Der Druck von Produktionskomponenten für den Form Wash L und Form Cure L auf dem Fuse 1
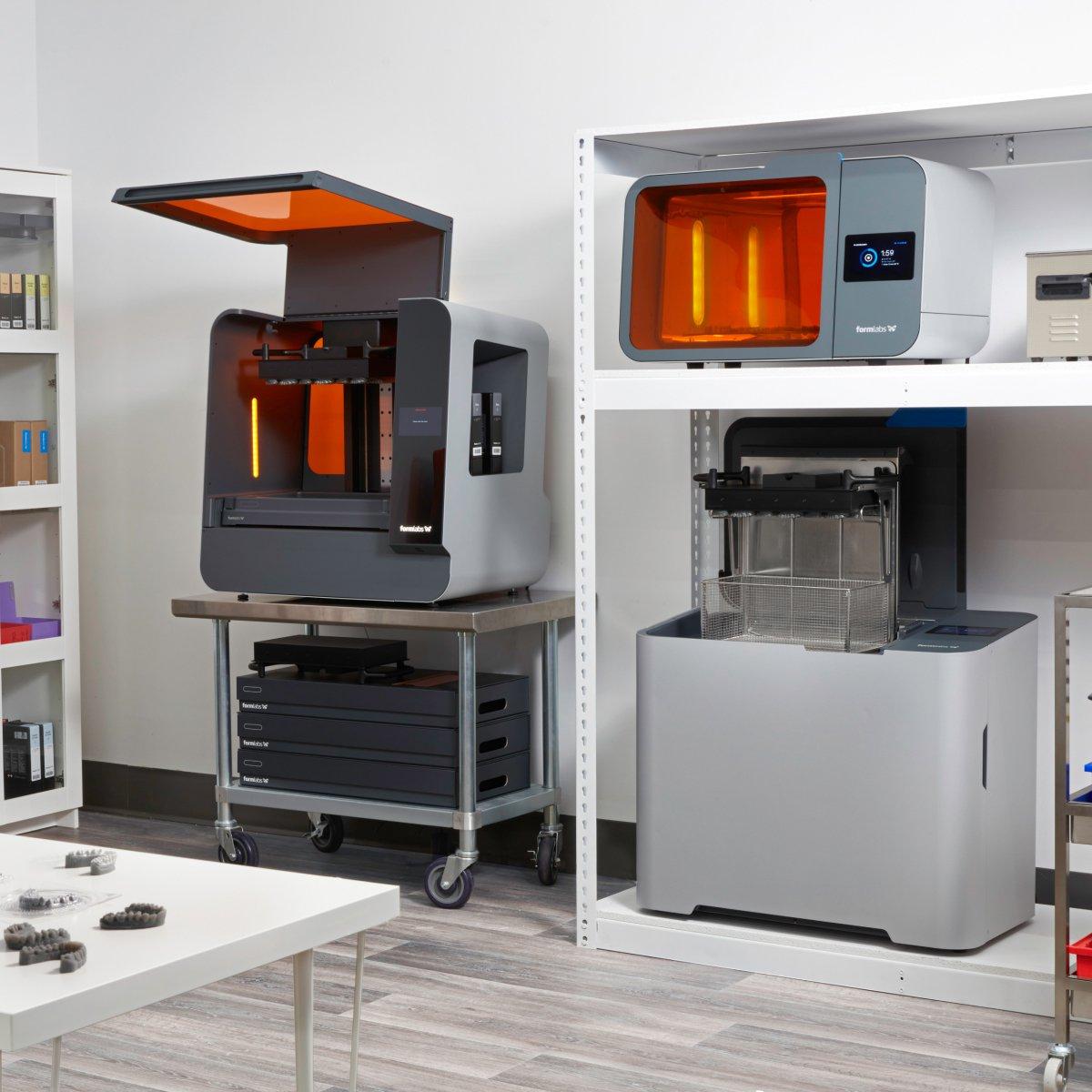
Vor der Veröffentlichung des Form Wash L und Form Cure L gab es nur wenige Optionen zur Nachbearbeitung großformatiger Stereolithografie-Teile (SLA). Vielerorts wurde bereits mit den großformatigen SLA-Druckern von Formlabs, Form 3L und Form 3BL, gedruckt, es fehlte jedoch noch die Nachbearbeitungslösung. Wir standen also unter Druck, um die zugehörigen Wasch- und Nachhärtegeräte zu entwickeln und zu fertigen.
Dafür benötigte das Ingenieurteam bei Formlabs eine reaktionsschnelle und hochqualitative Prototypenlösung und die Fähigkeit, robuste Endverwendungsteile für Designs zu produzieren, die sich jederzeit noch ändern könnten. Die Antwort darauf war jedoch nicht weit entfernt: Formlabs' hauseigener SLS-Drucker Fuse 1 und Nylon 12 Powder.
Im Folgenden erfahren Sie, wie Formlabs den Fuse 1 sowohl für die Prototypenentwicklung als auch für die Endverwendungsteile der Nachbearbeitungsstationen Form Wash L und Form Cure L einsetzte, mit denen sie noch heute an die Kundschaft ausgeliefert werden.
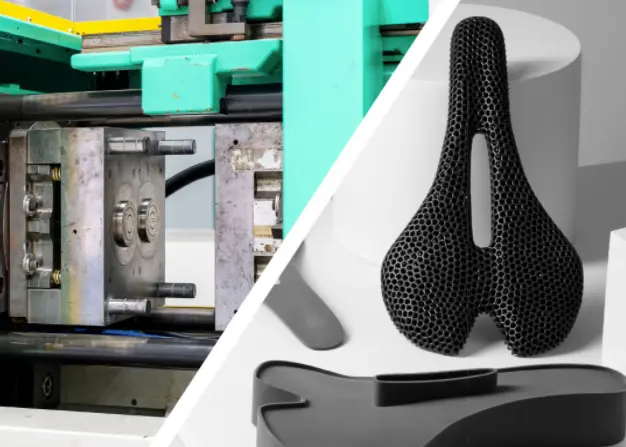
SLS-3D-Druck oder Spritzguss: Wann sollte man Spritzgussteile durch 3D-Druck ersetzen?
