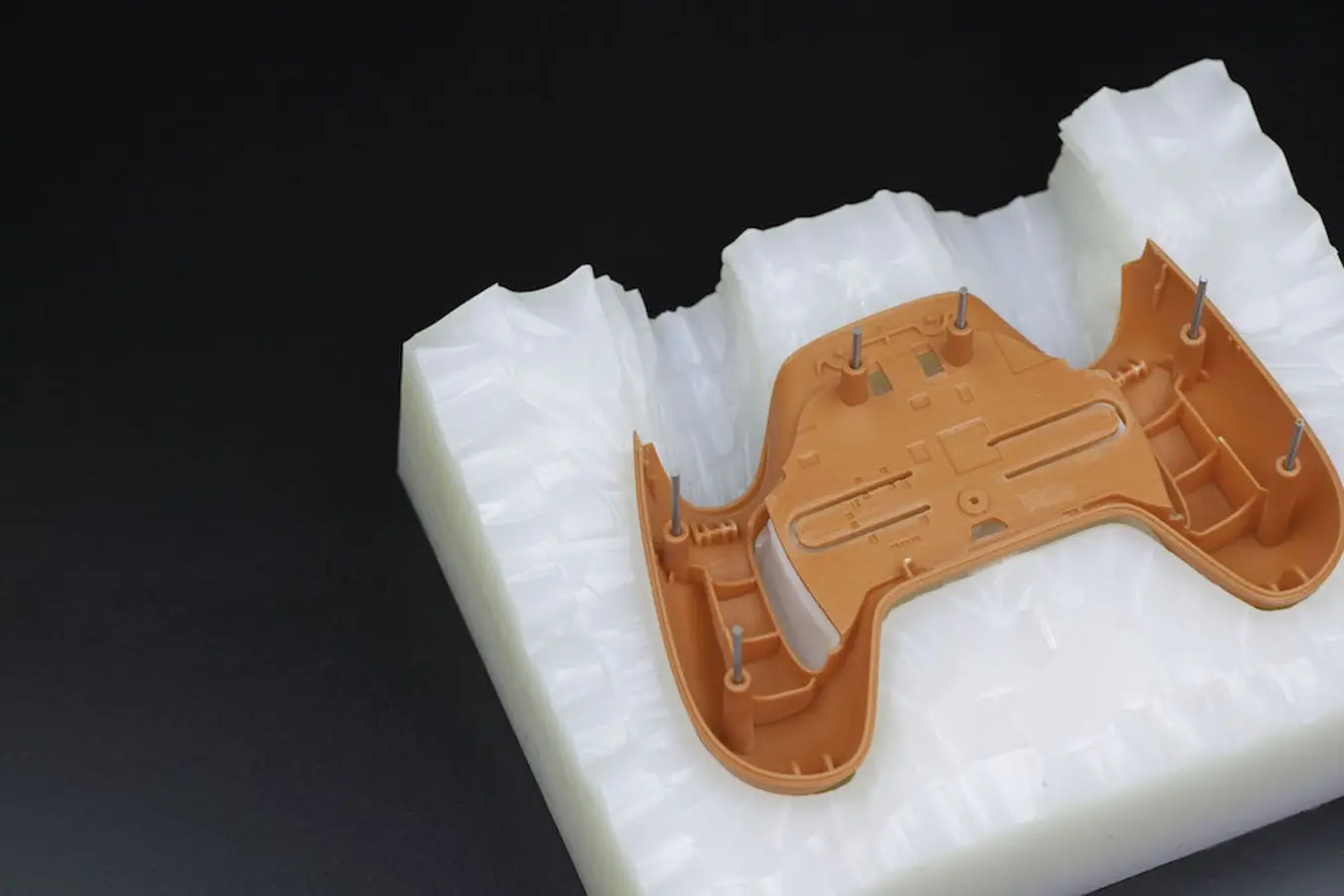
Un prototipo prodotto con la colata di uretano. Fonte: Fictiv
La colata sottovuoto è un metodo comune per la produzione in volumi ridotti di prototipi destinati a test di mercato, prodotti personalizzati, dispositivi medici su misura e molto altro.
Questa guida illustra in modo dettagliato il processo di colata sottovuoto, cosa lo differenzia da altre tecniche di produzione, le migliori attrezzature per la colata di uretano e come produrre modelli stampati in 3D per la colata sottovuoto.
Che cos'è la colata sottovuoto o colata di uretano?
La colata sottovuoto è un metodo di produzione simile allo stampaggio a iniezione in cui resina di uretano viene colata all'interno di una cavità tra due metà di uno stampo in silicone.
Il processo prevede la replica di un modello master ottenuta tramite versamento di silicone, che una volta indurito forma uno stampo. Seguendo una procedura altamente specialistica, lo stampo viene diviso in due metà, il modello master viene rimosso e in seguito viene aggiunto un sistema di iniezione e ventilazione. Una resina a base di uretano viene quindi colata nella cavità risultante, dopo di che viene eseguita la polimerizzazione sottovuoto per eliminare eventuali bolle d'aria.
Il risultato è una riproduzione estremamente precisa dell'oggetto originale.
Nota: negli Stati Uniti, la colata sottovuoto è meglio conosciuta come colata di uretano o colata di poliuretano. In questo articolo i due termini vengono usati in modo intercambiabile.
Applicazioni della colata sottovuoto
La colata sottovuoto è il metodo ideale per la produzione in volumi ridotti di parti con una qualità pari a quella industriale.
Il processo consente di realizzare modelli estremamente dettagliati, praticamente indistinguibili dal prodotto finale e dunque perfetti da usare nel settore della fotografia commerciale o durante fiere o presentazioni agli investitori. Dal momento che uno stampo in silicone può produrre circa cinquanta colate, la colata sottovuoto consente alle aziende anche di lanciare una prima serie del loro prodotto per test di mercato preliminari.
Se il progetto richiede maggiori quantità di parti, sono disponibili varie opzioni:
-
Lo stesso modello master può essere riutilizzato per creare più stampi in silicone.
-
Più modelli master possono essere utilizzati per creare uno stampo multi-cavità.
-
Anziché realizzare gli stampi in silicone per la vulcanizzazione a temperatura ambiente (RTV), è possibile scegliere silicone o gomma per la vulcanizzazione ad alta temperatura (HTV). Il risultato è uno stampo più resistente, in grado di produrre da 300 a 500 colate.
Con un tempo di realizzazione di soli dieci giorni dalla produzione del modello master alla ricezione dei prodotti, la colata sottovuoto è utile sia per la prototipazione rapida che per la produzione ponte. Inoltre, non comporta gli elevati costi iniziali di processi di produzione industriali quali stampaggio a iniezione, termoformatura e fusione in centrifuga.
Grazie alla compatibilità con un'ampia gamma di materiali, la colata sottovuoto permette di creare modelli estremamente dettagliati con una perfetta finitura superficiale e numerose proprietà meccaniche, il che la rende ideale per la produzione in volumi ridotti di prodotti per utilizzo finale come:
-
Dispositivi medici su misura: protesi, ortesi, apparecchi acustici
-
Parti per il settore automobilistico: pannelli per cruscotti, manopole, tachimetri, loghi, mascotte, vetri per fanali, collettori di aspirazione
-
Componenti per l'elettronica di consumo: alloggiamenti, controller, pannelli di interfaccia utenti, integrazione di sensori
-
Componenti critici e parti di ricambio per robot e apparecchi industriali
-
Beni di consumo: occhiali da sole in edizioni limitate, penne, custodie di telefoni cellulari
-
Strumenti musicali
-
Strumenti scientifici
-
Componenti aggiuntivi per attrezzature sportive
-
Oggetti artistici, miniature, modelli in scala, oggetti di scena
La colata sottovuoto è una soluzione che viene spesso utilizzata anche per realizzare copie di oggetti senza ricorrere a complicati workflow di ingegneria inversa. Si tratta il più delle volte di oggetti rari o non più in produzione, come sculture, fossili, reperti storici, oggetti antichi, pezzi da collezione e modelli artigianali dei quali non è più disponibile il disegno originale o il modello CAD.
