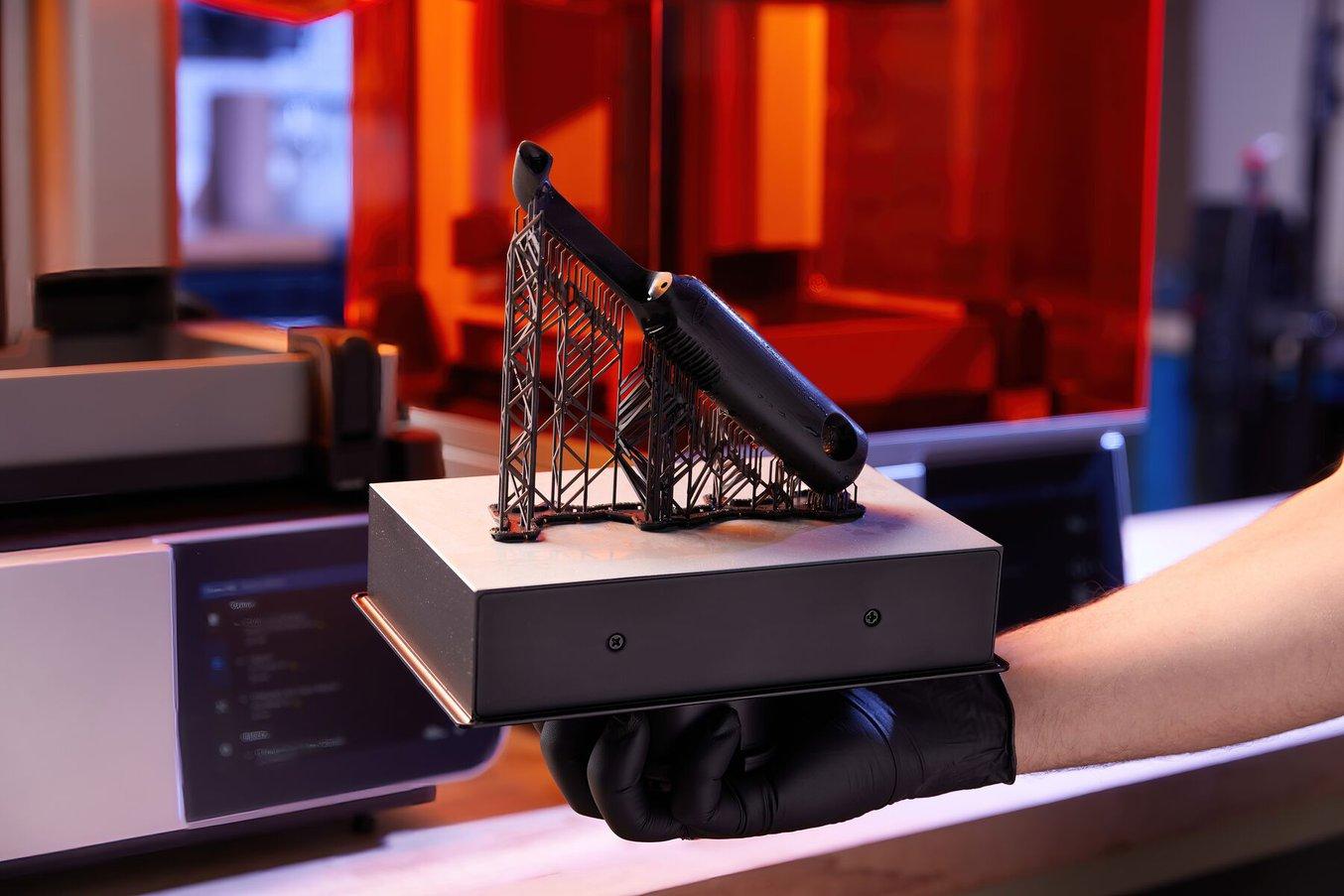
OXO entwickelt einige der beliebtesten und meistgenutzten Küchen- und Haushaltsutensilien auf dem Markt. OXOs Produktpalette erstreckt sich von ergonomischen und verblüffend langlebigen Gemüseschälern über elegante Lebensmittelbehältern bis hin zu Schneekehrern, die allesamt funktional, erschwinglich und – allem voran – notwendig sind. Alles, was den Alltag im Haushalt erleichtern könnte, wurde mit hoher Wahrscheinlichkeit bereits von OXO entworfen.
Um einen Produktkatalog mit Hunderten von Artikeln stets wettbewerbsfähig zu halten, muss das Produktentwicklungsteam von OXO die sensible Balance zwischen schnellem Markteintritt und perfektem Design finden. Bringen sie ein Produkt zu spät auf den Markt, sieht sich die Kundschaft womöglich woanders um. Gehen sie jedoch zu früh in die Lieferung, riskieren sie Produktfehler, wegen derer sich Kunden ganz von OXO abwenden könnten.
Die Antwort auf diese Zwickmühle ist die Iterationsgeschwindigkeit, oder anders betrachtet Gründlichkeit – das Designteam muss für Hunderte von Produkten sämtliche Optionen erkunden, wie klein die Unterschiede auch sein mögen. OXO setzt bereits seit Jahren auf die Drucker von Formlabs, doch seit das Team sein 3D-Drucklabor um den Form 4 erweiterte, konnte OXO die Anzahl der Designänderungen pro Tag verdreifachen.
