Introducing Formlabs First Carbon Fiber Reinforced SLS Powder: Nylon 11 CF Powder for Strong, Lightweight Parts
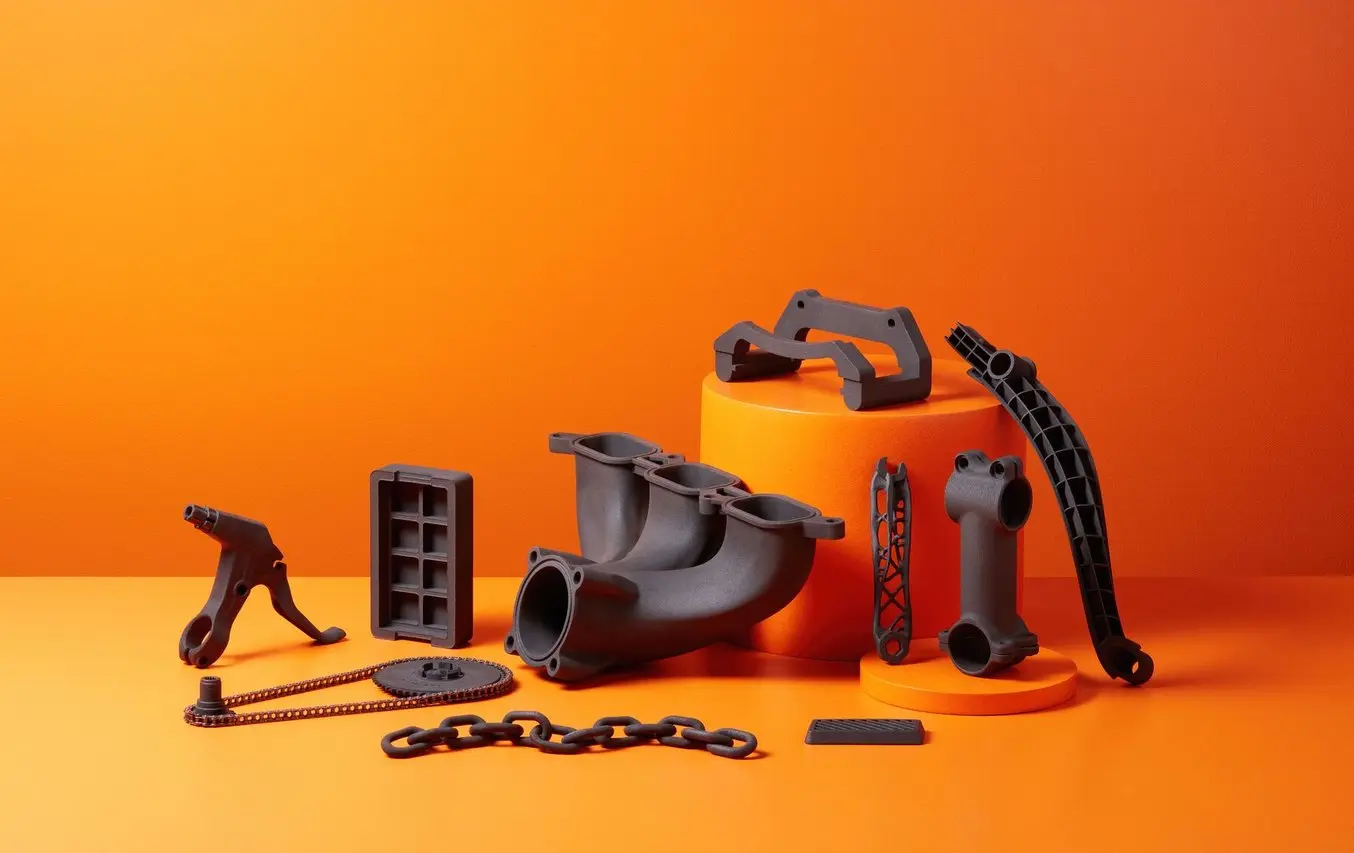
Formlabs is proud to announce the first carbon fiber-reinforced material in our library, Nylon 11 CF Powder for the Fuse 1+ 30W selective laser sintering (SLS) 3D printer. Nylon 11 CF Powder enables manufacturers to create strong, lightweight, and heat-resistant parts, without relying on traditional overlay or machining methods.
Due to its high heat deflection temperature, tensile modulus and high stiffness, Nylon 11 CF Powder is ideal for:
- Aerospace casings, jigs, and fixtures
- Automotive prototyping, testing fixtures
- Electric battery-operated vehicle casings
- Manufacturing replacement parts
Carbon fiber reinforced parts are used in high-performance industries for applications that require strength, heat-resistance, and stiffness, while remaining lightweight. While carbon fiber-reinforced parts are widely used already, few options exist for 3D printing, and none at the price point, quality, and ease of use of the Formlabs Fuse 1 Series printers.
