„Ich habe sogar den Weg zum Supermarkt zwei Straßen weiter aufgegeben.“
Als der Gründer von WHILL Satoshi Sugie diesen Satz hörte, war ihm klar, dass die Leute etwas Besseres verdienen. Heute leitet er eine Rollstuhlmanufaktur mit der Mission, den Fußweg um Spaß und Innovation zu bereichern.
Die nächste Generation des Rollstuhls zu bauen, war kein Leichtes. Ingenieure bei WHILL nutzen die Drucker von Formlabs und einen generativen Designvorgang für ein wahrlich einmaliges Produkt.
Im Folgenden erfahren Sie von Herrn Yasuhiro Hirata mehr über die Entwicklung des WHILL-Rollstuhls.
3D-Druck zur Beschleunigung der Entwicklung
Startups kämpfen mit zahlreichen Problemen, nicht zuletzt mit Zeitdruck und Kosteneffizienz. Ganz besonders gilt das für Startups in der Gerätetechnik (davon können wir selbst ein Lied singen), da diese oft brandneue Probleme von Grund auf lösen wollen. Dabei ist eine der entscheidendsten Prüfungen das Überwinden unvorhergesehener Hürden, die durchaus teuer und zeitaufwändig sein können. WHILL traft aufgrund der komplexen Teile des Rollstuhls auf zahlreiche Probleme, insbesondere weil die Kleinserienproduktion mit traditionellen Fertigungsverfahren eine Herausforderung darstellen kann. Damit das Unternehmen überleben konnte, musste es die Kosten jedes Rollstuhls verringern.
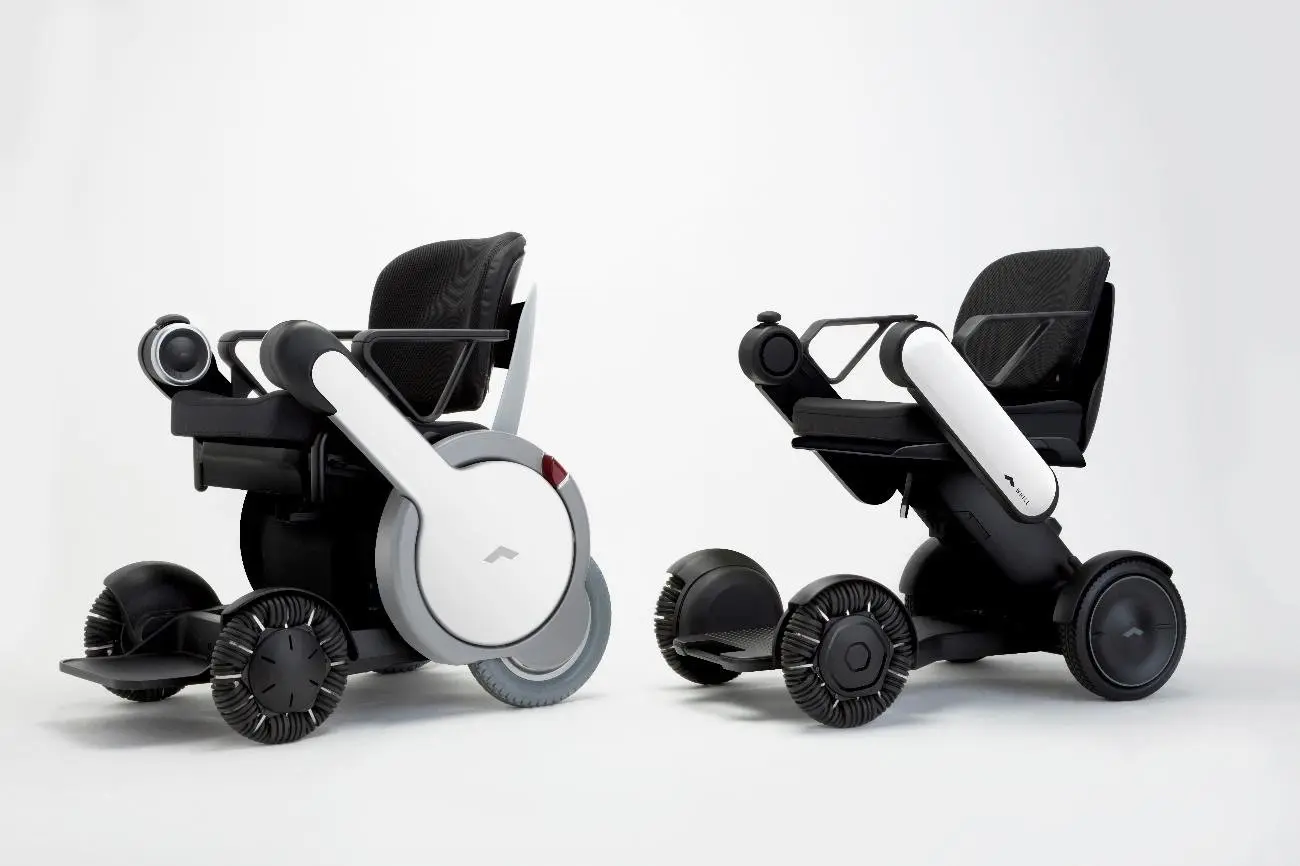
