Guitars to Bowls: Automation and End of Arm Tooling (EOAT) at Pacific Rim Tonewoods
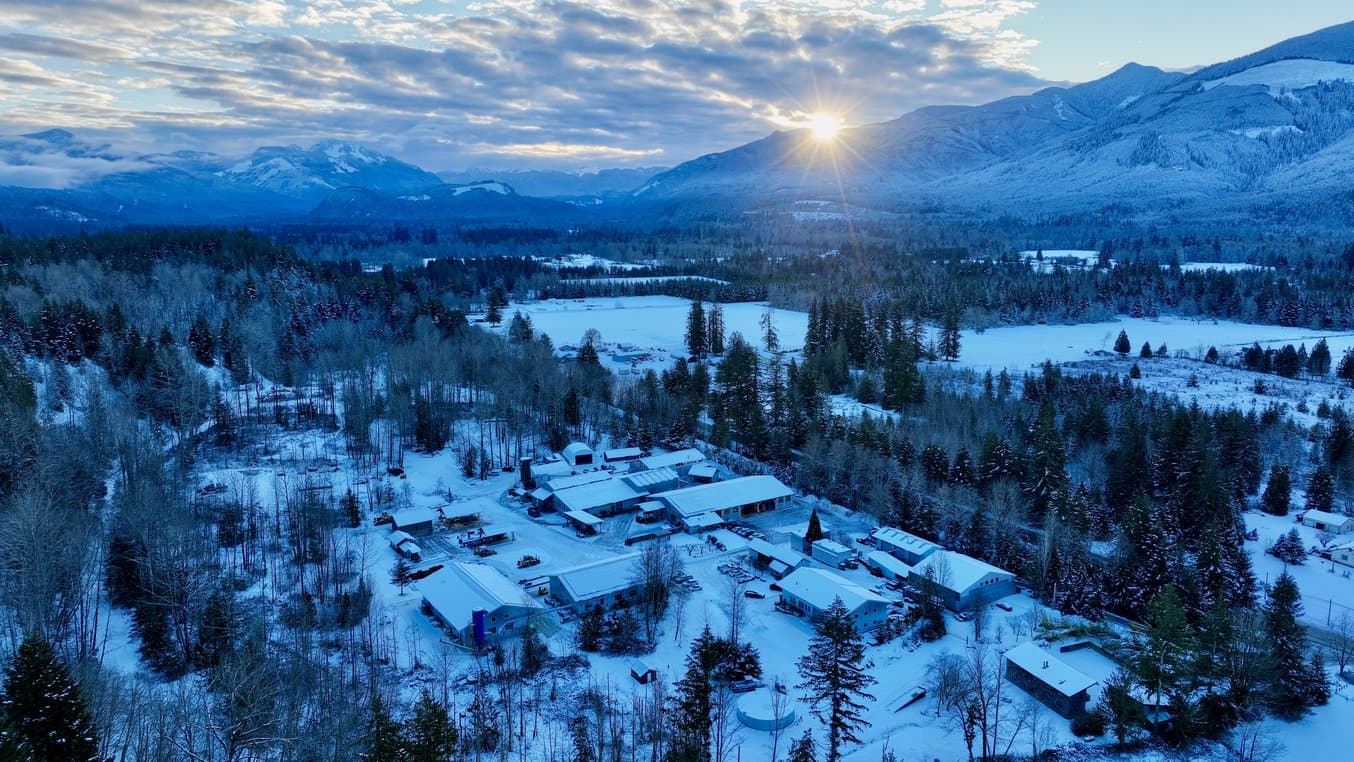
At a sawmill nestled in the North Cascades mountain range, robots are at work. Pacific Rim Tonewoods (PRT) supplies guitar makers large and small like Martin, Taylor, Gibson and Fender, as well as individual luthiers — craftspeople who build and repair string instruments — with ultra-high-quality wood milled and shaped from carefully selected types of trees.
About a decade ago, PRT overhauled their operations, focusing on minimizing waste and streamlining their milling processes. The changes they made improved their yield by over 12%. After these process improvements were made PRT set their signs on automation to open up new opportunities elsewhere at the company.
We spoke to engineer Jake Wells about how selective laser sintering (SLS) 3D printing with the Formlabs Fuse Series has made their robotic systems more affordable, efficient, and long-lasting. SLS 3D printed end-of-arm tooling (EOAT) and manufacturing aids have reduced lead time and optimized their automated workflows, helping them bring robotics integration in-house.
