The Digital Factory Podcast #11: How Jabil Circuit Adopts New Manufacturing Technologies with John Dulchinos
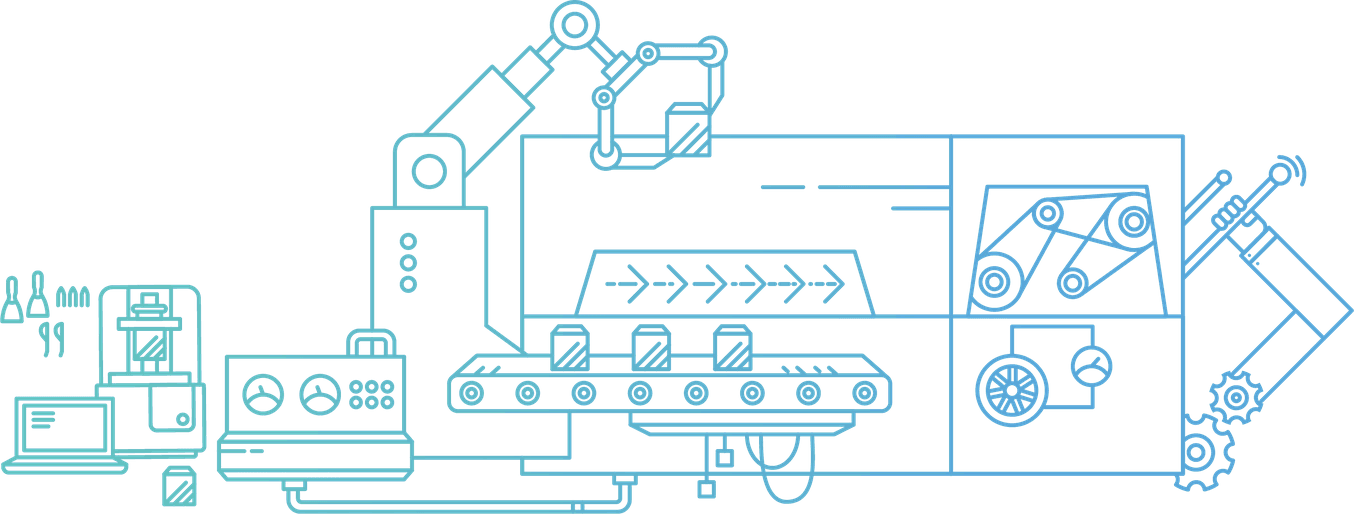
Jabil Circuit is a $20 billion contract manufacturer that produces everything from specialized medical devices to mobile phone accessories. Since Jabil doesn’t own any of the brands that roll off its lines, the company’s entire value is in its ability to spin up multitudes of new manufacturing processes that meet new requirements from its clients.
In this episode of the Digital Factory Podcast, Jon Bruner speaks with John Dulchinos, Jabil’s Vice President of Digital Manufacturing. He’s responsible for evaluating new manufacturing technologies and finding ways to apply them in Jabil’s supply chain, and he’s got hard numbers and real experience with many technologies that are still in their infancies.
Dulchinos is featured in The Digital Factory Report, an overview of recent advances in artificial intelligence, additive manufacturing, and advanced automation, and a look at how those technologies are transforming the business of making things. Download the report for free and watch Dulchinos’ presentation from the Digital Factory Conference at digitalfactory.xyz.
In this episode:
- The importance of ‘thinking big, starting small, failing fast’
- Strategy for scaling a new technology from prototyping into production
- The surprising cost-effectiveness of 3D printing: it used to be cheaper than injection molding for runs under 500-1,000 units, but the field has advanced so much that it’s now cheaper than injection molding for some runs up to 30,000 or 40,000 units
- Dulchinos’ current focus areas: additive manufacturing, new forms of robotics and automation, and interconnection between tools and factories
- Dulchinos’ favorite tools: Henckels kitchen knives
On 3D printing:
“Additive is a really interesting solution set. At its core it’s just another manufacturing process…But on the other side, additive has the potential to really disrupt how business is done. The ability to produce product without tooling and fixturing really opens the door to solving a wide set of problems in a completely different way.”
On radical changes to the product development process:
“Everything you’re taught [as a product manager] is to take the widest set of markets and pull them together into something you can satisfy with the minimum set of SKUs. 3D printing flips that around and says, ‘you know what, the cost of producing 10 different variants is no more expensive than producing one variant at 10 times the volume…Once product management understands this way of thinking, it’s going to allow the world to think about products in far more segmented, more targeted ways.”
On the use of 3D printing for part consolidation:
“We’ve taken products that were 5, 10, 15 components—in one case 39 components—and we’ll reduce those down to one or two 3D-printed parts. So you eliminate all of those manufacturing processes. We call it moving from physical assembly to digital assembly. That’s where 3D printing becomes more disruptive, and not just another manufacturing tool.”
Subscribe to the Digital Factory Podcast on iTunes, Google Play, Pocket Casts, Overcast, or Stitcher