Für Branchen, in denen die Arbeit auf – oder unter – dem Wasser stattfindet, wie Fischerei, Aquakultur oder Offshore-Windparks, sind die Dinge immer etwas komplizierter. Probleme in der Lieferkette, Reparaturen, Wartung und der tägliche Betrieb werden durch die sich ständig verändernde, oft unwirtliche Umgebung noch erschwert.
Da der 3D-Druck die Herstellung komplexer, individuell angepasster, wasserfester Teile ermöglicht, sind die Anwendungsmöglichkeiten hier nahezu unbegrenzt. Wasserfeste 3D-Druckteile werden als Endbauteile für Motoren, Forschungswerkzeuge, Propellerblätter, Ausrüstung für das Tiefseetauchen und vieles mehr eingesetzt. Neue Ideen gibt es zuhauf, aber für ein erfolgreiches Produkt braucht es auch das richtige Designverfahren, umfangreiche Tests und leistungsfähige Werkzeuge, damit sie in der rauen Umgebung unter der Wasseroberfläche einsetzbar sind.
Southern Ocean Subsea (SoSub), ein Entwickler und Hersteller von Unterwasser-Robotikanwendungen, kreiert schon seit Jahren Robotersysteme für Arbeiten unter Wasser. In Zusammenarbeit mit dem Formlabs-Partner ThingLab nutzt SoSub einen Form 3 und vier Form 3L, um komplexe Robotiksysteme zu erstellen.
SoSub-Gründer Kelsey Treloar und Ingenieur Miles Lewis haben so die Kosten und Durchlaufzeiten für die Entwicklung kundenspezifischer Lösungen wie ihrer ferngesteuerten Unterwasser-Fahrzeuge (ROVs) reduziert. Die Herstellung komplexer, wasserfester Robotikanwendungen wie der ihren wäre ohne additive Fertigung nahezu unmöglich. Mit dem 3D-Druck konnte das Team die Nachteile der traditionellen Fertigung umgehen, welche Startups den Erfolg in der Regel erschweren.
„Dank 3D-Druck stellt die Fertigung kein Hindernis mehr dar. Die einzige Beschränkung ist unsere eigene Vorstellungskraft – wir müssen uns interessante Lösungen für knifflige Probleme einfallen lassen. Die Frage lautet also nicht, ob es machbar ist, sondern ob wir die Lösung finden. Für moderne Ingenieure ist das ein Privileg“, so Lewis.
Wartung und Marktanpassung
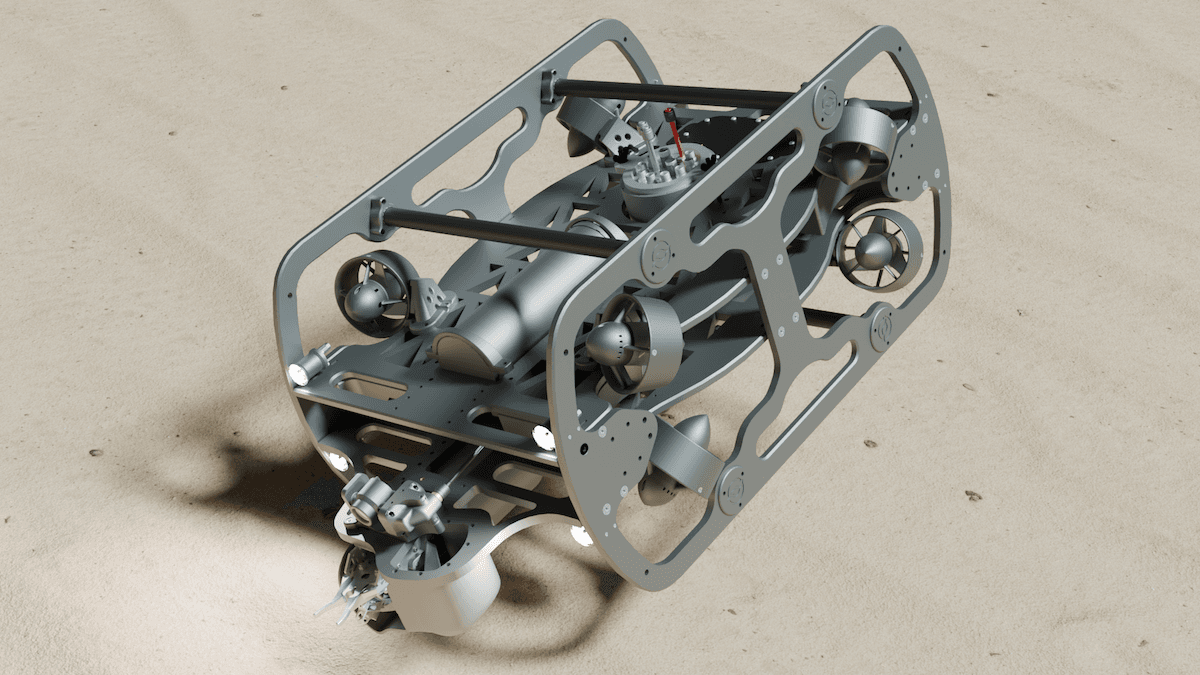
Das ROV von SoSub wurde zunächst als Lösung für ein Problem entwickelt, das Treloar unzählige Male begegnete – nämlich dass die Reparatur kommerzieller Fischernetze langwierig und potenziell gefährlich war. Es musste eine robotergestützte Lösung geben.
