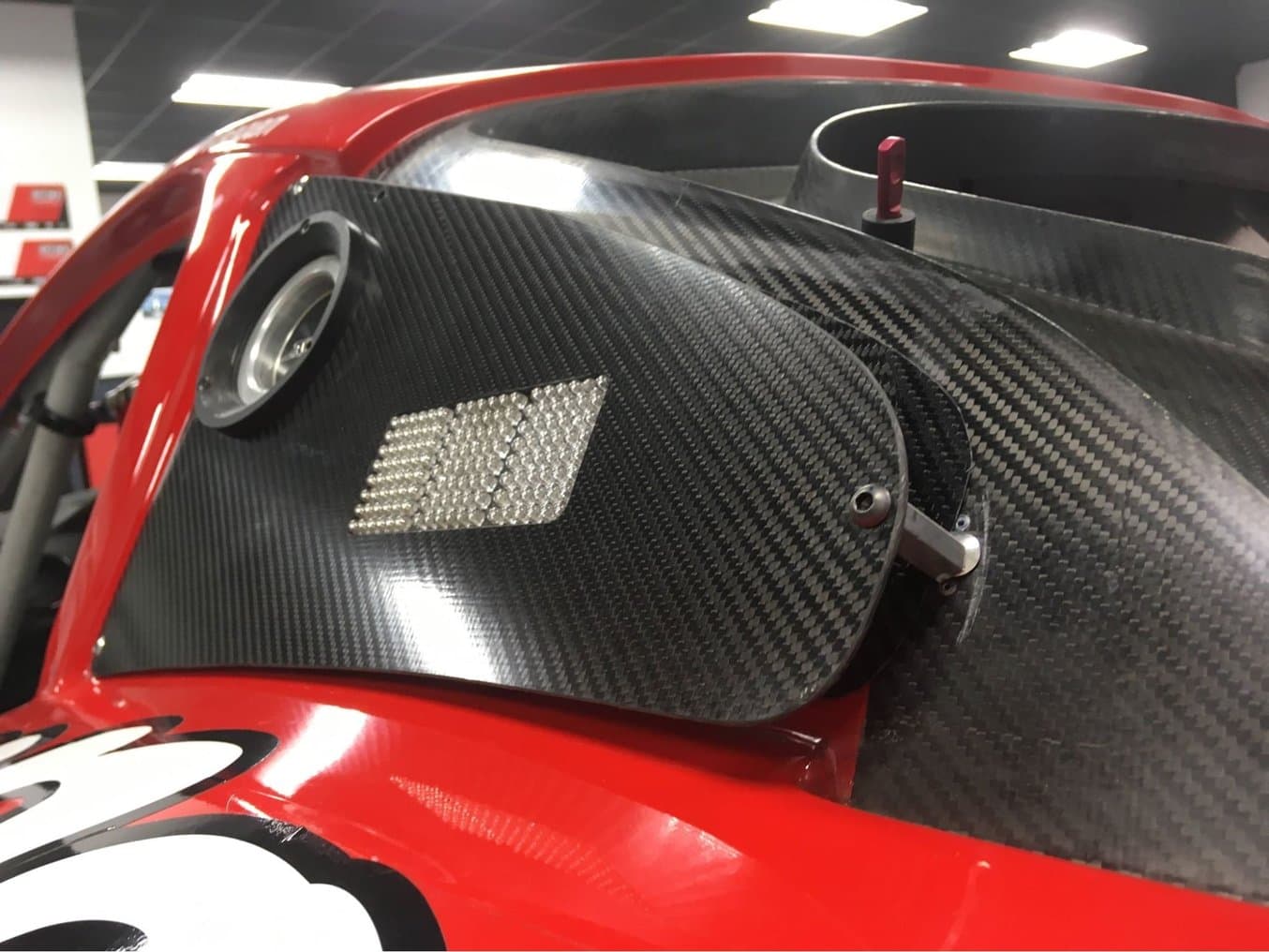
Composite materials, such as carbon fiber reinforced plastics are highly versatile and efficient materials, driving innovation in various markets from aerospace to healthcare. They outperform traditional materials such as steel, aluminum, wood, or plastic, and enable the fabrication of high-performance lightweight products.
In this guide, learn the basics of manufacturing carbon fiber parts, including the different carbon fiber layup, lamination, and molding methods, and how you can use 3D printing to make carbon fiber molds to lower costs and save time.
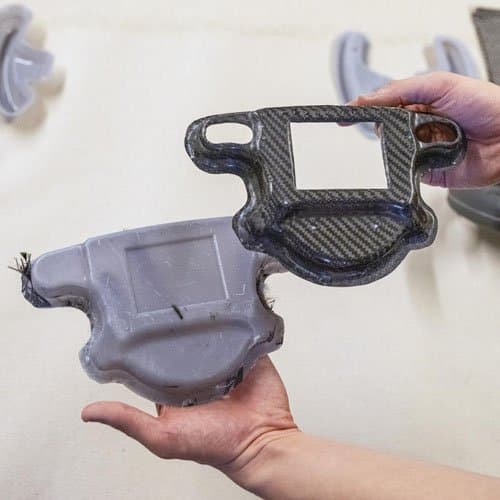
Carbon Fiber Parts Manufacturing With 3D Printed Molds
Download this white paper for composite mold design guidelines and step-by-step guides to the prepreg and hand laminating methods to create carbon fiber parts.
Composite Materials 101
A composite material is a combination of two or more constituents with characteristics different from those individual components by themselves. Engineering properties are typically improved, such as added strength, efficiency, or durability. Composites are made of reinforcement - fiber or particle - held together by a matrix (polymer, metal, or ceramics).
Fiber-reinforced polymers (FRP) dominate the market and have fueled the growth of new applications in various industries. Among them, carbon fiber is a widely used composite in particular for aircraft, racing cars, and bicycles as it is more than three times stronger and stiffer than aluminum, but 40% lighter. It is formed by reinforced carbon fiber linked with an epoxy resin.
