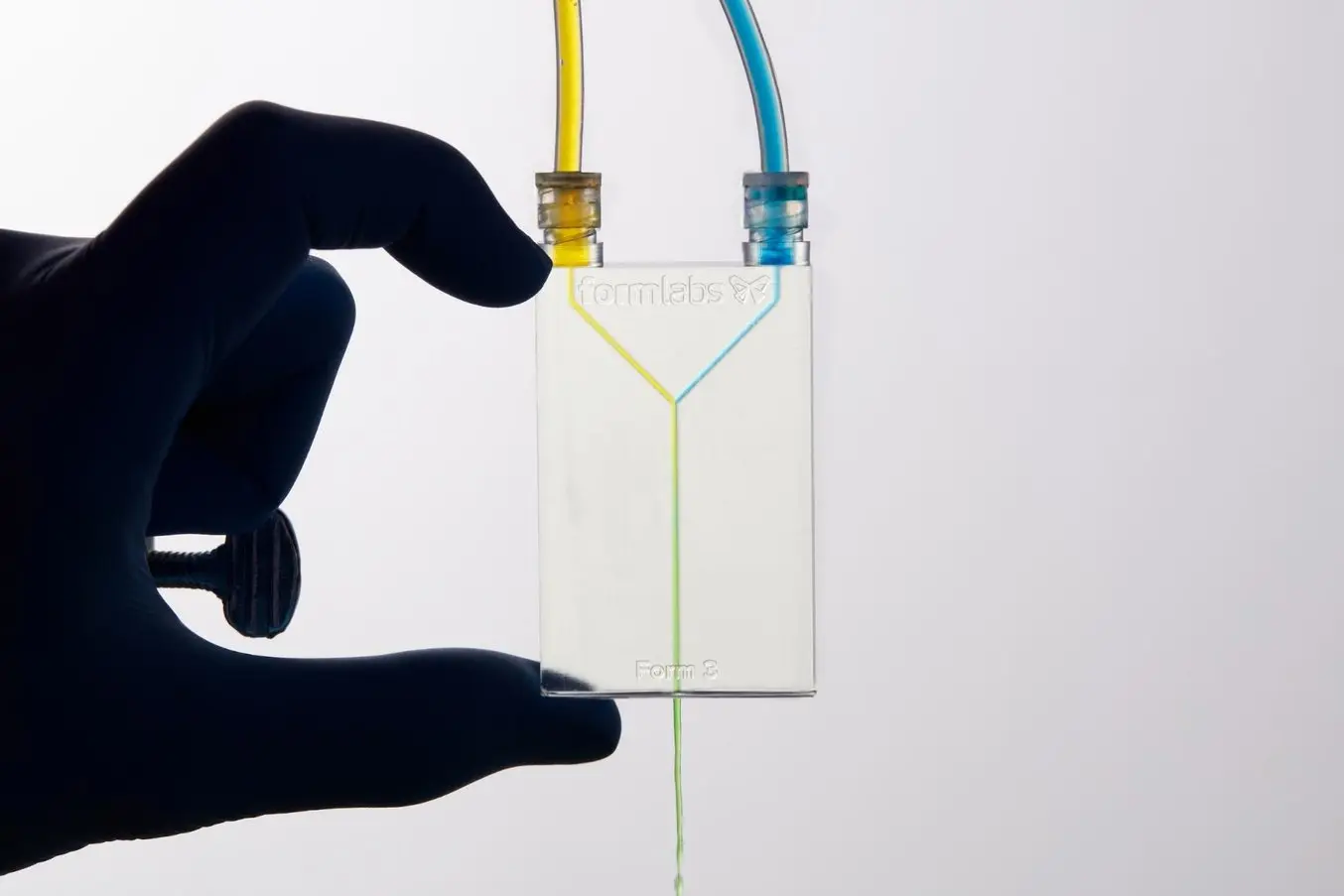
Microfluidics is one of the coolest technologies in the world of science and engineering. It’s playing a major role in some of the most cutting-edge developments in biodefense, chemical engineering, and medical testing.
In this guide, we’ll provide an overview of microfluidics, explain how it’s helping scientists make new discoveries, and show you how to get started creating your own microfluidic chips.
What Is Microfluidics?
