Supercharge Your Manufacturing Tools With 3D Printed Rapid Tooling
Accelerate product development, iterate quickly, and bring better products to market by incorporating 3D printed rapid tooling into your development process. Rapid tooling enables you to validate your design and material choice prior to transitioning to mass production, or alternatively provides an affordable means to produce custom or limited series of end-use parts.
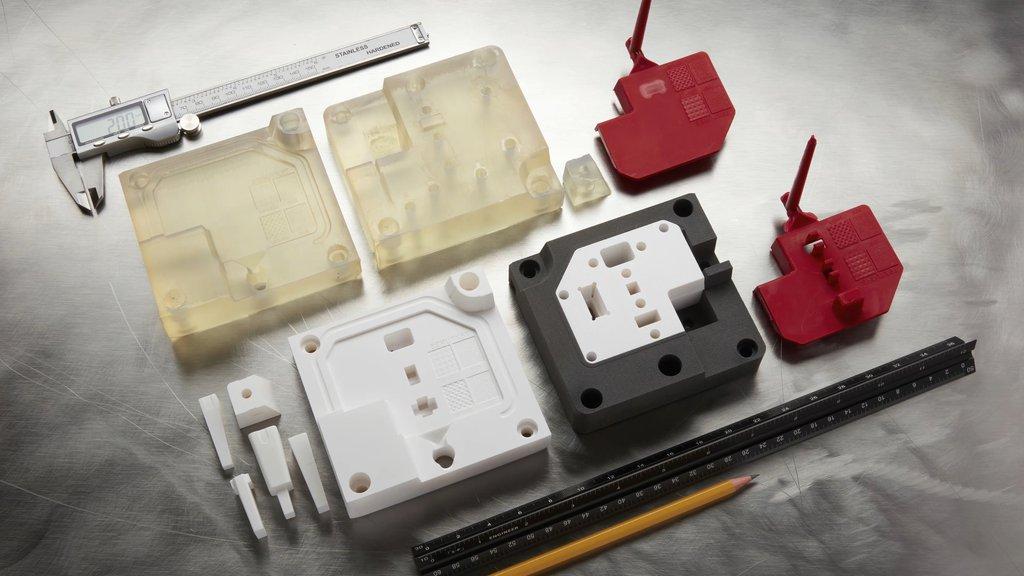
Rapid Tooling for Low Volume Production With Traditional Manufacturing Processes
Combine 3D printed rapid tooling with traditional manufacturing processes to produce limited quantities of parts in common plastics, silicones, rubbers, composites, or metals, with a flexible, agile, scalable, and cost-efficient tooling process.
3D printed tools can support the low volume fabrication of parts in various materials such as:
Plastics
Plastics
Produce Thermoplastics Parts Cost-Effectively In House
While most plastic manufacturing processes require expensive industrial machinery, dedicated facilities, and skilled operators, 3D printed tools allow companies to create rapid prototypes and end-use parts in common thermoplastics in-house easily.
Use 3D printed molds or patterns to produce plastics with the following manufacturing processes:
Resources:
Silicones & Rubbers
Silicones & Rubbers
Produce Complex Silicone Parts Quickly
Low-volume production for soft or flexible parts can be technically challenging, costly, and slow. Many professionals 3D print rapid tooling to mold or cast silicone parts. Desktop 3D printers offer many benefits, including design flexibility within CAD software, high accuracy, ease of prototype modification, and quick turnaround times.
Use 3D printed molds or patterns to produce silicone and rubber parts with the following manufacturing processes:
Resources:
Composites
Composites
Produce High-Detailed Composites In-House
Manufacturing parts in composite materials, such as carbon fiber, is a skillful and labor-intensive process for both one-off and series production. 3D printing offers a low-cost solution for rapidly producing molds and patterns. Stereolithography (SLA) 3D printing creates parts with a very smooth surface finish, which is essential for composite tooling. Stiff and temperature-resistant materials are able to sustain the heat and pressure of an autoclave and can be used to create a mold for prepreg lamination.
Use 3D printed molds to produce composites parts in the following manufacturing processes:
Resources:
Metals
Metals
Produce Metal Parts With Innovative Design
While 3D printers are primarily considered tools for creating plastic parts, their high-precision and broad material library make them well-suited for casting workflows and offer interesting properties for sheet metal forming as well. Leverage 3D printing to produce metal parts at a lower cost, with greater design freedom, and in less time than traditional methods.
Use 3D printed molds, patterns, or dies to produce metal parts with the following manufacturing processes:
Resources:
Rapid Tooling for Injection Molding, Thermoforming, Compression Molding, and More
3D printed tools can produce short runs with traditional manufacturing processes such as:
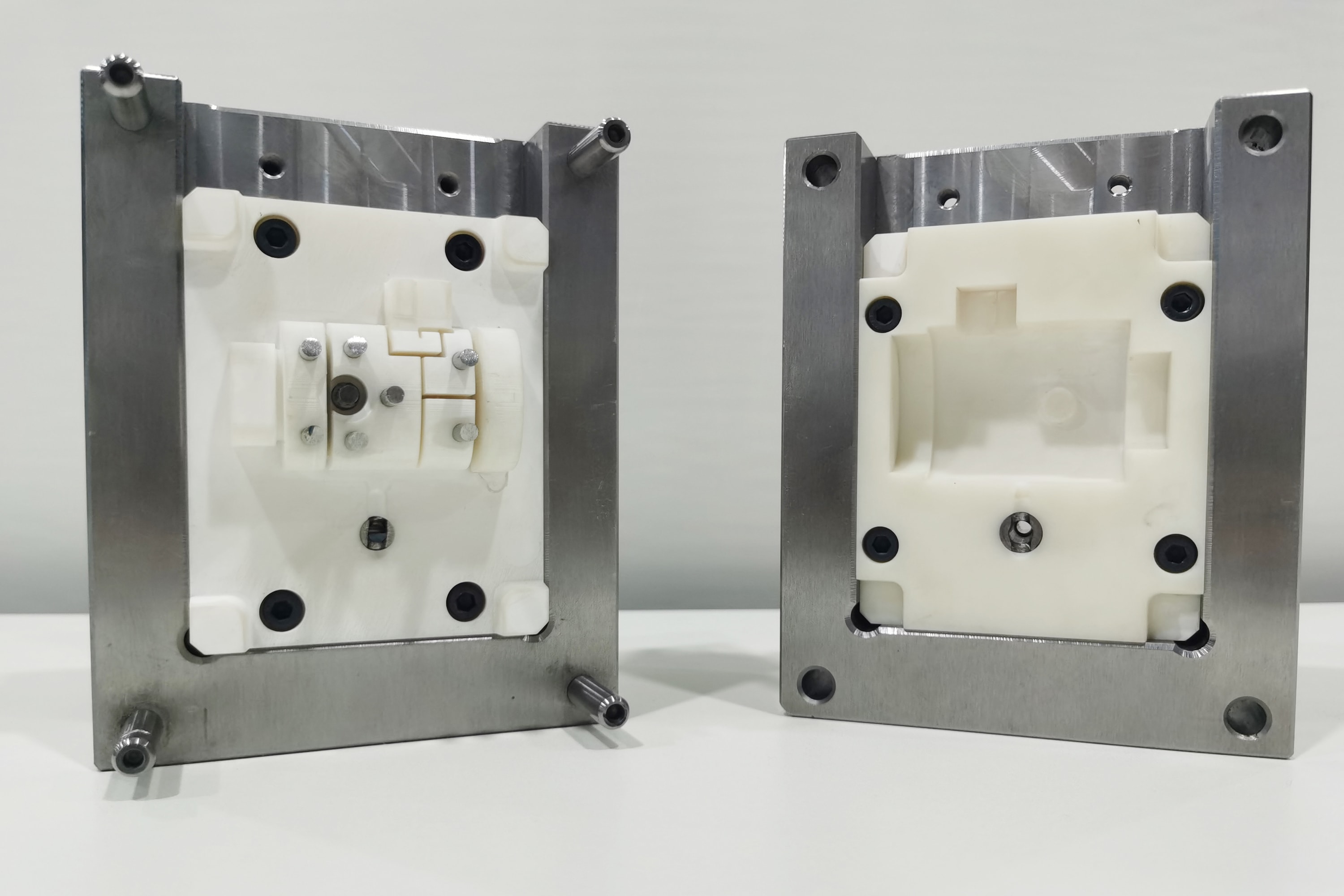
Injection Molding & Overmolding
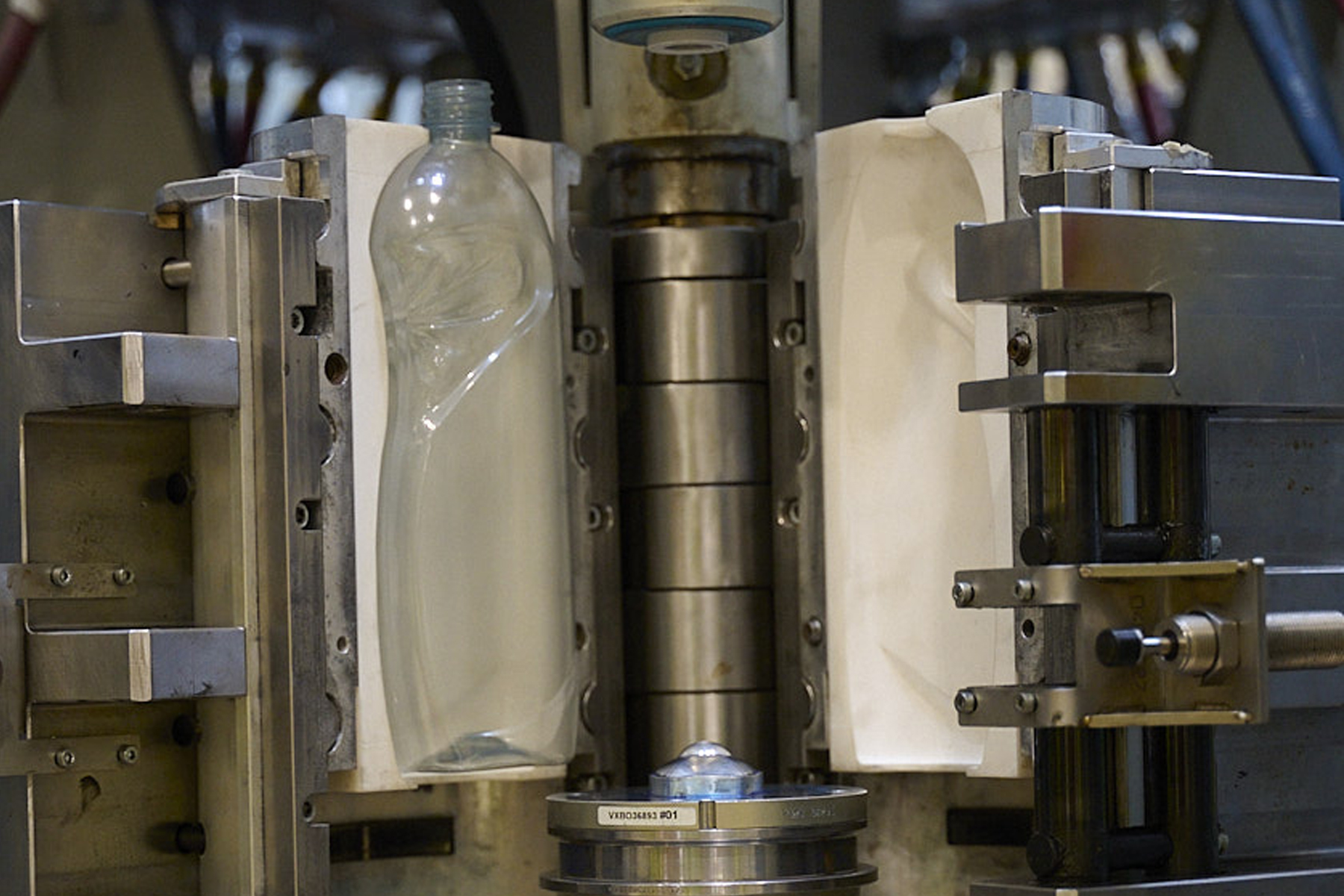
Blow Molding
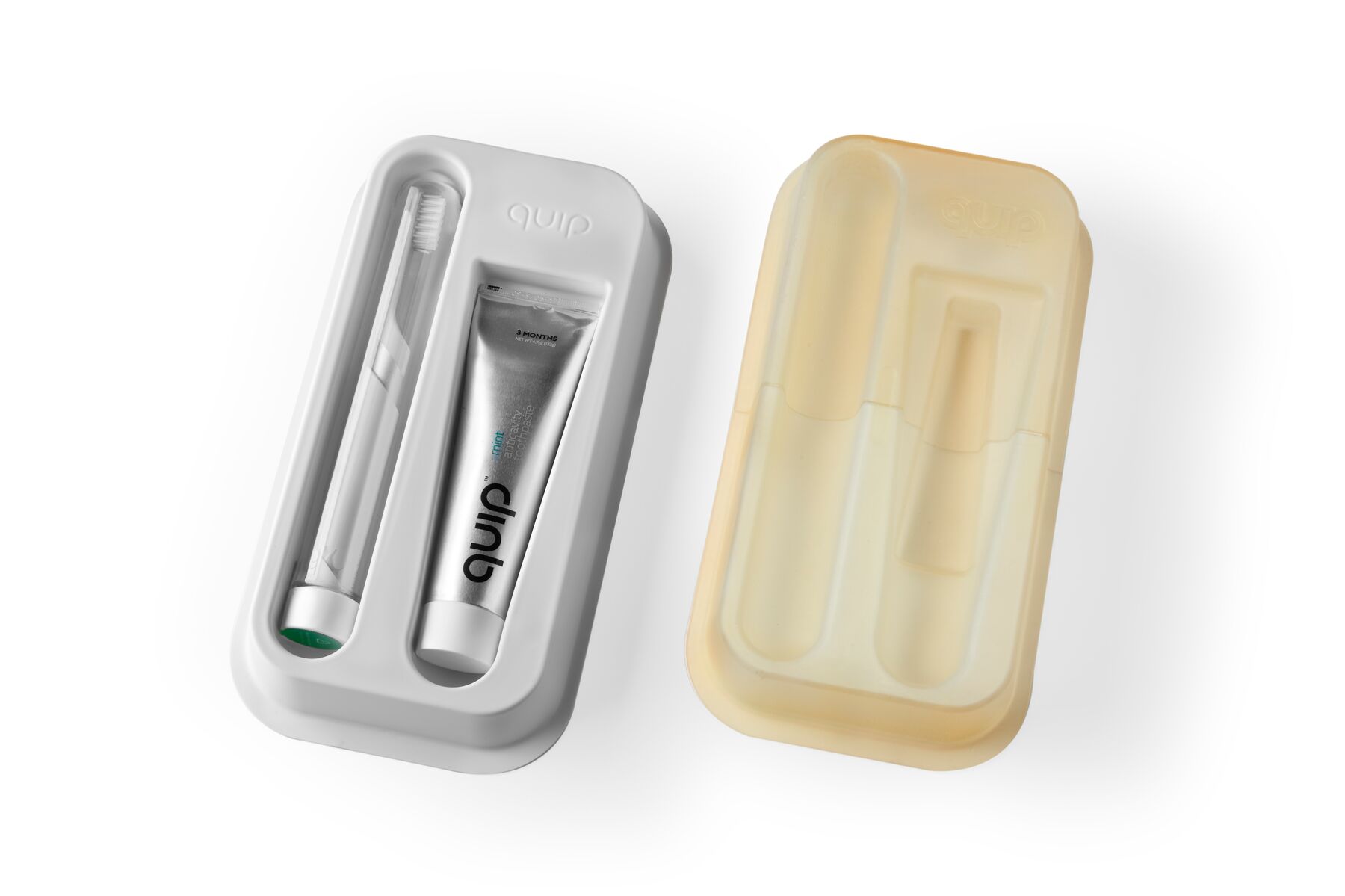
Thermoforming
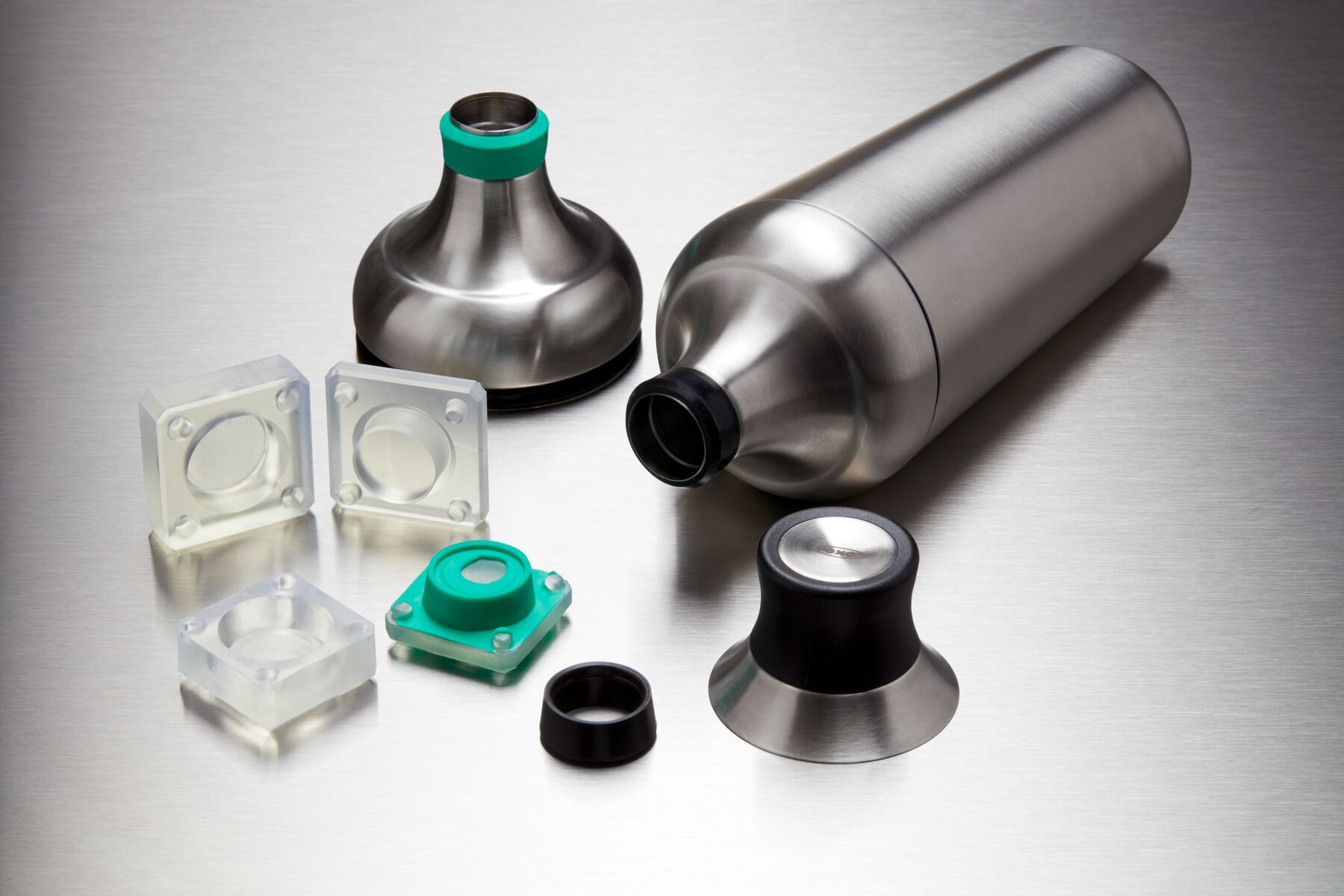
Compression Molding
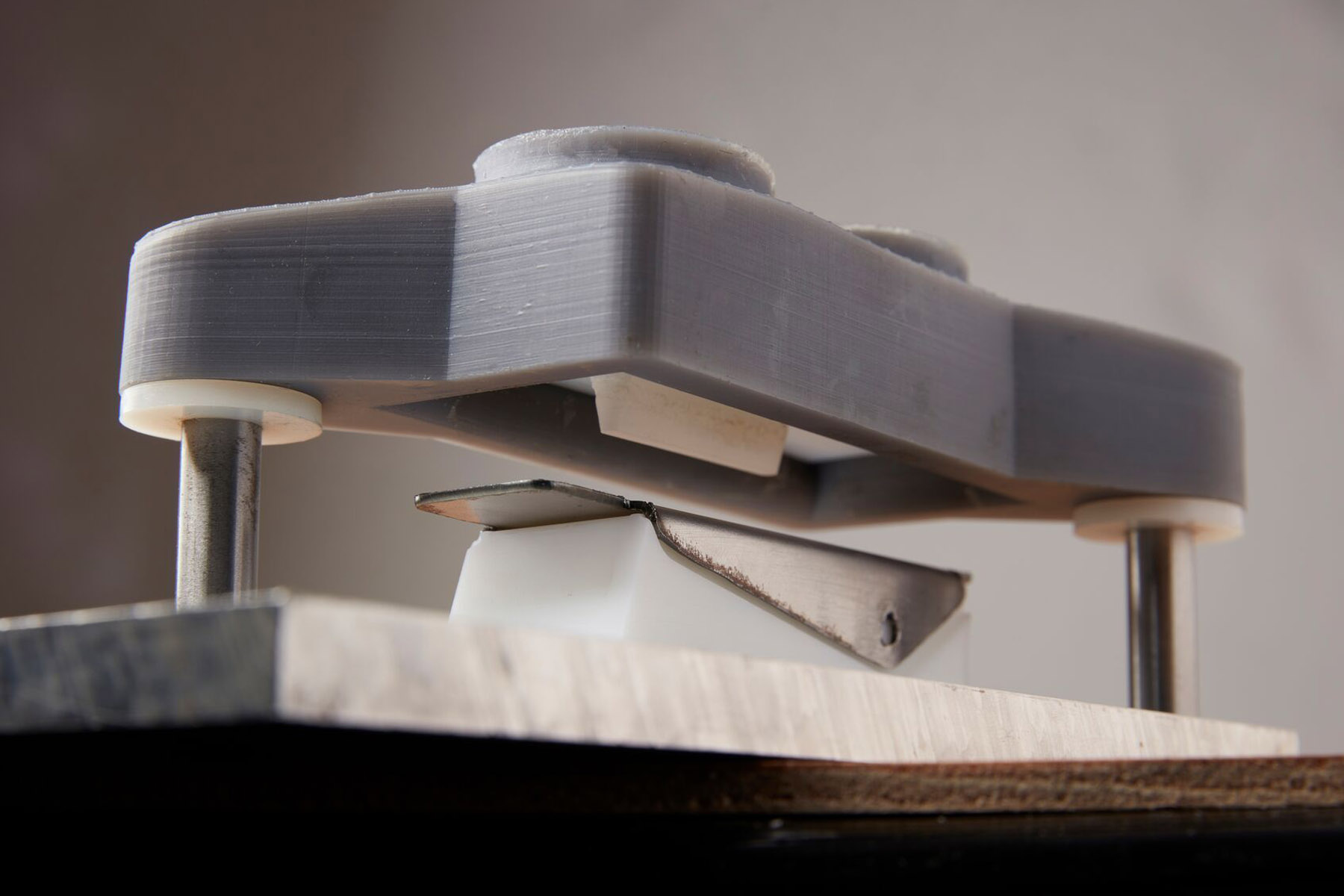
Sheet Metal Forming
Fast and Cost-Effective Low Volume Production
Whether you are looking to design functional prototypes with end-use materials, fabricate parts during pilot production, or manufacture end-use parts, 3D printing rapid tooling is a cost-effective and quick way to produce parts in limited quantities.