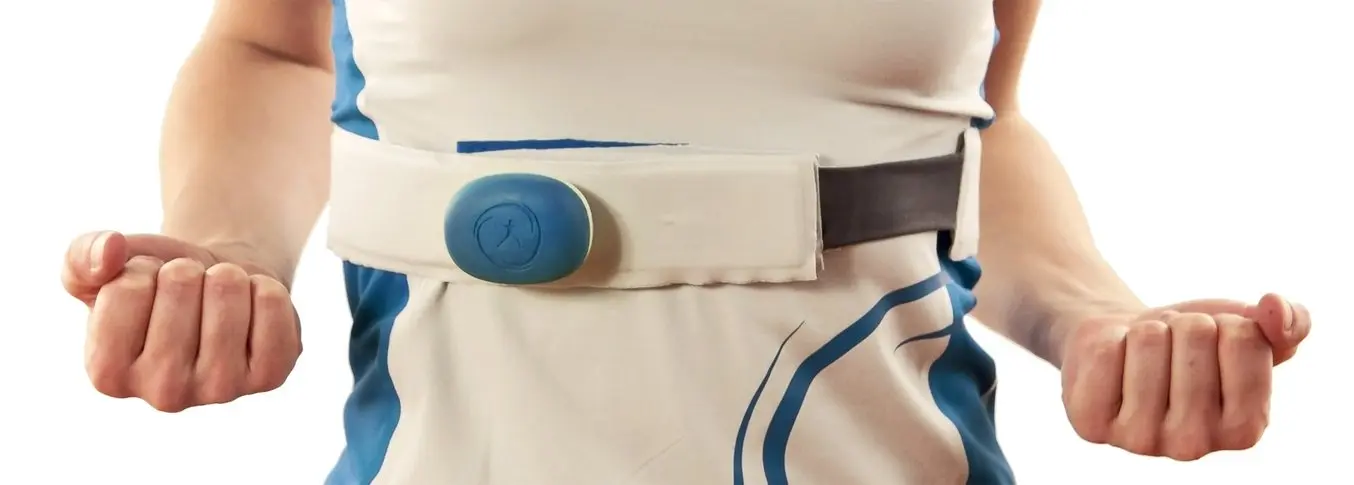
Alloggiamento elettronico per un sensore di respirazione indossabile, realizzato con il sovrastampaggio in silicone tramite colata sottovuoto. Fonte: IDZone Product Design. Colata: Venture Rapid Technologies.
Colata di uretano e alternative
Colata sottovuoto e stampaggio a iniezione
I team di ingegneria e design di prodotto ricorrono spesso alla stampa 3D per la validazione del design, dopo di che passano immediatamente allo stampaggio a iniezione per la validazione del prodotto. Il problema è che il costo di uno stampo a iniezione, realizzato tramite lavorazione meccanica CNC in acciaio di alta qualità e in grado di produrre milioni di parti, varia dai 5000 ai 100 000 €, a seconda delle dimensioni e della complessità della parte.
Per questo motivo, molte volte vengono utilizzati strumenti di qualità inferiore come soluzione intermedia prima dell'adozione di attrezzature rigide. Ad esempio, uno stampo in alluminio può comunque garantire fino a 1000-5000 cicli di stampaggio, ma a un costo molto più contenuto. Poiché i processi con attrezzature morbide sono molto più rapidi e consentono di creare design semplificati degli stampi, i tempi di realizzazione risultano praticamente dimezzati rispetto allo stampaggio a iniezione.
A seconda delle quantità di parti e della qualità richieste, un'opzione può essere l'utilizzo di uno stampo in acrilico o lo stampaggio a iniezione in volumi ridotti con stampi realizzati in 3D. Uno stampo realizzato in 3D con una stampante SLA di Formlabs costa in genere meno di 100 € e permette di realizzare più di 100 parti senza perdite rilevanti in termini qualità.
Tuttavia, i team di sviluppo di prodotto spesso trascurano il fatto che la colata sottovuoto rappresenta in molti casi una soluzione più efficiente per colmare la distanza tra le fasi di prototipazione e produzione. Tra tutti i metodi di prototipazione iniziali, la fusione in resina è quello che più assomiglia allo stampaggio a iniezione e per di più è molto conveniente: gli stampi costano tra i 200 e i 1000 € e il prezzo standard per unità va dai 10 ai 100 €.
Uno stampo in silicone per la colata di uretano viene realizzato in modo simile a uno stampo a iniezione, infatti è anch'esso costituito da due metà: una che forma il nucleo e l'altra la cavità, mentre il materiale liquefatto viene iniettato tra le due per formare il prodotto finale. Esistono però alcune differenze:
-
Nello stampaggio a iniezione, il polimero fuso viene spinto nella cavità dello stampo a pressione e temperatura elevate utilizzando un serbatoio e una vite di movimentazione. La colata sottovuoto è invece un processo a basse temperature che non utilizza plastica fusa, bensì resine liquide che vengono aspirate nello stampo per azione del vuoto, in modo simile all'azione capillare che avviene nello stelo di una pianta. Perciò, sebbene esistano molte resine diverse che simulano vari polimeri, la prototipazione con il materiale stampato a iniezione finale è impossibile.
-
Dopo la polimerizzazione in forno, le parti devono essere sottoposte a polimerizzazione post-stampa per circa una settimana e rimanere vulnerabili ai raggi UV e alle alte temperature.
-
Nonostante la flessibilità dello stampo comporti alcune limitazioni in termini di dimensioni e forma della parte, esistono alcune tecniche specifiche che offrono soluzioni alternative. Ad esempio, la fusione per fasi è l'utilizzo di supporti metallici che permette di contrastare la gravità durante la fusione di parti allungate all'interno di uno stampo di tre o quattro componenti.
-
Grazie all'assenza del ciclo di riscaldamento-raffreddamento del materiale, la colata sottovuoto gestisce lo spessore variabile delle pareti in modo migliore rispetto allo stampaggio a iniezione. Il risultato è una minore deformazione della parte.
-
Uno stampo in silicone consente di includere un numero significativo di sottosquadri nel design della parte. Tuttavia, quando si testa lo stampaggio a iniezione, si consiglia di attenersi il più possibile al design stampato a iniezione e di aggiungere gli angoli di sformo richiesti per il prodotto finale.
-
La colata sottovuoto consente di ridurre al minimo gli sprechi, mentre nello stampaggio a iniezione si perde fino al 20% del polimero usato per via degli scarti, dei residui e della sovrapproduzione.
Un modello realizzato tramite colata sottovuoto risulta estremamente fedele a un prodotto finale ottenuto da uno stampo a iniezione. Di conseguenza, poiché rappresenta un'anteprima di alta qualità del prodotto, i team di ingegneria possono ottimizzare il design per la produzione, così la dirigenza non dovrà sostenere i costi astronomici tipici della produzione a contratto in uno stabilimento di stampaggio a iniezione.
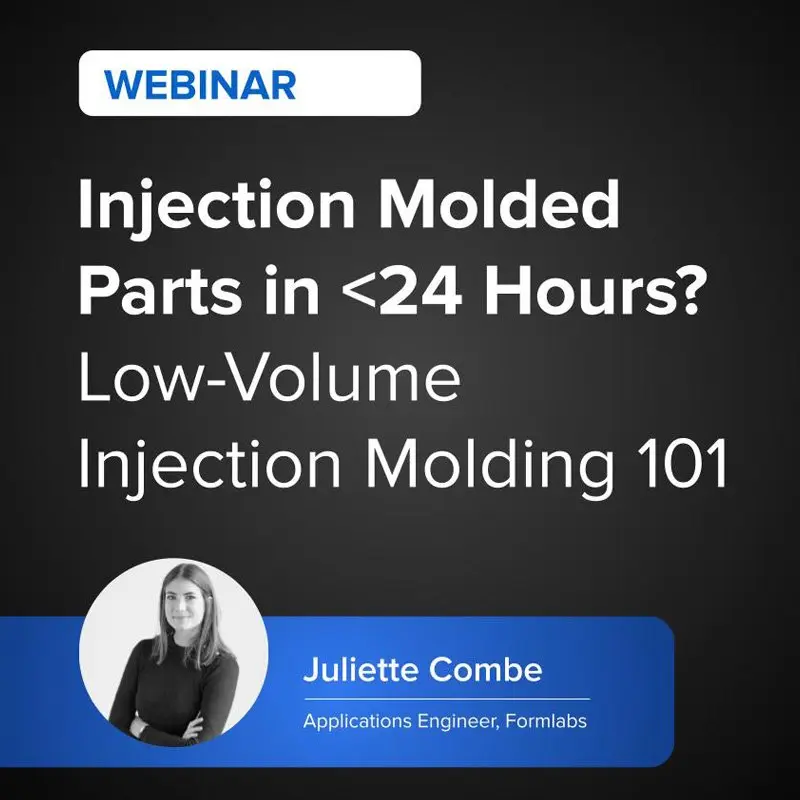
Parti stampate a iniezione in meno di 24 ore? Introduzione allo stampaggio a iniezione per volumi ridotti
In questo webinar illustreremo come utilizzare la stampa 3D stereolitografica nel processo di stampaggio a iniezione, al fine di abbattere i costi, ridurre i tempi di produzione e portare sul mercato prodotti migliori.
Colata sottovuoto e stampa 3D
It is a common misunderstanding that 3D printing is restricted to one-offs only. On the contrary, it is a viable method for low volume manufacturing of end-use parts. It is also increasingly popular for companies to invest in an in-house print farm. Such an array of 3D printers can handle low-volume batches of hundreds or even thousands of products.
The main factor influencing a choice between 3D printing and vacuum casting is product geometry. Vacuum casting is explicitly intended to simulate injection-molded parts. As a low-investment alternative to full-scale injection molding, it can even combine flexible and rigid materials in an overmold or add metal components directly in the prototype through insert molding. For creating a small series of injection-moldable components, vacuum casting is more cost-effective than 3D printing.
