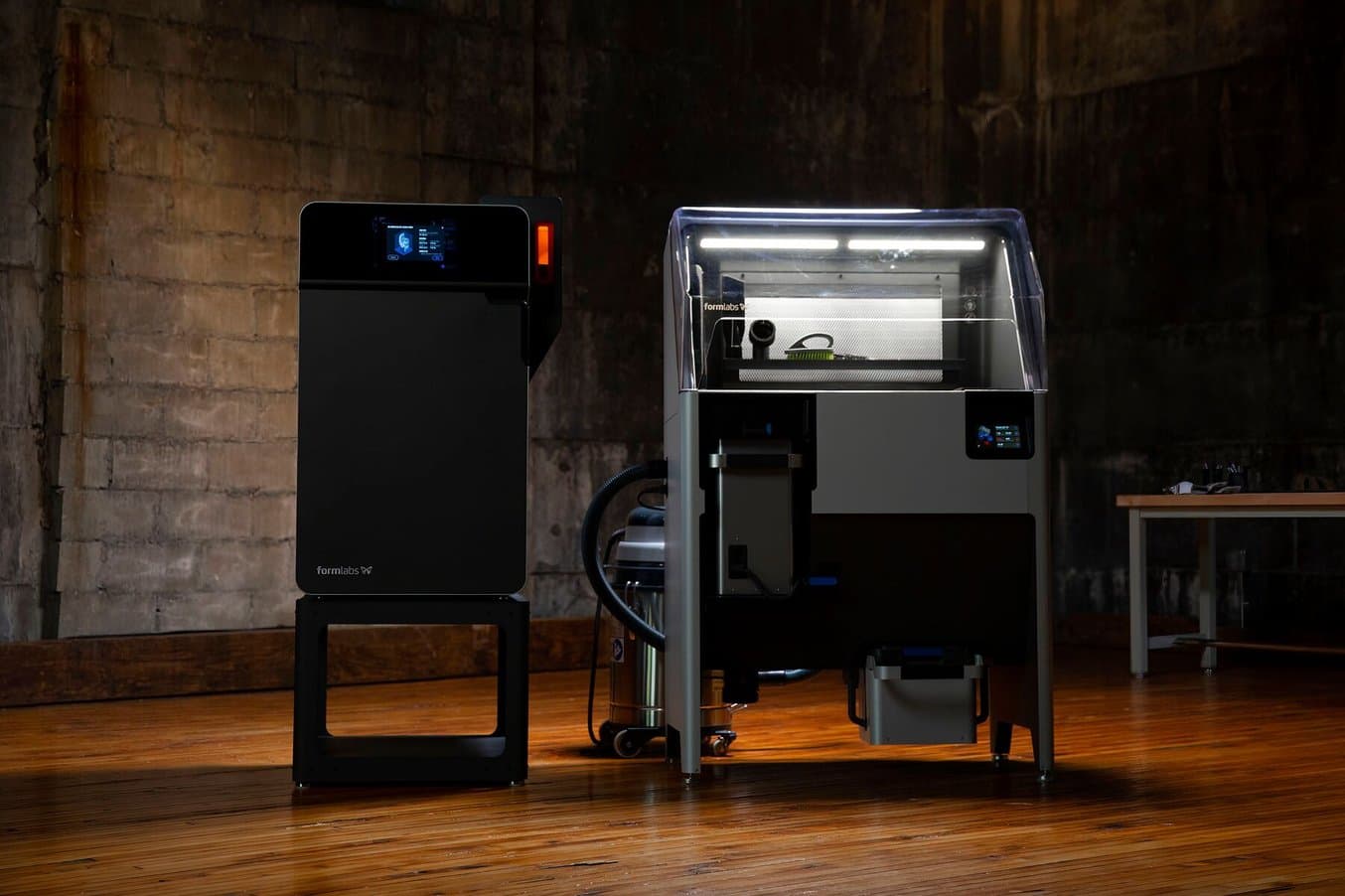
Der Fuse 1+ 30W, Formlabs' 3D-Drucker für selektives Lasersintern (SLS)
Seit seiner Erfindung in den 1980er Jahren wird das 3D-Druckverfahren des selektiven Lasersinterns (SLS) von großen Herstellern weitläufig für Prototyping und Kleinserienfertigung eingesetzt. Für kleine und mittlere Hersteller sind SLS-3D-Drucker allerdings erst in jüngsten Jahren erschwinglich geworden. Die steigende Zahl von SLS-3D-Druckern, die weltweit im Einsatz sind, ist ein Indikator für die hohe Teilequalität, die geringen Stückkosten und die Produktionsreife dieser Technologie.
Beim SLS-3D-Druck handelt es sich um ein additives Fertigungsverfahren, bei dem dünne Schichten von Kunststoffpulverpartikeln durch einen Hochleistungslaser in der Form eines Querschnitts des 3D-Modells miteinander versintert werden. Der Drucker trägt anschließend eine weitere dünne Pulverschicht in der Konstruktionskammer auf, welche ebenfalls vom Laser gesintert wird, sodass aus den Schichten stufenweise ein fertiges Druckteil entsteht. Bei Kunststoff-3D-Druckern mit Pulverbettfusion werden die Teile während des Drucks vom Pulverbett gestützt, sodass anders als bei den meisten anderen 3D-Druckverfahren keine Stützstrukturen erforderlich sind und auch komplexe Konstruktionen wie Überhänge, interne Kanäle und ineinandergreifende Teile möglich werden. Der Druck ohne Stützstrukturen sorgt außerdem für eine einfachere und weniger arbeitsintensive Nachbearbeitung, sodass Teile durchgängig in größerem Maßstab produziert werden können.