Fibers can be directionally uni-weave and strategically aligned to create strength relative to a vector. Cross woven fibers can be used to create strength in multiple vectors and they are also responsible for the signature quilted look of composite parts. It is common for parts to be produced with a combination of both. There are multiple types of fibers available, including:
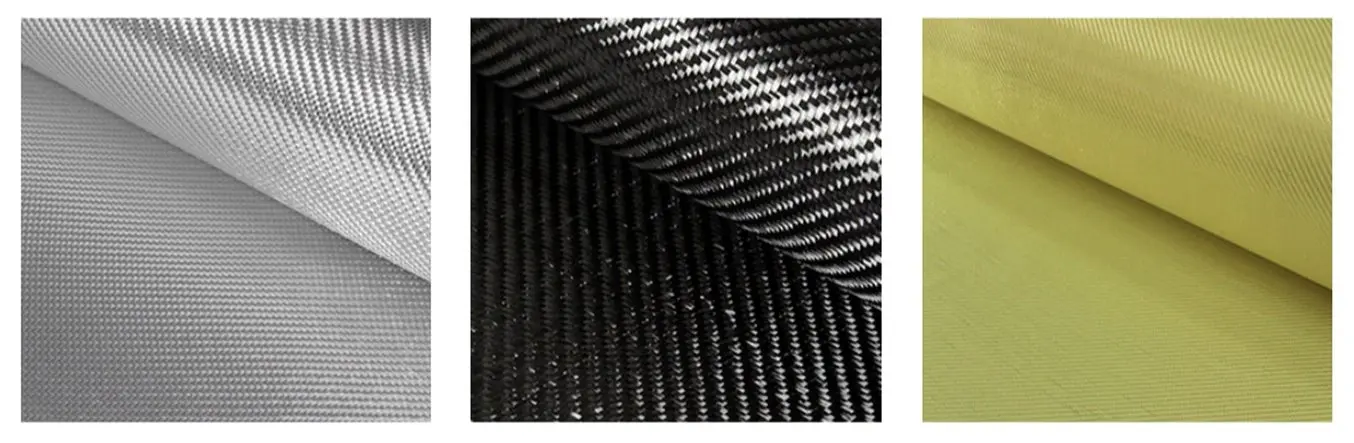
Fiberglass | Carbon fiber | Aramid fiber (Kevlar) |
---|---|---|
The most popular fiber Lightweight, moderate tensile and compressive strength Low cost and easy to work with | Highest strength and stiffness-for-weight ratio in the industry (ultimate tensile, compressive, and flexural strength) More expensive than other fibers | Higher impact and abrasion resistance than carbon fiber Low compressive strength Difficult to cut or machine |
Resin is used to hold these fibers together and create a rigid composite. While hundreds of types of resins can be employed, here are the most popular ones:
Resin | Pros | Cons | Curing |
---|---|---|---|
Epoxy | Highest ultimate strength Lightest weight Longest shelf life | Most expensive Sensitive to mix ratio and temperature variations | Uses a specific hardener (two-part system) Some epoxies require heat |
Polyester | Easy to use (most popular) UV resistant Lowest cost | Low strength and corrosion resistance | Cures with a catalyst (MEKP) |
Vinyl Ester | Mixes the performance of epoxy and the cost of polyester Best corrosion, temperature resistance, and elongation | Lower strength than epoxy and higher cost than polyester Limited shelf life | Cures with a catalyst (MEKP) |
Three Methods for Creating Carbon Fiber Parts
Manufacturing fiber-reinforced polymers, such as carbon fiber parts is a skillful and labor-intensive process used in both one-off and batch production. Cycle time ranges from one hour to 150 hours depending on the size and complexity of the part. Typically in FRP fabrication, the continuous straight fibers are joined in the matrix to form individual plies, which are laminated layer-by-layer onto the final part.
The composite properties are induced by the materials as much as the laminating process: the way the fibers are incorporated strongly influences the performance of the part. The thermoset resins are shaped together with the reinforcement in a tool or mold, and cured to form a robust product. There are various laminating techniques available, which can be differentiated into three main types:
1. Wet Lay-Up
In wet lay-up, the fiber is cut and laid into the mold then resin is applied via a brush, roller, or spray gun. This method requires the most skills to create high-quality parts, but it is also the least expensive workflow with the lowest requirements to get started with making DIY carbon fiber parts. If you are new to carbon fiber parts manufacturing and not equipped yet, we would recommend starting with wet lay-up hand lamination.
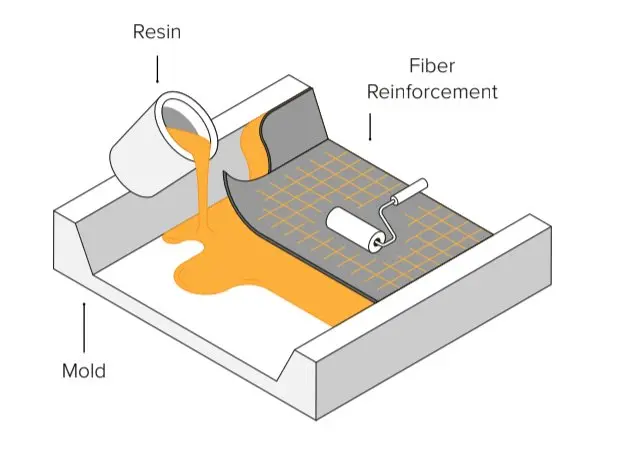
Watch the video to see how the wet carbon fiber lay-up process works.
2. Prepreg Lamination
With prepreg lamination, the resin is infused in the fiber ahead. Pre-impregnated sheets are stored cold to inhibit the cure. Plies are then cured into the mold under heat and pressure in an autoclave. This is a more precise and repeatable process because the quantity of resin is controlled but it is also the most expensive technique that is usually used in high-performance applications.
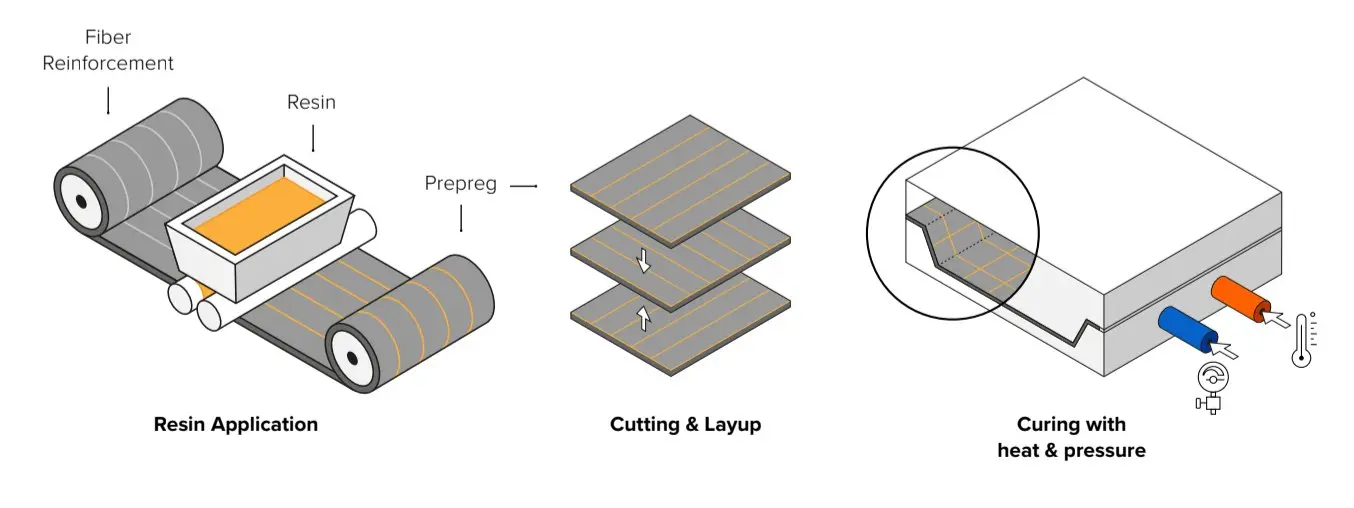
3. Resin transfer molding (RTM)
With RTM molding, the dry fiber is inserted into a two-part mold. The mold is clamped shut before forcing the resin into the cavity at high pressure. It is usually automated and used for larger volume manufacturing.
