Two of the most popular 3D printing technologies on the market are fused deposition modeling (FDM) and stereolithography (SLA). Each has its own benefits and strengths, with differences in print quality, materials, applications, workflow, speed, costs, and more.
Depending on your application, one technology might be better suited for specific parts than the other. But why not combine the two to get the best of both worlds?
In this post, we explore how three users view FDM and SLA as complementary technologies, and look into how they use both to optimize their projects.
Balancing Detail and Build Size for Roller Coaster Models
Matt Schmotzer has been tinkering with 3D printing for almost a decade. He currently creates miniature roller coasters; so far he’s made three full working models, containing tracks and highly detailed train assemblies. Matt leverages both FDM and SLA, playing to the strengths of each technology, and ultimately creating a more functional model as a result. Recently he’s been taking the roller coasters on the road, giving presentations at schools to inspire future engineering students.
Matt’s most ambitious models contain over 700 individual cross beams. Flat geometric beams are used for interior support and mate to a wooden scaffolding using Loctite brand adhesives. Since high detail quality is not a concern, and a large number of prints is required, Matt turns to FDM to quickly print most of the beams. FDM prints also offer an almost unlimited range of color options, meaning Matt has more creative freedom when putting the final assembly together.
The trains themselves offer their own unique challenges. The train models are printed on SLA machines since the small, 1.5x3” parts need to look realistic. For this task, Matt turns to Grey Pro on his Formlabs printer. SLA printers excel at creating final, high-quality end-use parts, and the train models are expected to look as realistic as possible down to the tiny handles on the doors.
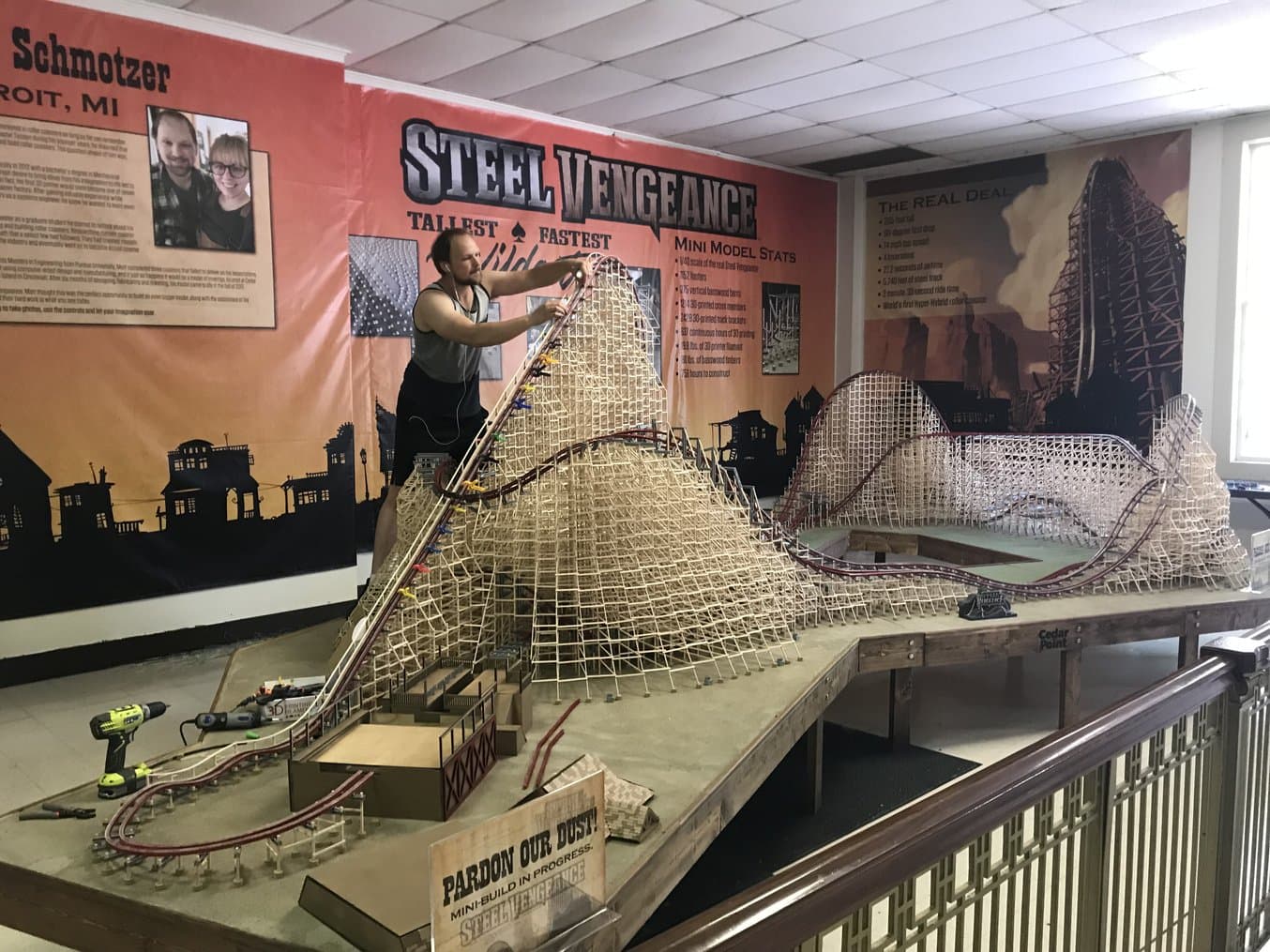
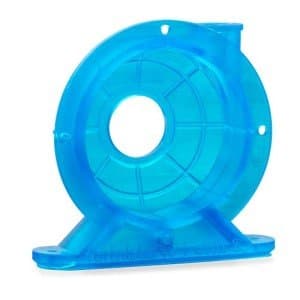
