Im Rausch der Geschwindigkeit: Rome Snowboards bringt seine Produktentwicklung mit SLS-3D-Druck auf Touren
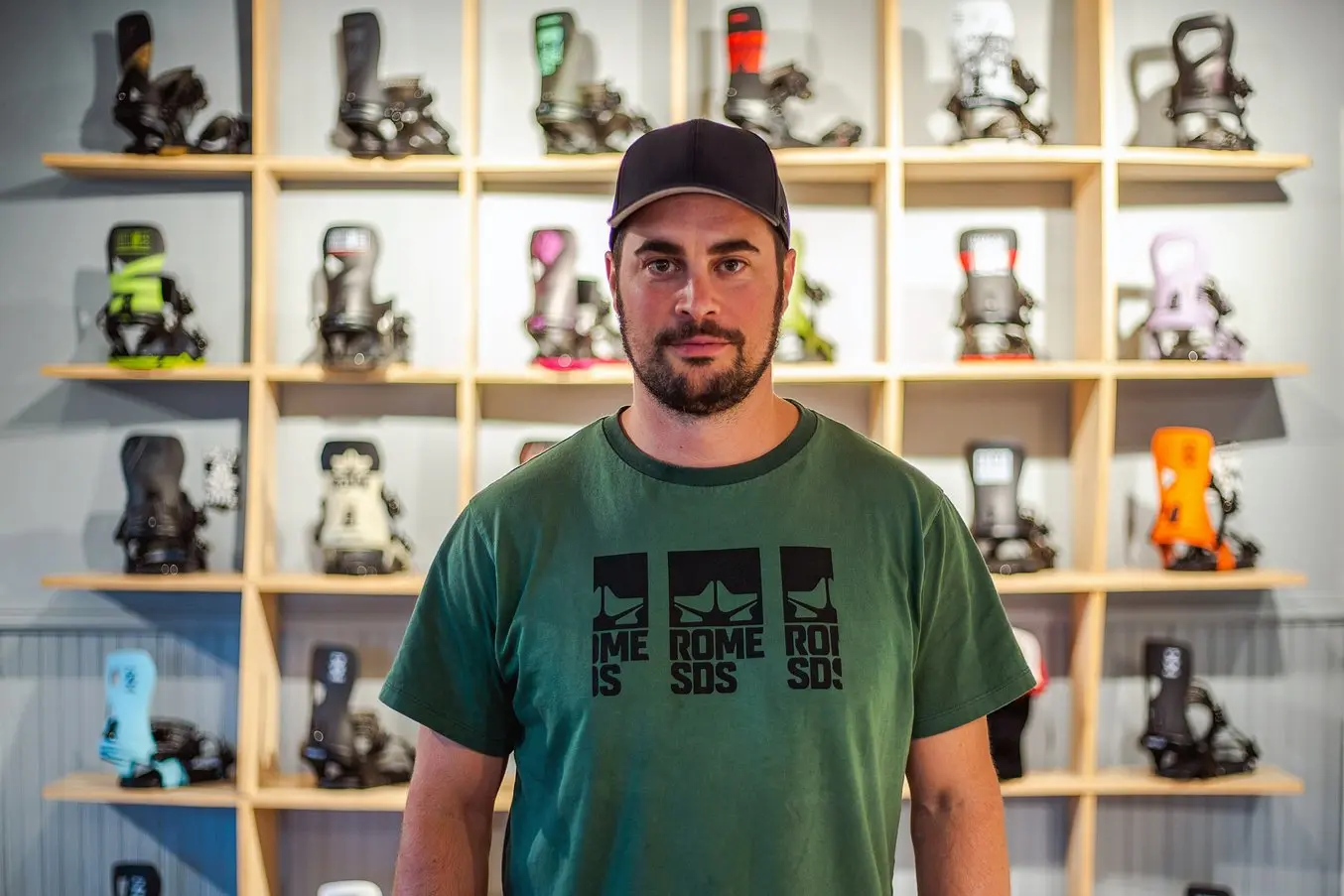
Justin Frappier ist einer der Product Designer von Rome Snowboards. Dank des betriebsinternen SLS-3D-Drucks kann er jeden Tag neue Designs und Prototypen erstellen und nach Belieben iterieren.
„Wir versuchen uns immer in Dingen, die noch keiner zuvor probiert hat. [...] Dabei sehen wir bereits, wie sich die Investition rentiert. Das haben wir schon in den ersten fünf Monaten, allein durch die schnellere Prototypenentwicklung.
Justin Frappier, Product Designer bei Rome Snowboards
Seit seiner Erfindung in den 60er-Jahren wird dem Snowboarden als Sport immer etwas Rebellisches zugeschrieben. Mit seinen jungen, unbesonnenen Stars, der Baggy-Mode und den prahlerischen Kunststückchen im Gelände ist es der punkige kleine Bruder der versnobten Wintersportwelt. Die stilistischen Ähnlichkeiten zum Surfen und Skateboarden sprechen dieselbe Zielgruppe an und stärken das Gefühl einer eigenen Kultur.
