3D-Druck maßgefertigter Einspritzdüsengreifer für einen Pick-and-place-Roboter
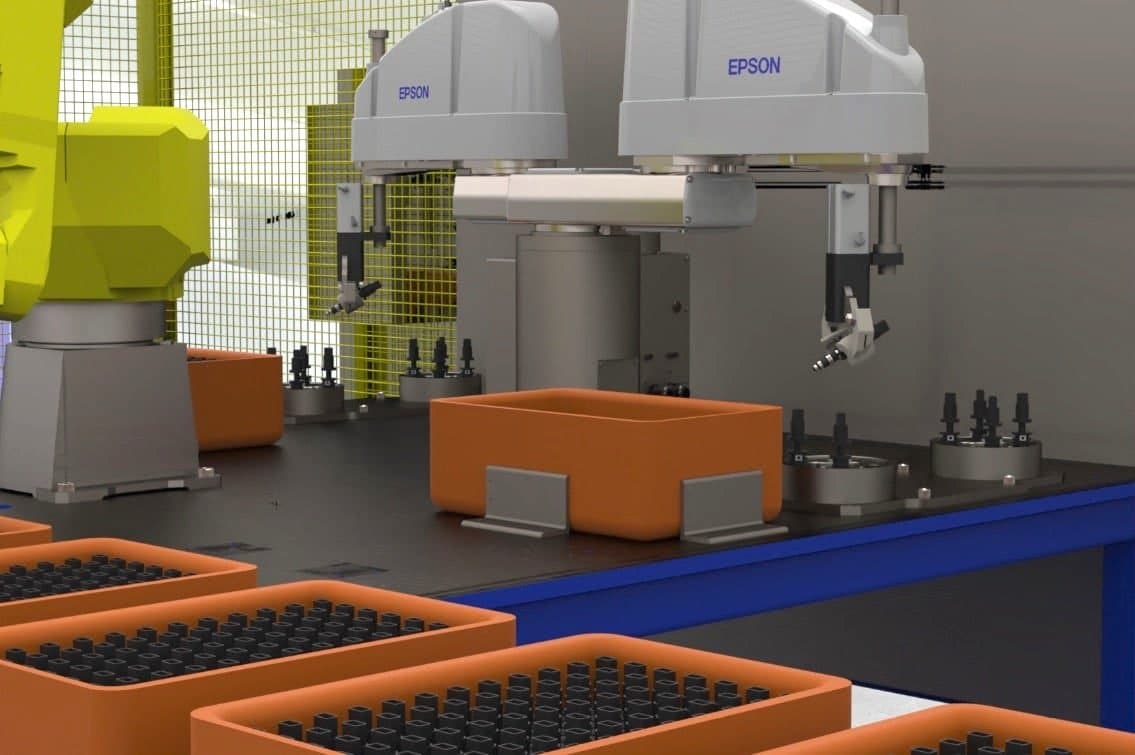
Die STS Technical Group mit Hauptsitz im US-Bundesstaat Wisconsin arbeitet seit fast 40 Jahren mit ihren Kunden an personellen, technischen Design- und Ingenieurherausforderungen. Das Unternehmen beschäftigt in den USA über 250 Mitarbeiter an verschiedenen Personalbeschaffungsstandorten. Dabei wächst es und passt sich an die stetigen Änderungen der Fertigungstechnologien an, z. B. mit neuen und innovativen Dienstleistungen.
Der Einsatz der 3D-Drucktechnologie von Formlabs bei STS beruht auf der Vielfalt der Materialien und deren Eignung für einen umfassenden Einsatz in der Fertigungsumgebung. Die überragende Qualität der 3D-Druckkomponenten – auch für medizinische Zwecke – ist dabei ein Schlüsselfaktor.
Benjamin Heard, Director of Engineering Services bei der STS Technical Group, beschreibt in dieser Fallstudie die Entwicklung individueller Greifer für die Positionierung von Einspritzdüsen in der Fertigung. Er unterstreicht dabei die Vorteile von Komponenten aus dem 3D-Druck gegenüber herkömmlichen Fertigungsmethoden wie Guss oder Zerspanung. Des Weiteren zeigt Heard auf, warum die Fähigkeiten der maßgefertigten 3D-Greifer den bisherigen traditionell hergestellten Greifern weit überlegen sind.
