Formlabs präsentiert Flame Retardant Resin für den 3D-Druck in Hochleistungsanwendungen
Mit dem neuen Flame Retardant Resin präsentiert Formlabs sein erstes selbstverlöschendes und nach UL 94 V-0 zertifiziertes Material für den Stereolithografie-3D-Druck (SLA). Dieses speziell für die Branchen Transport, Luft- und Raumfahrt, Fertigung, Elektronik und das Gesundheitswesen entwickelte Kunstharz eröffnet neue Anwendungen in Bereichen mit streng regulierten Prozessen, wie etwa Folgende:
-
Kleinserien von Teilen für Luft- und Raumfahrt, Automobilindustrie und medizinische Umgebungen
-
Werkzeug und Fertigungshilfen für Umgebungen mit hohen Temperaturen oder Nähe zu Zündquellen
-
Elektronik- und Verbindungsgehäuse oder -abdeckungen
-
Elektronikanwendungen mit hoher Leistung (z. B. Transformatorspulen und Relais)
-
Wartung, Reparatur und Instandsetzung (MRO)
Ab jetzt ist es möglich, die Geschwindigkeit und Gestaltungsfreiheit des 3D-Drucks auszunutzen und gleichzeitig mit behördlichen Bestimmungen konform zu bleiben. Formlabs' leistungsstarke SLA-Technologie in Kombination mit Flame Retardant Resin bietet eine umfassende Lösung für Design und Fertigung von Teilen, die flammhemmende Eigenschaften gemäß UL 94 erfordern.
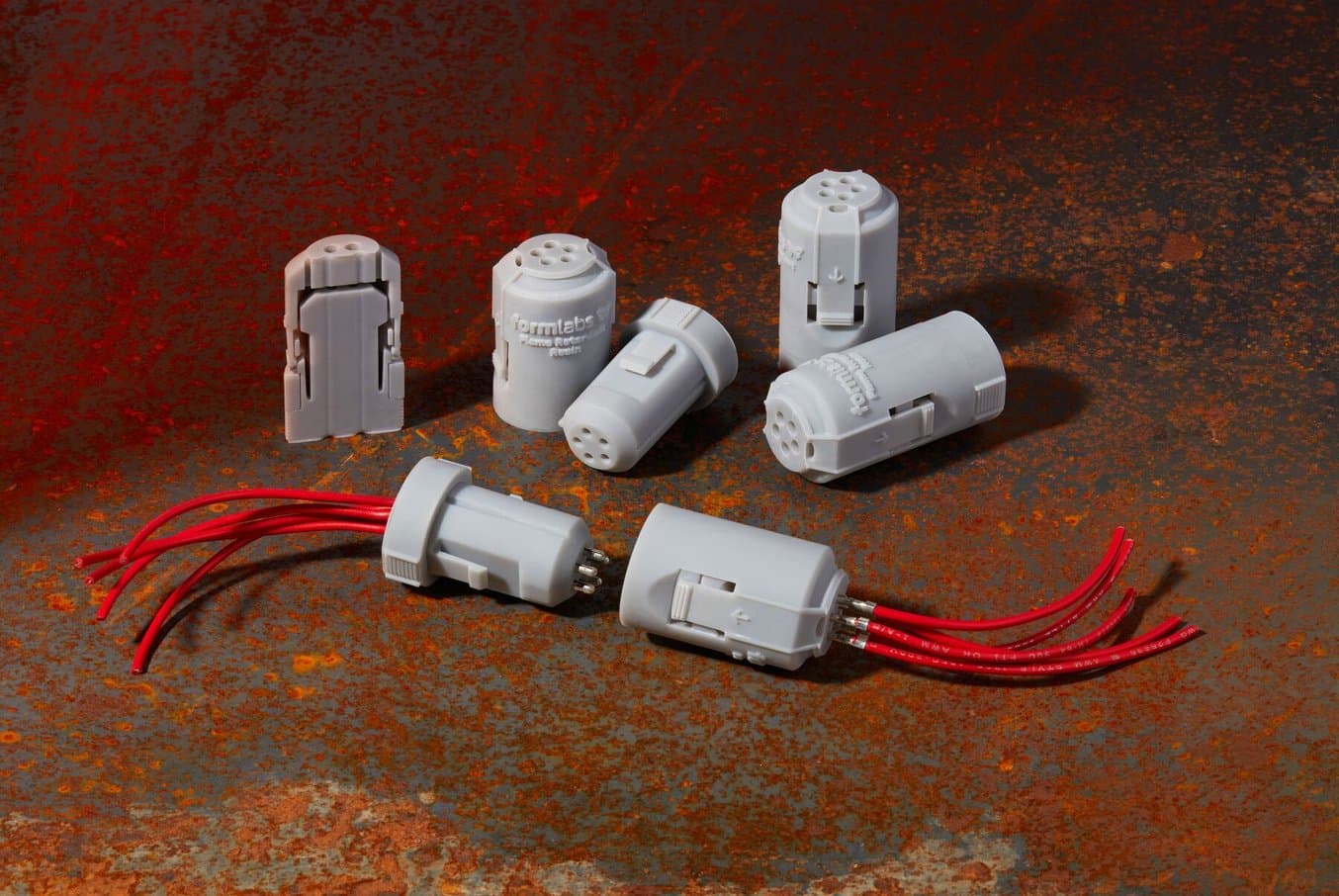
So eröffnet Flame Retardant Resin neue Anwendungen für Avance Design
Erfahren Sie, wie Sie mit Flame Retardant Resin mit Leichtigkeit flammhemmende, hitzebeständige, starre und kriechfeste Teile herstellen, die sich in Innenräumen und industriellen Umgebungen mit hohen Temperaturen oder Zündquellen auch langfristig bewähren.
