Wie man zu einer Leitfigur der digitalen Fertigung wird und aus dem Nichts ein Labor aufbaut
Marco De Rossi kam von Kolumbien nach Europa, um am Polytechnikum Mailand Produktdesign zu studieren. Damals waren 3D-Drucker noch ein seltener Anblick, selbst an Universitäten. Mit der Technologie arbeiten zu können, überzeugte ihn von ihrem Potenzial und so entschied er sich, einer Promotion in digitaler Fertigung in der Medizin an der Polytechnischen Universität Valencia nachzugehen.
Im Gegensatz zur gut ausgestatteten Universität in Mailand – mit Laserscannern, 3D-Druckern und fortschrittlichen Visualisierungsgeräten – fehlte es der neuen Hochschule an digitalen Fertigungswerkzeugen. Und so war sein erster Schritt, ein Labor aus dem Boden zu stampfen. „Ich musste erst ein 3D-Drucklabor einrichten, bevor ich überhaupt mit meinem Promotionsstudium beginnen konnte“, erzählt De Rossi.
Trotz knapper Ausgangsfinanzen entwickelte sich De Rossi zu einer Leitfigur der digitalen Fertigung und baute ein Labor mit drei Räumen und einer breiten Palette an Werkzeugen auf, das sich mittlerweile selbst trägt. Auf seinem Weg arbeitete er mit Forschern, Ingenieuren und Ärzten zusammen an zahlreichen Projekten wie anatomischen Modellen, Ersatzteilen eines Röntgenapparats und dem Reverse Engineering für eine Luftfahrtanalyse.
Im Folgenden erhalten Sie praktische Tipps zur Einrichtung eines Labors, wie man an die nötigen Ressourcen gelangt, mit anderen kollaboriert und engagierte Mitarbeiter findet.
Vier Tipps zur Einrichtung eines digitalen Fertigungslabors
Klein anfangen und Erfahrung sammeln
Ein Labor aus dem Boden zu stampfen, klingt zunächst nach einer überwältigenden Aufgabe. De Rossi zufolge ist es jedoch leichter, wenn man sie in kleine Schritte mit klaren Zielen unterteilt.
„Aller Anfang ist schwer, aber man muss halt irgendwo beginnen. Ich schlage vor, man besorgt sich die Erlaubnis zur Einrichtung eines festen Bereichs an der Uni und sammelt Erfahrung mit der digitalen Fertigung. Mit dieser Erfahrung kann man dann nach Fördergeldern fragen. Keinesfalls darf man warten, bis man das Startkapital zusammen hat. Irgendwo muss man anfangen, und wenn es mit einem billigen Drucker zum Experimentieren ist. Dann kann man schon einmal etwas vorführen und Leute begeistern“, berichtet De Rossi.
„Danach kann man sich um Förderung bewerben und Unterstützung von anderen Forschern anfragen. Ich habe nicht mit mehr angefangen als mit einem Raum und billigen Geräten aus zweiter Hand. Unser größter Durchbruch war wahrscheinlich die Genehmigung der Fördergelder. Endlich hatten wir 20 000 € zum Kauf der Ausrüstung. Aber man wird nicht einfach so mit 20 000 € gefördert, wenn man nicht auch etwas vorzuweisen hat", führt De Rossi an.
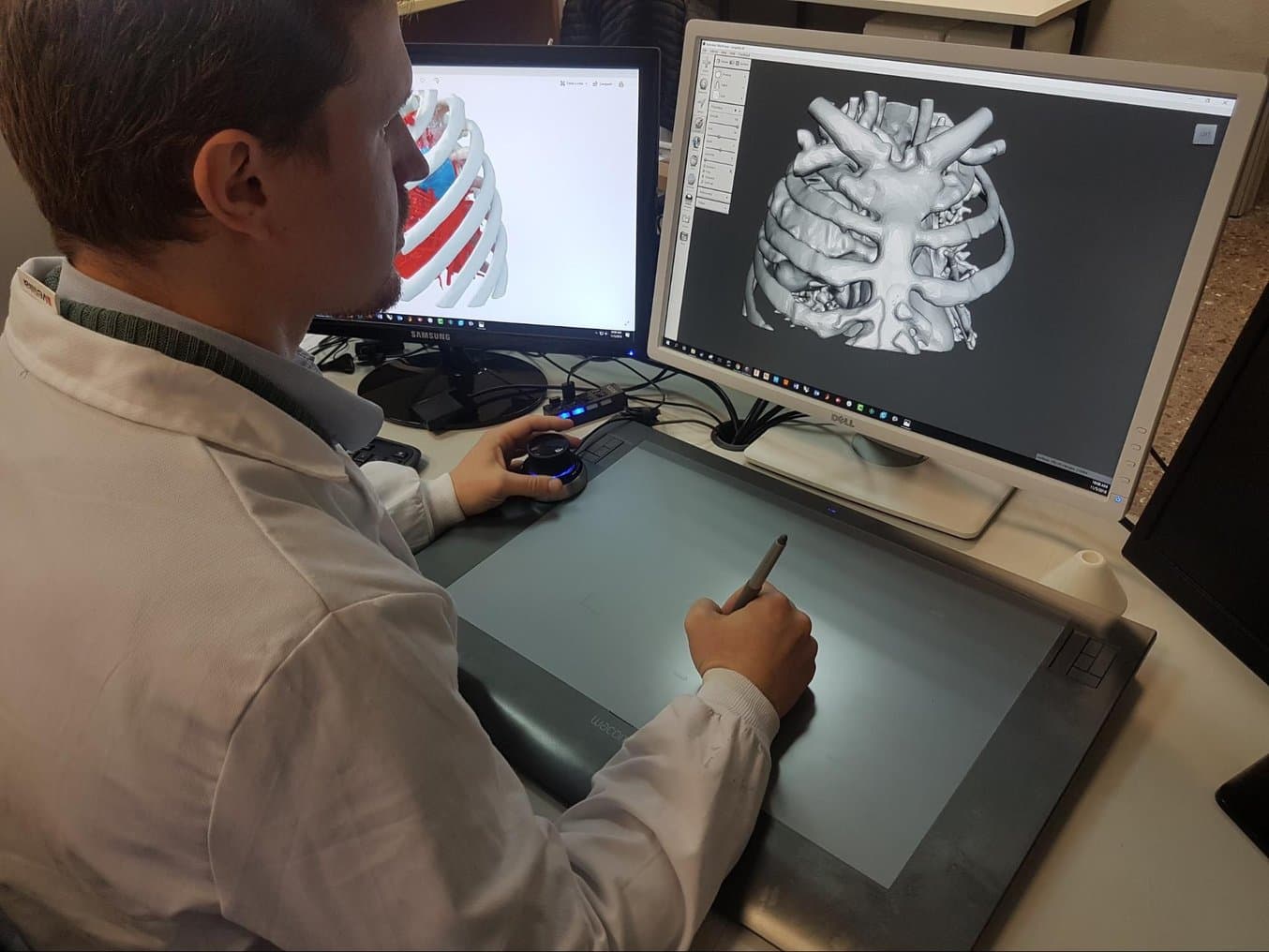
Anatomische Modelle auf Basis von CT- oder MRT-Scans eines Patienten. Die Scandaten müssen in einer Software segmentiert werden, um die wichtigen Bereiche für das 3D-Druckmodell zu isolieren.
Zusammenarbeit mit anderen Forschern
De Rossi bot seine Expertise und digitale Fertigungsausrüstung anderen Forschern im Austausch gegen Ressourcen an und erkannte, dass sowohl sein Studium als auch sein 3D-Drucklabor von dieser Zusammenarbeit profitierten.
„Um das Projekt am Laufen zu halten, muss man irgendwie Geld in die Kasse spülen. Man kann mit anderen Forschern zusammenarbeiten, um Ausrüstung und Materialien zu kaufen. Universitäten sind ziemlich groß und haben ein sehr begrenztes Budget. Findet man ein Projekt mit einem entsprechenden Ausrüstungsbudget, kann man sich absprechen und sagen: ‚Wir haben das nötige Fachwissen, wir helfen euch bei eurem Projekt[, wenn wir den Drucker am Ende behalten dürfen]‘“, erläutert De Rossi.
Ressourcen anderen zugänglich machen
„Ich habe Projekte erlebt, die zu Beginn viel Geld hatten, dann aber alles in einen Drucker investiert haben, der nur in der Ecke stand. Er wird ein paarmal benutzt und das war's. Hat man ein großes Projekt und baut ein Labor einzig für Selbstzwecke auf, wird es am Ende nicht ausreichend genutzt. Der Gedanke, alles für sich allein haben zu wollen, um die Kontrolle zu bewahren, schadet dem eigenen Projekt auf lange Sicht nur – genauso wie der Gemeinschaft als Ganzes“, erklärt De Rossi.
