
The blazing speed and high accuracy of Form 4 made waves this spring, powered by our next-generation Low Force Display™ (LFD) Print Engine that redefines the industry performance standard and delivers unmatched reliability, print speed, print quality, dimensional accuracy, and materials versatility in one printer.
With Form 4L, we’ve applied the same groundbreaking technology to bring you a large-format printer that can print parts up to 35.3 × 19.6 × 35.0 cm, for highly accurate large parts and high-throughput production at speed.
While Form 3L was the first truly accessible large-format resin 3D printer available, users experienced long print times, delaying development and production. With Form 4L, we’ve addressed these pain points, bringing blazing speed, reliability, and cost-efficiency to large-format printing, so your projects can move at the pace of your team — all while leveraging the intuitive workflows, material versatility, and quality you’ve come to expect from Form 4.
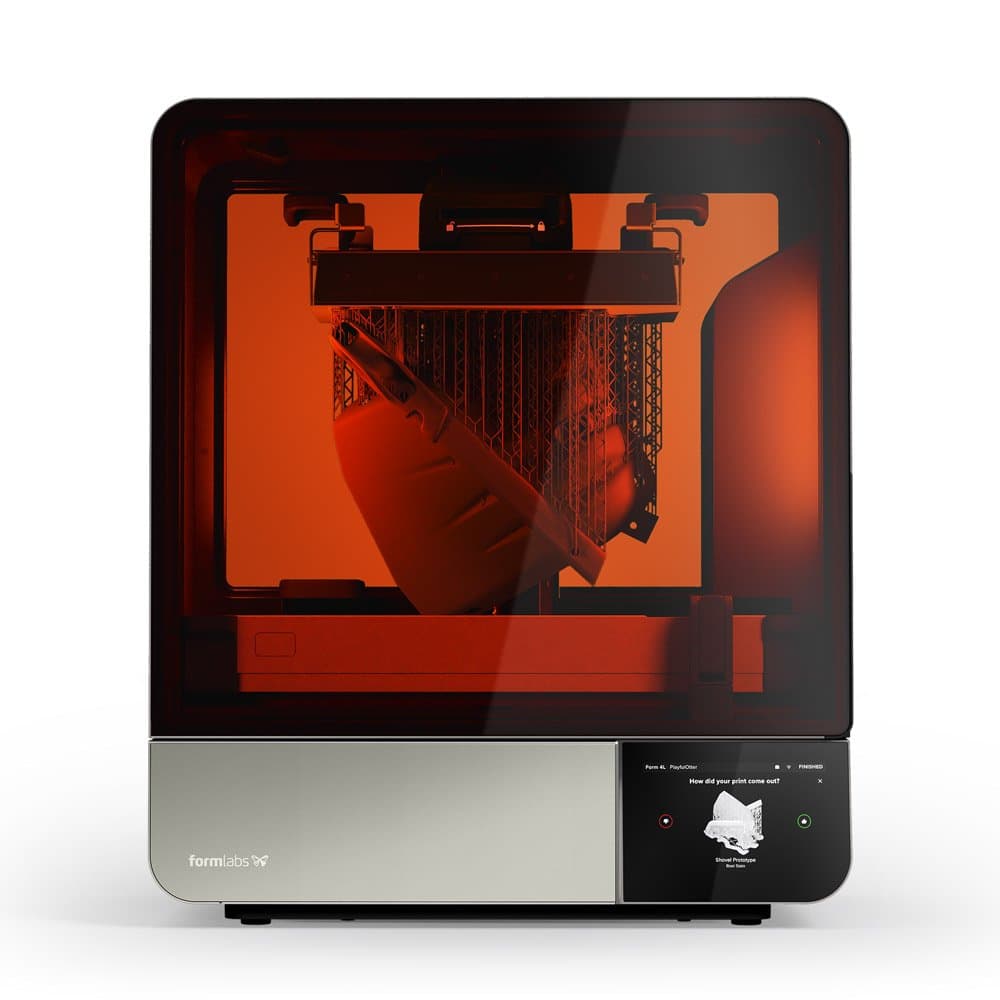
Product Demo: Form 4L
See how Form 4L, our next-generation large-format resin 3D printer, takes the speed, accuracy, and reliability of Form 4 to a completely new scale.
Powered by Low Force Display™ Technology
Form 4L is a masked stereolithography (MSLA) 3D printer, a photopolymerization process where a light source is selectively covered or masked by an LCD screen, and an entire layer of a print is exposed and cured. This results in vastly improved print speed, but often comes at the cost of surface finish, reliability, resolution, or hardware longevity. The technology of Form 4L solves these issues, for fast, reliable production of large parts with fine details, accuracy, and smooth surfaces.
