Das Unternehmen Tapestry nutzt den 3D-Druck für die Gestaltung von Produkten wie Schuhen.
Was geschieht, wenn Mode und 3D-Druck Hand in Hand gehen? Für die Mode, die Sie auf dem Laufsteg sehen, und die Produkte, die Sie in den Geschäften sehen – von Schmuck bis zu Schuhen – werden 3D-Drucker von Formlabs zunehmend für die Prototypenherstellung eingesetzt. Bei Tapestry, das erste New Yorker Modehaus für moderne Luxusmarken und das Mutterunternhemen der bekannten High-Fashion-Marken Coach, Kate Spade und Stuart Weitzman, wird der 3D-Druck bereits in frühen Phasen der Produktentwicklung eingesetzt.
Tomer Emmar gründete lange vor Tapestry und kurz nach seinem Abschluss in Industriedesign ein Schmuckdesign-Unternehmen namens Studio Forty Seven . Hier machte er seine ersten Erfahrungen mit dem 3D-Druck. Dabei kombinierte er zum ersten Mal in seiner Karriere Metallverarbeitungstechniken mit 3D-Druck. „Nach einer sorgfältigen Prüfung der Integration des 3D-Drucks in den Prozess wurde mir klar, dass der 3D-Druck jeden Designprozess effektiver machen würde. Auf diese Weise können Konzepte schnell validiert und Arbeiten auf Abruf produziert werden. So kann man sicher sein, dass die Konzepte funktionieren und die Produkte erzeugt werden können, ohne dass Platz für die Lagerhaltung benötigt wird“, so Emmar.
Tomer war nach seinem Umzug nach New York bei einem 3D-Druck-Servicebüro angestellt, bei dem er den Umgang mit verschiedenen 3D-Drucktechnologien – darunter Formlabs SLA-Drucker – erlernte, bevor er eine Stelle bei Tapestry annahm.
Wie wirkt Formlabs an der Entwicklung von Produkten bei Tapestry mit? In diesem Blogbeitrag gehen wir auf Folgendes ein:
- 3D-Druck als Kommunikationsmittel.
- Wie der Form 3L – der großformatige SLA-3D-Drucker von Formlabs – die Spielregeln verändert hat.
- Die Zukunft des 3D-Drucks für Tapestry.
3D-Druck als Kommunikationsmittel: Design-Intention + mechanische Funktionalität
Als Rapid Prototyping Manager bei Tapestry leitet Tomer Emmar das 3D-Drucklabor in New York und ein Team von Prototyping-Experten, das verschiedene additive Fertigungstechnologien einsetzt, um sowohl den Design- als auch den Produktentwicklungsprozess zu beschleunigen und Produkte in verschiedenen Kategorien zu prototypisieren. „Wir setzen den 3D-Druck früh und häufig im Produktdesign- und Entwicklungsprozess ein. Das Verfahren wird eingesetzt, um die Ästhetik und Funktionalität zu überprüfen und in den frühen Phasen der Produktentwicklung zu helfen. Mit der Technologie werden herkömmliche Herstellungsverfahren von Anfang an ergänzt“, sagte Emmar.
