Artus3D in Ridderkerk, Niederlande, bietet der Orthopädietechnik eine Komplettlösung zum Erstellen von Handorthesen, bestehend aus Software wie auch der Eigenfertigung mit verschiedenen Materialien. Artus3D verfügt über sieben Jahre Erfahrung im Bereich der Orthetik und begann zunächst mit ausgelagertem 3D-Druck. Aber es war schwierig, Dienstleister zu finden, die mit TPU druckten, und Artus3D stieß immer wieder auf Hürden in Bezug auf Zuverlässigkeit und Lieferzeiten – bis das Team letztes Jahr den Fuse 1+ 30W für selektives Lasersintern (SLS-3D-Druck) und TPU 90A Powder entdeckte.
Durch die Verlagerung des SLS-3D-Drucks ins eigene Haus hat Artus3D mehr Kontrolle über seine Fertigung gewonnen und spart sowohl Zeit als auch Ressourcen ein. Wir haben uns mit Lars Broxterman, Vertriebs- und Produktionsleiter bei Artus3D, getroffen, um mehr über den Übergang zur betriebsinternen Orthesenfertigung mit TPU zu erfahren.
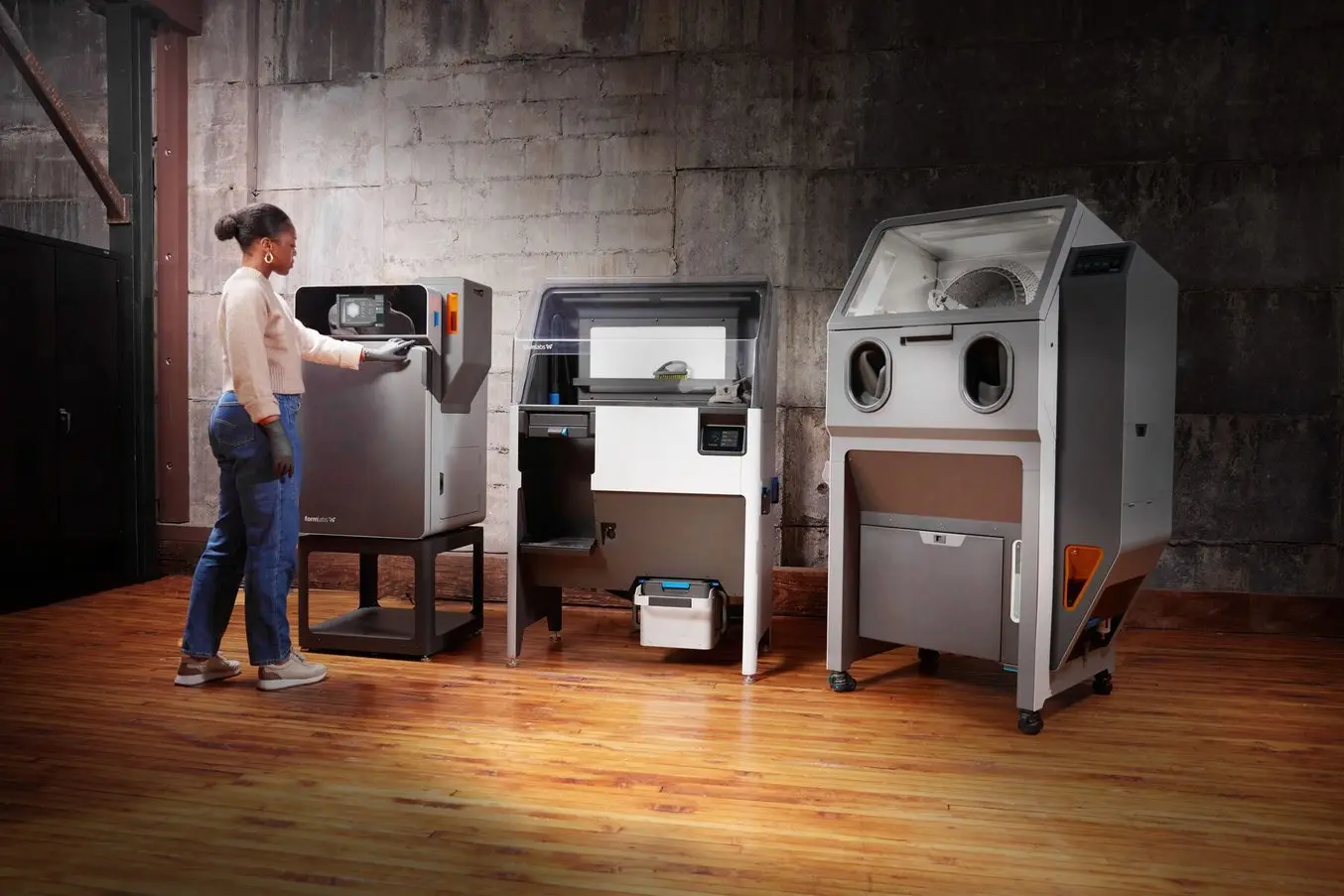
Arbeitsablauf mit dem Fuse 1+ 30W
Der Fuse 1+ 30W ist unser kompakter SLS-3D-Drucker für maximalen Durchsatz bei minimalem Abfall. Er ermöglicht Ihnen beispiellose Druckgeschwindigkeiten und Hochleistungsmaterialien für eine rekordschnelle Produktion im eigenen Betrieb.
Intuitive digitale Arbeitsabläufe