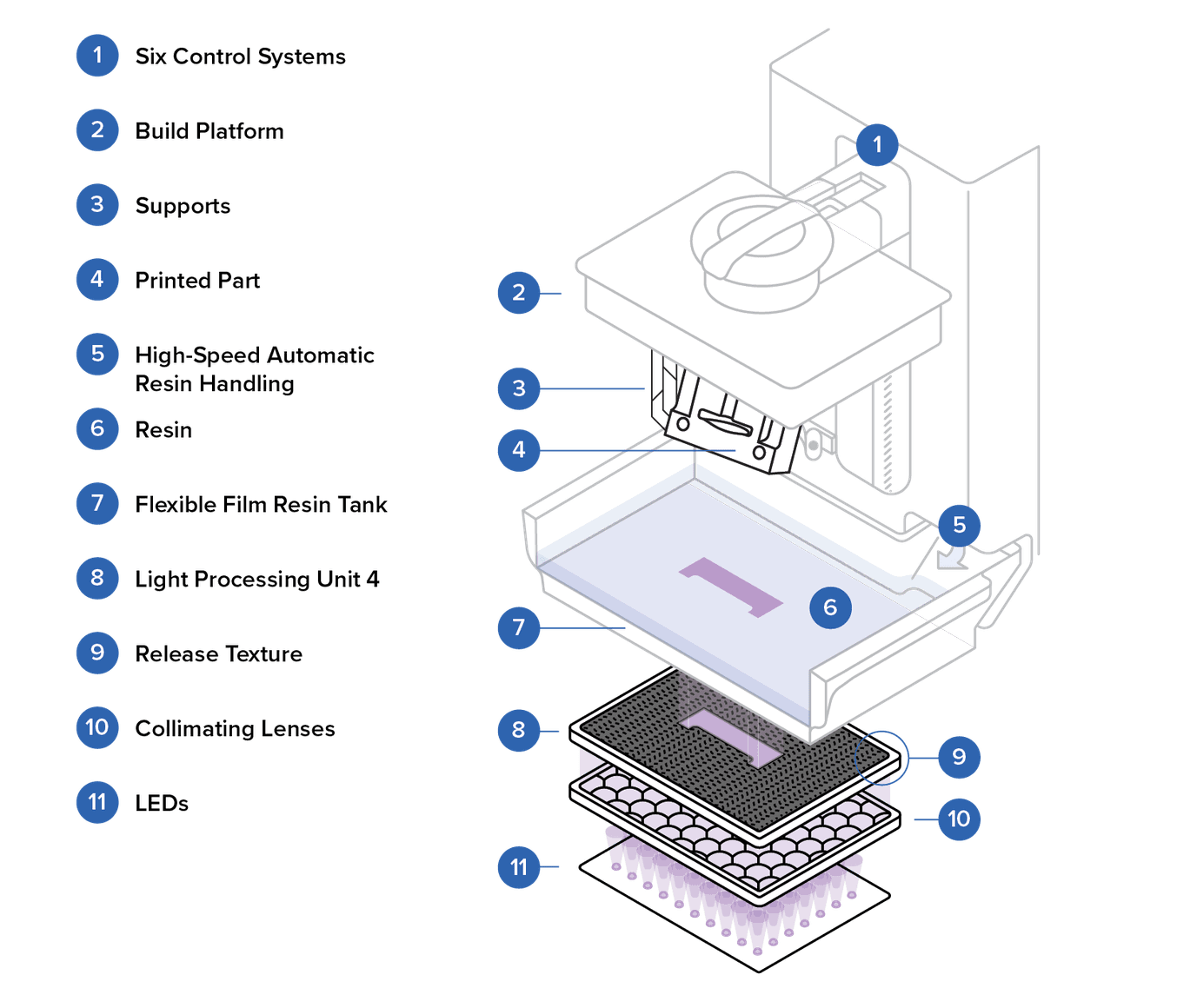
Form 4L is built on the same technological developments as Form 4.
Form 4L is built on the LFD Print Engine, at the core of which is the Backlight Unit, an ultra-high power light source of 145 LEDs and collimating lenses that deliver an optical power intensity of 16 mW/cm2. From here, the light passes through the Light Processing Unit (LPU) 4L, where it is formed into the shape of the printed layer using a series of polarizers, optical coatings, and a custom LCD screen, achieving blazing fast print speeds with excellent print quality and accuracy anywhere on the Build Platform.
The LPU 4L is engineered and manufactured for a long lifetime and reliable printing, delivering 600,000-1,900,000 layers of consistent print performance before replacement, depending on the material and layer height printed. If needed, the robust LPU 4L can quickly and easily be replaced.
Form 3L, as a stereolithography (SLA) 3D printer, uses lasers to trace each shape. By moving to MSLA and LFD, Form 4L achieves blazing fast speeds without compromising on print quality.
Dive deeper into the technology underlying Form 4 Series printers here.
Big Parts at Blazing Speed
Form 4L prints 2-4x faster than Form 3L, while offering 13% more build volume and a 6% larger maximum part length. This means that parts that might previously have been printed in multiple segments and reassembled can now be printed whole. Or, fit more small parts in one build for higher throughput.
Form 4L | |
---|---|
Maximum Speed | 80 mm/h with Fast Model Resin* |
Average | 30 mm/h** |
Range | 10-80 mm/h depending on material |
*Max print speed using Fast Model V1 Resin and 200 μm layer height. Based on actual print times from a collection of test parts covering common engineering, product design, manufacturing, and dental applications.
**Average print speed using 100 μm layer height, averaged across all materials. Print speed will vary depending on material, layer height, and part geometry.
Form 3L was already faster than large-format FDM 3D printers, but the technical innovations of Form 4L leaves them in the dust. Form 4L prints parts too big to fit in leading FDM printers, or fits larger quantities of batched parts for higher throughput — with most prints in under six hours. Printing the same parts with other 3D printing processes takes at least overnight, but often multiple days.