„Früher mussten wir über Nacht auf Drucke warten. Jetzt schaffen wir mit dem Form 4 drei bis vier Drucke pro Tag.“
Jesse Emanuel, Prüfingenieur und Leiter der additiven Fertigung, OXO
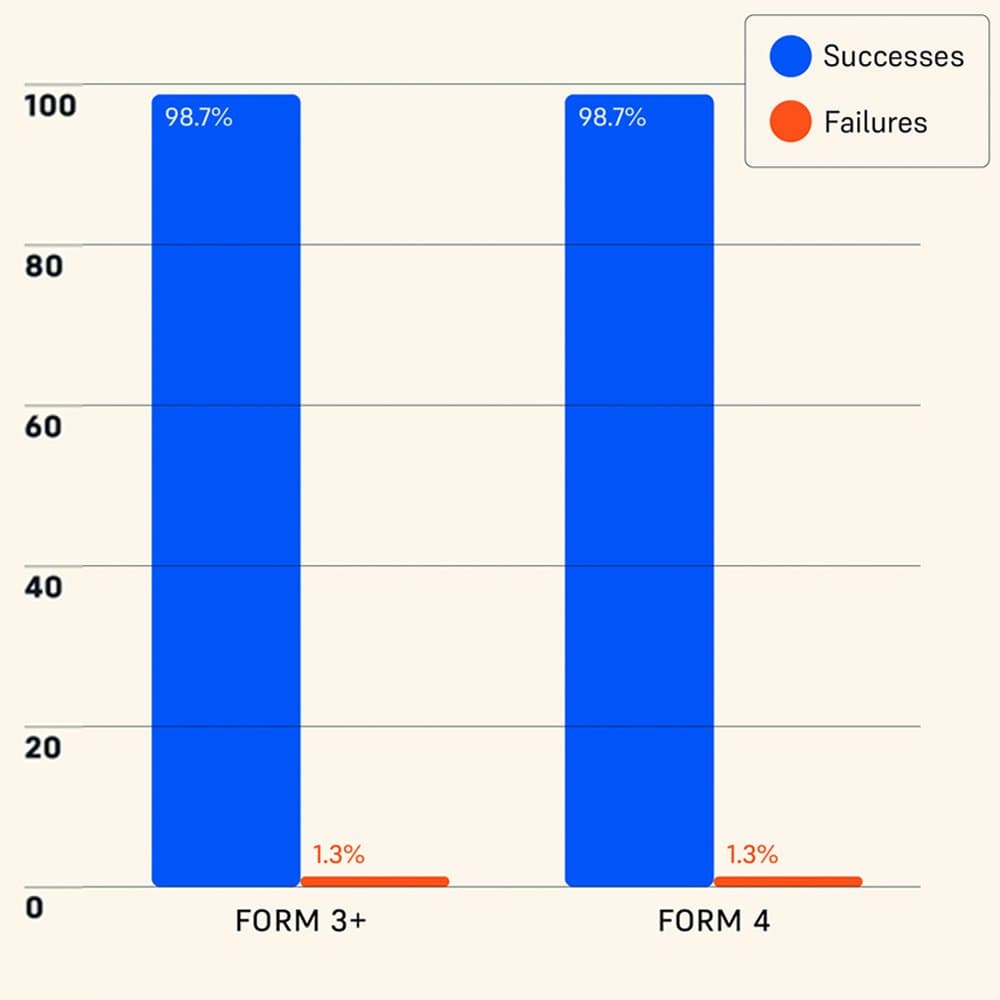
Zuverlässigkeit von Form 4 und anderen Kunstharz-3D-Druckern unabhängig getestet
Der Form 4 von Formlabs erreichte in einer Untersuchung eines unabhängigen, weltweit führenden Produkttesters eine Druckerfolgsrate von 98,7 %. Eine vollständige Beschreibung der Testmethode und die Ergebnisse finden Sie in unserem Whitepaper.
Beschleunigte Iteration revolutioniert OXOs Prozesse
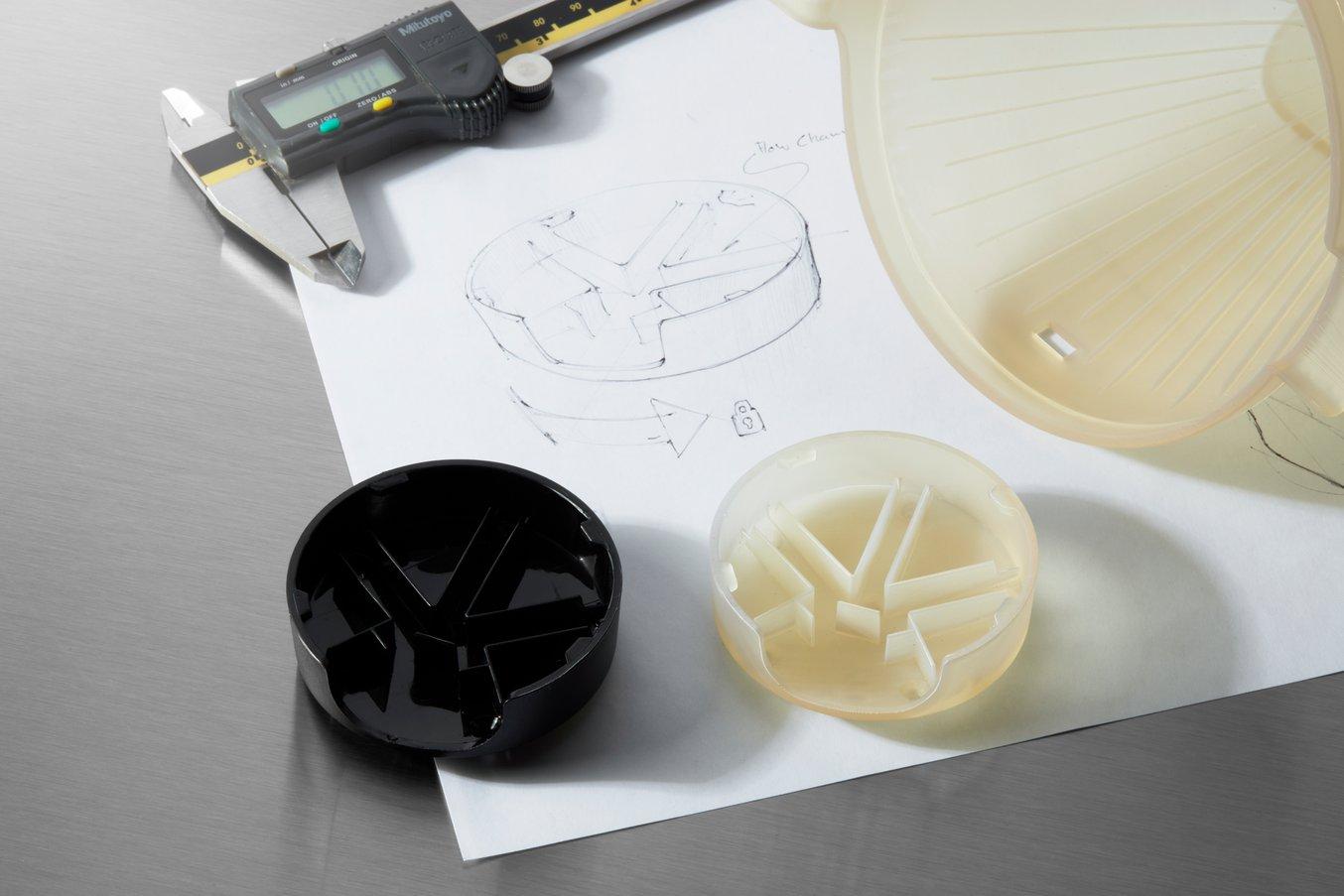
Prototypen von Teilen wie diesem müssen über den gesamten Designprozess hinweg enge Toleranzen einhalten, damit sie als Teil größerer Baugruppen getestet werden können.
