3D-gedruckte Kohlenstofffaserformen und Endverwendungsteile für die Rennwagen der Formula Student
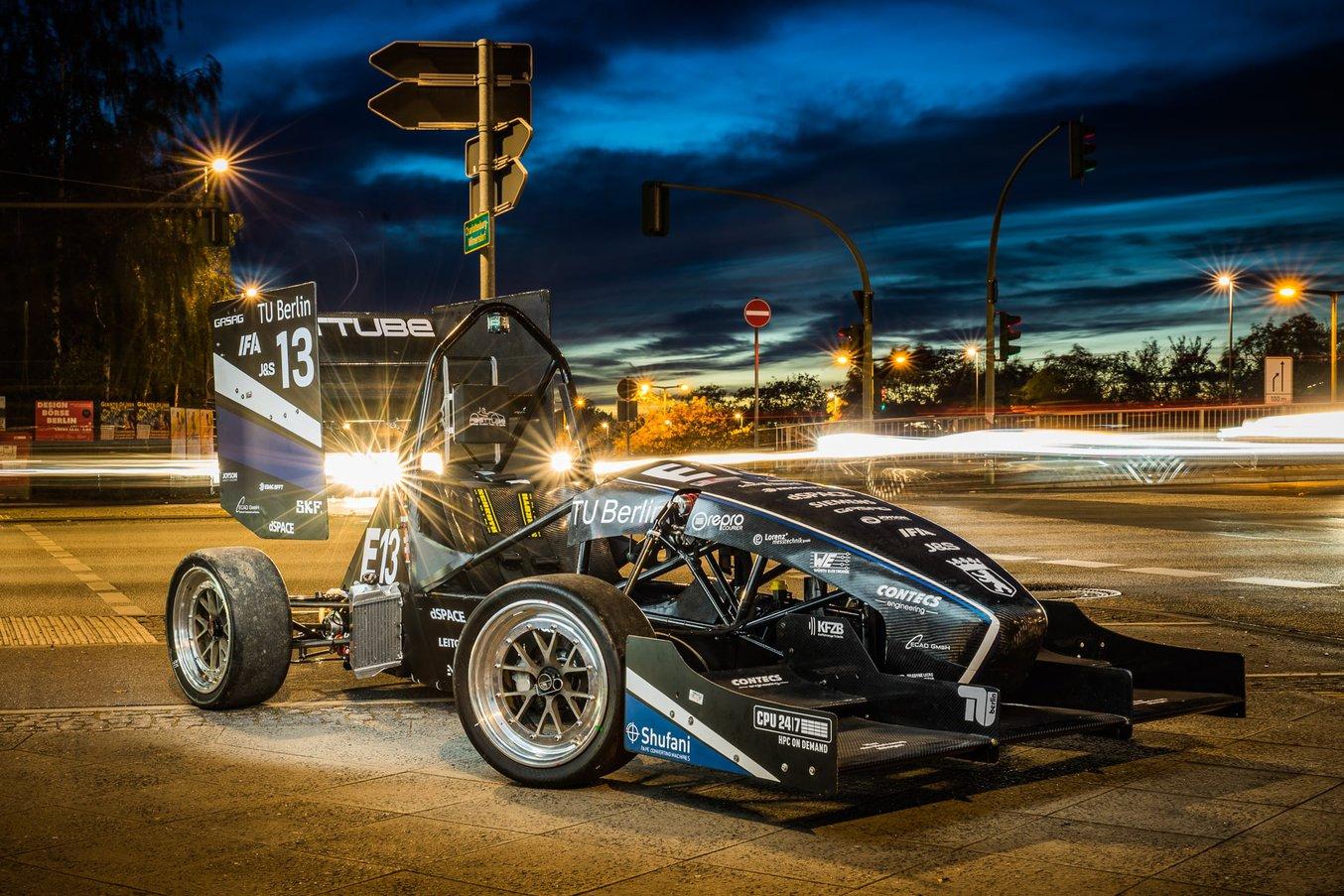
Die Formula Student ist ein alljährlicher Ingenieurdesign-Wettbewerb, bei dem Studententeams aus der ganzen Welt Rennwagen im Formel-Stil bauen und mit ihnen Rennen fahren. Das Formula Student Team der TU Berlin (FaSTTUBe) ist eines der größten darunter. 80-90 Studenten entwickeln dort seit 2005 jedes Jahr neue Rennwagen.
Das Team baut diese Saison zum ersten Mal drei Modelle: mit Verbrennungsmotor, mit Elektromotor und mit autonomer Versorgung. Von Herbst bis Sommer haben sie ein Schuljahr Zeit, die Fahrzeuge vor den Rennen zu entwerfen, zu produzieren, zu montieren und zu testen. Beurteilt werden die Teams nach Geschäftsmodell, Designkonzept, Kostenaufstellung und Wagenleistung (insbesondere Motorleistung, Effizienz und Ausdauer).
Dieses Jahr hat das Team ein neues Werkzeug zur Hand, den SLA-3D-Drucker Form 3. Mit selbigem konnten die Studenten Zeit und Kosten sparen sowie Teile erstellen, die anders unmöglich gewesen wären:
-
Prototypen: Das Team druckt Prototypen verschiedener Teile wie z. B. die Befestigungen der Überrollbügel oder die Halterungen der HV-Batterie.
-
Formen für Kohlenstofffaserteile: Das Team hat Dutzende Formen zur Herstellung von Kohlenstofffaserteilen gedruckt, die anders nicht möglich gewesen wären.
-
Endverbrauchsteile: Etwa 30 Endteile des Wagens wurden direkt 3D-gedruckt, von Knopfhalterungen über die Schaltung am Lenkrad bis zu Schläuchen und Sensorverbindungen des Kühlsystems.
Niklas Werner, der technische Leiter, Felix Hilken, Team Lead Carbon Fiber and Aerodynamics, haben uns durch den FaSTTUBe-Arbeitsbereich geführt und uns diese Anwendungen vorgestellt.
