Introducing Form 4BL: The Blazing Fast, Large-Format 3D Printer for Medical Applications
Introducing Form 4BL, the fastest large-format SLA printer for printing biocompatible parts. Whether you need high-throughput production of medical devices, a large anatomical model, or multiple prototypes, Form 4BL can deliver in a single workday.
- Blazing Fast Print Speeds: 2-4x faster print speeds than Form 3BL unlocks same-day printing at scale.
- Large Format Printing: A 4.6x larger build volume than Form 4B and 13% larger build volume than Form 3BL allows for the production of large biocompatible parts and anatomical models in a single build, or high-throughput of end-use parts.
- Exceptional Reliability: Industry leaders like Brian Albers of St. Louis Children’s Hospital and Todd Goldstein of Northwell Health highlight the exceptional reliability and performance of Form 4BL.
- Workflow Efficiency: Form 4BL streamlines workflows and meets high-demand production needs — while providing parts with finishes that rival those of injection molding.
With Form 4BL, we're not just evolving our technology, we're transforming how you can use it. Print with seven biocompatible BioMed Resins, including rigid and flexible materials, produced inside an ISO13485-certified Class 8 clean room, and validated on the printer for reliable printing right out of the box, or unlock the open system.
Form 4BL users can access an open system with the purchase Open Material Mode (OMM), enabling the printing of any 405 nm photopolymer resin and custom resins.* By embracing an open system, expert users and researchers can now leverage OMM to unlock unprecedented possibilities for material innovation and advanced applications, all while leveraging the advanced hardware and software of Form 4BL.
*Users printing their own biocompatible materials in Open Material Mode are responsible for validating biocompatibility and product safety. For more information on biocompatibility, our regulatory affairs and quality assurance team is here to help.
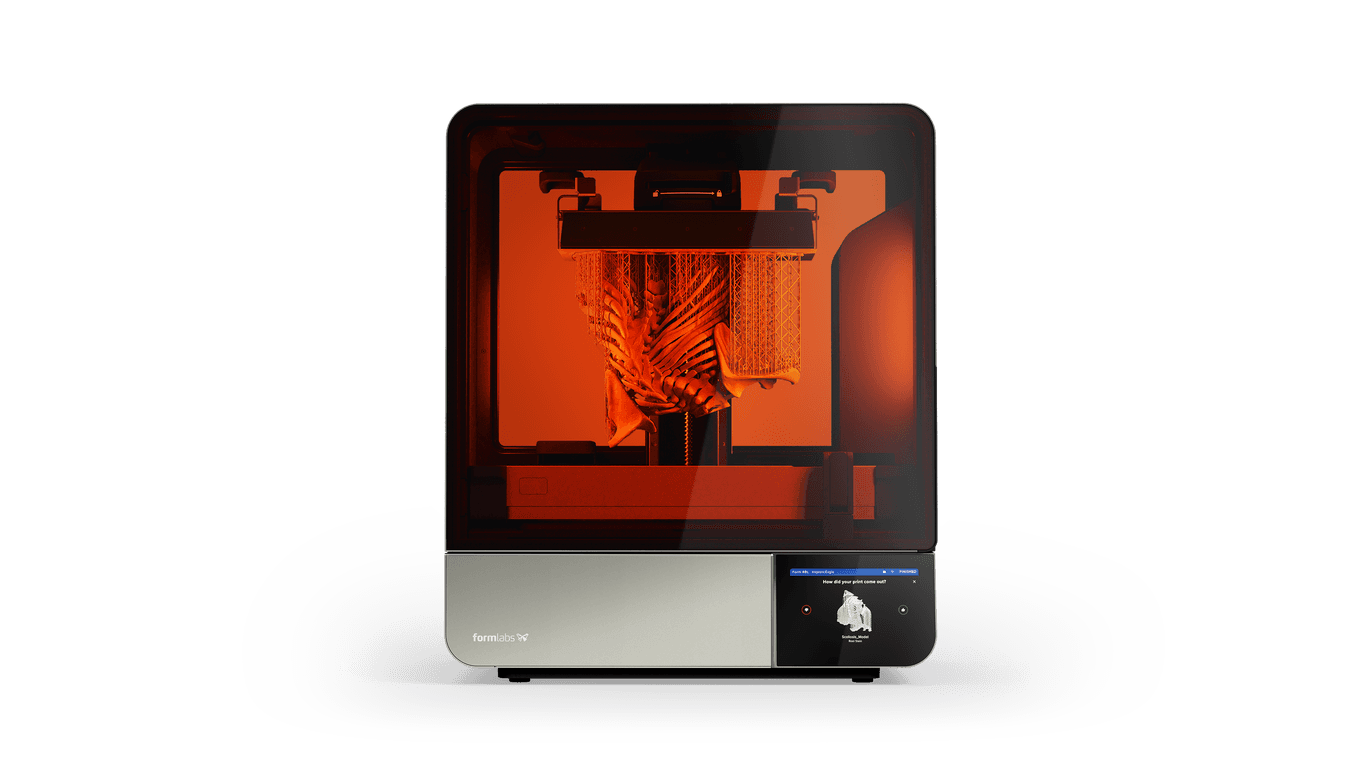
Product Demo: Form 4L and Form 4BL
See how Form 4L and Form 4BL can enable new levels of productivity and innovation through its unmatched speed, accuracy, and reliability.
