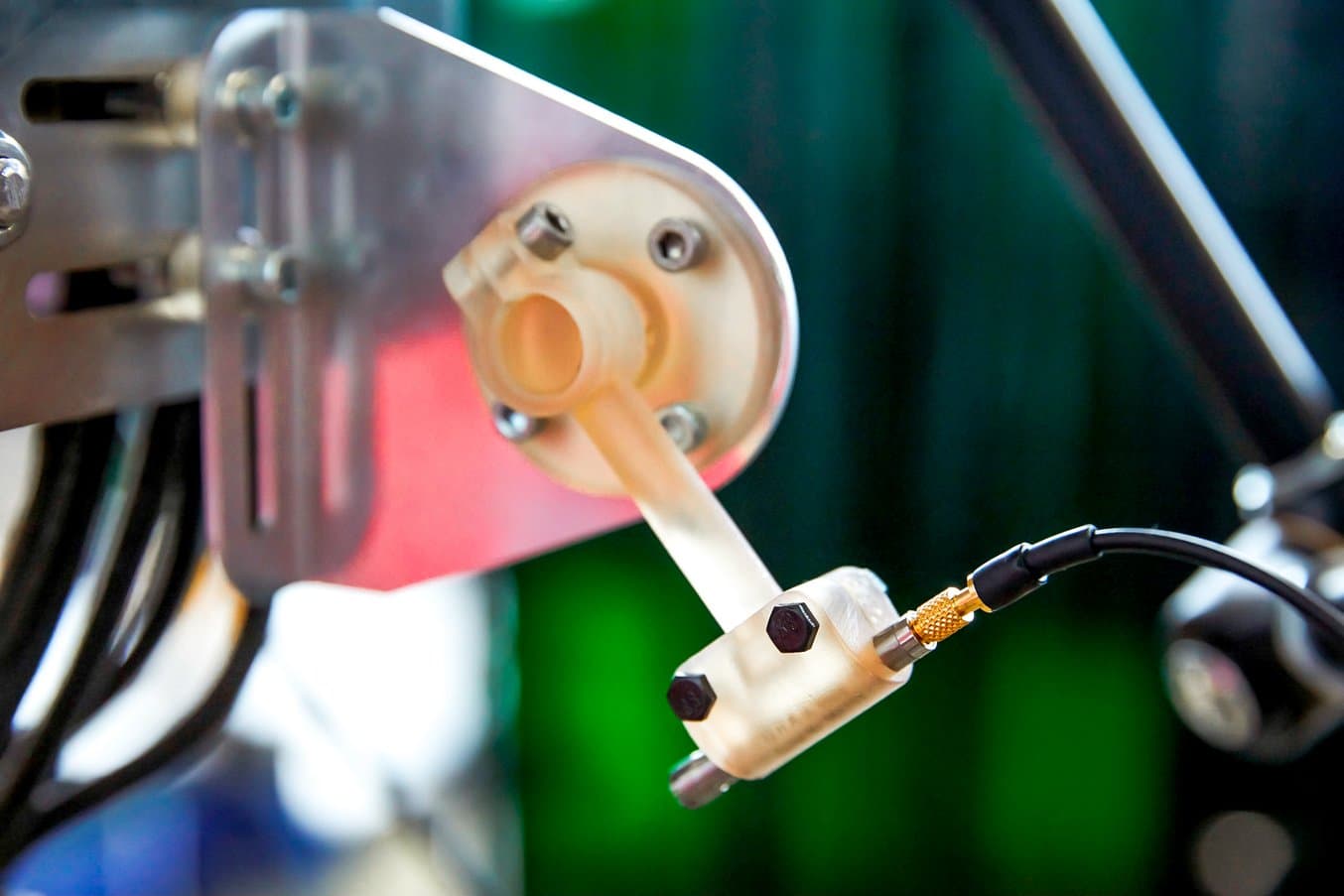
Il Nuclear Advanced Manufacturing Research Centre (Nuclear AMRC) è una collaborazione di partner accademici e industriali provenienti da qualsiasi punto della catena di approvvigionamento nucleare, che conduce ricerche mirate a trovare soluzioni di produzione avanzate per il settore nucleare civile e aiutare i fabbricanti del Regno Unito ad aggiudicarsi il lavoro in patria e nel mondo.