Another advantage of vacuum casting is that bigger parts can be created much faster and cheaper than 3D printing. It allows for mold sizes of roughly 50 cm (20 inches) for the longest dimension, and casting weight up to 1.5kg (3.3 lbs).
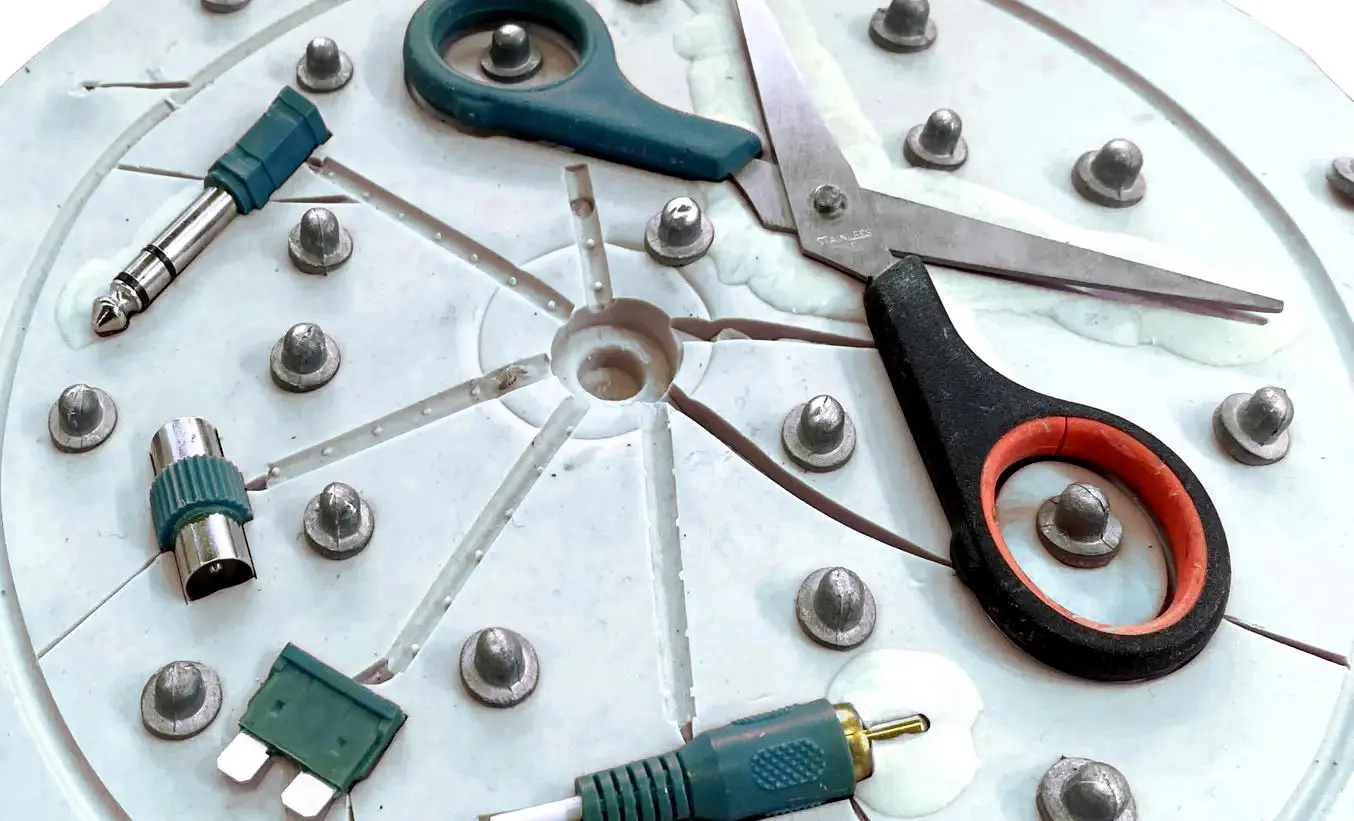
Colata sottovuoto in uno stampo in silicone con inserti metallici.
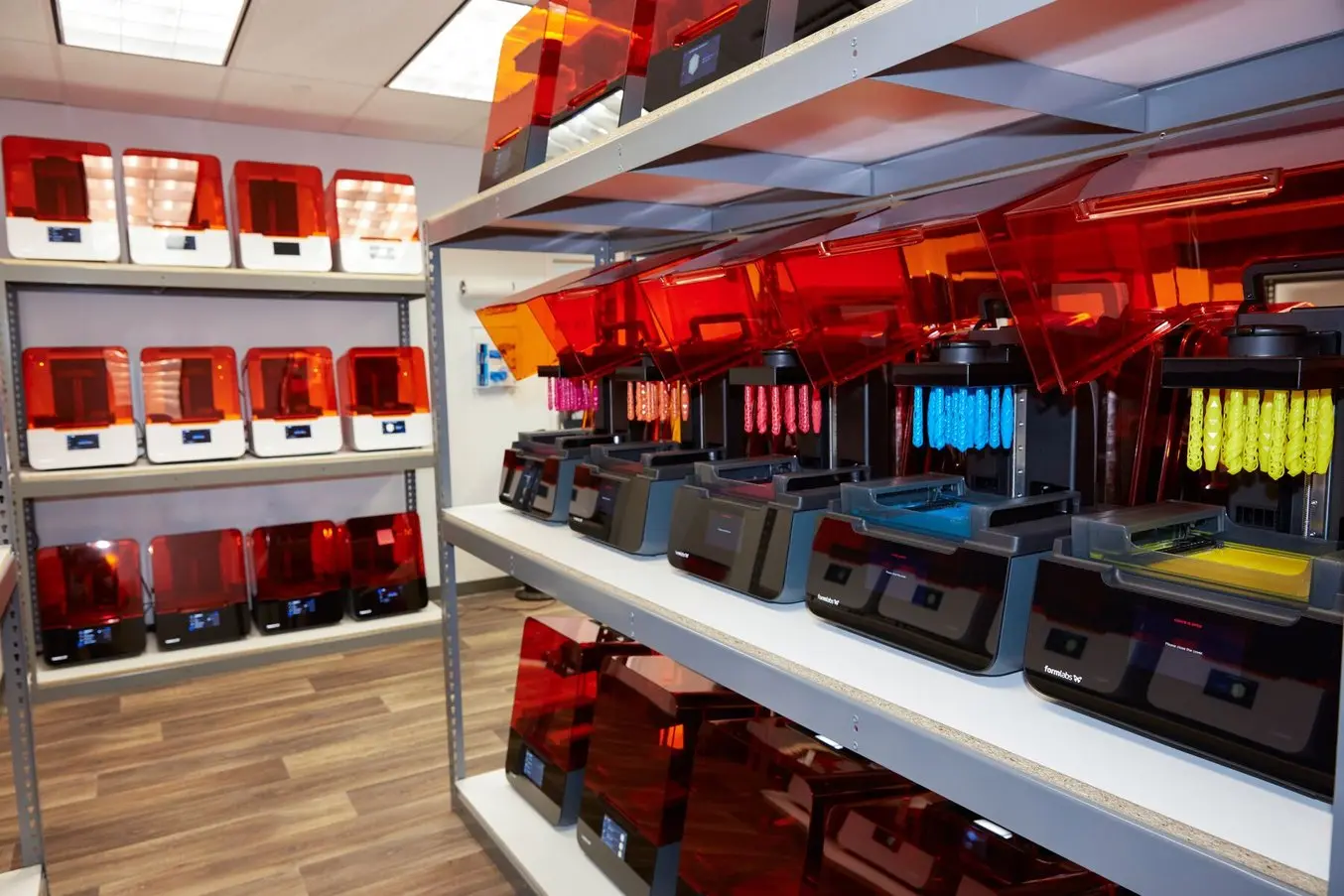
Come ottenere produzione a basso volume e personalizzata grazie a parti per utilizzo finale stampate in 3D
Guarda questo webinar per scoprire come produrre parti per utilizzo finale personalizzate in volumi ridotti in modo rapido e conveniente grazie alla stampa 3D.
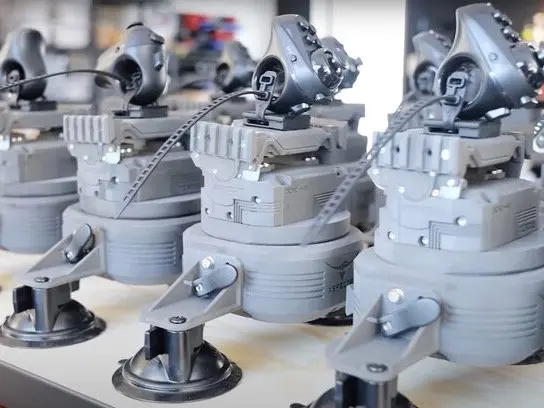
Test di resistenza su parti stampate in 3D per applicazioni per utilizzo finale
In questo whitepaper vengono illustrate le soluzioni di Formlabs in ambito di hardware e materiali per la stampa 3D di parti per utilizzo finale. Inoltre, vengono presentati casi di studio e risultati di test di resistenza eseguiti per verificare l'idoneità dei materiali di stampa 3D ad applicazioni per utilizzo finale.