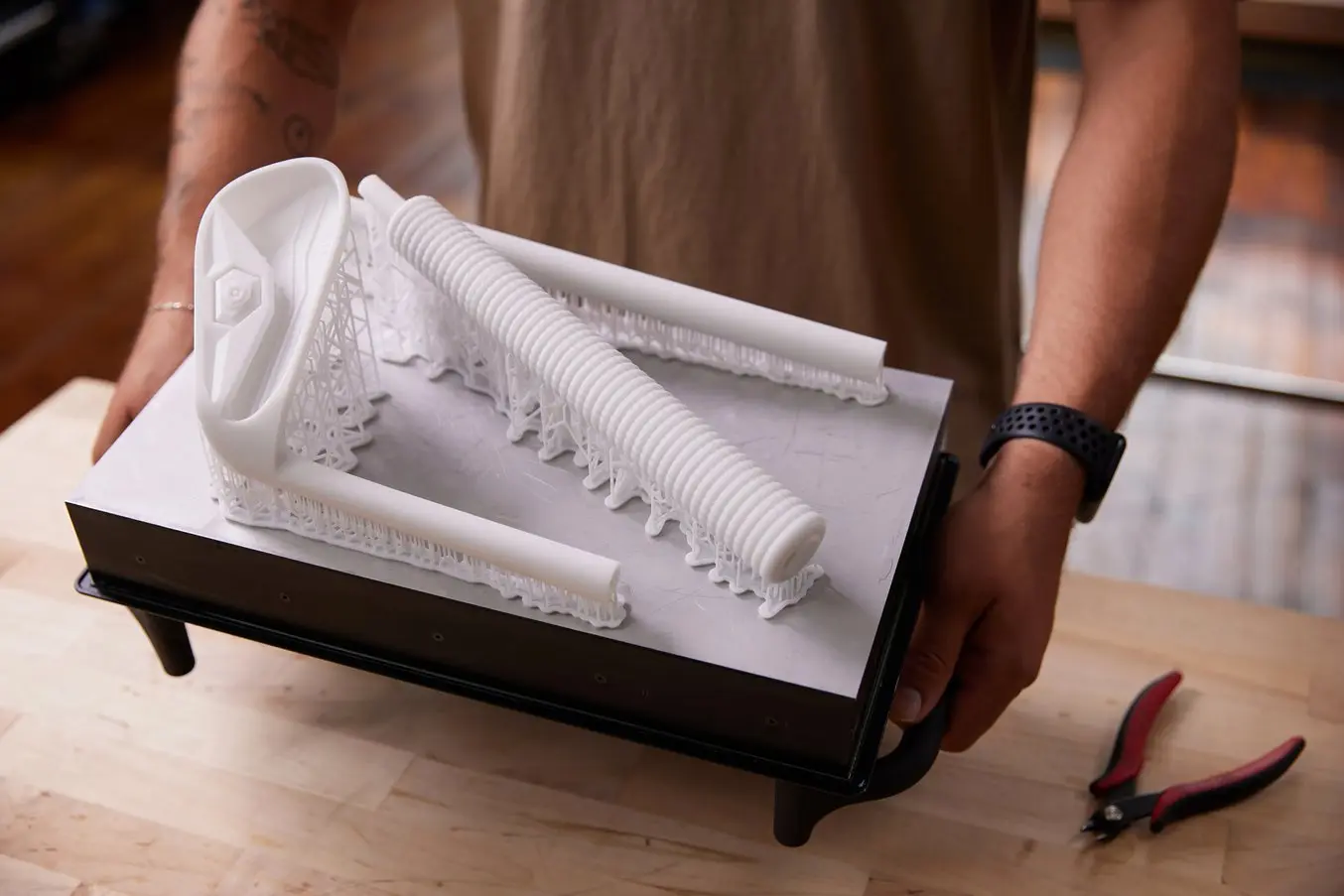
Mini Golf Clubs
Form 4L: 5 h 50 min
Form 3L: 17 h 17 min
Leading FDM: 10 h 38 min
Large-Format FDM: 68 h 34 min
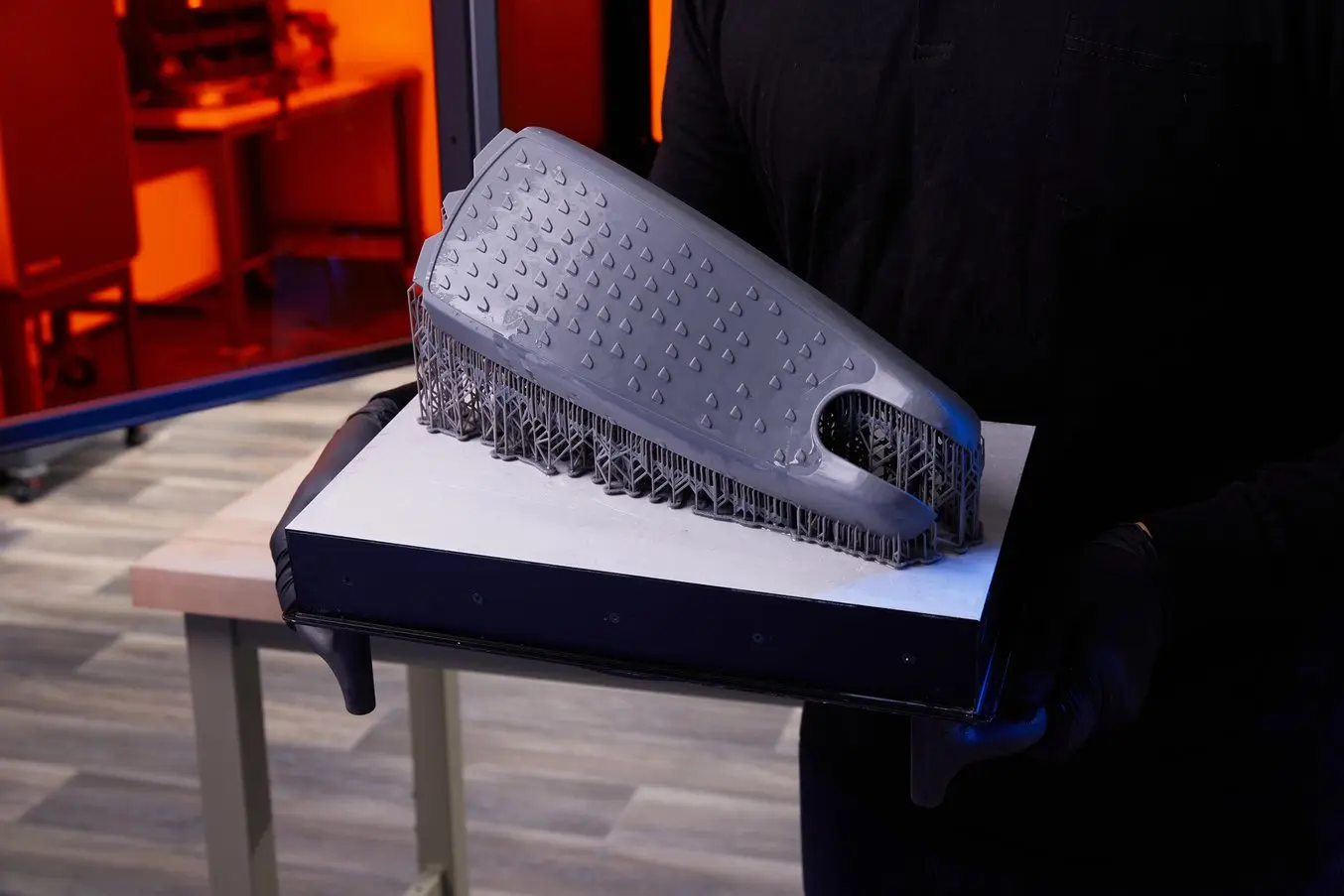
RadioFlyer Scooter Cover
Form 4L: 4 h 58 min
Form 3L: 18 h 47 min
Leading FDM: 12 h 43 min
Large-Format FDM: 76 h 48 min
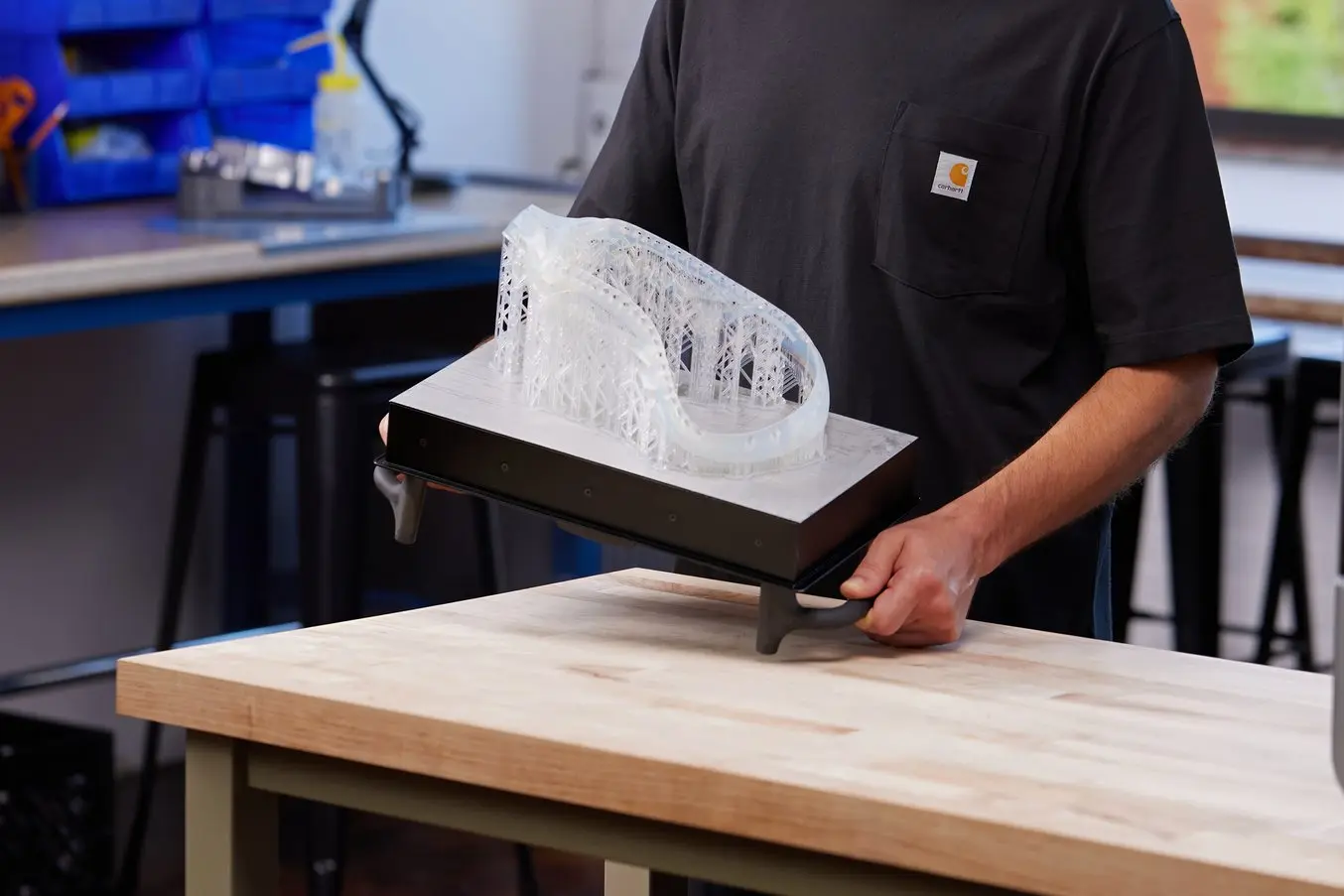
Lacrosse Head
Form 4L: 4 h 54 min
Form 3L: 21 h 57 min