Dieses Whitepaper zeigt die Kostendynamik für Anwendungsfälle aus der Praxis und stellt Leitfäden vor für den Einsatz von SLS-3D-Druck, Spritzguss oder einer Kombination beider Verfahren.
Ein allumfassender Arbeitsablauf für großformatigen SLA-Druck
Seit September 2020 vertreibt Formlabs den Form 3L, unser Aushängeschild der großformatigen SLA-Drucker. Nachdem wir unseren Kund*innen jahrelang erzählen mussten, dass die einzige Möglichkeit für große Teile daraus bestand, ihre CAD-Datei in der Mitte durchzusäbeln und nach dem separaten Druck mühsam zusammenzupuzzlen, machte der Form 3L es endlich möglich, große Teile ohne Abstriche in der Präzision, der Oberflächengüte oder der Materialeigenschaften zu fertigen – so, wie sie es von ihren normalen Formlabs-Druckern kannten.
Der Form 3L zeigte seinen Einfluss sofort in jeder Branche. Kieferorthopädische Labore konnten am Tag bis zu 120 Vollbögen drucken. Produktentwicklungsfirmen wie Black Diamond druckten Helmprototypen in Lebensgröße. Und Krankenhäuser druckten Anatomiemodelle des Brustkorbs eines Erwachsenen zur Operationsvorbereitung.
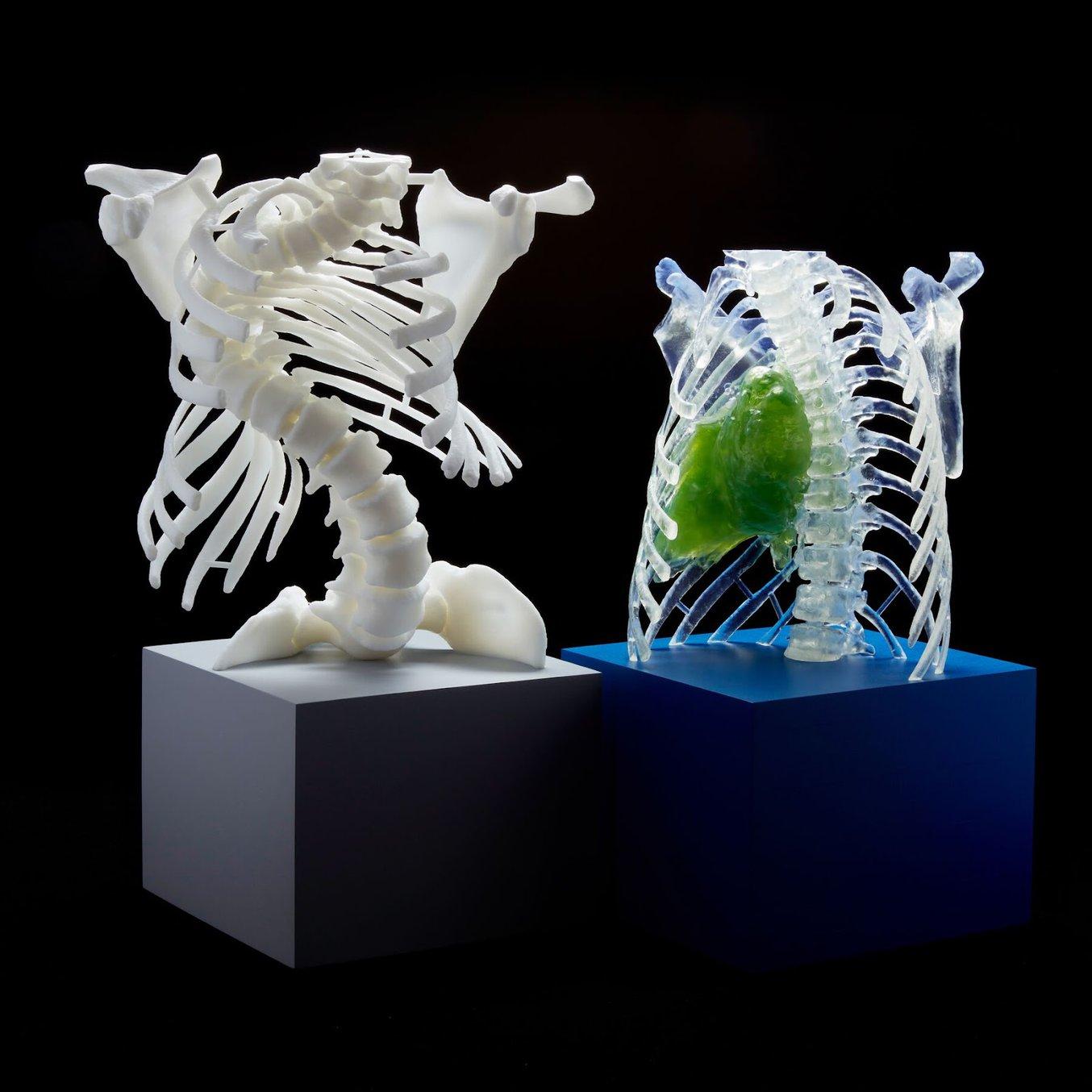
Und trotzdem spürten alle Kund*innen, dass der Arbeitsablauf unvollständig war. Die Verzögerungen bei den zugehörigen Nachbearbeitungsgeräten bedeuteten, dass sich die meisten nach Optionen von Drittanbietern umsahen oder selbstgebaute Lösungen einsetzten – beides führte zu ungleichmäßigen Ergebnissen.
Prototypenentwicklung des Form Wash L und Form Cure L mit dem Fuse 1
Der Grundgedanke der neuen Produkte lag auf der Hand: größere Versionen des Form Wash und Form Cure. Doch die Beschaffung einiger Teile wurde kompliziert, als die Probleme in der globalen Lieferkette durch COVID-19 nur noch verstärkt wurden. Das führte zu Verzögerungen bei vielen Materialien, die das Team zur Prototypenfertigung benötigte.