Das Snowboarden ist aus dem Drang entstanden, die Dinge anders zu machen – und das spiegelt sich auf der technischen Seite auch in der Ausrüstung wider. Snowboard-Ausrüster finden immer wieder neue Wege, um den Boardern mehr Zeit auf der Piste zu verschaffen. Die Ausrüstung muss zuverlässig, robust und bequem sein und einer ganzen Wintersaison auf den Hängen standhalten. Damit der iterative Prozess schneller vonstattengeht und ein konstanter Strom innovativer, neuer Designs fließt, wenden sich die Hersteller dem betriebsinternen 3D-Druck zu.
Rome Snowboards ist ein kleines, zehnköpfiges Unternehmen aus Waterbury im US-Bundesstaat Vermont. Das Firmenmotto lautet: „All Ways Down“ (alle Abfahrtswege, alle Abfahrtsformen), ein Wortspiel auf „Always down“ (immer bergab). Das ist sowohl ihr Credo auf dem Berghang als auch im Entwicklungsprozess. Product Designer Justin Frappier sucht immer nach neuen Prozessen und Methoden zur Herstellung der Bindungen und Stiefel. Romes angestrebtes Ziel ist die Entwicklung von Ausrüstung, die längere, bequemere Abfahrten ermöglicht und den Kräften und Stößen bei Sprüngen, Drehungen und beim Rutschen standhält. Dank des neuen, betriebsinternen SLS-3D-Druckers (selektives Lasersintern) Fuse 1 wird die Innovation bei Rome beschleunigt und die Prototypen können direkt auf dem Berghang getestet werden. Das macht den iterativen Prozess gründlicher. „Wir versuchen uns immer in Dingen, die noch keiner zuvor probiert hat. [...] Dabei sehen wir bereits, wie sich die Investition rentiert. Das haben wir schon in den ersten fünf Monaten, allein durch die schnellere Prototypenentwicklung“, sagt Frappier.
Bereits jetzt erstellt Rome einige der begehrtesten Produkte der Branche und verdient sich Bewertungen in Publikationen wie White Lines, die Romes Bindungen vom Typ Vice auf die Liste der 100 besten Snowboardprodukte 2021-22 setzten und kommentierten mit: „Es handelt sich um eine extrem vielseitige Bindung, die erprobte Technologie mit Premium-Eigenschaften kombiniert. [...] Rome hat mit der jüngsten Version des Verkaufsschlagers Vice genau ins Schwarze getroffen.“
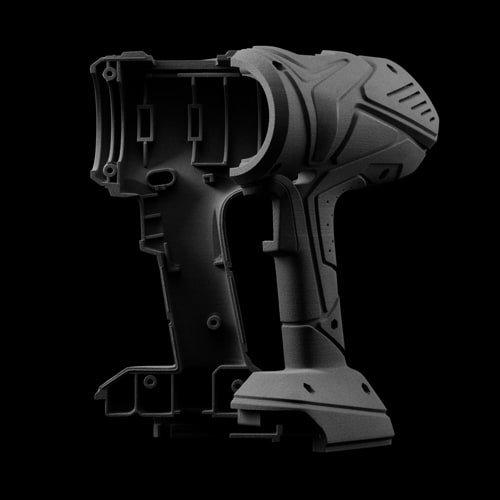
Einführung in den 3D-Druck mit selektivem Lasersintern (SLS)
Suchen Sie nach einem 3D-Drucker, mit dem Sie starke, funktionsfähige Teile herstellen können? Laden Sie unser Whitepaper herunter und erfahren Sie, wie SLS-Druck funktioniert und wieso es ein beliebtes 3D-Druckverfahren für funktionales Prototyping und die Produktion von Teilen für die Endverwendung ist.
Ab auf die Piste mit SLS-Druck
Vor dem Fuse 1 leisteten Frappier und sein Kollege in Romes Designteam den Großteil der Designarbeit von Hand. Dabei arbeiteten sie mit Materialien wie Formmasse oder Kitt sowie mit ausgelagerter Teileproduktion und alles musste für die letztendliche Prototypenoptik zusammengebaut und nachbearbeitet werden. Von 3D-Druck hatte er zwar schon gehört, aber es dauerte bis zu einem Teaser des Fuse 1, in dem eine Snowboard-Bindung vorkam, bis Frappier sich erkundigte. „Das ist etwas, das ich bestimmt schon seit acht Jahren ins Büro holen wollte ... Wir haben uns die Vor- und Nachteile verschiedener Drucker angesehen sowie die unterschiedlichen Preise. Dabei erschien uns der Fuse 1 als richtig gute Lösung, weil auch der Fuse Sift dazu gehört. Es wirkte alles sehr durchdacht“, berichtet Frappier.
