
Hersteller und Entwickler verschiedenster Branchen setzen auf den 3D-Druck mit selektivem Lasersintern (SLS), da mit dieser Technologie starke, funktionsfähige Teile hergestellt werden können.
In diesem umfangreichen Leitfaden decken wir das Verfahren des selektiven Lasersinterns, seine Anwendungsbereiche und die verschiedenen auf dem Markt erhältlichen Systeme und Materialien sowie den Arbeitsablauf mit SLS-Druckern ab. Außerdem gehen wir darauf ein, wann selektives Lasersintern anderen additiven und herkömmlichen Herstellungsverfahren vorzuziehen ist.
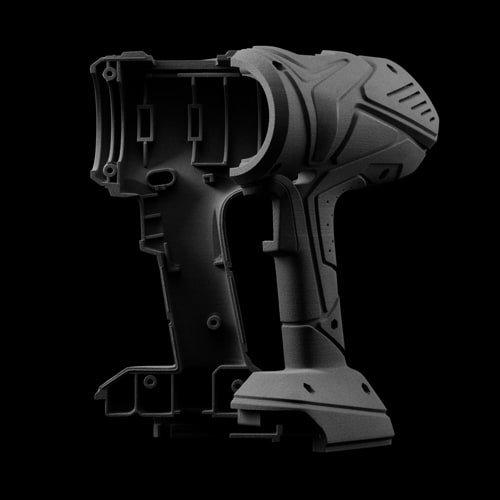
Einführung in den 3D-Druck mit selektivem Lasersintern (SLS)
Suchen Sie nach einem 3D-Drucker, mit dem Sie feste, funktionsfähige Teile herstellen können? Laden Sie unser Whitepaper herunter und erfahren Sie, wie der SLS-Druck funktioniert und wieso er ein beliebtes 3D-Druckverfahren für funktionales Prototyping und die Produktion von Teilen für die Endverwendung ist.
Was ist selektives Lasersintern?
Selektives Lasersintern ist ein additives Fertigungsverfahren, bei dem ein Hochleistungslaser kleine Polymerpulverpartikel zu einer massiven Struktur sintert, die auf einem 3D-Modell basiert.
SLS-3D-Druck erfreut sich seit Jahrzehnten großer Beliebtheit bei Ingenieurabteilungen und Herstellern. Durch geringe Teilkosten, hohe Produktivität und bewährte Materialien eignet sich die Technologie ideal für eine Vielzahl von Anwendungen, vom Rapid Prototyping bis hin zur Kleinserien-, Übergangs- oder kundenindividuellen Fertigung.
Die jüngsten Fortschritte in Sachen Technik, Material und Software haben SLS-3D-Druck für eine größere Zahl an Unternehmen zugänglich gemacht und damit die Implementierung von Geräten und Verfahren ermöglicht, die zuvor auf wenige High-Tech-Sektoren beschränkt waren.
Mit den SLS-Druckern der Fuse-Serie von Formlabs ist hochleistungsfähiger SLS-3D-Druck endlich zugänglich.
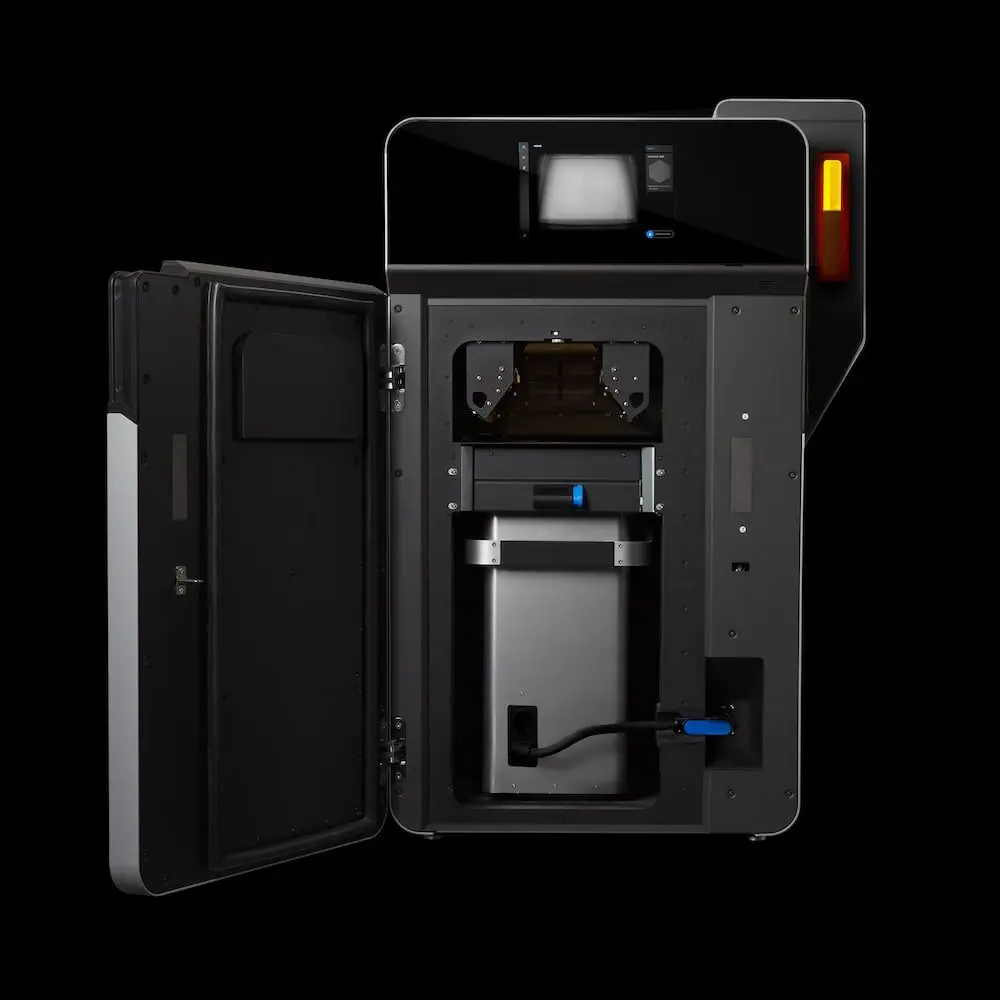
Rekordschnelle Produktion leistungsstarker SLS-Teile mit dem neuen Fuse 1+ 30W
Sehen Sie sich unsere Produktvorführung an und lassen Sie sich den Fuse 1+ 30W und den SLS-3D-Druck durch einen Formlabs-Experten erklären.
Wie SLS-3D-Druck funktioniert
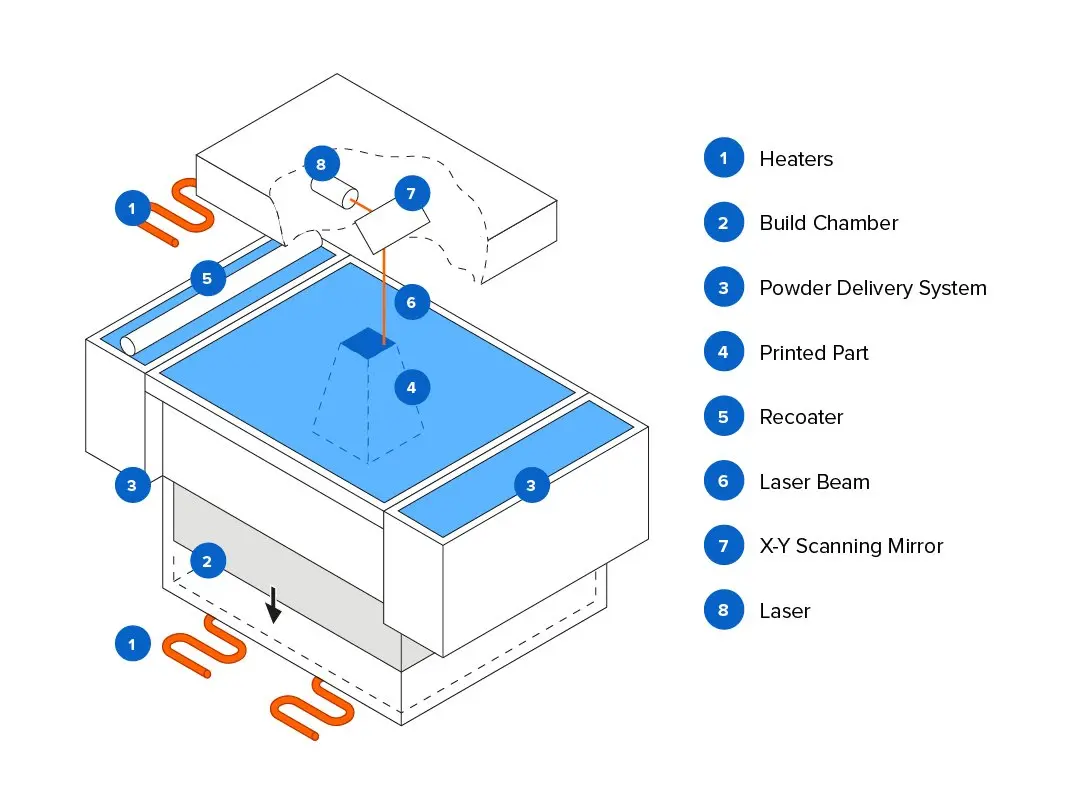
Schema des selektiven Lasersinterverfahrens. Beim SLS-3D-Druck kommt ein Hochleistungslaser zum Einsatz, der kleine Polymerpulverpartikel zu einer massiven Struktur sintert, die auf einem 3D-Modell basiert.
-
Druck: Das Pulver wird in einer dünnen Schicht auf einer Plattform innerhalb der Konstruktionskammer verteilt. Der Drucker erhitzt das Pulver auf eine Temperatur leicht unterhalb des Schmelzpunktes des Rohmaterials. Dadurch kann die Temperatur bestimmter Bereiche des Pulverbettes leichter vom Laser erhöht werden, welcher durch Nachzeichnen des Modells das Teil verfestigt. Der Laser tastet einen Querschnitt des 3D-Modells ab und erhitzt dabei das Pulver auf eine Temperatur knapp unterhalb des Schmelzpunktes des Materials oder exakt darauf. So werden die Partikel mechanisch verschweißt und es entsteht ein festes Teil. Da das ungesinterte Pulver das Teil beim Drucken stützt, sind keine zusätzlichen Stützstrukturen erforderlich. Die Plattform senkt sich anschließend um eine Schicht in die Konstruktionskammer, in der Regel zwischen 50 und 200 Mikrometer. Der ganze Prozess wiederholt sich dann für jede Schicht, bis das Teil fertiggestellt ist.
-
Abkühlen: Nach dem Druck muss die Konstruktionskammer abkühlen, erst innerhalb des Druckgehäuses und anschließend außerhalb des Druckers, damit die optimalen mechanischen Eigenschaften sichergestellt sind und sich die Teile nicht verformen.
-
Nachbearbeitung: Die fertigen Teile müssen aus der Konstruktionskammer entnommen, getrennt und von überschüssigem Pulver befreit werden. Das Pulver kann wiederverwendet werden und die Druckteile lassen sich mittels Sandstrahlen oder Gleitschleifen nachbearbeiten.
Den detaillierten Arbeitsablauf finden Sie unten im Abschnitt „Arbeitsablauf beim SLS-3D-Druck“.
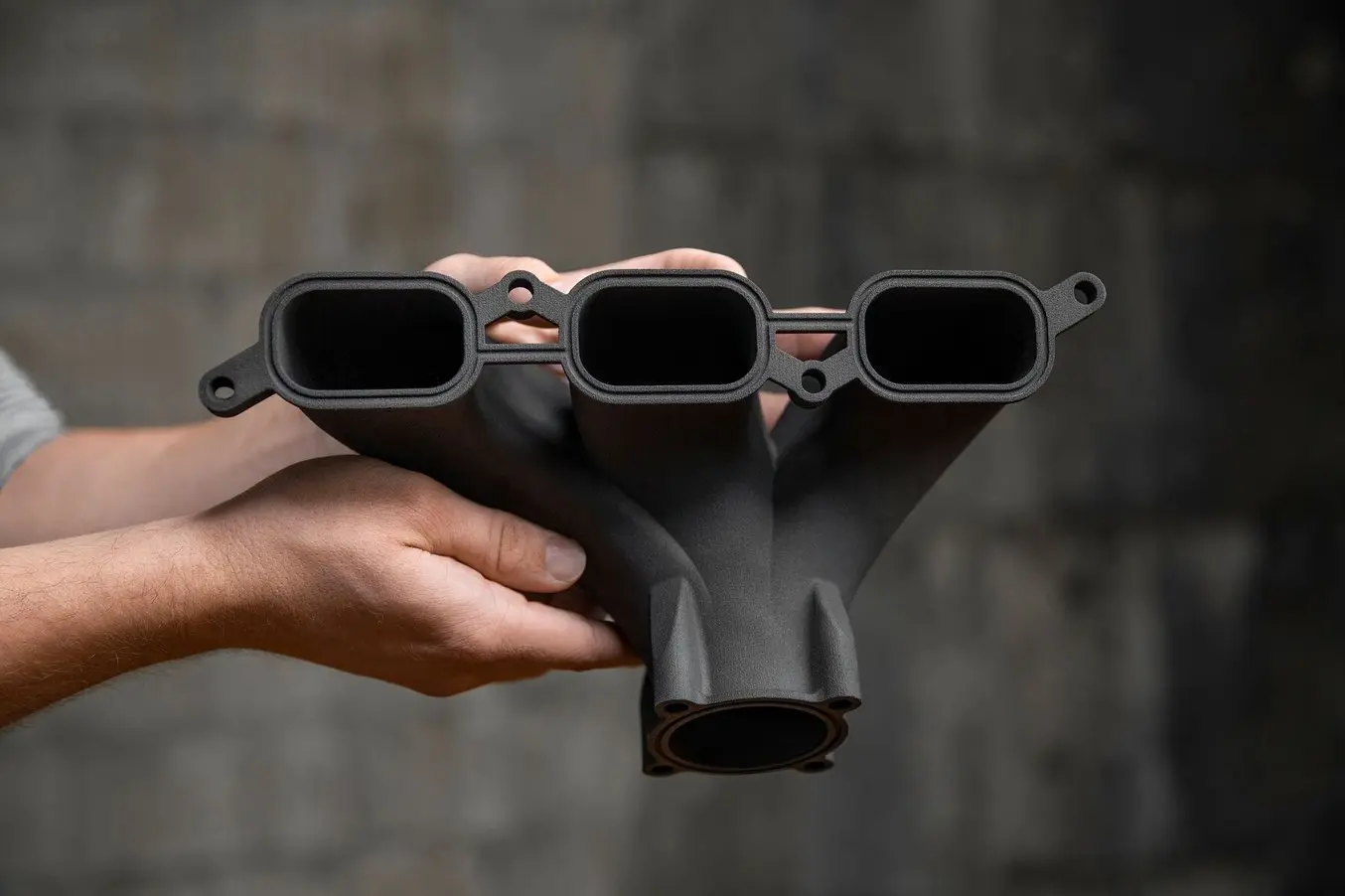
SLS-Teile haben eine leicht körnige Oberflächenbeschaffenheit, weisen aber nahezu keine sichtbaren Schichtlinien auf. Strahlen mit einem Strahlmittel oder Gleitschleifen wird empfohlen, um eine glattere Oberflächengüte zu erzielen. Dieses Teil wurde auf einem industriellen Benchtop-SLS-3D-Drucker des Typs Fuse 1+ 30W von Formlabs gedruckt.
Da das ungesinterte Pulver das Teil beim Drucken stützt, sind keine zusätzlichen Stützstrukturen erforderlich. SLS eignet sich somit ideal für komplexe Geometrien wie Merkmale im Inneren von Teilen, Hinterschneidungen, dünne Wände und negative Details.
Teile, die mit SLS gefertigt wurden, bieten herausragende mechanische Eigenschaften und eine Festigkeit, die mit der von Spritzgussteilen vergleichbar ist.
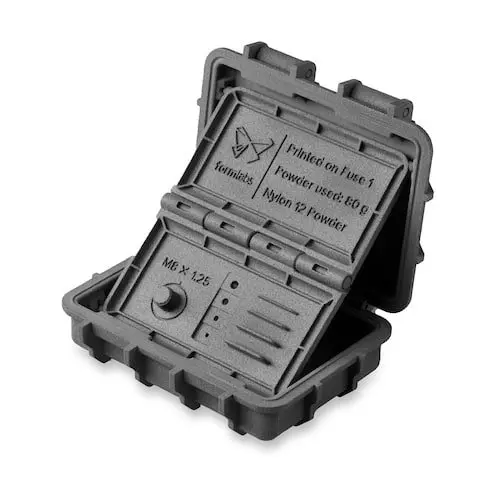
Kostenlosen SLS-Probedruck anfordern
Sehen und fühlen Sie die Qualität von Formlabs aus erster Hand. Wir senden Ihnen einen kostenlosen Probedruck aus dem Fuse 1+ 30W an Ihren Arbeitsplatz.
Eine kurze Geschichte des SLS-3D-Drucks
Selektives Lasersintern (SLS) war eines der ersten additiven Herstellungsverfahren, das Mitte der 80er Jahre von Dr. Carl Deckard und Dr. Joe Beaman an der University of Texas in Austin entwickelt wurde. Ihr Verfahren wurde seitdem an die Verarbeitung einer Reihe von Materialien angepasst, darunter Kunststoffe, Metalle, Glas, Keramik und verschiedene Verbundwerkstoffpulver. Heute werden diese Technologien kollektiv als Pulverbettfusion kategorisiert — additive Fertigungsverfahren, bei denen ausgewählte Bereiche eines Pulverbettes durch Wärmeenergie verschmolzen werden.
Die beiden heute gebräuchlichsten Pulverbettfusionssysteme sind das auf Kunststoff basierende Verfahren, allgemein als SLS bezeichnet, sowie die Pulverbettfusion von Metall, bekannt als Direct Metal Laser Sintering (DMLS) oder selektives Laserschmelzen (Selective Laser Melting, SLM). Bis vor Kurzem waren diese beiden Systeme noch unerschwinglich teuer und komplex. Dies führte dazu, dass ihre Verwendung auf die Herstellung kleiner Mengen hochwertiger oder kundenspezifischer Teile wie Luft- und Raumfahrtkomponenten oder medizinische Geräte beschränkt war.
In letzter Zeit hat dieses Gebiet jedoch zahlreiche Innovationen erlebt, und das auf Kunststoff basierte SLS ist nun bereit, nach dem Beispiel anderer 3D-Drucktechnologien wie Stereolithografie (SLA) und Schmelzschichtung (FDM) für immer mehr Anwendungsbereiche eingesetzt zu werden, dank erschwinglicher, kompakter Systeme.
Arten von SLS-3D-Druckern
Alle SLS-Systeme bauen auf dem oben beschriebenen Verfahren auf. Die wichtigsten Unterscheidungsmerkmale sind die Art des Lasers, die Größe des Fertigungsvolumens und die Komplexität des Systems. Es kommen, je nach Drucker, verschiedene Lösungen für die Temperaturregelung, die Pulverabgabe und die Schichtabscheidung zum Einsatz.
Selektives Lasersintern erfordert ein hohes Maß an Präzision und strenge Kontrollen während des gesamten Druckvorgangs. Die Temperatur des Pulvers und der (nicht fertiggestellten) Teile muss während der drei Stufen des Vorheizens, der Sinterns und der Lagerung vor der Entnahme innerhalb eines Bereiches von 2 °C kontrolliert werden, um Verzug, Spannungen und wärmebedingte Verformung zu minimieren.
Traditionelle industrielle SLS-3D-Drucker
Selektives Lasersintern war bei Fachleuten jahrzehntelang eines der beliebtesten 3D-Druckverfahren, doch seine Komplexität, seine Anforderungen und sein hoher Preis haben die Anwendung bislang auf Fertigungsdienstleister und große Unternehmen begrenzt.
Herkömmliche Geräte erfordern zudem spezielle Klimatechnik und eine Starkstromversorgung, und selbst die kleinsten Industriedrucker benötigen eine Standfläche von mindestens 10 m². Die Einrichtung der Geräte dauert mehrere Tage für die Installation und Schulungen. Aufgrund des komplexen Arbeitsablaufes und der steilen Lernkurve ist für die Bedienung und Wartung dieser Systeme außerdem betriebsinternes, geschultes technisches Personal vonnöten.
Bei einem Einstiegspreis von 200 000 USD – der Preis für Komplettlösungen liegt weit darüber – war herkömmliches industrielles SLS für viele Unternehmen bislang unzugänglich.
Fuse-Serie: Die ersten industriellen SLS-3D-Drucker für den Benchtop
Genau wie bei anderen 3D-Druckverfahren wie FDM oder SLA sind kostengünstigere, kompakte Systeme in der letzten Zeit auch für SLS auf dem Markt erhältlich geworden. Diese Drucklösungen hatten zunächst jedoch bedeutende Nachteile, wie etwa eine minderwertige Druckteilqualität und komplexe, manuelle Arbeitsabläufe aufgrund mangelnder Nachbearbeitungsgeräte. Dadurch waren sie für den Einsatz in industriellen und Produktionsanwendungen nur bedingt geeignet.
Mit dem Fuse 1 von Formlabs wurde diese Lücke geschlossen und eine eigene Gerätekategorie geschaffen: Er war der erste industrielle Benchtop-SLS-3D-Drucker, der hohe Qualität, kompakte Abmessungen und einen umfassenden, vereinfachten Arbeitsablauf zu einem Bruchteil der Kosten herkömmlicher industrieller SLS-Systeme bot. Die neue Generation, der Fuse 1+ 30W, erweitert diese Kategorie um ein Gerät mit einem leistungsstärkeren Laser, verbesserter Pulverhandhabung und neuen Materialmöglichkeiten, das Teile in Industriequalität bei hohem Durchsatz liefert.

Für das Ecosystem der Fuse-Serie ist keine spezielle Infrastruktur notwendig und es lässt sich leicht in Ihren Arbeitsplatz integrieren.
Bei den SLS-3D-Druckern der Fuse-Serie kommt ein einziger Laser zum Einsatz. Durch die kleinere Konstruktionskammer ist weniger Heizleistung erforderlich. Dank des insgesamt niedrigeren Energieverbrauchs können sie mit Standard-Wechselstrom ohne spezielle Infrastruktur betrieben werden. Durch die optional verfügbare Stickstoffzufuhr am Fuse 1+ 30W wird eine Inertgasatmosphäre erzeugt, die die Qualität des ungesinterten Pulvers bewahrt und somit eine niedrigere Neuzuführungsrate ermöglicht (das bedeutet mehr recyceltes als neues Pulver bei nachfolgenden Drucken), Abfälle minimiert und die Oberflächengüte der gesinterten Teile verbessert.