„Viele Ressourcen könnten geteilt werden. Wir leben in einer Zeit der Teilungswirschaft. So viele Leute wie möglich sollten von einer Investition profitieren. Wenn man lernt, zusammenzuarbeiten, dann kann man in bessere Ausstattung investieren, in besser ausgebildetes Personal, in bessere Infrastruktur. Das ist das Tolle an einer Universität“, so De Rossi.
Oft kamen Leute in De Rossis Labor und führten stolz ihr eigenes kleines Projekt vor. Sie konnten ihr Projekt aber häufig nicht weiterentwickeln, da ihnen die nötige Ausstattung zur Prototypenerstellung fehlte. Falls diese nun selbst die Zeit und das Geld in einen eigenen Drucker und dessen Erlernung investieren müssten, würden sie ihr Projekt wahrscheinlich einfach aufgeben. Aber mit Zugang zur benötigten Ausstattung und etwas Hilfe von jemandem mit Erfahrung können die meisten Projekte weiterlaufen und vielleicht Realität werden.
„Deshalb sind FabLabs auch so ein großer Erfolg. Dort konzentrieren sich die Ressourcen und man kann das voll auskosten. Man nutzt nur einen kleinen Teil der Ressourcen und hilft nur ein bisschen, aber die Zusammenarbeit unterstützt ein großes Projekt“, sagt De Rossi.
Personal bereitstellen
„Man muss irgendwie Personal an das Labor binden. Sonst hat man einen Raum, die Geräte, die Materialien, aber niemanden, der sich mit ihnen auskennt. Man benötigt eine Langzeitstrategie, damit immer jemand im Labor arbeitet“, erörtert De Rossi.
Einige Universitäten heuern Techniker an, die die Geräte bedienen und das Labor in Ordnung halten. Aber das genügt nicht. Laut De Rossi muss auch jemand gewillt sein, mit den Geräten zu helfen und andere den Umgang mit der Technologie zu lehren. Dabei kann es sich um einen Professor handeln, einen Doktoranden oder um jemanden, der Freude daran findet, anderen etwas beizubringen.
„In einer solchen Situation bietet sich ein Doktorand an, denn es überschneidet sich mit seiner Aufgabe: zu lernen, wie man forscht, etwas erklärt und jemanden lehrt. Die Leute sind hier, um etwas zu lernen. Gibt man ihnen die Möglichkeit, die Geräte und Materialien zu nutzen und sich in das Projekt einzubringen, widmen sie einem im Gegenzug ihre Zeit“, verrät De Rossi.
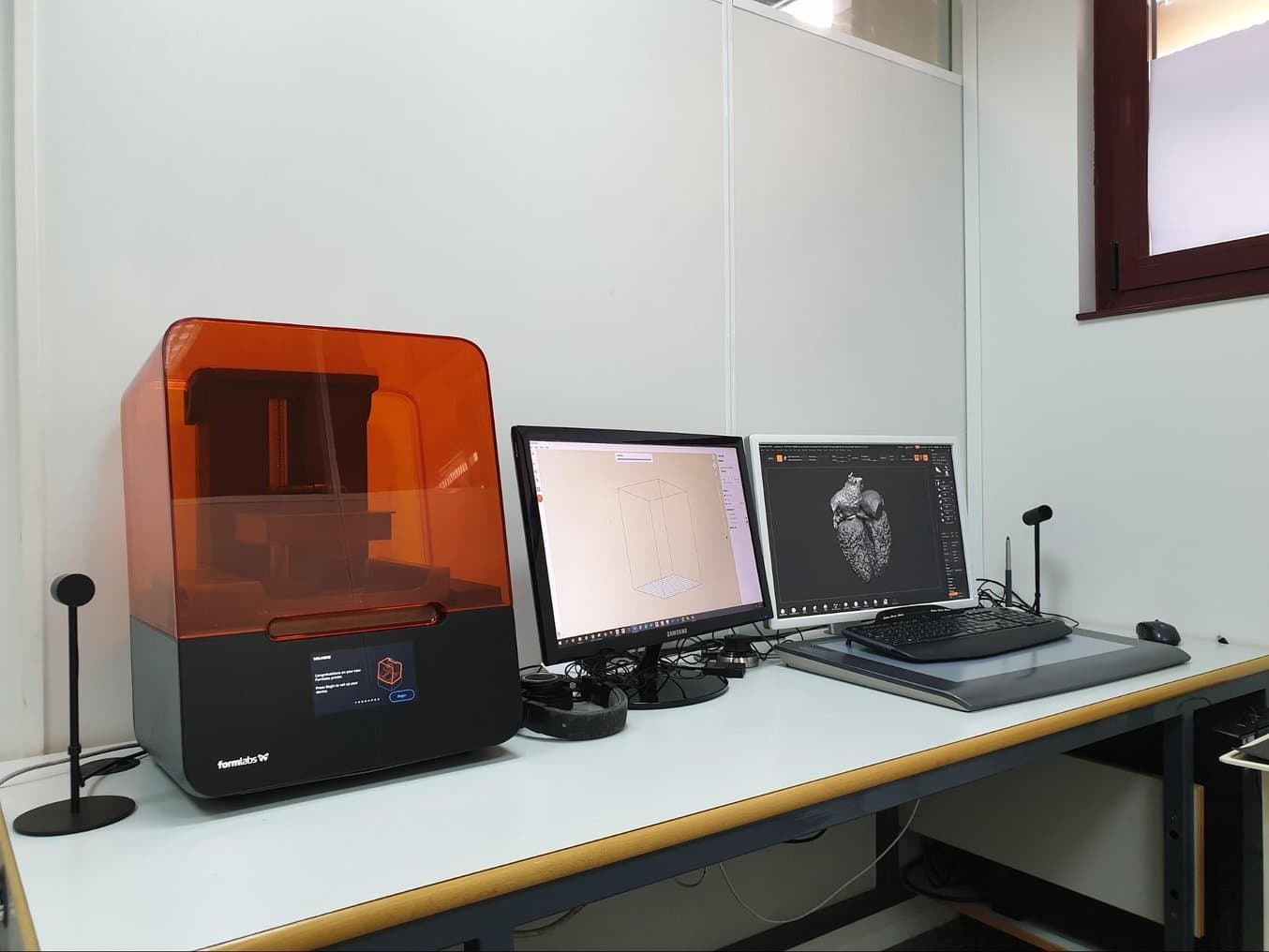
Das Labor besteht aus drei unabhängigen und spezialisierten Räumen. Im Designreinraum befinden sich die Desktop-3D-Drucker inklusive dieses Arbeitsplatzes mit dem SLA-Drucker Form 3.
Projekte von Anatomiemodellen bis zum Reverse Engineering
Das Labor an der Universitat Politècnica de València besteht aktuell aus drei unabhängigen und spezialisierten Räumen. In einem Raum befinden sich die verschiedenen digitalen Fertigungswerkzeuge wie Schneidlaser, kleine CNC-Maschinen, ein pulverbasierter Binder-Jetting-Drucker sowie ein Arbeitsbereich für Bemalung und andere unsaubere Arbeiten. Im nächsten Raum gibt es traditionelle Werkzeuge wie Sägen, Bohrmaschinen und andere Handwerkzeuge.
Zu guter Letzt gibt es noch den Designreinraum mit den Desktop-3D-Druckern einschließlich unserer Stereolithografie-3D-Drucker (SLA) Form 2 und Form 3, einiger Schmelzschichtungsdrucker (FDM) und einer Designstation. Mit wachsender Werkzeugauswahl kamen auch immer mehr Universitätskollege mit ihren Projekten zum Labor.
„‚Wenn du es baust, werden sie kommen‘, lautet das [leicht abgewandelte] Zitat [aus Feld der Träume]. Wir erledigen ständig irgendwelche Arbeiten für Forscher, für Studenten, für die Industrie“, gibt De Rossi an.
Dabei ist eine der häufigsten Anwendungen das Reverse Engineering spezifischer Komponenten, z. B. für die Luftfahrtanalytik von Turbinenkomponenten.
