How 3D Printing Prototypes, Jigs, and Fixtures Enables UbeCube to Bring Manufacturing to the USA
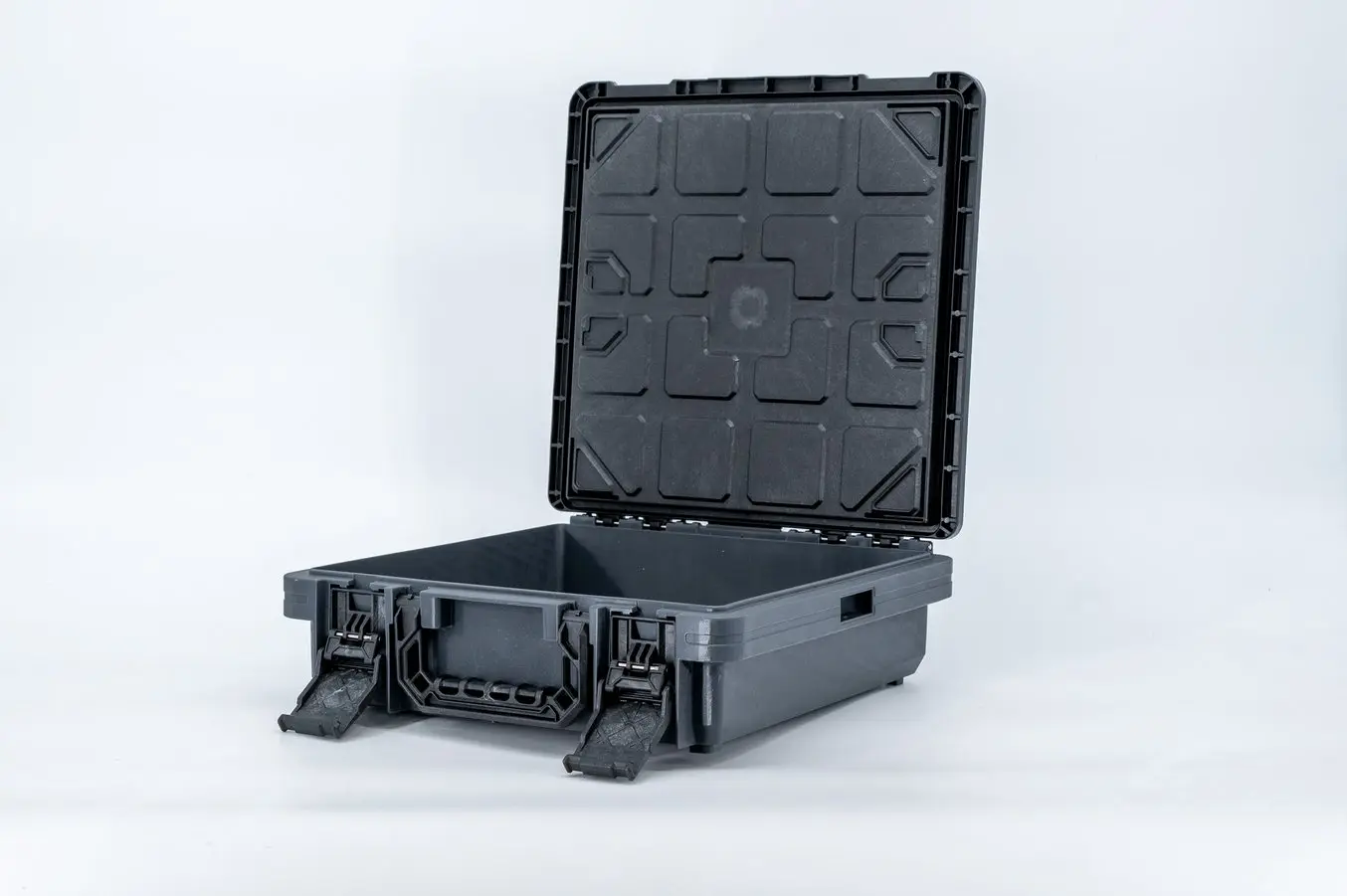
For UbeCube, a start-up that creates collapsible, stackable, modular storage system for a range of settings and applications, cost-efficiency and time-to-market are key. In order to reach their goals, they’ve not only moved large, functional prototyping in-house, but they’re also moving manufacturing to the USA.
“We're currently working on transitioning from overseas manufacturing to our manufacturing plant here in Grand View, Missouri. Our prototyping is becoming even more important as we have tooling at a quicker speed.”
Isaiah Tarwater, Industrial Designer, UbeCube
From working prototypes to jigs and fixtures for manufacturing, parts need to be produced at speed and hold up to demanding requirements. With a Formlabs Form 4L stereolithography (SLA) 3D printer, UbeCube has been able to quickly 3D print the robust prototypes they need, as well as jigs and fixtures to automate their new US factory.
Bringing Large-Format Prototyping In-House
When Industrial Designer Isaiah Tarwater started at UbeCube, the in-house print lab included two low-cost resin 3D printers. He brought in two Bambu Lab P1S FDM 3D printers, but large prototypes that needed to be printed in SLA were outsourced to China or, for shorter lead times, more locally in the USA. While overseas printing is less expensive than outsourced 3D printing in the US, the lead time could be four times longer. Tarwater saw the potential impact a fast, reliable, large-format SLA 3D printer could have if there was one in-house.
