Siemens Energy druckt großformatige Spritzguss-Formeinsätze und Testteile mit Form 3L und Build Platform 2L
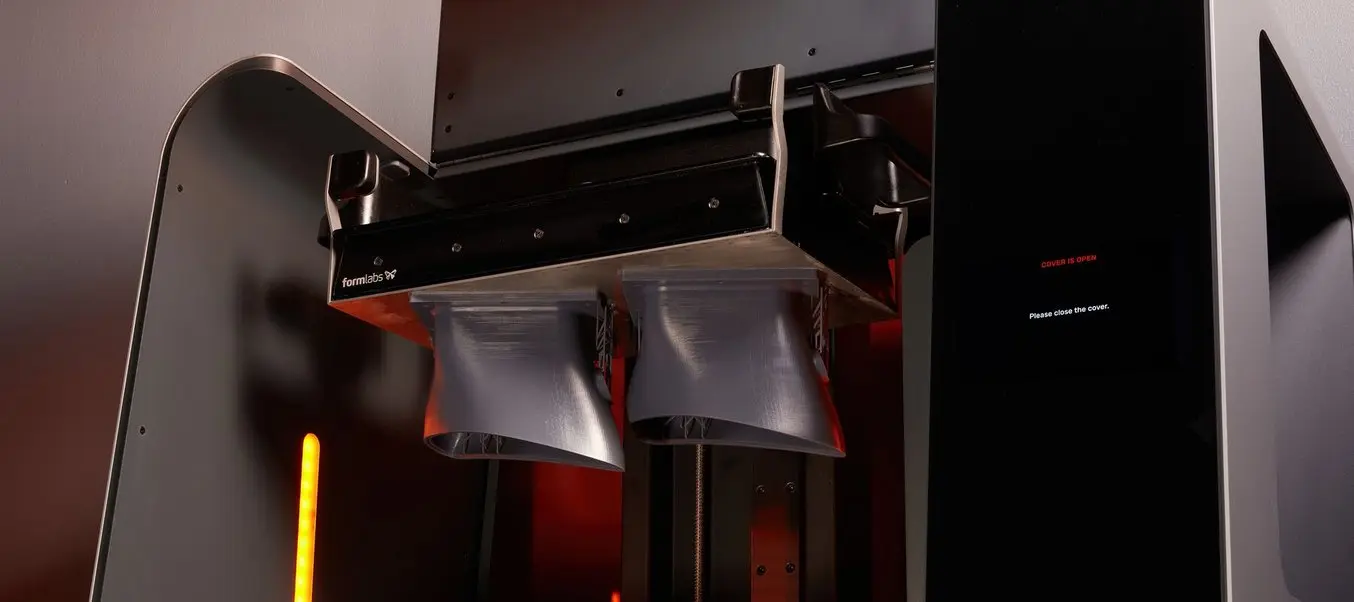
Diese Testteile, die von Maschinenbauingenieur Brian Biller am Siemens Energy Orlando Innovation Campus entworfen wurden, schließen an die Schaufeln von Gasturbinen in Luftstrom-Testanlagen an.
Der Siemens Energy Orlando Innovation Campus (OIC) entwickelt branchenübergreifende Projekte vom Konzept bis zur Umsetzung für Partner auf der ganzen Welt. Dem Ingenieurteam stehen alle erdenklichen industriellen Werkzeuge zur Verfügung; ihre Aufgabe ist, Fertigungsverfahren wie Zerspanung und Guss, Automatisierung und 3D-Druck zu kombinieren, um globale Probleme zu lösen.
Matthew Deutsch, Techniker für additive Fertigung (AM), ist für die Abteilung zur additiven Fertigung von Verbundstoffen zuständig, wo er eine Flotte von 3D-Druckern der Verfahren Schmelzschichtung (FDM) und Stereolithografie (SLA) sowie zwei Benchtop-SLA-Drucker des Typs Form 3L verwaltet. Bei der Umsetzung verschiedenster Projekte von Rapid Prototyping bis zu Formeinsätzen für den Spritzguss stützt sich Deutsch auf die Vielfalt der Materialbibliothek von Formlabs. Außerdem hat er mit Formlabs bei der Validierung der neuen Revolution für die Nachbearbeitung großformatiger SLA-Teile kooperiert: der Build Platform 2L.
Dank der patentierten Schnellablösetechnologie (Quick Release Technology) der Build Platform 2L hat Deutsch seine Form 3L pausenlos in Betrieb und druckt größere Teile wie Spritzgussformen und Fertigungshilfen nun direkt auf der Konstruktionsplattform.
