“Form 4L allows us to print big parts, super high quality, barely any hand finishing required, readily usable.”
Julien Thiebaud, Design Manager, Advanced Technologies, Archer
Archer Aviation, Inc. a leader in electric vertical takeoff and landing (eVTOL) aircraft, is reimagining air travel with the development of the next generation of air taxis. Julien Thiebaud is a design manager for the advanced technologies division, which is a full design studio doing interior design for aircraft. The studio makes full-size models and prototypes using tools including fused deposition modeling (FDM) and stereolithography (SLA) 3D printing.
Thiebaud says, “We print all the time. Absolutely everything that's going to come out of Archer at some point goes through the studio.” Archer's industrial design team spends the majority of their time working on functional prototypes made of advanced materials. These prototypes must meet performance standards while offering a superior surface finish and tight tolerances. Therefore, when selecting a 3D printer, Thiebaud says that the most important considerations are “Reliability, speed, surface quality, and customer service.”
“I am a car designer, hence picky. It's been a long time since I have met a company like Formlabs, in which everything is awesome from start to finish. From the unboxing of the machine, the user experience, the user interface, the design and aesthetics of the machine, the quality of the parts, and all the way to the customer support.”
Julien Thiebaud, Design Manager, Advanced Technologies, Archer
Speeding From Form 3L and FDM to Form 4L
“A big part is going to take 12 hours. If I do the same thing on 3L, it's 35 hours. So it's an absolute revolution for us. Night and day. And there's always those last-minute requests, "Hey, can I get this for yesterday?" Now that we have Form 4L, we can do that.”
Julien Thiebaud, Design Manager, Advanced Technologies, Archer
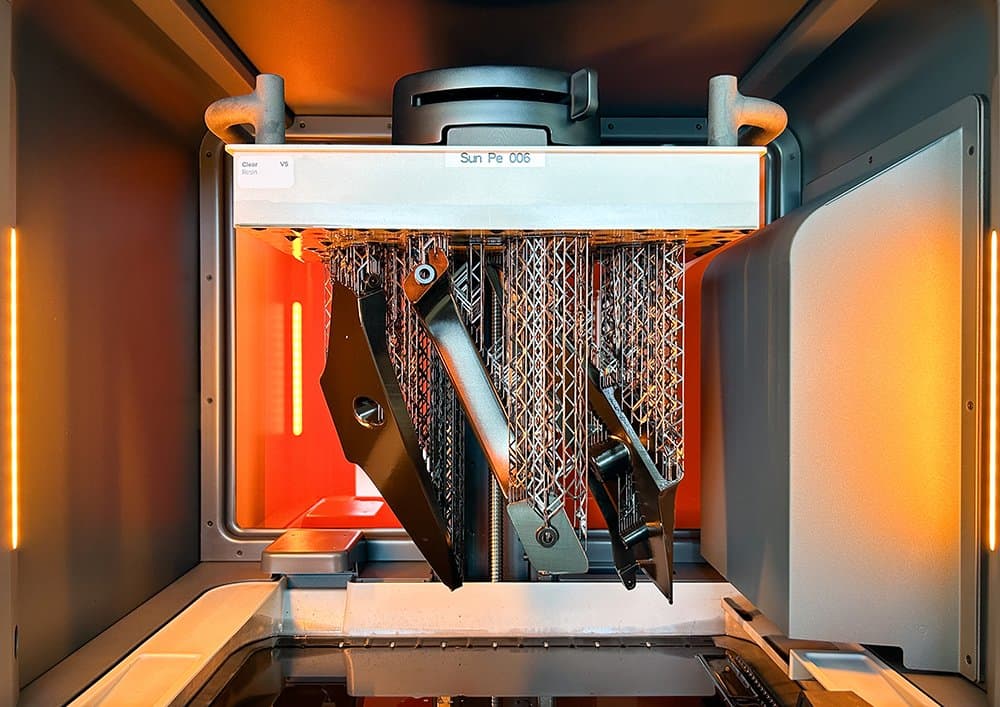
3D printing large prototypes in Black Resin V5 on Form 4L is faster and more cost-effective than traditional methods, and even FDM 3D printing.
Before bringing 3D printing in-house, Thiebaud would test prototypes with CAD simulation, or CNC prototypes by hand and manually test them, a long and costly process. Adding 3D printing was both more time-efficient and less costly. Fused deposition modeling (FDM) and stereolithography (SLA) 3D printing provided faster methods of producing prototypes.
Until Form 4L, Thiebaud would print big parts on FDM because it was faster and the parts were lighter than Form 3L, or print on Form 3L if a smoother finish was needed. But with Form 4L, print times for some parts went from 10 hours on Form 3L to an hour on Form 4L.
“The speed of Form 4L has put our best FDM to shame. For my team’s jobs, I don't even think about the FDM anymore when we start designing something.”