Un progetto su cui il centro ha lavorato di recente punta a sviluppare una soluzione autonoma per la saldatura di recipienti a pressione nel settore nucleare. Per raggiungere questo obiettivo, il team ha dovuto integrare nell'attrezzatura sensori multipli, in un ambiente pericoloso e ad alte temperature.
Matthew Smart, responsabile tecnico dei progetti del gruppo di lavorazione meccanica presso il Nuclear AMRC ci racconta come i ricercatori hanno utilizzato la stampa 3D per eseguire iterazioni rapide di diversi design e produrre decine di parti che hanno resistito alle alte temperature in prossimità del punto di saldatura.
Smart e il team di ricerca hanno lavorato con la postazione di produzione additiva a libero accesso dell'AMRC per creare le parti di cui avevano bisogno. Leggi il nostro caso di studio per scoprire come il libero accesso alla stampa 3D può aiutare centinaia di ingegneri all'interno della struttura.
Perché la saldatura dei recipienti può richiedere mesi nel settore nucleare
Gli attuali metodi di saldatura dei recipienti a pressione richiedono l'esecuzione di frequenti punti di tenuta per l'ispezione manuale, che richiede il raffreddamento e il riscaldamento ripetuto dei componenti. Per questo il processo è molto lungo: la saldatura di un grande recipiente può richiedere mesi. Il progetto del Nuclear AMRC mira a ridurre questo tempo di realizzazione tramite lo sviluppo di un sistema autonomo in grado di rilevare i difetti nel momento in cui si verificano, per cui il processo viene interrotto solo in presenza di un errore reale.
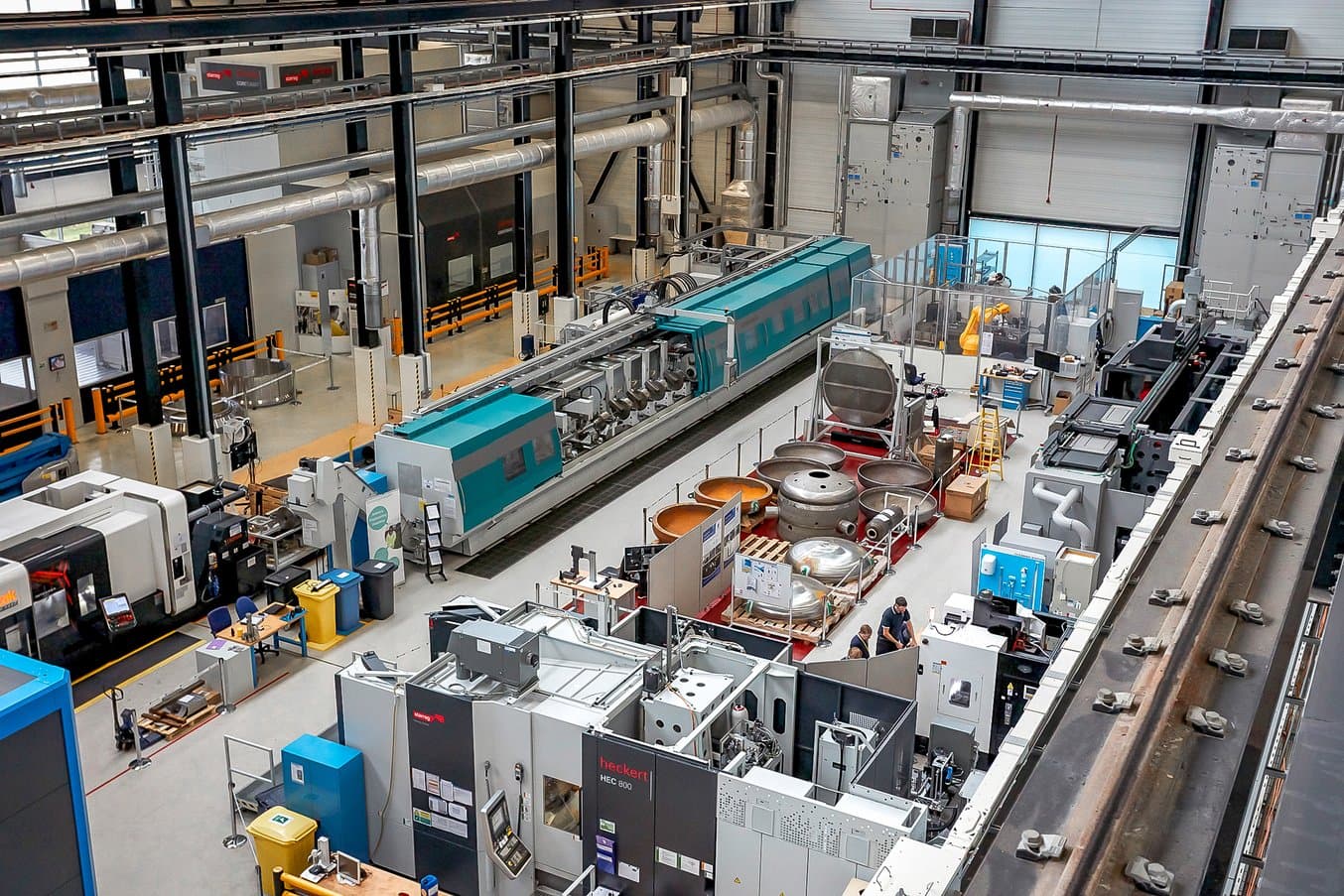
Per analizzare il processo di saldatura in tempo reale, il concetto dei ricercatori integra una serie di sensori diversi, come scanner laser, monitoraggio acustico, monitoraggio di tensione e corrente del processo, immagini termiche e un sistema di telecamere.
"L'integrazione meccanica di tutti questi sensori è una sfida in un ambiente pericoloso come questo. Dobbiamo testare diverse configurazioni e orientamenti per scoprire dove posizionare i sensori. Ma dobbiamo svolgere i test e utilizzare l'attrezzatura in maniera flessibile, perché è molto costoso prenotare il tempo per lavorare su questa macchina" spiega Smart.