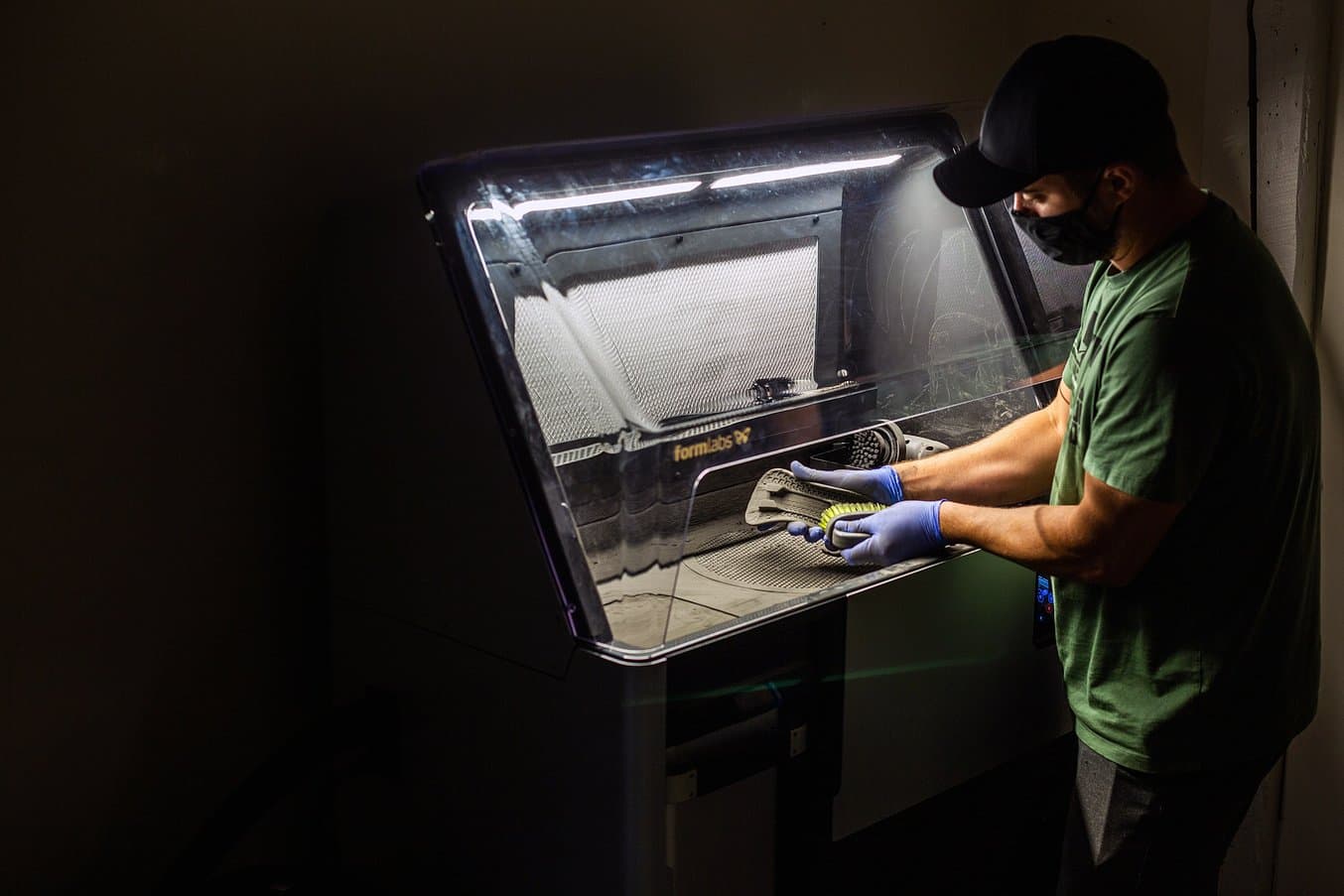
Der Fuse Sift optimiert die Nachbearbeitung und die Pulverwiederverwertung. So gewinnt Frappier mehr Zeit für schwierige Designaufgaben.
Neben Formmassemodellen bestellte das Team auch 3D-Druckteile von der anderen Seite der Grenze, aus Montreal. Und obgleich das nicht übermäßig teuer war, war es die Durchlaufzeit, unter der das gewohnte Designtempo litt. „Wir mussten uns hinter anderen Unternehmen anstellen. Und unsere Entwicklungszeit hing von der Geschwindigkeit ab, wie schnell wir die Teile zurückerhielten“, erklärt Frappier.
