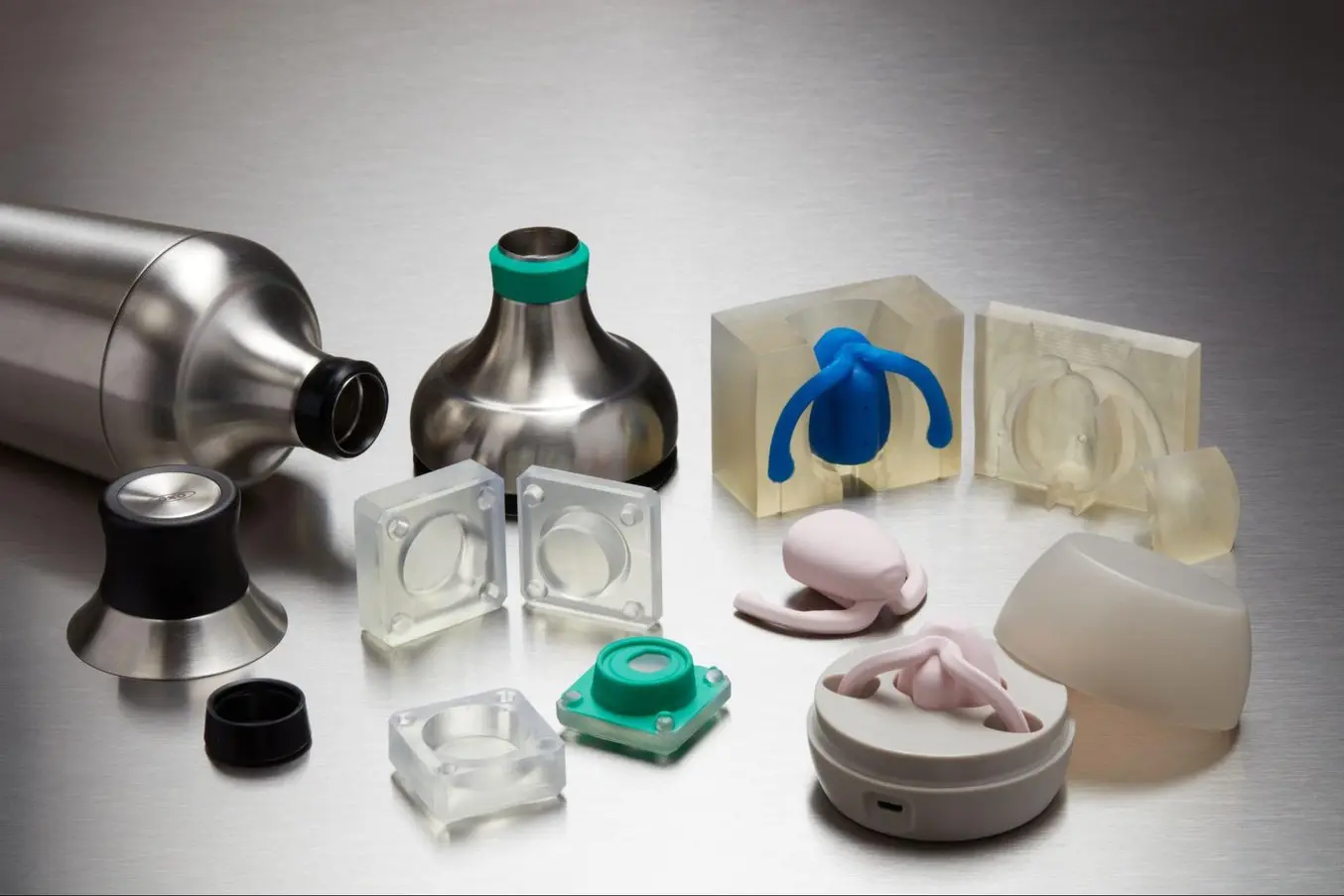
Mit der Erfindung von Gussformen im Bronzezeitalter machten die bis dahin von unseren Vorfahren genutzten primitiven Fertigungstechniken einen Sprung. Seitdem wächst die Bedeutung der verschiedenen Formenbaumethoden stetig an, denn auch die heute eingesetzten fortschrittlichen Fertigungstechniken wie Spritzguss, Thermoformen oder Guss, mit denen der Großteil aller von uns verwendeten Kunststoff-, Silikon-, Gummi-, Verbundstoff- und Metallteile hergestellt wird, beruhen auf der Nutzung von Formen oder Formwerkzeugen.
Ein Verständnis davon, wie Formen- und Werkzeugbauprozesse funktionieren, wie sie eingesetzt werden und wie sie sich zur Erzielung eines bestimmten Durchsatzes optimieren lassen, ist deshalb unerlässlich – sowohl für professionelle Hersteller als auch für Personen, die derartige Verfahren für Hobby-Projekte nutzen wollen.
In diesem umfassenden Leitfaden erhalten Sie einen detaillierten Überblick über alles, was Sie brauchen, um mit dem Formenbau loszulegen. Wir geben Einblick in verschiedene Formen- und Werkzeugbauprozesse, die Wahl der besten Technik für den Formenbau, Ausrüstung zur Optimierung des Verfahrens sowie die Rolle des 3D-Drucks in dieser Thematik. Zu jedem dieser Themenbereiche geben wir Ihnen außerdem eine Reihe von weiterführenden Links an die Hand, damit Sie gut für erfolgreiche Formenbau-Projekte ausgerüstet sind.
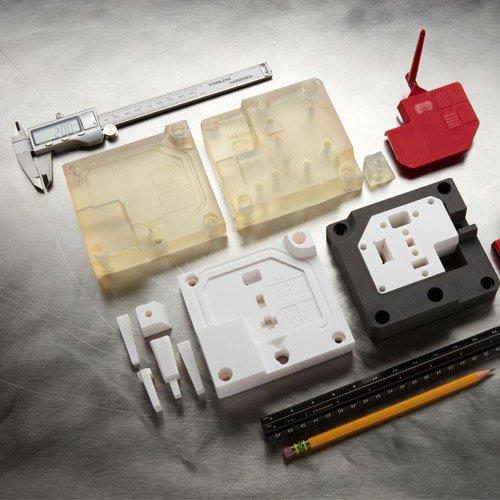
Formenbau durch 3D-Druck: Techniken für Prototyping und Produktion
Laden Sie unser Whitepaper über sechs Arten von Gussformen und Formwerkzeugen herunter, die sich mit einem betriebsinternen SLA-3D-Drucker herstellen lassen, für Spritzguss, Vakuumformen, Silikonformenbau und mehr.
Was sind Formen und wofür werden Sie genutzt?
Bei einer Vielzahl von Fertigungsverfahren wird formbares Rohmaterial zur gewünschten Geometrie ur- oder umgeformt, indem ein speziell entworfenes festes Werkzeug, eine Struktur oder ein Rahmen eingesetzt wird – diese werden als Formen oder Formwerkzeuge bezeichnet. Solche Formen oder Formwerkzeuge können konkav (Negativform) oder konvex sein (Positivform), je nachdem, welches endgültige Design der Hersteller anstrebt.
Die Form ist bei diesen Fertigungsverfahren der entscheidende Faktor und dient der einheitlichen Reproduktion zahlreicher Nachbildungen des jeweiligen Designs. Beim Formenbau kommen Materialien wie Metall, Kunststoff, Keramik, Holz, Schaumstoff und weitere zum Einsatz. Nach dem Entwurf und der Fertigung der Form mit geeigneten Hilfsmitteln wird die Form oder das Werkzeug in das Gerät zur Ur- oder Umformung eingefügt und Rohmaterial wie etwa Thermoplaste werden eingegossen oder über dem Formwerkzeug umgeformt. Beim Aushärten des Materials wird die Geometrie der Form auf das Werkstück übertragen.