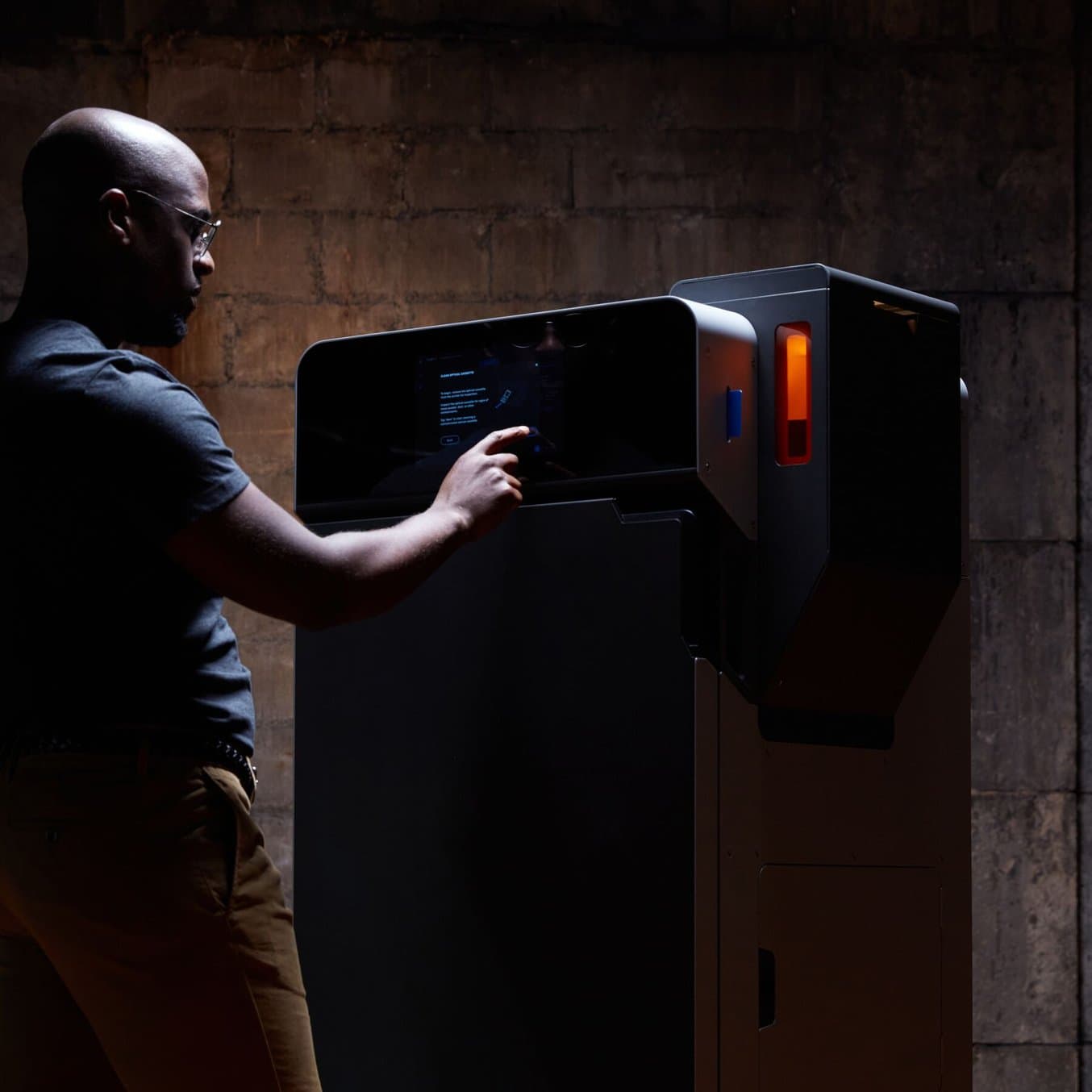
Outsourcing vs. In-House: When Does it Make Sense to Bring SLS 3D Printing In-House?
In this white paper, we evaluate the value proposition of bringing SLS 3D printers in-house, in comparison with outsourcing SLS parts from a service bureau.
What is Carbon Fiber?
Carbon fibers are created through an industrial process that takes a raw material, usually polyacrylonitrile or a wood byproduct, and brings it to an extremely high temperature, effectively ‘burning away’ the non-carbon components of the material. The resulting fibers are almost fully carbon crystalline structures that are woven together to produce what we know as carbon fiber. These can be added to a resin to produce moldable sheets, woven into fabric, or added to a powder to be sintered or bound together by a 3D printer.
Composite materials like carbon fiber reinforced plastics can outperform traditionally machined parts made from steel, wood, or aluminum. Though the carbon fibers add strength to the base material, they don’t add much weight, so these composites are often much stronger than homogenous materials, while being lightweight. They are commonly used in automotive ducts, manifolds, engine air flows, aerospace casings, performance sports equipment, and boat manufacturing applications. Electric vehicles, wind turbines, and other emerging, sustainable sectors are utilizing the strength and lightweight properties of carbon fiber parts to increase efficiency.
