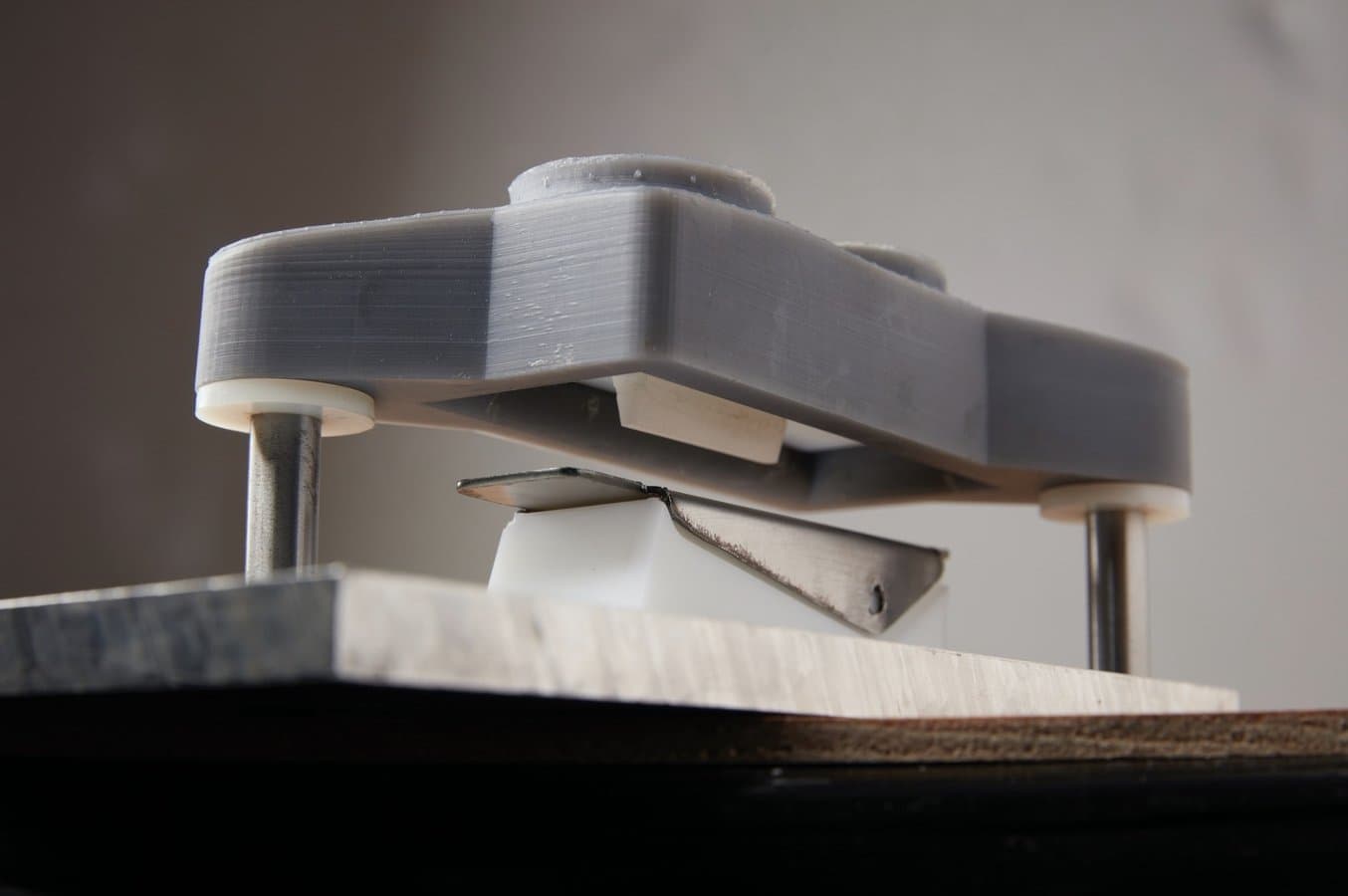
Metal manufacturing is essential for all areas of the economy. Because of their strength, stiffness, and long-term durability, metal components are used in applications from appliances to construction parts and car body panels. Traditional metal manufacturing techniques include forming, casting, molding, joining, and machining.
