Unilever, una delle più grandi aziende di beni di largo consumo del mondo, sviluppa costantemente nuovi prodotti per l'uso quotidiano, dalla cura della persona a quella della casa, all'alimentazione e molto altro ancora. È molto probabile che in questo momento tu abbia in casa uno o più dei prodotti di Unilever, dato che l'azienda possiede Dove, Domestos, Cif, Knorr, Axe (Lynx), Ben & Jerry's e decine di altri marchi internazionali e locali.
Quello dei beni di largo consumo è un settore in cui la richiesta costante si traduce in una concorrenza agguerrita, per cui i marchi devono innovare e adattare continuamente la propria strategia di prodotto. Un'importante area di innovazione è quella degli imballaggi: il design di un flacone può talvolta influenzare la percezione della clientela tanto quanto il suo contenuto. I marchi come Unilever devono tenere conto di fattori come il consumo di materiali, l'aspetto estetico, la sicurezza e la sostenibilità di un ampio catalogo di tipi di imballaggi e dei prodotti contenuti al loro interno. Se parliamo di un "semplice" flacone in plastica, il passaggio dal design sullo schermo del computer al riempimento nella linea di produzione richiede solitamente molti mesi.
"Un'azienda di beni di consumo come Unilever deve essere sul mercato il prima possibile o prima della concorrenza, nonché offrire il miglior prodotto con il miglior prezzo in tempi estremamente rapidi. Le stampanti 3D di Formlabs ci aiutano a velocizzare questo processo."
Stefano Cademartiri, responsabile del reparto CAD e prototipazione di Unilever
Scopri come Stefano Cademartiri, responsabile del reparto CAD e prototipazione presso il dipartimento di ricerca e sviluppo di Casalpusterlengo di Unilever, e Flavio Migliarelli, responsabile di design presso il dipartimento di ricerca e sviluppo di Serioplast Global Services, hanno lavorato fianco a fianco per testare l'idoneità degli stampi realizzati in 3D per lo stampaggio per stiramento e soffiaggio di volumi ridotti per accelerare la prototipazione e i test pilota, riducendo i tempi di produzione di sei settimane e i costi del 90%.
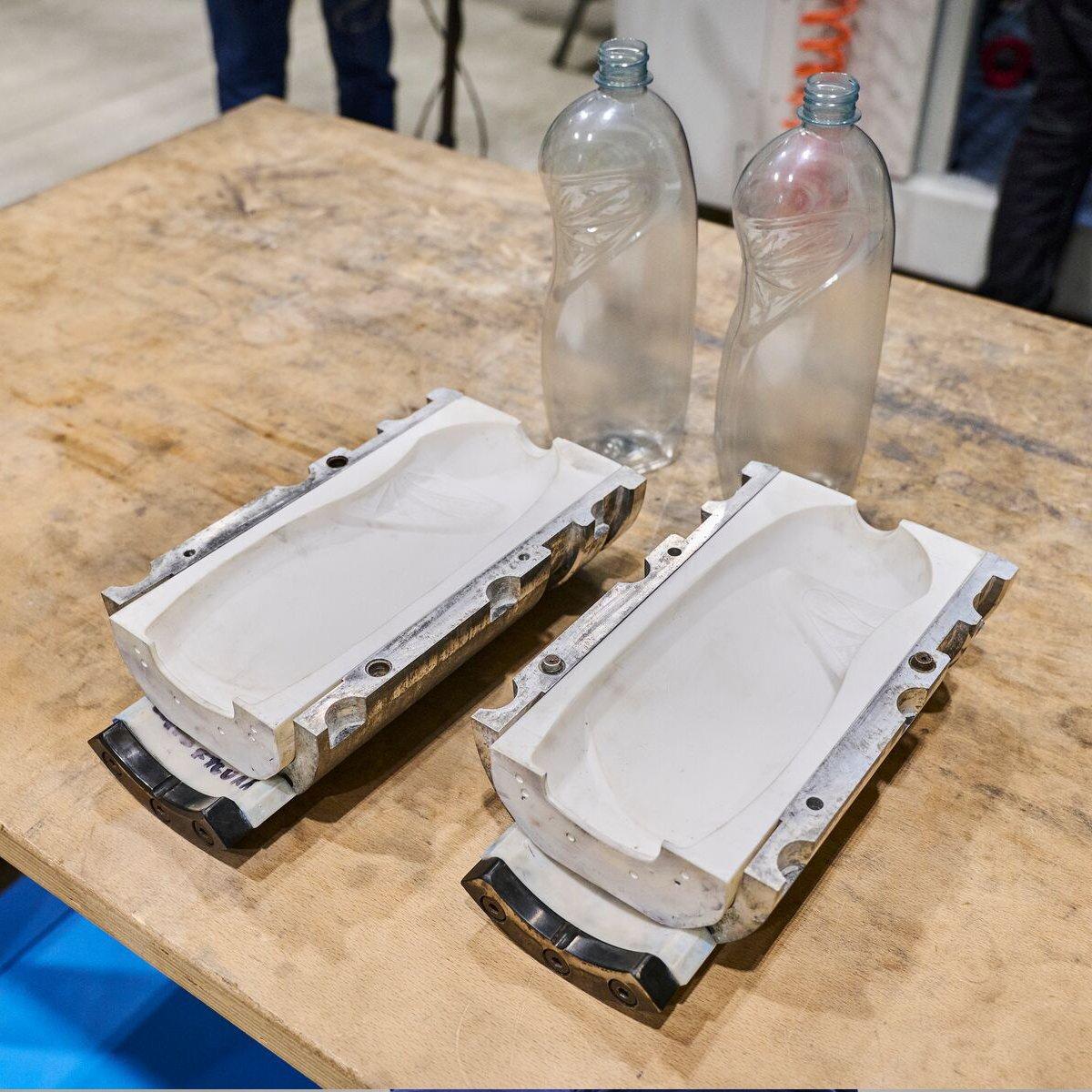
Stampaggio per stiramento e soffiaggio su scala ridotta con stampi 3D
Questo whitepaper illustra metodi e linee guida per l'uso di stampi realizzati con la stampa 3D SLA nel processo di SBM, al fine di ridurre i costi e i tempi di produzione durante la fase di pre-produzione. Partendo dalle considerazioni su design e workflow fino alle condizioni di stampaggio, il whitepaper descrive nel dettaglio lo studio di fattibilità condotto da due aziende leader del settore, Unilever e Serioplast.
Workflow tradizionale per lo sviluppo e il test di nuovi design di flaconi
I prodotti in plastica, come contenitori per alimenti e bevande, imballaggi per cosmetici e prodotti medicali, vengono solitamente prodotti mediante stampaggio per soffiaggio, un insieme di metodi di produzione di massa ormai consolidati per la creazione parti di alta qualità con pareti sottili. Lo stampaggio per soffiaggio ha tempi di ciclo molto brevi, mediamente di uno o due minuti, ed è estremamente conveniente per la produzione di volumi elevati. Di solito lo si utilizza per produrre milioni di parti identiche a un costo per unità ridotto.
Lo stampaggio per soffiaggio consiste nel gonfiare un tubo di plastica riscaldato, chiamato parison o preforma iniettata, all'interno di uno stampo fino a quando non assume la forma desiderata. Ne esistono tre tipi: stampaggio per estrusione e soffiaggio (EBM), stampaggio per iniezione e soffiaggio (IBM) e stampaggio per stiramento e soffiaggio (SBM). L'SBM viene comunemente utilizzato per produrre contenitori in PET trasparenti di alta qualità, come le bottiglie d'acqua.
Serioplast Global Services, fondata nel 1974 a Seriate (Bergamo), produce a livello globale imballaggi in plastica rigida per il settore ed è una delle principali aziende partner di Unilever per lo sviluppo e la produzione di imballaggi per il mercato della cura della casa e della persona. "Produciamo 4 miliardi di flaconi in PET, HDPE e PP all'anno", ha affermato Migliarelli.