Warum sollten Sie flammhemmende Teile 3D-drucken?
Vereinen Sie die Vorteile von traditioneller Fertigung und 3D-Druck
Für Hersteller in Branchen wie der Luftfahrt, Elektronik, Medizinprodukte-Fertigung und dem Transportwesen ist der Bedarf an flammhemmenden Teilen keine Neuheit. In derartigen Umgebungen mit vermehrtem Vorkommen von Funken, Äther oder Brennstoffquellen bedarf es strenger regulatorischer Kontrolle, um die Sicherheit des Arbeitsplatzes und der Produkte zu gewährleisten. Die maßgebliche Zertifizierung für solche Disziplinen ist UL 94 – eine Norm für die Brennbarkeit von Kunststoffen, die bestimmt, wie stark ein Material nach dem Entzünden zum Verlöschen oder zur Flammenausbreitung neigt. Flame Retardant Resin von Formlabs verfügt über die Blue-Card-Zertifizierung gemäß UL 94 V-0, erfüllt nach FAR 25.853(a) die Voraussetzungen bezüglich Flammenbildung sowie Tests zur Rauchbildung und Toxizität und hält gefährlichen Umgebungen mit offenen Flammen, Zündquellen und hohen Temperaturen stand.

Nach Entfernen der Zündquelle ist Flame Retardant Resin selbstverlöschend.
Herkömmlicherweise werden Kunststoffe, die diese Anforderungen erfüllen, entweder zerspant, spritzgegossen oder gegossen. Für diese Verfahren sind meist teure industrielle Geräte oder stundenlange manuelle Arbeiten nötig. Viele Unternehmen lagern die Fertigung daher an Metallwerkstätten oder Spritzgussdienstleister aus, was jedoch wochenlange Lieferzeiten oder hohe Bearbeitungsgebühren mit sich zieht. Kostengünstigere, intern durchführbare Methoden wie das Gießen erfordern wiederum einen mehrteiligen Prozess zum Guss von Silikon oder Polyurethan auf Basis zerspanter oder 3D-gedruckter Formen. Üblicherweise sind sowohl Outsourcing als auch betriebsinterne Arbeitsprozesse entweder zu teuer oder zu ineffizient und arbeitsintensiv, um sie dauerhaft zu nutzen, sodass sie für potenzielle Anwendungen mit Bedarf einer UL-94-Zertifizierung nicht in Frage kommen.
Durch Fortschritte bei einigen 3D-Druckmaterialien sind stark hitzebeständige oder flammhemmende Materialien bereits verfügbar geworden, allerdings unter Vorbehalten. Viele Hersteller von FDM-3D-Druckern (Schmelzschichtung) bieten flammhemmende Filamente an, die Druckteile eignen sich jedoch nicht für Funktionstests, Endverbrauchsteile zur Präsentation vor Kunden oder zur Nutzung für Wartung und Reparatur. Für andere Technologien wie den SLA-3D-Druck waren bereits hochgradig temperaturbeständige 3D-Druckmaterialien erhältlich, die isotrope, starke Teile mit hervorragender Oberflächenqualität produzieren, allerdings nicht UL-94-zertifiziert waren.