Treloar hatte ursprünglich nicht vor, ROVs und neue Unterwassertechnologien zu entwickeln. Anfangs begann SoSub als Wartungs- und Reparaturbetrieb für Fischereiausrüstung und Unterwassermaschinen. Treloar bemerkte jedoch, dass das Team immer wieder zu Reparaturen von industriellen Fischernetzen und -geräten gerufen wurde. Dabei handelte es sich um arbeitsintensive Einsätze, bei denen Tauchtrupps die Netze unter Wasser von Hand wieder zusammennähen mussten. Manuelle, sich wiederholende Arbeiten wie diese werden an Land schon seit Jahren von Robotern erledigt, aber unter Wasser sind derartige Einsätze komplexer und kostspieliger. Bestehende Lösungen können sechsstellige Beträge kosten und sind in der Regel für gut finanzierte Forschungsexpeditionen reserviert.
Treloar begann zu experimentieren – er eignete sich CAD-Kenntnisse an und erkundete verschiedene Möglichkeiten, die von ihm entworfenen Teile wasserfest zu fertigen. „Wir begannen unsere Suche nach kostengünstigem Produktionslösungen, die für ein Unternehmen wie uns wirtschaftlich sein können. Zuerst haben wir FDM-3D-Drucker getestet und dann andere Möglichkeiten ausgelotet“, berichtet Treloar.
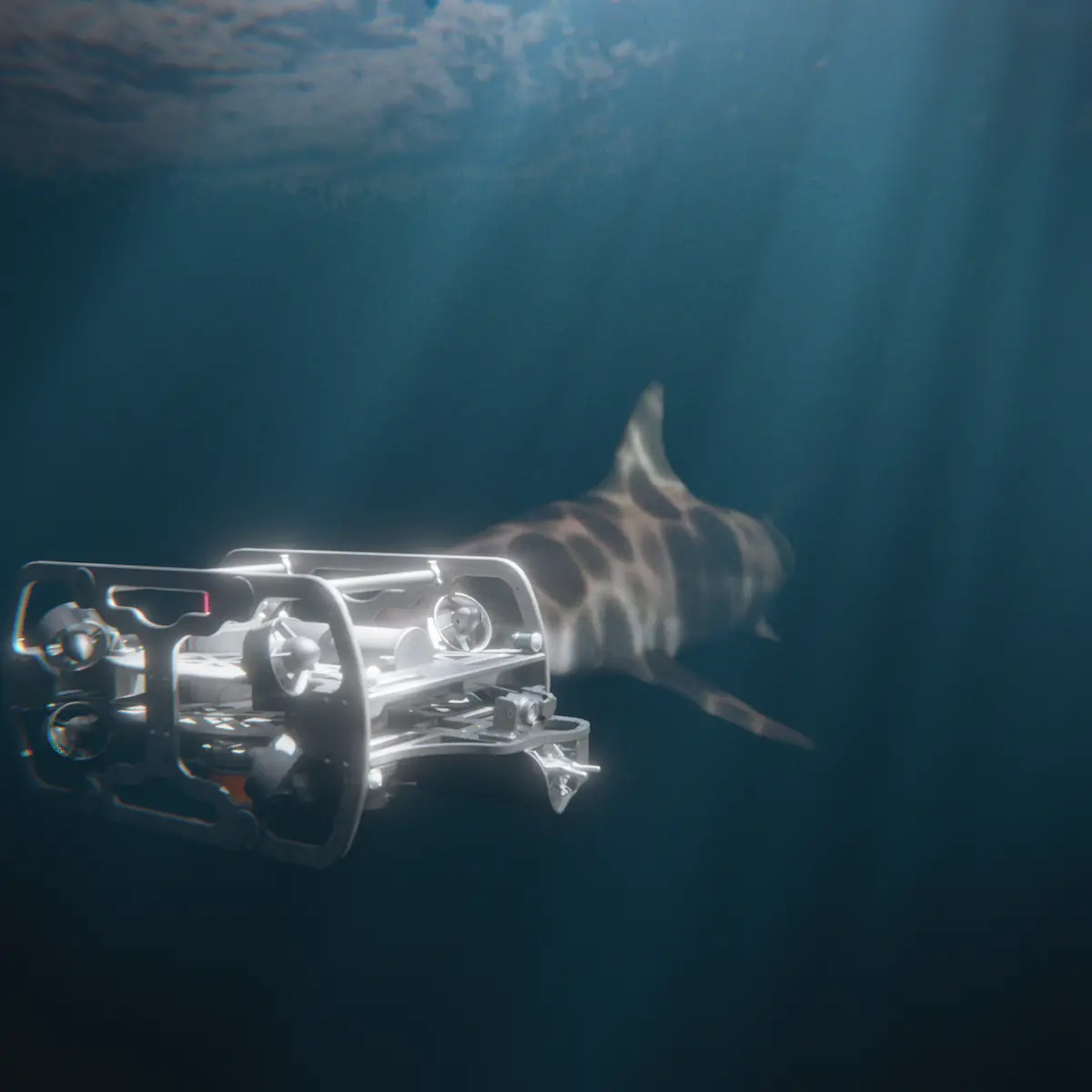