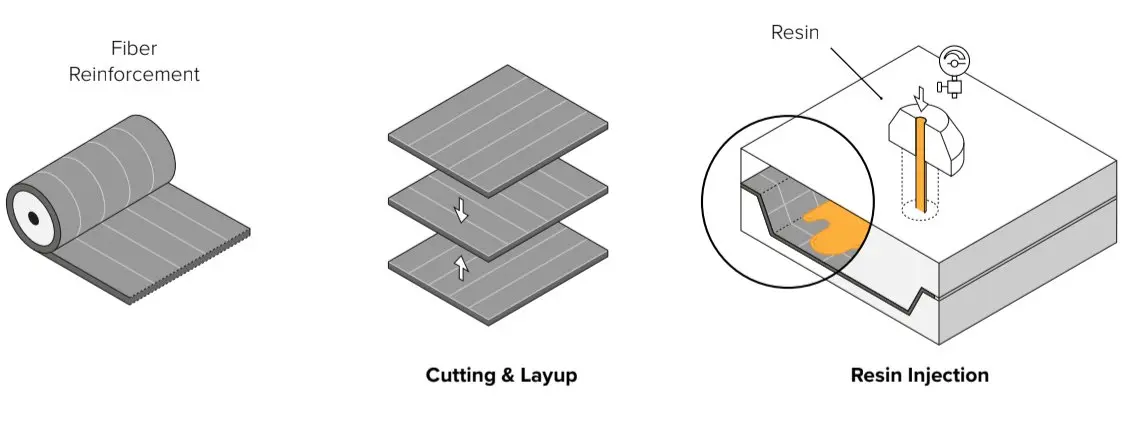
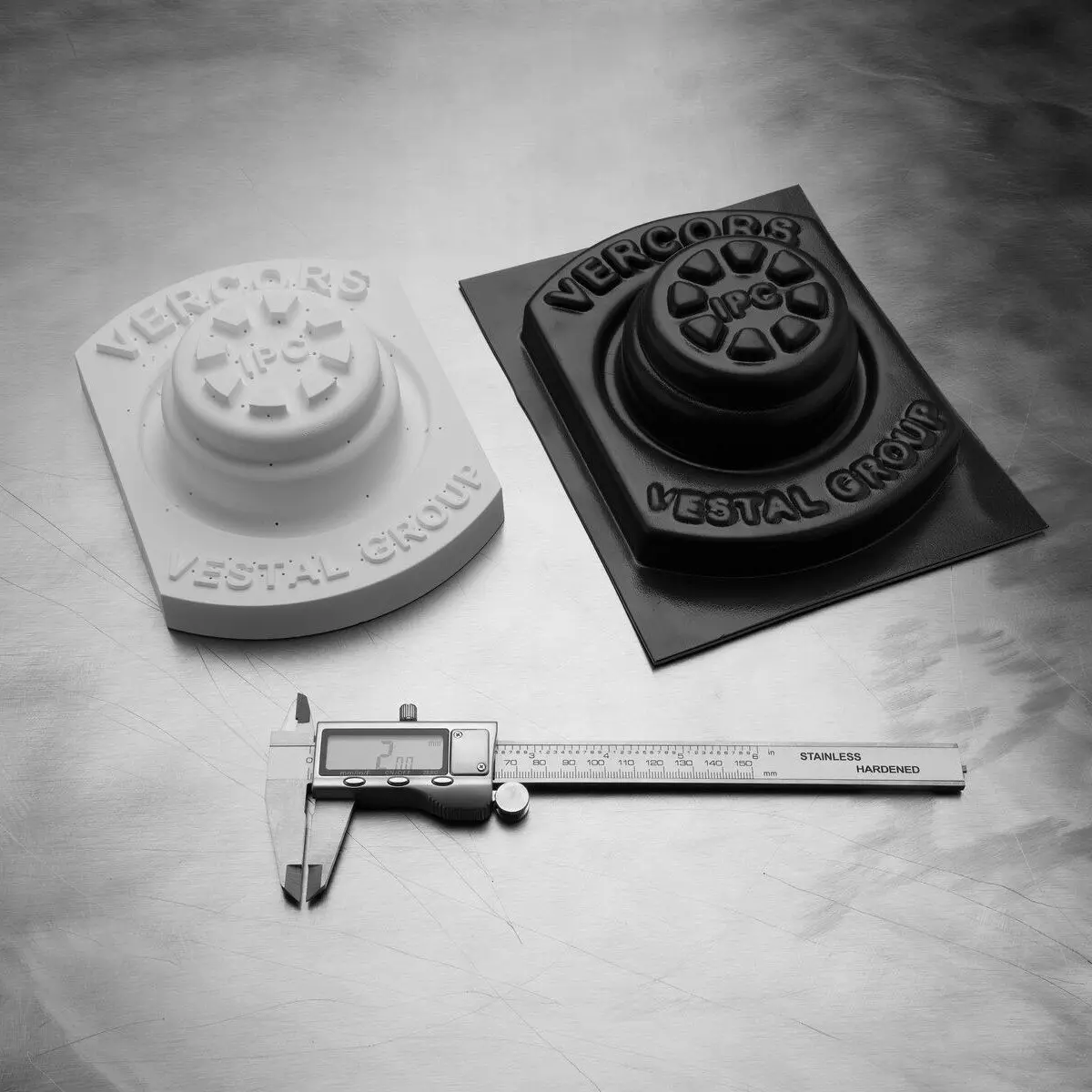
Low-Volume Rapid Thermoforming With 3D Printed Molds
Download our white paper to see how to create complex molds with 3D printing fast and learn about tips and guidelines that you’ll want to follow when preparing your mold parts.
Creating Molds for Carbon Fiber Parts Manufacturing with 3D Printing
Because the quality of the mold directly impacts the quality of the final part, tool making is a critical aspect of FRP manufacturing. Most molds are produced out of wax, foam, wood, plastic, or metal via CNC machining or handcrafting. While manual techniques are highly labor-intensive, CNC machining still follows a complex, time-consuming workflow—especially for intricate geometries—and outsourcing typically comes at a high cost, with a long lead time. Both options require skilled workers and offer little flexibility on design iterations and mold adjustments.
Additive manufacturing offers a solution for rapidly producing molds and patterns at low costs for making carbon fiber parts. The use of polymeric tooling in manufacturing processes is growing continuously. Replacing metal tools with plastic parts printed in-house is a powerful and cost-effective means to shorten production time while expanding design flexibility. Engineers already work with polymer resin 3D printed parts for manufacturing jigs and fixtures to support methods such as filament winding or automated fiber placement. Likewise, short-run printed molds and dies are employed in injection molding, thermoforming or sheet metal forming to deliver low-volume batches.
In-house desktop 3D printing requires limited equipment and reduces workflow complexity. Professional desktop resin printers like the Form 3+ are affordable, easy to implement, and can be quickly scaled with the demand. Manufacturing large tools and molds is also possible with large format 3D printers such as the Form 3L.
Stereolithography (SLA) 3D printing technology creates parts with a very smooth surface finish, which is essential for carbon fiber layup molds. It allows for complex geometries with high precision. Additionally, the Formlabs Resin Library has engineering materials with mechanical and thermal properties that pair well with mold and pattern manufacture.