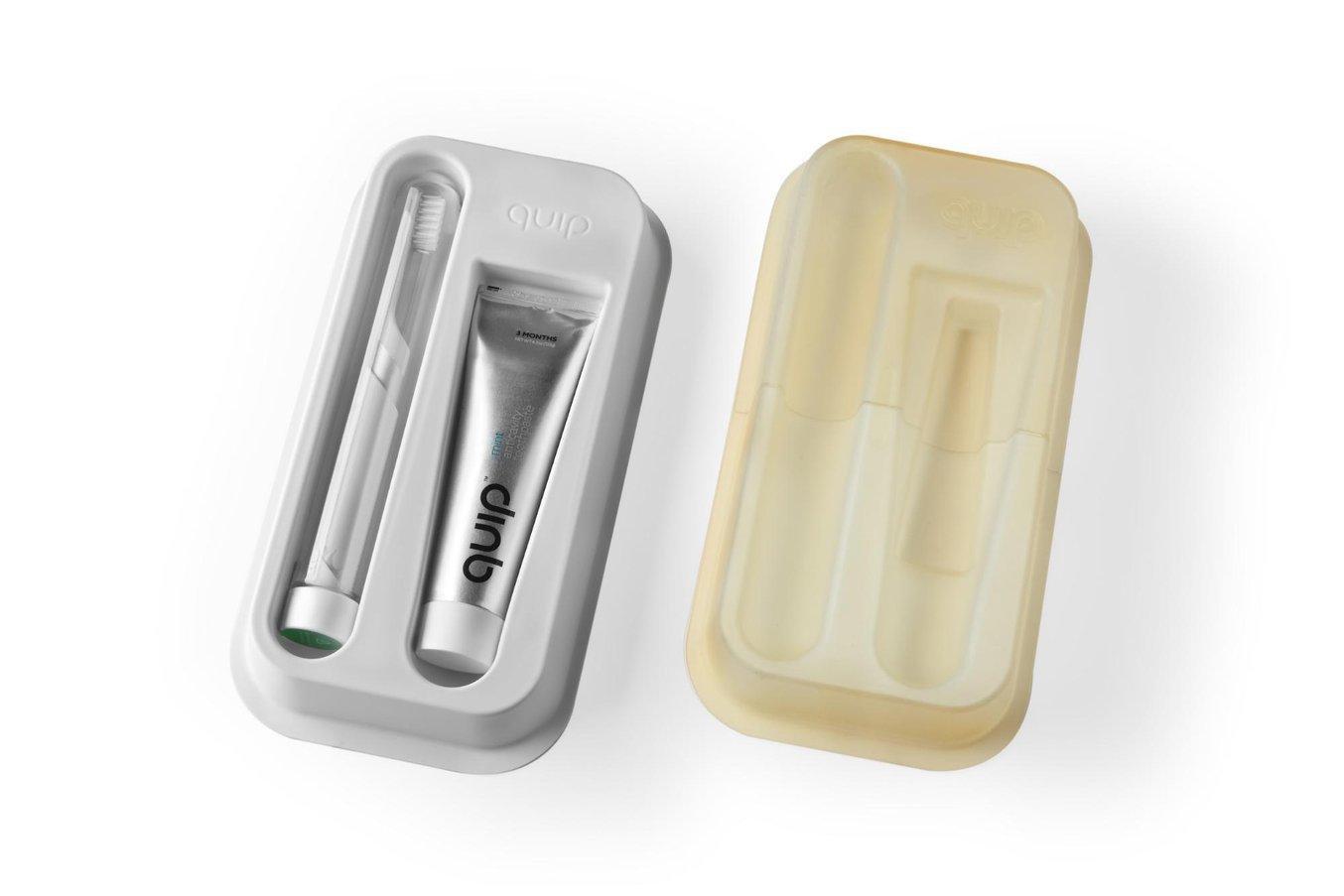
Ein Formwerkzeug für das Thermoformen von Kunststoffverpackungen und das fertige Teil.
Was lässt sich also mit Formen alles herstellen? So ziemlich alles von Prototypen bis hin zu komplexen Teilen für die Endverwendung. Ur- und Umformverfahren werden in der Fertigung verschiedenster Produkte eingesetzt, von Fahrzeugbauteilen über Verbraucherprodukte, Verpackungen und Schmuck hin zu Medizinprodukten und mehr – tatsächlich wäre es schwierig, ein funktionales Produkt ohne auch nur eine einzige Komponente zu finden, die mit diesen Verfahren hergestellt wurde.
Fertigungsverfahren mit Formen
Der Formenbau ist ein grundlegendes Element vieler Fertigungsverfahren; bei diesen Verfahren dient die Form als Blaupause zur Replikation einer Geometrie in Massenproduktion. Folgende Fertigungsverfahren beruhen auf der Nutzung von Formen:
-
Spritzguss ist eines der beliebtesten Fertigungsverfahren für Thermoplaste sowie Silikon- oder Kautschukteile. Es ist eine kostengünstige und extrem reproduzierbare Technologie zur Produktion hochwertiger Teile in Großserie. Bei diesem Verfahren wird die fertige Gussform in die Spritzgießmaschine eingesetzt, wo sie mit dem erhitzten Thermoplast oder sonstigem verflüssigten Rohmaterial gefüllt wird. Sobald das Material ausgehärtet ist, wird das Gussteil aus der Maschine ausgeworfen und der Vorgang wird in schneller Folge wiederholt.
-
Thermoformen, auch Tiefziehen genannt, ist ein Fertigungsverfahren, bei dem eine Kunststoffplatte oder -folie erhitzt und mithilfe eines Formwerkzeugs in bestimmte Formen gebracht wird. Dabei gibt das Formwerkzeug die Geometrie vor, welche von der Thermoformmaschine auf das fertige Formteil übertragen wird. Abhängig vom gewählten Thermoformprozess wird erhitztes, formbares Material entweder über das Formwerkzeug gezogen, gepresst oder mithilfe von Vakuumdruck über es gesaugt. Das Thermoformen ist das gängigste Verfahren zur Herstellung von Verpackungen, kommt jedoch auch bei der Produktion robuster Teile für die Endverwendung zum Einsatz.
-
Beim Gießen wird eine Gussform mit geschmolzenem Metall oder einem anderen verflüssigten Material gefüllt. Die Schmelze kühlt ab und härtet in der Gussform aus, um die für das Endprodukt gewünschte Form zu erhalten. Gießverfahren werden üblicherweise zur Fertigung von Produkten aus Metall sowie Silikon oder Kunststoff eingesetzt.
-
Das Formpressen ist ein Fertigungsverfahren, bei dem eine bestimmte Menge Formmasse üblicherweise vorgeheizt und dann mit Druck zwischen zwei erhitzte Hohlformen (Gesenke genannt) gepresst wird, bis die gewünschte Form erreicht ist. Das Formpressverfahren wird in der Regel als Alternative zum Spritzguss bei der Fertigung von Teilen mit relativ einfacher Geometrie in kleinen und mittleren Stückzahlen angesehen.
-
Beim Blasformen handelt es sich um eine dem Glasblasen ähnliche Technik. In einer Blasformmaschine wird Luft in ein erhitztes rohrartiges Teil geblasen, das üblicherweise aus Kunststoff oder Glas besteht und an eine hohle Form geklemmt ist. Durch den Lufteintritt dehnt sich das Material aus und passt sich an die Geometrie der Form an. Das Blasformen wird häufig zur Produktion hohler Produkte wie Flaschen verwendet.