Sheet metal forming involves various processes where force is applied to a piece of sheet metal to plastically deform the material into the desired shape, modifying its geometry rather than removing any material. Sheet metals can be bent or stretched into a variety of complex shapes, permitting the creation of complex structures with great strength and a minimum amount of material.
Sheet metal forming is the most cost-effective forming procedure today for manufacturing parts in large quantities. It can be highly automated in factories or, at the other end of the spectrum, manually operated in metal workshops for small series parts. It is a versatile, consistent, and high-quality procedure to create accurate metal parts with limited material waste. From metal cans to protective housing for hardware, parts created by sheet metal forming are found everywhere in our daily lives.
In this article, learn the basics of sheet metals, the various sheet metal forming processes, and how to reduce the cost of sheet metal forming with rapid tooling and 3D printed dies. For a detailed overview and the step-by-step method, watch our webinar or download our white paper.
Sheet Metal Basics
Sheet metal refers to thin, flat metal pieces that are formed by industrial processes. These can be extremely thin sheets, considered foil or leaf, to up to 6 mm (0.25 in) sheets. Pieces thicker than 6 mm are considered plate steel or "structural steel.” Sheet metal thickness is normally specified in millimeters around the world, while the US uses a non-linear measure known as the gauge. The larger the gauge number, the thinner the metal sheet.
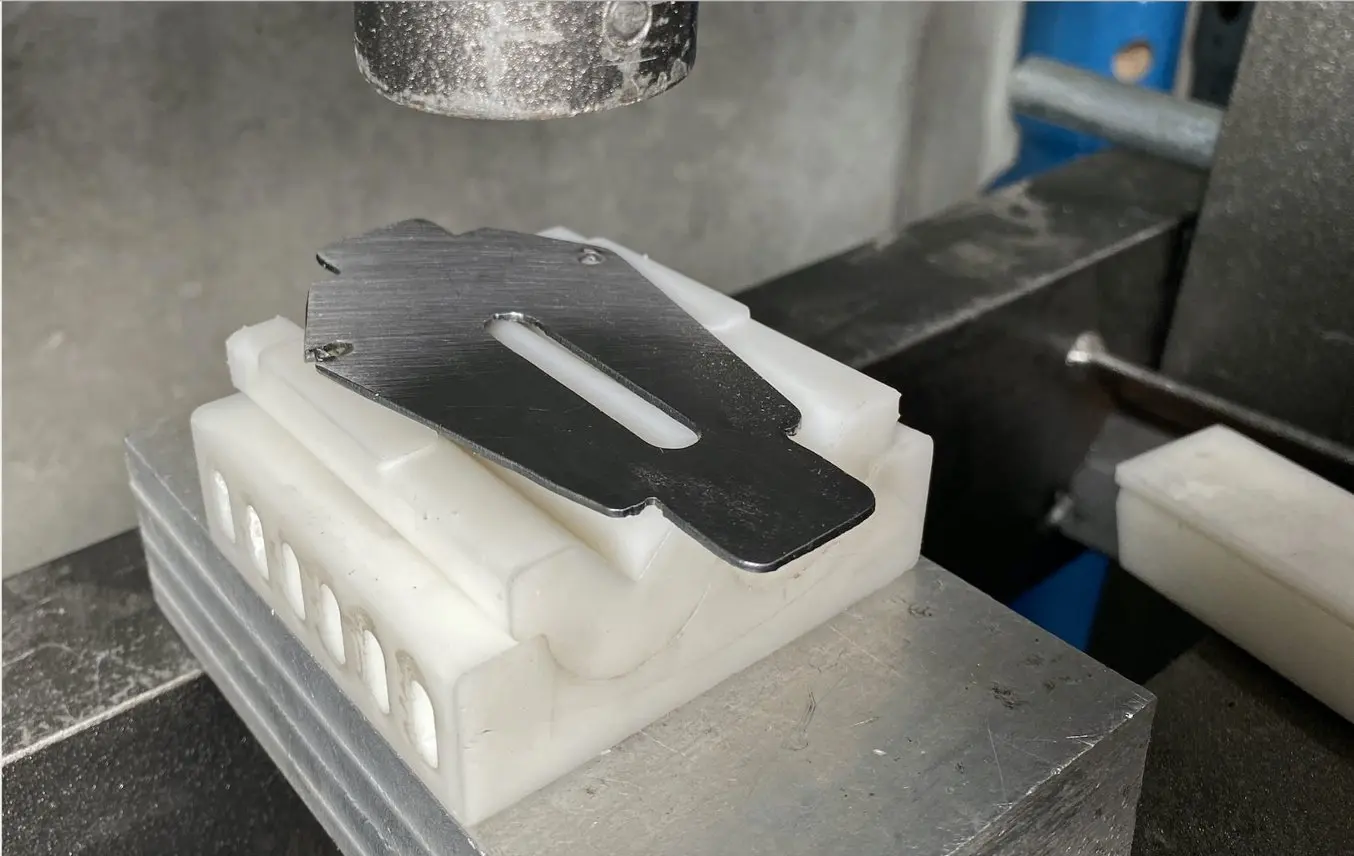
A sheet metal blank for forming a blade guard for an electric saw.