„Wir hatten definitiv Schwierigkeiten. Wir hatten einen knappen Zeitplan und da war die Beschaffung der Materialien für die Entwicklungsgeräte sehr knifflig. Es gab Probleme in der Lieferkette und wir sahen uns einem recht aggressiven Lieferplan gegenüber“, berichtet Formlabs' Supply Chain Engineer Megan Liu.
Glücklicherweise hatte das Team eine Lösung in Industriequalität für die Prototypenfertigung und Produktion direkt im Nebenraum. Als verschiedene traditionelle Fertigungsverfahren aufgrund von Kosten oder Durchlaufzeiten als Option versagten, ermöglichte das SLS-System des Fuse 1 dem Team des Form Wash L/Form Cure L, schnell mehrere Iterationen zu durchlaufen, bei jedem Teil des Designs der beiden Geräte. Sechs dieser Teile werden noch heute mit dem Fuse 1 gedruckt und kommen im Endprodukt zur Anwendung.
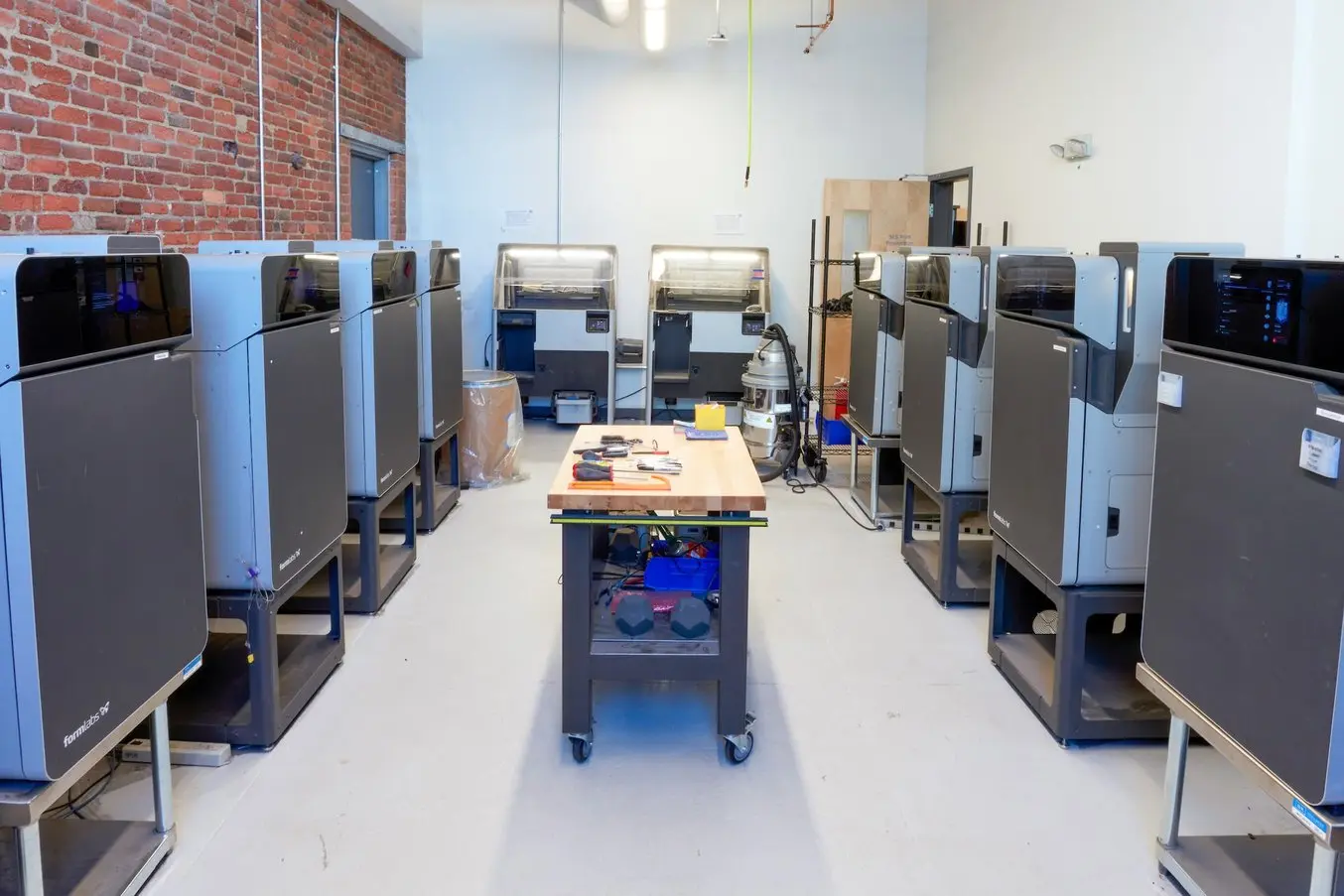
Die Herstellung von Teilen für den Form Cure L auf dem Fuse 1
Ein Form Cure L, der heute an die Kundschaft ausgeliefert wird, hat drei gedruckte Komponenten aus dem Fuse 1: ein Drehtellergetriebeteil, der Magnethalter der Tür und der Abstandhalter der Verriegelung. Auch der Form Wash L hat zwei verschiedene Pumpenklemmen, die aus Nylon 12 Powder auf dem Fuse 1 gedruckt werden. Zudem gab es bei der ersten Lieferserie auch noch eine kleine Magnetabdeckung. Außerdem ist dies nicht das erste Mal, dass unser Beschaffungsteam den Fuse 1 zur Produktion von Endverwendungsteilen von Formlabs-Geräten nutzt. Der Fuse 1 selbst hat ebenfalls Teile, die in der Formlabs-Fabrikation auf dem Fuse 1 gedruckt werden.