Das Reparieren von Netzen kann gefährlich sein – Robotiksysteme begrenzen das Risiko für menschliche Taucher, und 3D-Druck macht diese Systeme für die Fischereikunden von SoSub kosteneffizient.
Die richtige Technologie
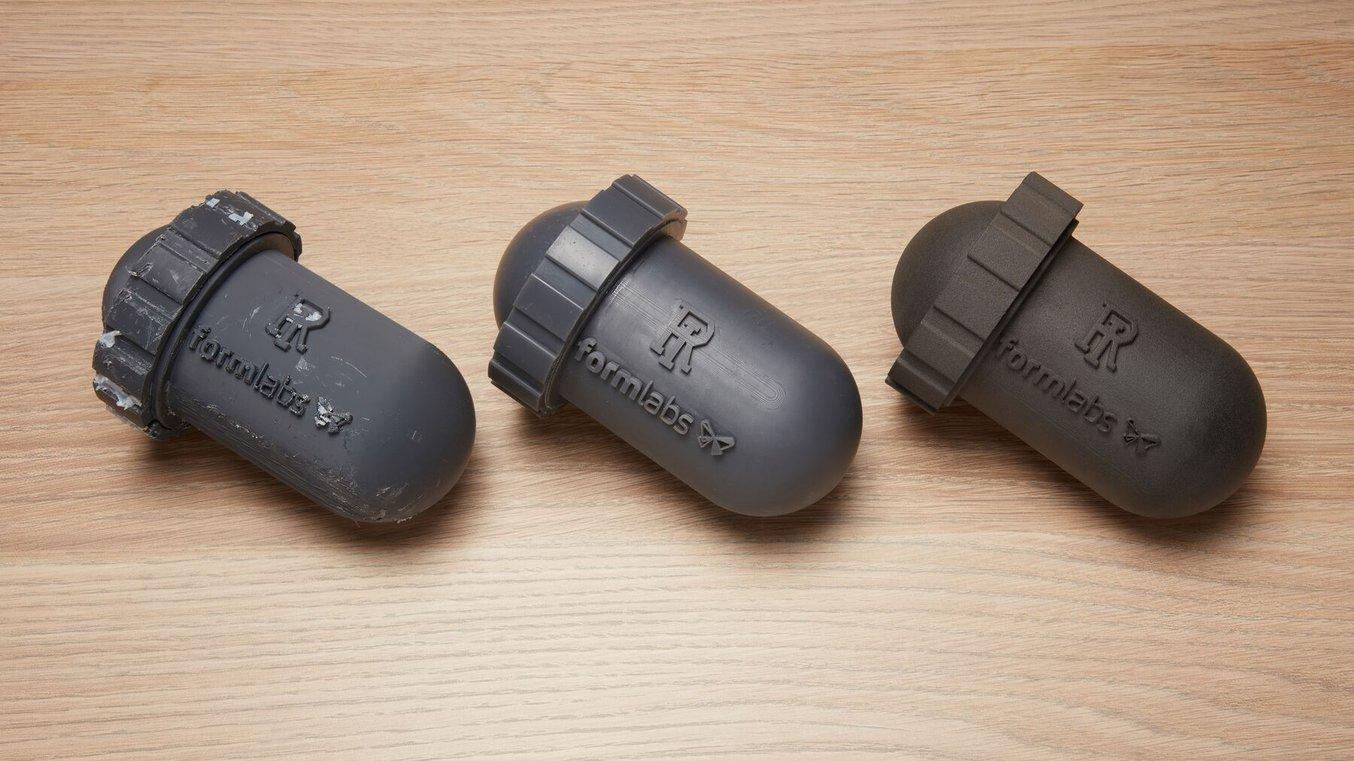
Mit FDM-3D-Druck hergestellte Gehäuse (wie das links abgebildete) sind nicht wasserdicht, da FDM-3D-Druckteile mikroskopisch kleine Lücken zwischen den Filamentschichten aufweisen.
Bei der FDM-Technologie traten von Anfang an Schwierigkeiten auf. FDM-Drucker können keine wasserdichten Teile erstellen – durch mikroskopisch kleine Lücken zwischen den Schichten, die nicht chemisch miteinander verbunden sind, kann Wasser eindringen, vor allem, wenn der Druck mit steigender Tiefe zunimmt.
Glücklicherweise hatte ein Kollege Erfahrung mit SLA-3D-Druckern. „Er war fest überzeugt, dass der Kunstharzdruck gut genug ist, also haben wir den Umstieg gewagt und es hat funktioniert. Nichts anderes, was ich bisher gesehen habe, ist zu so etwas in der Lage, und wir hätten es nicht geschafft, diese Teile auf andere Weise zu entwickeln“, berichtet Treloar.
