Vertiball erstellt verlässliche Prototypen, die spritzgegossenen Teilen gleichen
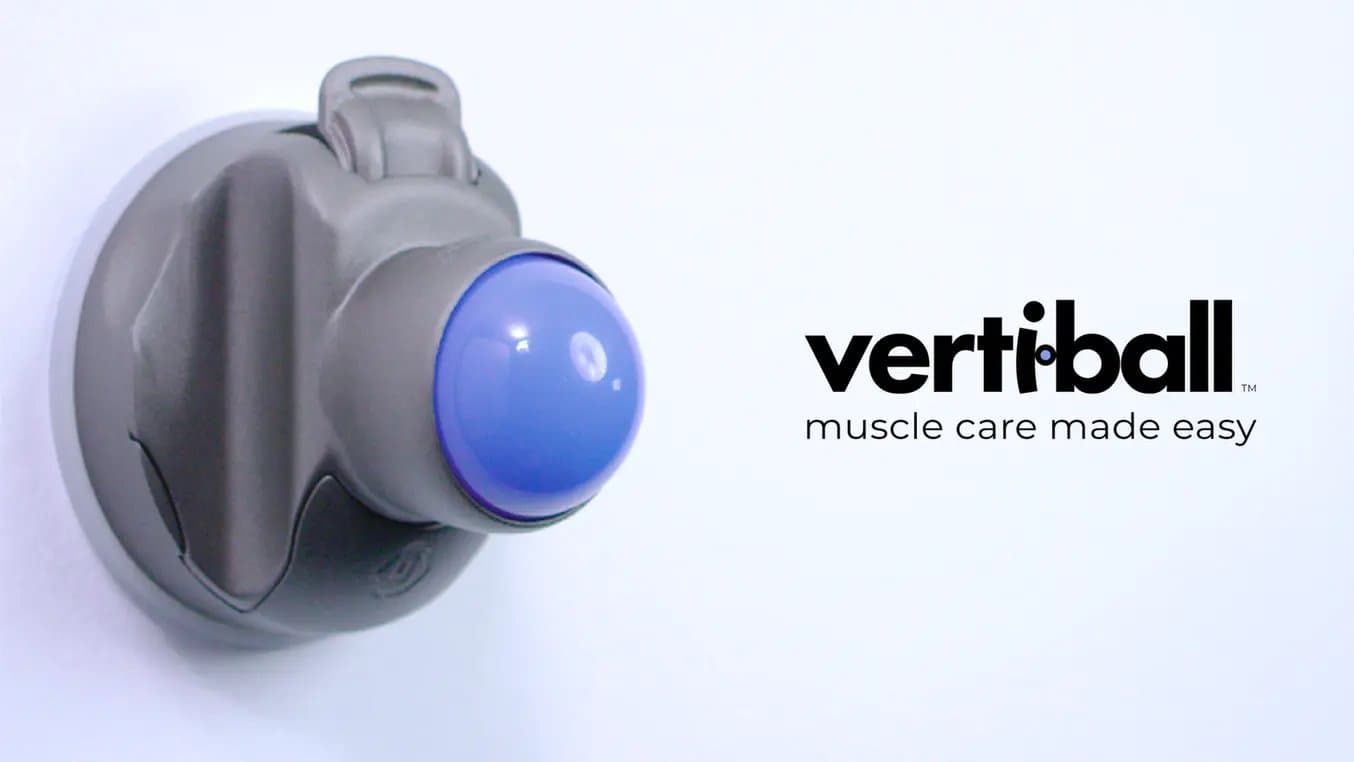
Curtis Kennedy, Gründer und Geschäftsführer von Vertiball, machte es sich zur Mission, neue Behandlungswege für Muskel- und Rückenschmerzen zu etablieren. Da er auch selbst schon mit Rückenschmerzen zu kämpfen hatte, probierte er zahlreiche von Ärzten empfohlene Heimtherapien aus ― darunter auch die gezielte Behandlung der Schmerzbereiche mit einem Tennisball. Für Curtis war die Massage eines bestimmten Rückenbereichs, während man auf einem Tennisball liegt, eine nur schwer zu meisternde Methode. Und so geht es auch vielen anderen Menschen, die ihre Schmerzen lindern oder etwaigen Verletzungen vorbeugen möchten.
