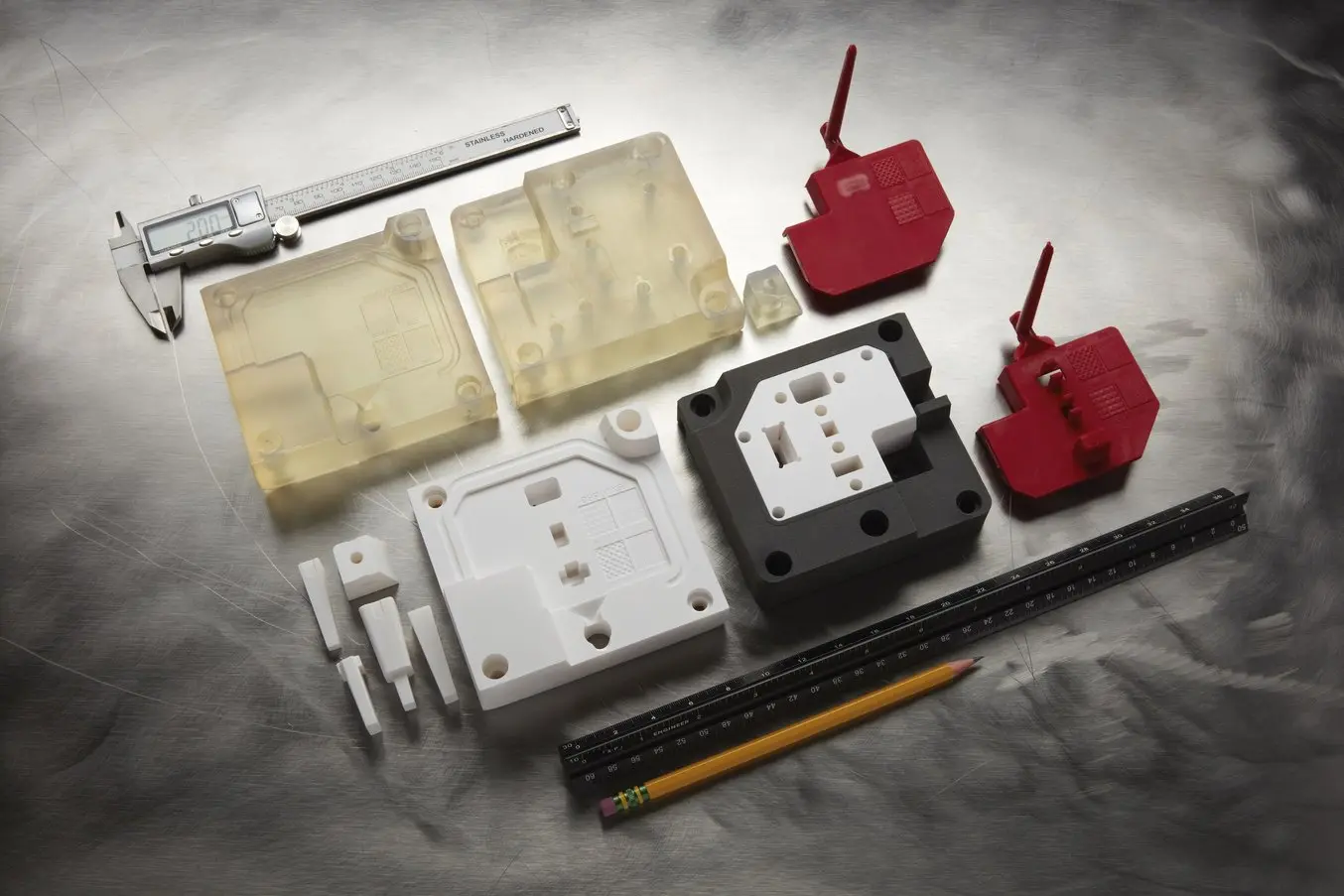
The French Industrial Technical Center for Plastics and Composites (IPC) conducted research to evaluate the usability of 3D printed molds for low-volume injection molding. Our report documents the fabrication steps and injection trials for molds 3D printed with Formlabs solution, highlighting results and best practices.
Why 3D Print Injection Molds?
Injection molding is a cost-effective and extremely repeatable technology for mass-producing plastic parts with tight geometrical or dimensional tolerances. The high cost of traditional steel tooling, however, makes injection molding challenging for smaller part quantities and can often be a barrier to introducing a new product. With 3D printed injection molds, engineers, manufacturers, and product designers can reduce costs, shorten lead times, and bring better products to market. 3D printed injection molds are a great option for those looking to design functional prototypes with end-use materials, fabricate a series of identical pre-production prototypes, or even manufacture custom or limited series of end-use parts.
