Der Weg zur Kosteneinsparung und Individualisierung: Labconcos strategischer Umstieg auf 3D-Druck
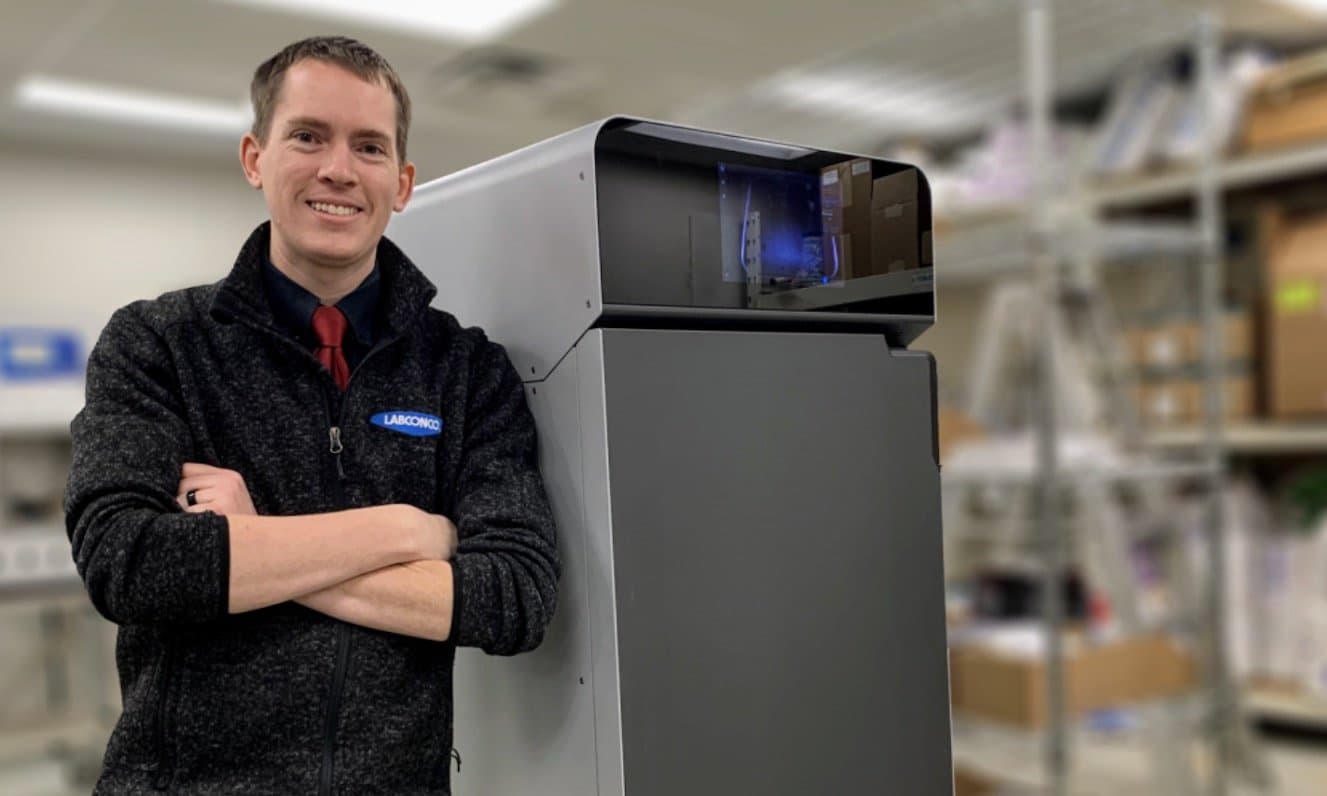
Bei seinem ersten Meeting bei Labconco Anfang 2020 ließ Brent Griffiths Vorschlag zur Nutzung von 3D-Druck den ganzen Raum verstummen. Bei der Besprechung ging es unter anderem um ein kleines Bauteil für Labconcos neues Produkt Logic Vue, das spritzgegossen werden musste. Weil es sich um ein neues Produkt handelte und noch keine Vertriebsmengen festgelegt waren, war es möglich, dass das über 15 000 € teure Spritzgusswerkzeug im ersten Jahr nur etwa 100 Teile produzieren würde. Die daraus resultierenden hohen Stückkosten verleiteten das Team dazu, nach anderen Lösungen zu suchen. „Ich meldete mich zu Wort und sagte, ‚Wisst ihr, ich kann das auch 3D-drucken und bis morgen voraussichtlich genug Teile für ein Jahr liefern'. Das verschlug allen die Sprache“, erinnert sich Brent Griffith, Produktingenieur bei Labconco.
Zu diesem Zeitpunkt hatte Labconco noch keine betriebsinternen 3D-Drucker. Als Griffith am nächsten Tag mit mehreren Versionen des Bauteils wiederkam, die er zu Hause auf seinen eigenen Druckern gefertigt hatte, lag der geschäftliche Nutzen von 3D-Druck auf der Hand.
Heute ist Griffith bei Labconco für ein wachsendes Labor zuständig, das aus drei Fuse 1+ 30W für selektives Lasersintern (SLS), dem Fuse Sift und Fuse Blast sowie einem SLA-3D-Drucker, dem Form 3L, und mehreren Druckern für Schmelzschichtung (Fused Deposition Modeling, FDM) besteht. Labconco stellt Laborausrüstung für eine Vielzahl von Branchen her, von der Lebensmittelprüfung über Arzneimittelentwicklung bis hin zur Krebsdiagnostik und Forensik. Mittlerweile druckt Griffith Hunderte von Teilen pro Woche, die zerspante oder spritzgegossene Komponenten ersetzen und verbessern, als Übergangslösungen im Fall von Lieferkettenverzögerungen dienen und die Entwicklungsphase vieler neuer Labconco-Produkte unterstützen.
Das Argument
Nachdem Griffith den Geschäftsfall mithilfe des ersten 3D-gedruckten Bauteils begründen konnte, begann er mit dem Druck anderer Komponenten für die Ingenieurteams des Unternehmens, um die Produktentwicklung zu unterstützen, wobei schon bald eine Warteschlange entstand. „Es wurde sehr schnell hektisch“, erinnert sich Griffith.
Um die Grenzen der Möglichkeiten von 3D-Druck auszutesten, führten er und ein anderer Ingenieur, Austin Orme, gemeinsam Inventur über die Tausenden von Teilen, Werkzeugen und Komponenten, die für die Produkte von Labconco benötigt wurden. „Unsere genaue Anweisung war, ein Gerät zu finden, das ein exzellentes Fertigungsvolumen hat und eine sehr hohe Druckteilqualität liefert, damit wir es sowohl für Prototypen als auch für die Produktion nutzen konnten“, erzählt Griffith. „Wir stellten schnell fest, dass ein Gerät für diese Aufgabe nicht ausreichen würde, da kein Modell über die Vielfalt an Möglichkeiten und die Flexibilität verfügen würde, die wir brauchten.“ Letztendlich startete das Labor mit sechs Druckern, darunter drei SLS-Drucker des Typs Fuse 1+ 30W und der großformatige SLA-Drucker Form 3L.
