3D-Drucken von schnellen und kostengünstigen Betriebsmitteln für die Uhrmacherei
Ursprünglich wurde der Form 3 bei der Sinn Spezialuhren GmbH für den 3D-Druck von Prototypen gekauft. Mehr darüber, wie das Produktentwicklungsteam mit Hilfe des 3D-Drucks hochpräzise Prototypen für Uhren erstellt hat, können Sie hier nachlesen.
Innerhalb kürzester Zeit erkannte das Unternehmens jedoch, dass es 3D-Druck auch für die Herstellung von Fertigungswerkzeugen, wie z. B. Halterungen, Vorrichtungen und Prüfmittel, nutzen kann.
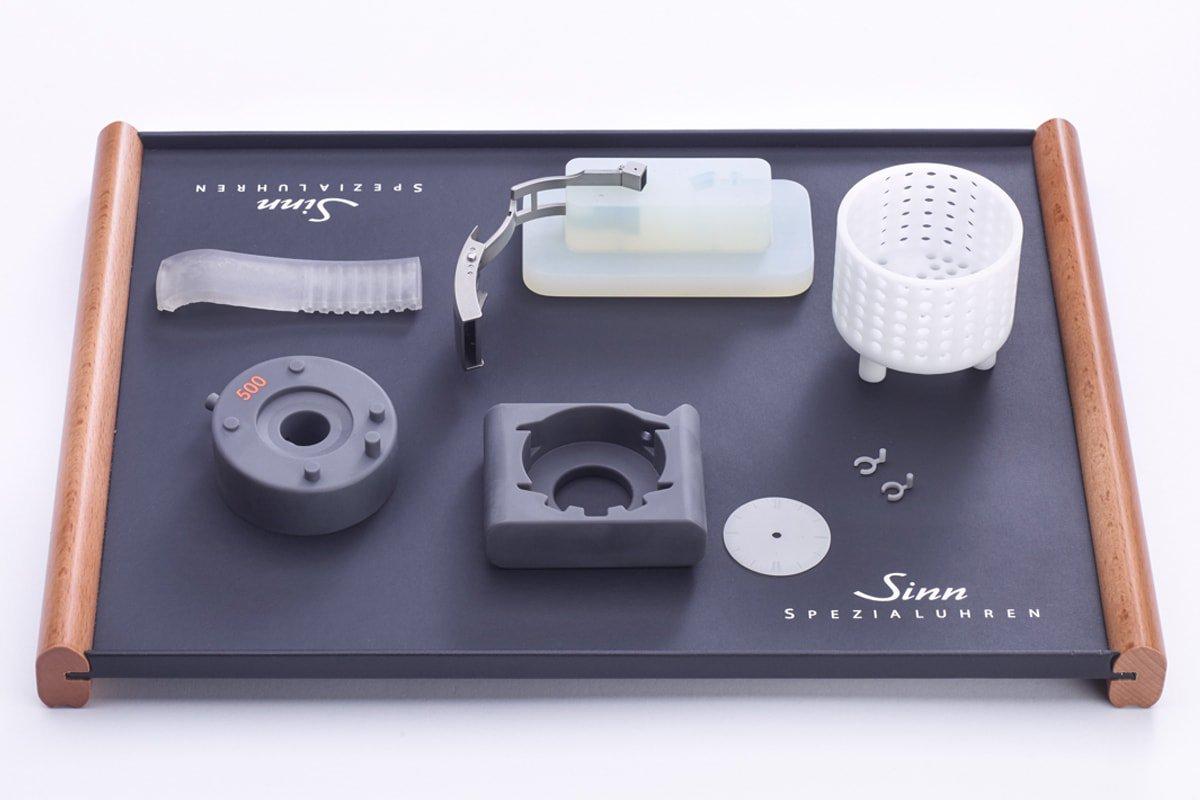
Prototypenteile der Uhren & nutzbare Vorrichtungen 3D-gedruckt auf dem Form 3.
Seit fast 60 Jahren steht Sinn Spezialuhren für funktionsstarke mechanische Uhren. Das Produktportfolio reicht von Fliegeruhren über Taucheruhren und Chronographen zu Einsatzzeitmesser, die von Piloten, Tauchern und der Eliteeinheit GSG 9 getragen werden. Daher richtet sich die Formgebung im Entwicklungsprozess nach der gewünschten Funktionalität, sodass oft firmenspezifische Betriebsmittel benötigt werden.