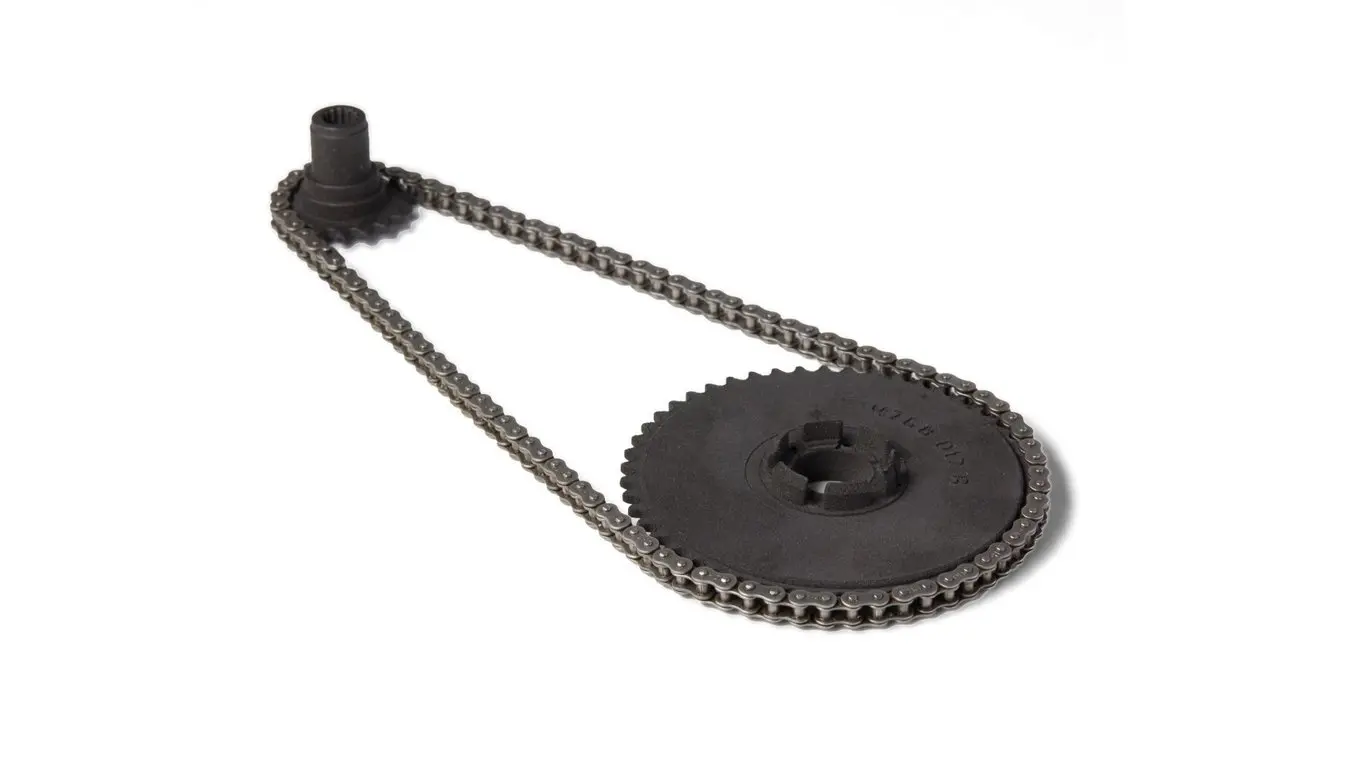
Traditional Methods for Producing Carbon Fiber-Reinforced Parts
The most common methods of carbon fiber part fabrication are wet lay-up, prepreg lamination, and resin transfer molding (RTM). These methods all require a mold, and can be extremely labor intensive.
The molds themselves can be made inexpensively through 3D printing, and this workflow has allowed small and medium manufacturers to produce end-use carbon fiber parts at a much lower cost than previously with traditional methods. However, even when using 3D printed molds, there are limitations on production volume and geometry. Parts with internal channels, small negative and positive features, or production runs in the tens and hundreds are difficult to create, and very time consuming.
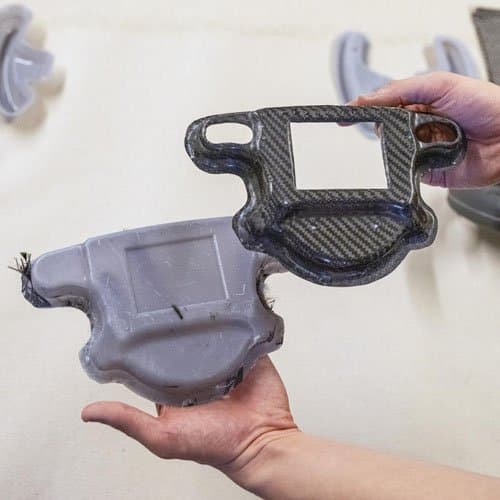
Carbon Fiber Parts Manufacturing With 3D Printed Molds
Download this white paper for composite mold design guidelines and step-by-step guides to the prepreg and hand laminating methods to create carbon fiber parts.
Direct 3D Printing of Nylon 11 Carbon Fiber Reinforced Parts
In recent years, directly 3D printed carbon fiber reinforced parts have been made possible with the introduction of higher powered sintering capabilities and material science developments that combine powderized carbon fiber particles with common SLS materials, like nylon particles.
As in many 3D printing applications, the direct 3D printing of carbon fiber reinforced parts will not completely replace traditional methods of carbon fiber part creation, but should be thought of as a complementary manufacturing method. Though their ultimate tensile strength (UTS) is not as high as traditionally manufactured carbon fiber parts, 3D printed parts made from Nylon 11 CF Powder offer significantly enhanced strength and stiffness compared to their un-reinforced polymer counterparts. The advantages of 3D printing carbon fiber reinforced parts lie in the abilities of the Fuse 1+ 30W printer to address geometrical challenges, provide a fast, low-labor alternative to traditional methods of production, and its accessible footprint and streamlined workflow.
