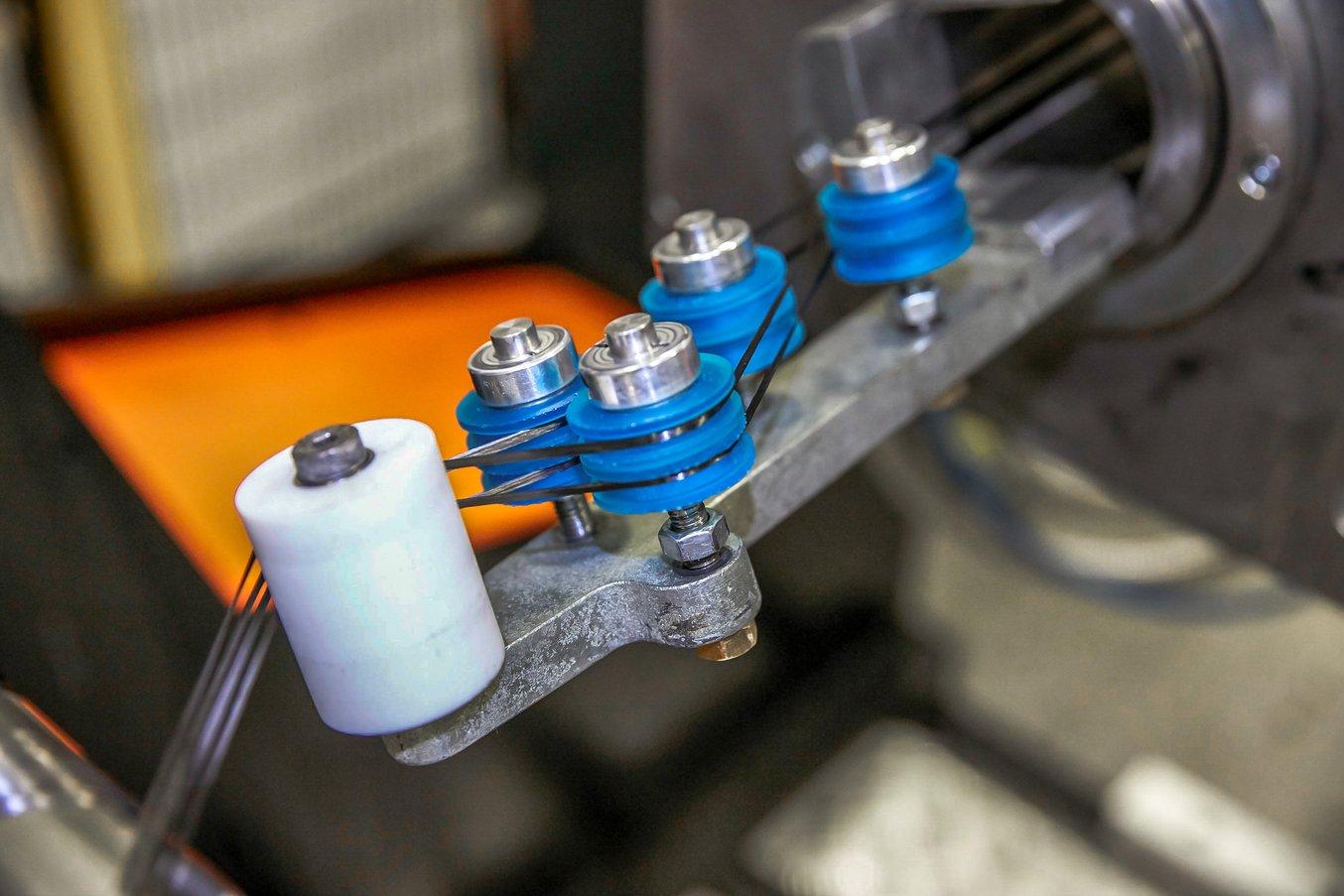
I materiali compositi come le fibre di vetro e la fibra di carbonio traggono la loro elevata resistenza e leggerezza dal modo in cui i filamenti di fibra sono tessuti e disposti all'interno delle parti, perciò offrono opportunità uniche per ottimizzare i progetti in base alle sollecitazioni a cui si pensa di sottoporre i componenti. Lavorare con questi materiali realizzati su misura, però, presenta anche una serie di sfide a livello di produzione.