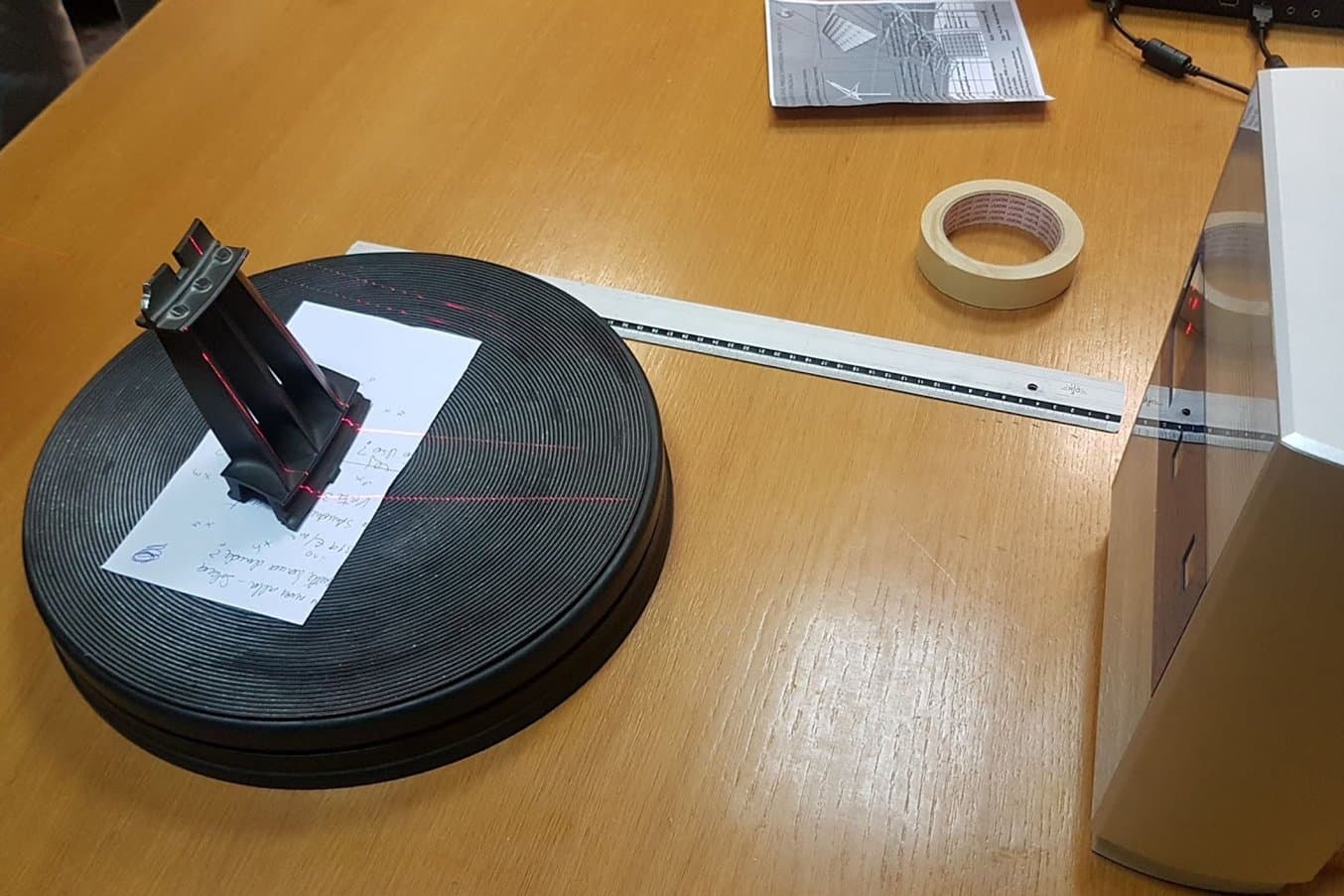
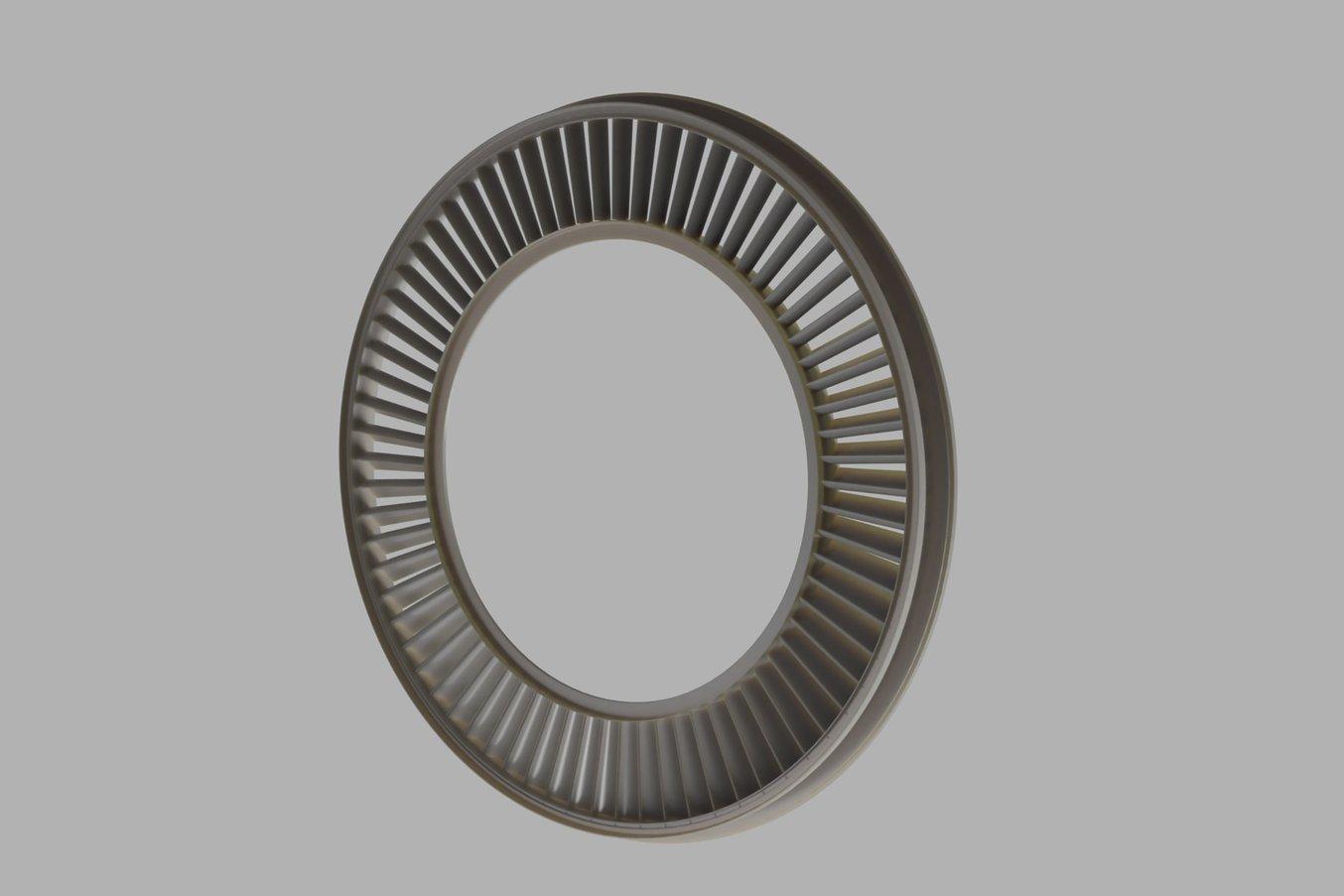
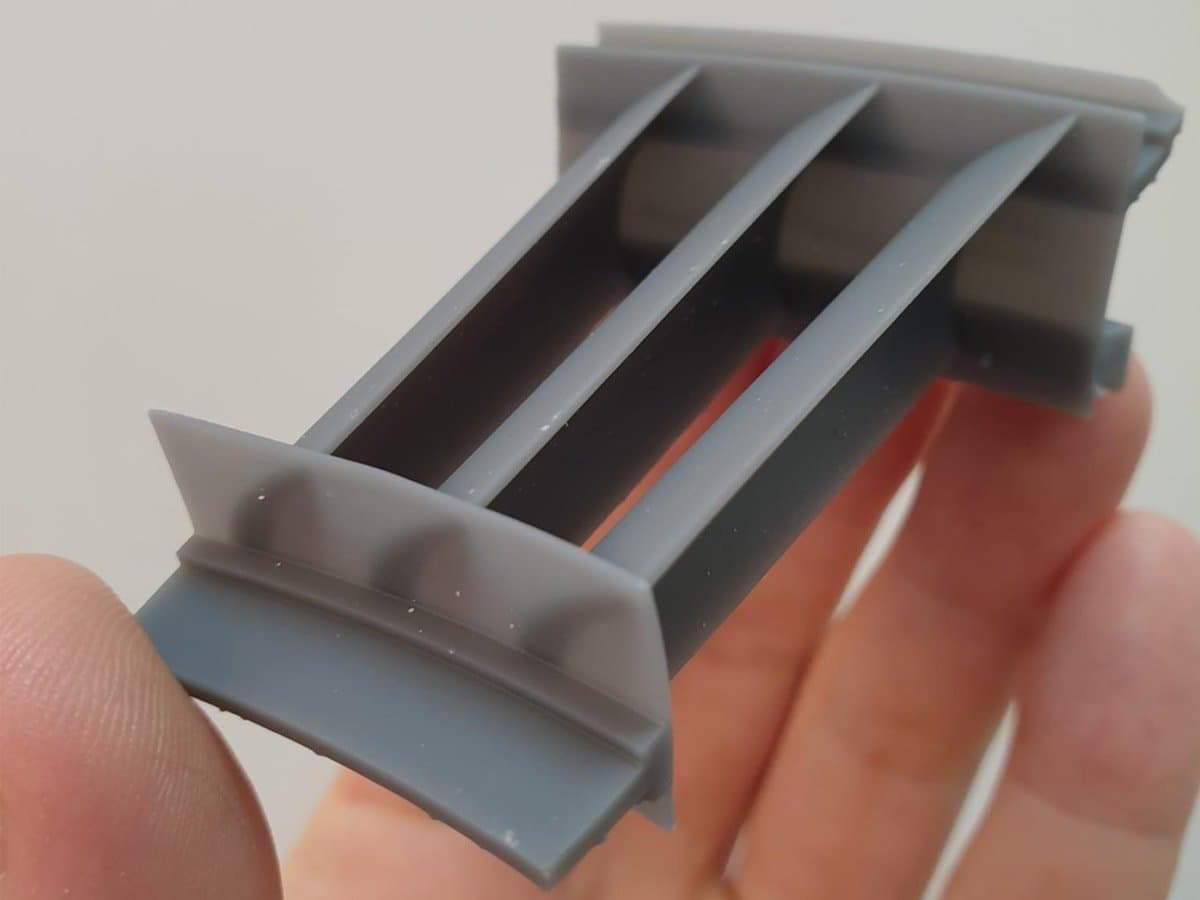
3D-Scanvorgang einer Sektion eines Flugzeugturbinenkompressors (oben links) und der 3D-Nachbau des kompletten Kompressorrings (oben rechts). Das Teil wurde auf dem Form 3 gedruckt und einem Windtunneltest unterzogen (unten).
„Wir holen uns eine kleine Sektion eines Flügels oder einer Flugzeugturbine. Dann führen wir einen 3D-Scan durch und erstellen daraus ein Modell, das wir anschließend mit einem SLA-3D-Drucker drucken. Da die Oberfläche sehr klein ist und die Details sehr filigran sind, ist die Möglichkeit der Reproduktion dieser Laser-dünnen Teile von entscheidender Bedeutung. Am Ende stecken wir