Die Herstellung eines Prototypen für eine transparente Luftschleuse für eine Brauanlage mit 3D-Druck

Der Produktdesigner Michael Kononsky und der Ingenieur Pål Ingebrigtsen lernten sich 2015 bei einem Startup-Event in Norwegen kennen. Beide hatten ihre ersten Stelle nach dem Uniabschluss angetreten und waren durstig danach, etwas komplett Neues zusammenzubrauen.
Beide waren leidenschaftliche Hobby-Bierbrauer und sahen im weltweiten Aufkommen von Craftbier-Brauereien und der wachsenden Beliebtheit des Bierbrauens in der eignen Küche eine riesige Geschäftsgelegenheit: Allein in den USA gibt es heutzutage mehr als eine Million Amateurbrauer.
Mehr als 1000 Prototypen später wurde Plaato geboren, das erste Brauprodukt, das die CO2-Abgabe während des Gärprozesses misst und Brauern so Daten zur Verfügung stellt.
Erfahren Sie in diesem Blogeintrag von Kononsky, wie das Team von Plaato ein neuartiges, mit dem Red Dot Award ausgezeichnetes Design entwickelte, dafür per 3D-Druck Prototypen transparenter Teile herstellte und schließlich die Fertigung in Asien aufbaute.
Mehr Kontrolle für Amateurbrauer durch Daten
Die Kunst des Bierbrauens ist Jahrtausende alt. Mit der Zeit haben industrielle Brauereien das Verfahren minutiös verfeinert und verwenden moderne Technologien, um alle Aspekte des Brauprozesses zu analysieren und zu kontrollieren. Doch Amateurbrauer sind häufig auf Glück angewiesen und erzielen somit wechselhafte Ergebnisse.
Kononsky und Ingebrigtsen hatten die Idee, ihre Kenntnisse mit neuen Technologien zu kombinieren, um das weltbeste Produkt für Amateurbrauer zu entwickeln.
„Wir hatten die Idee, dass es toll wäre, Daten beim Bierbrauen sammeln zu können. Denn der Gärprozess, mit dem alles steht und fällt, ist ein Mysterium. Du verschließt das Braugefäß für zwei Wochen und hast keine Ahnung, was in seinem Inneren vor sich geht. Du hast keine Ahnung, ob das Bier gut oder schlecht wird, ob es zu warm ist oder zu kalt...", so Kononsky.
„Dann öffnest du das Behältnis und stellst fest: ‚Na toll, das ist überhaupt nichts geworden.‘ Oder: ‚Oh ja, das ist echt gut!‘“ Aber dann schaffst du es nie, dein Ergebnis zu reproduzieren, und kannst dein Rezept nicht mit Freunden teilen, weil du nicht über die richtigen Tools dafür verfügst.“
Die Luftschleuse von Plaato misst die CO2-Angabe während der Gärung.
Kononsky entdeckte Forschungsergebnisse aus den 1980er Jahren, die belegten, das sich die Schwerkraft, die Gäraktivität und der Alkoholgehalt der Flüssigkeit aus dem während der Gärung freigesetzten CO2 berechnen lassen. Wenn er also die „Bläschen“ zählen und ihr Volumen per Maschinenlernen messen könnte, so könnte er diese biologischen Daten in digitale Daten überführen und bestimmen, ob die Gärung zu aggressiv oder zu langsam abläuft. Zudem könnte er so feststellen, wie sich verschiedene Zucker- und Hefearten auf die Gärungskurve auswirkten.
„Wir überwachen das Bier wie einen Patienten auf der Intensivstation. Es macht dein Bier nicht unbedingt besser, aber es macht dich zu einem besseren Brauer, weil es dir mehr Informationen zur Verfügung stellt. Nach jeder gefertigten Ladung erhältst du einen Bericht, der dir zeigt, was schlecht und was gut funktioniert hat. So kannst du das Ergebnis reproduzieren oder es mit leichten Abänderungen noch einmal versuchen und mit Freunden teilen, um es gemeinsam zu analysieren,“ so Kononsky.