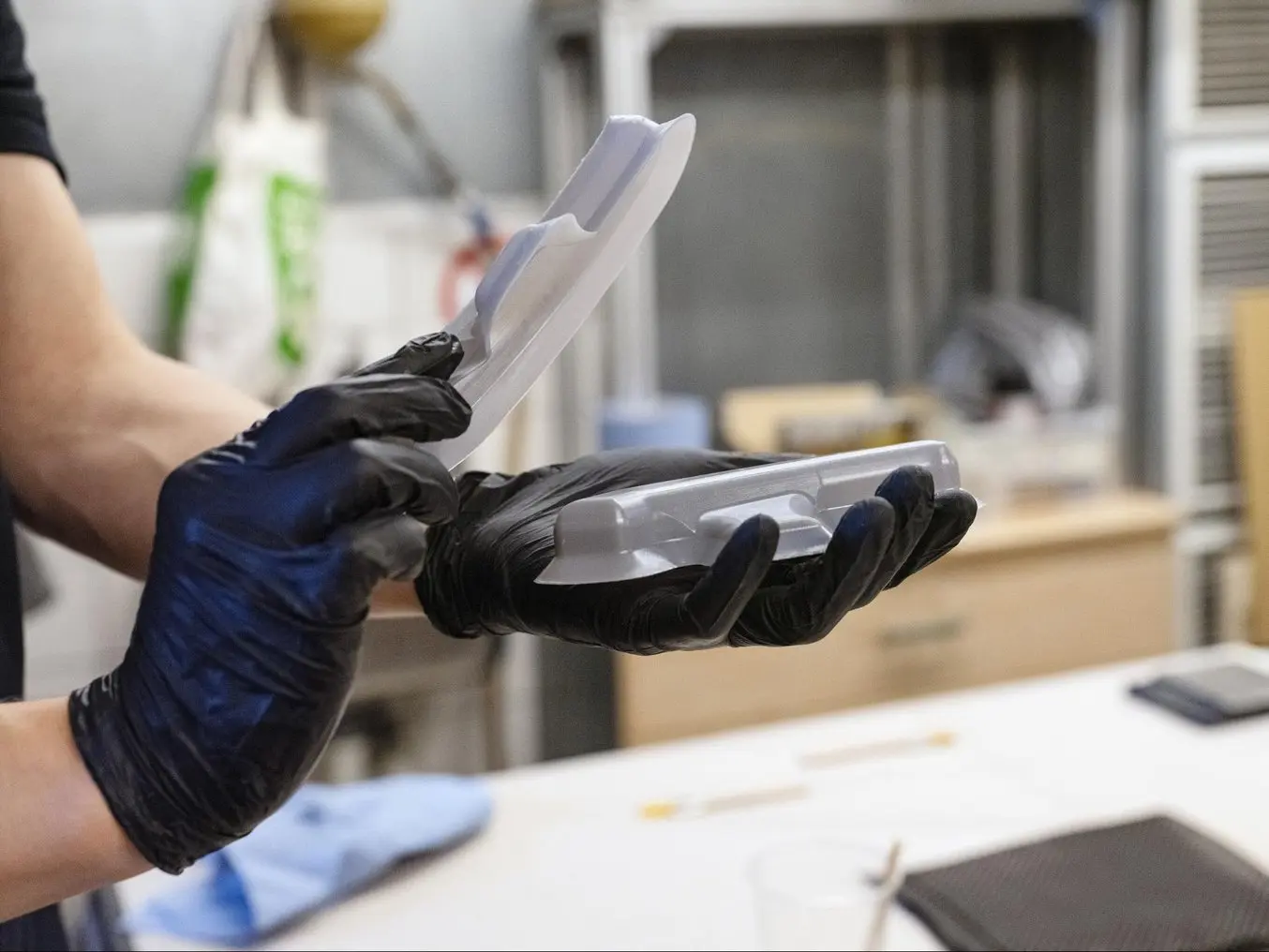
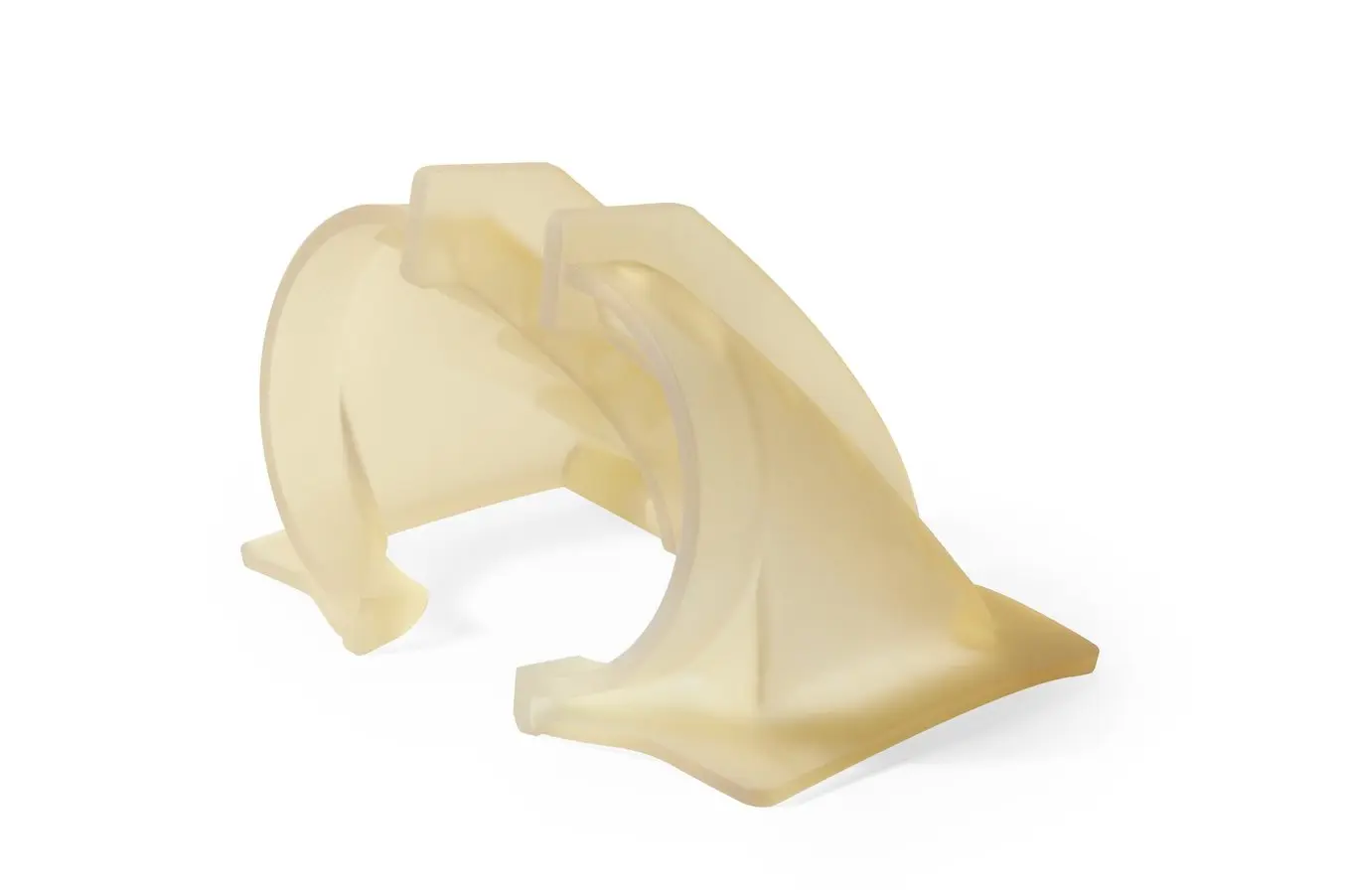
3D printed molds for manufacturing carbon fiber parts can reduce costs and lower lead times.
For small-scale production, engineers can directly print the mold at low costs and within a few hours without having to hand carve it or deal with CNC equipment; CAM software, machine setup, workholding, tooling, and chip evacuation. Labor and lead time for mold fabrication are drastically reduced, allowing for quick design iteration and parts customization. They can achieve complicated mold shapes with fine details that would be difficult to manufacture with traditional methods.
The Formula Student team of TU Berlin (FaSTTUBe) manufactured a dozen of carbon fiber parts for racing cars. Engineers in the team hand laminate on a mold directly printed with Formlabs Tough 1500 Resin. This resin is characterized by a tensile modulus of 1.5 GPa and elongation at break of 51%. It is not only strong and supportive during the layup but also sufficiently flexible to separate the part from the mold after curing.
