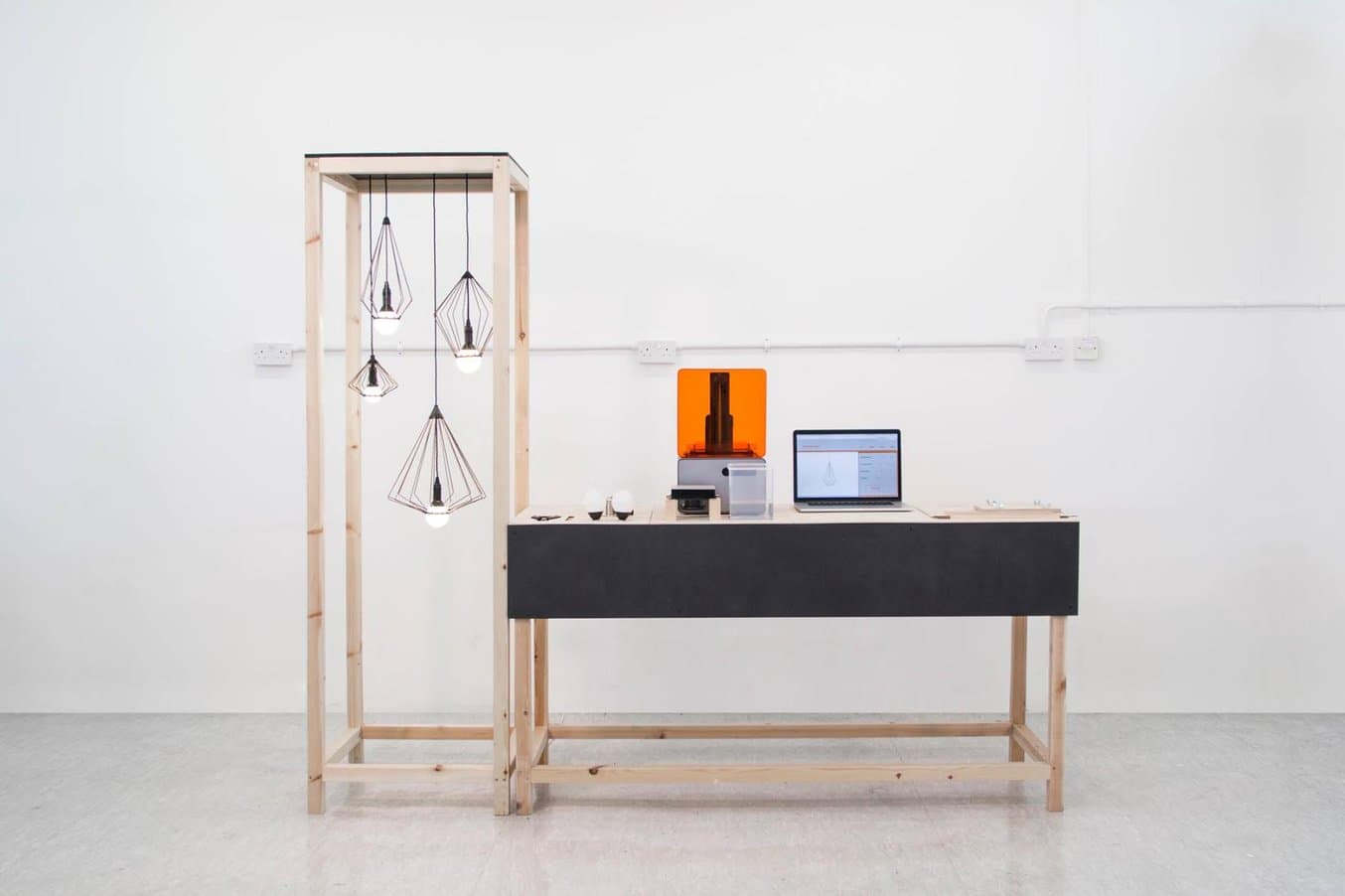
Studio deForm created a series of custom lamps by combining handcraft with digital prototyping. Their Factory lamps are designed and made from start-to-finish in a small workspace that includes only a Form 1+, laptop, and raw materials.
Reversing the typical design process, Studio deFORM designs each lamp by hand before it ever goes into a computer modeling program. The final shape of lamp is influenced by the number and length of the brass wires chosen by the designer, and the way they are bent together in a custom jig. After the wires have been bent manually, a parametric modeling program models a joint that connects all the wires together. The joint is then printed on the Form 1+ SLA 3D printer and added into the final lamp assembly.



Václav Mlynář, cofounder of Studio deFORM, believes designers are spending too much time behind the computer. Instead of using the computer to design, he sees it as a tool to aid him in the process of creating an object by hand. When he first began using the Form 1+, Václav was curious to discover the limits of the material and the high-resolution stereolithography printer.
From the beginning I was interested in joints, because they are often the crucial part of products and could be difficult to manufacture. I also like that if you combine 3D printed parts with standard pieces, you can create larger objects.


The custom Factory lamps are just the beginning for Studio deFORM. Vaclav plans to test print even larger assemblies with Formlabs Tough Resin and experiment with other raw materials such as glass and marble. Check out more of Studio deFORM’s work on their website.
Interested in our existing customer discounts for the new Form 2? Call our team at +1 (617) 702-8491 or contact sales to see if you qualify.