Die Herstellung eines Prototypen für eine transparente Luftschleuse
Kononsky und Ingebrigtsen sahen sich viele verschiedene Methoden an und fanden sogar das perfekte Messgerät für den CO2-Fluss. Doch die Verwendung für das Braugerät brachte einzigartige Herausforderungen mit sich.
„[Zum Brauen] musste das Produkt resistent gegenüber Korrosion und Flüssigkeiten sein. Du musst alles reinigen und desinfizieren können, da stets das Risiko einer Verunreinigung und Infektion besteht. Wir mussten eine Methode zur Überwachung der Gäraktivität entwickelt, bei der keine Sensoren direkt im Gebräu platziert werden mussten, da es äußerst sensibel auf invasive Messmethoden reagiert. Wir mussten also ein Produkt herstellen, dass die Aktivität maß, ohne mit dem Bier in Berührung zu kommen", so Kononsky.
Deshalb entschlossen die Unternehmer sich, eine transparente Luftschleuse zu entwickeln.
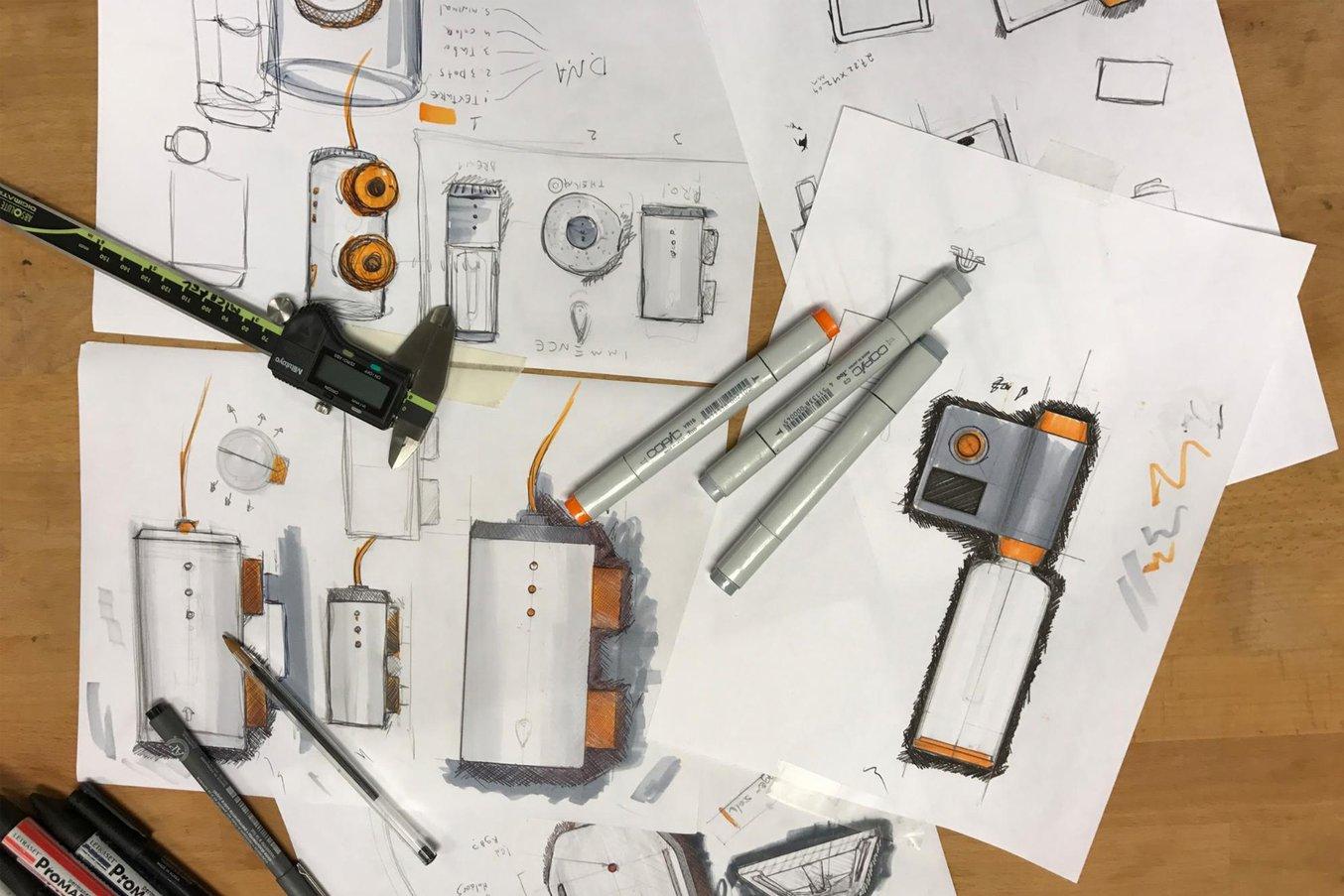