Emanuel leitet OXOs Labor für Rapid Prototyping, das von Teams im Industriedesign, der Produktvalidierung und der globalen Fertigung genutzt wird. Die Produkte müssen sich in einem übersättigten Markt bewähren und über Jahre hinweg zuverlässig funktionieren. Präzise Entwicklung, ausgiebige Anwendertests und Liebe zum Detail sind wichtige Grundpfeiler der Designphilosophie von OXO.
OXO nutzt bereits seit Jahren 3D-Druck, um sein Team bei der Produktion Hunderter von SKUs zu unterstützen. Bei den Produkten handelt es sich oft um Baugruppen mit Komponenten aus spritzgegossenem Kunststoff, leichten Metallen wie Aluminium sowie Elektronik. Beim Prototyping erster Modelle dieser Baugruppen sind enge Toleranzen gefordert, wie auch eine Materialpalette, die die Steifigkeit von Metall, die Festigkeit spritzgegossener Kunststoffe wie ABS oder auch die Flexibilität und Haltbarkeit von Silikon abdecken kann.
Da Handgeräte einen Großteil der Produkte ausmachen, spielen auch ergonomisches Design und Anwendertests eine große Rolle bei der Produktentwicklung. Die 3D-Druckerflotte von OXO muss dem Anspruch nach schnellen, genauen Modellen mit vielseitigen Materialeigenschaften gerecht werden.
Emanuels Flotte umfasst den Form 3, Form 3L und Form 4 sowie mehrere FDM-3D-Drucker (Schmelzschichtung). Die Drucker bewältigen Anfragen für eine Vielzahl verschiedener Materialien und mechanischer Eigenschaften, mithilfe von Formlabs' Kunstharzkatalog und in der Branche bewährten Filamenten für den FDM-Druck.