- Die Laminierung von Verbundwerkstoffen umfasst das Aufbringen von Verbundstoffen auf einer Form sowie Methoden wie Handlaminieren, Prepreg-Laminieren oder Spritzpressen (auch Resin Transfer Molding, RTM), mit denen das fertige Verbundstoffteil aus Hochleistungsmaterialien wie Kohlenstofffaser, Glasfaser oder Kevlarfaser geformt wird.
Arten von Formen
Es gibt zahlreiche Arten von Formen, die als Werkzeuge für die oben beschriebenen Fertigungsverfahren genutzt werden können. Beim Aluminiumguss werden beispielsweise ca. sieben verschiedene Arten von Formen eingesetzt, unter anderem Sandgussformen, Keramikformen und Formmasken. Um die Einordnung der verschiedenen Formenarten zu erleichtern, werden sie deshalb wie folgt kategorisiert:
-
Einteilige Formen sind die einfachste Art von Formen und haben einheitliche Oberflächen über alle Teile des Werkstücks hinweg. Formendesigns oder Objekte mit einer ebenen Seite können mit einteiligen Formen ebenfalls reproduziert werden. Einteilige Formen können zwar auch anhand von CAD-Modellen gefertigt werden, üblicherweise werden sie jedoch aus einem physischen Modell entwickelt.
-
Zweiteilige Formen sind eine nützliche Formenbaumethode zur Umsetzung komplexerer Designs. Derartige Formen bestehen aus zwei separaten Teilen, die an einer Trennebene zusammengefügt werden, um ein Werkstück zu formen. Die so gefertigten Teile bilden die Details beider Hälften der Form bzw. des Urmodells ab. Zur Herstellung einer zweiteiligen Form müssen die einzelnen Formhälften normalerweise anhand eines Urmodells oder CAD-Modells entwickelt werden.
-
Mehrteilige Formen eignen sich ideal für Teile mit komplexeren Geometrien, die eine andere Herangehensweise an den Formenbau erfordern als Prozesse mit ein- oder zweiteiligen Formen. Mehrteilige Formen dienen zur Wiedergabe verschiedener Aspekte oder Details eines Models. Mithilfe der einzelnen Teile der fertigen Form werden also unterschiedliche Elemente des Modells reproduziert.
-
Mehrfachformen verfügen über mehr als einen Hohlraum mit der gleichen Geometrie, sodass in einem Produktionszyklus mehrere Teile zugleich gefertigt werden können, was die Produktivität steigert.
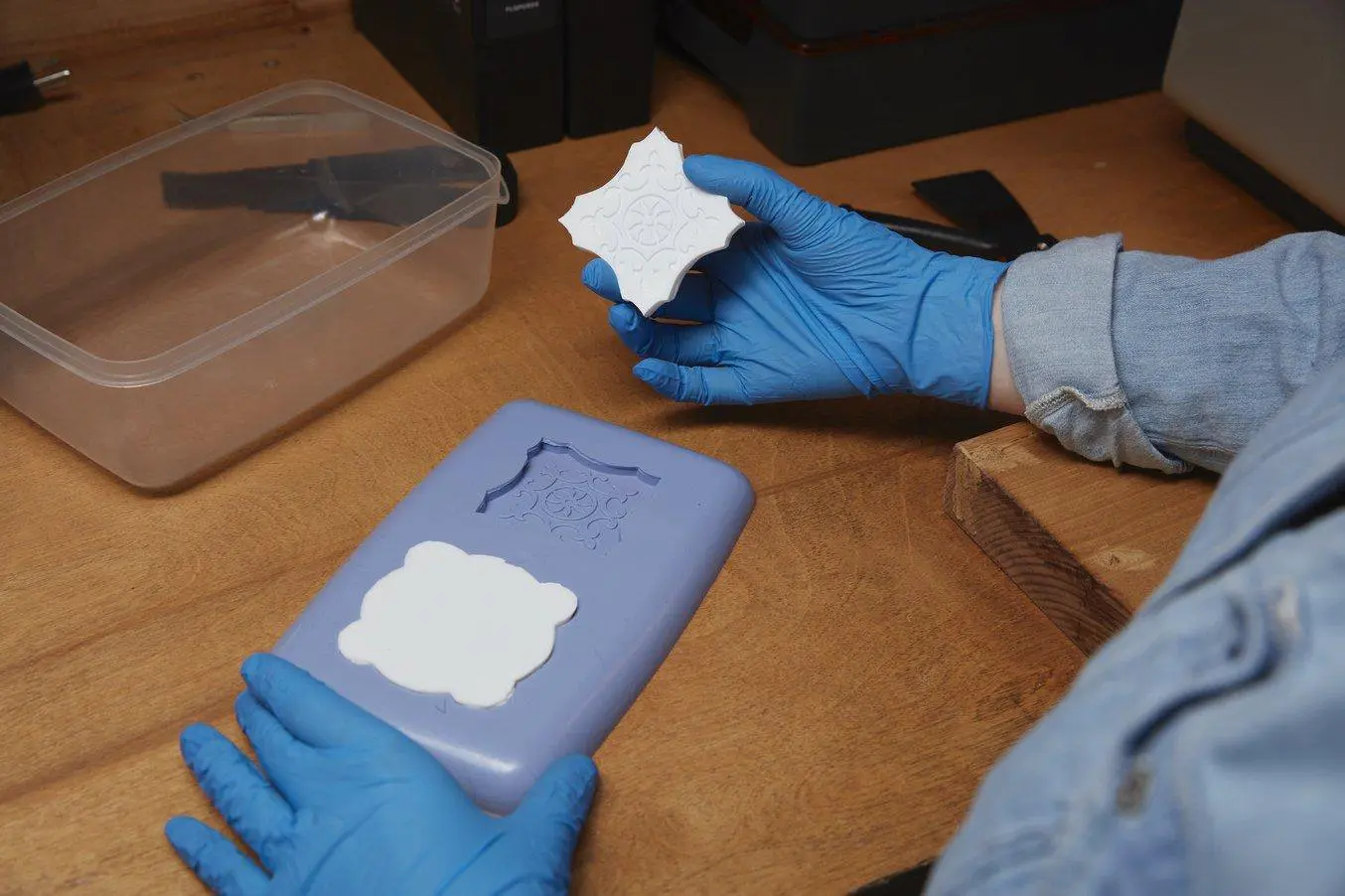
Eine einteilige Silikonform für Designs, die eine flache Seite und keine tiefen Hinterschnitte aufweisen.
