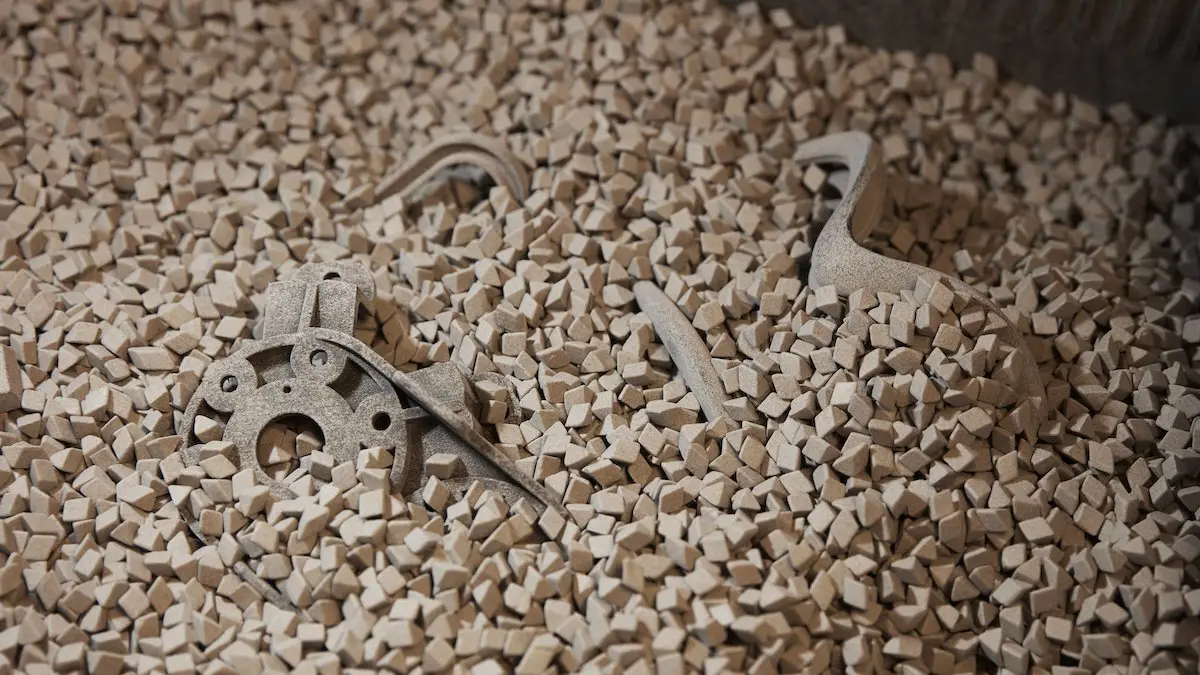
Das Vibrationsgleitschleifen ist eine etablierte Methode zur Steigerung der Oberflächenhärte und Glätte verschiedener Materialien. Traditionell wird es bei Metallteilen angewandt, um diese nach dem Zerspanen oder Pressen zu entgraten, doch viele Hersteller nutzen das Vibrationsgleitschleifen heute auch als wichtigen Nachbearbeitungsschritt bei 3D-gedruckten Teilen.
Gerade bei Teilen, die mit SLS-3D-Druck (selektivem Lasersintern) hergestellt wurden und oft eine leicht körnige Oberfläche aufweisen, kann das Vibrationsgleitschleifen dabei helfen, Teile für die Endverwendung oder die reibungslose Integration in Funktionsbaugruppen vorzubereiten.
In diesem Leitfaden erhalten sie eine Einführung in das Vibrationsgleitschleifen von SLS-3D-gedruckten Teilen. Sehen Sie sich unser Webinar an, um die vollständigen Ergebnisse unseres Vergleichs von Gleitschleifanlagen und unsere Testergebnisse kennenzulernen sowie tiefer in den Arbeitsprozess einzusteigen.
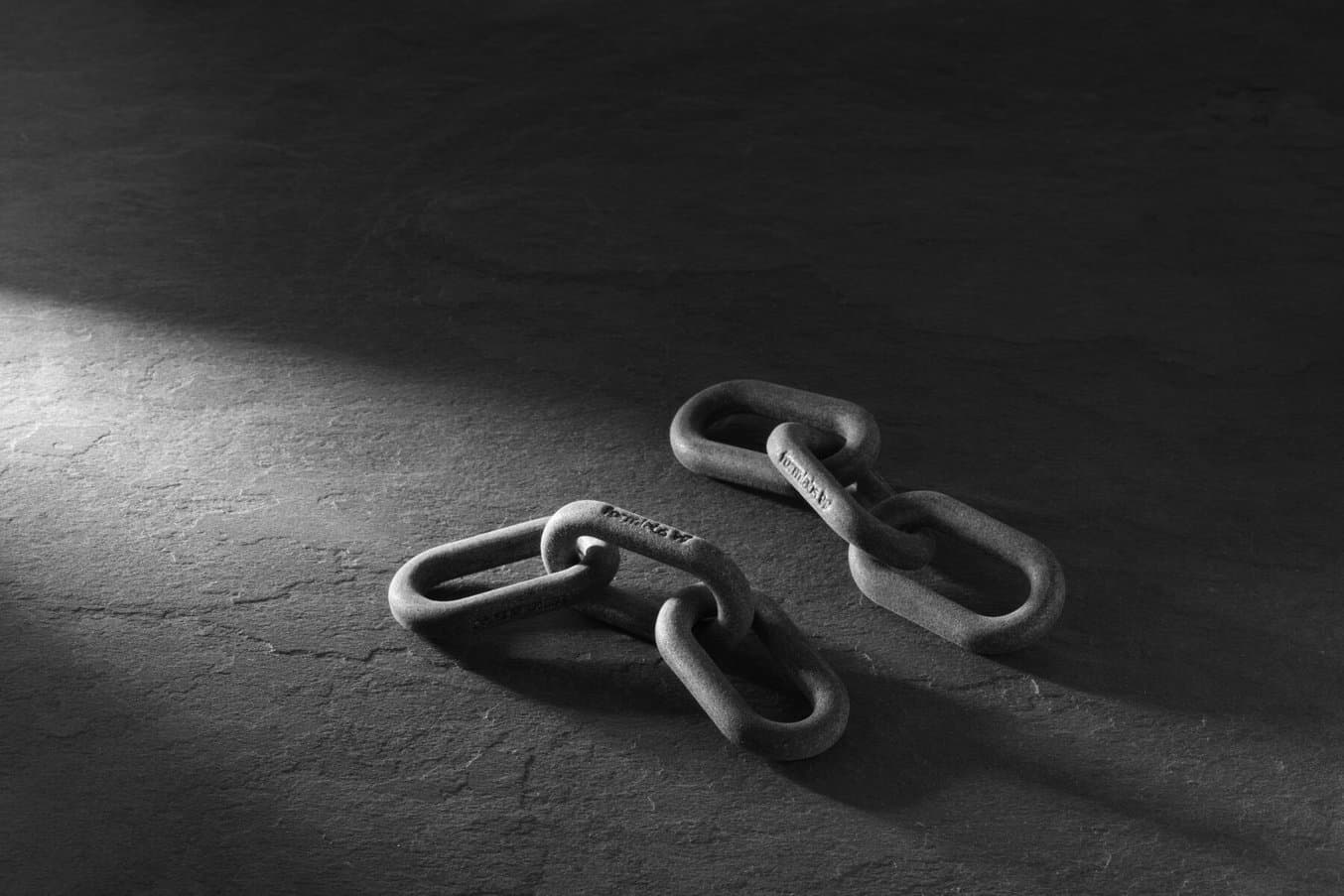
Vibrationsgleitschleifen von Teilen aus dem SLS-3D-Drucker
In diesem Bericht gehen wir darauf ein, wie Sie die richtigen Geräte und Materialien für Ihren Arbeitsablauf auswählen, und erläutern bewährte Praktiken und Methoden, mit denen Sie die besten Ergebnisse erzielen.
Ablauf und Vorteile des Vibrationsgleitschleifens
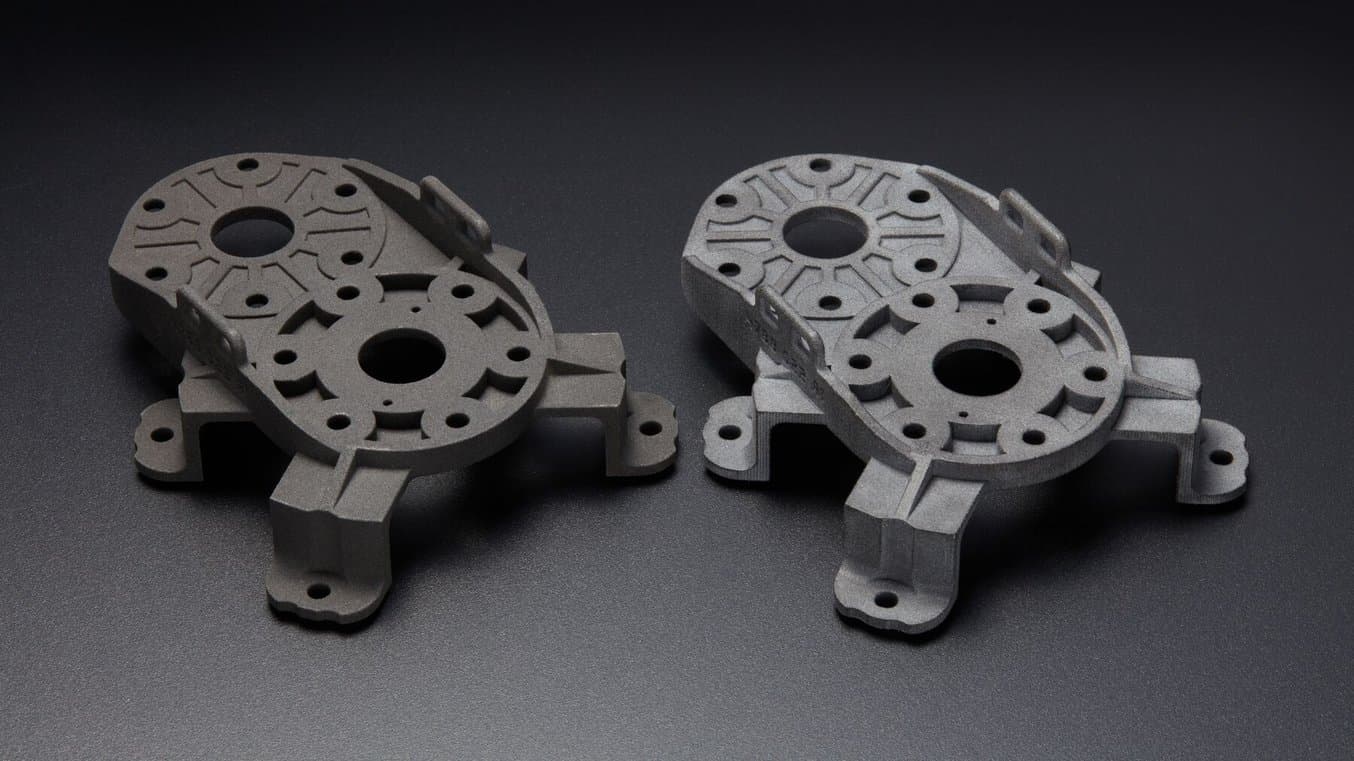
Unser Testteil vor und nach dem Vibrationsgleitschleifen. Das geschliffene Teil ist hellgrau und erscheint matt.