This additive manufacturing method avoids the geometrical limitations of a traditional molding process, and the self-supporting print bed of an SLS printer further reduces design limitations. The main obstacle to mass adoption of this method of carbon fiber reinforced part fabrication is the high start-up price for most 3D printing technologies capable of producing carbon fiber reinforced parts.
The Fuse 1+ 30W SLS printer removes that barrier, offering a solution for producing high-performance, reliable, and high accuracy carbon fiber-reinforced parts at an affordable price point. Compared to many industrial 3D printing solutions, Fuse 1+ 30W users can create carbon fiber parts for a fraction of the price and labor time. Nylon 11 CF Powder is available exclusively on the Fuse 1+ 30W printer, and has been validated along with the new Fuse 1 Series model for optimum reliability and consistency.
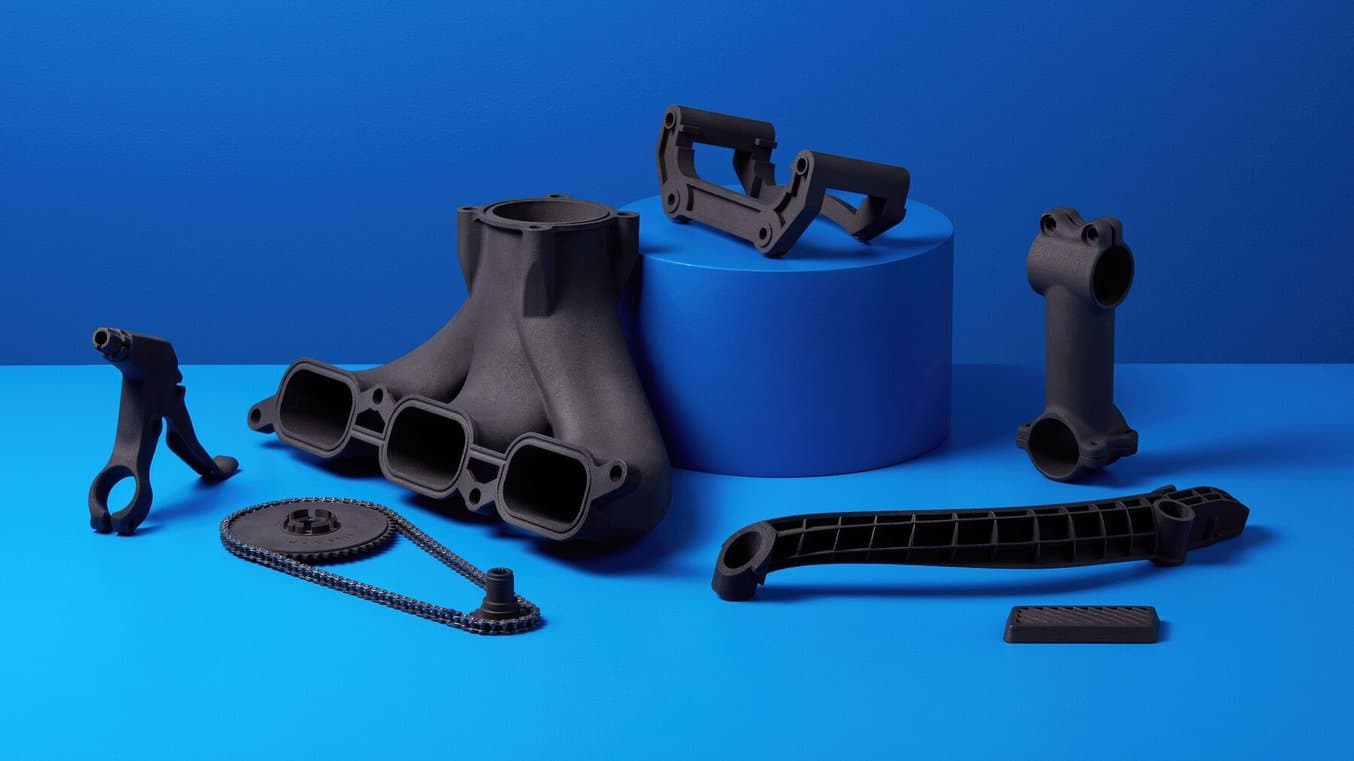
Ideal for High Performance Applications
Nylon 11 CF Powder should be the first material of choice for manufacturers looking to bring production of metal replacement parts in-house. When a piece of equipment breaks and needs a repair, every minute spent waiting for a solution from the OEM or a spare parts provider can mean thousands of dollars lost from stoppage time. Though 3D printed replacement parts have been on the horizon for years, many businesses have been waiting on the right material before investing in a solution. Nylon 11 CF Powder is the right material for the job, and can act as a stiff, strong, and lightweight alternative to metal for replacement parts that need to withstand repeated impact and high temperatures.