Die Drucker der Fuse-Serie verfügen außerdem über eine als Patent angemeldete Lösung namens Surface Armor – eine teilweise gesinterte Hülle, die dafür sorgt, dass der Bereich um die Teile beim Druck gleichmäßig erwärmt wird, was eine hervorragende Oberflächengüte, einheitliche mechanische Eigenschaften, hohe Zuverlässigkeit und bessere Neuzuführungsraten ermöglicht.
Um ein kompaktes, integriertes Ecosystem und einen Pulverhandhabungskreislauf zu bieten, werden die Drucker der Fuse-Serie zum einen durch den Fuse Sift ergänzt – eine Pulverrückgewinnungsstation und Komplettlösung, die die Teileentnahme, Pulverrückgewinnung, -lagerung und das Mischen in einem einzigen, frei stehenden Gerät kombiniert – sowie zum anderen durch den Fuse Blast als vollautomatisierte Lösung für die Reinigung und Politur.
Insgesamt bietet der industrielle Benchtop-SLS-3D-Druck mit den Druckern der Fuse-Serie gegenüber den kleinsten industriellen SLS-Systemen ein geringfügig kleineres Druckvolumen, dafür aber einen wesentlich geringeren Platzbedarf, einen vereinfachten Arbeitsablauf und niedrigere Kosten.
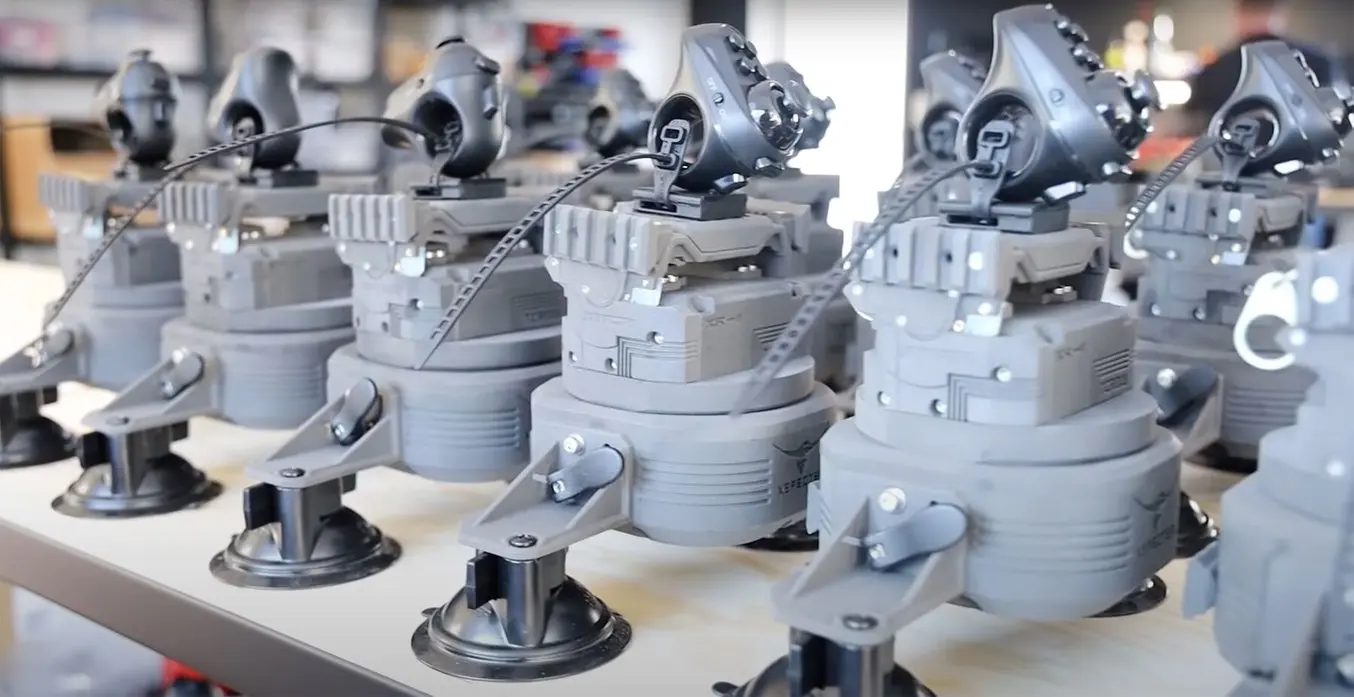
SLS-Produktion für die Endverwendung
3D-Druck für die Endverwendung ist nicht nur möglich, sondern dank des SLS-Ecosystems der Fuse-Serie auch noch erschwinglicher, agiler und leichter skalierbar denn je. Vergleichen Sie Produktionsverfahren, informieren Sie sich über unsere Mengenrabatte auf Pulver und entdecken Sie die Produktionsabläufe 15 verschiedener Hersteller, die derzeit die Fuse-Serie nutzen.
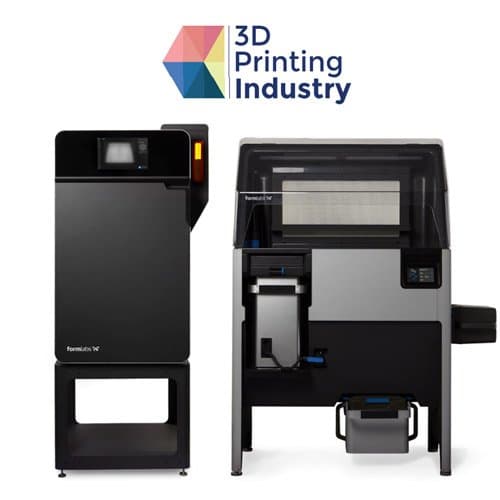
3D Printing Industry: Testbericht zu Fuse 1 & Fuse Sift von Formlabs
Lesen Sie diesen tiefgehenden Bericht des Ingenieurteams von 3D Printing Industry, in dem die SLS-3D-Drucker von Formlabs bewertet und detaillierte Ergebnisse von Präzisionstest dargestellt werden.
SLS-3D-Drucker vergleichen
Fuse-Serie: Industrielle SLS-3D-Drucker für den Benchtop | Traditionelle industrielle SLS-3D-Drucker | |
---|---|---|
Preis | Die Preise beginnen bei 30 000 € für einen Drucker und 60 000 € für das gesamte Ecosystem. | 200 000–500 000 € und mehr |
Fertigungsvolumen | 165 x 165 x 300 mm | Bis zu 550 × 550 × 750 mm |
Vorteile | Erschwinglich; Hochwertige Teile; Hoher Durchsatz; Verschiedene Materialoptionen; Vereinfachter Arbeitsablauf; Geringer Platzbedarf; Geringer Wartungsaufwand | Großes Fertigungsvolumen; Hochwertige Teile; Hoher Durchsatz; Verschiedene Materialoptionen; |
Nachteile | Kleineres Fertigungsvolumen | Teure Ausrüstung Großer Platzbedarf; Anforderungen an die Infratruktur; Hoher Wartungsaufwand; Erfordert eigenes Personal für Bedienung; |
Der Vergleich basiert auf den industriellen Benchtop-SLS-Systemen der Fuse-Serie von Formlabs und den traditionellen industriellen SLS-Systemen von EOS und 3D Systems.
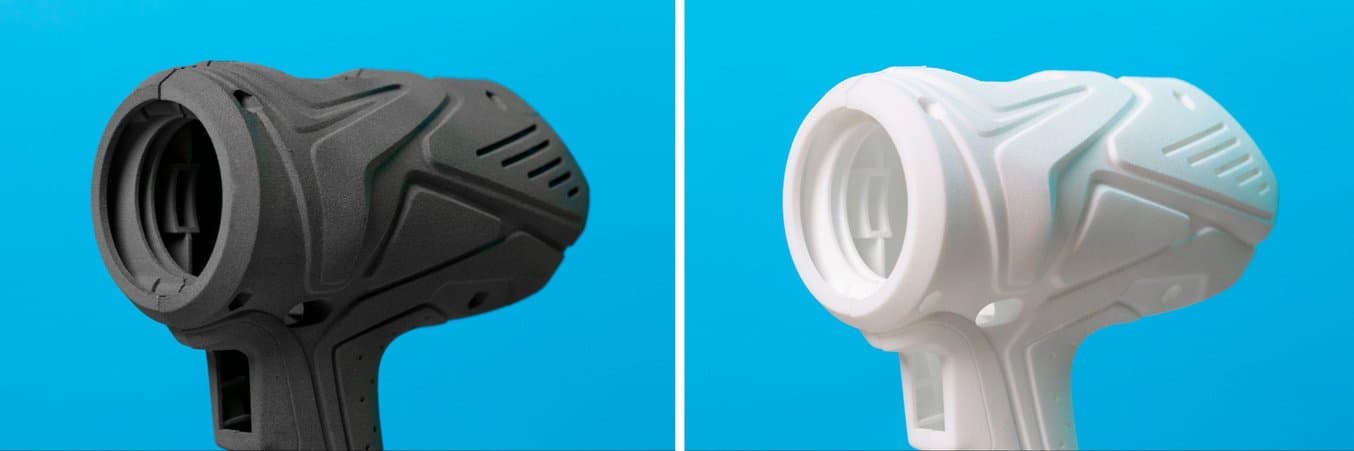
Prototyp einer Bohrmaschine, gedruckt auf dem Fuse 1+ 30W (links) und einem EOS-Drucker (rechts) bei vergleichbarer Qualität, aber zu stark unterschiedlichen Gerätepreisen.
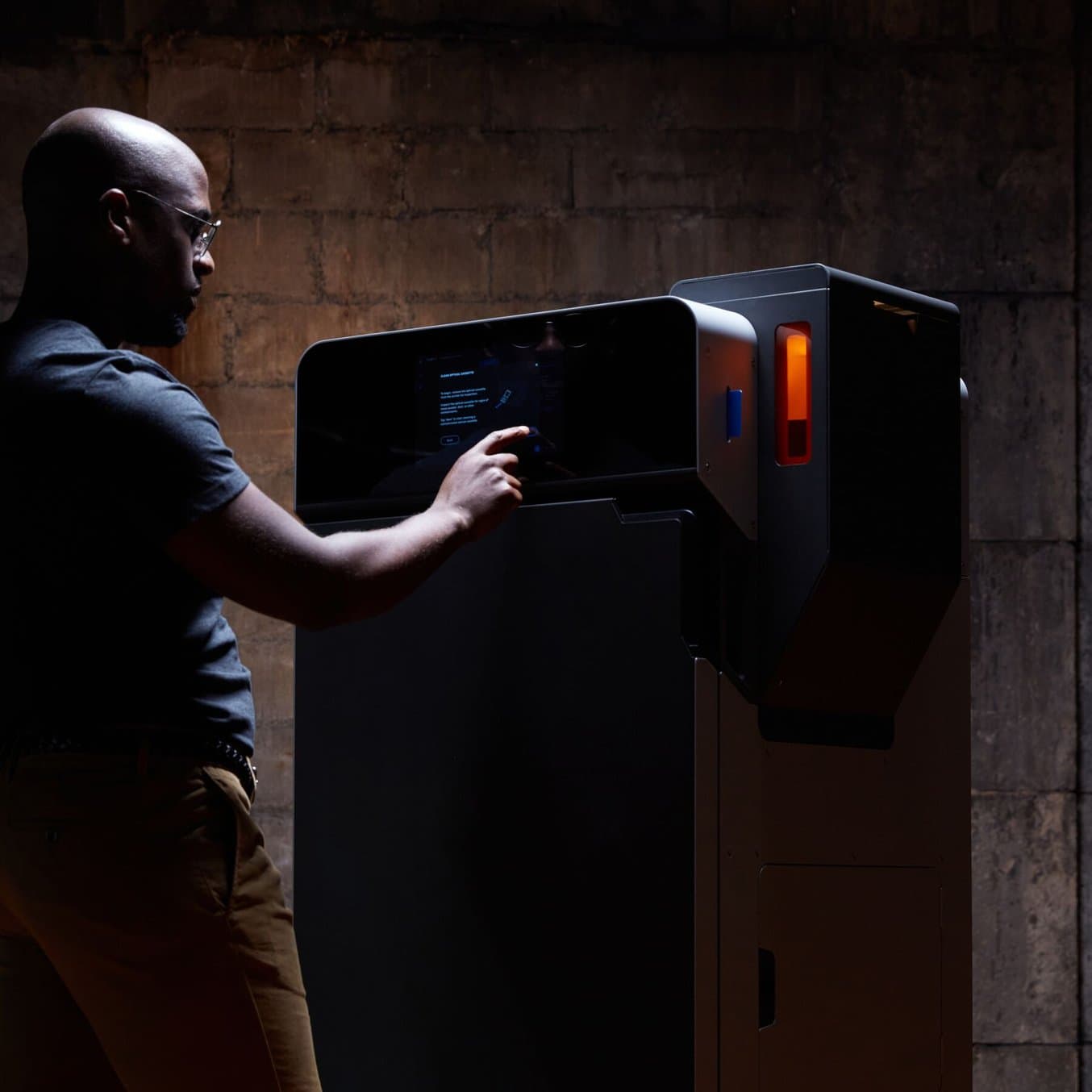
Outsourcing oder betriebsintern: Wann sollte man SLS-3D-Druck in den eigenen Betrieb holen?
In diesem Whitepaper untersuchen wir den Mehrwert betriebsinterner SLS-3D-Drucker im Vergleich zum Outsourcing von SLS-Teilen an einen Fertigungsdienstleister.
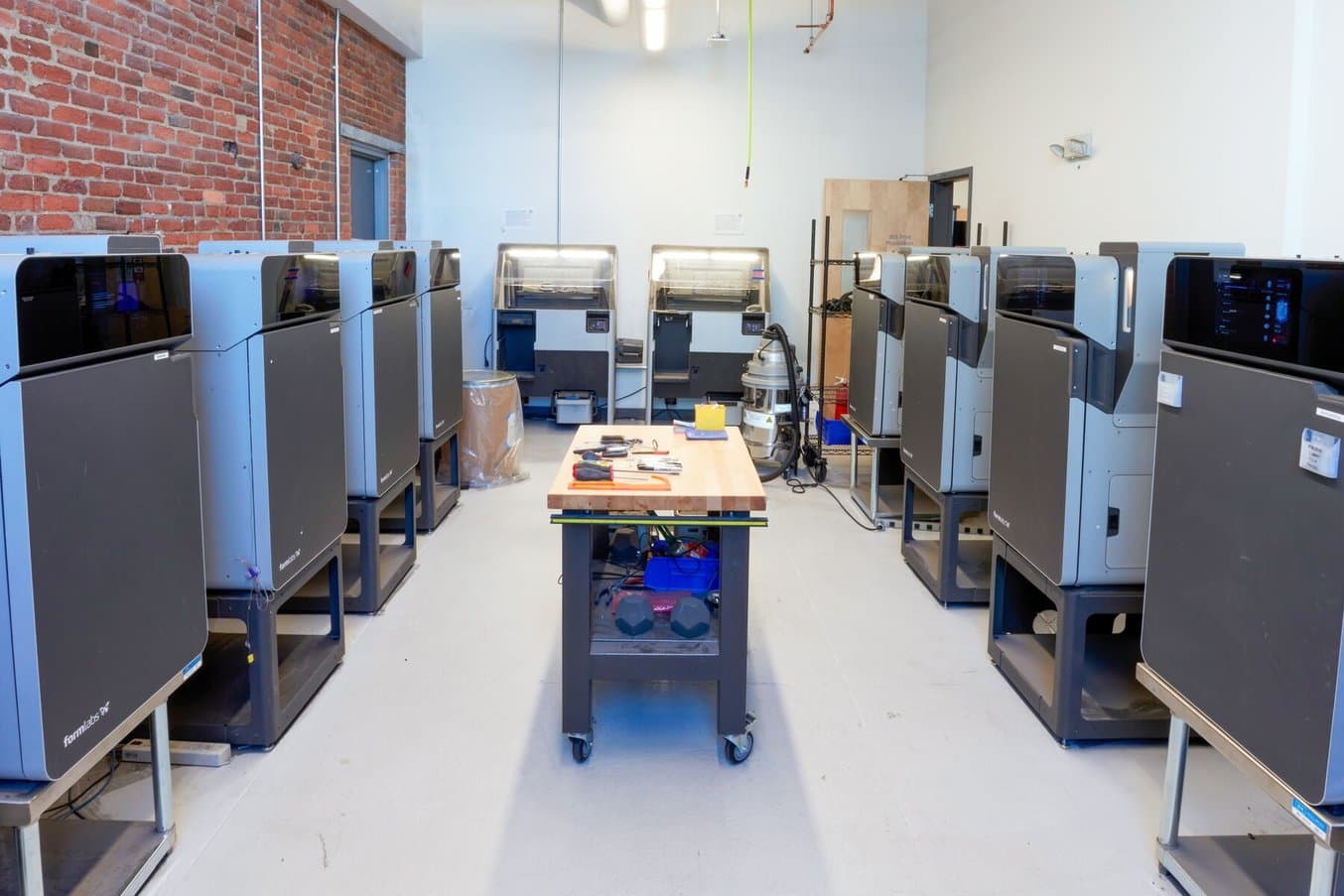
SLS-3D-Drucker der Fuse-Serie vs. konventionelle Pulverbettfusionsanlagen
In diesem vergleichenden Leitfaden stellen wir die wichtigsten Unterschiede zwischen kompakten SLS-Druckern wie der Fuse-Serie von Formlabs und herkömmlichen, großangelegten Geräten vor.
SLS-3D-Druckmaterialien
Das üblichste Material im SLS-Druck ist Nylon, ein leistungsstarker technischer Thermoplast, der sich sowohl für funktionale Prototypen als auch für Endprodukte eignet. Nylon ist ideal für komplexe Baugruppen und robuste Teile mit hoher Umweltbeständigkeit.
Mit SLS gedruckte Nylonteile sind stark, starr, robust und langlebig. Die Druckteile sind schlagfest und halten wiederholten Belastungen und Verschleiß stand. Nylon ist beständig gegenüber (UV-)Licht, Hitze, Feuchtigkeit, Lösungsmitteln, Temperaturschwankungen und Wasser. 3D-gedruckte Teile können auch biokompatibel und nicht reizend sein, wodurch sie auf der Haut getragen werden können und für viele Anwendungsfälle sicher sind.
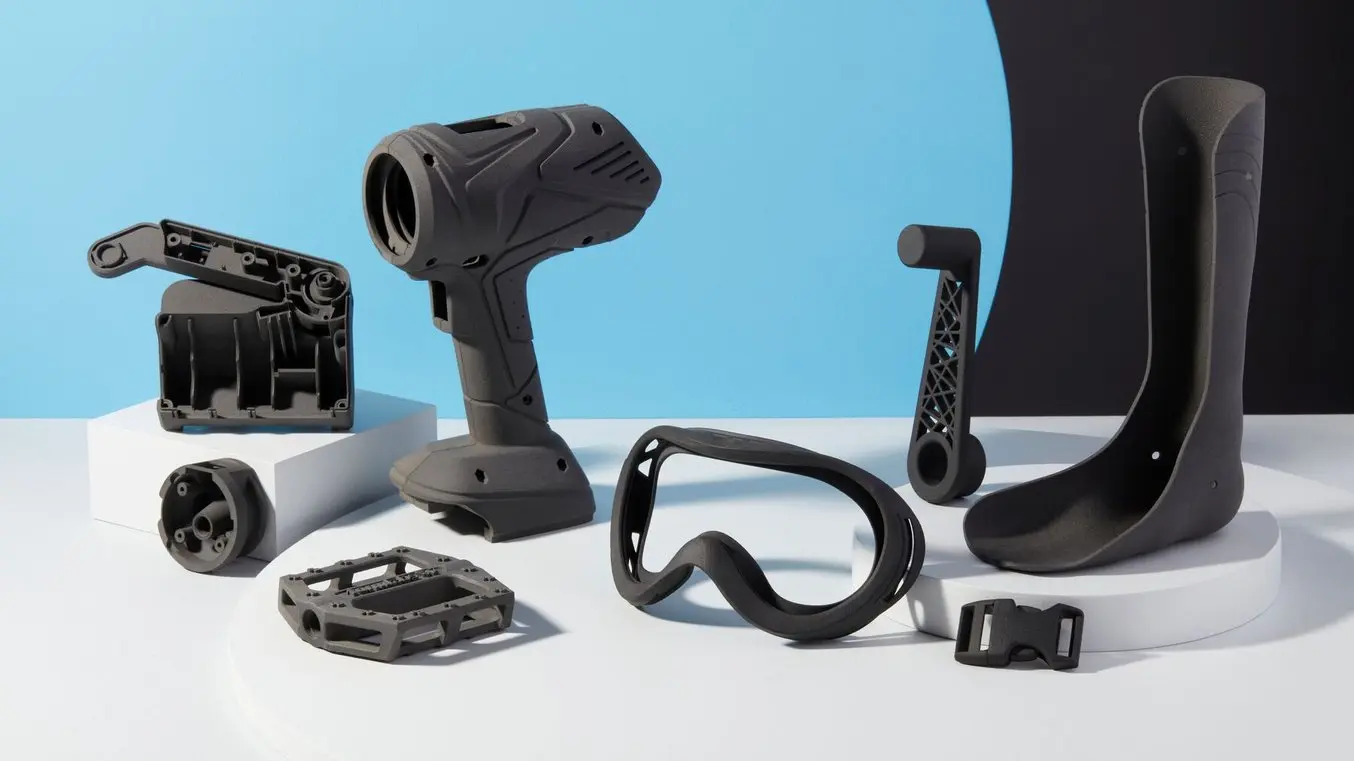
Nylon eignet sich ideal für eine Reihe funktionaler Anwendungen, von der Entwicklung von Konsumgütern bis hin zu Produkten des Gesundheitswesens.
Nylon ist ein synthetisches thermoplastisches Polymer, das zur Familie der Polyamide gehört. Es ist in mehreren Varianten verfügbar, von denen jede für unterschiedliche Anwendungen ausgelegt ist. Die gängigsten Pulver aus einer einzelnen Komponente sind Nylon 12 und Nylon 11, welche beide mit anderen Materialien wie Glas oder Kohlenstofffaser angereichert werden können, um Verbundwerkstoffe mit bestimmten Eigenschaften zu erschaffen, beispielsweise gesteigerter Festigkeit oder Steifigkeit.