Für ein kleines Unternehmen wie Rome, das für seine individualisierten Bindungen bekannt ist, bedeuten Entwicklungsverzögerungen Nachteile gegenüber großen Herstellern. Die Stärke des Unternehmens liegt in der Iteration und in der schnellen internen Absegnung, sodass es diese einzigartigen Produkte als erstes Unternehmen der Branche einführt, wie z. B. die patentierten Technologien AuxTech, PivotMount und AsymWrap.
„Wir hatten den Fuse 1 etwa sechs Monate und sahen die Vorteile des betriebsinternen Drucks ziemlich schnell. Ungefähr sechs Monate hatten wir an Schnallen verbracht. Schnalle drucken, zusammenbauen, Einraststufen prüfen, Probleme und Störungen sehen. Es war superhilfreich, den Drucker zu haben. Wir drucken ein Teil, prüfen es am nächsten Morgen, bauen es zusammen, machen unsere Änderungen und am nächsten Tag geht es wieder von vorne los“, erörtert Frappier.
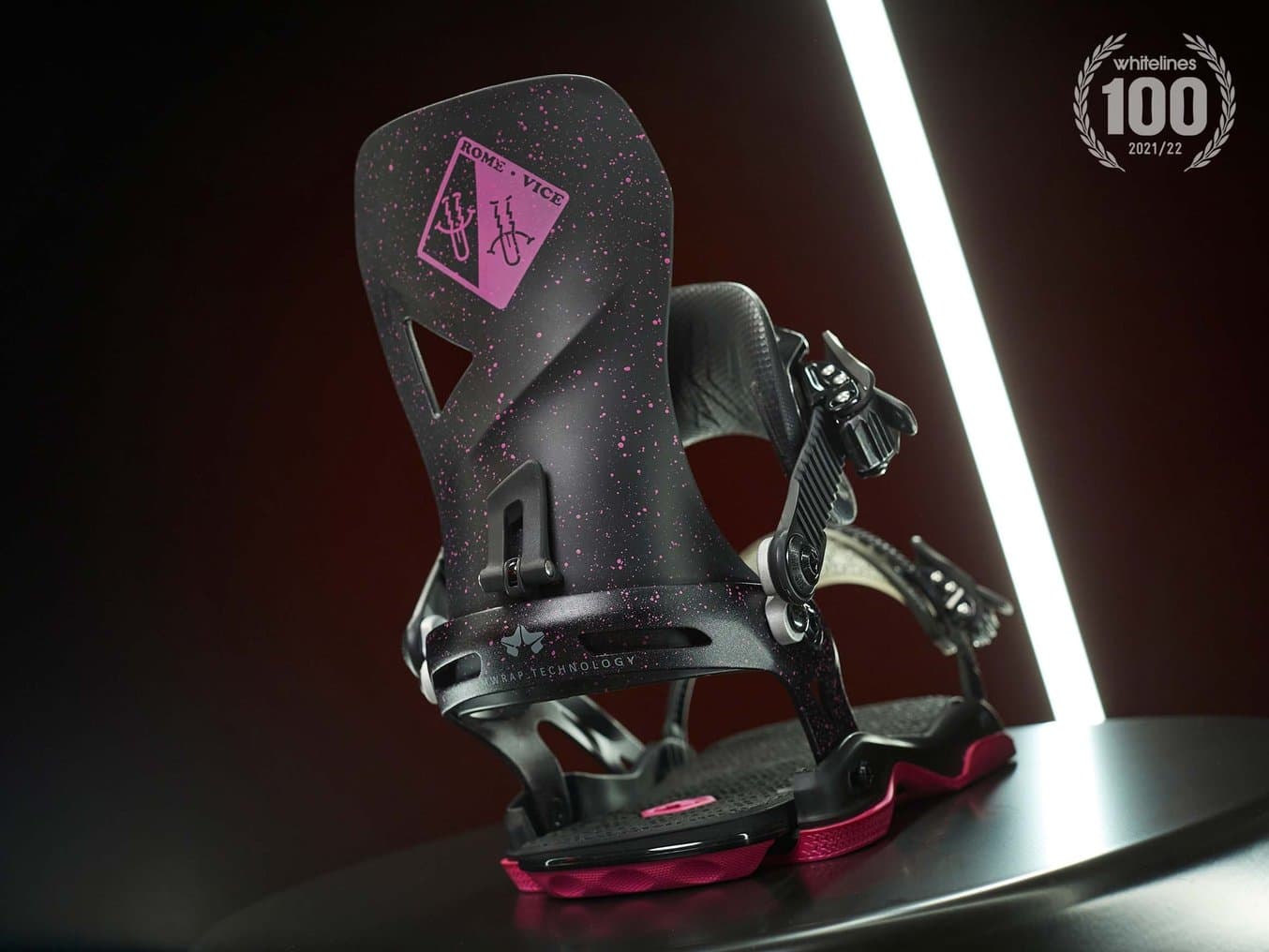
Die preisgekrönte Bindung „Vice“ in der Bewertung von White Lines Bild mit freundlicher Erlaubnis von White Lines
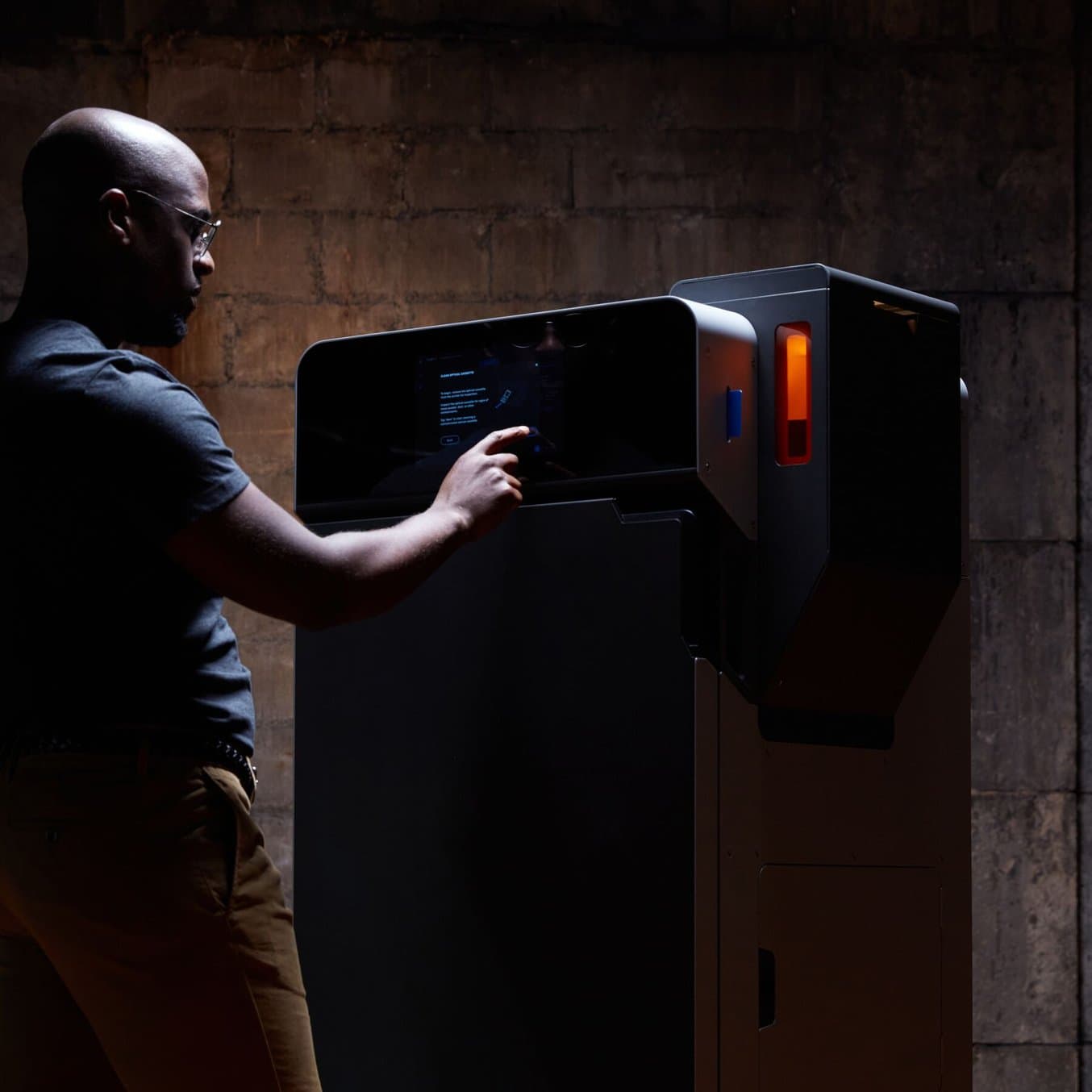
Outsourcing oder betriebsintern: Wann sollte man SLS-3D-Druck in den eigenen Betrieb holen?
In diesem Whitepaper untersuchen wir den Mehrwert betriebsinterner SLS-3D-Drucker im Vergleich zum Outsourcing von SLS-Teilen an einen Fertigungsdienstleister.