Materials | Nylon 11 CF Powder | Nylon 12 GF Powder | Nylon 12 Powder | Nylon 11 Powder |
---|---|---|---|---|
Ultimate Tensile Strength X (MPa) | 69 | 38 | 50 | 49 |
Ultimate Tensile Strength Y (MPa) | 52 | 38 | 50 | 49 |
Ultimate Tensile Strength Z (MPa) | 38 | 38 | 50 | 49 |
Tensile Modulus X (MPa) | 6500 | 2800 | 1850 | 1600 |
Elongation at Break, X (%) | 9 | 4 | 11 | 40 |
Elongation at Break, Y (%) | 15 | 4 | 11 | 40 |
Elongation at Break, Z (%) | 5 | 3 | 6 | N/A |
Notched Izod (J/m) | 74 | 36 | 32 | 71 |
Heat Deflection Temp. @ 1.8 MPa (°C) | 178 | 113 | 87 | 46 |
Heat Deflection Temp. @ 0.45 MPa (°C) | 188 | 170 | 171 | 182 |
This new performance material is also ideal for jigs, fixtures, and tooling on the production line due to its high stiffness, high impact strength, and low weight. For the creation of metal parts, if Nylon 11 CF Powder parts aren’t used as a direct substitute, they can be perfect benchwork tooling parts that can hold hot metal parts without deforming or fracturing.
When considering end-use parts, aerospace and flight applications like drone manufacturing can benefit from the high heat tolerance and impact resistance of the new Nylon 11 CF Powder as well. Drones and other airborne vehicles are subject to high temperatures, whether from the sun when flying above cloud cover, or from the fueling method—battery operated drones need heat-proof casings to protect the components from a hot battery, and jet fuel-powered craft are of course subject to high heat from combustion engine elements.
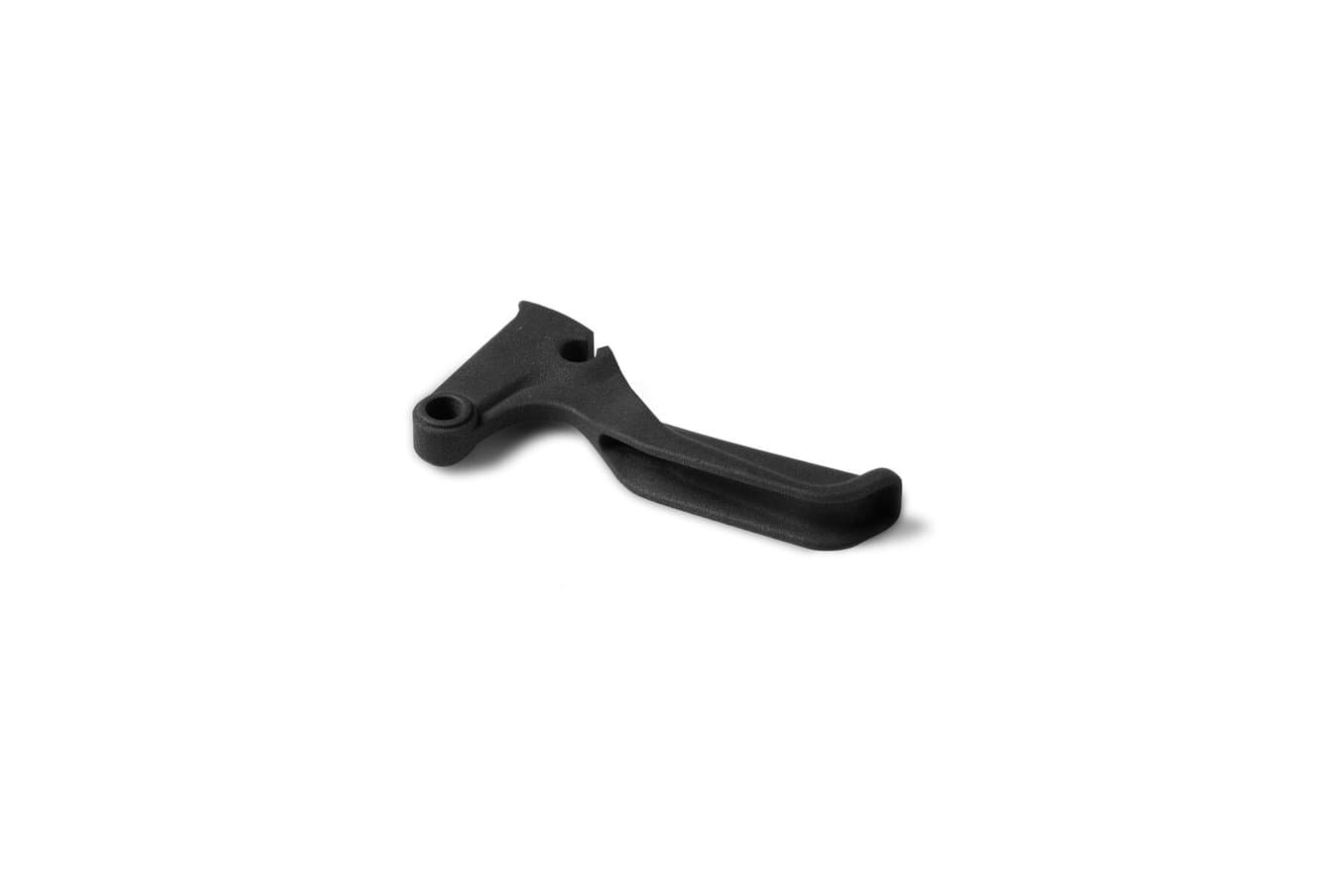
Request a Free Sample Part
See and feel Formlabs quality firsthand. We’ll ship a free sample part to your office.
