Produktion erfordert Optimierung, aber der Weg dorthin unterscheidet sich je nach Kontext und Zielsetzung stark. In diesem Beitrag behandeln wir die Bedingungen und Techniken, mit denen Hersteller und Ingenieure aus verschiedenen Bereichen das Meiste aus der additiven Fertigung herausholen.
Zunächst stellt sich die Frage, was optimiert werden soll. Ganz allgemein gibt es drei Ebenen, die der Ingenieur oder Hersteller bei der Optimierung betrachtet:
- Teileebene
- Prozessebene
- Produktebene
Auch wenn jede dieser Ebenen nach unterschiedlichen Überlegungen betrachtet werden muss, hängen sie alle in der Optimierungskalkulation von denselben Ressourcen ab: Zeit, Material, Arbeit und Qualität. Diese Kernfaktoren treiben Kosten und bestimmen den Spielraum bei einem bestimmten Teil, Prozess oder Produkt.
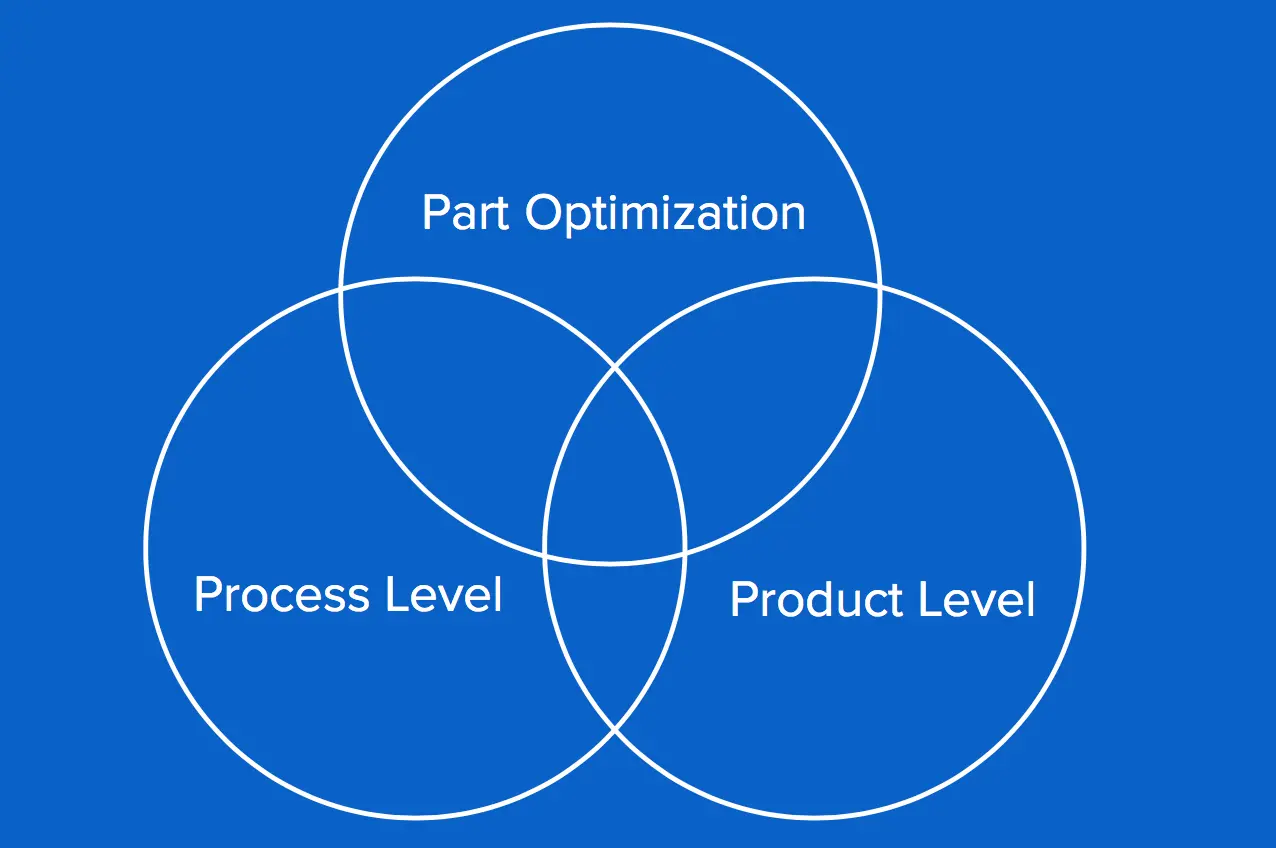
Optimierung auf Teileebene
Teileoptimierung ist wohl der Bereich, mit dem Ingenieure am besten vertraut sind: Wie entwickelt man eine Teilegeometrie, die die Anforderungen an Design und Leistung erfüllt und gleichzeitig den Zeit- und Kostenaufwand bei der Herstellung reduziert? Weitere häufige Kriterien für optimierte Teile sind Wartbarkeit, Montageaufwand, Gewichtsreduzierung und Haltbarkeit gegenüber mechanischen und Umweltbelastungen.