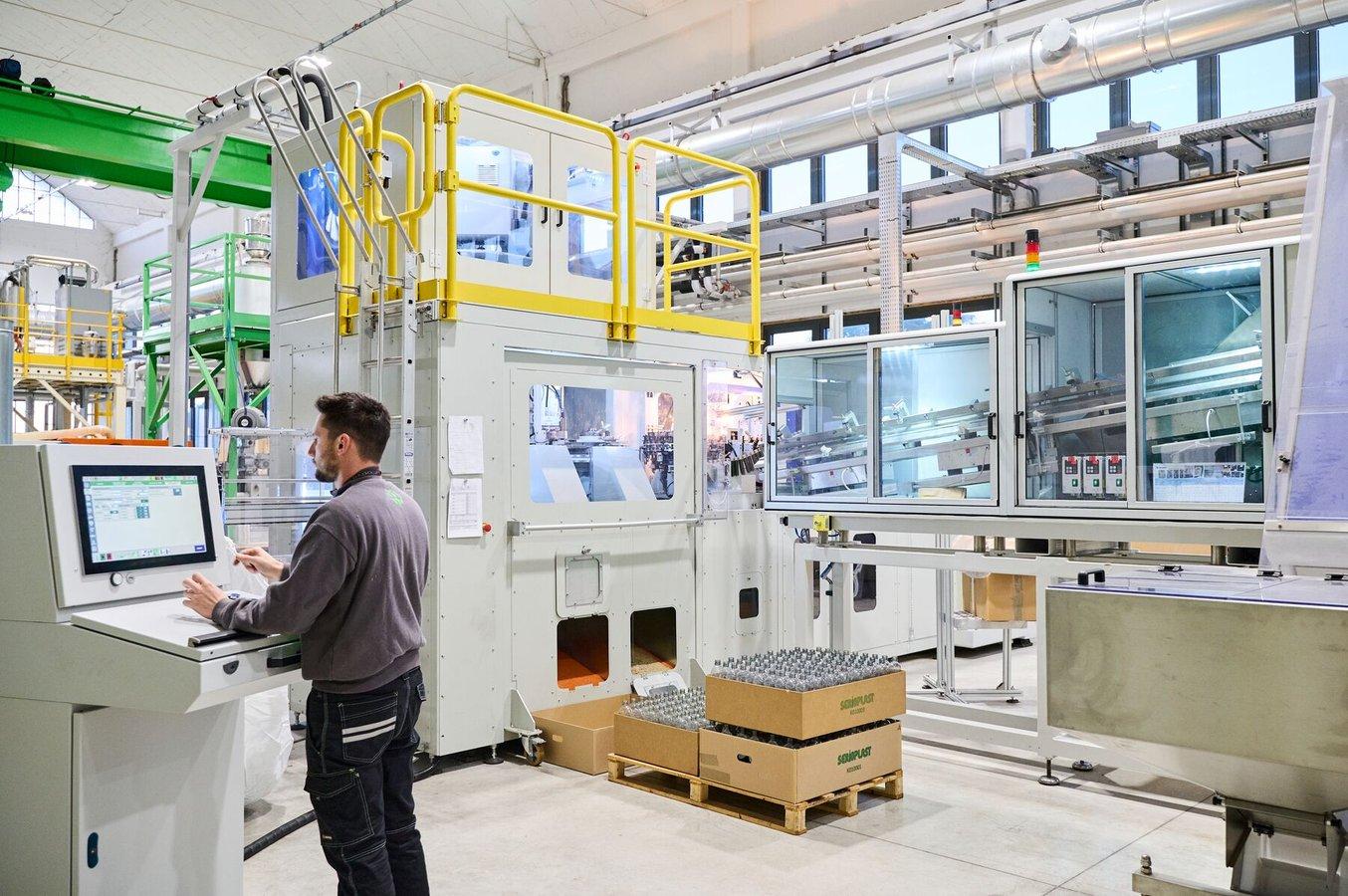
Apparecchio industriale per SBM UNIX a quattro cavità di Seriomac nello stabilimento di ricerca e sviluppo di Serioplast. Serioplast e Unilever hanno sviluppato un nuovo workflow utilizzando gli stampi realizzati in 3D in questi apparecchi industriali per la produzione su larga scala.
In passato, Serioplast stampava direttamente in 3D le riproduzioni per i prototipi o le produceva mediante stampaggio per soffiaggio, ma non avevano la giusta resa o trasparenza e non erano sufficientemente affidabili per essere inviate alla clientela. Tuttavia, la creazione di campioni di qualità mediante l'SBM richiede costose attrezzature in metallo che prolungano di sei-nove settimane i tempi di produzione di una tipica fase di test pilota, a causa della complessità del processo e dell'esternalizzazione della produzione dello stampo.
"Dobbiamo aspettare dalle sei alle 12 settimane prima di poter fornire alla clientela il campione vero e proprio, quindi dedichiamo parecchie settimane solo a provare il design di un nuovo flacone. A volte è un lavoro impegnativo e difficile, perché capita di dover rifare tutto da capo", ha dichiarato Migliarelli.
Gli stampi per SBM sono tradizionalmente realizzati in metallo mediante lavorazione meccanica CNC, che richiede attrezzature specializzate, software CAM e manodopera qualificata. La produzione di attrezzature in metallo è generalmente esternalizzata e prevede tempi di realizzazione di quattro-otto settimane e costi che vanno da 2000 a più di 100 000 €, a seconda della complessità della parte e del numero di parti per stampo. Anche la lavorazione meccanica in-house di uno stampo in metallo richiede solitamente sei settimane, in quanto sono previsti diversi passaggi: ordine dei materiali, configurazione del CAM e dell'apparecchio, lucidatura manuale e tempo di attesa per la disponibilità dell'apparecchio.
Di conseguenza, lo stampaggio per soffiaggio di volumi ridotti di parti per la prototipazione e i test pilota non è mai stato economicamente sostenibile. Le aziende come Unilever si sono trovate a dover pianificare con tempistiche prolungate e a prendere decisioni definitive sul design basandosi su prototipi estetici realizzati con materiali diversi, cosa che spesso ha prodotto attrezzature obsolete e costi nascosti.
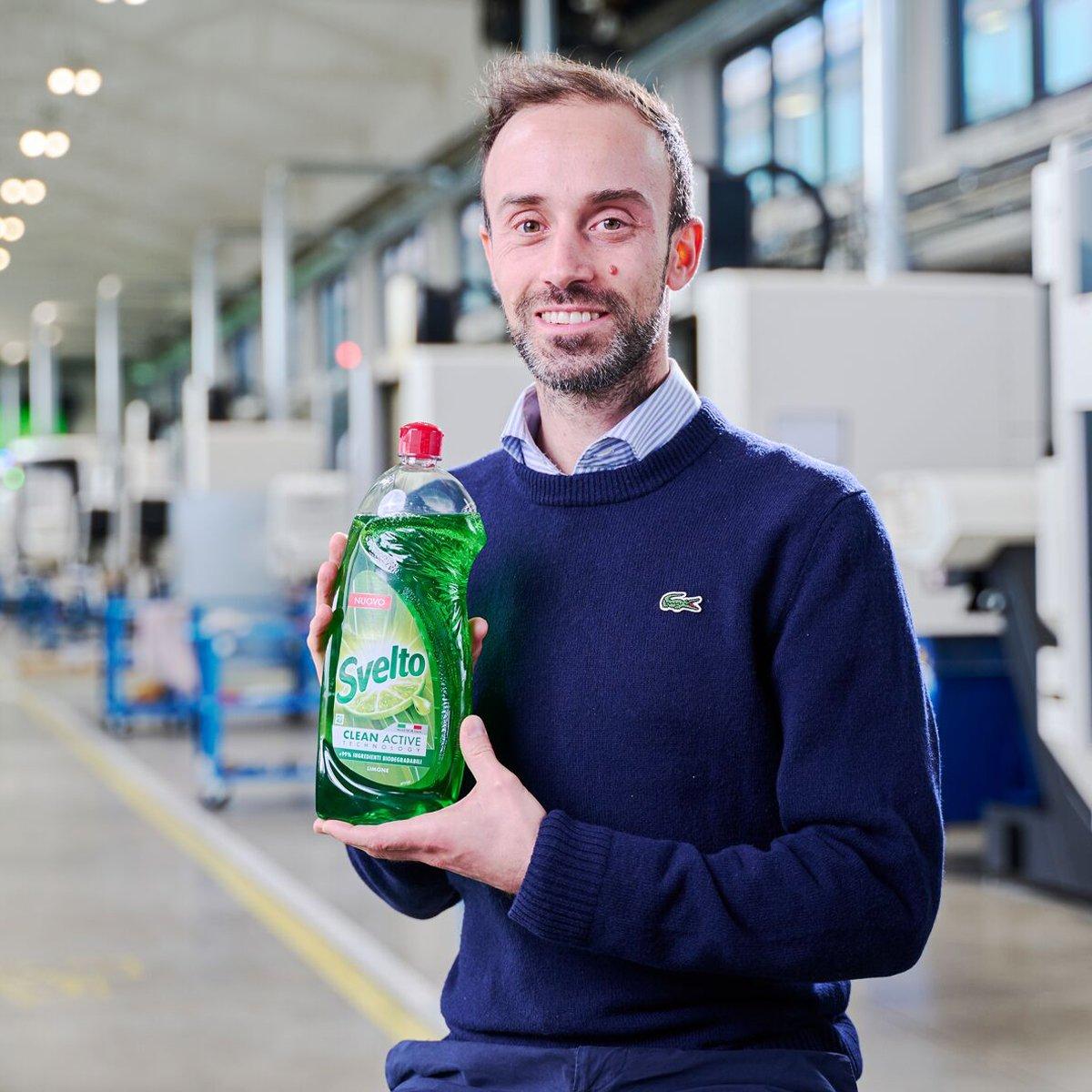
Riduzione di costi e tempi per i test pilota di imballaggi grazie allo stampaggio per soffiaggio rapido
In questo webinar, l'esperto di stampaggio per soffiaggio Flavio Migliarelli presenterà il workflow e le diverse fasi del processo e illustrerà i vantaggi e le applicazioni principali degli stampi realizzati in 3D per lo stampaggio per stiramento e soffiaggio rapido.