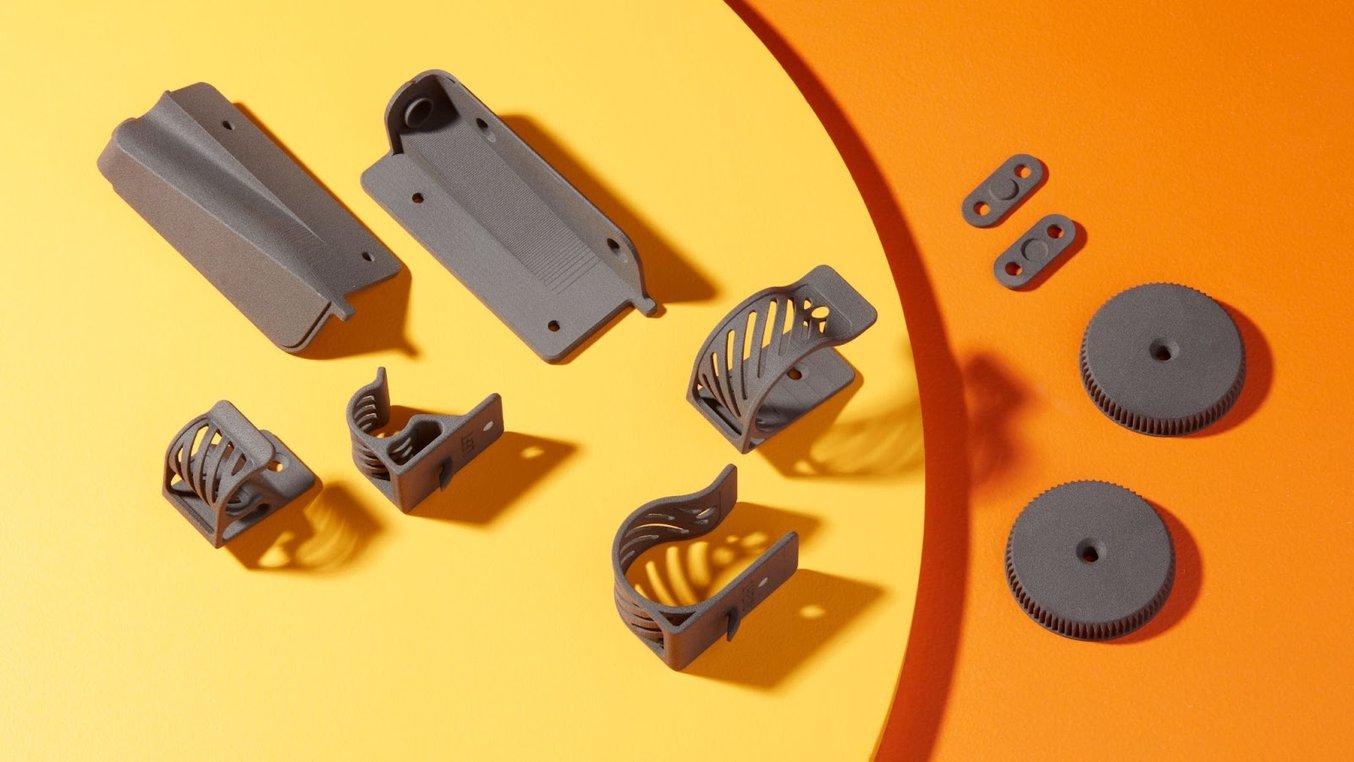
Beim Design des Drehtellergetriebes im Form Cure L musste das Team mehrmals iterieren, damit das gefaste Loch in der Mitte den Drehteller auch sicher festhielt und dabei genug Kraft übertrug, um den Teller zu drehen. Nach mehreren Entwürfen und Prototypen entschied sich das Team aufgrund des Kerndesigns in der Mitte für den 3D-Druck anstelle von Spritzguss. Beim Spritzguss hätte dieser Kern zweier Teile bedurft, aber bei SLS konnte das Designteam alle in einem Entwurf zusammenfügen – als einzelnes Teil.
„Wenn das Loch nicht passte, konnten wir es sofort ändern. Wir konnten alles richtig schnell anpassen, Funktionsprobleme beheben und etwas Neues ausprobieren. Der Wechsel zwischen den Iterationen war deutlich leichter, da wir uns bei neuen Iterationen nicht mit Veränderungen der Werkzeuge oder mit den Zulieferern herumschlagen mussten“, verrät Liu.
Den Abstandhalter für die Verriegelung des Form Cure L entwickelte das Team mithilfe des SLA-Druckers Form 3, bevor es das endgültige Teil auf dem Fuse 1 druckte. Kunststoff war das Material der Wahl, da Verriegelungssensoren am besten funktionieren, wenn sich zwischen Magnet und Sensor kein Metall befindet. Dieses Teil bildet einen ästhetischen Abschluss der Außenseite und sorgt für möglichst wenig Kunststoff vor dem Sensor. Gleichzeitig bestimmt es den Abstand des Sensors, indem es vier Abstandsstufen bietet. Das Team sparte Zeit und Geld dank des betriebsinternen Übergangs von Prototypenentwicklung zur Produktion. Durchlaufzeiten für Werkzeugbestückung wurden gänzlich eliminiert.