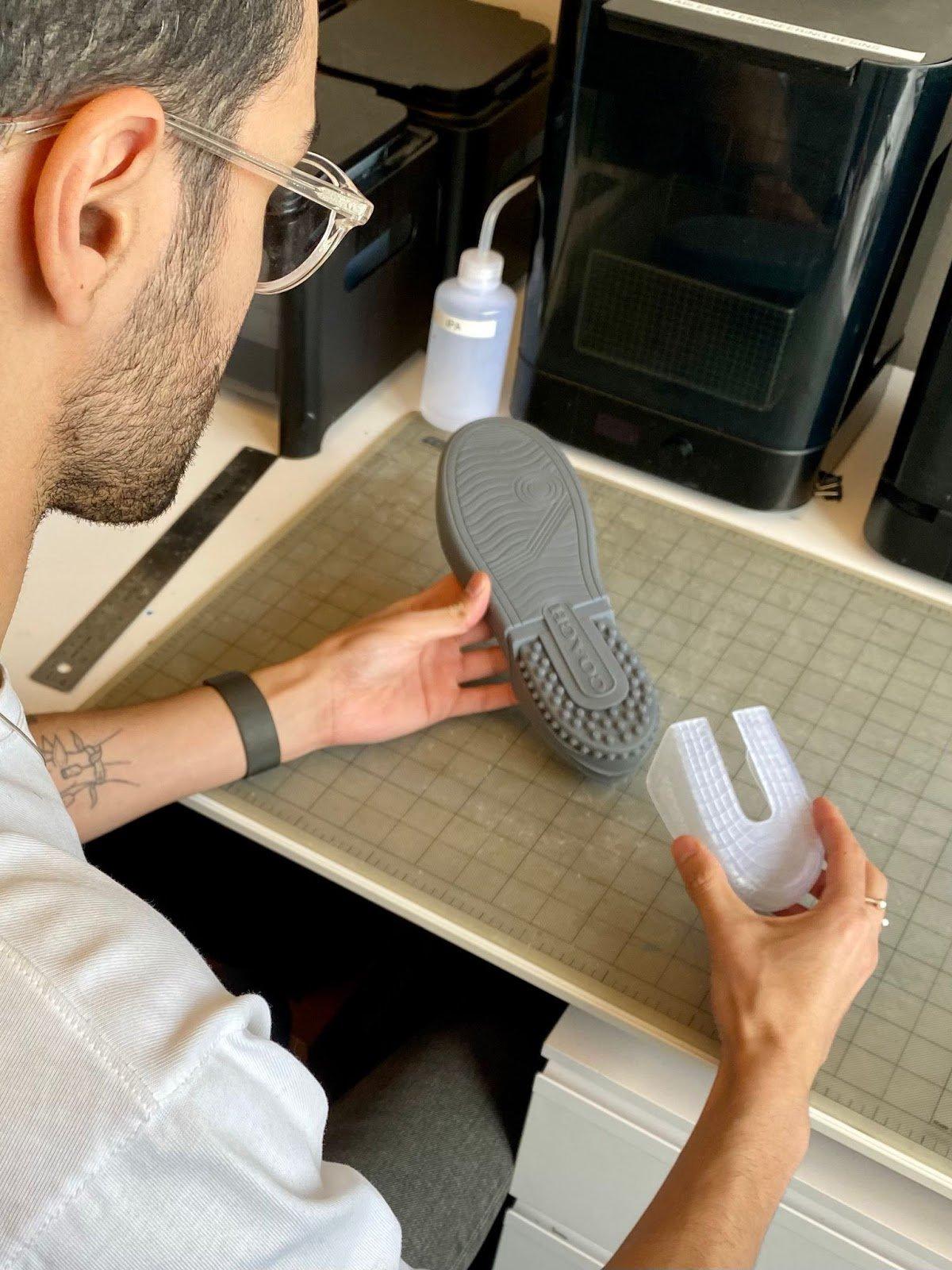
Mittlerweile ist der 3D-Druck bei Tapestry ein unverzichtbarer Bestandteil des Unternehmens. Die Mitarbeiter verwenden täglich 3D-Drucker von Formlabs. „Wir verfügen über den Form 2, den Form 3 und den Form 3L; hoffentlich werden wir bald einen weiteren Form 3L erhalten“, erklärte Emmar. „Sie werden für ein frühzeitiges Prototyping verwendet, um die Ästhetik und Funktionalität in den ersten Phasen des Produktentwicklungsprozesses zu überprüfen.
Bei Tapestry setzt das 3D-Team Arbeitsabläufe ein, die sowohl die Designziele als auch die mechanische Funktionalität vermitteln, um die Markteinführung zu beschleunigen. Sie unterstützen die technische und globale Fertigung mit digitalen Produktentwicklungslösungen, um den Prozess von der Produktentwicklung bis zur Vermarktung zu optimieren.
Drucken von Außensohlen in voller Größe: Der Form 3L bringt Bewegung ins Spiel
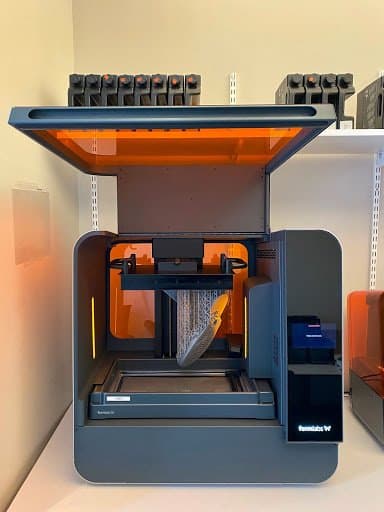
Der Form 3L gehört zum festen Bestandteil der täglichen Arbeit von Tapestry.
Tapestry ist dadurch in der Lage, größere Teile zu drucken. Nach Emmars Angaben hatte der Form 3 nicht die Kapazität – eine komplette Außensohle zu drucken – daher musste das Team die Außensohle in zwei Teilen drucken. Dies wirkte sich negativ auf die Maßgenauigkeit aus.
„Wenn man Prototypen in Einzelteilen zusammensetzt, wird die Maßgenauigkeit beeinträchtigt, weil zwei separate Teile zusammengeklebt werden müssen“, so Emmar. „Die Abweichung lag in der Regel bei ein bis zwei Millimetern. Das ist bei Schuhen von entscheidender Bedeutung, denn eine halbe Nummer größer macht schon einiges aus. Somit können ein bis zwei Millimeter beim Prototyp wirklich einen Unterschied ausmachen.“
Dank des Form 3L wurde die Maßgenauigkeit verbessert. Emmar zufolge ermöglichte ihm der Form 3L, die Maßgenauigkeit auf 0,1 Millimeter genau zu bestimmen. „Es ist dem endgültigen Produkt viel, viel näher. Die Variabilität ist nicht so groß. Ein Druck, der ein bis zwei Millimeter größer ist, kann eine völlig andere Schuhgröße sein“, erläuterte er.