Colata sottovuoto e metodi di produzione alternativi
Analizziamo pregi e difetti di alcune tecniche di produzione.
Colata sottovuoto | Stampaggio a iniezione | Stampa 3D | Creazione rapida di attrezzature | Lavorazione meccanica | Produzione manuale | ||
---|---|---|---|---|---|---|---|
Libertà di design | ★★★☆☆ | ★★☆☆☆ | ★★★★★ | ★★☆☆☆ | ★★★★☆ | ★★★☆☆ | |
Dimensioni della parte | ★★★★☆ | ★★★★☆ | ★★★☆☆ | ★★★☆☆ | ★★★★☆ | ★★★★★ | |
Rendimento | ★★★☆☆ | ★★★★★ | ★★★☆☆ | ★★★★☆ | ★★☆☆☆ | ★☆☆☆☆ | |
Gamma di materiali | ★★★☆☆ | ★★★★☆ | ★★★★☆ | ★★★★☆ | ★★★★★ | ★★★☆☆ | |
Costi di investimento | ★★★☆☆ | ★☆☆☆☆ | ★★★☆☆ | ★★☆☆☆ | ★★★★★ | ★★☆☆☆ | |
Costo per parte | ★★★★☆ | ★★★★★ | ★★★☆☆ | ★★★★☆ | ★★★☆☆ | ★★★☆☆ | |
Tempo di realizzazione | ★★★★☆ | ★☆☆☆☆ | ★★★★★ | ★★★☆☆ | ★★★★☆ | ★★☆☆☆ |
Processo di colata sottovuoto
La colata sottovuoto è una procedura altamente specialistica che prevede quattro passaggi.
1. Progettazione CAD
Il team di design o ingegneria crea una rappresentazione digitale dell'oggetto da produrre utilizzando un software CAD come Fusion 360 o SolidWorks. Per la colata di uretano è necessario considerare le seguenti linee guida di progettazione:
-
Lo spessore delle pareti deve essere compreso tra 1,5 e 4 mm. Lo spessore minimo assoluto è di 1 mm.
-
I rinforzi possono essere più sottili, con uno spessore pari al 60% di quello delle pareti.
-
Utilizza raggi >3 mm.
-
Evita pareti a 90 gradi per migliorare la resistenza della parte.
-
Per migliorare l'aspetto del prodotto, includi un solco di 0,5 mm tra due metà da assemblare.
-
Lo spessore delle pareti del foro di estrusione deve corrispondere al diametro del foro.
-
La profondità consigliata per le lettere incise è di 0,25 mm.
Una volta completato, il file CAD viene esportato in formato STL per produrre il modello.
2. Realizzazione del modello master
Il modello master è il modello positivo dal quale verranno realizzate le copie tramite colata. Poiché lo stampo in silicone per la colata sottovuoto rappresenta una replica esatta del modello master, è fondamentale che il modello stampato in 3D riproduca fedelmente il modello CAD originale, specialmente per quanto riguarda la finitura superficiale estremamente liscia. Alcune caratteristiche secondarie di un buon modello master sono durezza, robustezza e resistenza ad agenti chimici, alte temperature e usura.
In passato lo standard era usare modelli master realizzati tramite fresatura CNC, che però sono costosi, richiedono lunghi tempi di produzione e presentano alcune limitazioni legate a fori, canali, raggi interni e superfici organiche. La stampa 3D è un'alternativa all'avanguardia e attualmente il metodo più diffuso per produrre modelli master.
Sebbene siano disponibili diversi tipi di stampanti 3D sia per i clienti ordinari che per quelli commerciali, i processi più utilizzati per la colata di uretano sono la stampa 3D SLA e SLS.
La stampa 3D SLA consente di produrre parti con una finitura superficiale estremamente liscia, per questo è ideale per la colata sottovuoto di modelli. Con le corrette impostazioni di stampa è possibile ottenere parti SLA che presentano già una finitura superficiale liscia. Gli unici sforzi richiesti sono la sabbiatura e la lucidatura per rimuovere i supporti e ottenere una finitura superficiale impeccabile. Alcuni materiali avanzati come la Rigid 10K Resin offrono anche proprietà meccaniche straordinarie, resistenza alle alte temperature e robustezza.
La stampa 3D SLS con nylon consente di ottenere stampe robuste, precise e resistenti alle alte temperature. Il fatto che non richieda supporti la rende ideale anche per dettagli intricati come pareti sottili, particolari incisi, accoppiamenti a scatto, cerniere e parti nidificate o a incastro. Le parti stampate in 3D tramite SLS presentano una finitura superficiale eccessivamente ruvida per la stampa di modelli master adatti alla colata di uretano; per migliorare questo aspetto, è possibile sottoporle a sabbiatura o burattatura.
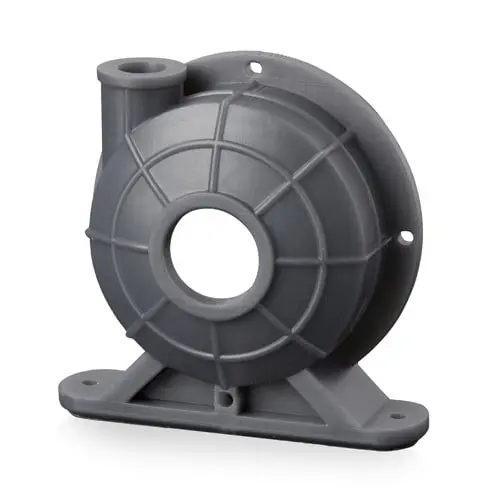
Richiedi un campione gratuito
Guarda e tocca con mano la qualità di Formlabs. Saremo lieti di inviare presso la tua azienda un campione gratuito.
3. Realizzazione dello stampo
Questa è la fase più complessa del processo, in cui viene creato un telaio di gettata utilizzando pannelli in melammina e colla a caldo. Successivamente il modello master viene fissato con piccole gocce di colla cianoacrilica. In alcuni casi, per un maggiore fissaggio, vengono create delle fessure con uno strumento rotante, in cui si inseriranno le linguette sporgenti presenti sul modello master.
Per ottenere una linea di separazione ridotta tra le due metà dello stampo, è necessario chiudere qualsiasi foro tra il modello master e il pannello inferiore. I materiali preferiti per questa operazione sono polimeri a blocchi di stirene e pasta da modellare Plastalina. In seguito vengono aggiunti perni e barrette di allineamento per ottenere una perfetta corrispondenza con l'altra metà dello stampo.
Il passaggio successivo consiste nella miscelazione del silicone bicomponente, che verrà poi versato e degassato all'interno di una camera sottovuoto. Ma prima, per evitare che rimanga aria intrappolata all'interno del modello master, è necessario riempire accuratamente tutti i piccoli spazi del modello con la miscela di silicone utilizzando un pennello per acido. Al termine di questa operazione, si può procedere a versare il silicone per formare la prima metà dello stampo.
Dopo diverse ore di polimerizzazione, lo stampo viene rimosso dal telaio di gettata e capovolto. Vengono quindi installati perni di sfiato in acrilico, cannucce di controllo e un canale di colata per la seconda metà del processo. Un agente distaccante viene spruzzato sopra il silicone e applicato con un pennello nelle aree più profonde. Infine, viene costruito un nuovo telaio simile al primo per la colata della seconda metà dello stampo.
Per preparare lo stampo per la colata sottovuoto, è necessario rimuoverlo dal telaio di gettata e spruzzare uno strato uniforme di agente distaccante E236 per materiali uretanici. A questo punto bisogna nuovamente assemblare le due metà dello stampo per formare un unico blocco. Affinché combacino perfettamente, è necessario reinserire i perni e le barrette di allineamento.
4. Colata di uretano sottovuoto
In questo passaggio, il modello master originale viene replicato tramite colata in una camera sottovuoto. In primo luogo, lo stampo viene fissato con nastro adesivo a un pannello in legno, dopo di che vengono aggiunti sfiati e un imbuto di colata.
La resina bicomponente viene misurata e miscelata con un agente colorante per la pigmentazione. In seguito, il materiale di colata viene degassato in una camera sottovuoto per alcuni minuti.
La miscela poliuretanica è finalmente pronta per la colata. Le cannucce di controllo indicheranno i punti in cui la cavità si è completamente riempita. Dopo aver lasciato polimerizzare a 70 ˚C, lo stampo viene aperto. Al suo interno sarà presente una copia esatta del modello originale, con dettagli e finitura superficiale perfettamente riprodotti.
I passaggi finali consistono nella rifilatura del materiale in eccesso in corrispondenza dei bordi, un ulteriore ciclo di lucidatura utilizzando carta abrasiva con grana 1000 e polimerizzazione in forno per migliorare le proprietà del materiale della parte.