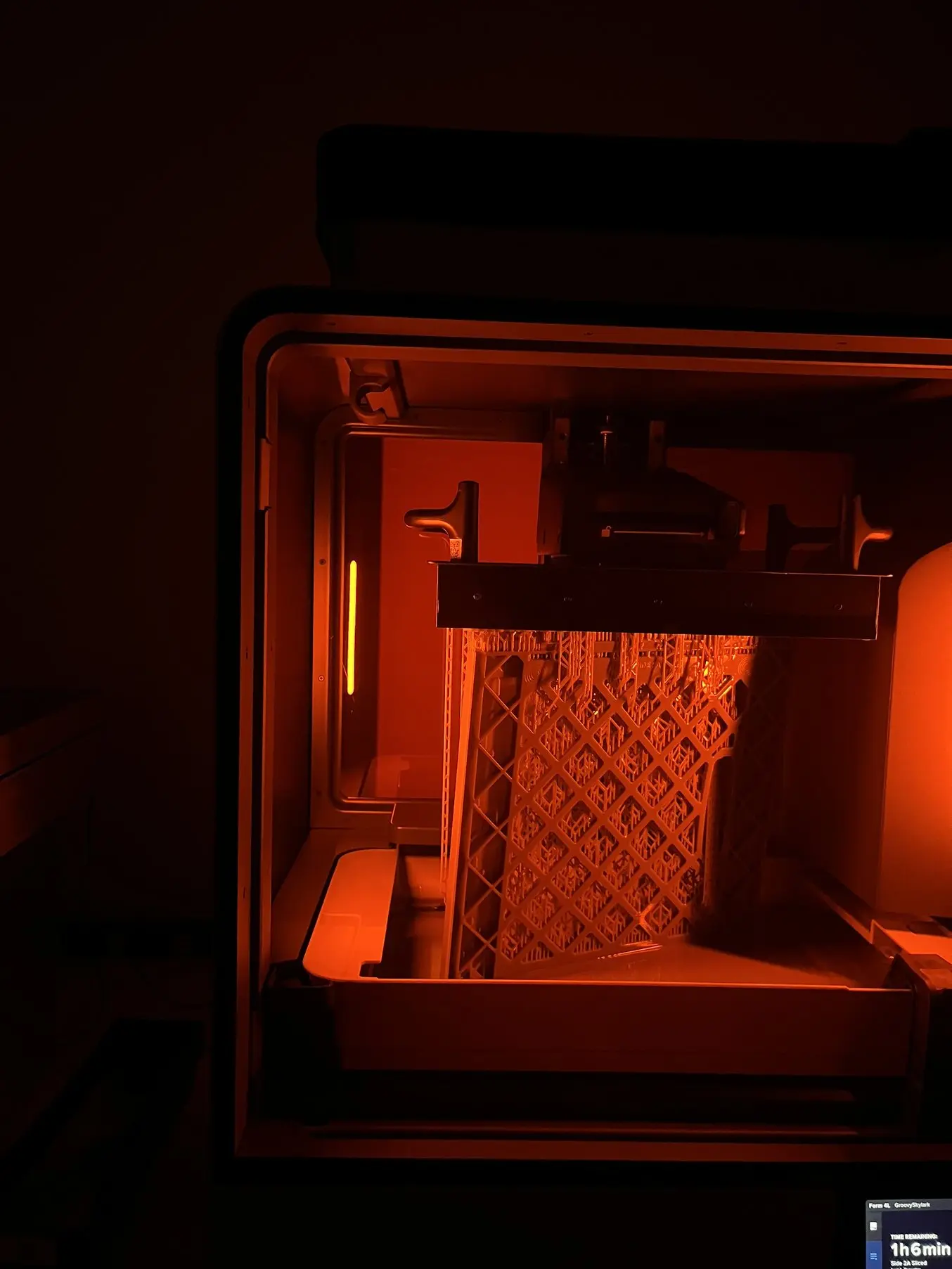
Prototyping functional parts and parts for photos are done on Form 4L.
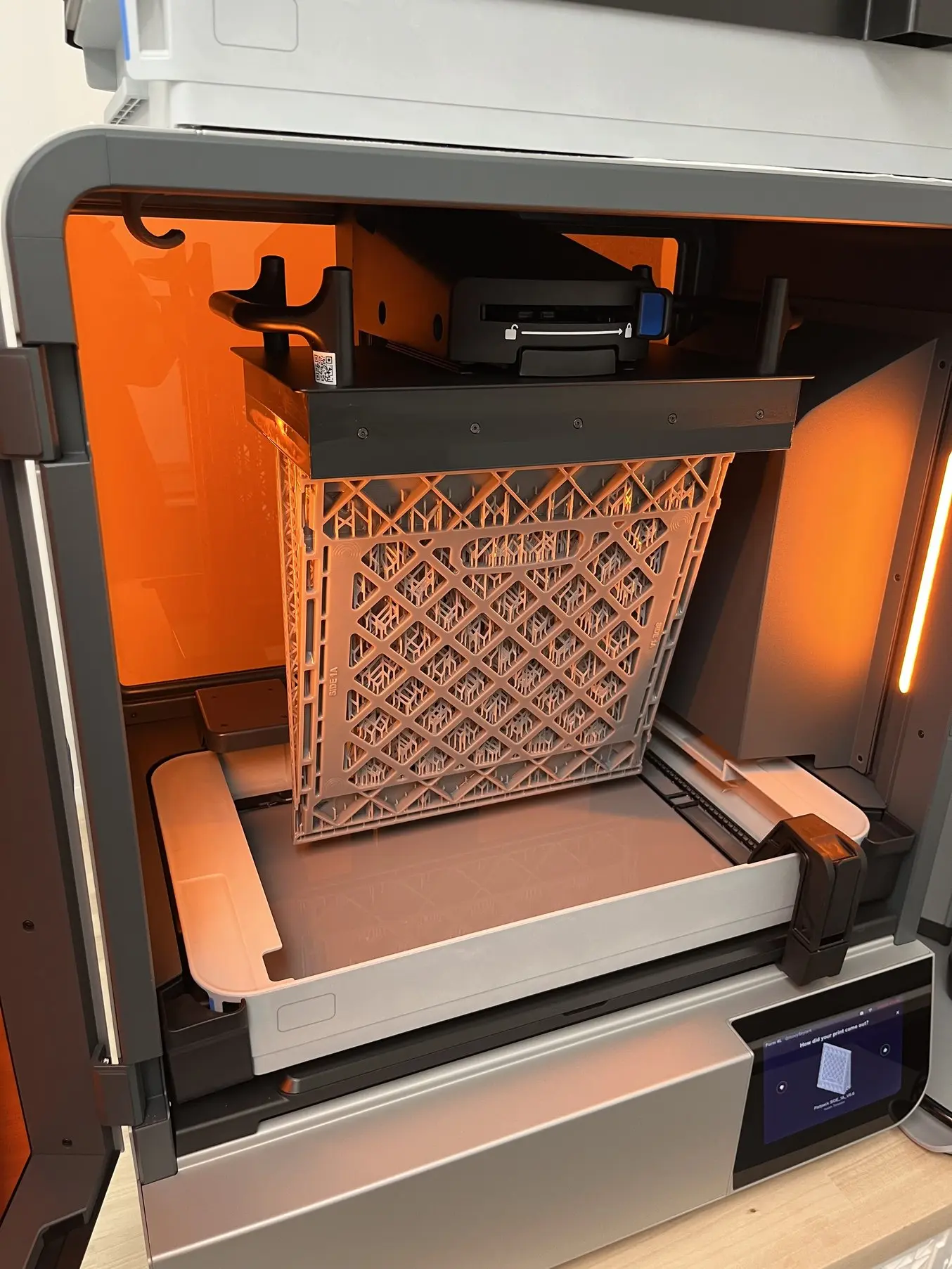
Form 4L is large enough that UbeCube’s crates can be prototyped inside.