“We’re continuously optimizing processes to make better products, with tighter tolerances and less material waste. It’s an ongoing pursuit of improvement and being more efficient.”
Jake Wells, Engineer, Pacific Rim Tonewoods
Introducing Robotics for Sawmill Operations
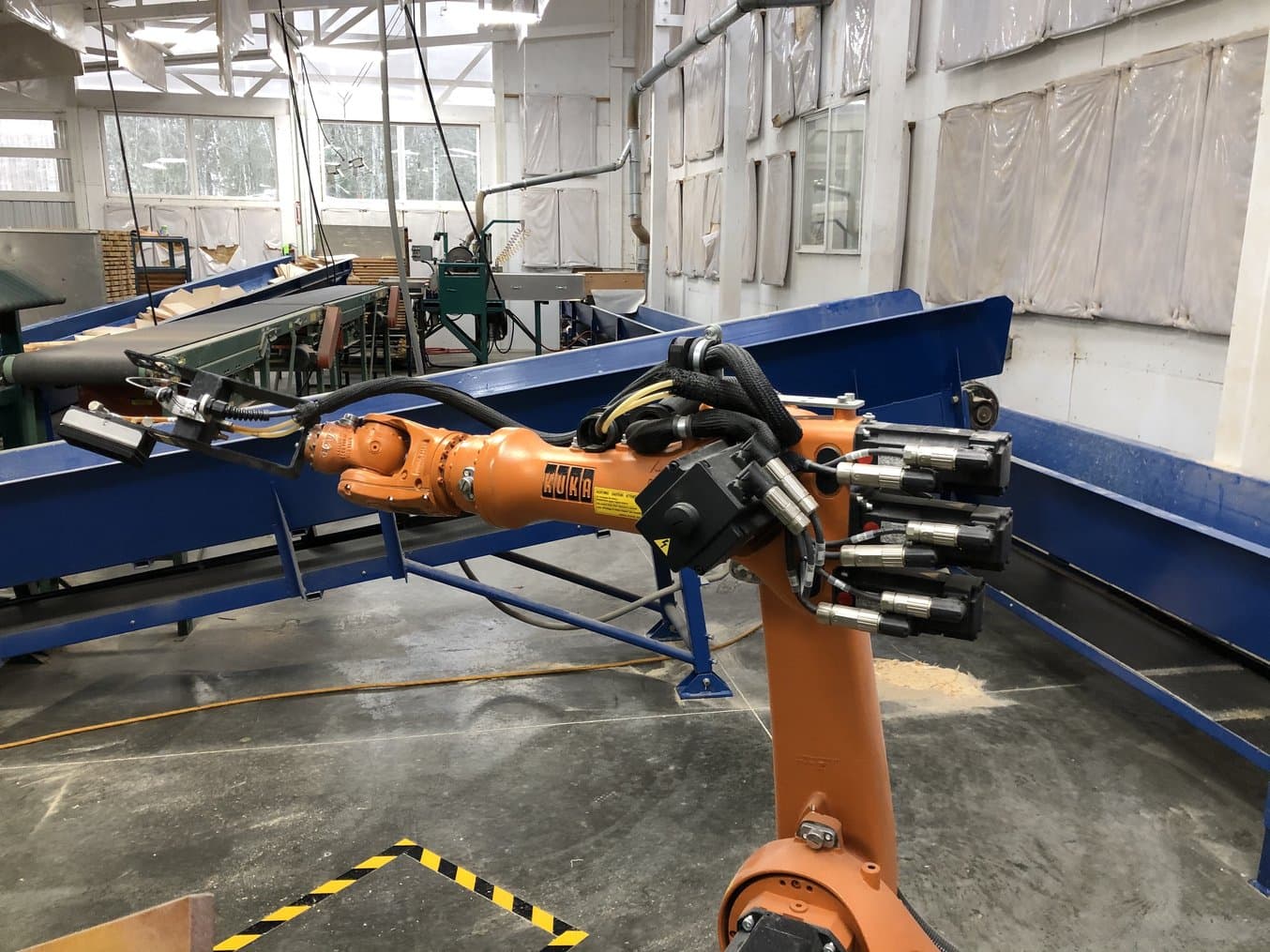
PRT's first robot, a Kuka KR-6, was powerful, but a bit too large for the intended workflow. Working with an outside integrator created a mismatch between the robot and the task, which was the first thing addressed by the in-house team led by Wells.