In einer Vibrationsgleitschleifanlage wird ein Granulat kleiner Schleifkörper (typischerweise Metall, Keramik, Kunststoff oder organische Materialien wie Walnussschalen) zusammen mit den Werkstücken in Bewegung gebracht, sodass die Oberfläche der Teile durch die Reibung geglättet und ihre Härte gesteigert wird. Gleitschleifanlagen finden aufgrund ihrer praktischen Größe, des erschwinglichen Preises und ihrer zahlreichen Vorteile ohne zusätzlichen Arbeitsaufwand weitläufig Anwendung.
Das Vibrationsgleitschleifen bietet zwei wesentliche Vorteile für den 3D-Druck: gesteigerte Funktionalität und verbesserte Ästhetik. Durch die Verringerung der Oberflächenrauheit können bewegliche Bauteile mit einem geringeren Reibungskoeffizienten arbeiten, weshalb das Vibrationsgleitschleifen die ideale Nachbearbeitungstechnik für Anwendungsfälle wie 3D-gedruckte Scharniere, Schalter, funktionale Klemmen und sonstige Bauteile ist, die entweder beweglich sind oder zu einer beweglichen Baugruppe gehören. Die verbesserte Oberflächentextur vermindert zudem die Porosität, sodass Teile nach dem Gleitschleifen eine höhere Beständigkeit gegenüber Flüssigkeitsaufnahme aufweisen.
Die ästhetischen Vorzüge des Vibrationsgleitschleifens umfassen in erster Linie die verbesserte Oberflächentextur und das reinere Erscheinungsbild, doch das Gleitschleifen sorgt auch für ein gleichmäßigeres Substrat zum Auftragen zusätzlicher Beschichtungen wie etwa Acrylfarbe oder Cerakote.
Bei allen 3D-Druckteilen, die für die Endverwendung dienen, zu funktionalen Baugruppen gehören oder als Konzeptnachweis zur Veranschaulichung dienen, ist das Vibrationsgleitschleifen eine einfache Lösung, um die Oberflächenhärte und Glätte stark zu verbessern.
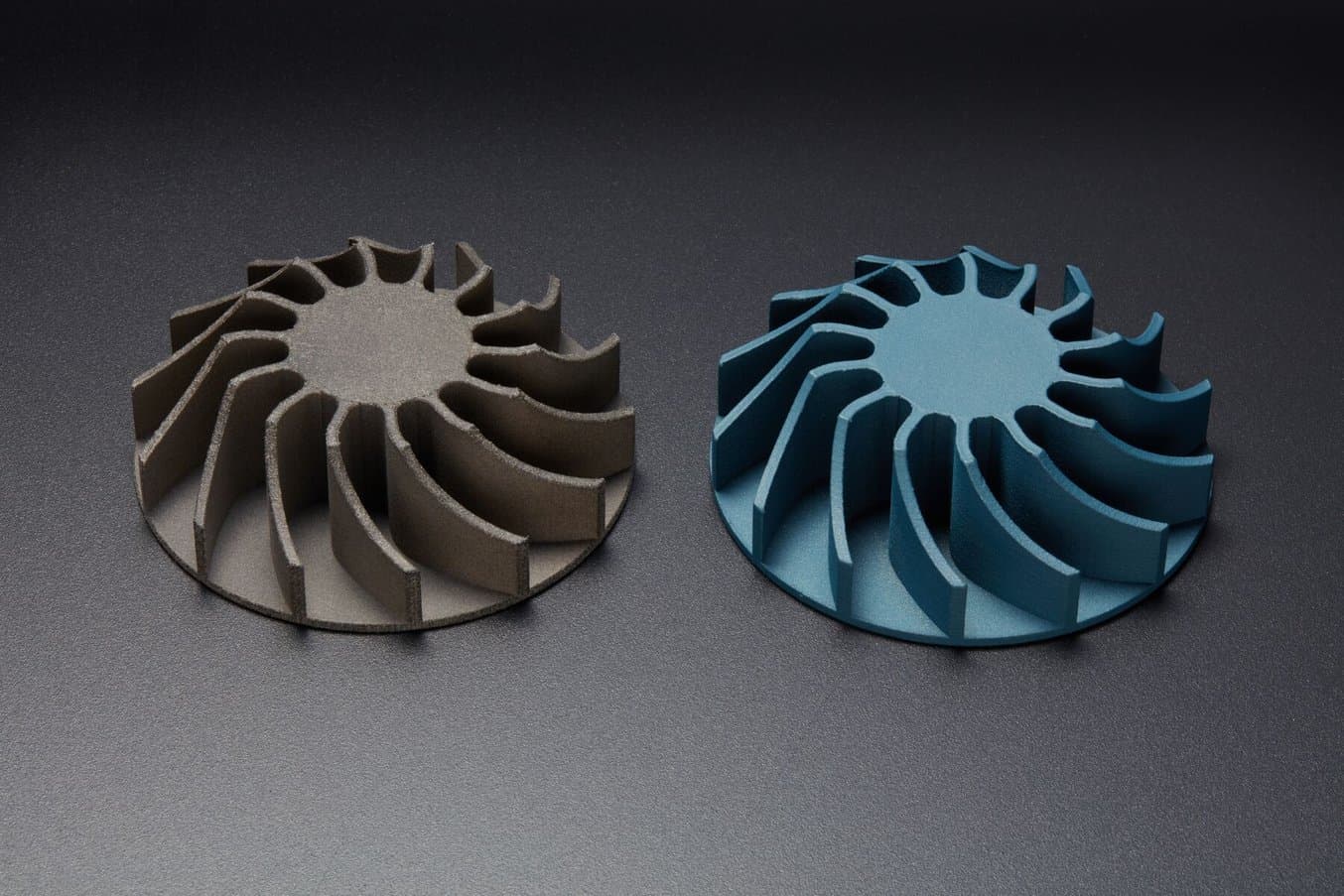
Das Gleitschleifen sorgt für ein gleichmäßigeres Substrat zum Auftragen zusätzlicher Beschichtungen wie etwa Acrylfarbe oder Keramikbeschichtung von Cerakote.
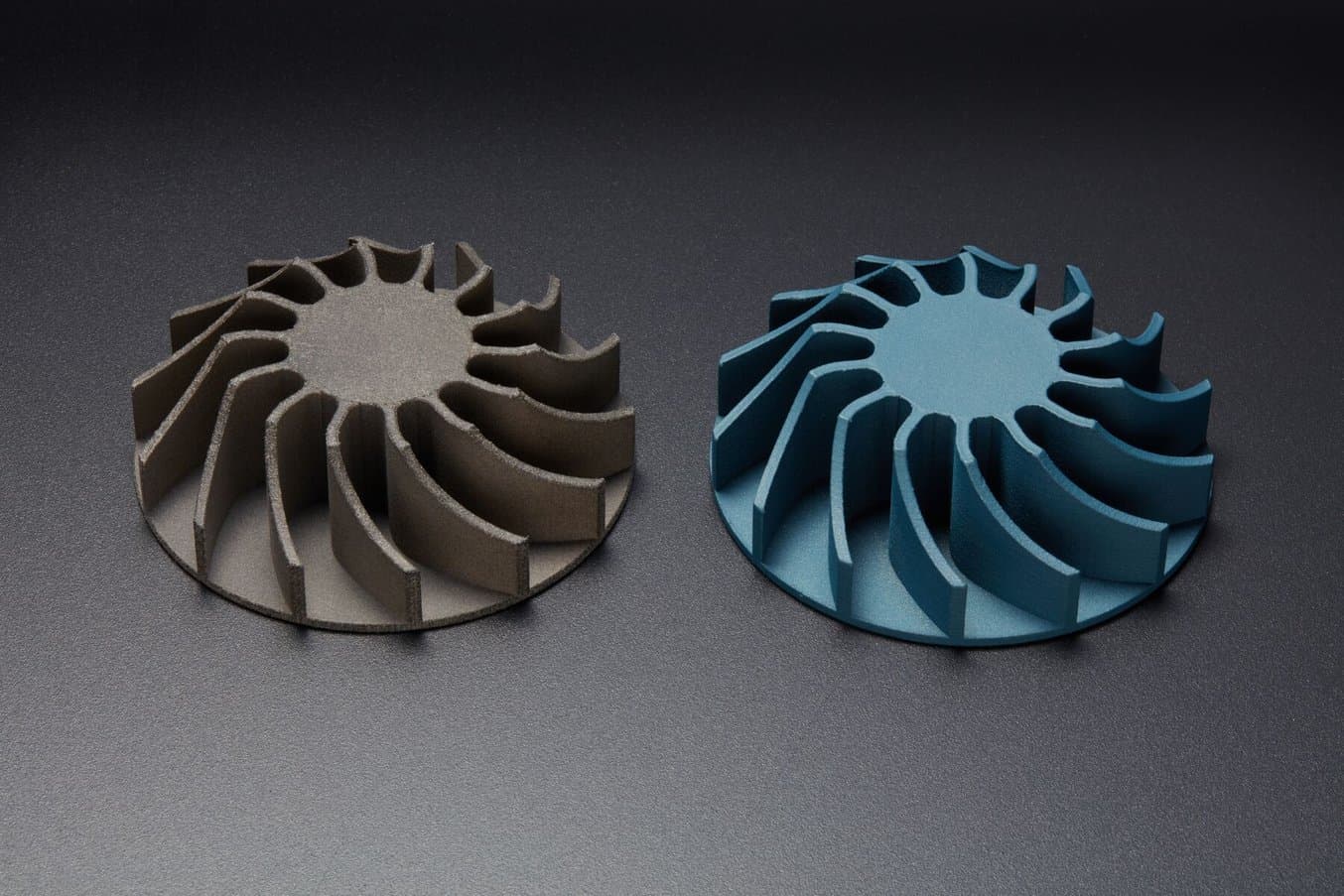
Fortgeschrittene Nachbearbeitungstechniken für den 3D-Druck
In diesem Webinar erfahren Sie alles Wissenswerte zu mehr als 11 fortgeschrittenen Nachbearbeitungstechniken für den 3D-Druck, unter anderem Cerakote-Beschichtung, Galvanisierung und chemische Dampfglättung.
