Prototyping Rapid Diagnostics for COVID-19 With 3D Printing
What are Rapid Diagnostics?
Problem
Rapid identification of COVID-19 enables quicker quarantine and access to care, and is critical in supporting global efforts in preventing further spread of the virus. Developing countries are more vulnerable to infection as they have limited access to specialist facilities.
Mologic, a leading developer of lateral flow and rapid diagnostic technologies based in the United Kingdom, has been awarded £1 million as part of the government’s £46 million international COVID-19 prevention and research funding package.
Building on their experience developing rapid test kits for the 2014 Ebola outbreak, Mologic’s hand-held diagnostics devices allow health officials to test for the virus at home or in the community, providing results in just ten minutes, without the need for specialist medical supplies, or even electricity.
Professor Paul Davis, chief scientific officer of Mologic, said that the test will look for the presence of a viral protein. The person performing the test would not require any special training as they would only have to take a small prick of blood, similar to a blood-glucose monitoring test, or a swab of saliva.
How are Rapid Diagnostics Kits Made?
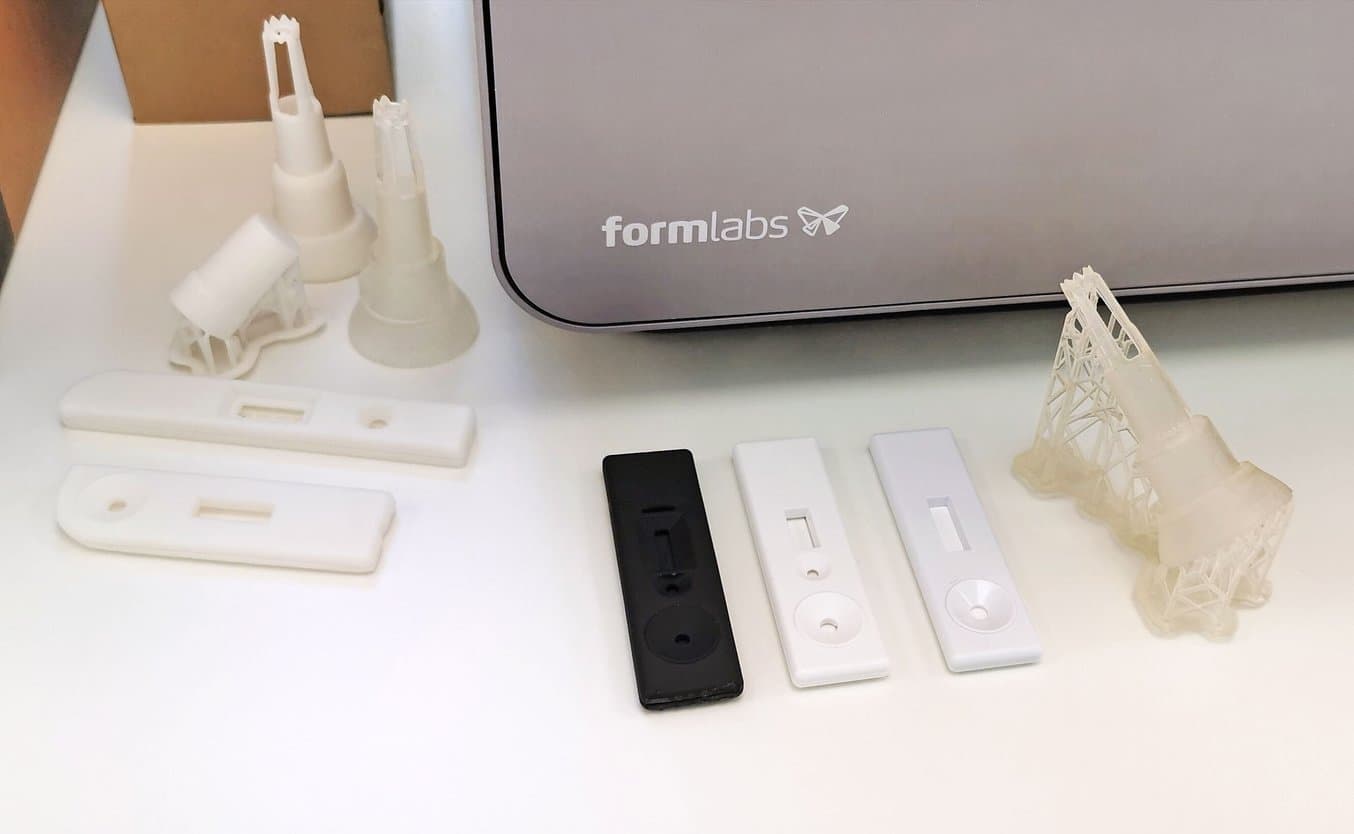
Mologic use their Formlabs desktop 3D printer to produce the housing for their rapid diagnostic kits.