Neben Nylon ist Polypropylen (PP) ein beliebtes Material für den SLS-3D-Druck. PP eignet sich ideal für die Produktion vollkommen funktionsfähiger, leichter Teile mit den mechanischen Eigenschaften herkömmlicher, spritzgegossener Polypropylenteile. Es liefert langlebige Prototypen und Endverbrauchsteile für anspruchsvolle Einsatzbereiche.
Mit SLS-3D-Druckern lassen sich auch flexible TPU-Teile mit unvergleichlicher Gestaltungsfreiheit und Mühelosigkeit herstellen. Die hohe Reißfestigkeit und erhöhte Bruchdehnung von Gummimaterialien, kombiniert mit der Vielseitigkeit des SLS-3D-Drucks, machen TPU ideal für die Herstellung flexibler, hautverträglicher Prototypen und Endverbrauchsteile, die den Ansprüchen des täglichen Gebrauchs standhalten.
Die konkrete Materialauswahl ist vom Druckermodell abhängig. Folgende Materialien sind mit dem Fuse 1+ 30W kompatibel:
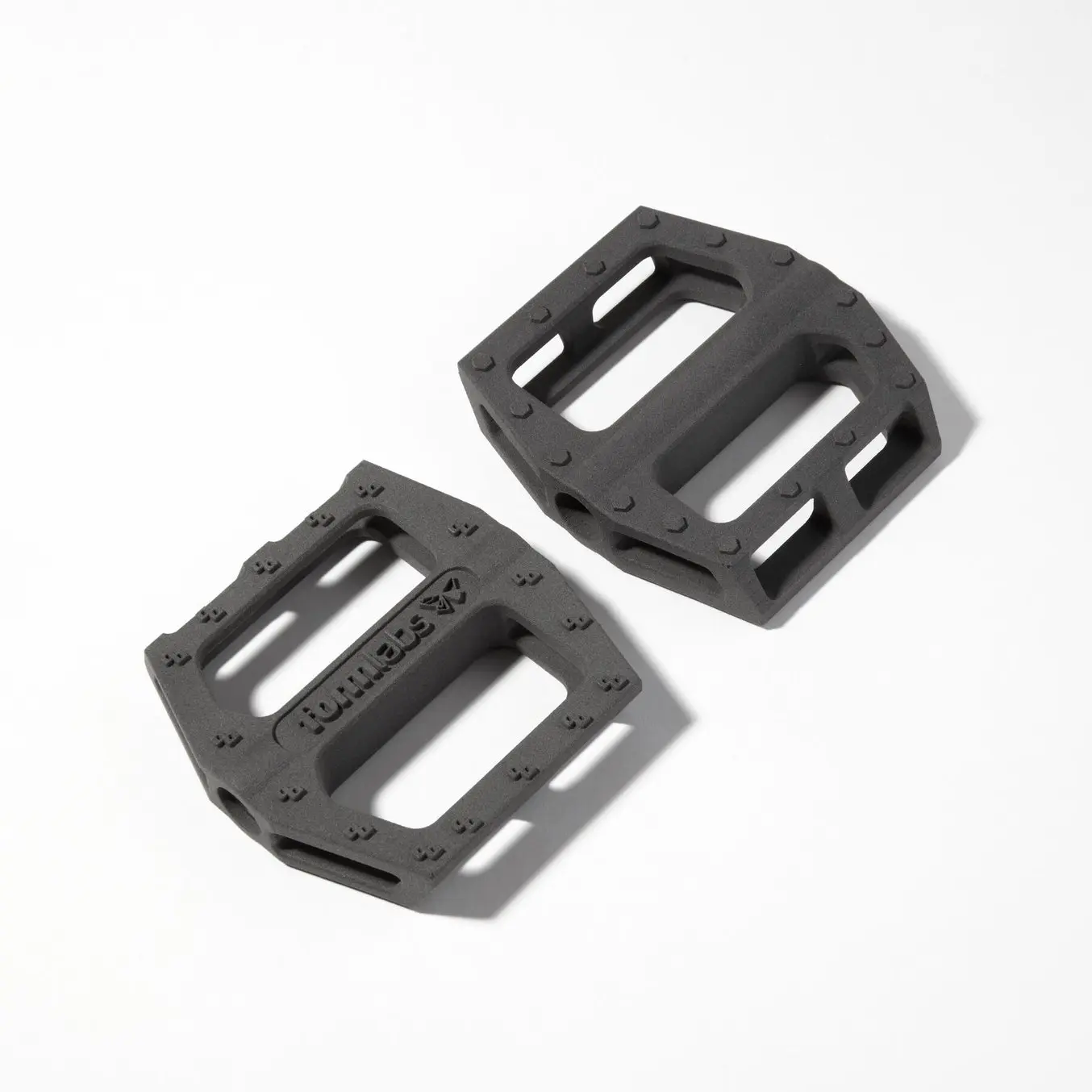
Nylon 12 Powder
Ein vielseitiges Allzweckmaterial mit hoher Detailtreue und Maßgenauigkeit.
- Hochleistungsfähige Prototypenentwicklung
- Kleinserienfertigung
- Permanente Halterungen, Vorrichtungen und Werkzeuge
- Biokompatible, sterilisierbare Teile*
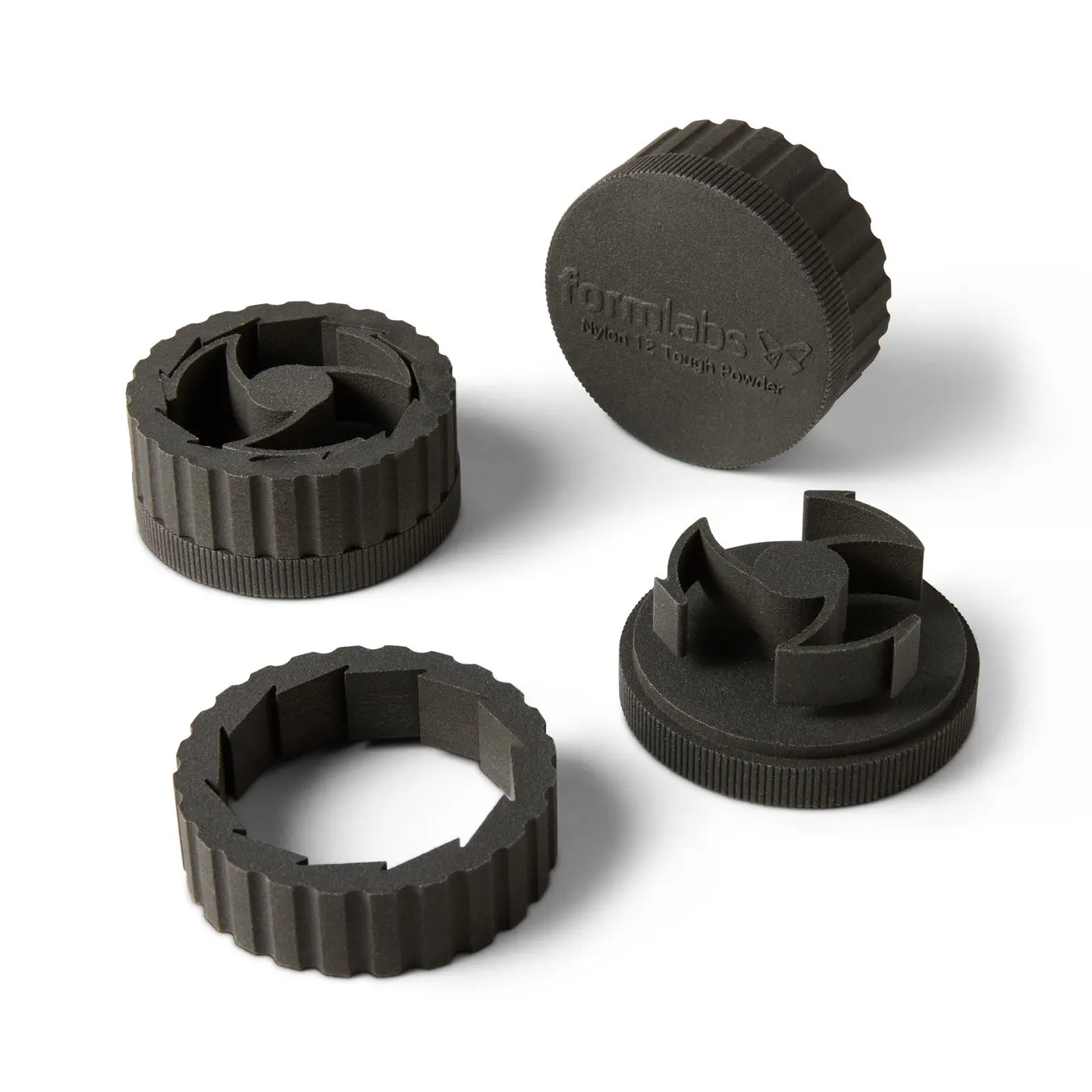
Nylon 12 Tough Powder
Marktführende Duktilität, geringste Neuzuführungsrate und großartige Maßgenauigkeit
- Hochleistungsfähige, schlagfeste Prototypen
- Duktile Teile; Schnappverschlüsse, Ratschen, Scharniere
- Lange Designs, die zum Verziehen neigen
- Endverwendungsteile für Umgebungen mit hoher Stoßbelastung oder starkem Verschleiß
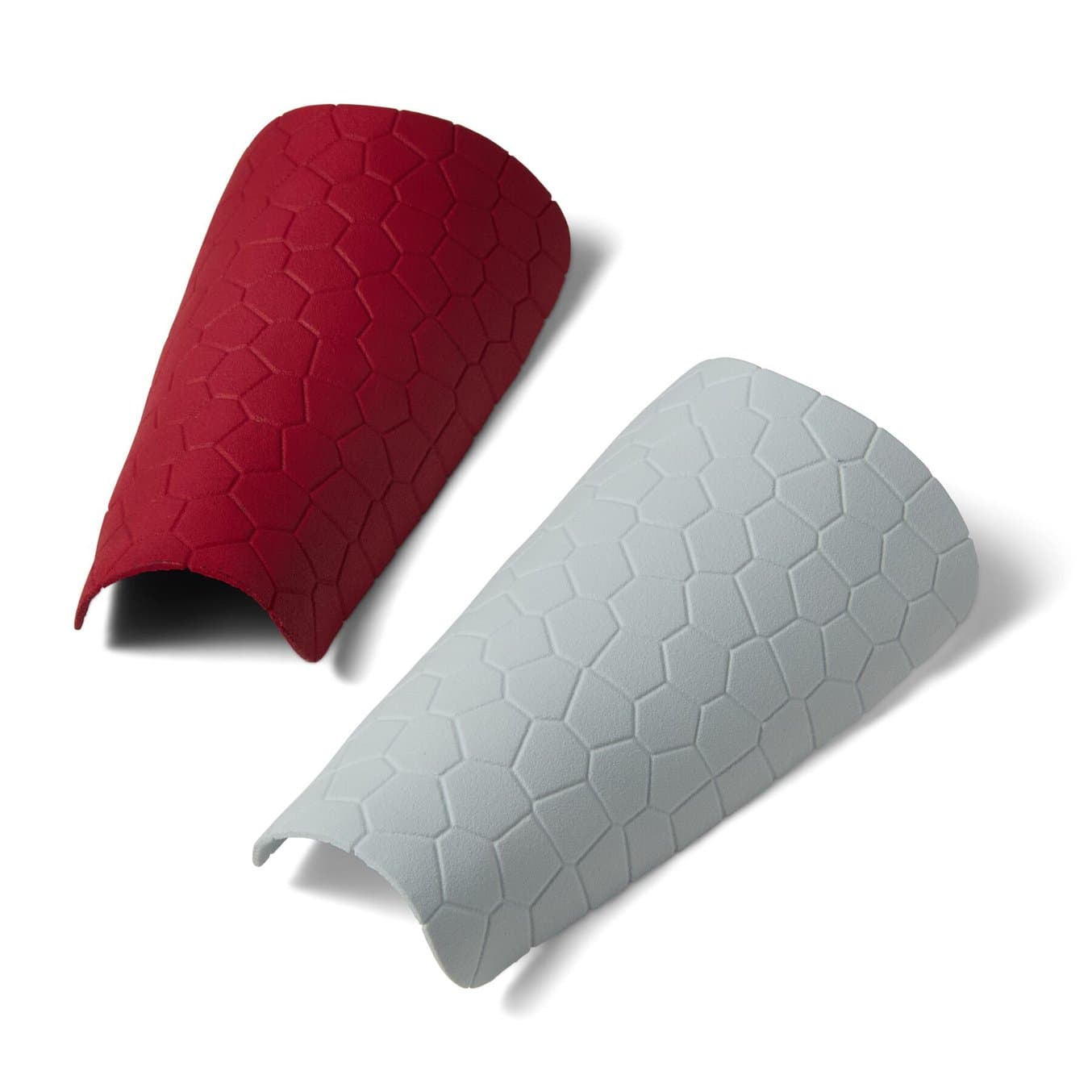
Nylon 12 White Powder
Profitieren Sie von der Zuverlässigkeit, Haltbarkeit und Festigkeit von Nylon 12 Powder mit dem zusätzlichen Vorteil eines einfachen Färbeprozesses.
- Gefärbte, lackierte oder anderweitig eingefärbte Teile
- Visuelle Prototypen nach Markenkonzept
- Biokompatible Medizinprodukte und Operationsschablonen*
- Kleinserienfertigung
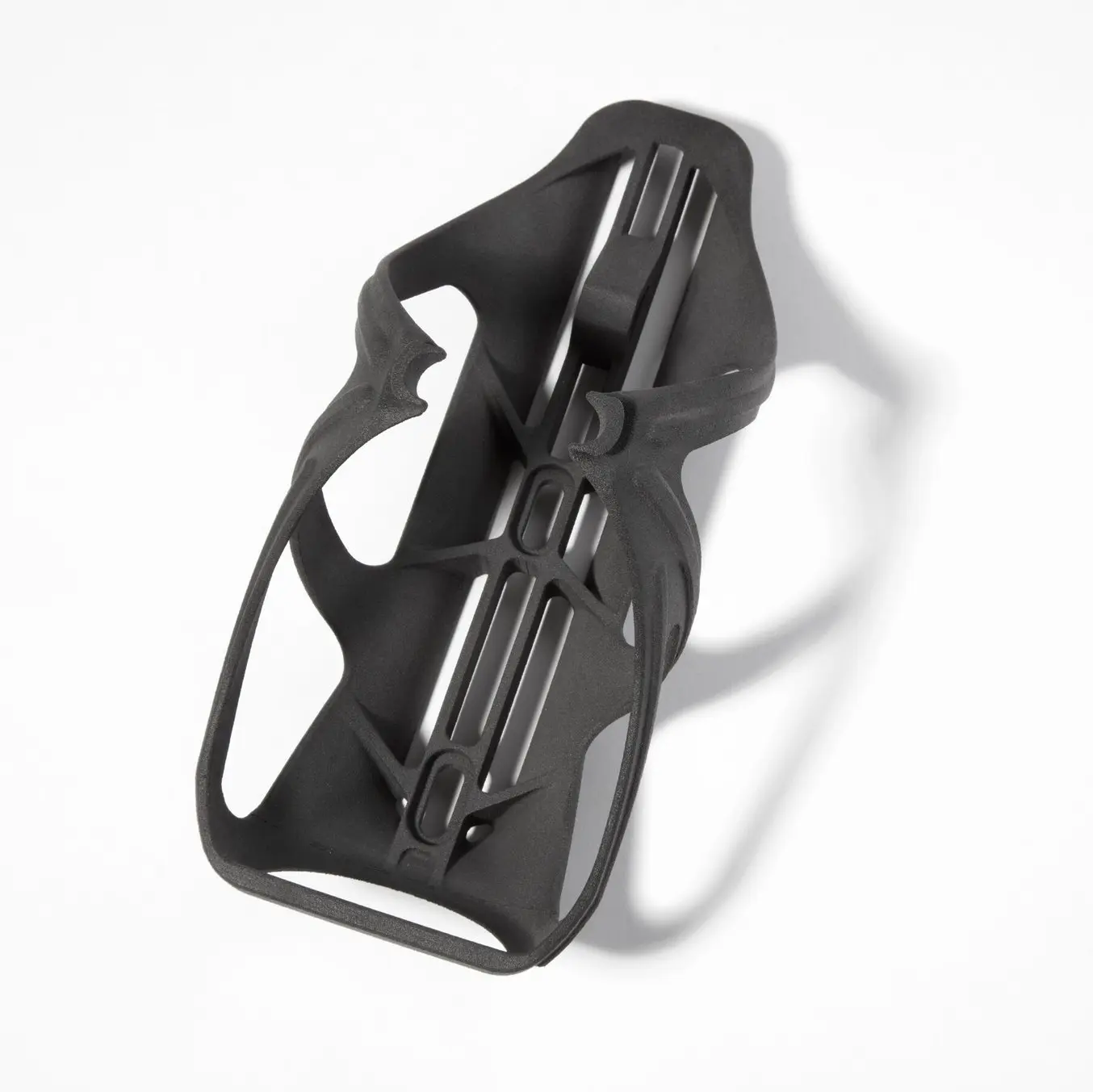
Nylon 11 Powder
Äußerst duktiles, robustes und starkes Material, das entwickelt wurde, um maximale Haltbarkeit und Leistung zu gewährleisten
- Schlagfeste Prototypen, Halterungen und Vorrichtungen
- Dünnwandige Kanäle und Gehäuse
- Einrastelemente, Klammern und Scharniere
- Orthetik und Prothetik*
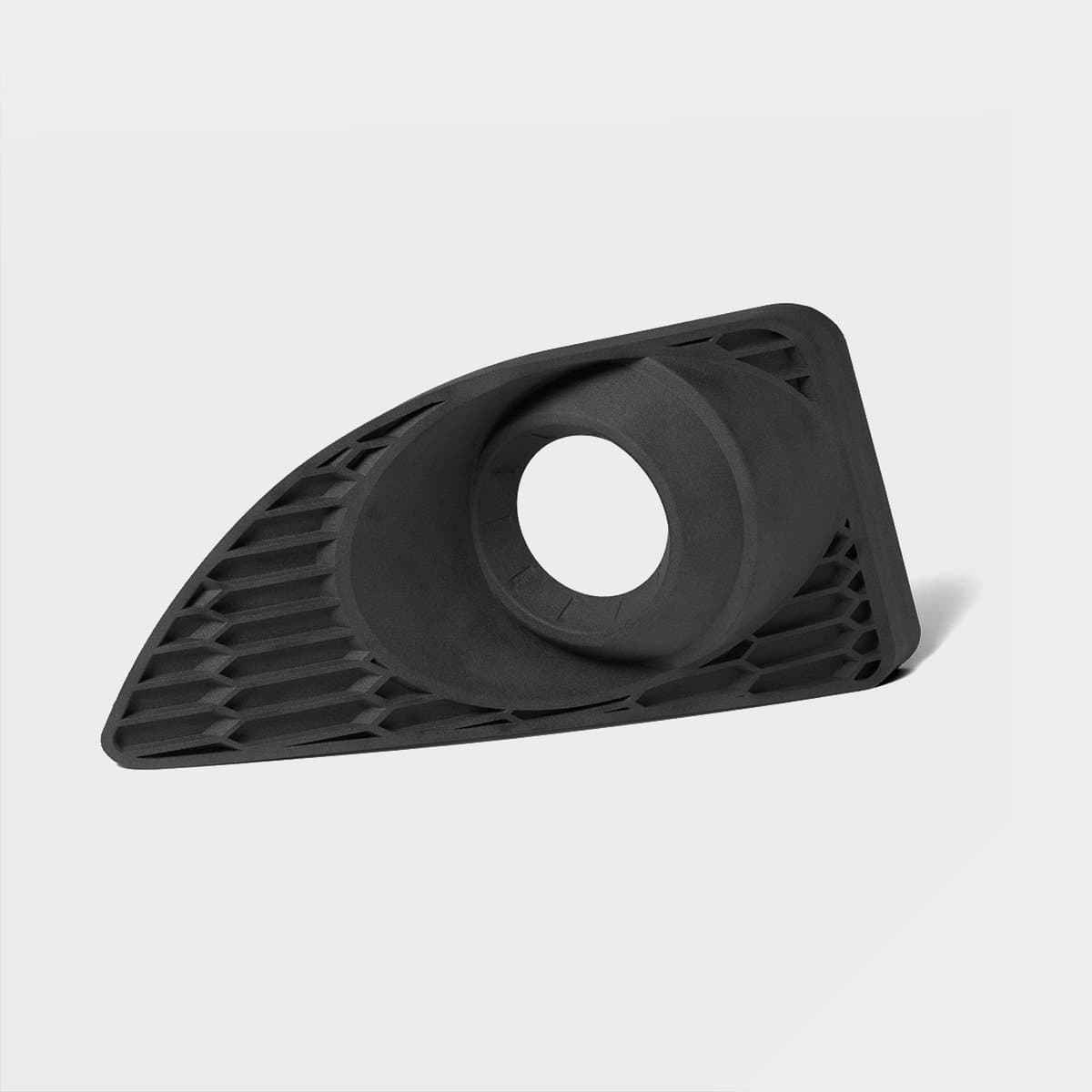
Nylon 12 GF Powder
Ein glasgefülltes Material mit erhöhter Steifigkeit und Wärmebeständigkeit für anspruchsvolle industrielle Umgebungen.