Seit dem Einstieg in den Kunstharz-3D-Druck hat SoSub seine 3D-Druckerflotte auf vier großformatige SLA-Drucker vom Typ Form 3L und ein Desktop-Gerät des Typs Form 3 erweitert. „Die Drucker haben den Grundstein dafür gelegt, dass wir mit dieser Arbeit überhaupt beginnen konnten“, meint Lewis.
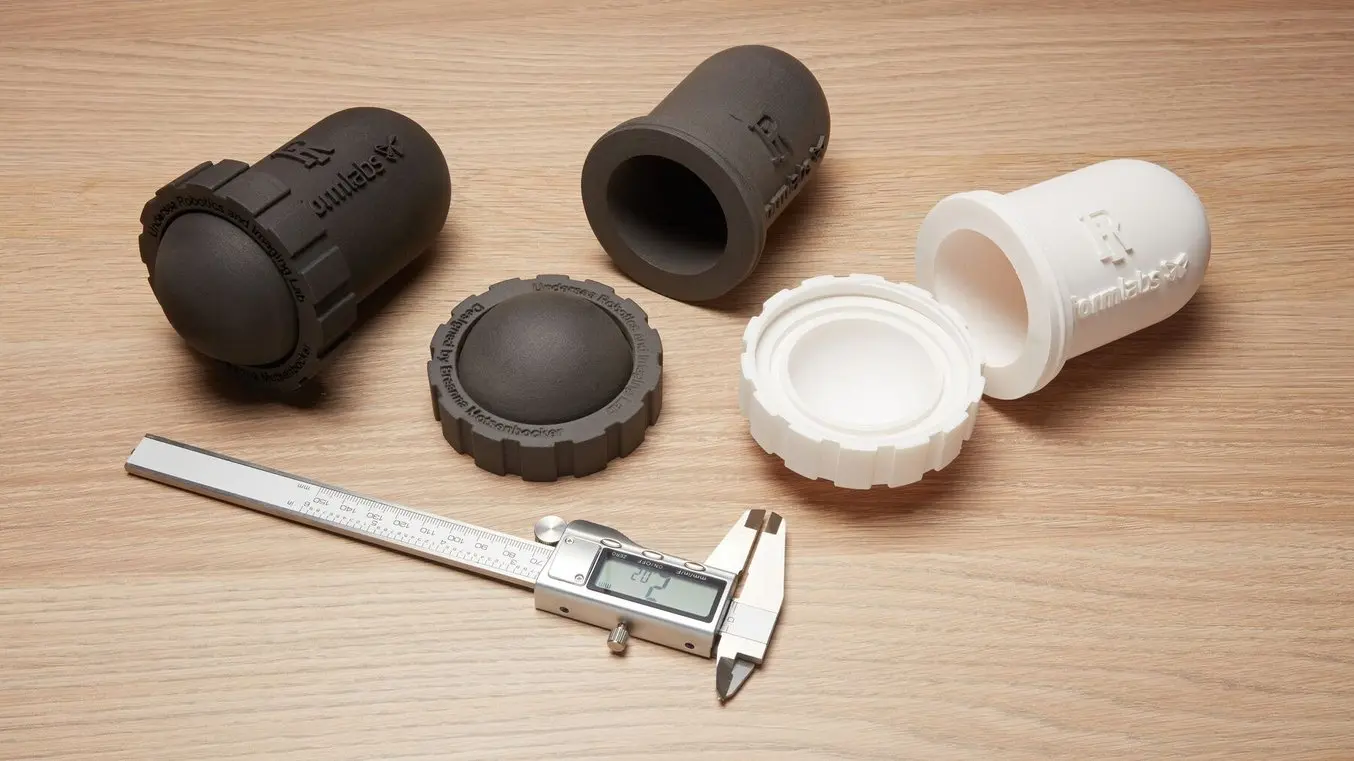
3D-Druck wasserdichter Behälter und Ergebnisse von Druckprüfungen
In diesem Whitepaper stellen wir die Testergebnisse vor und geben klare Richtlinien zum kostengünstigen 3D-Druck individueller wasserdichter Behälter.
Unterwasser-Bauteile: Der Herausforderung gewachsen
Unterwasser-Robotikanwendungen erfordern Teile, die wiederholten Belastungen standhalten, enge Toleranzen einhalten und eine präzise Maßgenauigkeit aufweisen, damit sie in Baugruppen verbaut werden können, welche mit O-Ringen abgedichtet werden und keinerlei Lücken durch Unebenheiten, Grate, Linien oder Druckartefakte aufweisen dürfen. Teile, die diesen Spezifikationen entsprechen, werden traditionell aus Metall gefräst oder mittels Gussverfahren hergestellt, aber die Auslagerung an Dienstleister ist teuer und kann Wochen oder Monate beanspruchen.
3D-Druck bietet Lewis und Treloar die Möglichkeit, Teile zu entwerfen, zu prototypisieren und zu testen, die spritzgegossene oder sogar zerspante Kunststoffe imitieren können.