Die Wahl eines Vibrationsgleitschleifers für 3D-gedruckte Teile
Vibrationsgleitschleifanlagen für 3D-gedruckte Teile lassen sich in zwei wesentliche Kategorien einteilen: industrielle und kommerzielle Anlagen. Industrieanlagen haben eine höhere Kapazität und einen höheren Energiebedarf und sind ab etwa 5000 € erhältlich. Industrielle Gleitschleifer eignen sich für Stückzahlen auf Produktionsniveau, also beispielsweise für Mass Customization oder Übergangsfertigung.
Viele kleinere Gleitschleifanlagen erzielen vergleichbare Endergebnisse wie industrielle Vibrationsgleitschleifer, verfügen jedoch über geringere Kapazitäten und erfordern für dasselbe Ergebnis längere Zykluszeiten – Werkstücke müssen in kleineren Anlagen beinahe 72 Stunden lang geschliffen werden, während industrielle Geräte nur sechs Stunden benötigen. Industrielle Gleitschleifanlagen verarbeiten problemlos mehrere Chargen von Teilen, sogar bei mittelgroßen bis großen Geometrien, sodass sie sich ideal für Unternehmen wie Fertigungsdienstleister oder großangelegte Fertigungsbetriebe eignen.
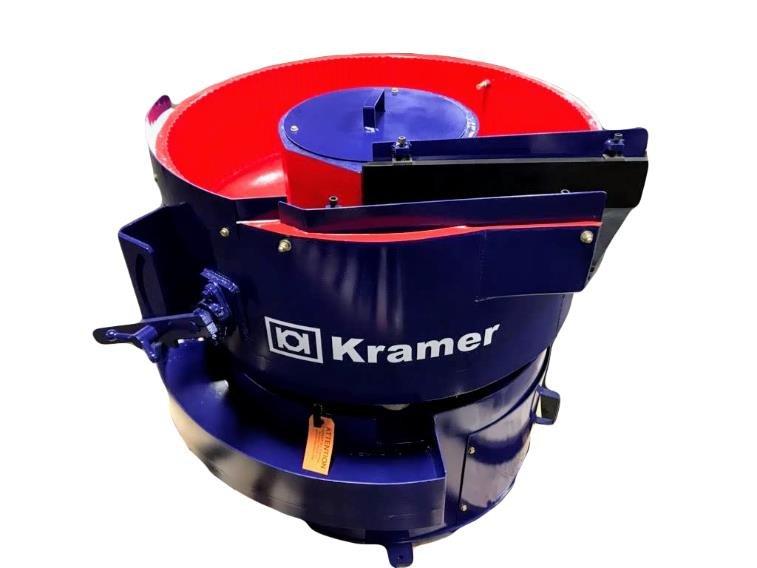
Industrielle Großserienproduktion
Beispiel: Rösler
Kosten: > 5000 €
Ideal für:
-
Hoher Durchsatz
-
Große Teile
-
Mehrere große Teile
-
Automatisierter Arbeitsablauf
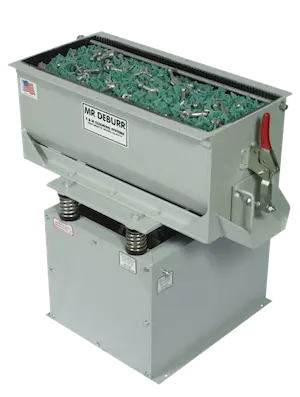
Mittleres Produktionsvolumen
Beispiel: CM Topline
Kosten: 1000–5000 €
Ideal für:
-
Große Teile
-
Chargen kleinerer Teile
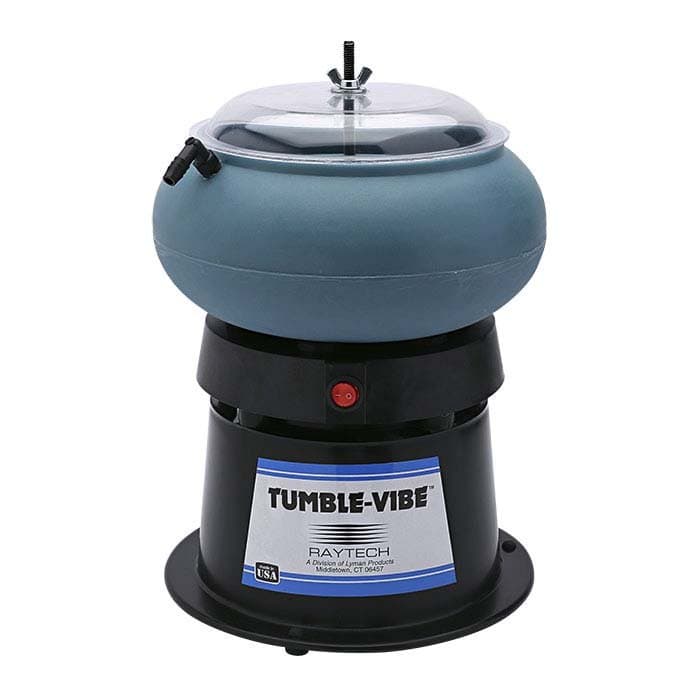
Einsteigerniveau, Kleinserien
Beispiel: Raytech, Tumble Vibe
Kosten: < 1000 €
Ideal für:
-
Einzelne mittelgroße Teile
-
Volle Konstruktionskammern kleinerer Teile
Die Wahl eines Schleifmittels und Compounds
Es gibt zahlreiche verschiedene Arten von Schleifkörpern, die beim Vibrationsgleitschleifen zum Einsatz kommen können, und die Wahl des Schleifmittels beeinflusst das Endergebnis maßgeblich. Typische Schleifmittel umfassen Edelstahl, Porzellan oder Silikat, Polyesterverbundstoffe oder Walnussschalen. Sie erzielen jeweils unterschiedliche Effekte, von aggressiver Glättung und Behebung der Oberflächenrauheit bis zu einer leichten Politur zu ästhetischen Zwecken.
Bei einigen Vibrationsgleitschleifprozessen, im sogenannten Nassverfahren, werden zusätzlich zum Schleifmittel auch Wasser oder chemische Zusatzstoffe (Compound genannt) eingefüllt. Die Flüssigkeit dient dazu, die durch die Reibung entstehende Hitze zu regulieren, und unterstützt das Entfernen von Verunreinigungen oder Oxiden von der Werkstückoberfläche. Compounds können jedoch teuer sein und Chemieabfälle verursachen, die dann sachgemäß entsorgt und verarbeitet werden müssen.
Media Shapes
When choosing media to be used in a vibratory tumbler, the size and shape of the individual pellets should be considered along with the type of material. Pellets come in large and small sizes and sharp or rounded shapes. Large pellets are used for rougher grinding, such as removing burrs or rust from metal parts. Smaller pellets are used for finer pieces, offer more polishing or burnishing effects, and can be used on a broader range of materials. Sharp pellets (triangles, wedges, and arrowheads) are ideal for finishing complex parts with edges, crevices, and channels, though they have a higher instance of chipping or flaking. Rounded pellets are ideal for lighter-touch polishing and burnishing, and very rarely chip or flake. Though they are slower to fully smooth surfaces, they are much more gentle and can be used for delicate parts.
Detergents
In some vibratory workflows, called ‘wet vibratory finishing,’ water or chemical detergents are added in with the pellets. The liquid helps temper the heat generated by the high friction and can help in removing contaminants or oxides on the surface of the part. Parts will appear cleaner and more polished than with a dry tumbling workflow. However, detergents can be expensive and generate chemical waste, which has to then be disposed of and treated properly. Metal, ceramics, or plastic media can be used in a wet workflow, but organic media such as walnut shells or corn cobs should not be.