Print Orientation for Maximum Strength
Because Nylon 11 CF Powder parts get their high tensile strength from carbon fibers, the direction in which the printed parts are oriented should be taken into consideration when printing.
The recoater within the Fuse 1+ 30W printer tends to lay out the carbon fibers lengthwise with regards to the X axis. As a result, the ultimate tensile strength (UTS) of the parts is most significantly enhanced in the X direction—the UTS is 38 MPa in the Z axis and 69 MPa in the X axis. To optimize the strength of a printed part, users should be sure to orient their prints with their intended stress taking place along the X axis.
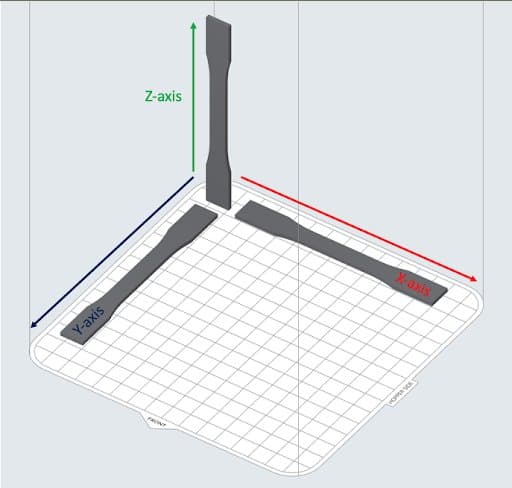
Orient parts with intended strain along the X axis to maximize the strength of the carbon fibers.
Validated Together for Maximum Reliability
The new Fuse 1+ 30W printer has been validated alongside this high-performance material in order to minimize any learning curve with the new material. Though this is Formlabs’ first carbon fiber-reinforced material, previous filled materials such as Rigid 10K Resin and Nylon 12 GF Powder are top performing materials, and have enabled new applications in industries such as automotive, aerospace, and manufacturing.
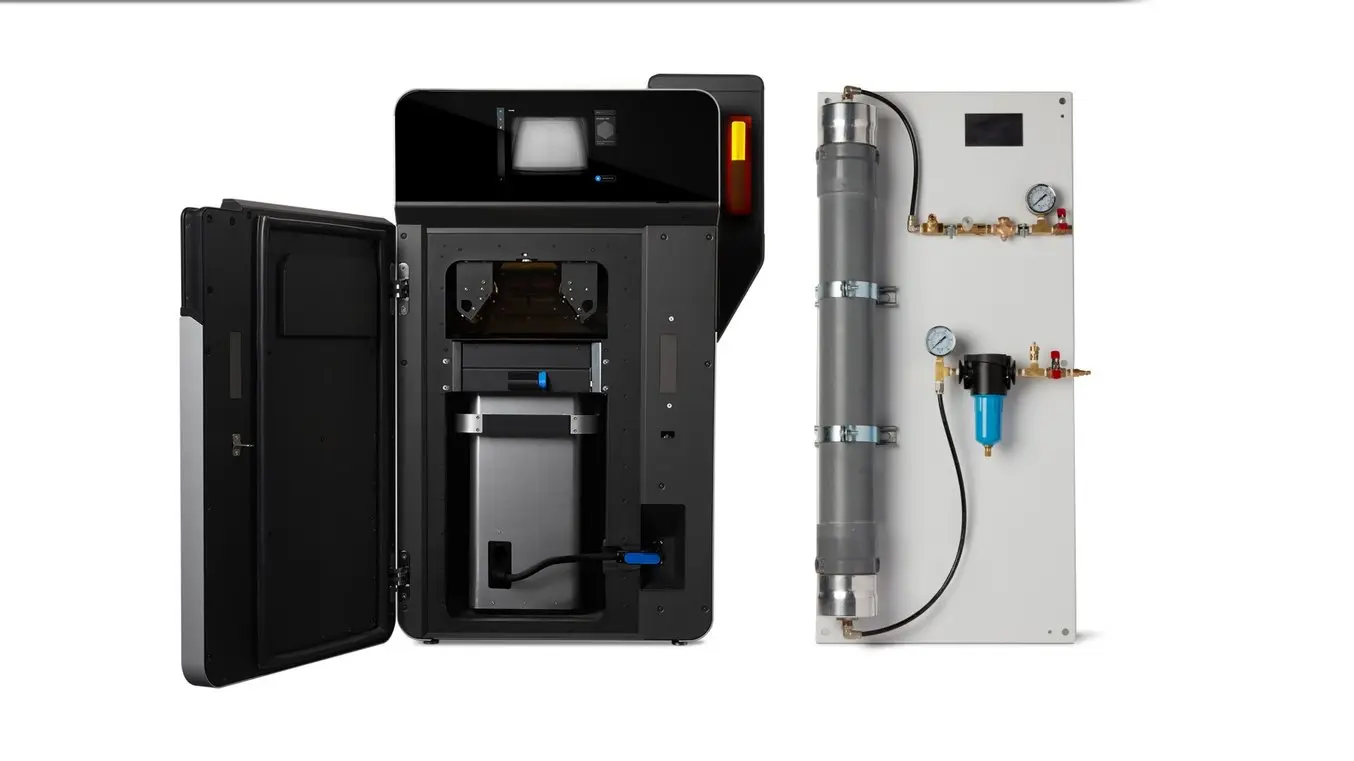
The Fuse 1+ 30W SLS printer and nitrogen generator pair together for a streamlined workflow.