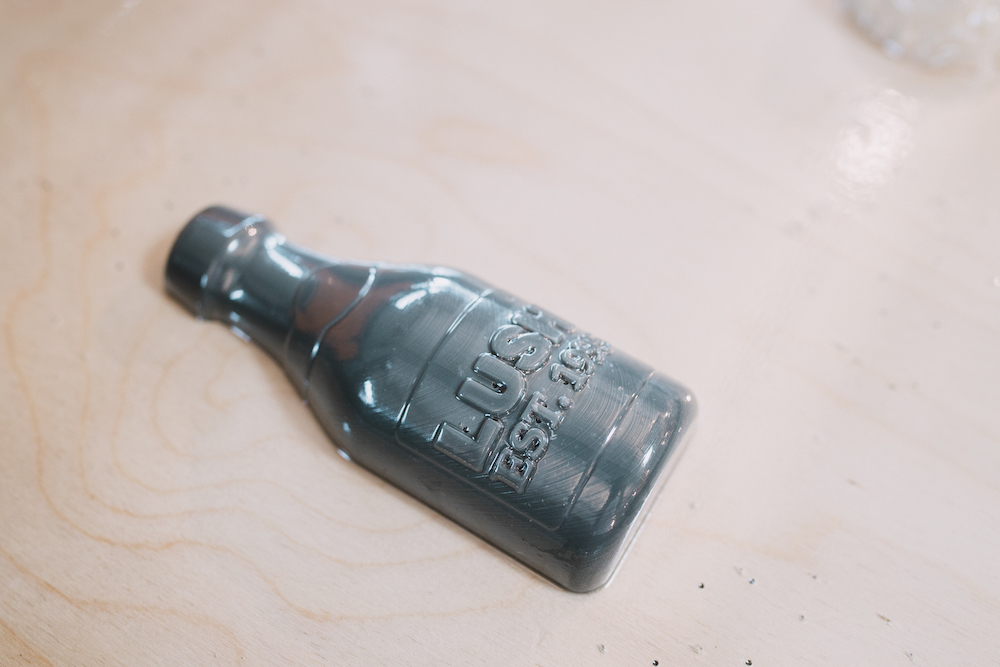
How Lush Cosmetics Take Ideas From Concept to Reality in Under 24 Hours
Learn how Lush Cosmetics use their fleet of Formlabs 3D printers to create patterns for vacuum forming molds for new cosmetic designs.
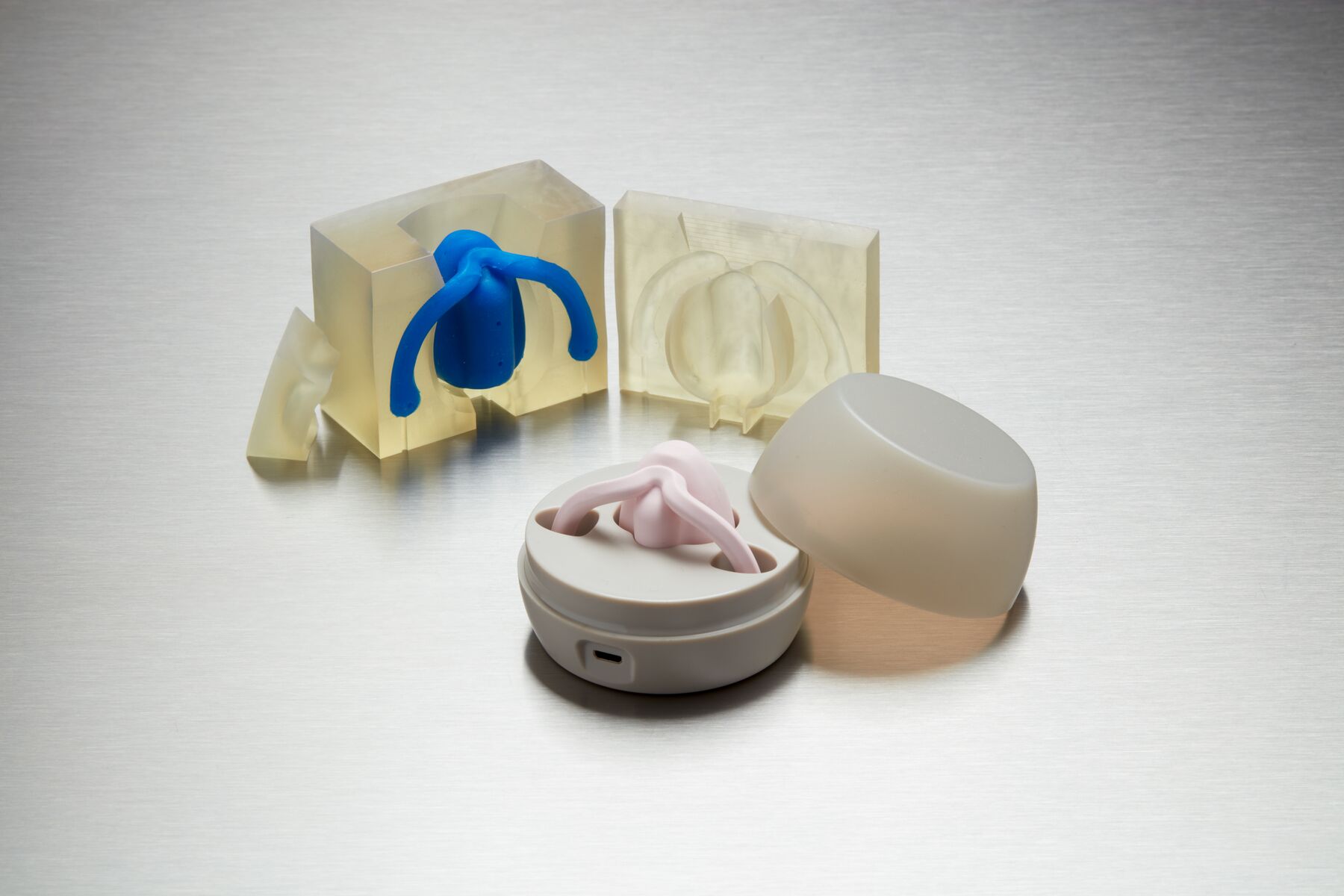
Dame Products Uses Silicone Overmolding for Customer Beta Prototypes
Learn how Dame Products engineers can prototype dozens of overmolded devices in one day by rotating
through three or four SLA printed molds.