Microfluidics is the science of precise control and manipulation of fluids that are geometrically constrained to a small scale, typically lower than 100 µm diameter, networks of channels.
People use the term microfluidics differently; it depends on the scientist or engineer you’re talking to. For many professors, microfluidics is a field of science focusing on the study and manipulation of tiny amounts of fluid through channels between 100 micrometers (µm) and 1µm in diameter.
Engineers, on the other hand, may use the term microfluidics to describe the manufacturing of parts (often referred to as chips) that guide the movement of fluids through channels 100 µm to 1µm in diameter.
Why Is Microfluidics Important?
In its most basic form, microfluidics is work involving tiny amounts of fluid—just tens of micrometers across. For reference, a micrometer is one-millionth of a meter. A strand of human hair is roughly 100 µm in diameter.
The benefits of working on this ultra-small scale are numerous. Compared to traditional testing methods using Petri dishes and eyedroppers, microfluidics utilizes significantly smaller sample sizes, which means you need lower amounts of costly chemicals and reagents. Microfluidics testing is safer in many instances as well, because toxic substances can be more controlled and contained.
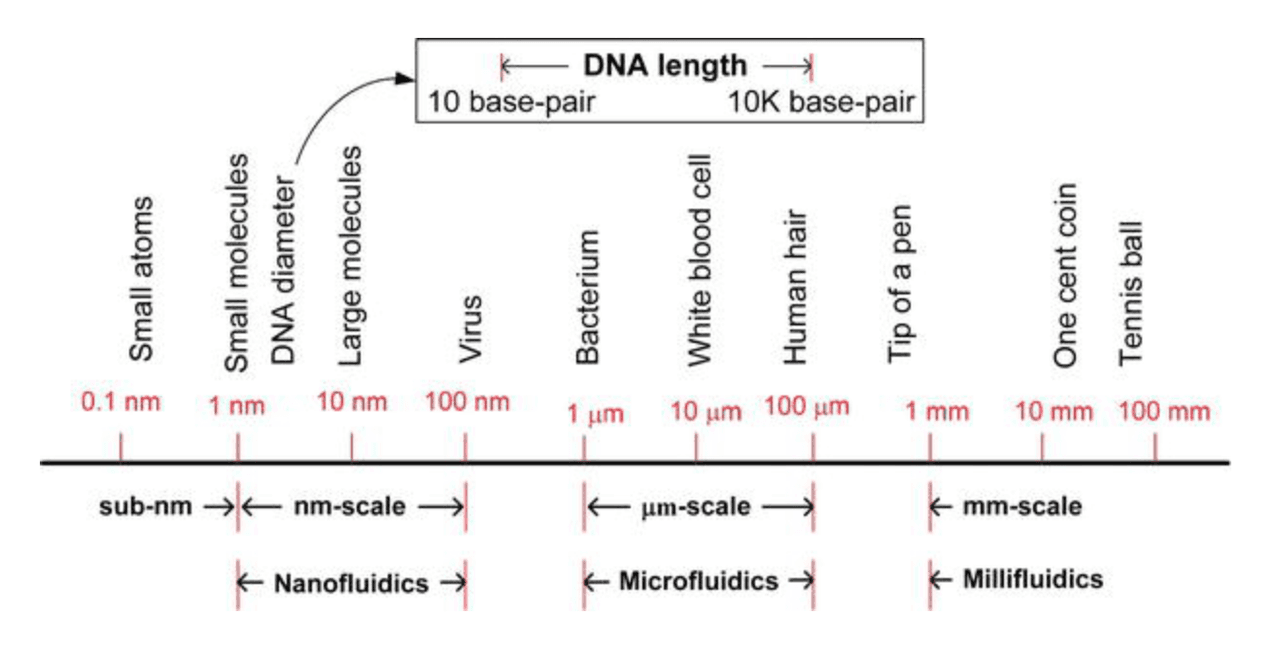
Examples of an approximate scale of things and the boundaries between nano, micro and millifluidics. (source)
Scientists also have a higher level of control with microfluidics, particularly when it comes to how fluids are mixed and the way they interact with one another. They can diffuse liquids slowly, have them flow side-by-side, or separate them into microscopic-sized droplets. Scientists and engineers can also employ electric charges, syringe pumps, and even acoustics to push liquids through microchannels.