Consigli professionali
La procedura descritta è particolarmente indicata per prototipi con pareti sottili, come alloggiamenti per componenti elettronici, recipienti per la conservazione e altri casi in cui si desidera evitare una linea di separazione visibile sulla superficie principale del prodotto.
Per altri articoli in cui questo aspetto è meno importante, è sufficiente incapsulare il modello master in un blocco di silicone e tagliarlo manualmente per aprirlo. Il taglio viene effettuato seguendo un'onda sinusoidale, il che richiede una certa esperienza e manualità.
Di seguito sono presentate alcune buone pratiche per eseguire al meglio la colata di uretano:
-
Fai attenzione quando spruzzi l'agente distaccante direttamente sul modello, poiché rischia di penetrare in una piccola area superficiale che sarà poi visibile nella colata.
-
Preriscalda le resine a 40 ˚C, preferibilmente un giorno prima dell'utilizzo, e di tanto in tanto capovolgi il flacone per impedire la cristallizzazione.
-
Previeni infiltrazioni di umidità nei flaconi di resina, poiché potrebbero far espandere il poliuretano. Per evitarlo, riempi i flaconi con gas di argon immediatamente dopo l'uso.
-
Quando misceli sostanze chimiche bicomponenti, utilizza sempre il metodo di miscelazione con due contenitori. Se si versa la miscela direttamente dal primo contenitore, i componenti potrebbero non essere ben miscelati tra loro e creare striature, rovinando la colata.
-
Utilizza alcool per frizioni per ammorbidire la colla a caldo durante lo smontaggio del telaio di gettata per un utilizzo futuro.
-
Per garantire il riempimento di tutte le aree, posiziona il canale di colata in un angolo del prodotto che presenta la minore distanza media dalle diverse sezioni della parte.
-
Per impedire la formazione di bolle d'aria, versa da un singolo punto e intorno alle aree delicate con molti dettagli. Non versare mai il materiale direttamente sopra di esse.
-
Posiziona il punto di iniezione in basso e lo sfiato in alto.
-
Aggiungi polveri metalliche per ottenere una finitura superficiale dall'aspetto vivace, altrimenti considera una polvere di polipirrolo o grafite per la conduttività elettrica.
-
Durante la miscelazione dell'uretano, lascia abbondante spazio libero al di sopra della superficie della miscela liquida, la quale diventerà schiumosa e si espanderà all'interno della camera sottovuoto, come un marshmallow in un forno a microonde.
-
Utilizza un apparecchio per la colata sottovuoto professionale per velocizzare il processo e ottenere risultati più affidabili.
Apparecchi per la colata sottovuoto
Due to the complexity of the process, most companies subcontract jobs to third-party urethane casting service providers.
For those planning to do vacuum casting in house, a professional vacuum casting machine provides an integral solution for taking prototyping efforts to the next level and speeding up the process towards production ramp-up. As much as fifty castings can be achieved within two days, each in a different material and color if needed.
A vacuum resin casting machine is a refrigerator-sized contraption that automates the process from mixing to casting to curing. It lets operators control parameters such as chamber pressurization, mixer speed, heated cup, and oven heat. The latest systems are programmable so that operators can create custom sequences to optimize casting cycles for specific materials and product types.
Vacuum casting machines come in different sizes to allow for different mold sizes. Most models can, next to working with resin, also be set up for casting injection-grade nylon, ceramics, wax, and even low-melt metal alloys.
Urethane casting machines are ideal for pre-production runs because they pull a vacuum much quicker and minimize manual labor. The downside is that they cost tens of thousands of dollars. Jewelry vacuum casting machines are much smaller and generally cost a few thousand dollars.
Here are some of the best vacuum casting machines:
-
Renishaw 5/01 PLC: Max. mold size 530 x 450 x 420 mm, price roughly $45k. The larger 5/04 model allows molds up to 750 x 750 x 900 mm and more materials, like glass-fiber reinforced nylon and wax, but it comes at nearly double the price.
-
SLM VCM 04: Max. mold size 750 x 750 x 900 mm, casting volume 2.2L, and includes casting with nylon and wax.
-
MCP 5/01: Max. part size 400 x 400 x 400 mm. MCP offers many larger models, including the MCP 003 with 560 x 600 x 600 mm part size, the 4/04 with 900 x 750 x 600 mm part size, and the 4/05 with 1300 x 750 x 800 mm part size. These machines are fully programmable and allow vario-pressure casting with wax, silicone, and nylon, next to PU resins. They can also be used with 3D printed injection molds.
-
Scott AM 1000: Max. mold size 500 x 450 x 425 mm, 1 kg casting weight. The 4000 model has a max. mold size of 750 x 750 x 900 mm and 5 kg casting weight. Besides resins, these apparatuses can be used for vacuum investment casting with ceramics and metals.
-
Multistation CSV 340: Max. mold size 340 x 340 x 435 mm, casting volume 600 mL. The CSV500 model fits molds up to 500 x 500 x 635 mm and casting volumes up to 1 liter.
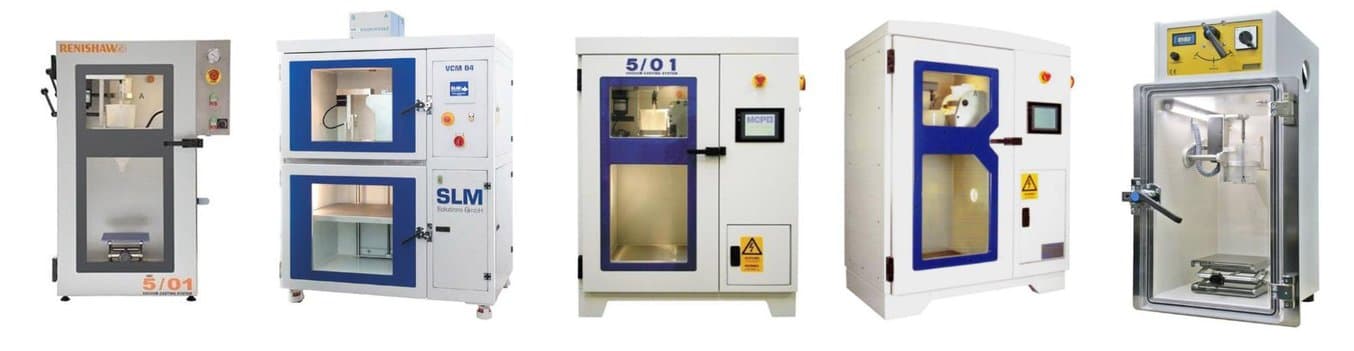
Apparecchi per la colata sottovuoto di Renishaw, SLM, MCP, Scott AM e Multistation.
Apparecchi per la colata sottovuoto e camere a pressione
Per un'alternativa economica, è possibile costruire un apparecchio per la colata sottovuoto in gravità fai da te. Poiché una singola bolla d'aria intrappolata nello stampo può rovinare l'intera colata, il degassamento è un passaggio fondamentale del processo di fusione in resina.
Esistono due strategie principali per eliminare tutte le bolle dalla miscela quando si utilizza un apparecchio per la colata sottovuoto fai da te: una camera sottovuoto o una pentola a pressione.
Una camera sottovuoto è una vasca che può essere usata per rimuovere l'aria dalla gomma siliconica prima della creazione dello stampo. Poiché l'approccio di creazione del sottovuoto è più lento rispetto all'approccio ad alta pressione, una camera sottovuoto funziona solo con resine a polimerizzazione lenta (venti minuti o più).
Una camera sottovuoto include due leve, una per l'ingresso di aria e l'altra per la pompa da vuoto, un manometro per verificare se è stato raggiunto il vuoto e un coperchio in acrilico trasparente per verificare lo stato di degassificazione. Può valere la pena di sostituire il coperchio in plastica con uno di vetro temperato: nonostante costi di più, non svilupperà crepe a lungo termine.
Le pentole a pressione sono leggermente più costose perché richiedono un compressore ad aria, ma sono senza dubbio la soluzione migliore per creare miscele e colate prive di bolle d'aria. A differenza delle camere sottovuoto, possono essere usate con lo stampo, sono compatibili con resine a polimerizzazione rapida e le colate risultano completamente prive di aria intrappolata.
Una camera sottovuoto ha il vantaggio di essere utile per molte applicazioni, ad esempio nella deaerazione delle infusioni di gesso, calcestruzzo o legno, mentre una pentola a pressione può essere utilizzata soltanto per degassare il silicone.