„Wenn man sich die ROV-Branche anschaut, werden die meisten Teile maschinell bearbeitet oder spritzgegossen, was mit langen Durchlaufzeiten und übermäßig hohen Preisen einhergeht. Da es sich um einen Nischenmarkt handelt, können die Bauteile Tausende von Dollar kosten. Einer der Wettbewerbsvorteile von SoSub ist, dass wir mit 3D-Druck sehr schnell, aber auch sehr kostengünstig arbeiten können.“
Kelsey Treloar, Gründer und Geschäftsführer, SoSub
Die Materialien von Formlabs liefern nicht nur die für Endbauteile erforderlichen glatten Oberflächen, sondern bewältigen auch den Druck beim Einsatz unter Wasser. SoSub hat die Wasserdichtigkeit von 3D-gedruckten Gehäusen aus Rigid 10K Resin, Tough 2000 Resin und Grey Resin in Hunderten von Metern Tiefe bewertet. „Wir haben einen kleinen, handelsüblichen Server für 100 Dollar genommen und ein Gehäuse 3D-gedruckt. Es hat unsere Erwartungen deutlich übertroffen, und dabei ging es 600 Meter in die Tiefe. Wir können einen für 600 Meter tiefe geeigneten Unterwasser-Server-Aktuator in einem halben Tag herstellen“, berichtet Lewis. Ein weiteres Gehäuse aus Rigid 10K Resin hat sich auch in über 1000 Metern Tiefe bewährt.