These cost and control benefits make microfluidics a rapidly growing area of interest for pioneers in both pharmacology and biotechnology. Microfluidics innovators are developing faster and cheaper ways to test patients for viruses, detect harmful chemicals in soil, and may one day make animal testing obsolete.
How Is Millifluidics Different From Microfluidics?
Millifluidics involves manipulating and observing fluids in channels that are 1 millimeter (mm) across. And while millifluidics uses larger amounts of fluid than microfluidics, it’s still a minimal amount compared to tests performed with traditional testing methods.
Millifluidic channels can often achieve the same level of fluid mixing as microfluidic channels, depending on the project requirements. Millifluidics offer many of the same benefits as microfluidics, but millifluidic chips are often easier and cheaper to manufacture.
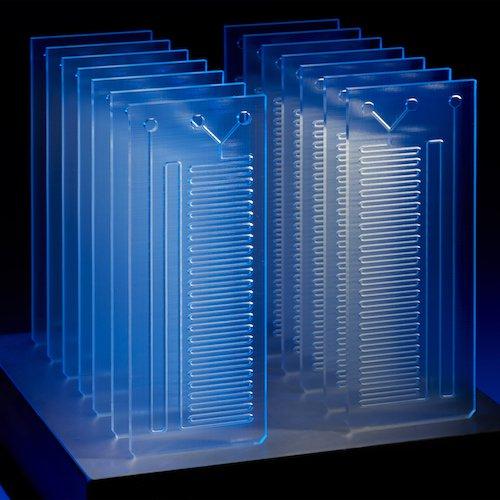
Desktop Millifluidics With SLA 3D Printing
This white paper delves into the implementation of millifluidic geometries using stereolithography (SLA) 3D printing and best practices for fabricating millifluidic chips in-house.
The Applications of Microfluidics and Millifluidics
The real-world applications of microfluidics and millifluidics range from simplified versions of commonplace medical tests to groundbreaking research projects. As you will see in the breadth of applications below, microfluidics and millifluidics are helping shape the future—and what’s on the horizon is truly fascinating.
Biotechnology
Regenerative medicine has focused on stem cell research for years—in large part because of their ability to divide and become other types of differentiated cells. When physicians inject stem cells into muscle tissue, for example, they can differentiate and become muscle cells, thus helping to repair and regenerate damaged tissue.
Cultivating and developing embryonic stem cells in vitro (outside of the body) has been one of the biggest challenges for stem cell researchers. This is due to the lack of morphogens and signaling produced in vivo (inside the body). Morphogens are like the conductors in the orchestra of embryonic development—they play a key role in stimulating the development of embryonic cells.
Scientists at the Swiss Federal Institute of Technology Lausanne recently found a way to overcome this morphogen challenge. Dr. Matthias Lütolf and his team replicated a process of embryonic stem cell development called gastrulation—which takes place at about the third week of human pregnancy—by introducing a carefully controlled regimen of morphogens in vitro using a microfluidic cell culture device.
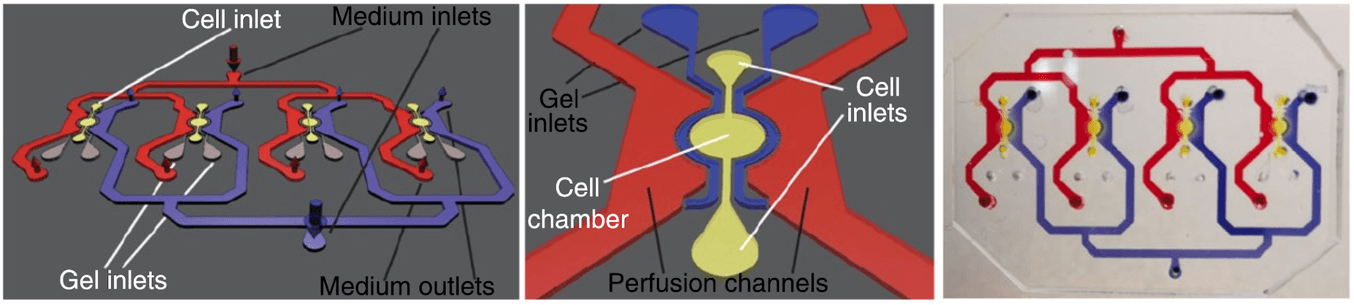
The polydimethylsiloxane (PDMS)-based microfluidic cell culture device developed by EPFL scientists. (source)
This is a significant development on the road to growing organs in a lab. As Dr. Lütolf explained in an interview with Genetic Engineering & Biotechnology News, “One of our long-term goals is to engineer organs for transplantation.”
