Globaler Automobilzulieferer Brose nutzt SLS 3D-Druck, um Endverbrauchsteile herzustellen
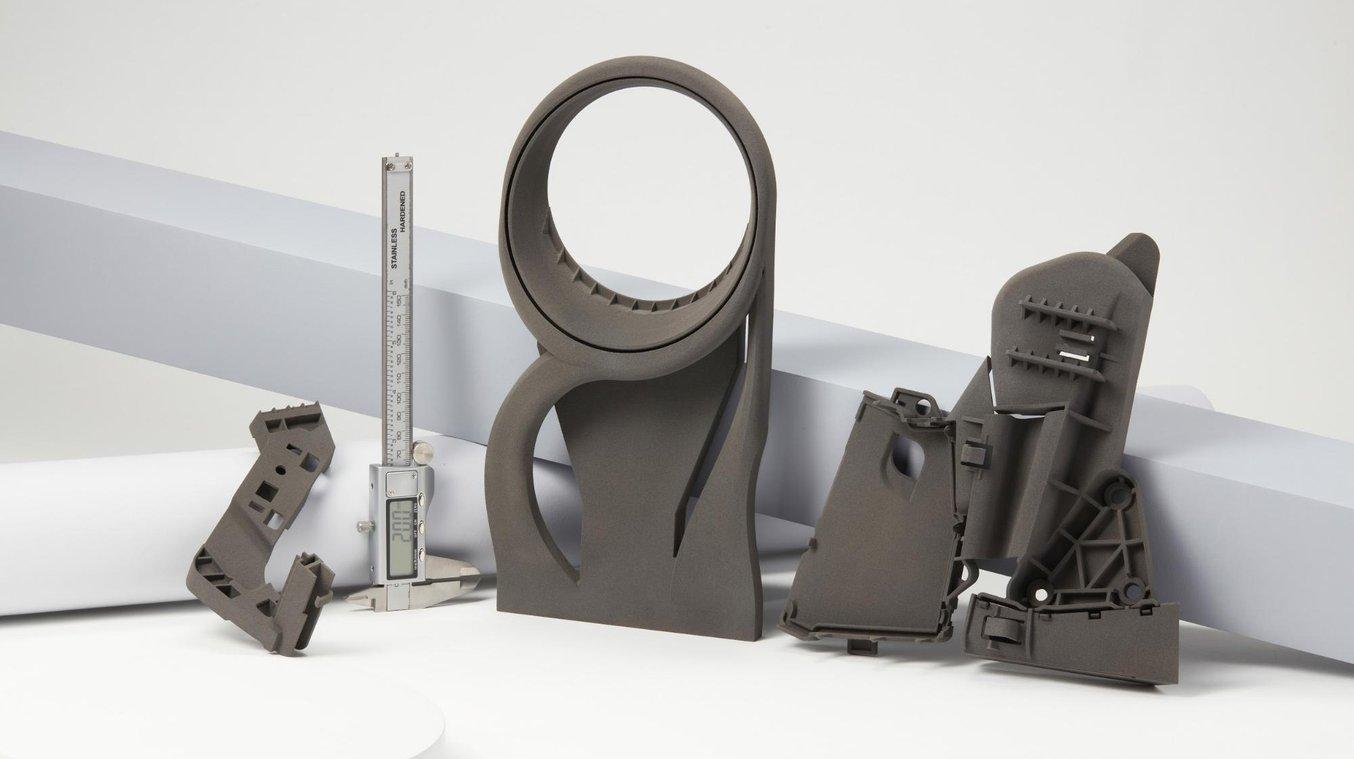
Wenn Sie schon einmal in einem Auto gesessen haben, haben sie höchstwahrscheinlich auch mit einem der Produkte von Brose interagiert. Mit 25 000 Mitarbeitern in 24 Ländern ist das Unternehmen einer der größten Tier-1-Automobilzulieferer in Familienbesitz. Es arbeitet mit 80 Automarken, über 40 Zulieferern und 50 E-Bike-Herstellern zusammen.
Jedes zweite neue Fahrzeug auf der Welt verfügt über mindestens ein Brose-Produkt. Dazu gehören verschiedene mechatronische Komponenten und Systeme, wie Sitzstrukturen, Türkomponenten und verschiedene Elektromotoren und Antriebe.
Als eines von Deutschlands innovativsten Unternehmen befindet sich Brose in einer hervorragenden Ausgangssituation, um additive Fertigung (AM) in seine Produkte und Fertigungsabläufe zu integrieren. Brose nutzt verschiedene AM-Technologien für die Fertigung von Prototypen, Werkzeugen und Vorrichtungen. Als nächstes Ziel wird die Serienfertigung angestrebt. Das neueste Mitglied Ihrer Druckerflotte, der Fuse 1, der erste industrielle Benchtop-3D-Drucker für selektives Lasersintern (SLS) von Formlabs, ist eines der Werkzeuge, die das Unternehmen dabei unterstützen wird.