“Before we got the Form 4L, we had to prototype larger items and we needed to get those relatively quickly. Sometimes those part batches shipped to the US in a month and would be $3,000-4,000. To get those same parts manufactured at a USA printing company is even more expensive, five to six thousand. At that point, Form 4L wasn't even a long-term payout — it paid for itself in two runs of parts.”
Isaiah Tarwater, Industrial Designer, UbeCube
Prototyping Costs
Cost per batch | Lead time | |
---|---|---|
Outsourced to China | $3,000-4,000 | ~1 month |
Outsourced in the USA | $5,000-6,000 | 7+ days |
In-house on Form 4L | $15-70/part* | <1 day |
*Depending on size, and not including machine costs.
Tarwater, having used Form Series 3D printers before, selected Form 4L for the build volume, reliability, and Formlabs material library.
“Formlabs resin printers are by far the least fidgety and most reliable printers. That reliability, and not having to troubleshoot, saves us so much time it's not even funny.”
Isaiah Tarwater, Industrial Designer, UbeCube
FDM 3D printing is used for the first few prototypes, fitment testing, and handheld ergonomics testing.
“As soon as we need prototypes that are up to photo quality or where we can actually look at draft angles and measure reliably, that's when we shift to the Form 4L. And if it's a part that needs to function as it would off of an injection molding machine, I'm doing SLA.”
Isaiah Tarwater, Industrial Designer, UbeCube
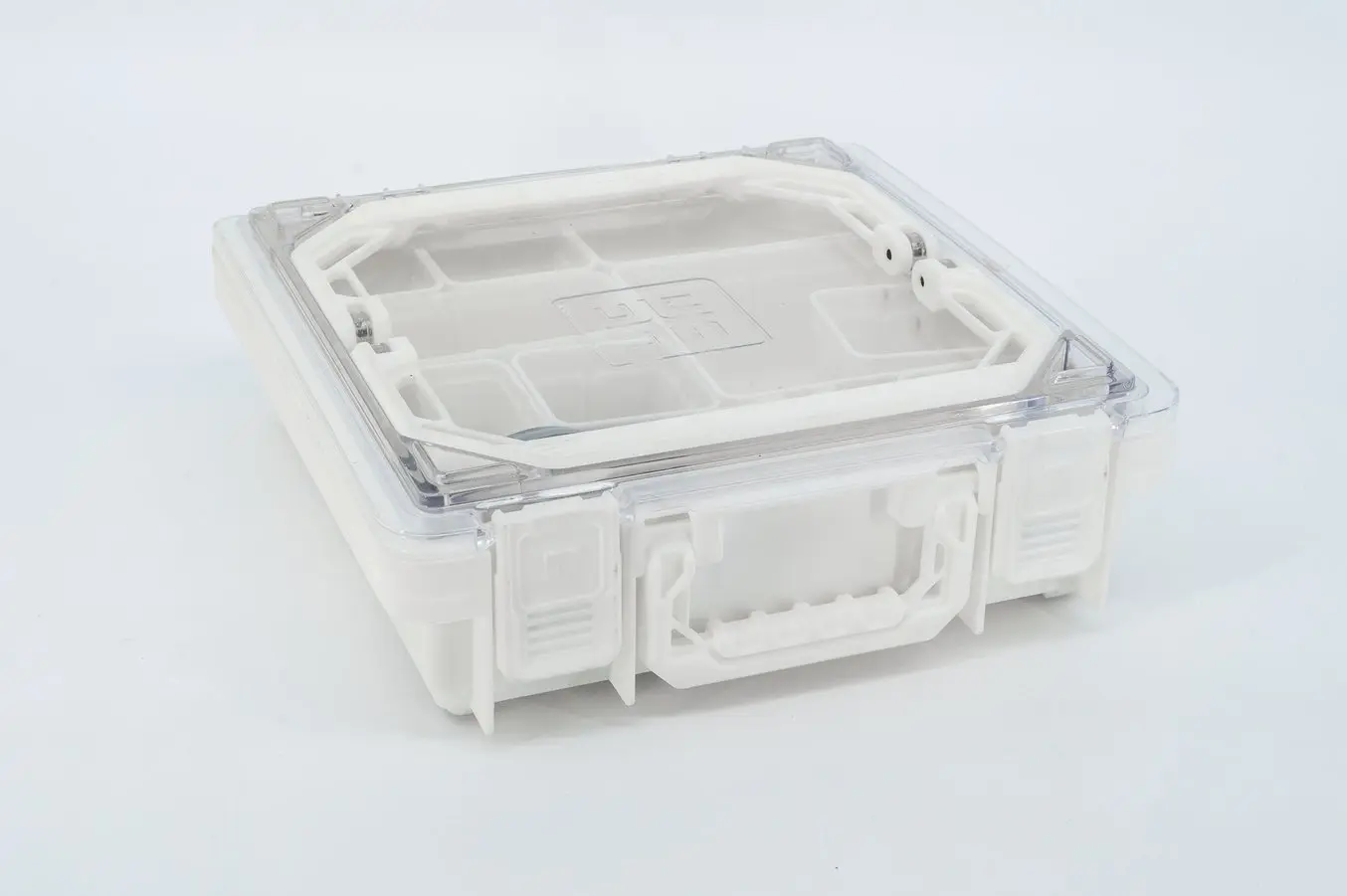
This Utility Box prototype was printed in White Resin V5 with an injection-molded polycarbonate lid.
For prototyping on Form 4L, Black Resin V5, a General Purpose Resin, is used for parts that don’t need to undergo tension or torsion, but might require a quarter turn for attachment. “At that price point,” Tarwater says, “it makes sense.” Another General Purpose Resin, Clear Resin V5, is used for visual prototyping of lids that will be manufactured in polycarbonate.