Handlaminierung von Kohlenstofffaserteilen mit 3D-gedruckten Formen
Eines der ikonischsten Teile jedes Rennwagens ist das Lenkrad. In der letzten Saison nutzte das Team einen Schneidlaser, um eine Kohlenstoffplatte anzufertigen, und selektives Lasersintern (SLS), um die Griffstücke und das Gehäuse für die Elektronik zu drucken.
Gewichtsverringerung ist beim Bau von Rennwagen entscheidend. Also versuchte man es mit dem Druck ausgehöhlter Griffe. Diese waren allerdings nicht stark genug, um dem festen Griff des Fahrers standzuhalten. Dieses Jahr entschieden Sie sich für Teile aus Kohlenstofffaser. Das ist ein großartiges Material zur Gewichtsreduzierung, welches ebenso stark oder sogar noch stärker ist.
Hilken entwickelte einen Arbeitsprozess, in dem 3D-gedruckte Formen zur Nasslaminierung eingesetzt werden. Das ist eine großartige Methode, mit minimalen Voraussetzungen Kohlenstofffaserteile herzustellen.
Dieses kurze Video zeigt den Laminierungsprozess für Kohlenstofffaser.
Dank der Verwendung von Kohlenstofffaser verringerte das Team das Gewicht des Lenkradgehäuses von 120 g auf 21 g. Hilken benötigte dabei einen Tag zum Design und Bau der Form. Dabei konnte das Team im Design Geometrien verwirklichen, die mit traditionellen Fertigungsmethoden nur überaus schwer umzusetzen sind.