- Robuste Halterungen und Vorrichtungen sowie Ersatzteile
- Teile, die dauerhafter Belastung ausgesetzt sind
- Gewinde und Buchsen
- Teile, die hohen Temperaturen ausgesetzt sind
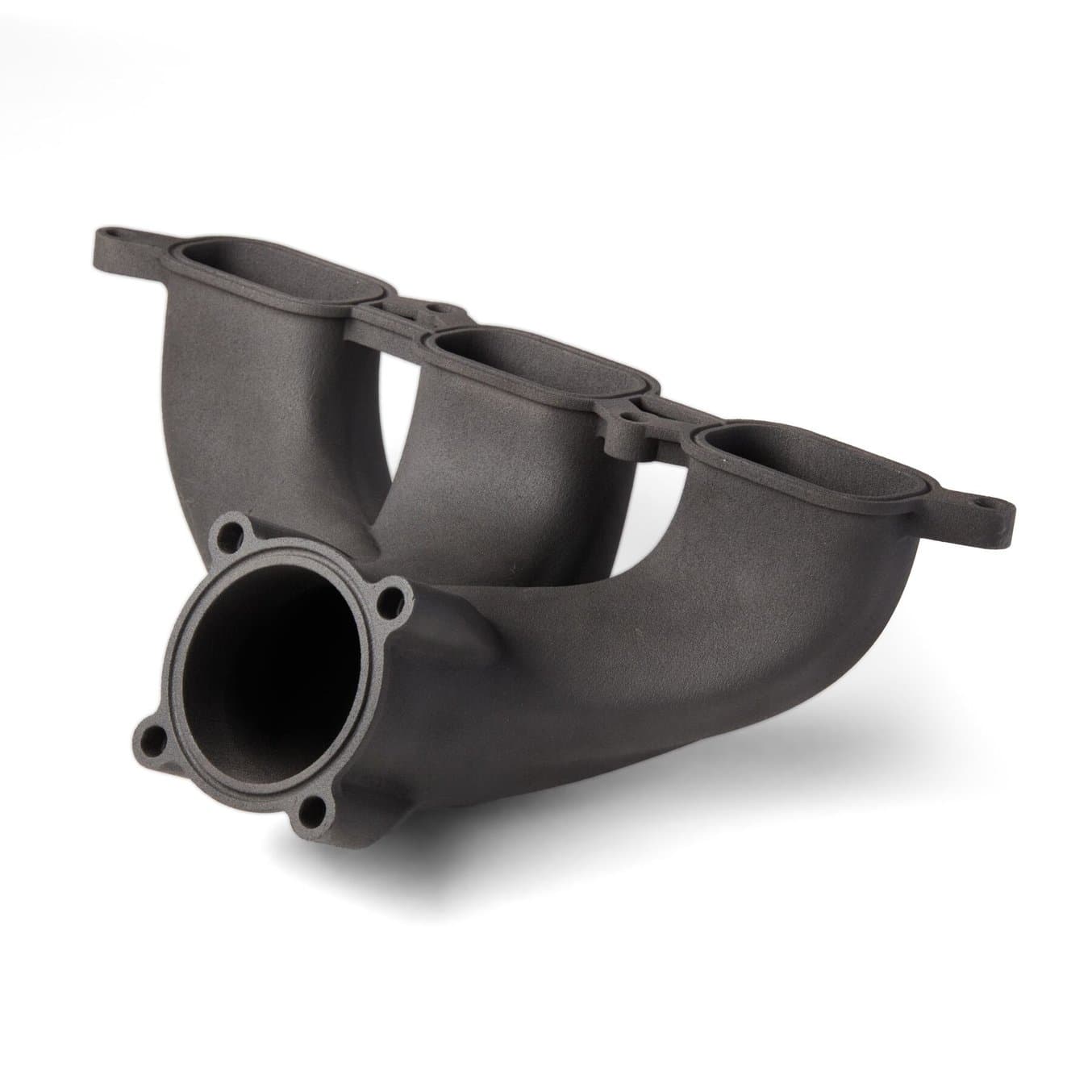
Nylon 11 CF Powder
Alle Vorteile von Nylon und Kohlenstofffaser vereint in einem hochstabilen, leichten und leistungsstarken Material.
- Austausch- und Ersatzteile für Metallkomponenten
- Werkzeuge, Halterungen und Vorrichtungen
- Stoßfeste Geräte
- Funktionsfähige Prototypen aus Verbundwerkstoffen
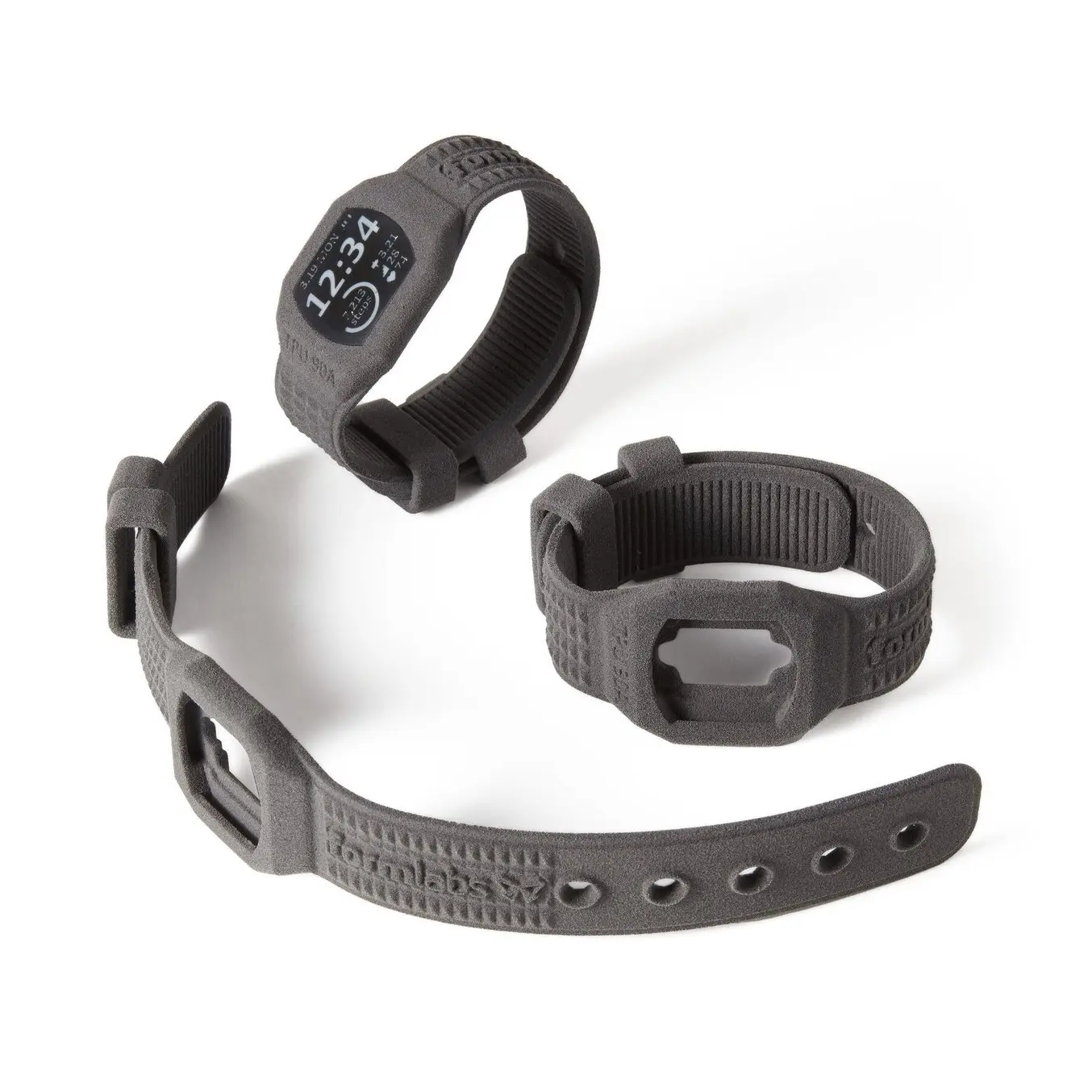
TPU 90A Powder
Ein Elastomer mit hoher Bruchdehnung und erhöhter Reißfestigkeit für flexible, hautverträgliche Prototypen und Endverbrauchsteile.
- Wearables und Komponenten mit weicher Haptik
- Polsterung, Dämpfer und Greifer
- Dichtungen, Abdeckungen, Riemen, Stöpsel und Schläuche
- Sohlen, Schienen, Orthetik und Prothetik*
* Materialeigenschaften können abhängig vom Design der Teile und den Fertigungsabläufen variieren. Es liegt in der Verantwortung des Herstellers, die Eignung der Druckteile für ihren Verwendungszweck zu überprüfen.
Materialeigenschaften der SLS-Pulver von Formlabs im Vergleich
Materialien | Nylon 12 Powder | Nylon 12 Tough Powder | Nylon 12 White Powder | Nylon 11 Powder | Nylon 12 GF Powder | Nylon 11 CF Powder | TPU 90A Powder |
---|---|---|---|---|---|---|---|
Maximale Zugfestigkeit X (MPa) | 50 | 42 | 47 | 49 | 38 | 69 | 8,7 |
Maximale Zugfestigkeit Y (MPa) | Keine Angabe | Keine Angabe | Keine Angabe | Keine Angabe | Keine Angabe | 52 | 8,7 |
Maximale Zugfestigkeit Z (MPa) | Keine Angabe | Keine Angabe | Keine Angabe | Keine Angabe | Keine Angabe | 38 | 7,2 |
Elastizitätsmodul X (MPa) | 1850 | 1450 | 1950 | 1600 | 2800 | 5300 | Keine Angabe |
Bruchdehnung, X/Y (%) | 11 | 25 | 8 | 40 | 4 | 9 / 15 | 310 |
Bruchdehnung, Z (%) | 6 | 15 | 6 | Keine Angabe | 3 | 5 | 110 |
HDT bei 0,45 MPa (°C) | 171 | 161 | 177 | 182 | 170 | 188 | Keine Angabe |
Schlagzähigkeit nach Izod (J/m) | 32 | 60 | 28 | 71 | 36 | 74 | Keine Angabe |
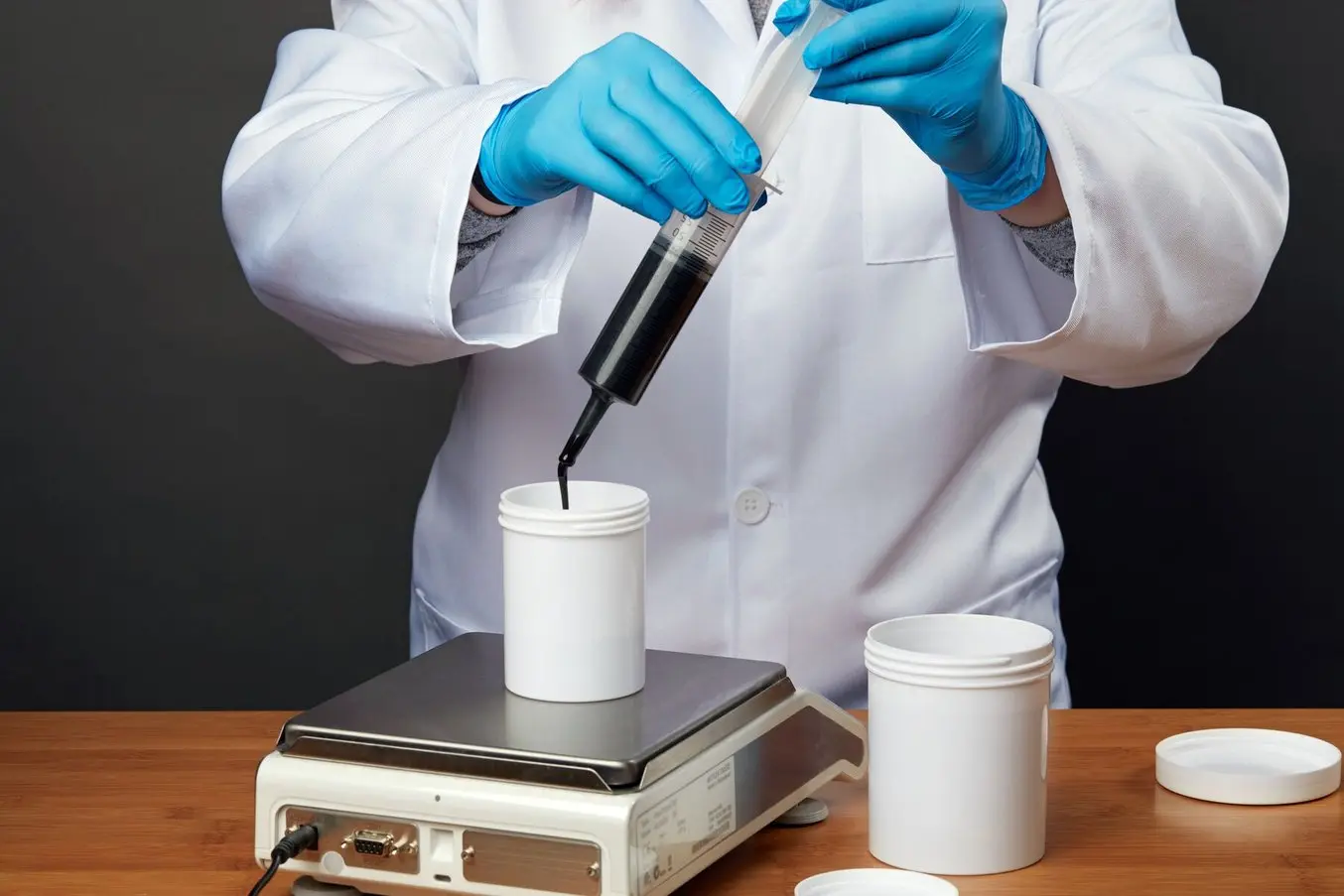
Formlabs als offene Plattform
Maximieren Sie das Potenzial Ihres 3D-Druckers mit Formlabs Developer Platform. Drucken Sie auf Formlabs-3D-Druckern mit jedem bei 405 nm härtenden Photopolymerharz bzw. jedem bei 1064 nm sinterbaren Pulver, legen Sie Ihre Druckeinstellungen individuell fest oder entwickeln Sie Softwareintegrationen.
Anwendungen für SLS-3D-Druck
Der SLS-3D-Druck beschleunigt die Innovation und unterstützt Unternehmen in einer Vielzahl von Branchen, darunter im Maschinenbau, der Fertigung und dem Gesundheitswesen.
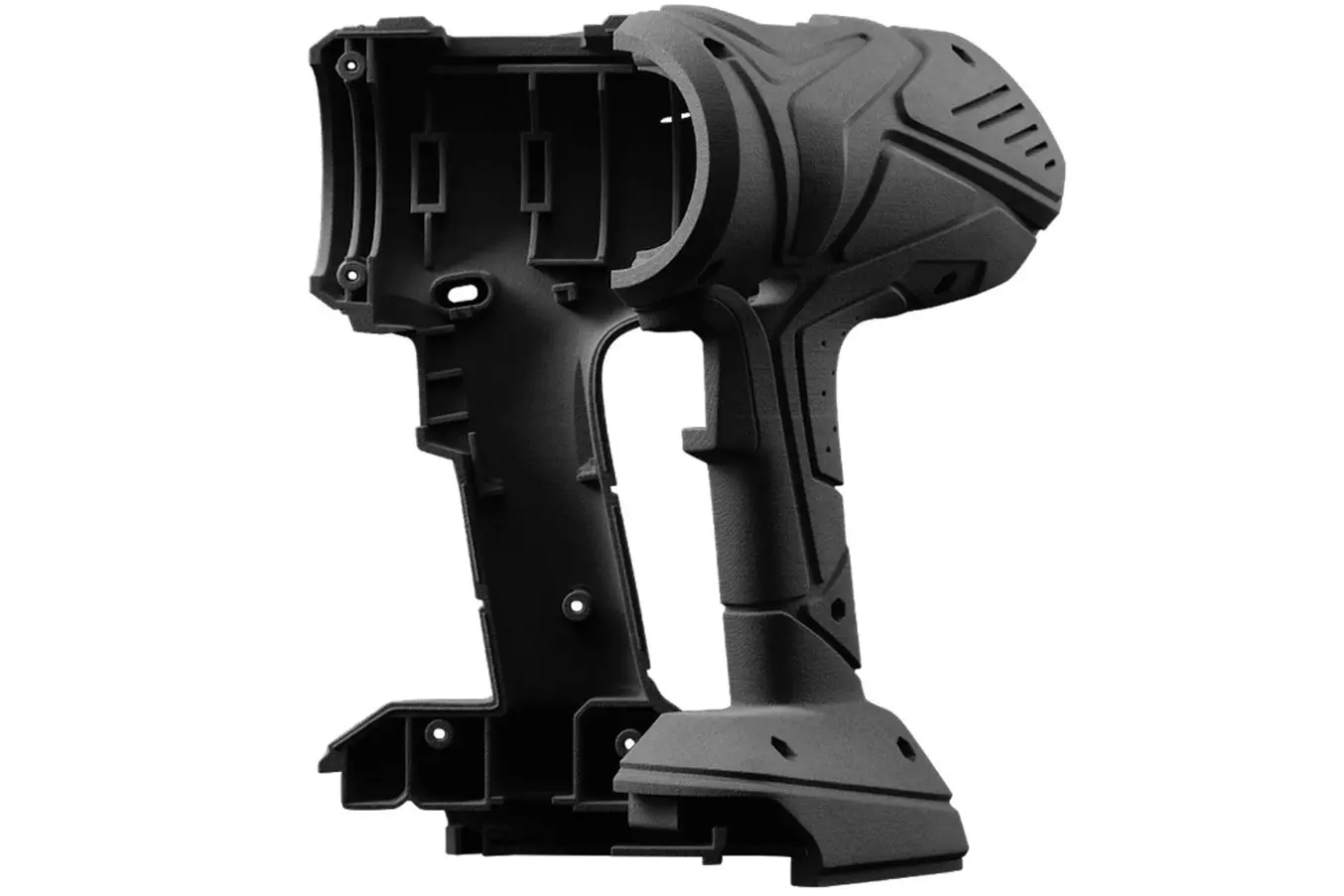
Maschinenbau
Übernehmen Sie die Kontrolle über Ihren gesamten Produktentwicklungsprozess, von der Iteration des ersten Konzeptdesigns zur Herstellung von Produkten für die Endverwendung:
- Rapid Prototyping
- Produktmodelle für praktisches Kundenfeedback
- Funktionsfähige Prototypen
- Anspruchsvolle Funktionstests von Produkten (z. B. Leitungen, Halterungen)
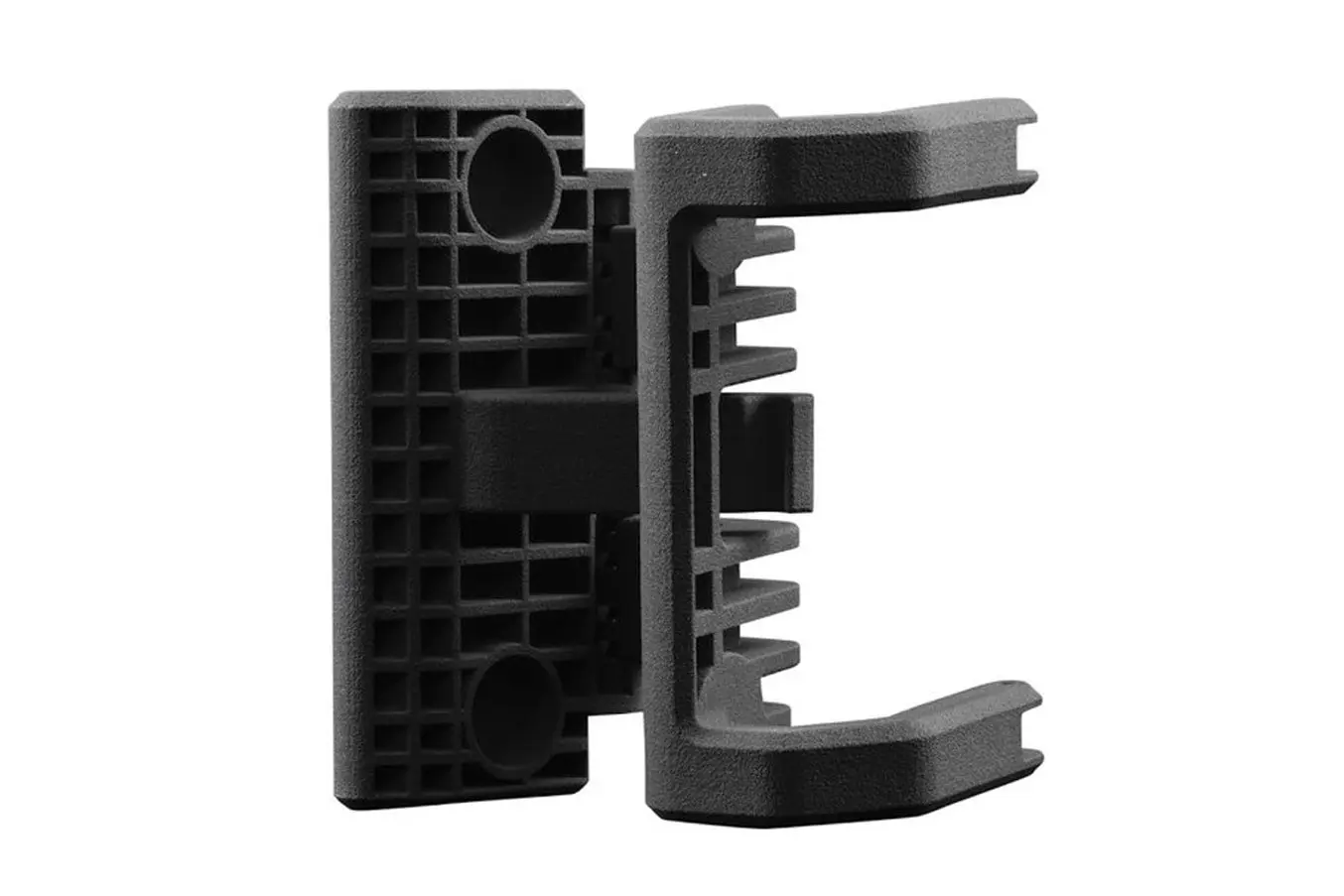
Fertigung
Behalten Sie Kontrolle über Ihre Lieferkette und reagieren schnell Sie auf sich verändernde Anforderungen:
- Produktion für die Endverwendung
- Kleinserienfertigung, Zwischenlösungen und Bridge Manufacturing
- Kundenindividuelle Massenproduktion von Konsumgütern
- Ersatzteile, Aftermarket-Produkte, Austauschteile
- Haltbare, belastbare Fertigungshilfen, Halterungen, Vorrichtungen und Werkzeuge
- Individuelle Kfz- und Motorradteile, Schiffsausrüstung, „Versorgung auf Nachfrage“ im Verteidigungssektor
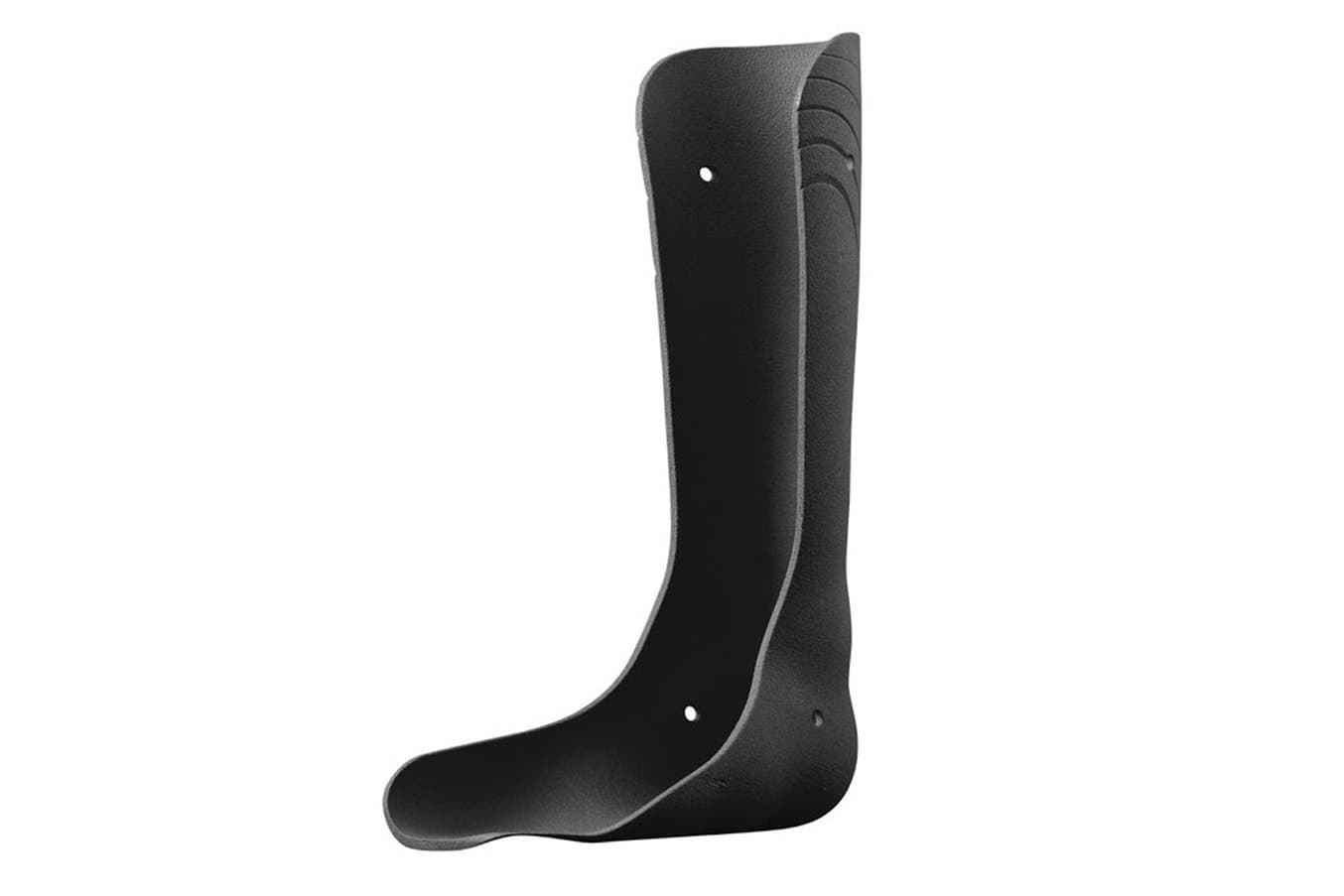
Gesundheitsversorgung
Stellen Sie patientenspezifische Medizinprodukte für die Endverwendung intern her:
- Prototypenentwicklung für Medizinprodukte
- Prothetik und Orthetik (z. B. Prothesen und Schienen)
- Chirurgiemodelle und Instrumente
- Teile für die Endverwendung*
* Materialeigenschaften können abhängig vom Design der Teile und den Fertigungsabläufen variieren. Es liegt in der Verantwortung des Herstellers, die Eignung der Druckteile für ihren Verwendungszweck zu überprüfen.