„Den Form 3L haben wir gekauft, weil wir Zugriff auf die Kunstharz-Bibliothek von Formlabs haben wollten. Ich wusste, dass er uns Flexibilität verschaffen und neue Möglichkeiten eröffnen würde. Und der Drucker hat genau das erfüllt, was wir uns erhofft haben.“
Brent Griffith, Produktingenieur
Dank der Materialvielfalt, die der Form 3L ermöglicht, und der mittleren bis hohen Produktionsvolumen mit den Druckern der Fuse-Serie konnte Griffith existierende Produkte verbessern, an Werkzeugkosten Beträge im fünfstelligen Bereich einsparen, die Entwicklungsphase der Projekte beschleunigen und Bauteile auf Abruf ersetzen.
Ersetzen, optimieren, skalieren: Anwendungen für 3D-Druck bei Labconco
SLS-Füllsensor: Austausch einer spritzgegossenen Baugruppe
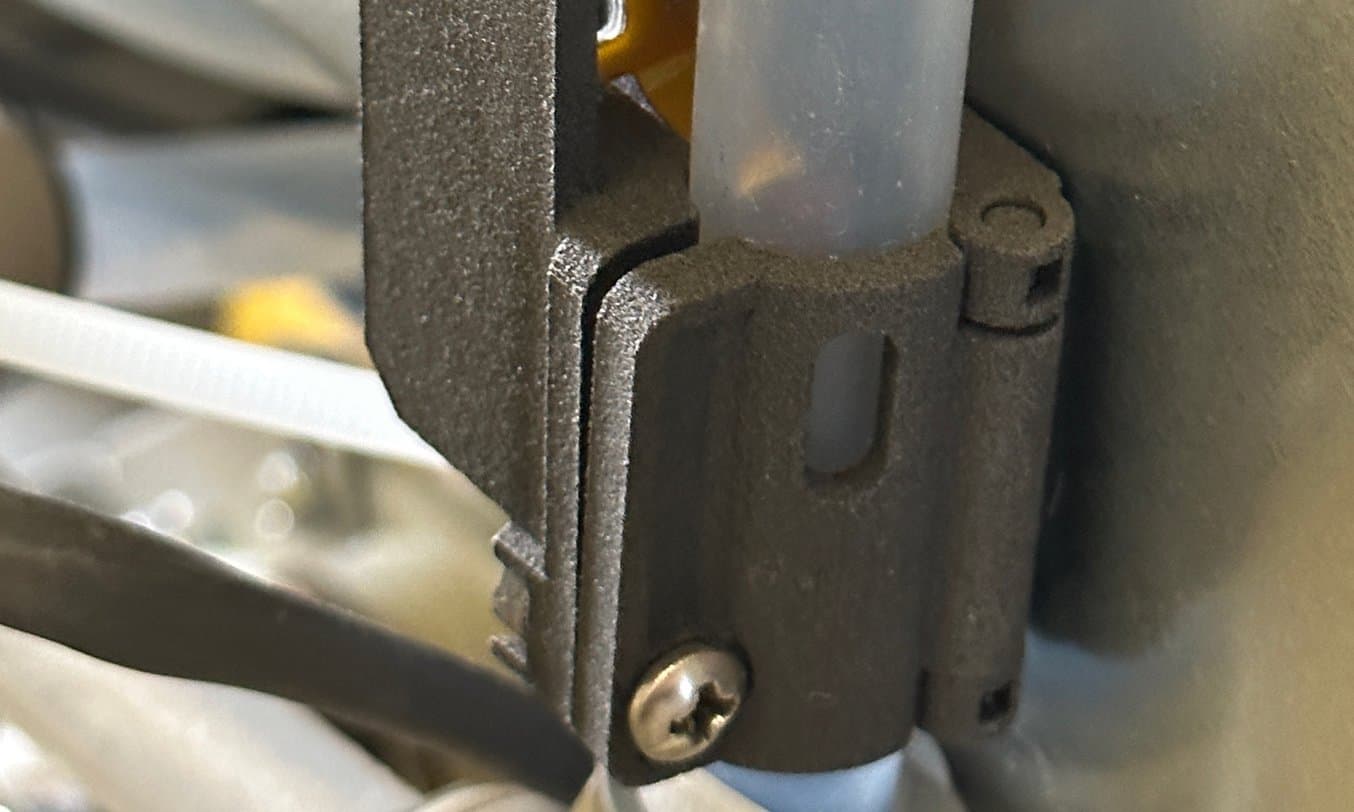
Diese Füllsensor-Komponente verfügt über ein funktionierendes Scharnier, das von Labconcos Produktingenieur Tim Grove anhand des standardmäßigen Probeteils aus Nylon 12 Powder entworfen wurde. Durch das Scharnier kann das Teil statt als mehrteilige Baugruppe als einzelne Komponente gedruckt werden, was Arbeitszeit und Materialkosten einspart.
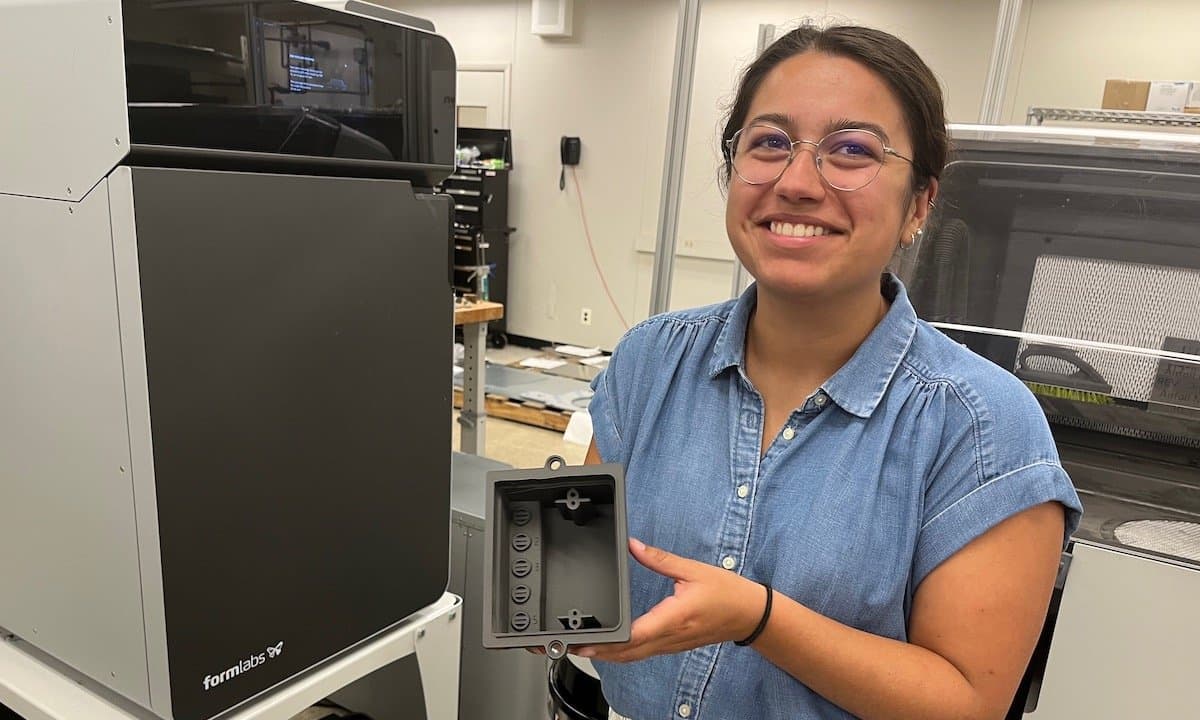
Da es dem Produktentwicklungsteam von Labconco gelungen ist, seine 3D-Druck-Anlage effektiv zu skalieren, haben viele Teammitglieder Zugang zu industriellen Technologien wie den SLS-Druckern der Fuse-Serie. Griffith zufolge untersuchen inzwischen mehrere Abteilungen des Unternehmens, wie sie den 3D-Druck in ihre typischen Prozesse einbeziehen können, um Kosten zu senken, Flexibilität zu erlangen und ihre Lieferketten abzusichern.