Il centro di ricerca sui materiali compositi dell'Advanced Manufacturing Research Centre (AMRC) dell'Università di Sheffield conduce ricerche utilizzando metodi all'avanguardia nel tentativo di risolvere queste sfide per industrie di grande valore come il settore aerospaziale, marino o automobilistico.
Uno dei loro progetti di ricerca esplora l'avvolgimento di filamenti, che di solito viene utilizzato per la realizzazione di tubi, vasi e alberi per l'industria aerospaziale e automobilistica. Siccome lavorano con materiali di diametri diversi, i ricercatori dovevano poter adattare il sistema per elaborare le fibre con l'alto livello di precisione richiesto nell'industria aerospaziale.
Continua a leggere per scoprire da Alexander Shaw, un tecnico dell'automazione dei compositi che lavora al progetto, come i ricercatori hanno sviluppato e stampato in 3D diverse versioni di rulli personalizzati, lavorando con la postazione di produzione additiva a libero accesso dell'AMRC per realizzare le parti in pochi giorni.
Guarda il video racconto per scoprire come i ricercatori del centro di ricerca sui materiali compositi hanno utilizzato i rulli personalizzati per l'avvolgimento dei filamenti.
Shaw e il team di ricerca hanno lavorato con la postazione di produzione additiva a libero accesso dell'AMRC per creare le parti di cui avevano bisogno. Leggi il nostro caso di studio per scoprire come il libero accesso alla stampa 3D può aiutare centinaia di ingegneri all'interno della struttura.
Le sfide uniche del lavoro con i materiali compositi
Un avvolgitore di filamenti funziona così: una bobina di fibre passa in un bagno di resina e poi attraverso dei rulli sottili, per andare dalla cantra sul retro del sistema fino alla testina fissata su un robot KUKA a 6 assi. I filamenti di fibre raggiungono poi un mandrino metallico, che viene fatto girare come un tornio. A mano a mano che la testina del robot si muove, la fibra viene depositata sopra il mandrino di filatura.