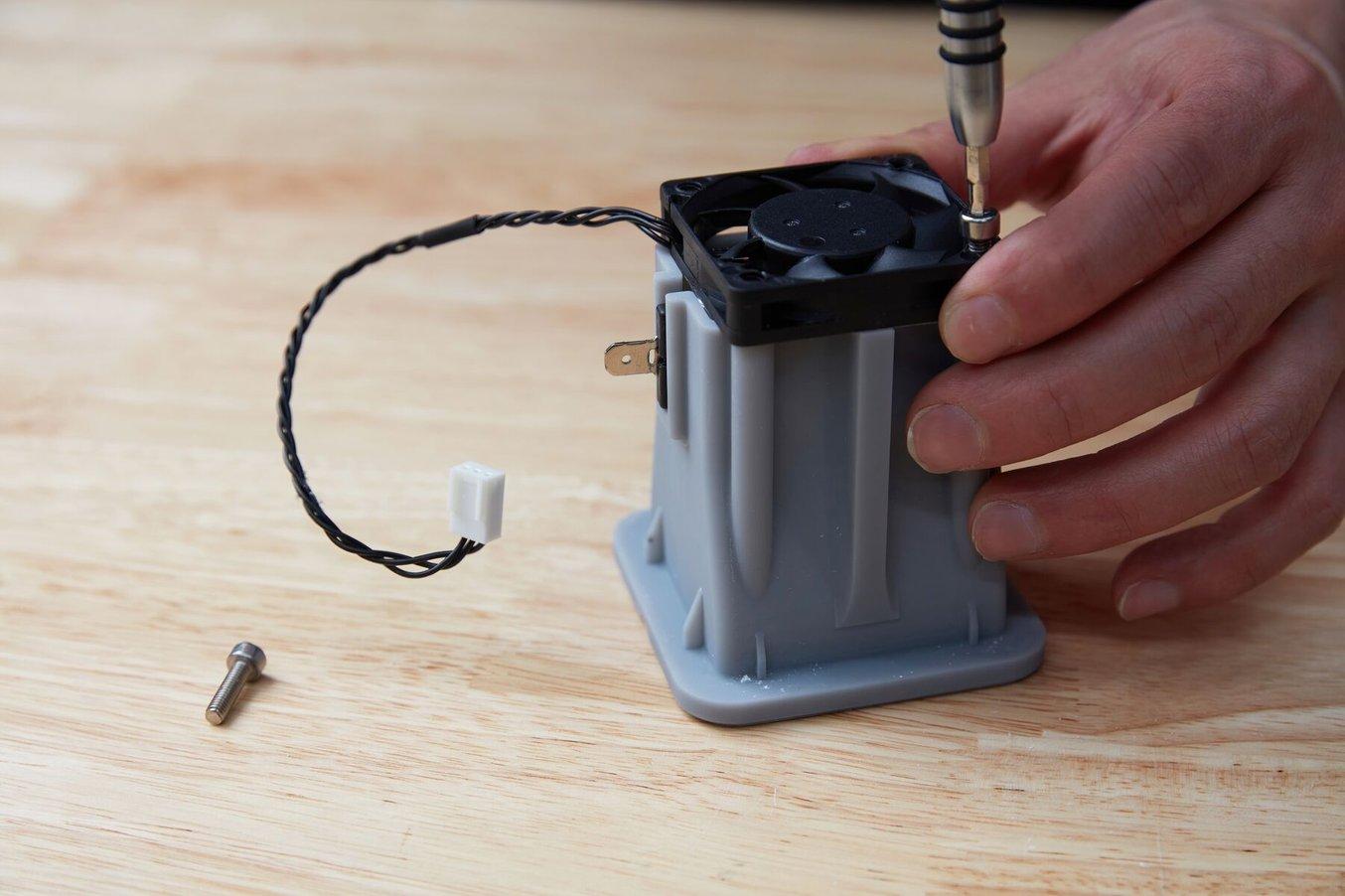
Teile aus Flame Retardant Resin (hellgrau) eignen sich als Bauteile in funktionalen Baugruppen und halten Nacharbeiten wie Bohren, Gewindebohren und Zuschneiden stand.
Flame Retardant Resin vereint alle Vorteile, um Hochleistungsanwendungen und zertifizierte, sichere Arbeitsprozesse möglich zu machen, mit der Zugänglichkeit und Leistungsstärke von Formlabs' SLA-Ecosystem. Nach dem Nachhärten bei 80 °C für 120 Minuten erzielen Teile aus Flame Retardant Resin eine Wärmeformbeständigkeitstemperatur (HDT) von 111 °C bei 0,45 MPa und einen Zugmodul von 3,1 GPa. Während andere Materialien für den Einsatz bei hohen Temperaturen spröde sein können, lassen sich Teile aus Flame Retardant Resin als Komponenten in funktionalen Baugruppen einsetzen und können für Gewindeeinsätze angebohrt werden. Die Druckteile sind starr und kriechfest, sodass sie in industriellen Umgebungen und Innenräumen konsistente Leistung erbringen. Im Gegensatz zu vielen FDM-Teilen weist Flame Retardant Resin eine glatte, matte Oberflächenbeschaffenheit mit scharfen Kanten und einer hohen Maßgenauigkeit auf. Somit eignen sich die Druckteile auch für die Endverwendung oder für Baugruppen mit engen Toleranzen.