Pharmaceutical Engineering
3D cell cultures, such as the microfluidic devices used by Dr. Lütolf and his team, are likely to revolutionize pharmaceutical engineering in addition to biotechnology. In fact, 3D cell cultures may one day make animal testing completely obsolete.
Drug testing typically begins with in vitro cultures, or 2D testing, outside of the body. If these tests show promising results, the next step is usually to test medications in animal models. The reason for this is that animal testing was the closest scientists could get to replicating what happens inside the human body before moving to human clinical testing.
3D cell cultures offer a promising new frontier in pharmaceutical testing and engineering. These cultures allow cells to develop more like they would inside the body, in an easy-to-see device outside of the body. Testing can be carefully controlled and may even provide results that are more accurate than animal testing.
Researchers at the Wyss Institute have developed human “Organs-on-Chips,” which allow scientists to study the impacts of bacteria, viruses, and therapies on in vitro tissue using a device roughly the size of a computer thumb drive.
Further research and development is needed before animal testing is gone for good, but 3D cell cultures may indeed be the new future of pharmaceutical and biological engineering.
Patient Testing and Diagnostics
In the not-so-distant future, microfluidics may radically change patient testing. Smaller amounts of blood or tissue may be required for diagnostics testing, resulting in a better patient experience. Genetic testing also may become more accessible.
Particularly for patients in geographical areas where lab testing is unavailable, lab-on-a-chip devices, like those being developed by University of Washington bioengineering professor Paul Yager, could be an affordable way to diagnose diseases like malaria.
Meanwhile, Professor Jason Heikenfeld of the University of Cincinnati is leading a team of researchers in developing completely non-invasive microfluidic sweat-analysis tests that may eliminate the need for blood to be drawn in certain cases. And Heikenfeld’s prototype can be conveniently powered by any smartphone.
Biodefense
For soldiers on the front lines, detecting biological and chemical weapons is a matter of life and death. That’s why the Defense Advanced Research Projects Agency (DARPA) has been funding microfluidics research for years.
Thanks to research and development conducted by Frantisek Svec and Jean Fréchet at Berkley Lab, the real threat of chemical warfare may soon be simple to detect. Svec and Fréchet are currently working on perfecting plastic microfluidic chips that would enable in-field testing for the presence of even diluted amounts of chemicals, microorganisms, toxins, and pollutants.
From a simple soil or air sample, soldiers may soon be able to perform tests that previously required extensive equipment. As Svec said, “We’ll take the lab to the sample rather than the sample to the lab.”
Chemical Engineering
As with most things, the applications of microfluidics are guided by the desires of the human wielding the technology. While much research involving microfluidics focuses on improving quality of life and society as a whole, we must also acknowledge that it could be used for more odious purposes, too.
Microfluidics is propelling biodefense capabilities, but there’s always the possibility that it may be used to develop biological and chemical weapons. Research published by national defense organizations such as the US Naval Institute has noted the possibility of some countries using microfluidics (which is easier to conceal given its small scale) to develop weapons without other countries knowing.
How to Make Microfluidics Chips
Each microfluidic project requires a custom-designed chip that needs to be manufactured on demand using advanced technologies capable of producing these intricate parts accurately. As the field of microfluidics continues to advance and adapt rapidly, it is informing and changing the way microfluidic chips themselves are manufactured as well.
Microfluidic chips are commonly made of glass, silicon, or plastic (though they can sometimes be crafted from other materials such as paper). Below, we will outline five common methods for manufacturing microfluidic and millifluidic chips. It is important to note that many engineers and manufacturing companies use a combination of production methods to design and produce chips.
Many engineers, scientists, and designers produce their chips in-house using a printing or manufacturing machine in their own lab to allow more freedom and faster turnaround times for prototyping.