Labconcos Produktlinie Glassware Washer umfasst hochmoderne Lösungen der Ingenieurtechnik, unter anderem Bauteile aus additiver Fertigung. Eine Komponente, nämlich eine Halterung für einen Füllsensor, dient als Sicherung für den Überlaufschutz. Der konventionelle Ansatz wäre, diese Komponente mittels Spritzguss zweier separater Bauteile zu produzieren, die dann mithilfe eines Stiftes zusammengebaut werden.
Tim Grove, ein Produktingenieur bei Labconco, erkannte jedoch das Potenzial zur Kosten- und Zeiteinsparung durch die Fertigung mit SLS-3D-Druck. Inspiriert durch das Scharnierdesign in Formlabs' standardmäßigem Probeteil aus Nylon 12 Powder begann Grove, die Halterung für den Füllsensor neu zu konzipieren, wobei er darauf abzielte, die Montage effizienter zu machen und die Kosten für die Bestellung von Werkzeug zu senken.
Im Zuge iterativer Kollaboration mit Griffith entwickelte Grove mehrere Designversionen, um eine reibungslose Funktion und vorbehaltlose Leistungsfähigkeit zu gewährleisten.
„So wie das Teil aus dem Drucker kommt, ist das Scharnier bereits funktionsfähig und einsatzbereit. Das spart uns also Kosten ein und bringt Flexibilität in die Produktion. Das Nylon 12 Powder stellt für uns im frisch gedruckten Zustand ein gutes Polymer der Mittelklasse dar. Wir haben eine Menge Einsatzbereiche dafür und es funktioniert gut für uns“, berichtet Griffith.
SLS-Füllsensor | Anzahl der Bauteile | Arbeitszeit für die Montage (pro 50 Komponenten) | Kosten pro fertigem Teil (mit Arbeitszeit) | |
---|---|---|---|---|
Spritzgegossen | 3 | 1 Stunde | 4,45 €/Stück + Werkzeug | |
SLS-3D-gedruckt | 1 | 0 | 2,56 €/Stück |
SLA-Gebläselaufrad: Die Lösung für Produktobsoleszenz
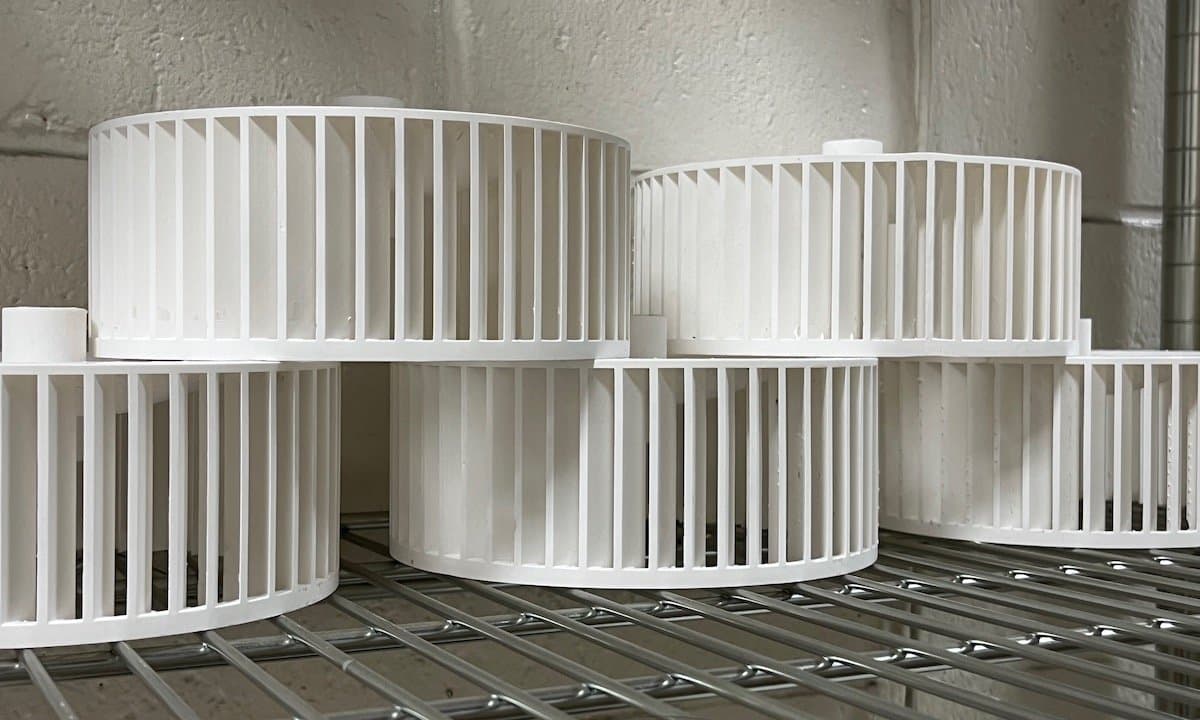
Diese Komponente für Labconcos Produkt Kjeldahl für die Kornanalyse wurde früher von einem externen Anbieter bereitgestellt – bis dieser die Produktion des Bauteils einstellte. Griffith erstellte mittels Reverse Engineering ein Modell von der Komponente und druckte dann auf dem Form 3L aus Rigid 10K Resin einen Monat lang täglich die neue Version, um das Ersatzteilinventar wieder aufzustocken und das Unternehmen vor Lieferkettenproblemen zu bewahren.
Für das Produkt Kjeldahl von Labconco, das zur Kornanalyse dient, arbeitete das Team mit einem externen Zulieferer zusammen, der ein Werkzeug für eine kritische Komponente des Gebläselaufrads herstellte. Da das Teil in niedrigen Stückzahlen gebraucht wurde, entschied sich der Zulieferer, dessen Produktion einzustellen, als das Produktionswerkzeug das Ende seiner Lebensdauer erreichte.
Labconco sah sich damit konfrontiert, einen neuen Zulieferer suchen zu müssen, auf Design und Produktion eines neuen Spritzgusswerkzeugs zu warten und hohe Kosten für Material und Arbeitszeit zu zahlen. „Wir sahen uns Dutzende verschiedene Lösungen an, aber keine erfüllte unsere Anforderungen auch nur annähernd, besonders in Bezug auf die chemische Kompatibilität. Also nahm ich mir am Ende ein Exemplar, betrieb Reverse Engineering, optimierte das Design und druckte es aus Rigid 10K Resin“, erzählt Griffith. „Nachdem wir durch Tests überprüften, dass es den Anforderungen standhält, stellte das für uns die beste Lösung dar.“
Der neue großformatige SLA-Drucker des Teams, der Form 3L, war gerade rechtzeitig angekommen – 40 Tage am Stück druckte das Team darauf das durch Reverse Engineering konzipierte Laufrad, um seinen Bestand dieser Komponente aufzustocken.