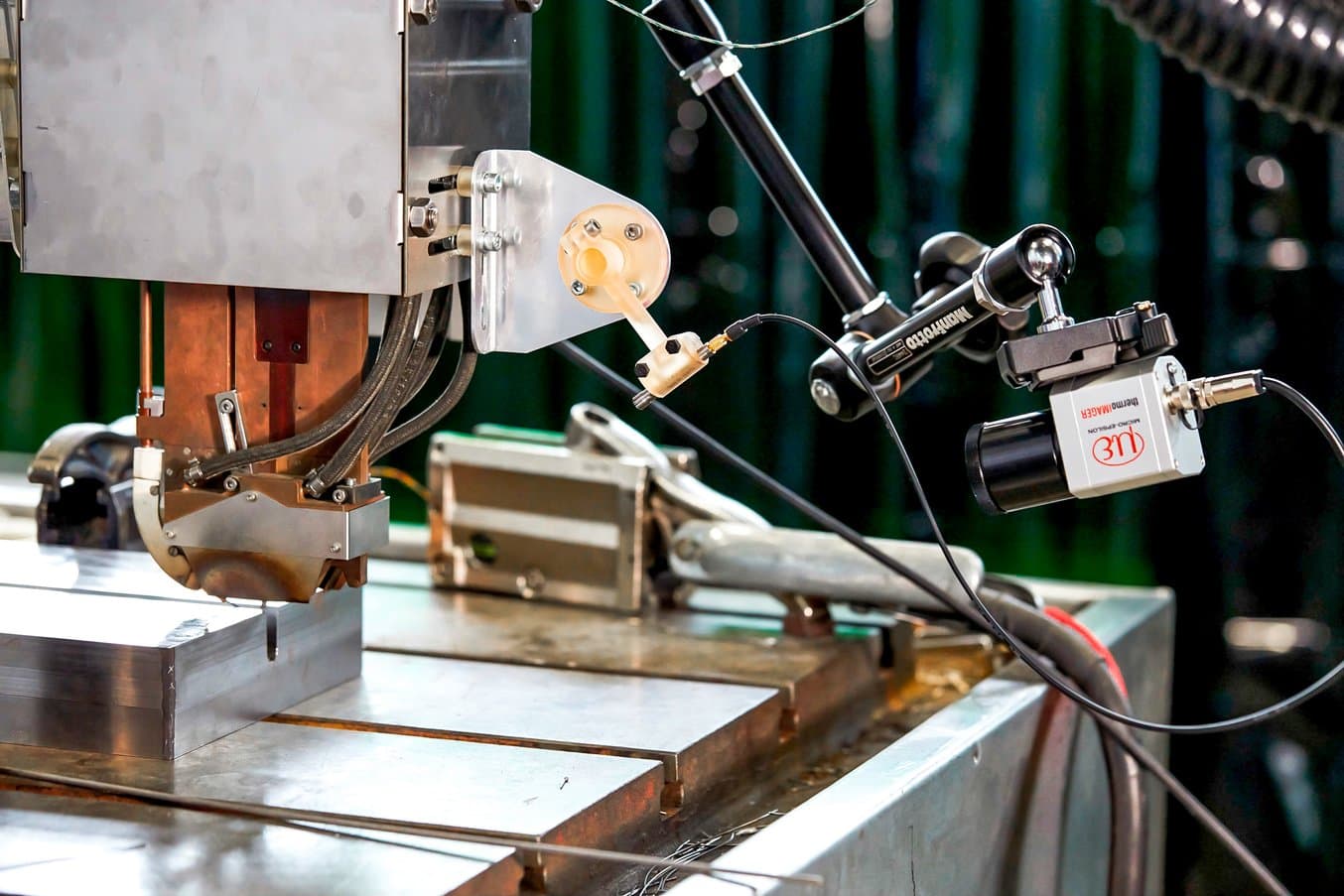
Iterazione rapida delle configurazioni dei sensori e della strategia di montaggio grazie alla stampa 3D
L'attuale configurazione dei sensori contiene circa una dozzina di diverse parti stampate in 3D, principalmente rondelle che tengono insieme le staffe e un sistema di montaggio per i microfoni acustici. Tutte queste parti devono resistere alle alte temperature in prossimità del punto di saldatura.
La High Temp Resin di Formlabs offre una temperatura di distorsione termica (ingl. "heat deflection temperature", HDT) di 238 °C a 0,45 MPa ed è perciò ideale per parti che devono resistere alle alte temperature.
"Se avessimo dovuto realizzare queste parti con un metodo tradizionale, avremmo dovuto essere molto più precisi nell'inserire le tolleranze esatte durante il processo di progettazione prima di fabbricarle. La stampa in 3D delle staffe ci consente di andare a tentativi, stampare più versioni con tolleranze diverse e provare diversi orientamenti e dimensioni. Quindi possiamo essere molto più innovativi e testare tutto più velocemente" spiega Smart.