es in den Windkanal und stellen sicher, dass es auch funktioniert. Es gibt so viele komplexe Objekte, die man nicht einfach so entwirft“, berichtet De Rossi.
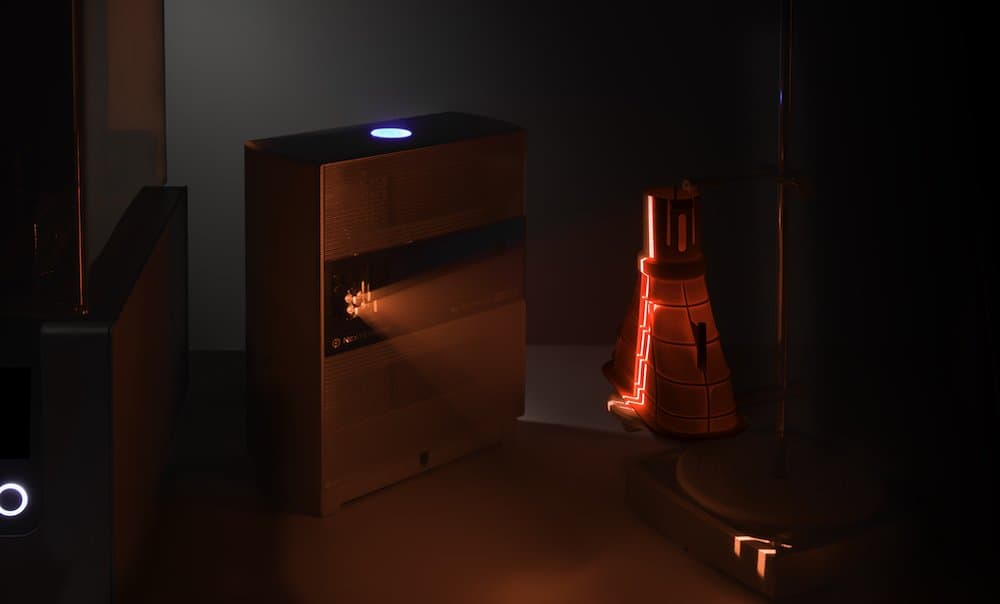
3D-Scannen für Reverse Engineering, Restauration und Metrologie
Dieses Whitepaper bietet einen detaillierten Einblick in die Nutzung von 3D-Scans zur Verbesserung des Designs und der Produktion von Teilen. Zusätzlich erklären wir Ihnen, wie Scantechnologieprozesse zusammen mit 3D-Druck effektiv bei der Nachbildung und Restauration, dem Reverse Engineering und der Metrologie angewendet werden können.
Whitepaper herunterladen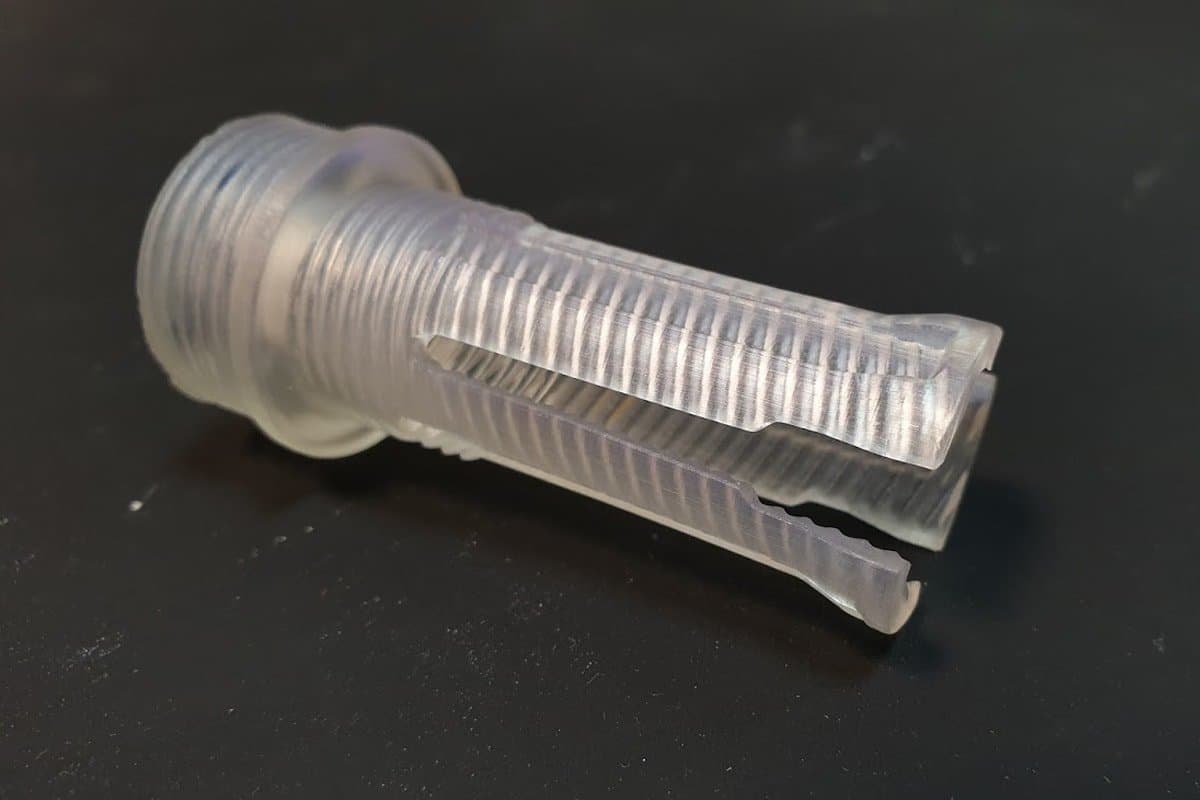
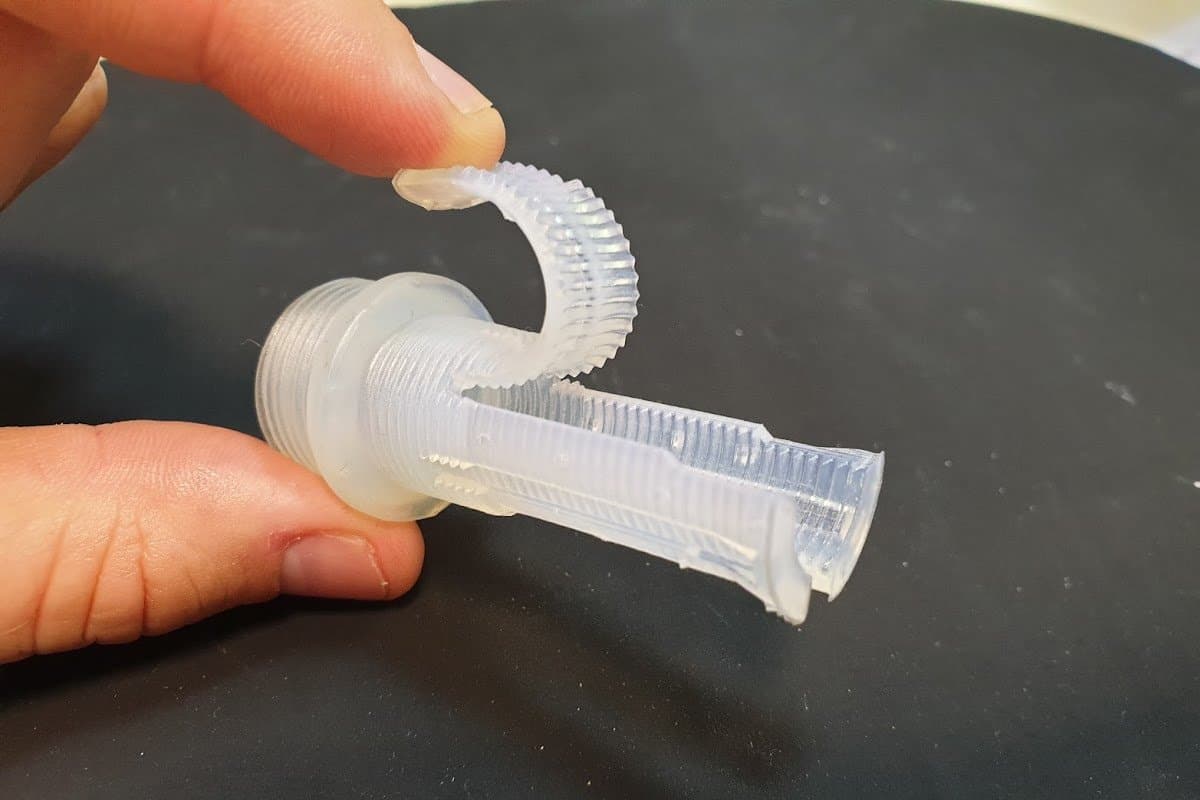