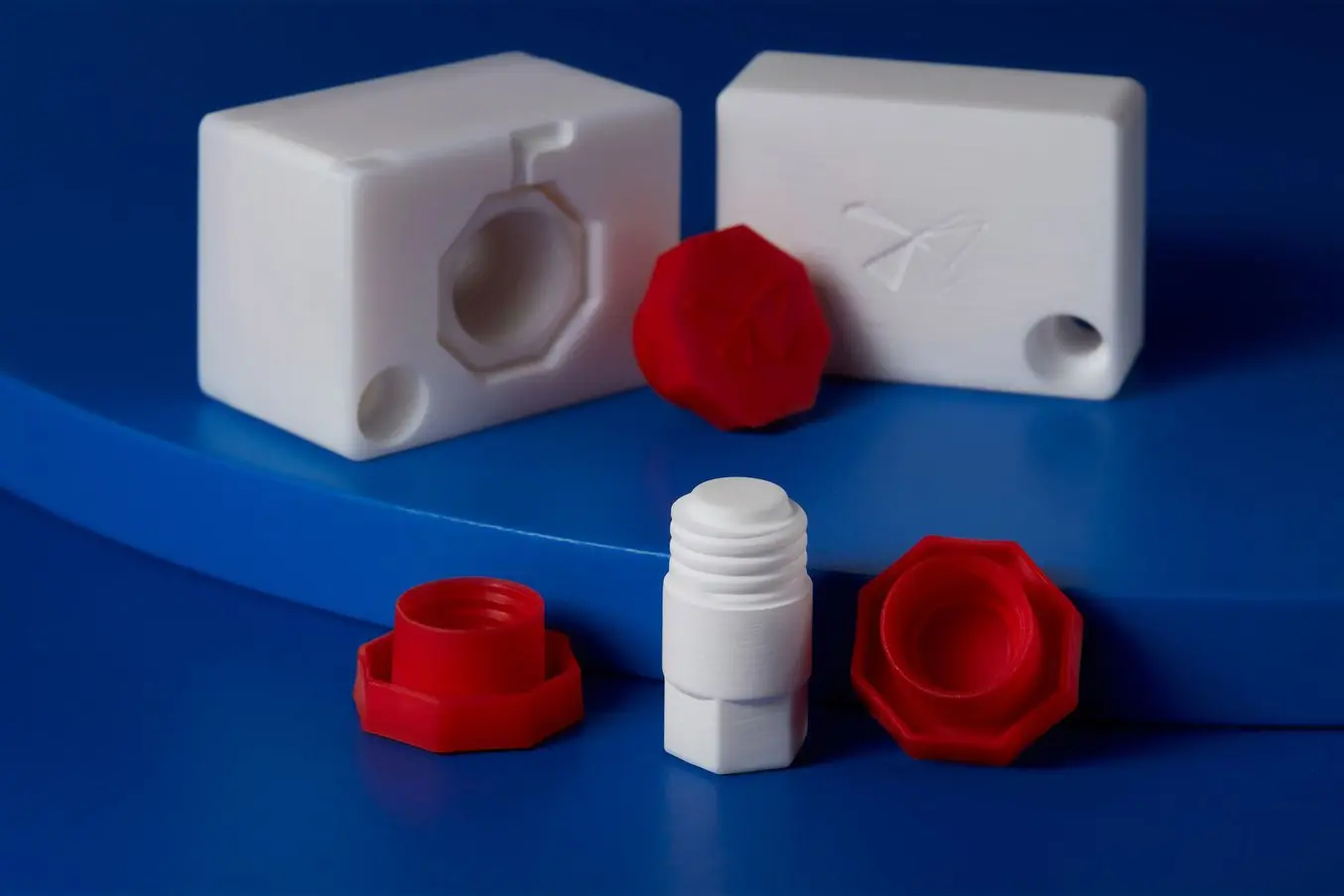
Für komplexere Designs wie diese Kappe mit Schraubgewinde und Hinterschnitten ist häufig eine mehrteilige Form erforderlich, die über Einsätze oder seitlich bewegliche Kerne verfügt.
Ein weiterer wichtiger Gesichtspunkt zur Klassifizierung verschiedener Arten von Formen ist die Wiederverwendbarkeit der fertigen Form. Die Wiederverwendbarkeit gibt an, wie viele Produktionszyklen ein Hersteller mit einer Form durchführen kann. Nach dieser Klassifizierung werden Formen in folgende Typen eingeteilt:
-
Einmal verwendbare oder verlorene Formen: Solche Formen werden nur zur Herstellung eines einzigen Teils verwendet und danach im Zuge des Entformungsprozesses zerstört. Verlorene Formen bestehen meist aus Sand, Ton, Silikon, Wachs oder Kunststoff.
-
Wiederverwendbare oder Dauerformen: Wie der Name bereits andeutet, können derartige Formen in mehreren Zyklen eingesetzt werden, sowohl für Klein- als auch Großserien. Für Kleinserien werden wiederverwendbare Formen aus Silikon, Schaumstoff, Holz, Kunststoff oder weicheren Metallen wie Aluminium hergestellt (manchmal auch als weiche Formen bezeichnet). Großserien erfordern robustere Formen, die nicht verschleißen und meist aus Hartmetallen wie Stahl hergestellt werden (oft auch harte Formen genannt).
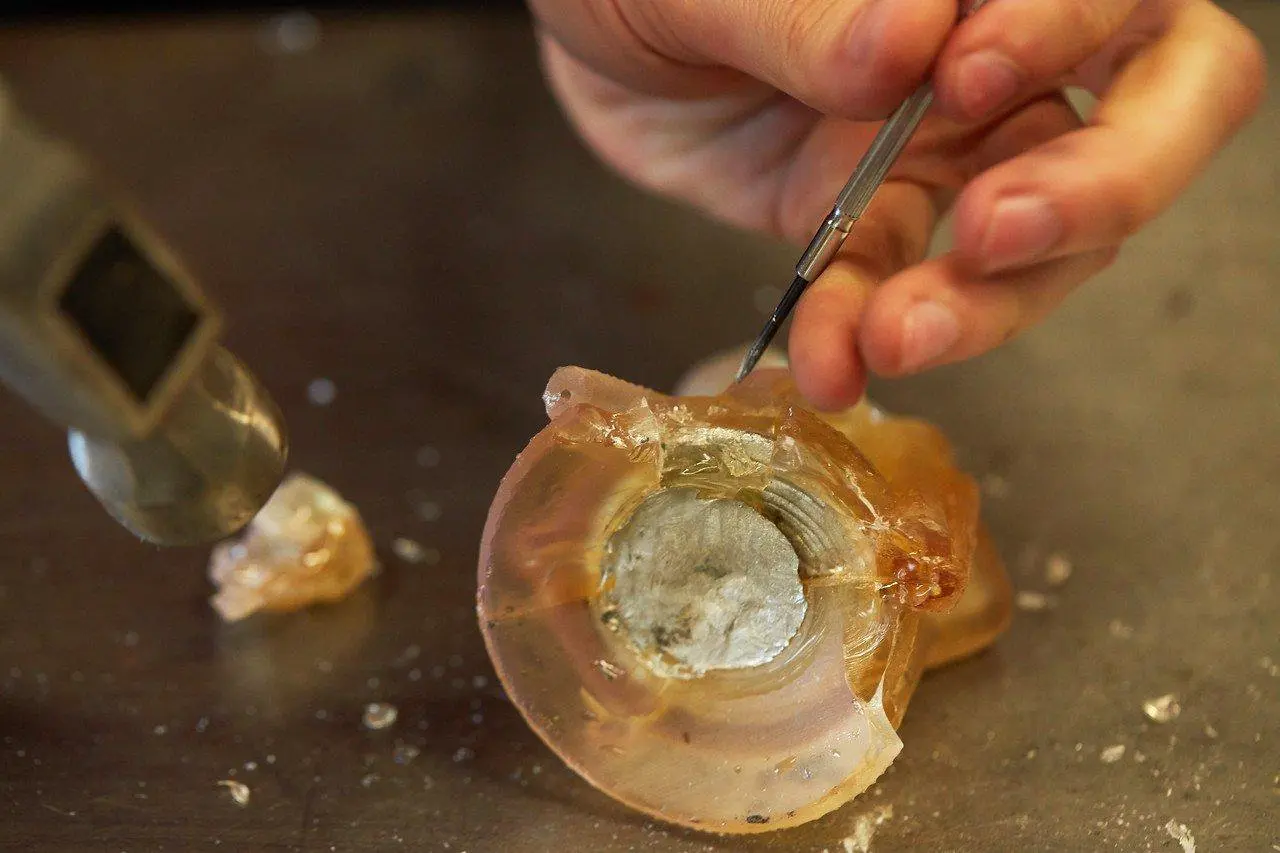
Verlorene Formen werden beim Entformungsprozess zerstört.