Unmatched Reliability at Blazing Speed
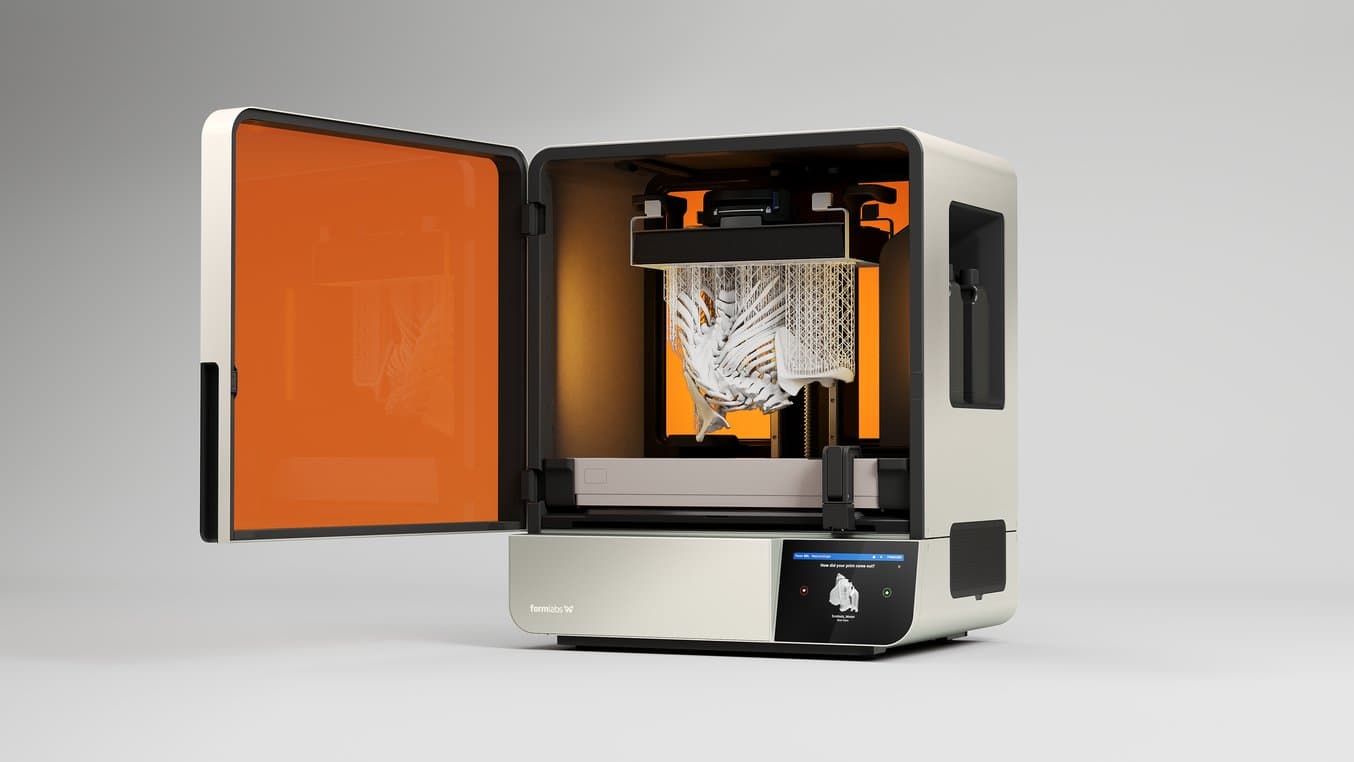
Print large anatomical models in Formlabs BioMed Resins that can be sterilized for use in the operating room.
Healthcare professionals need to be able to reliably meet deadlines set by the tight schedules of medical procedures, whether that’s printing a single-use surgical device or an anatomical model for surgery preparation. Form 4BL is built on the same innovative technology of Form 4B, delivering blazing speeds and reliable print quality.
Form 4BL solves for the pain points of users and is faster, more reliable, and easier to operate and maintain than our previous large-format SLA 3D printers. Start printing immediately with resin heating and resin dispensing that’s 5x-10x faster than Form 3BL, and monitor your prints with an integrated camera.
Harness industry-leading print speeds for every application, with a range of 10-80 mm/hr depending on the material and layer height. Like Form 4B, Form 4BL print time is similar whether you’re printing a single prototype or a full build of many parts.
Reliability starts at the factory with a 60-point calibration and quality control inspection, so Form 4BL arrives ready to print. While printing, six intelligent control systems precisely measure and maintain the temperature, resin level, print forces, and print status. Additionally, users can remotely monitor prints and manage printers from anywhere with an integrated camera, preventative maintenance reminders, and our free Dashboard software.
Consumables have been re-engineered for years of use, with a lifetime of over 75,000 layers for the Form 4BL Resin Tank and 600,000 - 1,900,000 layers for Light Processing Unit 4L (LPU 4L). When required, the LPU 4L is easy to replace, so Form 4BL can be up and running without delays.
Form 4BL Accelerates Response Time at St. Louis Children’s Hospital
"We’ve pushed Form 4BL to its limits, and it hasn’t failed a single print. Its reliability under pressure has been outstanding."