Lesen Sie weiter und erfahren Sie mehr von Christian Kleylein, Technologist für AM Polymer Series Manufacturing bei Brose, der über seine Erfahrung mit dem neuen Gerät berichtet und darüber, wie das Unternehmen plant, 3D-Druck für die Serienfertigung einzusetzen.
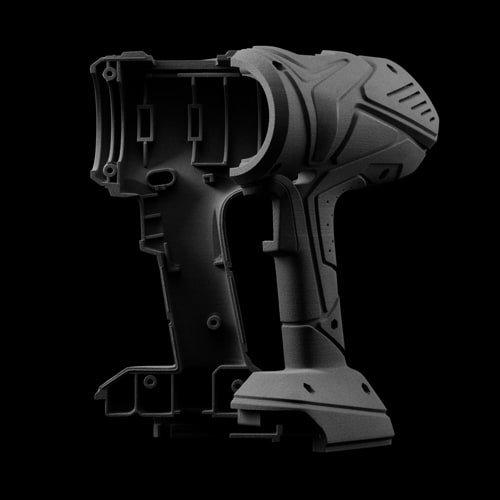
Einführung in den 3D-Druck mit selektivem Lasersintern (SLS)
Suchen Sie nach einem 3D-Drucker, mit dem Sie starke, funktionsfähige Teile herstellen können? Laden Sie unser Whitepaper herunter, erfahren Sie, wie SLS-Druck funktioniert und wieso es ein beliebtes 3D-Druckverfahren für funktionales Prototyping und die Produktion von Teilen für die Endverwendung ist.
Einsatz des Fuse 1 in einer industriellen Umgebung
Die additive Fertigung ist eine der neueren Kernkompetenzen von Brose. Das AM-Zentrum in Deutschland ist ein One-Stop-Shop für Prototypenfertigung, Prozessentwicklung, Materialentwicklung und Validierung und stellt Teile für die ganze Welt bereit.
Das Zentrum begann vor über zehn Jahren mit seinem ersten 3D-Drucker für Schmelzschichtung (FDM), hat seine Kapazitäten seitdem jedoch auf fast alle AM-Prozesse auf dem Markt erweitert, von Stereolithografie (SLA) über Jetting-Prozesse, selektives Lasersintern bis hin zu einem großen Maschinenpark an 3D-Druckern.
Zur Druckerflotte von Brose gehören verschiedene SLS-Systeme, von kleinen Desktop-Geräten hin zu den größten herkömmlichen Industriedruckern. Das Unternehmen hat umfangreiche Erfahrung mit dieser Technologie und gehörte zu den ersten Anwendern des Fuse 1 in Europa.
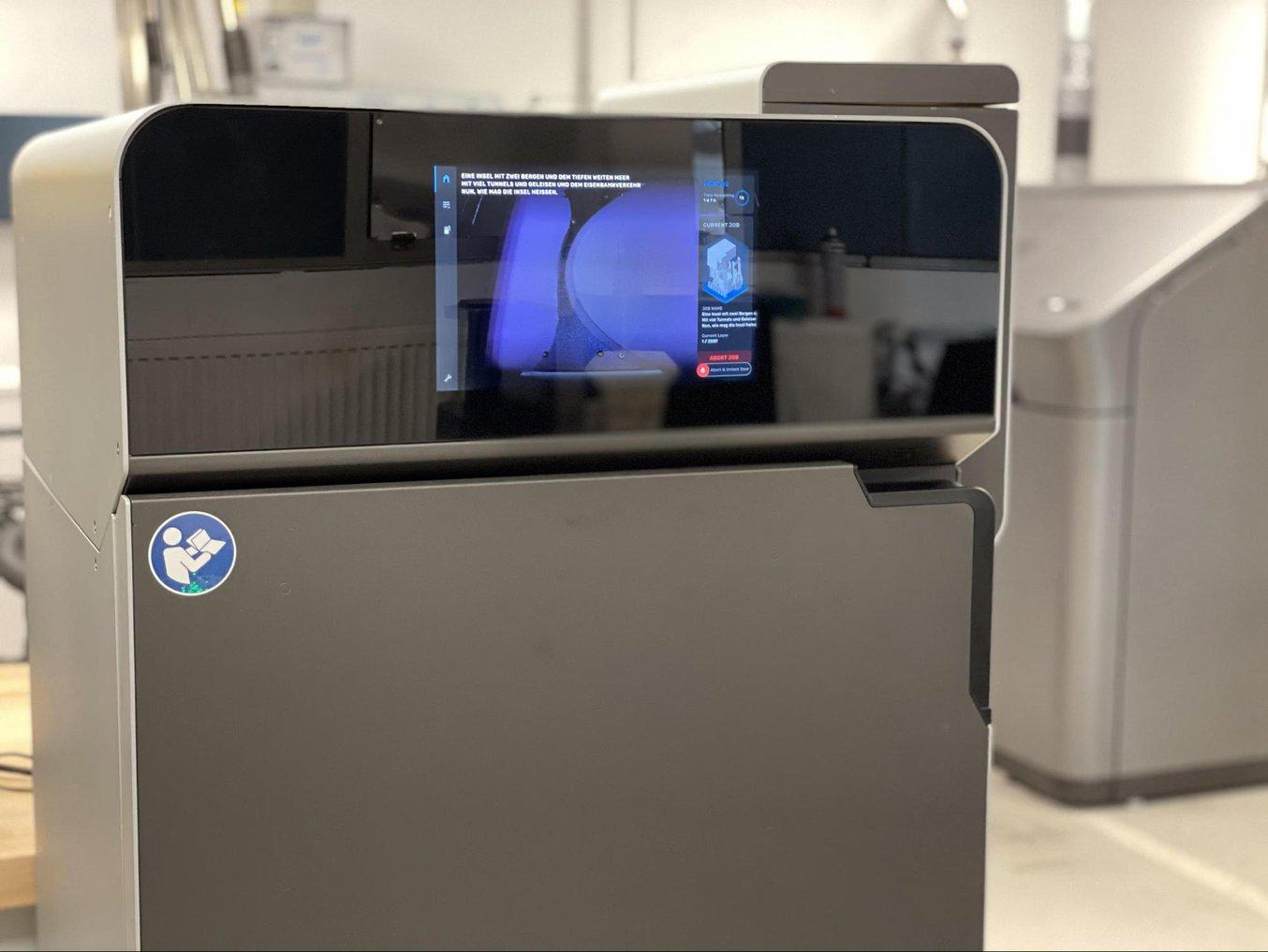