Erweiterter Einsatz des 3D-Drucks für den Formenbau
Sobald der 3D-Druck einmal im Unternehmen etabliert war, fiel die Hemmschwelle stark, die Technologie für den firmenspezifischen Betriebsmittelbau einzusetzen. Nils Hunder, der bei Sinn Spezialuhren für die Konstruktion von Uhren, die Entwicklung von Prototypen und den 3D-Druck verantwortlich ist, sagt dazu: “Wir haben gemerkt, dass der Drucker uns dort sehr gute Dienste leistet.”
“Wir können sehr schnell, sehr kostengünstig Halterungen und Vorrichtungen über Nacht anfertigen.”
Nils Hunder, Verantwortlicher für Konstruktion und Produktentwicklung sowie Prototypenentwicklung
Bisher wurden Betriebsmittel vorrangig durch externe Dienstleister hergestellt. Dies bedeutete hohe Outsourcingkosten und Lieferzeiten von durchschnittlich 1-2 Wochen für Halterungen und Vorrichtungen, bei denen man nie komplett sicher war, ob sie den gewünschten Zweck erfüllen, oder ob die Kosten im schlimmsten Fall vergeblich verursacht wurden.
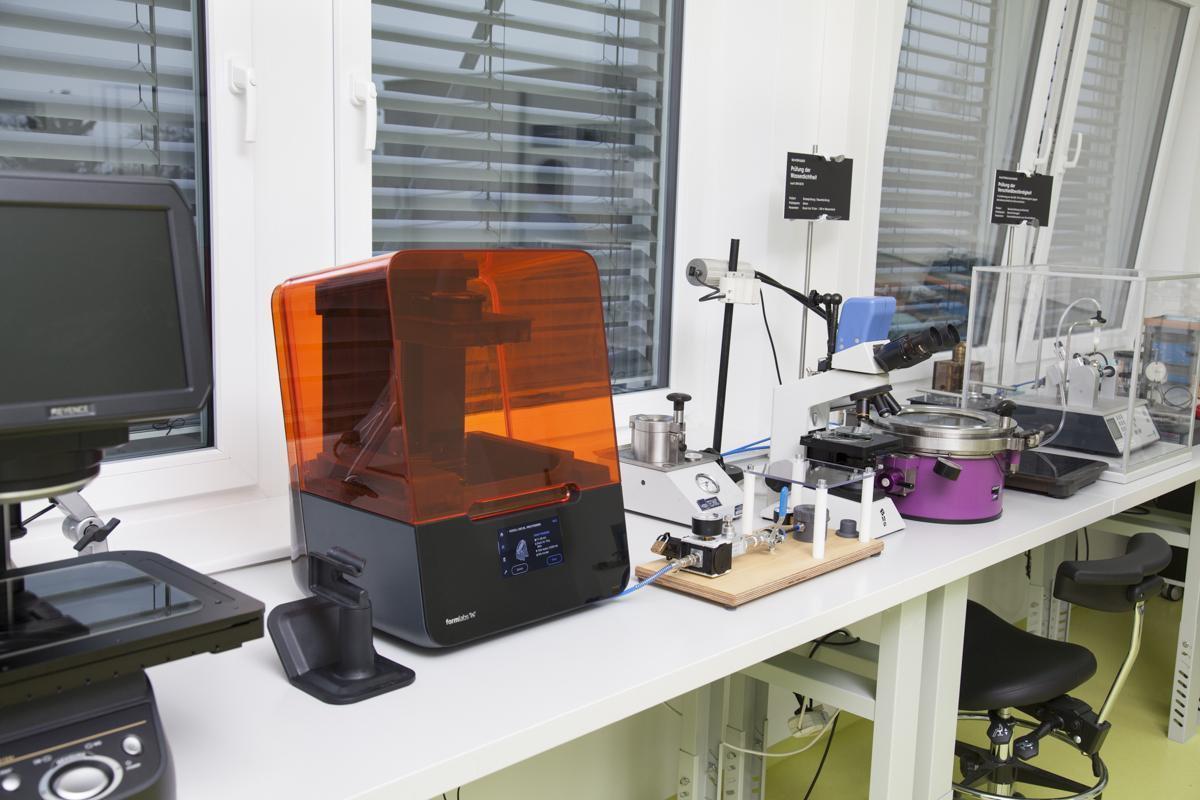
Der Form 3 im Labor von Sinn Spezialuhren
Jetzt kommt der Form 3 vermehrt im Betriebsmittelbau zum Einsatz. Damit fallen kostenseitig nur die Materialkosten und die geringe Arbeitszeit an, die für die Nachbearbeitung erforderlich ist. So erhält man meistens über Nacht das Druckergebnis und kann schnell Anpassungen vornehmen, wenn die Druckteile nicht den Anforderungen entsprechen.