Brian Albers, 3D Printing Engineer & Lab Manager, St. Louis Children’s Hospital
At St. Louis Children’s Hospital in Missouri, USA, Brian Albers, 3D Printing Engineer, 3D prints anatomical models and surgical guides using Formlabs printers for orthopedic cases and cranial maxillofacial cases, including for pre-bending titanium plates. Albers currently prints with Form 3L, Form 3BL, three Form 3Bs, one Form Auto, a Fuse 1 selective laser sintering (SLS) 3D printer, and now Form 4BL.
Albers says, “We lean very heavily on the Formlabs printers. It's great on the cost savings side of it, but it's also a quick and efficient process. We're manufacturing anatomic models very quickly with not a ton of hands-on cleaning. Just this last month we've nearly doubled the most models we've produced in a month since the lab's inception.” Due to the unpredictability of clinical demands, Albers says, “we have to make sure we have a good process so we know that we can respond to every case that comes our way.”
"I'm blown away by how fast the Form 4BL prints. We've been able to tackle cases we otherwise wouldn't have had time to print, and it's done so with incredible reliability. When I rendered a print and saw the estimated time was just an hour and 26 minutes, I honestly thought it was a glitch. I didn’t believe it until we printed it."
Brian Albers, 3D Printing Engineer, St. Louis Children’s Hospital
Within a week of receiving Form 4BL, Albers had a resident contact him two days before a procedure. The resident hadn’t put in a proper order for an anatomical model of a spine.
"With our other 3D printing technologies, producing an anatomical model of a spine would take 20 hours, making it impossible to complete in time for procedure planning. Using Fast Model Resin on Form 4BL, we printed it in just an hour and a half and delivered it the same day. Without that speed, we wouldn’t have been able to respond to the case in time."
Brian Albers, 3D Printing Engineer, St. Louis Children’s Hospital
Large anatomical models like hips and adult spines have to be printed in multiple parts on Formlabs desktop 3D printers. Albers has been using Form Auto so that he could have a queue of multiple parts run over an evening to assemble in the morning. But with the combined volume and speed of Form 4BL, he can fit both hips or all the parts of a spine in one build, for fewer print batches in less time, often eliminating the need to print overnight.
In addition to time savings, Albers says, “The spines for instance, we did them on the PolyJet and it was about $1600 in resin and to do it on the Formlabs, we got it down to about $80 in material per spine.” This is a cost-savings of 20x in materials alone, for cost-effective and efficient production.
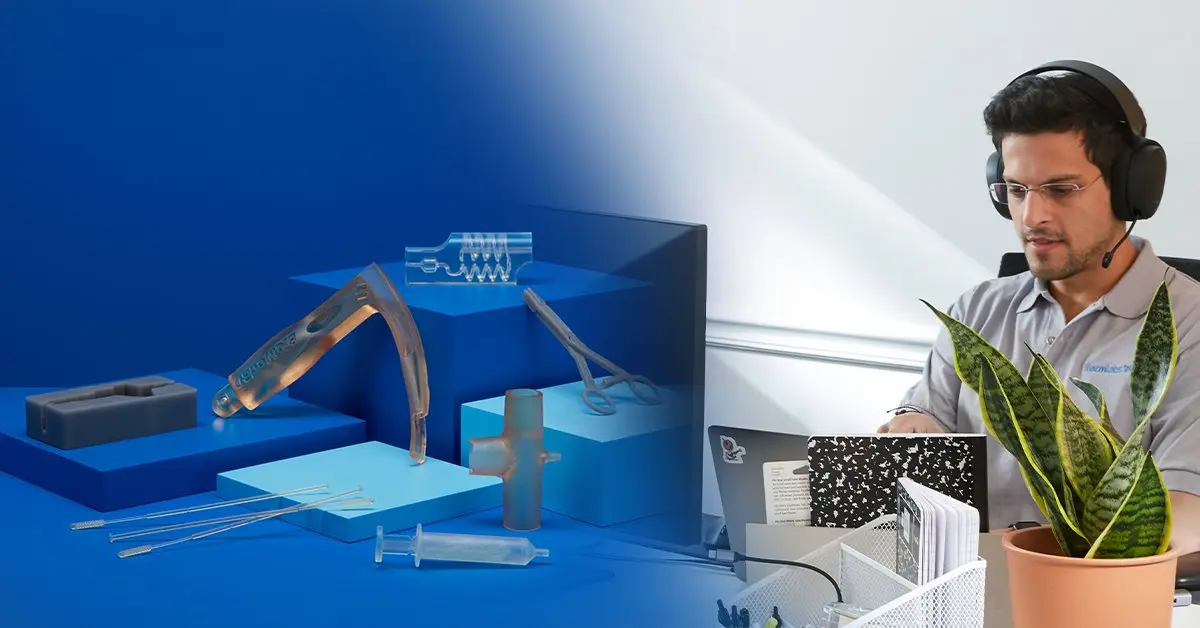
Talk to Our Medical Sales Team
Whether you need to make patient-matched surgical tools or are prototyping for a cardiac medical device, we’re here to help. Formlabs Medical team are dedicated specialists who know exactly how to support you and your company's needs.