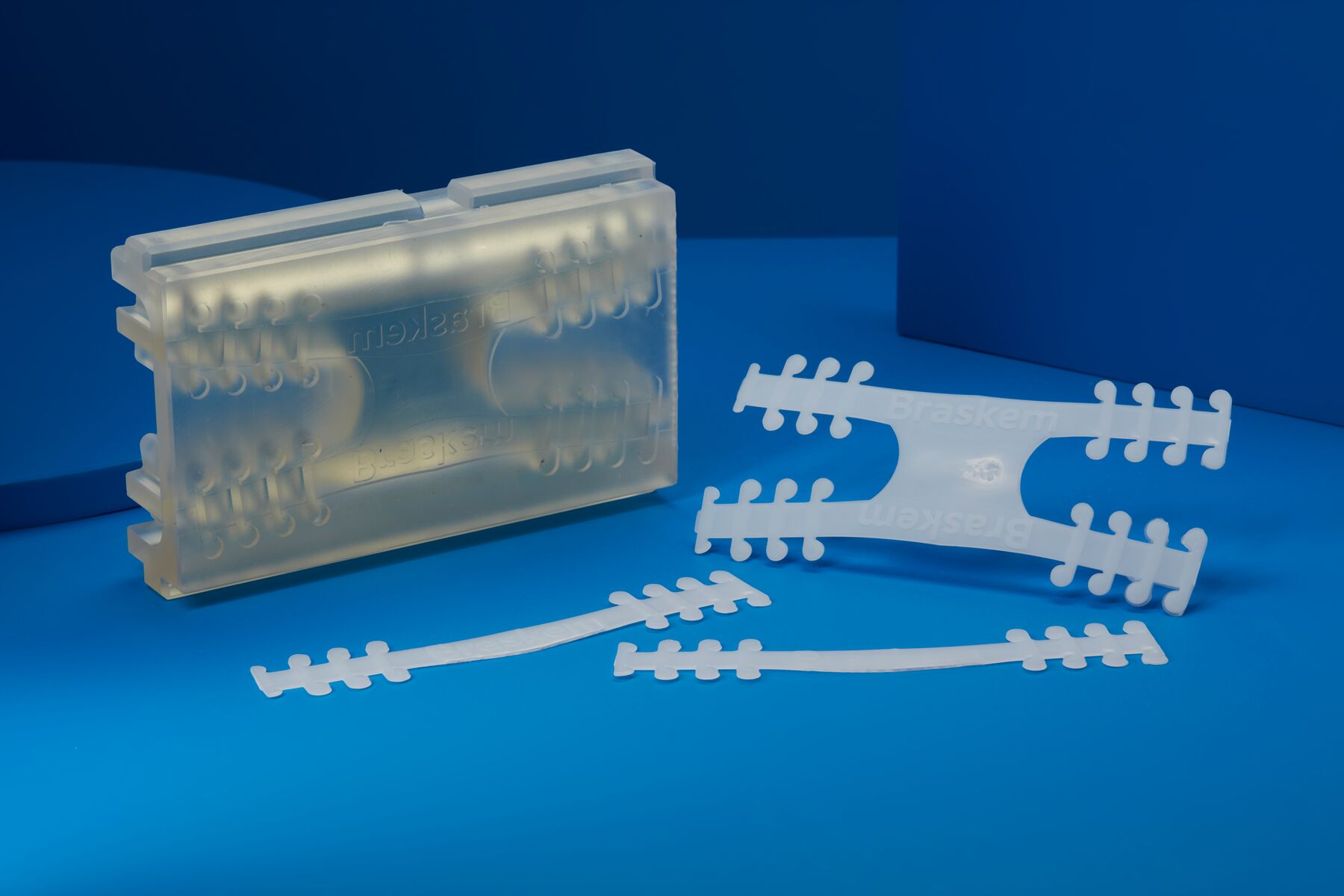
How Braskem Leveraged 3D Printing to Fabricate Injection Molds for End-Use Parts
Braskem, one of the world’s leading petrochemical companies, talks about their first foray into injection molding with a 3D printed mold.
From Design to Production Parts in 24 hours
Never again wait weeks for tooling to arrive from a service provider. Formlabs' complete, easy-to-use ecosystem can seamlessly be integrated into a range of traditional manufacturing workflows. Save time and money on low-volume projects by leveraging the benefits of 3D printed molds and patterns to quickly and affordably produce hundreds to thousands of parts in plastics and metal.
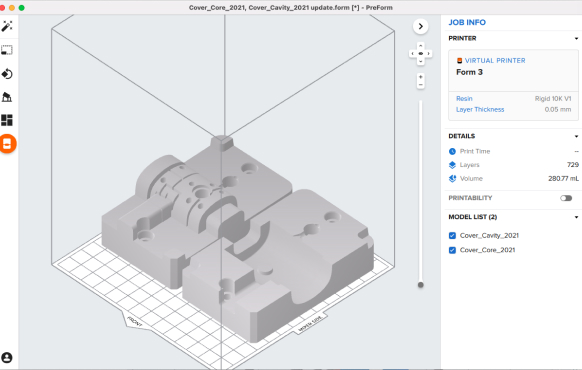
Design
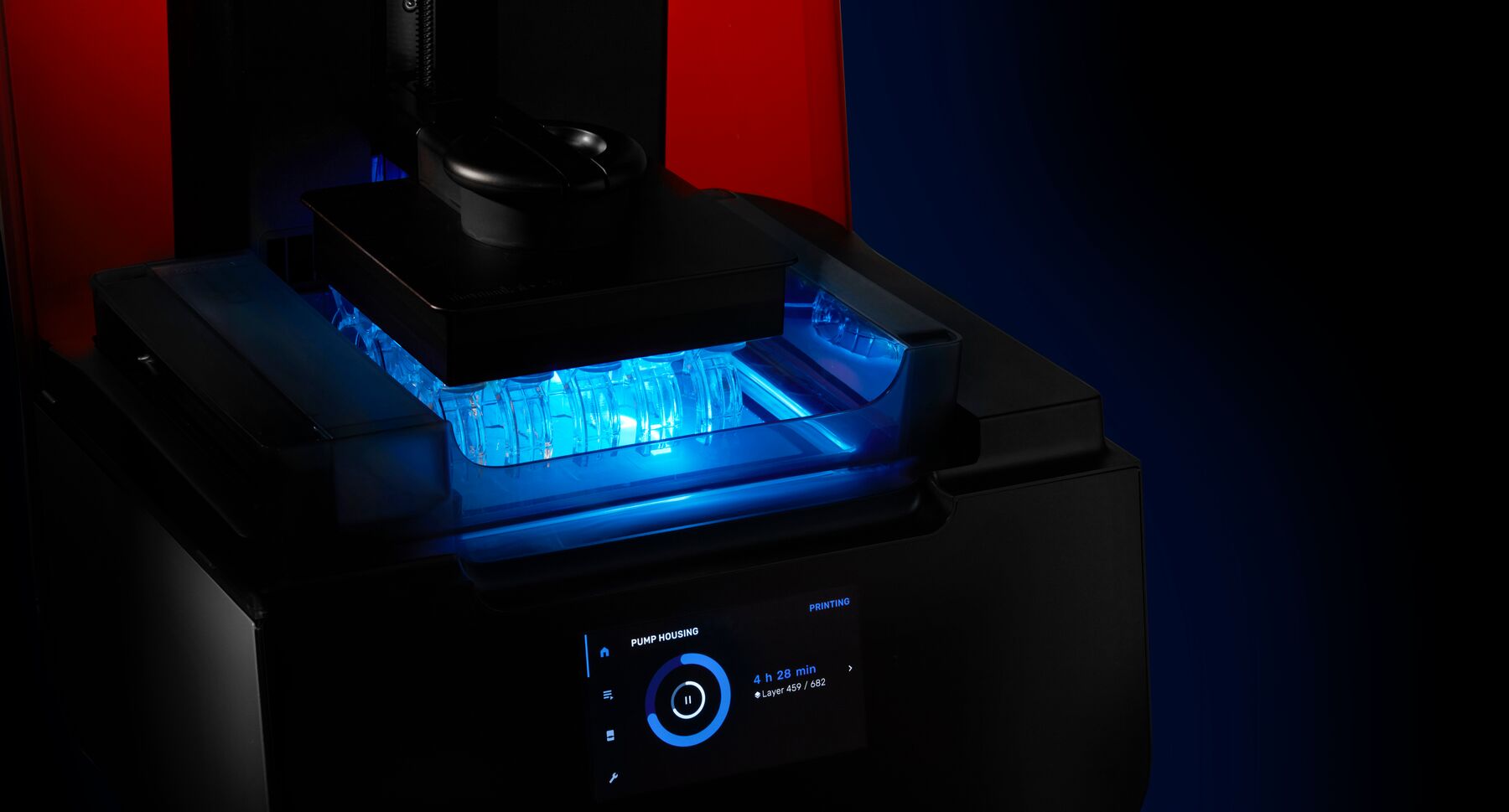
3D Print
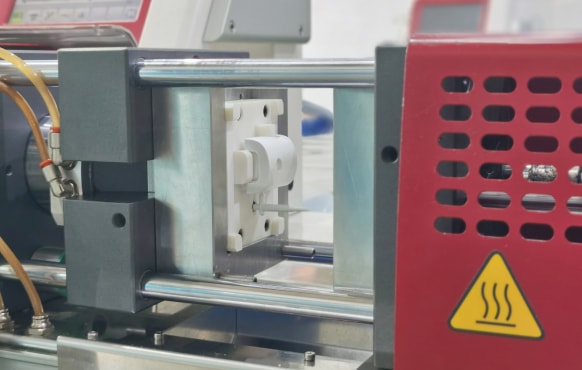
Manufacture
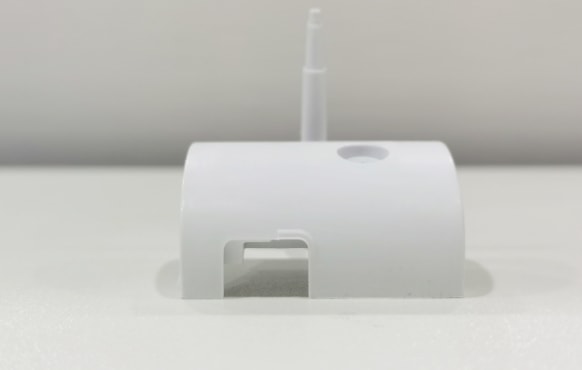
Post-Process
Save Money and Time
While the upfront cost of a printer setup can feel intimidating, it can pay for itself in just a couple of weeks or months when you compare it with how much you’d spend on outsourcing or an alternative production method.