Da die SLS-Technologie einen Hochleistungslaser, hohe Präzision sowie eine strikte Kontrolle des gesamten Druckprozesses erfordert, sind selbst die günstigsten SLS-Drucker noch teurer als die meisten FDM-Drucker (Schmelzschichtung) und als viele SLA-3D-Drucker (Stereolithografie). Trotz der höheren Einstiegskosten kann die Anschaffung eines betriebsinternen SLS-3D-Druckers jedoch innerhalb weniger Monate zu einem positiven ROI führen, und zwar dank des hohen Durchsatzes und der niedrigen Kosten neuer industrietauglicher Lösungen für den Benchtop.
In diesem Beitrag vergleichen wir die Preise verschiedener SLS-3D-Drucker und geben einen vollständigen Überblick über die Kosten des SLS-3D-Drucks, vom Kaufpreis bis hin zur Wartung, Materialanschaffung und mehr.
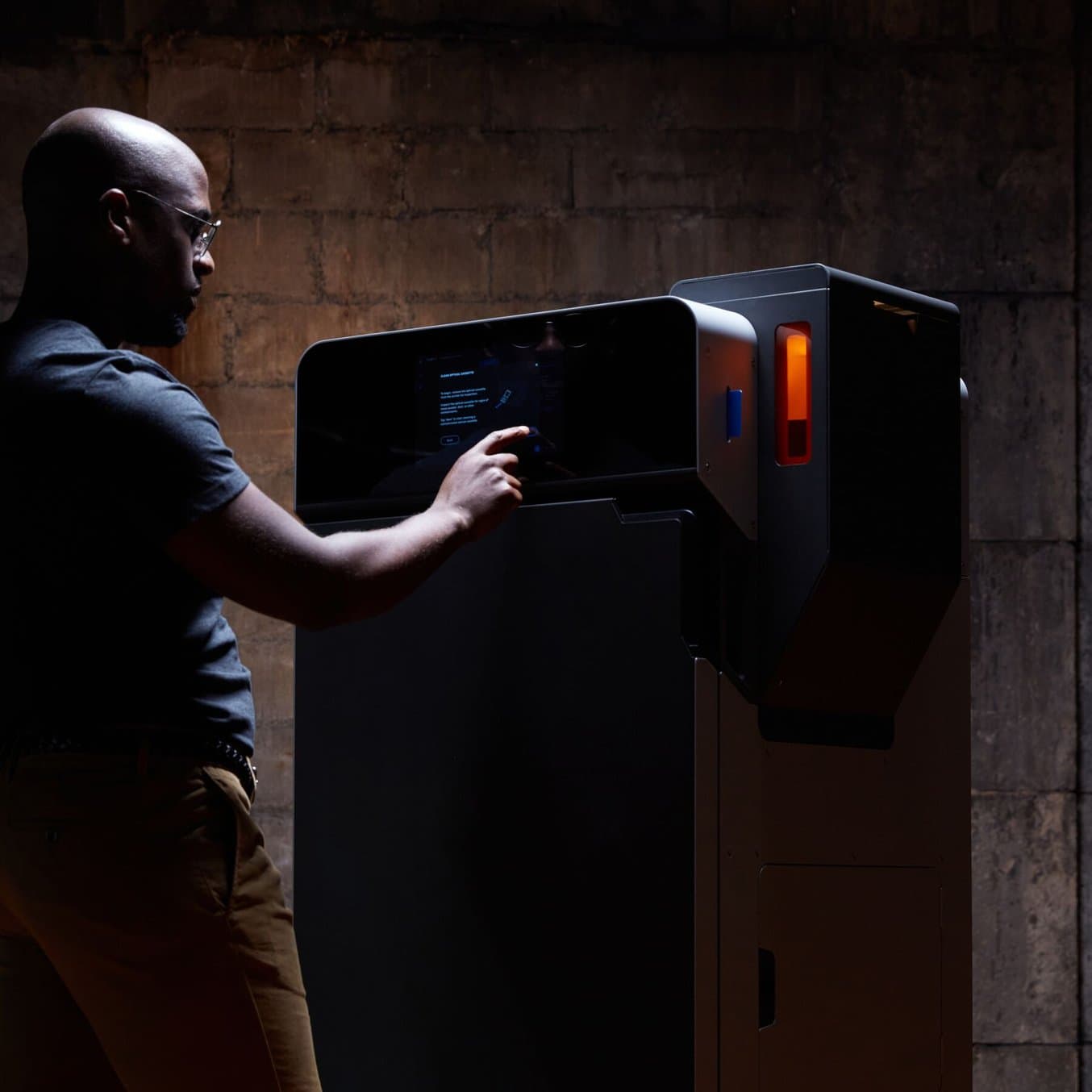
Outsourcing oder betriebsintern: Wann sollte man SLS-3D-Druck in den eigenen Betrieb holen?
In diesem Whitepaper untersuchen wir den Mehrwert betriebsinterner SLS-3D-Drucker im Vergleich zum Outsourcing von SLS-Teilen an einen Fertigungsdienstleister.