Comparison Table: Tumbling Media
Typical Material | Kosten | Vorteile | Nachteile | Aggressiveness | |
---|---|---|---|---|---|
Metall | Hardened carbon and stainless steel | $$$ | Short Run Times Prolonged service life and superior wear-resistance Heavy-duty burnishing and polishing | Might damage parts | Hoch |
Keramik | Porcelain Aluminum oxide Silicone Carbide Silica | $$ | Heavy-duty burnishing and polishing Most commonly used media | Might damage parts Ceramic bits may flake off and get stuck in channels/negative features | Hoch |
Plastic | Polyester, urea, and formaldehyde | $ | Ideal for safely finishing threaded or fragile parts Creates soft, bright surfaces and edges Range of densities available for customization per application | Longer run times | Mittel |
Organisch | Walnut shells Corn cobs | $ | Can be used as a secondary vibratory step Can absorb oils and moisture | Longer run times May need to be used in a two-part process | Light to medium deburring |

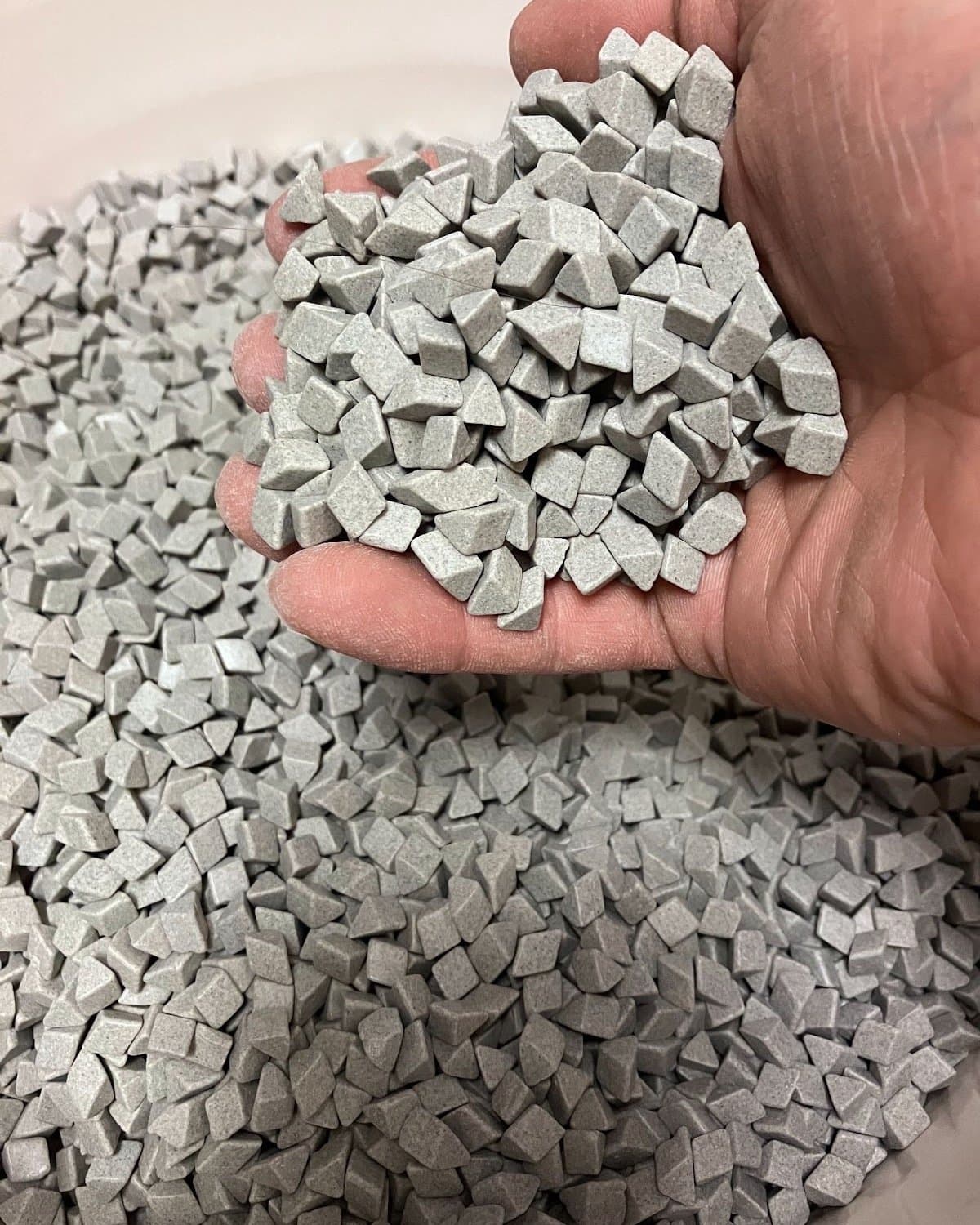
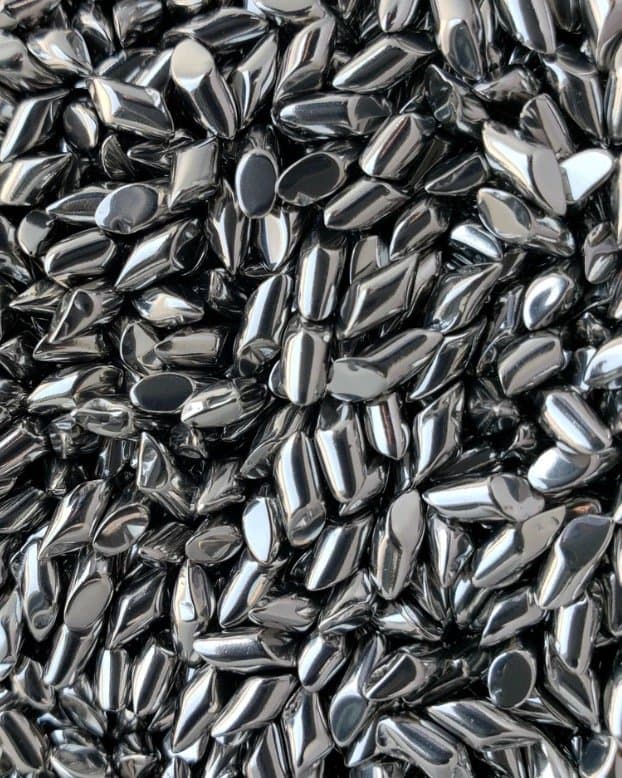
Von links nach rechts: Walnussschalen, Keramikschleifkörper und Stahlschleifkörper.
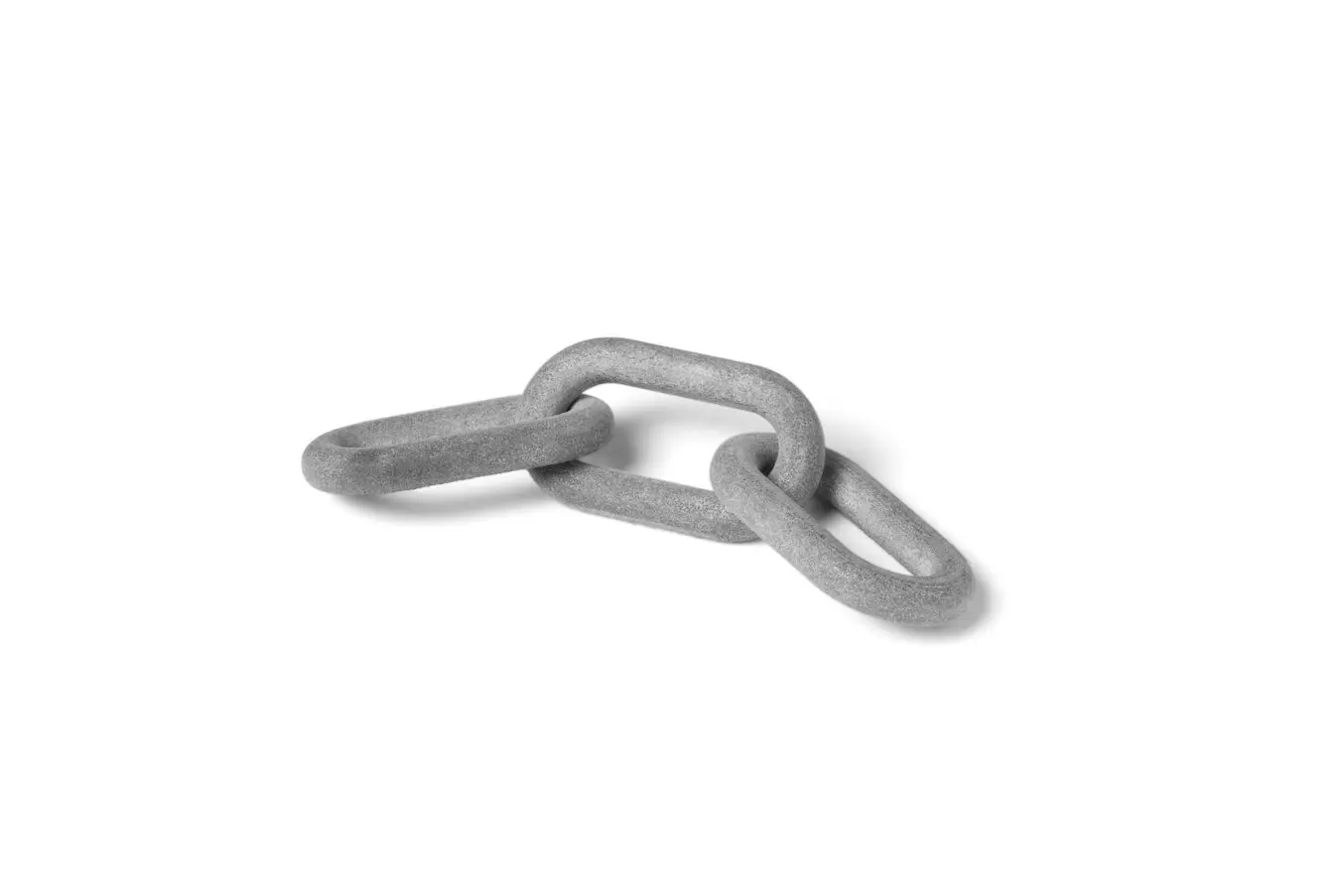
Kostenlosen gleitgeschliffenen Probedruck aus Nylon 11 CF Powder anfordern
Diese ineinandergreifende Kette wurde in einem Stück gedruckt und ihre Nachbearbeitung wäre mit manuellen Verfahren nahezu unmöglich. Das Teil wurde über Nacht in der Vibrationsgleitschleifanlage DB-300 geschliffen, wofür Keramik-Schleifmittel in Dreiecksform verwendet wurde. Die verbesserte Oberfläche eignet sich ideal für das Lackieren, Beschichten und Galvanisieren.
Anwendungen für gleitgeschliffene SLS-Teile
Viele Anwendungen des 3D-Drucks erfordern eine glatte Oberflächengüte und einen niedrigen Reibungskoeffizienten. Das Vibrationsgleitschleifen kann als Teil Ihres Arbeitsprozesses sowohl die Funktionalität als auch die Optik von Teilen für eine Vielzahl von Branchen und Umgebungen steigern.
Glatte, gleitgeschliffene SLS-Teile kommen insbesondere in folgenden Anwendungen zum Einsatz:
-
Endverbraucherteile: SLS-Drucker glänzen bei der Produktion kleinerer bis mittlerer Stückzahlen, und das Gleitschleifen ist eine unkomplizierte Möglichkeit, die Oberfläche der Teile chargenweise zu glätten.
-
Gesundheitswesen: Oberflächenrauheit ist beim 3D-Druck von Medizinprodukten, Modellen, Prothesen oder Orthesen ein großes Manko. In Kombination mit dem Gleitschleifverfahren liefern SLS-Drucker jedoch einen erheblichen Mehrwert für 3D-Druckprozesse in der Gesundheitsbranche.
