Eine der größten Herausforderungen bei der fortschrittlichen Fertigung ist es, sicherzustellen, dass komplexe Strukturen in Robotikanwendungen, Digitally Assisted Assembly und Zerspanungstechnologien perfekt montiert werden. Die Integrated Manufacturing Group mit Sitz in der 43 Millionen Pfund teuren Factory 2050 des Advanced Manufacturing Research Centre (AMRC) der University of Sheffield ist eine Forschungsgruppe, die mit Partnern aus der Industrie zusammenarbeitet, um diese fortschrittlichen Technologien zusammenzubringen und integrierte Systeme zu entwickeln.
Die Forschungsgruppe hat kürzlich an einem Projekt für Airbus, Europas größtes Luft- und Raumfahrtunternehmen, gearbeitet, bei dem Bohr- und Zerspanungsarbeiten mit engen Toleranzen an Kohlefaser-, Aluminium- und Titanbauteilen durchgeführt wurden.
In Anbetracht der strengen Anforderungen der Luft- und Raumfahrtindustrie musste eine Querkontamination zwischen den Bohrungen während dieser Versuche unbedingt vermieden werden. Kurz nach Beginn des Projekts stellte das Team fest, dass die geplante Lösung das Problem nicht beheben würde – es drohte eine Verzögerung von mehreren Wochen, wenn Ersatzteile zerspant oder spritzgegossen werden müssten.
Erfahren Sie von George Sleath, einem Projektingenieur der Integrated Manufacturing Group, wie das Team mithilfe von 3D-Druck schnell 500 hochpräzise Bohrkappen fertigte und so die Durchlaufzeit von mehreren Wochen auf nur drei Tage reduzierte.
Sleath und das Ingenieurteam arbeiteten an der frei zugänglichen additiven Fertigungsstation des AMRC, um die erforderlichen Teile herzustellen. Lesen Sie unsere Fallstudie, um zu erfahren, wie der freie Zugang zu 3D-Druck hunderten von Ingenieuren an einem Standort helfen kann.