Form 4 prescht durch die Druckwarteschlange
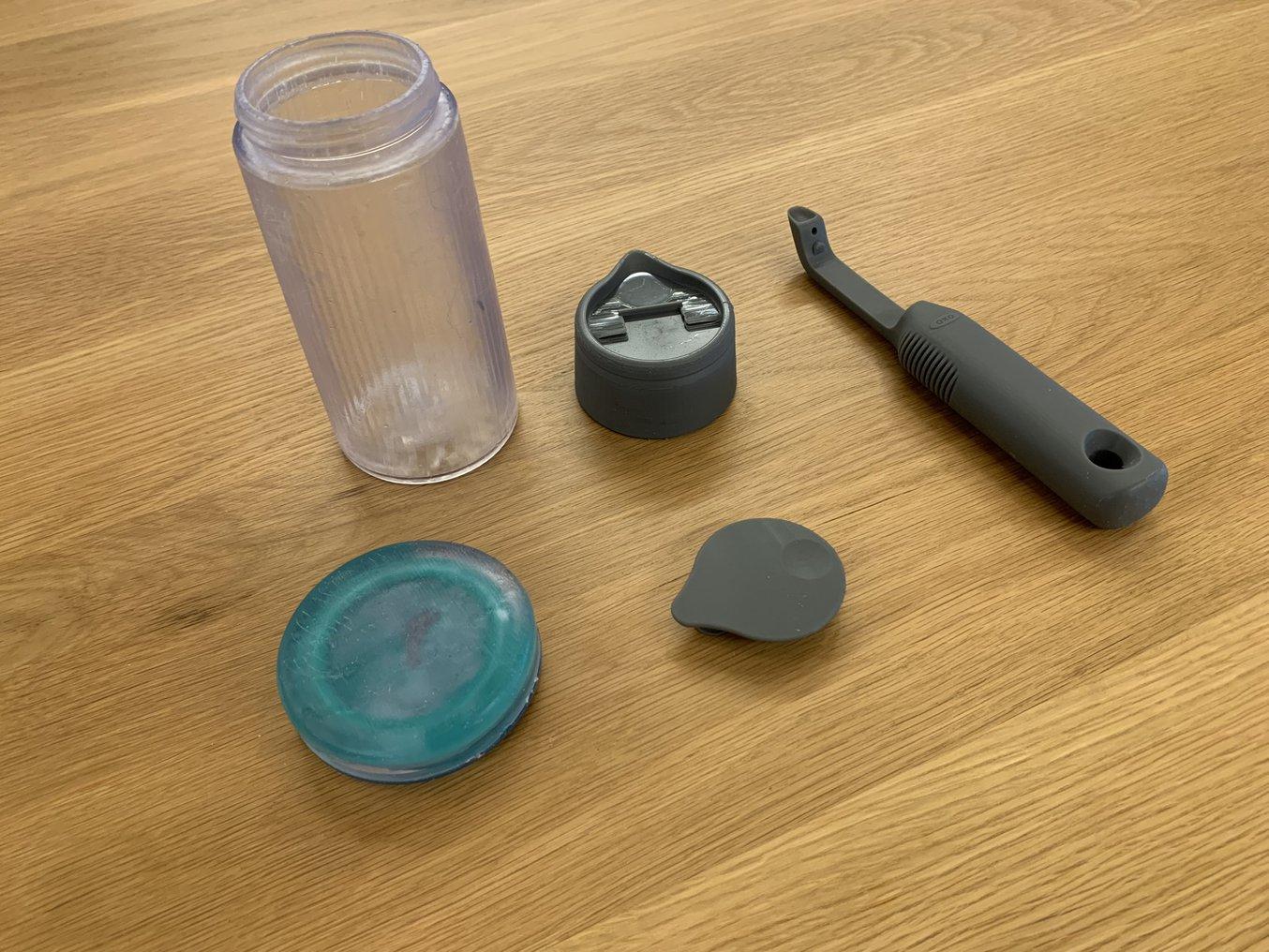
Der Form 4 unterstützt OXO bei seinen Designiterationen für eine Reihe von Projekten, angefangen von Flaschen aus Clear Resin (oben links), Deckeln und Schälern aus Grey Resin (Mitte und rechts) bis hin zur Herstellung von Formen für den Silikon- oder Urethanguss (blaues Formteil, unten links).
Emanuel bearbeitet bis zu 200 Anfragen pro Woche: Mit einfachen Formmodellen werden beim Industriedesign Ideen validiert, Modelle für funktionale Praxistests helfen dem Fertigungsteam, die Prozesse für die Massenproduktion abzustimmen, und präsentationsreife, ästhetische Teile werden von Marketing und Vertrieb zur Vorführung vor OXOs zahllosen Händlern genutzt. Jede Anfrage wird basierend auf dem Designzeitplan, der Produktveröffentlichung und der stetig wachsenden Verbrauchernachfrage an die Druckerwarteschlange gesendet und priorisiert.
„Die Nachfrage wächst, aber der Form 4 hat unseren Arbeitsprozess revolutioniert. Früher hatten wir aus Zeitgründen oft Probleme mit unserer Warteschlange. Mit dem Form 4 ist das jetzt Geschichte – Zeit stellt für uns keine Einschränkung mehr dar.“
Jesse Emanuel, Prüfingenieur und Leiter der additiven Fertigung, OXO
Dank des vergrößerten produktiven Zeitfensters sind die Teams in der Lage, Neues zu probieren, ohne die Sorge, dass Fehldrucke zum Verpassen ihrer Fristen führen könnten. „Die Designer arbeiten daran, alles vor der geplanten Testphase gedruckt zu bekommen. Oft senden Sie Teile am Abend vor dem Testen