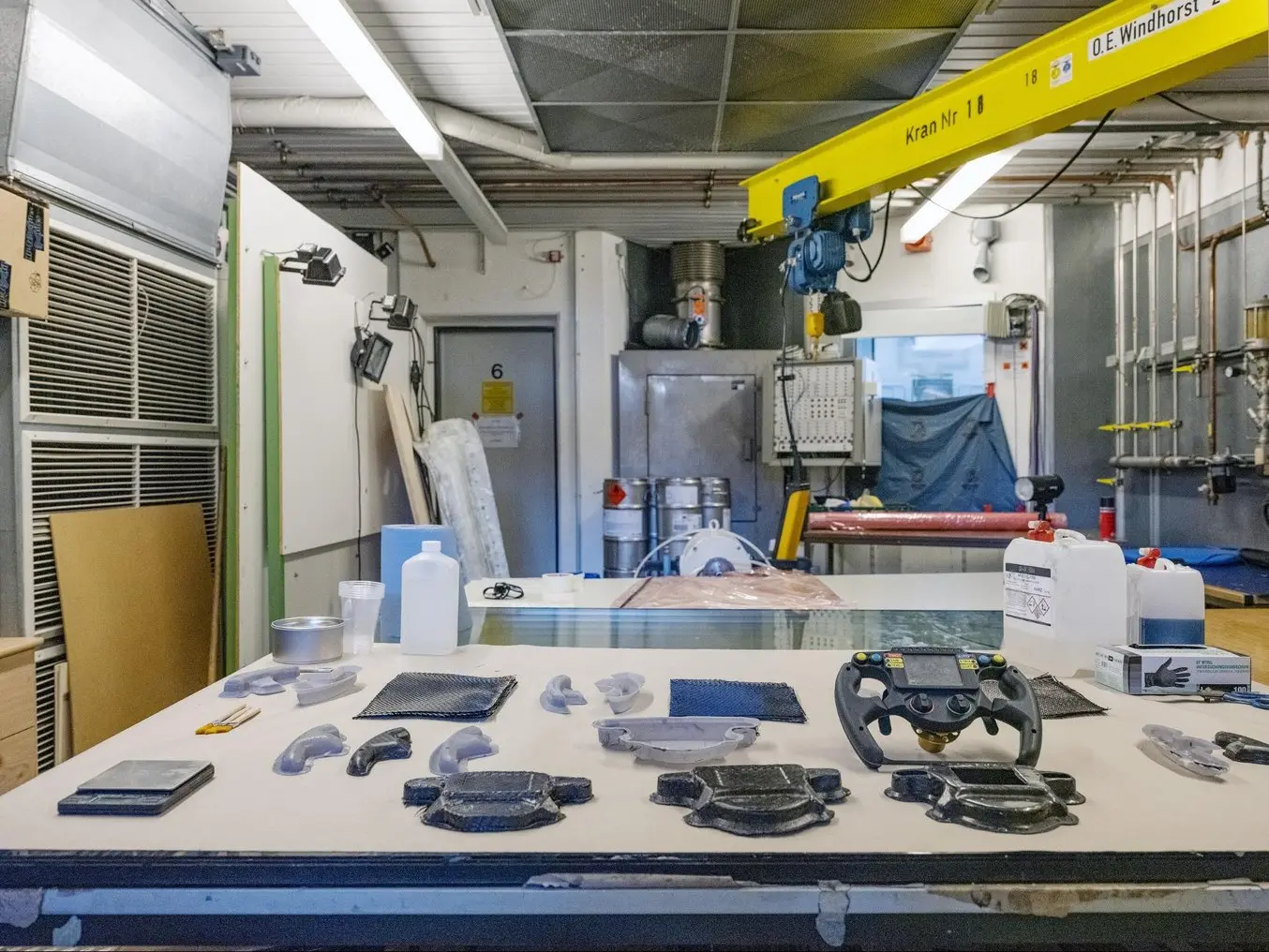
The FaSTTUBe test bench with the carbon fiber parts manufacturing set up.
While this technique is not associated with intensive curing conditions, other laminating processes often involve higher pressures and temperatures. The company DeltaWing Manufacturing uses High Temp Resin to create air flow components through the prepreg process. High Temp Resin has a heat deflection temperature (HDT) of 238°C @ 0.45 MPa and is able to sustain the heat and pressure of an autoclave. DeltaWing Manufacturing has been directly printing molds to produce a series of about 10 customized parts.
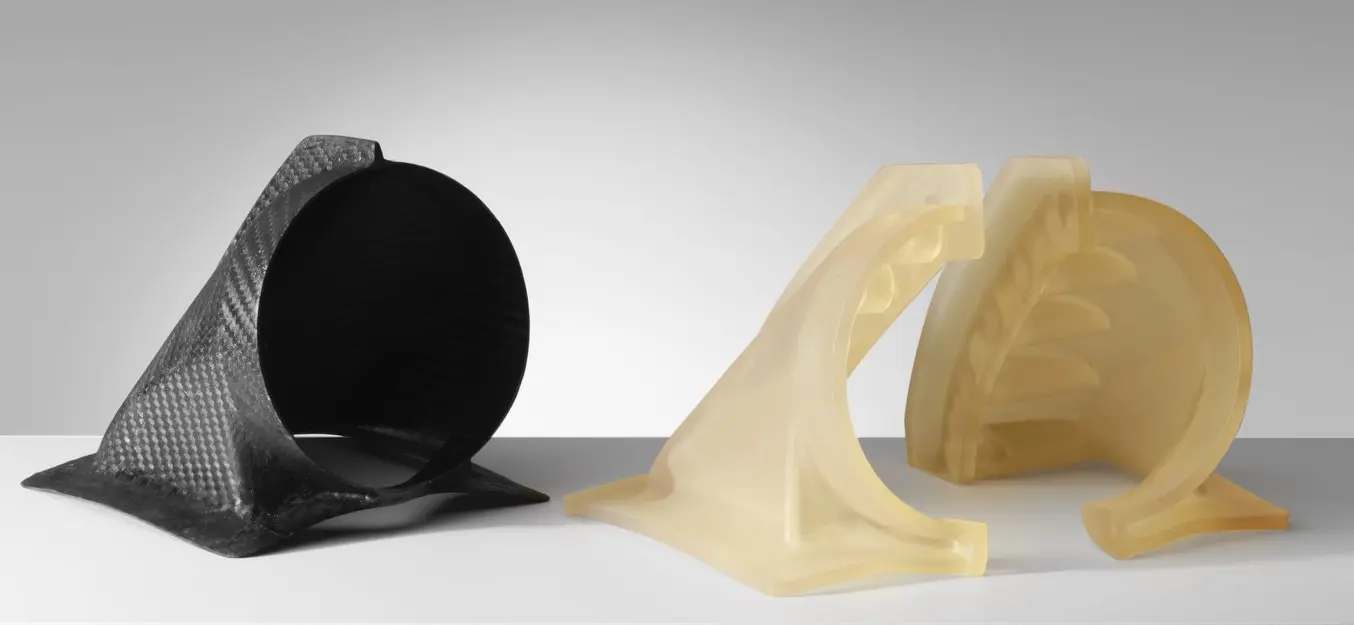
A carbon fiber fender air duct next to the two-parts mold printed with High Temp Resin, produced by DeltaWing Manufacturing.
Direct 3D printed polymeric molds are great tools to optimize short-run production. However, their lifetime is reduced from traditional molds, which makes them not suitable for high volume series.
To increase production, DeltaWing Manufacturing prints mold patterns with High Temp Resin and then casts them in resin. Printing the pattern is also a powerful alternative for laminating processes requiring intensive curing conditions that are not suitable for 3D printed molds. Manufacturers can print customized patterns on-demand and still eliminate one step from their mold-making technique, the pattern fabrication.