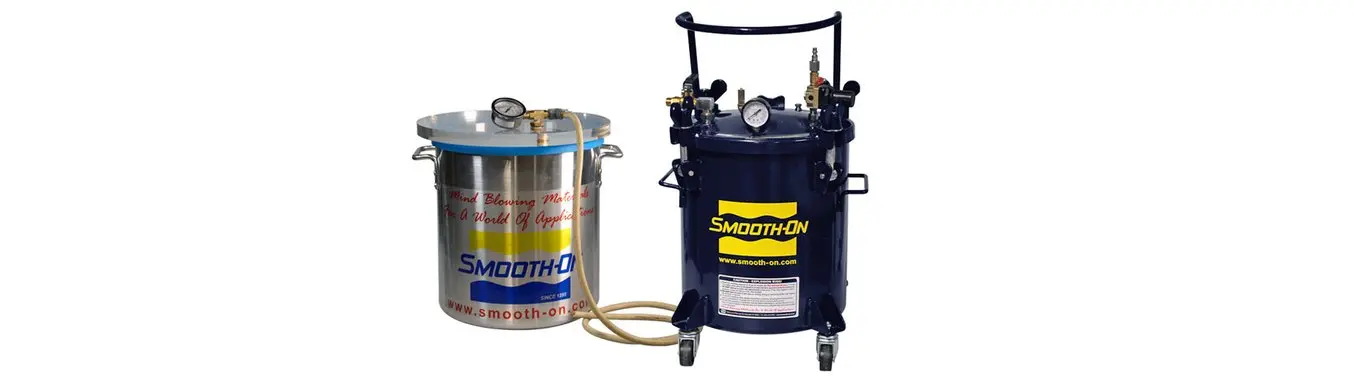
Camera sottovuoto (a sinistra) e pentola a pressione (a destra).
Materiali per la colata sottovuoto
Materiali per stampi in silicone
I siliconi per la fusione possono essere suddivisi in siliconi polimerizzati con stagno e siliconi polimerizzati con platino. I primi, che vengono polimerizzati per condensazione, subiscono un restringimento compreso tra l'1 e il 4%. Sebbene i modellisti facciano del loro meglio per compensare questo fenomeno, nel caso di applicazioni ad alta tolleranza è più indicato scegliere materiali di maggiore qualità, come il silicone polimerizzato con platino o gomme HTV.
Una durezza Shore A pari a 40-50 consente di realizzare uno stampo resistente e riutilizzabile decine di volte e agevolare la rimozione delle parti, incluse quelle che rischierebbero di rimanere bloccate in uno stampo rigido a causa di problemi di backdraft (ovvero, una rastremazione nel senso opposto rispetto a quello di rimozione). L'utilizzo di un silicone semitrasparente è consigliato in quanto fornisce visibilità su aria intrappolata, bolle, elementi contaminanti e qualsiasi altro residuo presente all'interno dello stampo.
Alcuni ottimi marchi di silicone bicomponente sono SmoothOn, Elastosil, V-Sure e Silicones and More (S.A.M.). La soluzione ideale, soprattutto nel caso di grandi quantitativi, è effettuare l'ordine direttamente da fabbriche chimiche estere. Così facendo si possono ottenere a prezzi ridotti prodotti di qualità professionale che rispondono a requisiti specifici.
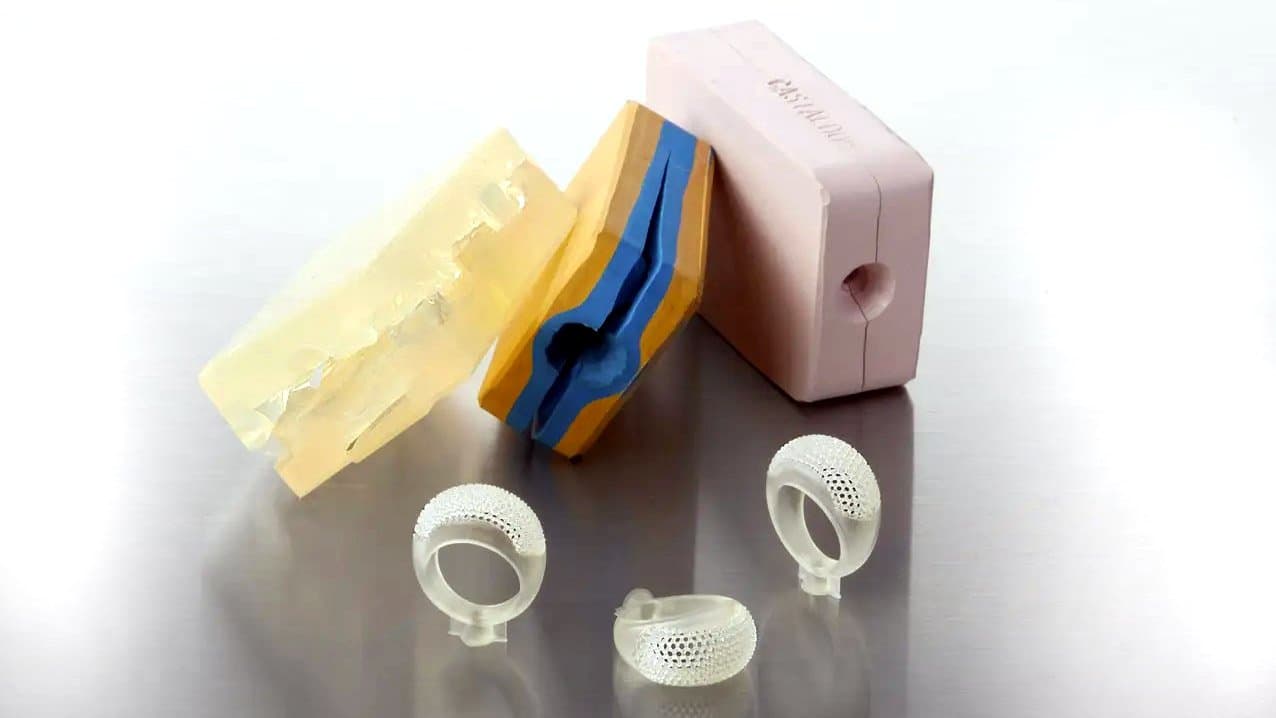
Gli stampi per gioielli in silicone RTV e HTV sono in grado di catturare le filigrane più sottili, per questo vengono utilizzati nel settore della gioielleria.
Resine uretaniche per la fusione
Esistono numerosi materiali adatti alla colata sottovuoto, ciascuno con diverse proprietà in termini di flessibilità, elasticità, rigidità e durezza:
-
Resine standard simili all'ABS per utilizzi generici
-
Materiali simili al nylon rinforzato con vetro per una maggiore rigidità
-
Materiali elastomerici simili all'elastomero termoplastico per applicazioni come dispositivi indossabili, impugnature, pulsanti e guarnizioni
-
Materiali simili al policarbonato
-
Uretano semitrasparente o trasparente per la colata (simile all'acrilico)
-
Materiali termoresistenti simili al poliossimetilene o al poliuretano
Per la colata di uretano sono anche disponibili alcuni materiali insoliti, tra cui vetro scenico, cera, resina epossidica, ceramica, compositi, nonché opzioni per uso alimentare, conduttive, a bassa densità e ignifughe. Alcuni marchi noti sono FastCast (resina per colata di uretano), Smooth-On e la Specialty Resin di SRC.
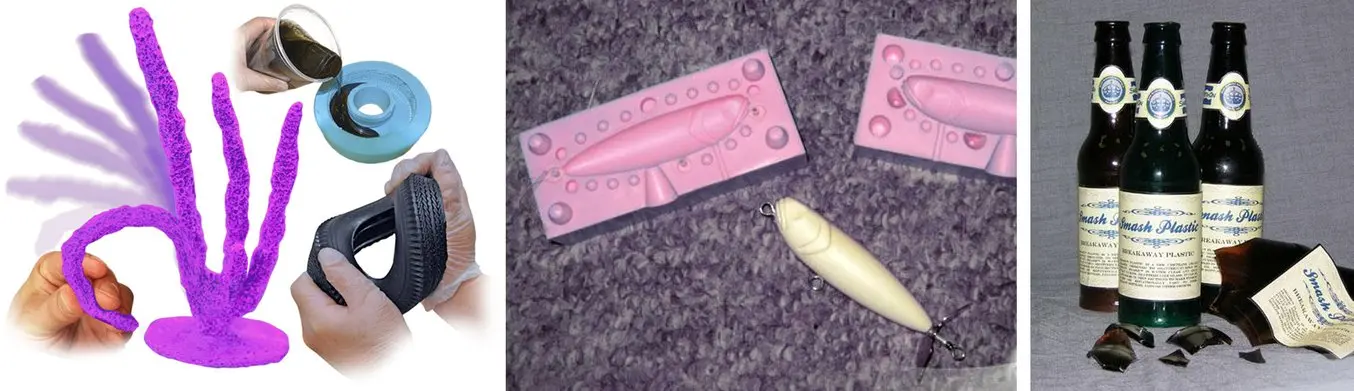
Un assortimento di resine uretaniche, da quelle simili alla gomma fino a quelle galleggianti o simili al vetro.
Casi di studio: colata di uretano con modelli stampati in 3D
Calibur Fencing
La colata sottovuoto è ideale per i cicli pre-produzione, in quanto consente di testare e modificare il prodotto finale prima di investire in attrezzature di stampaggio a iniezione per la produzione di massa. Una storia di successo è quella di Calibur Fencing, un dispositivo indossabile wireless che serve a tenere il punteggio durante gli incontri di scherma.