ein. Wenn dann ein Druckfehler auftritt, weil der Strom ausfällt oder etwas in der Art, wäre das früher ein echtes Problem gewesen – wir hätten die Produkttests verschieben, Teile auf mehrere Drucker aufteilen oder sie aus unterschiedlichen Materialien drucken müssen. Wenn sich jetzt am Morgen herausstellt, dass wir einen Fehldruck hatten, schicken wir ihn einfach an den Form 4 und haben das Teil am Nachmittag parat. Selbst der längste Druckauftrag, den wir auf dem Form 4 gedruckt haben, hat nur etwa vier Stunden gedauert“, so Emanuel.
Die Schnelligkeit des Form 4 macht den Drucker zu einer fehlersicheren Option für die zahlreichen OXO-Teams, die mit knappen Fristen und Durchlaufzeiten zu kämpfen haben. Sie können Designs schneller iterieren und neue Konzepte ausprobieren, und das mit der Gewissheit, bei Bedarf schnelle Ergebnisse zu erhalten. „Der größte Vorteil ist einfach die Zeit. Vergrößerte zeitliche Kapazitäten. Das ist es, wovon wir am meisten profitieren.“
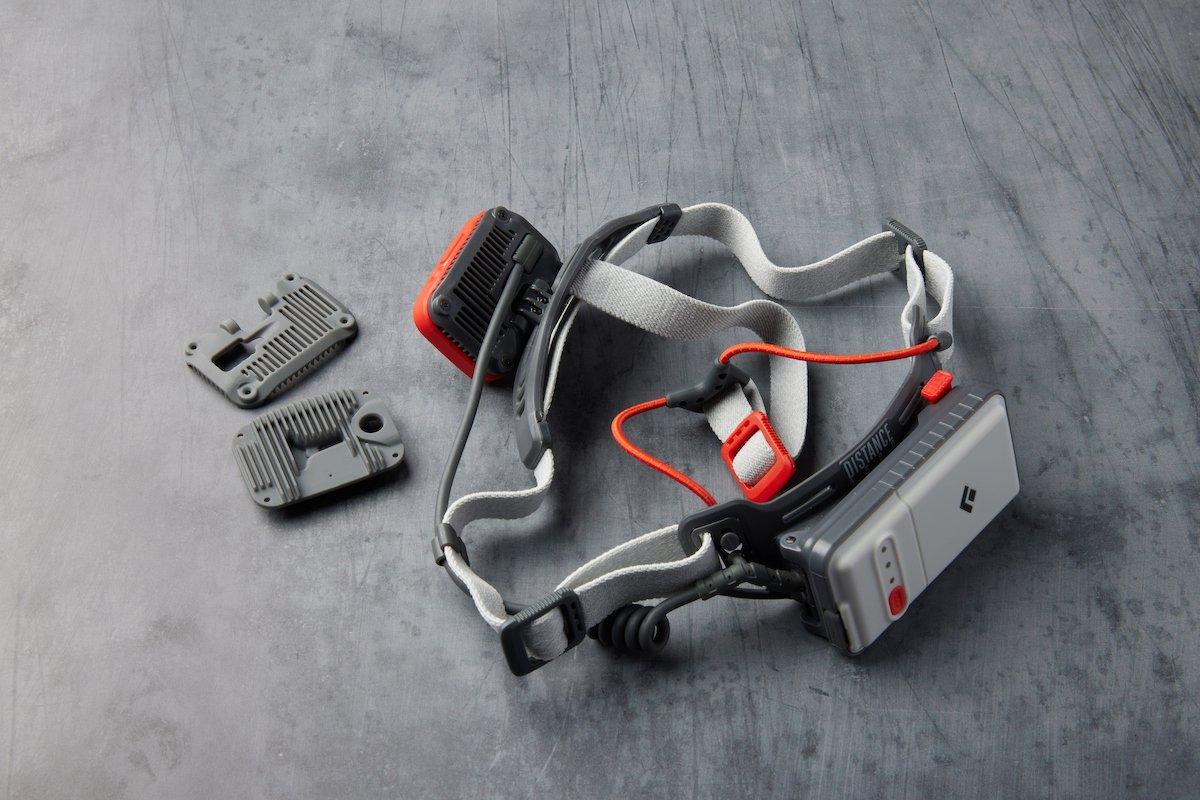
Leitfaden zum Rapid Prototyping für die Produktentwicklung
In diesem Leitfaden erfahren Sie, wie sich Rapid Prototyping in Produktentwicklungsprozesse einfügt, welche Anwendungsfälle dafür bestehen und welche Rapid-Prototyping-Werkzeuge den Produktentwicklungsteams von heute zur Verfügung stehen.
Fühltest und Maßgenauigkeit
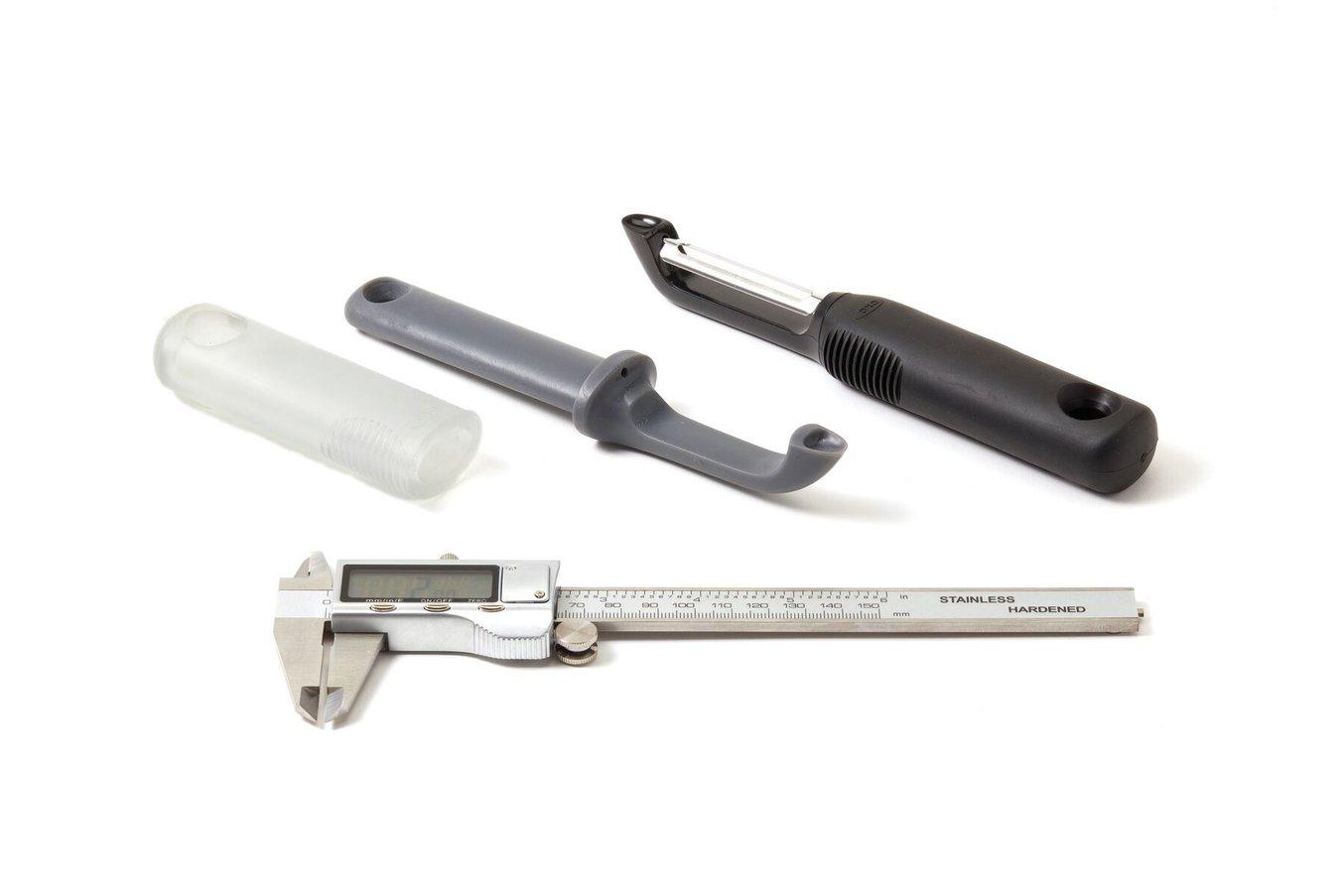
Die breite Materialpalette des Form 4 erlaubt es dem Team, neue Ideen und verschiedene mechanische Eigenschaften schnell und einfach zu testen.
