One year ago, Formlabs officially started shipping the Fuse 1. For the first time, businesses had access to affordable, industrial quality selective laser sintering (SLS) 3D printing right on their benchtop.
The Fuse 1 and its accompanying post-processing and powder recycling station, the Fuse Sift, have garnered global attention for their ease-of-use, industrial-level part quality, and accessibility. With just one year on the market, there are more Fuse 1 printers used globally than any other SLS printer.
In this review roundup, we’ll take a look at what our colleagues in the additive manufacturing industry are saying about the Fuse 1 ecosystem.
3D Printing Industry
“Bouncing off its market-leading position in the SLA sector, Formlabs has made one hell of an SLS 3D printing debut. The Fuse 1 truly delivers on its promise of an accessible and cost-effective SLS experience, bridging industrial-grade print quality with a nifty, scaled-down footprint.”
3D Printing Industry
The experts at 3D Printing Industry traveled to Formlabs’ partner in the UK, SolidPrint3D, to put the Fuse 1 and Fuse Sift through their paces. At every step of the workflow, they commented on the efficiency of the complete system. Beginning with the virtues of the machines’ compact size and limited infrastructure requirements, 3D Printing Industry then commented on the intuitive interface on both the Fuse 1 printer and the Fuse Sift.
“Much like the Fuse 1, the Fuse Sift’s user interface is expertly crafted for simplicity and elegance, all while maintaining its comprehensiveness. The system as a whole is very efficient and we had a blast using it.”
3D Printing Industry
When explaining the print preparation process, 3D Printing Industry again noted the overall efficiency, saying, “the PreForm slicer is fast, bug-free, and responsive, just how we like it.”
The bulk of the review was a quantitative and qualitative analysis of twelve different parts. The first set of three parts were circular trajectories, designed to test the repeatability and dimensional accuracy of the printer. Using precise measurement tools, they found that “the average standard deviation also came in at only 0.0395mm, which is a fantastic result.” Standard industrial systems used in automotive and aerospace industries frequently have up to 0.1mm standard deviations.
They then printed three rugged automotive part prototypes, and three end-use parts, commenting, “Unsurprisingly, the Fuse 1 delivered once again–both the electronics casing and the joining component were printed virtually flawlessly. The parts proved ready to use straight out of the build chamber, with minimal post-processing required and excellent surface finishes all around.”
Finally, the last three parts were dynamic parts, all with multiple moving components. Each part was printed-in-place, meaning they were fabricated as one overall file. This tested the printer’s accuracy in creating the tiny spaces in between joints that allow for functional movement.
“What’s most impressive is that the Fuse 1 managed to print each and every one of the tiny components without accidentally fusing any of them together, despite the extremely tight spacing in the joints and gaps. The success of the puzzle cube is a testament to the precision of the system’s laser and galvanometers.”
3D Printing Industry
The review was incredibly thorough, and made sure to mention standard maintenance scenarios, like replacing the optical cassette, and cleaning the HEPA filters. Formlabs was incredibly proud to hear their recognition of our Customer Support team and their tireless dedication to the customer experience.
“The company’s customer service is one of the best we’ve ever come across.”
3D Printing Industry
Overall, the 3D Printing Industry review provided a comprehensive overview of every step in the Fuse 1 and Fuse Sift workflow, and we’re happy to hear their conclusions were overwhelmingly positive.
“The streamlined printing workflow coupled with the reliable and refined processing parameters of the PreForm slicer make the Fuse 1 an ideal system for short-run functional applications…In the end, the Fuse 1 and Fuse Sift are a formidable duo and any criticisms are dwarfed by the sheer value offered by these systems.”
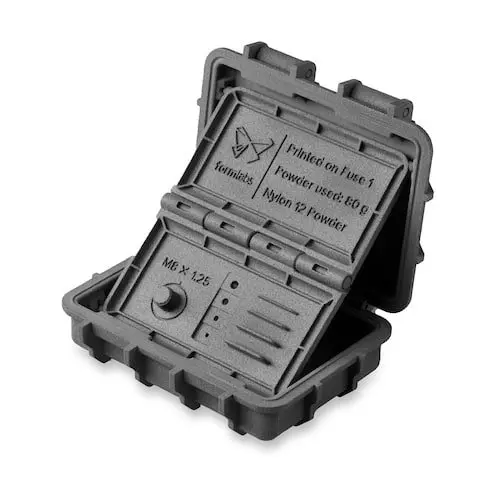
Request a Free Sample Part
See and feel Formlabs SLS quality firsthand. We’ll ship a free sample part to your office.
3D Natives 9.6/10
“As Formlabs previously achieved with stereolithography, the manufacturer really rethought the whole SLS technology to make it an easy process from slicing the model on PreForm, to printing on the Fuse 1 and post-processing parts in the Fuse Sift.
3D Natives
3DNatives’ review was a comprehensive walkthrough of the entire Fuse 1 experience, from unboxing to post-processing. At each step they emphasized the simplicity and intuitiveness of the Fuse 1 system, mentioning the quick set-up process, the straightforward powder management system, and how little infrastructure is required to power and ventilate the machines.