Dieses Ersatzteil eines Röntgenapparats wurde aus Durable Resin 3D-gedruckt, um die Einsatzbelastung auszuhalten.
„Einmal haben wir ein Teil eines Röntgenapparats nachgebaut. Röntgengeräte sind teuer und werden von Krankenhäusern ein ganzes Jahrzehnt lang oder noch länger genutzt. Am Ende dieses Zeitraums sind viele Komponenten nicht mehr verfügbar, aber das Gerät benötigt man immer noch. Ein Kleinteil war kaputt gegangen. Und wegen so eines kleinen Kunststoffteils wollten wir eine 100 000 Dollar teure Maschine nicht mehr benutzen. Man brachte mir das Teil. Wir haben es dann 3D-gescannt und mithilfe mehrerer Programme nachgebaut. Gedruckt haben wir es auf einem Formlabs-Drucker mit Durable Resin. Das Ergebnis war perfekt. Jetzt läuft der Apparat schon seit über einem Jahr ohne Probleme", schildert De Rossi.
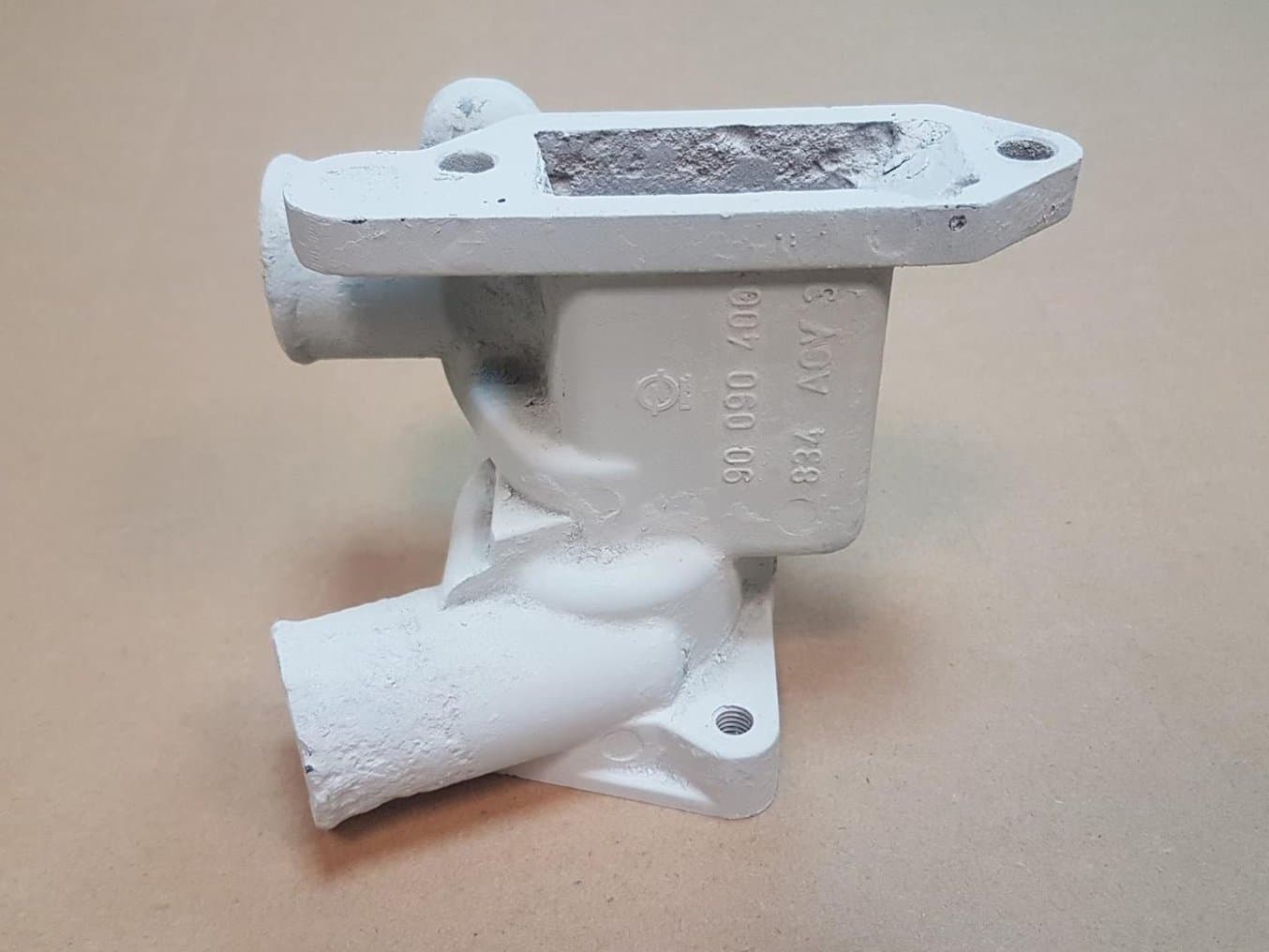
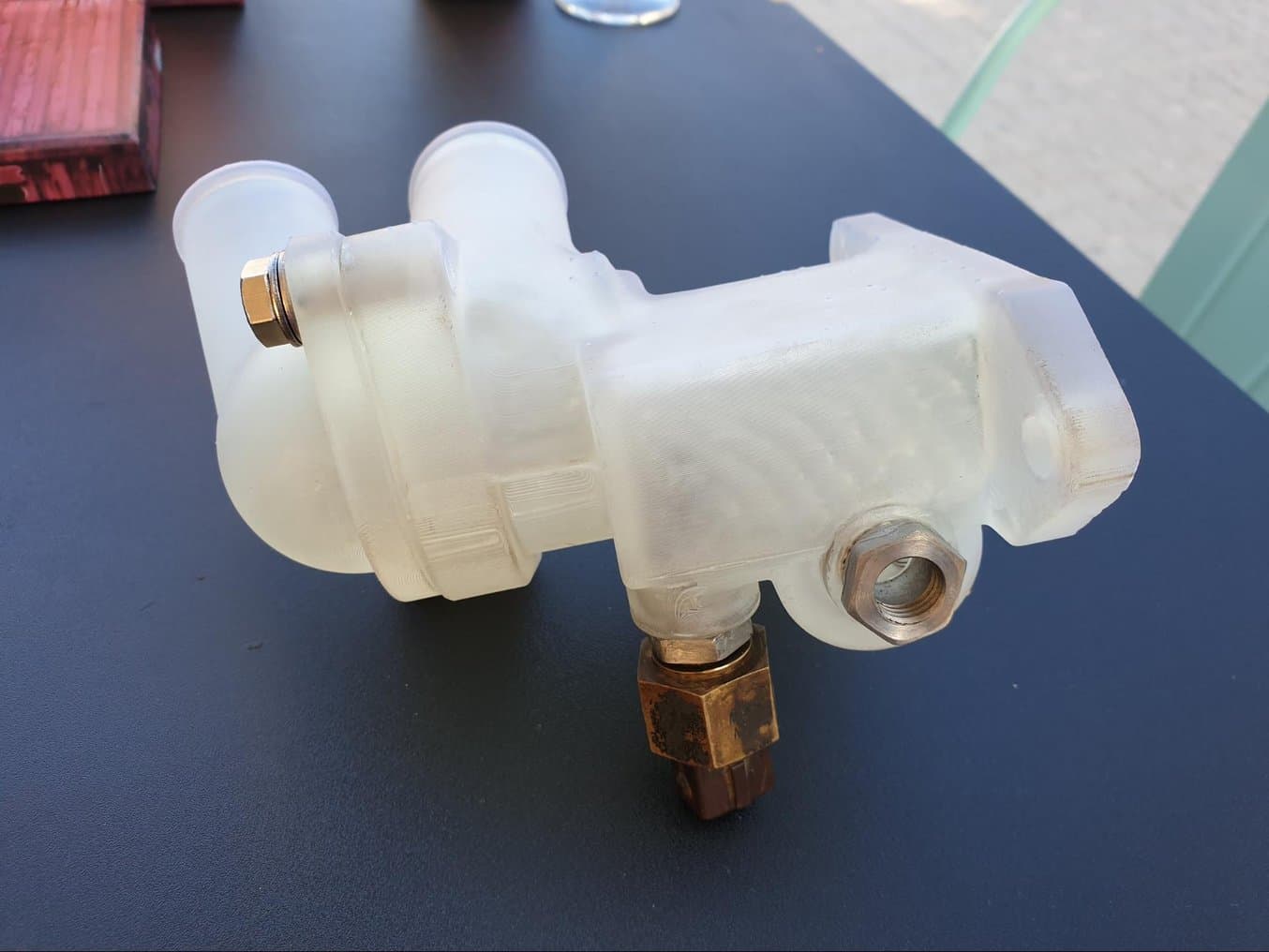
Bei einem der Projekte ging es um das korrodierte Thermostat eines klassischen Autos. Das kaputte Teil wurde für Scanzwecke weiß angemalt, mit CAD nachgebaut, aus hitzebeständigem High Temp Resin 3D-gedruckt und dann von einem Frässpezialisten mit Gewinden und Metallkomponenten versehen.
Gemäß dem Thema seiner Doktorarbeit hat De Rossi auch zahlreiche Projekte für die Medizin übernommen.
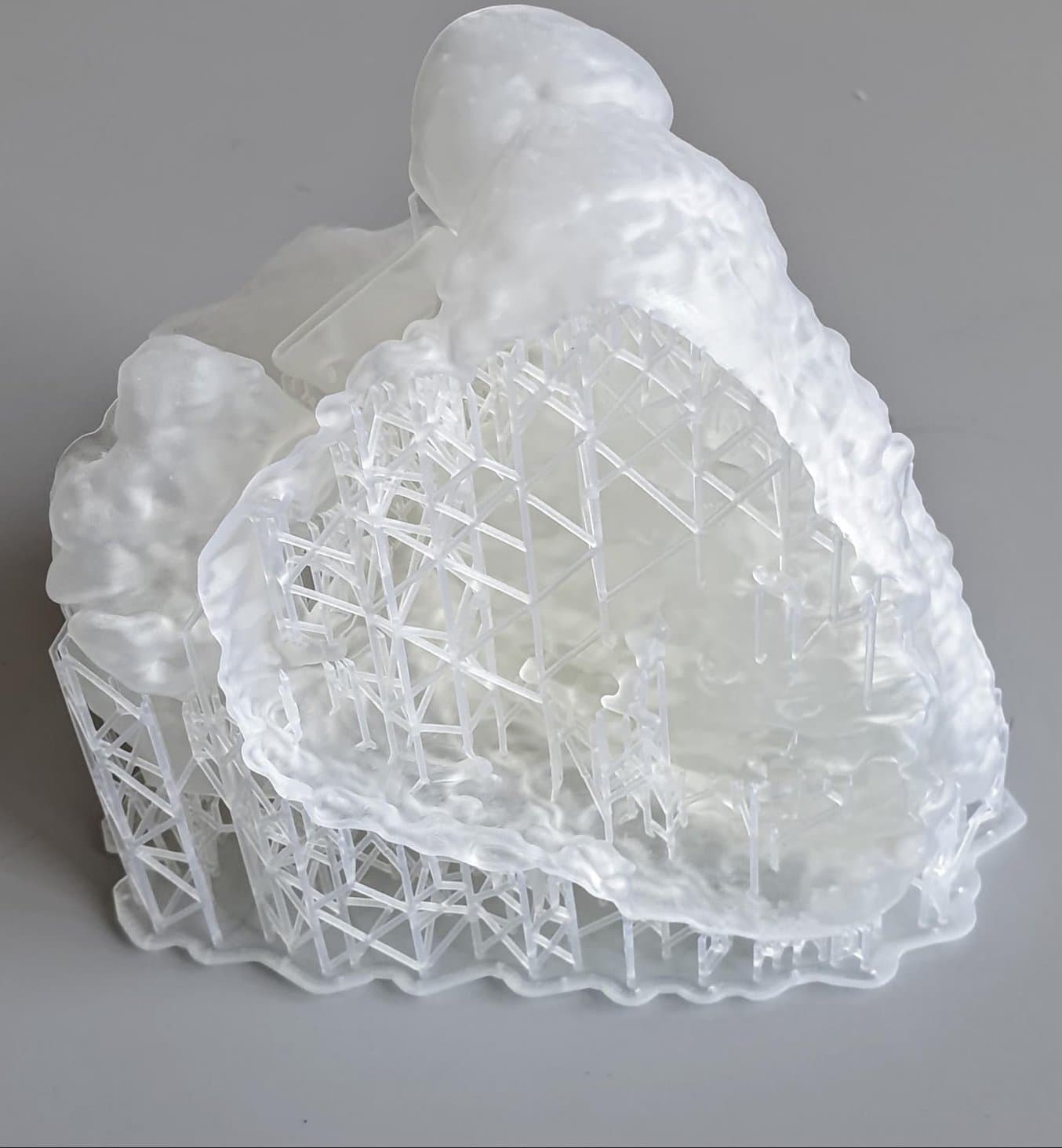
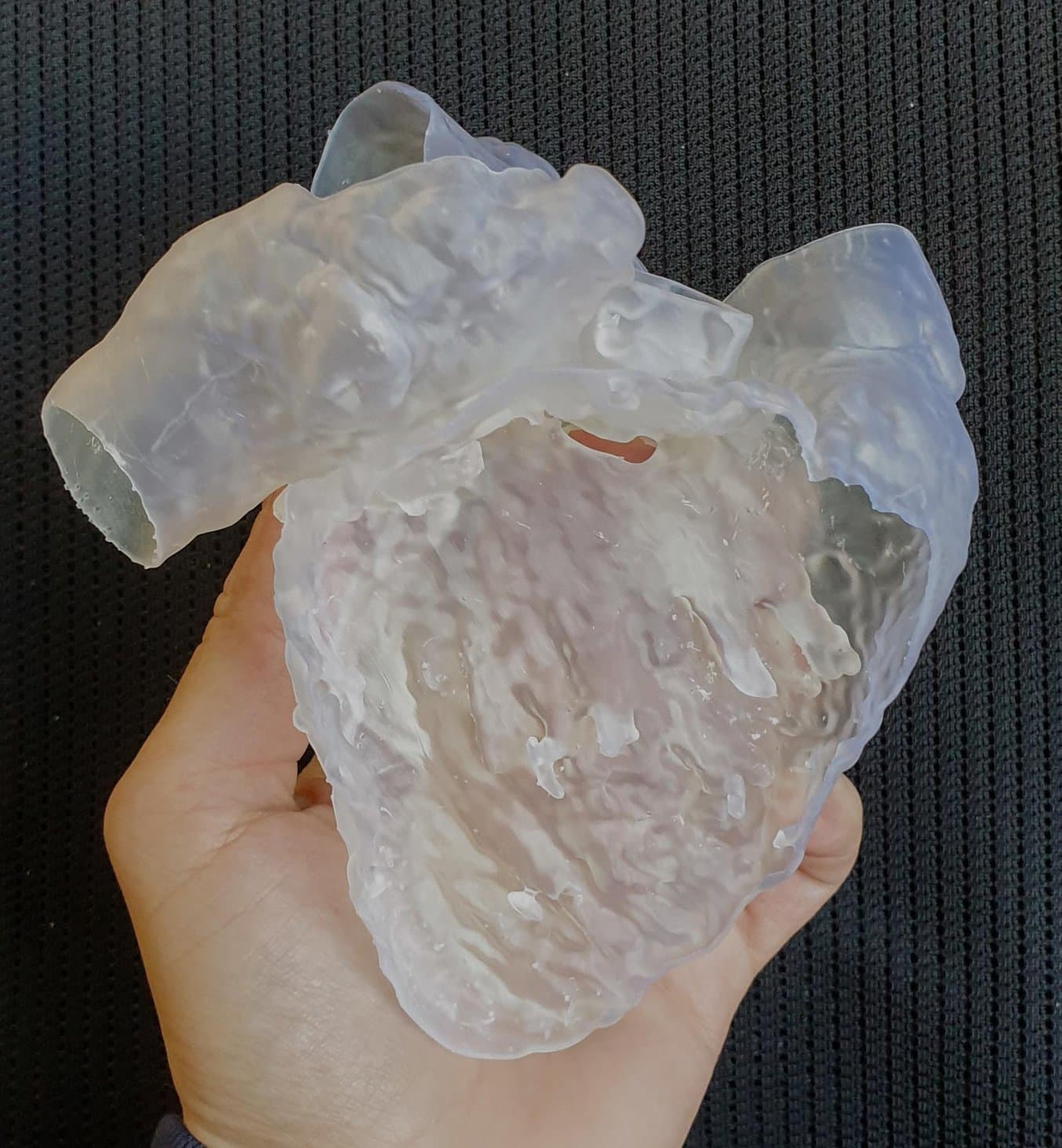
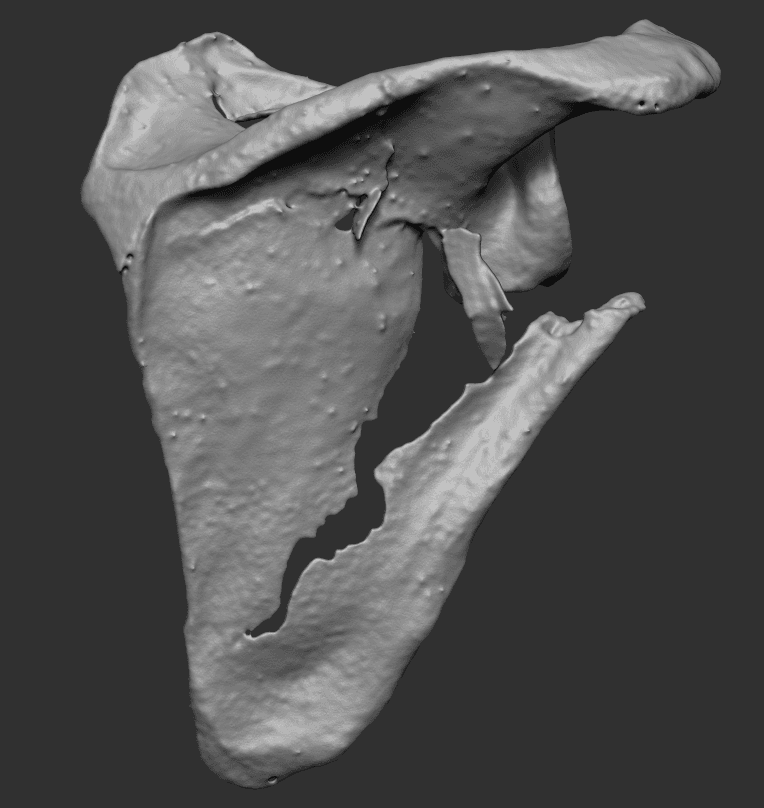
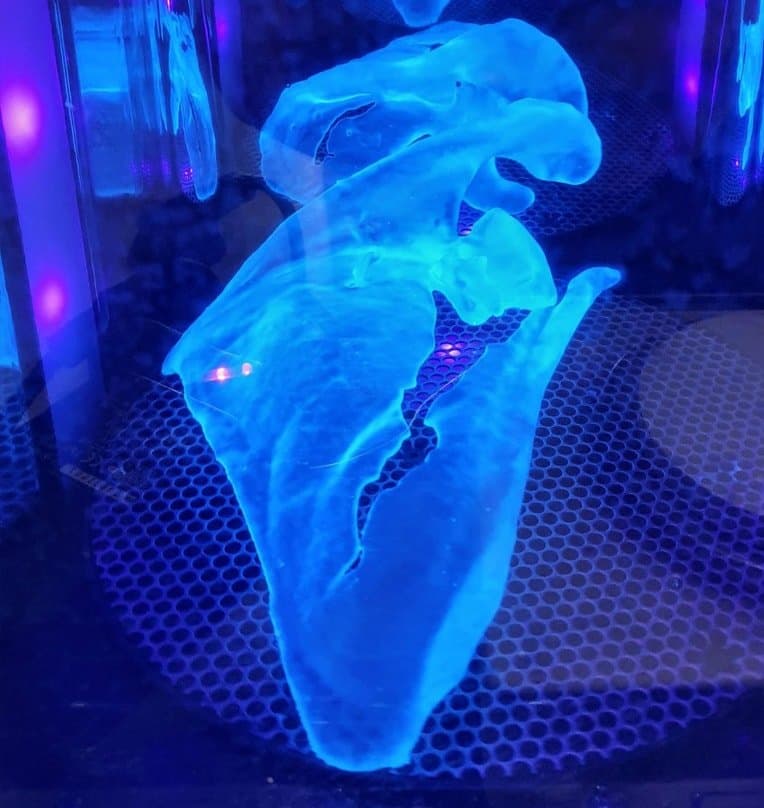
Ein 3D-gedrucktes Herzmodell zur Operationsvorbereitung, mit Stützstrukturen (oben links) und ohne (oben rechts). Ein digitales 3D-Modell eines Schulterblattbruchs (unten links) und das 3D-gedruckte Modell beim Nachhärten im Form Cure (unten rechts).
„Mein wohl anspruchsvollster und komplexester Arbeitsbereich sind pediatrische Cardiologie-Modelle. Das ist superkompliziert. Da hat man es mit winzig kleinen Herzen zu tun, von den die Chirurgen 3D-Modelle benötigen, um sie richtig zu begreifen und zu visualisieren. Einige Einrichtungen benutzen Jetting-3D-Drucker, die eine Viertelmillion kosten. Wir aber nutzen 3D-Drucker von Formlabs und arbeiten mit Krankenhauschirurgen zusammen. Und die sind mehr als zufrieden. Es ist fantastisch", so De Rossi.