„Das Tolle am 3D-Druck ist, dass sich komplexe Körper genauso leicht herstellen lassen wie einfache. Der Arbeitsaufwand ist der gleiche und die Ausrüstung ebenfalls. Einige dieser Elemente können mit anderen Verfahren tatsächlich nicht bezahlbar umgesetzt werden“, verrät uns Hilken.
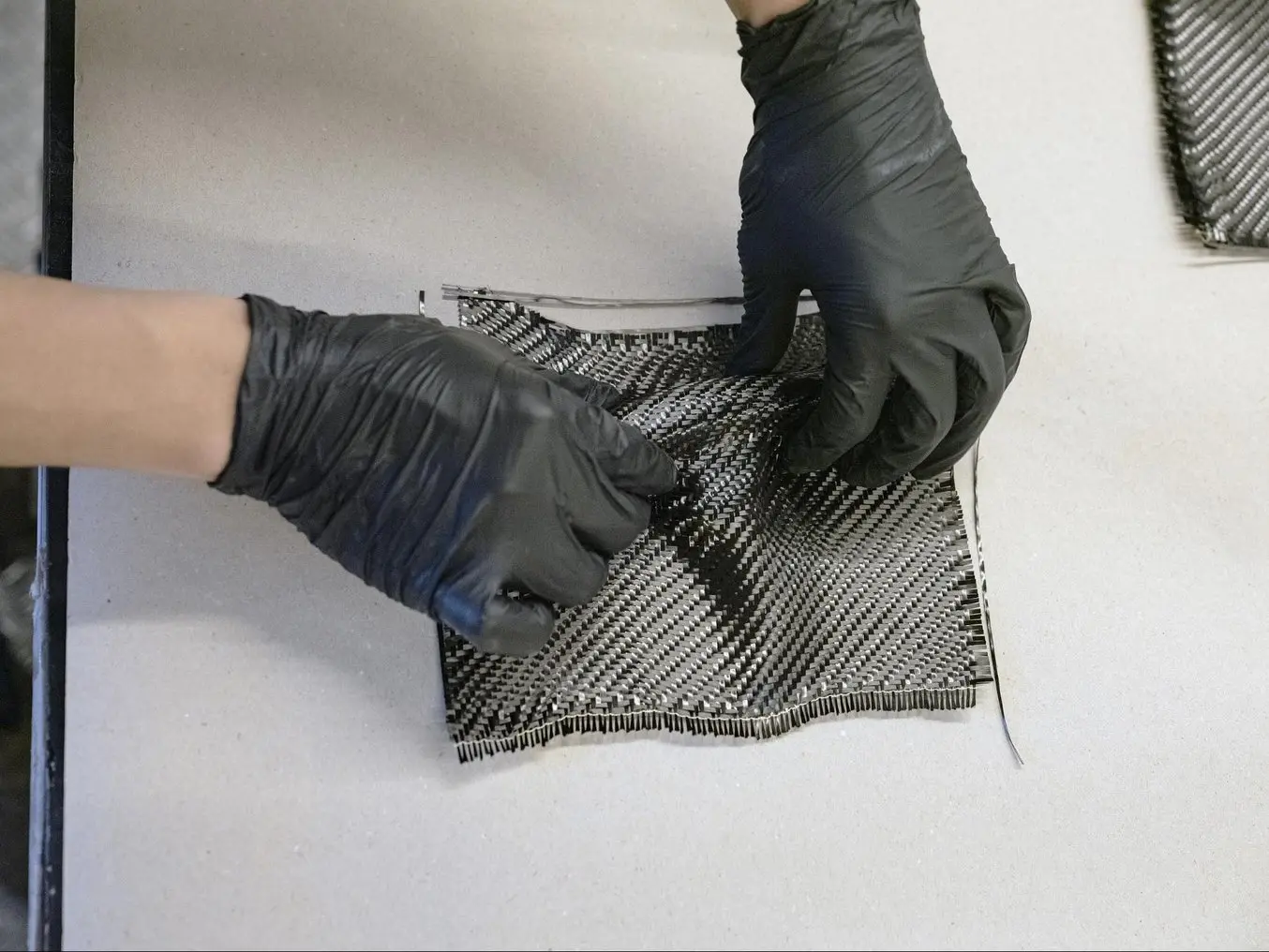
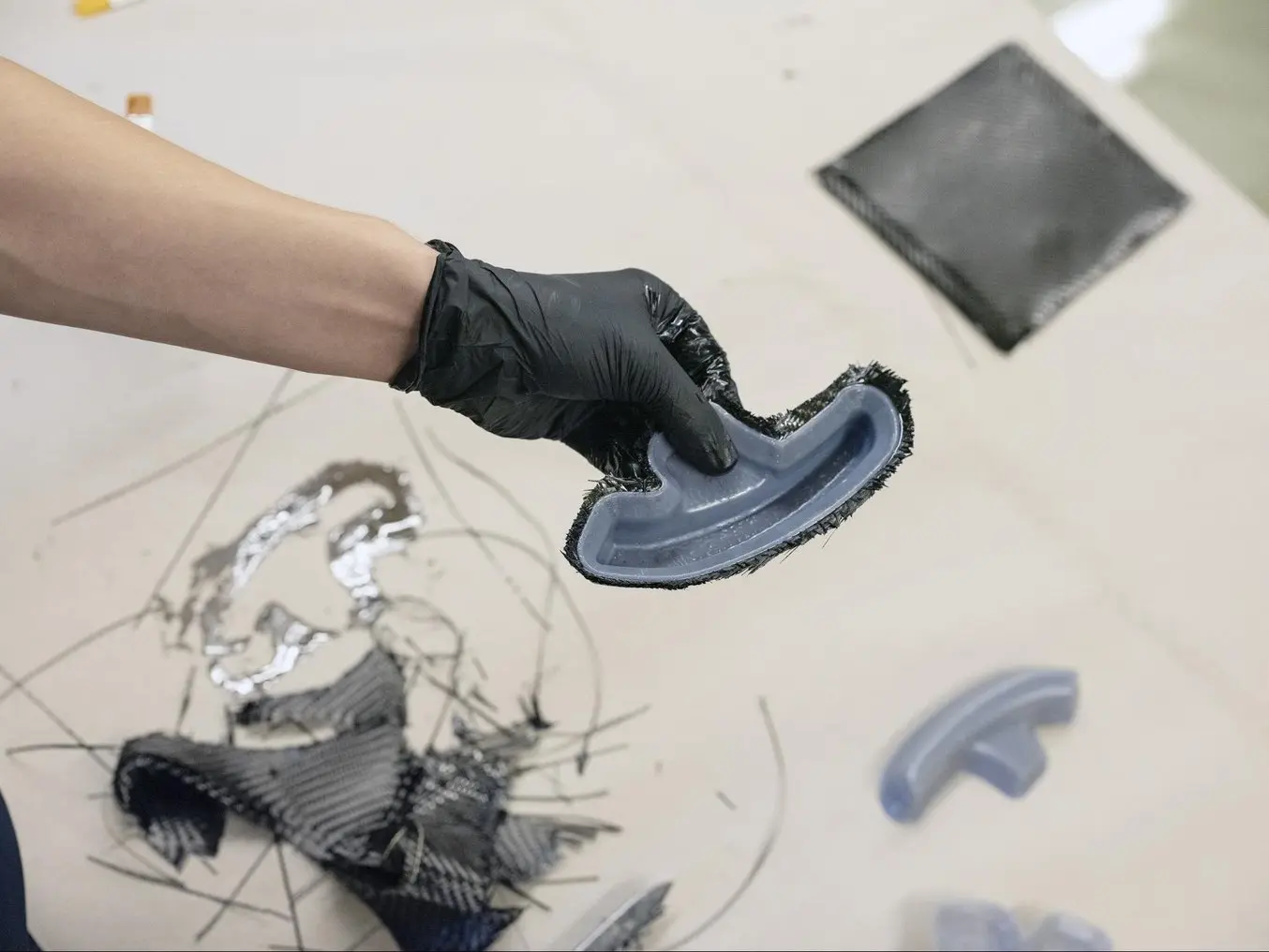
Hilken laminierte drei Kohlenstofffaserlagen über einer 3D-gedruckten Form und setzte dann eine Negativform auf, um die Lagen fest zusammenzudrücken.
Hilken verwendete dafür Tough 1500 Resin, da dieses ein gutes Gleichgewicht aus Dehnung und Modul bietet. Teile, die aus diesem Material gedruckt werden, lassen sich stark verbiegen und kehren schnell wieder in ihre ursprüngliche Form zurück. Das erleichtert die Entformung des Teils. Mit dieser Technik kann man Hilkens Einschätzung nach etwa zehn Teile mit einer Form anfertigen. Da dies ein manueller Arbeitsprozess ist, hängt alles davon ab, wie sorgfältig die Person arbeitet, z. B. können Fasern stecken bleiben oder es kann beim Entformungsprozess zu Beschädigungen der Form kommen.