Versuche zu verschiedenen Methoden gegen Querkontamination
„Eine der Hauptanforderungen beim Bohrprozess war es, dass es zu keiner Kontamination der Bohrungen kommen würde. Wir mussten also nach dem Bohren eines Lochs das erste Loch abdecken, bevor wir zum nächsten gingen, damit die entstandenen Späne die zweite Bohrung nicht verunreinigten. Als wir feststellten, dass wir diese spezifische Anforderung für eine Bohrkappe hatten, hatten wir nur wenig Zeit, um die Lösung bereitzustellen“, so Sleath.
Die Ingenieure versuchten es zunächst mit einem Aluminiumteil mit einem kleinen O-Ring aus Gummi, doch das löste das Problem nicht befriedigend. Das gesamte Projekt wurde aufgehalten, was aufgrund des engen Terminplans zur Fertigstellung des Projekts nicht akzeptabel war.
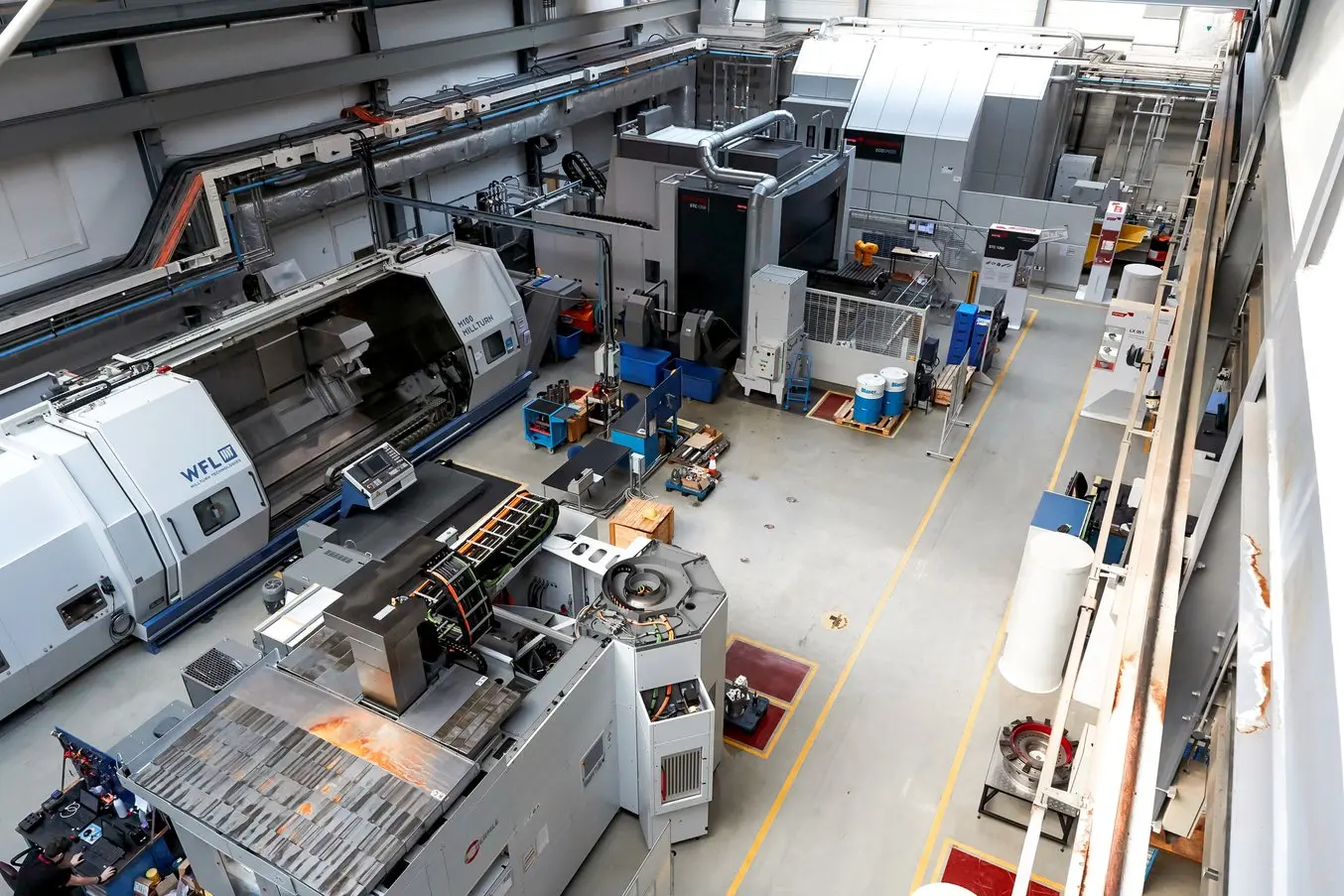
Das Team dachte sich dann ein neues Design aus: eine kleine Scheibe mit einer umlaufenden Nut für einen O-Ring. Für das Teil galten ziemlich strenge Toleranzanforderungen; wenn die Nut zu groß wäre, würde der Ring auf die Seite des Teils rutschen, wodurch nicht der O-Ring, sondern der Kunststoff die Dichtung bilden würde. Der annehmbare Toleranzbereich war die Hälfte der Dicke des O-Rings, lag also im Bereich von einem halben Millimeter.
Die Variationen der Teile sorgten ebenfalls für Komplikationen bei der Herstellung. „Wir benötigten verschiedene Variationen, da die Bohrungen verschiedene Größen hatten. Dadurch benötigten wir verschiedene Bohrkappen. Vom Gesichtspunkt des virtuellen Designs aus dauert es nicht lange, nur eine Abmessung zu verändern, aber wenn die Teile spritzgegossen werden müssen, muss für jedes einzelne eine neue Form hergestellt werden“, sagt Sleath.