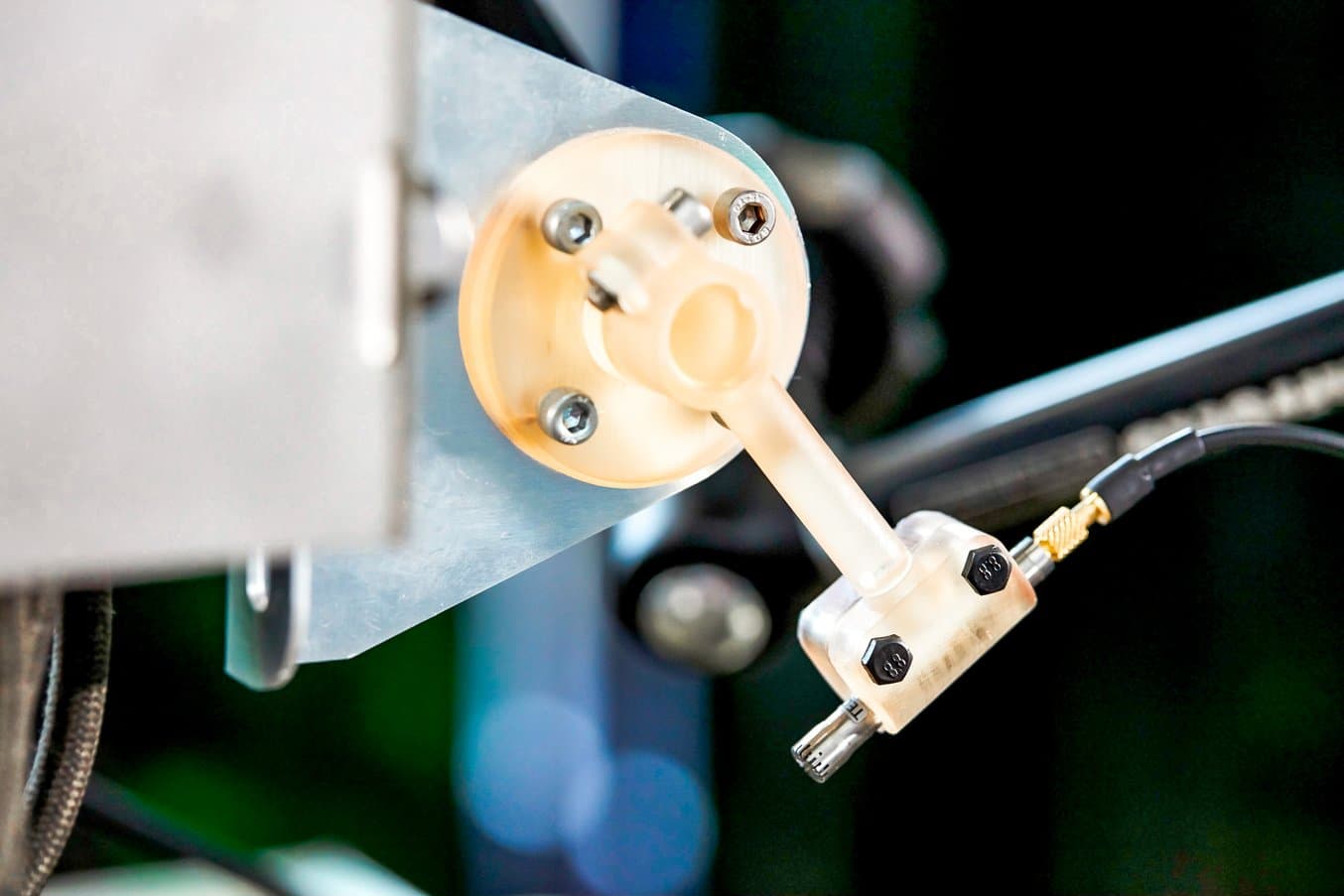
La possibilità di utilizzare la stampa 3D per testare rapidamente le diverse configurazioni dei sensori e la strategia di montaggio ha permesso al team di essere molto versatile e di ridurre significativamente i costi e i tempi di produzione delle parti.
"Sarebbero necessari diversi giorni di ingegneria per ottenere tutti i documenti, mettere in ordine il materiale, fare il lavoro di progettazione e subappaltare la produzione a un'azienda esterna. Mentre con la stampa 3D servono un paio d'ore su un programma CAD e il costo della plastica. È una frazione di quanto richiesto dai metodi tradizionali" spiega Smart.
"Non è facile quantificare l'agilità che la stampa 3D offre, perché ti permette di eseguire molti più test e iterazioni. Diciamo che se si inviava un progetto per la fabbricazione e si rivelava non adatto allo scopo, bisognava ripetere il processo, quindi erano necessarie diverse settimane per passare da un prototipo di prova all'altro. Con la stampa 3D bastano due giorni. Il ritmo dell'innovazione non è quantificabile."