Das AM-Zentrum von Brose bietet fast jeden 3D-Druckprozess auf dem Markt, darunter auch den neuen Fuse 1.
Es kann eine Woche dauern, bis ein größeres Gerät eingerichtet ist und läuft, doch die Einrichtung des Fuse 1 klappte bei Kleylein im Handumdrehen.
„Die Einrichtung ist sehr einfach. Wenn man einen geschlossenen Raum mit Klimatisierung hat, kann man im Grunde loslegen. Er benötigt nicht viel Platz, was sehr gut ist. Auch ist keine wirkliche Kalibrierung erforderlich; man muss nur sicherstellen, dass er eben ist. Man schließt ihn an, startet den Einrichtungsvorgang und druckt noch am selben Tag“, so Christian Kleylein.
„Der Lernprozess ist problemlos. Der erste Druck ist wahrscheinlich auf Anhieb ein Erfolg. Und dann kann man Feinabstimmungen vornehmen und das Gerät kennenlernen.“
Christian Kleylein
„Wir haben den Fuse 1 sehr umfangreich getestet. Wir drucken viele Teile mit der minimalen Dicke sowie sehr dünne und sehr lange [Designs]. Beim Testen der Teile stellten wir fest, dass, auch wenn es zu Abweichungen bei den Abmessungen kam, diese Abweichungen immer einheitlich waren. Wenn man den Prozess also einmal optimiert hat, erhält man hochgradig maßgenaue Teile“, sagt Kleyelein.
Das Team führte viele Drucke auf dem Fuse 1 durch, um seine Grenzen zu erproben, von kurzen Drucken über Nacht von ca. 12 Stunden bis hin zu vollständig gefüllten Konstruktionskammern mit mehr als 1000 kleinen Teilen, die vier Tage in Anspruch nahmen.
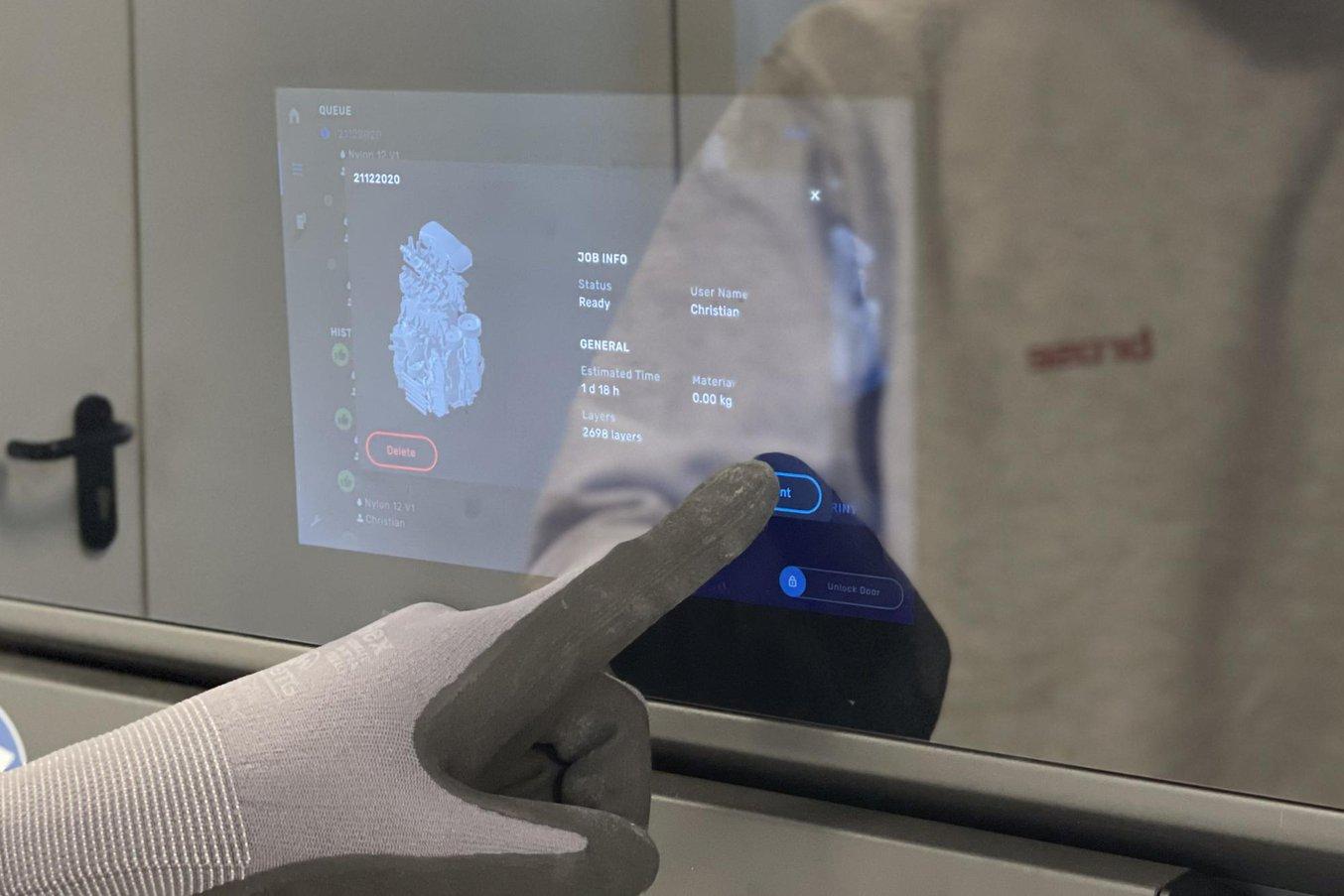
Beim selektiven Lasersintern sind keine Stützstrukturen notwendig, da nicht gesintertes Pulver das Teil während des Drucks umgibt. Für den Druck können mehrere Teile eng aneinander angeordnet werden, um den verfügbaren Raum optimal zu nutzen.