Il team di design è partito da semplici prototipi per testare la funzionalità del dispositivo, dopo di che è passato alla stampa a modellazione a deposizione fusa (FDM) per realizzare delle riproduzioni che consentissero di trovare la forma corretta. Infine, grazie a una stampante SLA Form 3 di Formlabs, ha creato prototipi di alta qualità rappresentativi del prodotto finale.
Il team ha quindi utilizzato le parti stampate in 3D tramite SLA come modelli e le ha inviate a un fornitore di servizi di colata sottovuoto per produrre le unità e sottoporle ai beta test. In questo modo ha potuto sviluppare rapidamente un prodotto finale mantenendo sempre un perfetto controllo della qualità.
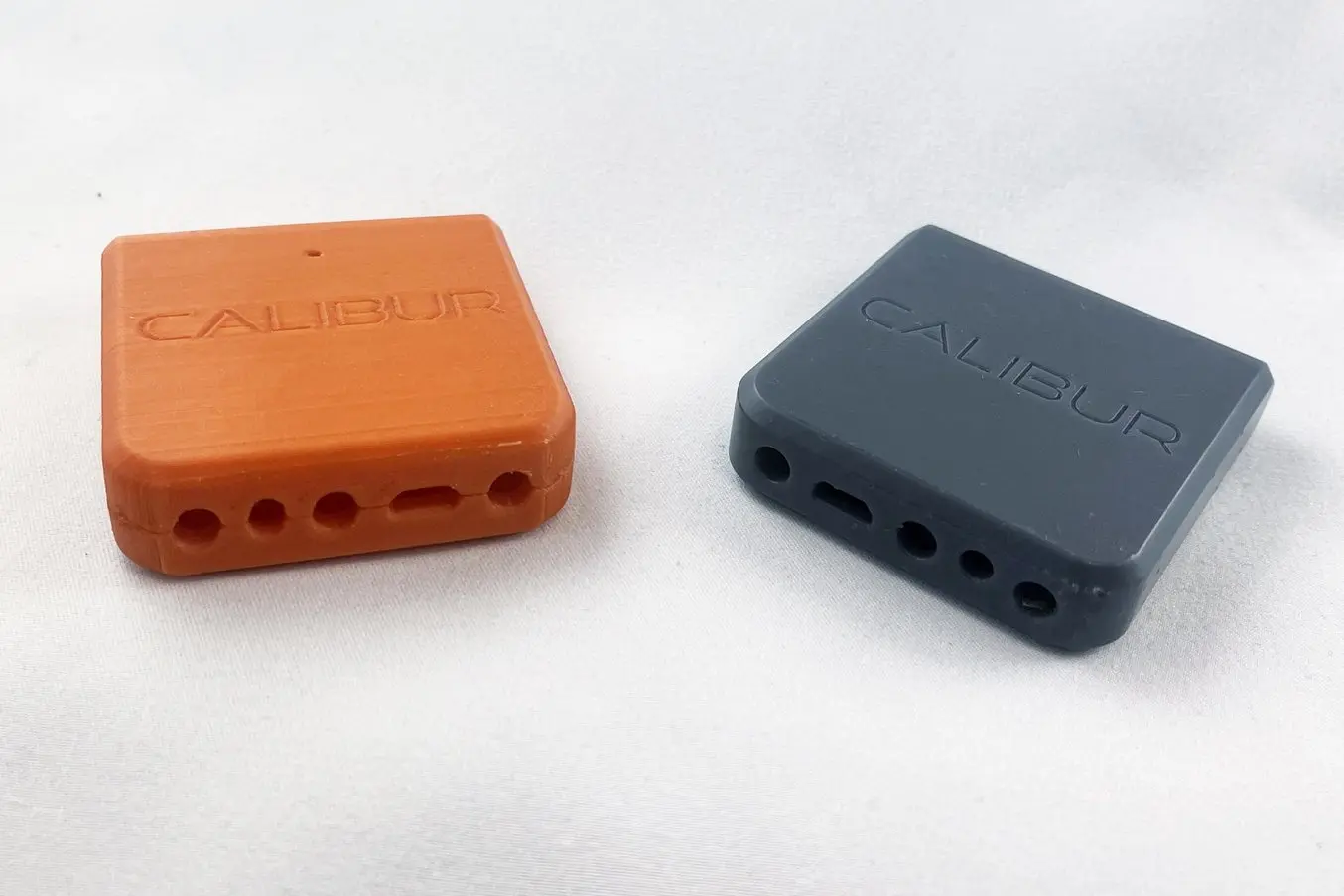
Il team di Calibur ha usato la stampa 3D FDM per le prime riproduzioni e in seguito è passato alla stampa 3D SLA per ottenere prototipi funzionali realistici.
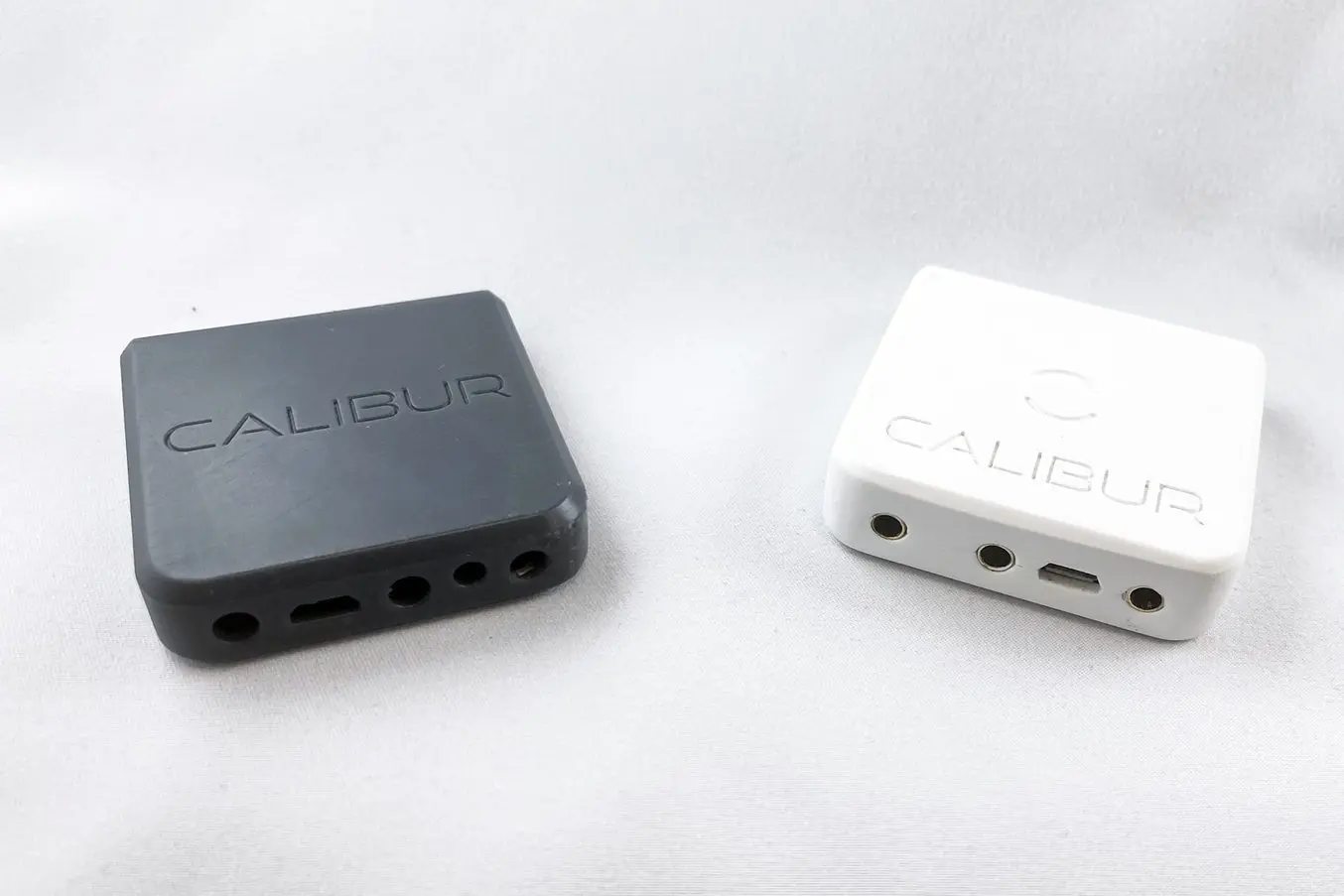
Il team ha poi usato le parti stampate in 3D tramite SLA come modelli per la colata sottovuoto della prima piccola serie di unità di prova per utilizzo finale.
Louisville Slugger
Il team del centro di innovazione di Louisville Slugger ha scoperto che anche i piccoli dettagli possono fare una grande differenza. L'azienda, fondata nel 1884 e specializzata nella produzione di mazze da baseball, conosce tutti i fattori che contribuiscono a una battuta veloce e potente.