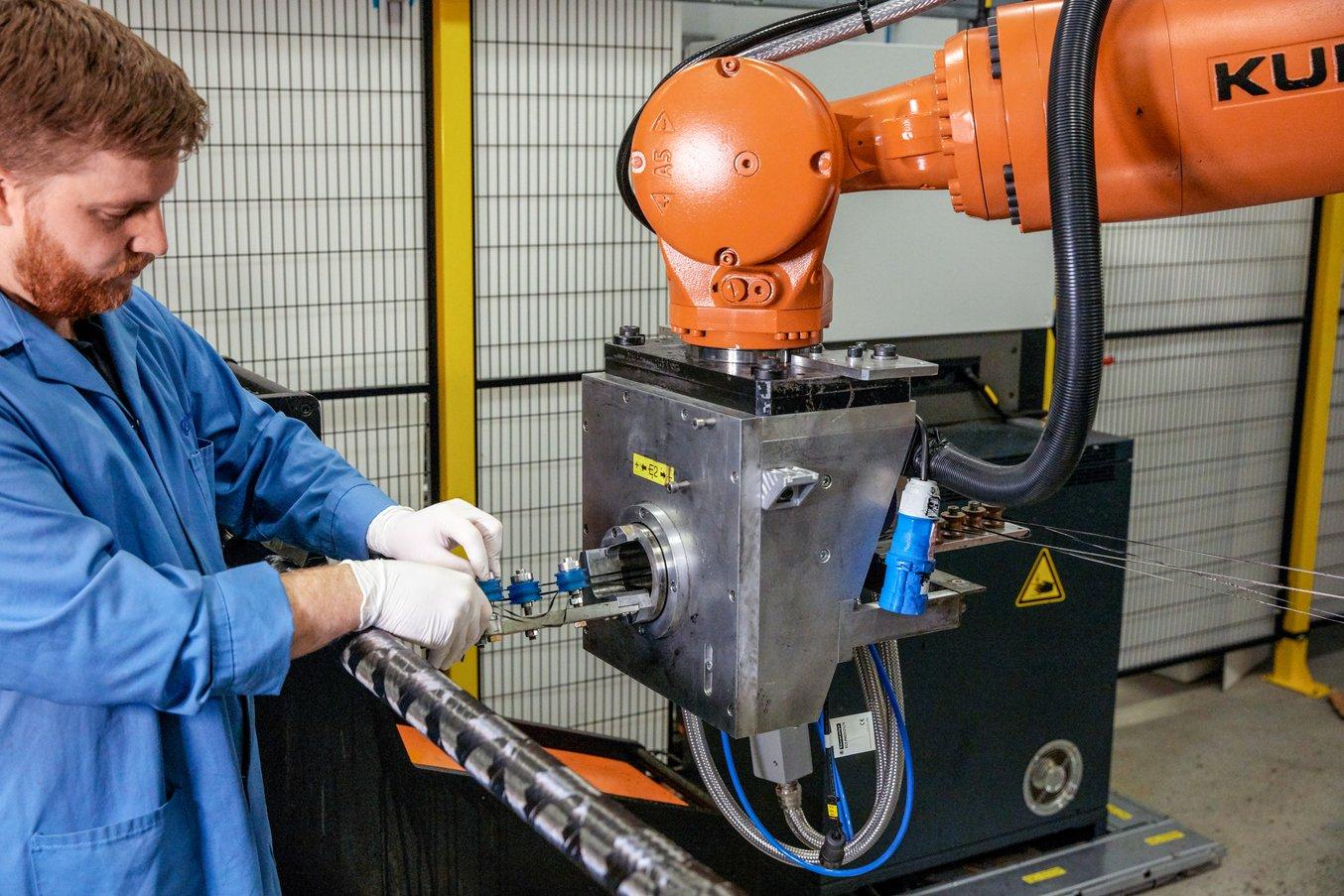
Fibre diverse possono avere diametri di materiale differenti o essere leggermente irregolari, e questo può causare problemi con il passaggio della fibra attraverso i rulli. Quando il ricercatore cambiava materiale e ne usava uno leggermente più stretto di quello precedente, la variazione di diametro richiedeva la produzione di un rullo un po' più piccolo del pezzo originariamente fornito con la macchina.
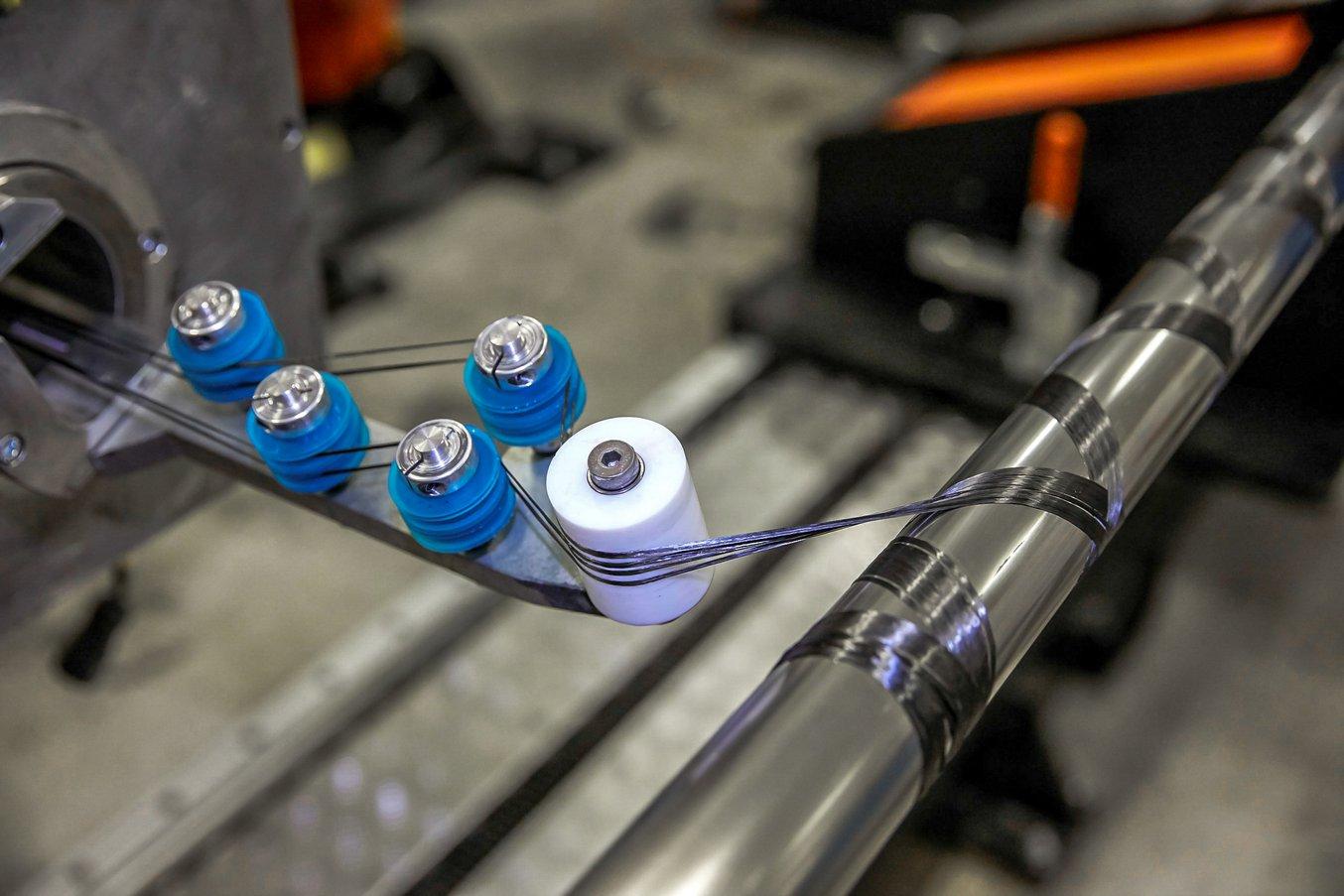
"Se il materiale è più stretto della scanalatura dei rulli, appaiono degli spazi tra i fili. Se questi spazi sono più grandi di un millimetro, la parte non soddisfa i requisiti del settore aerospaziale" spiega Shaw.
Produrre le parti con strumenti additivi o sottrattivi?