Request a Free Sample Part
See and feel Formlabs quality firsthand. We’ll ship a free 3D printed sample part to your office.
Request a Free Sample PartHelp Clients Achieve Project Goals at a 3D Printing Service Bureau
Christina Perla founded MakeLab, a 3D printing service bureau based in Brooklyn, New York, over two years ago. MakeLab is not simply a print farm, but a consultancy that guides discussions to help clients achieve project goals.
The firm works with both SLA and FDM technologies, steering clients to the printing method which meets their project needs. Right now, half of the company’s business comes from FDM requests, with the other half being SLA. MakeLab offers the full suite of Formlabs resins; in 2018, High Temp Resin was the most popular.
“Because we’re a service bureau, the part we play in our clients’ design process ends with the 3D print. We see SLA as an elevated offering alongside FDM. We have offered Formlabs resin as a material option from the very beginning of Makelab. We always saw the value in it and the value it brings to our clients.”
Christina Perla
While Christina says she tends to favor SLA, FDM still works well for bulk quantities and when large print sizes exceed most SLA printer volumes. Christina also tends to favor FDM printing if the part is intended as a basic internal proof of concept. For investor meetings, client pitches, or final presentations for projects that need approval, Makelab will print using SLA.
Christina finds it useful to pick one brand of 3D printer for each technology, and to invest in that company’s ecosystem. This allows her to master printing on a specific machine, offer the best prints possible, and to develop a relationship with printer brands should she ever need help.
"Keep it as minimal as possible by picking one brand for each [technology], and working within those ecosystems. Make sure whatever companies you buy into have great support, too. With only two support teams, two phone numbers, and two sets of spare parts -- it just streamlines everything."