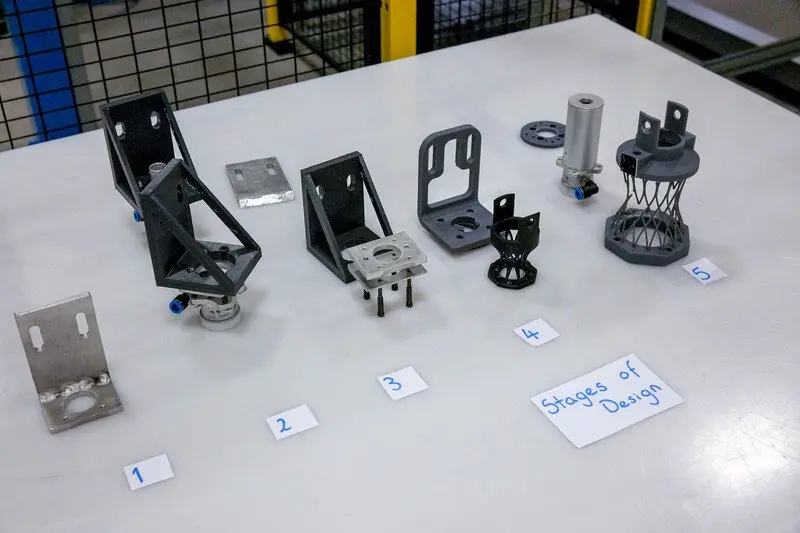
Der Optimierungsprozess einer Greiferhalterung beim AMRC umfasste fünf Stufen
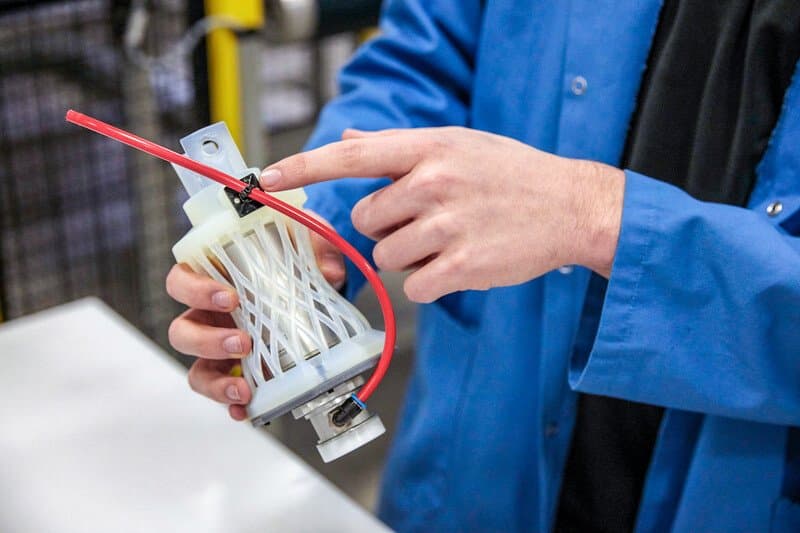
Das Teil wurde letztlich mit Stereolithografie (SLA) 3D-Druck hergestellt.