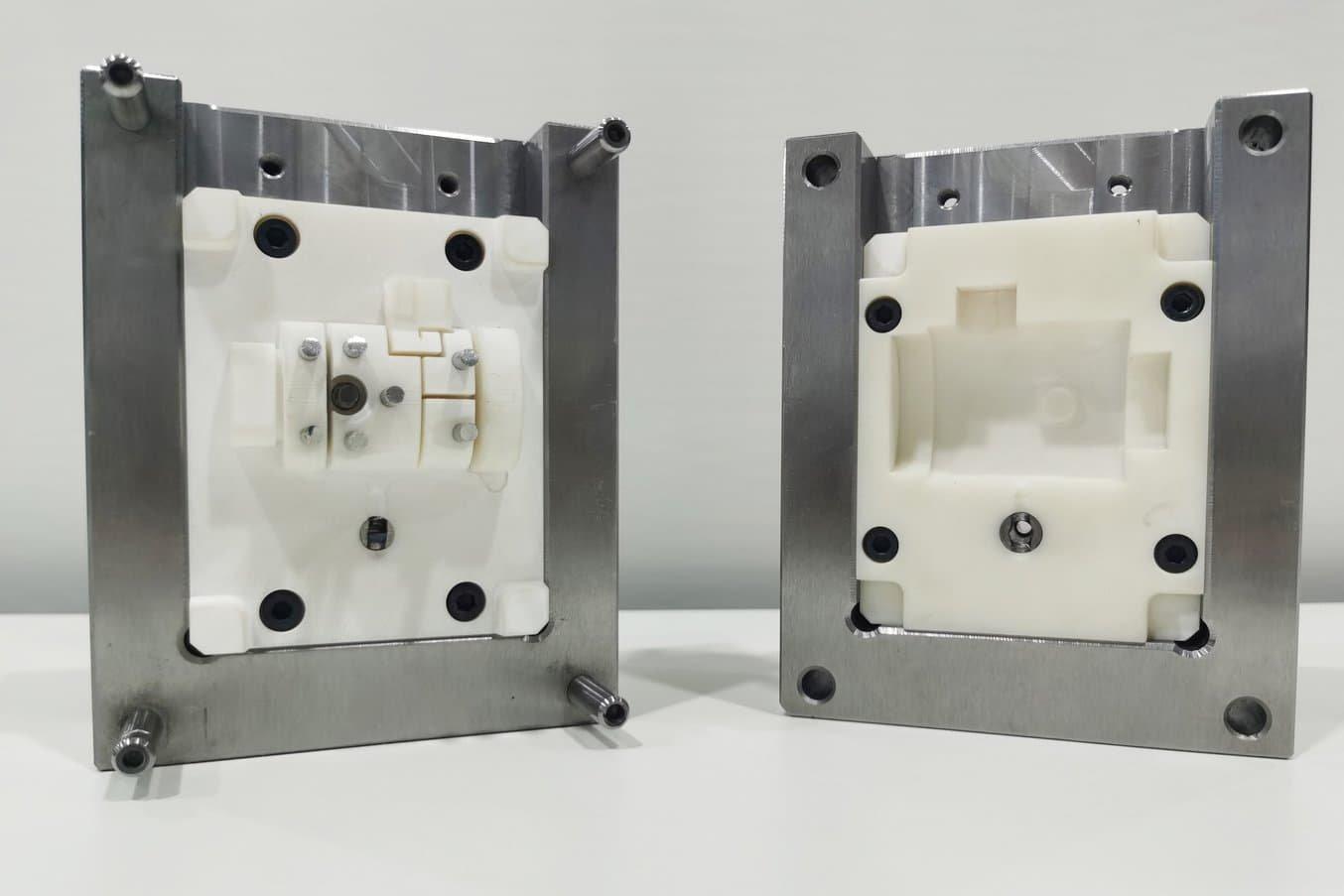
Dauerformen können für mehrere Produktionszyklen genutzt werden.
Wie wählt man die richtige Technik für den Formenbau?
Welche ist die beste Formenbautechnik für eine bestimmte Anwendung? Das hängt von einigen wichtigen Faktoren ab, nämlich unter anderem vom geplanten Material des Endproduktes, dem vorgesehenen Fertigungsverfahren, der Geometrie des Modells sowie vom Produktionsvolumen.
In den folgenden Punkten schildern wir eine vereinfachte, schrittweise Herangehensweise an die Wahl der richtigen Technik für Ihr Fertigungsvorhaben:
1. Umriss der Entwicklungskriterien Ihres Projekts
Ein Fertigungsplan kann Ihnen dabei helfen, sich ein klares Bild davon zu verschaffen, was von einem Projekt zu erwarten ist und wie der Entwicklungszeitplan und das Budget aussehen. Für Ihre Auswahl in den nächsten Punkten ist es entscheidend, ob Sie maßgefertigte Teile herstellen oder Tausende identische Teile massenproduzieren möchten. Die Entwicklungskriterien können je nach Projekt variieren, beinhalten jedoch im Allgemeinen das Teiledesign, die Größe, das Material, die Qualität, die erforderlichen Toleranzen, den Zeitplan, das benötigte Produktionsvolumen, finanzielle Einschränkungen usw.
In der Produktentwicklung werden viele dieser Fragen meist in erster Linie im Lastenheft beantwortet, während die Stückliste eine vollständige Liste aller Teile, Artikel, Baugruppen und anderer für die Herstellung des Produkts benötigten Materialien darstellt.
2. Wahl des Fertigungsverfahrens
Die Wahl des geeigneten Fertigungsverfahrens für ein Teil hängt weitgehend von den Entwicklungskriterien ab. In manchen Fällen lässt sich ein gegebenes Design über verschiedene Produktionsverfahren herstellen. Als Faustregel gilt, sich für den Prozess zu entscheiden, mit welchem das Teil in der erforderlichen Qualität und zu den niedrigsten Kosten bei gleichzeitiger Einhaltung aller sonstigen Entwicklungskriterien produziert werden kann. Die Materialauswahl und das Produktionsvolumen haben hierbei vermutlich den größten Einfluss auf die Entscheidung.
Für Kunststoffteile erhalten Sie genauere Informationen in unserem Leitfaden zu Fertigungsverfahren für Kunststoffe.
3. Wahl einer Technik für den Formenbau
Wenn Sie sich auf ein Fertigungsverfahren festgelegt haben, wird die Art der hierfür benötigten Form oder des Formwerkzeugs ebenfalls zu großen Teilen von den Entwicklungskriterien bestimmt. Die genauen Faktoren hängen letztendlich zwar vom Fertigungsverfahren ab, dennoch haben wir hier die wichtigsten Gesichtspunkte bei der Wahl einer Technik für den Formenbau zusammengestellt:
-
Teiledesign: Versuchen Sie, das Design weitestgehend zu vereinfachen und es mit den Designrichtlinien des jeweiligen Fertigungsverfahrens abzustimmen, damit Sie beim Formenbau eine möglichst kostengünstige Technik wählen können. Für einfache Designs können Formen genügen, die sich mit manuellen Verfahren herstellen lassen, während komplexe Designs oft mehrteilige Formen und digitale Fertigungswerkzeuge wie 3D-Drucker oder CNC-Maschinen erfordern.