Bruchzähigkeit (KIC) | Bruchzähigkeit (Wf) | Schlagfestigkeit | Zugmodul | Maximale Zugfestigkeit | Bruchdehnung | HDT bei 0,45 MPa | |
---|---|---|---|---|---|---|---|
Flame Retardant Resin | 2,17 | 848 | 22 J/m | 3,1 GPa, 2,9 GPa* | 41 MPa, 39 MPa* | 7,1 %, 9,4 %* | 111 °C, 94 °C* |
High Temp Resin | 0,55 | 47 | 18 J/m | 2,8 GPa | 58 MPa | 3,3 % | 142 °C |
Tough 2000 Resin | 3,61 | 3060 | 40 J/m | 2,2 GPa | 46 MPa | 48 % | 63 °C |
Grey Pro Resin | 1,76 | 541 | 19 J/m | 2,6 GPa | 61 MPa | 13 % | 78 °C |
Clear Resin | Keine Angabe | Keine Angabe | 25 J/m | 2,8 GPa | 65 MPa | 6,2 % | 73 °C |
Es gibt zwei Nachhärtungsoptionen für Flame Retardant Resin. Das technische Datenblatt verdeutlicht die Auswirkungen der verschiedenen Optionen auf die mechanischen Eigenschaften. Wählen Sie anhand dieser Informationen die Nachhärtungsoption, die sich am besten für die gewünschte Anwendung eignet. Für die maximale Wärmeformbeständigkeitstemperatur von 111 °C bei 0,45 MPa, härten Sie die Teile im Form Cure 120 Minuten lang bei 80 °C nach. Bei Anwendungen, die nicht die maximale Hitzebeständigkeit benötigen, aber von höherer Zähigkeit profitieren, härten Sie die Teile im Form Cure 60 Minuten lang bei 70 °C nach.
Erschließung neuer Anwendungen und Abläufe
Branchen wie die Luft- und Raumfahrt und Automobilindustrie integrieren den 3D-Druck häufig in ihre Prototyping-Prozesse, müssen aber meist bereits in der Entwicklungsphase zu traditionellen Fertigungsmethoden übergehen, um die behördlichen Vorgaben hinsichtlich der Entflammbarkeit zu erfüllen. Die meisten 3D-Druckmaterialien verfügen zwar über die Festigkeit und die Temperaturbeständigkeit, um auch Funktionstests zu widerstehen, jedoch nicht über die erforderliche UL-Zertifizierung. Mit Flame Retardant Resin verkürzen große Unternehmen jetzt nicht nur ihre Entwicklungsphasen, sondern können auch teamübergreifend dasselbe Material verwenden, von Design über Wartung und Reparatur bis hin zur Fertigung von Vorrichtungen.
In vielen Branchen müssen Bauteile für Wartung und Reparatur beim Erstausrüster bestellt werden, um die Konformität des Produkts zu gewährleisten. Der SLA-3D-Druck war für gewöhnlich keine taugliche Option, trotz seiner geringen Stückkosten und hohen Effizienz. Dank Flame Retardant Resin dient der SLA-3D-Druck nun endlich auch hier als Lösung zur Fertigung von Ersatzteilen auf Abruf.
Skalierbare Plattformen wie der Form 3+ und der Form 3L gestatten es großen Teams, ohne umfassende Investitionen die Kapazität ihrer 3D-Druckerflotte zu steigern, indem sie dem gesamten Team Zugang zu einem flammhemmenden, selbstverlöschenden, zähen und robusten Material gewähren, das für den Einsatz in Praxisanwendungen bereit ist.