„Rigid 10K Resin ist unser Material der Wahl für mehrere Komponenten. Seine chemische Kompatibilität in Bezug auf Säuren entspricht dem, was wir benötigen – in diesem Fall vor allem hinsichtlich verdampfter Schwefelsäure. Durch den Umstieg auf additive Fertigung sparen wir Hunderte von Arbeitsstunden, die wir ansonsten vergeblich zur Verifizierung von Zulieferern und Materialien aufgewandt hätten. In der Hinsicht ist der geschäftliche Nutzen sehr hoch“, erklärt Griffith.
SLA-Gebläselaufrad | Kosten |
---|---|
Spritzgegossen | 178,77 € |
Neu entworfen und gedruckt in Rigid 10K Resin | 52,65 € |
SLS-Lagerkäfig: Von 500 € auf 20 € reduziert
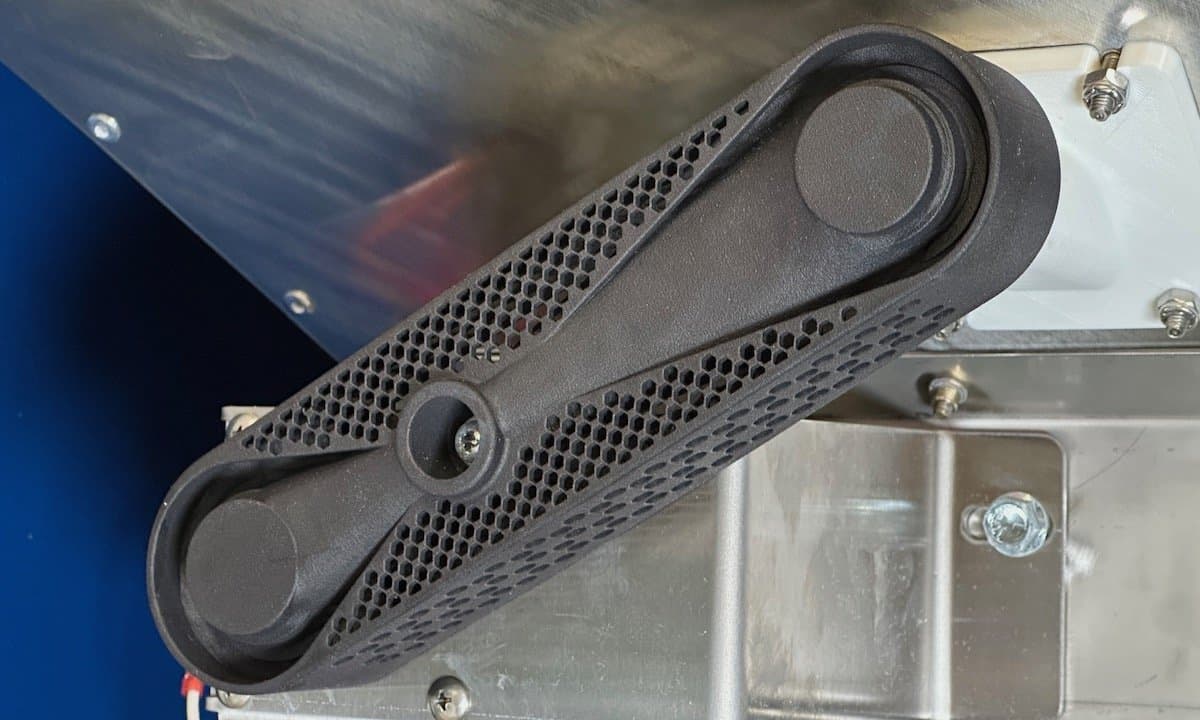
Dieses Teil hätte Griffith als exakte Kopie der Komponente drucken können, für die er von einer externen Metallwerkstatt ein Preisangebot von etwa 500 € bekommen hat. Stattdessen wandte er jedoch die Prinzipien an, die er an der Pennsylvania State University über additive Fertigung und Design gelernt hatte, und nutzte in seinem Design des Teils die geometrische Freiheit des SLS-3D-Druck aus. Die neue Komponente kostet Labconco ca. 21 €, sodass das Unternehmen Hunderterbeträge spart und zugleich seine Durchlaufzeit auf weniger als zwei Tage verkürzt.
Auch wenn ein Bauteil relativ simpel sein mag, kann seine Herstellung mit traditionellen Methoden dennoch kostspielig sein. Eine Metallwerkstatt machte für ein Bauteil, nämlich eine Lagerkäfig-Komponente, die zwei Lager abtrennt und deren Zusammenschieben verhindert, einen Kostenvoranschlag von etwa 500 € pro Stück. Dieses Bauteil wurde für ein neues Produkt benötigt. Da Labconco den Nutzen seines 3D-Drucklabors bereits belegt hatte, begann Griffith sofort mit dem Druck dieser Trennkomponente auf dem Fuse 1+ 30W und reduzierte den Preis auf etwa 45 € – also ein Zehntel dessen, was das Outsourcing an die Metallwerkstatt gekostet hätte.
Doch damit hörte die Optimierung des Prozesses noch nicht auf. Griffith wandte die Kenntnisse an, die er im Studium an der Pennsylvania State University zu additiver Fertigung und Design erworben hatte, und konzipierte den Prozess neu – aus einem einfachen Bauteilaustausch wurde ein komplettes Optimierungsprojekt.
„Das war genau das, was ich gelernt hatte: Wie man die opportunistischen und restriktiven Aspekte der additiven Fertigung anwendet. Statt also zu fragen, ob man etwas additiv fertigen kann, fragt man, ob man das sollte. In diesem Fall hätten wir das Teil 1:1 ersetzen können, aber dabei hätten wir die Chance verpasst, die Möglichkeiten der additiven Fertigung auszunutzen. Weil wir die Drucker der Fuse-Serie zur Verfügung hatten, die nur sehr wenig tatsächliche geometrische Einschränkungen vorgeben, konnte ich mich auslassen und neue Dinge probieren.“
Brent Griffith, Produktingenieur
Er experimentierte damit, mithilfe von generativem Design den Materialbedarf des gesamten Teils zu vermindern, wobei die schützenden Sicherheitsfunktionen des Lagerkäfigs erhalten blieben. Innerhalb eines Tages hatte Griffith ein überarbeitetes, optimiertes Design erstellt und Labconco begann, die Teile für etwa 20 € pro Stück intern durch SLS-3D-Druck zu produzieren.
„Der 3D-Druck liefert uns riesige Vorteile im Hinblick auf Geometrie. Wenn man eine leichte Version eines Teils erstellt oder verschiedene Designtechniken anwendet, lassen sich Komponenten auf noch nie dagewesene Weise kombinieren. Wir können die Fertigung in den eigenen Betrieb verlagern und eine Menge Geld sparen“, so Griffith.
