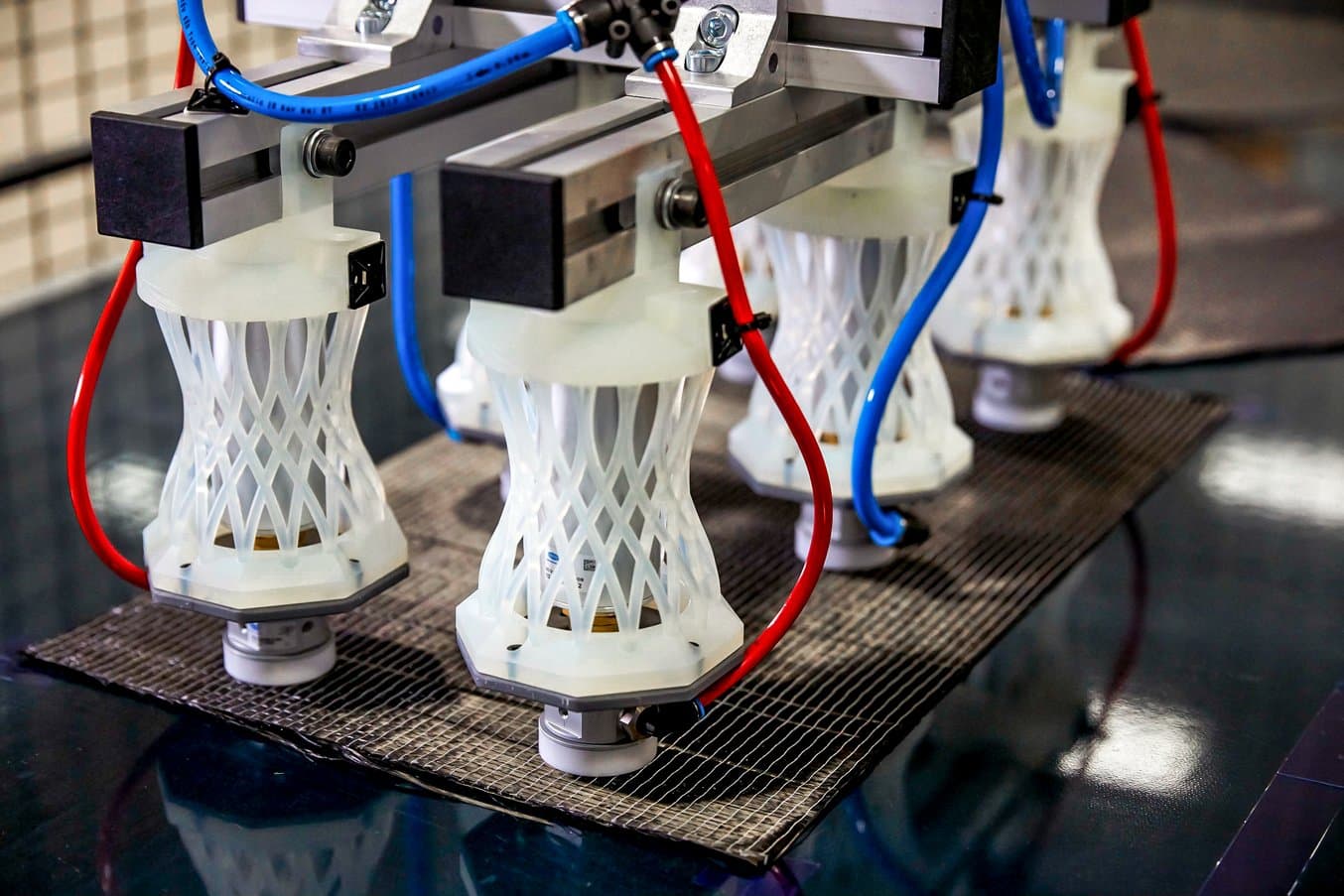
Le fibre di vetro e i materiali in fibra di carbonio sono sempre più utilizzati nell'industria aerospaziale, marina, automobilistica e in altre industrie di alto valore, perché offrono elevata resistenza e peso ridotto, ma presentano anche una serie di sfide dal punto di vista della produzione. Il centro di ricerca sui materiali compositi dell'Advanced Manufacturing Research Centre (AMRC) dell'Università di Sheffield conduce ricerche utilizzando metodi all'avanguardia nel tentativo di risolvere queste sfide.
In un progetto attuale, i ricercatori stanno esplorando la possibilità di automatizzare lo spostamento di strati mobili in fibra di carbonio con elevata precisione e velocità grazie all'utilizzo di un robot pick-and-place. Tuttavia, dopo un uso prolungato le staffe a L che sostengono le pinze ad aria compressa del robot iniziano a piegarsi attorno alle giunture, causando quindi guasti e costringendo i ricercatori a cercare una nuova soluzione.
Matthew Williams, il tecnico dei compositi al lavoro sul progetto, racconta le sfide di progettazione che ha affrontato durante la creazione di un componente elastico personalizzato e spiega come il team sia riuscito a produrre cinque iterazioni del complesso design in pochi giorni grazie alla stampa 3D.
Guarda la nostra intervista con il tecnico dei compositi Matthew Williams per vedere il robot pick-and-place in azione.