Leading FDM: 14 h 24 min
Large-Format FDM: 62 h 32 min

Stingray Seat
Form 4L: 2 h 37 min
Form 3L: 21 h 6 min
Leading FDM: Part too big
Large-Format FDM: 42 h 3 min
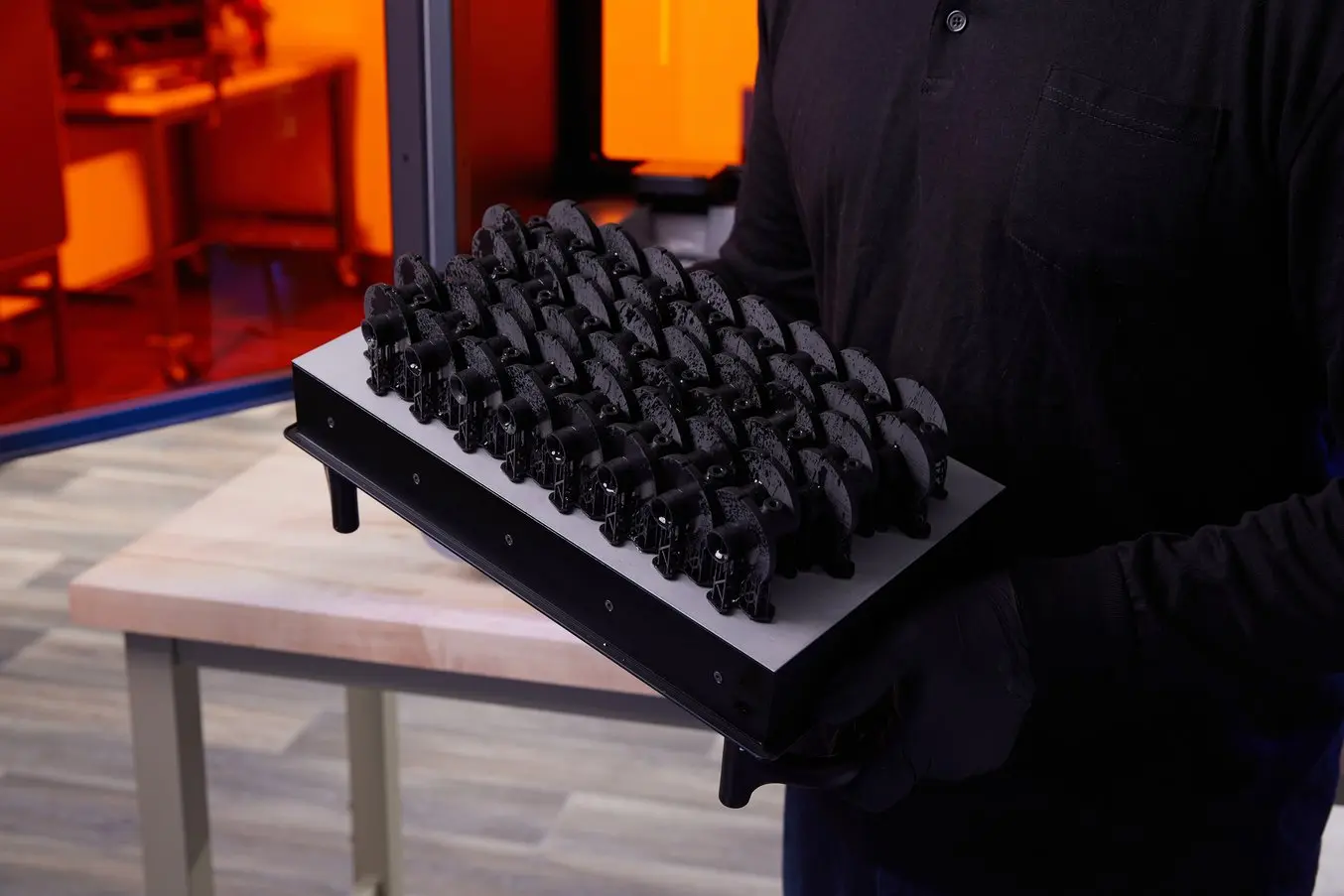
Back Holders
Form 4L: 4 h 12 min to print 50
Form 3L: 22 h 52 min to print 50
Leading FDM: 12 h 48 min to print 20
Large-Format FDM: 86 h 49 min to print 22
