Kurz nachdem Ashley Furniture den ersten Stereolithografie -3D-Drucker angeschafft hatte, hatte einer der Fertigungsingenieure eine Idee. Wäre es wohl möglich, auf der Drehbank gefertigte Führungsstifte mit 3D-gedruckten Fertigteilen zu ersetzen und auf diese Weise die langen Durchlaufzeiten und Mindestbestellmengen beim Outsourcen zu vermeiden?
Die Antwort lautete „Ja“ und warf noch weitere Fragen auf.
Heute, etwa zwei Jahre und einen zusätzlichen Drucker später, werden 700 3D-gedruckte Teile im Werk von Ashley Furniture in Arcadia im US-Bundesstaat Wisconsin von der Montage bis zur Fertigung eingesetzt – neben Industrierobotern und CNC-Fräsmaschinen.
Mitarbeiter im gesamten Unternehmen stellen weiter Fragen und schlagen Ideen vor, und das Unternehmen wächst weiter.
Sehen Sie sich das Video an und erfahren Sie, wie und wieso Ashley Furniture, der weltgrößte Möbelhersteller, neue Technologien wie 3D-Druck und Robotikanwendungen in seinen Werken nutzt.
Ein Rezept für Erfolg in der Herstellung
Ashley Furniture ist der weltweit größte Möbelhersteller und wächst trotz Problemen mit einem schrumpfenden Arbeitsmarkt immer weiter.
„Unser Geschäft im Werk in Arcadia allein ist um 10 Prozent gewachsen, und das mit wahrscheinlich fast 15 Prozent weniger Arbeitskräften“, berichtet Vaughn Pieters, Senior Director of Casegood Operations.
Hand in Hand mit einer Kultur, die Mitarbeiter ermutigt, aktiv an kontinuierlichen Verbesserungsprozessen teilzunehmen, wendet Ashley Furniture fortschrittliche Technologien an, um die Arbeit zu unterstützen und den Wert der Belegschaft zu maximieren, indem es die Verbesserungen und Innovationen umsetzt, die die Menschen vorschlagen, die am meisten mit der jeweiligen Arbeit vertraut sind.
„Die Automatisierung hat es uns wirklich ermöglicht, etwas von der schweren körperlichen Arbeit überflüssig zu machen, die in den letzten 50 oder 60 Jahren das Stigma der Fertigung war. Wir lassen unsere Mitarbeiter nicht mehr den ganzen Tag Schwerstarbeit machen. Das sollen die Maschinen machen. Wir wollen, dass die Mitarbeiter ihren Verstand einsetzen und versuchen, die Prozesse zu verbessern“, so Pieters.
„Wir haben unseren ersten Roboter vor fünf Jahren angeschafft, und jetzt können Sie bei der Besichtigung des Werks sehen, wo wir überall noch Automatisierung einsetzen. Beim 3D-Druck ist dasselbe Wachstumsmuster erkennbar.“

Von der Prototypenfertigung vor Ort zu Vorrichtungen und Werkzeugen
In den letzten 30 Jahren hat Brian Konkel, Fertigungsingenieur bei Ashley Furniture, in den Design-, Ingenieur- und Fertigungsabteilungen des Unternehmens gearbeitet und dabei Gelegenheiten gefunden, 3D-Druck in allen diesen Bereichen einzusetzen.
Vor dem Einsatz von 3D-Druck im Werk hatte Ashley Furniture 3D-Druck bereits firmenintern für die Prototypenfertigung eingesetzt. Tatsächlich hatte das Unternehmen den 3D-Druck schon Jahrzehnte eingesetzt und seit den 1990ern gelegentlich Teile outgesourct. Schließlich kam ein kostengünstiger FDM-(Schmelzschichtungs)-Drucker hinzu, als das Bestellvolumen zu wachsen begann.
Das Unternehmen druckte immer mehr vor Ort, doch die Qualität wurde zum Problem. Das Team stieg auf die lasergestützte SLA-Technologie um und kaufte den Formlabs Form 2 3D-Drucker.
„Wir stellten fest, dass wir eine etwas bessere Oberflächenbeschaffenheit und engere Toleranzen wünschten. Der SLA 3D-Druck auf dem Form 2 erlaubte es uns, Dinge wie Schnappverbindungen für verschiedene Befestigungselemente zu entwickeln“, sagt Konkel.
„Einer der Vorteile des Form 2 sind die verschiedenen Materialien, die zur Verfügung stehen. Wir können mit dem Druck eines Bauteils beginnen, und wenn das eingesetzte Material nicht genau das ist, was wir benötigen, gibt es weitere Optionen.“
Die Dinge entwickelten sich schnell, nachdem das Team den Form 2 3D-Drucker gekauft hatte. Zusätzlich zur Prototypenfertigung fand Konkel weitere Bereiche für den Einsatz von 3D-Druck in der Fertigung. Das Druckvolumen wuchs so stark, dass das Unternehmen ein halbes Jahr später einen zweiten Drucker bestellte.
„Wir lassen momentan beide Formlabs Drucker mindestens 40 Stunden pro Woche laufen“, berichtet Konkel.
Skalierung 3D-gedruckter Fertigungsteile
Der 3D-Druck von Teilen war eine schnelle, risikoarme Lösung zum Testen und Umsetzen von Ideen zur Effizienzsteigerung. Dies reicht von der Zeit- und Kostenersparnis durch die Herstellung von Ersatzteilen vor Ort hin zur Entdeckung kreativer Lösungen, die die Organisation der Werkshalle grundlegend verändert haben.