Dieses Beispiel einer Greiferhalterung beim AMRC veranschaulicht die Optimierung auf Teileebene hervorragend. Die Ingenieure haben die verfügbaren Materialien und die Einschränkungen des 3D-Druckprozesses untersucht, um ein Teiledesign zu schaffen, bei dem sich Optimierung für die Endanwendung und Herstellung die Waage halten.
Bei Polymerteilen ermöglicht additive Fertigung neue Geometrien und sorgt so für Verbesserungen in Sachen Funktion und Materialeffizienz.
Design für Nachgiebigkeit, Biegung und Leichtbau
Gitterstrukturen sind etwas, das man oft als 3D-Druckteile sieht, und das aus gutem Grund. Im Gegensatz zu Zerspanungs- oder Gussverfahren ist es einfach und kostengünstig, eine große Anzahl an Vertiefungen wie Löcher, Nute und Durchgänge zu fertigen. Dabei spielen Größe und Winkel in den meisten Fällen keine Rolle. Diese Vertiefungen sorgen dafür, dass der Bau des Teils weniger Material erfordert, reduzieren die gesamte Fertigungszeit und erhalten oder erhöhen gar die strukturelle Integrität und die Leistung des Teils.
Bei flexiblen oder halbsteifen Materialien können Gitterstrukturen die Belastbarkeit des Teils aus verschiedenen Winkeln und gegenüber unterschiedlichen Druckeinwirkungen erhöhen. Sie sorgen in anderen Bereichen bei Bedarf für zusätzliche Nachgiebigkeit und bieten die Festigkeit, um Kompression oder Biegung zu widerstehen.
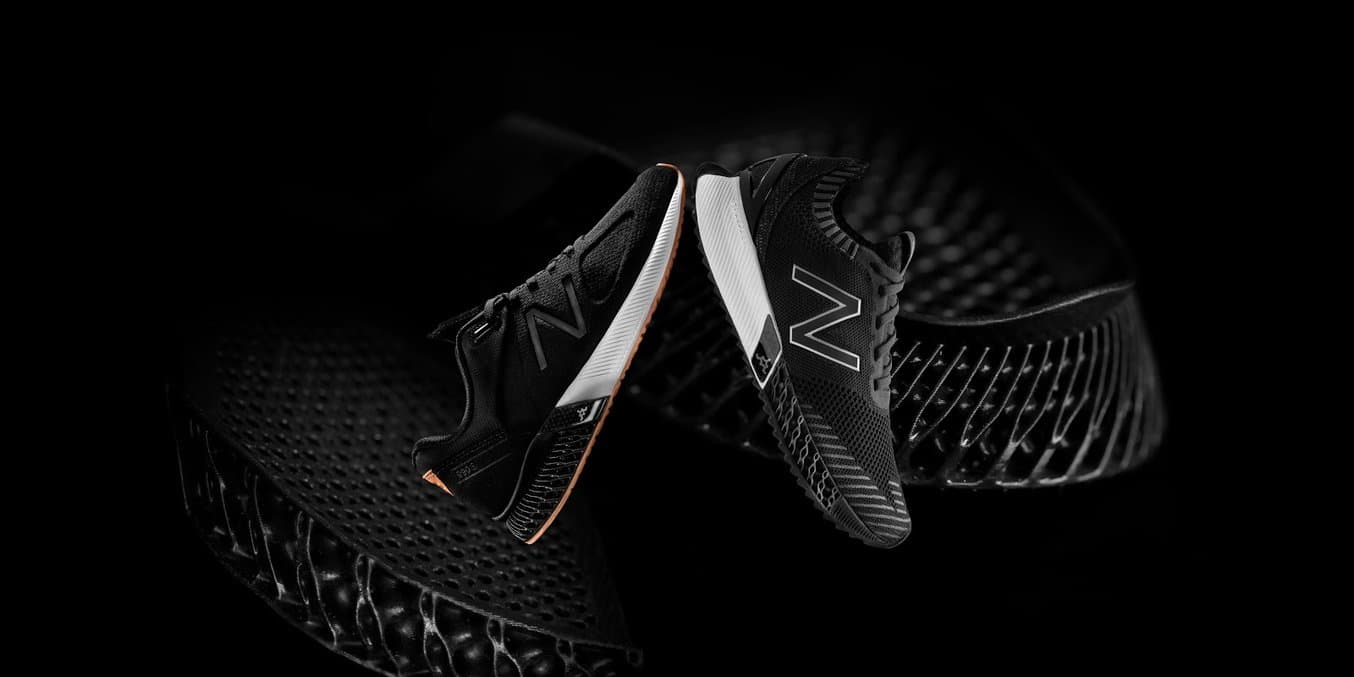
Zwei vor kurzem veröffentlichte Produkte von New Balance nutzen eine 3D-gedruckte Gitterstruktur, um Stöße aufzufangen und Energie zurückzugeben. Dabei sind sie leichter und benötigen weniger Material als herkömmlich gefertigte Teile.
