bene al tempo quali fossero le capacità interne dell'AMRC, Sleath chiese prima un preventivo a tre tipografie, ma le offerte erano esagerate, tenendo conto del valore assegnato alle parti all'interno del progetto.
"Ne parlai con Mark Cocking del nostro gruppo di progettazione e prototipazione e gli chiesi se fosse possibile produrre i pezzi internamente. Non si è fatto sentire per 24 ore, ma quando l'ho ricontattato mi ha detto che ne avevano già stampati la metà. 250 coperchi protettivi stampati in 24 ore: era straordinario" dice Sleath.
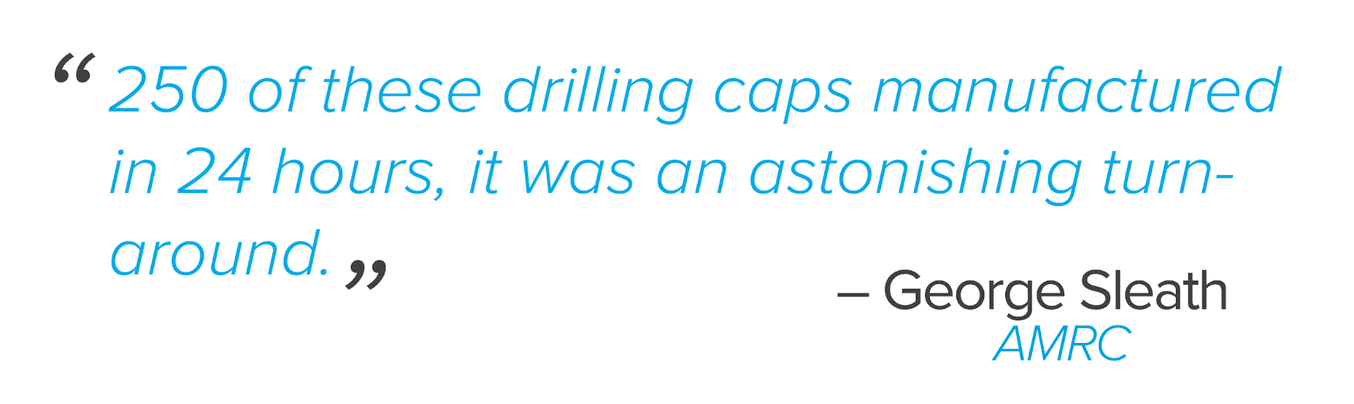
Alla fine, Cocking è riuscito a far produrre tutti i componenti in due giorni.
"Questo non solo ha voluto dire che le parti erano pronte per l'uso prima del previsto, ma ci ha dato anche l'opportunità di concentrarci sul progetto, senza doverci preoccupare di quando sarebbero arrivati i coperchi" racconta Sleath.
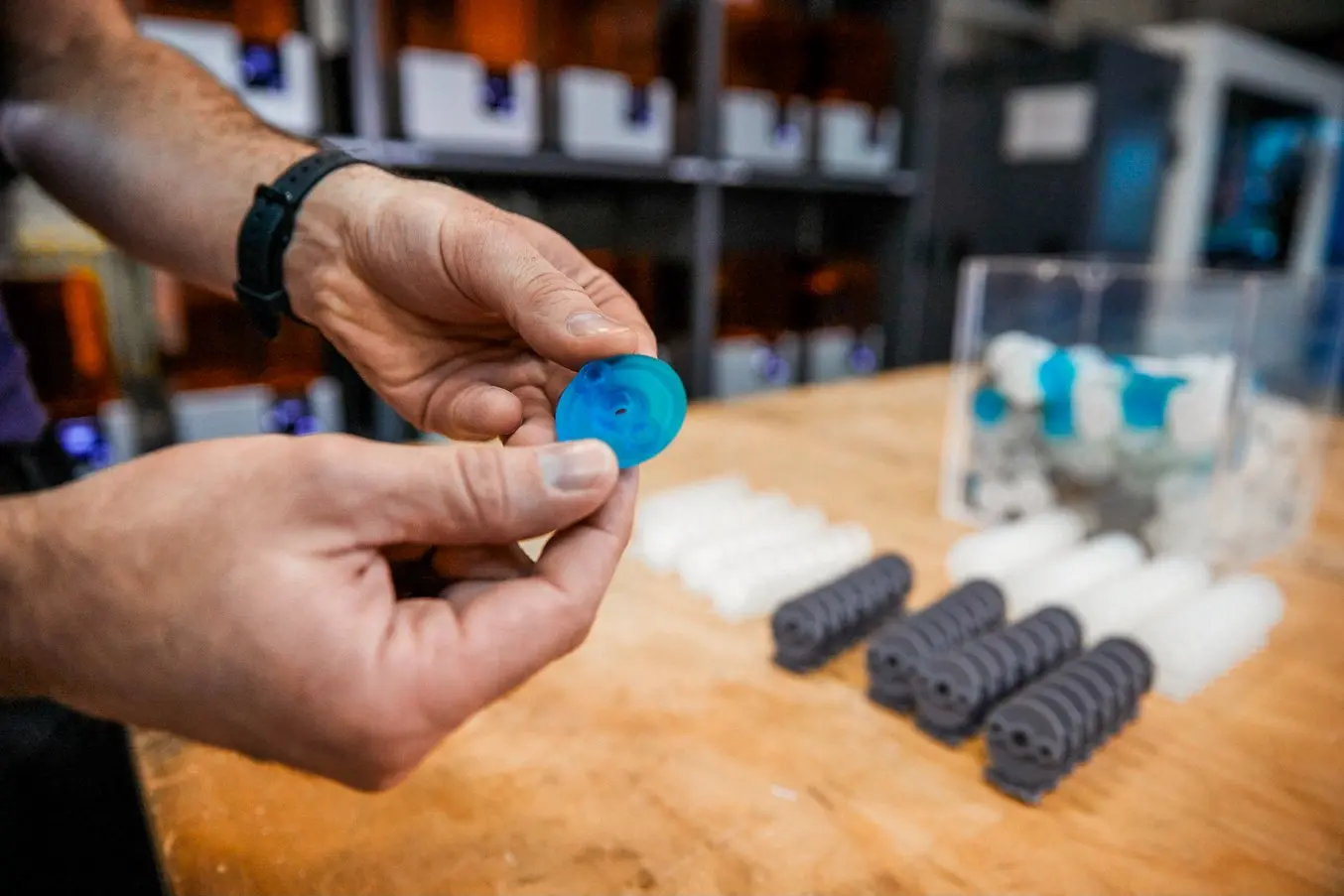
L'AMRC è riuscito a stampare in 3D 500 dei diversi coperchi protettivi in soli due giorni. Inoltre, grazie alla stampa 3D, gli ingegneri hanno potuto inserire delle geometrie nella parte, che hanno stampato a sua volta in 3D all'interno di uno strumento; ciò ha permesso di installare i coperchi in maniera facile e veloce.
Le postazioni di stampa 3D in house offrono flessibilità e possibilità di iterazione
Inoltre, dato che le parti sono state stampate in 3D, gli ingegneri hanno potuto inserirvi delle geometrie, che hanno stampato a sua volta in 3D all'interno di uno strumento; ciò ha permesso di installare i coperchi in maniera facile e veloce.
"Il riscontro degli operatori che hanno installato i coperchi è stato fantastico. La maggioranza delle parti ha funzionato come doveva e nessuna si è rotta durante il progetto", racconta Sleath.
Oltre al rapido tempo di produzione e il costo ridotto, un vantaggio importante offerto dall'accesso alla stampa 3D in house era la flessibilità.
"Se il design non avesse funzionato una volta testato, avremmo potuto rimandarlo rapidamente in progettazione e apportare le modifiche necessarie. Se invece avessimo utilizzato i servizi di una tipografia, ci saremmo resi conto di dover fare delle piccole modifiche solo qualche settimana dopo, una volta ricevute tutte le 500 parti", spiega Sleath.