Allein der 3D-Druck der Führungsstifte hat gegenüber dem Outsourcing zur Fertigung der Teile aus Nylon zu erheblichen Zeit- und Kosteneinsparungen geführt.
„Wir bezogen [die Stifte] zuvor von einer Metallwerkstatt mit einer großen Mindestbestellmenge von 1.200 Stiften, die aus Nylon gedreht wurden. Jetzt können wir das umgehen und die Kosten buchstäblich halbieren“, so Konkel.
Kostenvergleich Führungsstifte
Outsourcing zur Metallwerkstatt | 3D-Druck vor Ort auf dem Form 2 | |
---|---|---|
Kosten | 1200 Stück Mindestbestellmenge 10 US-$ pro Teil | Keine Mindestbestellmenge 5,90 US-$ pro Teil |
Durchlaufzeit | 3 bis 4 Wochen | 15 Std. 30 Min. für 16 Teile auf zwei Druckern |
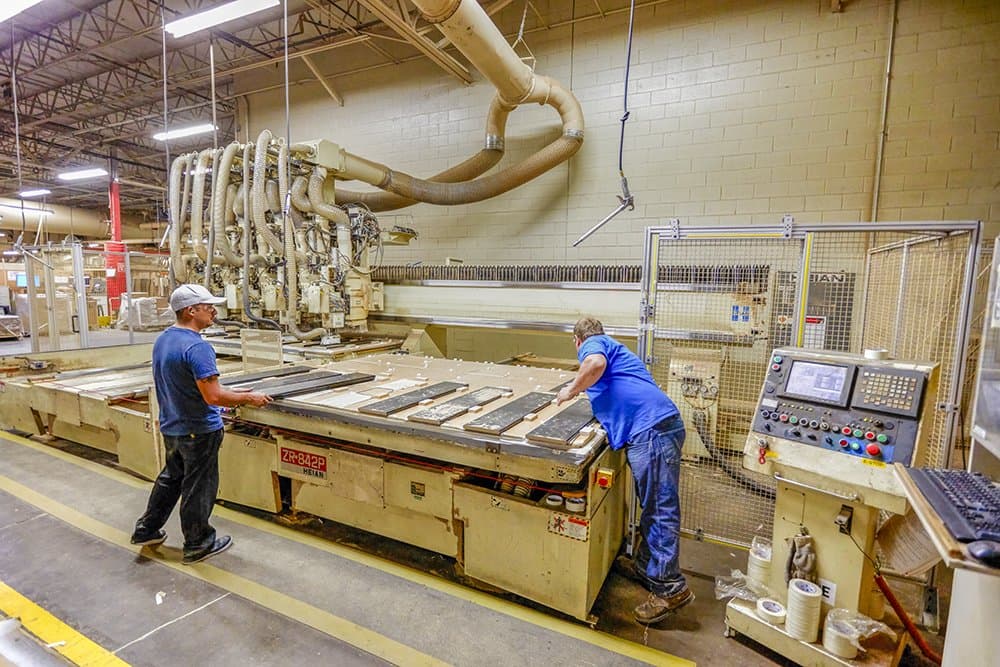
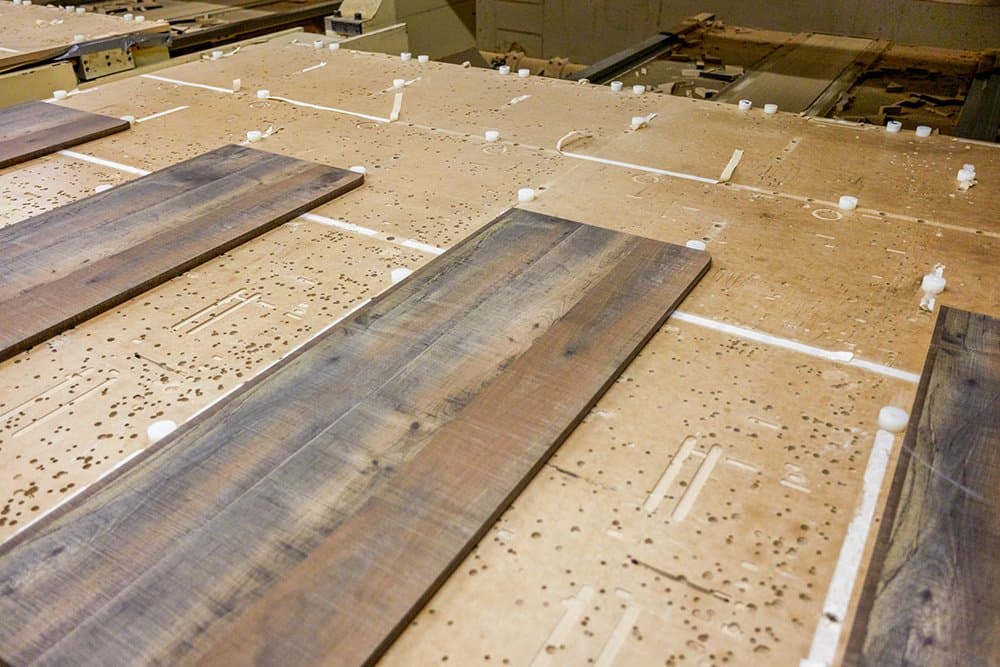
Ein universelles System für Montagevorrichtungen
Eine der bislang kreativsten Lösungen des Unternehmens ist ein universelles System für Montagevorrichtungen. Ähnlich wie das Gittermuster für die Führungsstifte der Oberfräse hat das Team ein universelles Vorrichtungssystem entwickelt, bei dem 3D-gedruckte Teile eingesetzt werden, um die Anpassungen bei Produktwechseln zu erleichtern. So fallen die Kosten für den Bau ganz neuer Vorrichtungen in Metallwerkstätten vollständig weg.