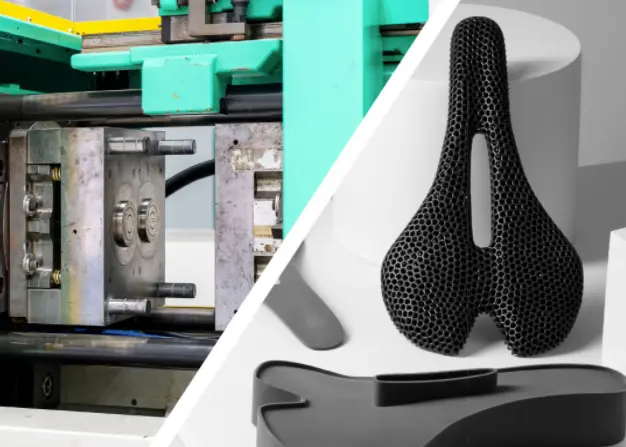
SLS-3D-Druck oder Spritzguss: Wann sollte man Spritzgussteile durch 3D-Druck ersetzen?
Dieses Whitepaper zeigt die Kostendynamik für Anwendungsfälle aus der Praxis und stellt Leitfäden vor für den Einsatz von SLS-3D-Druck, Spritzguss oder einer Kombination beider Verfahren.
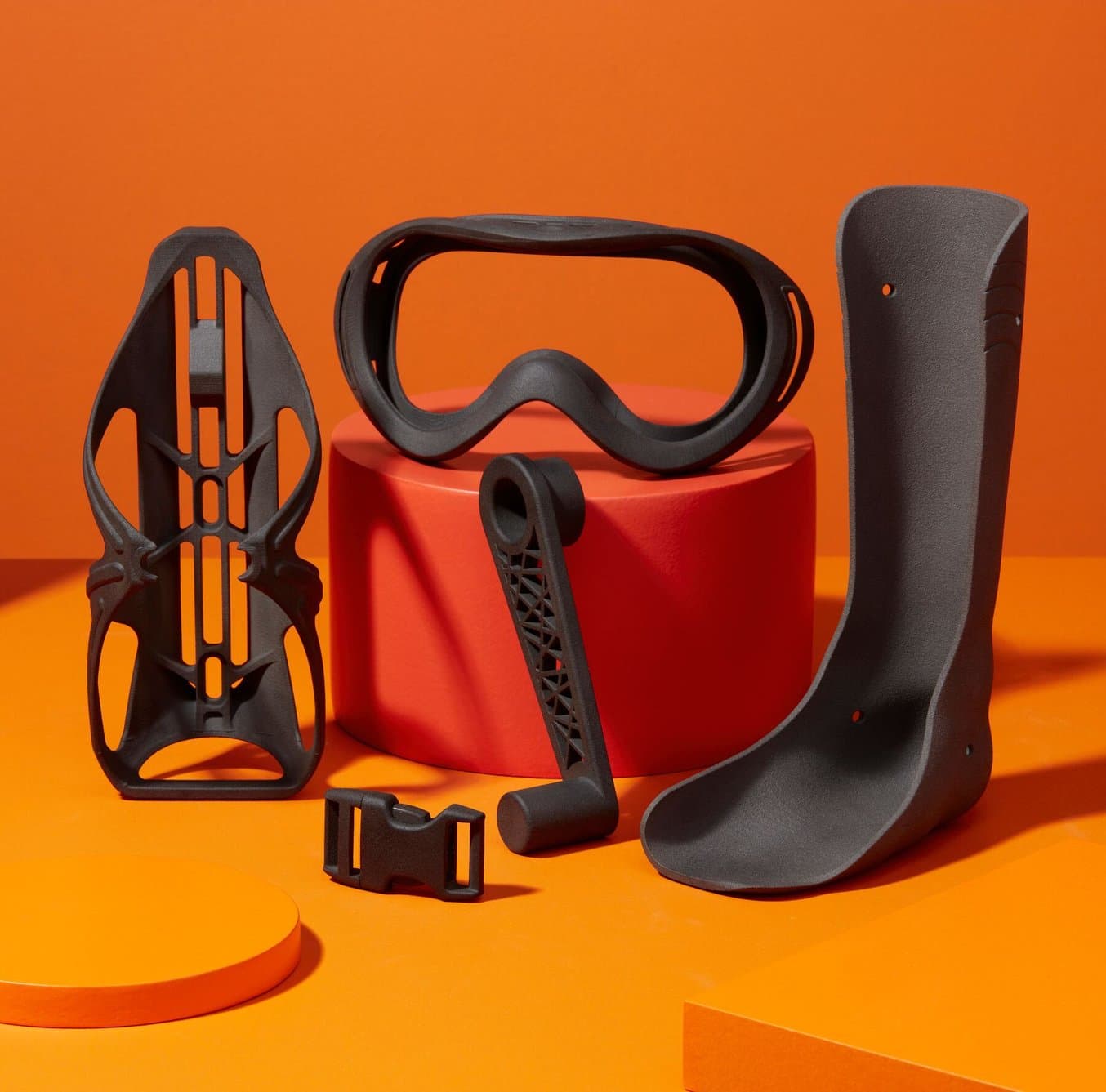
Wie Sie passende Anwendungen für SLS-Druck identifizieren
Erfahren Sie in diesem Webinar, weshalb die additive Fertigung mit erschwinglichen SLS-3D-Druckern in Industriequalität eine taugliche Alternative für die Produktion von Teilen für die Endverwendung und die kundenindividuelle Massenfertigung ist.
Arbeitsablauf beim SLS-3D-Druck
In diesem Video erlernen Sie Schritt für Schritt den Arbeitsprozess mit unseren SLS-3D-Druckern der Fuse-Serie sowie mit unserer Pulverrückgewinnungsstation Fuse Sift.
1. Design und Vorbereitung der Datei
Konstruieren Sie Ihr Modell mit einer beliebigen CAD-Software oder 3D-Scandaten und exportieren Sie es in einem für den 3D-Druck geeigneten Dateiformat (STL, OBJ oder 3MF). Jeder SLS-Drucker verfügt über eine Software mit feinjustierten Druckeinstellungen, mit der Teile ausgerichtet und angeordnet, Druckzeiten berechnet und die digitalen Modelle für den Druck in Schichten zerteilt werden. Sobald die Einrichtung abgeschlossen ist, sendet die Druckvorbereitungssoftware die Anweisungen über eine Drahtlos- oder Kabelverbindung an den Drucker.
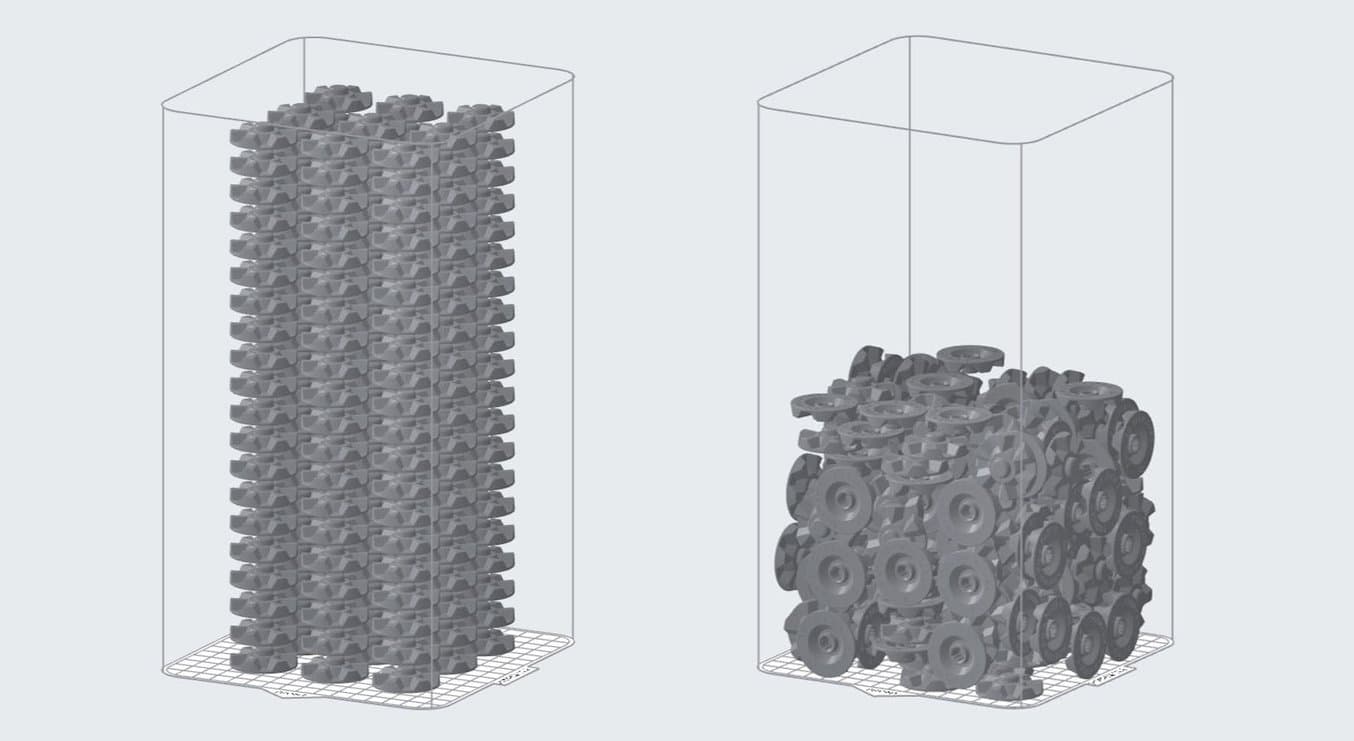
Bei Druckern der Fuse-Serie kommt die kostenlos installierbare Druckvorbereitungssoftware PreForm zum Einsatz. Sie ermöglicht Ihnen das nahtlose Duplizieren und Organisieren mehrerer Teile innerhalb eines 3D-Rasters, um für einzelne Druckvorgänge so viel Konstruktionsraum wie möglich zu nutzen. PreForm schlägt die optimale Ausrichtung und Teilepackung automatisch vor. Manuelle Anpassungen sind bei Bedarf ebenfalls möglich.
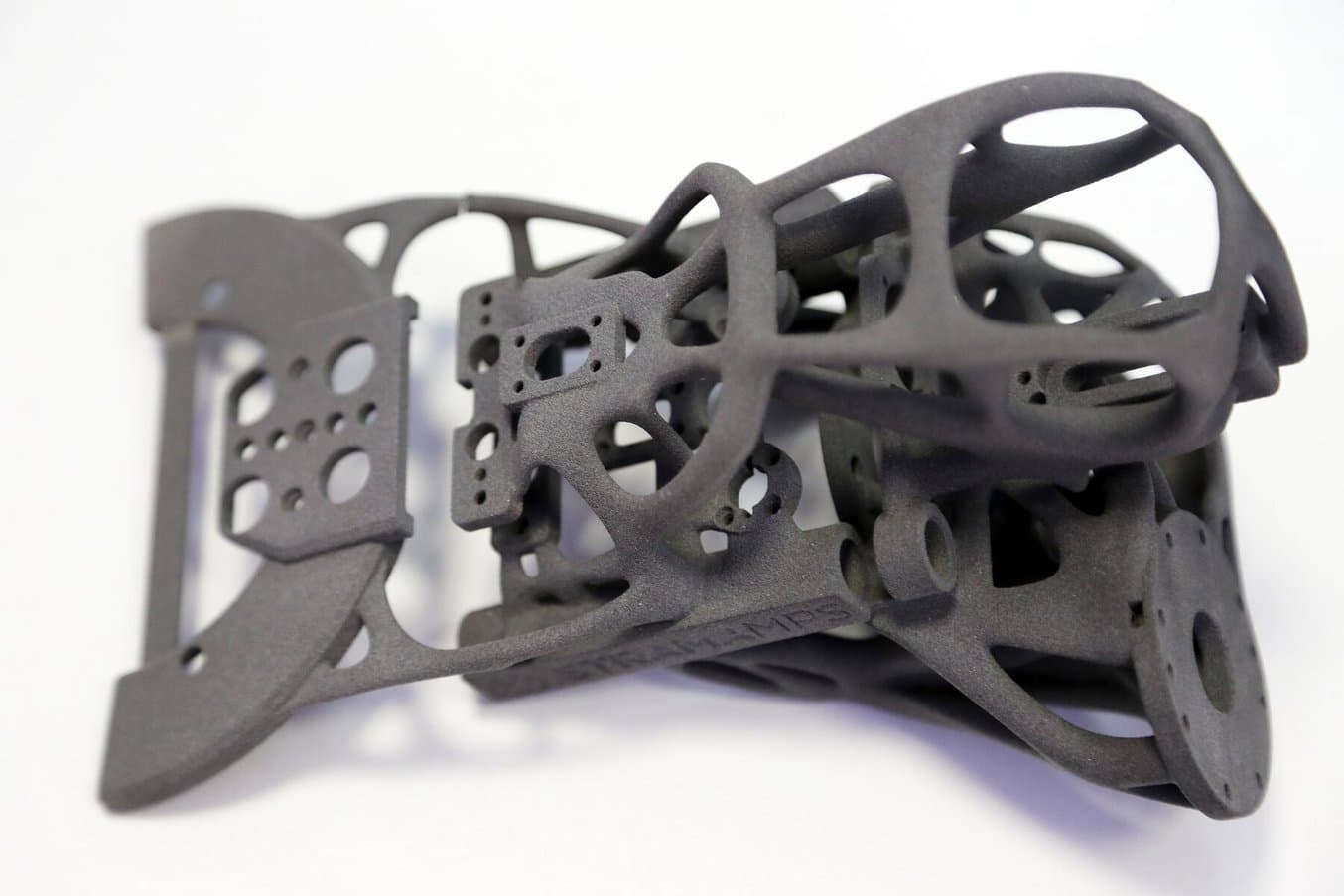
Design-Leitfaden für die Fuse-Serie
Dieser Leitfaden behandelt die wichtigen Abmessungen und Designüberlegungen, die bei der Konstruktion von Teilen für den SLS-3D-Druck auf der Fuse-Serie zu beachten sind. Sie lernen, wie Sie sich diese Praktiken zunutze machen, um leistungsstarke Teile zu produzieren.
2. Vorbereitung des Druckers
Der Arbeitsablauf zum Vorbereiten des Druckers hängt vom System ab. Die meisten traditionellen SLS-Systeme erfordern umfangreiche Schulungen, Werkzeuge und körperliche Anstrengung für Vorbereitung und Wartung.
Die Drucker der Fuse-Serie revolutionieren den SLS-Arbeitsablauf mit ihrer Einfachheit und Effizienz, wobei modulare Bauteile unterbrechungsfreien Druck und einen geschlossenen Pulverkreislauf ermöglichen.
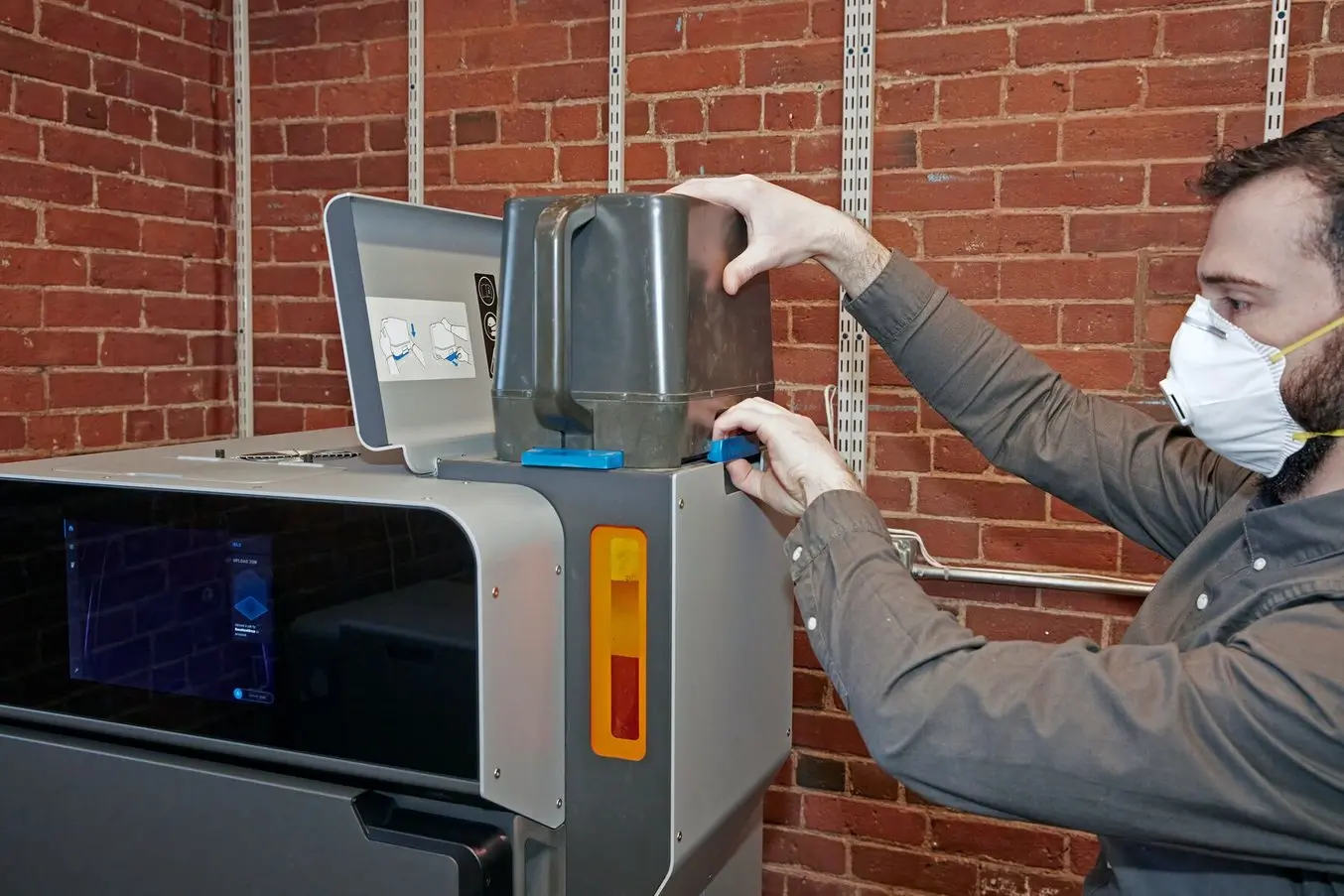
Bei Druckern der Fuse-Serie ist das Beladen mit Pulver ganz leicht mit der Pulverkartusche machbar.