Das Warten hat sich gelohnt. Wir können Spritzgussformen jetzt drucken und haben schon innerhalb von 24 Stunden spritzgegossene Kunststoffteile vor uns. Das ist eine Neugeburt für die gesamte Branche.
Matthew Deutsch, Techniker für additive Fertigung beim Siemens Energy Orlando Innovation Campus
Die Arbeit mit Notsituationen
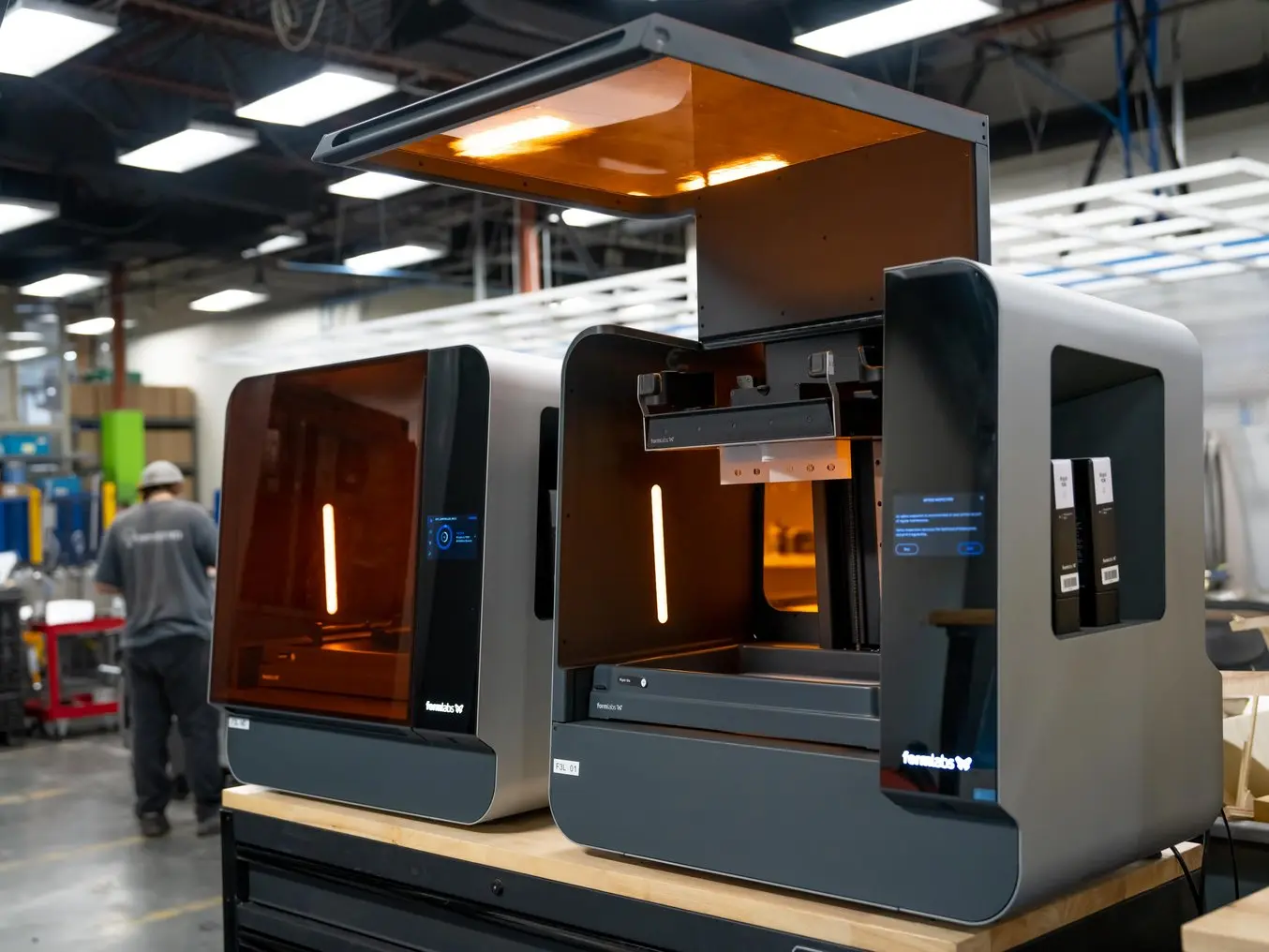
Seitdem Matthew Deutsch die zwei Form 3L angeschafft und andere Abteilungen über die Vielseitigkeit des SLA-3D-Drucks aufgeklärt hat, sind die Drucker ihm zufolge fast pausenlos in Betrieb.