„Die 3D-gedruckten Teile schlagen die Brücke zwischen verschiedenen Konfigurationen“, so Konkel.
Bei Konkels universellem Vorrichtungssystem kommen 3D-gedruckte Teile zum Einsatz, um die Anpassungen zwischen Produktwechseln zu erleichtern.
Jetzt, nach der Einführung einer neuen SKU, muss das Unternehmen nur einige Anpassungen an den Abmessungen bestehender massiver Modelle vornehmen, um neue Teile zu entwerfen und drucken, um das System anzupassen. Abgesehen davon können sie alle aktuellen Konfigurationen und Geometrien einsetzen. Montagemitarbeiter folgen einfachen Anweisungen bei jedem Wechsel, verfahren Aktoren entlang der Schienen und ziehen sie in ihrer neuen Position fest. Sie setzen auch die 3D-gedruckten Teile für die neue Konfiguration ein.
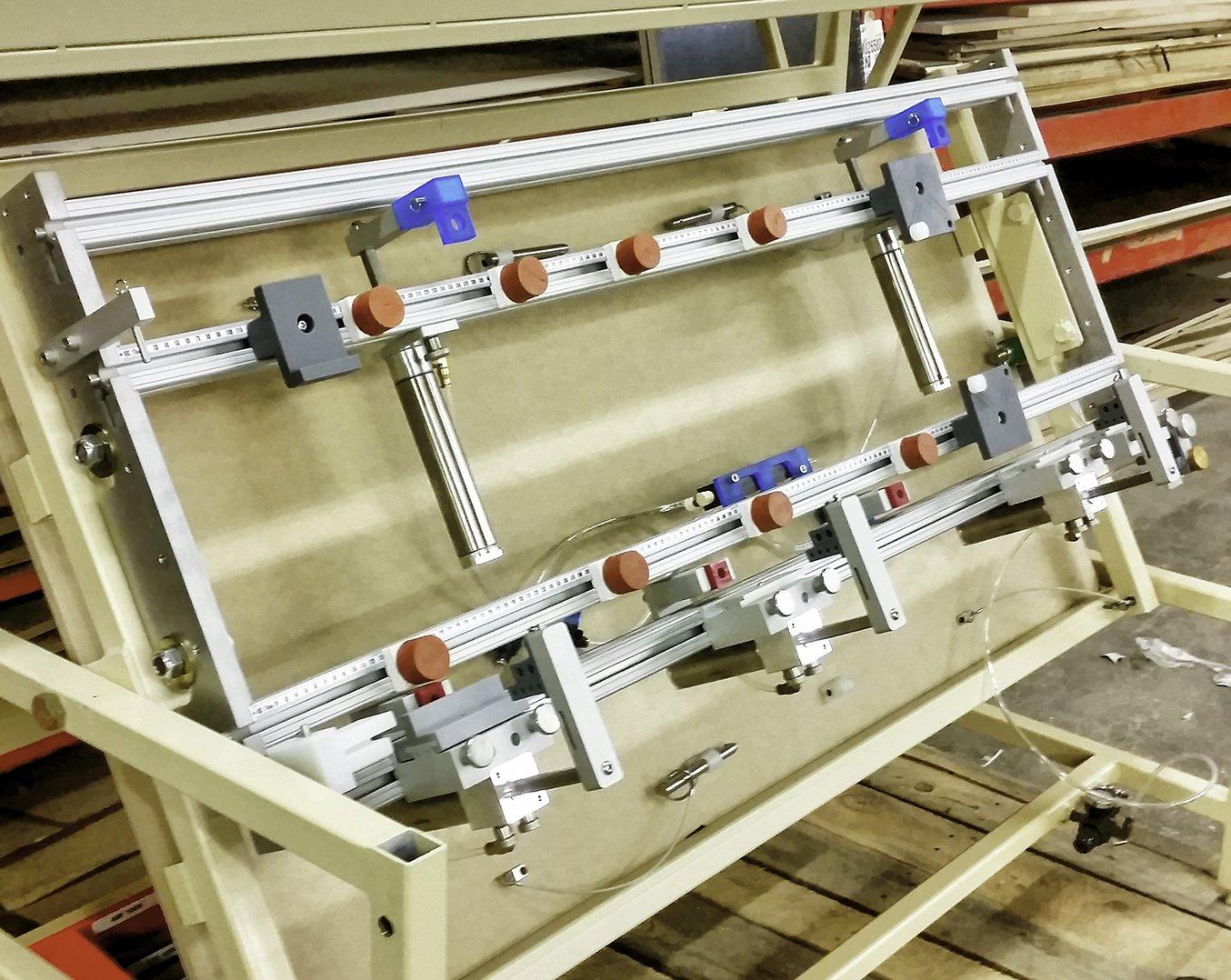
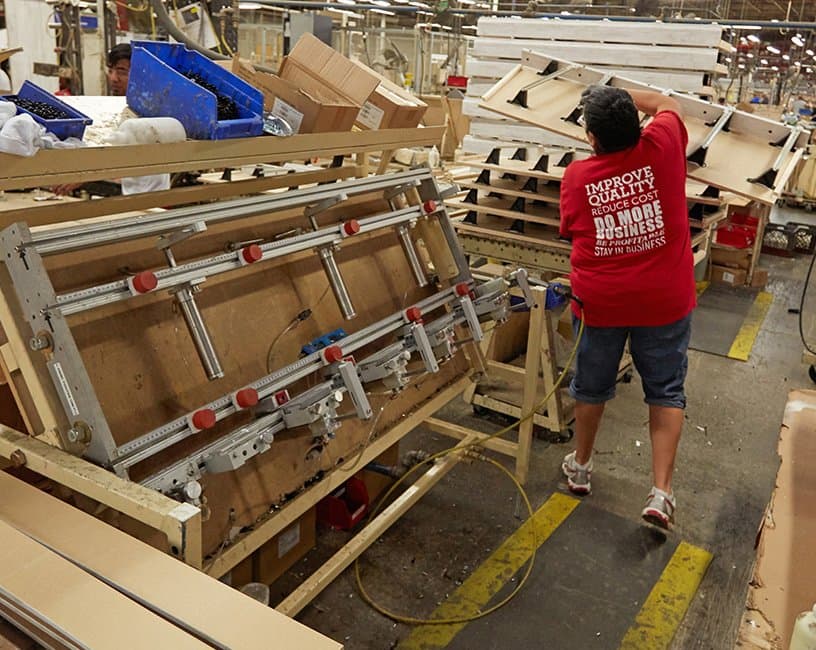