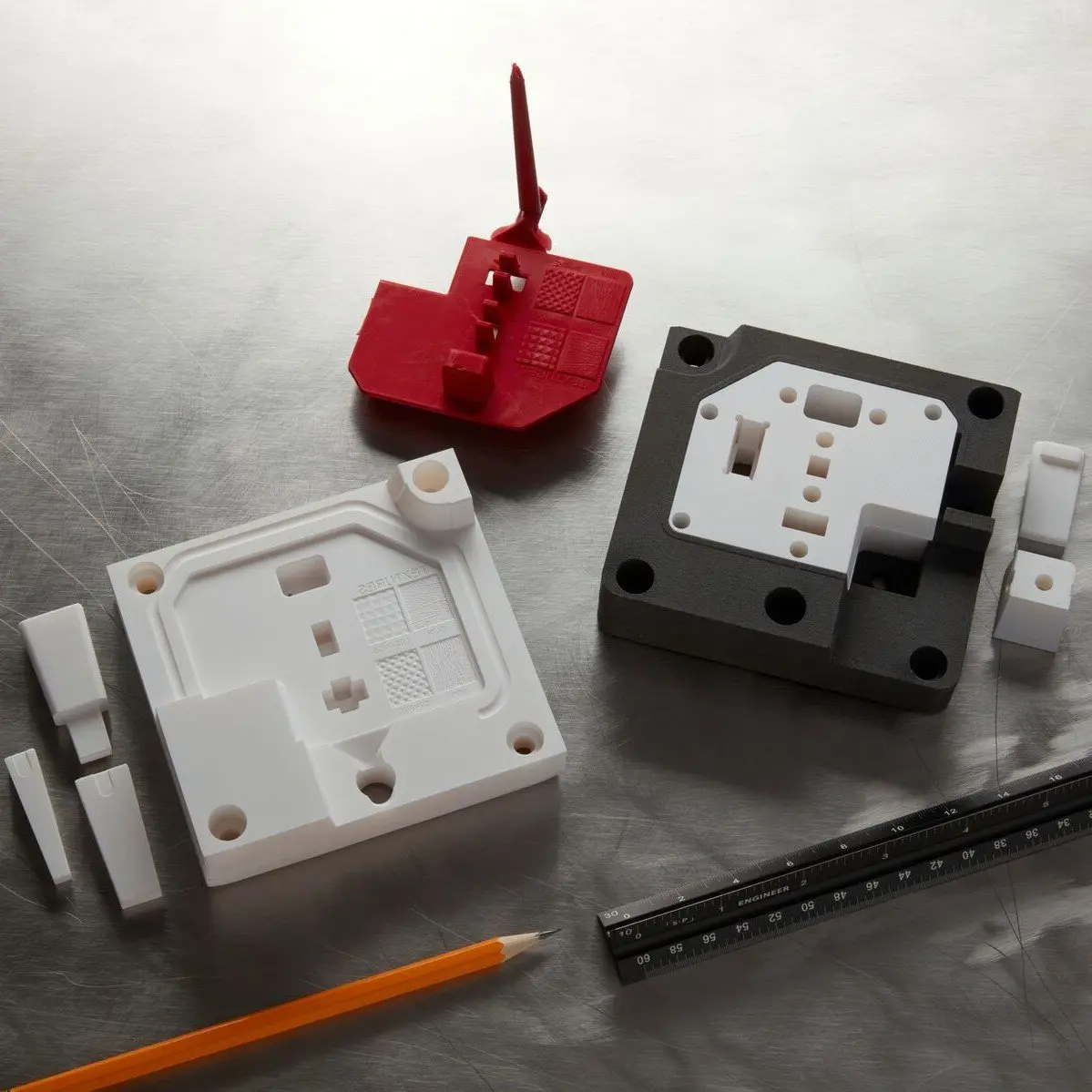
Guide to Rapid Tooling
In this white paper, learn how to combine rapid tooling with traditional manufacturing processes like injection molding, thermoforming, or casting.
Carbon Fiber 3D Printing
There is strong demand for workflows that combine the strength, durability, and ruggedness of traditional carbon fiber parts with the agility, geometric possibilities, and repeatability of 3D printing. It’s therefore not surprising that there are many 3D printing companies that offer carbon fiber 3D printing, with the two currently available processes being printing with chopped fibers or continuous fibers.