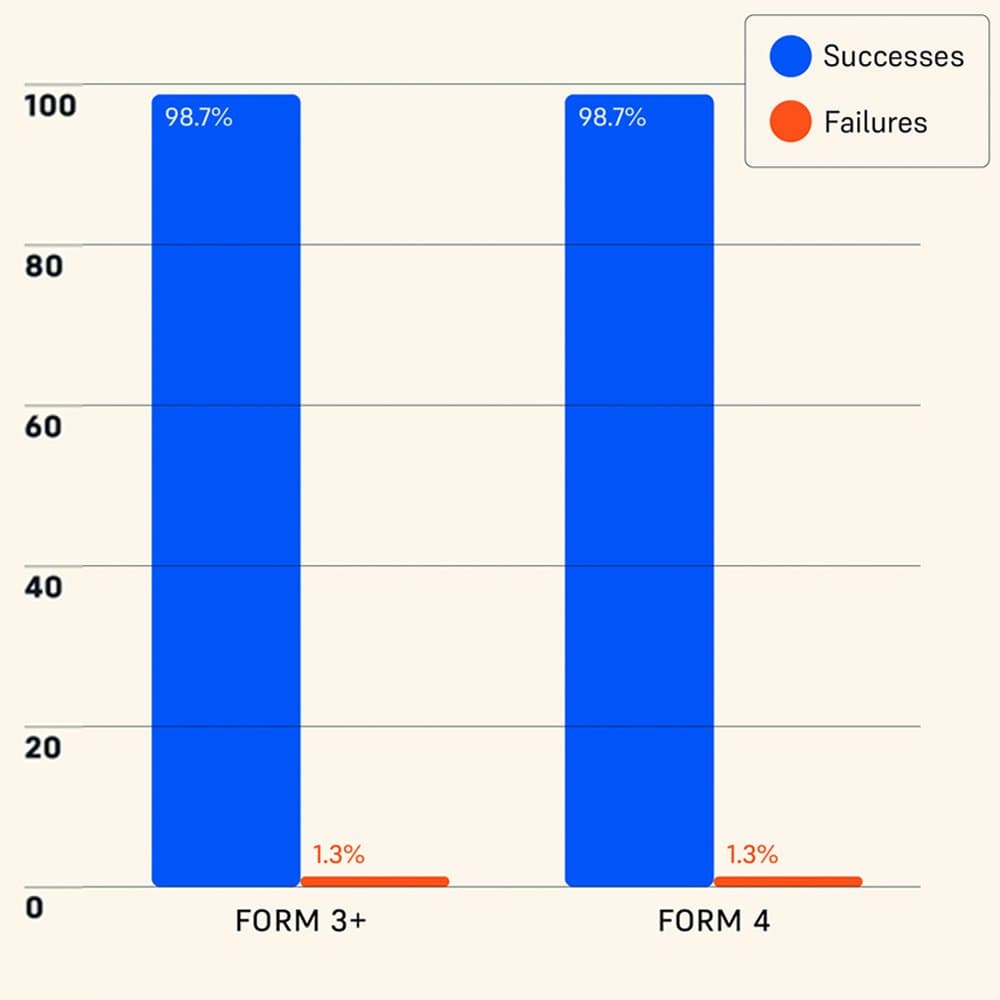
Independently Tested Reliability of Form 4 and Other Resin 3D Printers
Formlabs Form 4 was measured to have a 98.7% print success rate by an independent global leader in product testing. Read a complete description of the test methodology and see the results in our white paper.
Snap Fits With Tough 1500 Resin V2
“The vast majority of our products are in polypropylene and Tough 1500 Resin V2 lets us really emulate that.”
Isaiah Tarwater, Industrial Designer, UbeCube
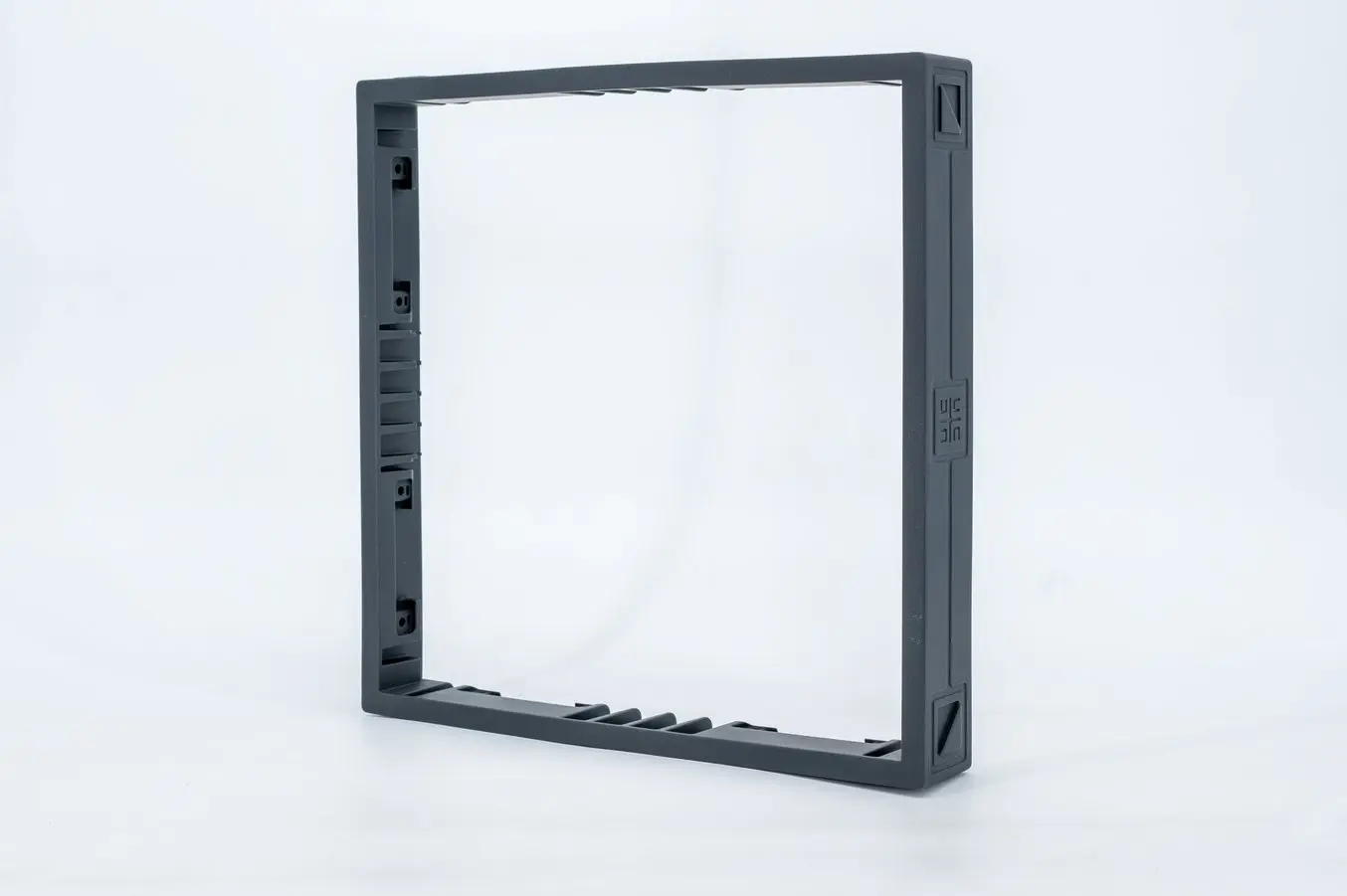
This prototype of a frame design for a crate was printed in Tough 1500 Resin V2 on Form 4L.