Stampaggio per soffiaggio di flaconi reali in modo più rapido ed economico
La stampa 3D è un'ottima soluzione che consente di produrre strumenti in modo rapido e a basso costo. Richiede un'attrezzatura molto limitata e permette di risparmiare il tempo necessario alla lavorazione meccanica CNC, dando modo al personale specializzato di dedicarsi ad attività più importanti. La stampa 3D in-house consente ad aziende produttrici e team di design di prodotto di integrare la creazione rapida di attrezzature nel processo di sviluppo del prodotto per convalidare i passaggi di progettazione e produzione prima di passare alla produzione di massa. Gli stampi realizzati in 3D vengono già utilizzati in processi come lo stampaggio a iniezione o la termoformatura per eseguire iterazioni rapide, accelerare lo sviluppo del prodotto e immettere sul mercato prodotti migliori.
La tecnologia di stampa 3D stereolitografica (SLA) è un'ottima scelta per lo stampaggio. È caratterizzata da una finitura superficiale liscia e da un'elevata precisione che lo strumento trasferirà alla parte finale e che agevola anche la rimozione dallo stampo. La Form 3L è una stampante 3D SLA di grande formato che consente la fabbricazione di parti e stampi di grandi dimensioni, pur essendo abbastanza compatta per un ufficio.
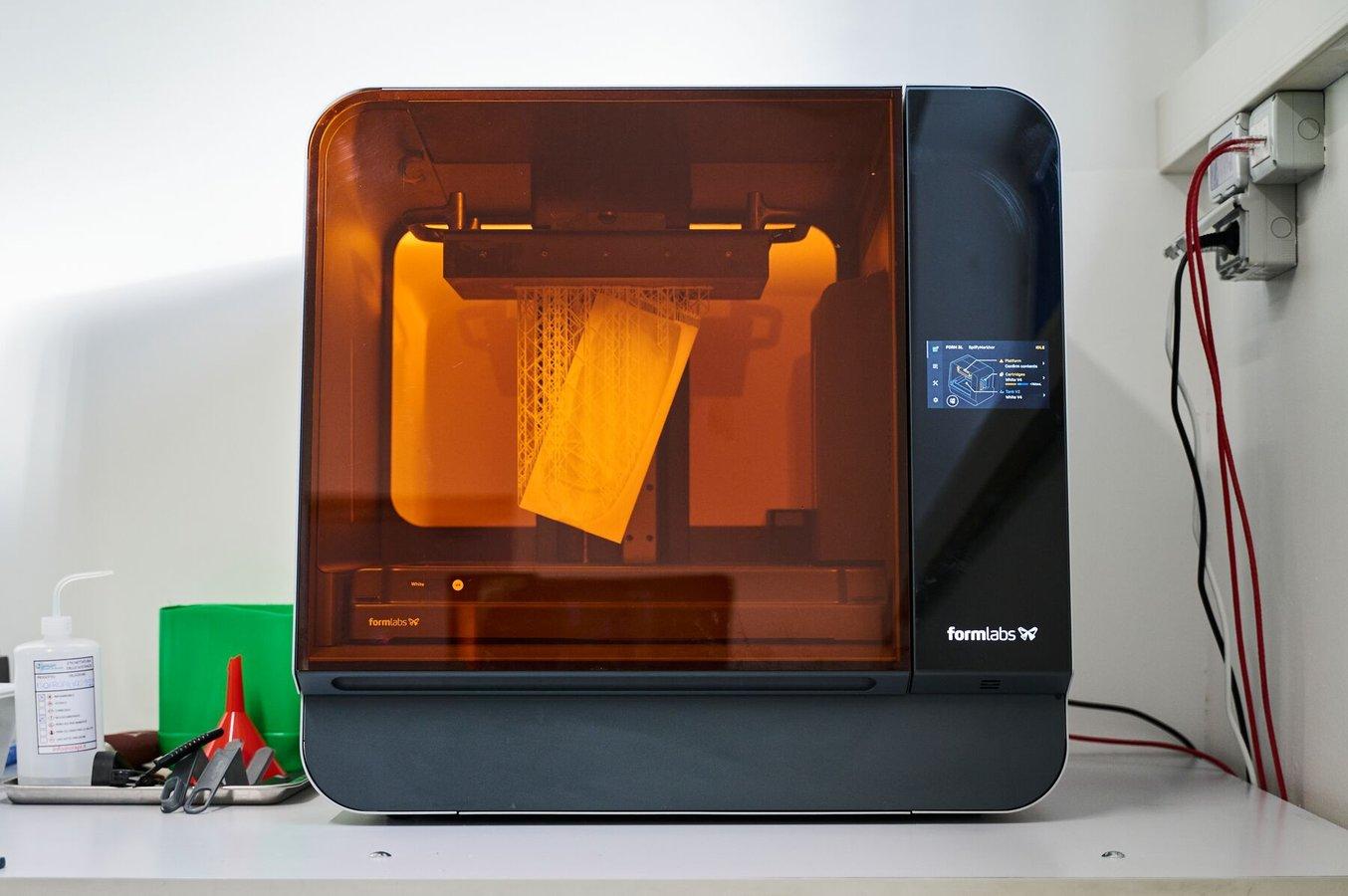
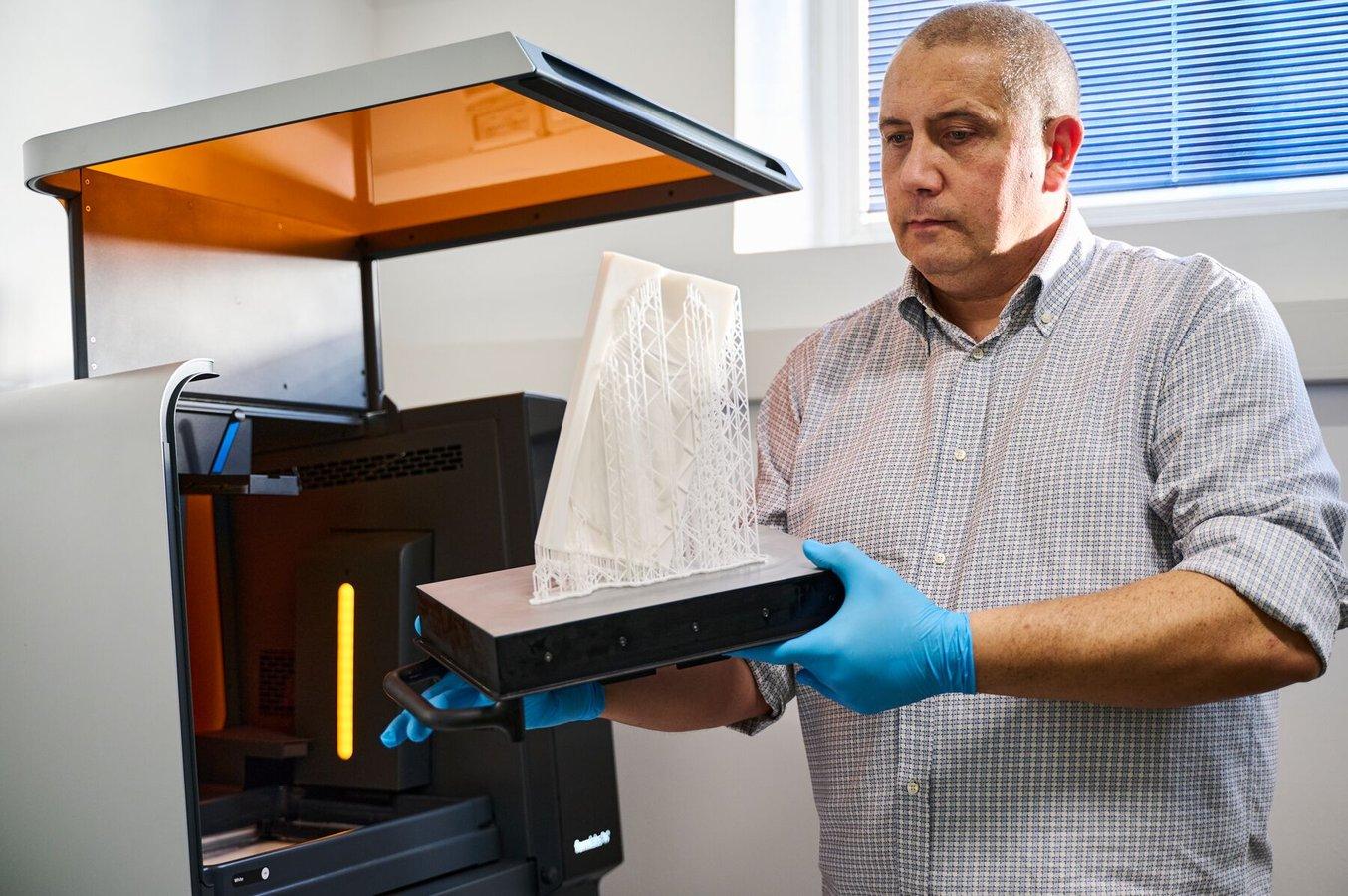
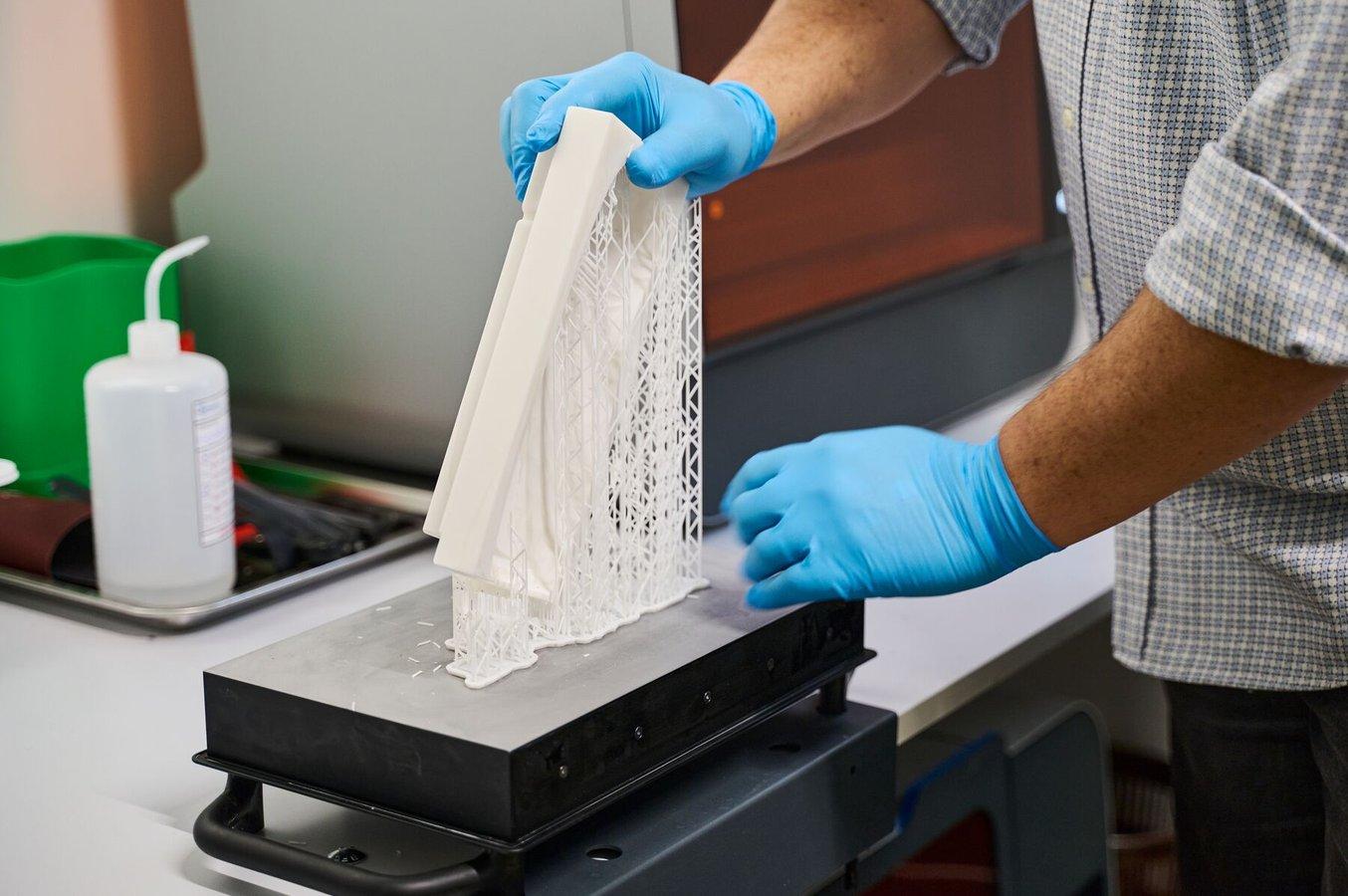
Lo stampo viene realizzato in 3D sulla Form 3L con la Rigid 10K Resin.
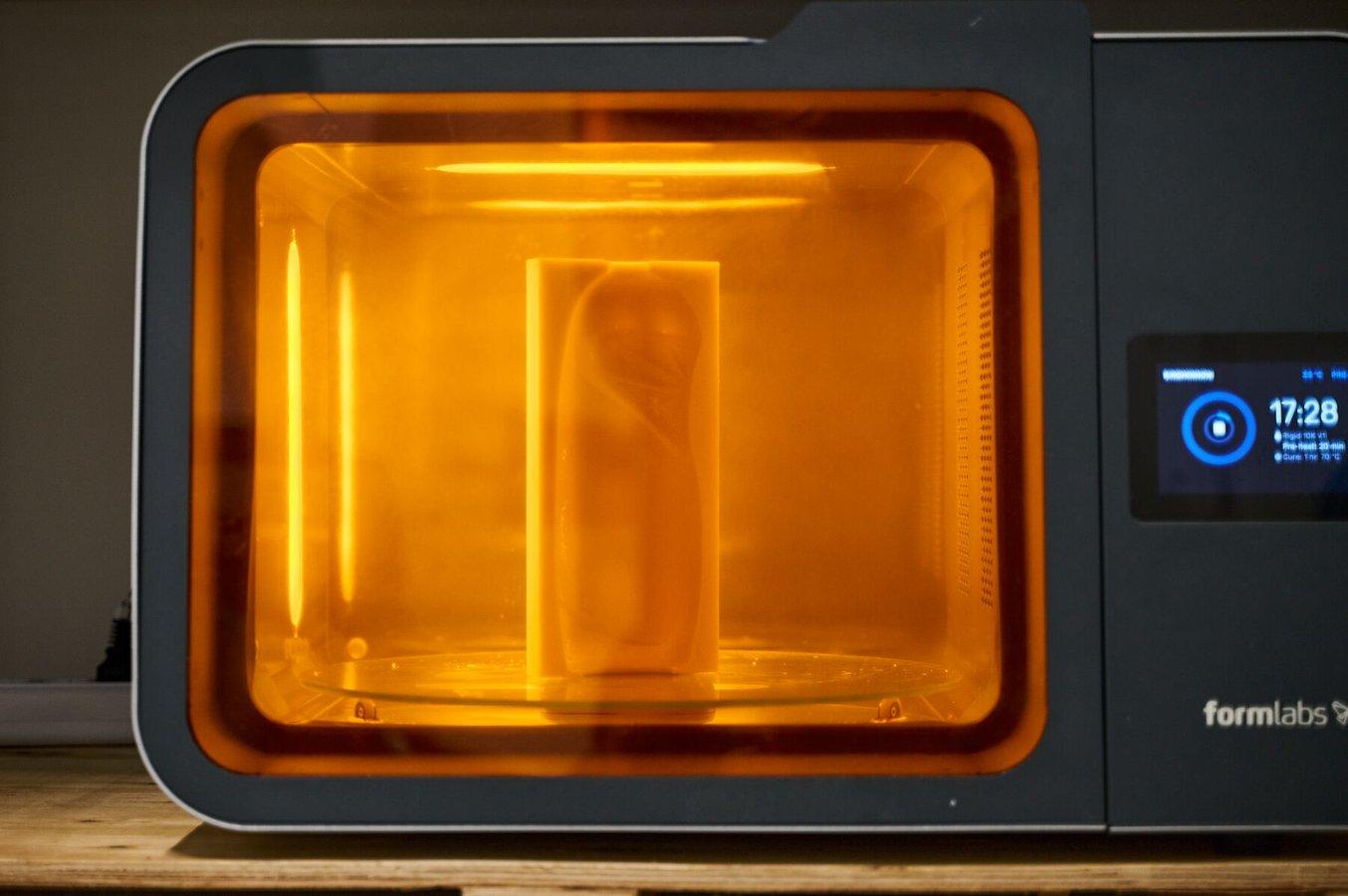
Dopo il lavaggio, i supporti vengono rimossi e lo stampo viene sottoposto alla polimerizzazione post-stampa.