Photolithography
Photolithography is one of the first manufacturing methods used in microfluidics and is still used today, often in conjunction with wet or dry etching. Photolithography harnesses the power of UV light to essentially burn a desired pattern or form into a component.
This video explains the process of photolithography and shows examples of applications in microfluidics as well as micro-electromechanical systems (MEMS).
Micro-Thermoforming
Micro-thermoforming is compatible with plastics and works very similarly to regular thermoforming, but on a much smaller scale. Thin plastic sheets are heated and then shaped around male or female molds to create microfluidic films.
Micro-Injection Molding
Micro-injection molding, sometimes referred to as micro-molding, is a miniaturized version of classic injection molding. This manufacturing process is well suited for labs that need to use the same chip design many times (or require a large order of a single design).
CNC Machining
Micromilling, or etching, is a popular way to create microfluidic chips: you start with a blank slab (commonly called a wafer) and etch or dig out channels and grooves. Many desktop computer numerical control (CNC) machines are capable of milling microfluidic and millifluidic chips.
3D Printing
3D printing is essentially the opposite of subtractive technologies like CNC machining or etching. While these involve excavating channels into a preexisting wafer, professional 3D printers build microfluidic chips from raw materials.
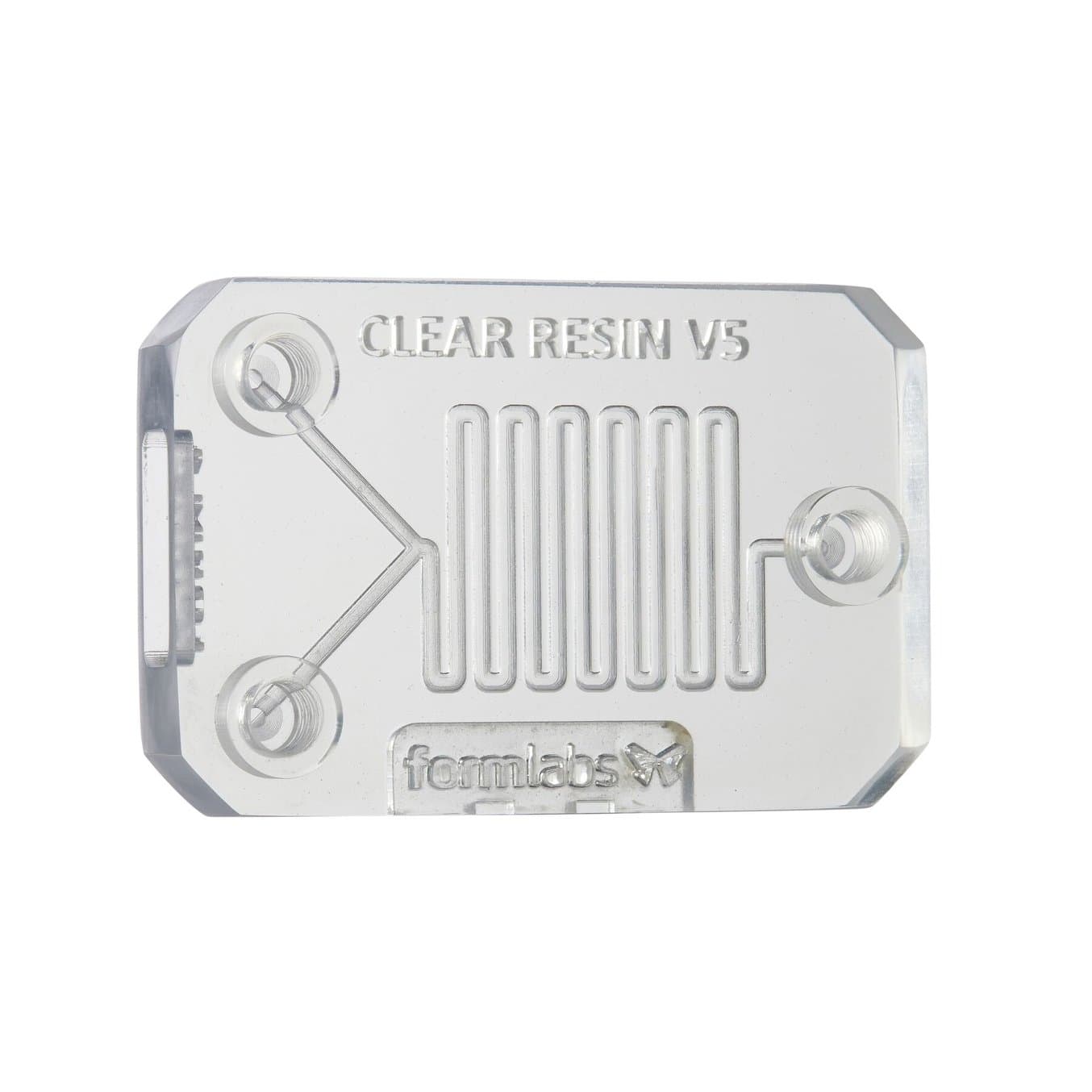
Request a Free Sample Part
See and feel the quality of SLA 3D printing firsthand. We’ll ship a free 3D printed millifluidics sample part to your office.