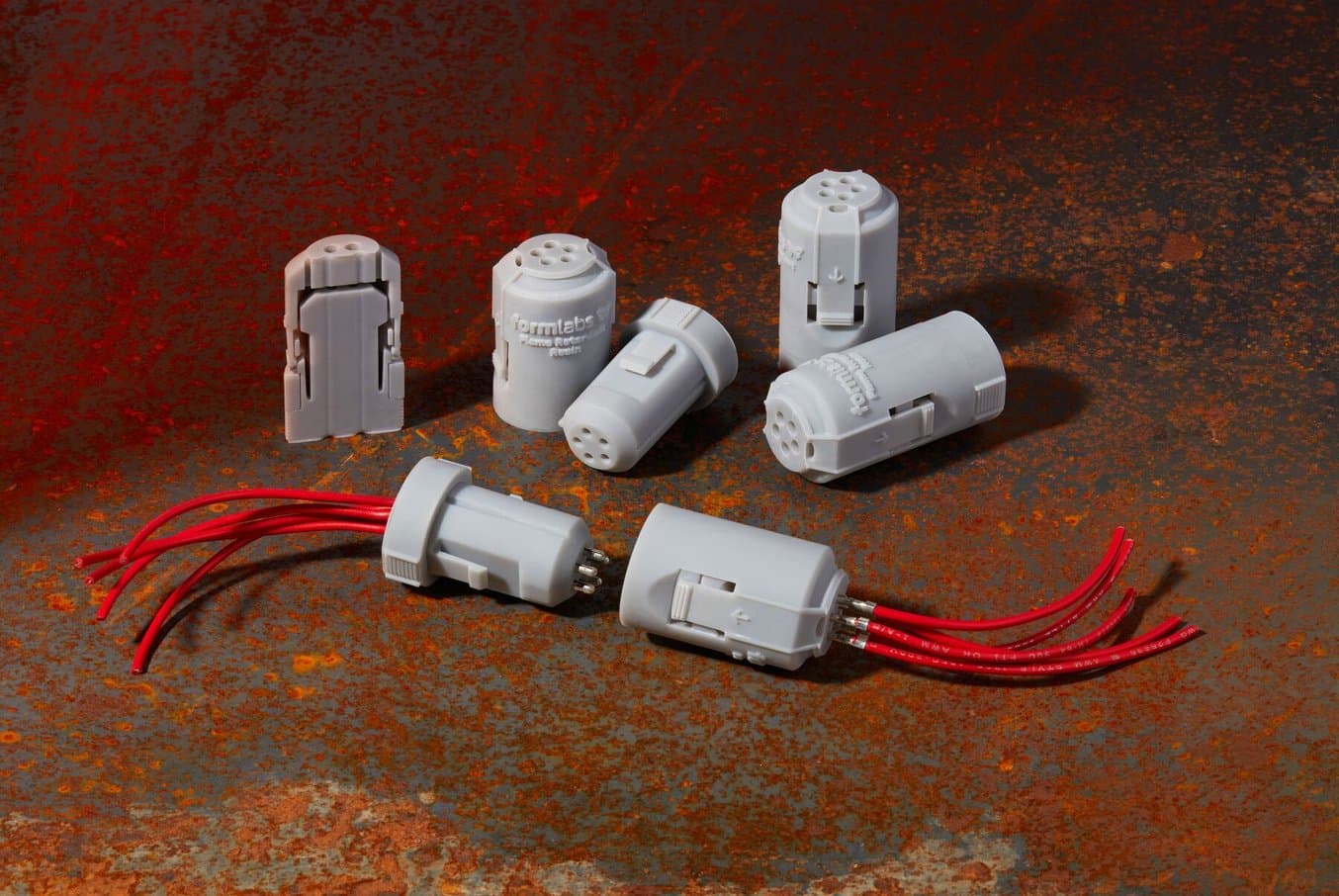
Mit flammhemmenden Teilen werden neue Möglichkeiten für den 3D-Druck im Transportwesen, der Luft- und Raumfahrt, Fertigung und Elektronik erschlossen.
Beschleunigen Sie die Markteinführung
Der Produktentwicklungsprozess von der Phase des iterativen Designs bis zu Kleinserien von Endverbrauchsteilen kann mithilfe von Flame Retardant Resin deutlich effizienter werden. Mit Flame Retardant Resin und den Formlabs-Druckern Form 3+ oder Form 3L lässt sich das Rapid Prototyping mit demselben Material umsetzen, das auch in Funktions- und Umgebungstests sowie der Produktion kleiner und mittelgroßer Chargen für Erstanwender zum Einsatz kommt. Die Verwendung eines einzigen Materials während des gesamten Prozesses macht es möglich, Designänderungen zu vermindern und sich voll auf die Leistung der Teile und Anwenderfeedback zu konzentrieren. Starke, funktionale Teile, die jegliche behördliche Auflage erfüllen können, unterstützen Unternehmen dabei, ihre Produkte an den Kunden zu bringen und Marktchancen auszunutzen.
Fallstudien: Anwendungen für flammhemmende 3D-Druckteile
NZ Technologies: Medizinprodukte für die Endverwendung
NZ Technologies (NZTech) ist spezialisiert auf das Design und die Fertigung fortschrittlicher Produkte für Human Machine Interaction (HMI), wie etwa berührungslose Visualisierungsplattformen für medizinische und chirurgische Anwendungen. Die Anwendungsumgebungen vieler dieser Produkte erfordern von Anfang bis Ende UL-zertifizierte Komponenten. Bei medizinischen Anwendungen wie etwa Medizinprodukten müssen die Produkte aus flammhemmenden und selbstverlöschenden Materialien hergestellt sein, um den Anforderungen zum Einsatz im OP-Saal zu genügen. Um den Designprozess zu optimieren, werden sogar visuelle Prototypen aus denselben Materialien hergestellt.