„Die Oberflächenbeschaffenheit ist sehr schön, sehr glatt, man sieht nur sehr wenige Schichten, wodurch man die Teile verwenden kann, wenn sie nach der Entnahme aus dem Drucker mediengestrahlt wurden, um die letzten Pulverreste zu entfernen. Man kann sehr feine Details herstellen. Beispielsweise erhält man beim Drucken von Zahnrädern sehr schöne runde Teile“, berichtet Kleylein.
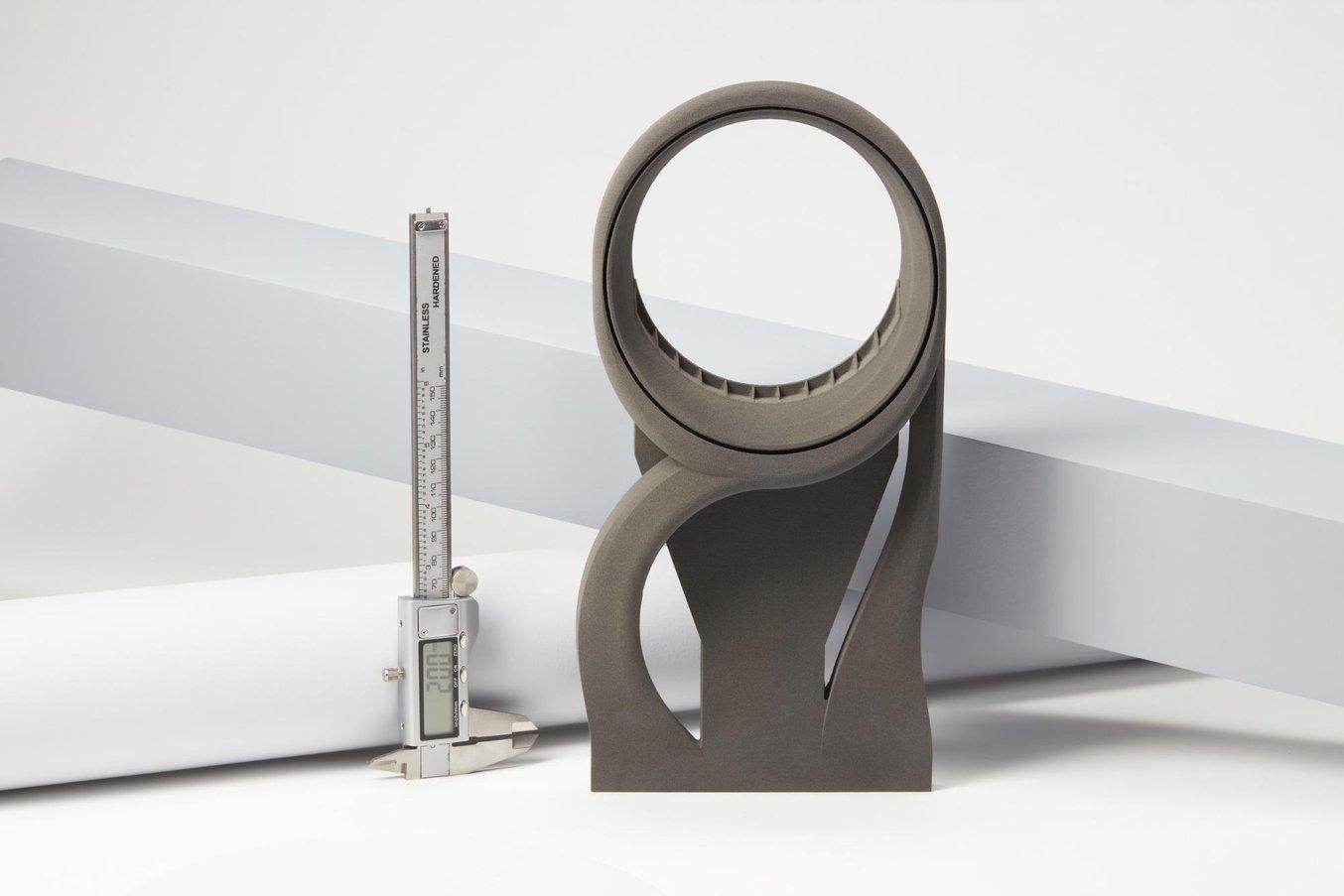
End-of-Line-Testausrüstung für Brose-Maschinen bei der Montage.
Mit dem Formlabs Fuse 1 soll die Lücke zwischen traditionell-industriellen SLS-Druckern und kostengünstigeren Druckern in kleinerem Format geschlossen werden: Er bietet hohe Qualität, kompakte Abmessungen und einen umfassenden, vereinfachten Arbeitsablauf zu einem Bruchteil der Kosten herkömmlicher industrieller SLS-Systeme.
„Er lässt sich mehr mit industriellen Druckern als mit Desktop-Geräten vergleichen. Dank dem Faserlaser hat Formlabs sein eigenes optisches Scannersystem entwickelt und der Laserstrahl wird korrekt umgelenkt“, so Kleylein.
„Es ist ein Gerät. Es fühlt sich nicht an wie ein Spielzeug, sondern wie ein richtiges Arbeitswerkzeug. Wenn man die Tür öffnet, macht es einen industriellen Eindruck, und alles funktioniert. Im Testing[-Team] sind alle sehr zufrieden. Man kann ihn ganz leicht in einer industriellen Umgebung einsetzen.“
Christian Kleylein
Man könnte denken, dass sich für Automobilteile größere Drucker besser eignen, aber Kleylein findet, dass das Fertigungsvolumen des Fuse 1 für die meisten Designs reicht.