Sheet metal is widely used in the manufacturing of cars, aircraft, trains, hardware enclosures, office tools, furniture, house appliances, computers, machine components, beverage cans, and in construction (ducts, gutters, etc.).
Plate metal is generally used in applications where durability is more important than weight, for example in larger structural parts of ships, pressure vessels, and turbines.
Many different metals can be processed into sheet metal, including aluminum, steel, brass, tin, copper, nickel, titanium, and for decorative purposes, also gold, silver, and platinum.
Sheet metal work stock is normally rolled and comes in coils that can be cut and bent into a variety of shapes.
How Does Sheet Metal Forming Work?
Sheet metal forming includes treatments such as bending, spinning, drawing, or stretching implemented by dies or punching tools. Forming is mostly performed on a press and parts are formed between two dies.
The sheet metal forming process is straightforward:
-
A sheet of metal is cut out from a stock metal to create individual blanks.
-
The blank is placed in the forming machine in between two tools.
-
Subjected to the high forces of the machine, the upper die (also known as the punch) pushes the sheet metal around the matching lower tool and bends it in the desired shape.
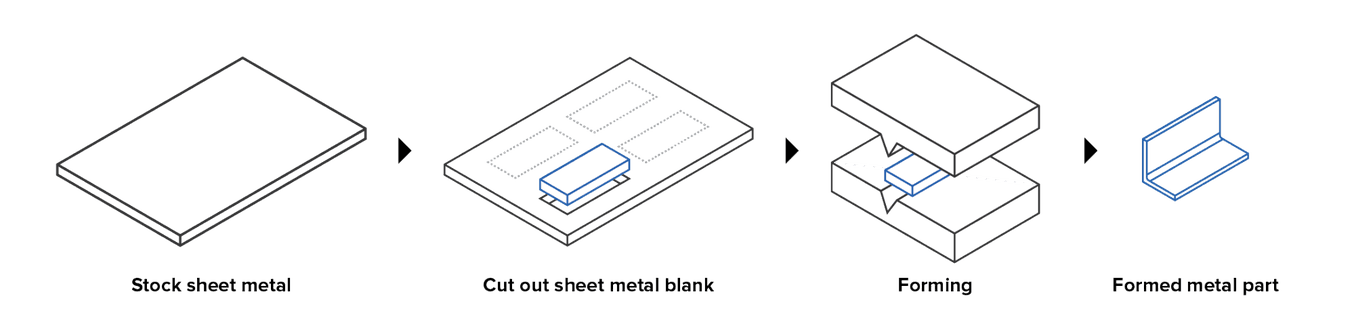
Process workflow for sheet metal forming.
As a downside, sheet metal forming is an equipment-intensive operation. The procedure requires machinery and specialized tools that are part-dependent. As shown above, the tool—also referred to as the form or die—is the part of the forming machine acting to bend the sheet.