Es gibt wenige Möglichkeiten, Prototypen transparenter Teile zu fertigen. Kononsky versuchte es mit CNC-Bearbeitung und dem Outsourcing an externe Serviceanbieter. Doch beide Methoden waren ihm zu langsam und zu teuer. „Wir berechneten, dass wir für den Preis von 3 – 4 Versionen einen neuen Formlabs 3D-Drucker kaufen konnten,” so Kononsky.
Lesen Sie unser Tutorial, in dem wir Fertigstellungsmethoden zur Herstellung transparenter 3D-gedruckter Teile erklären.
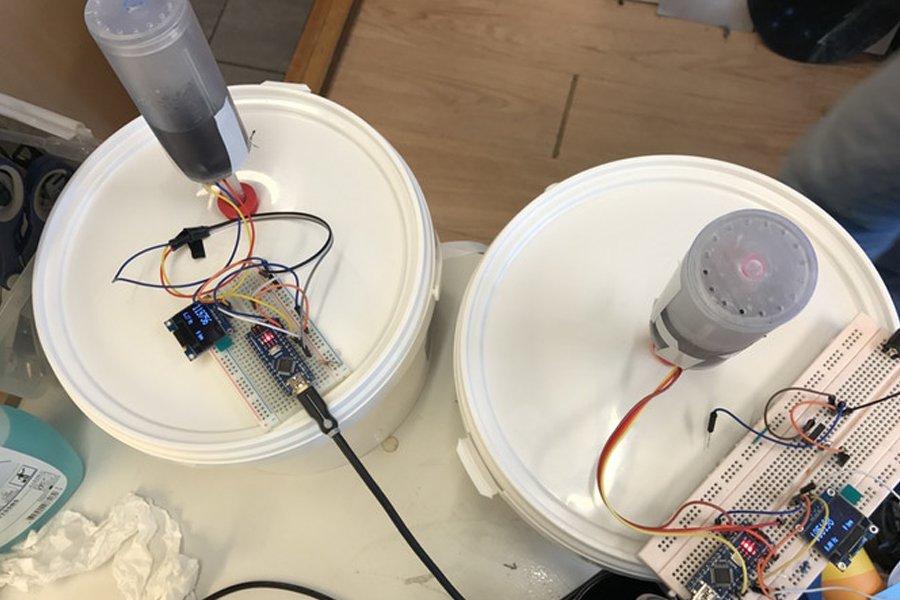
Der 3D-Drucker at their desk allowed the team to test multiple iterations a day, at low costerlaubt es dem Team, jeden Tag kostengünstig mehrere Versionen zu testen.
„Wir 3D-druckten sprichwörtlich Tag und Nacht, bis wir einen funktionierenden Prototypen hatten, weil die Kosten, um etwas Neues auszuprobieren, so gering waren. Die Stückkosten für diese transparenten Teile sind praktisch irrelevant. Der Drucker stellt einen großen Mehrwert für uns dar. Es war fast, als hätten wir einen weiteren Designer im Team", so Kononsky.