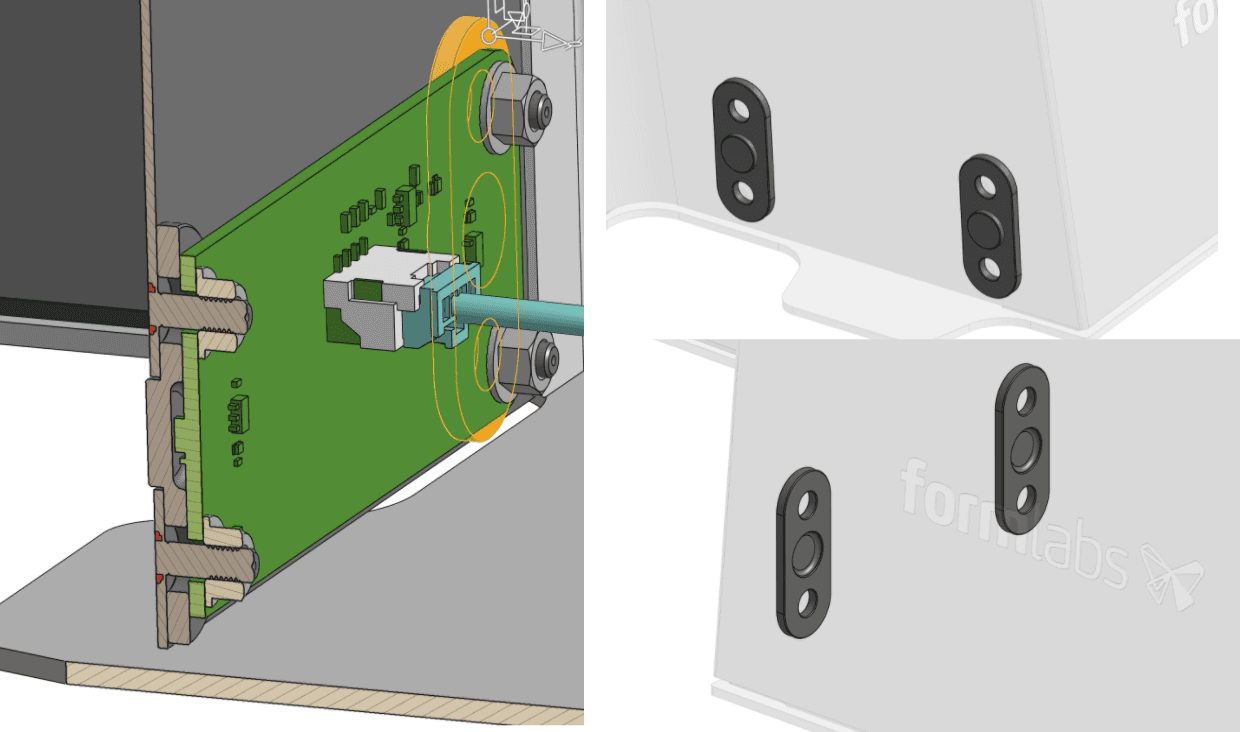
Der Abstandhalter der Verriegelung beim Form Cure L, dargestellt im CAD
Die letzten Fuse-1-Teile für den Form Cure L sind zwei Magnethalter für die Tür. Diese beherbergen die Magnete, welche die Klappe des Form Cure L geschlossen halten und für den „Klick“ sorgen. Wegen des Magnetismus und auch für das Berührungsgefühl mussten diese Teile aus Kunststoff bestehen. Ein Metallteil würde die Pulverbeschichtung verkratzen und unerwünschte Kratzgeräusche beim Schließen der Tür verursachen. Da dieses Teil zwei Aspekte abdecken muss – den objektiven (schließt die Tür?) und den subjektiven (wie fühlt sich das Schließen an?) – war die Einigung auf ein Design nicht leicht. Deshalb wurden erst einmal alle anderen Komponenten finalisiert. Hätte das Team an dieser Stelle den Spritzguss des Teils auslagern müssen, hätte das die Fertigungsplanung um Wochen verlängert. Der betriebsinterne Druck ermöglichte hingegen die Einhaltung des engen Zeitplans.
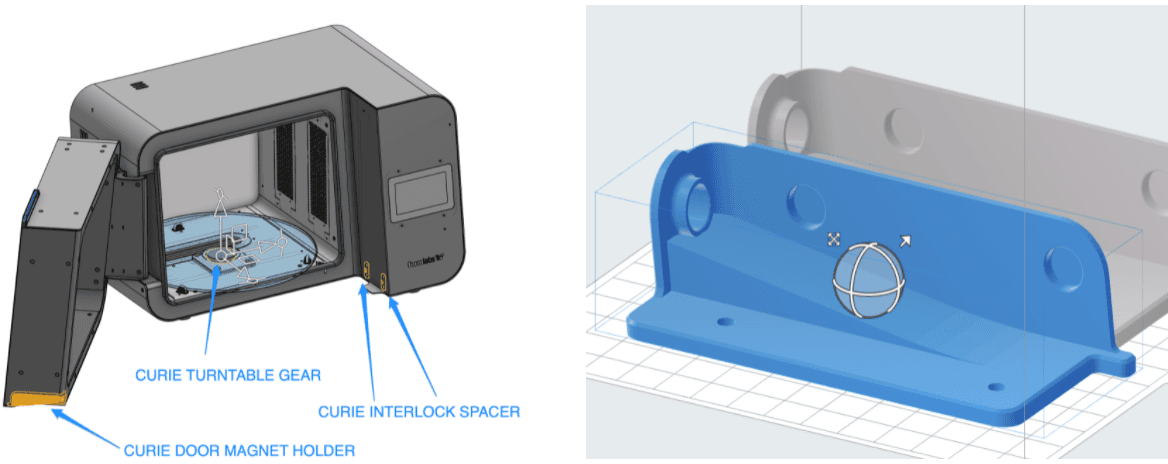
Links: die drei auf dem Fuse 1 gedruckten Komponenten des Form Cure L – rechts: eine Nachaufnahme der Magnethalter
Die Herstellung von Teilen für den Form Wash L auf dem Fuse 1
Die beiden Pumpenklemmen fixieren die batteriebetriebene Lösungsmittelpumpe im Staufach des Form Wash L. Sie musste speziell auf die Größe der Pumpe angepasst werden und wurden ebenso für höchste Materialeffizienz entworfen. Das einzigartige Design mit dem Spiralmuster an der Seite bedingt, dass sie gar nicht traditionell hergestellt werden können. Im Laufe des iterativen Prozesses konnte das Team Designanpassungen vornehmen, ohne sich um neue Werkzeugbestückung zu kümmern. Da das Teil während der Entwicklung komplett überarbeitet wurde, entlastete dies das Budget.