Un passaggio fondamentale per la produzione degli stampi è la scelta del materiale. Unilever e Serioplast avevano bisogno di un materiale in grado di resistere alla pressione interna e alla temperatura del processo di SBM e che mantenesse al contempo una buona precisione e stabilità dimensionale.
"Grazie al team di ingegneria di Formlabs, abbiamo trovato un materiale che ci permettesse di ottenere pochi flaconi nei materiali finali per eseguire i nostri test", ha affermato Cademartiri
La combinazione di stabilità, rigidità e resistenza termica rende la Rigid 10K Resin il materiale ideale per l'SBM. Si tratta di un materiale di qualità industriale rinforzato con vetro con una temperatura di distorsione termica di 218 °C a 0,45 MPa e un modulo di elasticità di 10 000 MPa. Gli stampi realizzati con la Rigid 10K Resin hanno una buona stabilità dimensionale e possono essere sottoposti a centinaia di cicli di stampaggio per soffiaggio con un'elevata ripetibilità.
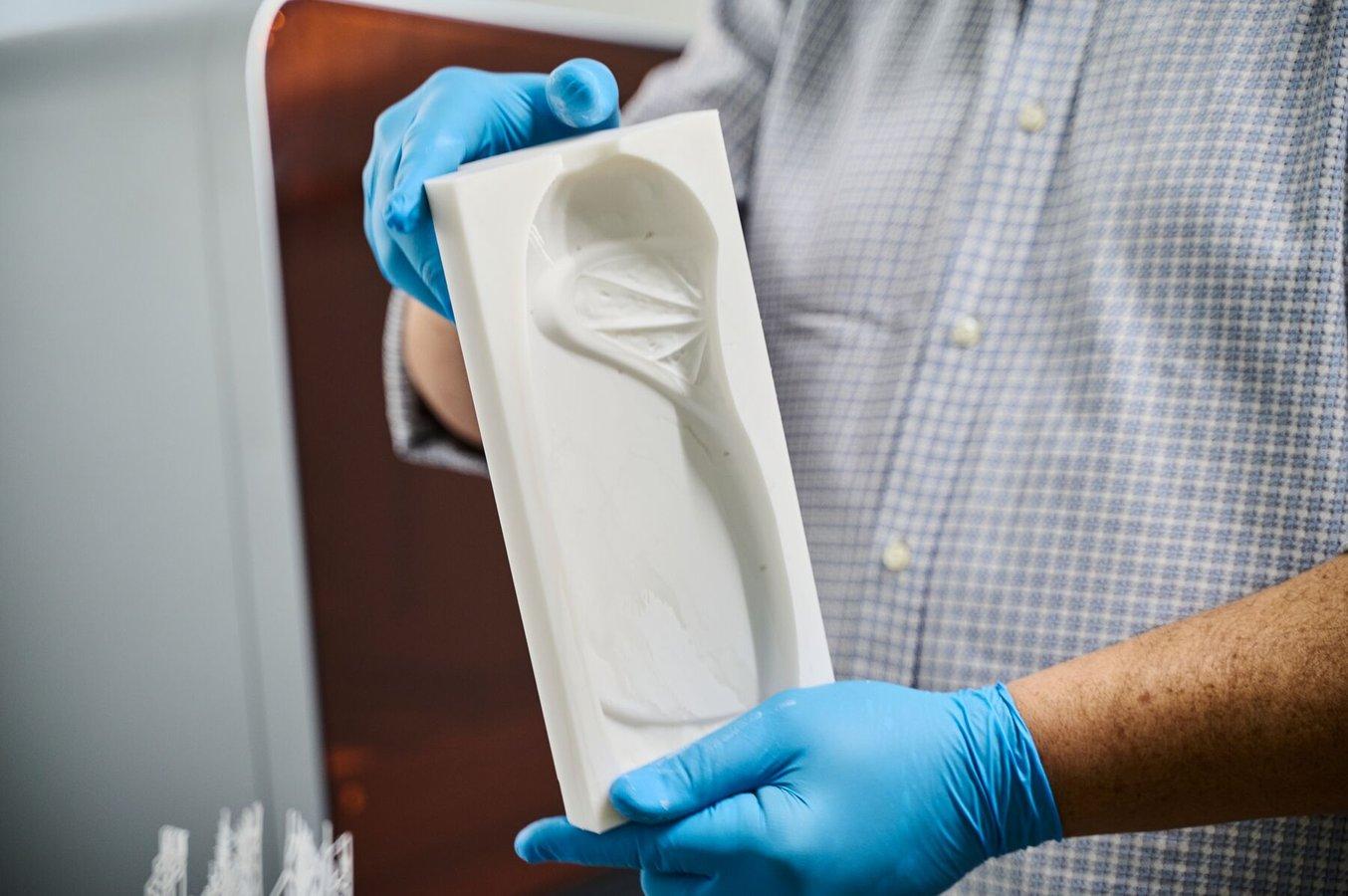
Utilizzando la Rigid 10K Resin, Serioplast è riuscita a fabbricare stampi precisi con una finitura superficiale liscia, che consentono di integrare dettagli complessi, come fori di soli 0,5 mm. Il team ha eseguito la post-elaborazione con una lucidatrice o mediante levigazione manuale per ottenere le dimensioni ottimali. Le superfici con trame sono state incorporate nella progettazione CAD della cavità dello stampo.
"Abbiamo definito i dettagli dello stampo, soprattutto per i flaconi che presentano loghi o dettagli, come un limone in rilievo, che richiedono molta precisione. La stampante Formlabs e la Rigid 10K Resin consentono di ottenere dettagli eccellenti che possono essere trasferiti successivamente sui flaconi finali", ha dichiarato Cademartiri.