Find out more about injection molding costs in our in-depth guide.
Research by IPC, a Leader in Plastics and Composites
IPC is the Industrial Technical Center whose expertise is dedicated to plastic and composite innovation in France. IPC develops new means to support all businesses, in particular small and medium-sized companies. The center works closely with European scientific key players, in order to support companies on R&D, innovation, technology and skills transfer concerns, regardless of the process used.
IPC built three technology transfer programs to tackle the major challenges of the industry. They support companies by providing R&D expertise for the circular economy (DIS 30), the additive manufacturing sector (PRINTER), industry 4.0, and for high added value products (HYPROD 2). IPC teams help industries or manufacturers to drive innovation with performing studies, establishing protocols, feasibility, and technology transfer.
Recently, IPC carried out a research project to assess the viability of injection molding with 3D printed molds. In the report, we summarize some of their findings, specifically those that involved Formlabs 3D printers.
Study Details and Benchmarks Geometries
The IPC research project consisted of a two year long technical study, divided in three phases:
-
Comparison of 3D printing technologies: A first classification was established from multiple manufacturers’ technical data. Thermal and mechanical data were evaluated respectively through the heat deflection temperature (HDT) and the Young’s modulus. Four types of benchmark allowing to highlight critical properties have been manufactured in each of the identified technologies in order to select the three most promising materials. Resin-based 3D printing solutions were selected as the best choice for injection molds, because of the high resolution and smooth surface of the parts.
Overall, a similar range of dimensional variations is measured for all the 3D printing technologies considered; between ±0.02 mm and ±0.05 mm for small features and between ±0.05 mm and ±0.2mm for larger dimensions. The standard accuracy of a machined metal tool is expected to be ±0.02 mm. This precision is desired to achieve a good fit at the parting line and avoid flashing. In this report, IPC will propose two methods to optimize the parting line of a 3D printed polymeric tool.
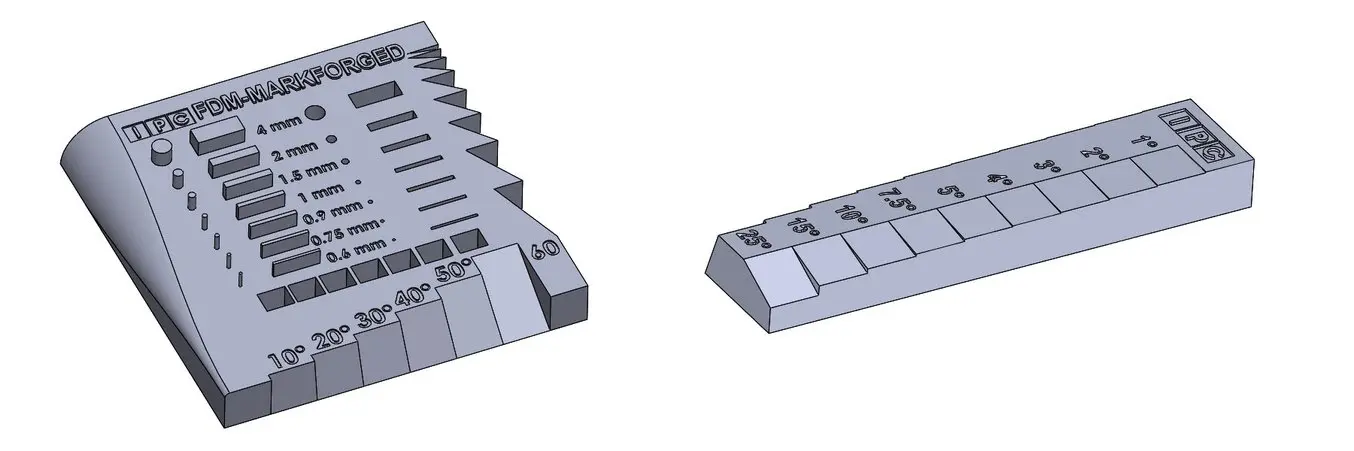
Benchmark geometries.
2. Material characterization, design, and 3D printing guidelines
3. Injection trials: IPC executed two tests with different sets of molds. In the first trial, they used a “torture-test” design and injected almost a hundred of polypropylene parts using a mono-material mold printed in Formlabs High Temp Resin. In the second trial, they used a more challenging “torture-test” design but this time injected thousands of polypropylene parts with a multi-material mold, core and inserts printed with Formlabs Rigid 10K Resin and the frame printed in PA12 with SLS.
Our white paper covers the part of the study made with Formlabs 3D printing solutions; in particular the design and fabrication recommendations, injection molding conditions, and results observed.