„Mit 3D-Druck ist es offensichtlich sehr einfach, [Teile] auszutauschen, aber wir waren von der langen Lebensdauer beeindruckt; einige dieser Teile hielten dreimal länger, als wir erwartet hatten, fast neun Monate, bevor sie ausgetauscht werden mussten“, erzählt Konkel.
„Beispielsweise werden manche Teile einmal pro Minute betätigt und fahren zum Einspannen herunter, damit eine Baugruppe verschraubt werden kann.“
Das universelle System hat die Einrichtungszeit im Montagebereich sowie den Lagerraum der ursprünglichen, bis zu 100 kg schweren Teile erheblich reduziert.
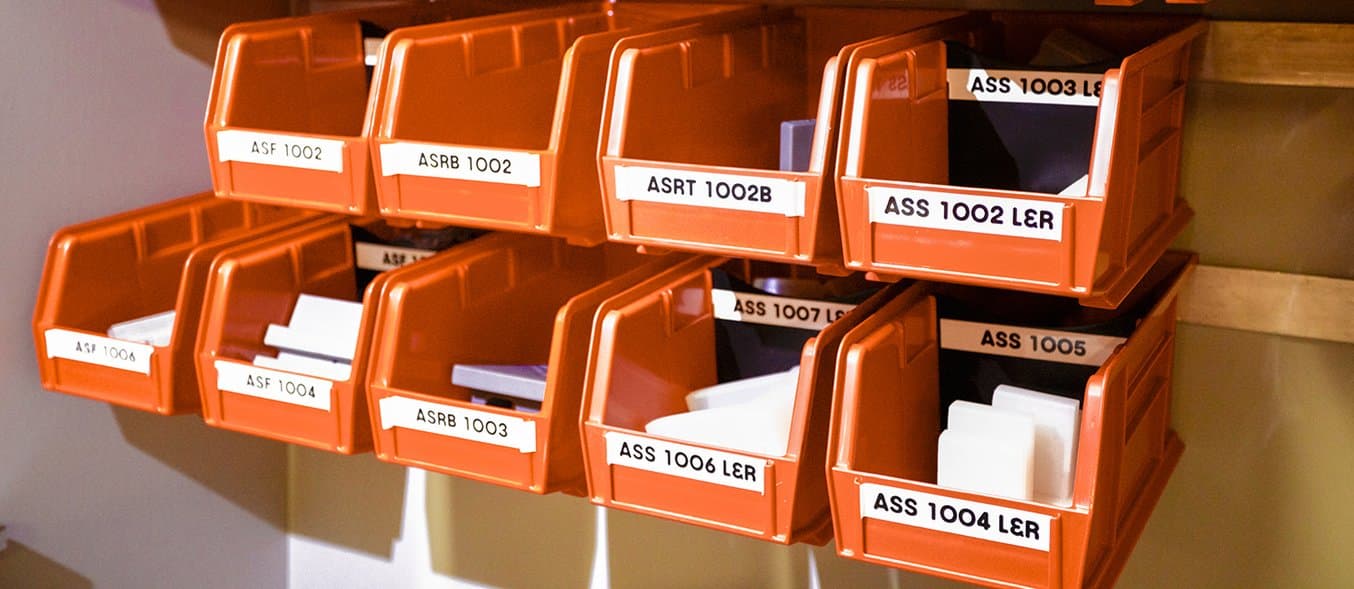
„Vorher haben wir jede einzelne Haltevorrichtung für eine spezifische Produktreihe gebaut. Mit dem 3D-Druck der Teile tauschen wir zur Anpassung an verschiedene SKUs einfach nur Teile aus. Wir haben wirklich Vorrichtungen