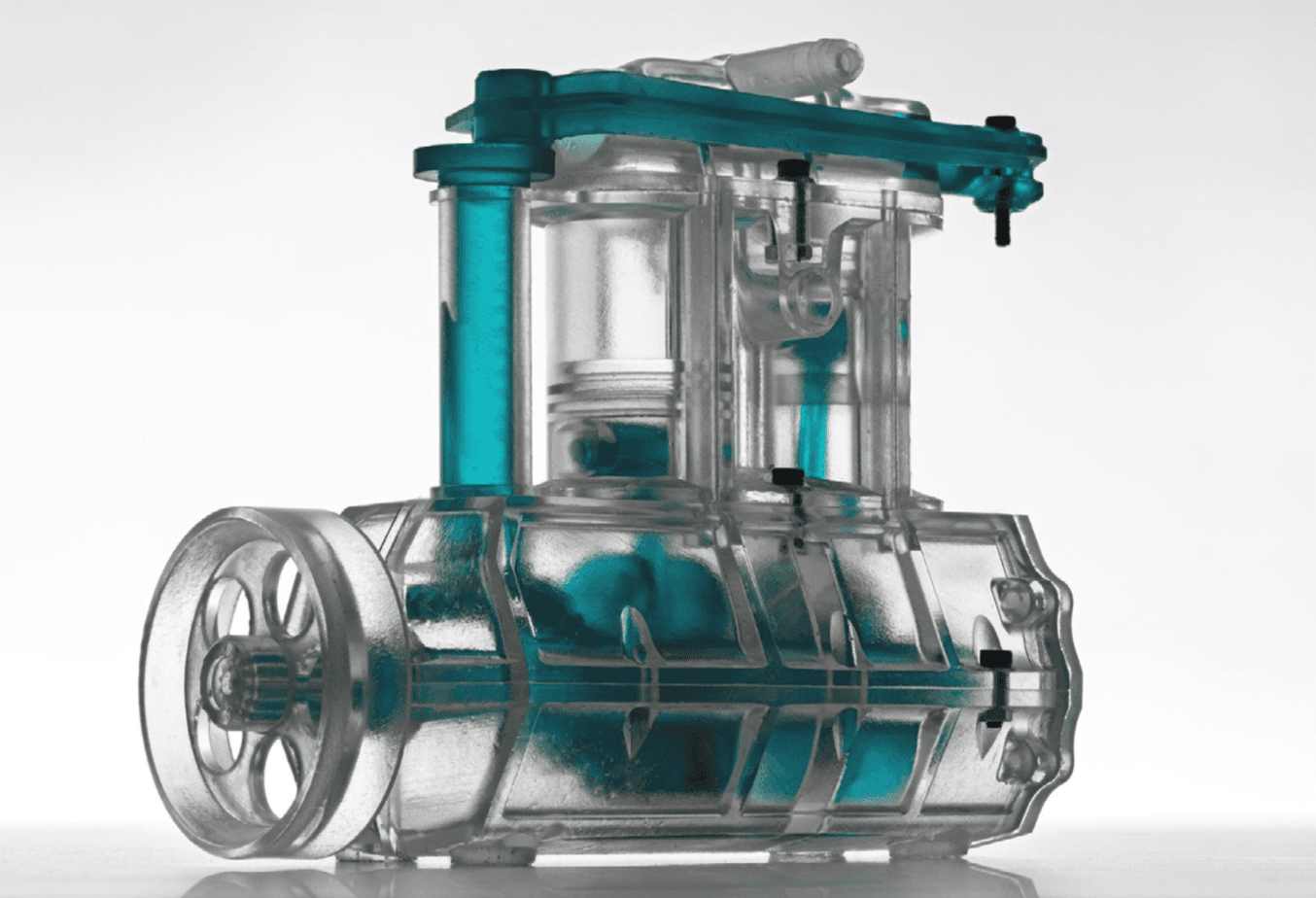
White Paper: Engineering Fit
Laden Sie unser Whitepaper herunter, um mehr über Toleranzen und Passungen im 3D-Druckdesign von funktionalen 3D-gedruckten Baugruppen zu erfahren.
White Paper herunterladen
3D-Druck von 500 Schutzkappen in zwei Tagen
Das Team benötigte etwa 500 dieser kleinen Kappen in einem Zeitraum von zehn Tagen, wodurch praktisch alle anderen Fertigungsoptionen als der 3D-Druck wegfielen.