Note: Leading FDM print times were calculated on a Bambu X1C and large-format FDM print times were calculated on an Ultimaker S7.
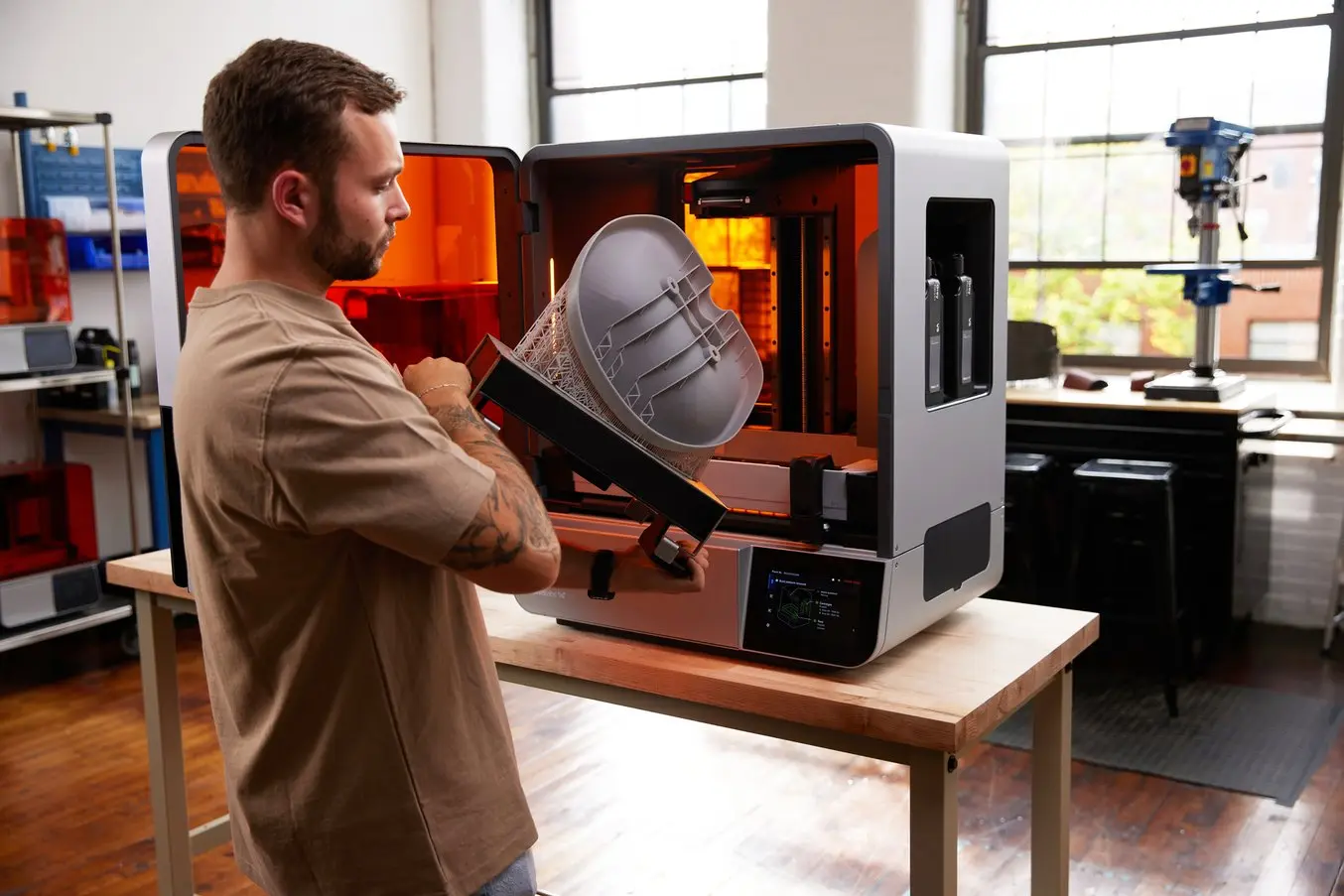
RadioFlyer’s Stingray seat is too big to print on a leading FDM printer, but can be printed on Form 4L in Fast Model Resin in two hours and 37 minutes. This is 8x faster than printing the same part on Form 3L and 16x faster than printing on a large-format FDM printer.