For functional prototyping, Tough 1500 Resin V2 is used. The majority of UbeCube’s molds are two-part without slides. This means that they focus on front-to-back moldability with snap-fits. Therefore, the ability to produce draft angles and snap fits on prototypes is important — as is getting large, one-off prototypes overnight.
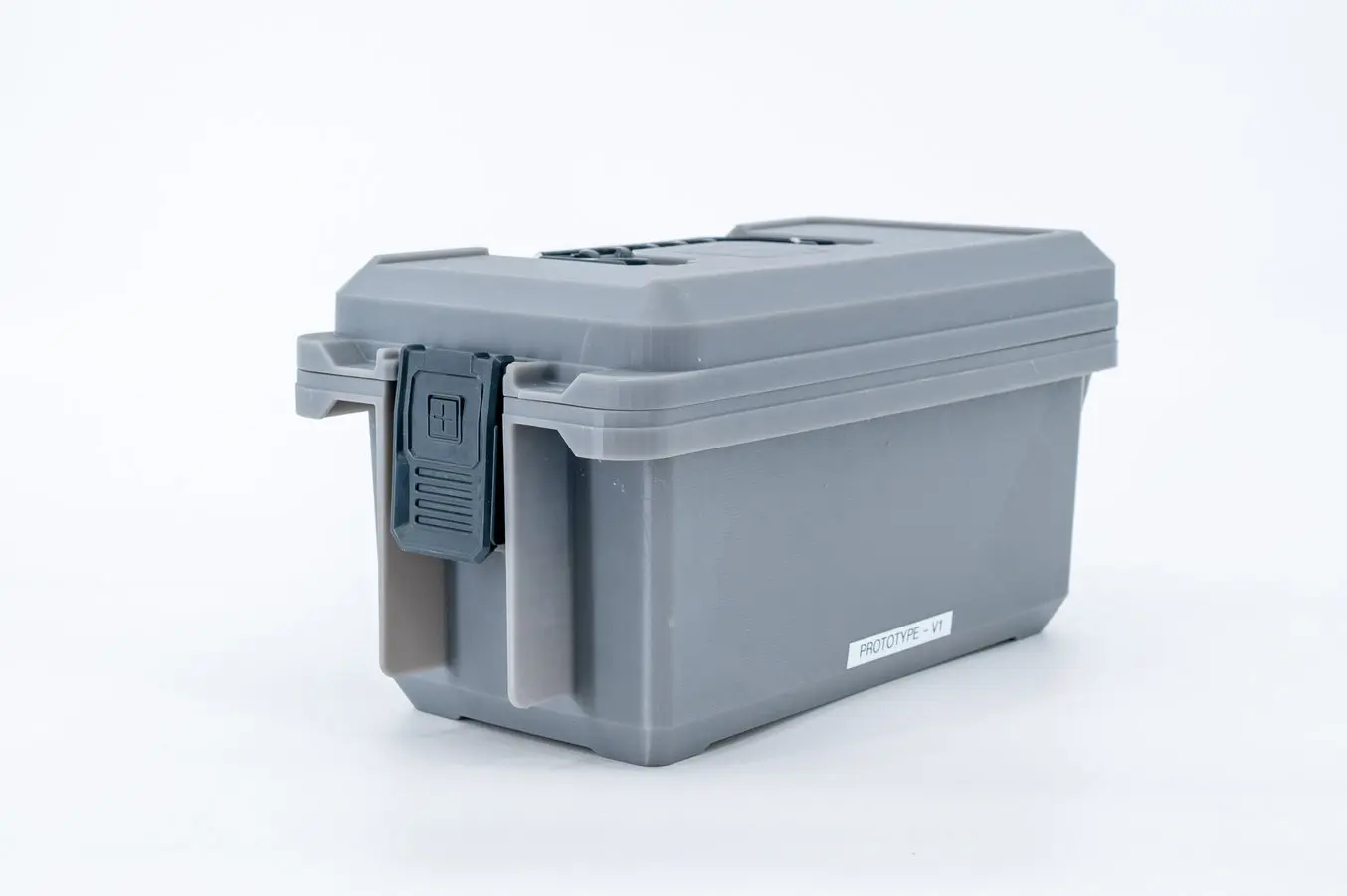
A prototype printed in Tough 1500 Resin V1. Tarwater began using Tough 1500 Resin V2 for functional prototypes once it was released. Secondary components of the Utility Box are injection-molded polypropylene.
Tough 1500 Resin V2 is a robust, resilient, and ductile material with properties comparable to polypropylene. Tarwater had used Tough 1500 Resin V1, but finds that the updated formulation holds up to repeated cycles without stress marks or deformation.
Prototypes printed in Tough 1500 Resin V2 hold up to the repeated cycles required of a prototype and look like the final, injection molded product.