Mold | In-House 3D Printing | Outsourcing |
---|---|---|
Time | < 1 day | 1-8 weeks |
Cost | $1-$100 | $100-$15,000 |
Curious to see how much you can save? Try our interactive ROI tool to calculate cost per part and lead time when 3D printing on Formlabs 3D printers.
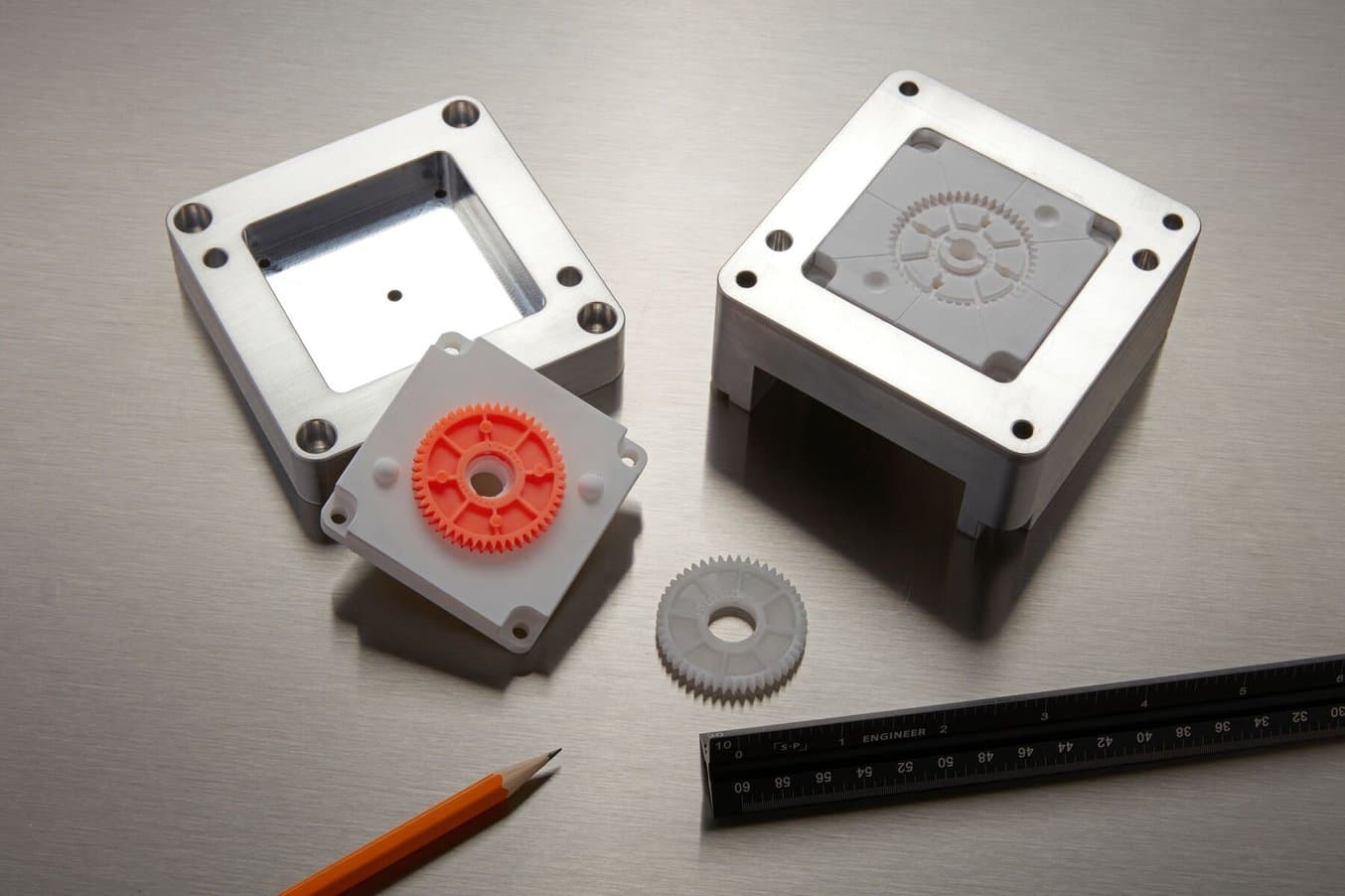
Tools to Get Started 3D Printing Rapid Tooling
Formlabs' ecosystem of accessible 3D printers and high-performance materials can be used to fabricate strong, smooth, highly detailed molds and patterns capable of producing hundreds to thousands of parts.
Tools for Rapid Tooling
Form 4
High Performance SLA 3D Printer
The Form 4 produces molds and patterns with a high-quality surface finish and fine features, ensuring that the production parts come out true to design with minimal post-processing.
Use the Form 4 at various points of the product development process for a faster ROI. From 3D printing prototype parts to producing molds for short-run production of those same parts, the Formlabs ecosystem is easy to integrate into any product development process.