SLS-Lagerkäfig | Kosten (inkl. Arbeitskosten) | Durchlaufzeit |
---|---|---|
Zerspant | 485,82 € | 2–3 Wochen |
1:1 SLS-Ersatz | 43,50 € | 29 Stunden |
Für SLS optimiert | 21,08 € | 28 Stunden |
SLS-Teile im Test: Weniger Komponenten bei gesteigerter Funktionalität
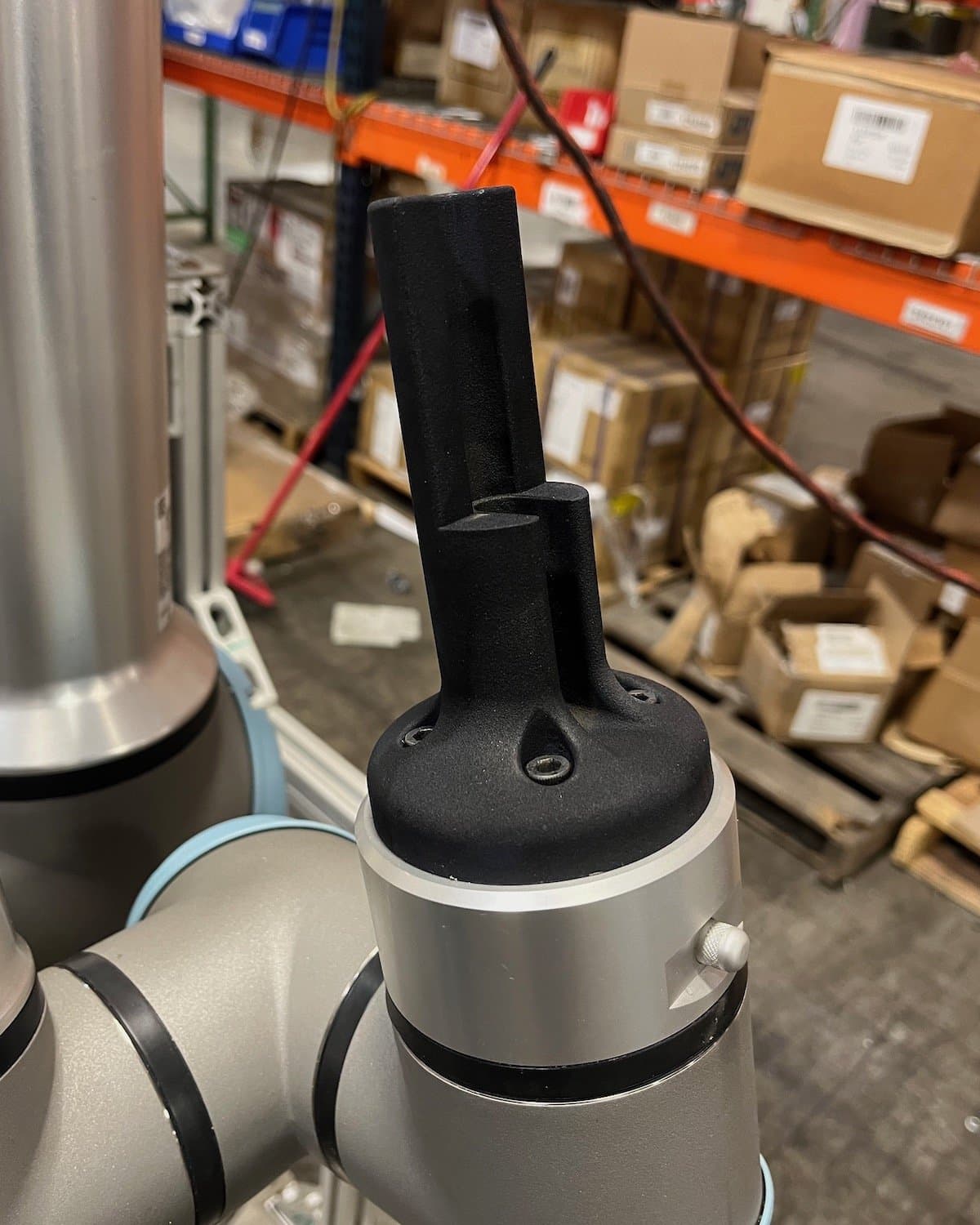
Um Labconco einen reibungslosen Umstieg auf einen hybriden Arbeitsprozess zu ermöglichen, bei dem manuelle und robotergesteuerte Arbeiten kombiniert werden, entwickelten Griffith und sein Team maßgefertigtes Werkzeug und Effektoren, die anschließend aus Nylon 12 Powder auf ihren Druckern der Fuse-Serie gedruckt wurden.
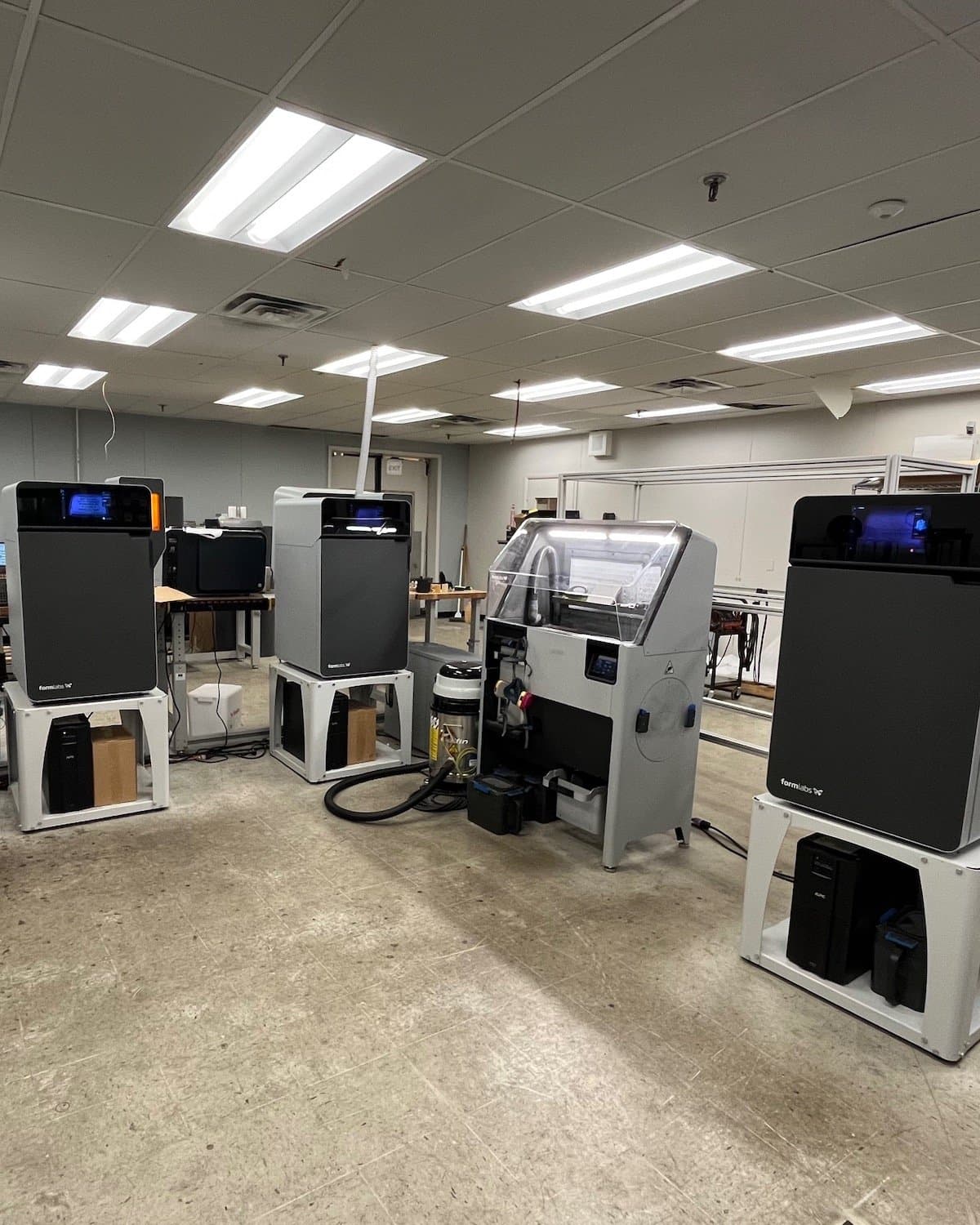
Die kompakte Größe und der niedrige Stromverbrauch der SLS-3D-Drucker der Fuse-Serie bedeuteten, dass Griffith und sein Team den SLS-Betrieb bei der Ausweitung ihrer Palette von Anwendungen für robuste, haltbare SLS-Teile ausreichend skalieren konnten.