Ein großer Vorteil des Arbeitsablaufs mit Formlabs ist die Schätzung der mechanischen Leistung von Formlabs-Kunstharzen in der Software Fusion 360 von Autodesk. „Für die technischen Materialien von Formlabs werden die Daten für die FEI-Analyse zur Simulation veröffentlicht. Das ist für andere Materialien nicht verfügbar. Wenn ein Kunde eine Schätzung der Festigkeit seines Teils anfordert, können wir das liefern und eine Aussage darüber treffen, ob das Teil der Belastung standhält. Danach können wir Tests durchführen, um das zu bestätigen“, erklärt Lewis.
Vereinfachung durch mehr Komplexität
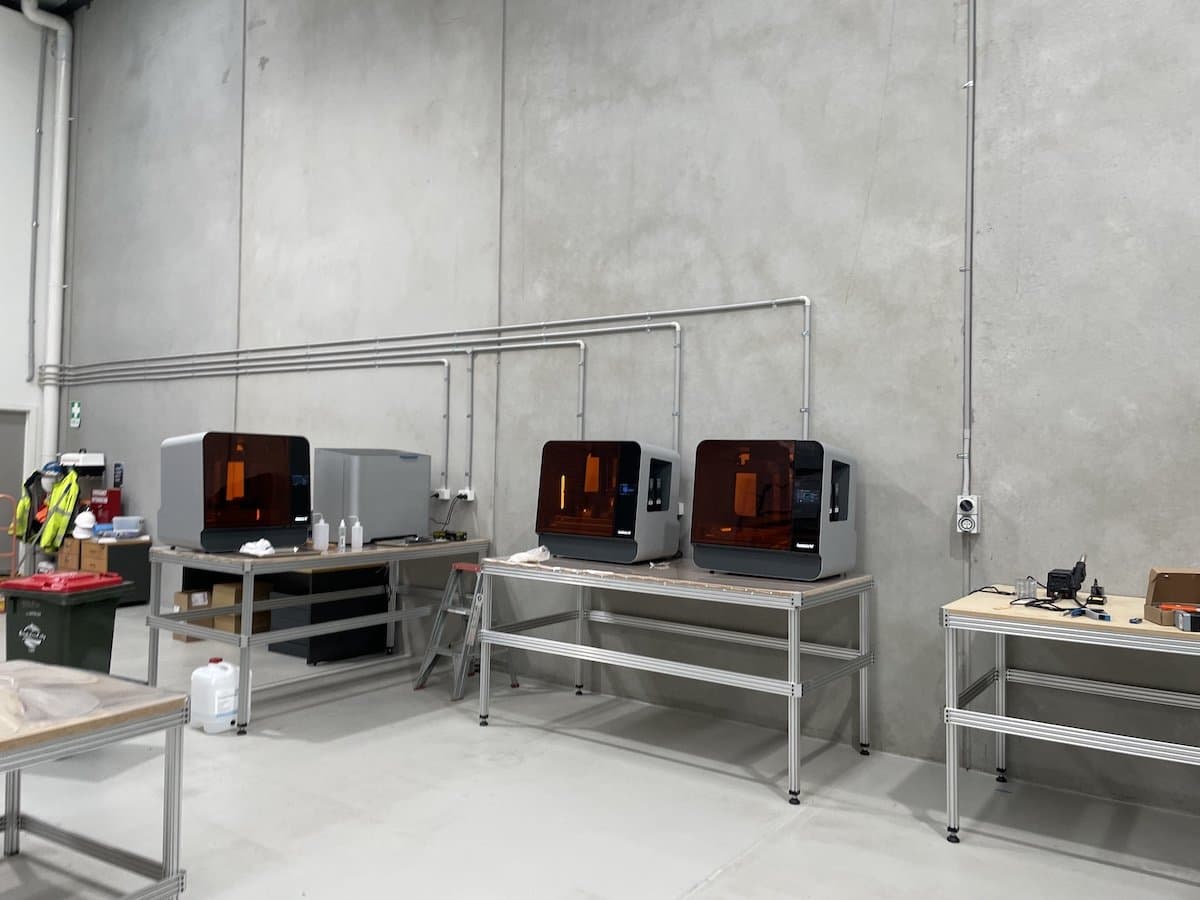
Mit seiner Flotte von Form 3L kann SoSub wasserdichte und maßgenaue Endbauteile entwerfen, testen und produzieren.