Bei der AM-Abteilung gehen die verschiedensten Anfragen ein, von Motorenmodellen für Messen bis hin zu essenziellen Vorrichtungen und Werkzeugen für die Reparatur von Gasturbinen am anderen Ende der Welt. „Wir haben immer mit Notsituationen zu tun. Siemens Energy wendet sich mit der Anfrage an uns, Reparaturprozesse für Komponenten eines Motors zu entwickeln, manchmal während eines Systemausfalls – also einer geplanten oder ungeplanten Phase, in welcher der Motor außer Betrieb ist. Jede Minute, in der dieser Motor keine Elektrizität produziert, bedeutet riesige Ausfälle. In einem unserer 3D-Druck-Projekte wurde der Verschleiß von Turbinenschaufeln beurteilt, um zukünftige Ausfälle zu vermeiden“, berichtet Deutsch.
Mehrere 3D-Drucker und eine große Materialauswahl zur Verfügung zu haben ist eine große Hilfe, um solche Projekte schnell abzuschließen. Deutsch war für die Einführung der SLA-Technologie im OIC zuständig und war zunächst mit Vorbehalten seiner Kolleg*innen gegenüber den Kunstharzen konfrontiert. Als diese jedoch die Vorteile einer so vielfältigen Materialbibliothek sahen, testeten sie immer mehr Wege aus, SLA-Druckteile in ihre Arbeitsabläufe zu integrieren. Heute erhält Deutsch mehr Anfragen nach Teilen aus dem Form 3L als aus jedem anderen Drucker. „Ich bekomme weniger Anfragen für die anderen Technologien als Anfragen nach Kunstharzdrucken. Das reicht von Rigid 10K Resin für Spritzguss-Formeinsätze bis hin zu Tough 2000 Resin und Clear Resin. Diese Geräte stehen niemals still“, so Deutsch. Tough 2000 Resin ist aufgrund seiner Festigkeit und Steifigkeit zu einem Grundpfeiler für das Team geworden. In Teilen wie Luftstromtüllen, die fest und luftdicht sein müssen, wird es als Ersatz für Aluminium eingesetzt.
Die Materialvielfalt der SLA-Produktlinie von Formlabs liefert eine Lösung für fast jedes Problem. Angesichts der globalen Ausmaße des Netzwerkes von Siemens Energy stellen Hilfsmittel, die verschiedenste Arbeitsprozesse unterstützen, einen riesigen Vorteil dar. „Jede Anfrage ist anders – keine Woche ist wie die vorherige. Dafür bietet uns der Form 3L eine unvergleichliche Vielseitigkeit“, erklärt Deutsch.
Produktion ganzer Chargen und großer Teile
Die Größe des Form 3L vereint mit der Materialvielfalt macht es möglich, einzelne großformatige Teile, Chargen vieler kleiner Teile oder auch mehrere Komponenten einer Baugruppe zu drucken. „Es ist eine tolle Fertigungsoption zu einem wirklich guten Preis. Häufig zahlt man für größere SLA-Drucker zehnmal mehr, doch dieser Drucker bietet eine hervorragende Leistung und Größe“, meint Deutsch.
Die Drucker sind rund um die Uhr in Betrieb, und für große Druckteile mit mehrtägiger Dauer lässt Deutsch den Drucker oft auch übers Wochenende laufen, da er sich darauf verlassen kann, dass der Drucker auch komplexe Aufträge erfolgreich fertigstellt. „Kleinserien oder großformatige Teile können wir übers Wochenende herstellen. Wir können schwierige Teile drucken lassen, am Montag zurück in den Dienst kommen, und fertig sind sie“, erzählt Deutsch. Einige Teile ließen sich jedoch dennoch nicht umsetzen – bis die Build Platform 2L kam.
Großformatige 3D-gedruckte Formeinsätze, noch einfacher
Am OIC sind Matthew Deutsch und andere Teammitglieder häufig eher für die Kreation von Prozessen statt von Produkten zuständig. Mithilfe einer 3D-gedruckten Vorlage für die Lesungsmarkierung, die zum Prüfen von Turbinenschaufeln dient, konnten sie diagnostische Prozesse optimieren und einen neuen, effizienteren Arbeitsablauf zur Wartung und Reparatur der Turbinen entwickeln.