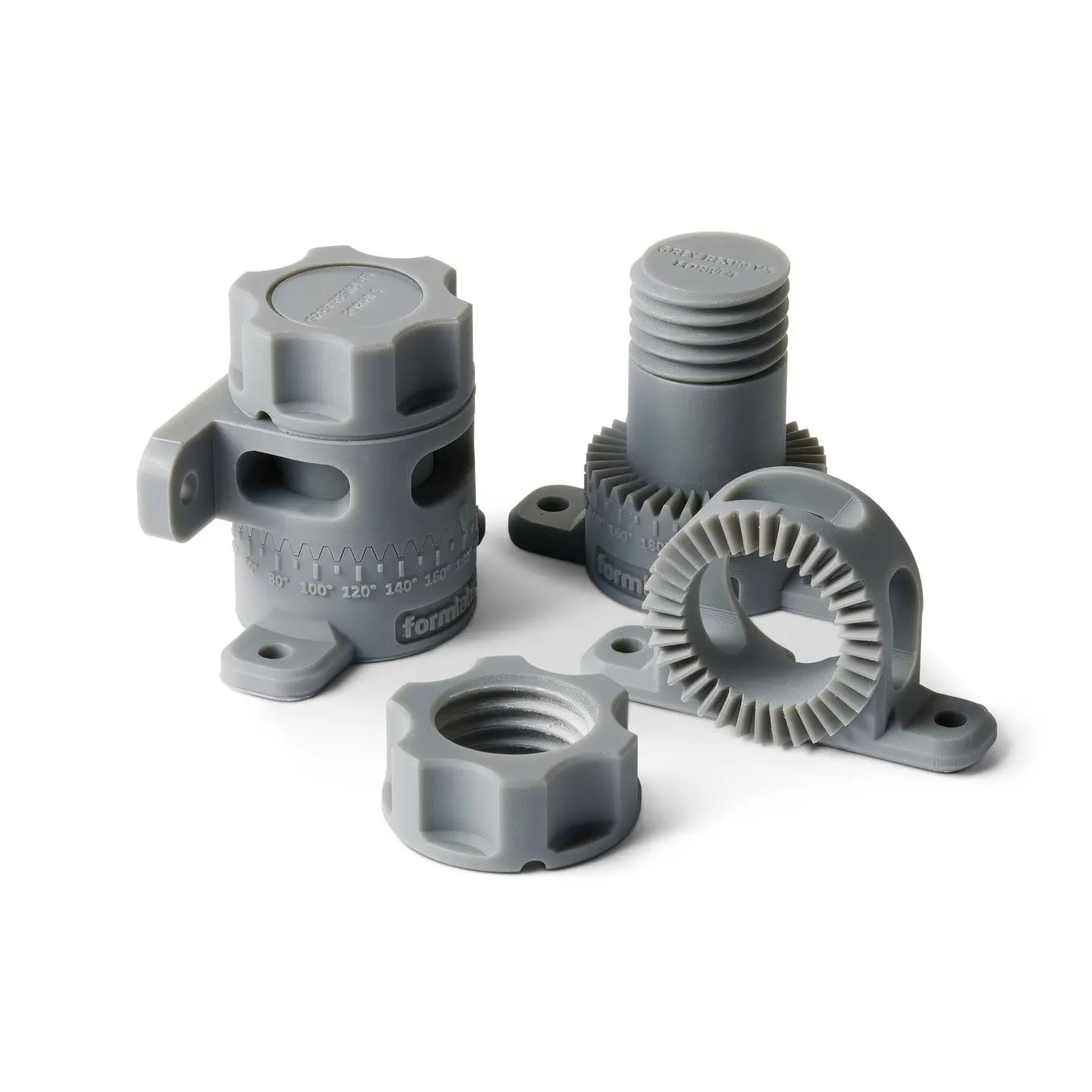
Request a Free Sample Part
See and feel Formlabs quality firsthand. We’ll ship a free 3D printed sample part to your office.
The Tackle Box
UbeCube’s Tackle Box is approximately a 12.5 x 12.5 x 4 in product prototyped on Form 4L in Tough 1500 Resin V2. The Tackle Box uses the entire 13.9 x 7.7 x 13.8 in (24.2 L) build volume of Form 4L — before Form 4L, it would’ve been impossible to prototype in-house. Printing in Tough 1500 Resin V2 means this is a functional prototype.
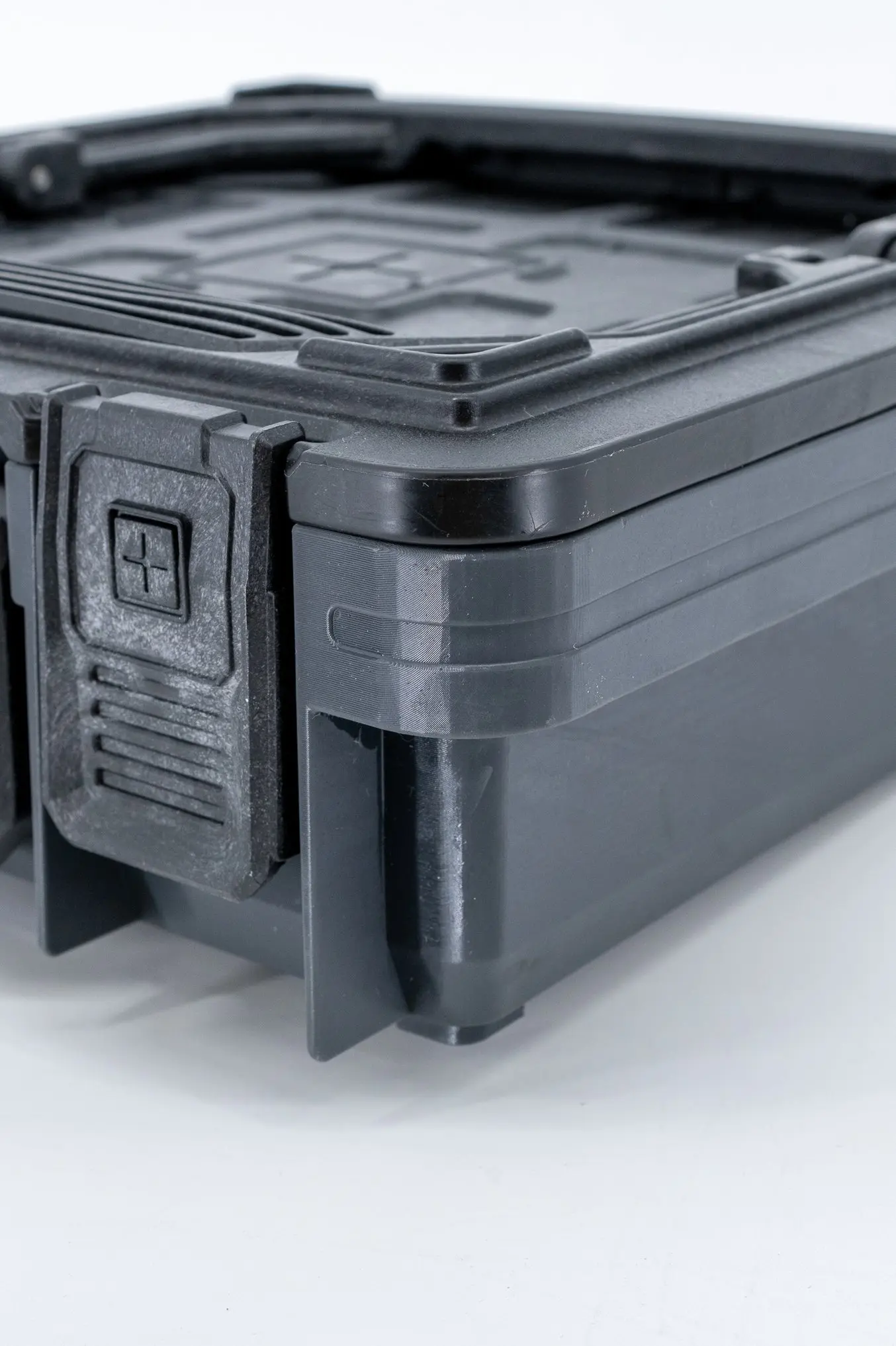