Per adattare il sistema ai nuovi materiali, Shaw ha esaminato i rulli standard e ha progettato tre nuove versioni, tutte con diametri e larghezze diverse a seconda del materiale utilizzato. Ad esempio, per un materiale largo un centimetro, stampavano rulli con una sezione centrale di tale larghezza e sezioni esterne di mezzo centimetro, in modo che non si creasse uno spazio tra cantra superiore e inferiore quando i due filamenti venivano posti uno accanto all'altro.
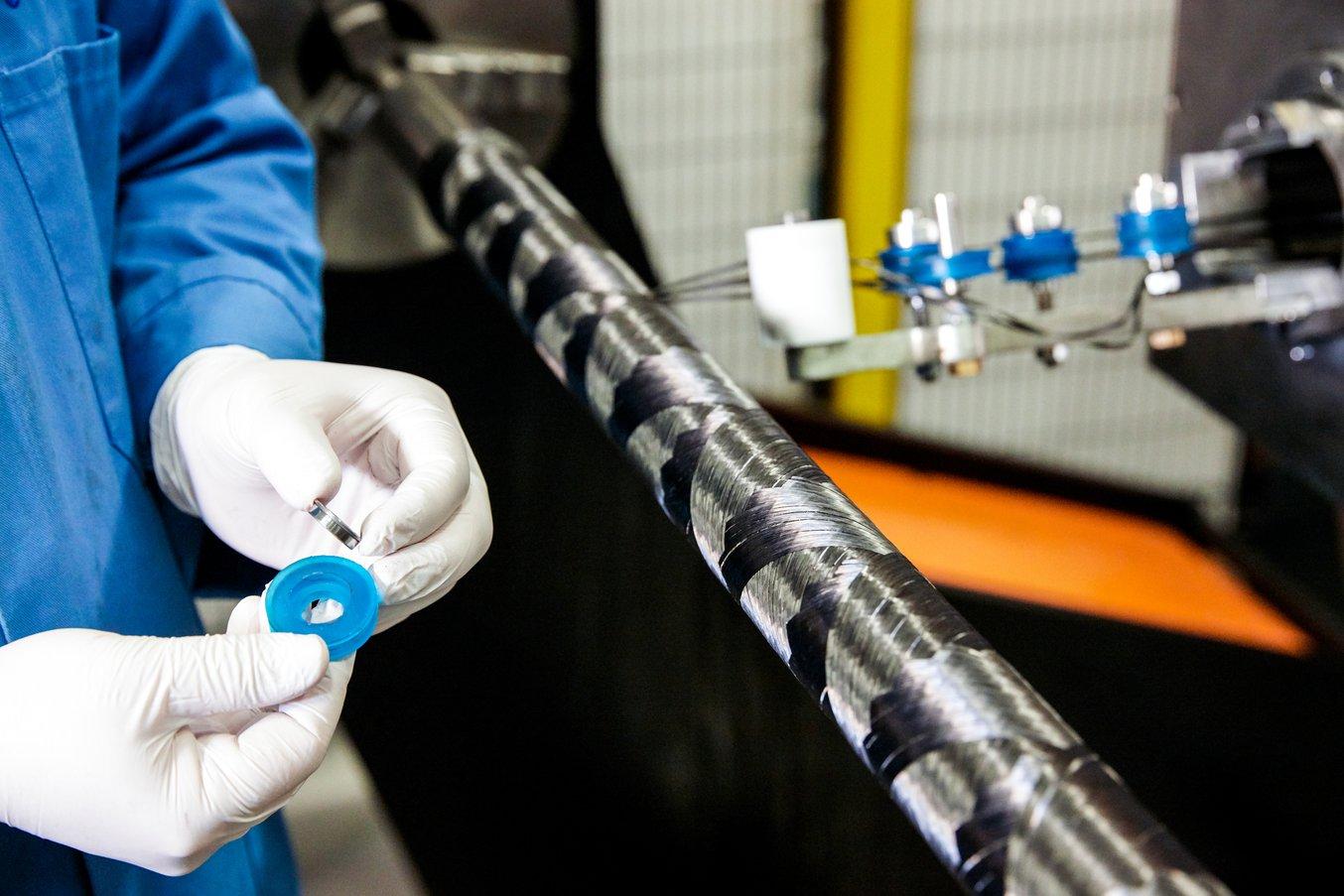
Per poter proseguire con il progetto, il team aveva bisogno dei nuovi rulli il prima possibile, quindi la stampa 3D si rivelò la migliore opzione di produzione delle parti.
"La lavorazione meccanica dei nuovi rulli aumenterebbe i costi di molto, e la realizzazione potrebbe richiedere più di una settimana, mentre, con le stampanti 3D di Formlabs, siamo in grado di stampare le parti e averle a disposizione il giorno stesso" spiega Shaw.