Ein Verfahren, das ohne die Build Platform 2L nicht möglich wäre, ist die Produktion von Spritzguss-Formeinsätzen für Kleinserien. Beim Spritzguss werden für gewöhnlich große Chargen produziert – denn um die hohen Kosten gefräster Metallformen zu rechtfertigen, müssen die Stückzahlen oft in den Zehntausenden liegen. Mittels 3D-Druck ist die betriebsinterne Herstellung von Formeinsätzen jedoch günstig und effizient, sodass auch kleinere Chargen wirtschaftlich produziert werden können.
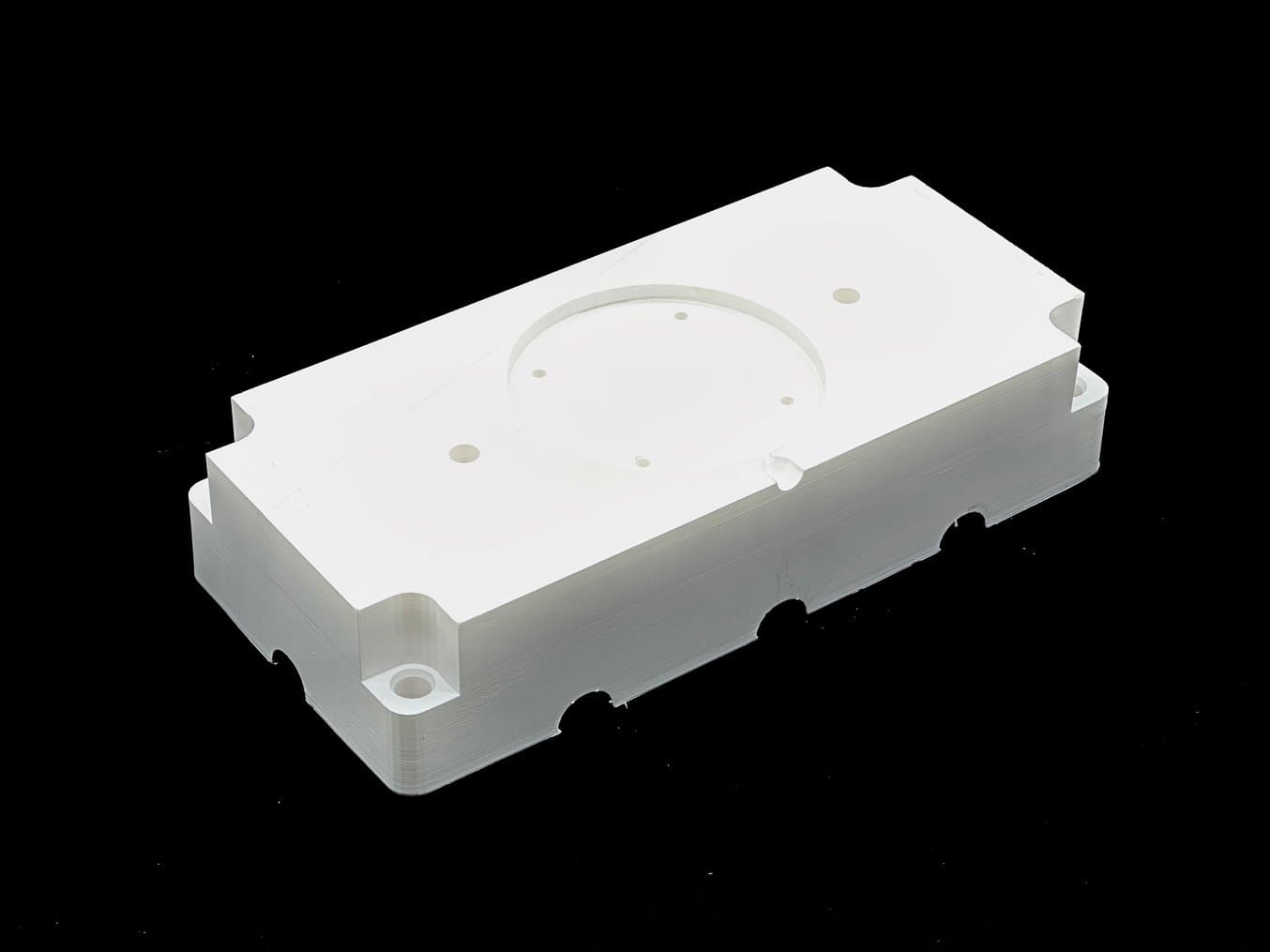
Großformatige Formen zu drucken, die dem Druck industrieller Spritzgussmaschinen standhalten, war bisher nahezu unmöglich. Mit der Schnellablösetechnologie der Build Platform 2L können Formen nun direkt auf der Konstruktionsplattform gedruckt und im Handumdrehen entfernt werden.