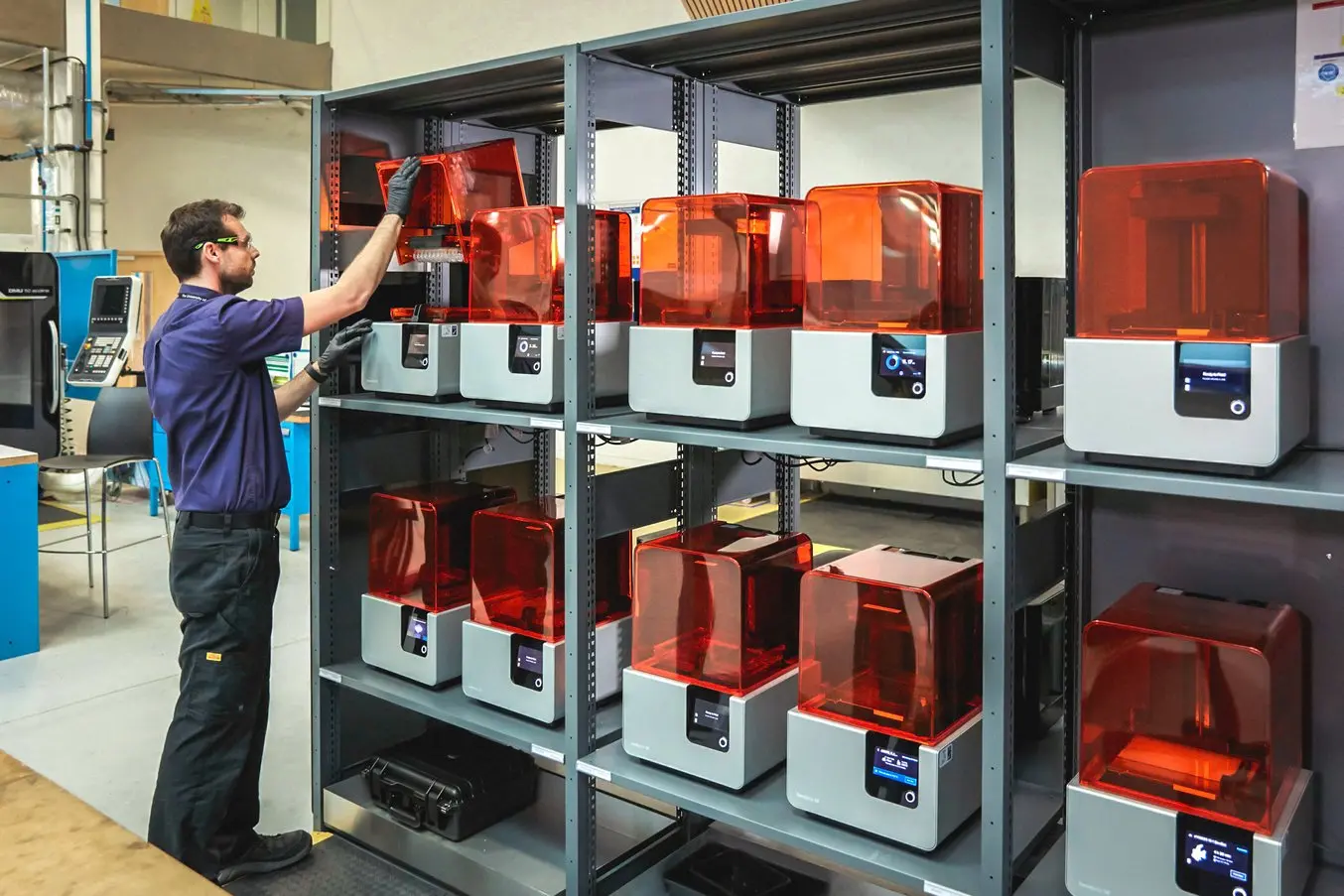
Scopri come una postazione di stampa 3D aiuta centinaia di ingegneri presso l'AMRC
"Mi piace molto utilizzare la stampa 3D per eseguire iterazioni rapidamente durante le fasi di progettazione. Creo una parte sulla stampante 3D, ne valuto le prestazioni sul campo e poi invio subito un nuovo design alla stampante. Data la velocità di stampa e il costo ridotto, a volte si riescono a creare due o tre modelli in un giorno solo. Grazie al nuovo progetto di libero accesso che si sta cercando di implementare nell'AMRC, penso che tutti inizieranno a usare molto di più la stampa 3D" dice Sleath.
Scopri di più sulla postazione di stampa 3D presso l'AMRC e su altre applicazioni, ad esempio una staffa del sensore resistente alle alte temperatura per la saldatura, staffe molto complesse per una pinza di presa robotizzata e rulli di avvolgimento dei filamenti personalizzati per la produzione di materiali compositi.
Vuoi saperne di più sulle stampanti e la tecnologia su cui è basata la postazione di stampa 3D dell'AMRC? Scopri le ultime stampanti 3D SLA di Formlabs, la Form 3 e il formato più grande Form 3L, e la raccolta di resine ingegneristiche di Formlabs , oppure richiedi un campione gratuito per toccare con mano la qualità della stampa 3D.