Williams ha lavorato con la postazione di produzione additiva a libero accesso dell'AMRC per creare le parti di cui avevano bisogno. Leggi il nostro caso di studio per scoprire come il libero accesso alla stampa 3D può aiutare centinaia di ingegneri all'interno della struttura.
La necessità di precisione nella produzione di materiali compositi
I materiali compositi traggono la loro resistenza dal modo in cui i filamenti di fibra sono tessuti e disposti all'interno delle parti. Ciò consente agli ingegneri di ottimizzare meticolosamente la progettazione in base alle sollecitazioni a cui si pensa di sottoporre i componenti, ma rende anche molto complesso il flusso di lavoro della produzione di compositi.
La posa dei fogli di fibra di carbonio è generalmente un processo manuale, ma l'interazione umana introduce alcune variazioni, poiché gli strati potrebbero deformarsi o non posizionarsi correttamente. Bastano pochi millimetri di errore per realizzare parti difettose e sprecare materiale costoso.
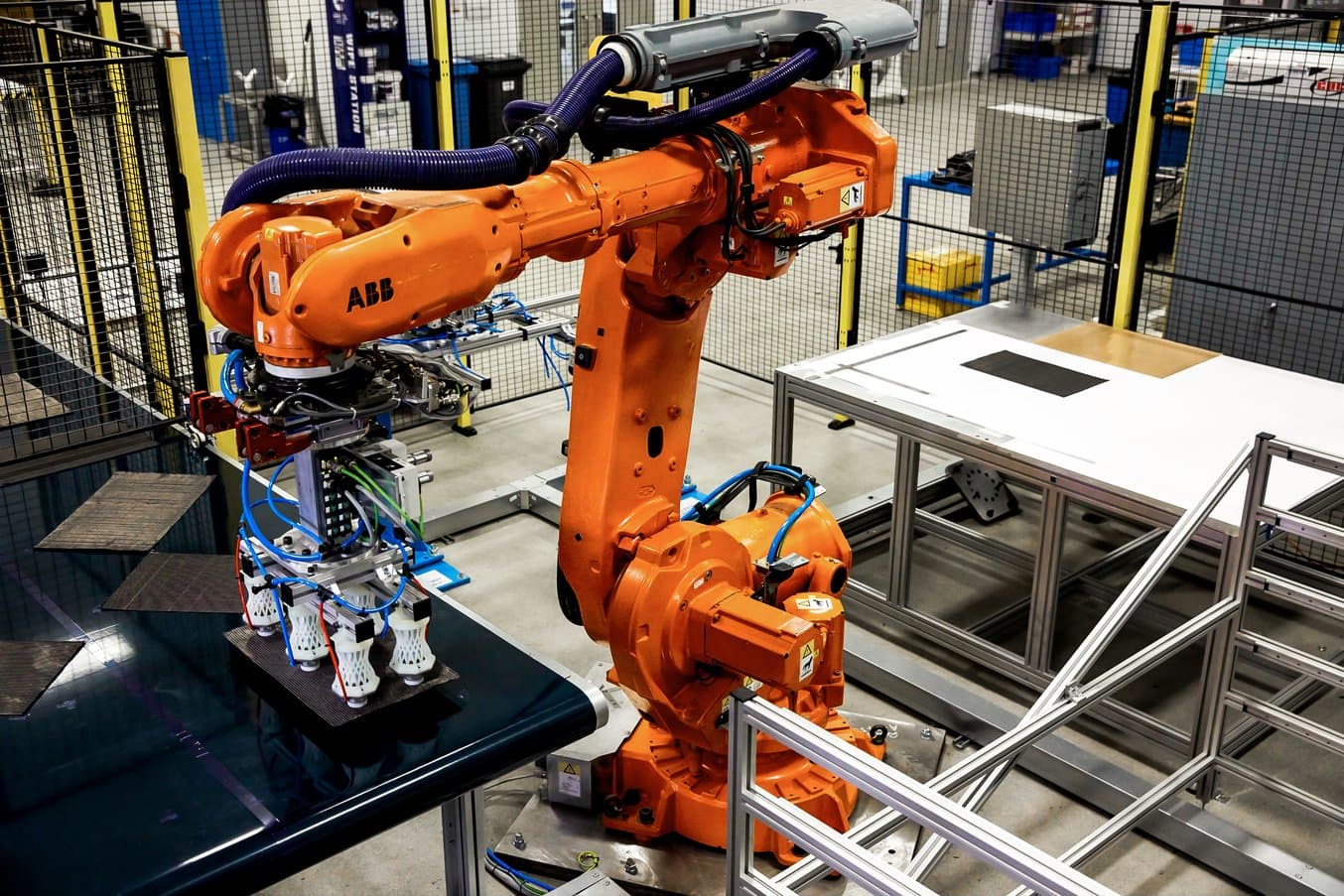
La cella robotica è progettata per automatizzare lo spostamento degli strati di composito. I fogli pretagliati entrano nella cella su un nastro trasportatore, da cui vengono prelevati tramite pinze fissate su un robot ABB a 5 assi, che sposta gli strati e li posiziona uno sopra l'altro.
Con una cella di robot pick-and-place progettata per creare un flusso di lavoro automatizzato, i ricercatori mirano a ridurre gli sprechi di materiale e aumentare la velocità e la precisione del processo. I fogli pretagliati di composito entrano nella cella su un nastro trasportatore, da cui vengono prelevati tramite pinze ad aria compressa fissate su un robot ABB a 5 assi, che sposta gli strati e li posiziona in maniera estremamente accurata uno sopra l'altro su un tavolo all'interno della cella.