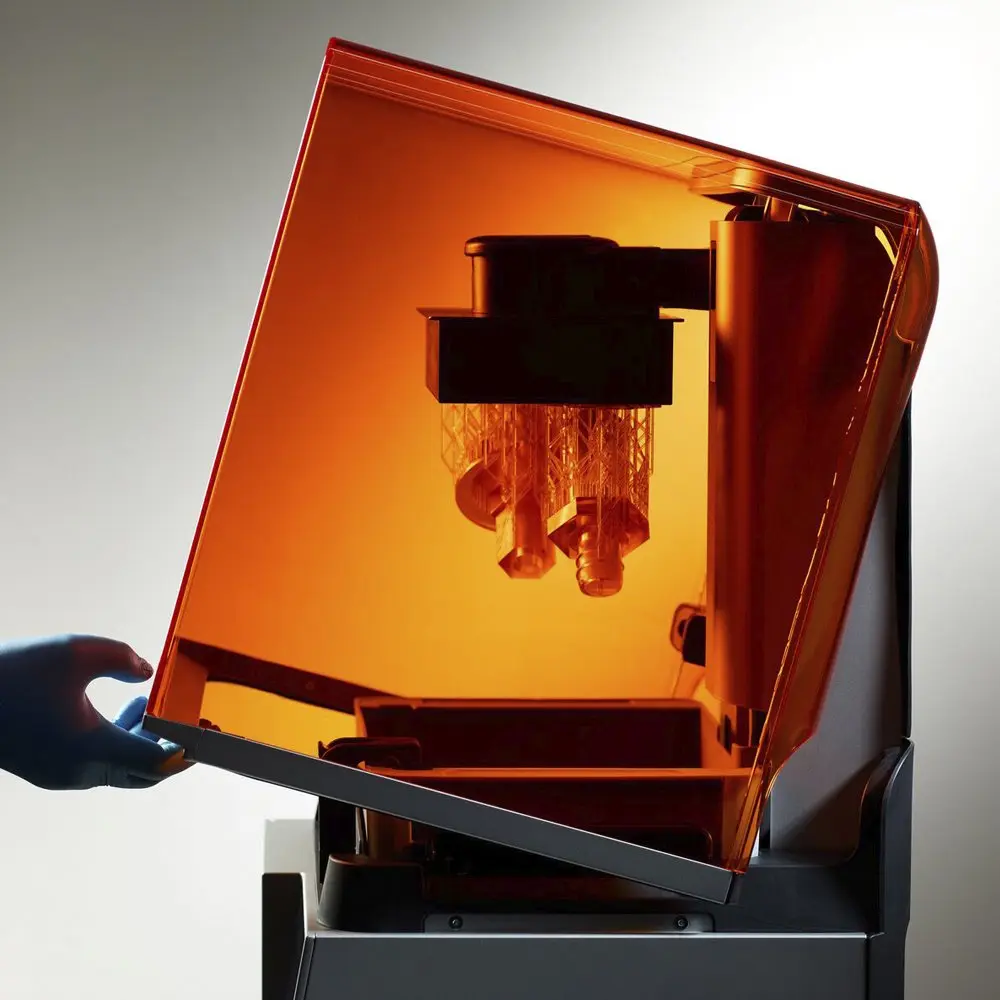
Introduction to 3D Printing With Desktop Stereolithography (SLA)
Looking for a 3D printer to produce high resolution models fast? Download our white paper to learn how SLA printing works and why it's the most popular 3D printing process for creating parts with incredible detail, high dimensional accuracy, and superior surface finish.