-
Produktionsvolumen: Für die Produktion von Großserien werden haltbare, robuste Formen benötigt, die Modelle genau reproduzieren, ohne nach ein paar Einsätzen zu verschleißen. Die Herstellung dieser Werkzeuge ist jedoch mit hohen Kosten und Durchlaufzeiten verbunden. Für Einzelstücke und Kleinserien kann es daher effizienter sein, preiswertere und schneller herstellbare Formen zu wählen, wie etwa verlorene Formen oder weiche Formen, die bei Anzeichen von dauerhaftem Verschleiß einfach entsorgt werden können.
-
Qualität: Sind engere Toleranzen gefordert, müssen Formen und Werkzeuge präziser sein, etwa durch die Fertigung mit digitalen Hilfsmitteln. Sie erfordern außerdem eine höhere Haltbarkeit, um auch über mehrere Fertigungszyklen eine konsistente Teilequalität zu liefern.
-
Zeitplan: Die Herstellung komplexer Metallformen durch einen Fertigungsdienstleister nimmt oft Monate an Zeit in Anspruch. Falls Sie einen engeren Zeitplan einhalten müssen, ziehen Sie zur Verkürzung der Durchlaufzeit Alternativen in Betracht, wie etwa Rapid Tooling aus dem 3D-Drucker.
-
Material: Materialien mit einem höheren Schmelzpunkt oder stärkerer Abrasion erfordern robuste Formen, die der Produktion der benötigten Produktionsmenge ohne Verschleiß standhalten.
So stellen Sie Formen für verschiedene Fertigungsverfahren her
In diesem Abschnitt geben wir einen kurzen Überblick über Techniken zum Formenbau für verschiedene Fertigungsverfahren. Über unsere Links erhalten Sie detaillierte Leitfäden und eine schrittweise Erläuterung des Arbeitsablaufs für jedes Verfahren.
Es gibt zwei grundlegende Techniken des Formenbaus – direkte und indirekte Formenbauverfahren. Beim indirekten Ansatz zum Formenbau werden Formen anhand eines physischen Urmodells erstellt. Bei direkten Verfahren wird die Form unmittelbar aus einem (digitalen) Design entwickelt, häufig mithilfe digitaler Fertigungsverfahren.
Silikonformen für den Guss
Der Silikonguss ist eines der beliebtesten Verfahren, bei denen Gussformen zum Einsatz kommen. Silikonformen werden in der Produktentwicklung, im Maschinenbau, der Hobbyfertigung und sogar beim Kochen genutzt, um Einzelstücke oder kleinere Serien von Teilen aus Kunststoff oder anderen Materialien herzustellen. Für den Formenbau stellt Silikon eine solide Wahl dar, da sich individuelle Designs damit leicht umsetzen lassen und die Formen selbst relativ robust sind. Sie können also mehrmals benutzt werden, ohne dass Beschädigungen zu befürchten sind.
Abhängig vom Teiledesign werden einteilige oder zweiteilige Formen benötigt. Die Prozesse zur Herstellung dieser Formen ähneln sich, jedoch dauert es etwas länger, eine zweiteilige Form herzustellen. Befolgen Sie die Schritt-für-Schritt-Anleitung in unserem Video oder unseren praktischen Leitfaden zur Herstellung von Silikonformen, um Ihre eigenen Formen zu kreieren.
Spritzgussformen
Spritzgussformen werden üblicherweise durch CNC-Bearbeitung oder Funkenerodieren (EDM) aus Metall hergestellt. Dies sind kostenintensive industrielle Verfahren, für die spezielle Geräte, hochwertige Software und hochqualifizierte Arbeitskräfte erforderlich sind. Daher dauert die Herstellung einer Metallform üblicherweise vier bis acht Wochen, bei Kosten zwischen 2000 und 100 000 €, in Abhängigkeit von der Geometrie und der Komplexität des Teils.
Es gibt jedoch Alternativen zur spanenden Fertigung von Formen aus Metall. Die betriebsinterne Herstellung von Spritzgussformen für Prototypen und Kleinserien via 3D-Druck ist deutlich kosten- und zeitsparender als Metallformen. Gleichzeitig zeichnen sich die so produzierten Teile durch hohe Qualität aus und sind problemlos reproduzierbar.
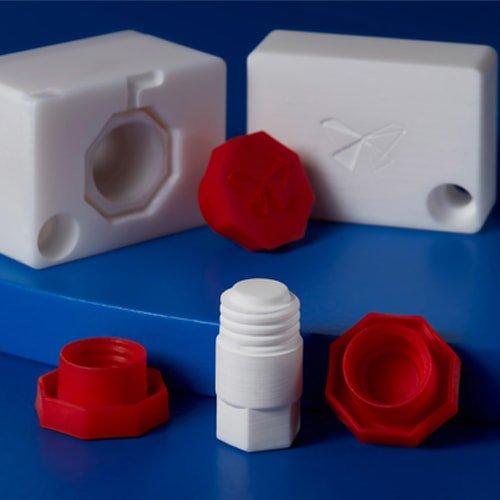
Schnelles Spritzgießen von Kleinserien mit Formen aus dem 3D-Drucker
Laden Sie dieses Whitepaper herunter und erfahren Sie mehr über die Methoden und Richtlinien zur Herstellung 3D-gedruckter Spritzgussformen, um die Kosten zu senken und Lieferzeiten zu verkürzen. Es enthält Fallstudien aus der Praxis von Braskem, Holimaker und Novus Applications.
Thermoformwerkzeuge
Die für Thermoformprozesse erforderlichen Formwerkzeuge können mit verschiedenen Fertigungsverfahren erzeugt werden, etwa durch manuelle Holzbearbeitung, CNC-Bearbeitung von Kunststoff, Strukturschaum, glasfaserverstärktem Kunststoff, technischen Verbundwerkstoffen oder Metallen, 3D-Druck von Polymeren oder Gießen von Gips oder Metall.
Viele Unternehmen nutzen vermehrt den Stereolithografie-3D-Druck (SLA), um Formen für Thermoformverfahren zu erstellen, da dieser insbesondere bei kleineren Auflagen, Sonderanfertigungen und Prototypenentwicklung eine schnelle Durchlaufzeit zu einem niedrigen Preispunkt bietet. Der 3D-Druck ermöglicht außerdem eine unübertroffene Gestaltungsfreiheit bei der Herstellung komplexer und filigraner Formen.