Print time and cost will vary depending on part geometry, material, layout, orientation, and layer height. However, Form 4L’s LFD Print Engine will significantly reduce print time for comparable parts. Plus, the bigger build platform and larger printer volume of Form 4L can fit parts that would formerly have needed to be printed in two batches or would require additional workflow time during finishing to assemble multiple pieces into one part.
Reliable Production
Speedy prints propel innovation, but only if the print is successful. Failed prints cost time, waste resin, and interrupt workflows. This is compounded for large format 3D printing, as large builds can be more prone to failure and the costs of these failures are also higher.
Printing larger parts is harder. User feedback from Form 3L overwhelmingly calls out reliability as the biggest pain point. As Agostino LoBello at Radio Flyer says, “There was a lot of baggage with Form 3L, but with Form 4L being more accurate, faster, and more reliable, I can trust this machine, and we’ll only use it more over time.”
"We’ve pushed Form 4BL to its limits, and it hasn’t failed a single print. Its reliability under pressure has been outstanding."
Brian Albers, 3D Printing Engineer, St. Louis Children’s Hospital
The technological improvements to Form 4L have directly addressed reliability. Beta testers and our in-house engineers put hundreds of prints to the test, pushing Form 4L to the limit. In addition to the LFD Print Engine, systems inside Form 4L work to ensure fast, accurate, and reliable prints.
Reliability starts at the factory, where every printer undergoes a 60-point calibration and quality control inspection. Once you start printing, systems and smart sensors inside Form 4L work to ensure reliable prints. Six integrated sensors precisely control resin temperature, resin level, print forces, and print status. High-speed conduction resin heating with infrared temperature sensing auto-heats resin to 25-45 °C (77-113 °F), depending on the material.
A mechanically coupled mixer is both faster and more reliable, able to mix resins with higher viscosities, unlocking high-performance materials. More reliable and faster cartridge dispense prevents pauses in printing, for uninterrupted printing in the projected time.
A Z-Axis Force Sensor automatically optimizes print quality and print speed based on part geometry and selected material. An integrated camera enables you to monitor your prints from anywhere while preventative maintenance reminders keep Form 4L up and running reliably.
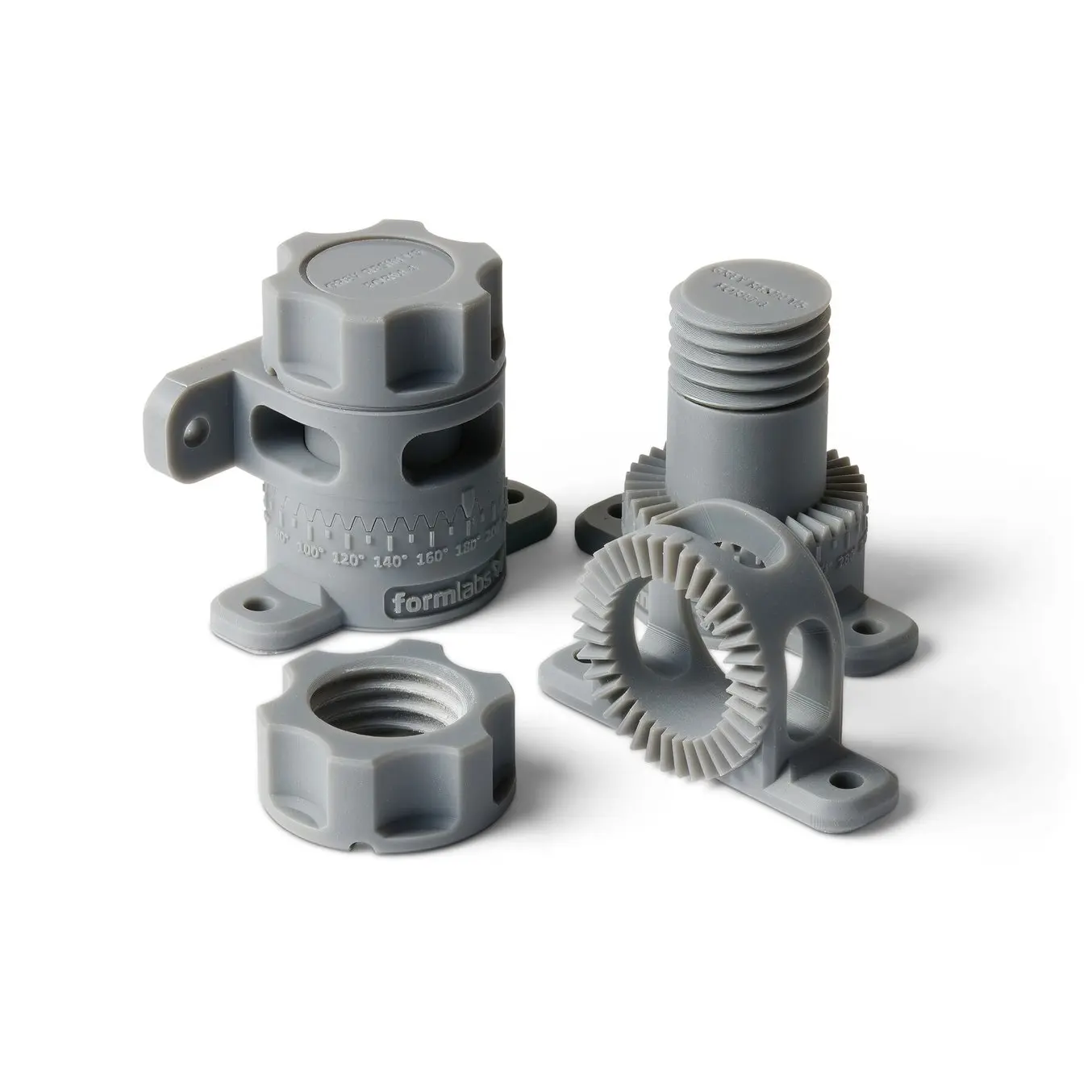
Request a Free Sample Part
See and feel Formlabs quality firsthand. We’ll ship a free 3D printed sample part to your office.
