Thousands of Meters Under The Sea: 3D Printed Enclosures for Deep Ocean Exploration
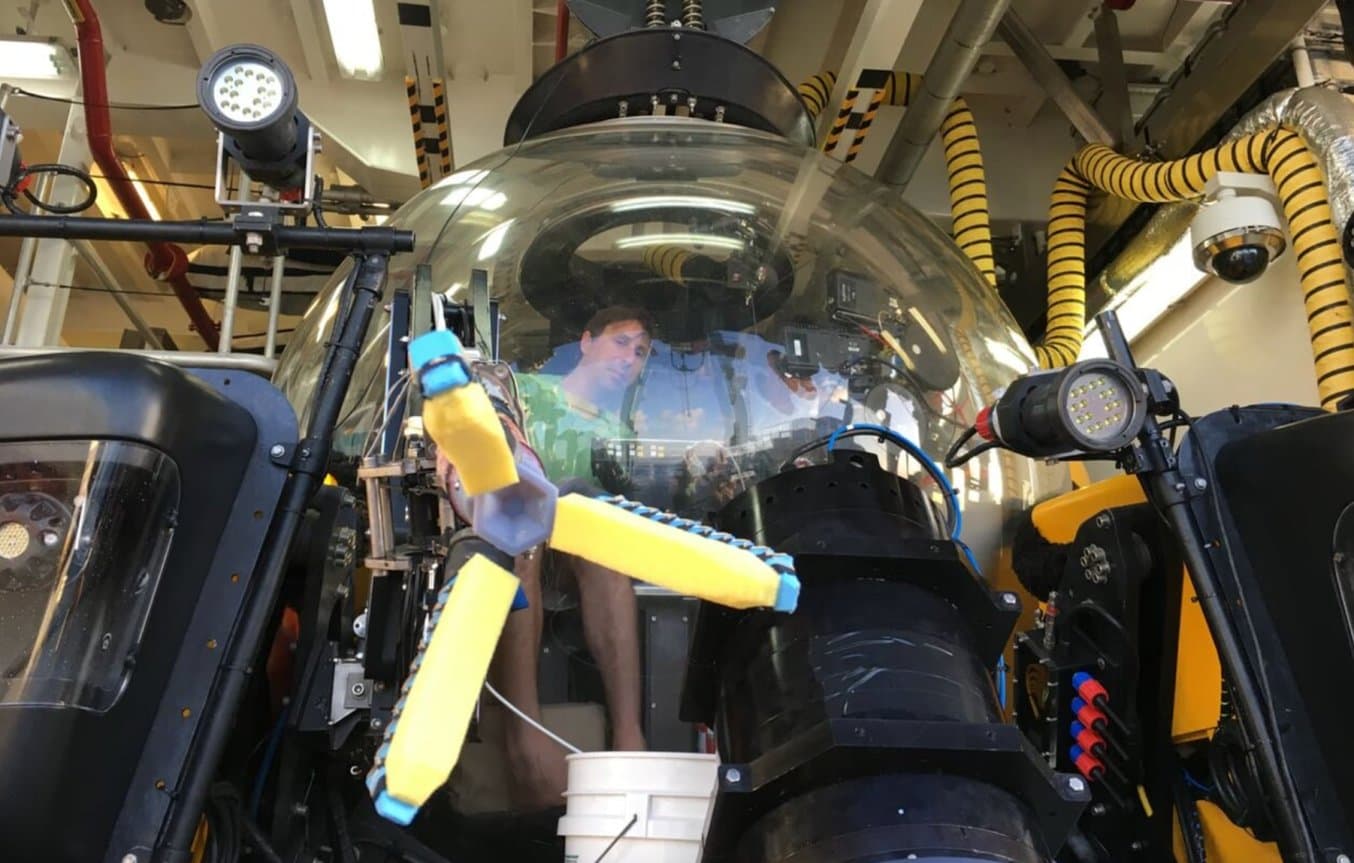
URI Deep Sea Robotics Lab Principle Investigator Brennan Phillips. Image credit David Gruber.
Despite international fervor for space travel, the true final frontier might be closer to home. Oceans cover over 70% of our planet’s surface, but the National Oceanic and Atmospheric Administration (NOAA) estimates that less than 20% of our oceans have been fully explored.1 Compared to the scale of space exploration, ocean exploration has been underfunded and underappreciated. However, some researchers are persevering despite the challenges, and have turned to accessible 3D printing as a way to dive deeper.