„80 Prozent der Teile, die wir drucken, sind etwa faustgroß; das ist die Maximalgröße. So können wir alle diese Teile mit dem Fuse 1 drucken. Es gibt ein paar Teile, die in der Mitte liegen, und der Rest ist wirklich groß“, erklärt Kleylein.
„Die Druckgeschwindigkeit ist gut und lässt sich durch Optimierung wahrscheinlich weiter beschleunigen. Aber für den Anfang ist es eine gute Druckgeschwindigkeit, und man hat das richtige Fertigungsvolumen für bestimmte Anwendungen“, so Kleylein weiter.
Teil des Ökosystems des Fuse 1 ist der Fuse Sift, eine Nachbearbeitungsstation, die Teileentnahme, Pulverrückgewinnung, Lagerung und Mischen in einem einzigen freistehenden Gerät kombiniert.
„In der Vergangenheit musste man bei bestimmten Geräten die Nachbearbeitungsausrüstung dazukaufen. Das haben Leute selbst entwickelt, sogar das Mischen. [Fuse Sift] ist ein schönes integriertes System. Man hat lauter Lüfter, die den Staub abführen und so muss nicht viel unpraktische Schutzausrüstung getragen werden. Er siebt das Pulver, sodass man alles, was zu groß für das Sieb ist, einfach für das Recycling sammeln kann. Er mischt das Pulver und man kann seine eigene Neuzuführungsrate bestimmen. Wenn bestimmte Eigenschaften gewünscht sind, kann man mit 100 % frischem Pulver oder 100 % altem Pulver drucken. Man gibt es in den Mischer, und das Pulver wird auch gleichmäßig verteilt“, berichtet Kleylein.
Kleylein stellte fest, dass die Herstellung von SLS-Teilen auf dem Fuse 1 wenig Aufwand erfordert; es ist nur wenig Zeit und Arbeit nötig, um den neuen Druck vorzubereiten, den Drucker zu warten und die Teile nachzubearbeiten.