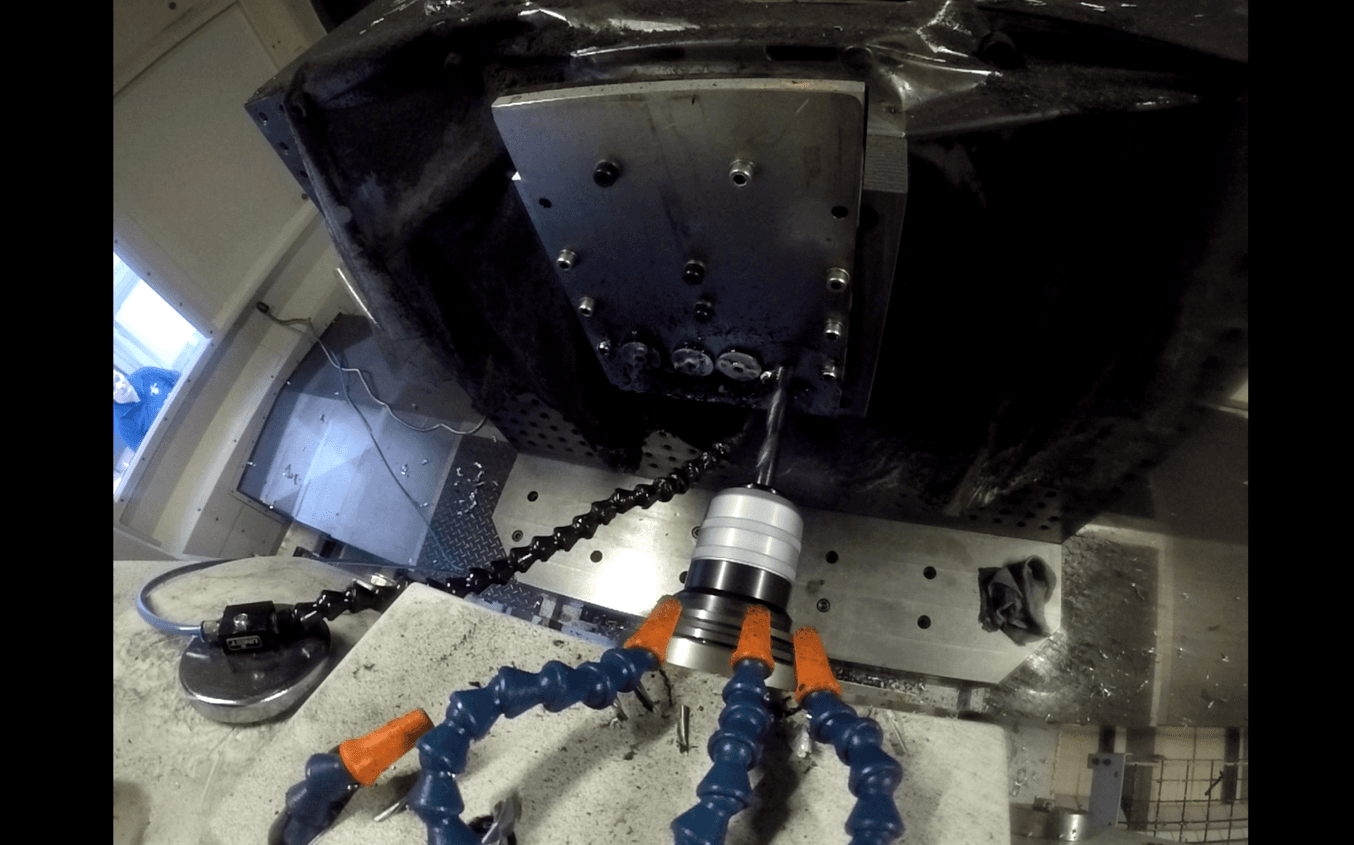
Da sich Sleath zu diesem Zeitpunkt über die internen Kapazitäten nicht sicher war, forderte er zunächst Angebote von drei externen Druckdienstleistern an. Doch die Preise waren exorbitant mit Hinblick auf die Rolle der Teile im Projekt.
„Ich sprach dann mit Mark Cocking in unserer Design and Prototyping Group und fragte nach, ob wir das nicht in unserem Betrieb herstellen könnten. Ich habe dann 24 Stunden lang nichts von ihm gehört, bis er mir dann sagte ‚Ja, wir haben die Hälfte schon gedruckt.‘ 250 dieser Bohrkappen in 24 Stunden, das war ein beeindruckender Durchsatz“, so Sleath weiter.