Form 4L vs. Form 3L at a Glance
Form 3L empowered users to print large parts while leveraging our versatile materials catalog and the fine surface finishes of SLA 3D printing. With Form 4L, we’ve redesigned and re-engineered our large format printer, cutting down print times for large prints to less than a workday—while achieving finishes that rival that of injection-molded parts.
Form 4L | Form 3L | |
---|---|---|
Technology | Masked Stereolithography (MSLA) | Stereolithography (SLA) |
Printer engine | Low Force Display™ (LFD) | Low Force Stereolithography™ (LFS) |
Key components of the print engine | Backlight Unit Light Processing Unit 4L (LPU 4L) Release Texture Redesigned Flexible Film Resin Tank Intelligent Control Systems High-Speed Automatic Resin Handling | Laser Light Processing Unit (LPU) Flexible Film Resin Tank Automatic Resin Handling |
Light source | Backlight Unit (LEDs) and collimating lenses | Laser |
Light processing unit | LCD and Release Texture | Galvanometer, mirrors, spatial filter |
Build volume | 35.3 x 19.6 x 35.0 cm 13.9 x 7.7 x 13.8 in 24.2 liters | 33.5 × 20 × 30 cm 13.2 × 7.9 × 11.8 in 21.4 liters |
“The speed has been the big difference maker, but also it’s been more dimensionally accurate. Right now, we’re successfully printing a box the full size of the build volume – when we tried to print that size on the Form 3L, the box and its lid wouldn’t match up. Before Form 4L we would rather CNC it on our router or piece it together with SLS.”
Agostino LoBello, Product Development Engineer, Radio Flyer
Unlocking Access to 37+ Industry-Leading Materials & Open Material Mode
The new technology of Form 4L unlocks the ability to print 23+ industry-leading Formlabs materials, including six new resins updated to provide higher performance, richer color, crisper features, and faster printing. To print with Formlabs’ biocompatible resins, Form 4BL is available with 37+ materials.
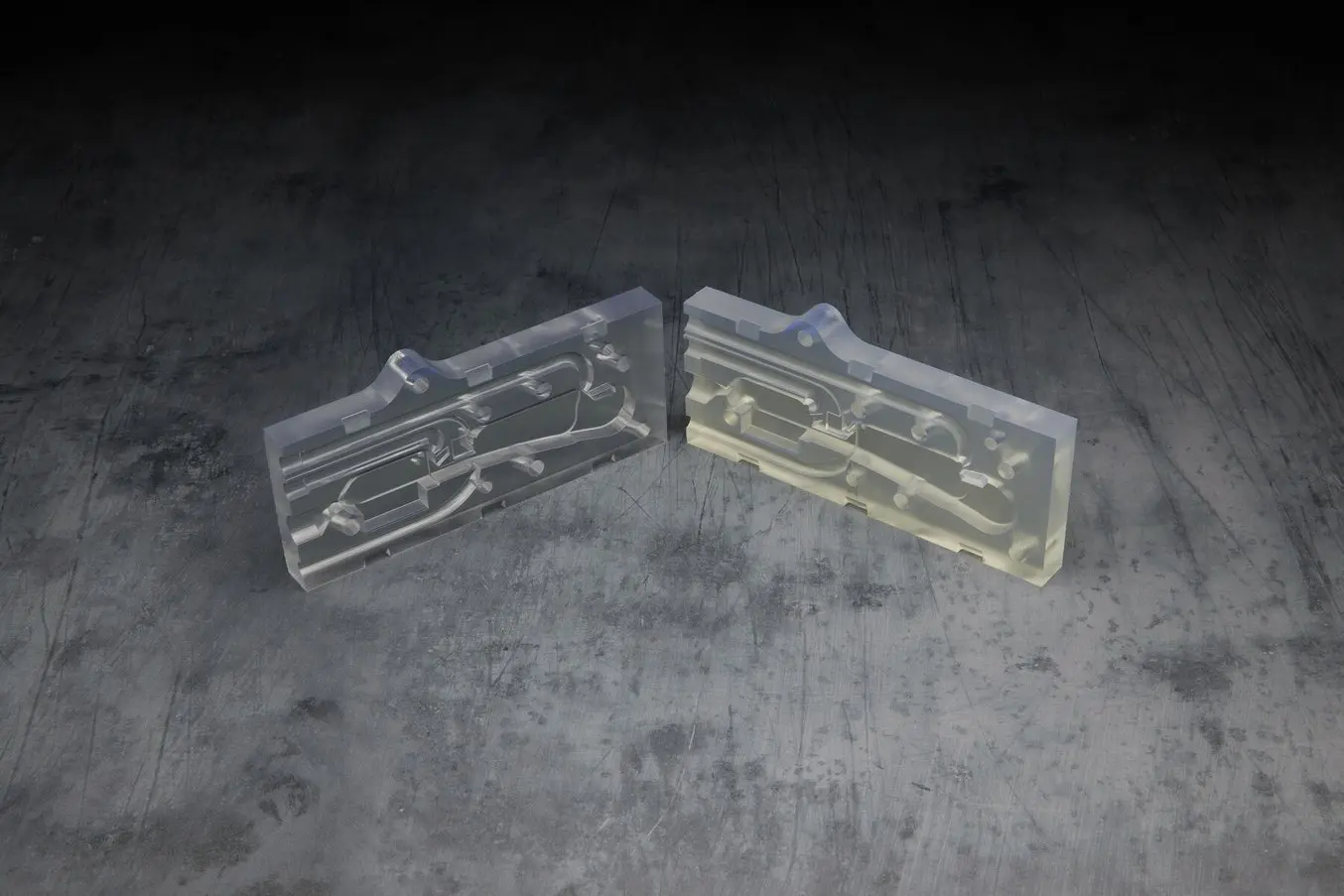
Clear Resin V5, for Form 4 generation printers, (left) is clearer and more transparent than Clear Resin V4 for Form 3 generation printers (right).