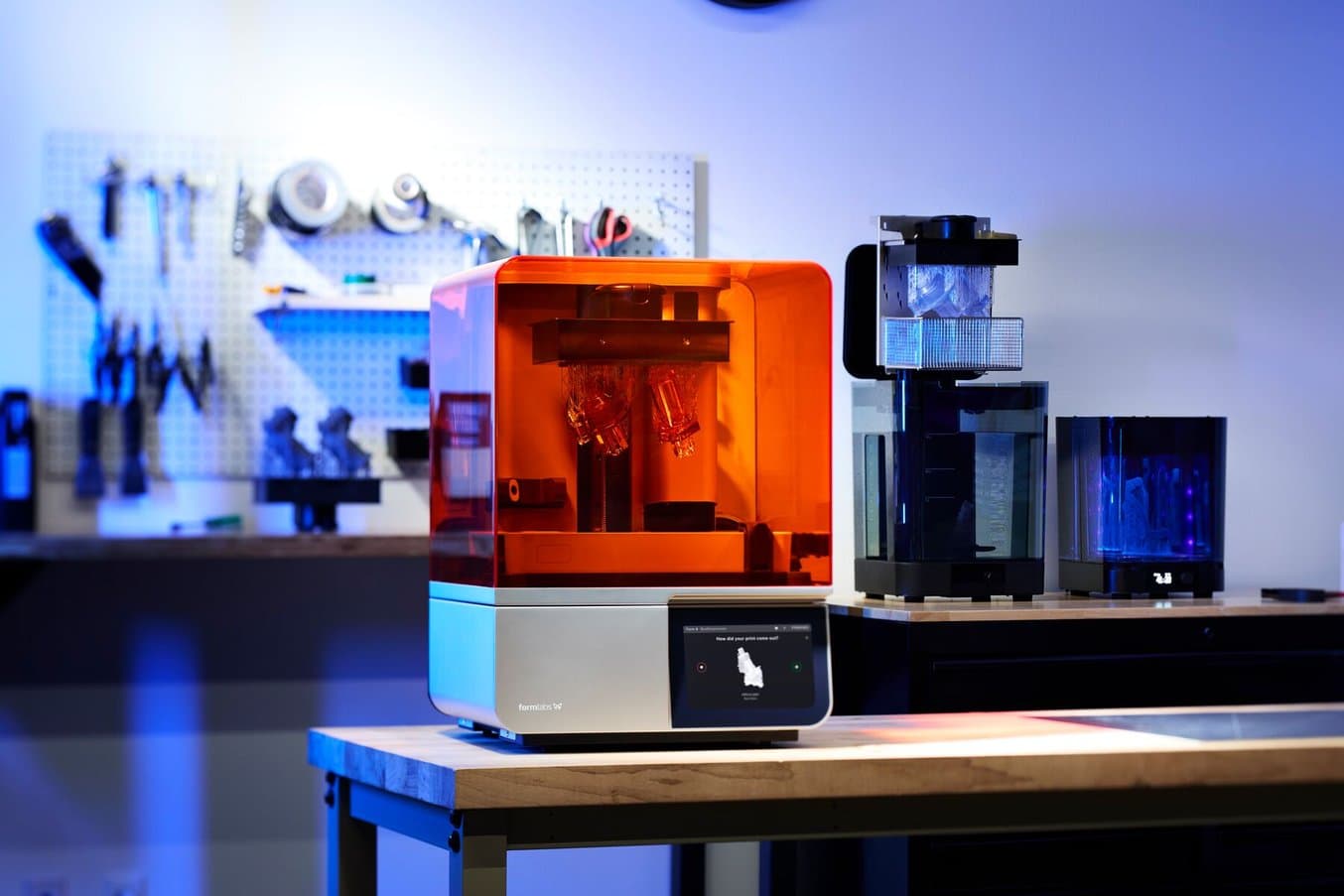
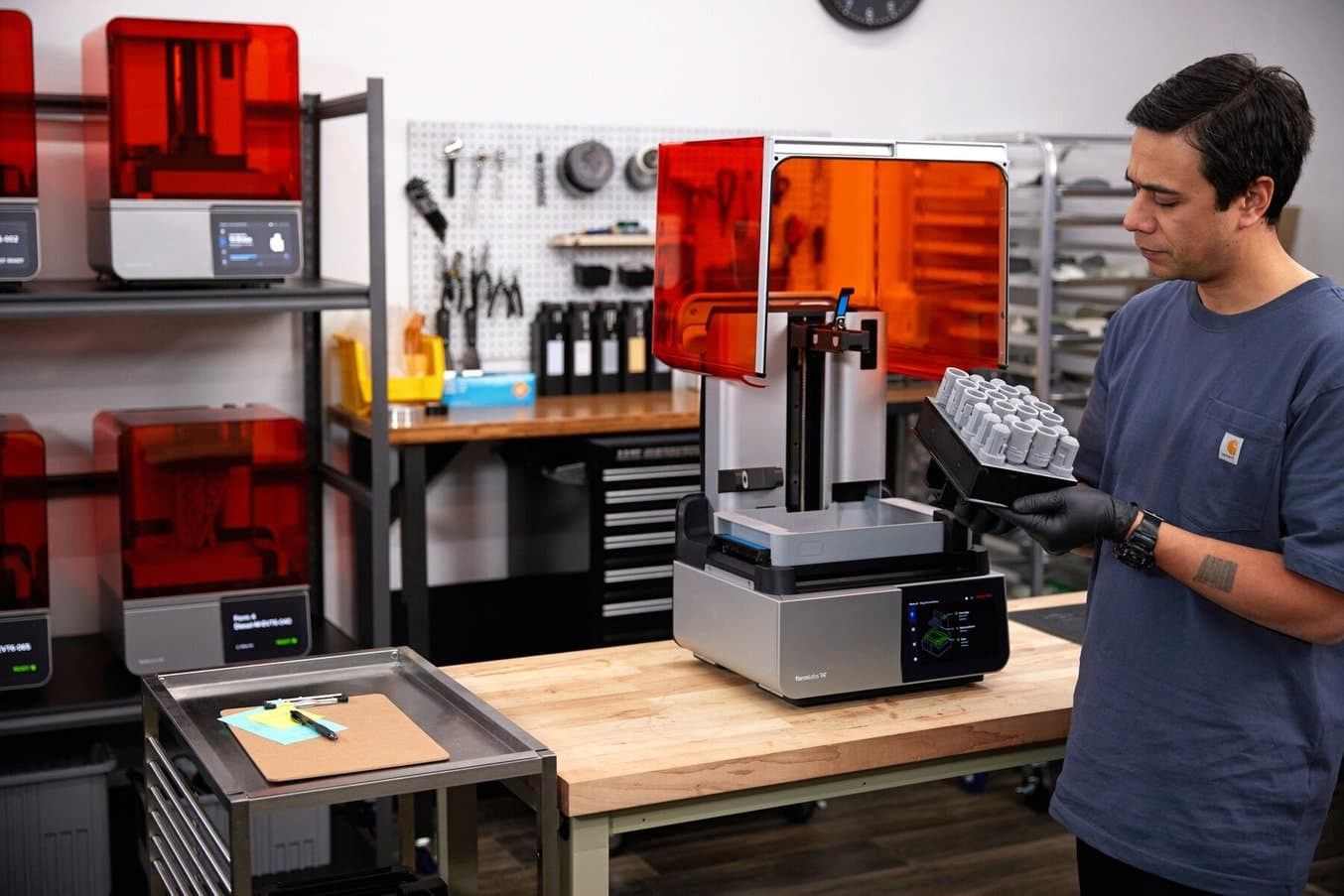
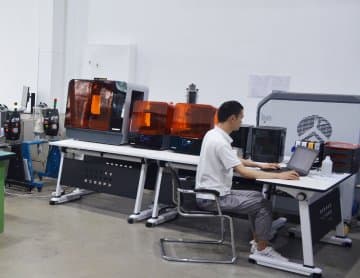
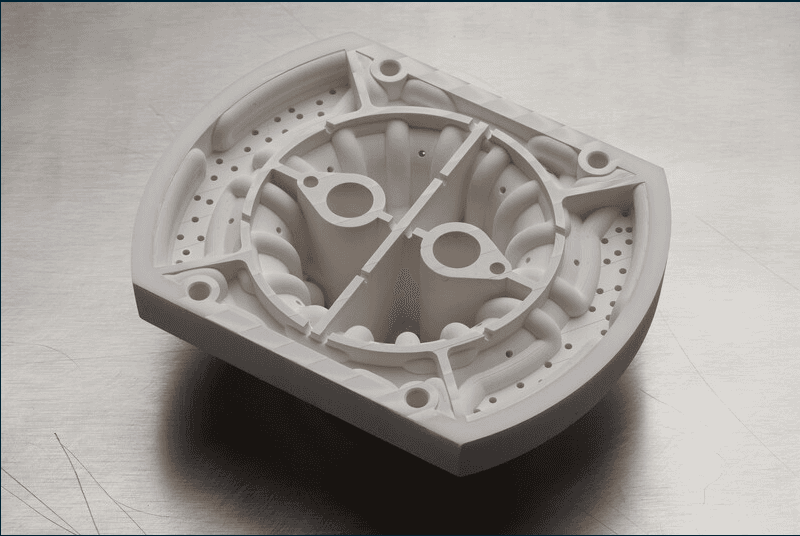
Formlabs is Open
Maximize your 3D printer’s potential with Formlabs Developer Platform. Unlock the possibility of printing with any 405 nm photopolymer resin or 1064 nm powder on Formlabs 3D printers, customize your print settings, or build software integrations.