Optimierung auf Prozessebene
Bei der Optimierung auf Prozessebene geht es weniger um die Einzelheiten eines bestimmten Teils und mehr darum, wie sich die alltäglichen Arbeitsprozesse verbessern lassen, mit Hinblick auf Zeit und Kosten oder zur Steigerung von Ertrag und Qualität.
Ein wichtiger Bereich, in dem der 3D-Druck zur Prozessoptimierung beiträgt, sind Halterungen und Vorrichtungen sowie maßgefertigte Werkzeuge für die Fertigung. Häufig nutzen Unternehmen betriebsinterne 3D-Drucker, um zu „revertikalisieren“, d. h. um die hohen Kosten ausgelagerter Bestellungen zu eliminieren sowie das Problem der Mindestbestellmengen und die langen Durchlaufzeiten von der Werkstatt des Anbieters bis zur Einbindung im Werk.
Betriebsinterne Revertikalisierung:
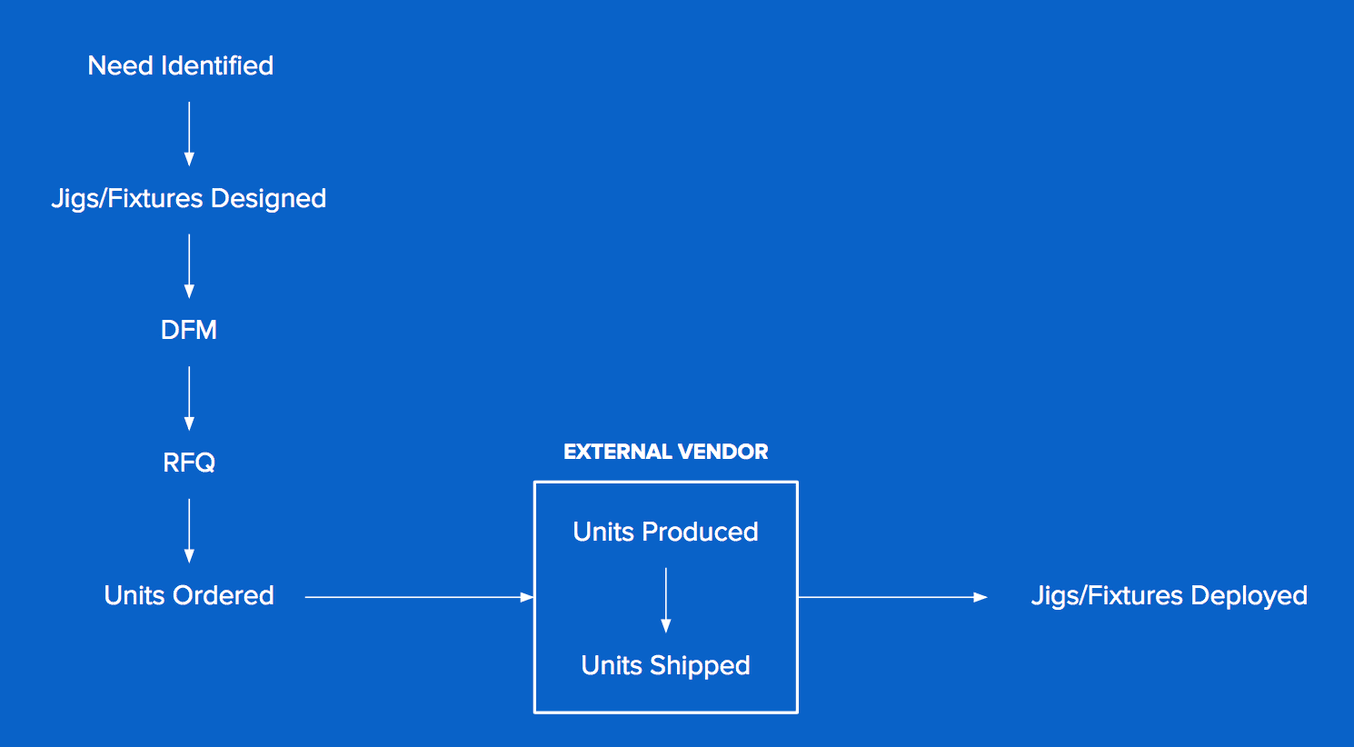
Ein traditioneller Arbeitsprozess mit ausgelagerter Zerspanungsproduktion von Halterungen und Vorrichtungen erfordert gezieltes DFM (Design for Manufacturing), involviert häufig Mindestbestellmengen, um kosteneffizient zu sein, und bringt Durchlaufzeiten von mehreren Tagen oder Wochen mit sich.
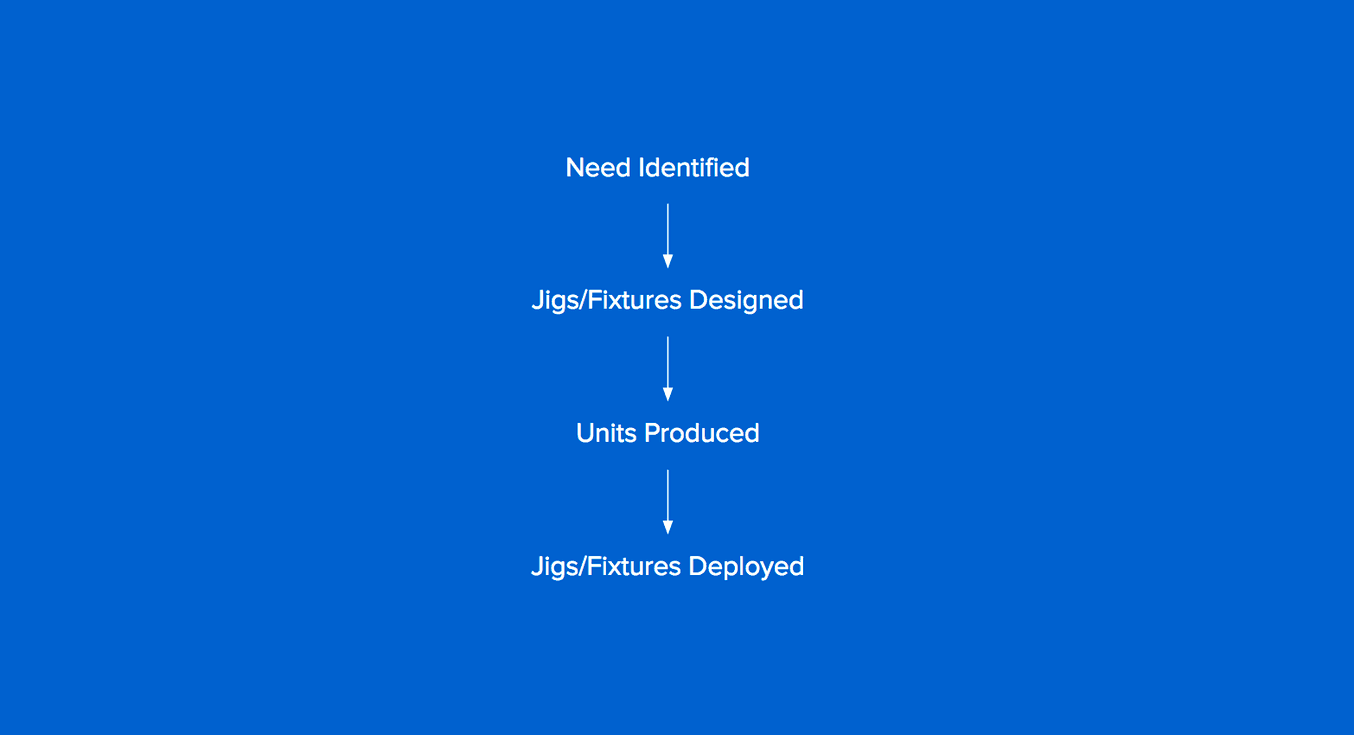
Arbeitsprozesse mit additiver Fertigung und betriebsinterner Herstellung von Halterungen und Vorrichtungen haben deutlich weniger Schritte von der Identifizierung des Bedarfs bis zur Implementierung der Lösung im Werk.