Preise von SLS-3D-Druckern: Benchtop- vs. industrieller Drucker
Ursprünglich waren SLS-Drucker komplexe, sperrige und teure Systeme, die nur für Industrieriesen mit ausgedehnten Fertigungsanlagen eine Option darstellten. In den vergangenen fünf Jahren haben Geräte für den Benchtop jedoch auch kleinen und mittleren Hersteller die Chance eröffnet, die Leistung und Produktivität des SLS-3D-Drucks auszunutzen.
Vergleicht man SLS-Drucklösungen für den Benchtop wie die Fuse-Serie mit konventionellen, industriellen Geräten, sind mehrere Faktoren zu berücksichtigen: Kaufpreis, Größe, Benutzerfreundlichkeit, Anforderungen an die Infrastruktur und laufende Kosten. Die folgende Tabelle stellt diese Faktoren jeweils für Benchtop-SLS-Geräte (den Fuse 1+ 30W von Formlabs) und traditionelle SLS-Systeme gegenüber (basierend auf der Produktpalette von EOS und 3D Systems).
Fuse-Serie: Industrielle SLS-3D-Drucker für den Benchtop | Traditionelle industrielle SLS-3D-Drucker | |
---|---|---|
Preis | Ab 23 699 € für den Fuse 1+ 30W | 200 000–500 000 € und mehr |
Fertigungsvolumen | Bis zu 165 × 165 × 300 mm | Bis zu 550 × 550 × 750 mm |
Vorteile | Erschwinglich; Hochwertige Teile; Hoher Durchsatz; Verschiedene Materialoptionen; Vereinfachter Arbeitsablauf; Geringer Platzbedarf; Geringer Wartungsaufwand | Großes Fertigungsvolumen; Hochwertige Teile; Hoher Durchsatz; Verschiedene Materialoptionen; |
Nachteile | Kleineres Fertigungsvolumen | Teure Ausrüstung Großer Platzbedarf; Anforderungen an die Infratruktur; Hoher Wartungsaufwand; Erfordert eigenes Personal für Bedienung; |
Wie sich die Kosten des SLS-Drucks zusammensetzen
Gesamtbetriebskosten
Die Kosten betriebsinterner SLS-Systeme beschränken sich nicht nur auf den Preis des Druckers an sich – auch die Zubehörsysteme sowie Wartung und Kundenservice müssen in Betracht gezogen werden. Die Preisspanne der Drucker selbst reicht von ca. 10 000 € für preiswerte DYI-SLS-Drucker bis hin zu 500 000 € oder mehr für die teuersten, großformatigen Industriedrucker.
Formlabs war der erste Hersteller, der 3D-Druck in Industriequalität zu einem erschwinglichen Kostenpunkt verfügbar machte: Der Fuse 1+ 30W ist ab 23 699 € erhältlich, bei einer Teilequalität, die mit konventionellen industriellen SLS-Lösungen Schritt hält. Unabhängig vom gewählten Drucksystem müssen jedoch zusätzliche Schritte nach dem Druck durchgeführt werden, um brauchbare Teile zu erhalten.
SLS-3D-Drucker bieten den Vorteil des Drucks ohne Stützstrukturen, sodass deren mühsames Entfernen entfällt, doch es gibt dennoch eine Schicht ungesinterten Pulvers zu entfernen, die die Druckteile umschließt. Hierfür ist weiteres Zubehör unabdinglich. Fast alle Hersteller von SLS-Druckern bieten auch Stationen zur Nachbearbeitung und Pulverrückgewinnung an, bei denen es ebenfalls große Preisunterschiede geben kann, von 959 € für Formlabs' Fuse Depowdering Kit, ein kostengünstiges Komplettpaket für die manuelle Nachbearbeitung, über 9599 € für den Fuse Sift als kompakte, effiziente Pulververwaltungsstation, bis zu 50 000 € für Lösungen von EOS.
Nach einer grundlegenden Reinigung wird empfohlen, SLS-Druckteile durch Sandstrahlen (oder genauer das Bestrahlen mit einem abrasiven Strahlmittel) zu bearbeiten, um das Pulver vollständig zu entfernen. Manuelle Strahlkabinen sind für unter 500 € erhältlich. Der Fuse Blast ist die erste erschwingliche automatisierte Sandstrahlanlage und kann Ihre Arbeitszeit zum Preis von 10 699 € drastisch reduzieren.
Dass ein gesamtes Ecosystem zur Produktion von Teilen in industrieller Qualität, einschließlich des SLS-Druckers Fuse 1+ 30W, der Pulverwiederverwertung und der Reinigung mit Fuse Sift und Fuse Blast, für unter 60 000 € erhältlich ist, ist revolutionär und hat kleinen Unternehmen, Einzelpersonen und Bildungseinrichtungen die Möglichkeit eröffnet, erstmals Kapazitäten für leistungsstarken 3D-Druck durch Pulverbettfusion ins eigene Haus zu holen.
Alle SLS-Drucker auf dem Markt verfügen über Servicepläne und Wartungsverträge; manchmal sind diese optional, manchmal obligatorisch. Die meisten Kundenserviceverträge für traditionelle industrielle Drucker kosten ungefähr 10 % des Gerätepreises – genug für den Kauf eines Druckers der Fuse-Serie pro Jahr. Zudem müssen Servicepläne für industrielle Geräte oft jährlich erneuert werden, was weitere laufende Kosten bedeutet.