Le staffe inizialmente fornite con il robot per sostenere le pinze erano dei supporti a L in alluminio fissati lateralmente all'effettore finale del robot. Tuttavia, poiché le diverse attrezzature della cella non sono perfettamente livellate, dopo un uso prolungato, le staffe hanno iniziato a piegarsi intorno alla giuntura della L. Con il passare del tempo questa piegatura è andata aumentando, finché la pinza non era più in grado di prelevare gli strati di compositi dal nastro trasportatore.
Da una semplice staffa a L a un design complesso
Progettare un componente con la giusta elasticità si è rivelata una sfida piuttosto complessa, e a Williams sono serviti cinque cicli di iterazioni per riuscirci.
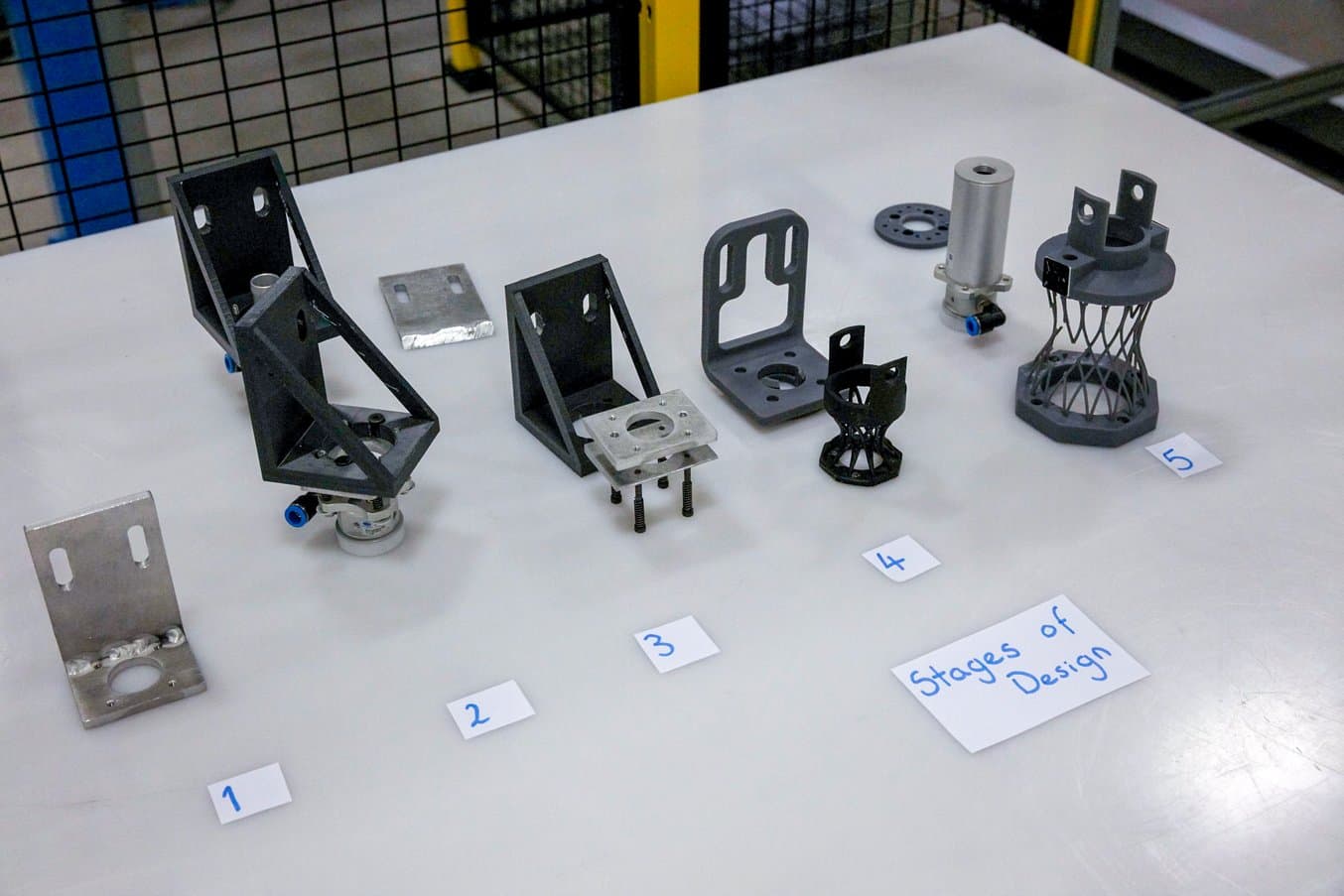
A Williams sono serviti cinque cicli di iterazioni, a partire da una staffa a L saldata in alluminio fino a un complicato design stampato in 3D in plastica.
"Ho iniziato con una staffa a L in alluminio composta solo da due piastre saldate assieme. Dato che si trattava di una saldatura, una volta che si piegava, non tornava al suo stato originale e rimaneva deformata. Perciò ho iniziato a usare la plastica, perché riprende la sua forma dopo le sollecitazioni. Si piegava molto più dell'alluminio però, quindi [le pinze] iniziavano a spargere fibre sul tavolo. Perciò abbiamo peggiorato il problema prima di risolverlo" spiega Williams.