Using chopped carbon fibers, Nylon 11 CF Powder for the Fuse 1+ 30W selective laser sintering (SLS) industrial 3D printer enables manufacturers to create strong, lightweight, and heat-resistant parts, without relying on traditional overlay or machining methods.
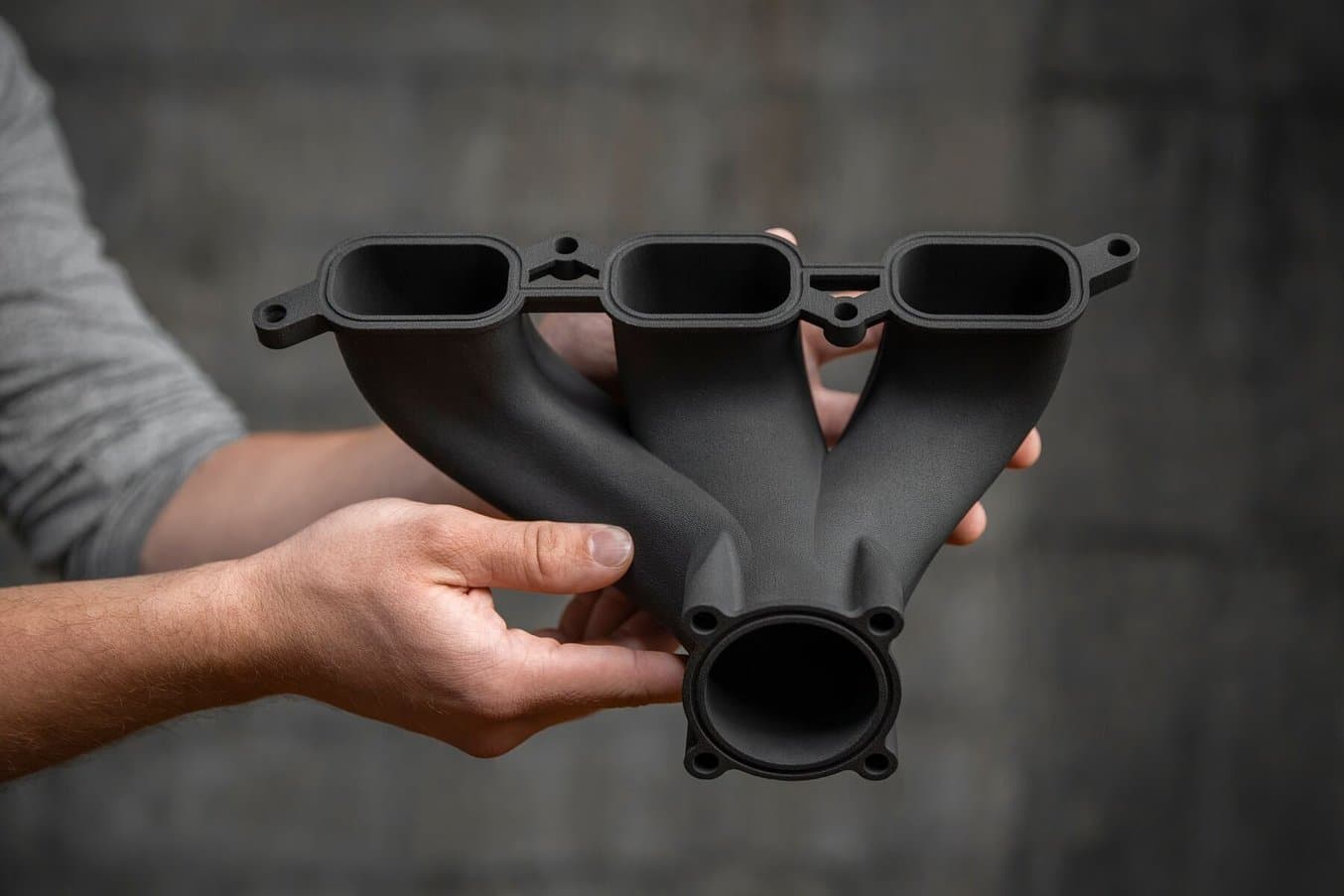
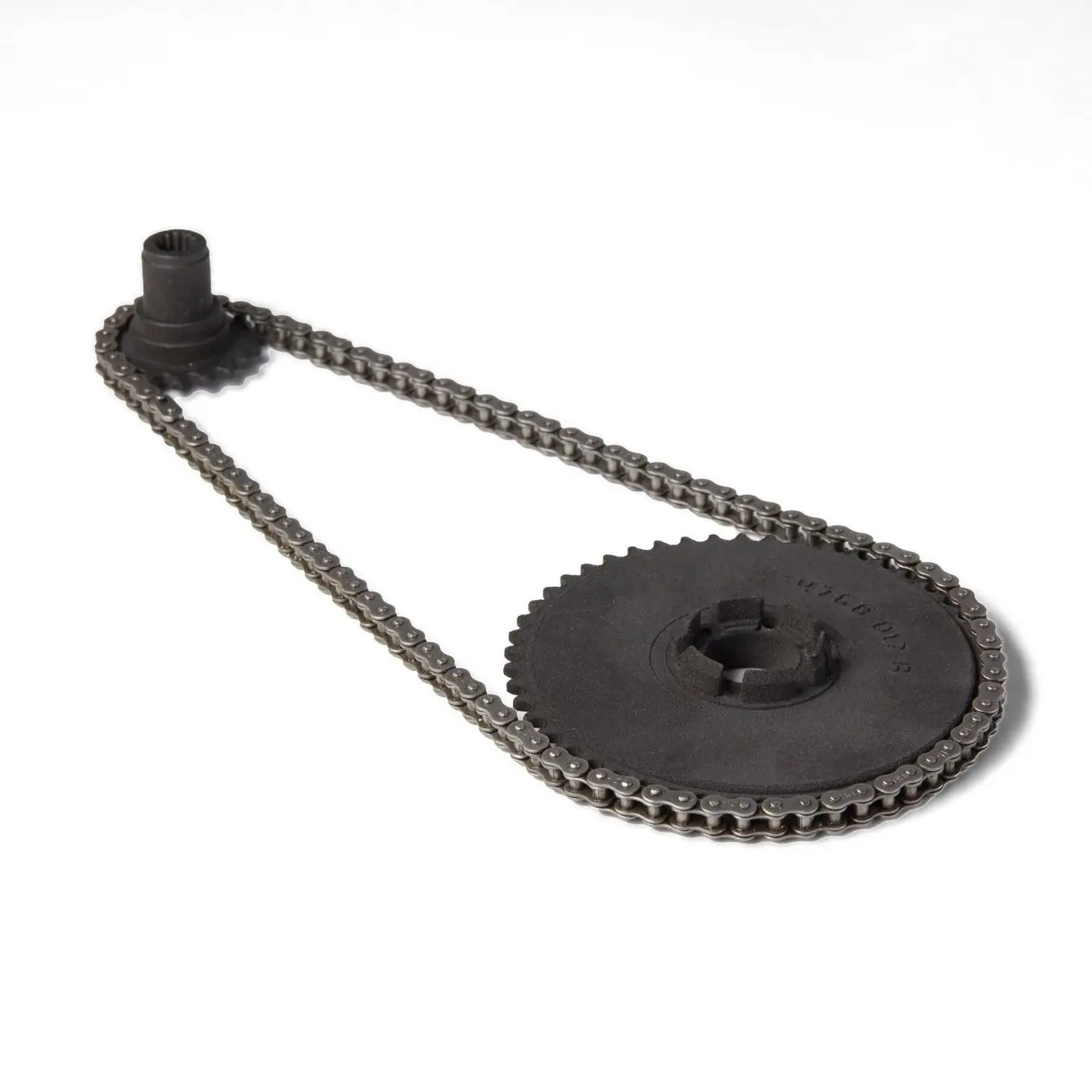
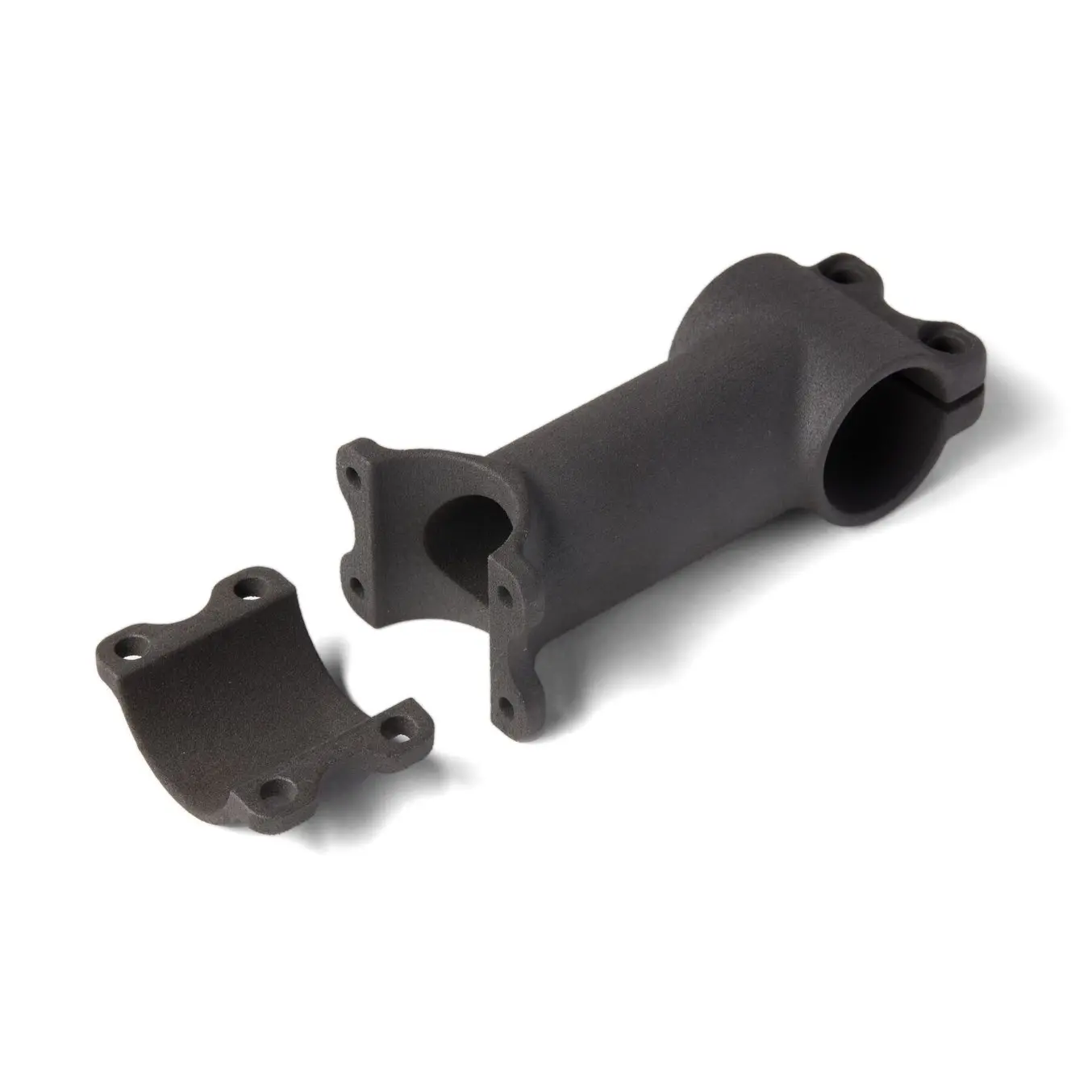
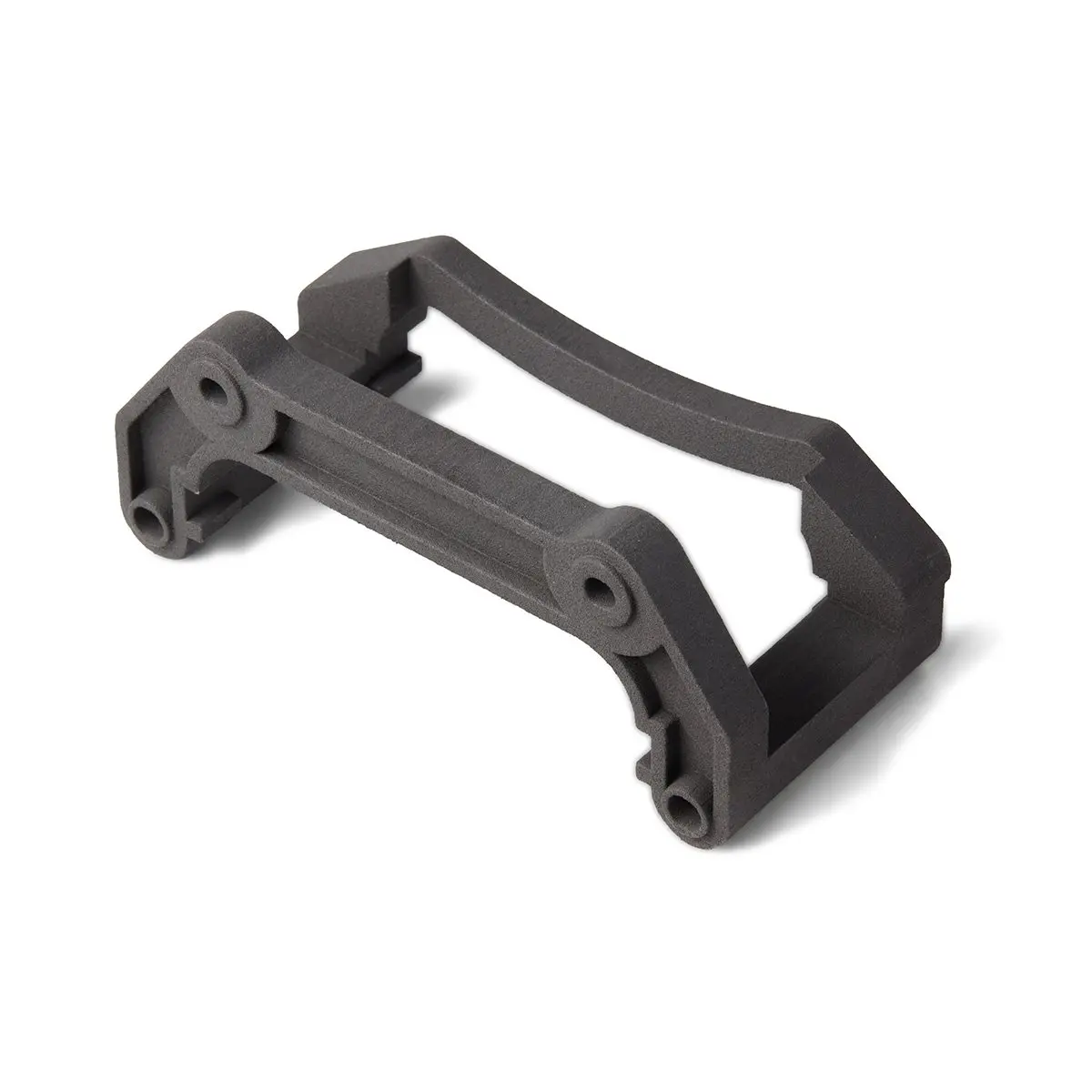
Formlabs Nylon 11 CF Powder is strong, lightweight, and heat resistant, making it ideal for automotive, aerospace, and manufacturing applications.
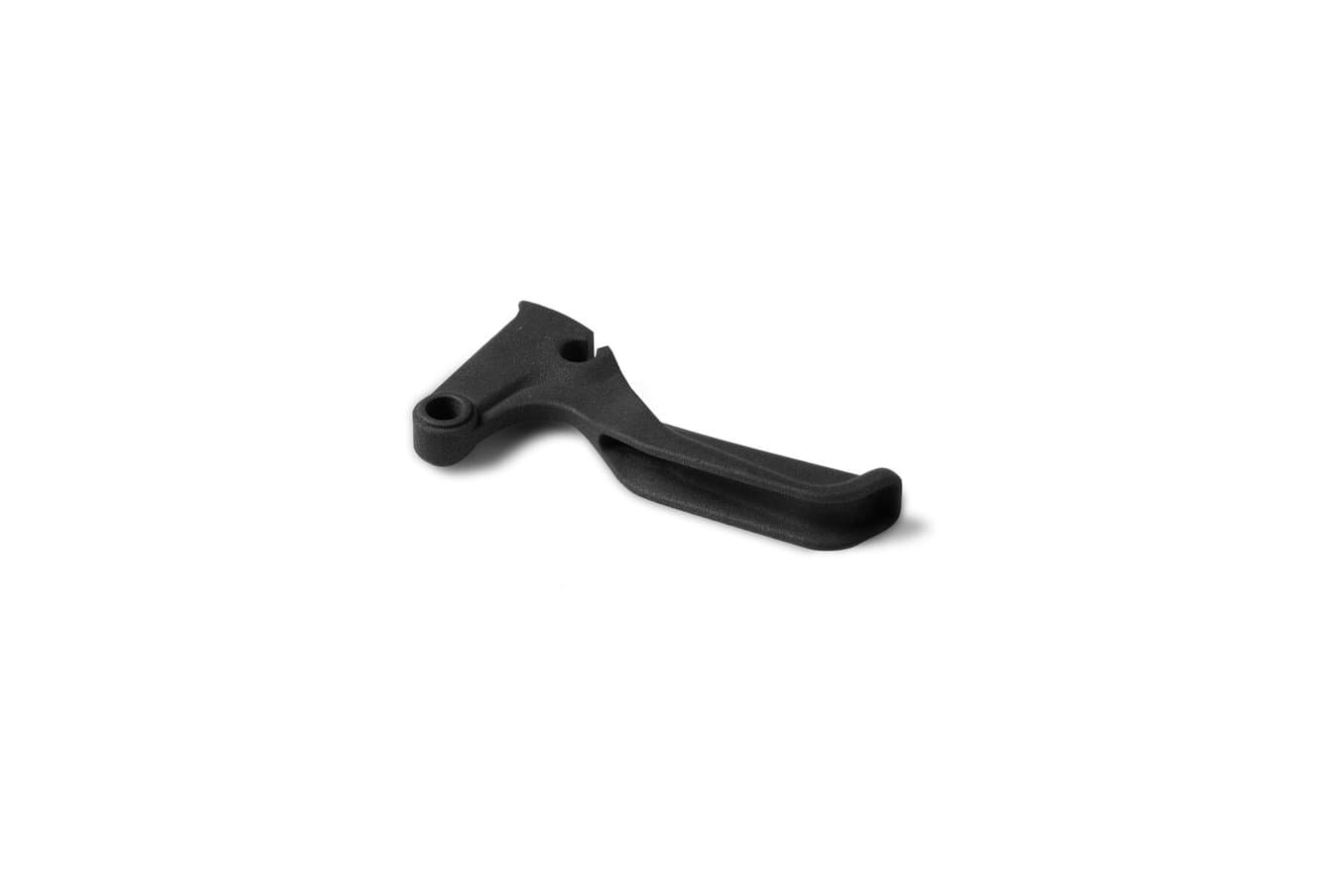
Request a Free Sample Part
See and feel Formlabs quality firsthand. We’ll ship a free sample part to your office.
Get Started With Carbon Fiber Manufacturing
Fiber-reinforced polymer manufacturing is an exciting, yet intricate, and labor-intensive process. Using 3D printed molds and patterns to make carbon fiber parts allows businesses to reduce workflow complexity, expand flexibility and design opportunities, and reduce costs and lead time.
Through case studies with TU Berlin and DeltaWing Manufacturing, our white paper presents three workflows to leverage 3D printing in composite manufacturing with the fast fabrication of molds and patterns.