Labconcos unermüdliches Streben nach Exzellenz erstreckt sich auch auf das Testen kritischer Komponenten, die in einem seiner zentralen Produkte zum Einsatz kommen: den biologischen Sicherheitswerkbänken. Diese Werkbänke spielen eine essenzielle Rolle beim Schutz des Personals und der Produkte, die in ihnen bearbeitet werden, und bauen auf bestimmten Luftstrommustern und HEPA-Filtern auf. Um ein höchstes Maß an Leistung zu gewährleisten, werden diese Filter strengsten Tests und Zertifikationsprozessen unterzogen, bevor sie für fertiggestellt erklärt werden.
In der Vergangenheit waren diese Prüfverfahren auf menschliche Arbeitskräfte angewiesen, wodurch es zu Uneinheitlichkeit und Einschränkungen kommen konnte. Labconco entschied sich jedoch für einen transformativen Ansatz und macht sich die Leistung robotischer Systeme zunutze, um das Scannen der Filter mit fehlerfreier Präzision zu automatisieren. Für diesen Umstieg auf Automatisierung war die Entwicklung von individuellem Werkzeug und Endeffektoren für die Roboterarme notwendig, welche die Tests durchführten. Mit traditionellen Fertigungsmethoden wäre das ein extrem kostspieliges Unterfangen gewesen, das Monate in Anspruch genommen hätte. Angesichts der niedrigen Stückzahlen, die benötigt wurden, war der 3D-Druck dieser Teile auf den Geräten der Fuse-Serie ein wichtiger Schritt in diesem transformativen Ansatz.
Dank der betriebsinternen Produktion der SLS-Teile auf dem Fuse 1+ 30W hat Labconco eine bemerkenswerte tägliche Nutzung der Komponenten erzielt und die Genauigkeit und Zuverlässigkeit seiner Produktsicherheitstests gesteigert. Diese entscheidende Implementierung additiver Fertigung hat nicht nur den Betrieb effizienter gemacht, sondern Labconco auch die Möglichkeit verliehen, eine vorbehaltlose Sicherheit und Leistungsfähigkeit seiner Produkte zu gewährleisten.
Effektor-Komponenten | Kosten |
---|---|
Zerspant | 508,32 € |
SLS-3D-gedruckt | 73,44 € |
Bauteil für Dunstabzug: Mittlere Produktionsvolumen mittels SLS für mehr Agilität
Labconco war das erste Unternehmen, das die Produktion von Dunstabzugshauben kommerzialisierte – heute eine seiner bedeutendsten Produktklassen. Dunstabzüge sind in großangelegten chemischen, pharmazeutischen oder landwirtschaftlichen Anlagen unverzichtbar.
Ein Bauteil dafür – ein Stopper, der verhindert, dass der Abdeckungsflügel über einen bestimmten Punkt hinaus geöffnet werden kann (und somit Energiekosten spart) – wurde zuvor mittels Spritzguss hergestellt. Da große Mengen des Teils bestellt werden mussten, die mit derselben Spritzgussform produziert wurden, konnte Labconco kaum Änderungen vornehmen oder Aufträge für große Kunden anpassen. Produktionswerkzeug verschleißt, und Zulieferer ersetzen dieses nicht immer zuverlässig. Um Lieferkettenproblemen entgegenzuwirken, begann das Team, die Stopper auf dem Fuse 1+ 30W zu drucken. Mittlerweile produziert Griffith pro Woche zwischen 50 und 100 Stück davon aus Nylon 12 Powder.
„Wenn man das Teil spritzgießt, kann man es nicht so leicht überarbeiten. Das kommt zwar erwartungsgemäß selten vor, aber wir hatten in der Vergangenheit bereits Komponenten, bei denen uns die Entscheidung für Spritzguss teuer zu stehen kam, denn als wir sie geliefert bekamen und einsetzten, gingen sie kaputt oder funktionierten nicht wie gewünscht. Jetzt ist den Ingenieuren bewusst, dass die Umstellung einiger Teile auf 3D-Druck Neuentwürfe viel weniger umständlich machen würde, falls das notwendig werden sollte, und dass mehr Optionen für Anpassungen offenstehen. Der Wert davon lässt sich nicht immer in Geldbeträge übertragen, und die additive Fertigung hat entscheidende ‚nicht greifbare' Vorteile, die meiner Meinung nach oft übersehen werden“, erklärt Griffith.