Materialien und Verbrauchsmaterial
Das beliebteste Material für den SLS-3D-Druck ist Nylon, ein robuster, technischer Thermoplast für starke, leichte funktionale Teile. Auch Verbundwerkstoffe aus Nylon kommen häufig zum Einsatz, und manche Hersteller bieten auch biegsamere Optionen wie TPU an. Die Kosten dieser Materialien variieren von Hersteller zu Hersteller, wobei der übliche Preis für Nylonmaterialien jedoch bei ca. 100 €/kg liegt und häufig Mengenrabatte verfügbar sind.
Auch wenn die Preise für Rohmaterialien bei verschiedenen Anbietern ähnlich ausfallen, können sich die laufenden Kosten für die Verwendung dieser Materialien je nach der Effizienz des Arbeitsablaufs ändern. Die Effizienz hängt von zwei Faktoren ab: Packdichte und Pulverneuzuführungsrate.
Bei Benchtop-SLS-Druckern wie der Fuse-Serie erreicht die Packdichte oft 30 % und ermöglicht somit Druckvorgänge ohne Abfälle. Der abfallfreie Druckprozess beruht auf dem Gleichgewicht zwischen der Packdichte und der Neuzuführungsrate. Die Neuzuführungsrate bezeichnet den Anteil frischen Pulvers, der in jeder neuen Konstruktionskammer benötigt wird. Meistens liegen die Neuzuführungsraten beim SLS bei 30–50 %, einige industrielle Systeme haben aber auch Neuzuführungsraten von nur 20 %.
Worauf es bei den laufenden Kosten für Verbrauchsmaterial am meisten ankommt, ist jedoch nicht nur die Neuzuführungsrate selbst, sondern dass diese im Gleichgewicht mit der Packdichte steht. Wenn beide den gleichen Wert haben oder letztere höher ist, muss nur das gesinterte Pulver mit frischem Pulver ersetzt werden, sodass letzten Endes sämtliches Pulver verbraucht wird. Das Ergebnis ist ein abfallfreier und maximal kosteneffizienter Druck.
Arbeitskosten
Dank der Stützfunktion des Pulvers bei der Pulverbettfusion entfällt der aufwendige Prozess des Entfernens der Stützstrukturen, der bei Druckteilen aus FDM- oder SLA-Druckern nötig ist. Es sind aber dennoch manuelle Arbeiten erforderlich, da die Teile durch Nachbearbeitungsprozesse von Pulver befreit werden müssen. Außerdem sind einige SLS-Systeme hochkomplex, sodass nach jedem Druck eine lange Liste von Schritten zur Wartung erledigt werden muss.
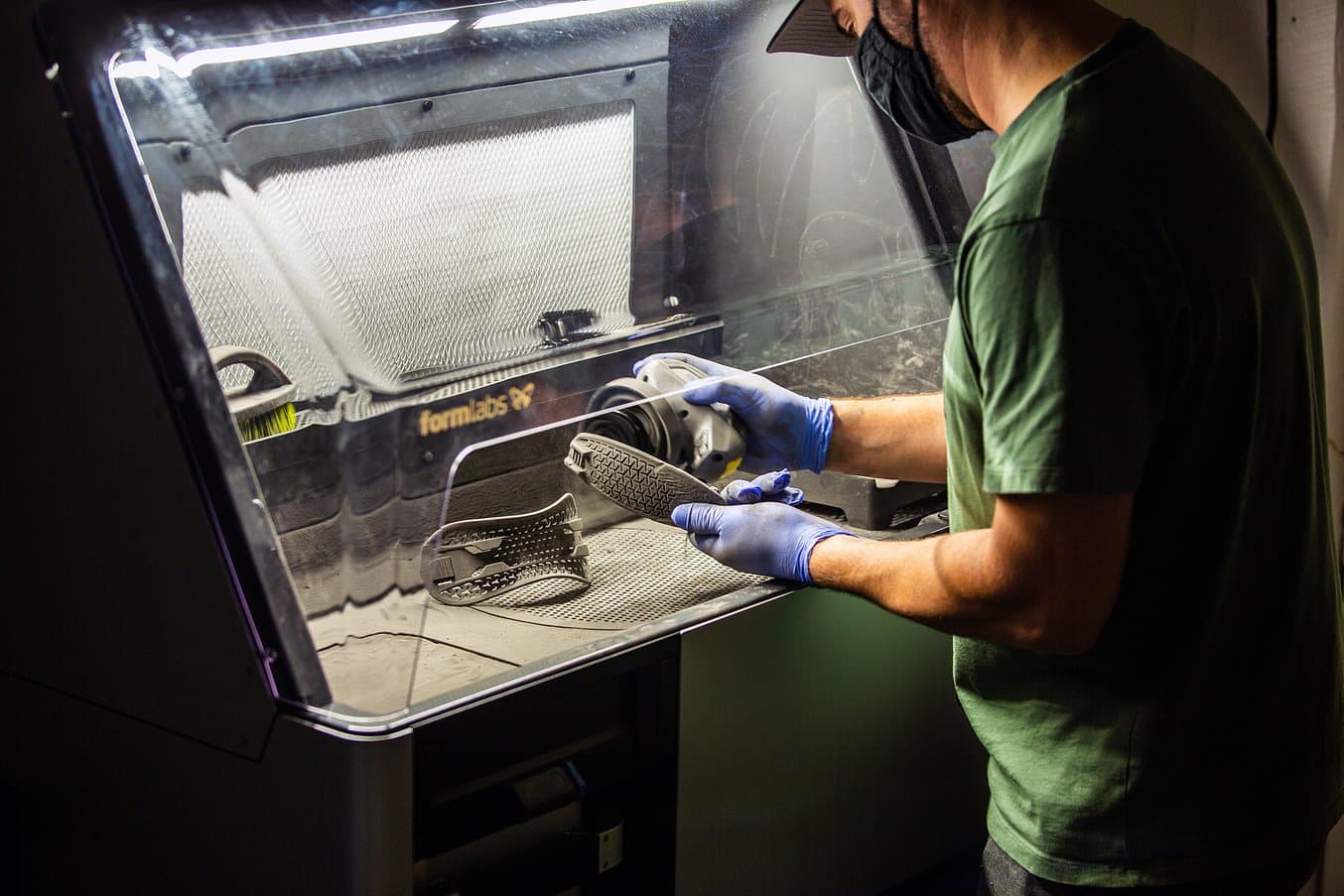
Die Nachbearbeitungsstation Fuse Sift vereinfacht den Arbeitsablauf zur Pulverentfernung, -wiederverwertung und -mischung.