In this case study, STS Technical Group’s Director of Engineering Services Benjamin Heard walks you through the development of custom grippers for moving and positioning fuel injectors in a manufacturing environment, highlighting the advantages of 3D printing a component versus producing it with traditional production methods like casting and machining. Heard will also explain why the capabilities of the custom 3D printed grippers are far superior to the previous, traditionally manufactured grippers.
Das richtige Produktionsverfahren für bestimmte Komponenten auswählen
Für die Fertigung eines speziellen Bauteils müssen bei der Entwicklung viele Produktionsverfahren berücksichtigt werden, wie z. B. Guss, Zerspanung und 3D-Druck mit Schmelzschichtung (FDM) oder Stereolithografie (SLA).
Die Vorzüge des 3D-Drucks bei der Fertigung von Bauteilen:
-
Größere Detailgenauigkeit als beim Gießen und/oder der maschinellen Bearbeitung. Die Druckschichtdicke kann sogar bis auf 25 Mikrometer verringert werden.
-
Kostengünstiger als Guss oder maschinelle Bearbeitung – speziell bei detailreichen Designs.
-
Wesentlich kürzere Durchlauf- und Produktionszeiten als bei Guss oder Zerspanung.
-
Nach dem Druck ist keine Zerspanung erforderlich und somit auch keine teuren Bearbeitungsgeräte, die qualifizierte Arbeitskräfte und aufwendige Einrichtung erfordern.
-
Große Auswahl haltbarer, leichtgewichtiger Materialien.
-
Entwürfe aus einer CAD-Software können gespeichert und bei Bedarf wiederverwendet werden. Es müssen also keine Teile eingelagert werden.
-
3D-gedruckte Gegenstände lassen sich für den Einbau vorbereiten, indem tragende Stellen durch zusätzliches Material verstärkt werden oder indem Sie Schrauben-/Bolzenlöcher und Sechskantaussparungen integrieren.
-
Erleidet ein SLA-3D-gedrucktes Polymerteil im Betrieb einen starken Stoß oder Schlag, bricht es wahrscheinlich. Metallteile hingegen neigen dazu, sich zu verformen, wodurch Sie dann Teile produzieren, die nicht den Spezifikationen entsprechen.
-
Geringere Kosten und kürzere Durchlaufzeiten für kaputte Komponenten und Ersatzteile.
-
Die gedruckten Teile haben eine ansprechende Ästhetik und lassen sich lackieren oder mit einer gewünschten Beschichtung versehen.
-
Eine Alternative für Materialien, die nicht für die Zerspanung geeignet sind, da sie dabei schmelzen, splittern oder reißen würden.
-
Niedrigere Versandkosten bedingt durch ein geringeres Gewicht und weniger Bedarf an Verpackungsmaterial.
Bei der Entscheidung zwischen Guss, maschineller Bearbeitung und dem Druck von Komponenten sollte die Haltbarkeit des Teils im Vordergrund stehen. Metallteile aus herkömmlichen Verfahren bieten zwar höhere Festigkeit, Haltbarkeit und Verschleißbeständigkeit. Dennoch lassen sich die Anforderungen vieler Bauteile durch spezielle technische Druckmaterialien problemlos erfüllen.
Die Arbeitsumgebung ist bei der Auswahl ebenfalls zu berücksichtigen: Muss das Material Temperaturen, Feuchtigkeit oder Korrosion standhalten? Der Druck großer Teile erscheint vielleicht als Herausforderung, aber großformatige 3D-Drucker wie der Form 3L sind auch solchen Druckaufträgen gewachsen.