„Man kann ihn in einer kleinen Werkstatt aufstellen, wodurch eine einzige Person nur ein Viertel ihrer Zeit aufwenden muss, um die Werkstatt zu führen. Die kostenlose Software ist gut und der Druckvorgang lässt sich mit größeren Druckern vergleichen, wodurch die Vorbereitung schnell geht“, sagt Kleylein.
„Es ist einfach und sehr durchdacht. Man kann den Drucker innerhalb von 30 Minuten neu starten.“
Christian Kleylein
„Es gehört zu den Geräten, die sich gut in Druckerfarmen einsetzen lassen. Es ist sehr planbar; wir können es durchgehend laufen lassen. Der Druck rund um die Uhr ist ein großer Vorteil. Wir haben hier keinen Leerlauf; der einzige Leerlauf ist, wenn das Fertigungsvolumen nicht ganz voll ist und der Druck am Wochenende fertig wird“, so Kleylein.
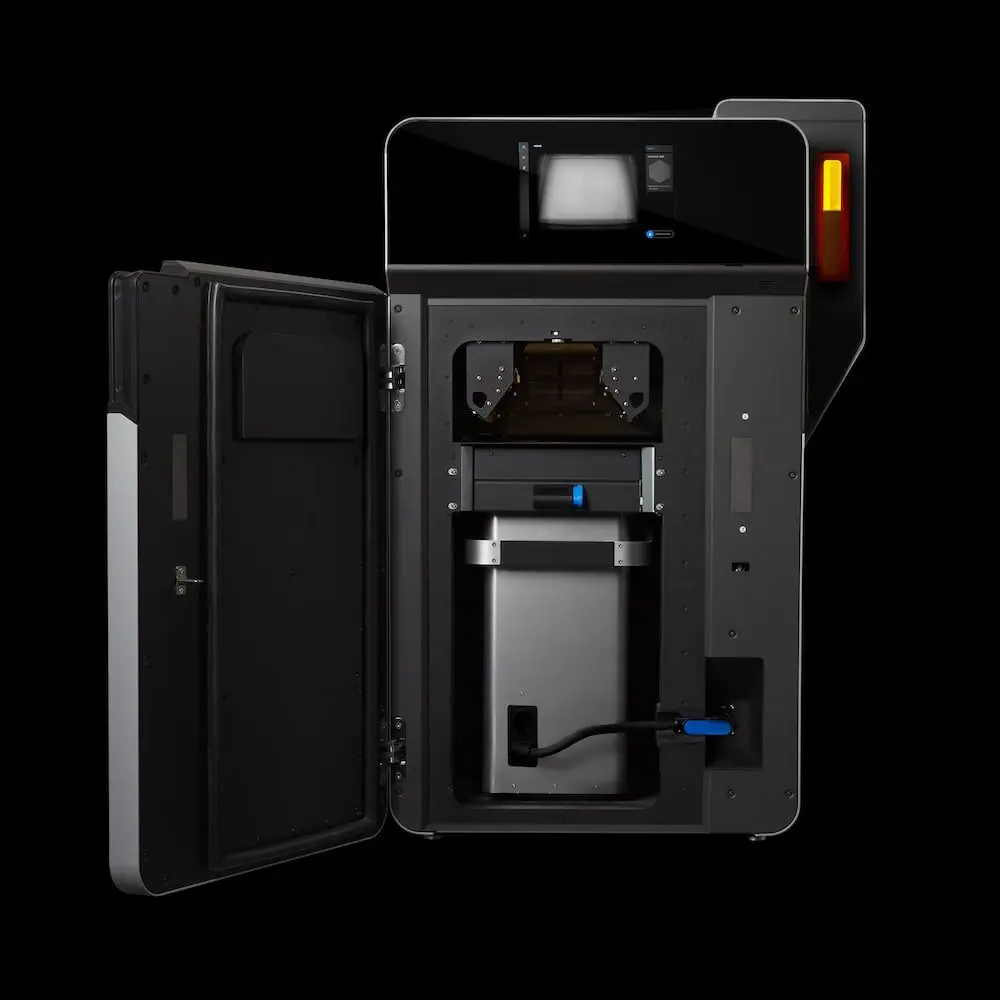
Fuse 1 Produktdemo
Sehen Sie eine Produktdemo an und lassen Sie sich den Fuse 1 und den SLS-3D-Druck durch einen Formlabs Experten erklären.
SLS für die Endverwendung: Ersatzteile und Teile für End-of-Life-Produkte
Brose plant, den Fuse 1 zunächst für funktionales Prototyping zu nutzen, um von dem schnellen Durchsatz und dem Material Nylon 12 zu profitieren, das über ähnliche Eigenschaften wie die aktuellen Produktionsmaterialien verfügt. Doch das Team von Kleylein validiert bereits Teile und gestaltet Anwendungsfälle für die ersten Endverwendungsprojekte, wobei Ersatzteile und Teile für End-of-Life-Produkte zu den ersten Kandidaten gehören.