-
Fertigungshilfsmittel: Mithilfe eines Vibrationsgleitschleifers lässt sich der Reibungskoeffizient verringern und die Oberflächenhärte steigern, was Teile robuster und langlebiger macht.
Vibratory Tumbling End-Use Goods
As 3D printing technology makes mass customization a reality, high-throughput 3D printing applications become more common. The Fuse Series ecosystem enables mid- to high-volume manufacturing of end-use goods that function like injection molded parts while still taking advantage of the design freedom of SLS technology.
Vibratory tumbling is a low-cost method to achieve a surface finish comparable to injection molding, without adding hours of labor or manual post-processing. Batching parts together in a larger tumbler keeps touchpoints low and results optimal. Tumbling also prepares parts for further coating, which can further elevate the functionality, finish, and color of SLS 3D printed parts.
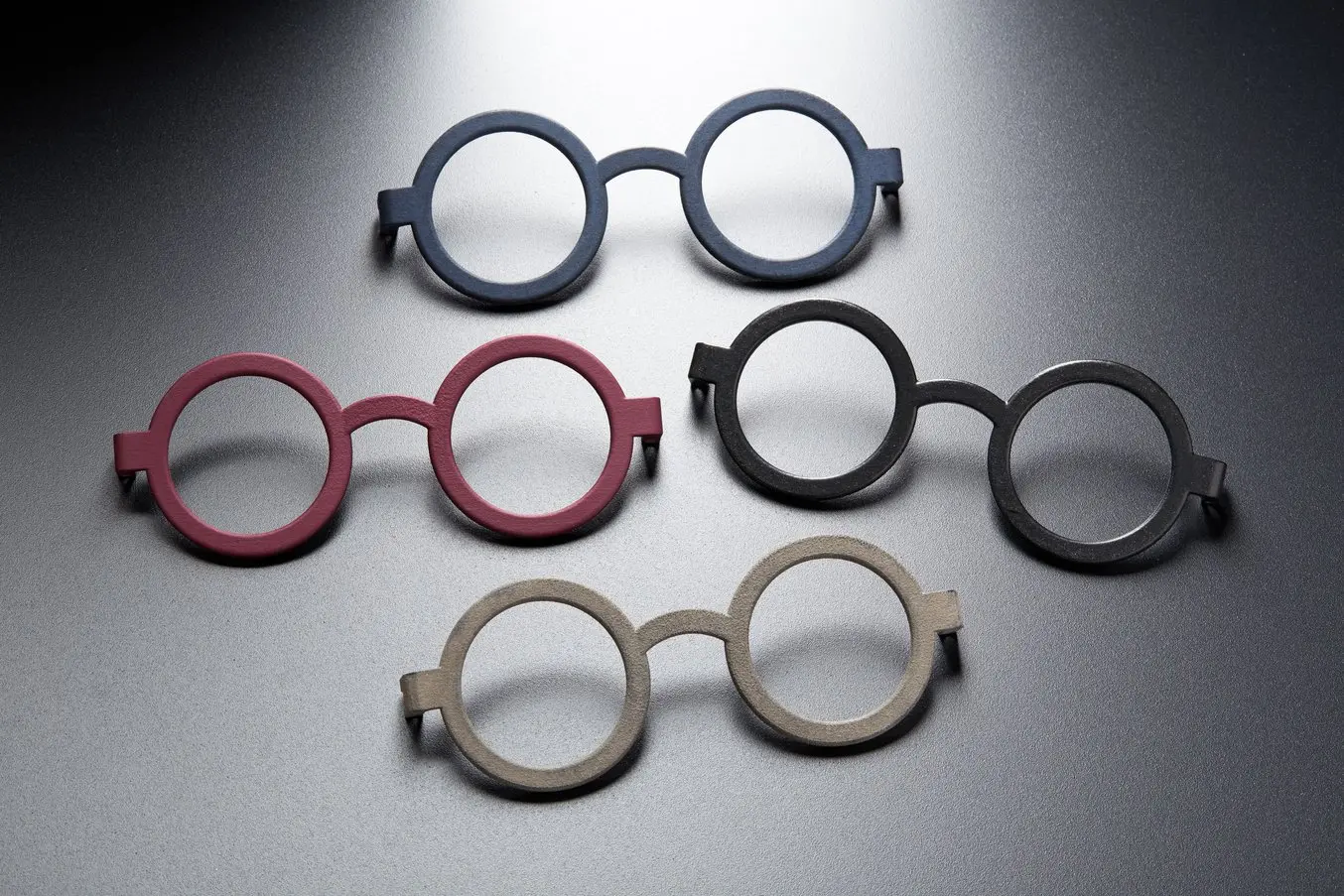
Vibratory tumbling is ideal for improving surface finish and preparing parts for further post-processing, such as dyeing, painting, or coating.
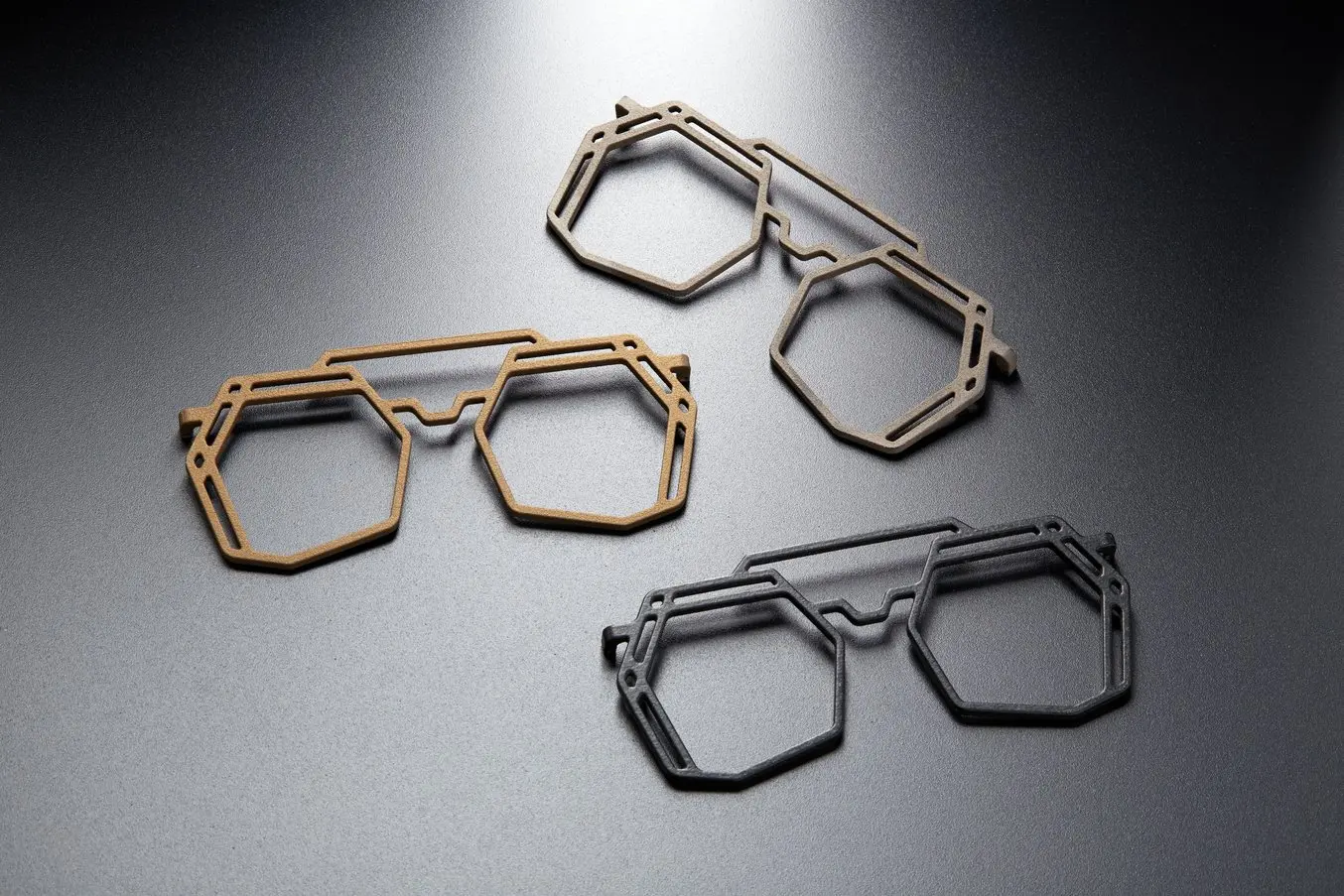
End-use eyewear frames are a perfect application for vibratory tumbling to have a major impact.
Vibratory Tumbling End-Use Goods
As 3D printing technology makes mass customization a reality, high-throughput 3D printing applications become more common. The Fuse Series ecosystem enables mid- to high-volume manufacturing of end-use goods that function like injection molded parts while still taking advantage of the design freedom of SLS technology.
Vibratory tumbling is a low-cost method to achieve a surface finish comparable to injection molding, without adding hours of labor or manual post-processing. Batching parts together in a larger tumbler keeps touchpoints low and results optimal. Tumbling also prepares parts for further coating, which can further elevate the functionality, finish, and color of SLS 3D printed parts.