Typically, manufacturers produce their forming tools out of metal by CNC machining in house or outsourcing to service providers. This upfront tooling is expensive and generates significant lead times.
Driven by innovation, industries using metal components need more intricate parts with increased agility in fabrication means. Reconsidering tooling techniques can be a powerful lever for this.
3D Printed Tools for Prototyping and Low Volume Sheet Metal Forming
Although large size parts such as car body panels are associated with heavy tooling, most metal workshops also produce all kinds of small units requiring lower bending forces. Replacing those metal tools with plastic parts printed in house for prototyping and low volume production can shorten development times and drive down production costs.
In-house 3D printing enables engineers to prototype metal parts and iterate tool designs in a matter of hours, achieving complex geometries while reducing reliance on outsourced providers. Professional desktop printers are affordable, easy to implement, and can be quickly scaled with the demand.
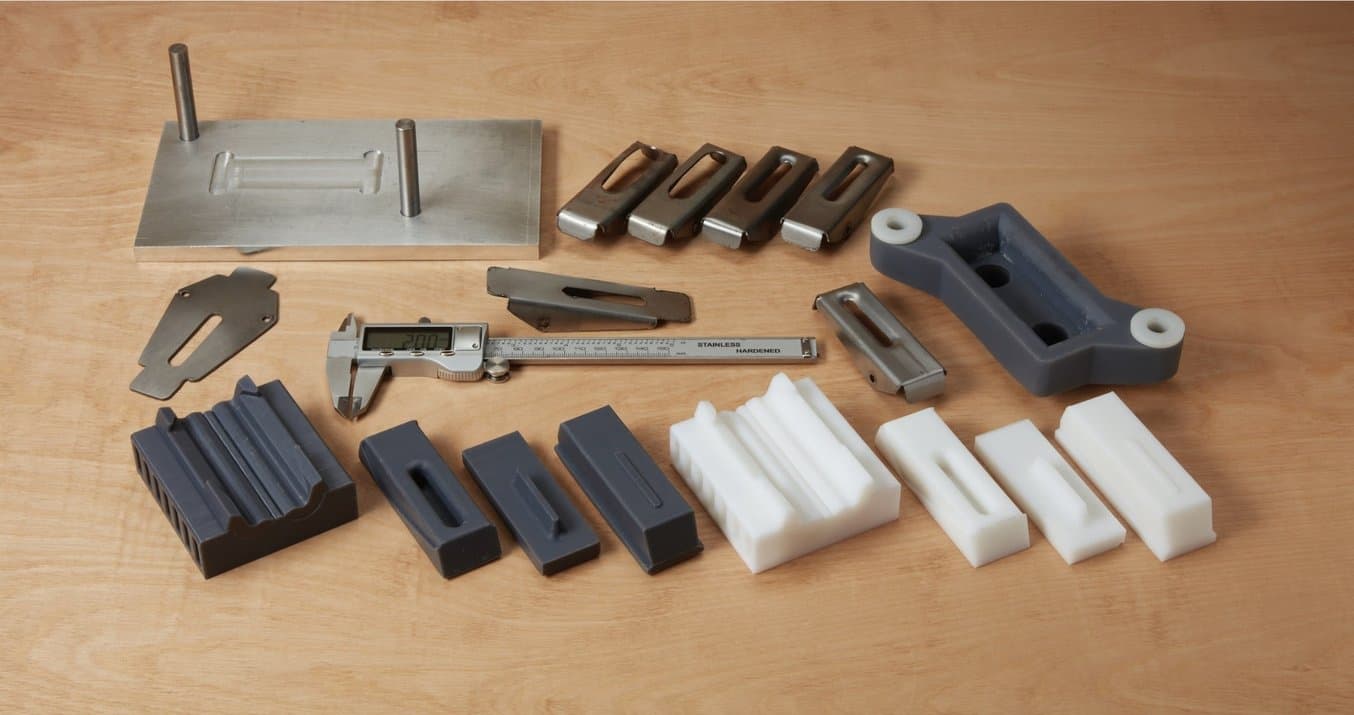
Different iterations of upper and lower dies manufactured with 3D printing for forming a replacement blade guard.