Bei großen, konventionellen SLS-Systemen erfordert die Bedienung der Drucker und des Nachbearbeitungsgeräts eigenes Personal. In manchen Fällen werden auch zusätzliche Geräte für die Pulverrückgewinnung benötigt. Solche herkömmlichen SLS-Systeme beanspruchen außerdem einen ganzen Arbeitstag zur Reinigung des Druckers und des Nachbearbeitungsgeräts und zur Pulverentfernung, bevor ein Materialwechsel durchgeführt werden kann. Sowohl die zusätzliche Arbeitszeit als auch die potenziellen Produktionseinbußen während der durch die Reinigung bedingten Stillstandszeiten sollten bei der Kostenberechnung berücksichtigt werden. Mit der Fuse-Serie von Formlabs dauert der Wechsel zwischen Nylon 12 Powder und Nylon 11 Powder nur vier Stunden, während ein Wechsel zwischen Materialien mit derselben Basiskomponente, z. B. Nylon 12 Powder und Nylon 12 GF Powder, sogar nur halb so viel Zeit in Anspruch nimmt.
Kostengünstige SLS-Optionen wie einige DIY-Systeme verfügen über keinerlei Zubehör zur Nachbearbeitung, weshalb die Pulverentfernung, -mischung, -wiederverwertung und sonstige Arbeitsschritte deutlich länger dauern. Zudem entstehen durch den weniger intuitiven Arbeitsablauf zahlreiche wiederkehrende manuelle Arbeiten.
Die Drucker der Fuse-Serie von Formlabs vereinen den effizienten Arbeitsablauf des konventionellen SLS-Drucks mit der kompakten Stellfläche kostengünstiger Optionen. Die Drucker und der Fuse Sift sind leicht in einem bestehenden Arbeitsbereich unterzubringen, und da die Pulverentfernung, -wiederverwertung und sonstige Arbeitsschritte zur Pulverhandhabung mit dem Fuse Sift einfach und intuitiv werden, bleibt mehr Zeit für wichtige Aufgaben.
Kapitalrendite-Rechner für den SLS-3D-Druck
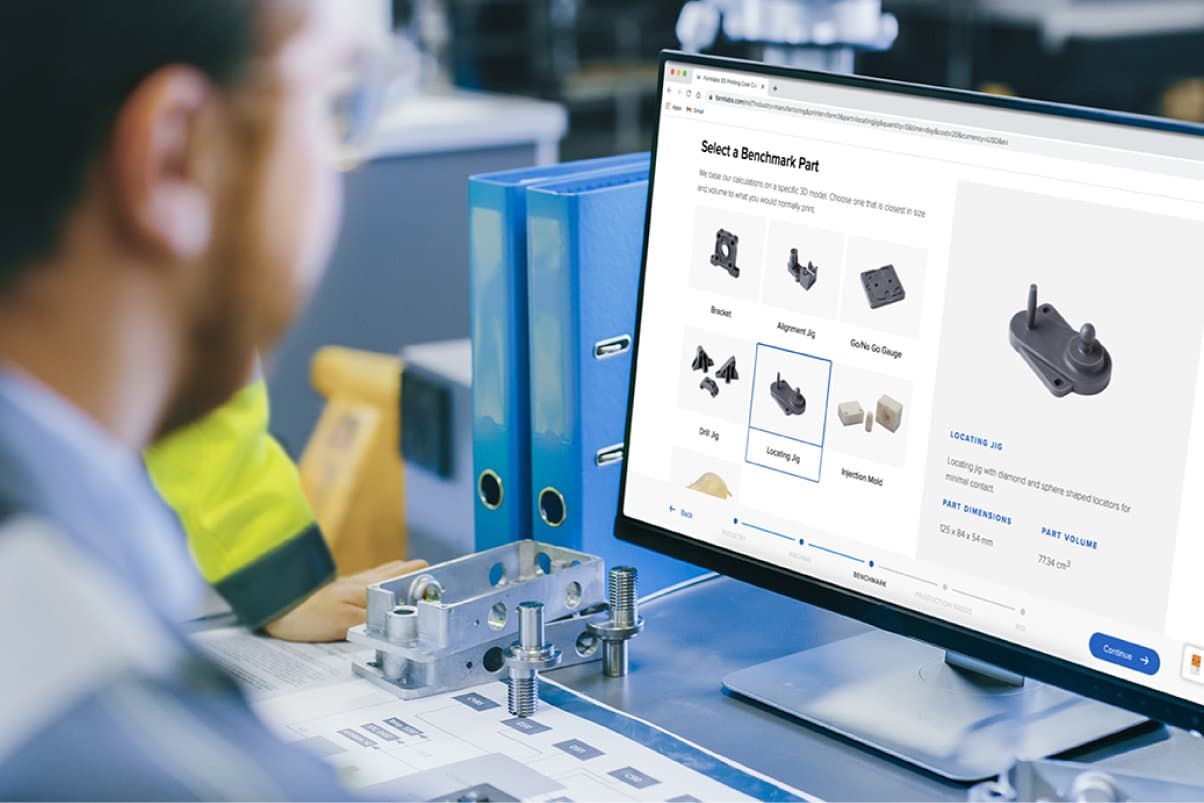
Der Kapitalrendite-Rechner von Formlabs macht die Budgetplanung für einen SLS-3D-Drucker ganz einfach, indem er die Anschaffungskosten der Geräte, die Materialien, Arbeit und alle weiteren Kosten aufschlüsselt und anhand eines bestimmten Produktionsvolumens die Kosten pro Teil berechnet. Sie können den Kalkulator auch nutzen, um Ihre Kosten- und Zeiteinsparungen beim SLS-3D-Druck im Vergleich zu Alternativen wie Outsourcing oder anderen Produktionsverfahren zu ermitteln.