Artus3D begann als Software-Lösung für die Herstellung von orthopädischen Hilfsmitteln durch technologische Innovationen, die Anwender*innen schnell, intuitiv und benutzerfreundlich vom digitalen Scan bis zum 3D-gedruckten Produkt führte.
Um die Zugänglichkeit und Integration dieser digitalen Arbeitsabläufe zu fördern, hat Artus3D den Prozess so einfach wie möglich gestaltet. Für den Einstieg, so Broxterman, kann man „jeden beliebigen Scanner verwenden. Sie laden den groben Scan einfach in die Software hoch, die Software erkennt automatisch, ob es links oder rechts ist, wo oben und wo unten ist, und schneidet die Teile ab, die sie nicht braucht. Die Software füllt die Lücken automatisch aus, und von da an haben Sie die volle Kontrolle über Ihr Design.“
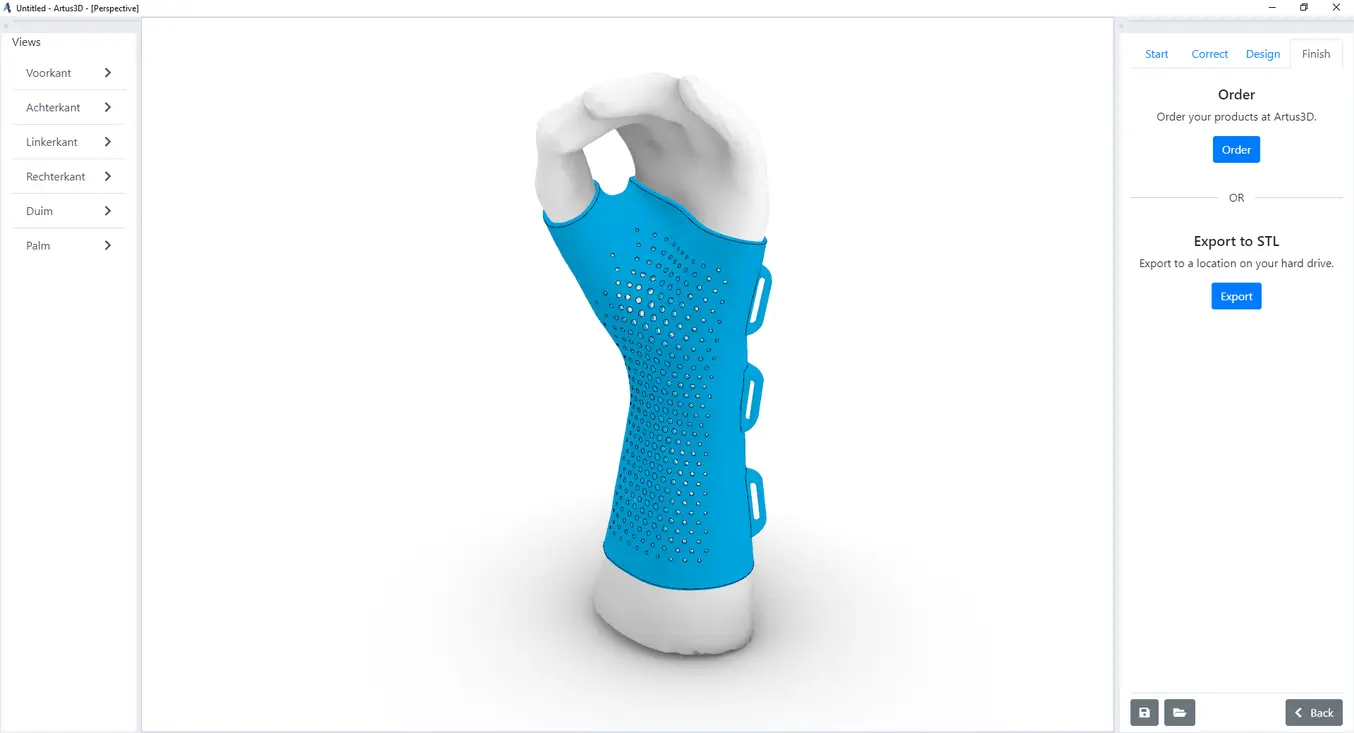
Wenn sie fertig entworfen ist, kann die Orthese bei Artus3D bestellt oder als STL-Datei zum Druck exportiert werden.
Die Software generiert automatisch einen Designvorschlag für die Handorthese, welcher danach angepasst werden kann. Dann, erklärt Broxterman, „wählen Sie das Material aus, mit dem Sie drucken möchten. Einige Einstellungen sind voreingestellt. Die Software zeigt in einer Vorschau an, wie die Orthese ihrer Meinung nach aussehen sollte. Dann können Sie alle angezeigten Schnittlinien anpassen. Sie können auch die Dicke manuell einstellen.“