Nils Hunder verwendet hauptsächlich Tough 1500 Resin und Tough 2000 Resin, da die Teile daraus stabil sind, aber dennoch leicht nachgeben. Zum Beispiel wurden damit die Serienteile für 500 Kronenstopper von Quarzuhren gedruckt, die nicht als Massenware zur Verfügung standen. Wenn Uhren am Lager liegen, werden die Kronen mit sogenannten Kronenstoppern blockiert, damit sich die Batterie während der Lagerzeit nicht entleert. Der reguläre Zulieferer von Sinn Spezialuhren hatte aufgrund der Corona-Pandemie keine Kapazitäten für die Kronenstopper und ihre Herstellungskosten, in Verbindung mit einer Mindestmenge von 10.000 Stück, wären damit zu teuer geworden. Glücklicherweise konnten auf dem Form 3 in einem Durchgang 50 dieser Kronenstopper gedruckt werden. Sie waren praktisch (Anm.: es reichte das Ablösen der minimalen Stützstruktur mit 0,1 mm ) sofort sofort einsatzfähig und sind dank des Tough 1500 Resin leicht nachgiebig. Damit verkratzen sie die Uhren nicht und sind wiederverwendbar.
Aber auch andere Materialien wie das Rigid 4000 Resin kommen vermehrt zum Einsatz. Die Uhrengehäuse aus Damaszenerstahl werden zu Testzwecken betriebsintern geätzt. Zur besseren Temperaturverteilung muss die Säure gerührt werden. Dabei kommen Körbchen aus Rigid 4000 Resin zum Einsatz, da dieses Material eine hohe chemische Beständigkeit hat und nicht von der Säure angegriffen wird.
Ein weiteres Einsatzgebiet ist die Ar-Trockenhaltetechnik, eine Technologie, die von Sinn Spezialuhren für Taucheruhren entwickelt wurde. Diese Uhren enthalten eine Schutzgasfüllung. Deshalb wurde eine Halterung für das Uhrengehäuse benötigt, um das Schutzgas in das Gehäuse einzuleiten. Mit konventioneller Fertigung durch Fräsen kosten die beiden Teile der dafür erforderlichen Halterung rund 200€ und benötigen 1-2 Wochen Fertigungszeit. Mit dem Form 3 lassen sich die Druckteile zu 30€ Materialkosten, mit Nachbearbeitungszeit also insgesamt zu der Hälfte der Kosten drucken. Auch wurde die Herstellungszeit drastisch gekürzt, indem der Druck meist über Nacht durchgeführt wird.
Durch spezielle Anpassungen der Teile mit eingravierten Schriften ist auf den ersten Blick ersichtlich zu welchem Uhrenmodell die Halterungen gehören und erleichtern somit den Arbeitsalltag enorm. Solche kundenspezifischen Markierungen der Werkzeuge würden Extrakosten in der konventionellen Fertigung verursachen.
Inhouse Entwicklung einer TÜV-bewerten Prüfanlage
Teil des Uhrensortiments von Sinn ist ebenfalls die Taucheruhr UX, die mit glasklarem Öl Flüssigkeit gefüllt ist. Diese Flüssigkeit verändert ihr Volumen bei Temperaturänderung, sodass die Uhr einen Membranboden besitzt der bei Erwärmung ausfährt bzw. sich bei Abkühlung ins Gehäuse einzieht. Den größten Aha-Effekt hatte das Team um Nils Hunder beim Entwickeln einer Prüfanlage für diesen Membranboden.