„Wir haben insgesamt etwa 1.000 verschiedene transparente Prototypen hergestellt. Wir stellten sechs Prototypen am Tag her und passten das Design nach unseren Vorstellung in Solidworks an, während sich ein weiterer Teil bereits im Druck befand. Wir maßen die Bläschen und den Luftstrom, spielten mit den Parametern und brachten Maschinen- und empirisches Lernen zur Anwendung. Wenn du so intensiv mit den Teilen arbeitest, verstehst du das Material und seine Eigenschaften durch und durch.“
Kononsky und Ingebrigtsen benötigten extrem genaue Prototypen, die sie zerlegen, reinigen, waschen und dann wieder zusammenbauen konnten. Nach dieser Prozedur musste das Teil sich wieder in exakt derselben Position einfügen, damit der Sensor auch beim nächsten Test den Messwert korrekt anzeigte.
Die Luftschleuse besteht aus mehreren Teilen, die gereinigt, gewaschen und dann wieder exakt wie zuvor zusammengebaut werden können müssen, damit akkurate Messung geliefert werden.
„Es ist dasselbe Prinzip wie bei einem Kugelschreiber mit einer Außenschale, die nach dem Aufklicken kein Spiel mehr hat. Wir haben das mit einer Kombination aus Clear Resin für den transparente Teil und Tough Resin für die Basis erreicht. Transparente Teile sind sehr fest, während das feste Unterteil Flexibilität für eine winzige Nut, Lamellen und einen Doppelklickring bot. Wir konnten so das Verhalten des Endprodukts simulieren; es funktionierte zu 100 % wie das im [Spritz-]Guss gefertigte fertige Teil“, so Kononsky.
In unserem Whitepaper ferläutern wir, wie Toleranzen für die einzelnen Passungen zu messen und anzuwenden sind und geben spezifische Empfehlungen für Tough Resin und Durable Resin von Formlabs. Sie finden zudem Downloadlinks für Testmodelle und Empfehlungen zu Schmierstoffen, Verbundteilen und maschineller Bearbeitung.
Der Benchmark für die Fertigung
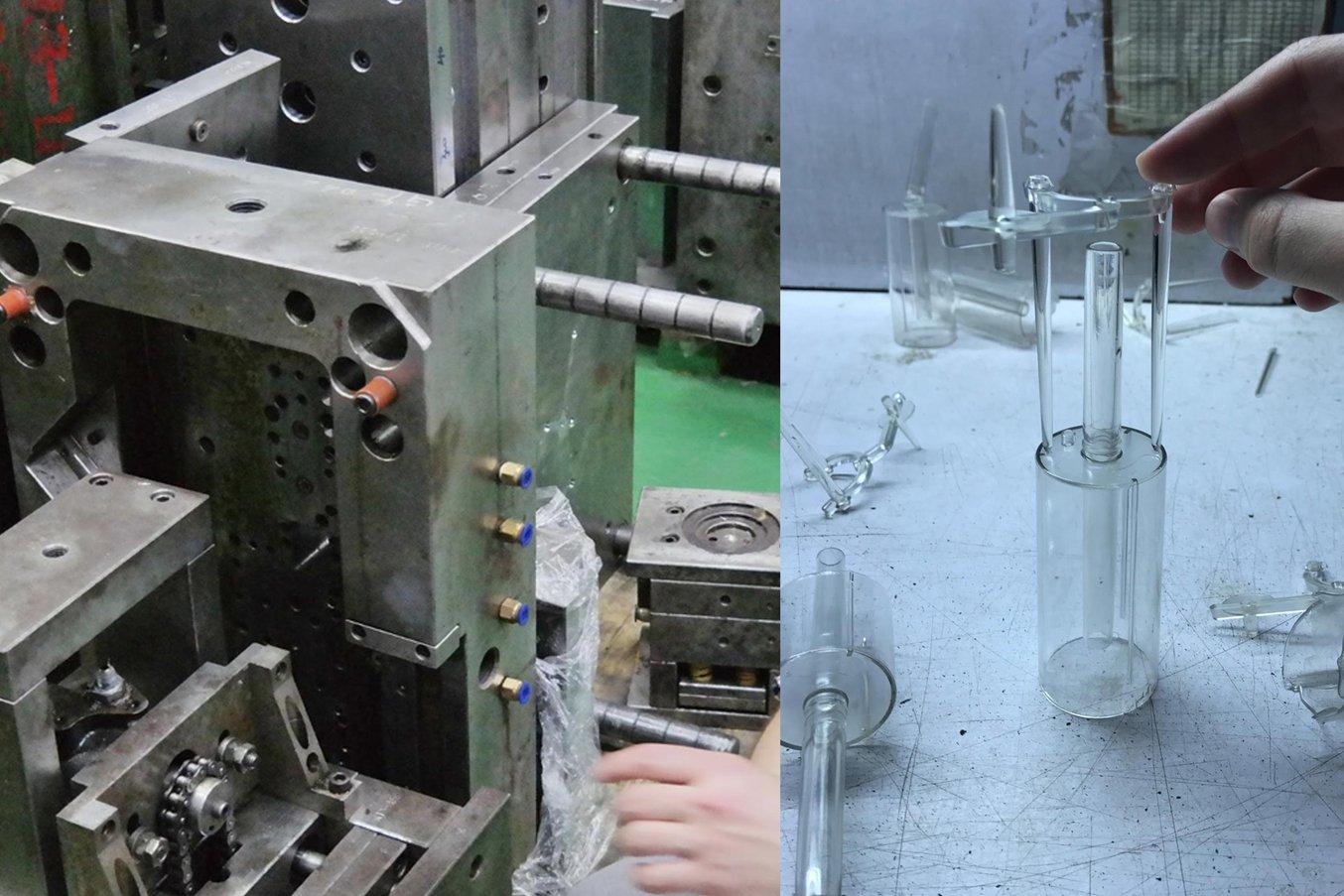
Nach einer erfolgreichen Crowdfunding-Kampagne, um die Kosten für die teuren Formen und die Werkzeugbestückung zu finanzieren, fuhr das Team die Fertigung in Asien hoch, wo der Prototyp als Referenz diente.