Laut Broxtermann ist das größte Problem für Orthopädietechniker*innen das Design des Produkts. Deshalb stand für Artus3D die Benutzerfreundlichkeit im Vordergrund. Das Ergebnis ist Broxtermann zufolge eine Software, „in der Endverbraucher oder orthopädische CPOs mit grundlegenden Kenntnissen des 3D-Drucks ihre eigenen Handorthesen entwerfen können, was den Einstieg und die Verwendung unserer Software einfach macht.“
Nach dem Design der Orthese können die Nutzer von Artus3D auf ihren eigenen Druckern drucken oder eine 3D-gedruckte Orthese direkt über die Software bestellen.
Die Vorteile des betriebsinternen 3D-Drucks
Anfangs lagerte Artus3D die 3D-Druck-Fertigung der Orthesen, die über ihre Software bestellt wurden, an Dienstleister aus. Dabei stieß das Team jedoch immer wieder auf Hürden, darunter die Zuverlässigkeit und die langen Lieferzeiten. Aber, wie Broxterman erzählt: „Wir konnten nicht viel dagegen tun, weil es nicht viele Unternehmen gab, die mit TPU druckten. Also mussten wir uns damit abfinden.“ Artus3D druckte fast 2000 Orthesen pro Jahr aus verschiedenen Materialien und brauchte eine Alternative zum Outsourcing, die mit der Nachfrage Schritt halten konnte.