At the Undersea Robotics and Imaging Laboratory, part of the University of Rhode Island’s Bay Campus, Professor Brennan Phillips and his students are building tools that can explore thousands of meters below the ocean’s surface. Using the Form 3+ and Form 3L stereolithography (SLA) printers, the lab 3D prints watertight camera enclosures and a wide variety of research tools for their work.
Waterproof Parts Under Pressure
Mapping the ocean requires creating tools that are not only waterproof, but remain that way even under the immense pressure far beneath the ocean’s surface. Phillips and the lab students began designing a 3D printed casing for a camera that could keep the device completely dry even under pressure, yet be easily disassembled to retrieve the data after deployment. After tens of iterations, the team settled on this cylindrical design printed in two parts on the Form 3+ in Clear Resin. The casing’s internal structure holds the circuit board and has an epoxy filling that suspends the camera lens in air. Everything below the lens is epoxy, injected through portholes built into the casing design.
“The challenge that is placed in front of us is, ‘what's the tiniest, cheapest deep-sea camera we could make?’ So now we’ve printed dozens of them in different shapes, and because it’s a printable thing, we can make any shape we want. We can design something quickly, build up the electronics, put it in there, optimize size, and then pour the epoxy,” says Phillips.
3D printing has allowed the lab to thoroughly iterate without worrying about running up the budget, and has introduced more design flexibility than was possible through machining.
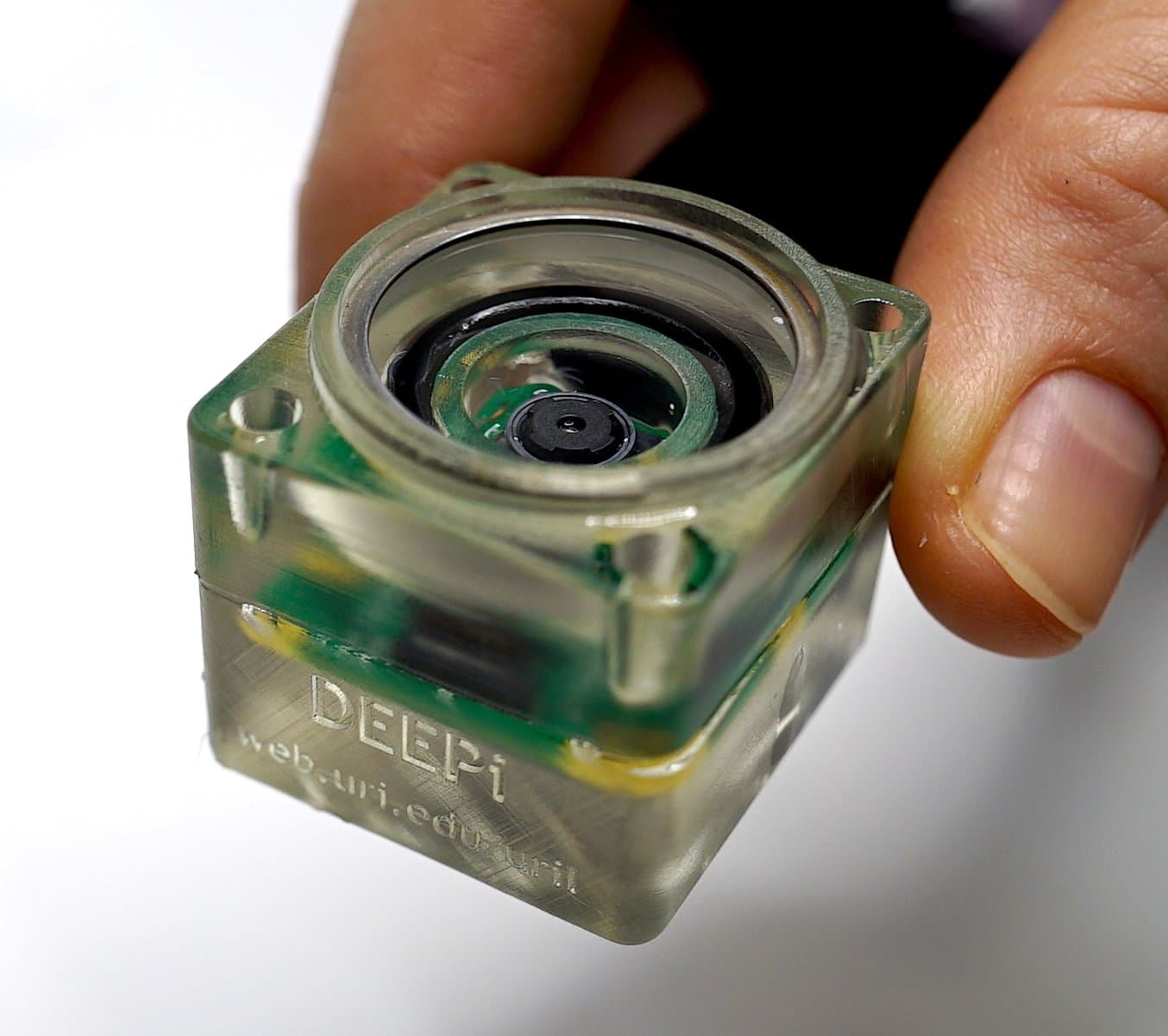
The DEEPi camera design uses a hybrid 3D-printed mold and o-ring seal design along with an epoxy-filled volume for the circuit board components and an external clear glass viewport (US Patent #16/920,577) (Image credit: Brennan Phillips).
The lab uses a pressure tank to simulate deep sea environments. Once Phillips and his students settled on the two-part design with epoxy, they put the parts into a pressure chamber, increasing the pressure to simulate a true deep-sea environment. “It was a total experiment and I started sending them down, and it was farther than we ever thought, thousands of meters even,” says Phillips.
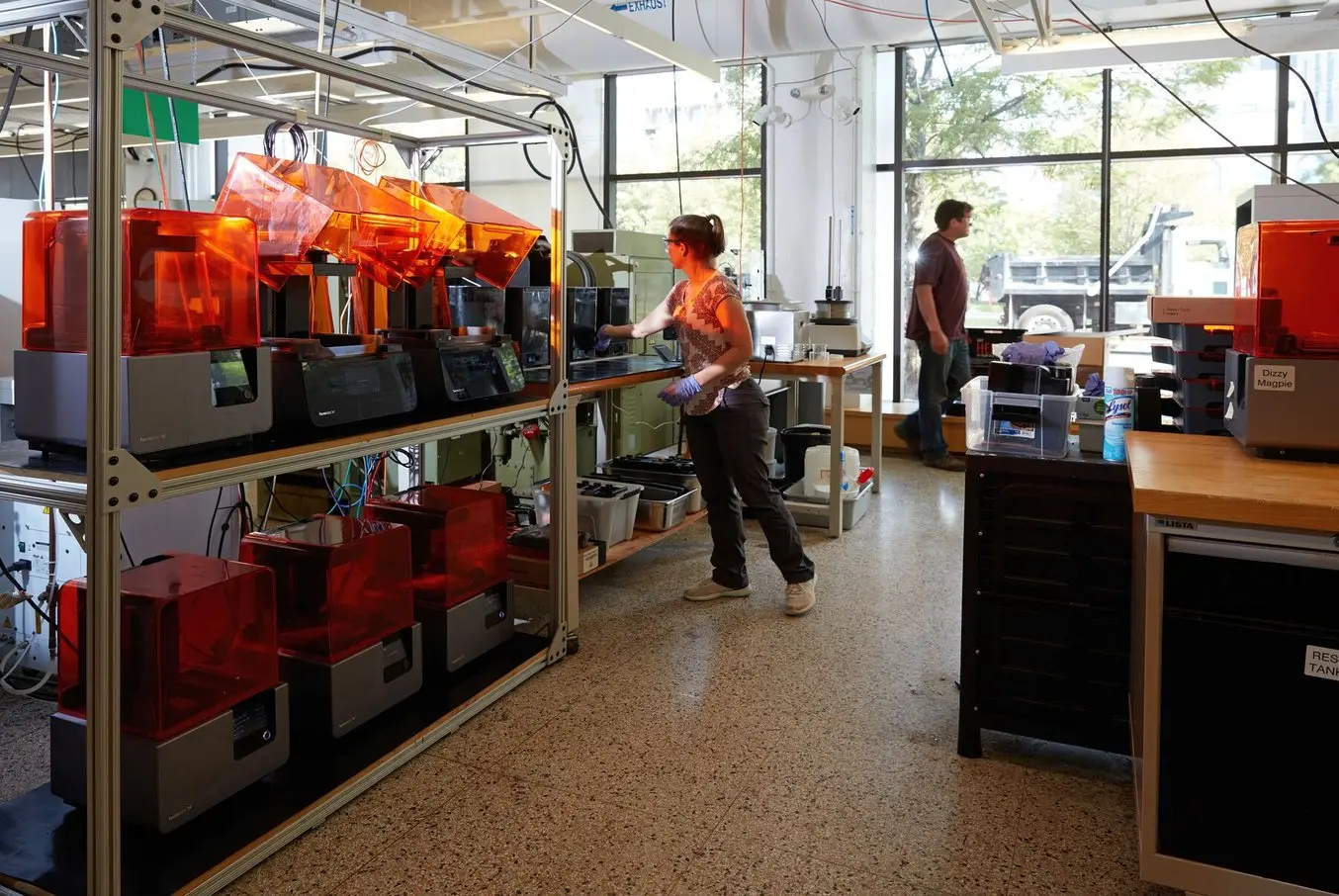
Special Pricing for Educational Institutions
Accredited educational institutions are eligible for special pricing, including a 10% discount on printers, hardware, and select accessories, and free Open Material Mode. Contact Formlabs or an Authorized Reseller to verify your eligibility.
Why SLA is the Perfect Fit for Deep Sea Robotics
When evaluating different 3D printers, accuracy and material properties were top of the list for Phillips’s lab. The isotropic nature of SLA 3D printed parts means that they aren’t porous, and won’t leak water as fused deposition modeling (FDM) printed parts