Jeder, der den fast allgegenwärtigen Drehschäler von OXO schon einmal benutzt hat, weiß, wie leicht er mit Eimern voller Kartoffeln oder noch so exotisch geformten Früchten fertig wird. Der einfache, rutschfeste Griff und die flexible Drehklinge gehen aus OXOs ausgiebigem, anwendergestützten Validierungsprozess hervor. Um ein allseits beliebtes Gerät zu entwickeln, das von Millionen einzigartiger Hände benutzt werden soll, müssen Hunderte von Griffdesigns getestet werden. „Wir entwickeln ständig neue Produkte. Sämtliches schnelles und einfaches Prototyping passiert hier. Wir durchlaufen firmenintern Dutzende über Dutzende, manchmal sogar Hunderte von Iterationen“, so Emanuel.
Diese Prototypen müssen darüber hinaus maßgenau sein. Sie müssen selbst die winzigsten Änderungen des CAD-Modells wiedergeben, damit das Druckteil die Vorstellungen des Teams auch tatsächlich widerspiegelt. Die Teams, die Druckteile anfragen, benötigen 3D-Drucker, die Schicht für Schicht wiederholbare Präzision erzielen und dieselben Toleranzen einhalten wie die spritzgegossenen Endprodukte.
Das neue Drucksystem des Form 4, Low Force Display™, bietet zwei wichtige Funktionen, um die Präzision während des gesamten Druckprozesses beizubehalten. Zum einen sind dies die scharfen Randlinien der einzelnen ausgehärteten Schichten, die durch das hochauflösende Drucksystem mit innovativer neuer Light Processing Unit (LPU) möglich werden. Die zweite Funktion ist die Ablösetextur, mit welcher die auf die Druckschichten wirkenden Kräfte minimiert werden, was verringertes Kriechverhalten und eine insgesamt höhere Maßgenauigkeit zum Ergebnis hat. Die Teams von OXO haben das Resultat bereits erlebt und senden Emanuel mittlerweile mehr Dateien speziell für den Form 4. „Unsere Ingenieure fragen jetzt Teile aus dem Form 4 an, weil sie ihrer Aussage nach maßgenauer sind“, berichtet Emanuel.
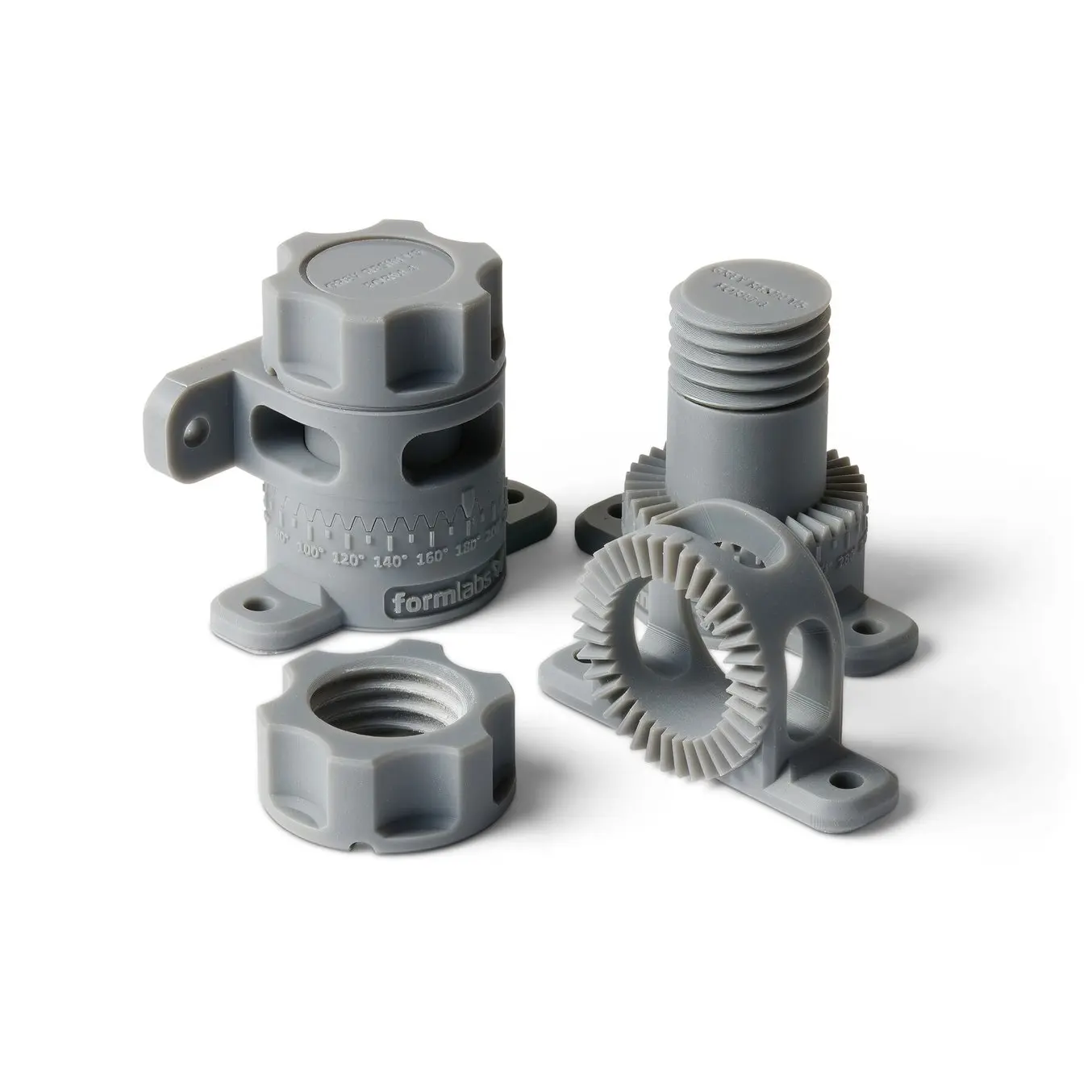
Kostenlosen Probedruck anfordern
Sehen und fühlen Sie die Qualität von Formlabs aus erster Hand. Wir senden Ihnen einen kostenlosen 3D-Probedruck an Ihren Arbeitsplatz.