Christina Perla
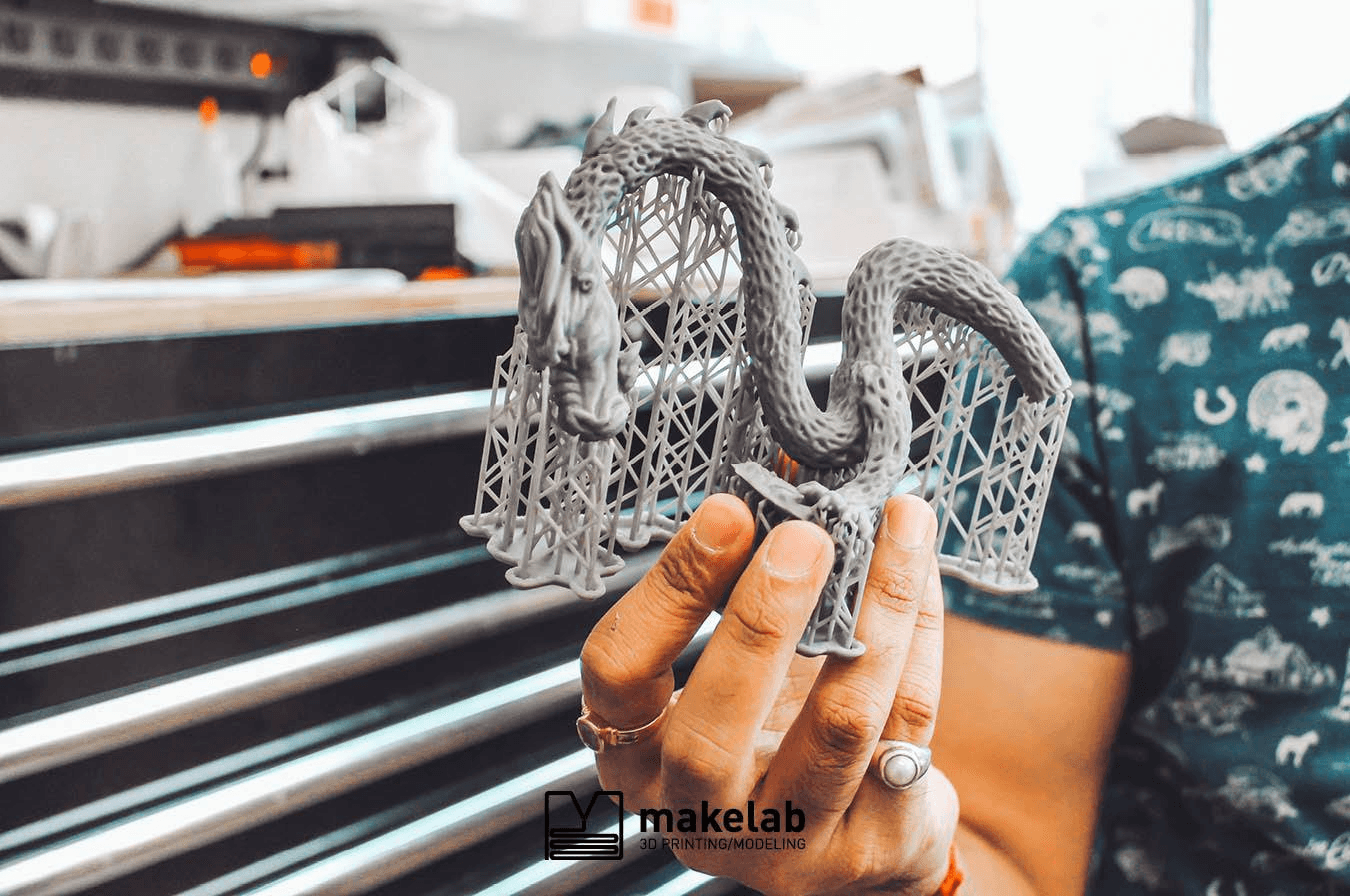
Picking the Right Flexible Materials for the Third Thumb
Dani Clode is the creator of the third thumb project, in collaboration with The Plasticity Lab in the Institute of Cognitive Neuroscience at University College London. The prosthetic thumb is controlled by the users’ foot, greatly expanding what is possible with a human hand. The ultimate goal of the project is to study and improve the usability and control of prosthetic devices.
One unique aspect of the project is that the thumb is composed of both SLA and FDM components. The wrist piece is printed in Formlabs Grey Resin, which provides a strong yet light and polished material that works well with the contours of the human body. Dani tried printing this part on a Selective Laser Sintering (SLS) machine, but switched back to SLA for Grey Resin. Dani has become comfortable with Grey Resin, a material she’s been using since she first started prototyping with 3D printing.
The thumb itself is FDM printed, with the fingertips in Formlabs Elastic Resin. Dani delicately combines multiple prints for both the thumb and wrist pieces, selecting the best materials for each. By experimenting with both technologies, Dani was able to find ways for FDM and SLA to complement each other, enabling a complex project that wouldn’t be possible otherwise.