Wenn ein Fahrzeugmodell nicht mehr produziert wird, sind Automobilzulieferer verpflichtet, weiter Ersatzteile bereitzustellen. In der Vergangenheit bedeutete dies, abzuschätzen, wie viele Ersatzteile benötigt werden, sie alle im Spritzguss zu fertigen und sie dann einzulagern.
„Das ist eine große Verschwendung von Ressourcen, Platz und Geld. Wenn wir sie drucken, müssen wir die Spritzgussformen und die Teile nicht die nächsten 15 Jahre lang einlagern. Es besteht viel Nachfrage nach Ersatzteilen und End-of-Life-Teilen, da Produkte immer auslaufen und wir haben wirklich eine Menge spritzgegossener Kunststoffteile. Wenn wir sie gut stapeln und für eine hohe Druckdichte sorgen können, wird der Prozess kosteneffizient“, so Kleylein.
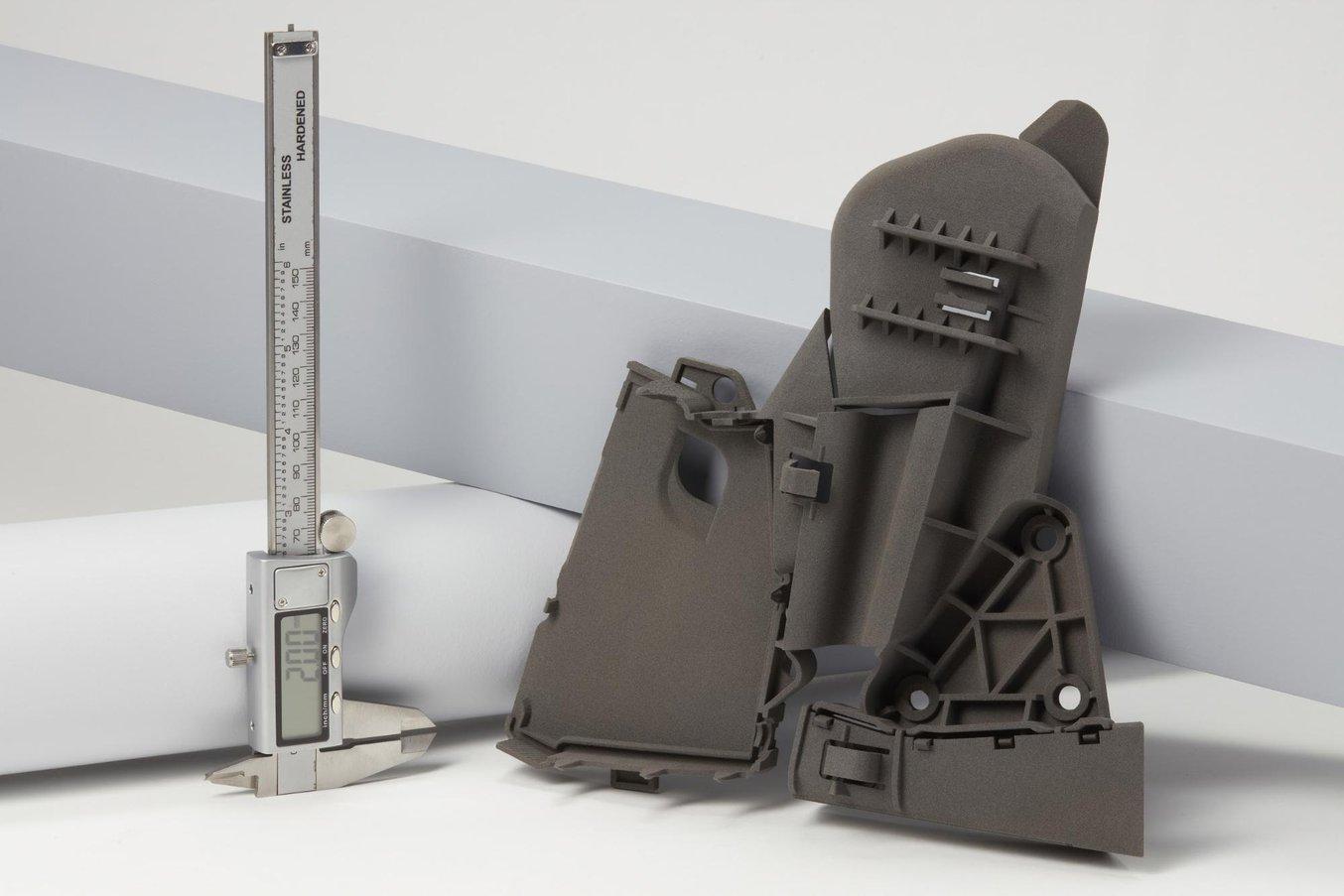
Ein 3D-gedrucktes Ersatzteil für ein Türgriffmodel, das für gewöhnlich spritzgegossen wird.