Das Team von NZTech nutzte bisher einen Filament für den FDM-Druck, um Prototypen seines Produktes TIPSO® AirPad zu fertigen, einer berührungslosen Schnittstelle für Chirurgen. Die Druckteile wiesen jedoch eine mangelhafte Auflösung und Genauigkeit auf. NZTechs leitender Hardware-Ingenieur Jordan Karyanto benötigte also die Auflösung und Leistungsstärke des Form 3+ sowie die UL-94-Zertifizierung, damit er sowohl die internationale Verordnung IEC60601-1 als auch die europäische Norm EN60601-1 zur Zertifizierung seiner Produkte erfüllen konnte. Als Erstanwender von Flame Retardant Resin war er in der Lage, diese Vorteile in einem einzigen effizienten Arbeitsprozess zu vereinen.
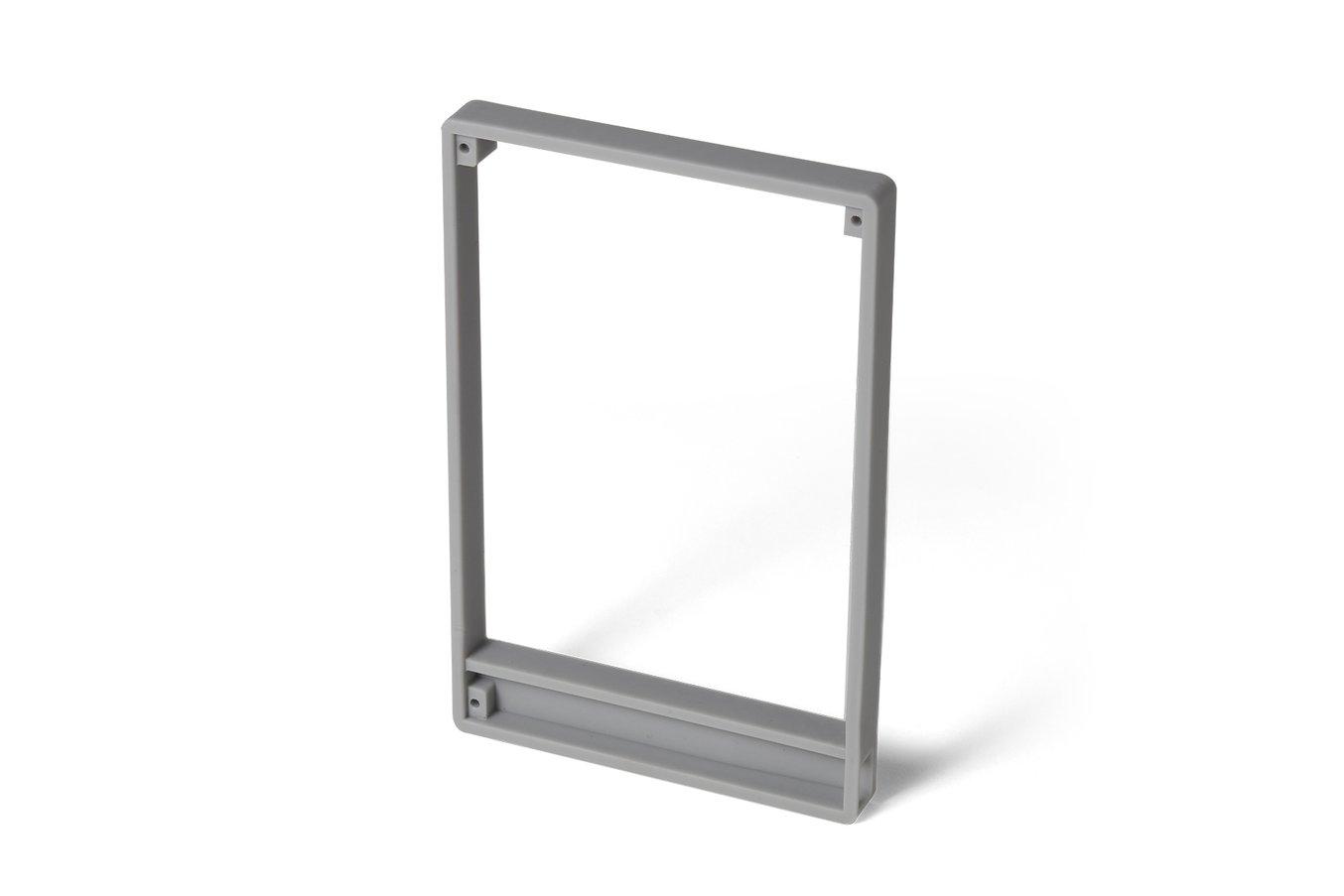
NZ Technologies druckte aus Flame Retardant Resin dieses Gehäuse für das Produkt TIPSO® AirPad, ein Gerät zur Visualisierung, das von Chirurgen im OP-Saal verwendet wird und eine UL-Zertifizierung erfordert.