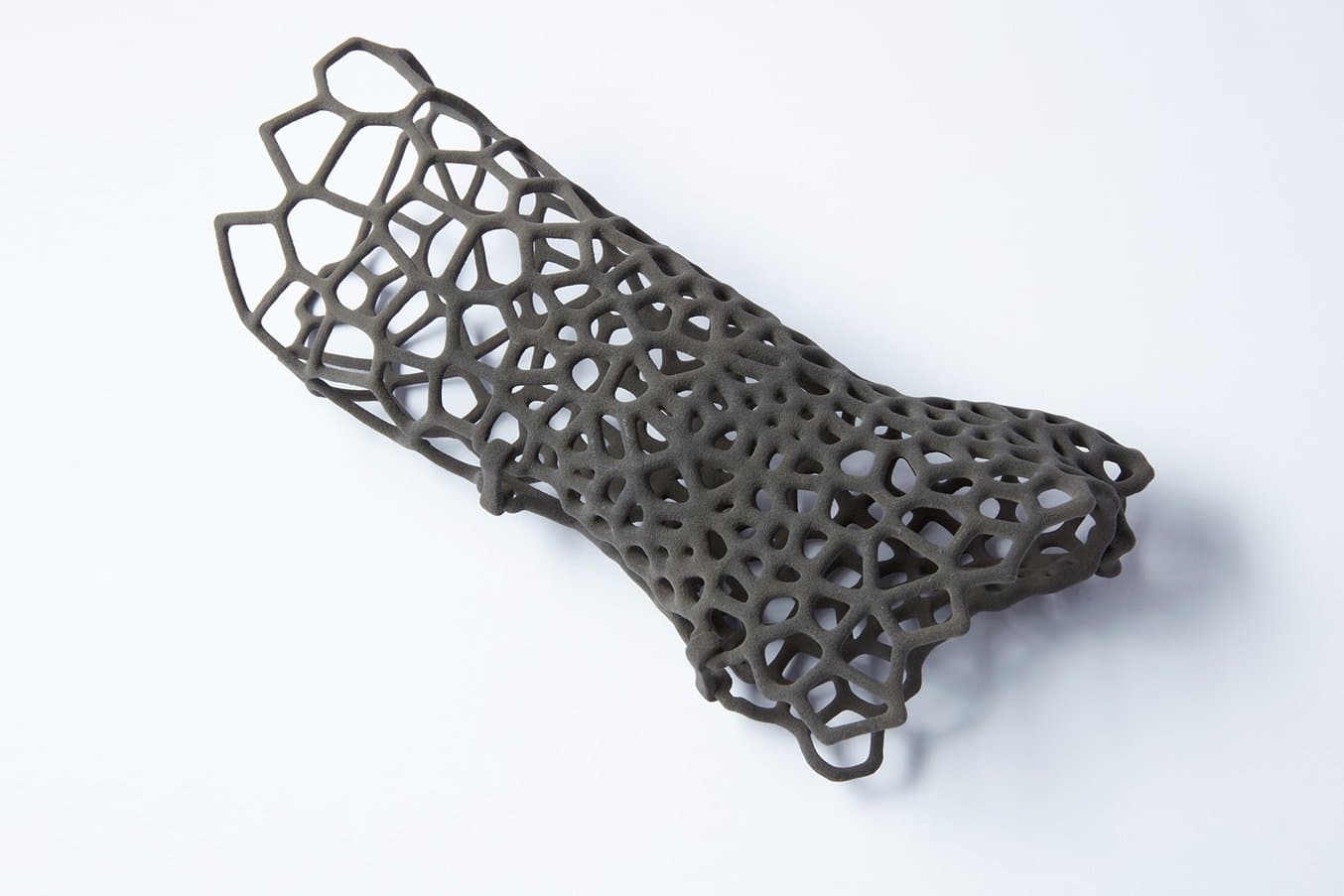
Vibratory tumbling is ideal for improving surface finish and preparing parts for further post-processing, such as dyeing, painting, or coating.
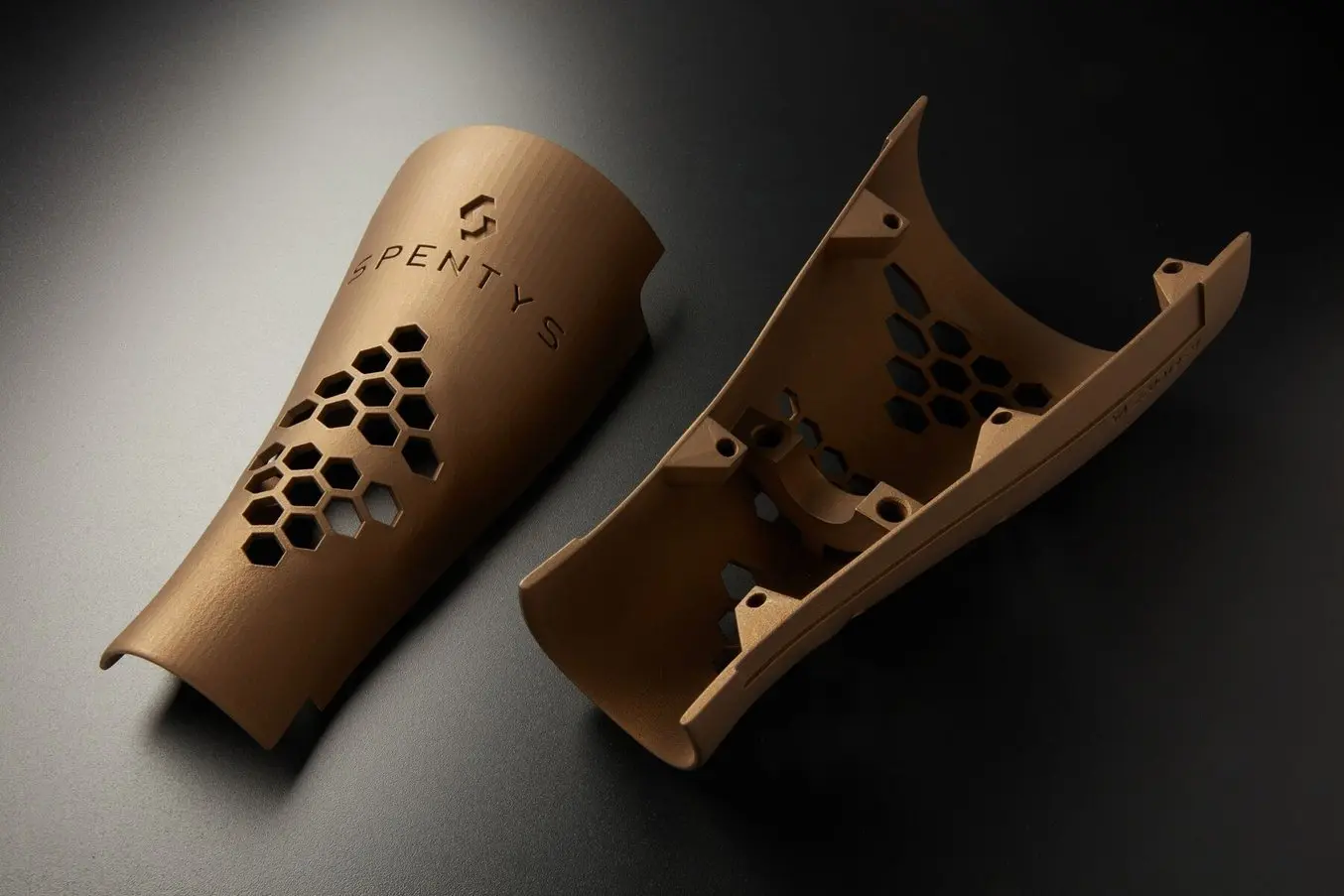
End-use eyewear frames are a perfect application for vibratory tumbling to have a major impact.
Vibratory Tumbling End-Use Goods
As 3D printing technology makes mass customization a reality, high-throughput 3D printing applications become more common. The Fuse Series ecosystem enables mid- to high-volume manufacturing of end-use goods that function like injection molded parts while still taking advantage of the design freedom of SLS technology.
Vibratory tumbling is a low-cost method to achieve a surface finish comparable to injection molding, without adding hours of labor or manual post-processing. Batching parts together in a larger tumbler keeps touchpoints low and results optimal. Tumbling also prepares parts for further coating, which can further elevate the functionality, finish, and color of SLS 3D printed parts.
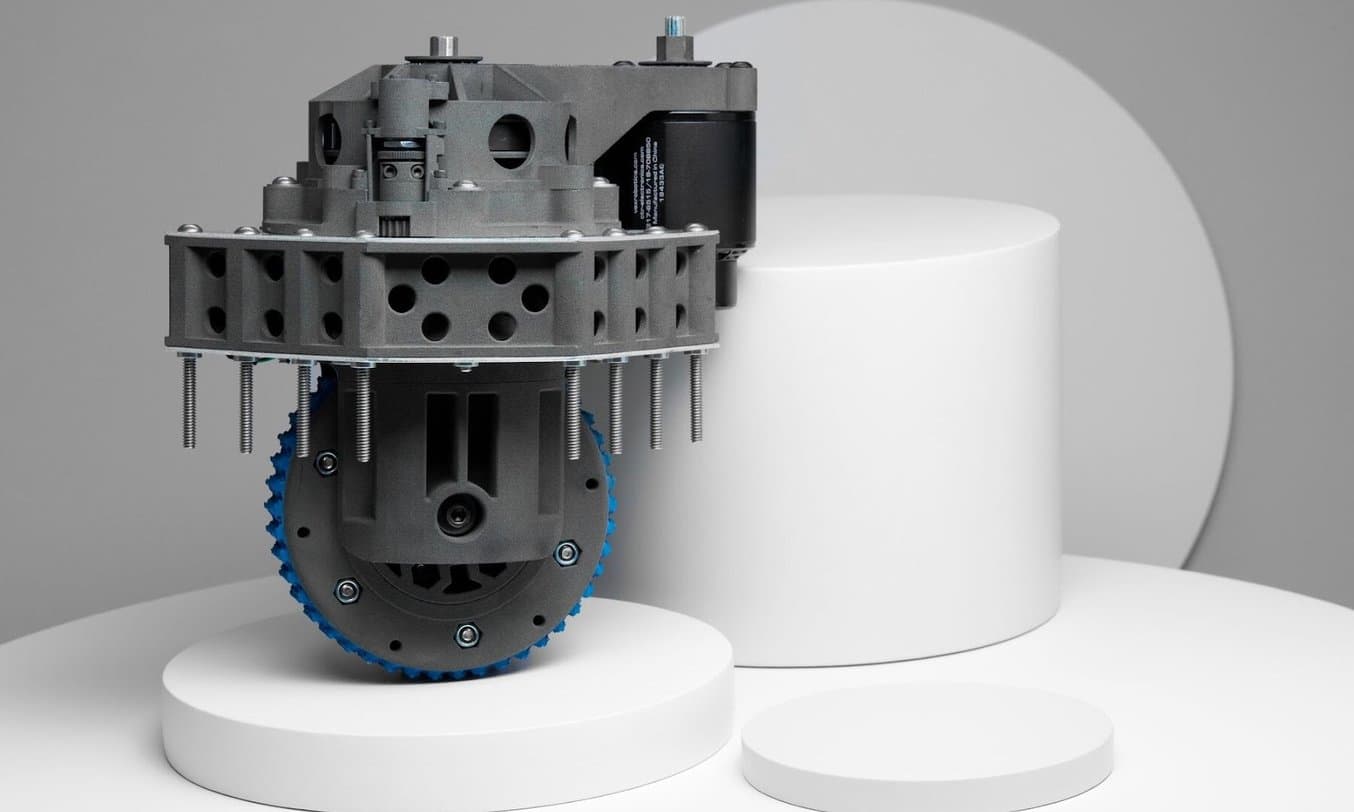
Das Vibrationsgleitschleifen verbessert die Haltbarkeit komplexer Baugruppen und Fertigungshilfen.