Allora il ricercatore decise di cambiare il design. Piuttosto che essere montate sul lato, le pinze ad aria compressa vennero montate sotto la staffa. Quando la forza viene applicata dalla parte inferiore della staffa, questa non si piega, ma si comprime come una molla. Con il progredire della ricerca, Williams scoprì che le pinze facevano troppo rumore per essere sicure in un ambiente di lavoro. Aveva bisogno di mettere un silenziatore sulle pinze, quindi serviva una staffa più grande per poterlo alloggiare.
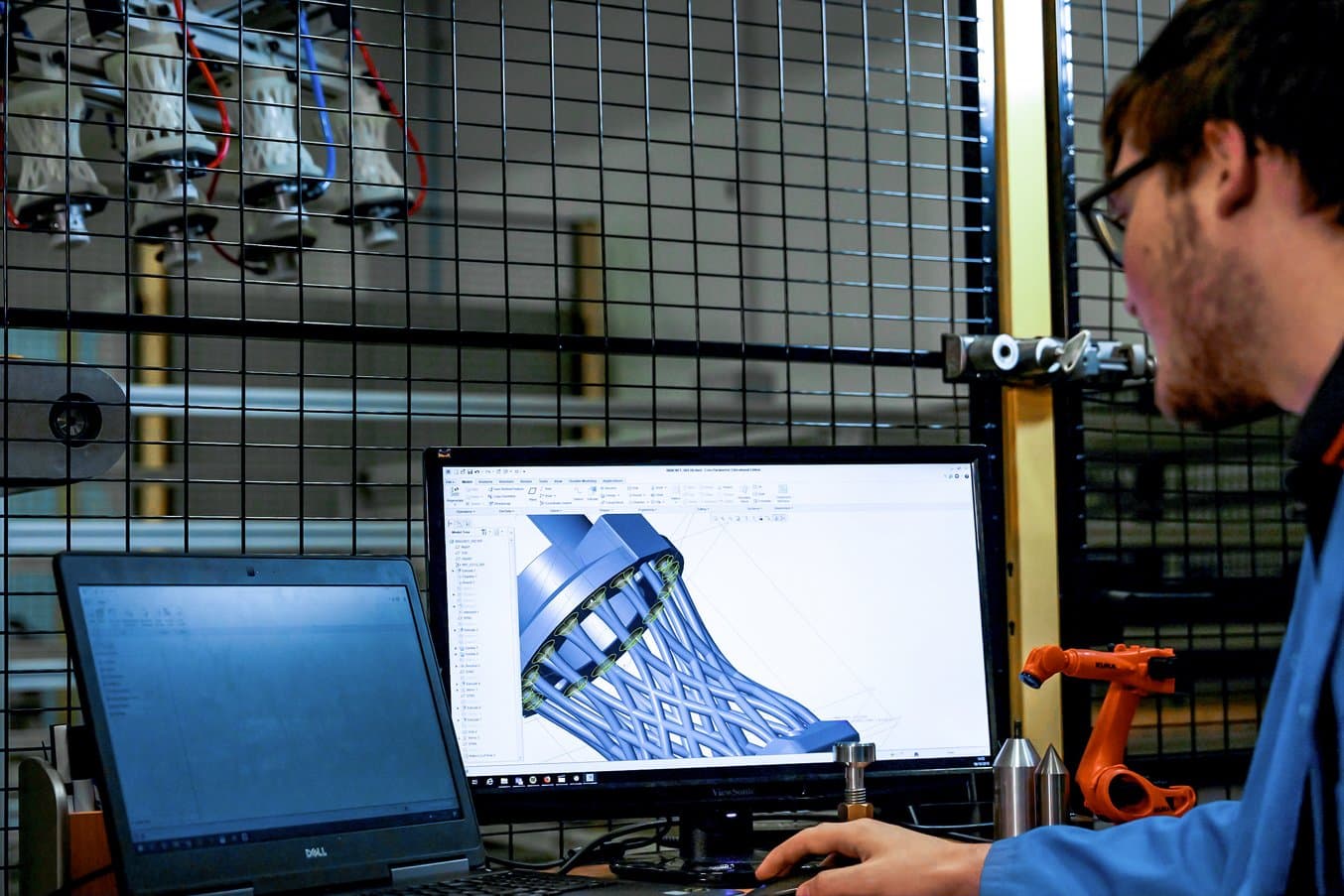
Nel design finale, le pinze ad aria compressa si trovano sotto la staffa, che si comprime come una molla.
"Ho reso la struttura più compatta e ho utilizzato un materiale più resistente, che funziona molto meglio, perché dona alla staffa maggiore elasticità. Si flette all'indietro e funziona alla perfezione" spiega Williams.