Für jeden Stil das Richtige
Mit den Produkten von Rome finden Snowboarder den für sie passenden Sitz und Halt, indem sie verschiedene Komponenten nach Bedarf einstellen. Alles lässt sich auf Gewicht, Größe, Fahrstil oder Streckenbedingungen anpassen. Eine größere Anzahl an Komponenten bedeutet allerdings auch ein komplizierteres Design und exakte Toleranzen, damit alles nahtlos zusammenpasst. Die Bewertung von White Lotus schreibt (übersetzt): „[...] der Highback aus 100 % Nylon sorgt für Flexibilität, bei der die Knochen aufatmen. So gut wie jeder Boarder kann die Vice anlegen und fühlt sich darin sofort wohl.“
Diese Benutzerfreundlichkeit liegt nur an der Sorgfalt und der Zeit, die das Rome-Team in jeden Entwicklungsschritt steckt. Frappier sagt dazu: „Wir arbeiten ständig daran, unsere Teile perfekt und zuverlässig zu machen. Selbst wenn wir mehr Einzelteile haben ist der Zusammenbau perfekt. Für den Kunden ist alles einwandfrei, weil die Bindung mit absoluter Sorgsamkeit entworfen wird. Dafür eignet sich 3D-Druck hervorragend, da wir jedes Einzelteil genau austarieren können. So stellen wir sicher, dass jedes Teil nach dem Zusammenbau einwandfrei funktioniert.“
Kleine Stellfläche, große Leistung
Viele Firmen erreichen dieselbe Designtiefe nur durch übergroße Designerteams, die untereinander Ideen austauschen und verbessern. Bei Rome gibt es nur zwei Designer. Das sorgt für schnellere Reaktionszeiten, macht die Arbeit manchmal aber auch zum Nonstop-Prozess. Der Fuse 1 arbeitet parallel zu den Designern und druckt den ganzen Tag lang, wann immer das Team ihn braucht. Außerdem ist er ein überzeugendes Argument bei der Gewinnung neuer Athleten für eine Sponsorenpartnerschaft. Die kompakte Größe und der erschwingliche Preis machen ihn zu einer leicht integrierbaren Lösung – selbst für Unternehmen mit begrenztem Platz oder Personal.
Verglichen mit anderen Bindungsherstellern sind wir ein sehr kleines Unternehmen. Wir sind in unserem Büro in Waterbury nur zu acht oder zu zehnt; und dass wir über eine komplette 3D-Druck-Einrichtung verfügen, ist echt fantastisch. Viele Leute glauben, wir wären ein größeres Unternehmen. Das ist das Schöne am Fuse 1: Auch kleine Unternehmen können ihn sich leisten.
Justin Frappier, Product Designer bei Rome Snowboards
Wann immer Sportler*innen oder Ausrüstungshändler*innen den Firmensitz in Waterbury besuchen, dann ist die Reaktion auf den Fuse 1 Frappier zufolge überwältigend positiv. „Wenn die Leute den Drucker sehen, haut es sie aus den Socken. Wir können uns ein Design nehmen und ihnen sofort das Teil zeigen, sowohl bei Athleten als auch bei Handelsvertretern. So holen wir auch das Feedback zum jeweiligen Teil ein, bevor es in die eigentliche Werkzeugbestückung geht“, so Frappier.
Immer schnellere funktionsfähige Prototypen
Romes 2022er Produktpalette geht nicht im 3D-Drucker in die Massenproduktion. Doch das hält das Team nicht davon ab, höchst realistische Validierungstests durchzuführen. In der ersten Wintersaison nach der Anschaffung des Druckers entschloss sich das Designteam zu wirklich funktionalen Tests. Sie wollten die Prototypen auf Herz und Nieren prüfen, damit auch jede Schnalle und jedes Bauteil den rauen Bedingungen gewachsen ist. So sendet das Unternehmen keine Teile an Hersteller, die nicht ganz sicher perfekt sind.
„Wir wollen weder Zeit verschwenden noch in falsche Werkzeugbestückung investieren, nur weil wir das Werkzeug zu früh in Auftrag geben. Das macht uns also effizienter“, gibt er an.
Frappier und seine Kolleg*innen nahmen die komplett aus dem Drucker stammenden Bindungen (einige Metallschrauben ausgenommen) mit auf den Berg in Vermont und erhöhten bei jeder Abfahrt die Geschwindigkeit. Sie testeten die Flexibilität, Festigkeit und Haltbarkeit jeder Bindung am Berghang, was Frappier ganze Wochen sparte, verglichen mit der üblichen Entwicklungszeit. Der Erfolg der Marke basiert auf der Innovation; und nichts schiebt der Kreativität schneller einen Riegel vor, als mehrere Wochen auf eine Produktiteration von einem Zulieferer zu warten.