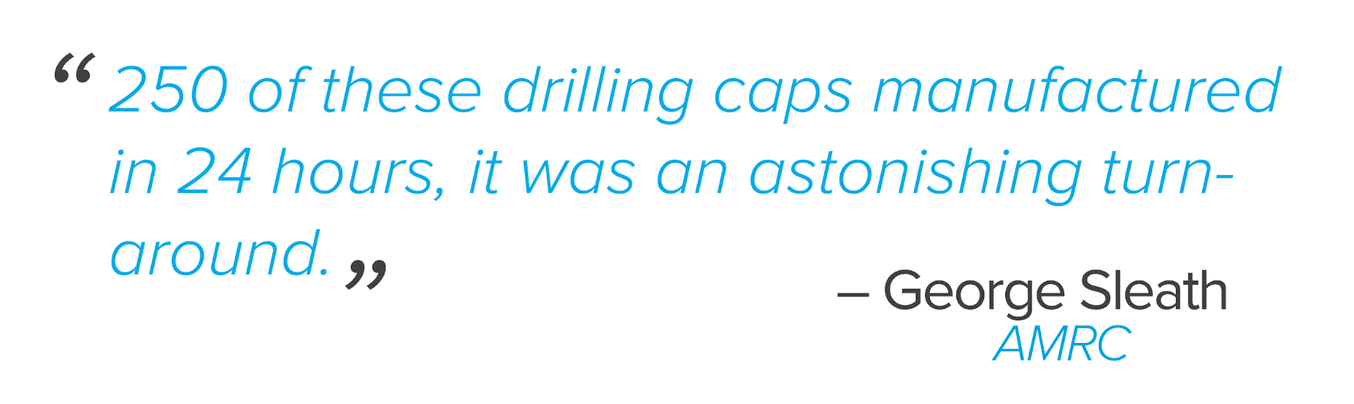
Schließlich schaffte es Cocking, alle Teile innerhalb von zwei Tagen herzustellen.
„Das bedeutete nicht nur, dass wir die Teile schneller hatten und mit ihnen arbeiten konnten, wir konnten uns auch auf andere Dinge konzentrieren und mussten uns keine Gedanken darüber machen, wann diese Teile endlich eintreffen würden“, erzählt George Sleath.
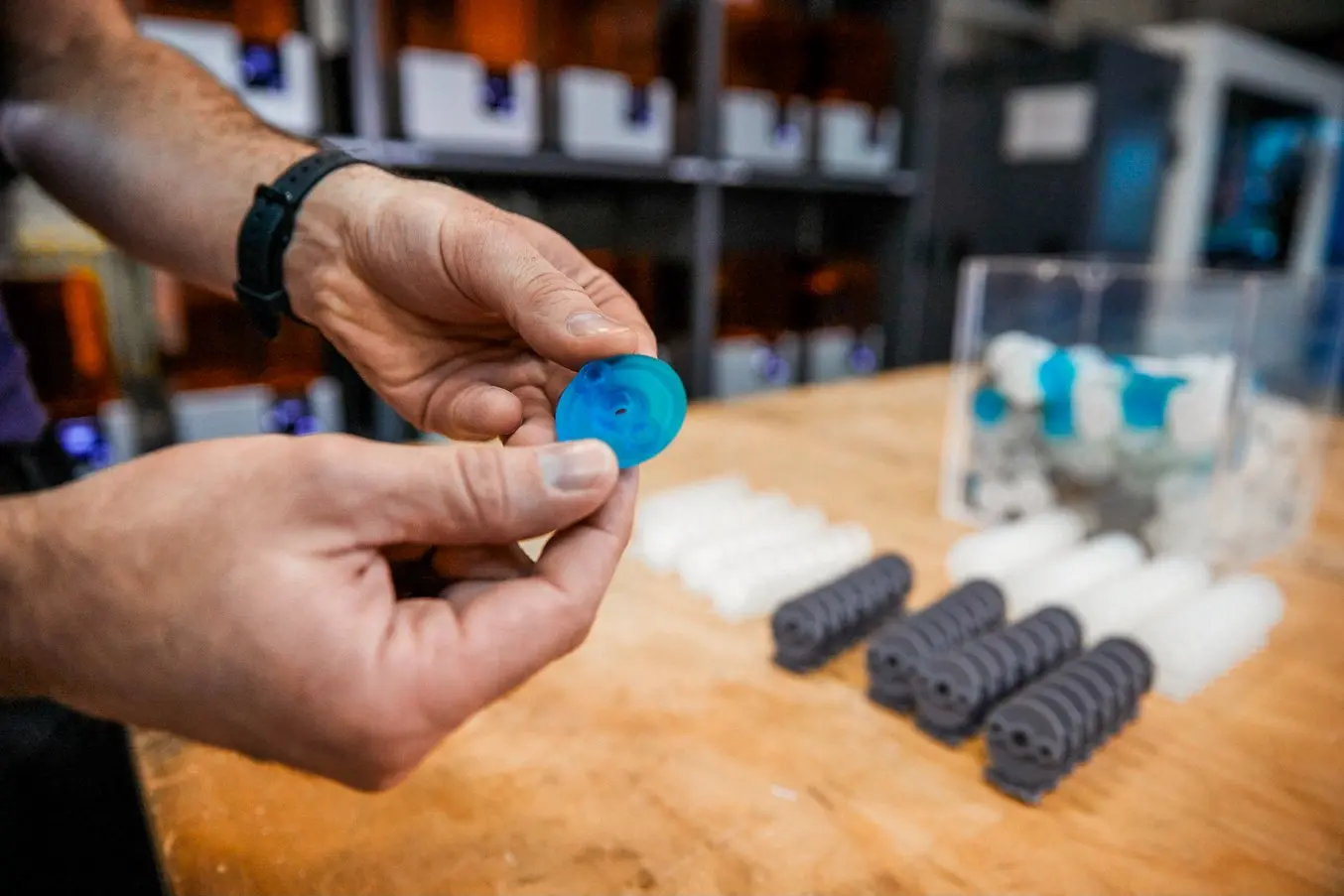
Eigene 3D-Druckstation bietet Flexibilität und Platz für Iterationen
Mit 3D-Druck konnten die Ingenieure ebenfalls eine Geometrie zu dem Teil hinzufügen, die sie auch für ein Werkzeug druckten. So konnten die Kappen schnell und einfach installiert werden.
„Das Feedback, das ich von den Arbeitern erhielt, die sie installierten, war fantastisch. Fast alle Teile funktionierten genauso wie vorgesehen und keines ging im Betrieb kaputt“, berichtet Sleath.
Neben den schnellen Durchlaufzeiten und den geringen Kosten war ein zusätzlicher wichtiger Vorteil beim 3D-Druck vor Ort die Flexibilität.
„Hätte das Design nicht funktioniert, als wir es getestet haben, hätten wir das Feedback schnell an den Designprozess geben und die Dinge ändern können. Wir hätten nicht erst das erste Design an einen Dienstleister gesendet und dann erkannt, dass eine geringfügige Änderung nötig ist, wenn wir alle 500 Teile nach einigen Wochen zurückerhalten hätten“, so Sleath.