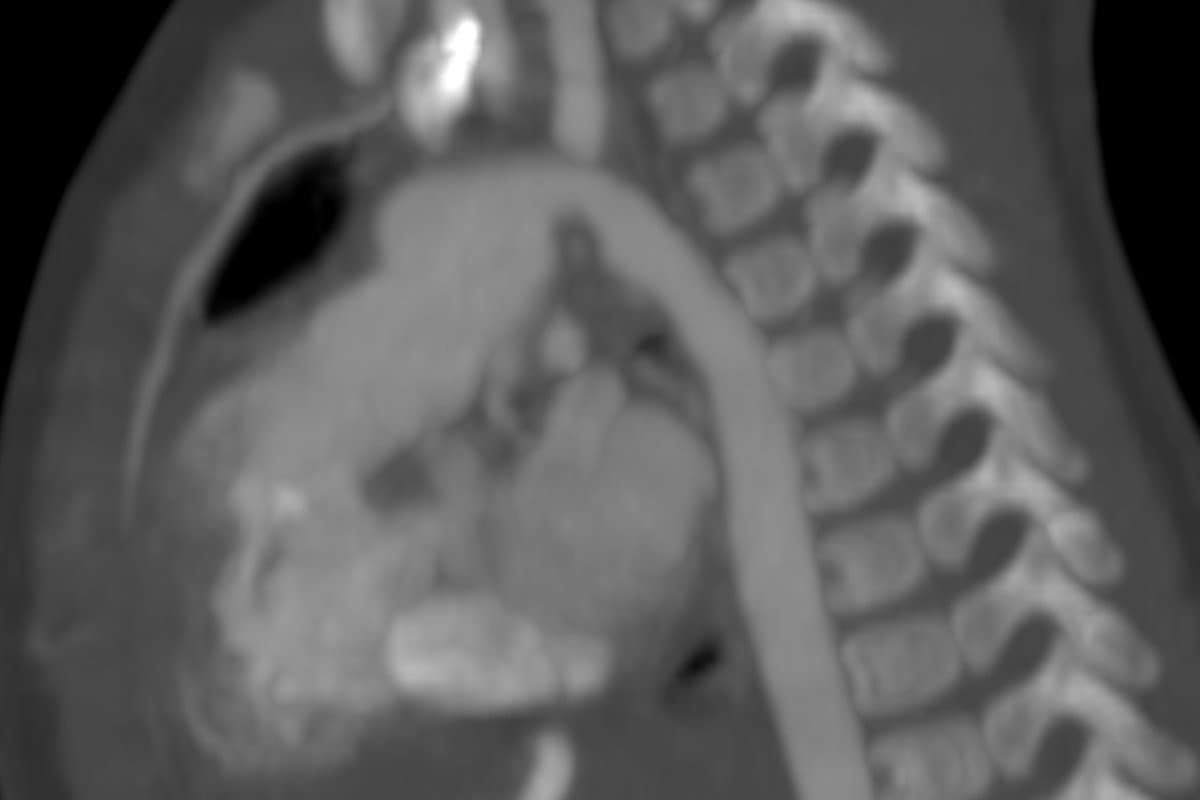
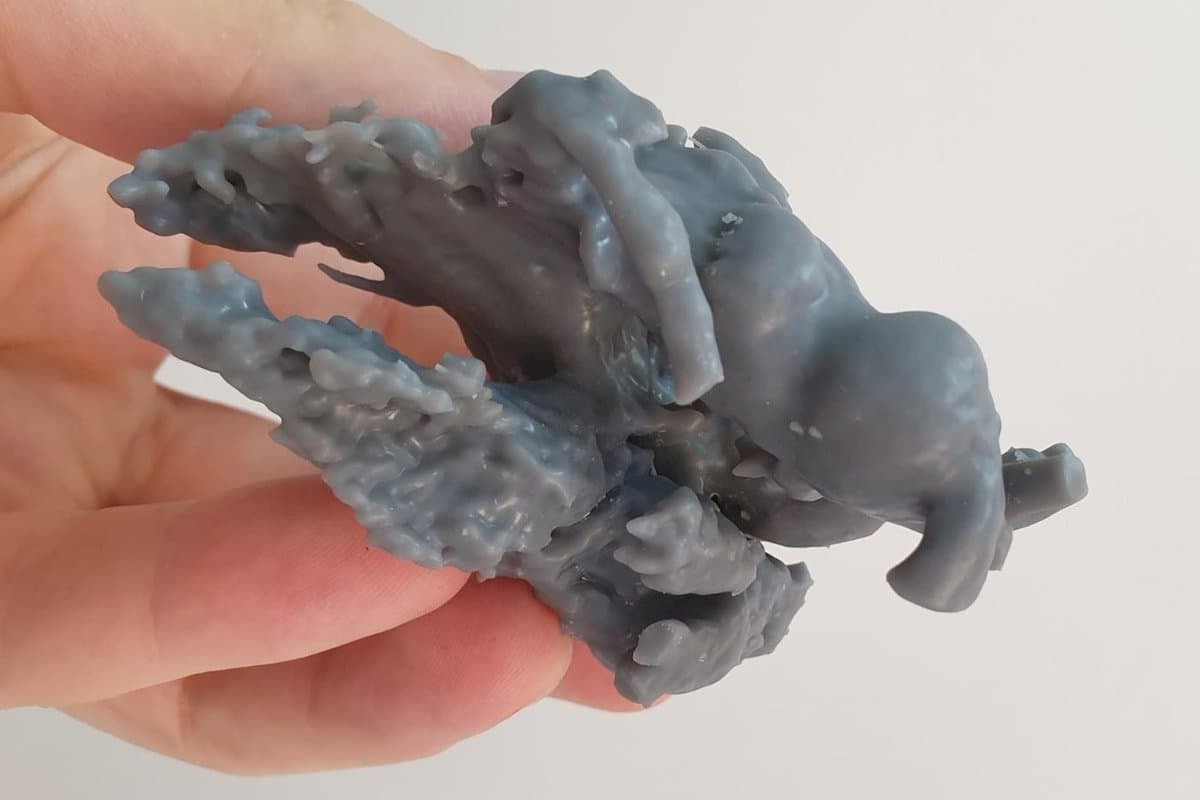
Herkömmliche Ansicht eines CT-Scans (links) und 3D-gedrucktes Modell der Herzhöhlen zur Planung der pediatrischen Herzoperation (rechts).
Für De Rossi ist die große Bandbreite an Materialien einer der Hauptvorteile des SLA-3D-Drucks.
„Wenn man einmal begriffen hat, dass man fast jede beliebige Form abbilden kann, dann benötigt man nur noch unterschiedliche Materialien. Dabei ist ein Gerät mit einer solchen Materialienvielfalt ein riesiger Vorteil. Das gilt insbesondere, wenn man nicht weiß, was für ein Auftrag einen am nächsten Morgen erwartet. Vielleicht benötigt ein Künstler ein gussfähiges Teil. Vielleicht benötigt ein Ingenieur ein belastbares, widerstandsfähiges Gehäuse. Ein Gerät mit einer solchen Materialpalette ist ein riesiger Vorteil. Selbst wenn man jetzt noch nicht alle Materialien nutzt, ist es eine praktische Investition in die Zukunft“, sagt De Rossi.
Dabei ist ein Gerät mit einer solchen Materialienvielfalt ein riesiger Vorteil.
Marco De Rossi
Digitale Fertigung auf den Lehrplan bringen
Nach seiner Promotion hofft De Rossi auf eine Professorenstelle an der Universität, den Aufbau seiner eigenen Forschungsgruppe und neue Doktoranden, die seine Arbeit im Labor weiterführen.
„Man benötigt vor Ort unbedingt jemand Lernwilligen. Diese Rolle ist in einem 3D-Drucklabor unabdingbar. Man benötigt jemanden, der sich ein paar Jahre involviert und dann das Wissen an die nächste Generation weitergibt“, erklärt De Rossi.
„Ich glaube, das gefällt mir mit am besten am Universitätsleben: dass man sich aufs Lehren konzentriert und nicht darauf, bei einer Sache der Beste zu sein. Stattdessen muss man in vielen Dingen gut und flexibel genug sein, um alle möglichen Projekte verstehen zu können. Man gibt den Studenten die Werkzeuge an die Hand, mit denen sie selbst zu den besten ihres Fachs werden können“, führt De Rossi an.
„Man benötigt eine systematische Methode, um jemandem die nötigen Fähigkeiten für die digitale Fertigung beizubringen. Mittlerweile haben einige Universitäten vielleicht ein 3D-Labor oder einen Kursus. Aber ich glaube nicht, dass es ein integraler Bestandteil [des Lehrplans] ist. Jeder Aspekt eines Berufs muss sich um die digitale Fertigung drehen. Das ist die Zukunft. Das ist die heutige Realität. Wenn man das nicht lehrt, dann gehört man schon fast zum alten Eisen“, erzählt De Rossi.