Manufacturers are already using stereolithography (SLA) polymer resins to substitute metal jigs, fixtures, and replacement parts in factories. In processes such as injection molding or thermoforming, using test molds in plastic is an effective practice to validate designs and solve DFM challenges before committing to expensive metal molds. Savings in material costs from metal to plastic are significant.
Watch the video to see how Shane Wighton from the Formlabs engineering team formed a sheet metal part using 3D printed tools for concept validation.
SLA 3D printing technology presents some interesting properties for sheet metal forming. Characterized by high precision and a smooth surface finish, SLA printers can fabricate tools with excellent registration features for better repeatability. Thanks to a broad material library with various mechanical properties, choosing a resin tailored to the specific use case can optimize the result of the forming. SLA resins are isotropic and fairly stable under load compared to other 3D printing materials. Plastic tooling can also eliminate a polishing step, as plastic dies do not mark the sheet as metal.
The mechanism is similar to the general sheet metal forming workflow. The difference lies in the design and print of the two-part tool made of upper and lower dies. The blank sheet is then placed between both plastic dies, and pressed with a hydraulic press or other forming equipment.

Process workflow for sheet metal forming with 3D printed dies.
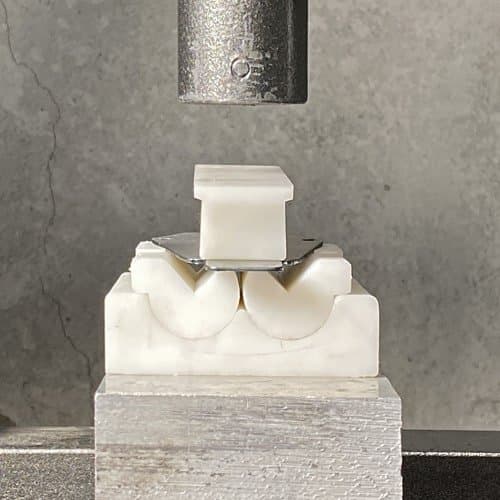
How to do Rapid Tooling for Sheet Metal Forming with 3D Printed Dies
This research work tests and demonstrates the viability of SLA 3D printed dies to form sheet metal parts.
Cost and Lead Time Comparison For Rapid Tooling for Sheet Metal Forming
3D printing a tool for sheet metal forming in house can give flexibility to designers and engineers by reducing the lead time from weeks to a day.
For large volume production, prototyping the tool in plastic allows verifying the design before committing to an expensive metal tool. For short-run production, printed dies would save hundreds of dollars compared to outsourcing the part.