Robotics and automation are cornerstones of the long-heralded digital manufacturing future, and in many industries, they’ve made good on their promise to make operations more efficient. The most successful businesses, like PRT, have integrated automation in ways that take over the ‘three D’s,’ or the ‘dirty, dull, and dangerous’ tasks that are too slow, difficult, or hazardous for humans to do consistently.
But as PRT started bringing in their first robots, the integration — the hardware and software components that program and outfit a robot for a specific application — left something to be desired. Their first robot was a $60,000 KUKA KR-6 that had to palletize pieces of specialized and super high-quality wood. The system freed up a lot of time for employees to work on higher-value, more complex tasks, but working with the outside integrator created a mismatch between robot and task, and Wells knew there was a more efficient workflow possible.
“The main issue we had was the crude integration. The outside integrators weren't used to wood handling and chose this robot which was larger than we needed. When we decided to bring these decisions in-house, we reevaluated that system and it became clear that a better, more efficient approach was out there. Our approach would be to holistically match a robot to its tooling,” says Wells.
3D Printing End-Effectors for Optimization
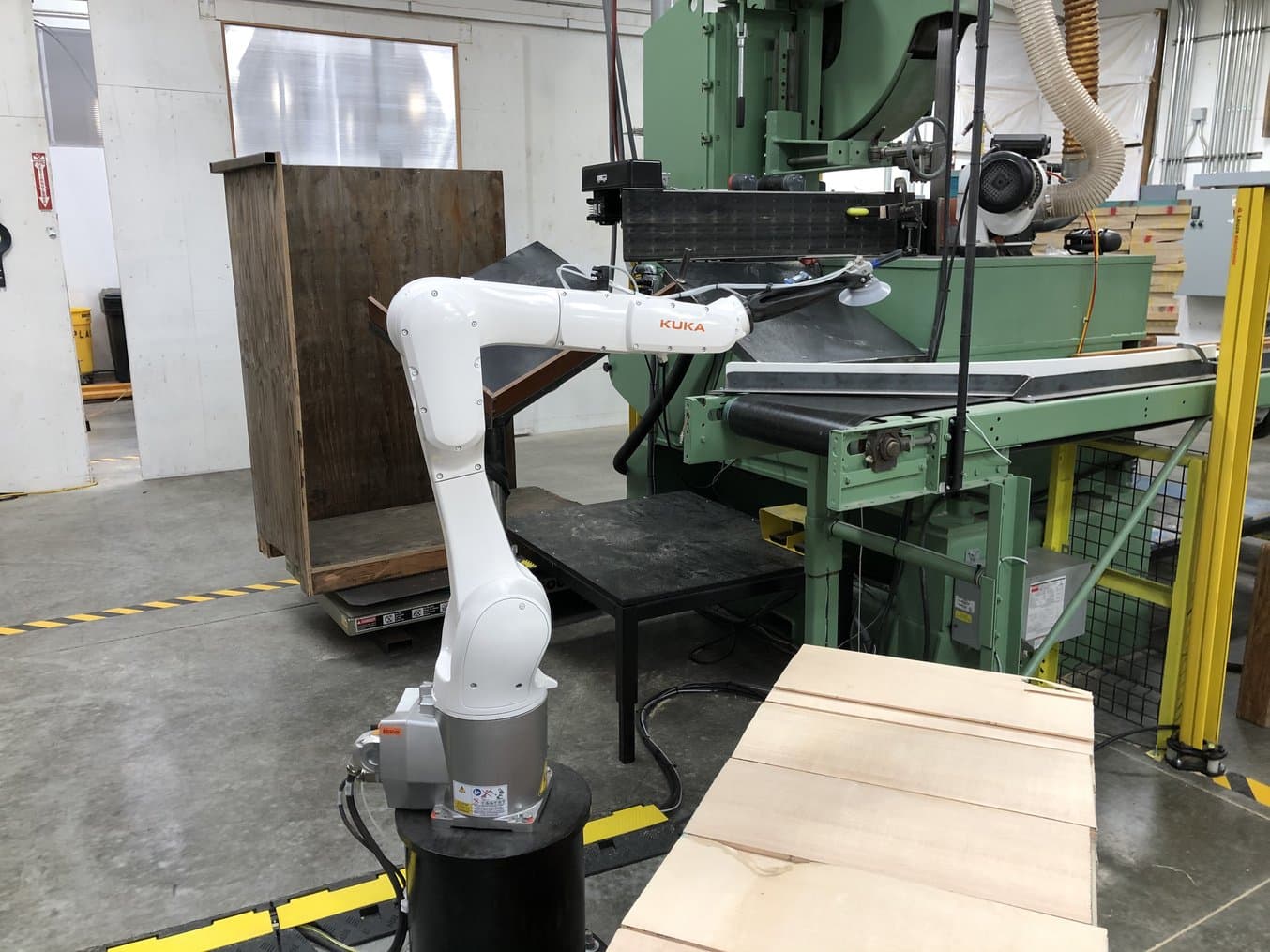
Once they brought the robotics integration in-house and chose a lighter, more inexpensive robot, the PRT team realized they could design customized EOAT to further optimize their process.