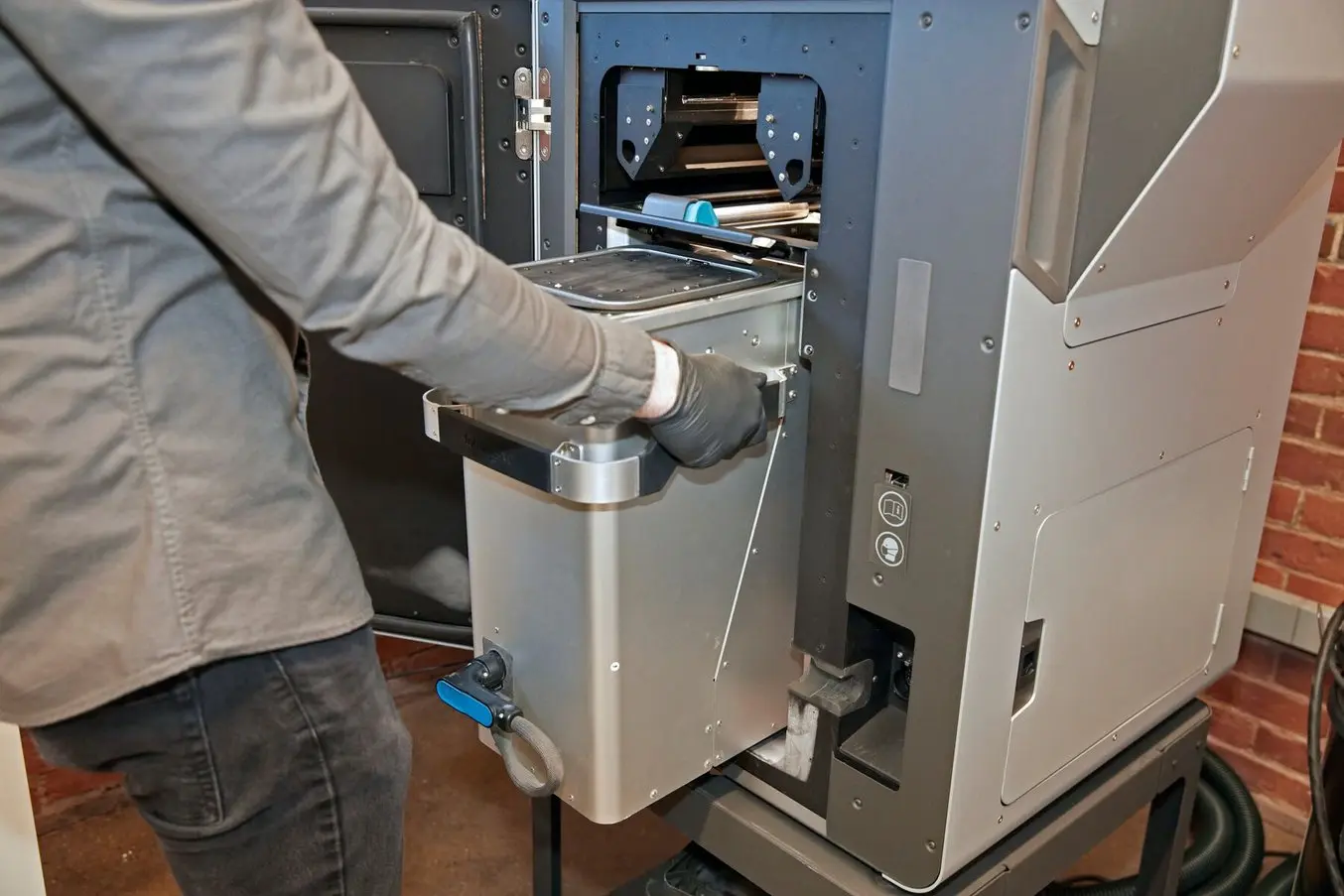
Die Drucker der Fuse-Serie verfügen über eine herausnehmbare Konstruktionskammer, wodurch sie bereits einen neuen Druck durchführen können, während der aktuelle Druck abkühlt.
3. Druck
Wenn alle vor dem Druck notwendigen Überprüfungen abgeschlossen sind, ist das Gerät druckbereit. Die Druckzeit kann bei SLS-3D-Drucken wenige Stunden oder gar mehrere Tage betragen. Dies hängt von der Größe und Komplexität der Teile sowie von der Packdichte ab. Dank seines Hochleistungslasers schließt der Fuse 1+ 30W üblicherweise selbst Druckaufträge mit vollen Konstruktionskammern innerhalb von 24 Stunden ab.
Nachdem ein Druck abgeschlossen ist, muss die Konstruktionskammer im Druckergehäuse vor dem nächsten Schritt etwas abkühlen. Anschließend kann die Konstruktionskammer entnommen und eine neue eingesetzt werden, um den nächsten Druck zu starten.
Vor der Nachbearbeitung muss die Konstruktionskammer mit den Druckteilen noch stärker abkühlen, damit die optimalen mechanischen Eigenschaften sichergestellt sind und ein Verziehen der Teile vermieden wird. Dieser Vorgang kann die Hälfte der Druckzeit beanspruchen.
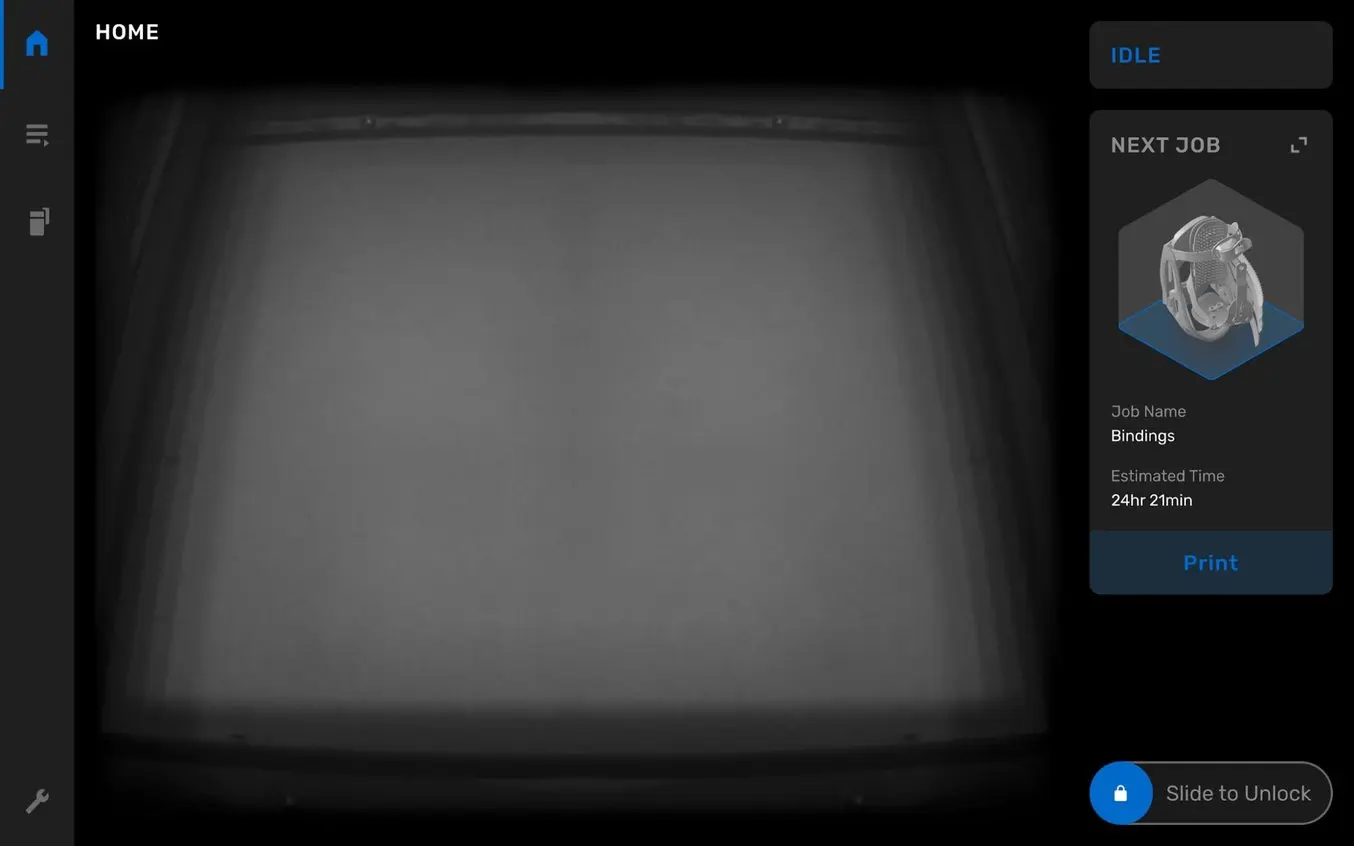
Der Touchscreen auf den Druckern der Fuse-Serie zeigt einen Livestream des Druckbetts, sodass Sie beobachten können, wie jede neue Schicht Gestalt annimmt. Diese Kameraansicht ist auch von Ihrem Computer aus in PreForm verfügbar, sodass Sie Ihren Druck im Auge behalten, ohne Ihren Arbeitsplatz zu verlassen.
4. Teileentnahme und Pulverrückgewinnung
Die Nachbearbeitung von SLS-Teilen nimmt im Vergleich zu anderen 3D-Druckverfahren wenig Zeit und Aufwand in Anspruch. Sie lässt sich leicht skalieren und liefert einheitliche Ergebnisse bei den Chargen, da keine Stützstrukturen erforderlich sind.
Nachdem eine Konstruktionskammer abgekühlt ist, können die Druckteile entnommen und aus dem ungesinterten Pulver extrahiert werden. Hierfür stehen verschiedene Lösungen zur Verfügung, angefangen von kostengünstigeren Hilfsmitteln für die manuelle Pulverrückgewinnung wie dem Fuse Depowdering Kit bis hin zu Allround-Stationen für die Pulverhandhabung wie dem Fuse Sift, der sich sowohl für die Trennung von Teilen und ungesintertem Pulver als auch für die Lagerung, Dosierung und Mischung von Pulver eignet.
Überschüssiges Pulver, das nach der Teileentnahme verbleibt, wird gefiltert, um größere Partikel zu entfernen, und kann anschließend recycelt werden. Nicht verschmolzenes Pulver büßt durch die hohen Temperaturen geringfügig an Qualität ein, sodass es für nachfolgende Druckaufträge mit neuem Material aufgefrischt werden sollte. Aufgrund der Wiederverwertbarkeit des Materials für Folgeaufträge ist SLS eine der abfallärmsten Fertigungsmethoden.
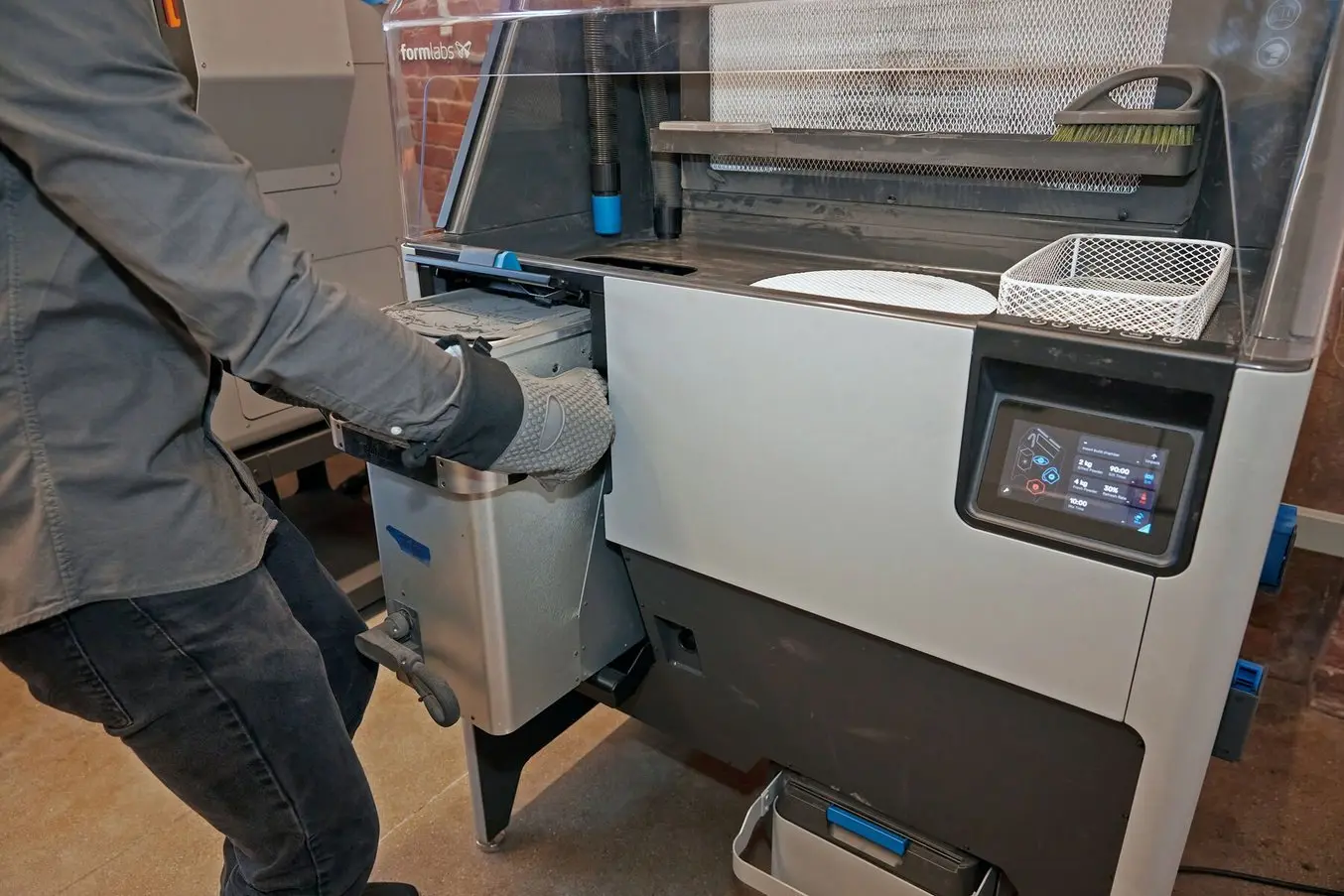
Der SLS-Arbeitsablauf mit Druckern der Fuse-Serie durch den Fuse Sift ergänzt. Er ist ein sicheres und effizientes System zur Entnahme von Druckteilen und zur Pulverrückgewinnung.
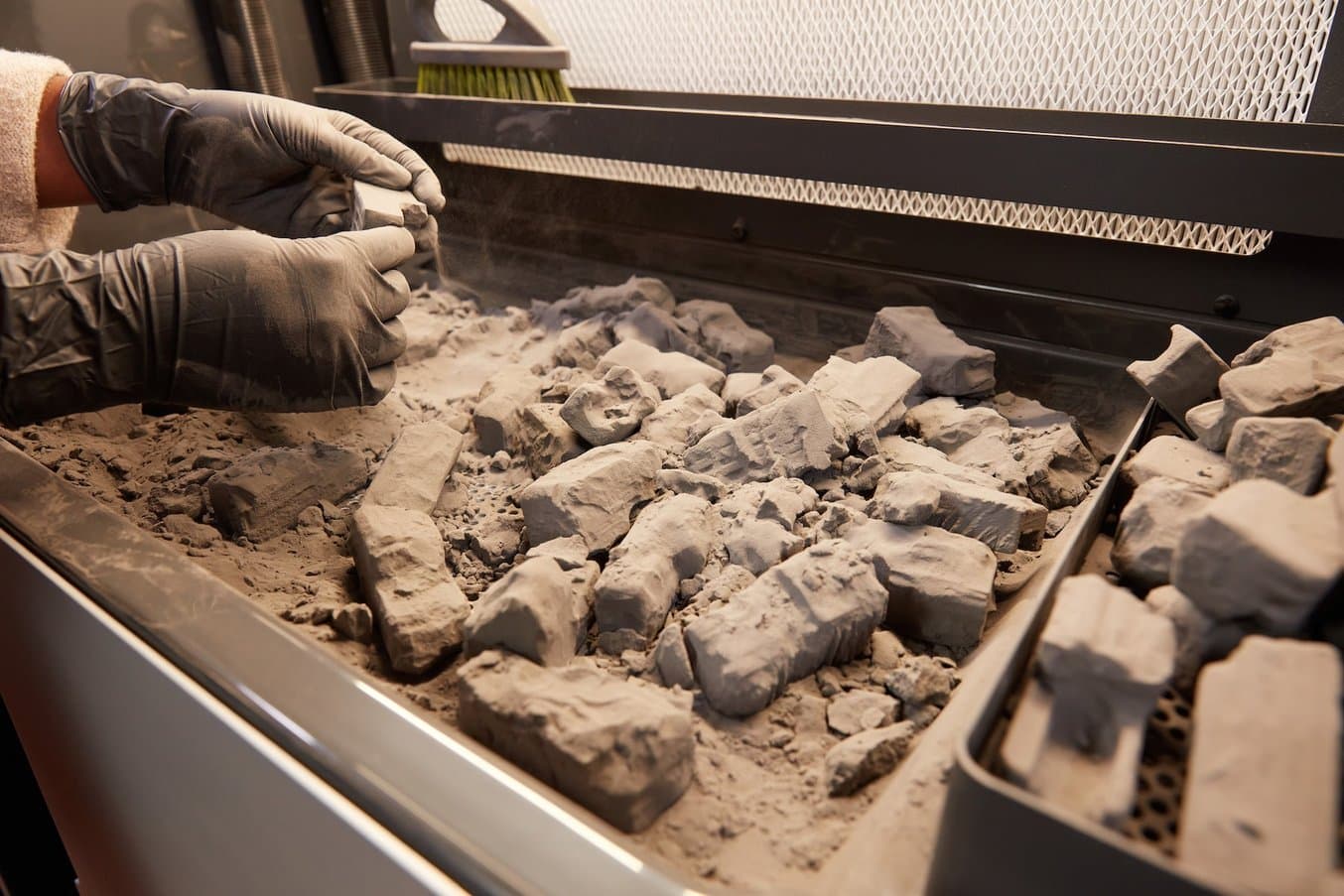
Der Fuse Sift gibt gebrauchtes und neues Pulver automatisch ab und mischt sie, sodass Sie Abfall reduzieren und Ihren Pulvervorrat kontrollieren können.
5. Nachbearbeitung
Nach der Extraktion aus dem sogenannten Pulverkuchen ist das Sandstrahlen für die vollständige Entpulverung von SLS-3D-gedruckten Teilen entscheidend. Außerdem lässt sich dadurch ein glattes, pulverfreies Oberflächenfinish erreichen. Durch das Sandstrahlen werden loses Pulver und die halbgesinterte Hülle (Surface Armor) von den Druckteilen entfernt.
Auf dem Markt sind zu unterschiedlichen Preisniveaus verschiedene Lösungen zur manuellen oder automatischen Bestrahlung verfügbar. Der Fuse Blast von Formlabs ist die erste erschwingliche automatisierte Sandstrahlanlage, die entweder zur Vervollständigung des SLS-Ecosystems der Fuse-Serie dient oder als druckerunabhängiges Strahlgerät mit anderen Arten von 3D-Druckern auf Basis von Pulverbettfusion eingesetzt werden kann.
Mithilfe des Sandstrahlens wird der zeitaufwändigste und körperlich anspruchsvollste Teil des SLS-Workflows drastisch verkürzt. Durch die Ergänzung des Nachbearbeitungsprozesses mit dem Fuse Sift durch den Fuse Blast lässt sich der Zeitaufwand für die Reinigung auf gerade einmal 15 Minuten verkürzen – das entspricht einer 80%igen Verringerung der durchschnittlichen manuellen Arbeitsdauer.
Zusätzlich zur bloßen Reinigung erledigt das optionale Poliersystem des Fuse Blast in einem geschlossenen Komplettsystem auch noch die Oberflächenveredelung. Die Politur im Fuse Blast liefert innerhalb von 15 Minuten Teile, die nicht nur frei von Pulverrückständen sind, sondern auch glatt, abriebfest und bereit für das Lackieren, dank einer professionellen, halbglänzenden Oberflächengüte. Das konzentrierte Strahlmittel schleift effizient die mikroskopischen Rillen ab, die die typische raue Oberflächenbeschaffenheit von SLS-Teilen verursachen. Das sorgt für eine Glättung der Oberfläche und einer Verminderung ihrer Porosität.
Abgesehen von den standardmäßigen Nachbearbeitungsschritten gibt es zahlreiche fortgeschrittene Nachbearbeitungstechniken für SLS-Teile, die dazu dienen, ein glatteres Oberflächenfinish zu schaffen, die chemische Beständigkeit zu steigern, die Oberflächenhärte zu reduzieren, die Farbe zu ändern, Teile leitfähig zu machen und mehr.
Lesen Sie hierzu unseren Beitrag, in dem wir die Optionen separat behandeln. Falls Sie daran interessiert sind, Nachbearbeitungstechniken zu kombinieren, um ein bestimmtes Ergebnis zu erreichen, kontaktieren Sie unser Expertenteam für eine Beratung zu Ihrem Anwendungsfall.
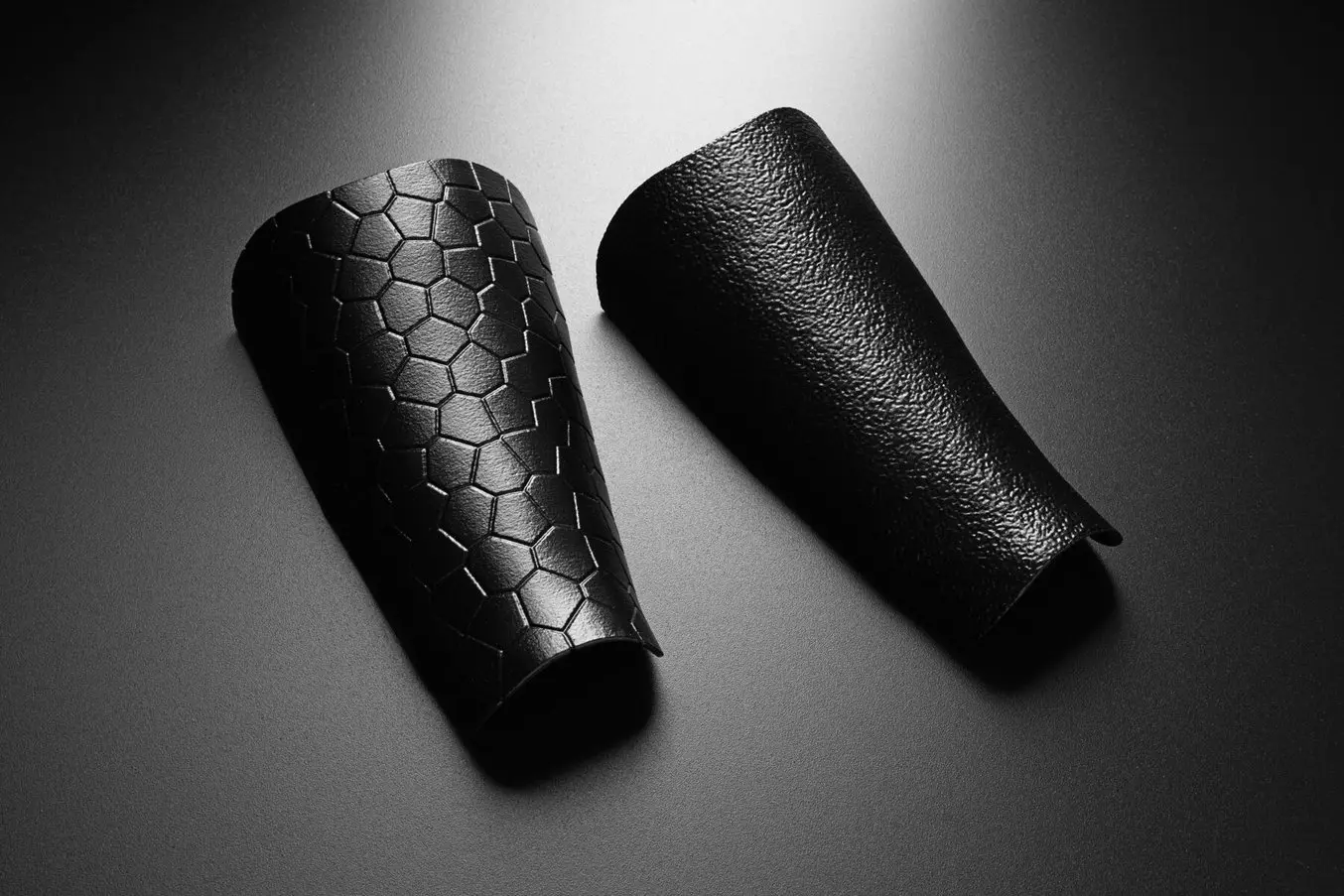
Mithilfe von chemischer Dampfglättung erreichen SLS-Teile eine vergleichbare Oberflächenqualität und Haltbarkeit wie Spritzgussteile.