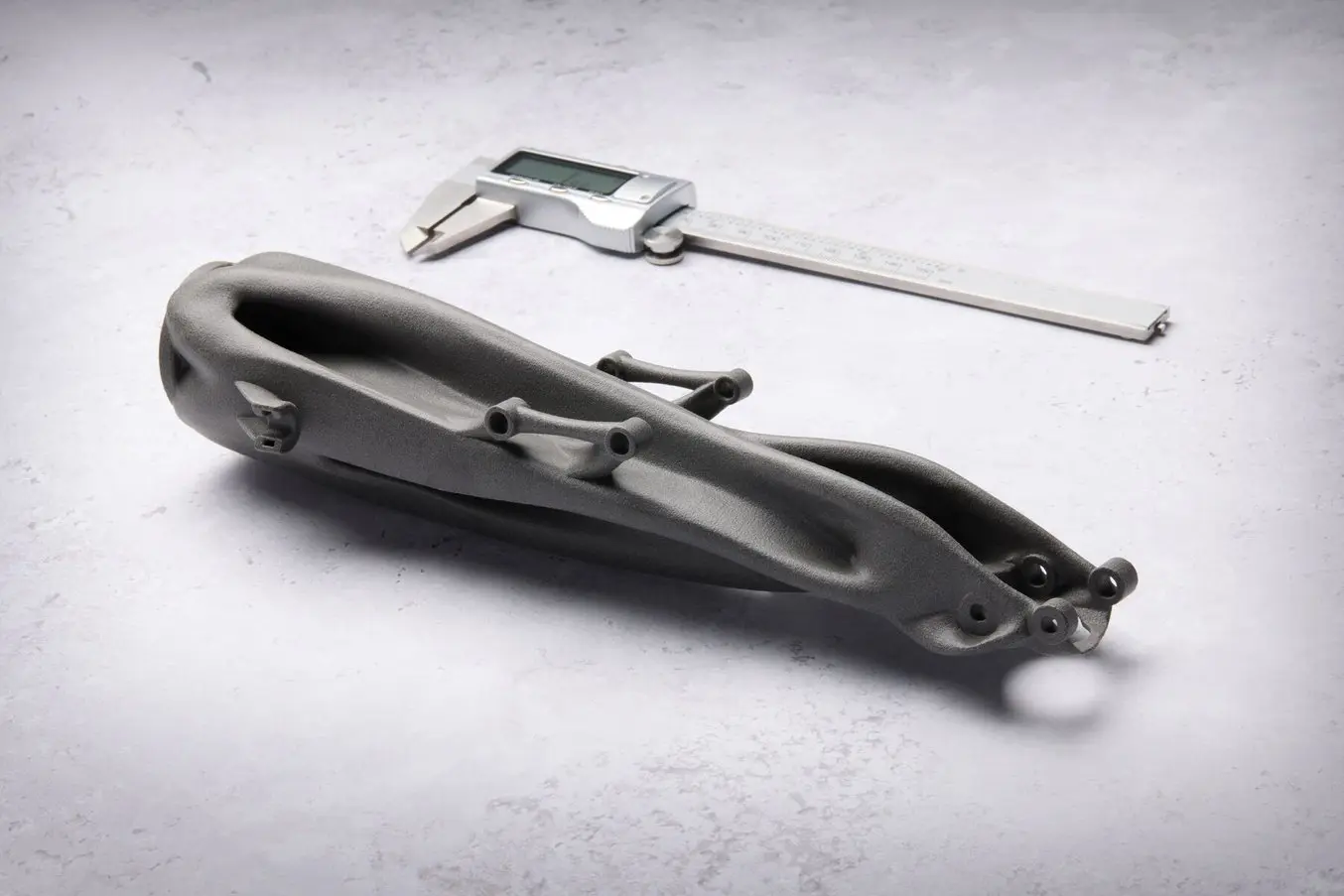
End-use eyewear frames are a perfect application for vibratory tumbling to have a major impact.
Tests und Ergebnisse
Formlabs hat das Vibrationsgleitschleifverfahren ausgiebig an SLS-3D-Druckteilen getestet, um Empfehlungen über die richtigen Arbeitsabläufe für optimale Ergebnisse geben zu können. Basierend auf einem Standard-Design mit ebenen und gekrümmten sowie inneren und äußeren Oberflächen haben wir mehrere Teile 3D-gedruckt.
Die Teile aus Nylon 12 Powder und Nylon 11 Powder wurden auf dem SLS-3D-Drucker Fuse 1+ 30W gedruckt, auf dem Fuse Sift anhand der standardmäßigen Nachbearbeitungsrichtlinien entpulvert und anschließend in der Vibrationsgleitschleifanlage CB300 (auch Mr.Deburr genannt) für vier, sechs bzw. acht Stunden geglättet. Die Maßgenauigkeit der Teile wurde jeweils vor und nach dem Gleitschleifen mit Messschiebern bestimmt und die Oberflächenrauheit mit einem Laser-Scanning-Mikroskop von Keyence gemessen. Wenn Sie die vollständigen Ergebnisse unserer Tests einsehen möchten, laden Sie gern unser Whitepaper herunter.
The Process
We 3D printed several parts based on one standard design that has flat and curved surfaces as well as interior and exterior surfaces. The parts were printed on the Fuse 1+ 30W SLS 3D printer, depowdered in the Fuse Sift according to standard post-processing guidelines. Parts were printed in both Nylon 12 Powder and Nylon 11 Powder.
Aside from an identification number, each part was identical. These parts were each measured for dimensional accuracy using calipers and for surface roughness using a laser scanning microscope by manufacturer Keyence.
We chose to primarily test in a CB300 vibratory tumbler, commonly referred to as Mr.Deburr. This machine has three cubic feet of tumbling capacity and operates using a 0.75 horsepower motor. Retailing for $3500, Mr. Deburr is a good choice for high-throughput applications. The volume capacity enables multiple batches of SLS 3D printed parts to be tumbled at the same time, or a lower quantity of very large parts. The media used were ceramic pellets in angle-cut triangle shapes, with side dimensions of ¼ inch. A general-purpose finishing compound was used to assist with the process. The liquid compound chosen was “Kramco 1010” provided by Kramer Industries. This liquid works well with ceramic media and is good for deburring and light cutting.
The components tumbled for two, four, six, and eight hours before being removed and re-measured to determine if changes in dimensions and reduction in surface roughness occurred, and to what degree. The surface roughness was again measured using a Keyence VR-5000. The roughness was measured in terms of Sa. Sa is the arithmetic mean of a surface. The Keyence profilometer takes the average height of a surface and then compares the difference in height of each point when compared to the mean. The dimensional accuracy measurements were taken using vernier calipers with an accuracy of ±0.02mm. This allows us to determine the amount of material removed from each surface during the tumbling process. It should be noted that the outcome may be different if using different media, detergent, or machine and that there is a huge range of media in different materials, shapes, and sizes — all of which will impact your results. Based on our discussions with industry leaders, we chose to use ceramic for our tests.
A Note on Smaller Machines
To test out the efficacy of smaller, more entry-level tumbling machines, we also tested parts in a lower-cost model and found that it was unable to achieve the same results as Mr. Deburr, most likely due to the less aggressive churning of the media. However, the smaller tumbler was still able to get the parts mostly polished, to about a 70% reduction in surface roughness over a 48-72 hour period. These results are not included in our tables in order to highlight the efficacy of larger machines and their efficiency for volumes of this size.
Results With Mr. Deburr
Both Nylon 11 Powder parts and Nylon 12 Powder parts were able to have their surface roughness reduced by more than 80% of their original surface roughness after eight hours of vibratory tumbling, and some of the parts managed to reach 80% or less in four to six hours.
A key finding — Nylon 11 Powder and Nylon 12 Powder both started and finished with different surface roughnesses, but their proportional changes are quite similar. In our trials, we determined that Nylon 11 Powder parts have an average initial surface roughness of approximately 35 µm, whereas Nylon 12 Powder parts have an initial surface roughness of approximately 26 µm. Nylon 12 Powder parts were reduced to 4 µm, whereas the Nylon 11 Powder parts saw a reduction down to 5.5 µm. In terms of overall material removed, Nylon 11 Powder (0.12 mm) exhibited slightly less wear than Nylon 12 Powder (.15 mm) over the eight hours of tumbling. This is approximately the same surface roughness as commercial steel piping.
Looking at both graphs that compare the surface roughness reduction to tumbling time, it is apparent that both the smoothing rate and the amount of material removed per hour are decreasing. For both materials, it does not appear that the surface roughness has plateaued, and we hypothesize that if we were to continue tumbling for longer, you would see the Sa values continue to decrease but at increasingly slower speeds.
Visually, we saw several changes over longer tumbling periods; hard corners and edges became slightly rounded, thinner extrusions and highly detailed embossing became slightly worn, and media became embedded in holes and pockets closer to the 72-hour mark.