This Tackle Box prototype was printed in Tough 1500 Resin V2, which holds up to repeated cycles without stress marks or deformation.
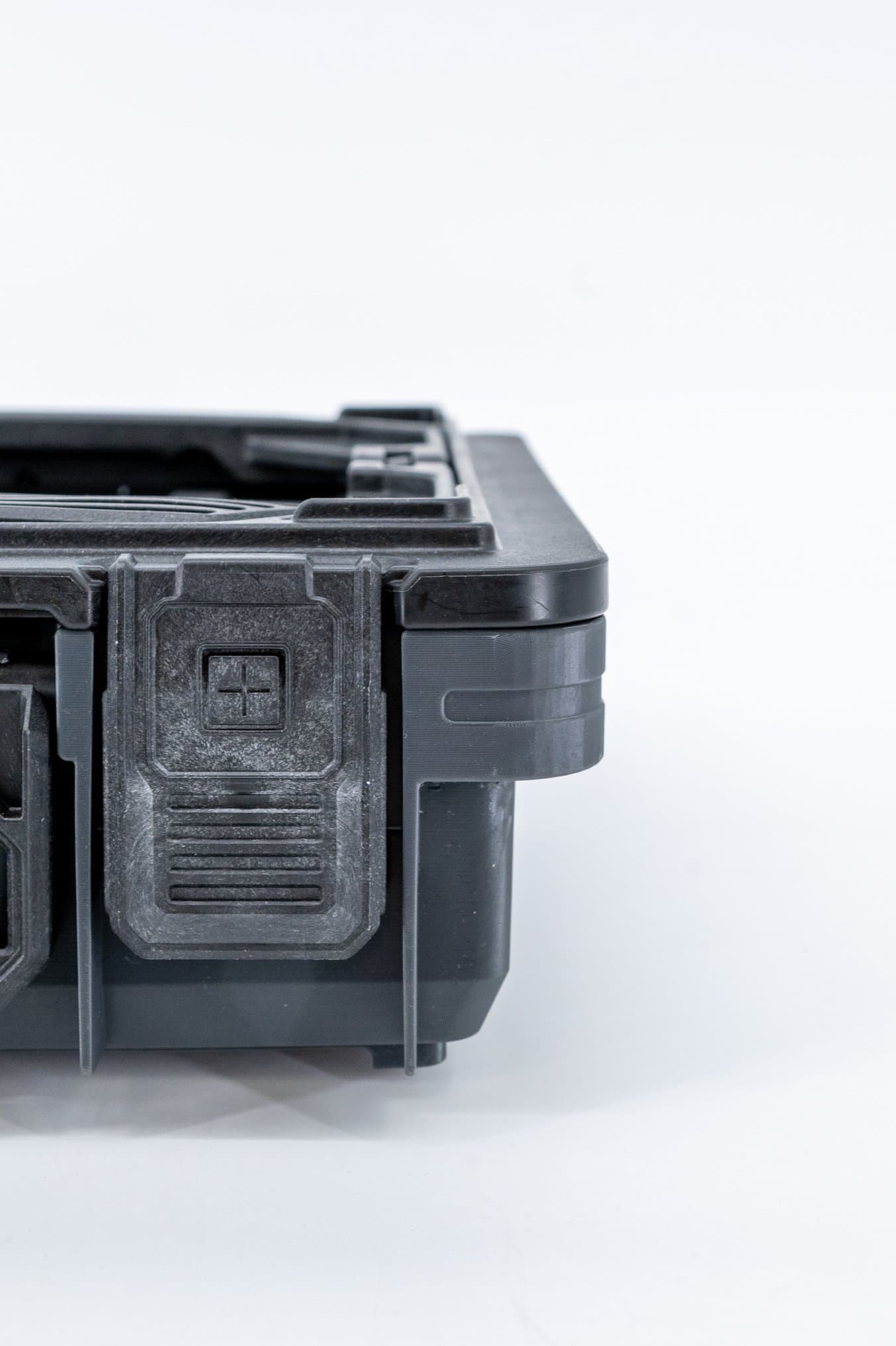
Secondary components are injection-molded polypropylene.
The lid on the box has a halfway point that holds the lid up before it’s opened the rest of the way. Having a working prototype enables Tarwater to “test the friction and the bump in there with every iteration. A quarter of a millimeter could be the difference between it staying up, or falling, or being too hard to open the rest of the way. That's something that we're fine-tuning right now that we've been testing with 3D prints.”