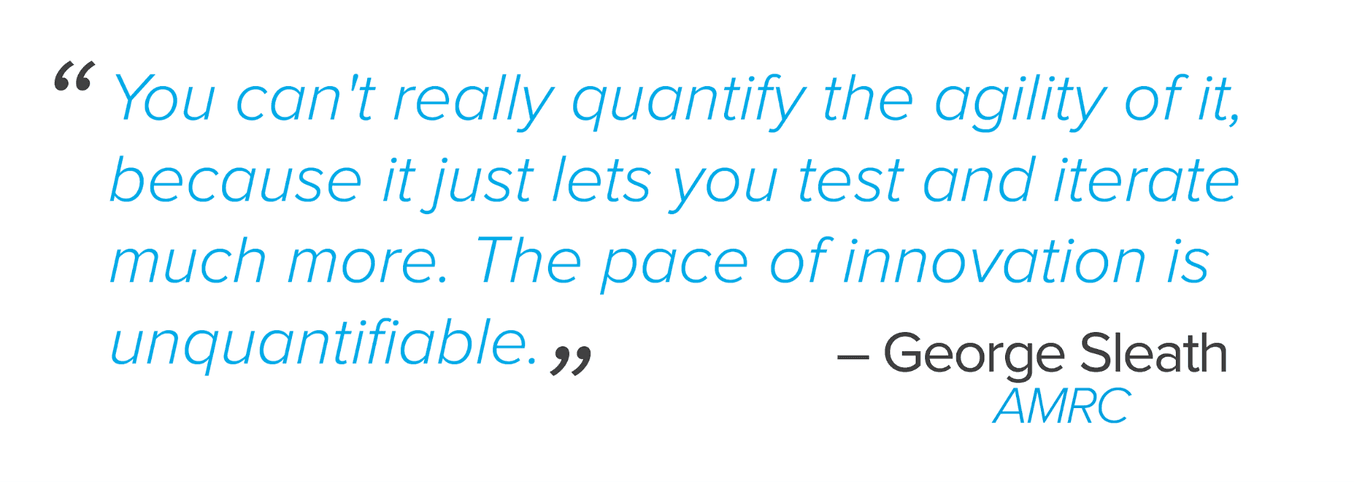
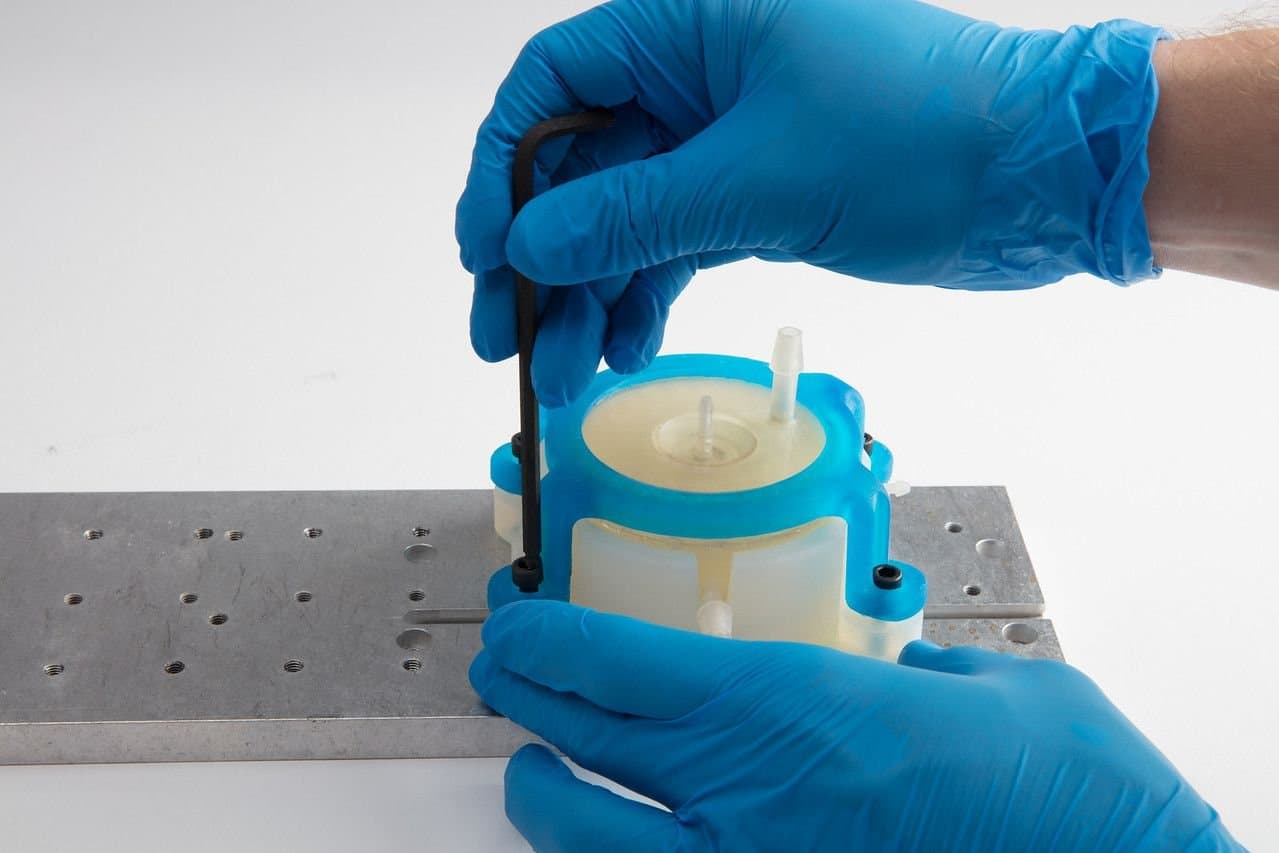
Progettazione di dime e attrezzi destinati alla stampa 3D
Scarica il nostro whitepaper per scoprire come ridurre i costi, i tempi di sviluppo e creare un workflow di produzione più efficiente grazie alla stampa in 3D di dime e fissaggi.
Scarica il whitepaper
Usare una postazione interna di stampa 3D per ridurre i tempi di realizzazione
Smart ha collaborato con il Design and Prototyping Group dell'AMRC per realizzare le parti stampate in 3D. Di recente, il gruppo ha installato una postazione di produzione additiva con una flotta di 12 stampanti 3D stereolitografiche (SLA) Form 2, a cui hanno accesso tutti gli ingegneri che lavorano nella struttura.
"Lavoriamo a stretto contatto con il Design and Prototyping Group. Sono stati molto disponibili nel coinvolgerci e mostrarci che cosa è possibile realizzare, quali attrezzature sono disponibili e come ottimizzare il design per ottenere una stampa in 3D facile e veloce. È fondamentale avere accesso e sapere quali sono le capacità della postazione per poterla utilizzare all'interno del gruppo di ricerca" spiega Smart.