Und so dachte sich Curtis eine Möglichkeit aus, einen Ball an einer senkrechten Fläche zu befestigen, damit man als Nutzer die betroffene Stelle exakter, leichter und besser massieren kann. Die Schlüsselinnovation des Vertiballs ist das patentierte mobile Befestigungssystem mit einem Saugnapf in Industriestärke, der sich an glatten, porenfreien Flächen befestigen lässt, wie z. B. an gestrichenen Gipswänden, an Metall oder auch an Holz. Die Vorderseite des Geräts enthält einen sich frei drehenden Massageball, der am Basismechanismus befestigt ist. Das Gerät ist zudem klein und tragbar, sodass man es als Nutzer vom Fitness-Studio mit nach Hause ins Wohnzimmer nehmen kann.
„Ich bin mir sicher, dass der Vertiball die Behandlungsstandards bei Rücken- und Muskelbeschwerden verändern wird, damit seine Nutzer ihren Schmerz in den Griff bekommen und sich selbst die Linderung verschaffen, die sie brauchen.“
Curtis Kennedy, CEO von Vertiball
Derzeit führen die Ingenieure bei Vertiball all ihre Produktkonzepte und all ihre CAD-Arbeit in Autodesk Fusion 360 durch. Die entsprechenden Prototypen erstellen und validieren sie dann mit ihrem Stereolithografie-3D-Drucker (SLA) Form 3. Jedoch war es ein langes Abenteuer aus Versuch und Irrtum, bis man schließlich bei diesem Prototypenentwicklungsprozess landete.
Einen zuverlässigen SLA-Arbeitsablauf finden
Curtis begann mit dem Design des Vertiball, als er noch an der University of New Brunswick studierte. Dabei nutzte er die am Campus verfügbaren Werkzeuge. Seine ersten Prototypen erstellte er mit Schmelzschichtungsdruckern (FDM). Als Curtis jedoch glaubte, beim fertigen Design angekommen zu sein, ließen sich seine bestellten Spritzgussteile nicht richtig zusammenbauen. Er fand heraus, dass wichtige Komponenten seines Prototypen aufgrund der Schrumpfung beim FDM-Druckverfahren ungenau war.
Da es ein Endverwendungsprodukt ist, ist das Design des Vertiball in Wahrheit sehr anspruchsvoll. Das Gerät ist für die tägliche Verwendung gedacht, deshalb muss der Verriegelungsmechanismus Hunderten oder Tausenden von Einsätzen standhalten. Und darüber hinaus enthält das Produkt Teile aus spritzgegossenem Kunststoff, die mit Metallkomponenten verbunden werden. Die Vorder- und Rückseite müssen ineinander gleiten, ohne zu reißen, und der Ball muss sich bei äußerst geringer Reibung frei drehen können. Aus den genannten Gründen entschied sich das Team bei den letztendlichen Gussteilen für Polycaprolactam (PA 6), ein robustes, reibungsarmes Material.
Für Curtis war klar, dass er hochpräzise Prototypen drucken musste, mit der Präzision und der Oberflächengüte der angestrebten spritzgegossenen Teile. Sein erster Schritt war, bei Formlabs einen individualisierten Probedruck aus Durable Resin anzufordern, mit dem er das veränderte Design prüfte. Mit seinem SLA-Druckteil in der Hand schoss er sich auf das fertige Design ein, welches er dann an den Spritzgussdienstleister schickte. Später investierte sein Team dann in einen eigenen Form 3.