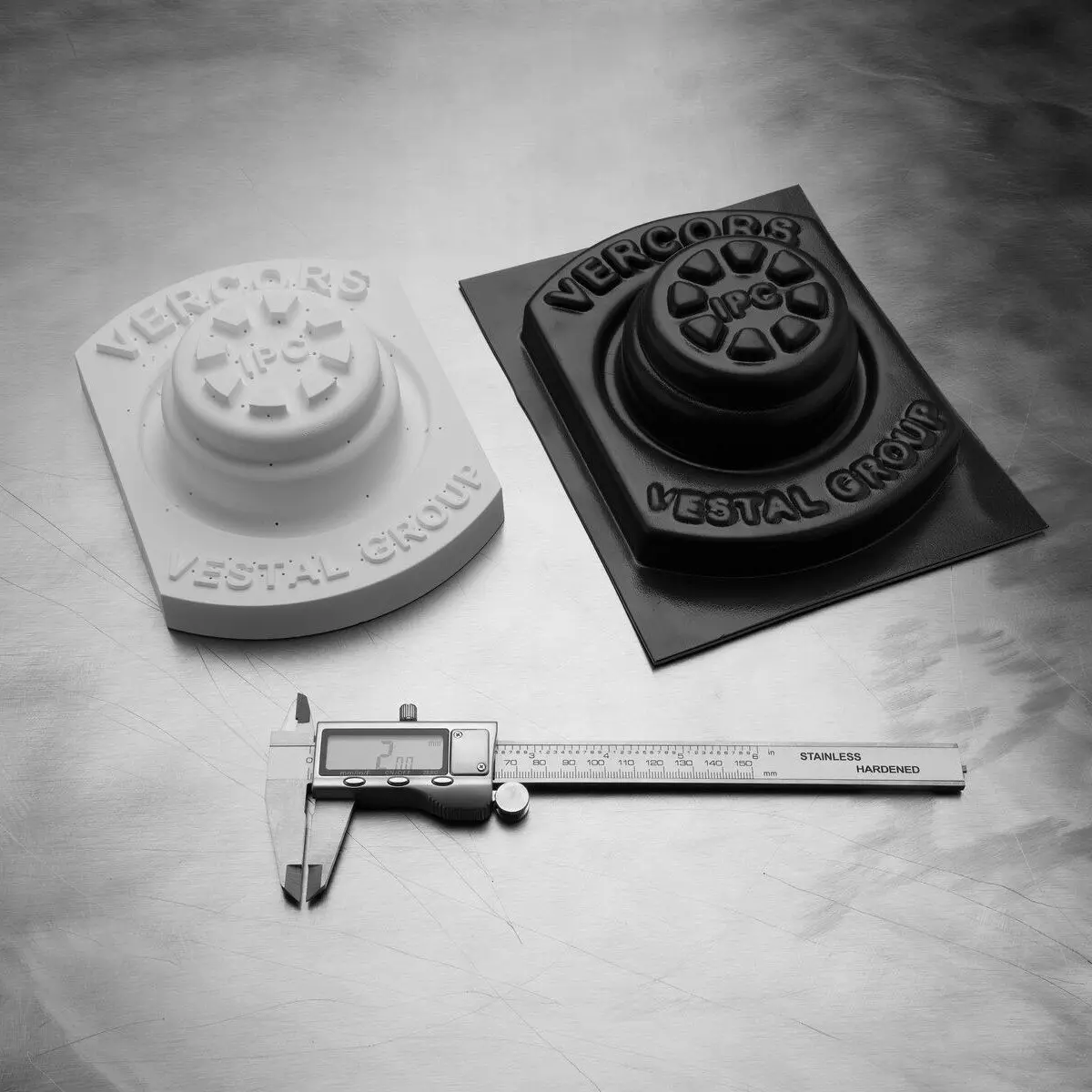
Vakuumformen mit 3D-gedruckten Formwerkzeugen
Laden Sie unser Whitepaper herunter und erfahren Sie mehr über die schnelle Erstellung komplexer Formwerkzeuge mittels 3D-Druck. Wir geben außerdem Tipps und Richtlinien zur Vorbereitung der Bestandteile der Form.
Formpressen
Abhängig vom zu formenden Material bzw. Rohling gibt es verschiedene Möglichkeiten des Formenbaus, zum Beispiel Druckguss, CNC-Bearbeitung oder 3D-Druck. Der Schlüssel zum Erfolg ist hierbei, dass die Gesenke dem gesamten Formpressprozess standhalten. Wenn Sie also mit Hitze arbeiten, müssen Sie Gesenke verwenden, die extreme Temperaturschwankungen tolerieren. Außerdem müssen die Gesenke natürlich dem aufgebrachten Pressdruck widerstehen.
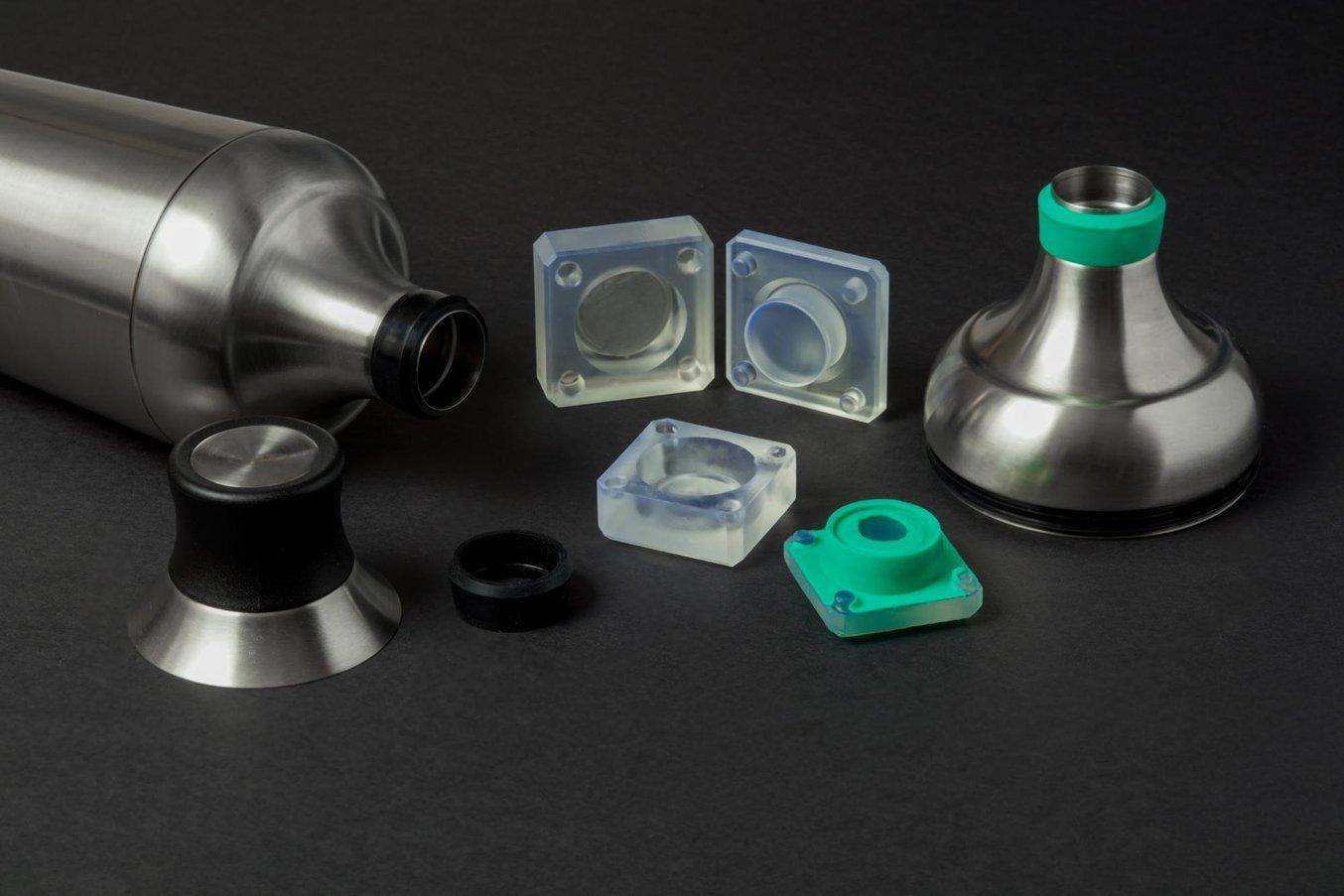
3D-Druck ist eine schnelle und billige Methode zur Herstellung von Formpressgesenken.