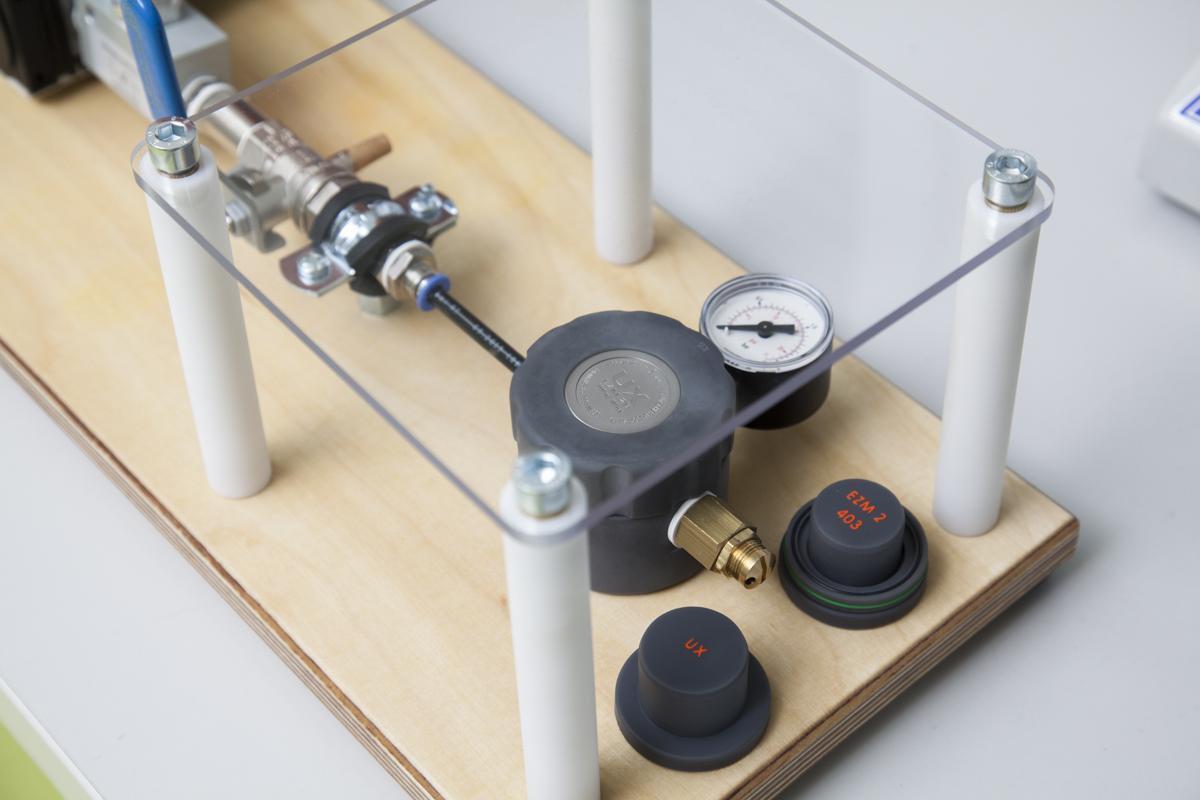
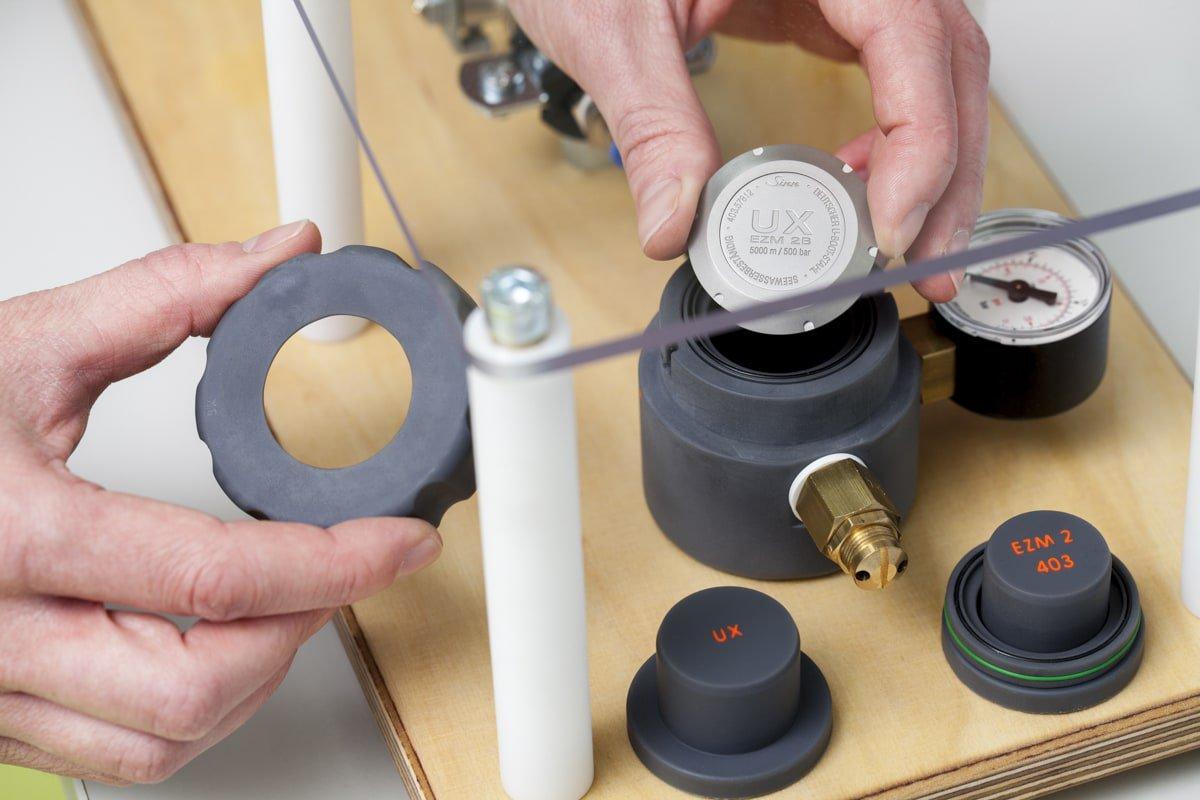
Membranboden-Prüfanlage für das Uhrenmodell UX mit 3D-gedruckter Halterung.
Ziel der Prüfanlage ist es den Hub des Membranbodens zu kontrollieren, ob er gerade ausfährt oder leicht schräg und dann dementsprechend aussortiert werden kann. Dafür wurde bisher eine komplette Uhr gebaut und erwärmt, was sehr aufwändig ist, da alle Komponenten mit Flüssigkeit verunreinigt wurden und dann wieder gesäubert werden mussten.
Um diese aufwändige Arbeit zu erleichtern, wurde eine Prüfanlage entwickelt, die mit Luftdruck das Verhalten der Flüssigkeit simuliert.
Die 3D-gedruckte Membranboden-Prüfanlage in Arbeit
Aus Tough 2000 Resin wurde der Drucktopf mit unterschiedlichen Einlegeringen, in die verschiedene Gehäuseböden passen, sowie der Verschlussring, der über einen Bajonettverschluss schließt, gedruckt. Dieser Bajonettverschluss stellte dabei die größere Herausforderung dar, da dieser in der konventionellen Fertigung sehr schwierig herzustellen ist. Außerdem wurden Stützen für eine Acrylglasabdeckung aus Rigid 4000 Resin hergestellt.