mit Abmessungen von 90 cm × 180 cm mit einem einfachen Behältersystem ersetzt; die Einrichtungszeit beträgt zwei Minuten.“ Konkel sagt:
„Vorrichtungsbauer können sich jetzt anstelle von monotonen Arbeiten wichtigeren Problemen und größeren Herausforderungen zuwenden.“
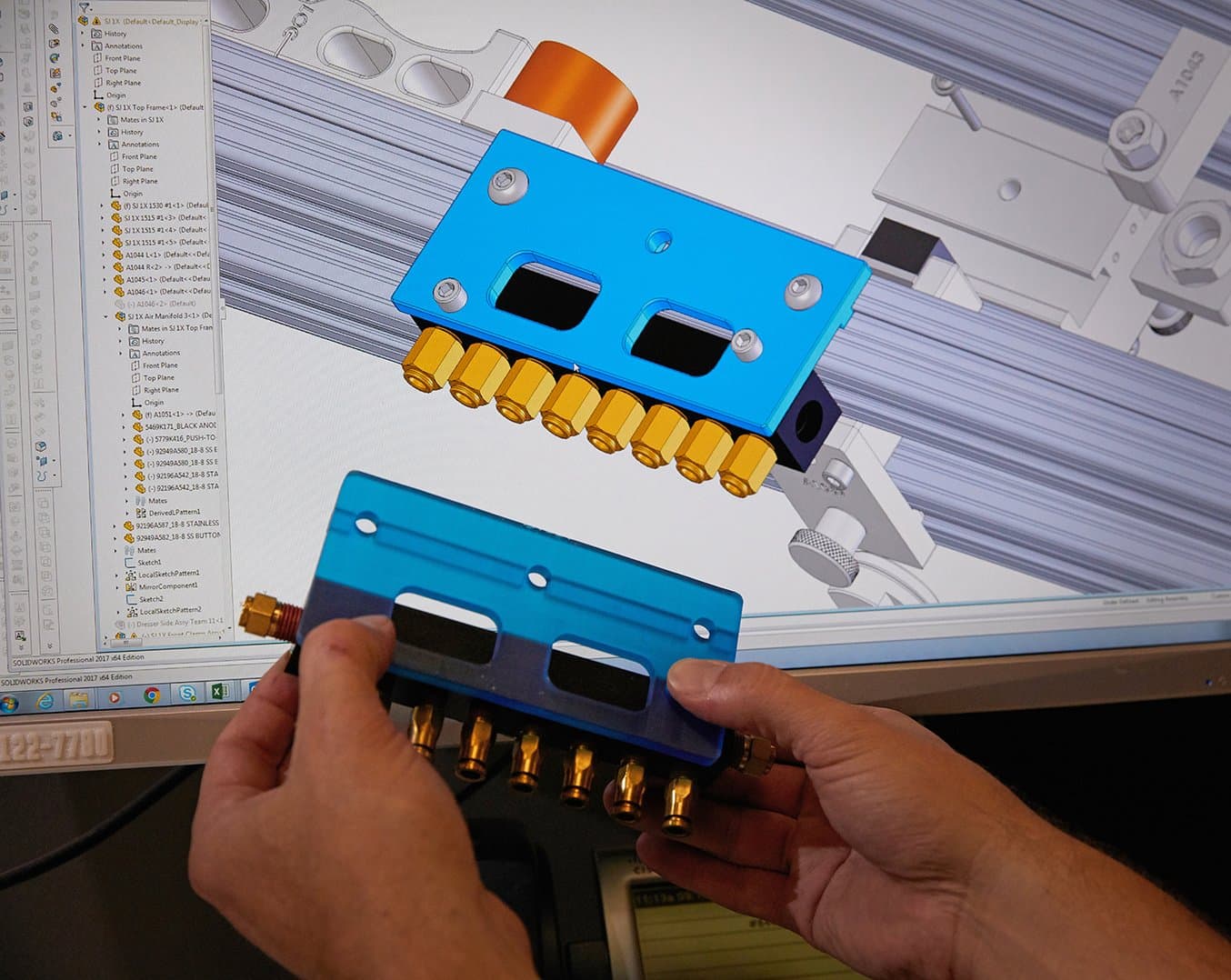
„Tough Resin ist ein Material, das uns bei Haltevorrichtungen und allem, was wir an das Ende eines Aktors setzen würden, ziemlich gute Dienste erwiesen hat. Es hat die entsprechende Schlagfestigkeit“, so Konkel.
Maßgefertigte Werkzeuge und kein teures Austauschen mehr dank Ersatzteilen
Ein einfacher, praktischer Erfolg war ein bestimmtes Ersatzteil. Eine Vakuumdichtung für ein CNC-Bohrwerk konnte nicht allein gekauft werden, und die einzige Möglichkeit wäre gewesen, die gesamte Baugruppe zu kaufen, was teuer war.