The new Fuse 1+ 30W printer includes the option to print with a nitrogen supply, which creates a stable, inert environment in the build chamber. This environment allows Nylon 11 CF Powder parts to be built without risk of oxidation, preserving the quality of unsintered powder around the parts, which leads to better refresh rate and more economical printing.
In a nitrogen environment, Nylon 11 CF Powder has a refresh rate of 30%, meaning each new build chamber only requires 30% fresh, or new, powder, while the rest can be recycled powder from previous prints. This workflow can potentially lead to zero waste printing, reducing material cost and helping keep your workspace, and the environment, cleaner and less wasteful.
Nylon 11 CF Powder can be integrated into your workflow easily, and requires only two to three hours of cleaning time when switching from Nylon 11 Powder (compared to full days spent cleaning when switching materials on other traditional SLS machines). This feature helps you free up your workday to concentrate on revenue-generating tasks while still enabling a multi-material production unit.
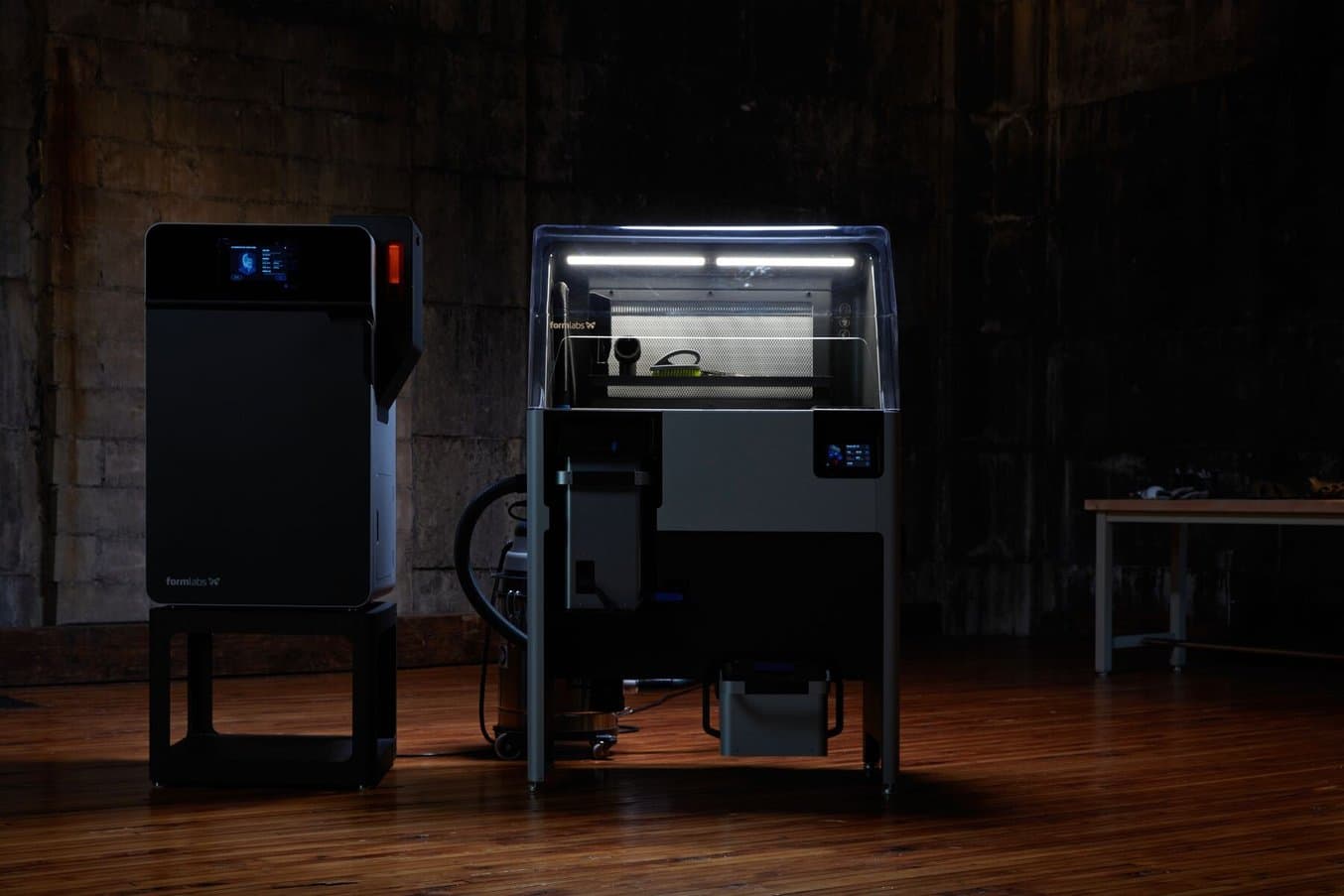
By upgrading your Fuse Sift with a new sieve, you can utilize the same printing and post-processing workflow as your other SLS materials.