SLS-3D-Druck: Betriebsintern vs. Outsourcing
SLS ist eine ideale Möglichkeit zur schnellen und kostengünstigen Herstellung funktionsfähiger, starker Prototypen in Industriequalität und kann auch als Fertigungstechnologie für Endverbrauchsteile in Kleinserien oder Maßanfertigungen dienen. Viele Hersteller, Entwicklungs- oder Designteams bauen schon jetzt auf SLS-Teile, ob sie sie betriebsintern herstellen oder von einem Fertigungsdienstleister beziehen.
Seit die Technologie existiert, war Outsourcing für die meisten Unternehmen lange Zeit die einzige Möglichkeit, SLS-Teile zu nutzen, denn die Anschaffung eines betriebsinternen Geräts war lediglich für die allergrößten Hersteller erschwinglich. Auch heute noch kann sich die Auslagerung des SLS-3D-Drucks in bestimmten Szenarien rentieren – beispielsweise zur Fertigung von Einzelstücken oder für Unternehmen, denen schlichtweg die Mittel zum Kauf eines leistungsstarken SLS-Druckers fehlen. Fertigungsdienstleister bieten eine Übergangslösung für die Prototypenfertigung oder sogar für die Kleinserienproduktion. Doch seitdem betriebsinterner, leistungsstarker SLS-Druck erschwinglich geworden ist, lohnt es sich auch für kleine und mittlere Hersteller, sich mit den Kosten des SLS-3D-Drucks vertraut zu machen.
Ein betriebsinterner Drucker des Typs Fuse 1+ 30W ist zu einem Zehntel des Preises herkömmlicher SLS-Systeme erhältlich und bietet die Chance, einen größeren Anteil des Fertigungsprozesses in die eigene Hand zu nehmen. Nach der Installation im eigenen Betrieb liefern die Drucker der Fuse-Serie in Produktionsszenarien häufig bereits nach nur fünf Wochen einen positiven ROI, während sie sich beim Prototyping in zwei bis drei Monaten rentieren. So verringern Unternehmen Ihre Abhängigkeit von Dritten, beschleunigen die Prototypenfertigung oder Kleinserienproduktion und reduzieren Faktoren wie Lieferzeiten in ihrem Zeitplan. In einem neueren Whitepaper haben wir sechs verschiedene Szenarien für Produktion und Prototypenentwicklung betrachtet, um genau zu ermitteln, wie schnell sich die Anschaffung eines betriebsinternen Fuse 1+ 30W bezahlt macht. Eines dieser Szenarien war das Folgende:
Prototyp: Gehäuse einer Bohrmaschine
Material: Nylon 12 Powder
Druck: 2 Teile pro Baugruppe, insgesamt 4 Teile
Fuse 1+ 30W Betriebsintern | SLS-Auftragsfertigung | |
---|---|---|
Druckzeit | 13 h 10 min | |
Abkühlzeit | 13 h 45 min | |
Nachbearbeitung | 40 min | |
Gesamtzeit | 27 h 35 min | 7–10 Werktage |
Materialkosten | 50 € | |
Arbeitskosten | 11,22 $ | |
Gesamtkosten | 61,22 $ | 752,50 $ |
Stückkosten | 15,31 $ | 188,13 $ |
Die Gesamtzeit für die Produktion dieser Prototypen mit betriebsinternem SLS würde es zulassen, fünf vollständige Produktionsläufe pro Woche durchzuführen, womit zehn Iterationen der zweiteiligen Baugruppe für das Bohrmaschinengehäuse möglich wären. Verglichen mit Outsourcing, das eine einzige Iteration alle zwei Wochen erlaubt, eröffnet ein betriebsinterner SLS-Drucker also mehr Möglichkeiten, wirksam zu iterieren. Es könnten zahlreiche Modelle mit jeweils anderer Ästhetik, unterschiedlichen Griffdesigns oder anders platzierten Schraubgewinden kreiert werden, die dann schon am Folgetag als physische Modelle zur Genehmigung präsentiert werden können.