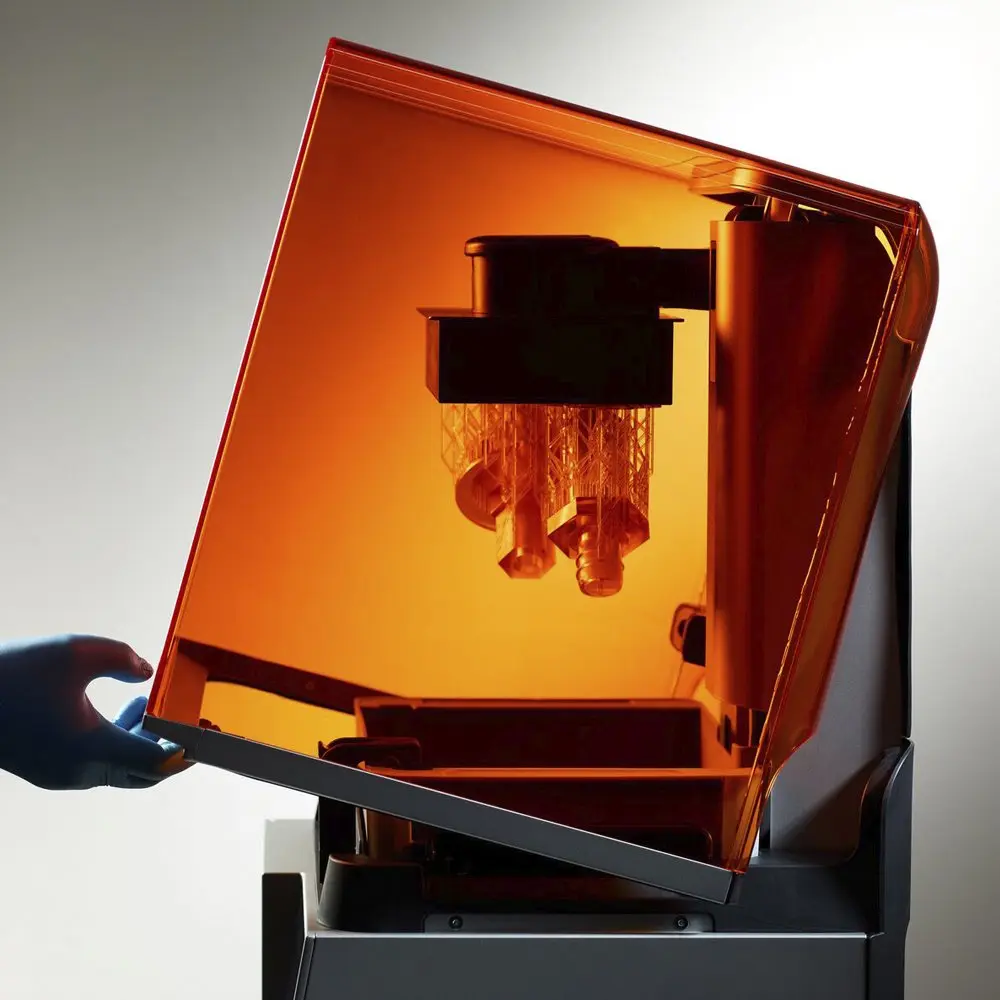
Einführung in den 3D-Druck mit Desktop-Stereolithografie (SLA)
Sie suchen einen 3D-Drucker, der Ihre 3D-Modelle in hochauflösender Qualität Wirklichkeit werden lässt? Lernen Sie in diesem Whitepaper das Verfahren der Stereolithografie (SLA) näher kennen – von seiner Funktionsweise bis hin zu den Gründen für seinen Status als populärste 3D-Drucktechnologie für die Umsetzung hochgradig detailtreuer Modelle.
Entwurf und 3D-Druck maßgefertigter Greifer für Einspritzdüsen
Viele Faktoren fließen ein in den Entwurf von Platzierungsgreifern. Die Materialien des zu greifenden Teils und des Greifers, die Greifkraft, die Geometrie des zu greifenden Teils, kreisförmige oder lineare Bewegungen, die umgebenden Freiräume und die erforderlichen Toleranzen bei der Aufnahme und Platzierung.
Das Material für die Greiferfinger ist normalerweise deutlich stärker und härter als das aufzunehmende Teil, damit die Arme auch nach Tausenden oder gar Millionen von Zyklen nicht verschleißen. Ein gängiges Greifermaterial ist gehärteter Stahl, der aber auf weicheren Oberflächen Kratzer hinterlassen kann. Ist die Oberfläche empfindlich, werden die Greifer mit Beschichtungen oder Ausätzen versehen. Bei Teilen, die nach der Positionierung weitere maschinelle Bearbeitungen durchlaufen, führt schlechter Greiferkontakt oft dazu, dass das Teil verrutscht. Das kann Bearbeitungsfehler nach sich ziehen.