Julien Thiebaud, Design Manager, Advanced Technologies, Archer
The speed of Form 4L has increased the number of iterations the team can do in a week. For a headrest prototype, Thiebaud 3D prints the substrate and the mounting fixture on which to test upholstery and stitching placement. He says, “3D printing on Form 4L allows us to do five different designs and five different tests a week,” halving the time to produce a prototype.
Prototypes That Perform
“We needed to make a bracket and braces for structural rigidity, a portion of a chassis. We 3D printed it in FDM. It didn't work. We tried some different techniques. Printed with the Form 4, it was perfect right away.”
Julien Thiebaud, Design Manager, Advanced Technologies, Archer
Thiebaud prototypes small parts for lighting systems, interior design for transportation (such as finishers for seats, dash, and cabin), and some scale models for architecture. Some of these parts sometimes have to withstand high temperatures and be resistant to corrosion against chemical components. For prototypes that need to have these characteristics, Thiebaud uses High Temp Resin, which has a heat deflection temperature (HDT) of 238 °C @ 0.45 MPa — the highest among Formlabs resins.
“Prototypes are put to use in a very similar way that we would do in production. So it's important for us that, in terms of tensile strength and mechanical properties, they match what the final part would be doing.”
Julien Thiebaud, Design Manager, Advanced Technologies, Archer
Parts printed with SLA are isotropic and can withstand the functional demands of prototyping. Formlabs material scientists leveraged the technology of Form 4 to release updated resins with improved mechanical properties and aesthetics, enabling not only faster printing, but improved performance.
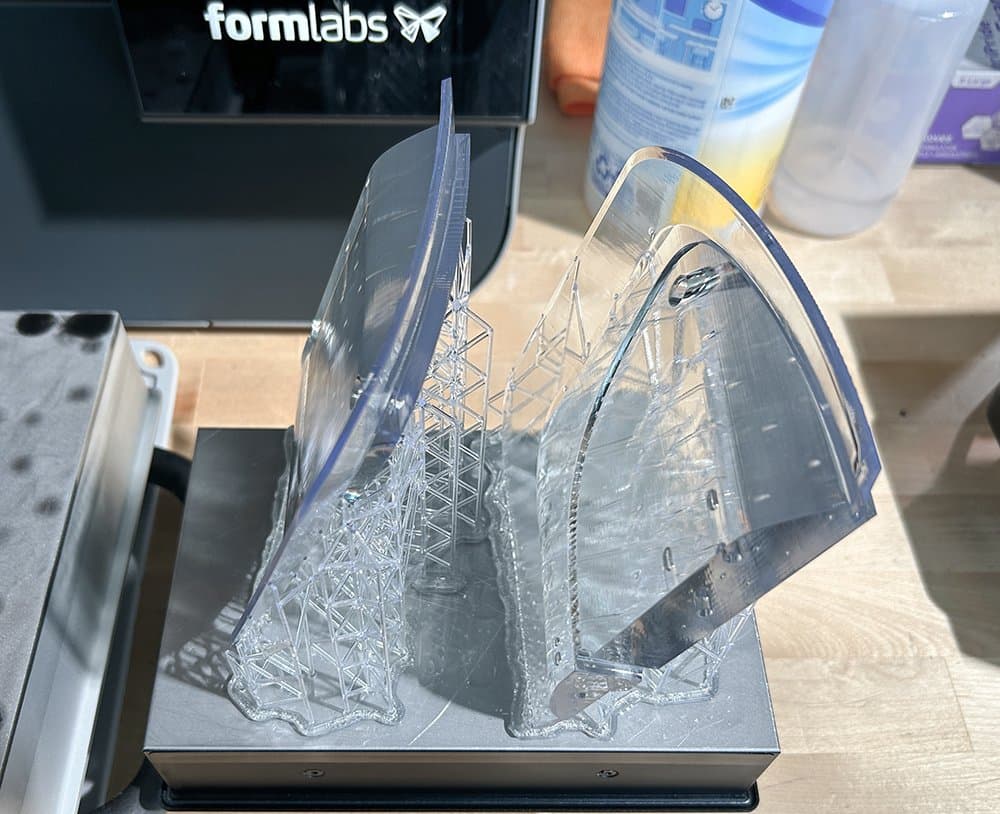
Clear V5 Resin was designed to print on Form 4 Series 3D printers. Prototypes printed in Clear V5 Resin offer exceptional clarity and less yellowing than previous versions.
“The difference between Clear Resin V4 and V5 is phenomenal. We have printed exactly the same parts, and the transparency is greatly improved. There was even a time we forgot to clear coat, and then realized a couple days later, and the part was still fine, so the UV resistance has greatly improved.”
Julien Thiebaud, Design Manager, Advanced Technologies, Archer
Time Savings During Post-Processing & Finishing
“The quality is fantastic. Since we got the Form 4, parts require 80% less sanding and finishing. I love the fact that we can remove all the support pieces only with a finger, not even using a tool. Wash them, cure them, and then slap them onto the prototype. There's very little, if any, hand finishing to be done. The overall quality is incredible.”