Cost-Efficient, USA Manufacturing With 3D Printed Jigs and Fixtures
The Tackle Box will be UbeCube’s first product to be developed and manufactured entirely in the USA. It will be manufactured via injection molding in UbeCube’s new manufacturing facility — using jigs and fixtures also 3D printed on Form 4L.
“We don’t have the time to wait nine months to a year for a tool to be completed at a factory overseas. We need it ASAP. So we're willing to spend that extra push at the beginning if it means saving by getting our product to market.”
Isaiah Tarwater, Industrial Designer, UbeCube
UbeCube is currently working to bring manufacturing to the United States, building out of a facility next door. Labor is the most costly component of US manufacturing, so UbeCube is automating as much of the process as possible.
“If we were hiring a lot of US labor for assembly and machine monitoring, it wouldn't make sense financially — we would just stay overseas even with tariffs. One of our biggest pushes, and the reason why it's taken us a little bit to get to full US manufacturing, is because we are using a mostly automated manufacturing process. We use a lot of alignment jigs and pneumatic placement components. With Rigid 4000 Resin, we're able to print off reliable components that'll last hundreds of cycles.”
Isaiah Tarwater, Industrial Designer, UbeCube
Building out this automation includes printing jigs and fixtures that can withstand hundreds of cycles. For these parts, Tarwater uses Rigid 4000 Resin, a glass-filled resin that offers a similar stiffness to PEEK and PEKK thermoplastics and which is highly resistant to heat and chemicals.
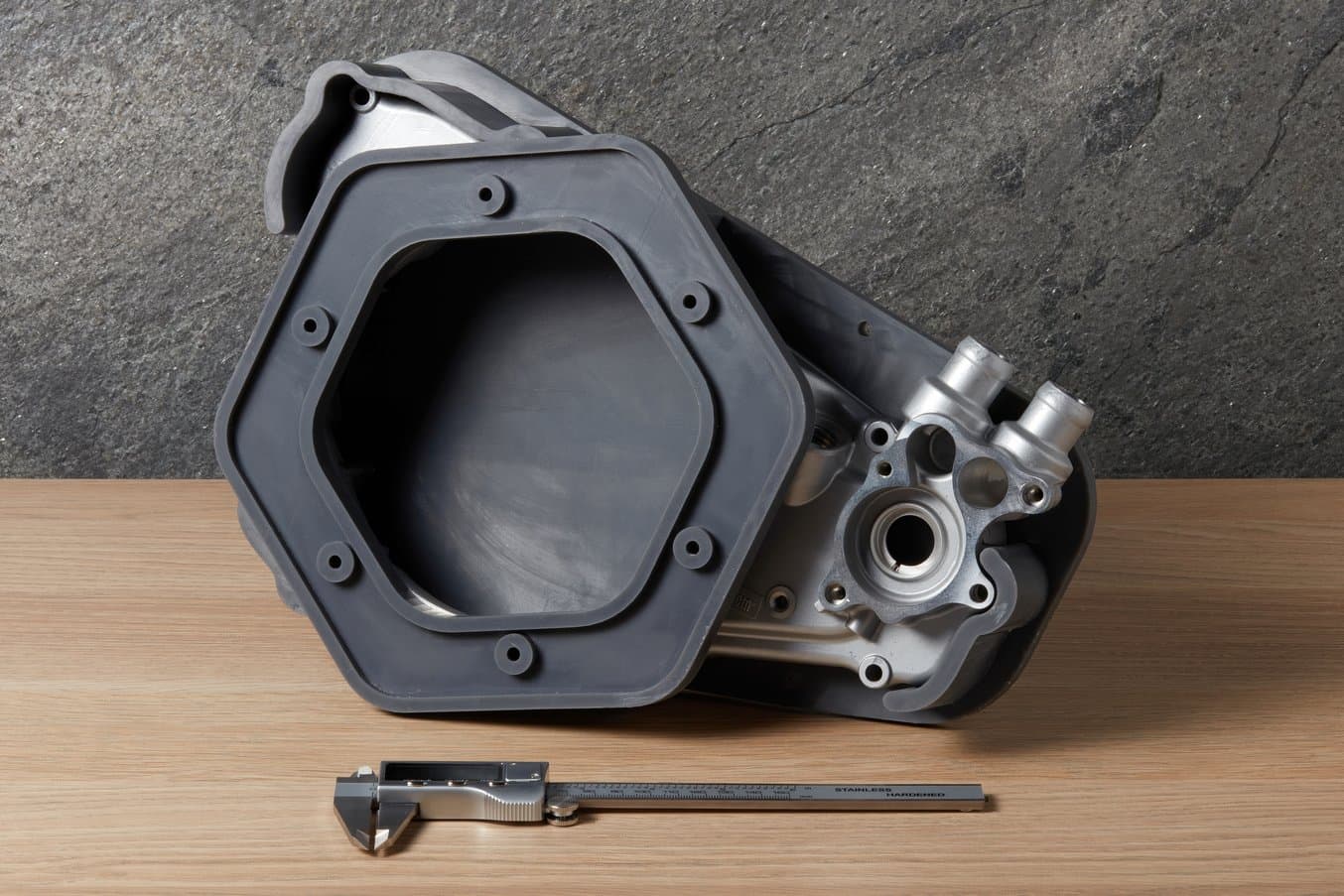
How to 3D Print In-House Jigs, Fixtures, and Other Manufacturing Aids
This white paper outlines the principles behind creating effective jigs, fixtures, and other manufacturing aids in-house.
Speeding Ahead
Getting products to market as fast as possible is key for an agile start-up like UbeCube. In addition to rapid prototyping of looks-like, functional prototypes, Tarwater has been working to add texture to parts, mimicking the effects of the foaming agent used to texture some of the injection-molded products. “Being able to produce a product that looks like it should instead of being a 3D printed prototype is pretty important,” says Tarwater. With a looks-like prototype, photos can be taken before the product is in-hand, shortening the timeline to salability.
3D printing jigs and fixtures on Form 4L is also propelling UbeCube’s speed, aiding the automation of their US manufacturing while saving labor costs and the time it takes to get tooling.
By bringing 3D printing in-house, UbeCube can control timelines, increase cost-savings, and minimize the time it takes to bring their products to market.
Request a free sample part to evaluate Formlabs resins for yourself. To learn more about large-format resin printing, explore Form 4L or contact sales.