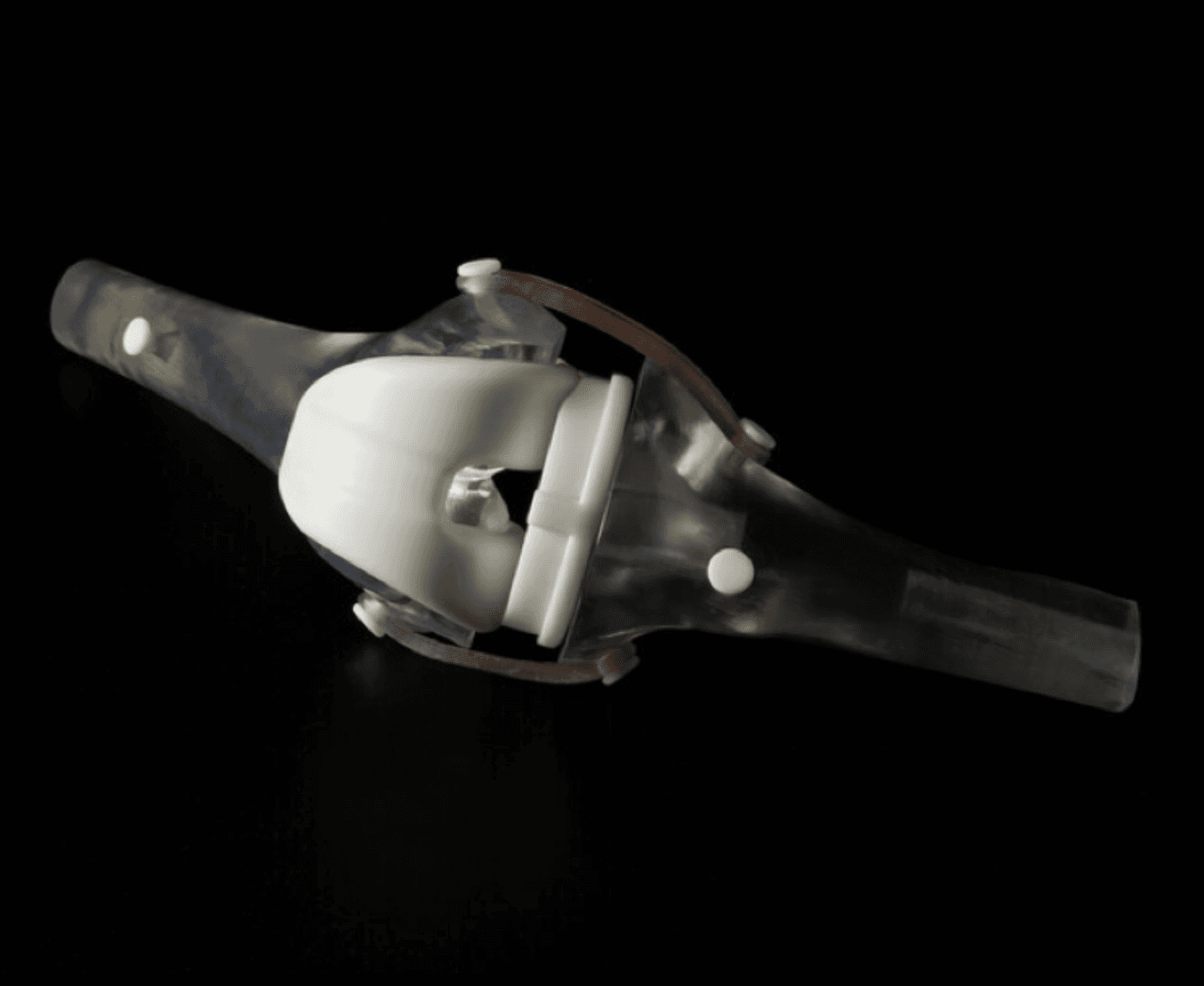
Creating Bone Simulation Models for Cutting and Drilling
3D printed bone-simulation models are revolutionizing medical training, surgical planning, research, and medical device development. This application guide walks through the bone-simulation material options for stereolithography (SLA) 3D printing and the entire in-house manufacturing process for bone-like anatomical models intended for cutting and drilling.