Nylon 12 Vibratory Tumbling Results
Runtime (hours) | Surface Loss (mm) | Surface Roughness (Sa) | Surface Roughness Reduction (%) |
---|---|---|---|
0 | Keine Angabe | 25.687 | 0% |
2 | -0.108 | 10.393 | 59.54% |
4 | -0.126 | 6.314 | 75.42% |
6 | -0.139 | 6.168 | 75.99% |
8 | -0.150 | 4.513 | 82.43% |
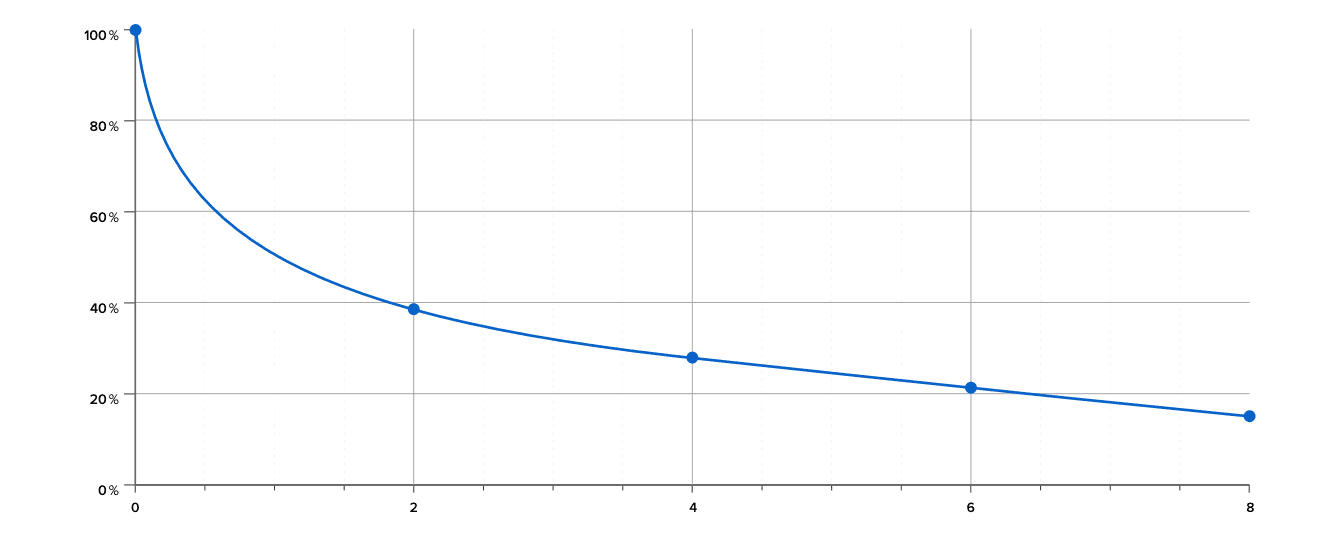
Nylon 12 Vibratory Tumbling Results
Runtime (hours) | Surface Loss (mm) | Surface Roughness (Sa) | Surface Roughness Reduction (%) |
---|---|---|---|
0 | Keine Angabe | 35.081 | 0% |
2 | -0.046 | 11.916 | 66.03% |
4 | -0.081 | 10.056 | 71.43% |
6 | -0.106 | 8.367 | 76.15% |
8 | -0.120 | 6.712 | 80.87% |
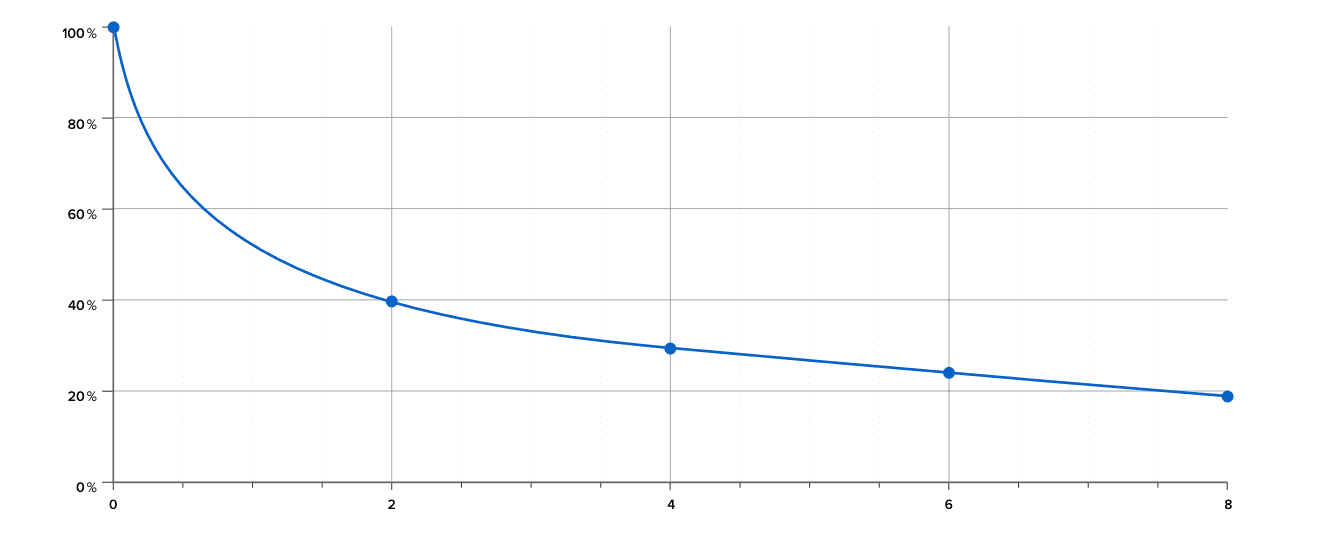
Recommendations
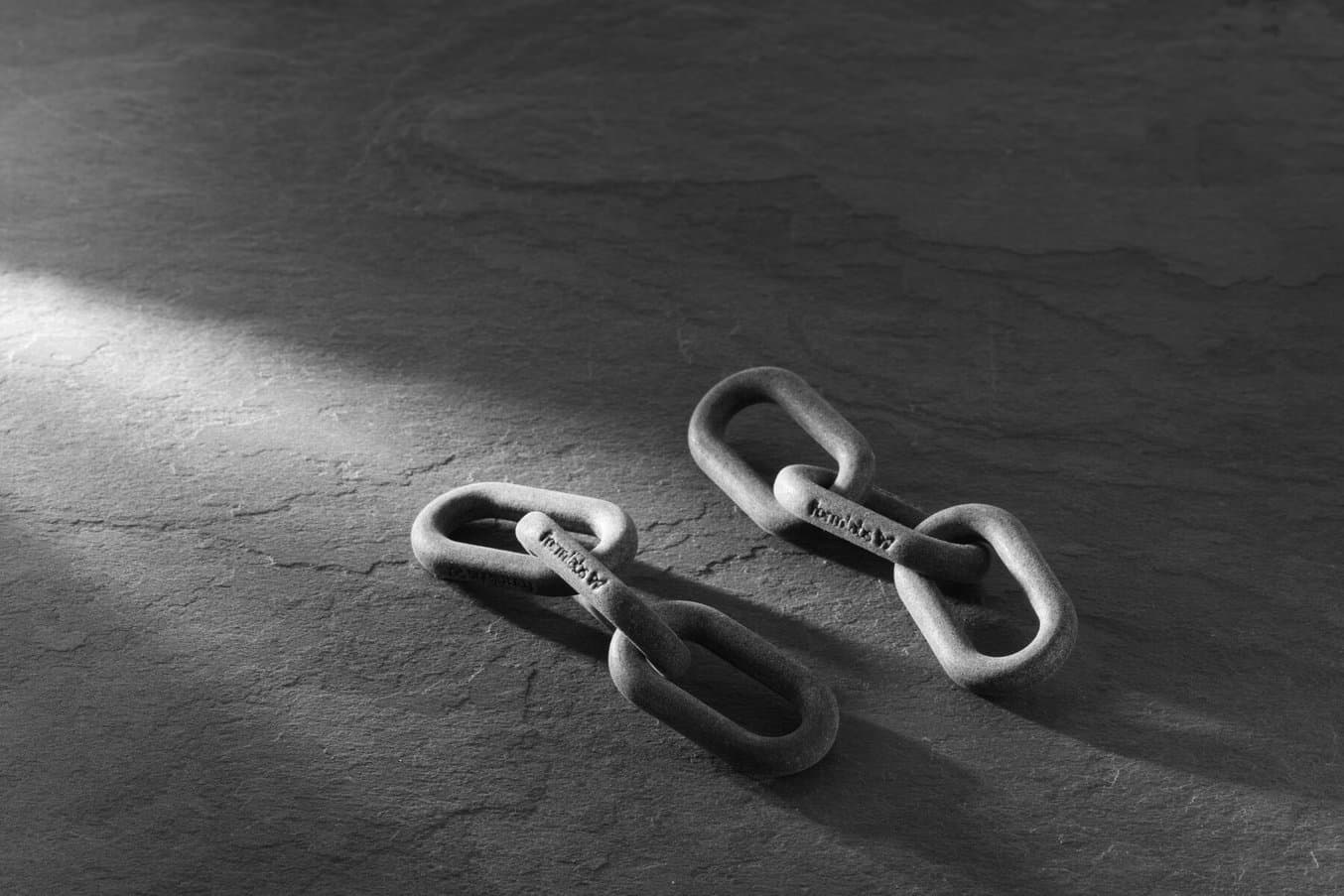
Vibratory tumbling is an excellent way to improve the surface finish of your 3D printed parts. Equipment is affordable, and the workflow is customizable to your exact needs. When adding tumbling to your workflow, keep in mind that different machines and media will produce different results.
When choosing which tumbler to purchase for a 3D printing workflow, first consider your volume of 3D printed parts: mid to high production volumes will require a larger industrial tumbler, while prototyping, manufacturing aids, and rapid tooling applications might only require a smaller, inexpensive tumbler. In these applications, the longer time required by the smaller tumbler shouldn’t negatively affect your workflow.
Choosing your media is the next consideration, and very part dependent. For SLS 3D printed parts, ceramic, plastic, or organic materials will all work, while metal might be too abrasive. For parts with many internal pockets or channels, ceramic media might become flaked and embedded in the parts. Although removal is simple with small hand tools, organic or plastic media might be a better option. For parts that have very fine features, delicate embossing, or thin extrusions, a less abrasive media is optimal. Likewise, choosing rounded media instead of sharp media will help protect delicate parts.
Legen Sie los mit 3D-Druck und Vibrationsgleitschleifen
Das Vibrationsgleitschleifen ist eine leicht zugängliche Lösung, um die Optik und Funktionalität von SLS-3D-gedruckten Teilen noch stärker an Spritzgussteile anzunähern. Ihren Arbeitsablauf im 3D-Druck um diesen Schritt zu ergänzen, muss weder teuer noch aufwendig sein – es gibt zahlreiche Angebote von Gleitschleifmaschinen, die erschwinglich und auch hinsichtlich ihres Platz- und Energiebedarfs leicht integrierbar sind.