Wells started by printing designs of end-effectors on a fused deposition modeling (FDM) 3D printer he had at home. Right away, the value of 3D printing became apparent — they were able to design, fit, test, and iterate multiple times a week, trying to find the best balance of strength and weight. “I was the only engineer for a while, and it made so much more sense to just print something, throw it on the robot, and see how it worked than to spend all that upfront time engineering something for machining,” says Wells.
PRT has an in-house machine shop with a powerful, 4-axis CNC machine, which can handle the complex parts required for customized end-of-arm-tooling. Committing to machining something, however, requires that the design be completely finalized, otherwise, it’s a waste of material and hours of the skilled operator’s time.
The FDM 3D printed parts would work for test fit pieces, and even as end-use in some cases, but they were unreliable and could break too easily when force was applied along their layer lines. “It was hard to tell if the FDM parts were quality until they were in service. Parts that looked great could fail at 20,000 cycles for no apparent reason, others could go 120,000 cycles before failure, and even then it could just be due to a collision," says Wells.
They started sending parts out to be 3D printed by a service bureau and liked the strength, weight, and durability of the MJF nylon 12 parts they received. However, outsourcing cost them too much time. As they looked to start new projects, they couldn’t wait weeks to get a part in for tests.
Why Use SLS 3D Printing for End-of-Arm-Tooling?
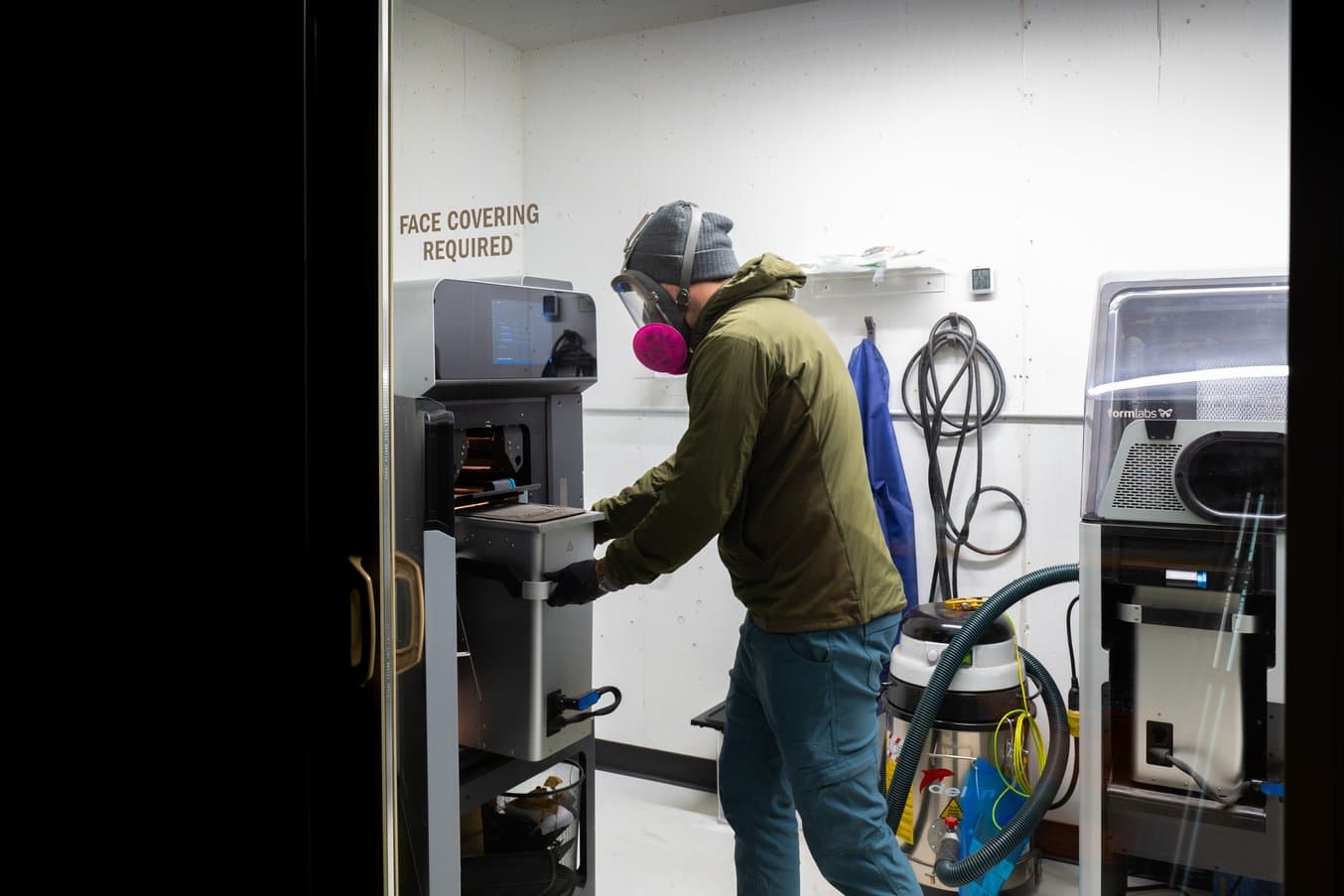
Wells brought SLS in-house to reduce lead times and enable customized geometries for strong, functional end-of-arm-tooling. The accessible price point and small footprint of the Fuse Series ecosystem means that Wells and his colleagues can print every day if necessary and easily teach new colleagues to use the technology as the company expands.