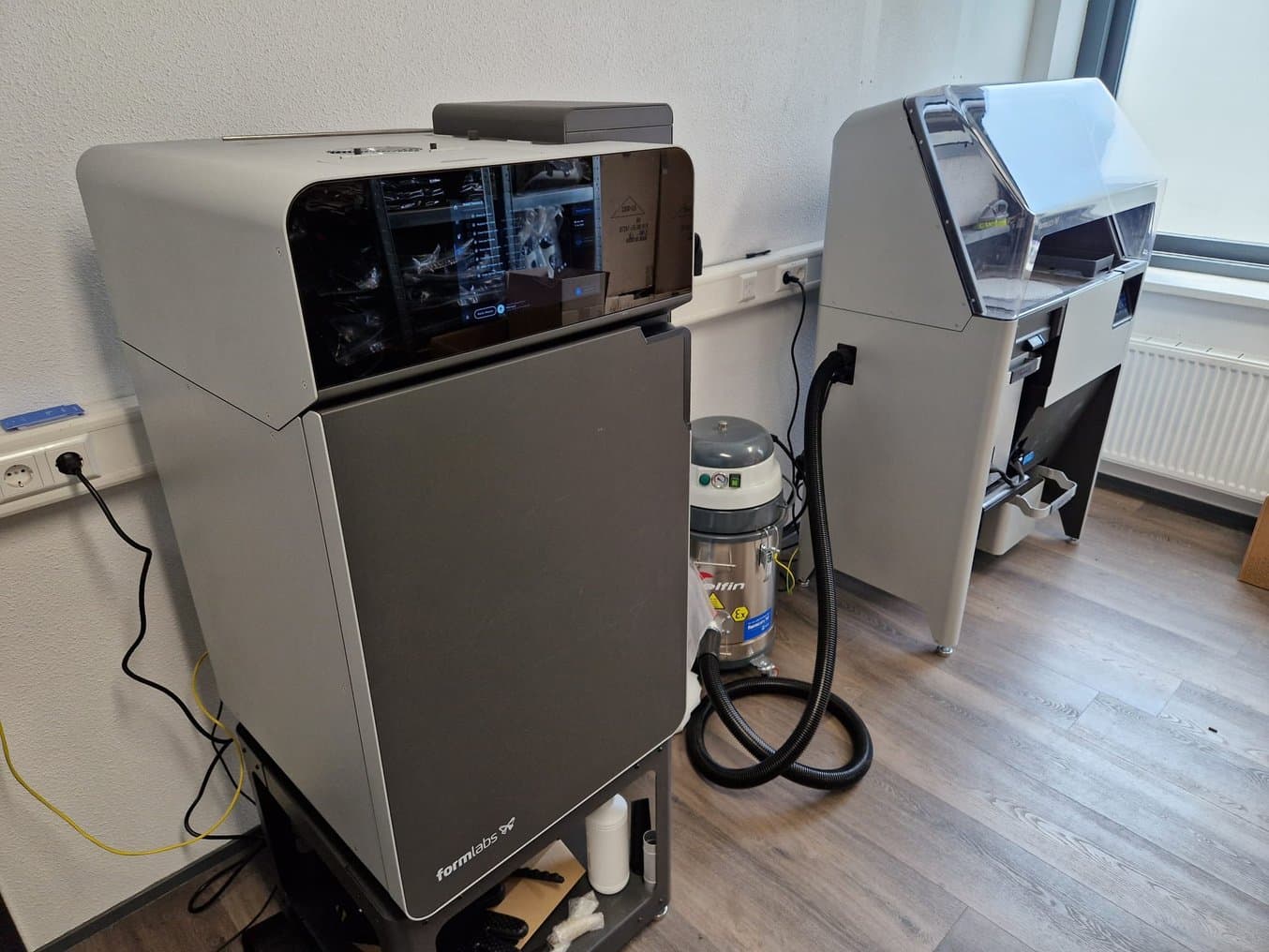
TPU-Orthesen werden betriebsintern auf dem Fuse 1+ 30W (links) gedruckt. Der Fuse Sift (rechts) ist die Station für die Pulververwaltung und der Fuse Blast (nicht abgebildet) wird für die automatische Reinigung und Nachbearbeitung verwendet.
Mit betriebsinternem 3D-Druck hätte Artus3D volle Kontrolle über seine Fertigung, aber sie brauchten einen 3D-Drucker, der sowohl zu ihrem Budget passte, mit der Nachfrage Schritt halten konnte als auch TPU druckte. Im Jahr 2023 arbeitete das Team mit dem Formlabs-Partner Visiativ Benelux zusammen, der ihnen den Fuse 1+ 30W vorstellte. Dieser Drucker gab Artus3D die Möglichkeit, den 3D-Druck von TPU-Orthesen endlich im eigenen Betrieb umzusetzen.