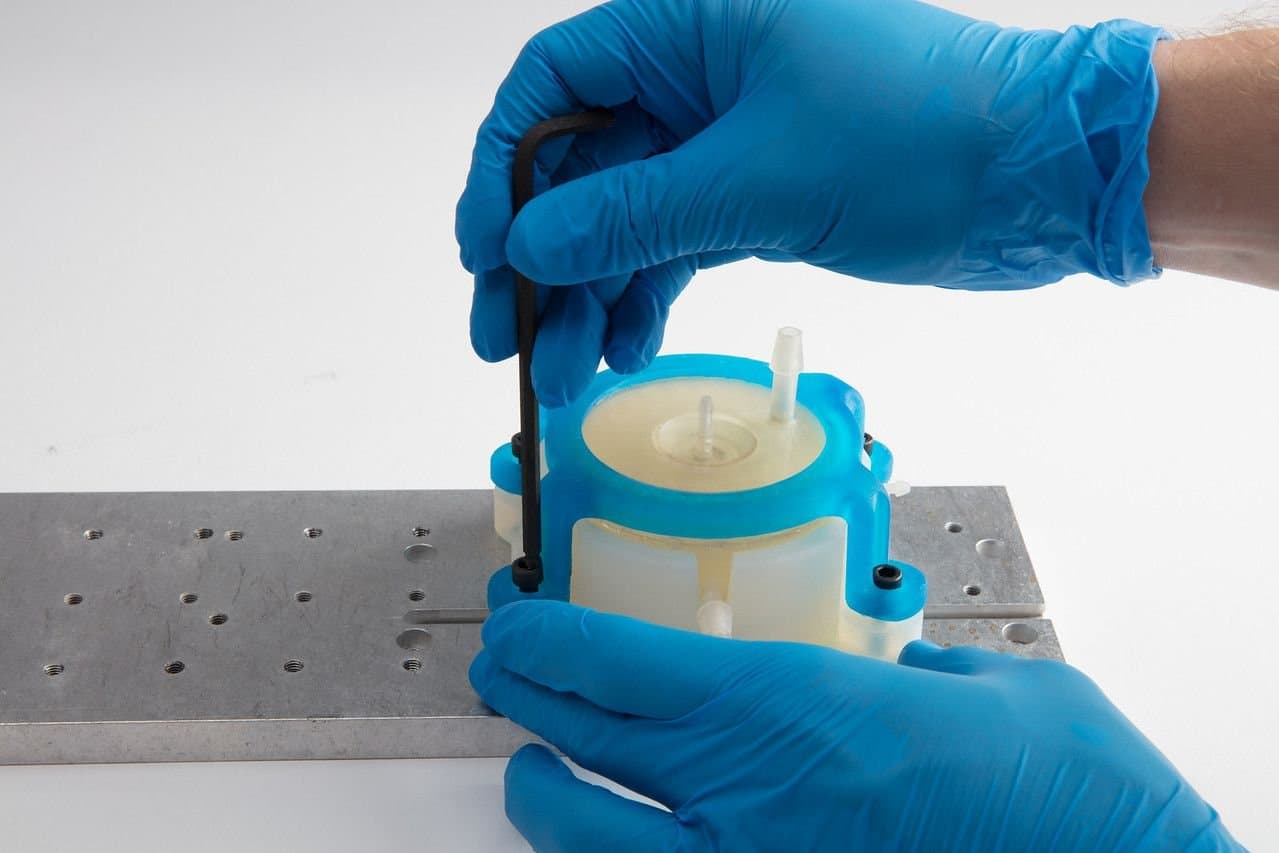
Progettazione di dime e attrezzi destinati alla stampa 3D
Scarica il nostro wihitepaper per scoprire come ridurre i costi, i tempi di sviluppo e creare un workflow di produzione più efficiente grazie alla stampa in 3D di dime e fissaggi.
Scarica il whitepaper
Libertà di progettazione e iterazioni rapide con la stampa 3D
"Grazie alla stampa 3D sono molto più libero di creare e progettare le parti. Data la flessibilità delle macchine, posso ideare praticamente qualsiasi forma e produrla. È molto efficace quando si tratta di forme complesse come quella che ho dovuto realizzare per risolvere questo problema" spiega Williams.
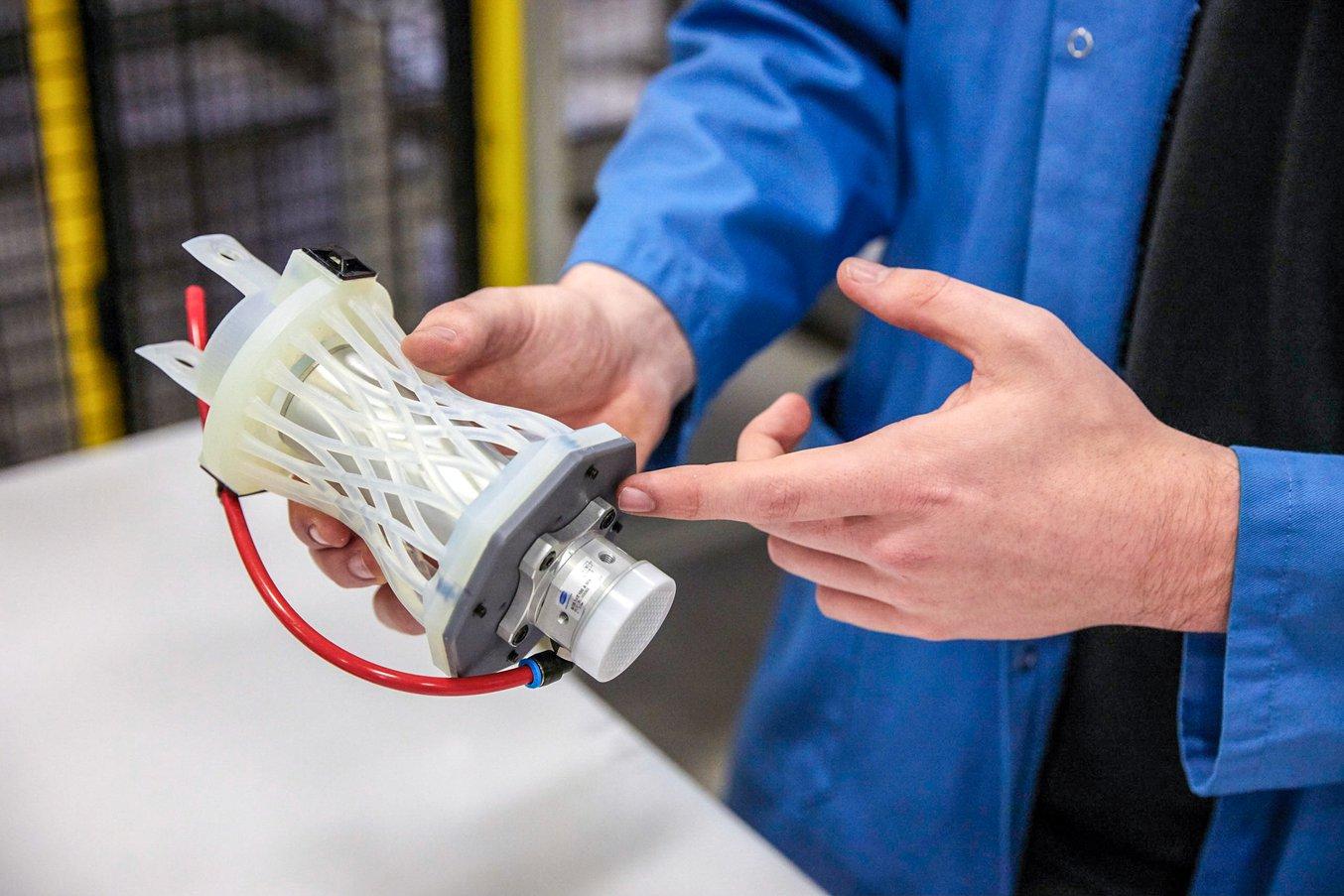
Il design è stato stampato in 3D con la Durable Resin di Formlabs, che Williams considera più adatta per questa applicazione, data la sua elasticità.
La stampa 3D ha permesso a Williams di essere più creativo e ha reso il processo di progettazione più flessibile, non essendo vincolato alle regole di progettazione associate ai metodi di produzione tradizionali.