PRT needed an in-house solution that could deliver end-use quality parts strong enough for hundreds of thousands of reps as EOAT components. They liked the nylon parts they were outsourcing to MJF printers, and also needed a build chamber with the right size for the end effectors. The Fuse 1 was the right fit on all accounts. “We were getting into parts that were complex enough to be a real bear to machine, and materials like aluminum would be overkill. We needed to fill the void for complex but durable parts and bring it in-house,” says Wells.
The Fuse Series and Nylon 12 Powder offer the ability to create end-use quality parts in a familiar, industrial-grade material. The self-supporting nature of SLS technology made it possible to 3D print the generatively designed end-effectors with their organic curves and hollowed-out cores, without adding extra time post-processing and removing supports.
“I’d never worked with SLS before, but the ability to design without worrying about geometric constraints has been huge. We’ve got a system that has more universal strength and is easier to work with than previous solutions. It opened up possibilities for us to make things much more quickly and push our designs forward. It’s been a huge positive.”
Jake Wells, Engineer, Pacific Rim Tonewoods
Cable Management and Sensor Mounts
Though end-effectors get the most buzz — and perhaps rightly so — there are so many parts of automated robotic systems that 3D printing can help manage. On each of the robots, dozens of complicated cables deliver energy and signals to the machine’s various components. During daily operations, these cables can get caught, clamped, broken, frayed, or just be in the way, during maintenance an incorrectly routed cable can wreak havoc on fragile wires and connectors. Wells started printing custom clamps to hold the cables onto the machine and in certain groupings, making the entire system more efficient and less prone to damage.
“Cable management is one of the things that’s actually been the most important. Cables are customized to the robot arms themselves, and travel the length of the machine, and there are so many ways to get tangled and twisted. Our 3D printed clips and clamps keep those systems reliable and efficient. It’s part of our goal to achieve and maintain a higher standard of optimization.”