Karyanto und sein Team stützen sich zur Fertigung maßgenauer Teile mit wenig Nachbearbeitungsbedarf auf den Form 3+, damit die Teile für Prüf- und Zertifizierungsverfahren in anderen Branchen bereit sind. „Wenn wir Teile für Tests herstellen, müssen diese in Optik und Funktion dem Endprodukt entsprechen. Wir wollen elektronische Komponenten leicht in Gehäuse einfügen können, deshalb ist uns Maßgenauigkeit wichtig. Wenn wir das Gehäuse aus flammhemmenden Materialien herstellen, wird es auch in der Testphase akzeptiert, sodass wir Funktionalität und Konformität in einem erfüllen“, so Karyanto.
Wir führen eine Menge Demo-Tests durch, deshalb ist dieses Kunstharz für uns sehr hilfreich. Wenn wir ein Produkt herstellen müssen, das für den Einsatz im OP bestimmt ist, dann ist Flame Retardant Resin eine nützliche Option für das funktionale Prototyping und Testsituationen mit offenen Flammen.
Jordan Karyanto, leitender Hardware-Ingenieur bei NZTech
Avance: Kleinserien von Endverbrauchsteilen
Avance Design, ein Beratungsunternehmen im Bereich Produktentwicklung und Maschinenbau in Indianapolis, Indiana, USA, nutzt 3D-Drucktechnologien bereits seit über einem Jahrzehnt – dennoch entdeckt das Team in jedem neuentwickelten 3D-Druckmaterial neue Chancen und Anwendungsmöglichkeiten. Wir haben uns mit Tony Parker, Direktor bei Avance Design, über seinen Arbeitsprozess mit Flame Retardant Resin unterhalten.
Abgesehen vom Guss, Spritzguss, Zerspanen und FDM-Druck nutzt Avance drei SLA-Drucker des Typs Form 3+ und zwei Form 3L, um Produkte für die Gesundheits-, Robotik-, Architektur- und Elektronikbranche zu entwickeln. Um Bauteile für einen Kunden aus der Elektronikbranche zu produzieren, musste Avance normalerweise auf einen Gussprozess mit Polyurethan zurückgreifen. Hierfür stellte Tony Parker ein Modell über 3D-Druck oder Zerspanung her, konstruierte eine Silikonform um das Modell herum, beschaffte ein kommerziell verfügbares, UL-zertifiziertes Polyurethan und goss es in die Silikonform, um das Gussteil aus Polyurethan anschließend zu entnehmen und nachzubearbeiten. „Jedes einzelne Teil brauchte Tage, und wir hatten Bestellungen über 20 Stück, was etwa drei Wochen beanspruchte“, erinnert sich Parker.
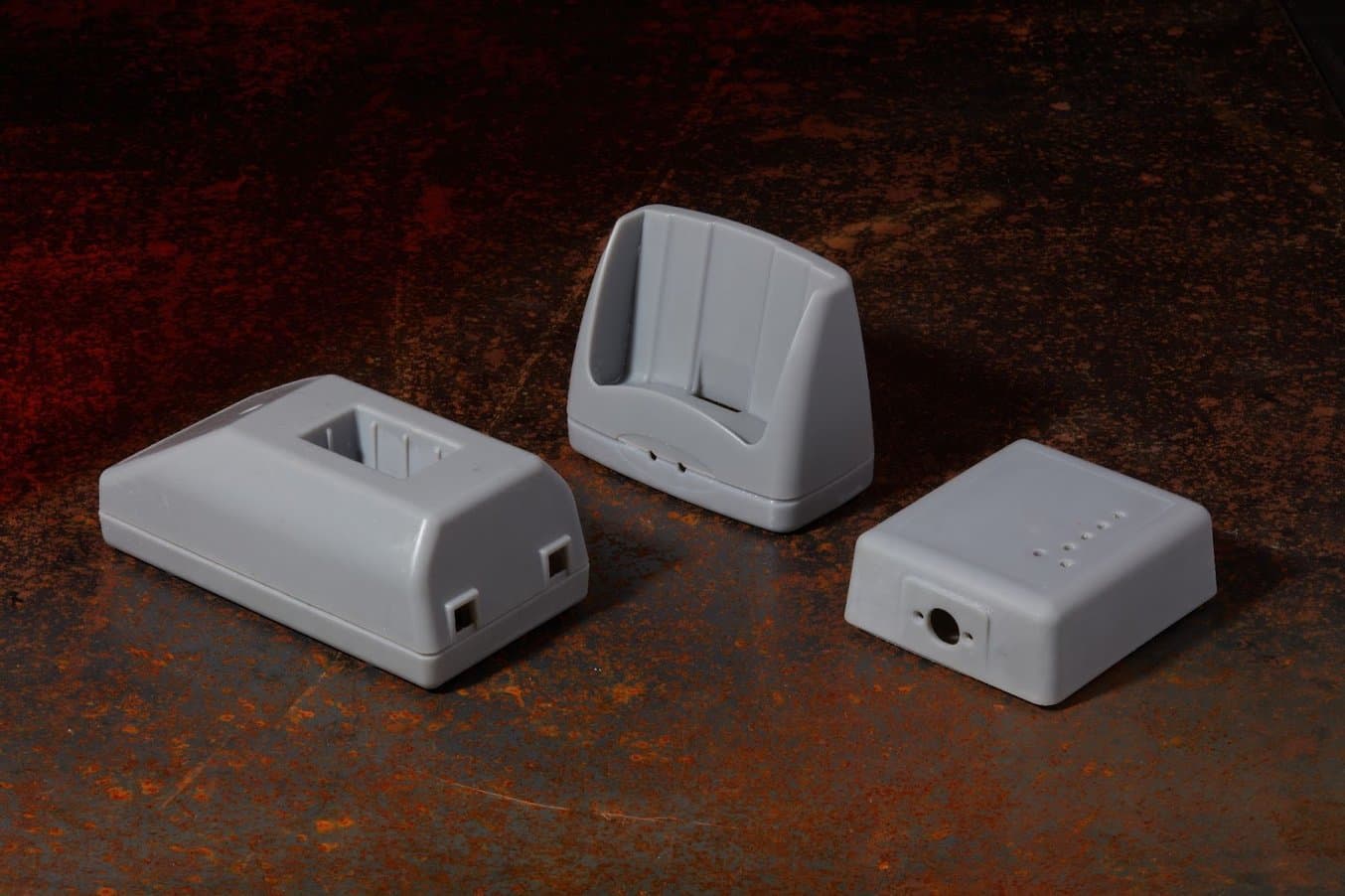