Das richtige Material für jedes erdenkliche Teil
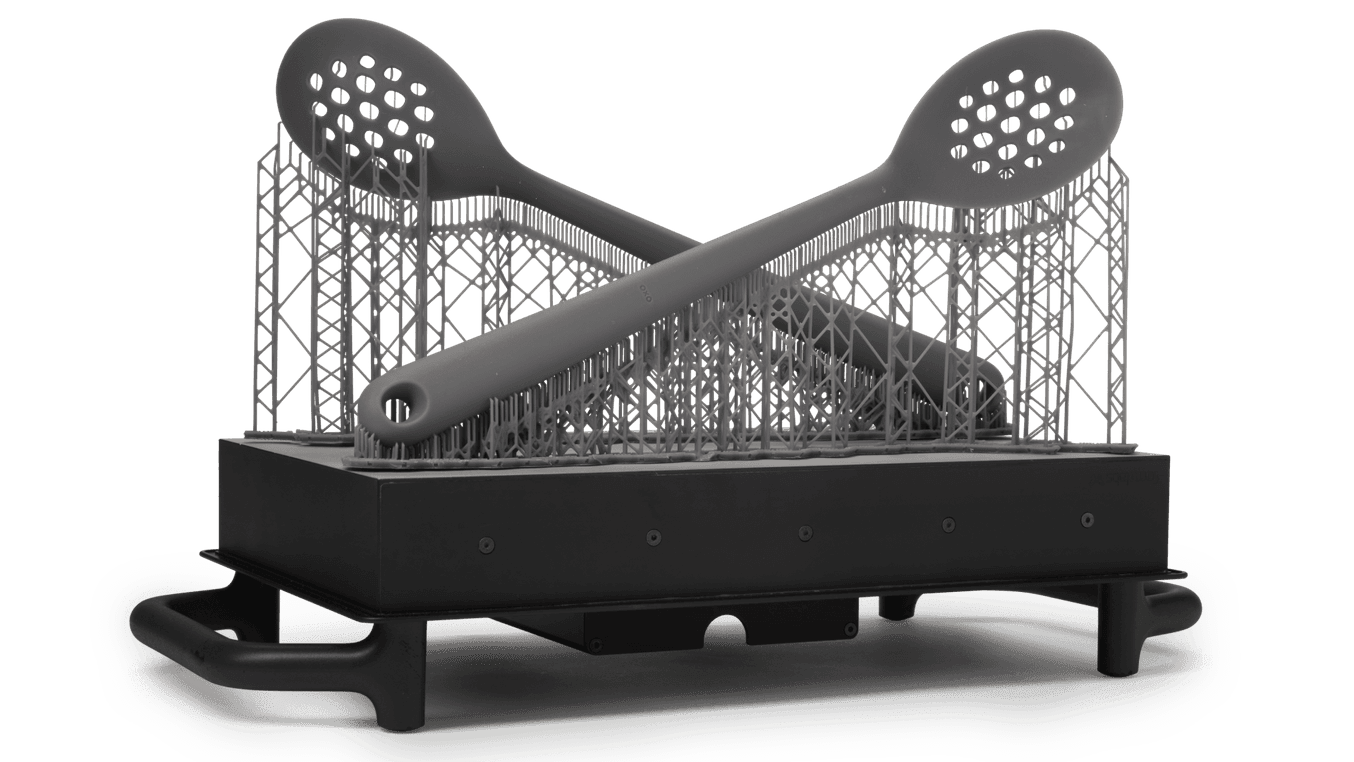
Das Ausmaß von OXOs Produktkatalog und das rasante Tempo des Marktes für Küchenutensilien führen dazu, dass das Team jeden Tag und auf jedem Drucker mehrere Materialien einsetzt. Deshalb müssen Materialwechsel einfach, sauber und fehlerfrei ablaufen. „Wir haben Hunderte von Produkten, die sich in ihrer Funktionsweise und den verwendeten Materialien stark unterscheiden. Die Formlabs-Materialien bieten und eine breitere Basis beim Prototyping der unterschiedlichen Produkte“, so Emanuel.