„Das Unternehmen wollte den Ring nicht allein verkaufen, und wir hätten das ganze Gehäuse für 700 US-Dollar kaufen müssen“, erzählt Konkel. „Stattdessen konnten wir das Teil 3D-scannen, um die Geometrie zu erfassen, und ein Ersatzteil für nur 1 Dollar drucken, um unsere Bohrausrüstung am laufen zu halten, ohne die gesamte Baugruppe kaufen zu müssen.“
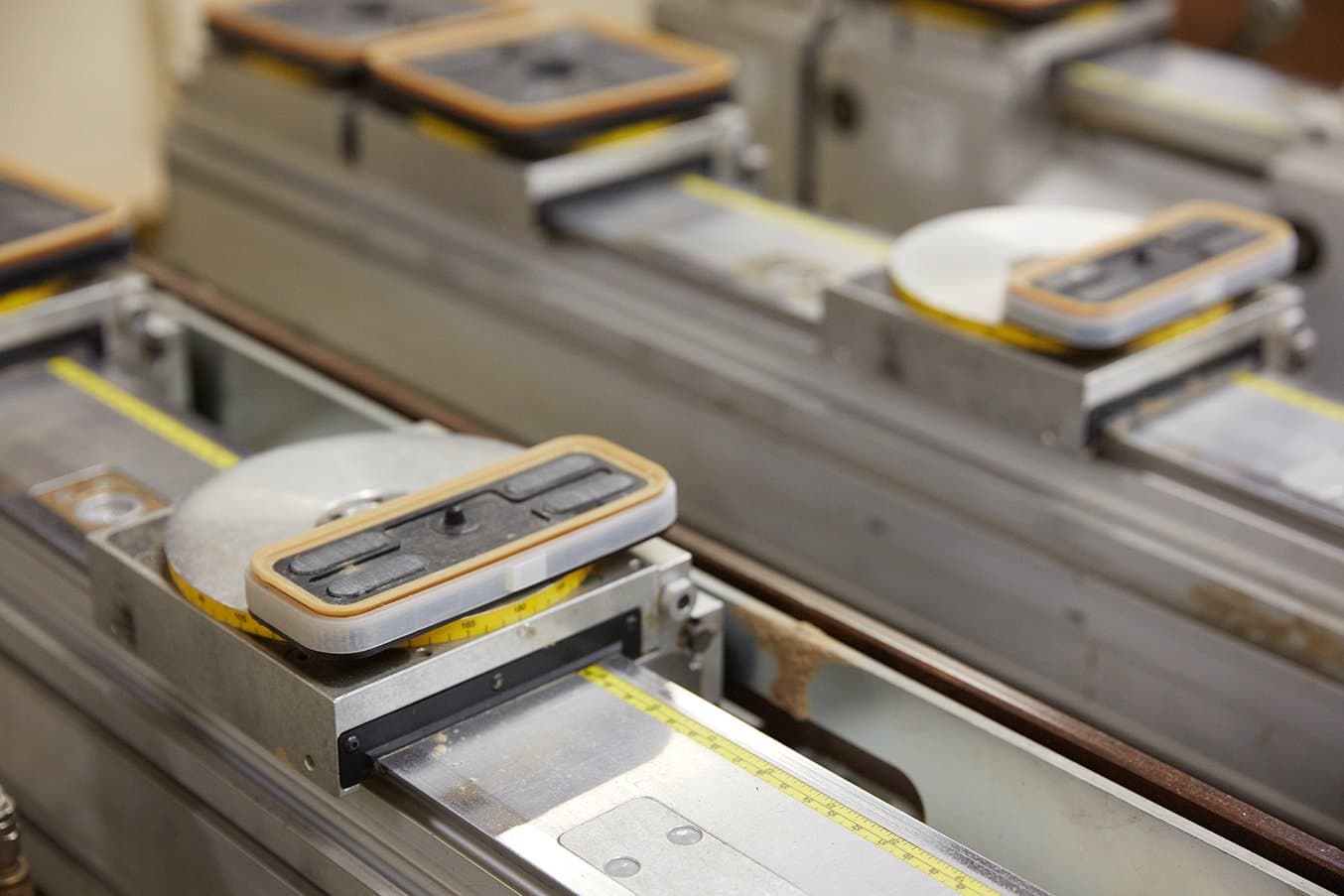
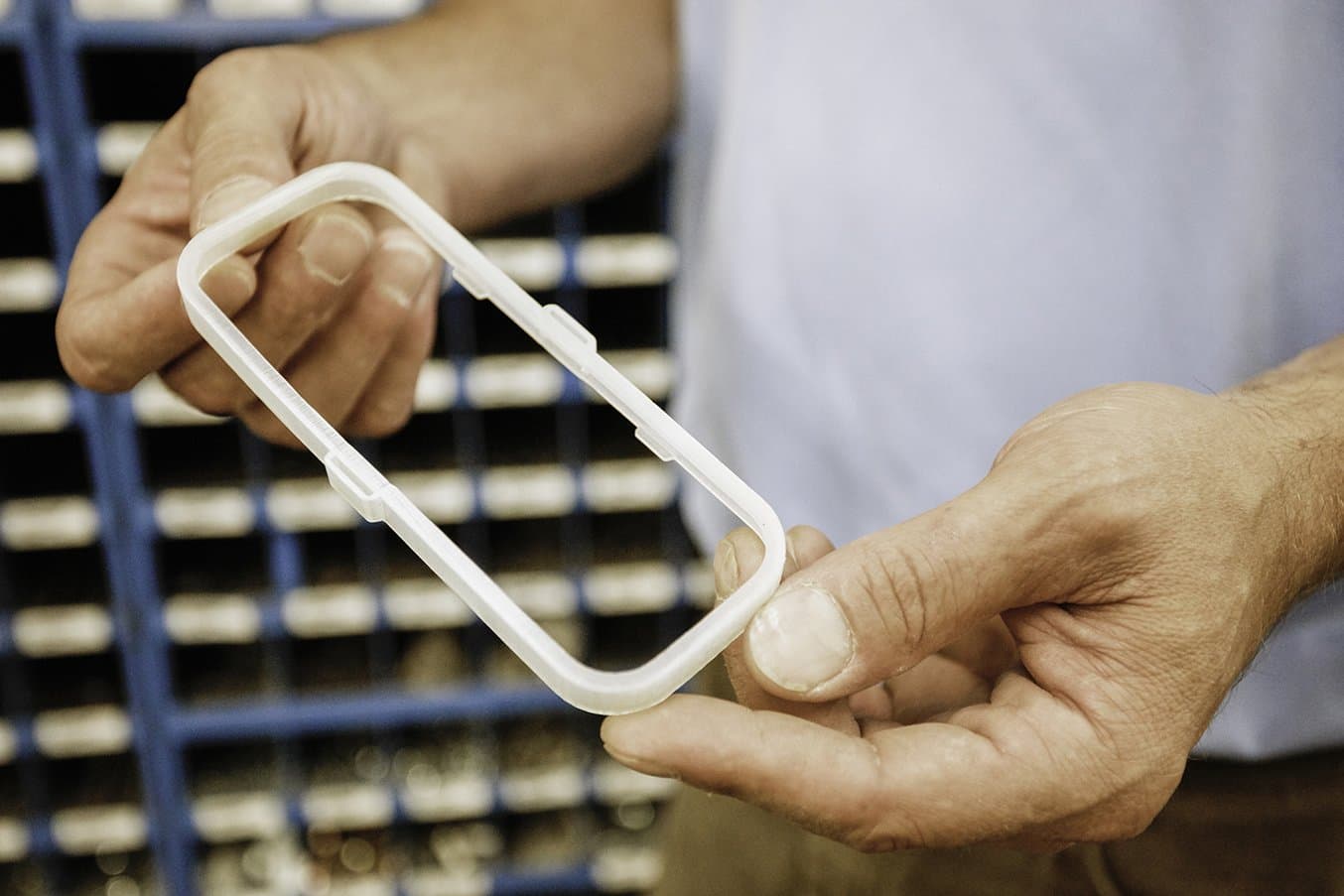