„Die Kontrolle über den gesamten Prozess zu behalten ist für uns der größte Vorteil, aber auch die Geschwindigkeit. Wenn wir genügend Bestellungen erhalten, können wir sie heute an den Drucker schicken und morgen versenden, das ist für uns eine echte Revolution.“
Lars Broxterman, Leiter von Vertrieb und Fertigung bei Artus3D
Broxterman stellte fest, dass der betriebsinterne Druck mit dem Fuse-Ecosystem nicht nur mehr Kontrolle über die Lieferzeiten bot, sondern auch die Fertigung beschleunigte. Beim Outsourcing des Drucks, so Broxterman, hatten sie „Lieferzeiten von etwa zwei Wochen festgelegt, aber jetzt können wir problemlos auf eine Woche heruntergehen.“
Durch den betriebsinternen Druck hat Artus3D seine Kosten und Durchlaufzeiten verringert und gleichzeitig dafür gesorgt, dass seine Kunden dringend benötigte Orthesen schneller erhalten.
Nach dem 3D-Druck mit dem Fuse 1+ 30W verwendet Artus3D den Fuse Sift für die Entnahme der Teile, die Rückgewinnung, die Aufbewahrung und das Mischen von neuem und gebrauchtem Pulver, was Abfälle minimiert. Seit kurzem verfügt das Team auch über einen Fuse Blast zum vollautomatischen Reinigen und Polieren, der mühelos saubere, glatte Teile liefert.
