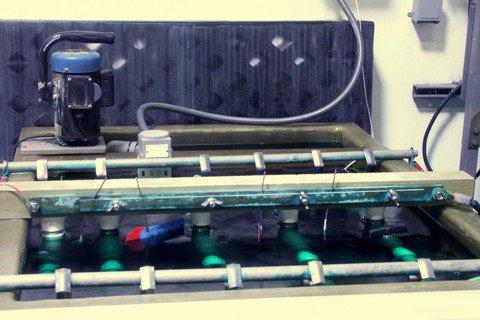
Prints on the Form 1 desktop 3D printer capture all of extraordinary detail of your model, and have an incredible smooth surface-finish. That means it's easy to push your prints further, whether it's making molds for casting or painting prototypes and models (shout-out to Brian Anderson for his awesome work!).
There are also finishing processes that not only change your prints' appearance, but also their physical properties. We're excited to give you a peek at the electroplated Form 1 parts from our friends at RePliForm.
Electroplating is a chemical process that uses an electric current to deposit a thin layer of dissolved metal ions on a surface. It takes place at low-temperatures, and can be used with a variety of substrates, making it perfect for prints from the Form 1. Not only does it add a beautiful metallic finish to parts, further bringing out surface detail, it also dramatically increases their strength.
The pictures don't do these justice. You have to hold them in your hand. They have the heft and feel of solid metal part. A prototype–like the watch-case above–feels like a finished product. And you'd never know that the ring was a 3D-printed prototype.
Our parts were plated by RePliForm, an electroplating service bureau, and we were blown away by the results. They plated the parts with layers of copper and nickel a few thousandth-of-an-inch thick (that's about as thick as a sheet of paper). By polishing and finishing them in different ways, they gave each a different surface-finish: polished, matte, or bronzed. Plating parts also dramatically increases their strength and durability. Though it depends strongly on part geometry and coating-thickness, electroplating a part can dramatically increase its strength and stiffness.
RePliForm is excited about the possibilities of working with Form 1 owners.