Why 3D Print Fluidic Chips In-House
Additive manufacturing (3D printing) provides a number of benefits over traditional chip production methods, including significant cost and time savings due to in-house printing, and the ability to quickly test complex three-dimensional designs.
Cost and Time Savings
The first and most significant is the cost savings associated with in-house 3D printing. Ordering a custom-made millifluidic chip normally incurs an exorbitantly high cost and can take up to two months before having a prototype in-hand. Instead, SLA 3D printers can print any geometry needed right in your lab and have it ready in hours, not months.
Here’s the breakdown for a single large chip 3D printed on Form 4:
Technology | Cost | Lead Time |
---|---|---|
SLA 3D Printing | ~$2 | <2 h including post-processing |
Lithography | $73.75 | 2+ days |
*Cost of materials per part if using Clear Resin V5. Bulk materials pricing is available and can decrease cost per part.
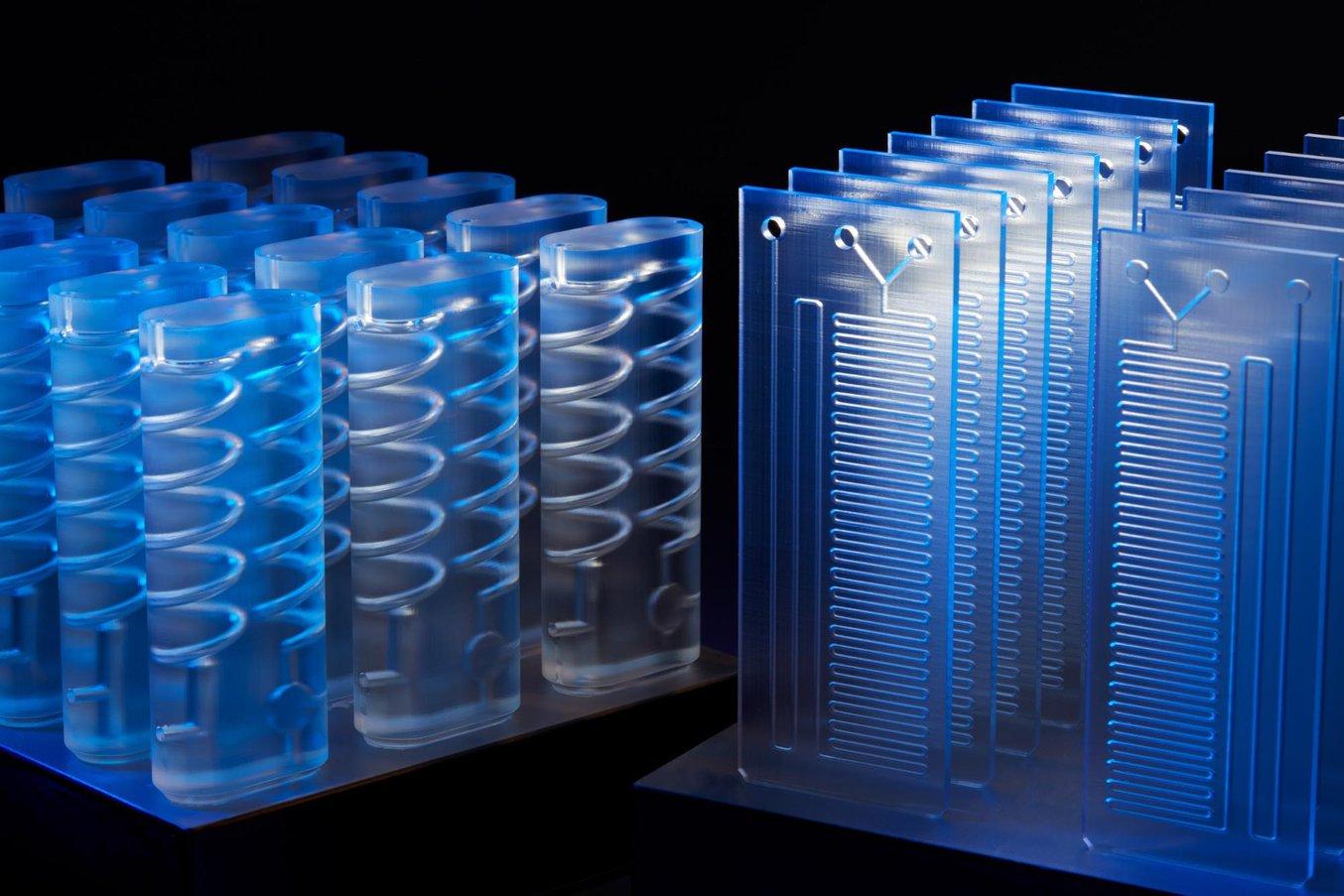
A single large chip prints in under two hours.