might. The smooth surface finishes of SLA parts also ensure that functional assemblies like the two-part cylindrical enclosures can fit together without a rough surface causing air gaps. Accuracy and high resolution also contribute to that watertight nature—incredibly tight tolerances and small feature size allow users to print screw threads directly into the material, and Phillips’s lab does this for both the two-part enclosure and the screws that act as further attachment security.
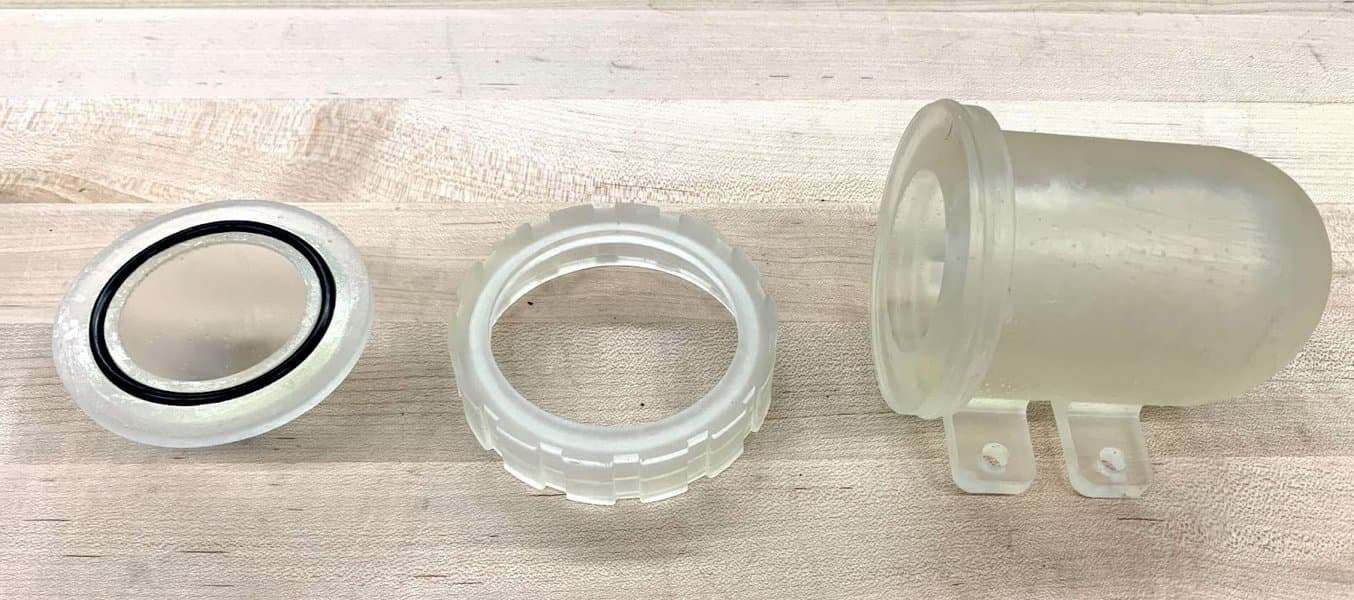
A complete 3D-printed pressure housing assembly capable of protecting electronics from seawater at depths exceeding 1000 meters. The o-ring seals are directly printed into the parts and the enclosure is sealed using a hand-screwed bezel. Photo and design credit: Breanna Motsenbocker
“You need the hundred percent in-fill of SLA parts—with FDM you can maybe get an IP rating out of them, but you can’t sustain it past a couple meters of pressure. Second, you need resolution, so that the O-ring between the two parts makes a complete seal. These parts come right out of the printer, and we maybe sand it a little bit, but then we orient them so the critical surfaces are smooth, and we get perfect seals,” says Phillips. “And the third reason is that the material properties of the SLA materials are way better—there's generally no comparison. They're far better in terms of yield strength. All the modulus' are just better than any other material we’ve found.”