Der Form 2 hat es dem Team auch ermöglicht, maßgefertigte Handwerkzeuge herzustellen, wie etwa eine einfache Führung für einen Handtacker.
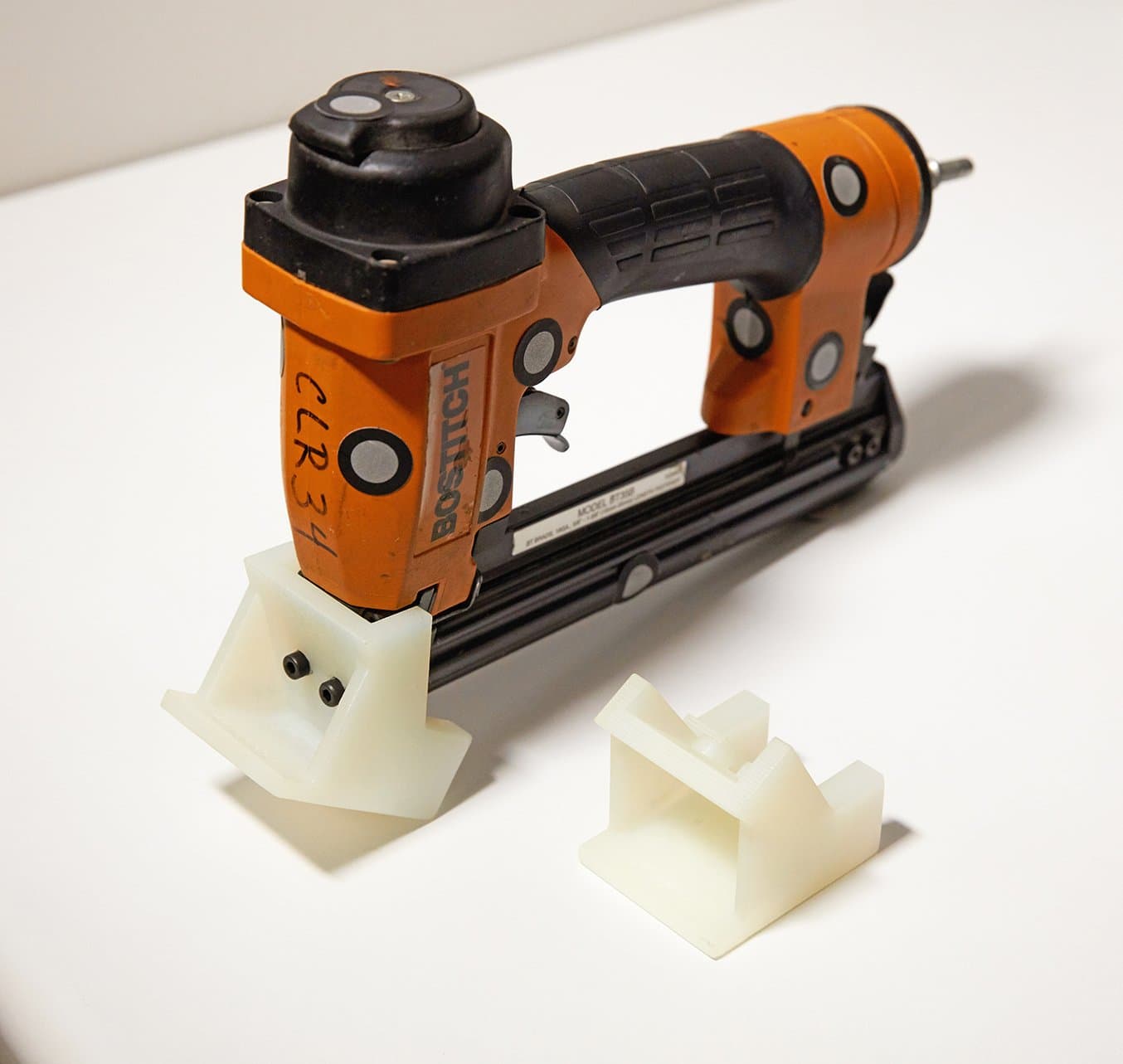
Erforschung von 3D-Druck in der Produktion
Firmeninterner 3D-Druck mit dem Form 2 hat den Mitarbeitern von Ashley Furniture mehr Möglichkeiten eröffnet, Probleme kreativ zu lösen und die Produktivität im Werk zu steigern. Das Team betreibt beide Drucker 40 Stunden pro Woche und das Unternehmen erforscht weiterhin neue Möglichkeiten, um Prozesse zu verbessern.