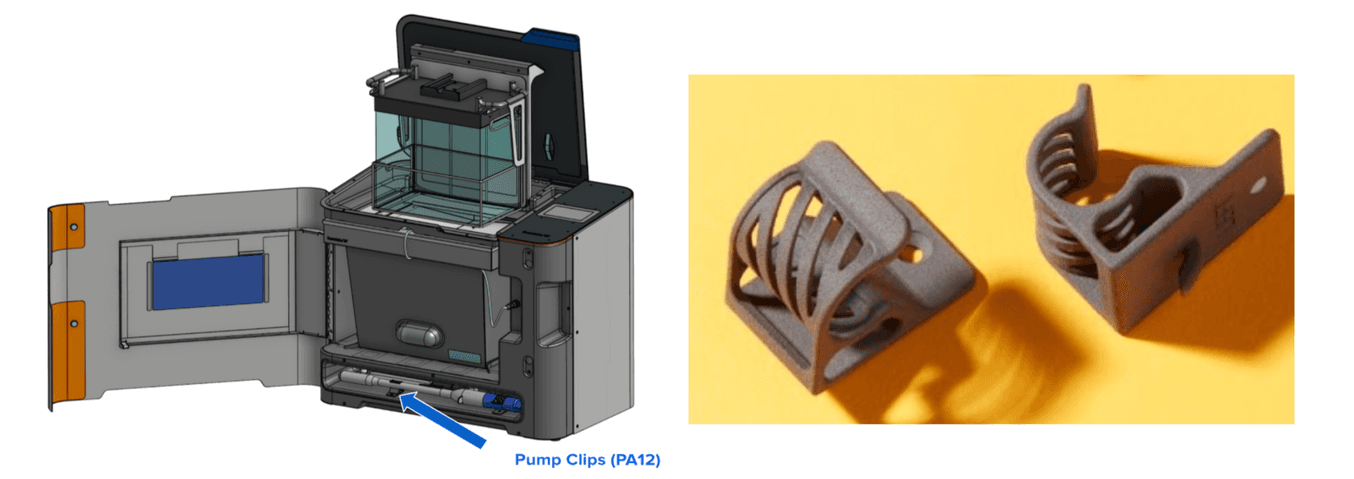
Im Form Wash L hält ein Magnet den Lösungsmittelsensor im Waschbehälter an Ort und Stelle. Um diesen Magnet vor Rost und Kratzern zu schützen, entwarf das Ingenieurteam eine kleine Magnetabdeckung. Der Druck dieser Abdeckung für die ersten paar Hundert Geräte war eine Übergangslösung. Heute wird das Teil mithilfe von Spritzguss produziert. Doch in Anbetracht der langen Lieferzeiten war der Druck auf dem Fuse 1 zu diesem Zeitpunkt die sinnvollste Lösung. Dabei konnte dieses kleine Teil leicht in den Freiräumen anderer Druckteile untergebracht werden – mit praktischer Hilfe des verbesserten Packalgorithmus des Fuse 1.
Enge Zeitpläne, unterbrochene Lieferketten
Der Produktionsplan des Form Wash L und Form Cure L überlappte mit der COVID-19-Pandemie sowie mit den Beeinträchtigungen der Lieferkette. So hatte das Team Probleme, an Materialien zu kommen und sich mit den Vertragsherstellern abzusprechen.
Liu und der Rest des Ingenieurteams bei Formlabs haben über die Jahre Beziehungen zu einer Reihe von Anbietern aufgebaut. So findet sich normalerweise zuverlässig ein Händler für die benötigten Teile. Doch in Anbetracht überlasteter Häfen, geschlossener Fabriken seitens der chinesischen Zulieferer, Gewerkschaftsstreiks bei den Transportunternehmen und Personalausfällen durch COVID-19 versiegten alle Quellen der Prototypmaterialien.
„Betriebsinterne Drucker machen uns äußerst flexibel, selbst wenn es um Muster geht, die wir letztendlich mit traditionellen Verfahren herstellen. Dabei verwenden wir 3D-gedruckte Teile als Übergangslösung, um unsere Zeit effektiv zu nutzen.“
Megan Liu, Formlabs Global Sourcing
Aufgrund dieser Materialverzögerungen wurde der Zeitplan des Teams des Form Wash L und Form Cure L drastisch gestaucht. Anstatt der angestrebten sechs Wochen für die Produktion von 600 Geräten hatte man nun nur die Hälfte der Zeit. Jede Woche mussten 200 Geräte vom Band laufen, um die Frist zu erfüllen. Formlabs' Druckerfarm in der Materialproduktion in Ohio hatte nicht die nötigen Kapazitäten. Deshalb druckte das Ingenieurteam die Teile im Hauptquartier in Somerville.
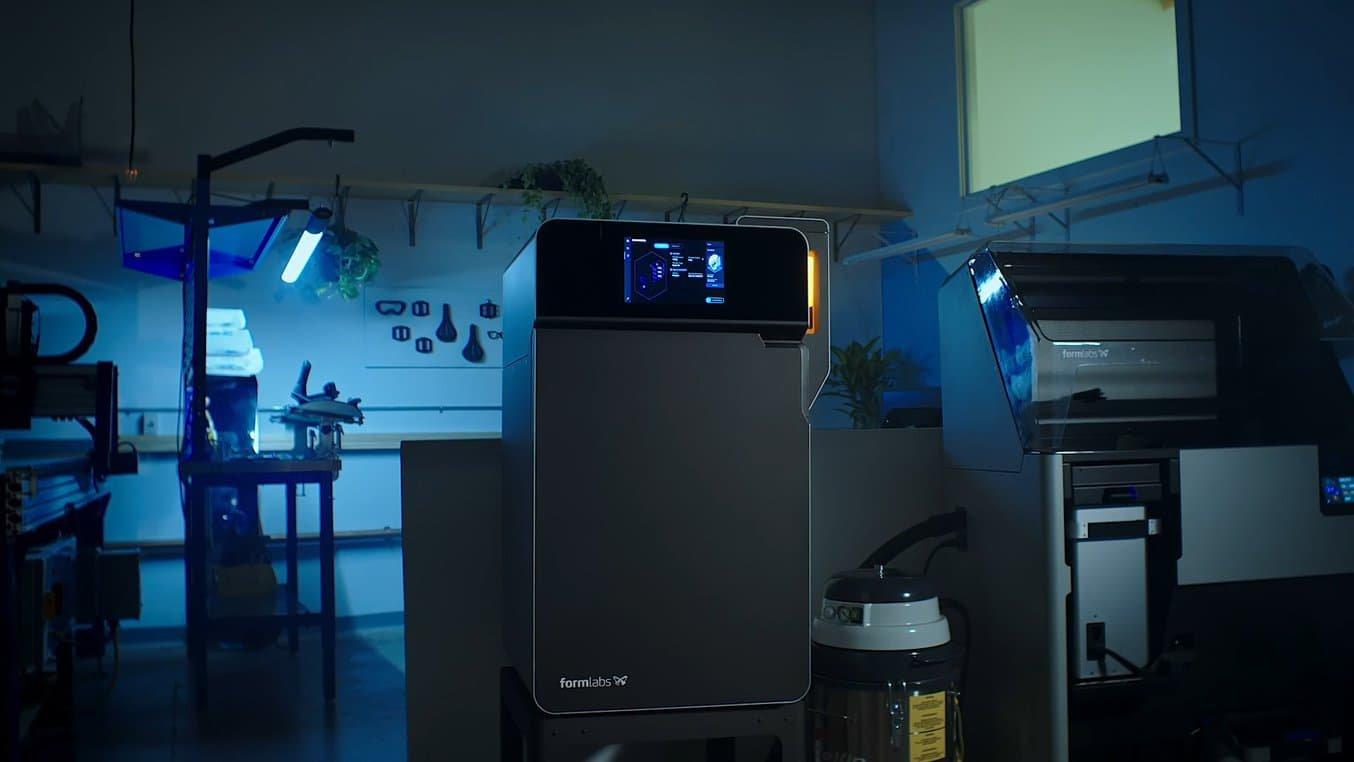
„Mit diesen Druckern konnten wir die Kapazität sofort verdoppeln. Hätten wir mit Outsourcing gearbeitet und der Dienstleister müsste seine Türen schließen, dann hätten wir das Spitzgusswerkzeug nicht einfach an einen anderen Dienstleister schicken können. Doch mithilfe der Drucker konnten wir die Produktion dezentralisieren und sofort die Kapazitäten erhöhen, um im Zeitplan zu bleiben“, erklärt Liu.