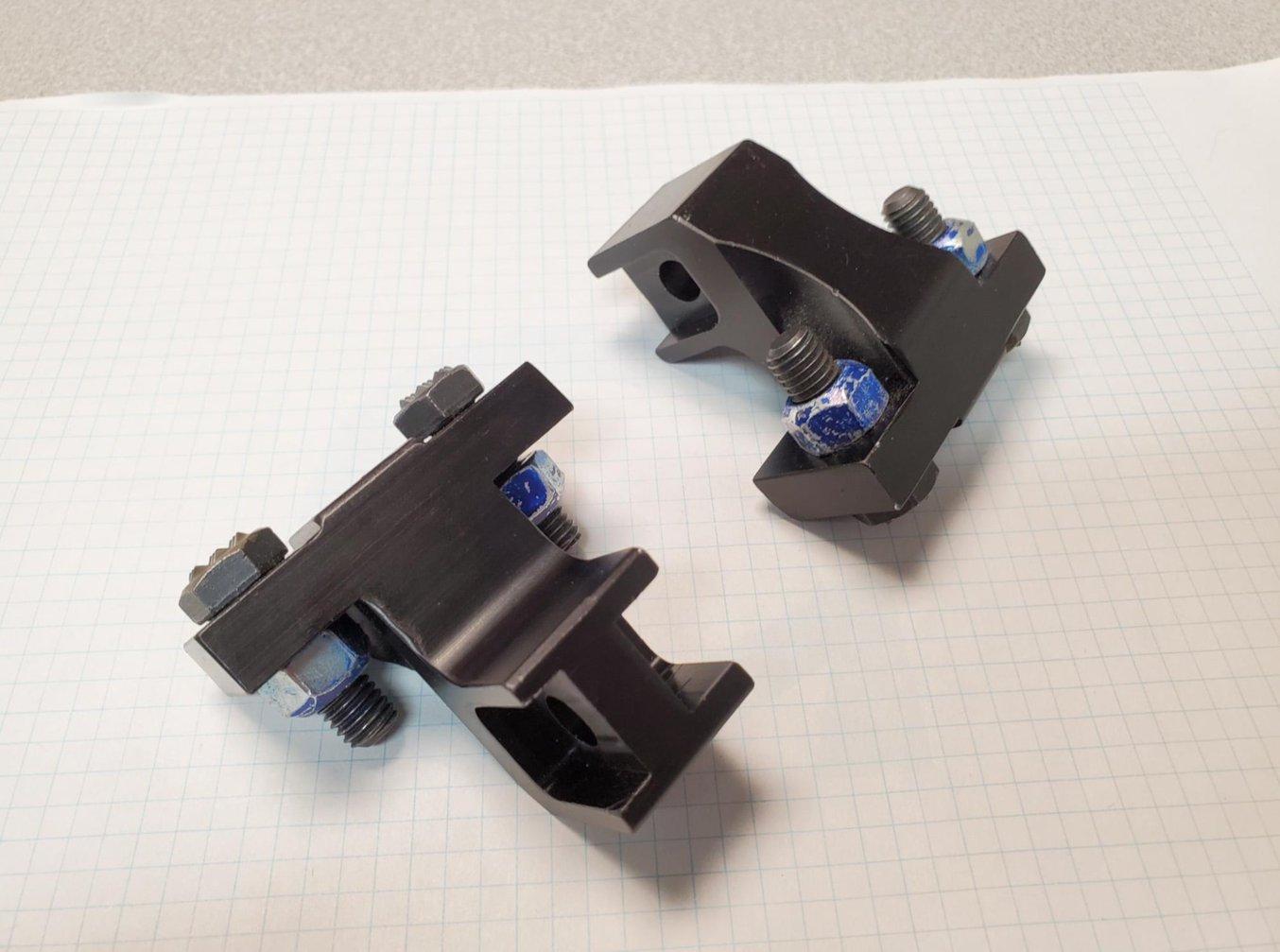
Die ursprünglich auf dem Pneumatikzylinder installierten Standardgreifer.
Im Allgemeinen sind die Greifer V-förmig geschnitten, um zylindrische Gegenstände oder Gegenstände mit unebenen Kanten aufzunehmen. Dieses Design schafft einen sicheren Kontakt mit dem Teil an jeweils zwei Stellen pro Seite mit einem weichen Berührungspunkt. Vor allem aber handelt es sich hierbei um ein einfaches und kostengünstiges Design – skalierbar für eine beliebige Anzahl von Prozessen.
Die Nachteile dieser Bauweise sind Kraftkonzentrationen, die sowohl den Greifer als auch den Gegenstand belasten und zu punktuellem Greiferverschleiß führen. Außerdem eignen sich V-Greifer nur für die abstrakte Positionierung eines Gegenstands. Somit benötigt man einen zweiten Positionierungsmechanismus für weitere Fertigungsprozesse.