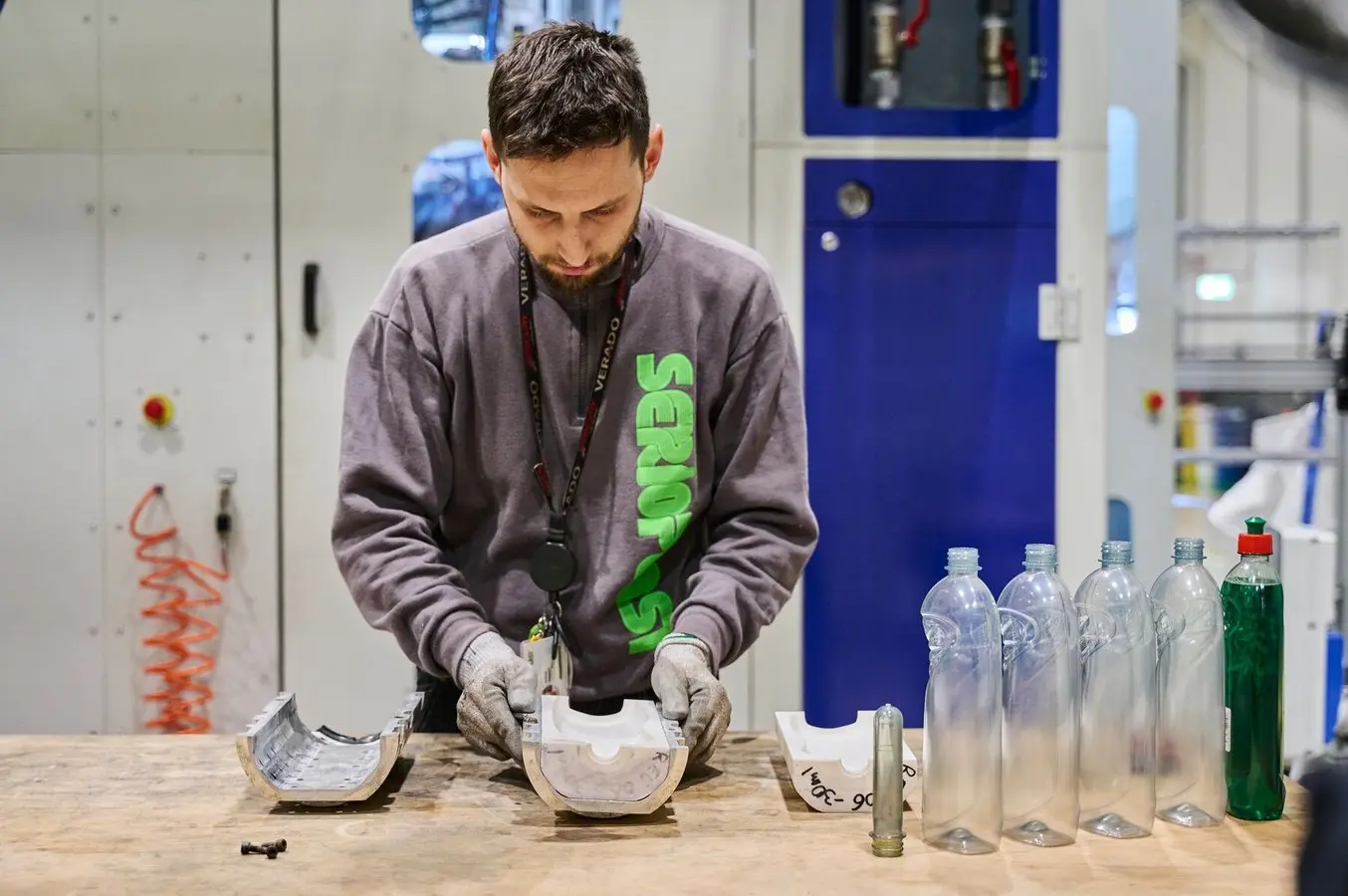
Lo stampo realizzato in 3D con la Rigid 10K Resin viene lucidato manualmente e poi assemblato in un telaio metallico.
La stampa 3D SLA consente di realizzare uno stampo in due giorni. Gli stampi realizzati in 3D riducono da sei a due settimane il tempo necessario per avviare i test pilota e consentono di ottenere parti pre-produzione realistiche, con una qualità molto simile a quella di produzione e con lo stesso materiale e gli stessi apparecchi utilizzati per le unità di produzione finali. Inoltre, gli stampi realizzati in 3D consentono di eseguire i test pilota di più design contemporaneamente.
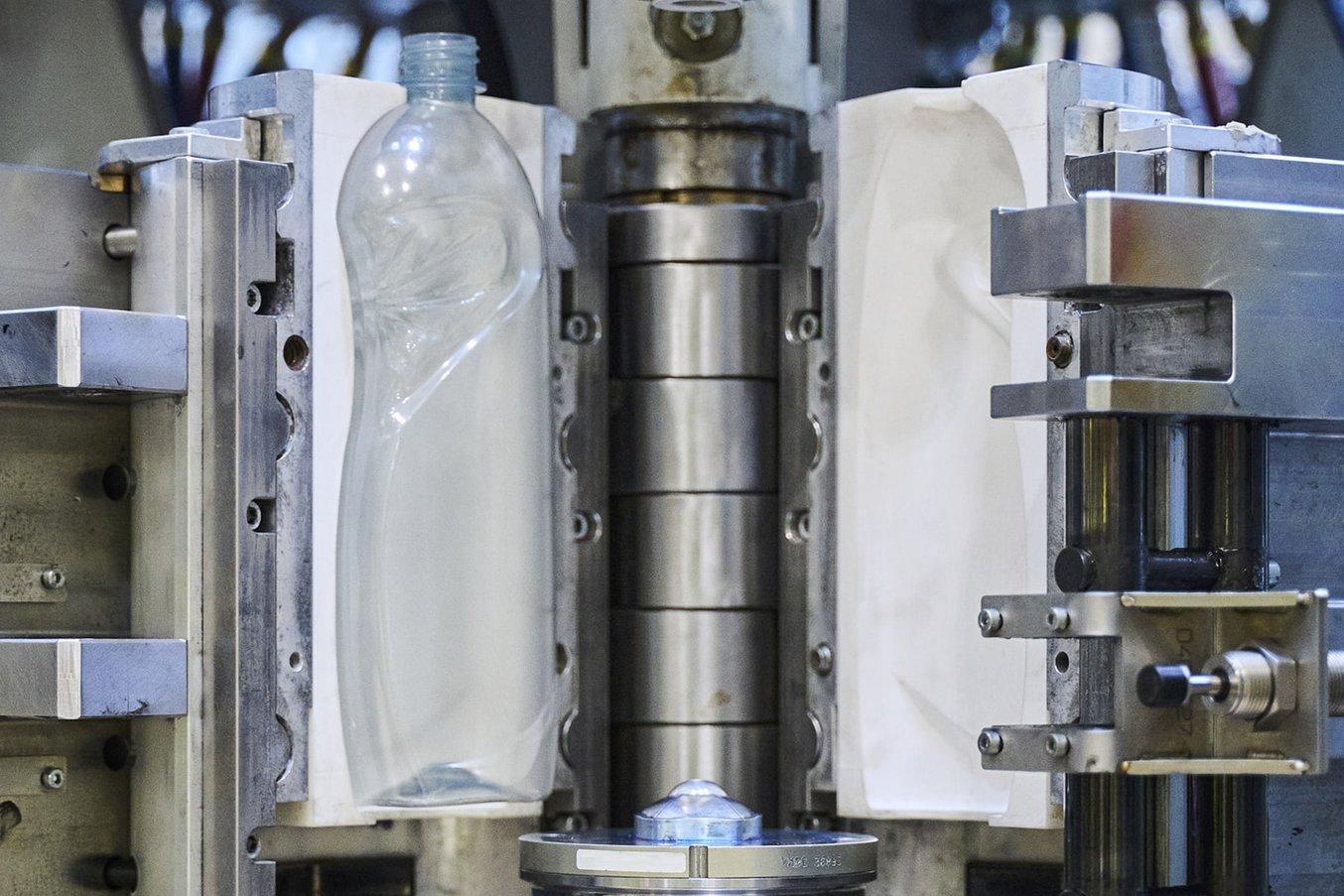
Stampo realizzato in 3D con la Rigid 10K Resin per il flacone Slice da 750 mL di Unilever installato sul supporto a guscio dell'apparecchio. Il team può utilizzare la stessa finestra di processo di uno stampo pilota standard, che consente di testare in modo affidabile il processo finale.
“Con lo stampo realizzato in 3D, utilizziamo un layout standard all’interno di un supporto a guscio che viene posizionato nell'apparecchio per lo stampaggio per soffiaggio. In questo modo, risparmiamo molto tempo per il design degli stampi e siamo in grado di gestire la programmazione della stampa 3D con estrema facilità", ha dichiarato Migliarelli.
Produzione di 200 unità | Stampo in metallo realizzato con lavorazione meccanica | Stampo realizzato in 3D |
---|---|---|
Attrezzature | Macchina a controllo numerico in-house o esternalizzazione | Form 3L Rigid 10K Resin |
Tempi di esecuzione dei test pilota | 6-8 settimane | 2 settimane |
Costo delle attrezzature | 2500-10 000 € | 500-1000 € |
"Con lo stampo realizzato in 3D, possiamo ridurre i tempi del 70% e i costi del 90% rispetto a uno stampo standard. Se in passato [la nostra clientela] doveva aspettare fino a 12 settimane per un solo design; ora possiamo realizzarne cinque."