„Es handelte sich um unser (fast) perfektes Muster. Beim Spritzguss muss man immer ein gewisses Maß an Schrumpfung berücksichtigen, die beim 3D-Druck nicht anfällt. Auch die Oberflächenspannung und die Eigenschaften des Kunststoff wichen leicht ab. Doch damit lag uns ein Benchmark vor, sodass wir gemeinsam mit Ingenieuren innerhalb weniger Formversionen dieselben Toleranzen erzielten wie beim 3D-Druck. Wir mussten einfach nur die Eigenschaften des gedruckten Prototypen nachbilden. Wir hatten also einen Referenzpunkt zur Hand, sodass wir nicht blind raten und testen mussten“, so Kononsky.
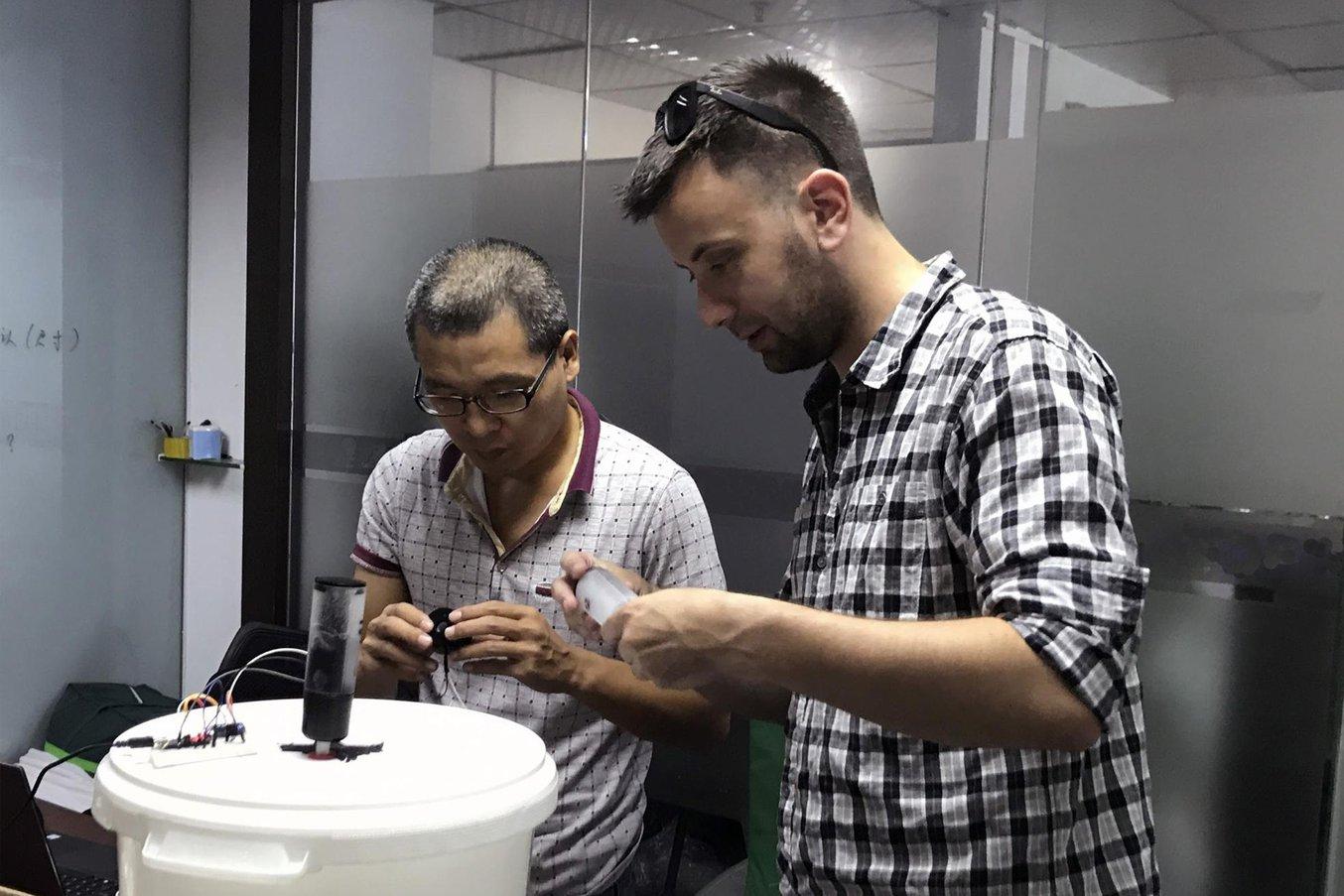
Von der Amateurbrauerei zur Mikrobrauerei
Die Unternehmer erhielten den prestigeträchtigen Red Dot Award für das „ästhetisch ansprechende, raffinierte Design des Plaato, das die traditionell beim Bierbrauen verwendete Luftschleuse in das digitale Zeitalter befördert.“
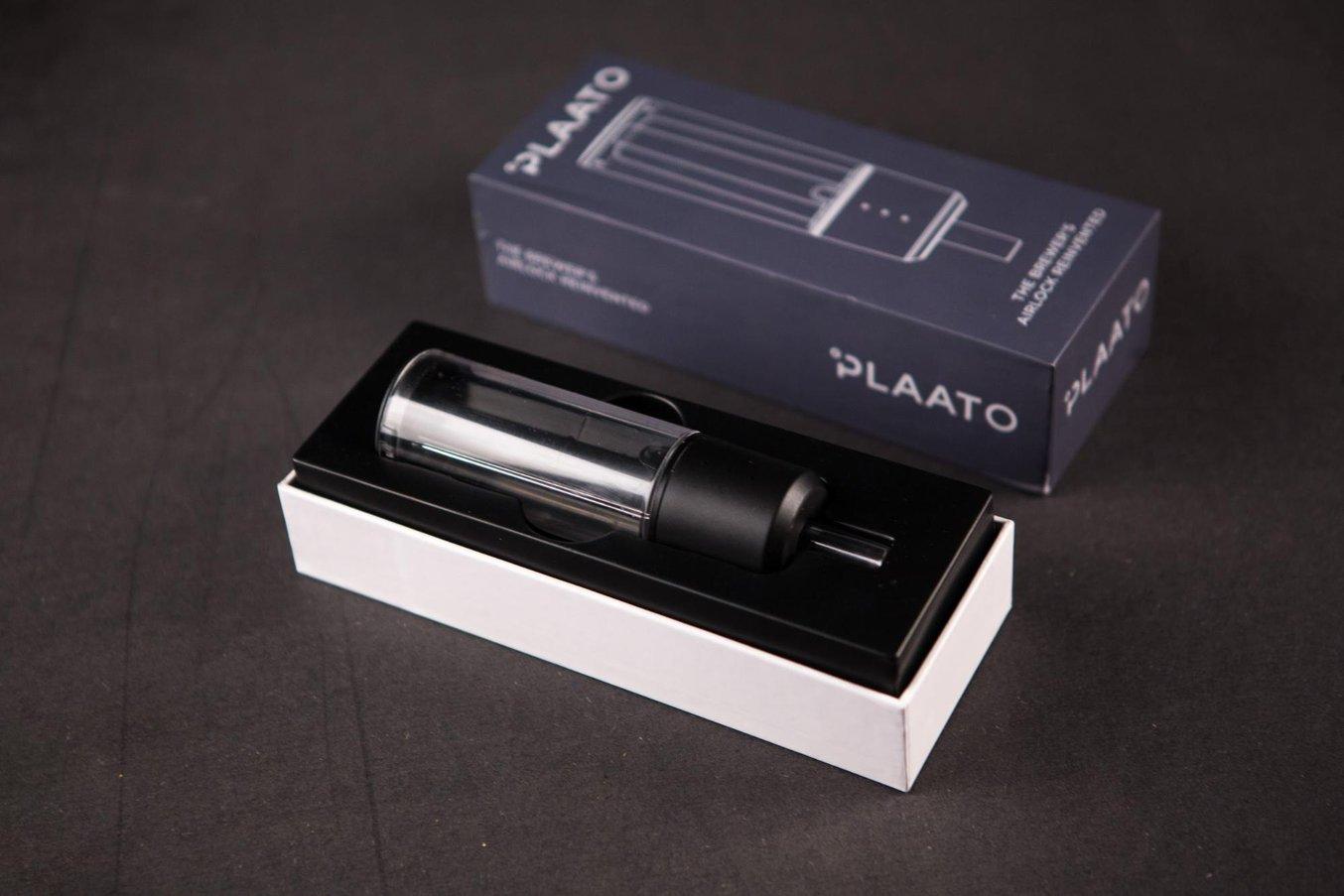