„In der Automobilbranche ist es wichtig, die höchstmögliche Qualität zum bestmöglichen Preis zu liefern. Aktuell könnte alles unter 10 000 Teile pro Jahr mit SLS gedruckt werden.“
Christian Kleylein
SLS ist eine ideale Produktionstechnologie in vielerlei Hinsicht:
-
Es ermöglicht hochwertige Teile mit Eigenschaften, die sich mit denen von spritzgegossenen Teilen vergleichen lassen.
-
Es kann in einer Fertigungsumgebung implementiert werden.
-
Es ist einer der abfallärmsten und saubersten AM-Prozesse, was bei der Fertigung immer wichtiger wird.
„Man kann technische Polymere verwenden, um technische Teile zu drucken, und es sind keine Stützstrukturen erforderlich. Die Nachbearbeitung ist auch sehr sauber; man kann den Großteil des Pulvers bereits vor dem Medienstrahlen entfernen“, erklärt Kleylein.
„Viele Kunden von Brose stehen der Technologie sehr offen gegenüber; ihnen gefällt die Idee, da wir versuchen, nahezu ohne Abfall zu drucken. Wir können das Pulver wiederverwenden und müssen es nicht wegwerfen. Es müssen auch keine Chemikalien recycelt werden. Wir erwarten, dass die SLS-Geräte bis Ende des nächsten Jahres abfallfrei laufen“, so Kleylein.
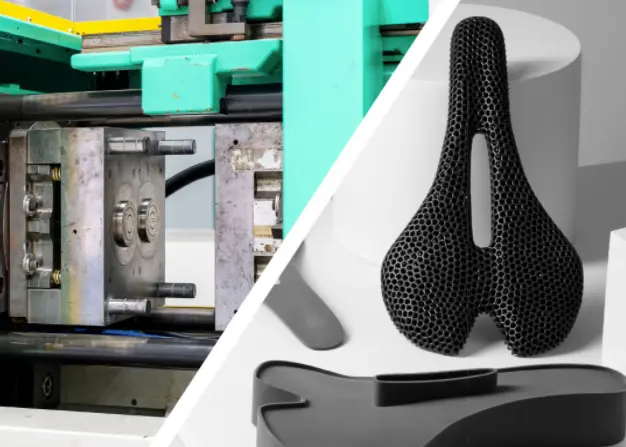
SLS-3D-Druck oder Spritzguss: Wann sollte man Spritzgussteile durch 3D-Druck ersetzen?
In diesem Whitepaper werden der Spritzguss und seine Vor- und Nachteile erörtert sowie der SLS-3D-Druck und die Anwendungen vorgestellt, bei denen er als ergänzende Technologie eingesetzt werden kann.
Die Zukunft von SLS in der Serienfertigung
Natürlich ist das endgültige Ziel der Einsatz von SLS bei der Serienfertigung von Teilen für die nächste Generation von Automobilprodukten, deren Einführung Christian in der näheren Zukunft erwartet.
„Prototypen und Ersatzteile können jetzt gefertigt werden. In Anbetracht der aktuellen technischen Entwicklungen sehe ich die [Serien-]Fertigung in vier bis fünf Jahren.“
Christian Kleylein
Um es dahin zu schaffen, müssen zwei wichtige Veränderungen erfolgen: AM muss bei der Produktentwicklung schon in der Designphase eingeplant werden; außerdem müssen Material- und Gerätekosten weiter sinken.
„Das größte Hindernis ist es, den Produktdesignern zu vermitteln, was tatsächlich möglich ist mit 3D-Druck, und sie dazu zu bringen, das Teil mit 3D zu drucken. Man erzielt nie Kosteneffizienz mit Komponenten, die für den Spritzguss ausgelegt sind. Man muss die Teile für den Prozess designen“, meint Kleylein.
„Es kommt darauf an, wie viele Teile man drucken möchte und wie effizient herkömmliche Fertigungssysteme sind. Sobald das Leistungsversprechen gut ist, fertigen wird das Teil mit dem effizientesten Fertigungssystem, das zur Verfügung steht. Wir werden den 3D-Druck bei einem Produkt nicht erzwingen, aber wenn es die beste Möglichkeit zur Fertigung eines Teils darstellt, drucken wir es“, sagt Kleylein.
Da der Fuse 1 die Hürde zum Einstieg in den SLS 3D-Druck senkt, wird er eine wichtige Rolle bei dieser Verlagerung auf die Produktion spielen. Brose hat bereits Pläne, seine 3D-Druckkapazitäten schnell weiter auszubauen. Die zweite Kunststoff-AM-Werkstatt wird aktuell in den USA gebaut, wo auch bald der erste Fuse 1 eintreffen wird.
„Es gibt immer noch viele große Herausforderungen, aber wenn ich den Fuse 1 betrachte, sehe ich, dass wir ein sehr leistungsstarkes Produkt zu einem sehr wettbewerbsfähigen Preis haben.“
Christian Kleylein