Übergang zum Spritzguss: wann und weshalb?
Once the team successfully produced those 600 units, they had the opportunity to assess their options for full production with established timelines and demand. Though some parts, like both pump clips, the interlock spacers, and turntable gear still make sense to produce on the Fuse 1, other parts, like the magnet cover, have been moved to an injection molding workflow.
Nach der erfolgreichen Produktion der angesprochenen 600 Geräte konnte das Team die Optionen zur vollen Produktion evaluieren, anhand etablierter Fristen und bestehender Nachfrage. Die beiden Pumpenklemmen, die Abstandhalter der Verriegelung und das Drehtellergetrie – die Produktion dieser Teile auf dem Fuse 1 ergibt immer noch Sinn. Andere Teile wie die Magnetabdeckung wurden stattdessen zum Spritzguss überführt.
Wir werfen einen Blick auf zwei dieser Teile, das Getriebeteil und die Magnetabdeckung, anhand welcher wir die Entscheidungsfindung offenlegen – wann ist es sinnvoll, vom direkten SLS-Druck zum traditionellen Spritzguss überzugehen.
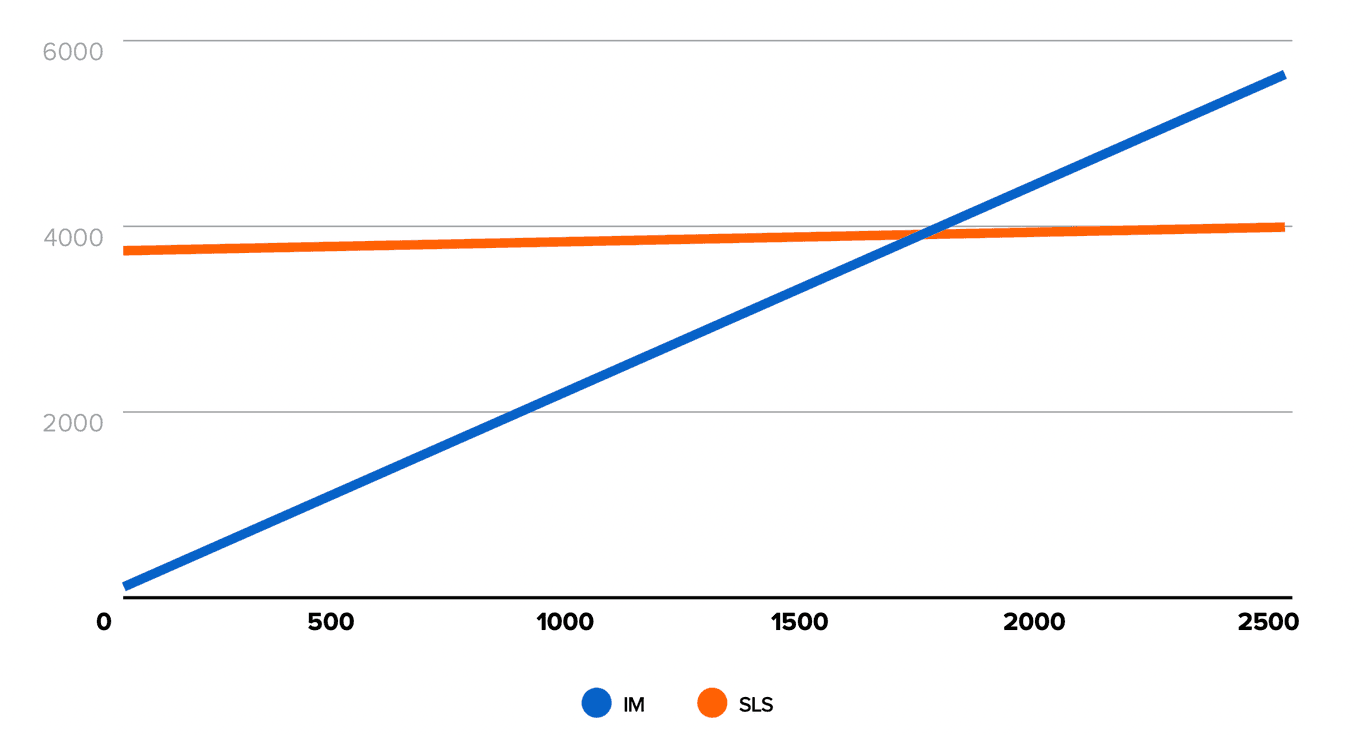
Teil 2: Drehtellergetriebe
Das Teil hat in der Mitte eine angefaste Kerbe, um den Drehtellerzapfen festzuhalten und genügend Kraft für die Drehung des Drehtellers des Form Cure L zu erzeugen.