Results
IPC evaluated the usability of 3D printed molds for low-volume injection molding. With a mold core printed in Formlabs Rigid 10K Resin, and a soft frame printed in PA12, they could inject thousands of parts with polypropylene, reducing by 80-90% the cost of a metal mold.
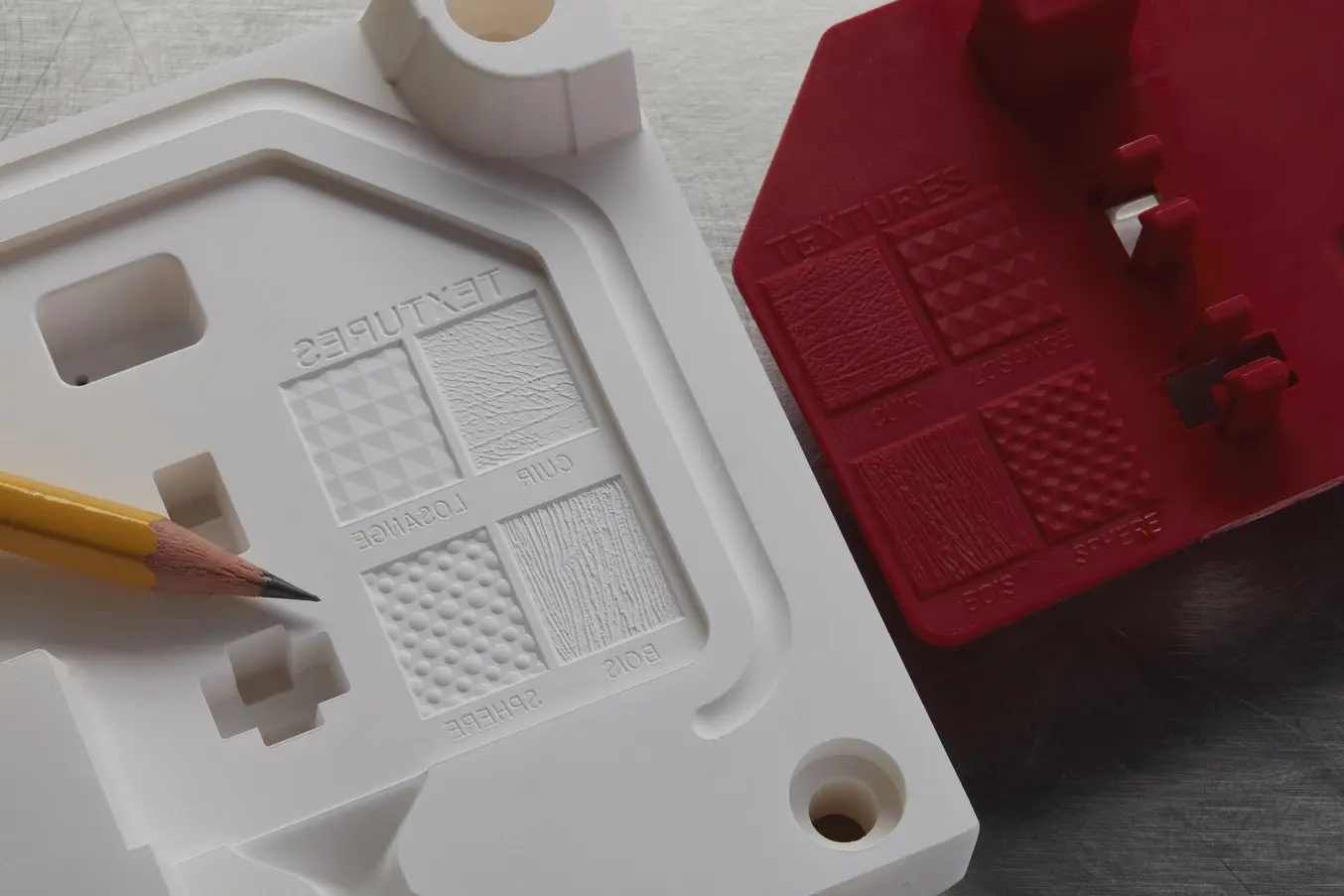
Textures on the final parts injected with the multi-material mold that consisted of a mold printed with Rigid 10K Resin assembled in the metal die.
Desktop 3D printing is a powerful solution to fabricate injection molds rapidly and at low cost. It requires very limited equipment, saving CNC time and skilled operators for other high-value tasks in the meantime. They can seamlessly be integrated into any injection molding workflow as they are easy to implement, operate, and maintain.
Manufacturers can benefit from the speed and flexibility of in-house 3D printing to create the mold and couple it with the production force of industrial injection molding to deliver a series of units from common thermoplastics in a matter of days.
Download the full report for the summary of the technical study, including 3D printing guidelines and insights on the mold assembly and process conditions.