Das Unternehmen stellte fest, dass es die Prototypen vieler der komplexen Rollstuhlteile beschleunigen musste, und wandte sich deshalb an das Outsourcing zu einem 3D-Druckdienstleister. WHILL erfuhr schon bald, dass die Kosten- und Geschwindigkeitseinschränkungen beim Outsourcing des 3D-Drucks nicht auf Dauer mit dem Arbeitsprozess vereinbar waren. Herr Hirata wusste, WHILL könnte das Projekt ohne handfeste Prototypen niemals beenden. Und so brachte man den 3D-Druck in den Betrieb.
„Wenn Sie bezüglich der besten Form nicht sicher sind, dann stellen Sie sie her und prüfen Sie es.“
Herr Hirata war von den älteren Schmelzschichtungsdruckern nicht beeindruckt, mit denen er zuvor gearbeitet hatte. Doch hatte er den Erfolg von Formlabs mitverfolgt und entschied sich für die Investition in eines unserer Geräte. 2016 integrierte WHILL den ersten Formlabs-Drucker in das Team. Seitdem wird das Gerät für verschiedene Projekte genutzt und bietet genau das, was das Team braucht: schnelle, hochqualitative Prototypen. Die wichtigsten Teile sind jene, die direkt vom Nutzer berührt werden. Bei solchen Prototypen müssen die Teile realistisch aussehen und sich auch so anfühlen, und nicht einfach nur billig und innen hohl. Der Formlabs-SLA-Drucker bot genau das, was Herr Hirata für seine Endverwendungsprototypen brauchte: hochqualitative, detaillierte und kostengünstige Teile.