„Der Form 3 ist ein entscheidender Bestandteil unseres Arbeitsablaufs, da er der einzige unserer 3D-Drucker mit der benötigten Maßgenauigkeit ist, um neue Prototypen in Spritzgussqualität für unsere Funktionstests anzufertigen.“
Curtis Kennedy
Auch bei ihrem CAD-Programm haben Curtis und sein Team einen ähnlichen Prozess durchgemacht. Am Ende sind sie dann aber bei einem CAD-Paket gelandet, mit dem sich alle Designer anfreunden konnten. Curtis schildert: „Nachdem wir eine Reihe anderer CAD-Programme ausprobiert hatten, erwies sich Fusion 360 als am besten für unsere Zwecke geeignet. Die Benutzeroberfläche ergibt einfach Sinn und ist intuitiv. Und die Arbeit damit ist verglichen mit anderen 3D-Modellierungsprogrammen um ein Vielfaches leichter.“
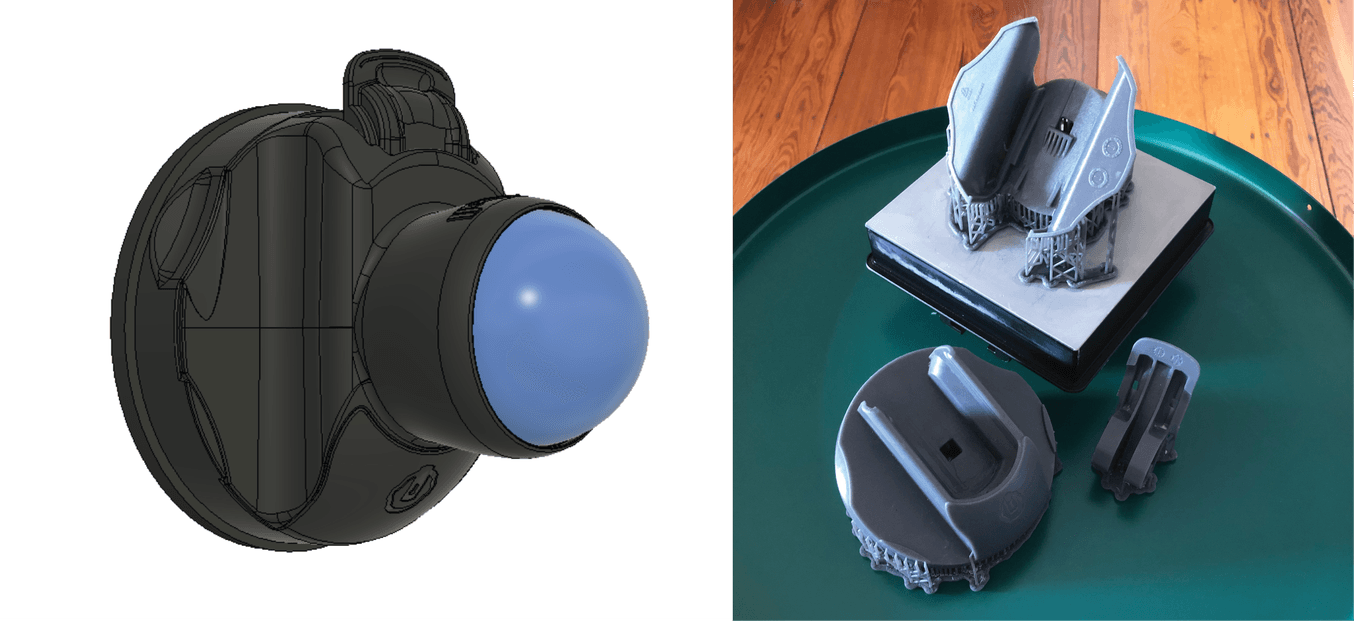
Das Vertiball-Design in Fusion 360 und als Druck aus dem Form 3.
Mit Fusion 360 können sich die Designer bei Vertiball auch ein Bild davon machen, wie sich ihr Produkt unter realistischen Bedingungen verhält. Dazu nutzen Sie die Simulationsumgebung von Fusion 360 für Belastungstests. Sie analysieren die Krafteinwirkung auf bestimmte Punkte und optimieren dann alle Bereiche des Modells, die sich noch nicht ihren Vorstellungen entsprechend verhalten. Obgleich sich also ein Großteil der iterativen Tests in einer Simulation abspielt, hält das Team handfeste Prototypen weiterhin für unabdingbar. „Ein neues Design kann am Computer fantastisch aussehen, aber ohne einen Test ist das nichts wert. Erst validieren wir die Funktionalität des Designs durch Simulation in der Theorie und dann gehen wir zur Prototypenfertigung mit dem Form 3 über.“
Vertiballs Vorzeigeprodukt wurde 2019 erfolgreich über Kickstarter finanziert, wobei das Kapitalziel fast um das Achtfache überschritten wurde. Das Einzelhandelsprodukt sammelt immer noch fleißig lobende Bewertungen von Physiotherapeuten und Profisportlern wie z. B. den NFL-Spielern CeeDee Lamb und Minkah Fitzpatrick. Curtis und sein Team arbeiten auch fleißig weiter an neuen, innovativen Muskelentspannungsprodukten ― ganz nach dem Motto ihres Unternehmens: „If we can feel our best, we can be our best.“ (Frei übersetzt: Nur wer sich gut fühlt, kann auch alles geben.)