3D-Drucktechnologie sorgt bei der Herstellung von Greifern für mehr Gestaltungsmöglichkeiten und schafft formgerechte Greifpunkte zur Kraftverteilung über eine größere Kontaktfläche.
In unserem Beispiel haben wir mithilfe eines 3D-Laserscanners von Creaform und der Modellierungssoftware VX Elements einen virtuellen 3D-Scan der Einspritzdüse vorgenommen und den Entwurf der Greifer darauf aufbauen lassen. Der Scan lieferte ein Bild mit komplexen Details und ersparte uns somit die mühsame Messung jeden Spalts, Zylinders und jeder Öffnung an der Einspritzdüse. Anschließend ließ sich der Scan in eine 3D-CAD-Software importieren und mithilfe enthaltener Formfunktionen in einen äußerst detaillierten Entwurf verwandeln.
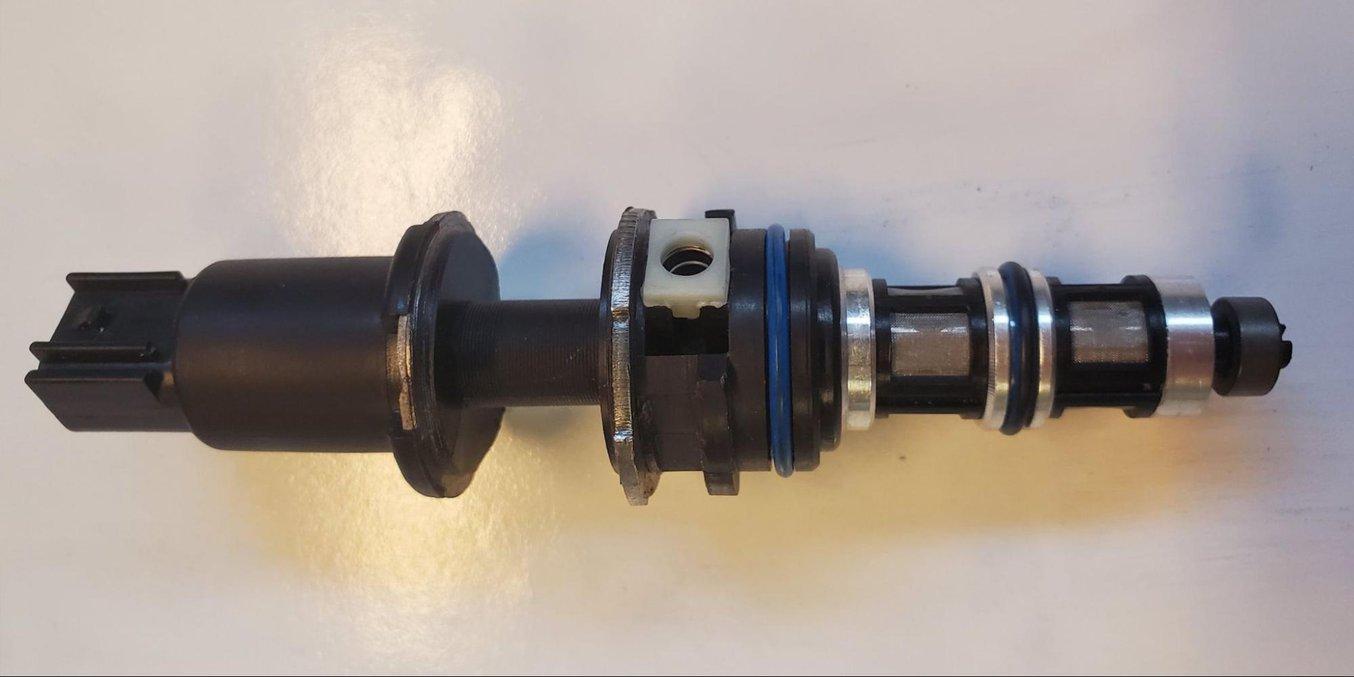