"Quando progetti qualcosa da lavorare a macchina, devi pensare a molte altre cose; ad esempio, come fissarlo e come raggiungere un determinato punto con gli utensili. La parte è piuttosto complicata all'interno, quindi lo spazio che uno strumento dovrebbe avere per creare le tasche e le caratteristiche dall'interno probabilmente non sarebbe sufficiente. Dovrei semplificare il design o crearne uno nuovo complicato. Potrebbe non funzionare altrettanto bene, avere un costo maggiore e tempi di lavorazione più lunghi" spiega Williams.
Avendo a disposizione le stampanti 3D all'interno dell'azienda, Williams poteva anche eseguire rapidamente delle iterazioni e risparmiare mesi sui tempi di realizzazione per tutta la durata del progetto.
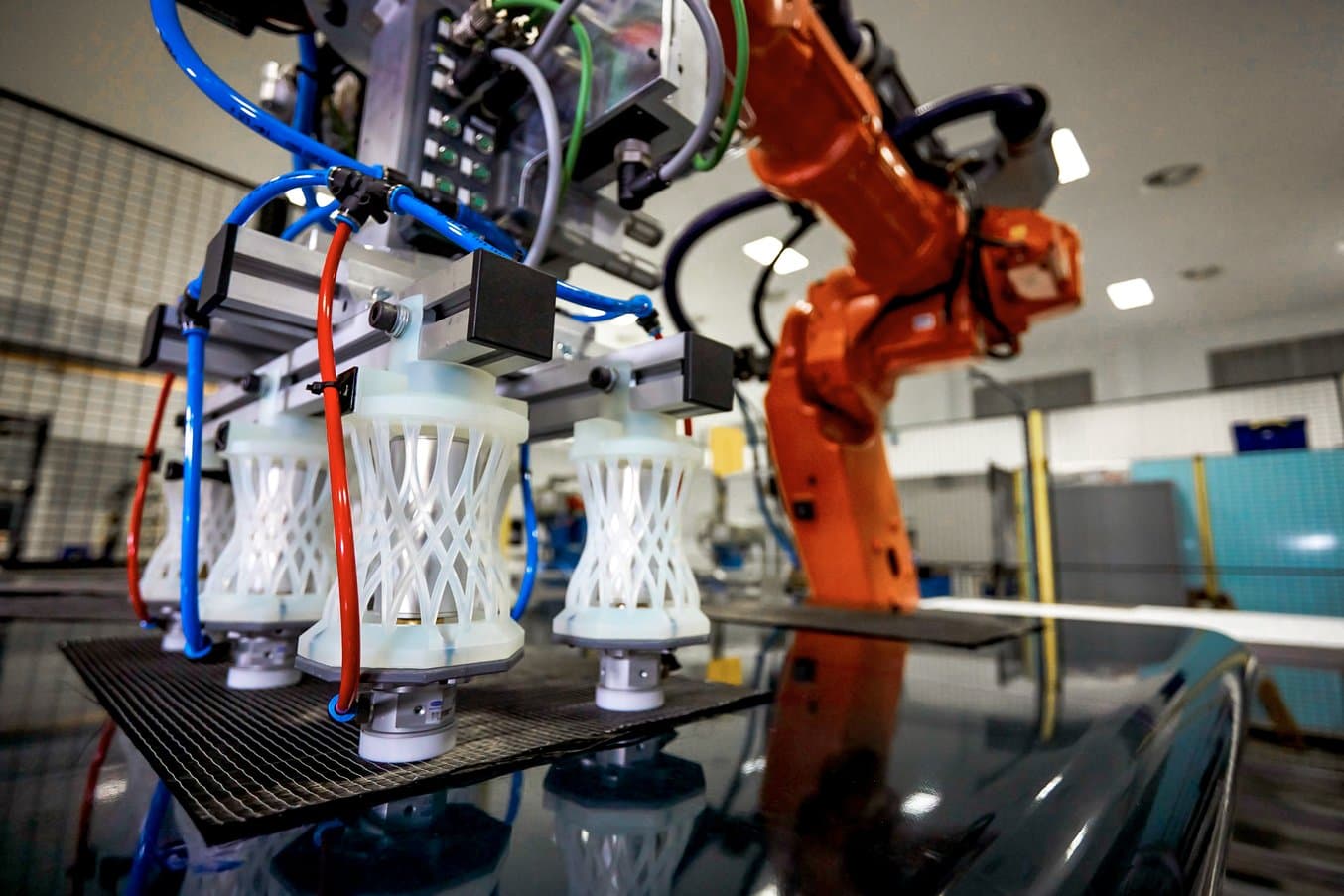
Il robot pick-and-place dispone di sei pinze ad aria compressa e ciascuna richiede una staffa. Sono state necessarie sei ore per stamparne una in 3D.