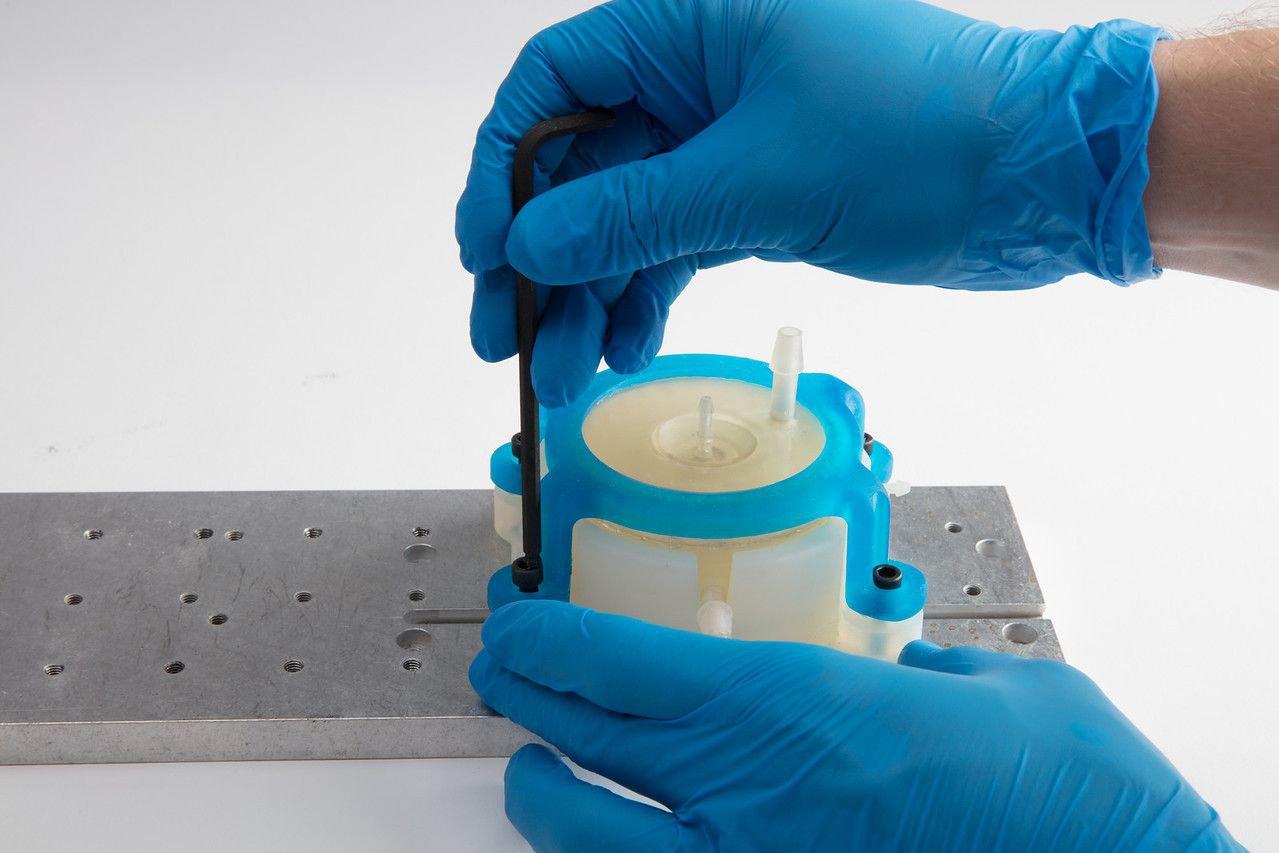
Progettazione di dime e attrezzi destinati alla stampa 3D
Scarica il nostro whitepaper per scoprire come ridurre i costi, i tempi di sviluppo e creare un workflow di produzione più efficiente grazie alla stampa in 3D di dime e fissaggi.
Scarica il whitepaperUso della postazione di stampa 3D in house
"Avevamo già considerato in precedenza la stampa 3D. Soprattutto perché è davvero accessibile a tutti. Prima c'erano solo tre o quattro persone che sapevano usare le macchine. Ci è voluto un po' di più per imparare a utilizzare il software e tutto il resto" spiega Shaw.
Shaw ha collaborato con il Design and Prototyping Group dell'AMRC per realizzare le parti stampate in 3D. Di recente, il gruppo ha installato una postazione di produzione additiva con una flotta di 12 stampanti 3D stereolitografiche (SLA) Form 2, a cui hanno accesso tutti gli ingegneri che lavorano nella struttura.