Production-Ready Throughput, Commercial-Quality Parts
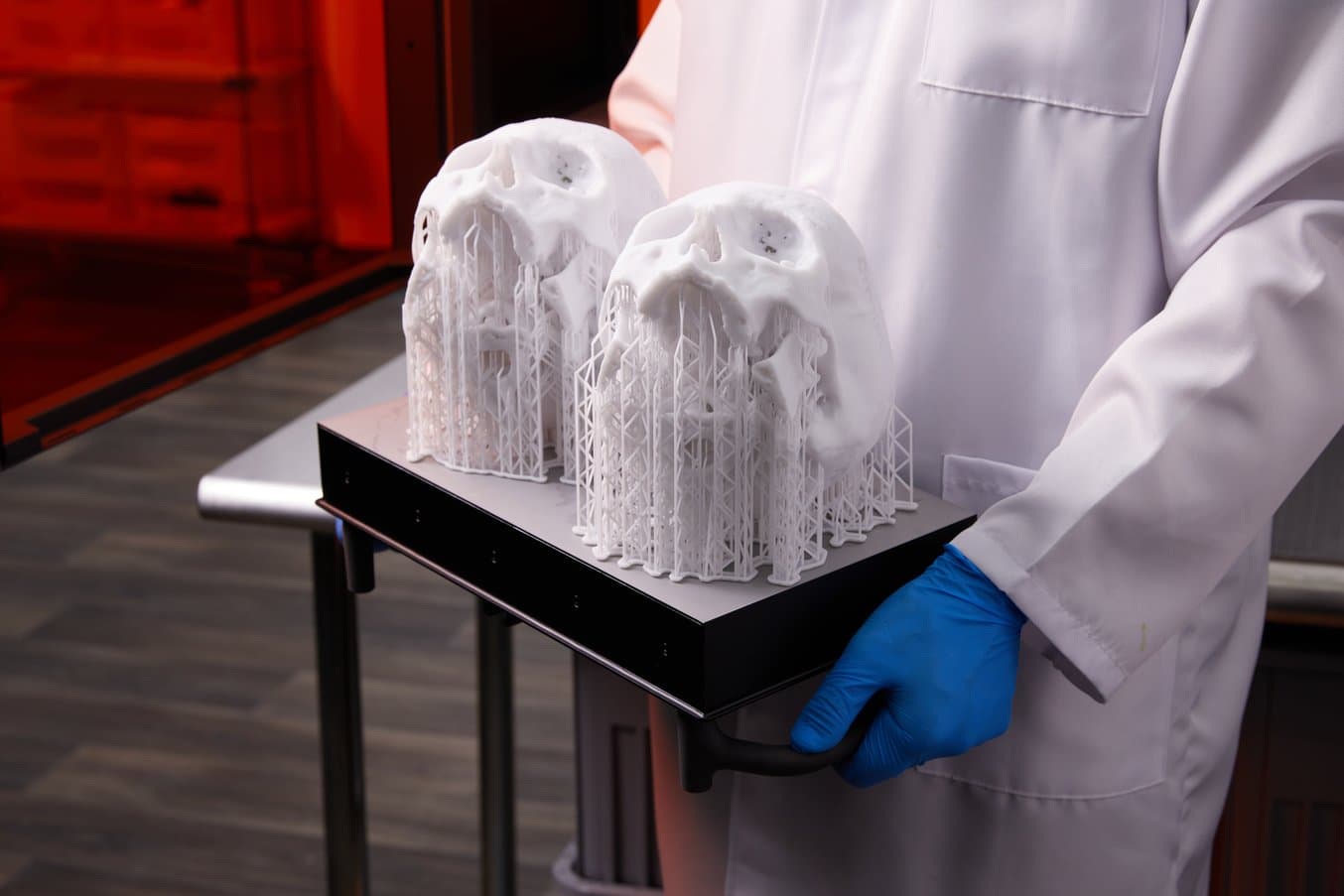
The build volume of Form 4BL is 4.6x larger than Form 4B, enabling the printing of large parts that are highly accurate.
Form 4 Series 3D printers are so easy to use that anyone can learn to print in 15 minutes, and Form 4BL brings this ease to large-format printing. Form 4BL has a build volume of 35.3 x 19.6 x 35.5 cm (13.9 x 7.7 x 14.0 in) — 4.6x larger than Form 4B — enabling for the printing of large medical devices, prototypes, multi-part assemblies, and models.
For users producing high volumes of small parts, Form 4BL keeps production running with the ability to print thousands of small parts per day with fewer touch points. For example, rather than printing six jobs on Form 4B, users can print two on Form 4BL, for the same number of parts per day with fewer user interactions.
Medical procedures require exacting accuracy, whether for a single, patient-matched part, or the commercial production of thousands of parts. Parts printed on Form 4BL have ±0.15% XY dimensional tolerances, for parts that match your design parameters every time.
Parts for clinical trials and human factor testing need to look and feel like end-use parts. Parts printed with Form 4BL have surface finishes that are indistinguishable from injection molded plastics, for a simpler design-to-mass-production workflow. Achieve the sharpest details and smooth surfaces with highly collimated light and 46 µm pixel size with pre-tuned anti-aliasing for subpixel resolution, plus lower peel forces and Light Touch Supports.
Whether you’re producing looks-like and feels-like prototypes, or manufacturing end-use medical devices, 3D printing is easy to scale for agile, on-demand production. Optimize inventory by printing when you need it and deliver quality devices at lower costs.
The Potential to Scale Production at Adaptiiv
“As demand continues to grow for our personalized medical devices, this technology will enable us to meet that demand, ensuring cancer patients around the world receive the best treatment possible.”
Kyle Gillis, VP Finance & Operations, Adaptiiv
Adaptiiv provides software for the design of patient-specific surface brachytherapy applicators for the treatment of cancer, with the option for users to order these devices via Adaptiiv’s On Demand Program. Brachytherapy applicators ordered from Adaptiiv are manufactured on Formlabs 3D printers. These devices have fine features, 2.5 mm tunnels for delivering radiation, and require material clarity.