The accuracy and the material availability of Formlabs’ printers have allowed the main work of the lab, the waterproof deep sea enclosures, to flourish, both on land and on sea. In January 2020, Phillips and his students published their process for 3D printing using a stabilization rig for the Form 2. They were able to print the same enclosures with no measurable differences from their land-printed counterparts, meaning that these devices can be printed and deployed on location, on ships across the world. Furthering the lab’s mission of democratizing deep-sea science, this paper provides the proof that these important tools can be manufactured inexpensively and locally.
Adopting the Form 3L
When Formlabs announced the introduction of the Form 3L, Phillips and the lab were among the first to dive right in. “We were some of the first Form 3L adopters,” Phillips said. The large format size of the Form 3L has allowed them to experiment with larger underwater designs and improve other lab functions through innovative research tools.
To deploy these enclosures and other monitoring devices underwater, the lab has to use and maintain thousands of feet of thin fiber optic cable. To avoid tangles or knots, they first used repurposed bike wheels to guide the fiber optics over the side of a boat. With a large format SLA printer on hand, however, they were able to prototype designs to reduce the size and improve the performance of this process.
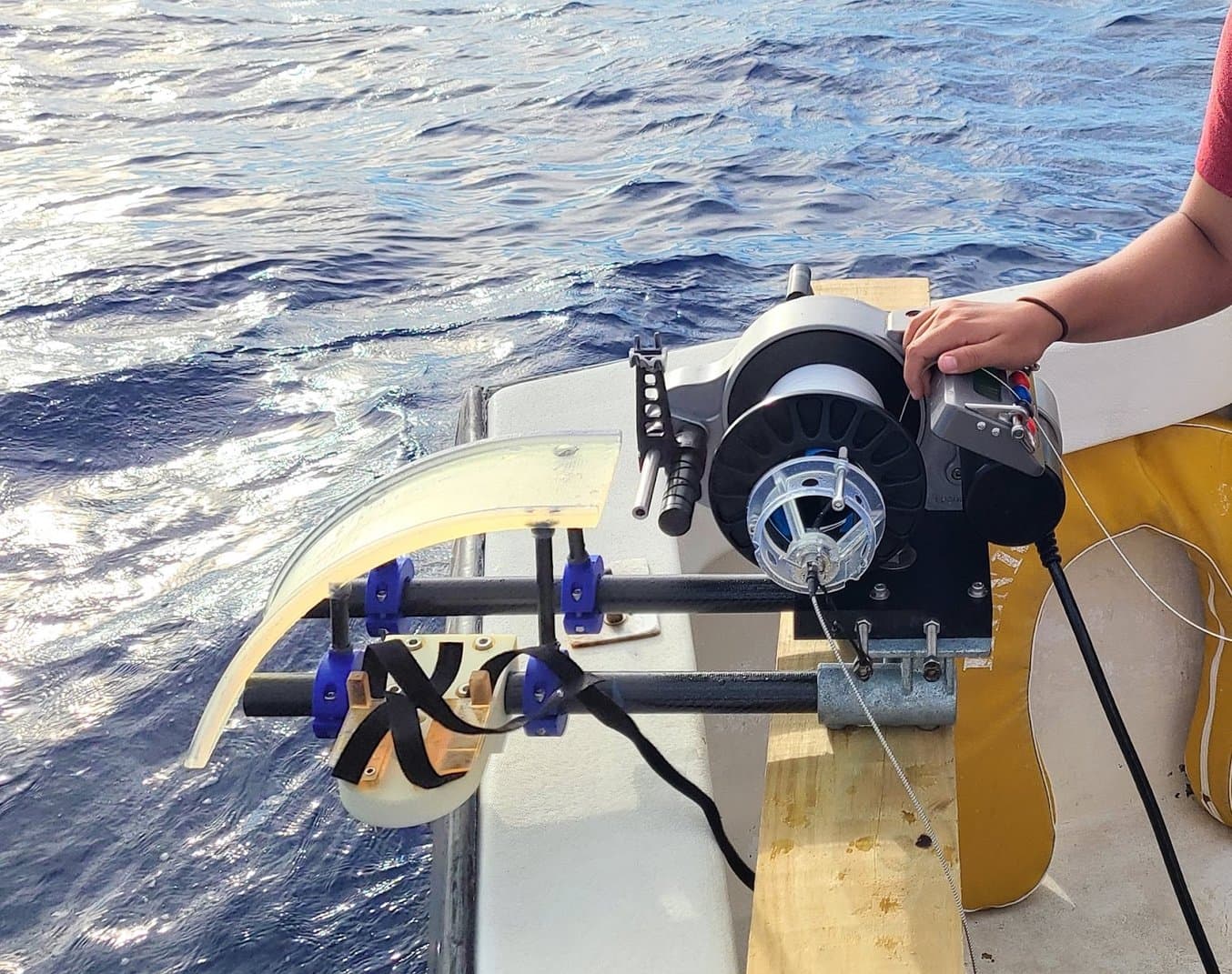
A 3D-printed ‘slide’ helps smoothly guide fiber optic cables over the side of a boat without tangling or breaking them. (Image credit: Brennan Phillips)