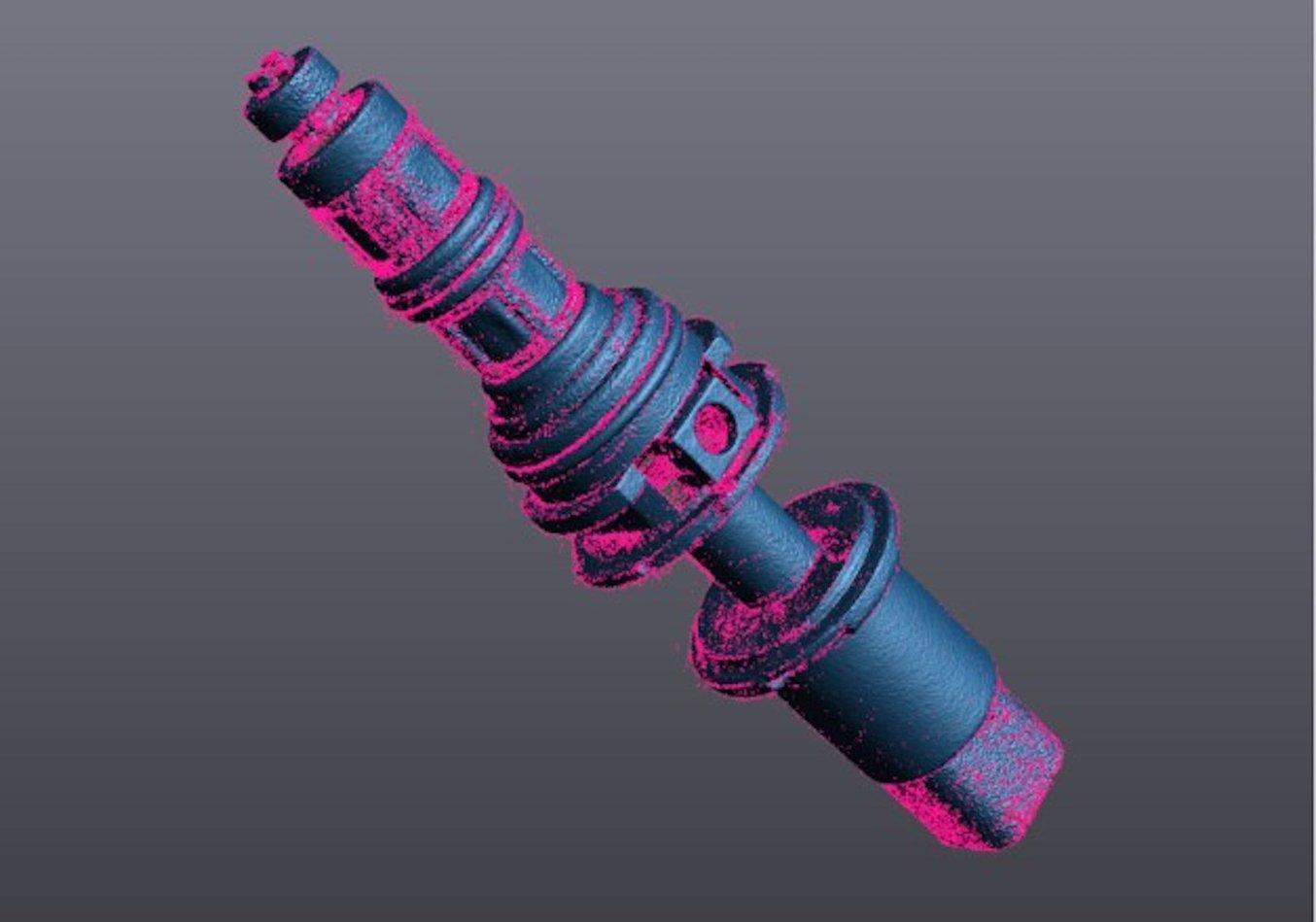
Die Einspritzdüse (oben) wurde 3D-gescannt und als Modell (unten) zur Erstellung der maßgefertigten Greifer verwendet.
Unser neues, detailliertes Radialgreiferdesign wird an den Dreharmen am Kolben eines pneumatischen Zylinders befestigt.
Der Prototyp des neuen Greifers wurde mit dem Form 3 hergestellt, einem SLA-3D-Drucker von Formlabs. Formlabs bietet mehrere Materialien für Rapid Prototyping, z. B. Draft Resin zur schnellen Prototypenfertigung. In unserem Fall kam Black Resin zum Einsatz, um den ersten Prototyp des Entwurfs zu entwickeln. Die beiden Greiferhälften wurden auf dem Form 3 in einem einzigen Arbeitsgang gedruckt. Der Materialwechsel ist einfach. Das beschleunigt den Weg von der ursprünglichen Idee zum Endprodukt.