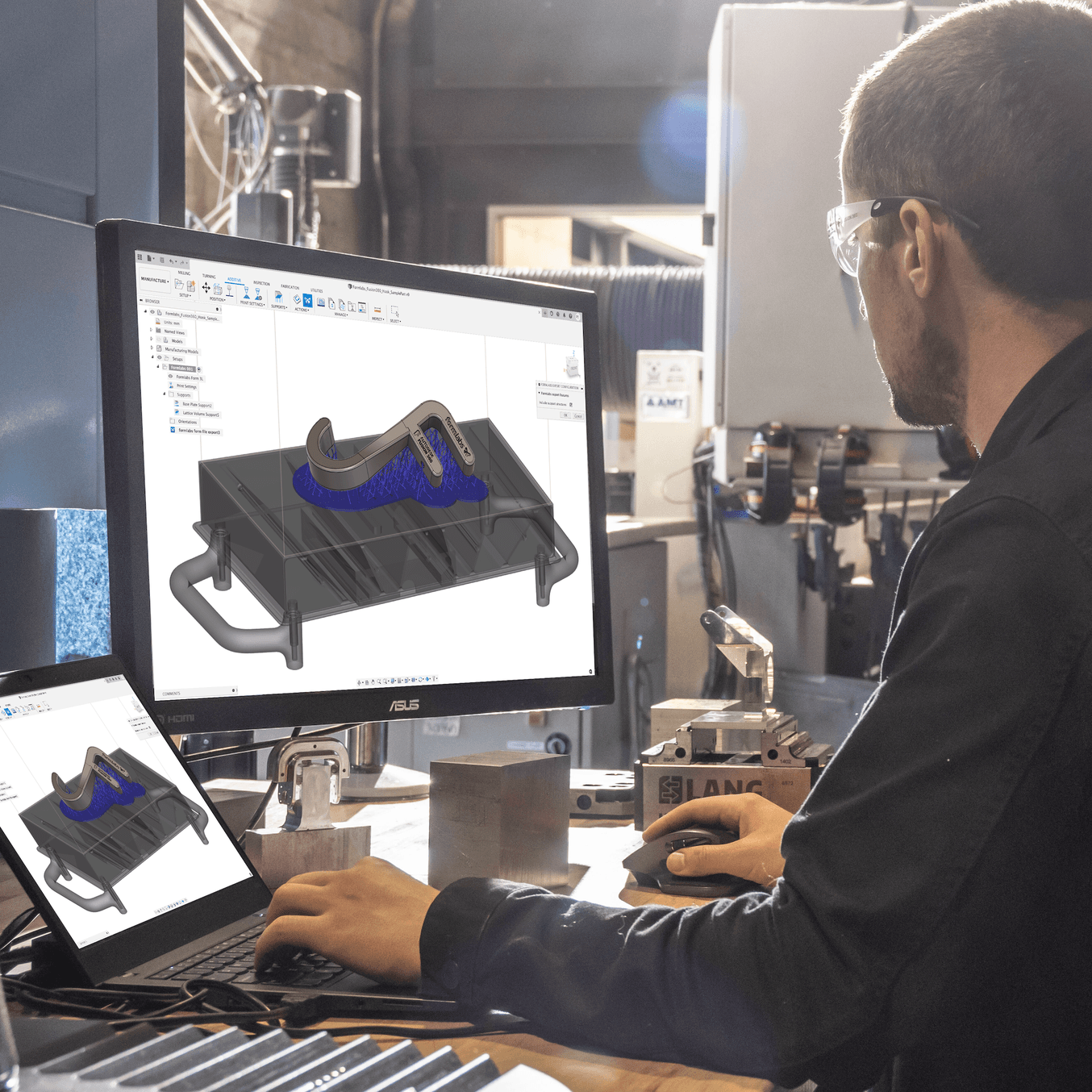
Integration von Formlabs und Fusion 360
Formlabs und Autodesk Fusion 360 arbeiten zusammen, um Ihren digitalen Arbeitsablauf zu optimieren ― mit einer neuen CAD-Software für 3D-Druck-Integration. Besuchen Sie unseren Integration Hub, um mehr über die neuesten SLA-Funktionen von Fusion 360 zu erfahren, weitere Geschichten unserer Nutzer zu lesen und unseren Design-Leitfaden herunterzuladen.