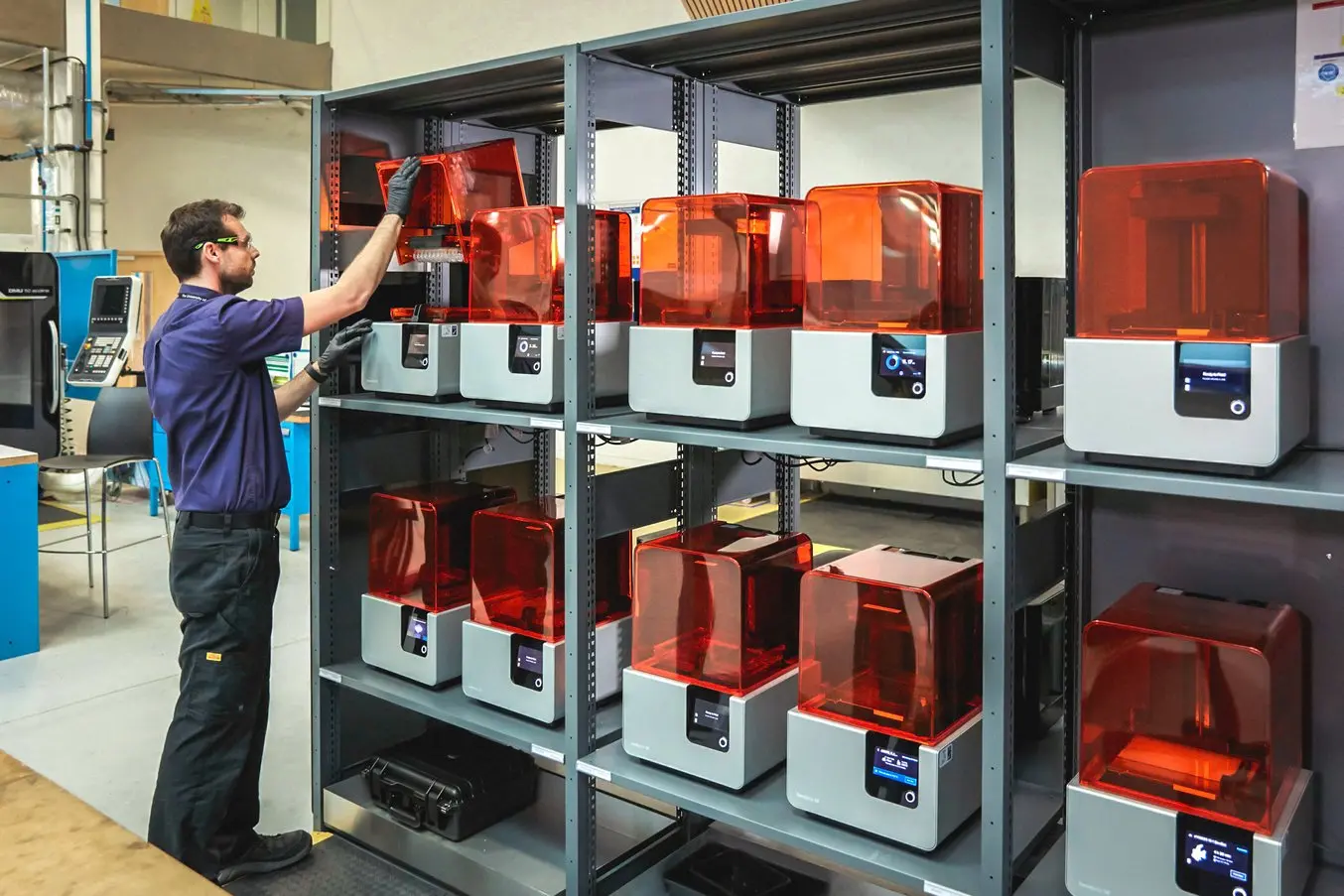
Erfahren Sie, wie eine 3D-Druckstation hunderte von Ingenieuren im AMRC unterstützt
„Ich nutze gerne 3D-Druck, um Designs schnell zu iterieren. Ich stelle ein Teil auf dem 3D-Drucker her, um zu sehen, wie es in der Praxis funktioniert, und sende dann schnell ein neues Design an den Drucker. Man kann dank der Geschwindigkeit und der niedrigen Kosten manchmal zwei oder drei Designs am Tag ausprobieren. Mit dem neuen Open-Access-Projekt de AMRC, auf das der ganze Standort hinarbeitet, wird wohl jeder hier 3D-Druck immer mehr einsetzen“, meint Sleath.
Erfahren Sie mehr über die 3D-Druckstation des AMRC und über andere Anwendungen wie temperaturbeständige Sensorhalterungen für das Schweißen, hochkomplexe Halterungen für einen Robotergreifer, und maßgefertigte Faserwickelrollen für die Herstellung von Verbundwerkstoffen.
Möchten Sie mehr über die Drucker und die Technologie hinter der 3D-Druckstation des AMRC erfahren? Lernen Sie den Form 3, den großformatigen Form 3L, und Bibliothek an technischen Kunstharzen von Formlabs für Ihr eigenes Projekt kennen, oder fordern Sie einen kostenlosen Probedruck an, um sich selbst einen Eindruck von den Materialien zu verschaffen.
Kostenlosen Probedruck anfordern