Abgesehen von den reduzierten Kosten und Durchlaufzeiten erlaubt der 3D-Druck es SoSub auch, Teile zu entwickeln, die aufgrund ihrer Komplexität nicht mit herkömmlichen Methoden gefertigt werden können. Dies hat ihre Herangehensweise an die Erstellung neuer Teile revolutioniert. Um die Anzahl der separaten Bauteile in einer Baugruppe zu reduzieren und so die Handhabung und den Betrieb zu vereinfachen, schneidet SoSub seine Designs speziell auf die additive Fertigung zu. „Teile, die man traditionell durch Zerspanung fertigen würde, wären mit solchen Designs völlig unmöglich umzusetzen oder extrem teuer. Man muss also vollkommen umdenken und Teile so kompliziert wie möglich gestalten, damit sie in einem Stück gedruckt werden können. Man kann acht Fertigungsprozesse einfach eliminieren, was sowohl die Fertigung als auch den Designprozess schneller und einfacher macht“, fasst Lewis zusammen.
Squid Lock: 3D-Druck vom Design bis zur Endverwendung

Tough 2000 Resin hat eine hohe Festigkeit und eine hervorragende Maßgenauigkeit – das macht es perfekt für die wasserdichten Gehäuse am Hauptteil des Squid Locks.
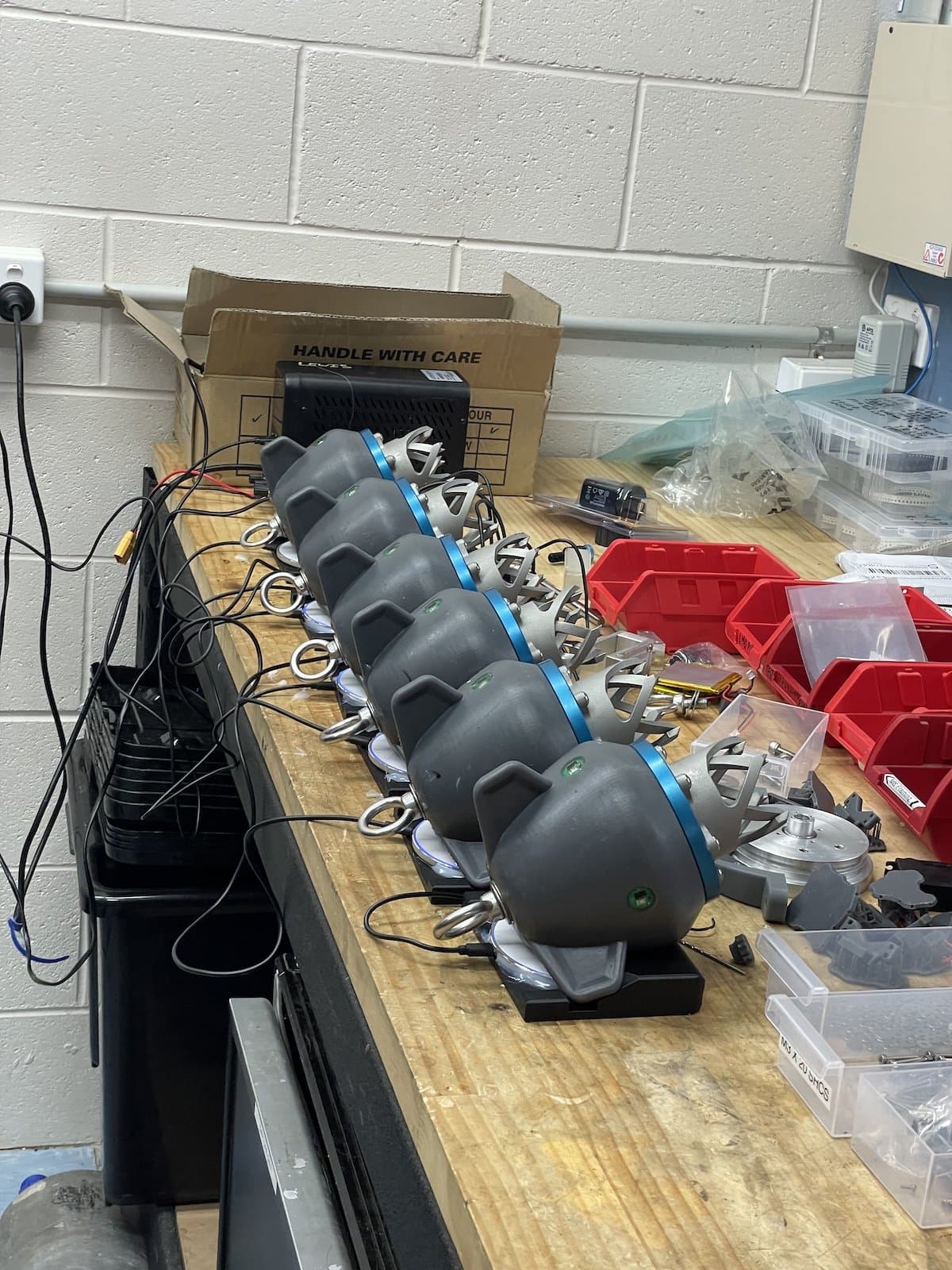
Das zusammengebaute Squid Lock besteht aus einem Gehäuse, das auf dem Form 3L aus Tough 2000 Resin 3D-gedruckt wurde, und 3D-gedruckten „Zähnen“ zur Fixierung am Netz.