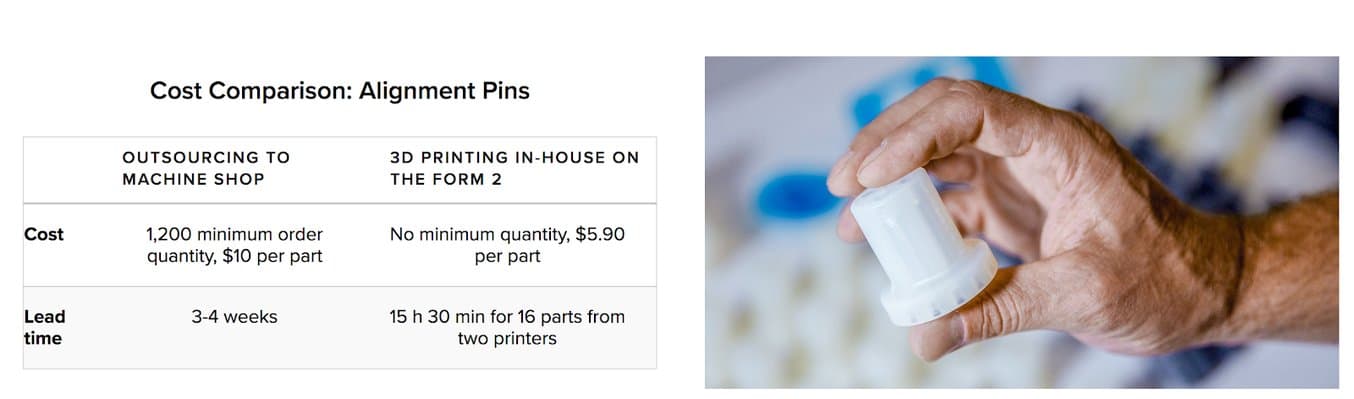
Betriebsinterner 3D-Druck zur Revertikalisierung hat der Korpusmöbelabteilung von Ashley Furniture Zeit und Geld gespart bei Werkzeugbestückung, Halterungen und Vorrichtungen wie diesem Führungsstift.
Zugang führt zu Innovation
Es kommt zu erheblicher Ablaufoptimierung, wenn Prozessänderungen auf niedriger Ebene (wie die betriebsinterne Fertigung von Halterungen und Vorrichtungen) mehr Experimente und Innovationen ermöglichen. So etwas wäre schwer zu planen, ergibt sich jedoch häufig, wenn Ingenieure Zugang zu automatisierten Herstellungstechnologien wie 3D-Druck haben.
Bislang waren hochwertige 3D-Drucker teuer und erforderten fachkundige Techniker, wodurch die meisten Unternehmen die Technologien mit einem Top-down-Ansatz nutzten.
Top-down-Ansatz:
- 3D-Druck in einer lokalen Einrichtung
- Hochleistungsfähige Industriegeräte
- Bedient durch spezielle, fachkundige Mitarbeiter, die Ratschläge zur Einführung des 3D-Drucks geben
- Projekte werden vor Start vollständig geplant und autorisiert
- Hohe Investitions- und Betriebskosten
Da aber die Kosten von 3D-Druckern gesunken sind und ihre Zugänglichkeit gestiegen ist, gibt es einen neuen Bottom-up-Ansatz.