Die Ersparnis im Vergleich zur Auslagerung an einen Dienstleister liegt bei fast 700 $, was pro Zyklus mehr als 90 % Einsparungen bedeutet. Der Fuse 1+ 30W könnte also in etwas mehr als drei Monaten einen positiven ROI erreichen, bzw. in etwas mehr als einem Jahr, wenn er nur einmal pro Woche genutzt wird.
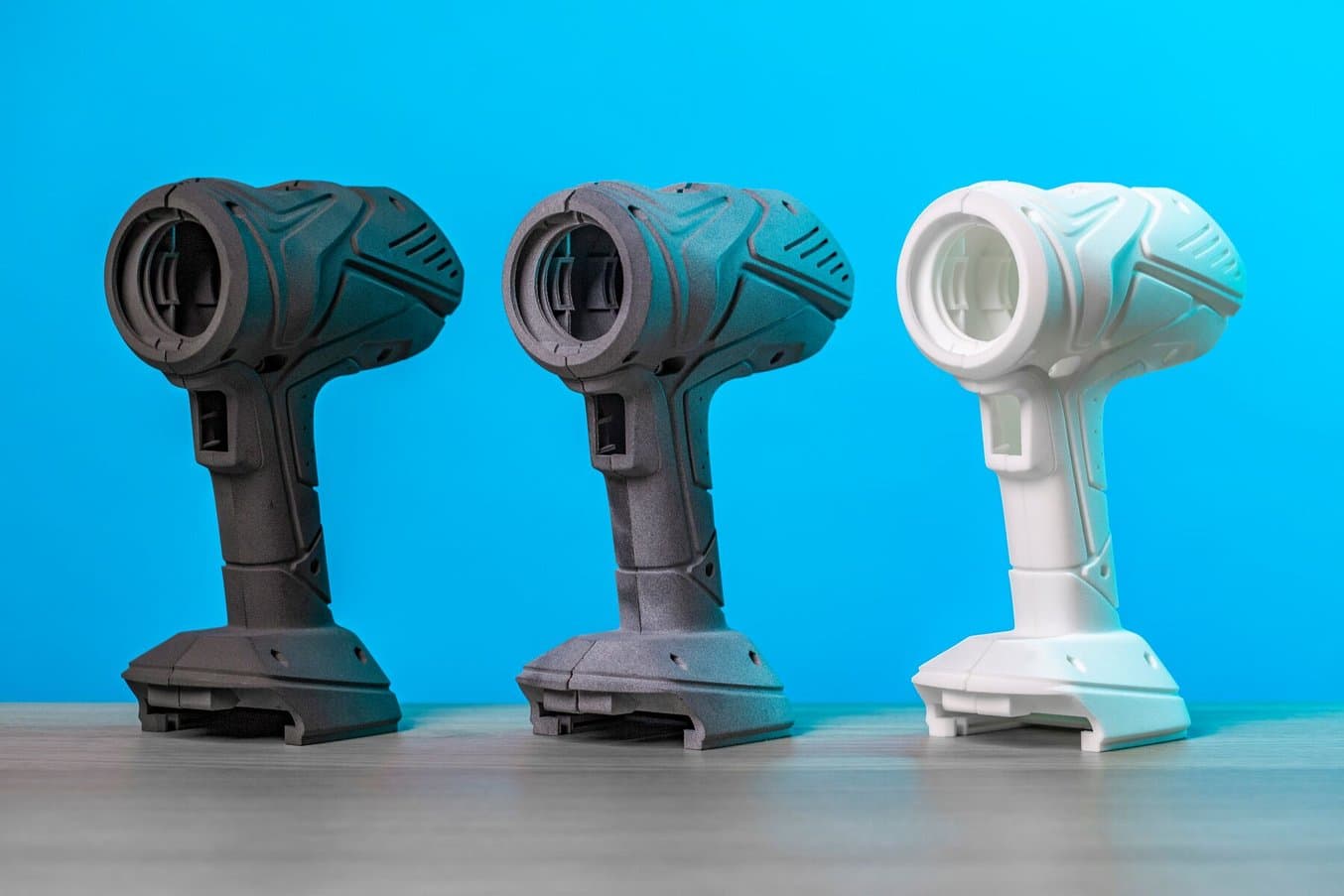
Der Prototyp der Bohrmaschine, betriebsintern auf einem Fuse 1+ 30W gedruckt (links) sowie von einem Fertigungsdienstleister mit einem MJF-Drucker von HP (Mitte) und einem SLS-Drucker von EOS bestellt (rechts).
Die Anwendung für Rapid Prototyping ist jedoch nicht das einzige Szenario, das so schnell eine positive Kapitalrendite erzielt. Unser Whitepaper analysiert auch die Ersparnisse, die durch den betriebsinternen Druck von Fertigungshilfen und kleiner Chargen von Endverbrauchsteilen erreicht werden. Dabei ergab sich, dass die Einsparungen durch derartige betriebsinterne Produktion die Druckerkosten in einem vergleichbaren Zeitraum kompensierten.