Jake Wells, Engineer, Pacific Rim Tonewoods
The customized clamps can be designed to let sawdust move through them easily rather than trapping it to be cleaned out later. They hold the cables in certain positions to make them easier to service or replace, and they improve the overall cleanliness and efficiency of the operation. The Fuse Series made it possible to design and iterate a small, simple part that has an outsize impact, and to do it all without hours of engineering design work for CNC or weeks of lead time.
3D printing customized components also made the operation safer. Every robotic system is monitored by several safety sensors that monitor the task and create a feedback loop for the safety system. These sensors improve safety and alert any operators to issues or potential risks. Though the sensors are mass-produced, they’re being used in unique settings, so every integrator needs to find a custom way of mounting them so that they’re effective.
“Our whole robot is being designed in CAD and tested in simulation software. We’re able to place the sensors into the model and figure out the optimal angle and placement, then print out the mount perfectly so every sensor is exactly where it should be. This is extremely important for safety sensors, where an incorrectly placed sensor could pose a safety risk” says Wells.
The mounts serve another purpose: future-proofing the system. Digitally integrating the sensor mounts into the CAD layout of the entire system makes it easy for anyone to 3D print replacement mounts at any point. “Anybody can replace that sensor down the road and it will be perfectly pointed at what they want it to be already. We did the same approach with safety radar systems. No safety problems and just better results,” says Wells.
When to Machine and When to SLS 3D Print
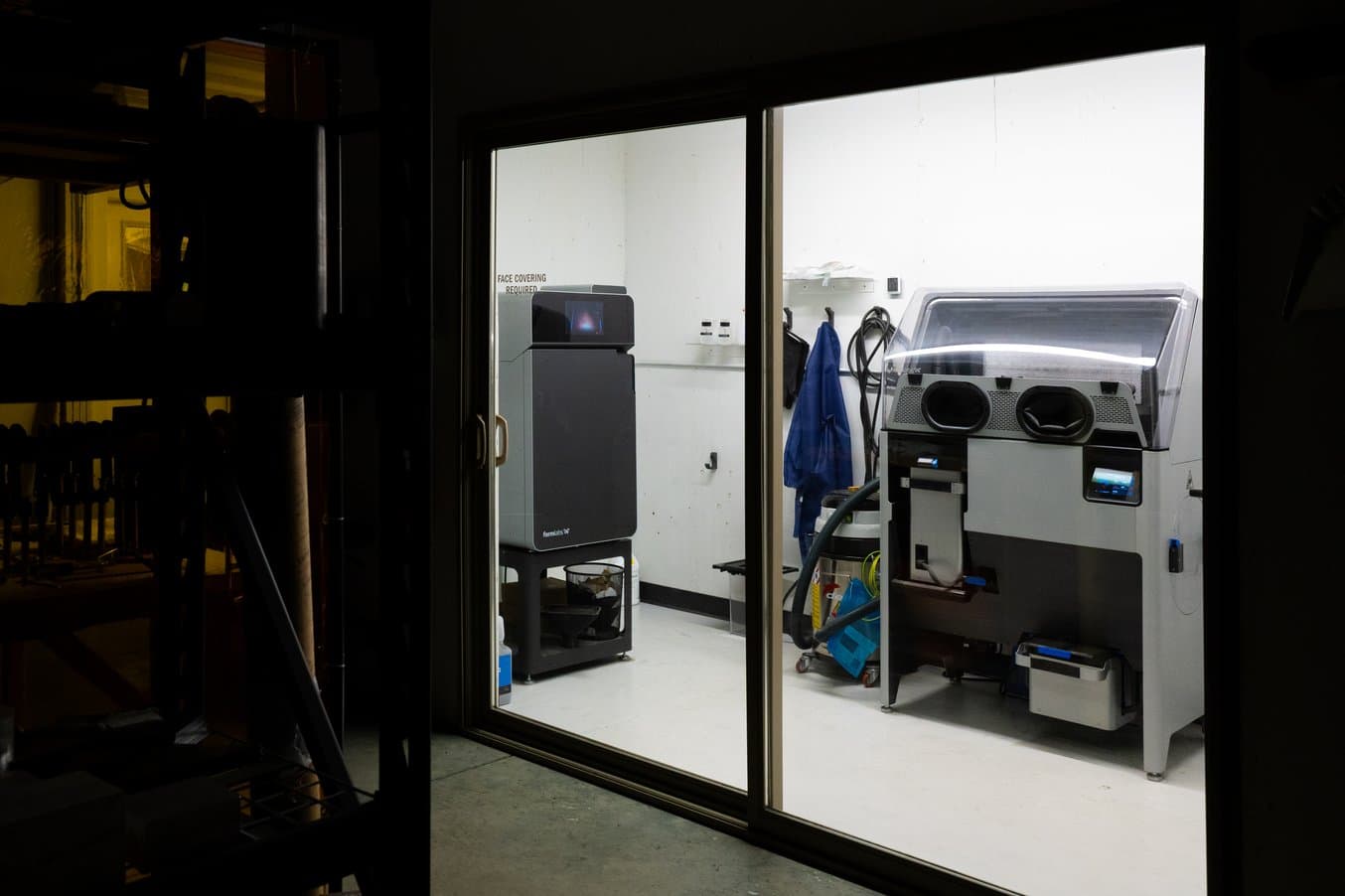
The Fuse 1 SLS printer and Fuse Sift were added to the machine shop, which already had a 4-axis CNC machine as well as a host of other fabrication tools and an FDM 3D printer.