Julien Thiebaud, Design Manager, Advanced Technologies, Archer
Print time is only one part of the story. Post-processing and finishing 3D printed parts have to be factored into the overall production time. The finer a surface is coming off a 3D printer, the less finishing will be required. Thiebaud notes, “Every time you remove supports you have to sand the touchpoint. The Form 4 system has managed to reduce the density of supports. The surface quality on the part when they come out of the machine is really, really good. Basically, once the part is cured, put a quick sandpaper on it and it's good to go.”
In the beginning, Thiebaud auto-generated light-touch supports in PreForm, designed to minimize removal time and keep surfaces cleaner. As he became more experienced, he dialed in custom support density and touchpoints for even faster prints and minimal finishing. Additionally, he manually orients parts to ensure key surfaces stay pristine.
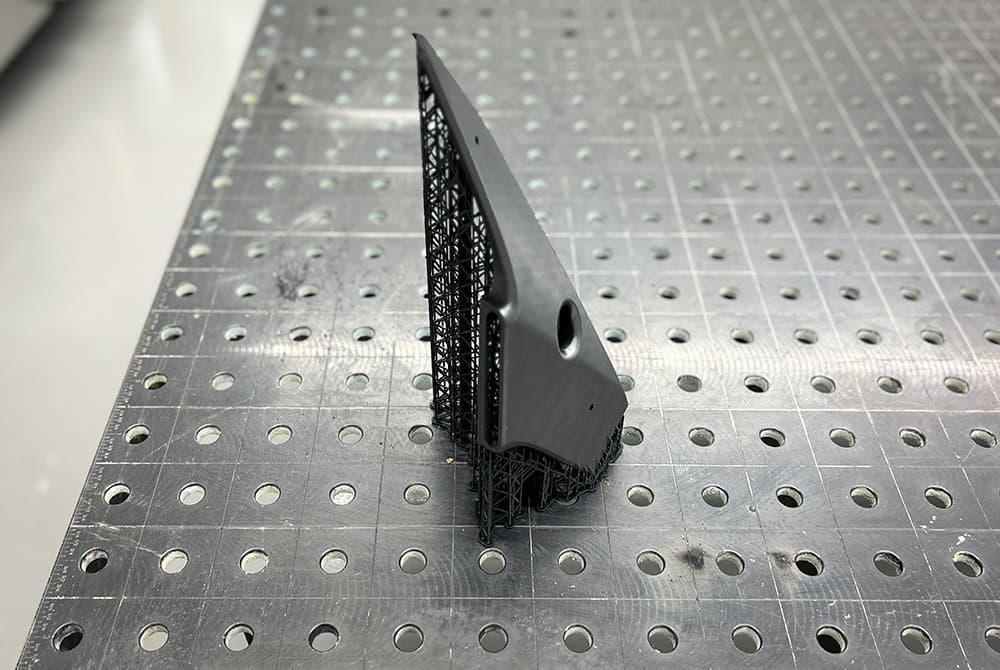
Seat Side Finisher Prototype
Printer: Form 4L
Print time: 1 h 30 min
Post-processing time: 30 min (Wash + Cure)
Finishing time: 30 min sanding (No paint)
Total: 2 h 30 min
Non-Stop Reliability
“When we discovered Formlabs, the primary thing was the reliability of the print. These machines are running non-stop. We beat them up. And the fact that they can print and never skip a beat, it's amazing. Reliability is everything.”
Julien Thiebaud, Design Manager, Advanced Technologies, Archer
Thiebaud is constantly printing. Able to design a CAD model in 30 minutes, he has a constant stream of prototypes to print. With this volume of prints, any printer downtime would seriously affect timelines and cause a massive disruption of workflows. Thiebaud says, “When we discovered Formlabs, the primary thing was the reliability of the print.”
Thiebaud needs to know that whatever part he sends to the printer is going to print accurately. In Form 4 Series printers, six integrated sensors precisely control resin temperature, resin level, print forces, and print status, while preventative maintenance reminders keep printers up and running reliably.
“Customer service is really important and Formlabs has been phenomenal in that regard.”
Julien Thiebaud, Design Manager, Advanced Technologies, Archer
If troubleshooting is ever needed or questions arise, Thiebaud can talk directly with an expert at Formlabs, to ensure design studio production stays on track.
Speeding Ahead With High-Quality Prototypes
“Form 4L allows us to print big parts of super high-quality, barely any hand finishing on them, and readily usable. The machine has been flawless for the entire time we have had it.”
Julien Thiebaud, Design Manager, Advanced Technologies, Archer
Prototyping the cutting-edge technology powering Archer’s aircraft requires speed, precision, accuracy, and reliability, and Form 4L is up to the task. Delivering prototypes with fine finishes and easy-to-remove supports, Thiebaud and the fabrication team are saving time, enabling a quicker turnaround on prototypes.
Explore Form 4L to learn more or contact sales to see how Formlabs can help speed your product development.