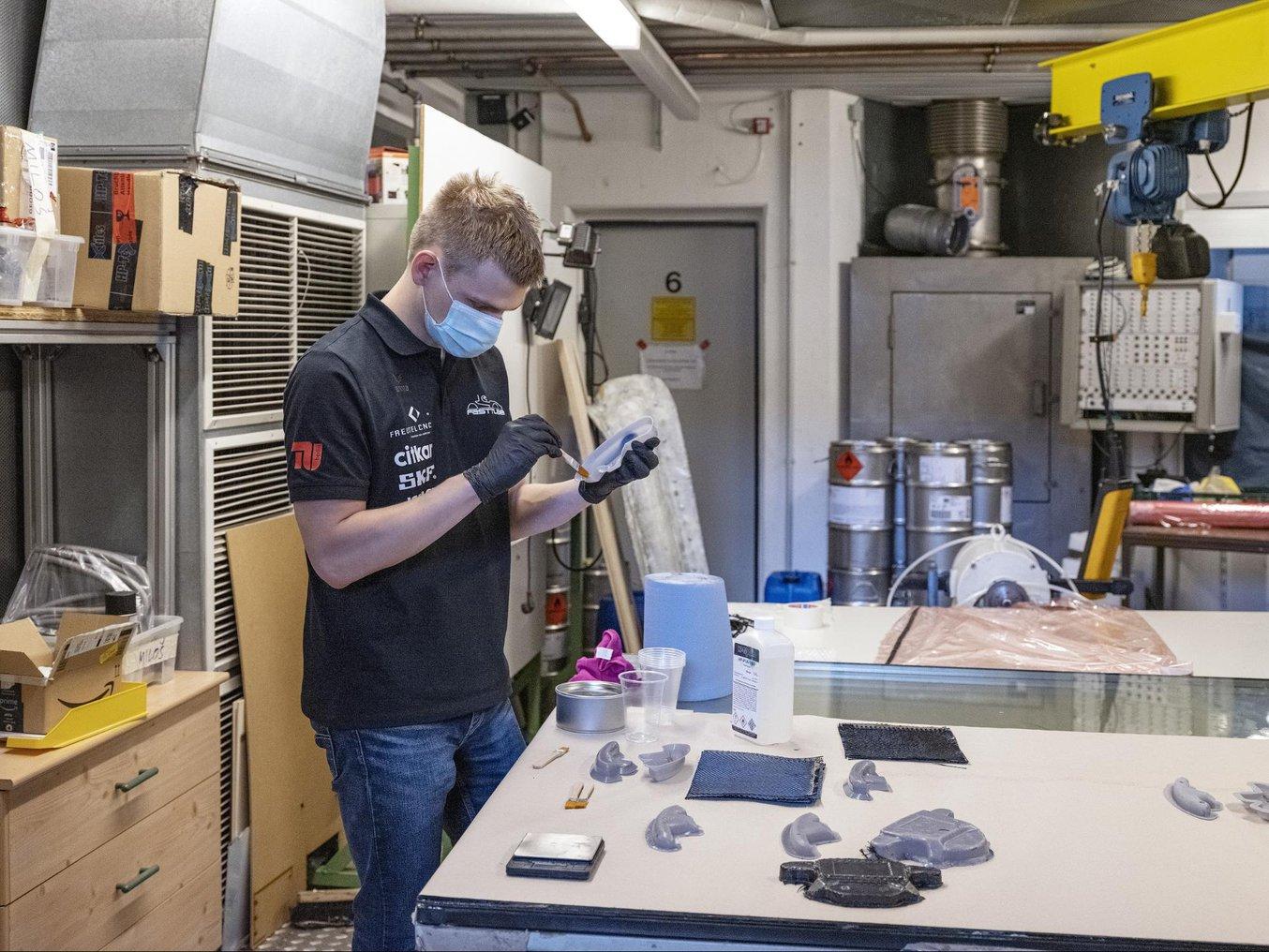
Nasslaminierung mit 3D-gedruckten Formen ist eine großartige Methode, mit minimalen Voraussetzungen Kohlenstofffaserteile herzustellen.
Ohne 3D-Druck hätte das Team eine zerspante Aluminiumform in Auftrag geben müssen. Das ist teuer, hat eine lange Durchlaufzeit und benötigt Spezialwerkzeuge.
„Würde ich die Form über CNC-Bearbeitung herstellen, müsste ich mir Spezialwerkzeuge beschaffen und darauf warten, dass die Maschine mal frei wird. Und selbst dann hätte ich diese Geometrie nicht hinbekommen. Insbesondere einige der kleinen Ecken. Ich bräuchte ein Design ganz ohne Schrauben, damit die Positionierung des Teils keine Rolle spielt“, so Hilken.
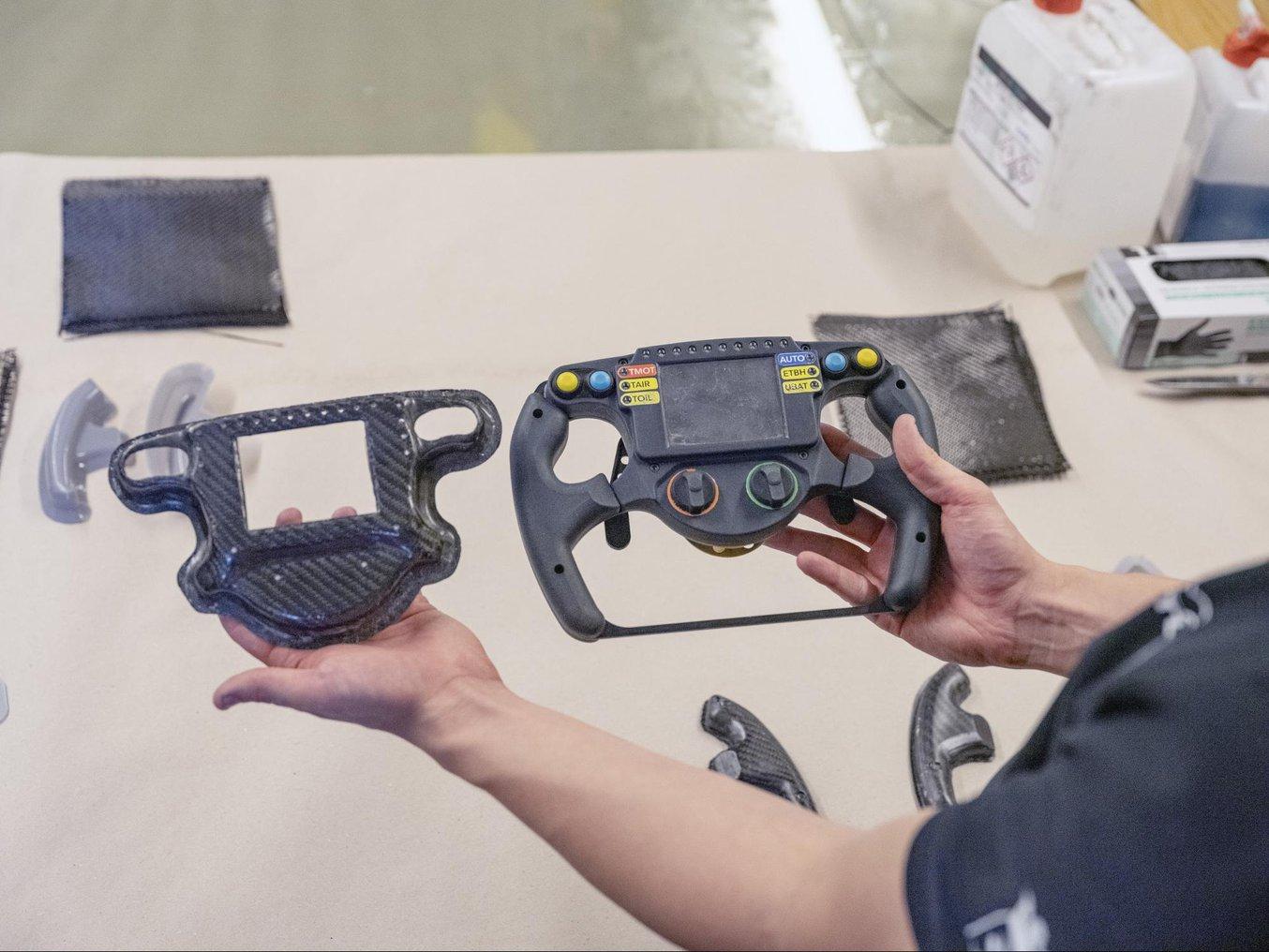
Das neue Kohlenstofffasergehäuse (links) neben dem zusammengebauten Lenkrad aus dem Vorjahr (rechts).
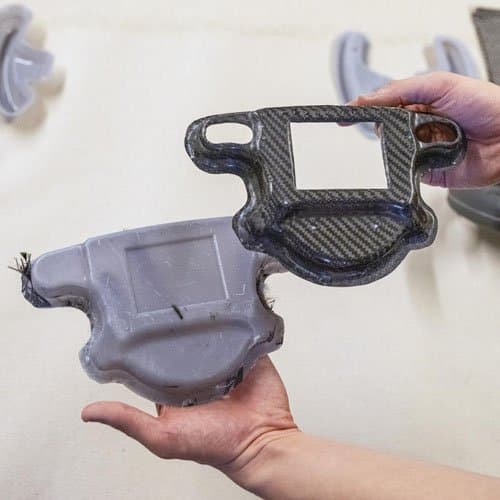
Fertigung von Kohlenstofffaserteilen mit 3D-gedruckten Formen
Laden Sie dieses Whitepaper zur Erstellung von Kohlenstofffaserteilen herunter. Es erläutert Designleitfäden für Verbundwerkstoffformen sowie schrittweise Anleitungen für die Prepreg- und Handlaminierung.
Vergleich von Kosten und Durchlaufzeit