“For this fishing line, we don't want to use a turning sheave or a wheel. We needed a slide. So we’ve printed about three or four iterations of this slide. It’s big, it’s nice and smooth, and that smoothness is helpful with the thinner lines,” says Phillips. The slide printed on the Form 3L in Clear Resin reduces the time it takes to carefully stow away the fishing line for reuse, and reduces the number of times they’ll need to replace their equipment.
Fiber Optics Innovations
Fishing line, though laborious to rewind, isn’t the most delicate of materials. Fiber optic cables, however, cannot be treated the same way, and are much more expensive when broken. Phillips’s lab, in partnership with Nautilus Defense LL based in Pawtucket RI, pioneered the invention of a new type of fiber optic fishing line, or FOFL (US Patent Pending). “Fiber optics gives us ethernet, live feed video, that kind of stuff. It's very hard to do that with copper cables over long distances. So that exists now, it didn't exist before—the fiber optic fishing line,” says Phillips.
But the fiber optic fishing line wasn’t quite usable on its own—it needed a mechanical termination point so that you could pull on it without breaking the fiber optic core. Because fiber optic cables can’t be knotted or manipulated in the same way as other, more durable lines, the lab had to invent a fixture for the end of the cable.
Using a 3D-printed part with tight tolerances achievable with Formlabs’ high resolution SLA printers, the load-bearing external braids of the fishing line can be separated from the fragile fiber optic core. Using injected epoxy, the braided line adheres to the 3D printed fixture, and the fiber optic passes through into a metal furcation tube, which can connect to the computer to receive the information that the fiber optic is carrying.