Mit dem 3D-gedruckten Prüfstand sollte ursprünglich nur die generelle Durchführbarkeit der Prüfanlage und der Einsatz des Bajonettverschlusses getestet werden. Allerdings funktionierte diese am Ende so gut und es konnten sogar Gewinde für den Rest der Prüfanlage und Manometer eingeschnitten werden, sodass eine konventionelle Fertigung gar nicht mehr erforderlich war. Zusätzlich wurde der 3D-gedruckte Prüfstand auch durch den TÜV begutachtet und freigegeben.
„Wenn man feststellt, man kann das benötigte Teil drucken, kann ich mich rein auf die Funktionalität konzentrieren, was ein großer Vorteil ist.“
Nils Hunder, Verantwortlicher für Konstruktion und Produktentwicklung sowie Prototypenentwicklung
Das Team um Nils Hunder hatte die Fertigung der Prüfanlage auch bei ihrem Zulieferer der Seriengehäuse angefragt. Da die Fräsanlage aber zur Herstellung der Uhren genutzt wird, hätte eine Fertigung durch den Zulieferer zu einer Verzögerung in der Uhrenproduktion geführt. Außerdem wäre die Produktionszeit der Prüfanlage enorm lange gewesen. So hat Sinn Spezialuhren die betriebsintern konstruierte Prüfanlage an ihren Zulieferer gesendet und wurde somit selbst zum Zulieferer - eine ganz neue Erfahrung für das Team.