„Der Fuse Blast war für uns ein Wendepunkt. Er spart so viel Zeit bei der Reinigung der Teile und wir müssen nicht mehr auf sie warten.“
Lars Broxterman, Leiter von Vertrieb und Fertigung bei Artus3D
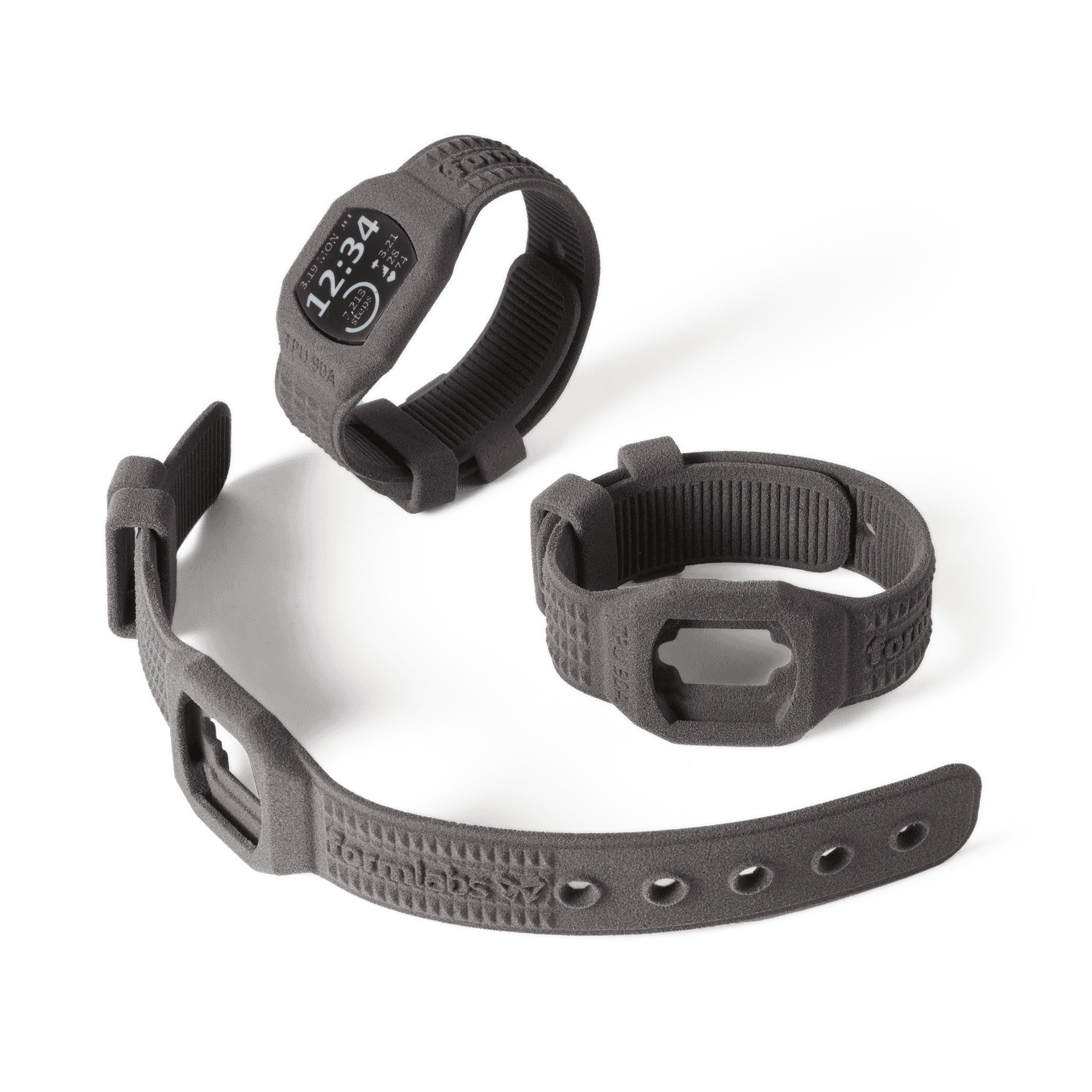
Kostenloser Probedruck
Fertigen Sie mit Leichtigkeit flexible 3D-Druckteile, die den Ansprüchen des täglichen Gebrauchs standhalten. Die hohe Bruchdehnung von TPU 90A Powder und seine überragende Reißfestigkeit machen es möglich, funktionale Prototypen oder robuste Endverbrauchsteile betriebsintern zu produzieren.
Stark, flexibel und hautverträglich
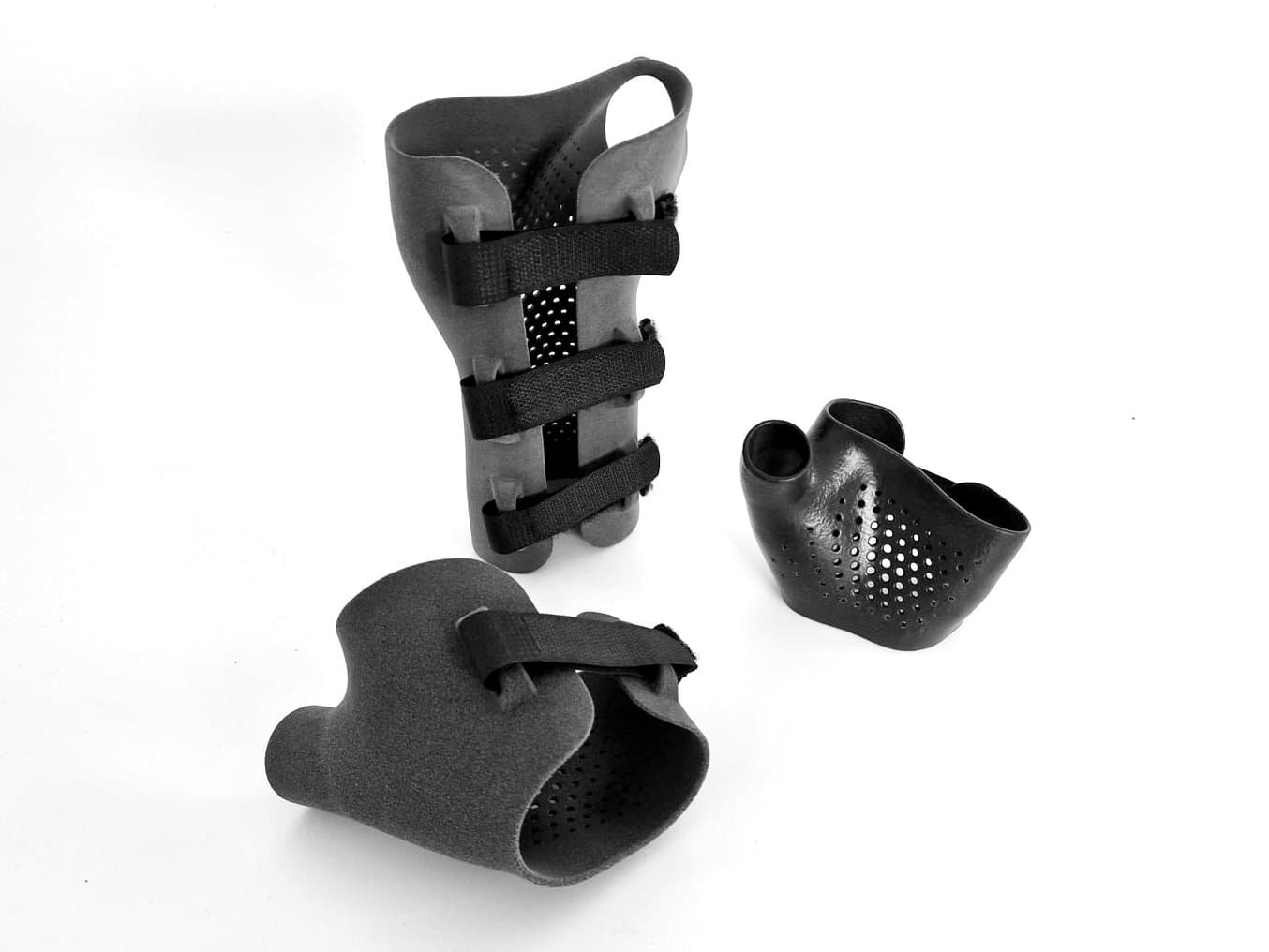
Bei der Fertigstellung der Orthesen werden Riemen hinzugefügt und sie können dampfgeglättet werden wie das Teil rechts, um eine glattere, glänzendere Oberfläche zu erreichen.
Einer der Hauptgründe, warum sich Artus3D für den Fuse 1+ 30W entschieden hat, war die Materialauswahl. Broxterman sagt: „Es gab nicht viele Unternehmen, die 3D-Druck mit TPU anboten, also mussten wir uns an ihre Zeitpläne halten. Der Wendepunkt für uns war erreicht, als das TPU-Material für den Fuse 1+ 30W auf den Markt kam.“
„Die Orthesen müssen letztendlich zwei Jahre lang getragen werden, also müssen sie auch zwei Jahre lang halten. Sie müssen flexibel und für Hautkontakt zugelassen sein. Bevor das TPU-Pulver kam, war es recht schwierig, flexible Orthesen zu drucken. TPU war ein Wendepunkt für uns.“
Lars Broxterman, Leiter von Vertrieb und Fertigung bei Artus3D
Artus3D bietet eine Reihe von Materialoptionen an, aber TPU 90A Powder für den Fuse 1+ 30W stellte einen Durchbruch dar. TPU 90A Powder ist ein zähes Elastomer mit hoher Bruchdehnung und hervorragender Reißfestigkeit, das flexible, widerstandsfähige und hautverträgliche Teile ergibt. Diese Eigenschaften machen das Material ideal für den 3D-Druck von Orthesen, die langzeitigem Gebrauch standhalten müssen und gleichzeitig Tragekomfort und Sicherheit bieten. „Wir drucken nicht alles mit dem Fuse, aber wir haben unseren Kunden das neue Material in kleinen Schritten vorgestellt. Sie sind glücklich, also sind wir auch glücklich“, berichtet Broxtermann.