Mithilfe des 3D-Drucks der Formen für die Handlaminierung der Kohlenstofffaserteile verringerte das Team die Kosten und die Durchlaufzeit drastisch. Hier ist ein Kostenvergleich zwischen dem Outsourcing einer Metallform und dem betriebsinternen 3D-Druck besagten Lenkrads. Dabei berücksichtigen wir die Arbeits- und Materialkosten und gehen von einer Ingenieurrate von 200 USD pro Stunde aus.
Outsourcing einer zerspanten Form | Betriebsintern 3D-gedruckte Form | |||
---|---|---|---|---|
Ausrüstung | Kohlenstofffaser, Harz, Werkzeuge, Vakuumfolie | Kohlenstofffaser, Harz, Werkzeuge, Vakuumfolie, 3D-Drucker Form 3, Tough 1500 Resin | ||
Zeitaufwand für die Formherstellung | 4–6 Wochen | 2 Tage | ||
Arbeitskosten | 0 | 300 USD | ||
Materialkosten | 0 | 10 USD | ||
Gesamtkosten der Formherstellung | 900 USD | 310 USD |
Endverbrauchsteile vom Schalthebel bis zur Kabelverbindung
Die Griffe und das Gehäuse sind nicht die einzigen Teile des Lenkrads, bei denen 3D-Druck zum Einsatz kam. Abgesehen von den laminierten Kohlenstofffaserteilen, der Kohlenstofffaserplatte und der Elektronik wurden alle Teile des Lenkrads auf dem Form 3 gedruckt.
Die Knopfhalterungen, Schalthebel, deren Halterungen und die Knöpfe wurden allesamt mit Tough 2000 Resin gedruckt, da es beste Belastbarkeit und Haltbarkeit bietet, bevor alles sprühlackiert wurde.