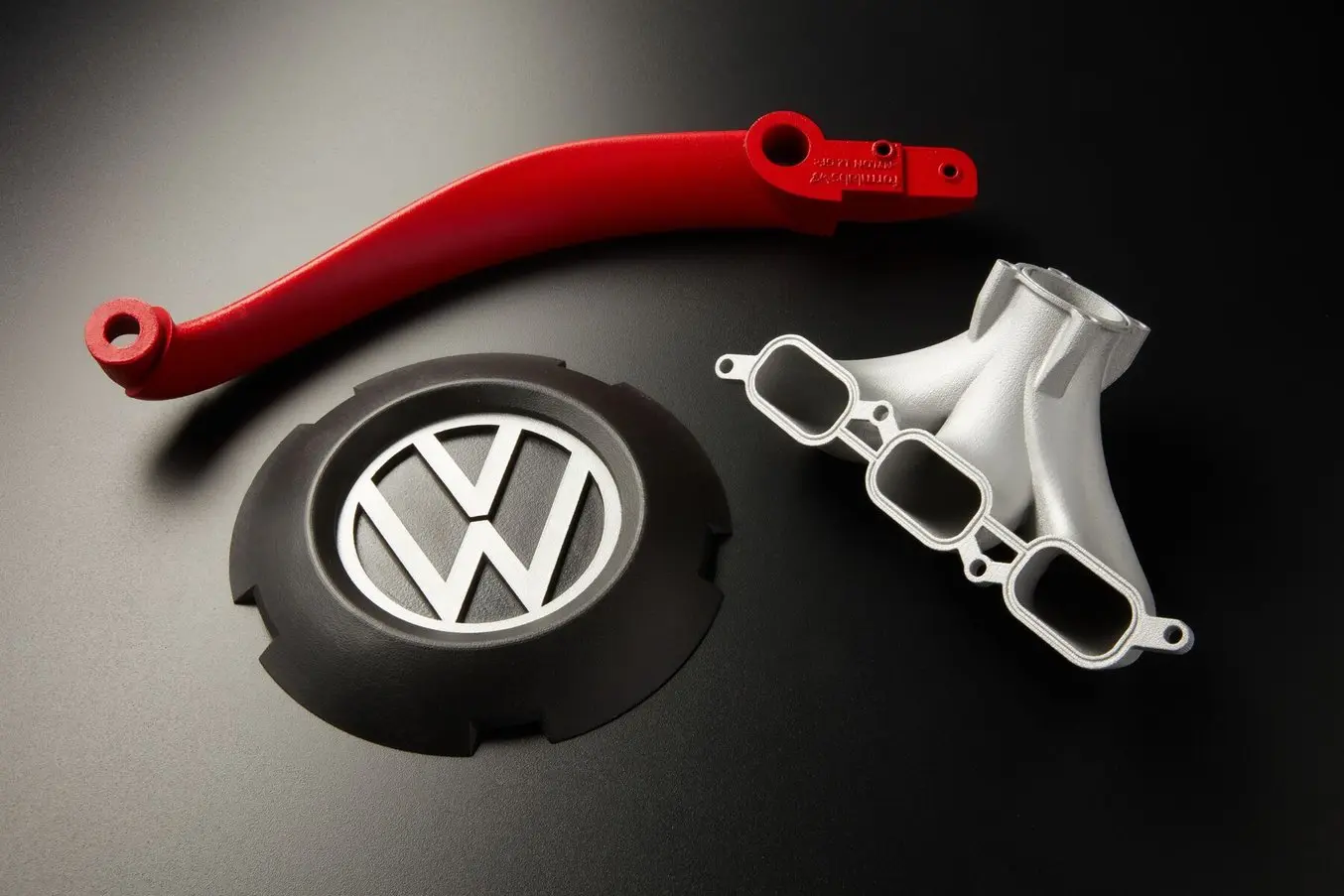
Keramikbeschichtungen wie die von Cerakote liefern Vorteile sowohl in Bezug auf Leistung als auch Ästhetik, wie zum Beispiel leuchtende Farben.
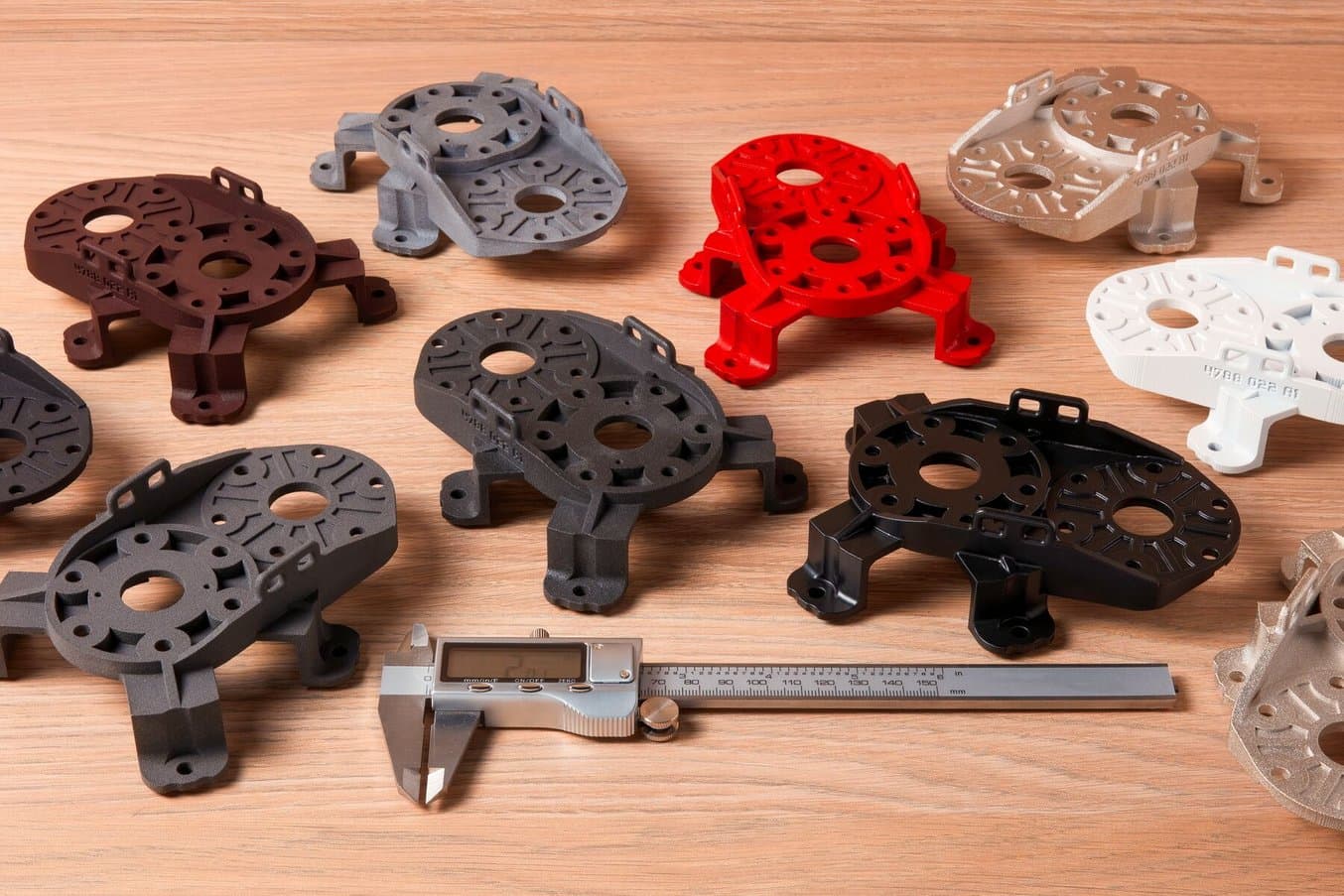
Fortgeschrittene Nachbearbeitungstechniken für den 3D-Druck
In diesem Webinar erfahren Sie alles Wissenswerte zu mehr als 11 fortgeschrittenen Nachbearbeitungstechniken für den 3D-Druck, unter anderem Cerakote-Beschichtung, Galvanisierung und chemische Dampfglättung.
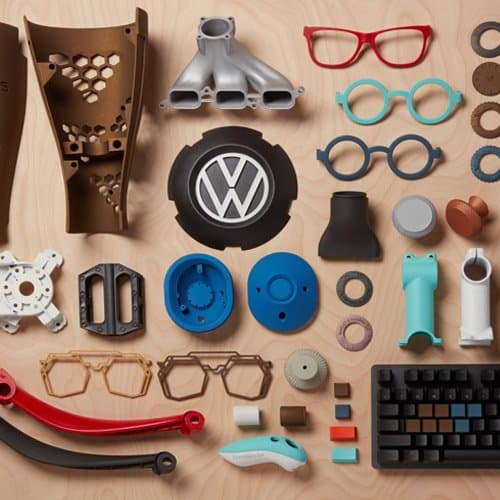
Wie Sie mit fortschrittlichen Keramikbeschichtungen hochleistungsfähige 3D-Druckteile herstellen
In unserem Webinar erfahren Sie, wie das Auftragen der Keramikbeschichtungen von Cerakote die Leistung Ihrer 3D-Druckteile steigern kann.
Welche Gründe sprechen für SLS?
Ingenieurteams und Hersteller wählen SLS aufgrund der Gestaltungsfreiheit, der hohen Produktivität und des hohen Durchsatzes, der niedrigeren Stückkosten und der bewährten Materialien für die Endverwendung.
Gestaltungsfreiheit
Bei den meisten additiven Fertigungsverfahren, wie Stereolithografie (SLA) und Schmelzschichtung (FDM), sind zur Herstellung von Designs mit überhängenden Merkmalen spezielle Stützstrukturen notwendig.
Beim selektiven Lasersintern sind keine Stützstrukturen erforderlich, da nicht gesintertes Pulver das Teil während des Drucks umgibt. Mit SLS lassen sich daher komplizierte Geometrien umsetzen, die bisher unmöglich waren, wie beispielsweise ineinandergreifende oder bewegliche Teile, Teile mit Innenkomponenten oder Kanälen sowie weitere höchst komplexe Formen.
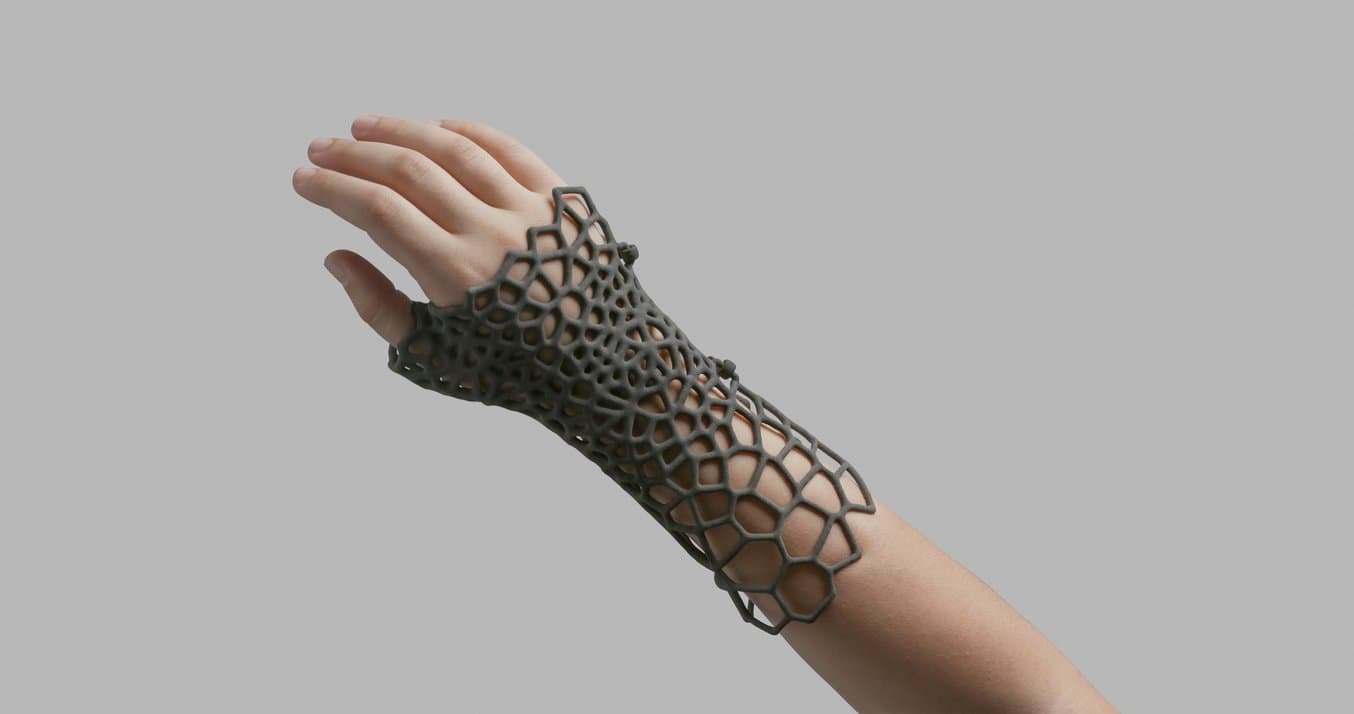
Handschiene mit komplexem Muster zur Gewichtsreduzierung.
Ingenieur*innen entwickeln Teile in der Regel unter Berücksichtigung des endgültigen Herstellungsverfahrens, was auch als Design for Manufacturing (DFM) bekannt ist. Werden additive Fertigungsverfahren nur zur Fertigung von Prototypen eingesetzt, dann sind sie auf Teile und Designs beschränkt, die sich in der späteren Produktionsphase durch herkömmliche Fertigungswerkzeuge reproduzieren lassen.
Da selektives Lasersintern für eine zunehmende Anzahl von Endanwendungen ein durchführbares Fertigungsverfahren wird, lassen sich mit diesem System neue Design- und Konstruktionsmöglichkeiten verwirklichen. Mit SLS-3D-Druckern können komplexe Designs hergestellt werden, die mit herkömmlichen Verfahren entweder gar nicht oder nur mit hohem Kostenaufwand gefertigt werden können. Mit SLS können Designteams auch komplexe Baugruppen, die gewöhnlich aus mehreren Teilen bestehen, zu einem einzigen Teil zusammenführen. So können schwache Verbindungen vermieden und die Montagezeit verkürzt werden.
Selektives Lasersintern kann das volle Potenzial des generativen Designs ausschöpfen, indem es leichte Designs mit komplexen Gitterstrukturen umsetzen kann, die mit herkömmlichen Herstellungsverfahren nicht möglich wären.
Hohe Produktivität und hoher Durchsatz
SLS ist das schnellste additive Fertigungsverfahren zur Herstellung funktionaler, strapazierfähiger Teile und Endverbraucherteile. Die Laser, die das Pulver verschmelzen, haben eine wesentlich schnellere Abtastgeschwindigkeit und sind genauer als die Schichtabscheideverfahren, die in anderen Prozessen wie dem industriellen FDM zum Einsatz kommen.
Während des Drucks können mehrere Teile eng aneinander angeordnet werden, um den verfügbaren Fertigungsraum maximal zu nutzen. Anwender*innen verwenden zur Optimierung jedes Drucks und für höchste Produktivität spezielle Software und lassen deshalb nur wenig Abstand zwischen den einzelnen Teilen.
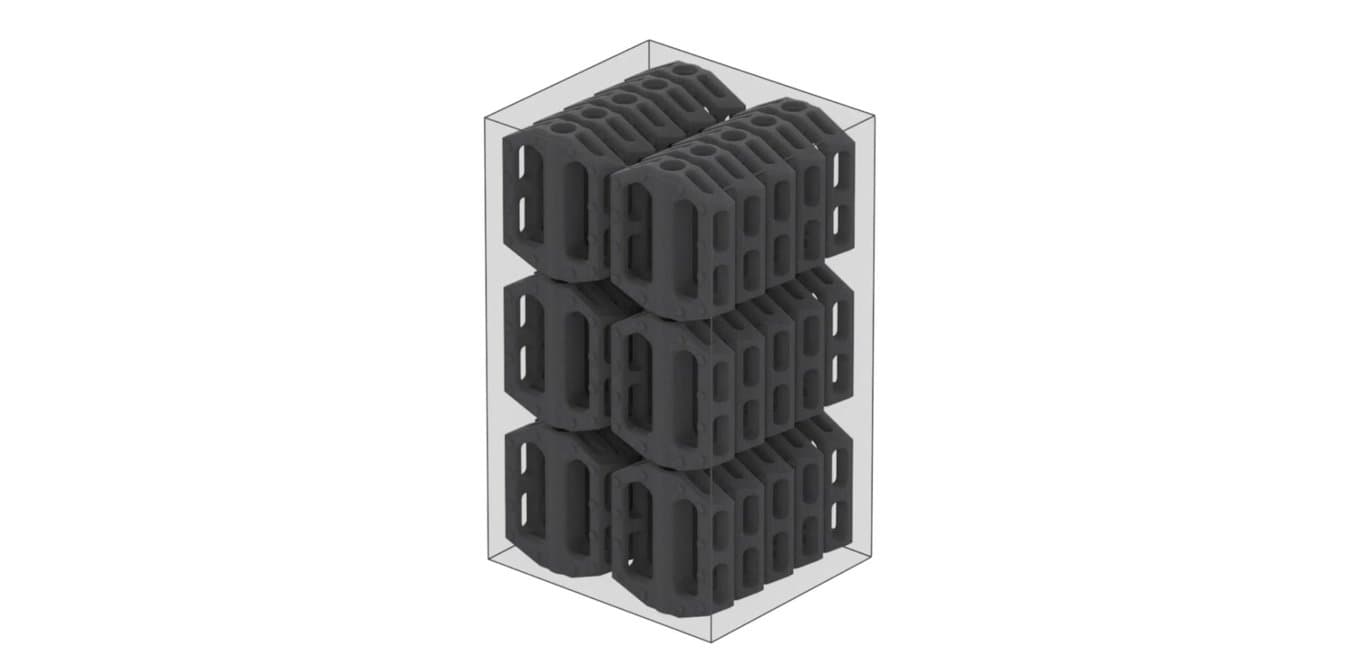
Dank SLS können so viele Teile in die Baukammer gepackt werde, wie hineinpassen, und ohne Stützstrukturen gedruckt werden, was Zeit bei der Nachbearbeitung spart.
Bewährte Materialien für die Endverwendung
Der Schlüssel zur Funktionalität und Vielseitigkeit des SLS-3D-Drucks sind die Materialien. Nylon, Nylon-Verbundwerkstoffe und TPU sind bewährte, hochwertige Thermoplaste. Nylonteile, die durch selektives Lasersintern gefertigt wurden, weisen nahezu hundertprozentige Dichte auf und ihre mechanischen Eigenschaften sind mit Teilen vergleichbar, die mit herkömmlichen Herstellungsverfahren wie Spritzgießen hergestellt wurden.