Dass das Team die Formlabs-Kunstharze stellvertretend für gängige Industriekunststoffe verwenden kann, macht die Design- und Testphase für OXO einfacher. Das Team verwendet Tough 2000 Resin für ABS-ähnliche Teile, Tough 1500 Resin für Polypropylen (PP), Silicone 40A Resin für Validierungsmodelle aus echtem Silikon, High Temp Resin für Prototypen, die in kochendem Wasser getestet werden, und Rigid 10K Resin für Spritzgussformen. „Für alle unserer Produkte nutzen wir eine Unmenge an unterschiedlichen Komponenten und Produkten.“
Zusätzlich zu den vielseitigen Materialoptionen der Formlabs-Drucker hat das Labor von Emanuel mehrere weitere Arten von 3D-Druckern im Einsatz. Doch seit dem Form 4 ist die Zahl der Anfragen nach SLA-Teilen angewachsen, aufgrund seiner Schnelligkeit und Maßgenauigkeit. „Ein wichtiger Grund, weshalb wir SLA statt FDM nutzen, sind die Materialoptionen. Wir nutzen etwa 12–15 Formlabs-Materialien, die wir aus den unterschiedlichsten Gründen einsetzen. Etwa Elastic oder Flexible für Teile mit geringem Härtegrad, oder Rigid für extrem steife Teile. Aber auch viel Grey Resin und viel Clear Resin.“
Für jede Aufgabe das passende Hilfsmittel
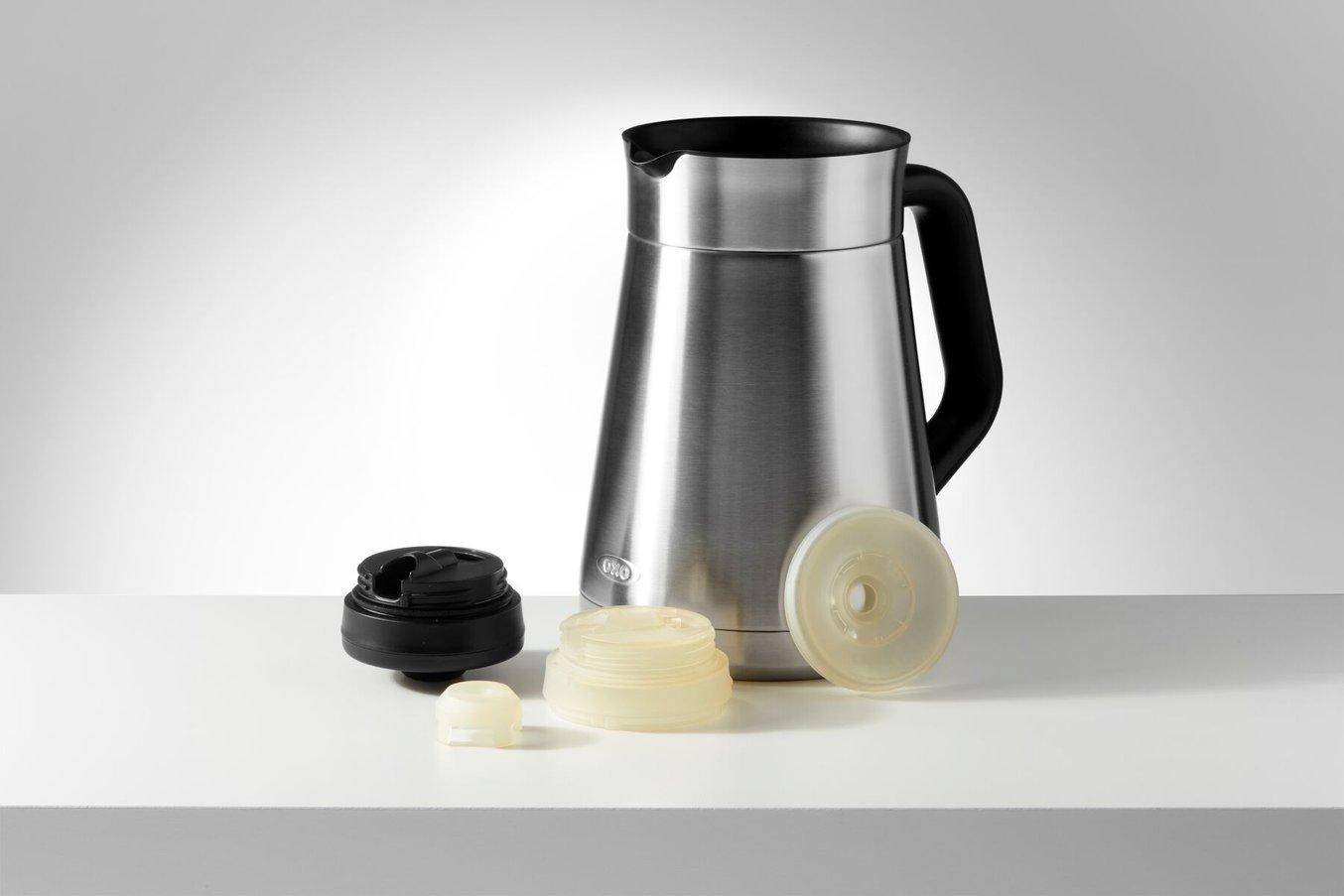
Die Produkte von OXO sind allgegenwärtig – in jedem Spülschrank und jeder Küchenschublade findet sich mit hoher Wahrscheinlichkeit mindestens eins davon. Jedwede Aufgabe, ob es um das Schälen von Gemüse oder das Kratzen von Eis auf der Windschutzscheibe geht, wird sofort leichter durch zuverlässige Hilfsmittel, die mit Sicherheit jedes Mal funktionieren.
Das ist auch im Prototyping-Labor von OXO nicht anders: Das Team benötigt Werkzeuge, die seinen Produktentwicklungsprozess beschleunigen, und nicht hemmen. Die Schnelligkeit, konsistente Genauigkeit und Materialauswahl des Form 4 ebnen den Weg zur Produktinnovation. Der 3D-Druck ist für OXOs Teams in Design, Konstruktion und Fertigung ein wertvolles Hilfsmittel, das Ihnen die Umsetzung neuer Ideen ermöglicht und sie vom Druck knapper Fristen befreit.
„Bis jetzt hat der Form 4 uns überwältigt.“
Jesse Emanuel, Prüfingenieur und Leiter der additiven Fertigung, OXO
Um mehr zu erfahren, besuchen Sie die Produktseite zum Form 4 oder fordern Sie einen kostenlosen Probedruck an, um sich selbst von der Qualität zu überzeugen.