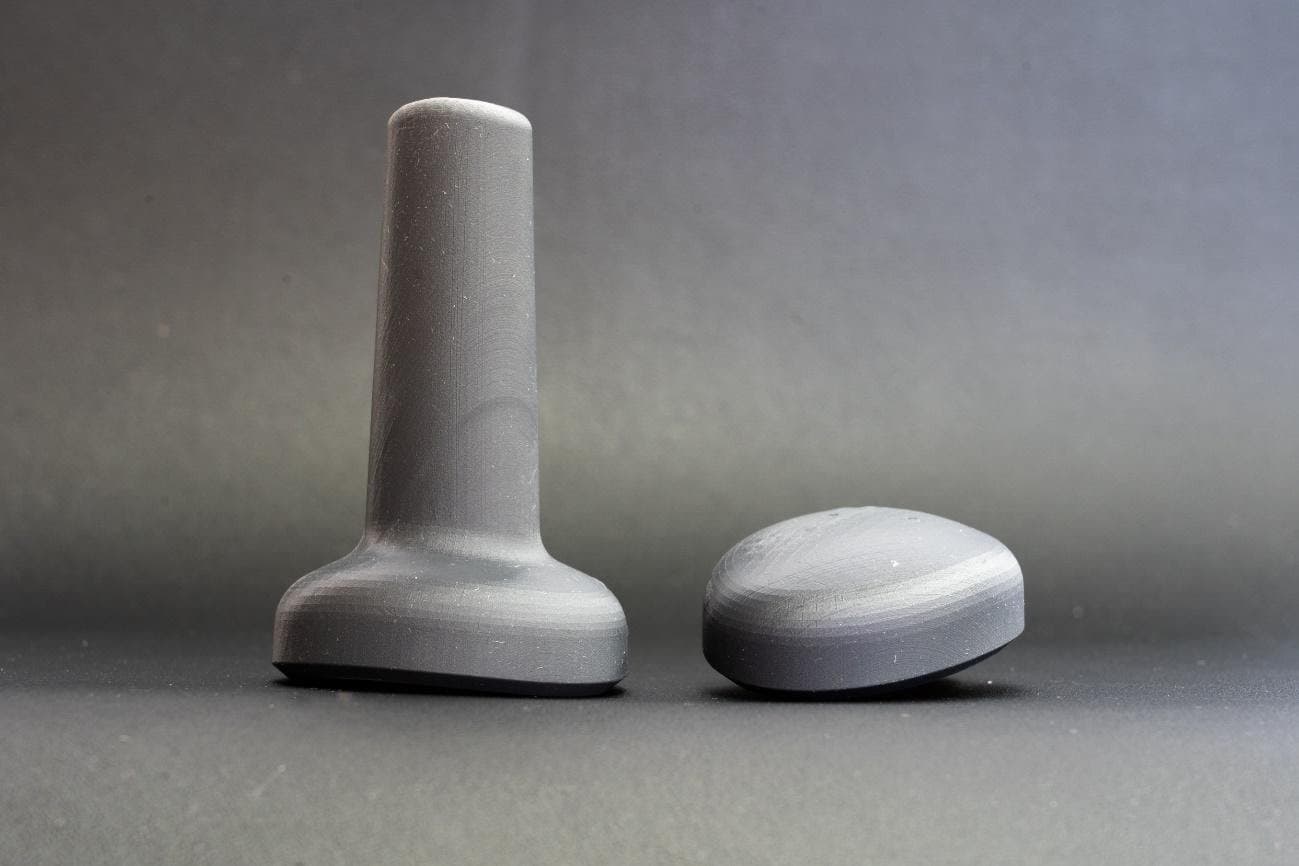
Ohne die Integration des hochauflösenden 3D-Druckers in das Entwicklungsteam bei WHILL wäre das Endprodukt nicht möglich gewesen. Bei der Bewertung insbesondere der Tastempfindung ist eine Verifikation sinnlos, solange die Teile nicht mindestens dieselbe Qualität haben wie die letztendlichen Massenfabrikate. Für WHILL erwiesen sich die Formlabs-Teile als perfekte Repräsentationen sowohl für interne als auch für Nutzertests der Rollstuhlprototypen.
„Für die vom Nutzer berührten Teile wie die Steuerung versuchen wir, so viele Prototypen wie möglich zu erstellen und zu prüfen. Beim Outsourcing der Prototypen in der Vergangenheit waren die Produktions- und Testmöglichkeiten eingeschränkt durch Budget und zeitliche Planung. Der Form 2 bietet mit Flexible Resin ein ähnliches Tastgefühl wie das letztendliche Produkt. So modellieren und verifizieren wir hochpräzise Prototypen, ohne dabei mengenmäßig Kompromisse einzugehen.