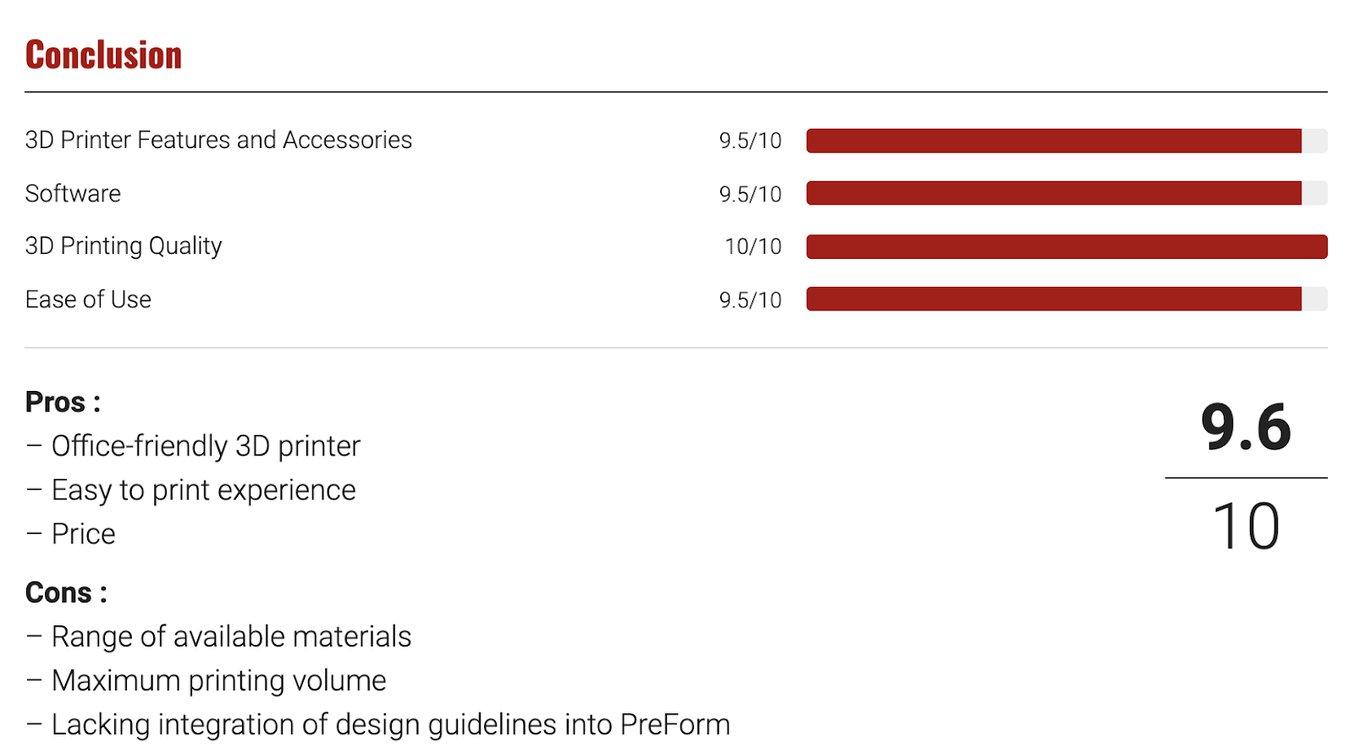
3D Natives Fuse 1 Review Chart
During the hands-on portion of the review, 3D Natives put the Fuse 1 to the test, printing a 3DBenchy, a torture test, and a lattice cube in Nylon 12 Powder. Each test showcased the dimensional accuracy of the Fuse 1. On the 3DBenchy specifically, the reviewers noted the precision necessary to create clear text on the bottom of the model. Though their torture test had a feature below the design guidelines’ recommendations for wall thickness, the reviewing team was pleased with the overall result, saying, “the bridges, cylinders and the text were built nicely.”
3D Natives took time to go through the entire customer experience with the Fuse 1 and Fuse Sift, concluding that the Fuse 1 and Fuse Sift have been designed with ease-of-use, part quality, and economy of cost in mind.
“The Fuse 1 will fit small service bureaus, design studios, or engineers looking for high quality 3D printed parts at a fraction of the cost of regular industrial SLS machines.”
3D Natives
3D Printing Nerd
The man behind the social media sensation 3DPrintingNerd, Joel Telling, visited Formlabs partner Engitype to test the Fuse 1 and Fuse Sift. The video is more of a how-to guide than a formal review, but Telling does a really wonderful job of explaining and showing each step in the Fuse 1 workflow.
Designed for an audience that might not be familiar with the SLS workflow, Telling first takes time to walk through the differences between fused deposition modeling (FDM) and SLS printing, noting that the ‘staging,’ or set-up of the parts is very important. Using helpful graphics, Telling comments on the efficiency and ease-of-use of PreForm.
“The software is going to help you figure out where to put the parts and how far apart to space the parts, and the orientation of the parts, to give you the greatest chance of success and also have the shortest amount of print time.”
While noting the Remote Print option, Telling sends a print to the Fuse 1 from one room away, much like a typical workflow in an industrial manufacturing environment.
Telling mentions that the printer creates part-labeling text sintered onto the top of the powder cake, a feature created in PreForm for ease of identification of different builds.
He then walks the viewer through a full workflow, cut into footage under seven minutes in duration, making sure to show up-close shots of him completing each step, from inserting the build chamber into the Sift for post-processing, to removing excess material underneath the fume hood.
Accompanied by zoomed-in footage of Telling using the Fuse Sift, his voice-over details the advantages of carefully post-processing each build, and the virtues of a powder reclamation and powder-recycling station, with his recommendations for use, saying “It’s very important to get as much unused material over the Fuse Sift plate because it can all be reused.”
He was also pleased to note the efficiency of the Fuse Sift vacuum and accompanying tools for removing extra powder from the surface of the parts. After using a sand blaster to further clean the parts with silica, Telling presents his finished parts, the 3DBenchy and a mini version of himself! His takeaways were all positive, commenting on the professional feel of the finished parts.
“There’s just something about SLS printed nylon that looks and feels incredible. It doesn’t feel like something made, it feels like something manufactured.”
3D Printing Nerd