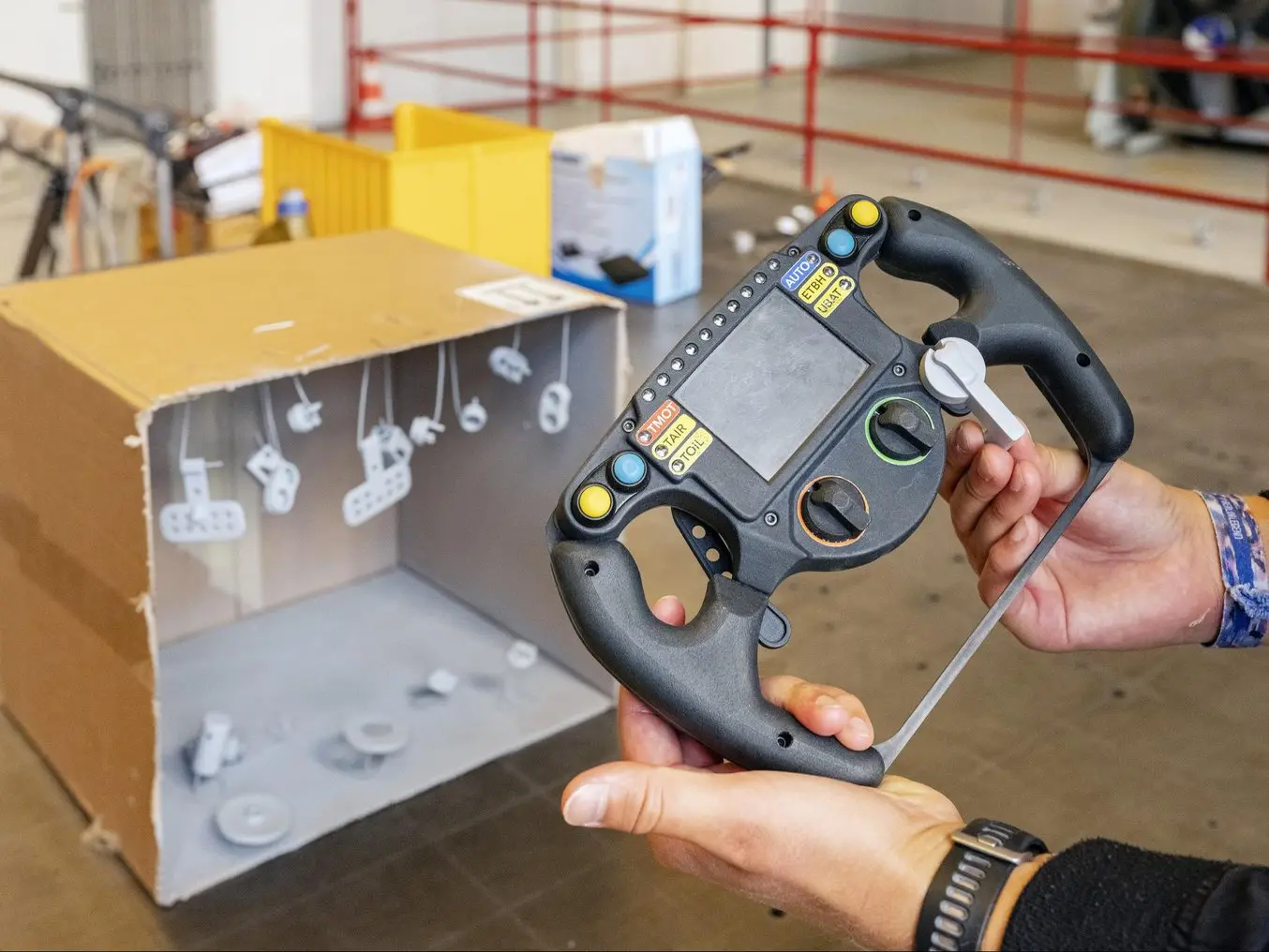
Die Knöpfe, die Schalthebel und die Halterungen beider wurden für das neue Lenkrad direkt 3D-gedruckt.
Insgesamt gibt es im Rennwagen aktuell ca. 30 SLA-Druckteile. Beispielsweise druckte das Team auch Kabelverbindungen, um den Kabelbaum besser zu organisieren. Diese bestehen aus Durable Resin und bieten deshalb genügend Flexibilität, um sich an die Rohre des Chassis anzuschmiegen.
„Die Dinger sind klasse für den Kabelbaum, denn sie sehen gut aus. Und das ist wichtig für den ersten Eindruck, wenn die Schiedsrichter kommen und ihn sehen“, berichtet Werner.
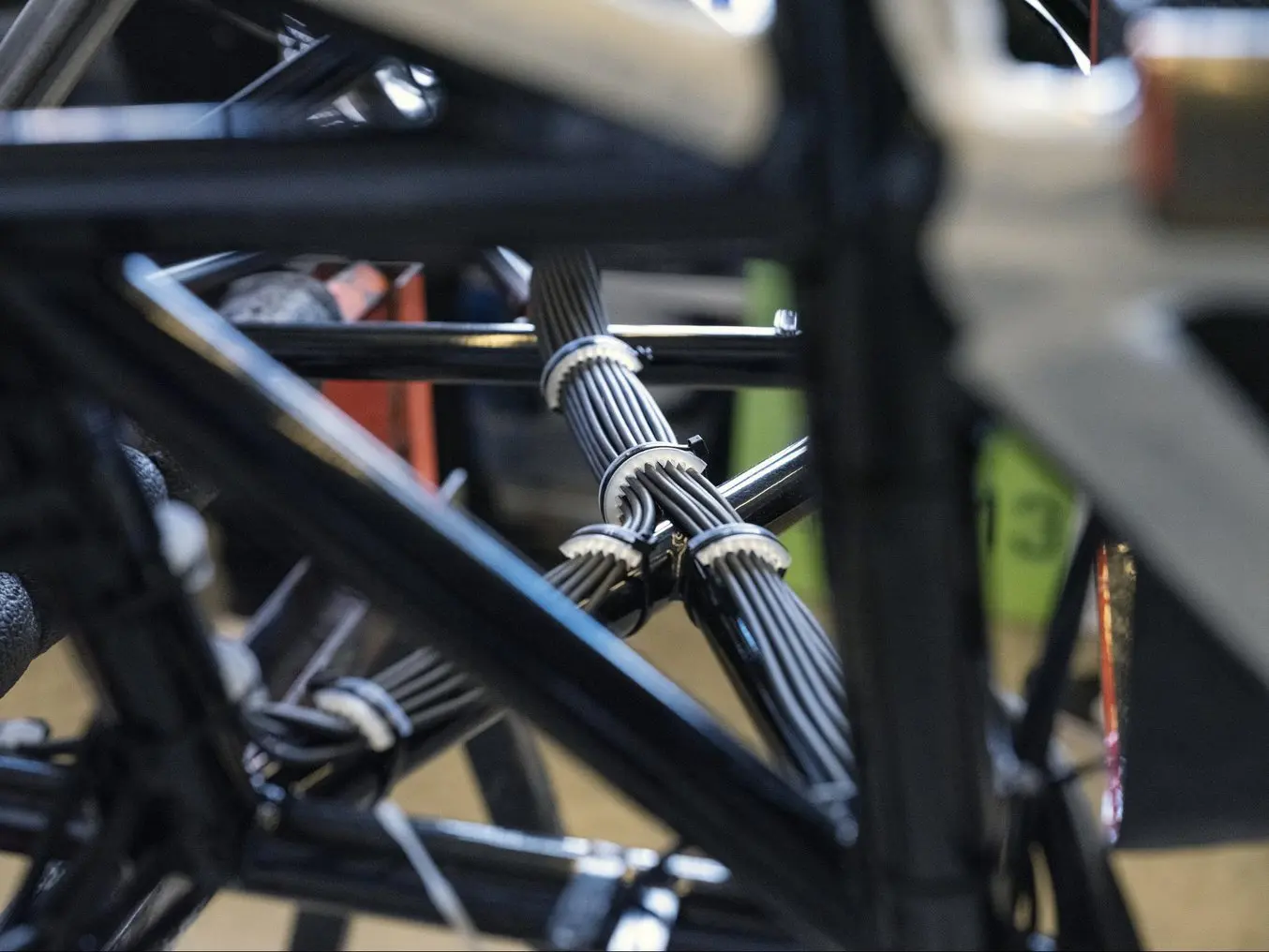
3D-gedruckte Kabelverbindungen helfen dabei, den Kabelbaum besser zu organisieren.