Ein weiterer Vorteil davon, 3D-Drucktechnologien in den eigenen Betrieb zu holen, ist das Vertrauen, dass es jungen Mitarbeitenden am Anfang ihrer Laufbahn verleiht. Wenn nicht der Anspruch besteht, bei der Bestellung eines neuen Werkzeugs absolute Perfektion zu erreichen, probieren Mitarbeitende bereitwilliger neue Dinge aus oder bringen Ideen hervor. „Die jüngeren Ingenieure haben keine 20-jährige Erfahrung, anhand derer sie entscheiden könnten, ob ein Teil funktioniert. Wenn es ihnen offen steht, ihre Ideen mit 3D-Druck auszuprobieren, sodass es keinen so großen oder überhaupt keinen Schaden verursacht, wenn es nicht funktioniert – das bekräftigt sie“, meint Griffith. „Die Möglichkeit zu haben, für jedes Problem die beste, kreativste Lösung zu suchen – das ist genau die Herangehensweise, die wir wollen, und da spielt der 3D-Druck eine zentrale Rolle.“
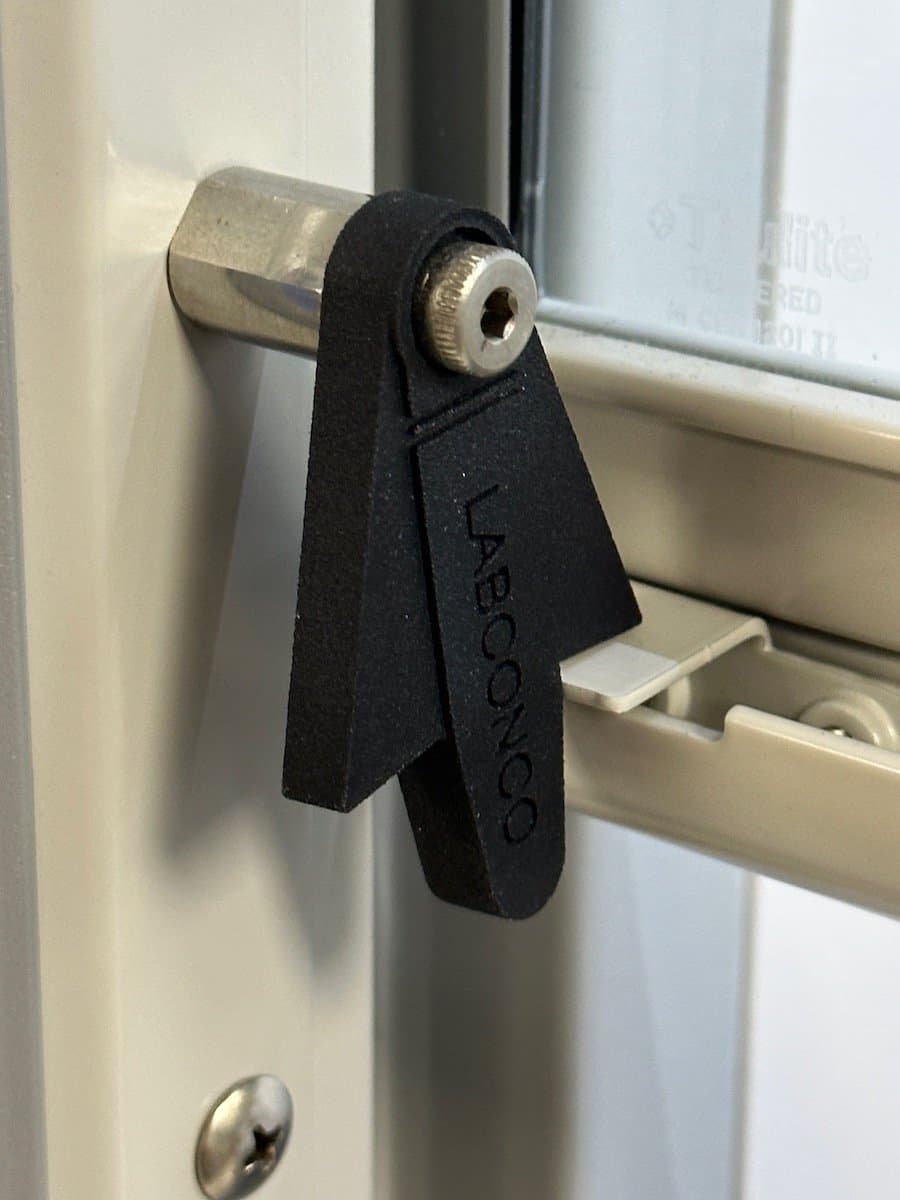
Griffith produziert auf dem Fuse 1+ 30W aus Nylon 12 Powder 50–100 Stopperbauteile pro Woche, wodurch er die Kosten und Risiken von Fertigungsprozessen umgeht, die auf Werkzeug aufbauen.
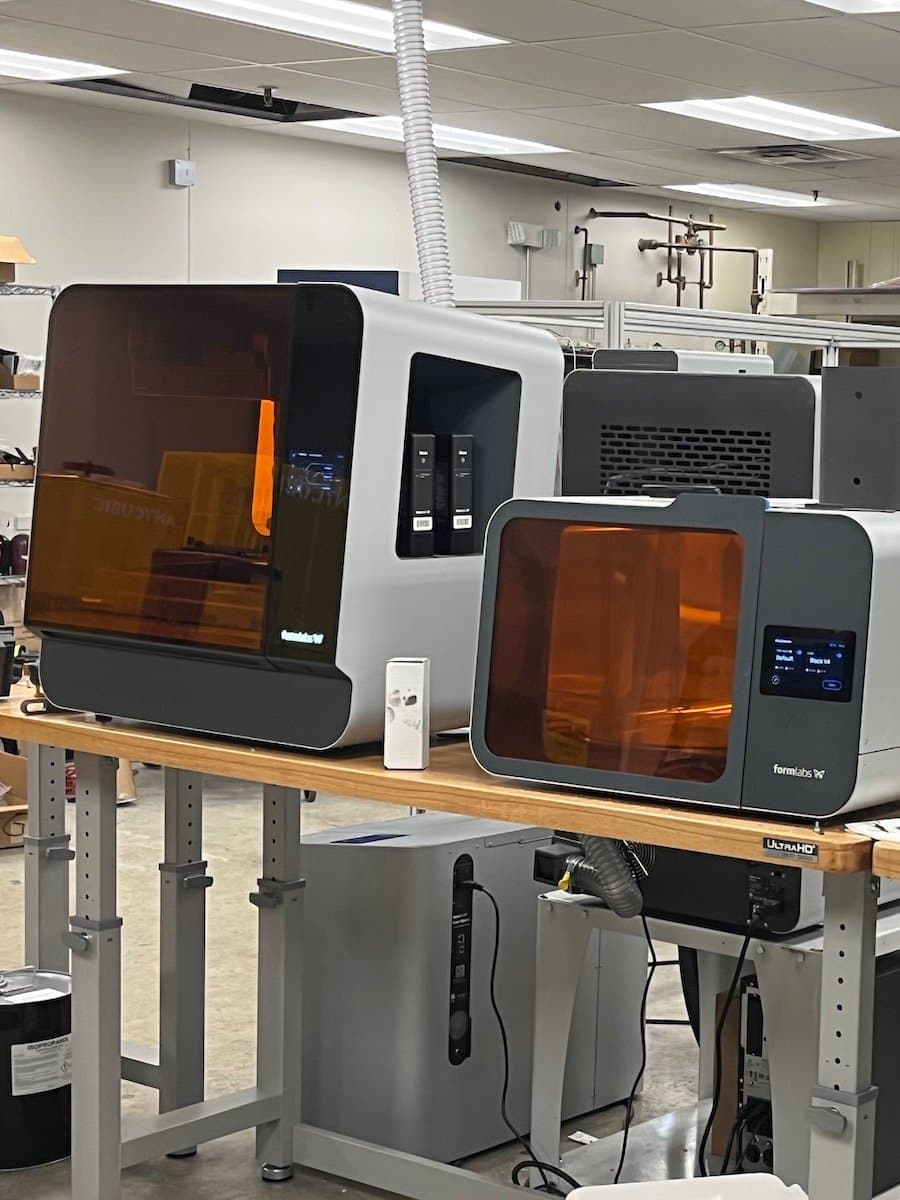
Die Benutzerfreundlichkeit der SLS- und SLA-Drucker (wie der hier gezeigte Form 3L und Form Cure L) geben jungen Teammitgliedern am Anfang ihrer Karriere die Möglichkeit, Erfahrung mit neuen Technologien zu erlangen und neue Ideen vorzubringen.