Bottom-up-Ansatz:
- 3D-Drucker im gesamten Unternehmen verteilt
- Preiswerte, zugängliche Desktop-Geräte
- Bedienung durch Endnutzer, die Experten ihrer eigenen Prozessen sind
- Projekte können als risikoarme Experimente durchgeführt werden
- Niedrige Investitions- und Betriebskosten
- Kulturwandel: Mitarbeiter werden zu Innovationen ermutigt, während 3D-Druck zum integralen Bestandteil wird
„Ich brauchte Geräte, an denen Mitarbeiter einfach geschult werden können und die Erfolgserlebnisse liefern, sodass man sie erneut benutzen möchte. Der Form 2 ist das erste kleine SLA-Gerät, das ich ausprobiert habe und bei dem ich dachte: ‚Ja, das ist wirklich revolutionär.‘ Das Gerät lässt sich so einfach bedienen“, erzählt Cocking. „Die Software ist sehr intuitiv und Ingenieure lernen sie extrem schnell. Sie verstehen sie leicht und verinnerlichen die Grundlagen, und von da ab können sie selbst lernen und ihre additiven Erfahrungen ausweiten. Bislang wurden etwas über 100 Ingenieure an der Form-2-Station geschult.“
Das Advanced Manufacturing Research Centre (AMRC) der Universität Sheffield
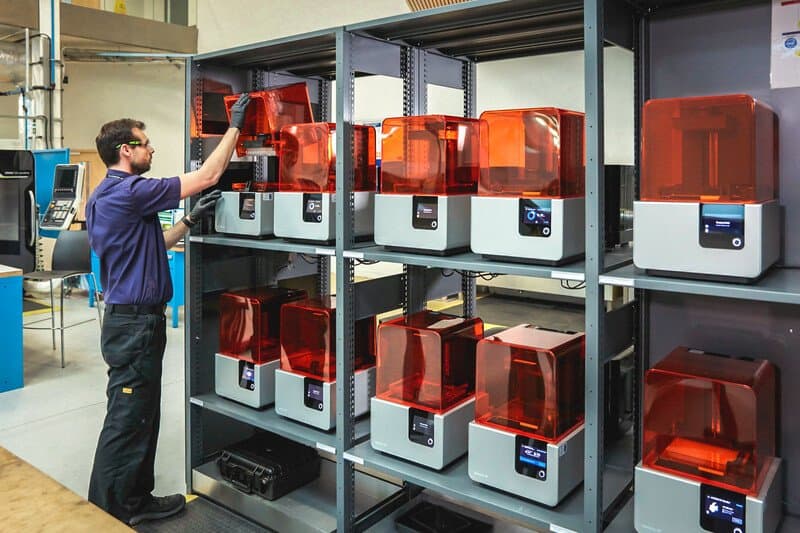
Die Formlabs-Druckerfarm des AMRC wird von einem Team aus über 100 Ingenieuren intensiv genutzt.
Optimierung auf Produktebene
Die Optimierung auf Produktebene unterscheidet sich von der Teile- und Prozessebene dadurch, dass es häufig ebenso darum geht, neue Geschäftsmodelle zu ermöglichen oder zu erproben, wie neue Produkte zu entwickeln.
Der 3D-Druck eliminiert die Risiken bei Unternehmen bezüglich innovativer Konzepte wie der seriellen Maßanfertigung. Der Bedarf an Werkzeugbestückung entfällt und damit auch die hohen Kosten und langen Durchlaufzeiten. Beim Direktdruck haben Unternehmen die Freiheit, kontinuierlich zu experimentieren – mit neuen Geometrien, Mechanismen oder Produktangeboten – und das in robusten Materialien, die auch für den Endverbrauch geeignet sind.