Für die Fertigung der Endkomponente brauchte es ein haltbareres Material, das den Anforderungen der Produktionsumgebung standhält. Rigid 4000 Resin war daher das Material der Wahl für die fertigen Greifer. Dieses äußerst steife, glasgefüllte Polymermaterial bietet hohe Haltbarkeit, Steifigkeit und eine hochwertige Oberflächengüte der gedruckten Teile.
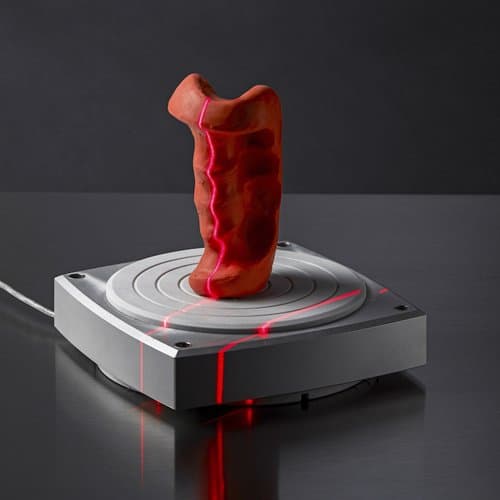
3D-Scannen für Reverse Engineering, Restaurationen und Metrologie
3D-Scan- und -Druckverfahren lassen sich zum Nachbau, zur Restauration, für Reverse Engineering, für verschiedene Messverfahren und viele weitere Anwendungen einsetzen. Laden Sie unser Whitepaper herunter oder sehen Sie sich unser Webinar an. So lernen Sie, wie Sie mit dieser Technologie Ihre eigenen Designprozesse verfeinern.
Ergebnisse
Die Entwicklung und der 3D-Druck der unregelmäßigen Greifer war ein voller Erfolg und sie funktionieren, wie erwartet. Die Leistungsfähigkeit der gedruckten Greifer ist den bisherigen Greifern weit überlegen.

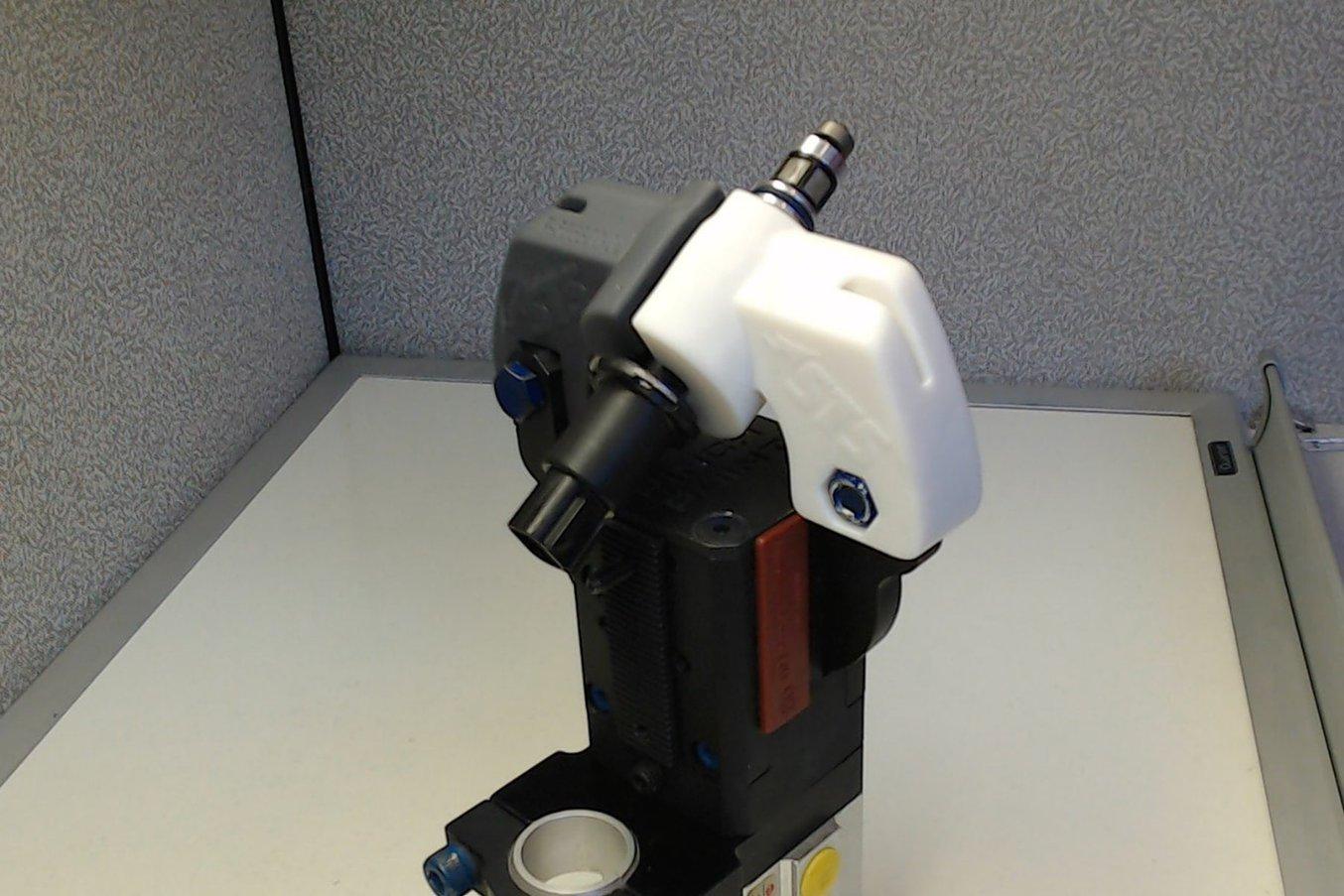
Die Baugruppe des Pneumatikzylinders inklusive der 3D-gedruckten Greifer, die die Einspritzdüse aufnehmen.
Folgende Vorteile ergeben sich aus den 3D-gedruckten Greifern:
-
Eine größere Greiffläche bei den Einspritzdüsen verringert die Kraftkonzentration an den Druckstellen und somit den Verschleiß des Greifers sowie Beschädigungen oder Kratzer an der Einspritzdüse. Dank des einzigartigen, vollumfassenden Designs bleibt der Greifer auch bei Verschleiß auf dem gewünschten Niveau funktionsfähig.
-