PRT has a fully-equipped machine shop with a 4-axis CNC machine, and Wells has plenty of experience as a skilled machinist and designer for complex, machined parts. The two technologies are made to work in concert with each other, and both machining and 3D printing offer different benefits.
The biggest difference is the upfront buy-in. Wells could spend days or even weeks getting the design for a machined part perfect, so the setup and material usage are as efficient as possible. For 3D printing, especially with the intuitive workflow of the Fuse Series, everything goes a bit quicker. “In our shop we’re optimized highly for machining, but at the same time, there’s more that goes into design for CNC manufacturing, a lot of prerequisite knowledge. Whereas with 3D printing, there’s a lot of stuff I can design in a couple of hours and see if it works — which could be a few weeks if you were to machine it,” says Wells. The ease of use of the Fuse Series has helped Wells work with everyone on the team to get parts printed and put into use.
“Anybody can use it. I can still have super critical parts but anyone who knows how to drag into PreForm can still get that part, and they’ll be functional and strong, too.”
Jake Wells, Engineer, Pacific Rim Tonewoods
Design Considerations for 3D Printing EOAT

The SLS 3D printed end-of-arm-tool that Wells designed combines strength, functionality, geometric complexity, and the rigidity necessary to palletize wood.
For end effectors, parts need to be strong enough to pick up and place the pieces of wood going on the pallet, but light enough to not overload the robotic arm. Impact-resistance and dimensional accuracy are also primary concerns. “3D printing allows you to consolidate clunky metal assemblies so you have one part, this simplifies assemblies so it can be maintained in the future,” says Wells.
But the advantages of 3D printing EOAT aren’t there if you operate like a normal machinist shop, used to fabricating clunky metal tools. The design process isn’t one-to-one, Wells told us. To fully take advantage of 3D printing, there are workflow changes and new lanes of creativity.
“You won’t see a big benefit if you just make the same big blocks of tooling. But if you pair 3D printing with generative design, using known materials, you can clean up your workflow a lot and pretty quickly get to a very optimized solution for your structural parts.”
Jake Wells, Engineer, Pacific Rim Tonewoods
Opening Up New Revenue Streams

As Wells builds out new ways of designing tooling and automating their workflow, PRT is looking to expand into new product categories.
3D printing has made PRT's robotics integrations smoother, simpler, and more streamlined. “It’s helped hugely when integrating automation. If you have a specific problem with cable management, or a certain pain point with a robot, you can likely use 3D printing to help fix it,” says Wells.
The positive effects of in-house automation and machine design have opened up more opportunities for PRT. “We have set our sights on the production of high-quality wooden bowls at an affordable price. We will need purpose-built solutions to make this happen, adding 3D printing to our toolbox of options helps us make our systems further optimized for their role,” says Wells.
Similarly, Wells’ success with SLS 3D printed parts is leading him to consider EOAT and automation components as yet another revenue stream. “We have parts that we’re using in production that we may sell to other people in the automation world. We didn’t buy the Fuse with the intention of printing 200 end effectors, but it’s a tool in the toolbox. If you have people who understand the tool, it can be really powerful,” says Wells.
To learn more about the Fuse Series, visit our page. To see the strength of Nylon 12 Powder for yourself, request a free 3D printed sample part.