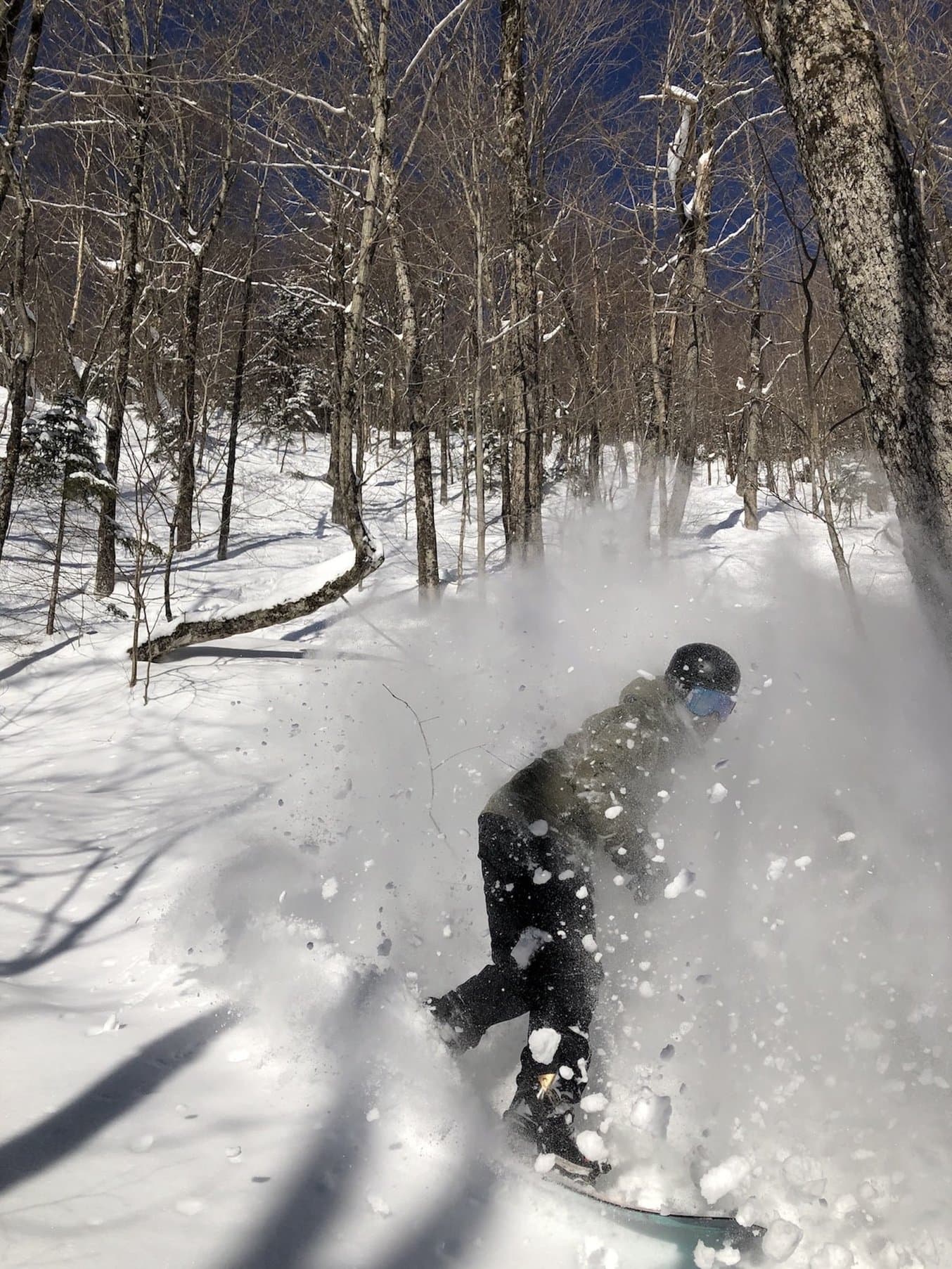
Das Hauptargument war, dass wir mit den Druckteilen abfahren konnten. Das konnten wir zuvor mit anderen Teilen noch nie machen. Bei unserem ersten Mal hatten wir die Basis und die Chassiskomponenten. Mit jeder Abfahrt legten wir einen Zahn zu und die Teile haben fantastisch durchgehalten und sich großartig angefühlt. Heute drucken wir, fahren eine Runde und drucken am nächsten Tag etwas Neues.
Justin Frappier, Product Designer bei Rome Snowboards
Die Möglichkeit des Designteams, den kompletten Kreativ-, Test- und Iterationsprozess zu kontrollieren, ist für Rome Snowboards der Schlüssel dazu, die Grenzen der Snowboard-Ausrüstung weiter auf die Probe zu stellen.
„Wir sind in jeder Kategorie die ersten der Branche. Wir versuchen uns immer in Dingen, die noch keiner zuvor probiert hat. Und wir werden immer besser. Dabei sehen wir bereits, wie sich die Investition rentiert. Das haben wir schon in den ersten fünf Monaten, allein durch die schnellere Prototypenentwicklung“, gibt Frappier zu verstehen.