Il personale dei centri di innovazione di Slugger ha mantenuto un approccio analitico al design sportivo, e con l'ausilio delle soluzioni di stampa 3D di Formlabs ha creato un accessorio per migliorare la presa della mazza. La geometria a gradini aiuta i giocatori a ottenere la massima stabilità durante la battuta grazie a una presa perfetta.
Come in altri casi, il team di progettazione di Slugger ha scoperto che avere a disposizione sia apparecchi di stampa 3D che apparecchi per la colata sottovuoto all'interno della stessa struttura permette di velocizzare le iterazioni di design e al contempo acquisire nuove conoscenze. Utilizzando una stampante SLA Form 3 con spessore dello strato di 50 μm sono stati realizzati modelli di prototipi dettagliati, successivamente utilizzati per creare uno stampo positivo. Sfruttare la colata di uretano ha permesso al team di creare modelli resistenti adatti ai test, di qualità simile a quella del prodotto finale stampato a iniezione in silicone.
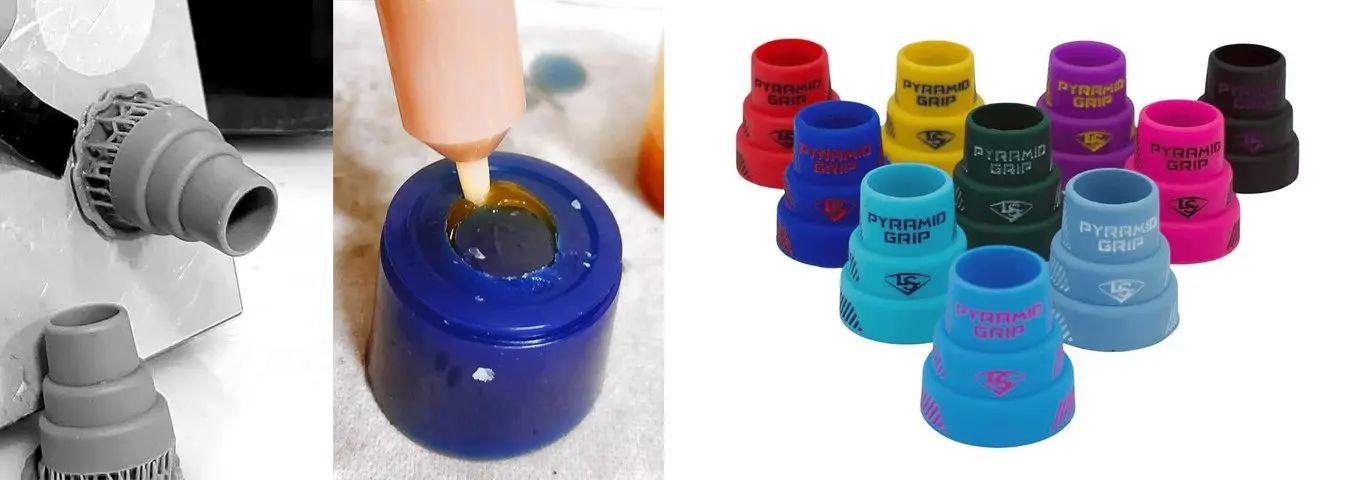
Dal modello positivo stampato in 3D alla fusione in-house, fino al prodotto finito.
SiOCAST
SiOCAST è protagonista di una storia unica che riguarda l'integrazione tra stampa 3D e fusione in resina. Grazie al successo dei giochi online MMORPG e dei giochi di ruolo, si è verificata una rapida crescita della domanda di miniature personalizzate. Anziché ricorrere alla costosa fusione in centrifuga o alla produzione di serie limitate con stampi in silicone realizzati tramite colata sottovuoto, l'azienda ha creato un sistema brevettato di iniezione di resina compatibile con un apparecchio sviluppato in modo individuale e stampi in gomma HTV.
SiOres, il suo materiale brevettato, può essere utilizzato anche con resine termoplastiche fuse fino a 240 ˚C. Un apparecchio SiOCAST ha una velocità pari a 20 volte quella della fusione in resina tradizionale e può produrre 1000 parti all'ora in modo automatico e con stampi multicavità rotanti.
Tutti i modelli master vengono stampati in 3D usando una stampante SLA e sottoposti a post-elaborazione con i sistemi di pulizia e polimerizzazione avanzata di Formlabs, ovvero la Form Wash e la Form Cure. Grazie a canali riutilizzabili prodotti con la stampa 3D SLS, il processo diventa ancora più veloce, arrivando a creare 64 miniature per colata.
Mentre lo stampaggio a iniezione introduce errori occasionali dovuti ai materiali viscosi e alle condizioni di processo più critiche, questi modelli realizzati tramite colata sottovuoto rappresentano sempre repliche impeccabili della scultura originale e sono molto apprezzati dalle comunità di gamer.
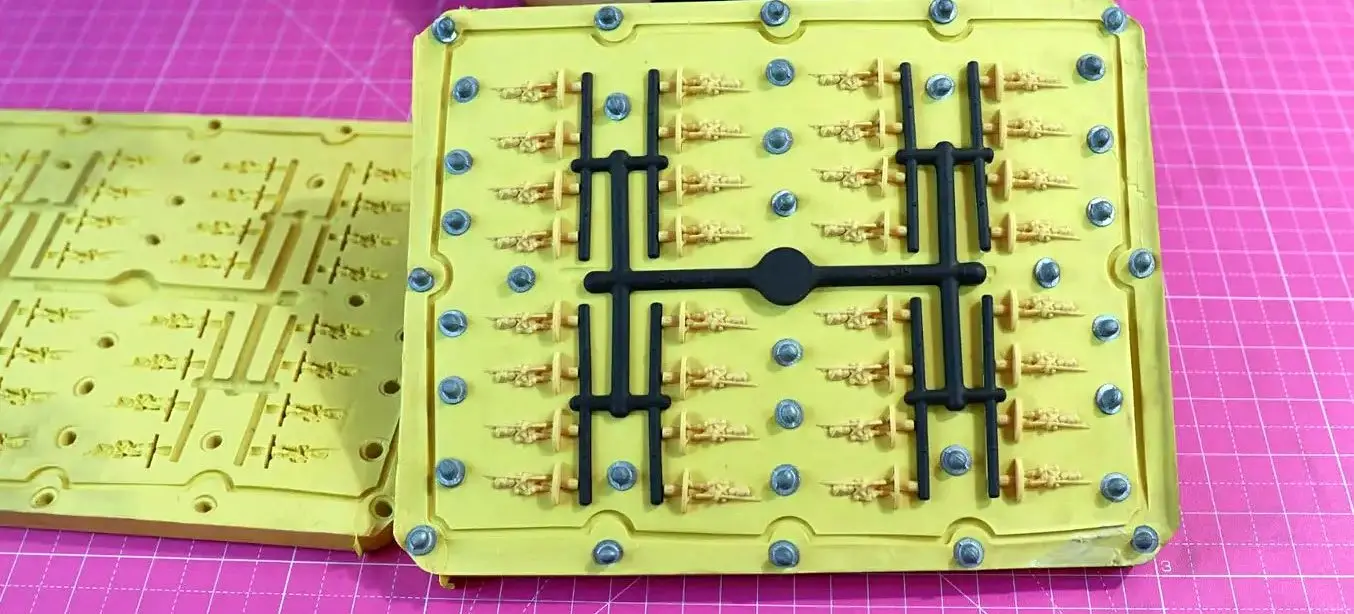
SiOCAST, utilizzando un silicone HTV brevettato, modelli master realizzati tramite SLA e canali in nylon riutilizzabili ottenuti tramite SLS, produce in serie fino a 10 000 duplicati di miniature.
Inizia a usare colata sottovuoto e stampa 3D
La colata sottovuoto è un processo ideale per lo stampaggio di prodotti senza i costosi investimenti iniziali richiesti dai metodi di produzione industriali. Può essere utilizzata per creare prototipi, modelli estetici, serie pre-produzione, nonché prodotti finali per un'ampia gamma di applicazioni. Il modello ottenuto dalla colata sarà una replica esatta del modello master, a condizione che la geometria del prodotto consenta la rimozione dallo stampo e rispetti le linee guida di progettazione specifiche della colata sottovuoto.
Inoltre, la colata sottovuoto trae vantaggio dai nuovi progressi della stampa 3D. Ad esempio, la capacità della stampa 3D di creare modelli master estremamente dettagliati con una finitura superficiale perfettamente liscia la rende il complemento ideale del processo di colata sottovuoto.
Tuttavia, a differenza della stampa 3D, la colata sottovuoto fai da te non è facile da eseguire in-house e richiede procedure rigorose. La stampa 3D, grazie alla sua alta precisione, al workflow semplice e ai brevi tempi di realizzazione, rappresenta inoltre una valida alternativa alla colata sottovuoto non solo per la prototipazione, ma anche per la produzione in volumi ridotti.