Flavio Migliarelli, responsabile di design del dipartimento di ricerca e sviluppo di Serioplast Global Services
Svolgere test così approfonditi con i metodi tradizionali è pressoché impossibile, perché bisognerebbe investire in uno stampo in metallo per ciascun design, rinunciando ai vantaggi delle economie di scala e non recuperando mai i costi delle attrezzature.
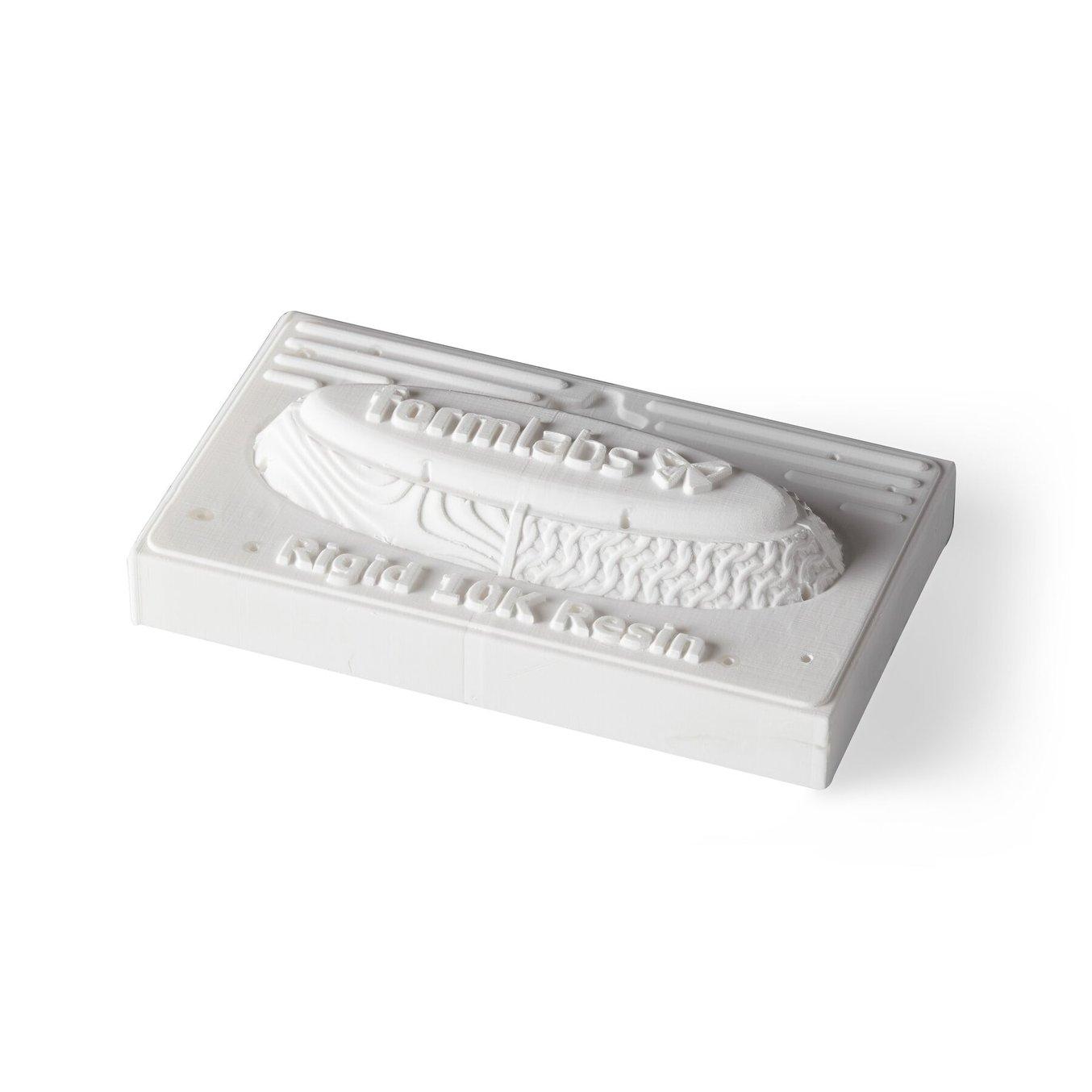
Richiedi un campione gratuito
Guarda e tocca con mano la qualità di Formlabs. Saremo lieti di inviare presso la tua azienda un campione gratuito.
Dai test sulla clientela alla programmazione della linea di produzione
In primo luogo, gli strumenti stampati in 3D vengono utilizzati per produrre campioni per i test sulla clientela. Questi riproducono il prodotto finale dal punto di vista fisico, estetico e funzionale e sono percepiti agli occhi della clientela come il prodotto vero e proprio.
"Riusciamo ad avere un flacone vero e proprio prima di creare lo stampo reale. In questo modo, siamo in grado di capire subito se abbiamo sviluppato correttamente il prodotto o se è necessario apportare delle modifiche prima di commettere errori che possono costarci anche di più."
Stefano Cademartiri, responsabile del reparto CAD e prototipazione di Unilever
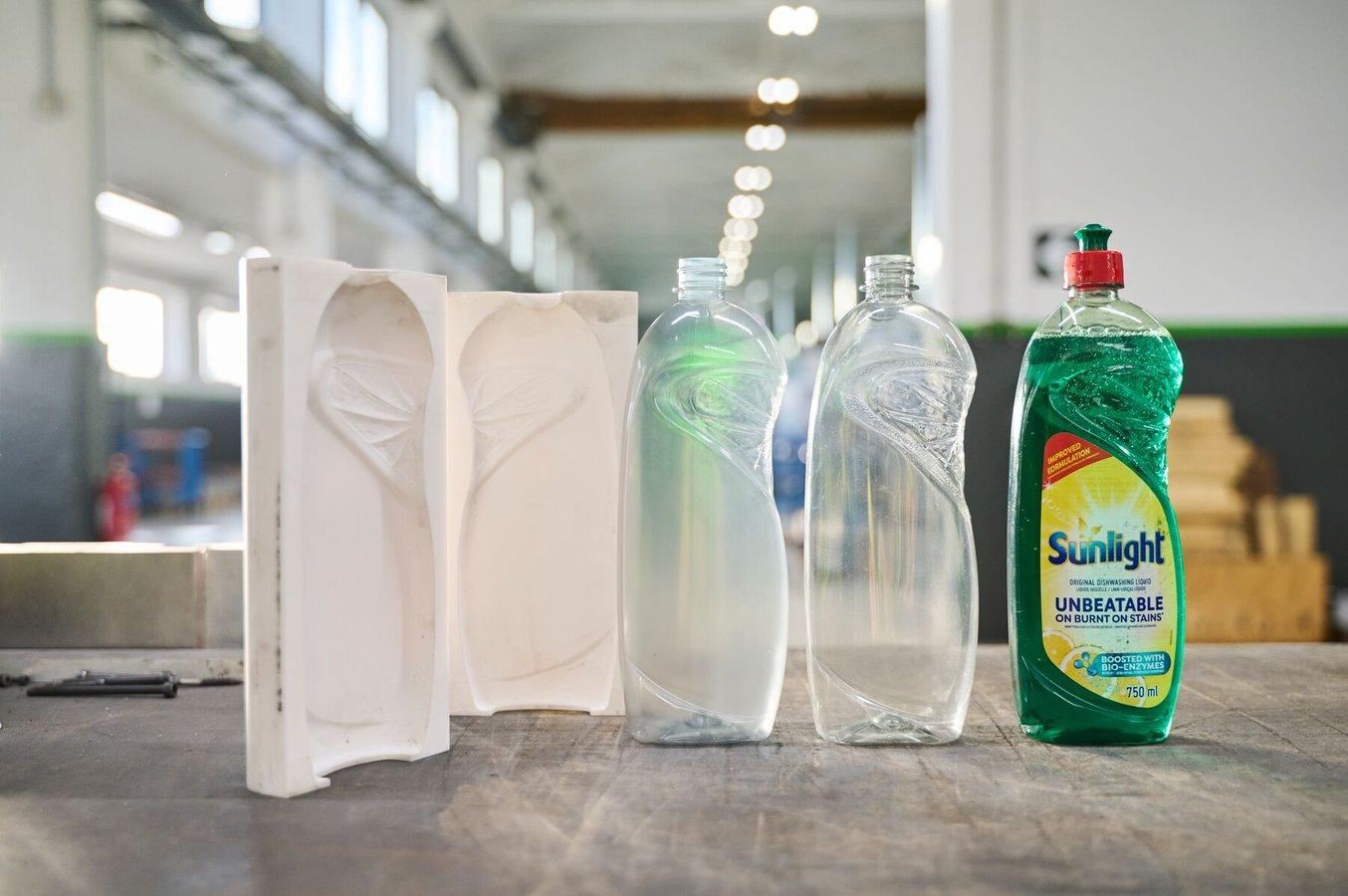
I flaconi prodotti con uno stampo realizzato in 3D sono quasi identici al prodotto finale creato mediante attrezzature in metallo tradizionali. Da sinistra a destra: lo stampo in due parti realizzato in 3D con la Rigid 10K Resin, un flacone prodotto con lo stampo realizzato in 3D con la Rigid 10K Resin, un flacone prodotto con uno stampo in metallo e un prototipo di flacone etichettato per i test sulla clientela.
