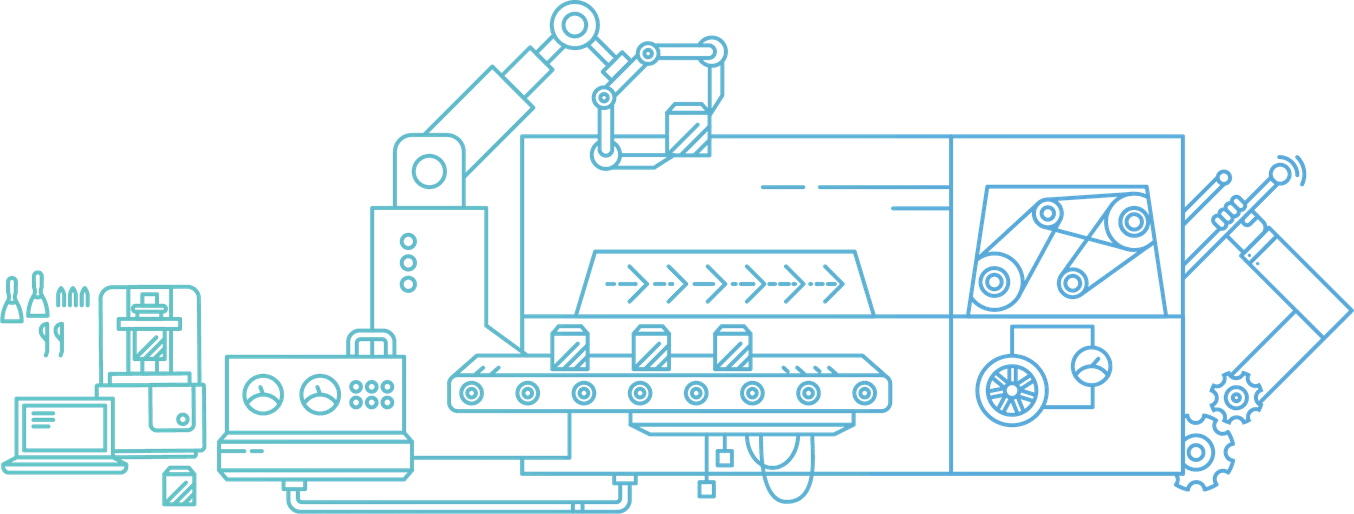
Most people who design 3D printed objects want them to keep their shape as closely as possible after printing, but an emerging field known as 4D printing aims to make objects that can reconfigure themselves after fabrication.
In episode 8 of the Digital Factory Podcast, we speak with Kristina Shea, professor of Engineering Design and Computing at ETH Zürich, on why self-assembly and 4D printing could be foundational design technologies in the very near future, with applications from aerospace to medical devices.
Kristina Shea is a keynote speaker at The Digital Factory Conference in Munich on May 14. Join executives and technical experts from companies like GE, BMW, Henkel, Carl Zeiss, Deloitte, EOS, HP, and SAP to learn strategies for digital transformation in manufacturing. Visit digitalfactory.xyz to see the program and register.
Play the full podcast to hear about:
- What goes into 4D printing, which is able to produce reconfigurable 3D-printed objects
- How computational design contributes to 4D printing, and how it’s changing the role of human designers
- Potential practical applications of 4D printing
4D Printing and the Future of Design

On The Fourth Dimension in “4D Printing”
“4D printing is about including time, or reconfiguration of 3D printed objects after the printing. The term was coined by Skylar Tibbits at MIT, and there are a number of us working in the field now. The time dimension comes in in terms of having an environmental impulse, for example, temperature change, but it could also be pressure or even vibration to change or reconfigure the object after printing.
A lot of the work started with anticipating geometric or shape change. You design the object in such a way that it's printed in one shape, and after, let's say, a temperature change, it converts into a second shape.”
On Designing Parts for 4D Printing
“We start with understanding the materials. That's the basis. For example, if we're using shape memory polymers, we have to understand what temperature we need to heat the object to change it. Second, we create simulation models so that we can design in a systematic way. Then we design the geometries and simulate the potential changes either using finite element or dynamic relaxation, and then we experiment. There is quite a bit of trial and error.”
On the “Grammar” of Generative Design
“My background started with what's called grammars—spatial grammars, graph grammars—as a way to generate designs. You can think about these as how one of our systems integrates with a CAD system. It's a type of generative system where you can control the style of design that you get out, whether it's a lattice, or a roller blade wheel, or some other object.
When we have a generative part that's using, say, spatial grammar, we can link that with optimization. We use a lot of different optimization methods. Sometimes we use GAs [genetic algorithms], but also simulated new link pattern search and gradient-based methods. It really depends on the problem. I think with generative design it's not the just GAs or just one method. It's a whole class of methods and it's always about what's appropriate for the problem.”
On the Designer’s Curatorial Role
“We can generate a whole number of designs. Once we create the method, we can generate 10 different designs, 20 different designs. The designer might not like them all, and then they can choose the ones they like, and also look at the trade-offs, like the visual properties compared to the structural performance.
It's this trade-off between engineering or manufacturing performance versus aesthetics or optics. Most designers I talk to generate a few designs, maybe three. We tell our students, ‘minimum three.’ But three is not a lot, especially if you think about 3D printing, because the space is so wide open for geometry and material variations.”
On the Biggest Challenge for the 3D Printing Industry Now
“Better materials, as always… They improve every year, but still I think we still need improvements, for example, reliability and time stability. Especially with the multi-material printing, they change over time.
The second would be more access to the printing process. I know some researchers do it and it's possible. I think the more we can make these printers not necessarily totally open, but have some ways to change and modify the process for everybody, the more that we'll get out of them.”
More Lessons from Manufacturing Innovators
The Digital Factory Conference is coming to Munich on May 14! Visit The Digital Factory for an archive of talks, podcasts, and more from experts at the forefront of digital manufacturing, and to register to attend our next event.
The Digital Factory Podcast is hosted by Jon Bruner, produced by Alyce Currier, and edited by Inky Stainsworth.