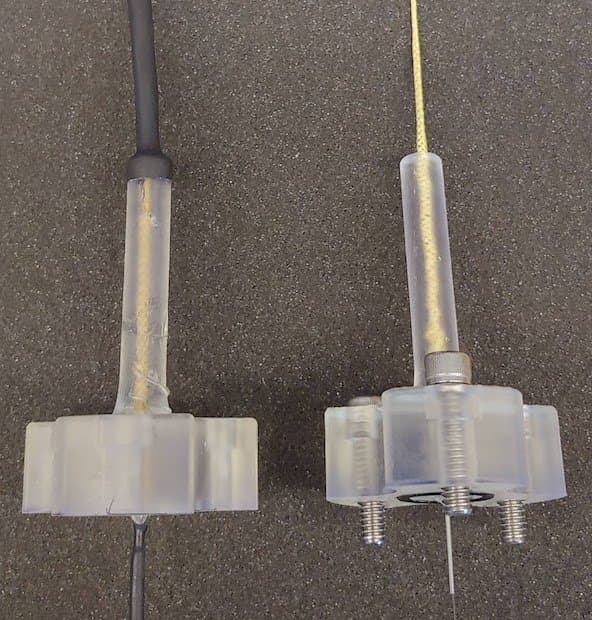
SLA-printed parts are used as mechanical terminations for “fiber optic fishing line” or FOFL (US Patent Pending), separating the load-bearing external braid from the delicate fiber optic core. Image credit Brennan Phillips
“This type of attachment is very strong, it’s resistant to at least one hundred pounds. We filed for a patent and we also made it published as open access,” says Phillips. “Without 3D printing, in a normal manufacturing process, these could cost $3,000 or $4,000 each time, and we went through several iterations. I don’t think anyone did this because the path to production was too expensive. It’s the combination of rapid prototyping methods like the Formlabs printers and the new fiber optic line that enables new ideas like this,” says Phillips.
3D Printed Lowering Seals at Lower Costs
Before 3D printing, these tools were costly to develop, deterring researchers from making necessary design changes and preventing underfunded programs from developing them at all. The Undersea Robotics and Imaging Laboratory is part of a global ‘deep and cheap’ movement—an effort to democratize science and open up access to these technologies, creating a better understanding of the oceans that surround us. “I started 3D printing end caps that had o-ring seals integrated into them, and it worked. If you machine this, it costs hundreds if not thousands of dollars, and the drawings have to be spot specific. With these printers I can print out three or four and get the fit just right, for maybe $50 of material,” says Phillips.
The lab team hasn’t limited themselves to printing only end-use parts; using Clear Resin, they’ve locked down a successful workflow for printing molds as well. The end result is an optimized way to splice underwater cables quickly using 3D printed molds.
Diverse Use Cases
In Phillips’s lab, the Formlabs printers are being used to prototype, create end-use products, rapid tooling, jigs and fixtures, and even medical devices. Even in a small research lab, the applications and opportunities are continuously being pushed forward by the innovative spirit of Phillips and his students.
During the COVID-19 pandemic, Phillips and his students realized they had the capacity to make a real difference in Rhode Island’s pandemic response. Through extensive testing and exhaustive research, the lab was able to publish chemical off-gassing results of the Formlabs Surgical Guide Resin for use in 3D printed ventilator parts. They accomplished the feat of not only scientific publication, but also submitted for FDA and Emergency Use Authorization (EUA) approval.