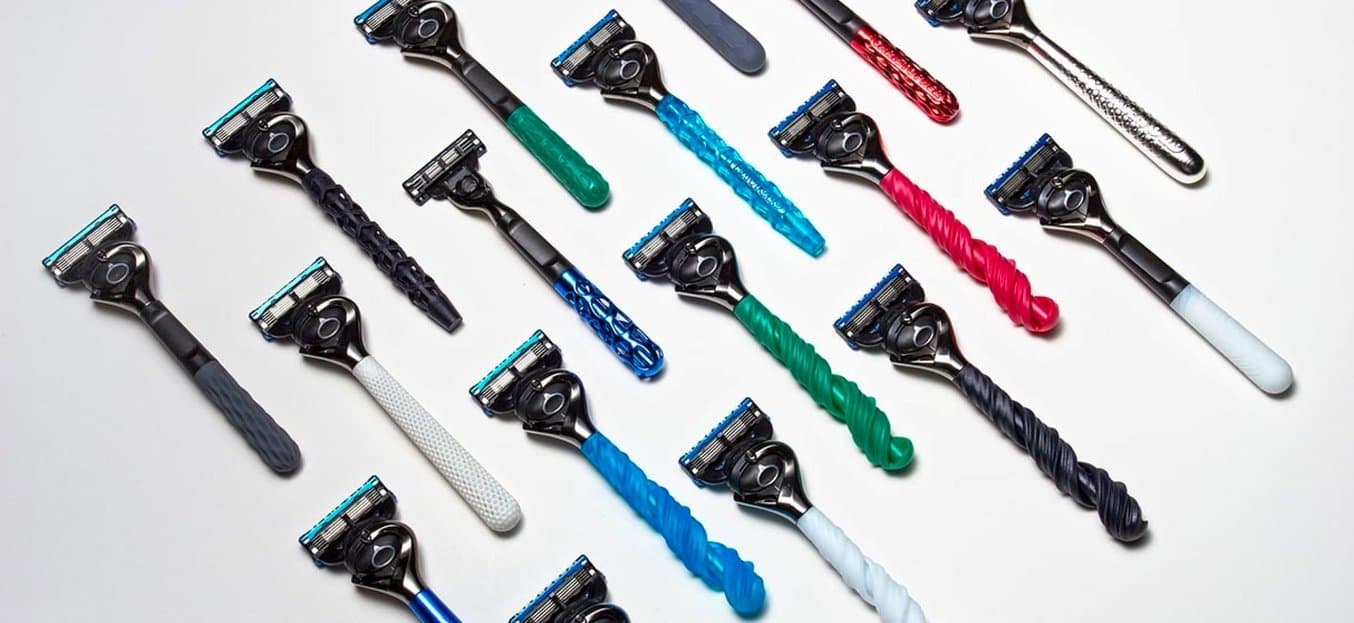
Beispielsweise hat Gillette den direkten 3D-Druck bei der „Razor Maker“-Initiative eingesetzt, bei der Kunden aus einer riesigen Palette an Farb- und Musterkombinationen auswählen konnten. Die Rasierergriffe konnten sogar mit Namen personalisiert werden. Die Fertigung von Teilen auf Anfrage – mit Losgrößen von nur einem Exemplar in manchen Fällen – wäre mit herkömmlichen Fertigungsverfahren nicht kosteneffizient.
Ähnliche Personalisierungs- oder Individualisierungsansätze gibt es in der Orthetik, bei Ohrstöpseln und bei Fahrzeugteilen. Bei allen diesen Beispielen ermöglichen individualisierte oder personalisierte Waren optimierte Produkte, angepasst an den Körper oder den Geschmack des Kunden. Marken können Kunden besser das bieten, was diese wünschen und wann sie es wünschen.
Ausweitung der Zugänglichkeit
3D-Drucktechnologien gibt es seit den 1980er-Jahren. Aber die Chancen zur Optimierung wachsen noch immer rapide mit der Entwicklung neuer Materialien, Rechenwerkzeuge und operativer Rahmenbedingungen.
Fortschritte beim kostengünstigen, hochauflösenden Druck machen die Technologien für Unternehmen jeder Größe zugänglich und schmälern die Kluft zwischen Konzept und Umsetzung. Erfahren Sie mehr über die neueste Generation von SLA-Druckern und darüber, wie LFS Ingenieuren und Herstellern die Macht gibt, jeden Tag für Innovationen zu sorgen.
Probedruck aus dem Form 3 anfordern