3D and Custom Designs
SLA resin printers enable research teams to test fluidic chips quickly, which means they can make adjustments based on real-time feedback.
Complex designs are only limited by what a user can create in CAD, opening up quick testing of microfluidic and millifluidic chips in labs for the first time. In 3D-printed millifluidic chips, channels can take any three-dimensional path. By comparison, etched glass channels are restricted to a two-dimensional plane and a rectangular cross-sectional shape. This can especially be helpful for students looking to understand how different channels mix fluids.
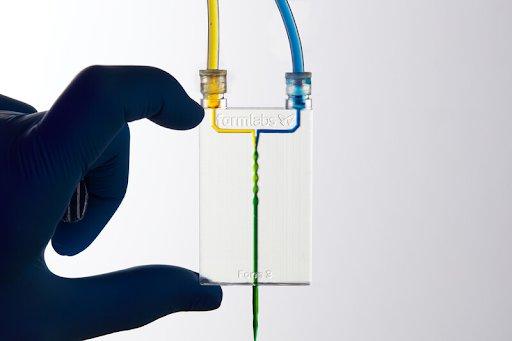
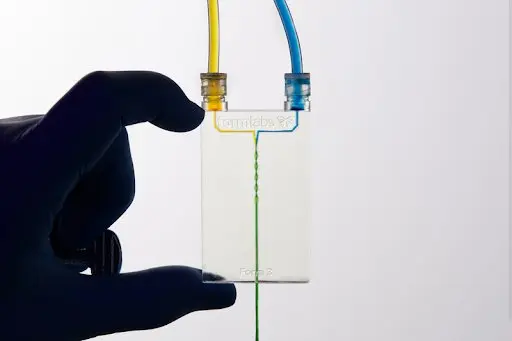
3D channels highlight a unique and powerful feature of 3D printing in-house millifluidic models. Sharp 3D features disrupt laminar flow in narrow channels and allow the designer to control when and how fluids mix.
The Formlabs engineering team wanted to test these 3D features, so they designed, printed, and tested a unique 3D millifluidic geometry containing a twisting channel. The mixers were tested using standard food dye dissolved in tap water. One syringe was filled with yellow, the other blue. Each color was injected into a mixing port printed directly to the chip. Then the mix was projected onto a white surface where the uniformity of the mix could be observed.
Formlabs offers several options for optically clear resins, offering another benefit to 3D printed chips, as different materials may offer better chip design and mixing properties. While Clear Resin (a General Purpose Resin) is great for prototyping, Surgical Guide Resin and High Temp Resin can also provide the required properties for common millifluidics applications.
Surgical Guide Resin is more rigid than Clear Resin. It excels at resolving negative features and is an autoclavable biocompatible material. Surgical Guide Resin can also print with a 50-micron layer height for super-precise channel geometry. This could help push chip and channel designs even smaller, enabling truly microfluidic 3D printed chips.
Shaping the Future With 3D Printing and Microfluidics
One thing is certain: microfluidics and millifluidics will continue to empower new and exciting developments in science.
In-house printing creates new opportunities for microfluidics and millifluidics. Critical custom chip designs, used in engineering applications, advanced medical analysis, and educational institutions, can be designed and printed in-house with affordable, high-resolution SLA 3D printers.
Read our white paper to fully understand the benefits and challenges involved, contact our team to discuss your application, or request a free millifluidics sample part to see the quality firsthand.