Solution
With a team of over 40 scientists, Mologic has extensive experience in dealing with simplex or multiplex tests, as well as device housing and product design. In 2018, they approached the UK based additive manufacturing specialist and Formlabs authorised partner, GoPrint3D, to help choose an affordable desktop 3D printing solution that could turnaround high-precision parts, in minimal time.
Using their Formlabs Form 2 desktop stereolithography (SLA) 3D printers, they can quickly iterate their test devices in-house in their lab, to create point-of-need diagnostics for patients who are suspected to have picked up the virus.
Mologic tested various prototyping solutions before progressing with SLA, such as fused deposition modeling (FDM), but found that it could not match stereolithography in terms of surface quality. SLA offers a balance of feature resolution, surface finish, durability, choice of materials and dimensional accuracy, while being fully functional for tests and iterations.
“Mologic currently uses Formlabs 3D printers for the prototyping of all of its test devices for COVID-19 as the system is easy to use, has a wide range of materials, and is quick. The production of high-quality detailed parts is invaluable to speedy device development and the fact we can produce parts in a matter of hours with Formlabs technology enables us to progress quickly with our research,” said Adrian Walker, Biomedical Engineer at Mologic.
Dr. Joe Fitchett, Medical Director, Mologic, said: “The COVID-19 outbreak is at a critical juncture, and to bring it to an end, we need next-generation diagnostics for use at the point-of-need at home or in the community, in limited and well-resourced settings. Rapid detection of the virus is important to stop its spread. We are pleased that the UK government acknowledged this, supporting Mologic and the work of our partners to prevent further outbreaks internationally.”
Alongside their work on diagnostics, the UK government's aid is also supporting Mologic in the development of a COVID-19 vaccine candidate for further evaluation.
“At Formlabs, we’re aware that trust, accessibility, and scalability are everything in a time of crisis. Medical professionals depend on tools that are intuitive, versatile, and validated by industry and clinical leaders. We’re thankful of Mologic’s pioneering research to help prevent the spread of COVID-19, and proud of the role that 3D printing is playing at this critical time.” Gaurav Manchanda, Director of Healthcare at Formlabs.
Validation Status
Mologic’s COVID-19 laboratory and point of need antibody tests have both graduated from research and development, achieved design freeze and are ready for manufacture.
Both COVID-19 tests have been independently assessed by the Liverpool School of Tropical Medicine (LSTM) and St George’s University of London (SGUL) and are now being prepared for launch with CE mark. Mologic is proactively engaging with further independent validation groups, including the UK government, the World Health Organization, and the Africa CDC.
Clinical performance of IgG ELISA among known COVID-19 cases (PCR positive >10 days of diagnosis):
- Sensitivity 99% and Specificity 98%
- Total PCR positive cases tested 101
- Total negative cases tested 314 (pre-2019)
Update
Mologic recently disclosed that work is underway on a new diagnostic manufacturing facility adjacent to the firm’s current laboratory in Bedfordshire, UK - which will have capacity to produce up to 40 million tests per year.
The facility has been incorporated as an independent, sustainable social enterprise under the name of Global Access Diagnostics, with a commitment to deliver diagnostics at a fair price to both national and international markets.
3D Printing to Support COVID-19 Response
Formlabs is dedicated to helping the medical community address the COVID-19 epidemic and associated supply chain shortages with 3D printing technology. We have worked with dozens of hospitals and healthcare organizations around the world on various projects spanning COVID-19 testing, PPE, and medical equipment.
Formlabs' 3D printing systems are helping to deliver treatments and devices customized to better serve each unique individual, saving time and costs from the lab to the operating room.
In Partnership With

Disclaimer
Formlabs has created this website and has become involved in varying degrees with the projects described here during a global medical crisis. Formlabs is working on many projects to address global healthcare-related supply shortages around the world, but in trying to mitigate these shortages, patient safety is still Formlabs’ top concern. We must remind those who are helping to alleviate these shortages that masks, swabs, face shields, and other 3D printed products intended to prevent or treat COVID-19 are medical devices that these devices must be safe for their intended purpose and anyone considering the manufacturing of these products should consider the following items:
-
Formlabs is a manufacturer of 3D printing materials capable of fabricating finished devices according to their labeling and any other product manufactured from these materials should be verified and validated according to their intended purpose.
-
You may be fabricating a device that does not have the required regulatory approvals and clearances. If you are fabricating devices, follow the guidelines on the label for each material. You may seek to obtain reliable regulatory advice.
-
Please consider local regulations, material safety data sheets, software capabilities, sterilization requirements, and institutional requirements before 3D printing medical devices.
-
Regulatory agencies (such as the MHRA, BfraM, etc.) may consider an expedited review of manufacturing information and/or premarket submissions.
Formlabs cannot warrant that any products not manufactured by Formlabs are suitable for their intended purpose. Formlabs has not independently verified or validated the specific design parts mentioned in this case study and if they are safe or effective for their intended purpose. Any 3D printed appliances that are subjected to skin contact should meet the biocompatibility requirements stated in ISO 10993-1.