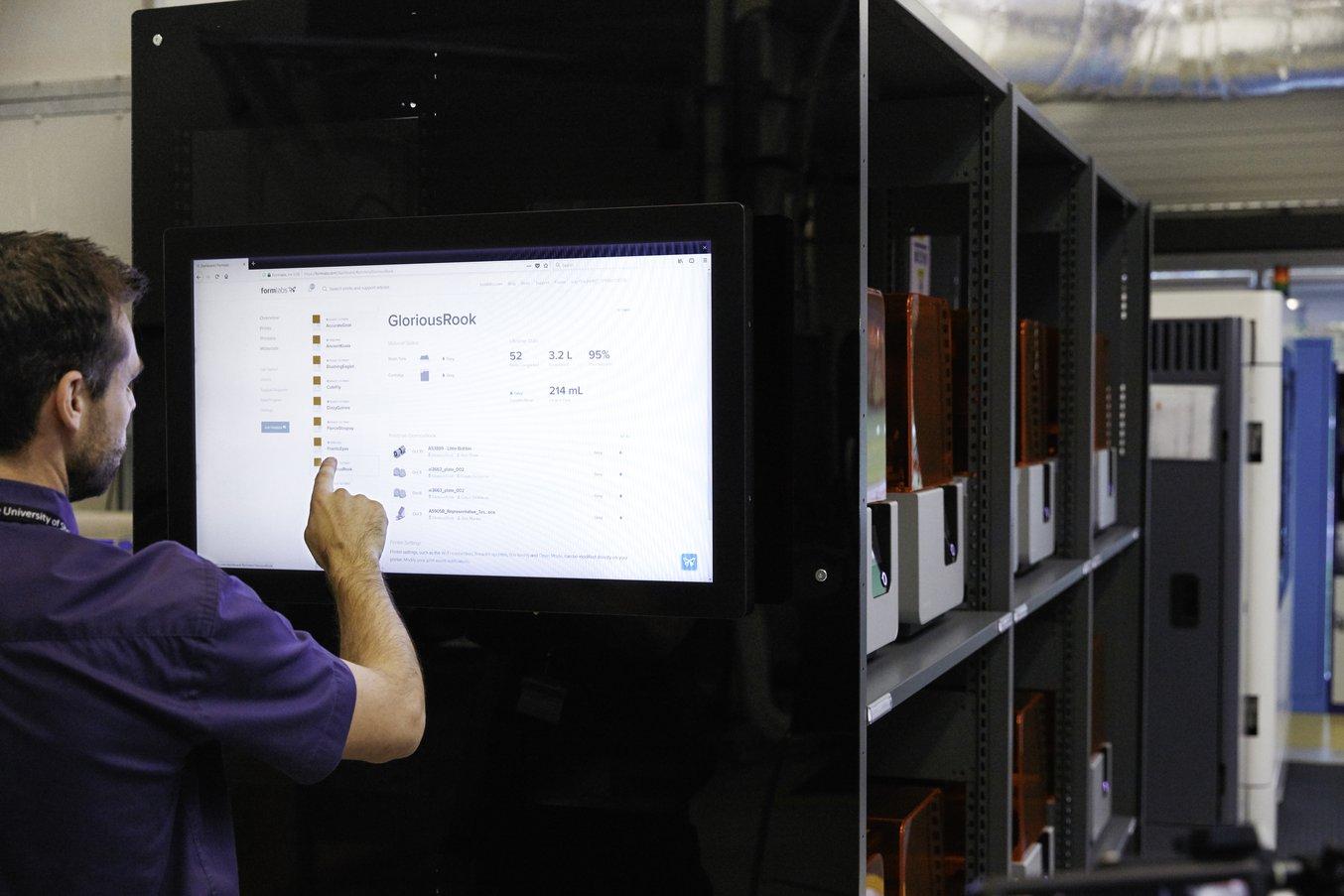
"Se non ci fosse stata [una postazione di stampa 3D], sarei stato a conoscenza della tecnologia, ma non avrei saputo nulla delle sue capacità e di come progettare qualcosa per produrlo. In realtà sono stato addestrato su alcune delle macchine, e avervi libero accesso per potervi inviare componenti da realizzare è incredibilmente utile" spiega Smart.
Scopri come una postazione di stampa 3D aiuta centinaia di ingegneri presso l'AMRC
Scopri di più sulla postazione di stampa 3D presso l'AMRC e su altre applicazioni, ad esempio la stampa in 3D in serie di 500 tappi di protezione ad alta precisione per i test di foratura di AirBus, staffe molto complesse per una pinza robotica utilizzata nella produzione di materiali compositi e rulli di avvolgimento dei filamenti personalizzati per la produzione di materiali compositi.
Vuoi saperne di più sulle stampanti e la tecnologia su cui è basata la postazione di stampa 3D dell'AMRC? Scopri le ultime stampanti 3D SLA di Formlabs, la Form 3 e il formato più grande Form 3L, e la raccolta di resine ingegneristiche di Formlabs, oppure richiedi un campione gratuito per toccare con mano la qualità della stampa 3D.