Es wurde klar, dass die Form 3L intuitiv ist. „Vom ersten Augenblick an, also nach dem Auspacken, fühlte sich alles sehr vertraut an. Ich hielt es einige Wochen lang für mich selbst bereit, bevor ich die Kapazität für meine bereichsübergreifenden Partner öffnete, aber ich lernte schnell, dass es gar nicht so lange dauern würde. Die Handhabung ist sehr einfach und bekannt. Selbst bei 200 Mikrometern ist die Oberflächenqualität erstaunlich glatt,“ so Emmar.
Emmar nutzte die große Materialbibliothek von Formlabs und setzte auf Draft Resin für größere Projekte und solche, die weniger Details erfordern. Sein Team verwendet Tough 1500 Resin auch für Prototypen von Funktionsteilen, wenn die Baugruppe erfordert, dass sich die Teile verformen und wieder in ihre ursprüngliche Form zurückkehren.
Sobald Formlabs ein neues Material veröffentlicht, bezieht Emmar es für das Team, um deren Materialbibliothek zu erweitern. Das Team wendet verschiedene Forschungs- und Entwicklungsmethoden an, um die Eigenschaften und Merkmale neuer Materialien zu untersuchen und das am besten geeignete Material zu finden. „Die Materialwahl hängt vom Anwendungsfall des zu druckenden Prototyps und von den Bedürfnissen unserer internen Kunden ab. Wir betreiben eine Menge F&E für neue Materialien, um abzuwägen, ob sie ein nützliches Angebot für unsere funktionsübergreifenden Partner sein könnten. Falls es einen Mehrwert für den Prozess darstellt, nehmen wir es in unsere Materialbibliothek auf und bieten es auf der Grundlage des Anwendungsfalls für die jeweilige Anfrage an“, so Emmar.
Tapestrys Zukunft mit dem 3D-Druckverfahren
Tapestry profitierte stark vom 3D-Druck, um den Anforderungen der schnelllebigen Modeindustrie gerecht zu werden. Somit war das Team in der Lage, Prototypen im Handumdrehen herzustellen, was schneller und kostengünstiger ist als die Zusammenarbeit mit Produktionsstätten aus Übersee. Tapestry-Designer profitieren auch von der Flexibilität und Geschwindigkeit, die die Technologie bietet, da sie schneller fundierte Entscheidungen treffen können. Letztendlich unterstützt der 3D-Druck das Unternehmen dabei, seine Nachhaltigkeitsziele zu erreichen, da die Prototypenherstellung betriebsintern erfolgt. „Wir reduzieren damit den Verbrauch von Rohstoffen und den Versand von Probedrucken aus Übersee. Lieber ein bisschen weniger und dafür besser machen“, meint Emmar.
Angesichts der verteilten Prototyping-Möglichkeiten im Ausland hilft der 3D-Druck Tapestry, die Kommunikation zwischen den weltweiten Niederlassungen zu erleichtern. „Unser Unternehmen verfügt nun über die Möglichkeit, Prototypen auf der ganzen Welt zu erstellen. COVID-19 war der Auslöser, der die Einführung des 3D-Drucks vorangetrieben hat. Es wurde deutlich, wie wichtig Agilität und die Fähigkeit sind, Prototypen auf lokaler und regionaler Ebene zu entwickeln. Wir drucken die Teile auf Abruf, egal wann und wo sie für die Auswertung benötigt werden“, berichtet Emmar.
Für Tapestry bildet der Form 3L einen wichtigen Baustein für die Zukunft. „Dank dem Gerät ist unsere Kapazität erheblich gestiegen, und es eröffnete uns neue Möglichkeiten in der Prototypenfertigung größerer Teile. Bevor wir den Form 3L nutzten, mussten wir große Teile zuschneiden und anschließend zusammenbauen. Dieser Kompromiss beeinträchtigte die Maßgenauigkeit des Prototyps. Beim Drucken größerer Objekte müssen wir mit dem Form 3L keine Kompromisse mehr eingehen, und wir können weiterhin den wachsenden Prototyping-Bedarf unserer internen Kunden erfüllen“, so Emmar.
Tapestry erweitert derzeit seine Rapid-Prototyping-Kapazitäten und etabliert in allen Marken neue Wege der Zusammenarbeit mit neuen funktionsübergreifenden Partnern. Das Ziel ist es, die Vorteile des 3D-Drucks für alle bestehenden und zukünftigen Tapestry-Marken in allen Kategorien einzusetzen, um die Bedeutung des 3D-Drucks in der Mode hervorzuheben.