“During the pandemic, there was a massive maker effort, and we wanted to really dial in and help where we could do the most good. Because of the quality of these printers and because Surgical Guide Resin existed, we could contribute at a higher level,” says Phillips.
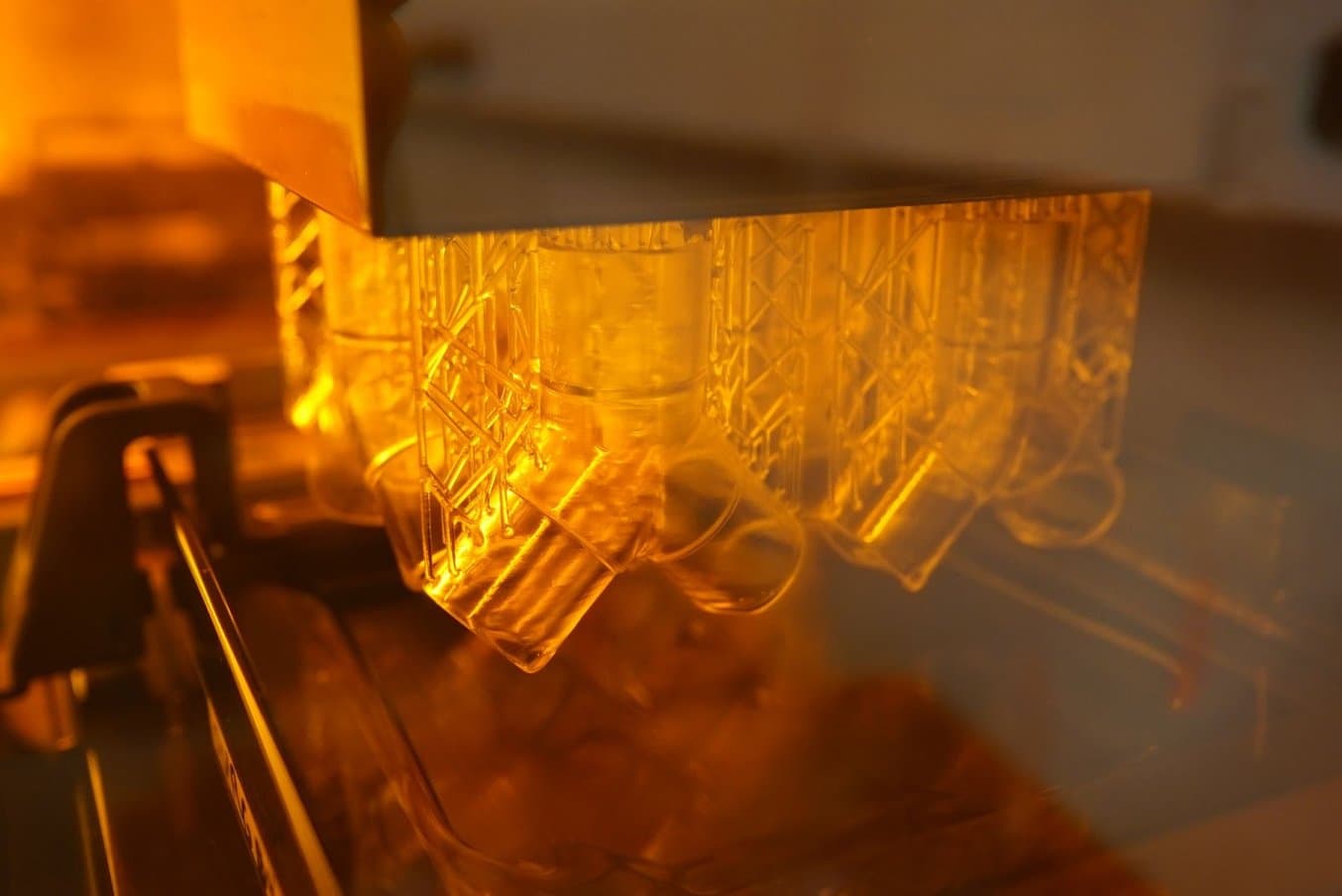
Ventilator “Y-splitter” parts, designed in collaboration with researchers at Brown University and the Rhode Island Hospital, are 3D-printed using Surgical Guide resin during the early stages of the COVID-19 pandemic. Photo credit: Brennan Phillips
Democratizing the Deep
The lower cost of manufacturing these parts is not just beneficial to the lab’s budget, it also means that learning (and the inherent failure stage of trying new ideas) does not prohibit students from access to these machines. Undergrad students designing parts for the first time can access the technology and learn 3D printing, without fear of any mistakes costing precious resources.
Sophomore URI students have the opportunity to design and 3D print pressure housings every year, contributing to the research at the same time as learning valuable new CAD and 3D printing skills. “Before these 3D printers, students wouldn't design or make their own underwater housings until they were a graduate student, or in the industry and could take all the training, because the cost and access were so restrictive. But these printers open doors— I had a high school student make a pressure housing,” says Phillips.
These opportunities aren’t limited to just college students in America—Phillips is part of an international community looking to improve access and affordability of deep sea research tools in underdeveloped coastal countries around the world. “We’re working on capacity development for nations that want to do their own exploration in the deep ocean. Money is a restriction, training is a restriction, but these methods have the potential to really open that up, and democratize deep sea exploration,” says Phillips.
1 https://oceanservice.noaa.gov/facts/exploration.html
2 Brennan T. Phillips, Josh Allder, Grady Bolan, R. Sean Nagle, Allison Redington, Tess Hellebrekers, John Borden, Nikolai Pawlenko, Stephen Licht,
Additive manufacturing aboard a moving vessel at sea using passively stabilized stereolithography (SLA) 3D printing, Additive Manufacturing, Volume 31, 2020, 100969, ISSN 2214-8604, https://doi.org/10.1016/j.addma.2019.100969.