The Final Push for Bringing SLS In-House
There are many manufacturers currently sourcing SLS parts from suppliers for a range of applications—prototyping, end-use parts, replacement/repair parts, and manufacturing aids. To bring that manufacturing in-house requires a high enough volume of necessary parts (often across several of these application groups) to justify the investment.
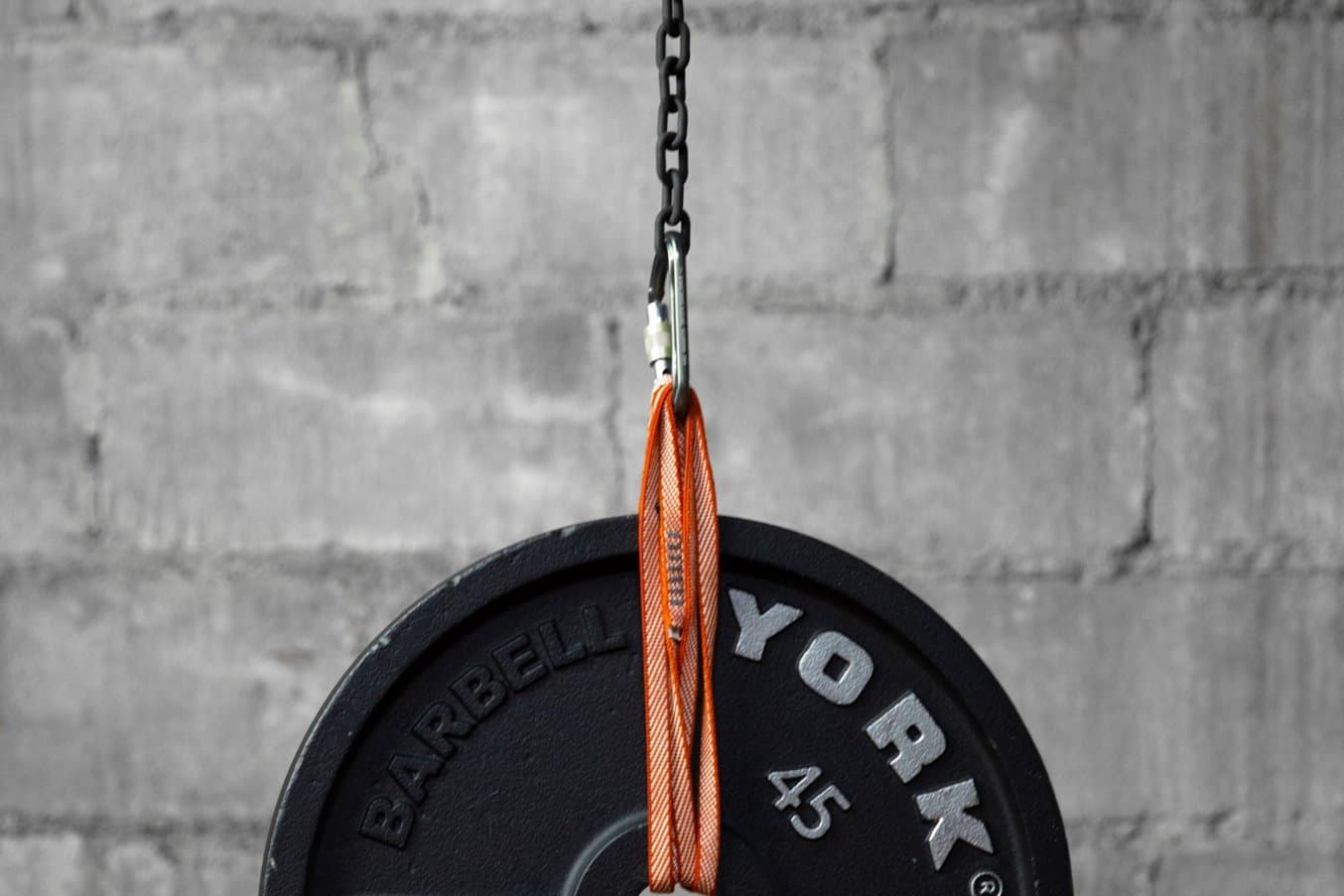
The launch of Nylon 11 CF Powder adds one material to the Formlabs SLS powder series, but this one powder opens up a wide range of newly possible applications. Manufacturers need to be able to rely on SLS parts for high temperature, repeated impact, and high strength applications, and this new powder delivers. Alongside the Fuse 1+ 30W printer, the new workflow is easy to integrate, maintain, and manage, at an affordable price.
NOTICE: Nylon 11 CF Powder can act as an irritant of skin and mucosal membranes. Formlabs recommends using personal protective equipment (PPE). Always consult the Safety Data Sheet (SDS) and support article as the primary sources of information to understand safety and handling of Formlabs materials.