Additional Resources About Rapid Tooling
Check out some additional resources to help you get started combining 3D printed rapid tooling with traditional manufacturing processes.
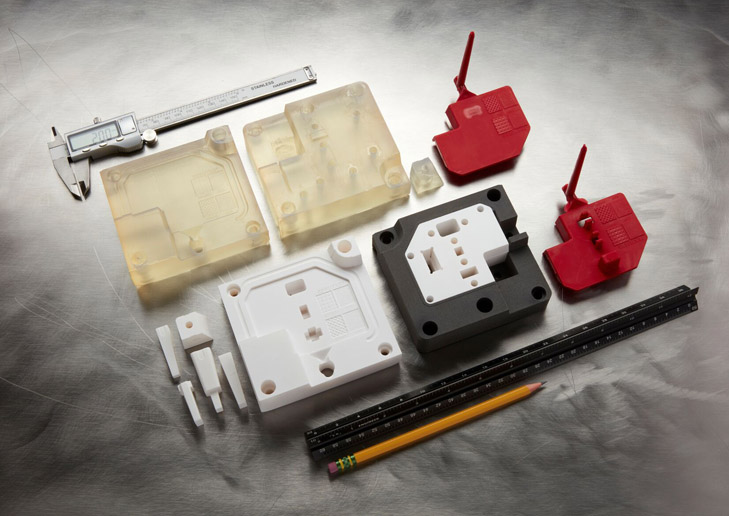
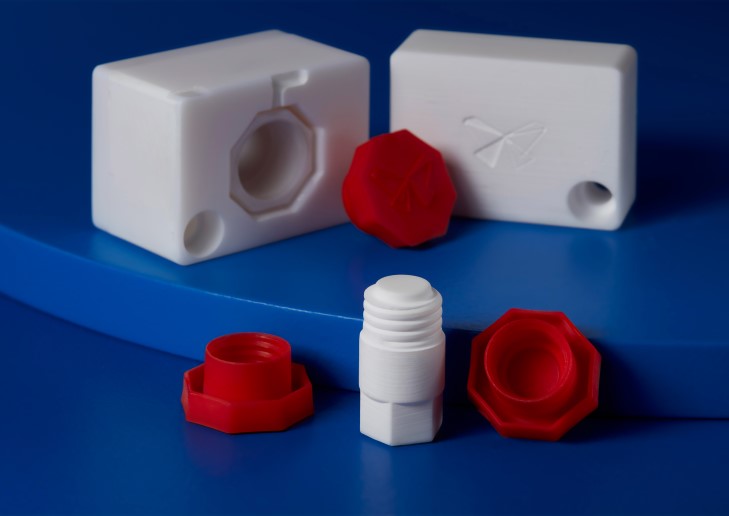
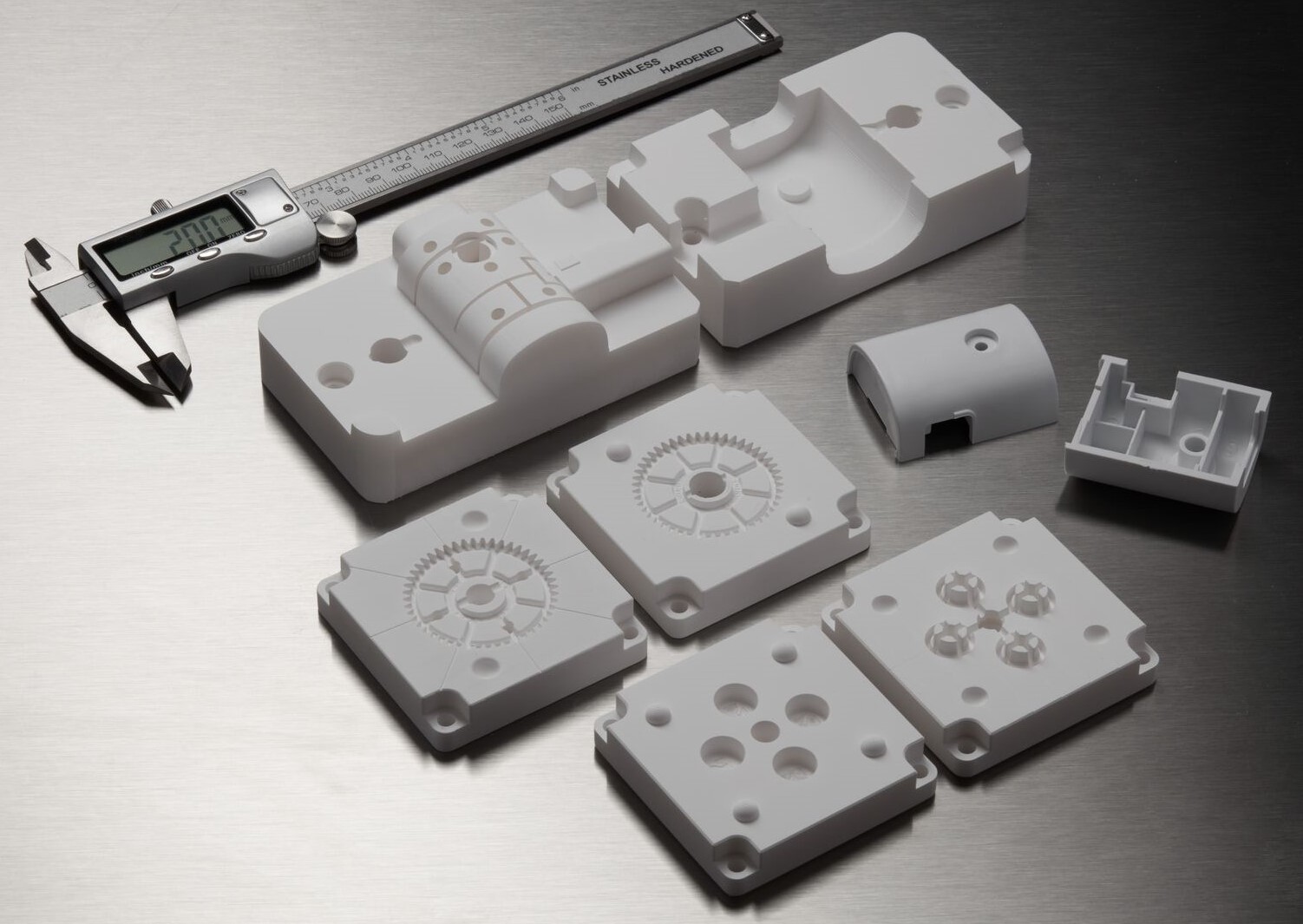
Get Started 3D Printing Rapid Tooling
Contact a Formlabs Solution Specialist to get started with rapid tooling.