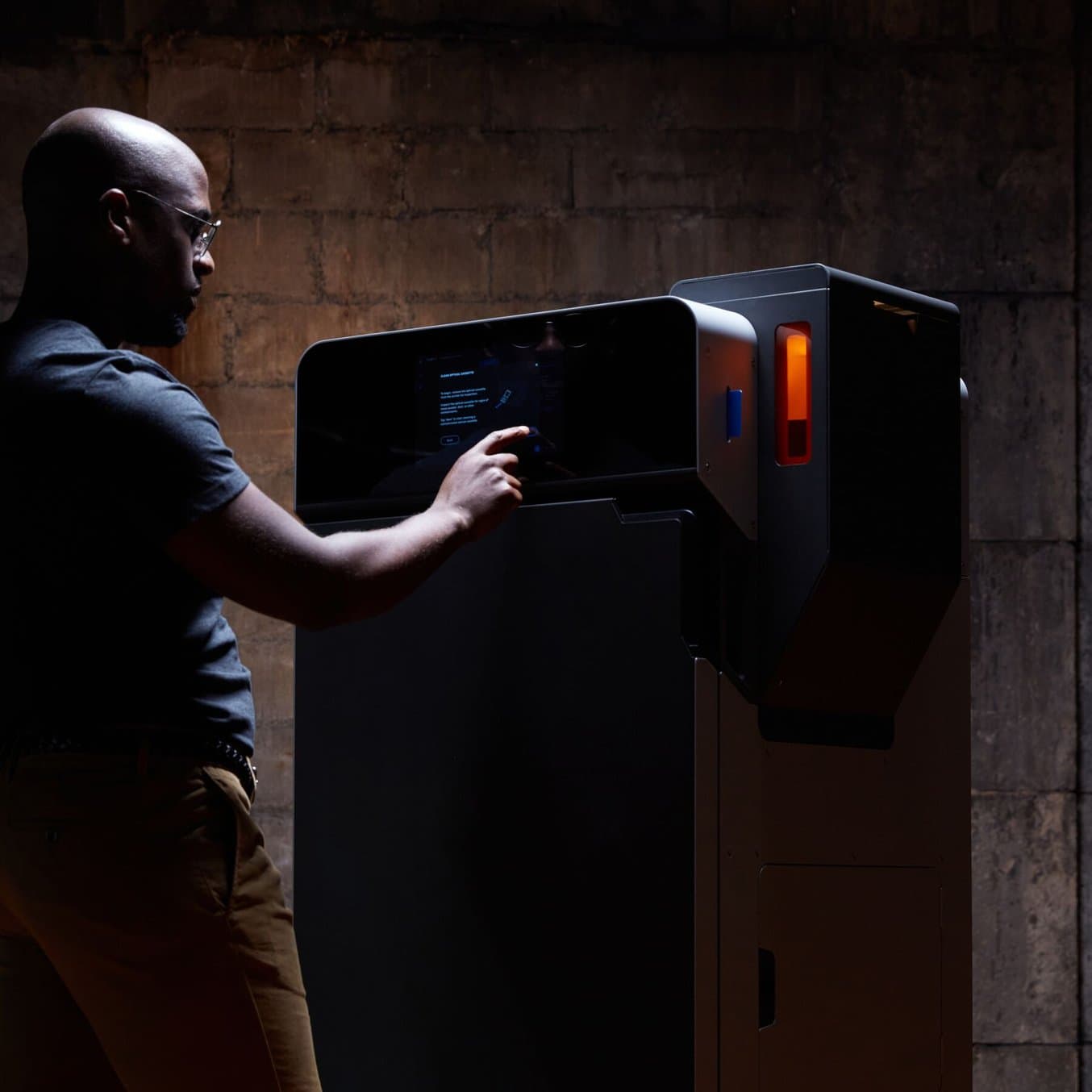
Outsourcing oder betriebsintern: Wann sollte man SLS-3D-Druck in den eigenen Betrieb holen?
In diesem Whitepaper untersuchen wir den Mehrwert betriebsinterner SLS-3D-Drucker im Vergleich zum Outsourcing von SLS-Teilen an einen Fertigungsdienstleister.
Fazit
Lange Zeit war die Investition in betriebsinternen SLS-3D-Druck für die meisten Unternehmen zu kostspielig – sowohl aufgrund der Gerätekosten als auch der laufenden Materialkosten, Servicepläne und Wartungsarbeiten.
Heute ist betriebsinterner SLS-Druck zugänglich, dank erschwinglicher Hardware und effizienter Arbeitsabläufe, die zu verringerten Betriebskosten führen. Die Technologie mag verglichen mit FDM und SLA noch immer kostenintensiv sein, doch SLS-3D-Drucker bieten Herstellern ein enormes Wertschöpfungspotenzial. Dank des hohen Durchsatzes und der überragenden Teilequalität verkürzen Unternehmen ihre Markteinführungszeit mittels rekordschneller Iterationen und Kleinserienproduktion. Zugleich verringern sie ihre Abhängigkeit von externen Herstellern von Werkzeug oder Ersatzteilen. Schneller, effizienter und hochwertiger 3D-Druck macht sich innerhalb kürzester Zeit bezahlt, vor allem im Vergleich zu alternativen Lösungen wie Outsourcing.
Die Drucker der Fuse-Serie von Formlabs produzieren Teilen von vergleichbarer Qualität wie konventionelle großformatige SLS-Geräte, bieten dabei aber erschwingliche Preise, eine ähnliche Materialauswahl und effizientere Systeme zur Pulverwiederverwertung. Sowohl hinsichtlich der Gerätepreise als auch der laufenden Kosten sind die Drucker der Fuse-Serie die erschwinglichste Lösung, um die Produktion hochqualitativer Teile auf Industrieniveau in den eigenen Betrieb zu holen.