Here’s a cost and lead time comparison for the dies required for the metallic blade guard in our white paper:
Process | Equipment | Lead Time | Material Cost for 1 Final Part | Material Cost for 50 Final Parts |
---|---|---|---|---|
In-house 3D printed tool | Form 3, pressing machine, metal cutting equipment | 10-24 hours (tool print time and post-processing) | $40 ($30 die + $10 sheet metal stock) | $60 ($30 die + $30 sheet metal stock) |
Outsourced 3D printed tool | Pressing machine, metal cutting equipment | 6 business days | $160 ($150 die + $10 sheet metal stock) | $180 ($150 die + $30 sheet metal stock) |
Outsourced metal tool | Pressing machine, metal cutting equipment | 25 business days | $460 ($450 die + $10 sheet metal stock) | $480 ($450 die + $30 sheet metal stock) |
Outsourced metal part | None - fully outsourced | 15 business days | $230 | $700 |
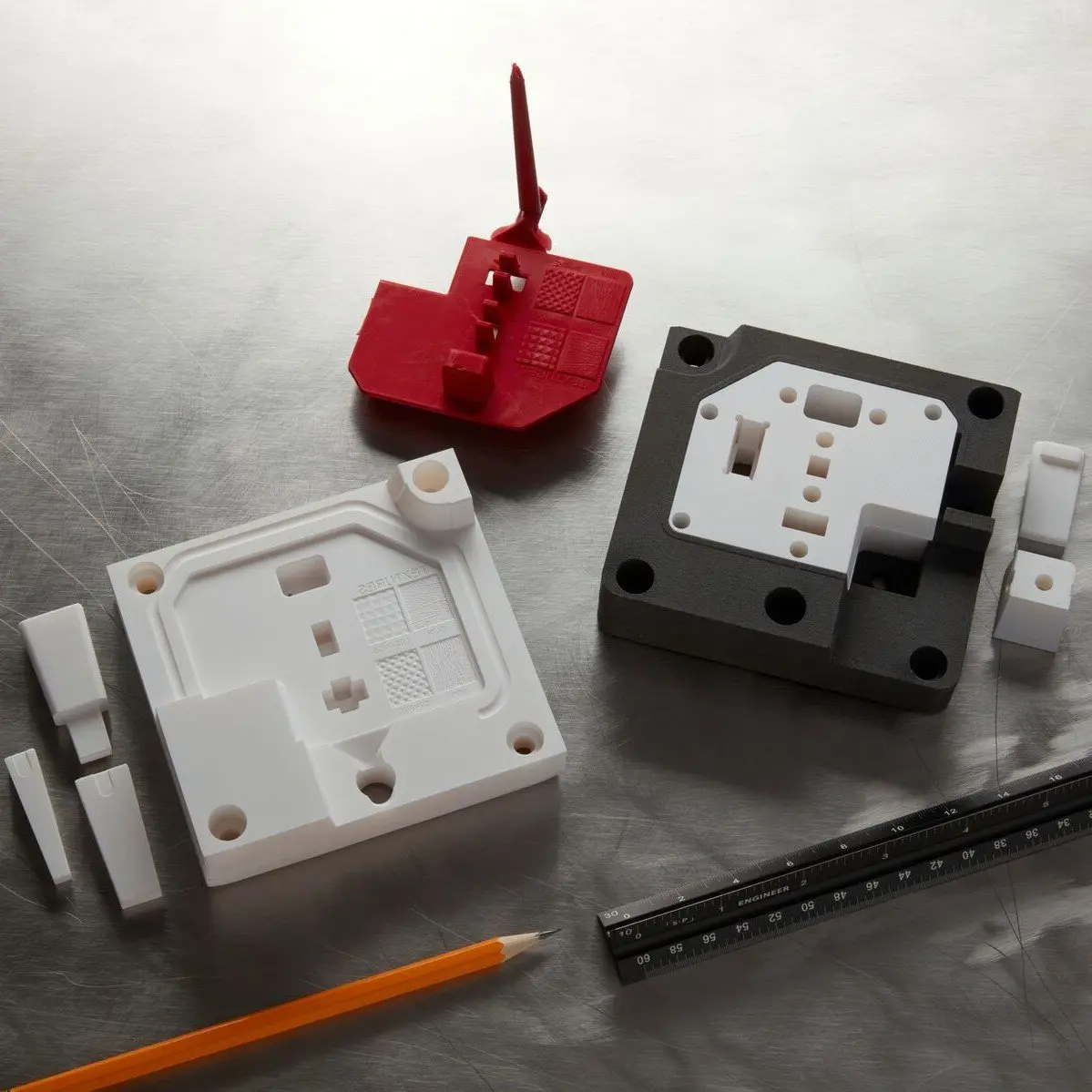
Guide to Rapid Tooling
In this white paper, learn how to combine rapid tooling with traditional manufacturing processes like injection molding, thermoforming, or casting.
Rethinking Tooling for Sheet Metal Forming
Rethinking toolmaking is a powerful way for reducing costs in metal manufacturing. Beyond the agility provided by prototyping expensive tools, 3D printed plastic dies can be efficient and affordable substitutes to expensive metal tools. For sheet metal forming, 3D printed tools offer multiple opportunities for applications from bent brackets to embossed parts, louvers, grille, and off the shelf set of dies for a press brake.
In our free white paper, we demonstrate how we successfully fabricated a metallic blade guard with the help of 3D printed plastic dies. We could potentially produce dozens of these parts with a single set of dies, bringing short-run production in house. Download the white paper now for the detailed case study and the step-by-step method and watch the webinar for specific design considerations and application examples.