Außerdem gibt es noch mehr 3D-gedruckte Halterungen und Gehäuse und das Team plant den 3D-Druck auch für weitere Teile, z. B. die Endteile der Bremslichter und TSAL-Teile – Lichter am Elektrofahrzeug, die auf Systeme mit Hochspannung hinweisen.
Die Prototypenentwicklung eines generativen Teils für den Metall-3D-Druck
Es überrascht bestimmt niemanden, dass das Team den 3D-Druck auch in der Prototypenentwicklung einsetzt. So war es beispielsweise beim Prototypen der Halterung der Endarmatur an der Chassisfront – ein komplexes Teil, das mithilfe von Topologieoptimierung entworfen wurde. Das letztendliche Teil wird dann mittels Metall-3D-Druck gefertigt.
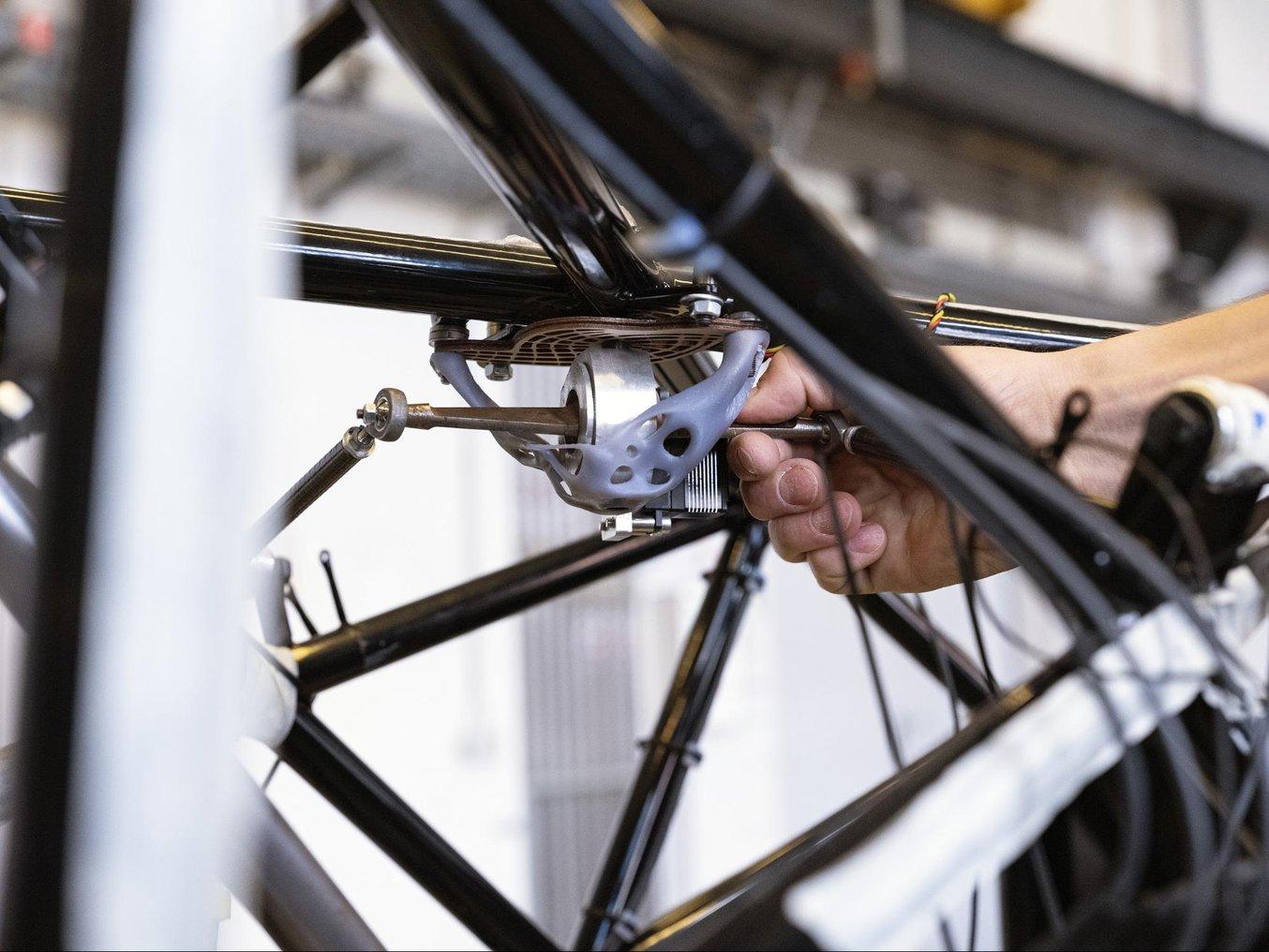
Das Team nutzte 3D-Druck für den Prototypen einer komplexen, topologieoptimierten Halterung, die später aus Aluminium gedruckt wird.