Der 3D-Druck hat es SoSub ermöglicht, kreative Lösungen für komplizierte Probleme zu finden. Das SoSub-Team wurde zu den Offshore-Fischfarmen vor Melbourne gerufen, um ein ROV für einen sehr speziellen Auftrag zu entwickeln. Es müssen große Fischernetze von den Booten gezogen und im Wasser ausgebreitet werden. Dies ist eine mühsame und repetitive Aufgabe, die bislang von Tauchern erledigt wurde. Die Schwierigkeit bestand darin, einen Aktuator zu designen, der mit dem im Wasser schwimmenden Netz genauso geschickt agiert wie menschliche Hände und es ausreichend festhält. Die Lösung war SoSubs „Squid Lock“, ein Roboterteil, das auf ein Netz zu schwimmt, sich in das schwimmende Gewebe einhakt und es dann mit einer Kraft von etwa 400 kg wegzieht, ohne es zu zerreißen oder sich zu lösen.
„Wir sind innerhalb von eineinhalb Monaten von einem sehr groben Konzept zu einem Endprodukt gelangt, indem wir Test-Prototypen der Zähne aus Grey Resin und Prototypen des Gehäuses aus Tough 2000 Resin 3D-gedruckt haben. Der 3D-Druck gibt uns die Gewissheit, dass wir innerhalb einer kurzen Durchlaufzeit tatsächlich etwas schaffen können. So können wir beim Design mehr Risiken eingehen“, erklärt Treloar.
SoSub lieferte innerhalb von zwei Monaten acht voll funktionsfähige Squid Locks an den Betrieb. Das endgültige Design beinhaltet 3D-gedruckte Zähne aus Metall, verfügt aber immer noch über das Gehäuse aus Tough 2000 Resin. „Grey Resin eignet sich gut für Details, und Tough 2000 Resin ist ein ziemlich starkes Material für Teile mit dem Detailgrad von Grey Resin, aber mit höherer Festigkeit“, urteilt Lewis.
Digitale Pläne für die Zukunft
SoSub hat gerade erst begonnen, auf die überwältigende Nachfrage nach individualisierbaren Maschinen für die maritime Branche zu reagieren. In Zukunft wollen sie nicht mehr nur End-to-End-Lösungen anbieten. „Irgendwann wollen wir Produktionsvolumen von Hunderten von Einheiten pro Jahr erreichen, und uns dabei weiterhin auf 3D-Druck stützen. Wir können Kunden empfehlen, eigene 3D-Drucker anzuschaffen, und ihnen dann die Dateien verkaufen, sodass sie alles direkt vor Ort herstellen können“, sagt Treloar. Im Moment baut SoSub die Nachfrage nach vollständig 3D-gedruckten Lösungen noch aus, aber Treloar und Lewis sind zuversichtlich, dass der 3D-Druck an neue und kompliziertere Projekte angepasst werden kann. „Wir verwenden es für alle möglichen Dinge. Nicht nur für den ursprünglichen Zweck, für den wir die Drucker gekauft haben, sondern es schafft auch ganz neue Ideen“, meint Treloar.
Wenn Sie neugierig sind, wie man wasserfeste Gehäuse 3D-druckt, laden Sie unser Whitepaper herunter. Um den Form 3L kennenzulernen, besuchen Sie unsere Website.