Yasuhiro Hirata
Das Team nutzte verschiedene Kunstharze beim selben Projekt und damit die Vielseitigkeit eines einzelnen Formlabs-Druckers. Flexible Resin eignete sich ideal für Berührungspunkte, aus Clear Resin druckte man lichtdurchlässige Teile im Bereich des Rollstuhldisplays und Tough Resin fand Verwendung bei Teilen, die mehreren Tests auf Festigkeit unterzogen wurden. Ein einziges Gerät, das mehrere Teile aus verschiedenen Materialien abhängig vom Zweck drucken kann, spart wichtige Zeit und Kosten in einem Startup für Gerätetechnik.
„Der Form 2 ist nicht nur präzise, er lässt uns auch nur selten im Stich. Diese Zuverlässigkeit ermöglichte uns mehrere Prototypenvariationen am selben Tag sowie die zugehörigen Prüfungen, die zur Verbesserung unserer Qualität beitrugen.“
Yasuhiro Hirata
Prototypenentwicklung ist mehr als nur die Perfektion eines einzelnen Teils. Durch den Test verschiedener Designs lassen sich mehrere Teile optimieren und auch zusammenfassen, um die Montage zu erleichtern. WHILL konnte die letztendlichen Produktionskosten des Rollstuhls senken, indem man die Gesamtmenge der Teile verringerte. Dies bedeutete einen großen Durchbruch für das Team, der erst durch betriebsinternen 3D-Druck möglich wurde sowie durch das generative Design der Teile.
Generatives Design
Generatives Design nutzt Algorithmen, um Hunderte oder Tausende optimierte Designs zu erstellen, die auf Schlüsselgrundsätzen des Designs basieren und Funktionen, Platzeinschränkungen, Materialien, Herstellungsverfahren und Kosten berücksichtigen.
Das Team von WHILL hatte sich ein einzelnes, solides Teil für die Mitte des Rollstuhls zum Ziel gesetzt. Mithilfe generativen Designs wurden mehrere Entwürfe gleichzeitig analysiert. Das Problem bei designten Einzelstücken ist, dass sie kostspielig oder mit herkömmlichen Fertigungsverfahren nicht umsetzbar sind.
„Falls die Kosten keine Rolle spielen, kann man mit einem leichtgewichtigen Material wie Kohlenstofffaser arbeiten. Aber das ist nicht realistisch. Bei unserem Ziel, das Gewicht mit einem realistischen Material zu verringern, kamen wir auf die Idee mit dem generativen Design. Wir mussten Prototypen mit komplexer Gestalt in kürzester Zeit herstellen, und das war meiner Meinung nach nur mit den 3D-Druckern und Kunstharzen von Formlabs möglich.“
Yasuhiro Hirata
Dieses neue, komplizierte Teil wurde zuerst betriebsintern mit Castable Wax Resin von Formlabs gedruckt. Das Team nutzte Autodesk Fusion 360 zur Erstellung des Hauptgestells seines Rollstuhls und führte die Prototypenentwicklung anhand generativen Designs betriebsintern durch – was für das Team ein eindrucksvolles Erlebnis war. Das Endergebnis war, dass WHILL allein das Gewicht des Rollstuhlgestells um 40 % verringern konnte.
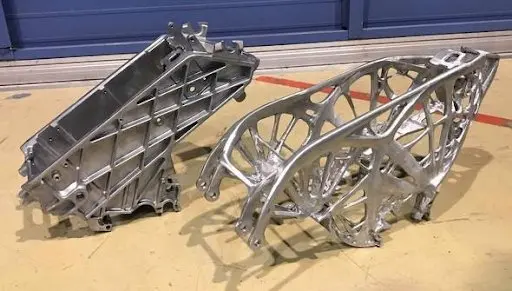
Betriebsinterne Prototypenentwicklung mit Formlabs
WHILL ist nur eines von vielen Unternehmen, die unglaubliche Produkte mithilfe betriebsinternen Rapid Prototypings herstellen. Laden Sie unser kostenloses E-Book zum Rapid Prototyping herunter, in dem wir Ihnen sechs weitere Unternehmen vorstellen, die ihr Geschäft mit der Anschaffung eines Formlabs-Druckers komplett umgewandelt haben.