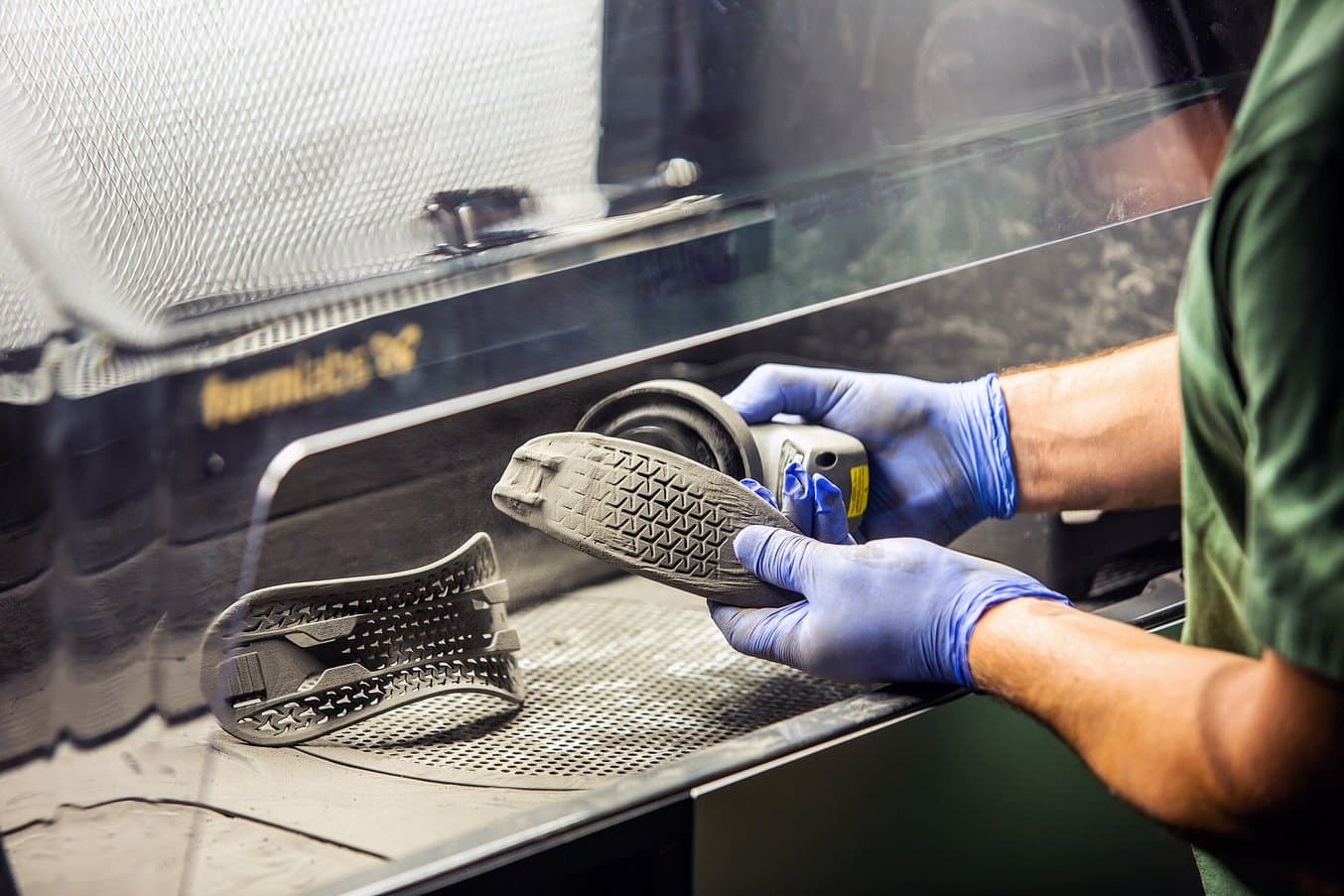
Das Entfernen und die Wiederverwertung des ungesinterten Pulvers ist ein Kinderspiel, dank des geschlossenen und optimierten Arbeitsablaufs mit dem Fuse Sift.
Mithilfe der Drucker der Fuse-Serie führen Designer Funktionstests ihrer Produkte durch und iterieren ganz ohne Wartezeiten seitens eines Zulieferers. Bei Rome Snowboards hat der Fuse 1 den Entwicklungsprozess um ein Vielfaches beschleunigt und ermöglicht das Firmenmotto „All Ways Down“ mit 3D-gedruckten Bindungen auf der Piste auszuleben. Um herauszufinden, ob der Fuse 1 bei Ihren Produkten ähnliche Erfolge feiern kann, bestellen Sie am besten einen Probedruck. Oder lesen Sie unser Whitepaper mit Fallstudien, das den betriebsinternen SLS-Druck mit Teilen von einem Dienstleister vergleicht.