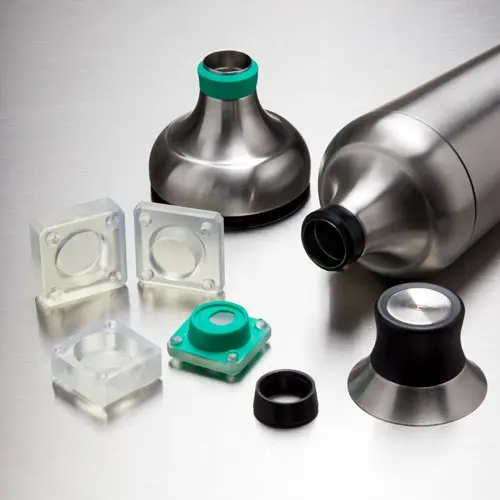
Silikonformenbau für das Produktdesign
Laden Sie diesen Bericht mit Fallstudien von OXO, Tinta Crayons und Dame Products herunter, um von drei verschiedenen Umsetzungen des Silikonformenbaus in Produktdesign und Fertigung zu erfahren, einschließlich Umspritzung und Insert-Molding.
Gussformen für den Metallguss
Obwohl alle Metallgussverfahren im Kern auf demselben Prozess beruhen, gibt es verschiedene Methoden, die je nach Anwendung unterschiedlich gut geeignet sind. Einige der geläufigsten Verfahren sind Druckguss, Feinguss und Sandguss.
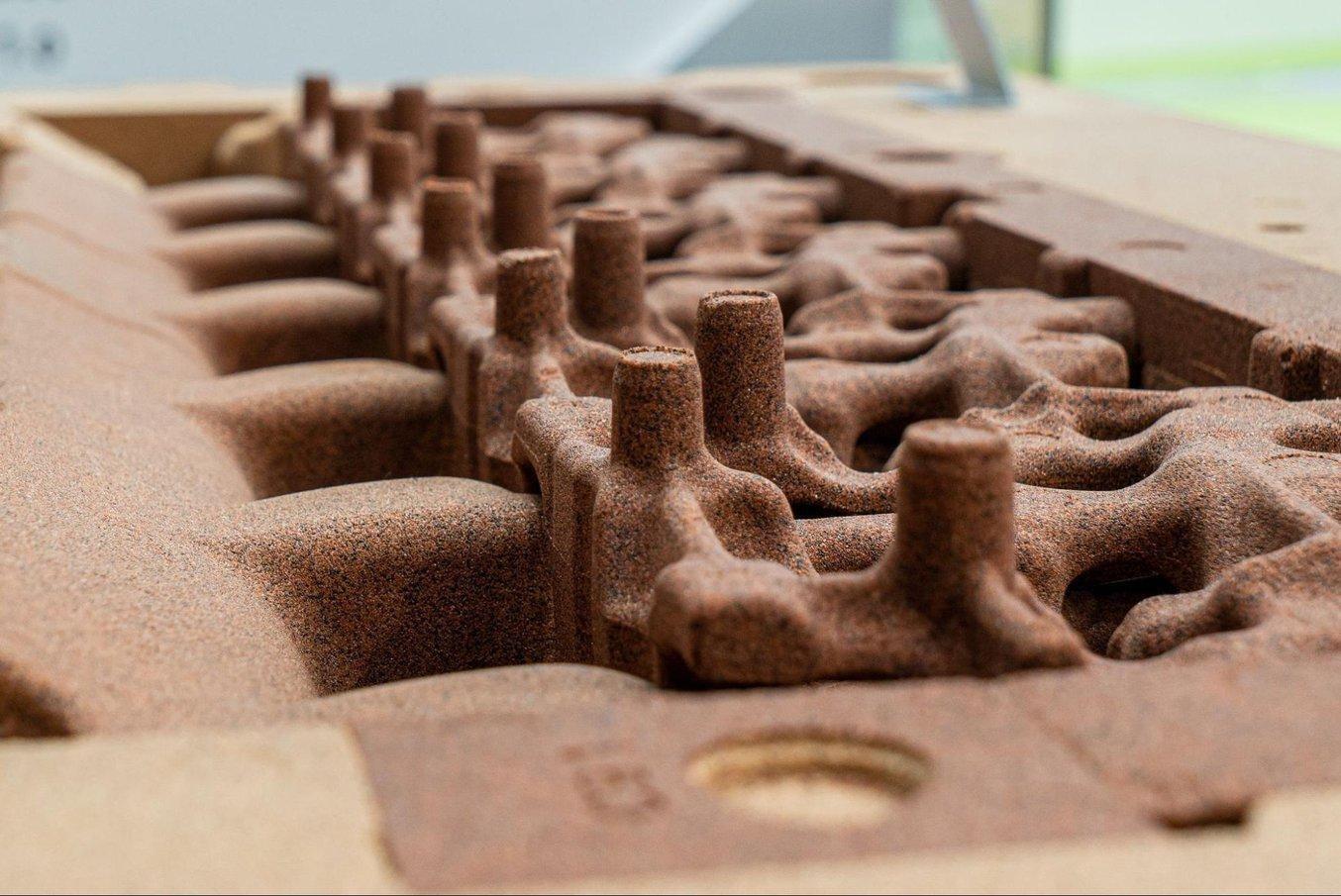
Eine Gussform für den Sandguss.
Sowohl die Urmodelle für den Formenbau als auch direkt hergestellte Formen zum Gießen von Metallteilen können mithilfe verschiedener Methoden gefertigt werden. Lesen Sie unseren Leitfaden zum Metallguss für genauere Einblicke in die Verfahren.
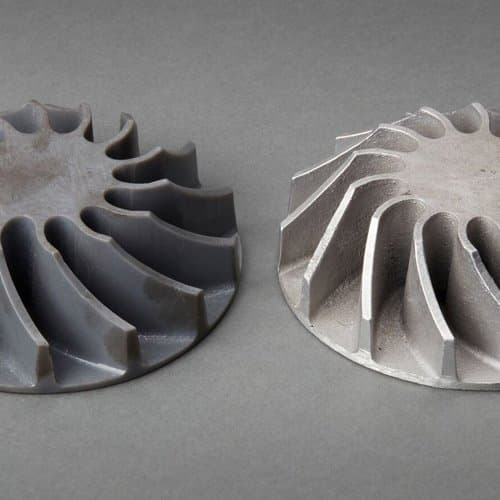
Herstellung von Metallteilen mit 3D-Druck
In diesem Whitepaper erhalten Sie Designleitfäden zur Erstellung 3D-gedruckter Modelle, werden Schritt für Schritt durch das Direktfeingussverfahren geführt und lernen die Richtlinien für indirekten Feinguss und Sandguss kennen.
Legen Sie los mit dem 3D-Druck von Formen
Die Kombination herkömmlicher Techniken wie Spritzguss, Thermoformen oder Silikonguss mit 3D-gedruckten Formen und Werkzeugen beschleunigt die Markteinführung dank zeit- und kosteneffizienterer Fertigungsprozesse. Der Desktop-3D-Druck bietet Unternehmen eine vielseitige und kostengünstige Methode zur Herstellung von Modellen und Formen für indirekte und direkte Formenbauprozesse, und das vollkommen betriebsintern.
Laden Sie unser Whitepaper herunter, um mehr über sechs Verfahren zum Formenbau zu erfahren, die sich mit einem betriebsinternen SLA-3D-Drucker umsetzen lassen. Die verschiedenen Verfahren sind durch echte Fallbeispiele illustriert.