Mit 4000 ausgelieferten Einheiten konzentrieren Kononsky und Ingebrigtsen sich jetzt auf die Optimierung der Fertigung. Sie wollen sie kosteneffektiver machen und ihre Produktlinie um eine neue kommerzielle Version ihrer Luftschleuse für kleine und mittlere Brauereien ergänzen, bei denen ein höheres Gärvolumen anfällt.
Schnellere Produktentwicklung mit dem Form 2
„Ich sage dem Team immer wieder, dass ich keine Ahnung, was ich ohne den Form 2 getan hätte. Wir hätten wahrscheinlich nicht einmal unsere Fertigungskapazitäten verstanden. Wahrscheinlich würden wir ein sperriges Teil mit einem Glasfensterchen verwenden. Weit entfernt von den Maßen, die wir dank 3D-Druck erzielt haben“, so Kononsky.
Unternehmensinternes Rapid Prototyping hat Tausenden Ingenieuren und Produktdesignern geholfen, in jeder Phase der Produktentwicklung komplexe Probleme zu lösen und Kosten und Zeit einzusparen.
Lernen Sie den Form 2 und die Bibliothek an technischen Kunstharzen von Formlabs und fordern Sie einen kostenlosen Probedruck an, um sich selbst einen Eindruck von den Materialien zu verschaffen.