"Ho eseguito cinque iterazioni del set di sei pinze. Ci sarebbero volute circa 10-15 settimane per lavorarle a macchina. Senza nemmeno poter fare una prova" spiega Williams.
"Ci vogliono solo sei ore per stamparle in 3D. E se un'iterazione non funziona, posso semplicemente creare un nuovo design durante il giorno mentre lavoro. Quando la sera torno a casa, posso avviare la stampante, che avrà terminato entro la mattina dopo. In questo modo, potrò lavorare tutto il giorno con la nuova parte" spiega Williams.
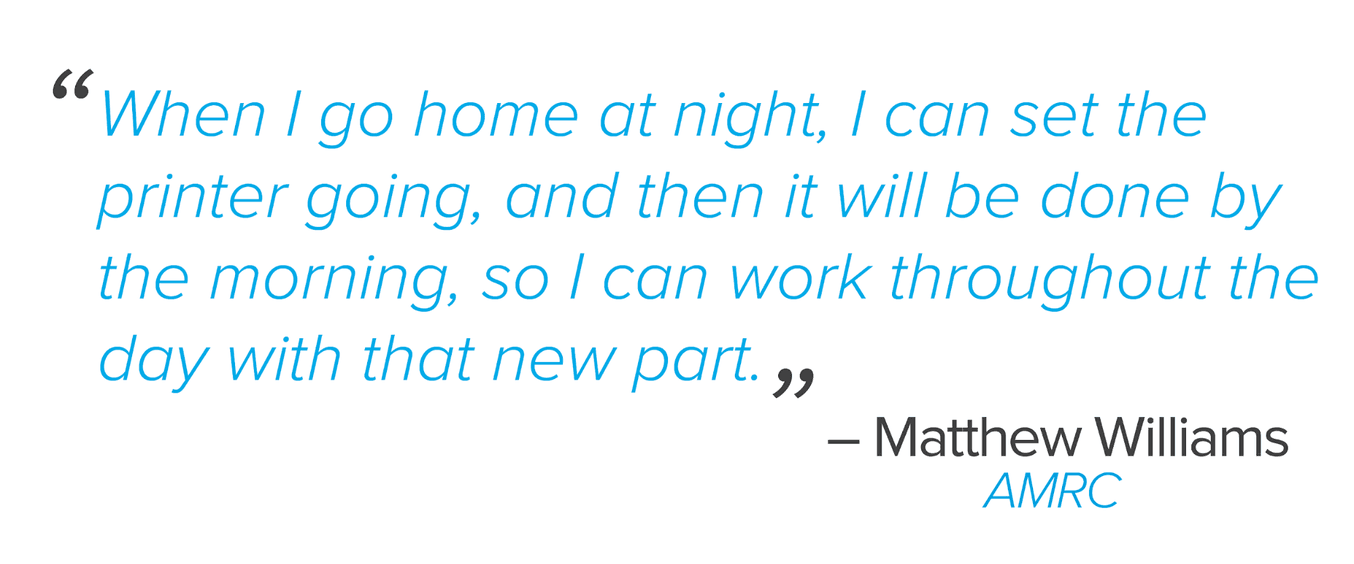
Scopri come una postazione di stampa 3D aiuta centinaia di ingegneri presso l'AMRC
Williams ha collaborato con il Design and Prototyping Group dell'AMRC per realizzare le parti stampate in 3D. Di recente, il gruppo ha installato una postazione di produzione additiva con una flotta di 12 stampanti 3D stereolitografiche (SLA) Form 2, a cui hanno accesso tutti gli ingegneri che lavorano nella struttura.