Eine Spritzgussform für dieses Design würde zwei Teile erfordern, und eine zweiteilige Form ist teurer. Der Kostenvoranschlag des Spritzgussunternehmens belief sich auf 10 000 USD.
SLS | SG pro Teil | Kosten der SG-Form | |
---|---|---|---|
Drehtellergetriebe | 3,50 USD | 2,20 USD | 3700 USD |
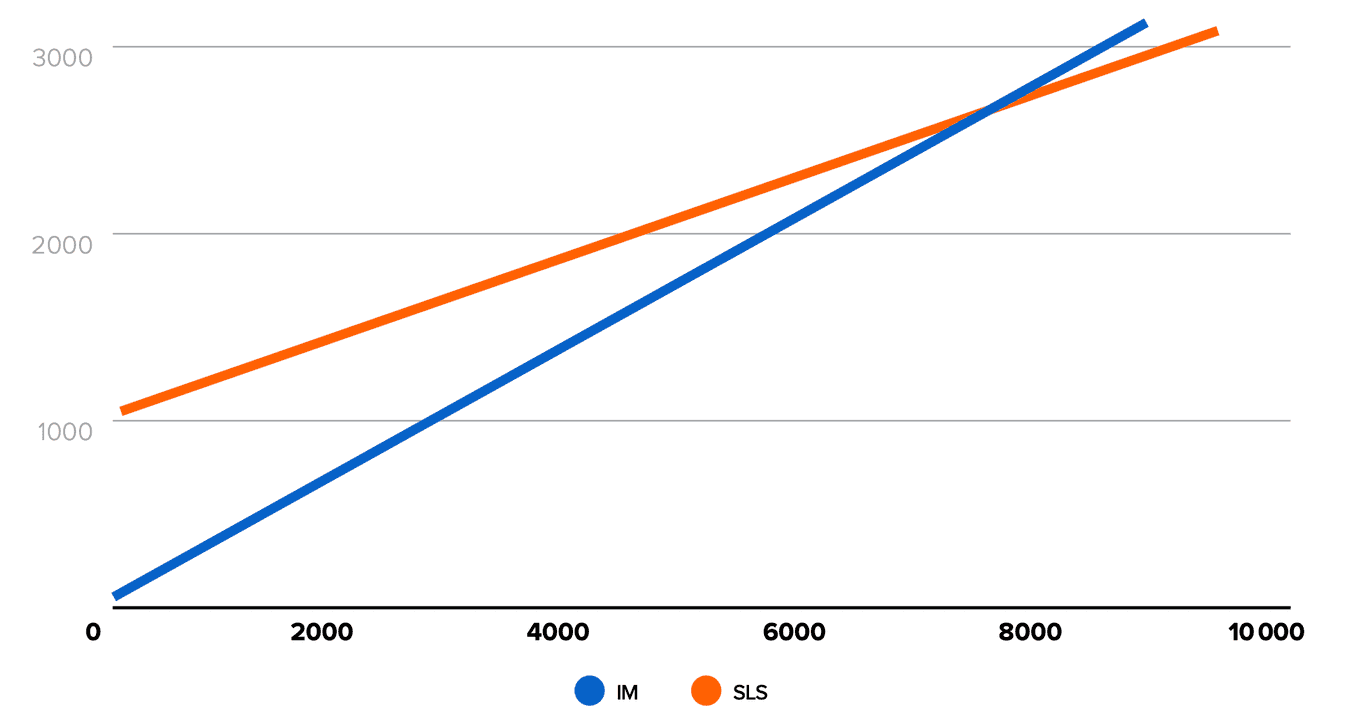
Beim SLS-3D-Druck konnte das Team das Drehtellergetriebe als einzelnes Teil gestalten. Die Kosten pro Teil betrugen nur 3,50 USD, d. h. Spritzgussteile wären erst ab ca. 8000 Stück rentabel. Das Team druckte das Teil also auf dem Fuse 1 und sparte so Tausende von Dollar, was die Kosten des Endprodukts senkt. Bis dieses Produktionsniveau erreicht wird, hat das Beschaffungsteam noch genügend Zeit, vorauszuplanen, Formwerkzeuge zu bestellen und zum Spritzguss überzugehen, sobald dies wirtschaftlicher werden sollte. Der SLS-3D-Druck hingegen beschleunigte den Weg zur Veröffentlichung und erlaubte eine Fokussierung auf andere Bereiche des Produkts.
Kann man Spritzguss durch 3D-Druck ersetzen?
Die Druckerflotte der Fuse 1 ist eine Ergänzung der Lieferkette. Obgleich sie bei einigen Teilen die traditionellen Verfahren ersetzt hat, sind Werkzeugbestückung, Guss, Formenbau und CNC-Bearbeitung immer noch notwendige Bestandteile des Lebenszyklus eines Produkts. Die Verfügbarkeit von 3D-Druckern in Industriequalität gibt Herstellern jedoch mehr Kontrolle über den Prozess und bietet eine Absicherung gegen externe Variablen wie z. B. Verzögerungen bei den Rohstoffen oder lange Durchlaufzeiten bei der Werkzeugbestückung.
Das Ingenieurteam von Formlabs konnte dank der SLS-Drucker zwei Produkte mit engen Fristen pünktlich auf den Markt bringen und gleichzeitig die Hürden der COVID-19-Pandemie und der überlasteten Lieferketten überwinden. Die Endprodukte seitens Form Wash L und Form Cure L haben jeweils mehrere Teile, die auf Formlabs' hauseigener Technologie gedruckt wurden. Das beweist, dass der Fuse 1 gleichzeitig eine Entwicklungs- und Produktionslösung ist. In unserem Whitepaper SLS-3D-Druck oder Spritzguss werfen wir einen detaillierten Blick auf die möglichen Endanwendungen des SLS-Druckers Fuse 1, von Ersatzteilen über individuelle Prothesen bis zum Zubehörmarkt von Motorteilen.