„Da wir den Form 2 haben und über die Möglichkeit verfügen, Teile zu drucken, konnten wir einige herkömmliche Methoden zur Herstellung von Vorrichtungen und Werkzeugen umgehen“, so Konkel.
„Wir haben die Möglichkeit, schnell auf Vorschläge oder Bedürfnisse einzugehen, die wir haben, und Geometrien zu erzeugen, die mit traditionellen Verfahren nicht gefertigt oder spanend hergestellt werden können. Wir können Dinge tun, die vor einigen Jahren noch nicht möglich waren.“
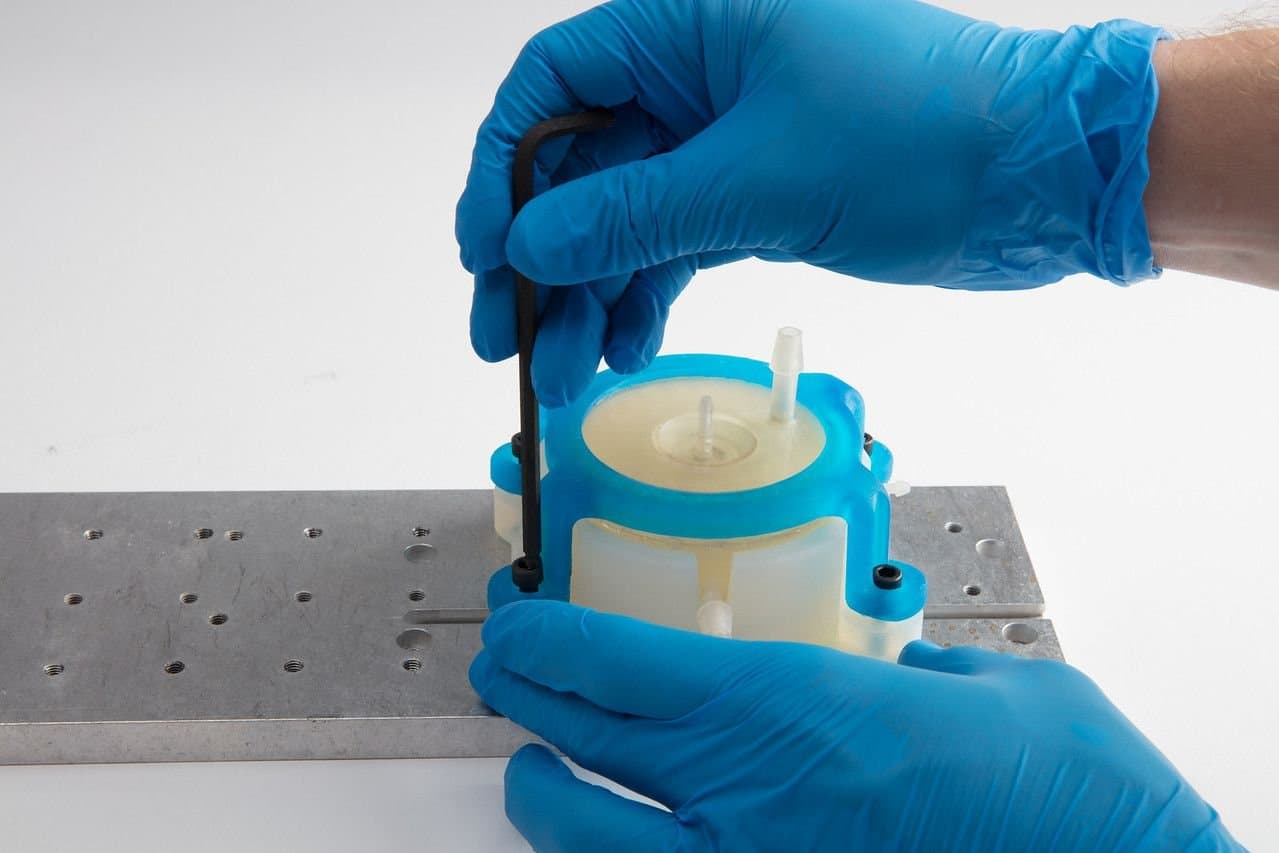
Design von Vorrichtungen und Halterungen mit 3D-Druck
Laden Sie unser Whitepaper herunter, um zu erfahren, wie Sie Kosten senken, Entwicklungszeiten verkürzen und optimierte Produktionsabläufe mit 3D-gedruckten Vorrichtungen und Halterungen erstellen können.
White Paper herunterladen