A next-generation resin cartridge with 5-10x faster filling (depending on material viscosity) means prints start faster. Plus, cartridges have been designed for 63% less waste and 30% less shelf space. Like Form 3L, Resin Pumping System (RPS) is available for Form 4L, providing 5 L of resin to the printer to enable less frequent cartridge changes and unlock discounted resin prices for time and cost savings.
Large prints don't have to mean high costs. General Purpose Resins for Form 4L are priced at least 30% lower than resins for Form 3 Series 3D printers, and consumables like resin tanks are longer-lasting, more durable, and, if replacement is needed, lower cost.
Formlabs' open ecosystem is available also for Form 4L. Print with third-party materials using Open Material Mode (OMM) or leverage the powerful hardware and nuanced Print Settings Editor to develop custom resins. These tools empower researchers and expert users to push the boundaries of 3D printing, advancing resin development and application-specific material properties.
Explore the Formlabs material library or request a free sample part to evaluate our resins for yourself, or buy OMM to start printing with third-party materials.
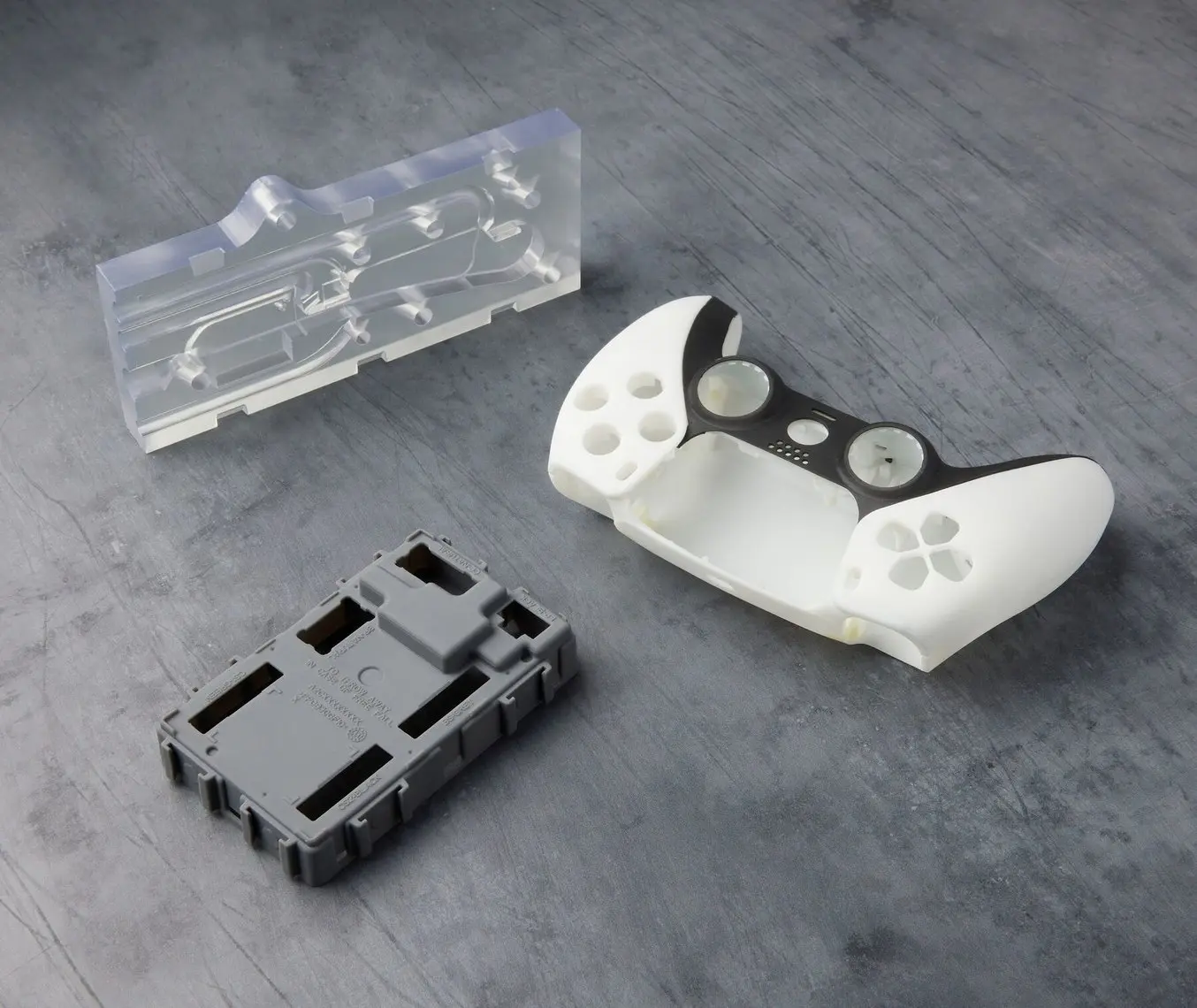
Form 4 Materials Guide
Learn more about all the high performance materials available on Form 4 and how to leverage the right material for your application.
Upgrade Your Productivity
Form 4 set a new standard for accurate and precise printing at blazing speed. Form 4L takes this to the next level, revolutionizing the throughput potential of MSLA production, and raising the bar on part size. Large prints are now possible in under six hours, so you can have a large prototype in-hand by the time you’re done with lunch, or a full build by the next morning.
To start printing large parts at blazing speed, buy Form 4L now. Watch the webinar to learn more about Form 4L, or contact sales to discuss how Form 4L can power your innovation.