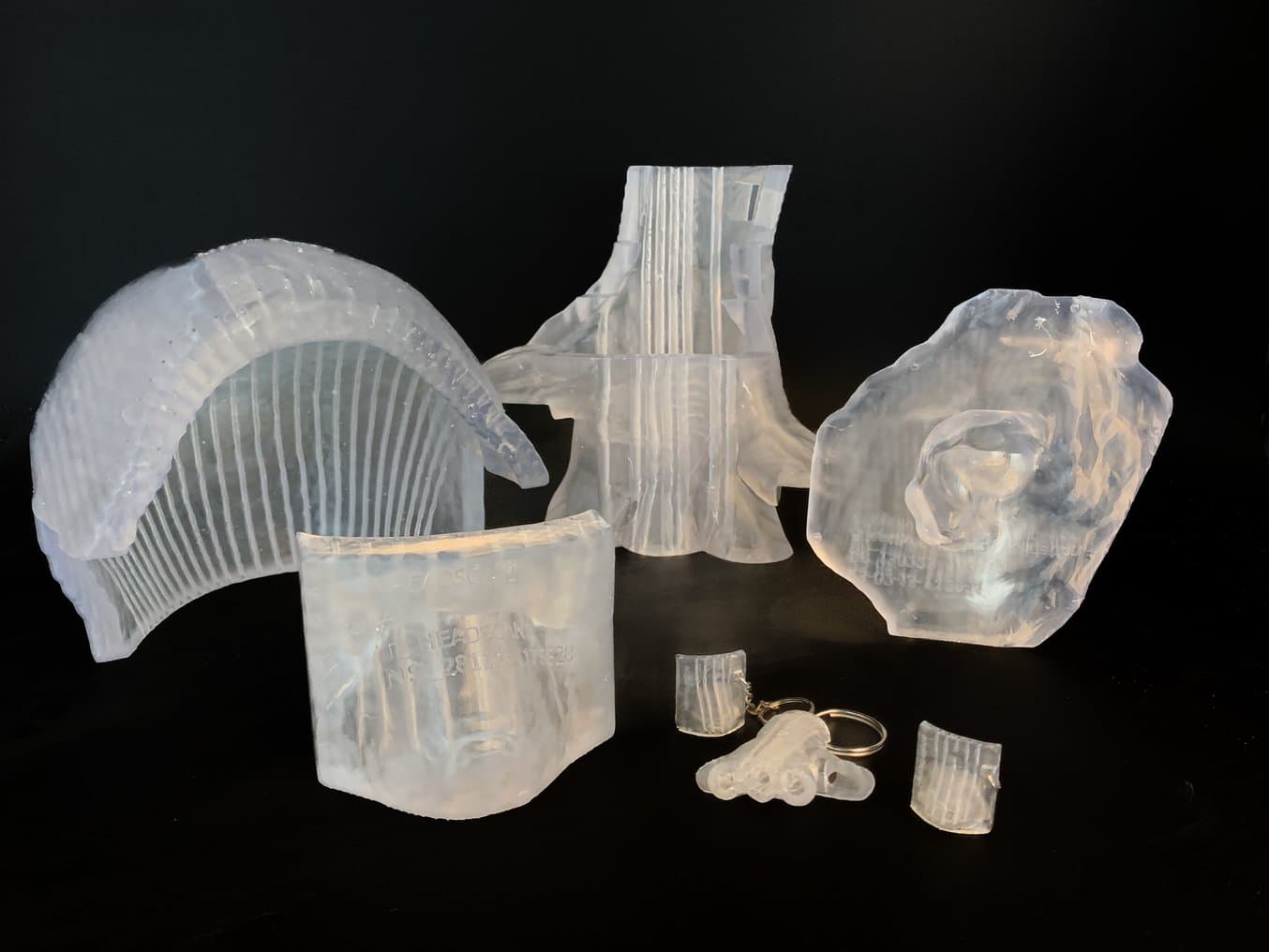
Adaptiiv’s patient-specific surface brachytherapy applicators have fine features and 2.5 mm tunnels for delivering radiation.
Manufacturing medical devices requires speed, accuracy, and reliability. Product Specialist Allison Sibley runs production at Adaptiiv’s R&D facility. For Sibley, the speed of Form 4BL means Adaptiiv can double the number of prints in a day, with one batch being printed during working hours and a second that will finish overnight.
This speed helps not just the team, but shortens the time in which customers receive their orders. Shawn Hunt, Controller at Adaptiiv, says, “Any way that we can make things faster, without sacrificing quality and reliability, we will always do it that way. The Form 4BLs will get that [speed] for us.”
“Form 4BL is great. We’ve pushed it to its limits and not had any failed prints.”
Allison Sibley, Product Specialist, Adaptiiv
For Adaptiiv’s tight production timelines, printer reliability is required. Formlabs 3D printers provide a reliable, scalable manufacturing method. With Form 4BL, the large format provides the option to print large brachytherapy devices, as well as batching smaller devices, allowing for increased throughput before needing to add new printers to their fleet.
“As we scale up, the ability to fit three or four parts in a single build on Form 4BL, compared to only two on Form 4B, would be a game changer for us.”
Shawn Hunt, Controller, Adaptiiv
Material Flexibility: Biocompatible Resins and Open Material Mode
Formlabs’ material library of 37+ materials includes seven biocompatible BioMed Resins designed for healthcare professionals seeking medical-grade materials with a range of mechanical properties. Formlabs BioMed Resins are developed and manufactured within our robust Quality Management System that is ISO 13485 and EU MDR certified.
With Form 4BL and BioMed resins, users can print large, sterilizable anatomical models for use in operating rooms, large medical device prototypes, devices for human factor testing, or leverage the throughput power to manufacture end-use devices.
Formlabs resins for Form 4BL are validated on the printer, with optimization engineers putting hundreds of printed parts to the test, dialing in validated print settings to empower reliable printing right out of the box. Additionally, FDA master files for BioMed resins are available upon request, so you can accelerate your time to market.