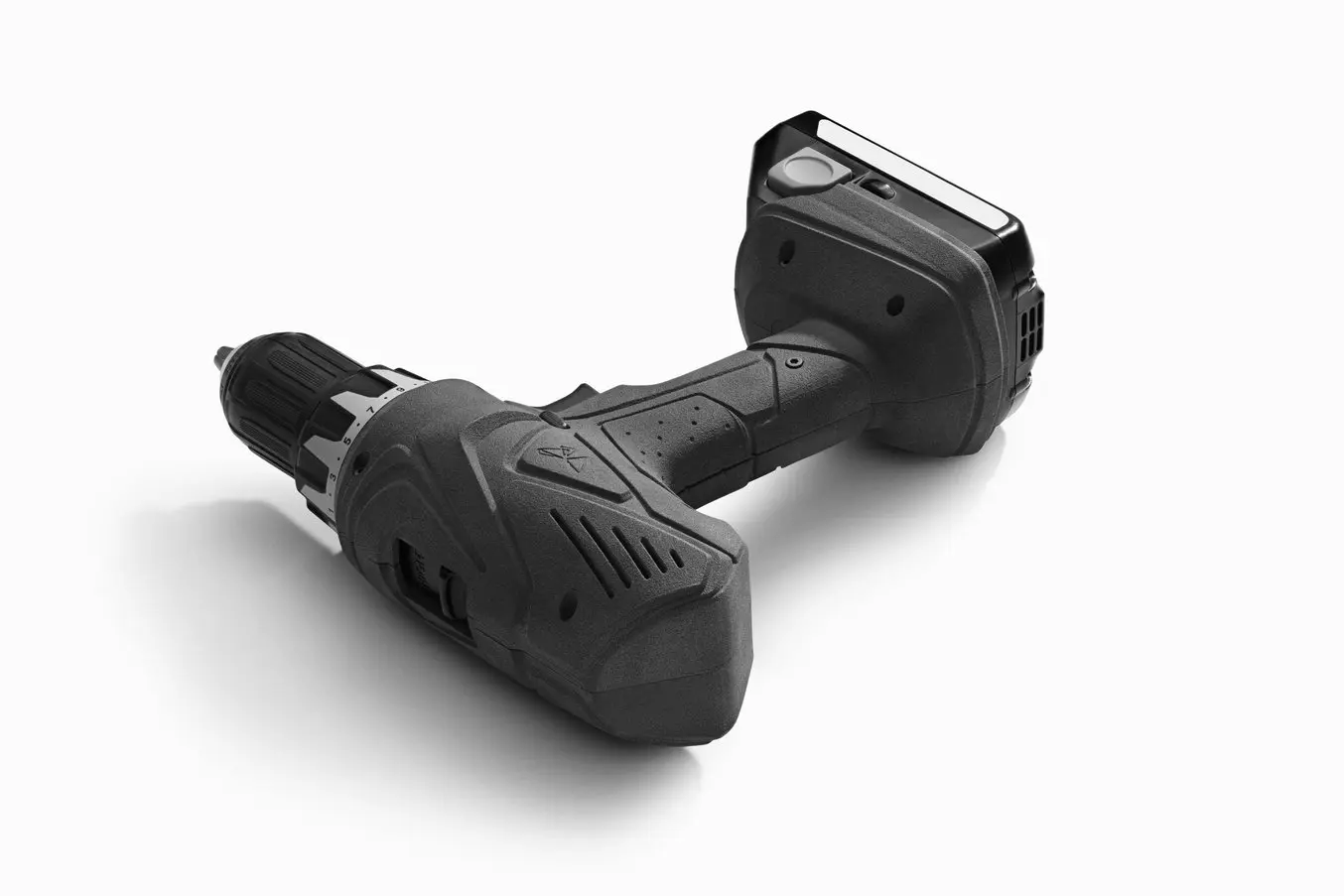
Aus Nylon 12 Powder gedruckte Bohrmaschine. Nylonteile lassen sich einfach nachbearbeiten für eine glatte, professionelle Oberflächenbeschaffenheit.
SLS-Nylon und -Polypropylen sind eine perfekte Alternative zu gebräuchlichen Spritzguss-Kunststoffen. Die Fertigung von Schnappverbindungen und mechanischen Gelenken aus Nylon mit SLS ist allen anderen additiven Fertigungsverfahren deutlich überlegen. Sie eignen sich ideal für funktionale Anwendungen, für die Kunststoffteile benötigt werden, die auch in Umgebungen haltbar sind, in denen mit anderen additiven Fertigungsverfahren produzierte Teile im Laufe der Zeit zersetzt und spröde werden.
Der SLS-Druck von TPU bietet eine großartige Alternative zu traditionellen Formverfahren und ist anderen 3D-Druckverfahren zur Produktion zäher und langlebiger flexibler Teile überlegen. Er eignet sich ideal für Rapid Prototyping, Fertigungshilfen auf Abruf und Sonderanfertigungen oder Kleinserien von Endverbrauchsteilen.
Wettbewerbsfähige Stückkosten
Bei der Berechnung der Stückkosten müssen in der Regel die Eigentumskosten für die Ausrüstung sowie die Material- und Arbeitskosten berücksichtigt werden.
-
Eigentum der Geräte: Je mehr Teile eine Maschine über ihre Lebensdauer produzieren kann, desto geringer sind die Stückkosten. Infolgedessen führt eine höhere Produktivität auf die Stückzahl gerechnet zu niedrigeren Eigentumskosten für die Ausrüstung. Angesichts der schnellen Abtastgeschwindigkeit des Lasers, der Packung von Teilen zur Maximierung der Druckkapazität sowie der einfachen Nachbearbeitung bietet SLS die höchste Produktivität und den höchsten Durchsatz aller additiven Fertigungsverfahren für Kunststoffteile.
-
Material: Während die meisten 3D-Drucktechnologien firmeneigene Materialien verwenden, ist Nylon ein geläufiger Thermoplast, der in großen Mengen für industrielle Zwecke hergestellt wird, und damit einer der billigsten Rohstoffe für die additive Fertigung ist. Da beim SLS-3D-Druck keine Stützstrukturen erforderlich sind und das Pulver wiederverwendet werden kann, fällt nur wenig Abfall an.
-
Arbeitsaufwand: Die Achillesferse vieler 3D-Drucklösungen ist der Arbeitsaufwand. Die meisten Verfahren haben komplexe Arbeitsabläufe, die schwer zu automatisieren sind, was die Stückkosten wesentlich beeinflussen kann. Dank des einfachen Nachbearbeitungsprozesses ist bei SLS jedoch ein geringerer Arbeitsaufwand notwendig.
Ein großformatiger SLS-3D-Drucker erfordert anfänglich eine erhebliche Investition, macht diese jedoch noch schneller wett als kleinere Geräte. Benchtop-SLS senkt diese Einstiegshürde sowie die Stückkosten bei den meisten Anwendungen erheblich.
Das Outsourcing der Fertigung an Dienstleister empfiehlt sich, wenn Sie den 3D-Druck nur gelegentlich nutzen, ist aber auch mit höheren Kosten und längeren Durchlaufzeiten verbunden. Einer der größten Vorteile des 3D-Drucks ist seine Schnelligkeit im Vergleich zu herkömmlichen Fertigungsmethoden, was jedoch schnell an Relevanz verliert, wenn ein outgesourctes Teil erst Tage oder gar Wochen später ankommt.
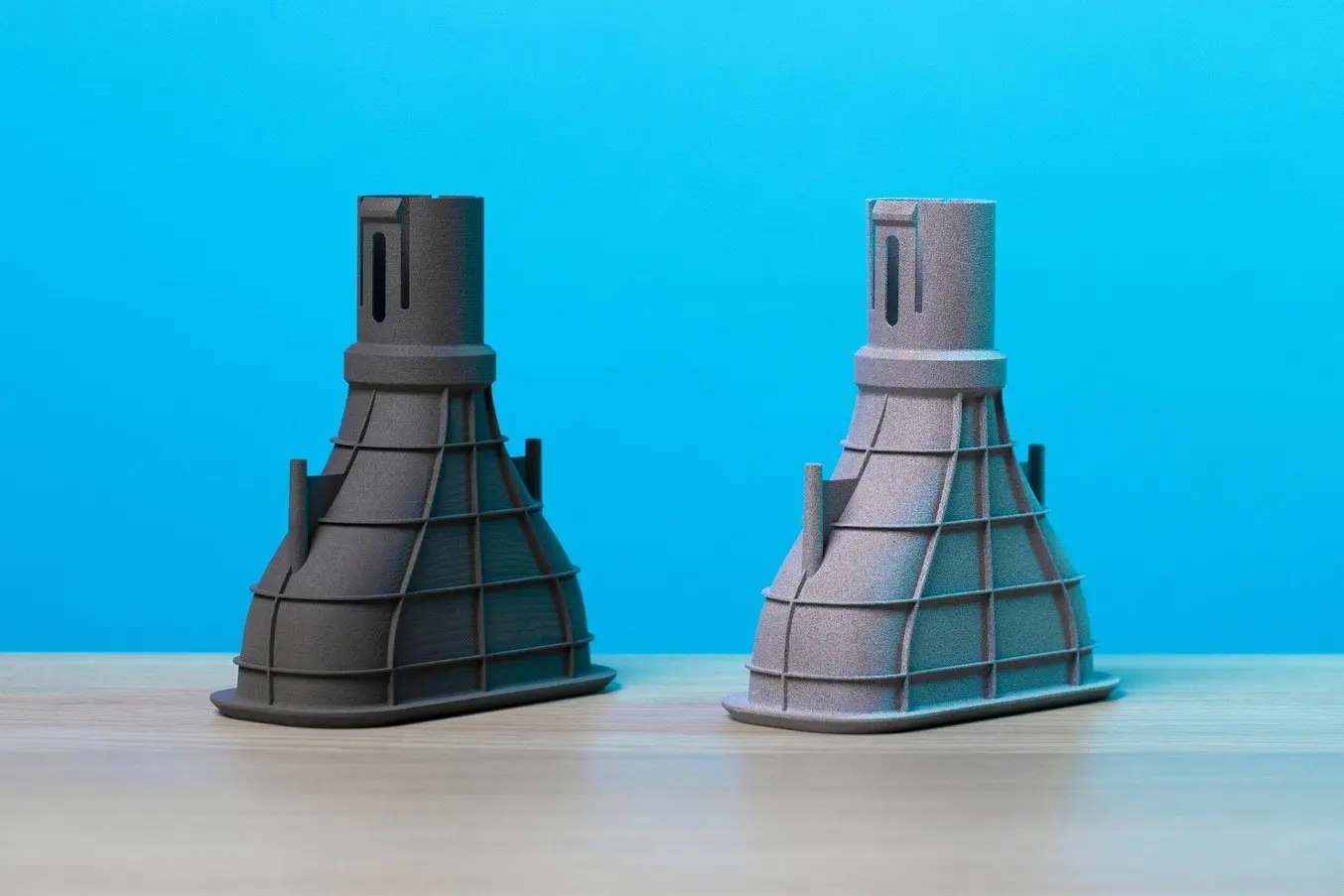
Krümmer eines Kraftfahrzeugs
Kosten | Durchlaufzeit | |
Fertigungsdienstleister | 118,33 € | 7–10 Tage |
Fuse 1+ 30W | 9,02 € | 13 Stunden |
Kontaktieren Sie unser Team für eine detaillierte Analyse Ihrer Modelldateien, um mögliche Kosteneinsparungen zu ermitteln und Ihre Abläufe zu optimieren.
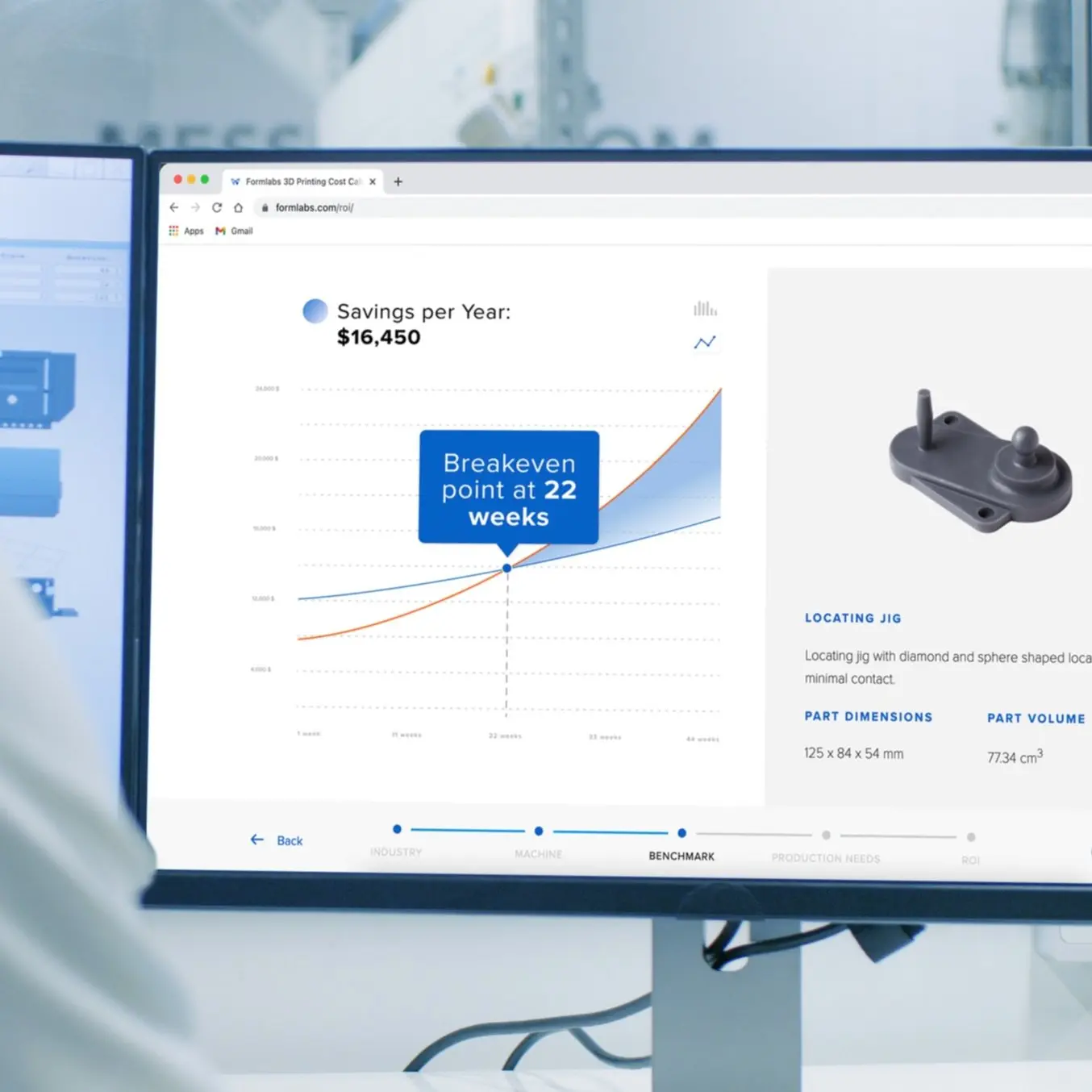
Berechnen Sie Ihre Zeit- und Kostenersparnis
Nutzen Sie unser interaktives ROI-Tool zur Berechnung Ihrer Zeit- und Kostenersparnis beim 3D-Druck mit einem Formlabs-Drucker.
Verkürzte Produktentwicklungszyklen
Dank selektivem Lasersintern können Ingenieure Prototypen bereits frühzeitig im Entwurfszyklus herstellen und anschließend dasselbe Gerät und dasselbe Material zur Herstellung von Endverbrauchsteilen verwenden. SLS erfordert keine ebenso teure und zeitaufwendige Werkzeugbestückung wie die herkömmliche Fertigung. So können Prototypen von Teilen und Baugruppen im Laufe weniger Tage getestet und leicht modifiziert werden. Dadurch wird auch die Produktentwicklungszeit drastisch reduziert.
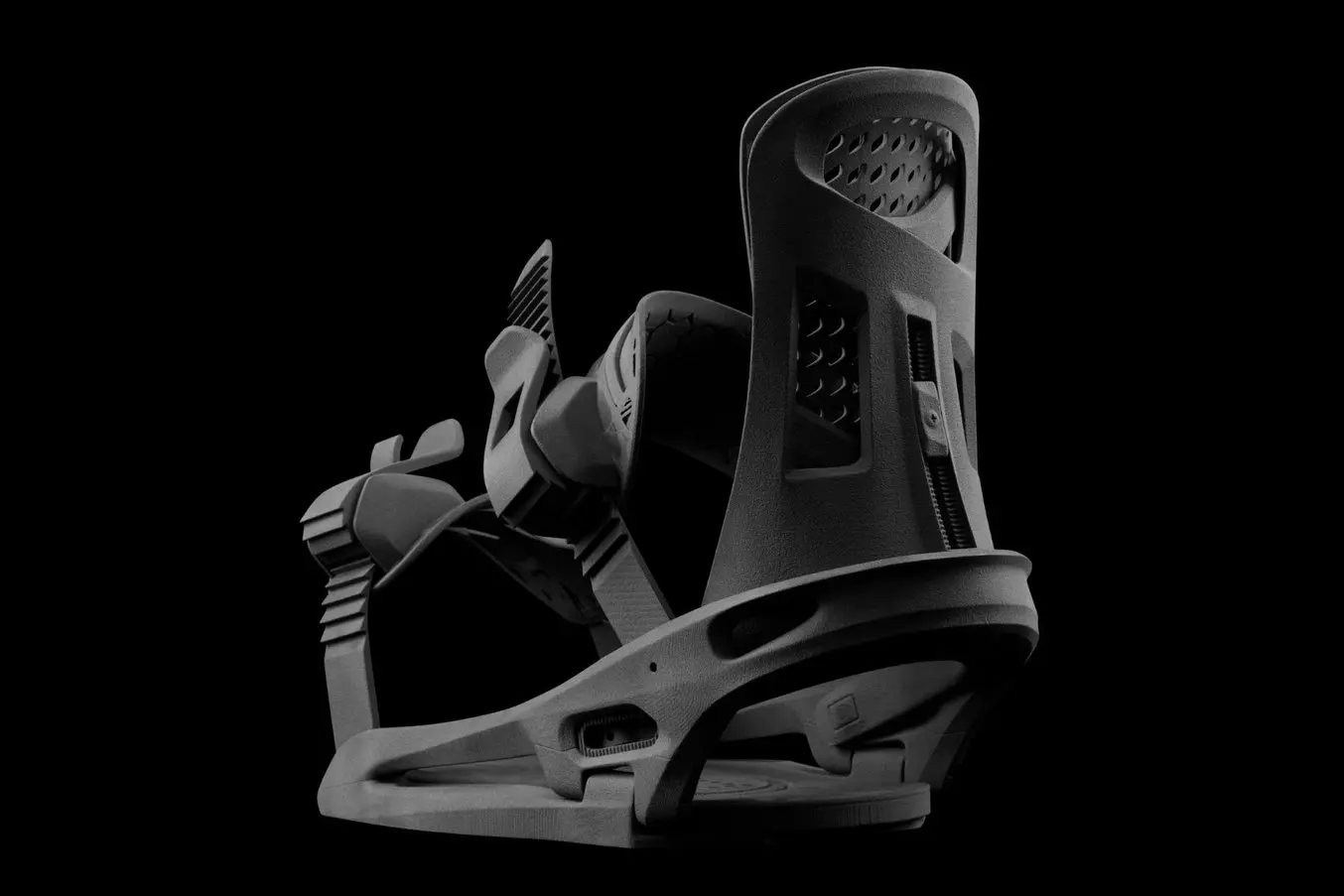
SLS-3D-Druck eignet sich ideal für die Herstellung haltbarer, funktionsfähiger Prototypen. Die Druckteile sind bereit, intensive Funktionstests zu durchlaufen beziehungsweise als Ersatzteile oder gebrauchsfertige Produkte an Kunden ausgeliefert zu werden.
Angesichts der geringen Stückkosten und der robusten Materialien stellt SLS-3D-Drucke eine sparsame Methode zur Herstellung komplexer Sonderanfertigungen oder einer Serie kleiner Komponenten für Endprodukte dar. In vielen Fällen ist SLS eine kostengünstige Alternative zum Spritzgießen für die Fertigung einer begrenzten Stückzahl oder das Bridge Manufacturing.
Lernen Sie den SLS-3D-Drucker Fuse 1+ 30W kennen
Bisher waren industrielle SLS-3D-Drucker für die meisten Unternehmen unerschwinglich. Die Kosten für eine einzige Maschine beliefen sich bislang auf über 200 000 €.
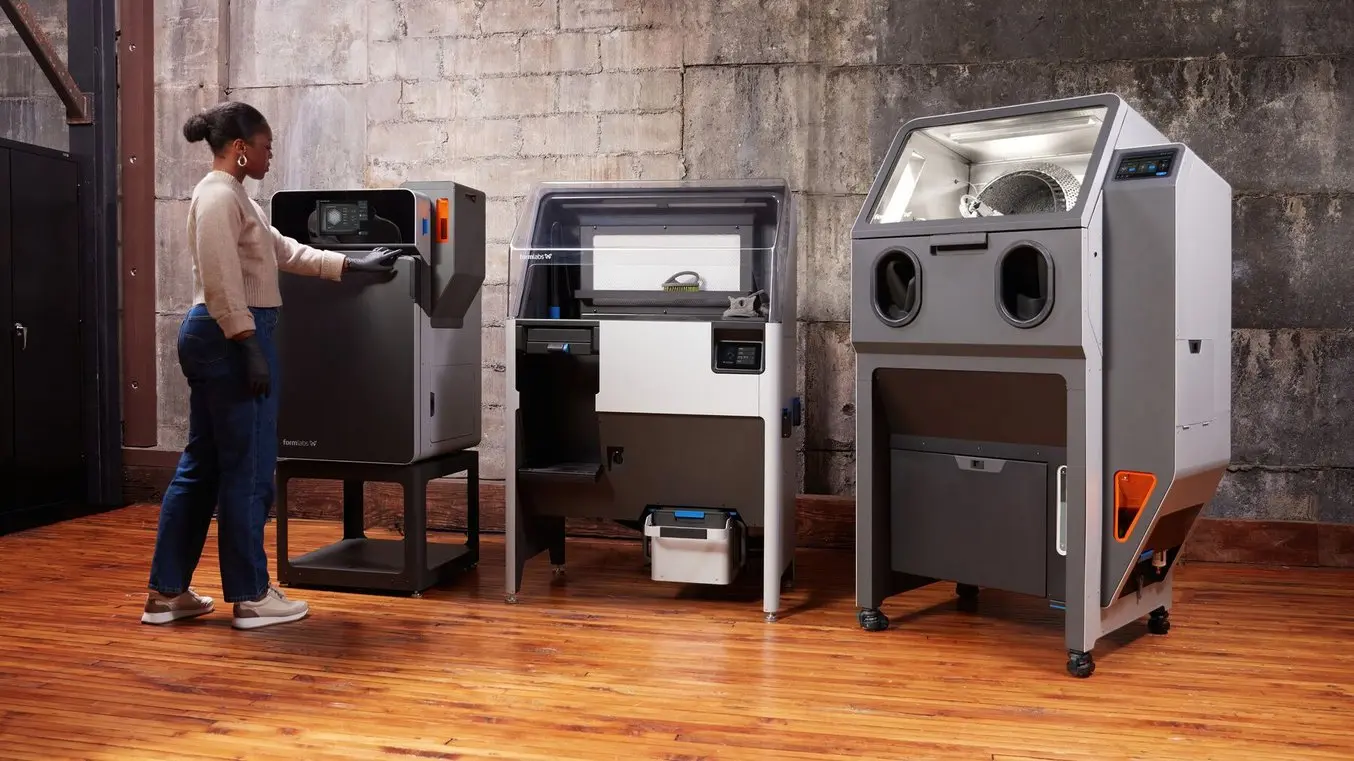
Mit dem Fuse 1+ 30W bringt Formlabs die industrielle Leistung des selektiven Lasersinterns an Ihren Arbeitsplatz. Die Technologie bietet Hochleistungsmaterialien zum geringstmöglichen Stückpreis sowie eine kompakte Standfläche und einen einfachen Arbeitsablauf.
Mit dem Fuse 1+ 30W eröffnen sich neue Möglichkeiten für die unabhängige Fertigung und Prototypenentwicklung.