Der Fuse Blast komplettiert das SLS-Ecosystem von Labconco
Bei Produktionsvolumen von über einhundert SLS-Teilen pro Woche beanspruchten manuelle Nachbearbeitungsschritte wie das Sandstrahlen und Reinigen von Teilen bisher Stunden der Handarbeit – Zeit, die stattdessen für höherwertige Aufgaben in Design und Maschinenbau genutzt werden könnte. „Die Firma möchte, dass wir uns auf die Erkundung neuer Möglichkeiten, neue Designs zur Optimierung von Komponenten und die Einsparung von Kosten fokussieren, statt hier zu stehen und Teile von Hand zu reinigen“, erklärt Griffith.
Neben einer automatisierten Sandstrahlanlage aus dem oberen Preissegment ergänzte Labconco sein SLS-Ecosystem der Fuse-Serie durch einen Fuse Blast. Nach der zehnminütigen Installation konnte Griffith die Reinigung und das Sandstrahlen von zwei vollen Konstruktionskammern der Fuse-Serie automatisieren. „Die Installation war ein Kinderspiel. Das Gerät hat fast dieselbe Größe wie unsere manuelle Strahlanlage. Wer also Platz für eine manuelle Sandstrahlanlage hat, was auf jedes Unternehmen mit einem SLS-Drucker zutreffen sollte, der hat auch ohne Weiteres Platz für den Fuse Blast“, so Griffith.
Gesteigerte Qualität und Leistungsfähigkeit
Die Teams, die Teile von Labconco anforderten, bemerkten sofort einen Unterschied in deren Oberflächenglätte und Qualität.
„Der Fuse Blast hat gleich einen riesigen Unterschied gemacht. Jedem einzelnen von den Ingenieuren, denen ich Teile für das Prototyping lieferte, fiel die Veränderung auf – auch ohne dass ich ihnen erzählte, dass wir die Nachbearbeitung automatisiert hatten. Sie bemerkten sofort, dass weniger Pulverreste auf den Teilen waren und dass sie sich glatter und angenehmer anfühlten und besser aussahen. Es hat einen spürbaren Unterschied für die Teilqualität ausgemacht.“
Brent Griffith, Produktingenieur bei Labconco
Die glatten Oberflächen und die Behebung von Pulverrückständen hatten auch auf die Leistung der Teile einen unerwarteten Effekt – mit Bauteilen aus dem SLS-3D-Drucker, die im Fuse Blast gereinigt wurden, funktionierten Maschinen reibungsloser. „Wir haben bei einigen der gefertigten Komponenten sogar eine etwas bessere Leistung erzielt, weil sie so viel sauberer waren, vor allem bei der ersten Produktionscharge eines unserer Produkte im Zuge der Auftragsvergabe“, berichtet Griffith.
Das Team erreichte praktisch dieselben Ergebnisse wie mit dem automatisierten Strahlsystem aus dem oberen Preissegment. „Ich bemerke nicht wirklich einen Unterschied. [Der Fuse Blast] spielt definitiv weit oberhalb seiner Gewichtsklasse“, meint Griffith.
Kürzere Nachbearbeitung heißt mehr Zeit für Designoptimierung
Die Automatisierung mit dem Fuse Blast leistet viel mehr, als nur die Zeit für das manuelle Sandstrahlen von Teilen einzusparen – sie verkürzt auch die Bearbeitungszeit, die Griffith und sein Team am Fuse Sift benötigen. Früher hat sich eine längere Entpulverung im Fuse Sift gelohnt, um das manuelle Sandstrahlen zu beschleunigen. Jetzt durchläuft der Fuse Blast seine Zyklen jedoch automatisch und liefert saubere Teile, selbst wenn diese zu Beginn noch von einer Schicht Pulver bedeckt sind. „Ich kümmere mich jetzt viel weniger darum, wie viel Pulver wir [im Fuse Sift] ablösen, weil ich weiß, wozu der Fuse Blast in der Lage ist. Eine gründliche Reinigung der Teile im Fuse Sift bringt mir keine Zeitersparnis mehr. Und die geringfügige Pulvermenge, die wir durch eine gründliche Entpulverung im Sift auffangen würden, ist die zusätzlichen Arbeitskosten, die dabei entstehen, nicht wert“, erklärt Griffith.
Ein Teil, von dem wöchentlich konsistent 50 Stück produziert werden, hat Griffiths Team früher manuell sandgestrahlt und musste pro Teil drei Löcher mit einem Pfeifenreiniger freilegen. Mit dem Fuse Blast schaltet Griffith einfach einen automatischen Bearbeitungszyklus ein und geht weg. Wenn er nach 20–30 Minuten wiederkommt, erwartet ihn ein Set perfekt gereinigter Teile. „Der Blast ist ein phänomenales Gerät. Er bekommt auch Löcher fantastisch gesäubert, was für uns wahrscheinlich eine der größten Zeitersparnisse bedeutet“, so Griffith.
Skalierung des 3D-Drucks
Griffith und sein Team gingen beim Umstieg auf 3D-Druck systematisch vor – die erste Prüfung belegte den geschäftlichen Nutzen der ersten sechs erworbenen Geräte. Nun, da das Team weitere Kosten- und Arbeitseinsparungen ausfindig gemacht und Designs für einen umfassenden Katalog von Komponenten optimiert hat, möchte es seine 3D-Druck-Kapazitäten erhöhen.
„Jedes Mal, wenn mir ein Teil begegnet, ist meine erste Frage: Können wir mit additiver Fertigung etwas daran verbessern? Ich glaube, die Suche nach solchen Chancen ist der Bereich, womit wir das Meiste erreicht haben, das meiste Geld gespart haben oder die meisten Kosten für Komponenten eingespart haben“, urteilt Griffith.
Die Vorteile liegen für das gesamte Unternehmen auf der Hand – Teams, die für Kunden nach Optionen für spezifische Probleme oder Nischenanwendungen suchen, können dank der Möglichkeit der betriebsinternen Kleinserienfertigung kosteneffiziente Lösungen anbieten. „Selbst wenn Kunden nur fünf, zehn oder fünfzig Stück eines maßgefertigten Teils benötigen, können wir die Anfrage meist auf kosteneffiziente Weise bedienen. So können wir schnell auf Marktanforderungen reagieren“, erklärt Griffith.
Angefangen vom ersten Anwendungsbeispiel, das einen ganzen Raum verstummen ließ, hat Griffith inzwischen einen Geschäftsfall für Hersteller jeder Größenordnung entwickelt – die betriebsinterne Produktion mit SLA- und SLS-3D-Druck kann neue Anwendungen erschließen und Unternehmen zum Erfolg verhelfen, indem sie die Produkte verbessert, Lieferketten abschirmt und Kosten reduziert.
Um mehr über den Einstieg in den betriebsinternen SLA- und SLS-3D-Druck zu erfahren, buchen Sie eine Beratung mit unserem Vertriebsteam.