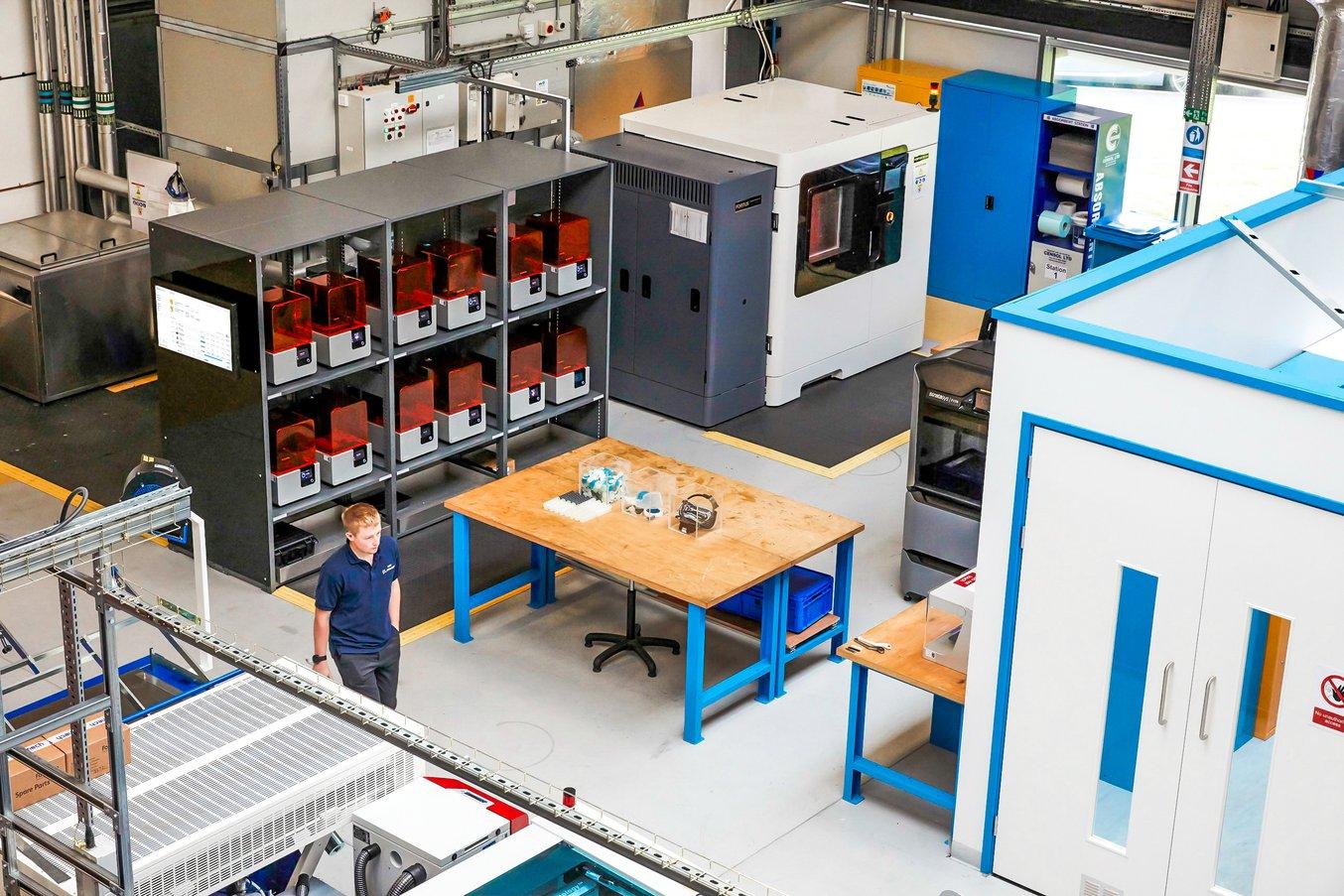
Dopo aver ricevuto le nuove stampanti, Mark Cocking, il responsabile tecnico dell'additivo polimerico, ha chiesto a tutti i membri del centro di ricerca sui materiali compositi se fossero interessati a prendere parte alla formazione.
"Credo che il 90% del personale del centro di ricerca sui materiali compositi abbia pensato che si trattava sicuramente di qualcosa di utile. Ci sono voluti circa 20-30 minuti per mostrarci il software e spiegare tutti i passaggi. Il software è davvero facile da usare: basta creare un file STL, trascinarlo nel software e il resto è tutto automatico. Ora ci sono quasi una dozzina di persone nel nostro gruppo che sanno usare le stampanti Formlabs" spiega Shaw.
Scopri come una postazione di stampa 3D aiuta centinaia di ingegneri presso l'AMRC
Scopri di più sulla postazione di stampa 3D presso l'AMRC e su altre applicazioni, ad esempio la stampa 3D in serie di 500 tappi di protezione ad alta precisione per i test di foratura di AirBus, una staffa del sensore resistente alle alte temperatura per la saldatura e staffe molto complesse per una pinza robotica utilizzata nella produzione di materiali compositi.
Vuoi saperne di più sulle stampanti e la tecnologia su cui è basata la postazione di stampa 3D dell'AMRC? Scopri le ultime stampanti 3D SLA di Formlabs, la Form 3 e il formato più grande Form 3L, e la raccolta di resine ingegneristiche di Formlabs , oppure richiedi un campione gratuito per toccare con mano la qualità della stampa 3D.