“The thumb itself is FDM printed flexible thermoplastic polyurethane, with a low print fill. FDM flex is hard to work with, but it is the best option for the thumb at the moment. Is also makes it light and strong. The fingertips are Formlabs elastic, and that’s because I need a high-resolution flexible material that can be printed thin, hold its shape and grip nicely. I also love that it can be secured easily to my other materials, unlike silicone. SLA is the only printing method that can handle my intricate internal piping to control the thumb.”
Dani Clode
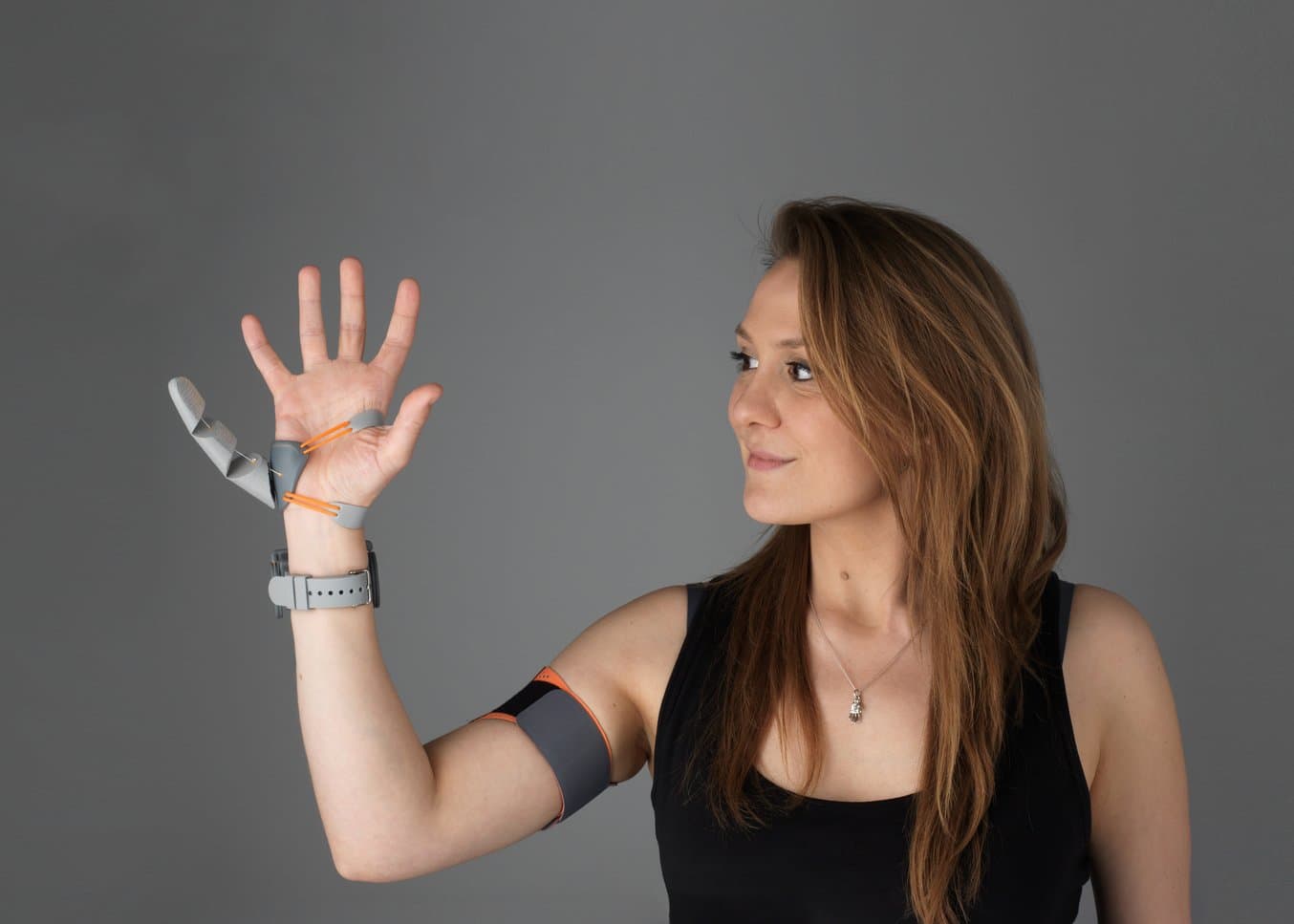
Happen to have interesting projects enabled by both technologies, let us know on social media by tagging @Formlabs in your posts!