„Wir haben sie auf dem Formlabs-Drucker aus Kunstharz gedruckt, weil das nicht so teuer ist. So konnten wir validieren, ob sie an das Chassis passt oder nicht. Wir haben gesehen, dass sie passt, und jetzt lassen wir sie aus Aluminium anfertigen“, gibt Werner an.
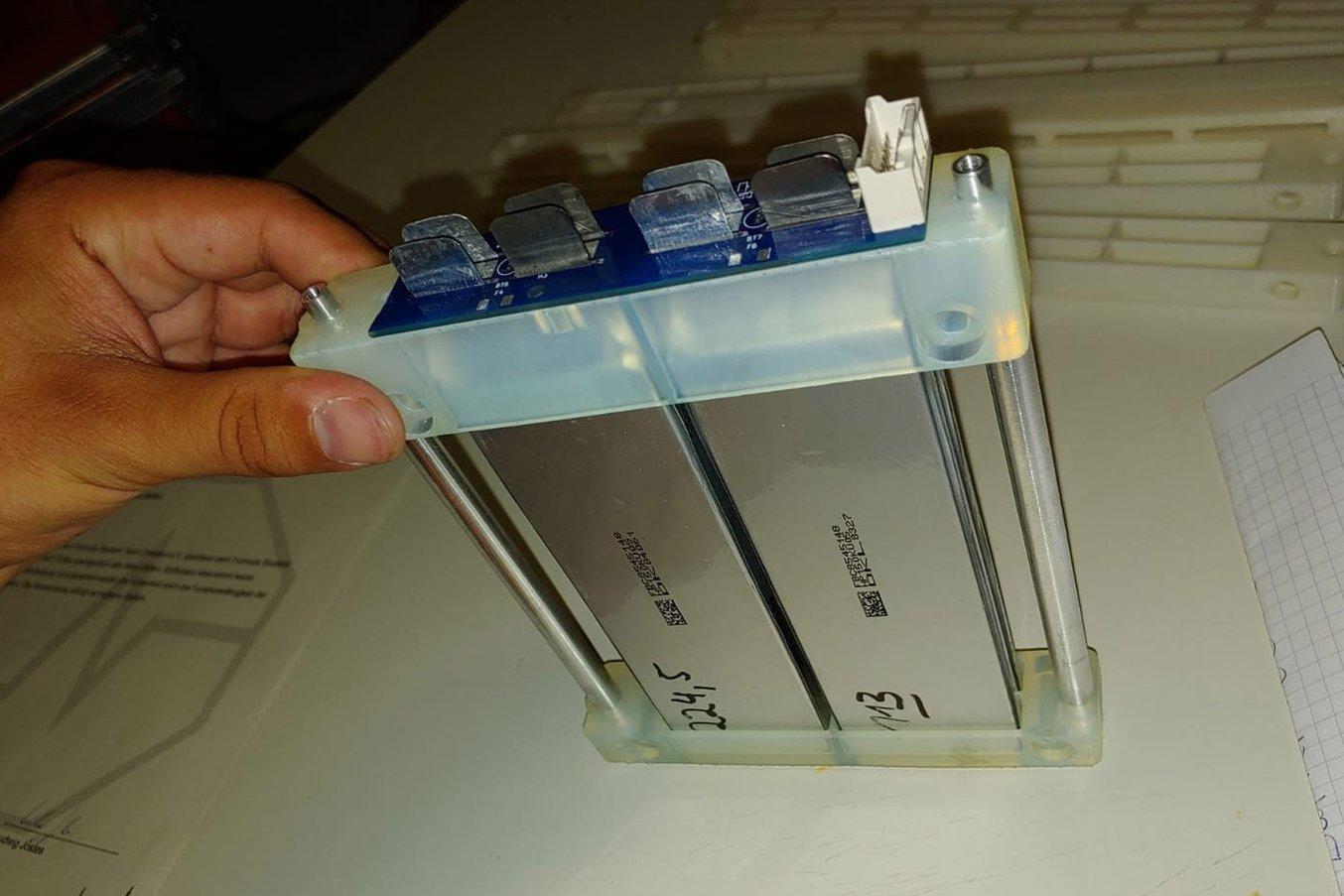
Auch die Prototypen der Halterungen der Batteriezellen für den elektrischen Rennwagen wurden mithilfe von 3D-Druck erstellt.
Fertigstellung der Wagen für die Rennsaison

Das Team befindet sich derzeit noch immer in der Entwicklung der drei Rennwagen, somit wachsen die Anwendungsfälle des 3D-Drucks unweigerlich noch weiter.
Eines der ehrgeizigsten Zukunftsprojekte ist die Herstellung eines Lufteinlasses aus Kohlenstofffaser. Das ist ein größeres Teil, bei dem die Form aus mehreren 3D-Drucken zusammengesetzt wird, bevor es an die Handlaminierung geht.
Die drei Rennwagen sollten es im Frühjahr noch zu Tests auf die Strecke schaffen. Werner, Hilken und das Team hoffen darauf, dass die Rennsaison starten kann, sobald die Beschränkungen im Rahmen von COVID-19 aufgehoben werden.