Open Material Mode (OMM) is available for purchase on Form 4BL, empowering expert users and researchers to push the boundaries of 3D printing by allowing them to leverage the speed, accuracy, and heating capabilities of Form 4BL to print with any third-party 405 nm photopolymer resin or develop their own custom resin. Learn how OMM is empowering medical device companies Poly-Med and restor3d in our blog.
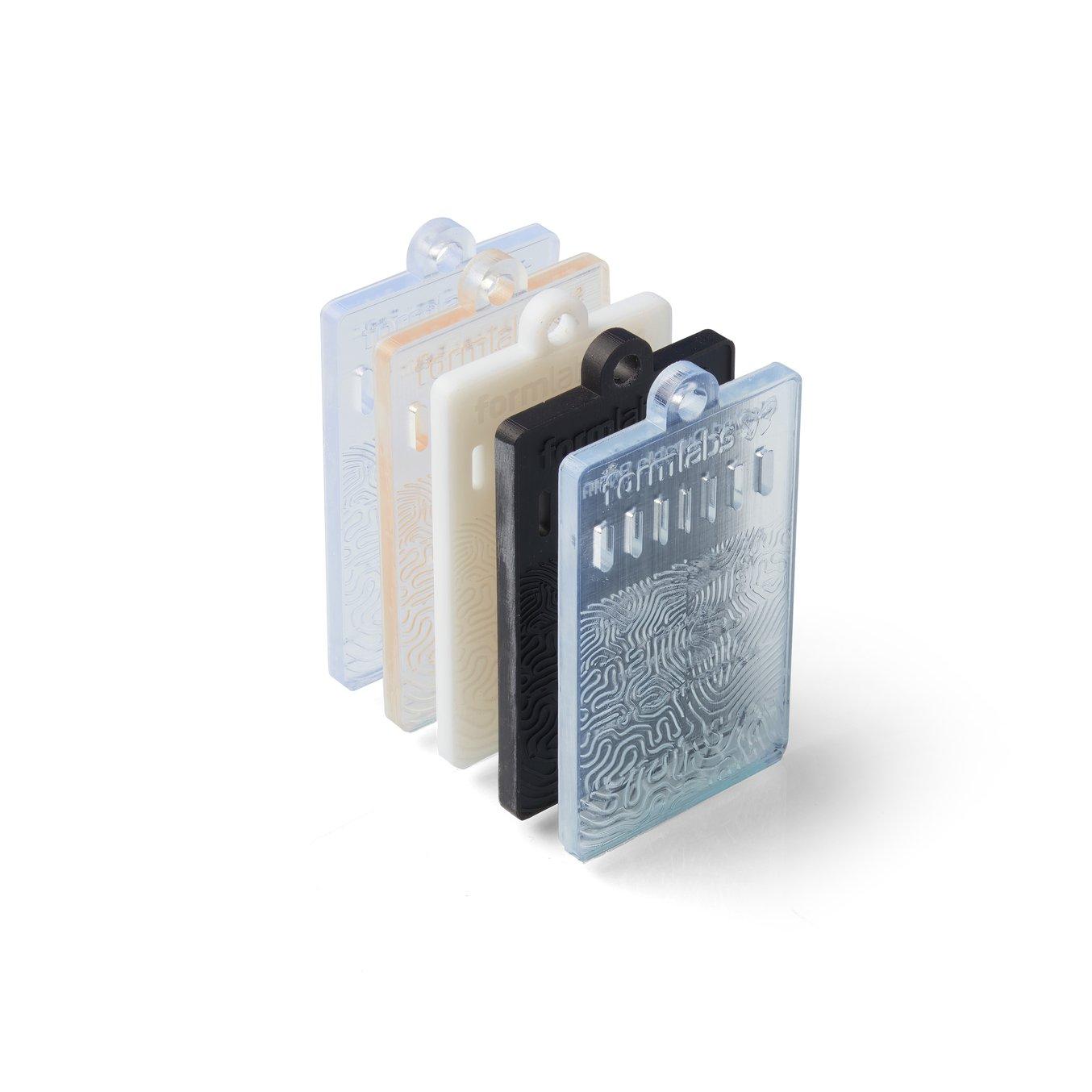
BioMed Resin Swatches
Each BioMed Resin swatch features embossed and debossed designs, 0.5-2.0 mm cutout thicknesses, as well as regulatory information unique to that resin.
24/7 Production at Northwell Health
At Northwell Health, Todd Goldstein runs a hospital-based 3D printing facility for surgical planning, anatomical model creation, and some medical device development. The facility has all types of Formlabs printers — all of which are actively utilized: a Form Cell with Form 2s, a Form 3, a Form 3BL, a Form 4, a Fuse 1, and now, Form 4BL. Goldstein says that, “With Formlabs, we have a wide variety and library of resins, and your printers are part of the FDA-validated pathway for Mimics.” This validation is key for printing inside the hospital.
"Since we're producing surgical-grade equipment, the biocompatibility of the resins is crucial. The ability for prints to start and finish correctly, along with the duration of the prints, can impact patient care if we’re working against a deadline. With Form 4BL, we’ve achieved a 100% success rate on our parts."