Avance nutzt Flame Retardant Resin für Teile wie diese, die von Kunden aus dem Transportwesen, der Luftfahrt, Fertigung, Elektronik, dem Gesundheitswesen und der Raumfahrt angefordert werden.
Dank Flame Retardant Resin kann Parker nun mehrere Arbeitsschritte überspringen und erheblich schneller vom CAD-Design zum fertigen Bauteil übergehen. „Dass ich das Teil direkt in Flame Retardant Resin 3D-drucken kann, verkürzt die Fertigungsdauer für alle 20 Teile auf ungefähr eine Woche“, so Parker.
Zusätzlich zur Verringerung des Zeit- und Arbeitsaufwands für die Herstellung UL-zertifizierter Teile ermöglicht der SLA-Arbeitsablauf mit Formlabs-Druckern und Flame Retardant Resin auch Gestaltungsfreiheit, eine erstklassige Oberflächenqualität und starke, haltbare Teile, die zusätzlichen Belastungsfaktoren wie Schrauben widerstehen.
3D-gedruckte Teile zu erhalten, die sich wirklich wie Thermoplaste verhalten, eine gute Oberfläche und feine Details aufweisen und ähnliche mechanische Eigenschaften bieten wie Spritzgussteile, ist ein großes Plus und spart viel Zeit. Mit Flame Retardant Resin können wir vom CAD-Design direkt zum fertigen Teil übergehen, ohne die zusätzlichen Arbeiten, die bei anderen Verfahren anfallen.
Tony Parker, Direktor von Avance
Legen Sie los mit dem 3D-Druck flammhemmender Teile
In stark regulierten Branchen, bei denen Sicherheit an erster Stelle steht, hat der 3D-Druck in der Vergangenheit bereits den iterativen Designzyklus optimiert und durch seine Gestaltungsfreiheit und erschwingliche Produktionswerkzeuge Innovationen ermöglicht. Mit Materialien wie Flame Retardant Resin legt Formlabs den Fokus jetzt speziell auf Hindernisse, die bisher Markteintrittshürden für kleine Unternehmen bedeutet haben oder den Fortschritt in großen Unternehmen verlangsamt haben.
Einige der Barrieren, die im Produktdesign beim Übergang von visuellen Modellen zu Funktionstests oder Kleinserien vom Endprodukten auftraten, werden durch Flame Retardant Resin bereits beseitigt. Mit den notwendigen Zertifizierungen für den Einsatz in der Fertigung, Luft- und Raumfahrt, Automobilindustrie und Elektronikbranche ist Flame Retardant Resin in der Lage, Arbeitsprozesse zu optimieren und die Iterationsschleife zu verkürzen.
Um mehr über die Materialeigenschaften zu erfahren oder selbst ein Probeteil zu testen, kontaktieren Sie unser Vertriebsteam oder fordern Sie einen 3D-Probedruck an.