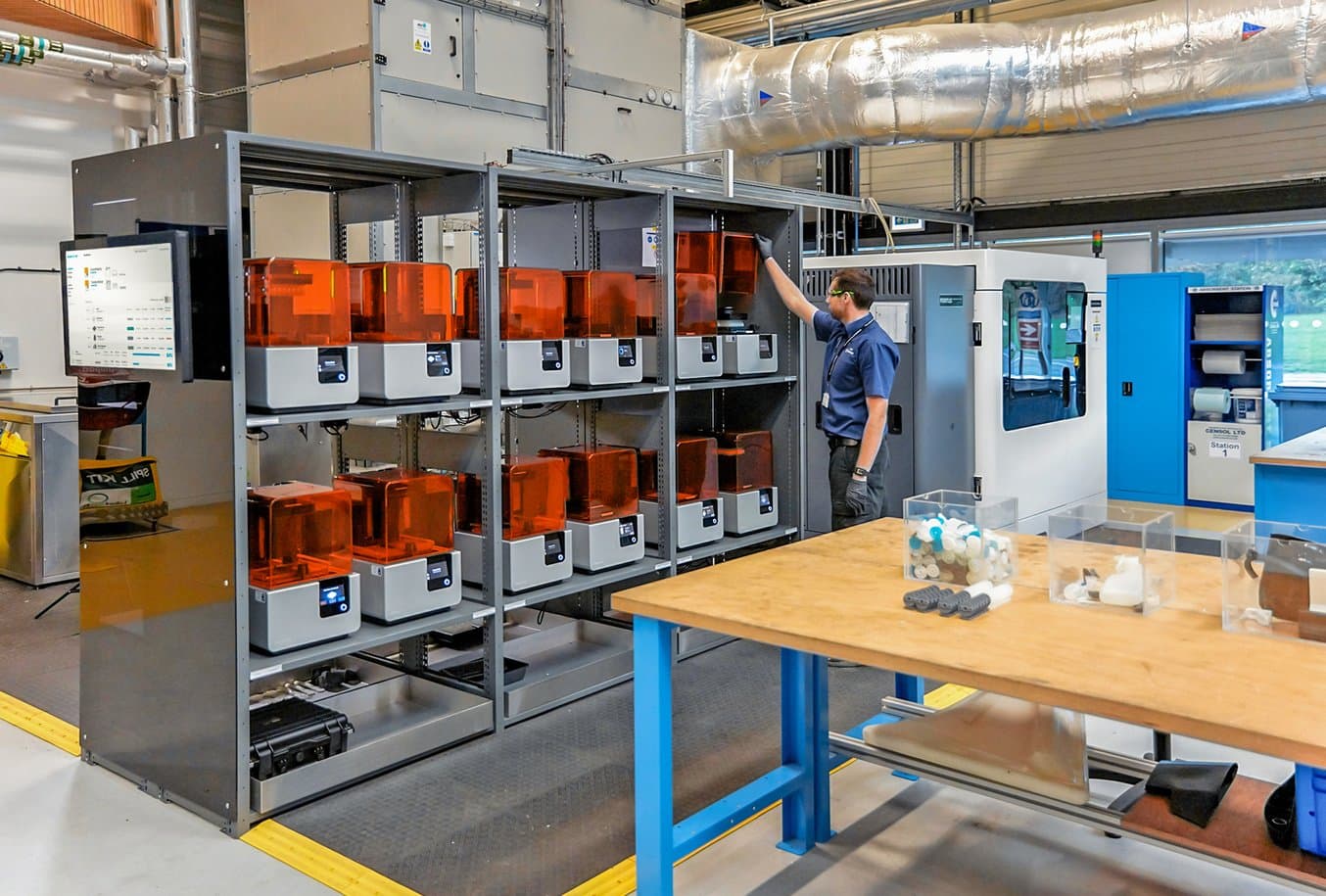
Williams ha stampato le parti utilizzando la nuova postazione di stampa 3D dell'AMRC, che ospita una flotta di 12 stampanti 3D stereolitografiche Form 2.
"È straordinario avere le stampanti nel centro. Mi permette di risparmiare un sacco di tempo, perché posso semplicemente avviare le stampe, attraversare la strada quando sono terminate, rimuovere le parti dalla stampante, portarle qui e utilizzarle subito. È molto più veloce rispetto a dover parlare con qualcuno in un'azienda esterna per farle produrre e spedire qui" spiega Williams.
Scopri di più sulla postazione di stampa 3D presso l'AMRC e su altre applicazioni, ad esempio la stampa 3D in serie di 500 tappi di protezione ad alta precisione per i test di foratura di AirBus, una staffa del sensore resistente alle alte temperature per la saldatura e rulli di avvolgimento dei filamenti personalizzati per la produzione di materiali compositi.
Vuoi saperne di più sulle stampanti e la tecnologia su cui è basata la postazione di stampa 3D dell'AMRC? Scopri le ultime stampanti 3D SLA di Formlabs, la Form 3 e il formato più grande Form 3L, e la raccolta di resine ingegneristiche di Formlabs, oppure richiedi un campione gratuito per toccare con mano la qualità della stampa 3D.