Todd Goldstein, Northwell Health
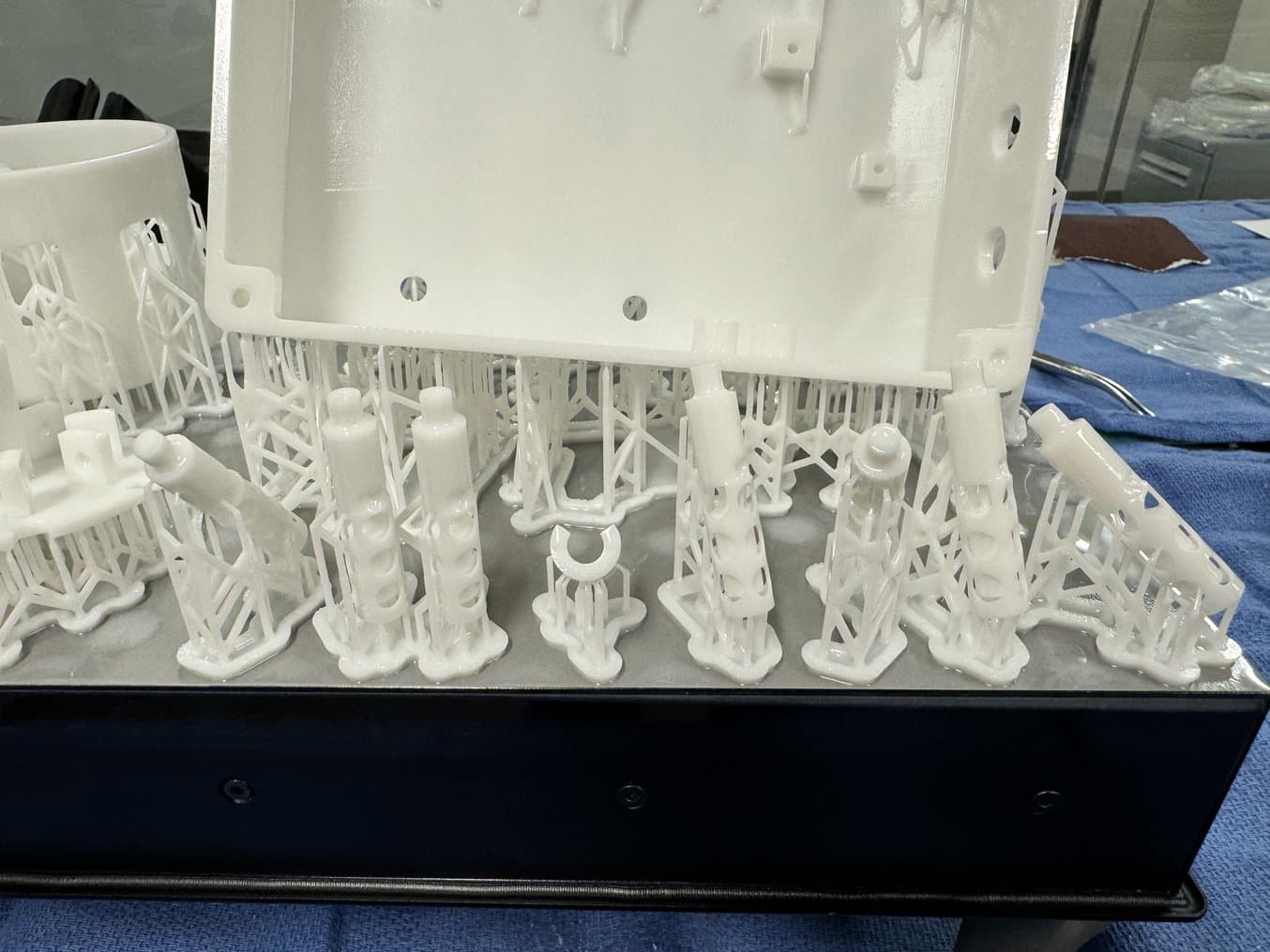
The significant time improvements of Form 4BL enable Goldstein to print an extra batch of prints each day.
3D printing at Northwell Health never stops because the hospital operates 24/7, meaning Goldstein gets requests at all hours, so efficiency, reliability, and ease of use are requirements for 3D printers. Setting up Form 4BL, says Goldstein, was “pretty straightforward. Plug it in and we're up and running within a couple of minutes.” He also saw significant drops in print time, with some large batches going from 20 hours to eight.
“The speed has been great. We're getting an extra batch on the printers, which helps with the quantity we can produce. The improvements with the dashboards have been really appreciated and utilized heavily — you can start prints remotely as long as the printer's primed. That's been very helpful.”
Todd Goldstein, Northwell Health
Ultimately, Goldstein says, “We could probably get away with having no Form 4Bs and only having the Form 4BLs, because the resolution, accuracy, and printing capabilities are pretty much similar.” This would give him the option of printing large parts or batches no matter when requests arrive.
The Fastest Large-Format Medical 3D Printer
Form 4BL is our response to the pain points of users, enabling fast, reliable, and accurate printing of large parts so you can spend more time innovating and less time printing. Meet the needs of surgeons with a printer capable of printing an entire spine. Print large medical devices in a single day. Or reduce inventory and production costs with on-demand manufacturing of end-use medical devices.
To learn more about Form 4BL, watch our webinar. To see how Form 4BL can help you reach your business goals, contact sales.