Da die Greifer in einer radialen Greifbewegung arbeiten, lässt sich das Spiel an den Innenkanten der Greifer in das Design integrieren, anstatt sie maschinell zu bearbeiten. Dadurch werden eckige Kanten in der Greifmulde vermieden und ein gleichmäßiger Griff und vollständiges Lösen der Einspritzdüse ermöglicht.
-
Die präzisen Greifer richten die Einspritzdüse in der gewünschten Position aus. Somit entfallen zusätzliche Geräte und Fertigungsstationen zur Ausrichtung der aufgenommenen Teile.
-
Dank des vollumfassenden Greiferdesigns ist zum Greifen der Einspritzdüse weniger Druck erforderlich. So werden geringere pneumatische oder hydraulische Druckanforderungen an die Materialhandhabungsgeräte gestellt.
-
Die Greifer eliminieren eine dünne Bauteilstrukturen und bieten ein einzigartiges Design zur Maximierung der Materialstärke. Dazu gehört auch eine Sechskantaussparung, die eine Sechskantmutter in die Baugruppe einschließt. Das erleichtert den Einbau.
-
Die Seriennummer oder Beschriftung des SLA-gedruckten Teils wird während des Druckvorgangs integriert, sodass Stanz- oder Ätzprozesse entfallen.
Fazit
Der Form 3 von Formlabs verfügt über eine große Auswahl an Druckmaterialien und ist eine hervorragende Alternative zu konventionellen Fertigungsverfahren für die Herstellung kundenspezifischer Komponenten, wie z. B. Fertigungshilfsmittel.
Die Komponenten sind haltbar, kostengünstig für detailliertere Entwürfe und können in einem Bruchteil der Zeit hergestellt und implementiert werden. Die automatisierte Fertigung von morgen wird aus hochdetaillierten Produkten bestehen, die mit CAD-Software entworfen und in 3D aus einer Vielzahl von Materialien gedruckt werden.
Mithilfe der Drucker von Formlabs und CAD-Software entwirft und konstruiert die STS Technical Group hochdetaillierte, unregelmäßige Komponenten für ihre Kunden.