Mit der Software von Artus3D und TPU 90A Powder lassen sich Orthesen in drei Stärken herstellen – dünn, normal und dick –, sodass je nach Fall individuelle Lösungen angeboten werden können. Broxterman berichtet, dass die mit TPU 90A Powder gedruckten Orthesen auch den Kunden gefallen. „Wir haben von den Endverbrauchern gehört, dass sie leicht zu reinigen sind. Sie fühlen sich auf der Haut gut an und sind leicht, sodass sie sehr angenehm zu tragen sind.“
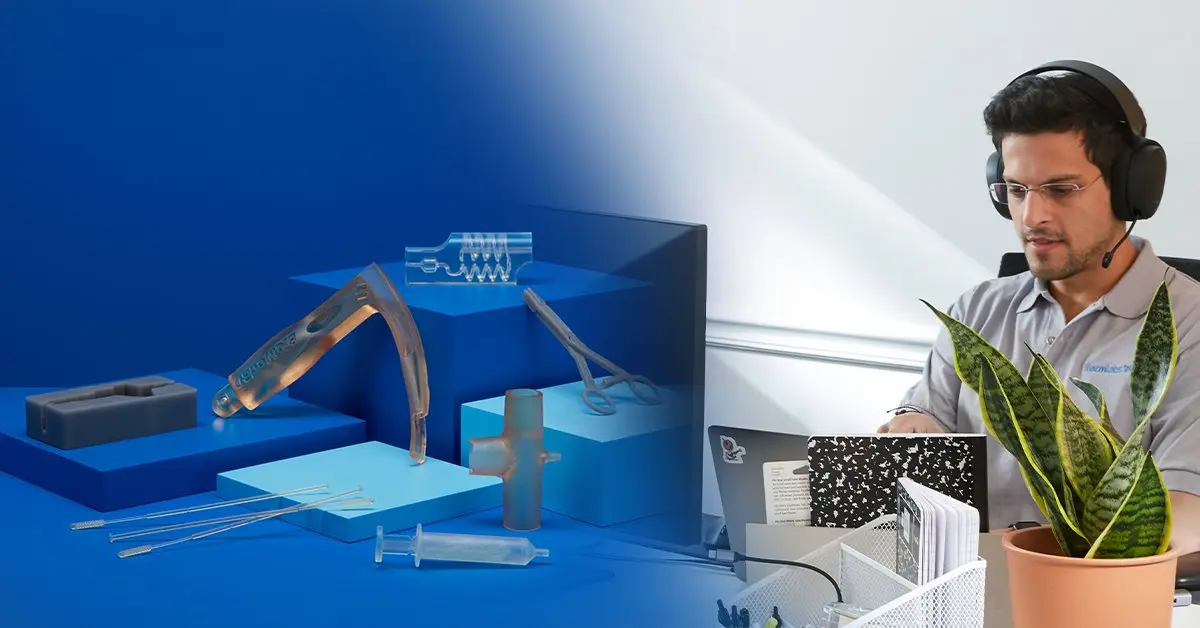
Kontakt zum Vertriebsteam von Formlabs Medical
Ob Sie patientenspezifische chirurgische Instrumente erstellen möchten oder Prototypen kardiologischer Medizinprodukte anfertigen: Wir stehen Ihnen zur Seite. Hinter Formlabs Medical steht ein engagiertes Spezialistenteam, das Sie und Ihr Unternehmen bei Bedarf mit professioneller Hilfe unterstützt.
Die Zukunft der Orthopädiebranche
„Ich denke, man muss 3D-drucken. Die Kosten steigen ins Unermessliche. Die Gehälter steigen ... Ich denke, 3D-Druck ist die Zukunft der Orthopädiebranche.“
Lars Broxterman, Leiter von Vertrieb und Fertigung bei Artus3D
Mit intelligenten Algorithmen zur Automatisierung des Designs und der einfachen Bestelloption direkt auf der Plattform macht Artus3D den 3D-Druck von Hand- und Handgelenkorthesen zum Kinderspiel. Durch die betriebsinterne Fertigung mit TPU 90A Powder auf dem Fuse 1+ 30W hat Artus3D die Kontrolle über die Produktion übernommen und den Zeit- und Kostenaufwand für die Herstellung von Orthesen aus einem, wie Broxterman sagt, bahnbrechenden Material gesenkt.
Intuitive Arbeitsabläufe und Benutzerfreundlichkeit stehen sowohl bei Artus3D als auch bei Formlabs an erster Stelle. Ihre Lösungen machen es für die Orthopädietechnik einfacher und schneller als je zuvor, Patient*innen mit Orthesen zu versorgen.
Erfahren Sie auf ihrer Webseite mehr über die Software von Artus3D, oder wenden Sie sich an Formlabs' Expertenteam, um weitere Informationen über 3D-Druck-Lösungen und das Fuse-Ecosystem zu erhalten.