Lo stampo modulare viene utilizzato anche per convalidare il processo di SBM e la preforma in PET che verrà soffiata in termini di finestre di processo, rapporto di stiramento e distribuzione del materiale ottenibile. Serioplast produce le preforme in-house mediante stampaggio a iniezione. Sebbene alcune preforme siano realizzate su misura per uno specifico flacone, di solito vengono utilizzate con articoli standardizzati che non si possono modificare. Il team di Serioplast voleva capire la gamma di possibilità offerte da questa preforma standard. Queste informazioni sono utili per stabilire se una determinata preforma è adatta allo stampaggio per soffiaggio di uno specifico flacone prima di avviare la produzione.
"Utilizziamo la stessa finestra di processo di uno stampo pilota standard. In questo modo, possiamo testare le finestre di processo finali e vedere cosa succede al flacone. Utilizziamo una pressione che può arrivare a 30 bar, ma la preforma resiste senza problemi. Inoltre, la riscaldiamo a circa 100 °C senza che la cavità dello stampo realizzato in 3D si usuri. Potremmo produrre molto facilmente 100-200 flaconi al giorno o anche 1000, se abbiamo più tempo", ha dichiarato Migliarelli.
La terza applicazione per la produzione rapida di stampi è il test preliminare di alcuni aspetti della linea di produzione. Dal momento che i flaconi formati con gli stampi realizzati in 3D sono molto simili alle unità di produzione, possono essere impiegati per svolgere alcune operazioni di convalida preliminare della linea di riempimento, come il movimento della linea, il funzionamento delle ruote stellari per le riempitrici, la tappatura o l'azione dell'incartonatrice robotizzata. I test pilota della linea di produzione consentono agli stabilimenti di munirsi in anticipo delle parti di ricambio, preparare la linea per la produzione di massa e accelerare i tempi di commercializzazione.
Lancio sul mercato di prodotti migliori in tempi ridotti
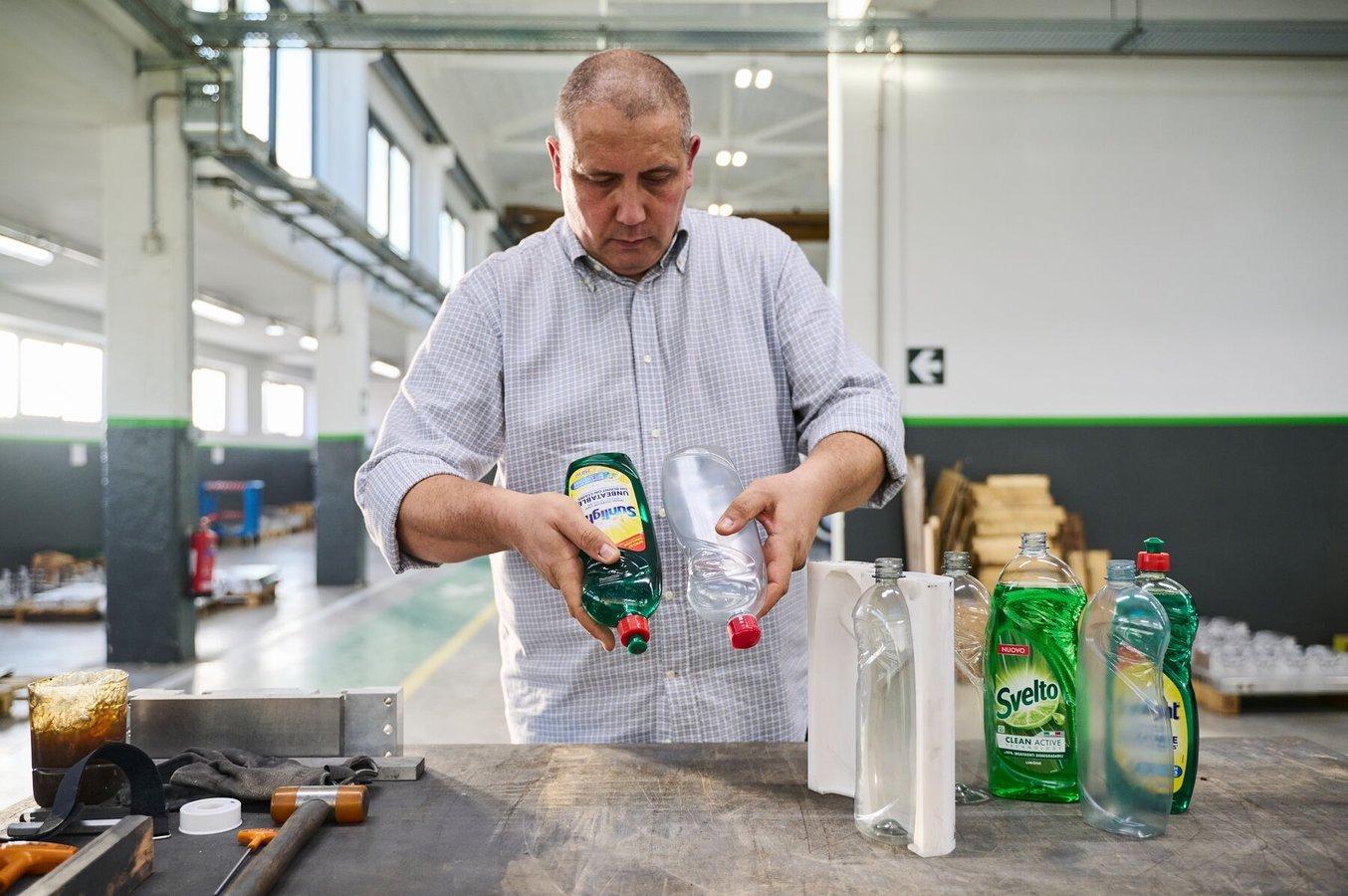
Cademartiri e Serioplast hanno già testato circa 15 diversi modelli di flaconi con il nuovo processo.
Con le stampanti SLA di Formlabs e la Rigid 10K Resin, Unilever e Serioplast sono riuscite a ridurre i tempi di produzione del 70% e i costi delle attrezzature del 90% per produrre cicli pilota di 200 unità in sole due settimane.
"Formlabs è un ottimo partner, non solo perché produce gli apparecchi che utilizziamo, ma anche perché ci supporta nella scoperta delle proprietà dei materiali. Questa collaborazione mi ha aiutato a capire le possibilità offerte dall'uso degli stampi realizzati in 3D", ha affermato Cademartiri.
Il nuovo workflow consentirà a Unilever di immettere sul mercato prodotti migliori più velocemente e ridurre drasticamente i rischi e i costi associati allo sviluppo di imballaggi.
"Il vantaggio che offre la stampante 3D è la possibilità di trasformare i sogni in realtà. Quello che vediamo sullo schermo viene realizzato in poche settimane. Un prodotto vero, in un flacone vero, con un tappo vero e un'etichetta vera", ha concluso Cademartiri.
Hai altre domande sull'uso di una stampante SLA per lo stampaggio per soffiaggio o per altre applicazioni ingegneristiche o legate alla produzione? Contatta il nostro team specializzato per richiedere una parte stampata in Rigid 10K Resin come campione gratuito.