Damit das gesamte Teil dem enormen Druck industrieller Spritzgussmaschinen gleichmäßig standhält, müssen Formen flach gedruckt werden. Je größer die Form, desto schwerer wird es jedoch, sie auf dem Form 3L zu drucken, da die Haftwirkung auf der Konstruktionsplattform das Ablösen der Teile erschweren kann. Mit der Build Platform 2L ist der Druck von Teilen direkt auf der Konstruktionsplattform jetzt kein Problem mehr. Das verkürzt die Druckzeit, verringert den manuellen Arbeitsaufwand und eröffnet ganz neue Anwendungsbereiche.
Wir können ganze kiloschwere Teile jetzt in einem Stück drucken und sie ohne Stützstrukturen durch Biegen von der Plattform ablösen, was vorher nicht ging – unsere einzige Option für den Formenbau war maschinelle Bearbeitung.
Matthew Deutsch, Techniker für additive Fertigung beim Siemens Energy Orlando Innovation Campus
Druckdaten: Form für eine Münze
Druckzeit | Nachbearbeitungszeit | Gesamtzeit | Materialverbrauch | |
---|---|---|---|---|
Ohne Build Platform 2L | 14 Stunden | 1 Stunde | 15 Stunden | 391,43 ml |
Mit Build Platform 2L | 6,5 Stunden | 10 Minuten | 6 Stunden 40 Minuten | 363,20 ml |
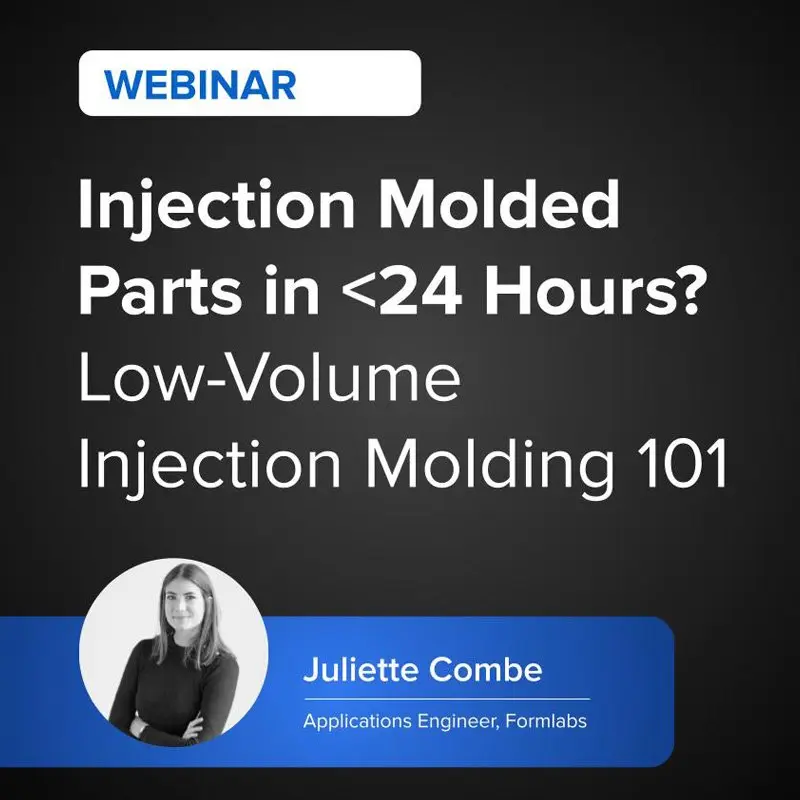
Spritzgussteile in unter 24 Stunden? Einführung in den Spritzguss für Kleinserien
In diesem Webinar zeigen wir Ihnen, wie Sie in Ihrem Spritzgussverfahren Formen aus dem SLA-3D-Drucker einsetzen, um Kosten und Durchlaufzeiten zu verringern und bessere Produkte zu liefern.
Kürzere Druckzeiten ohne Anpassung der Schichthöhe?
Ohne die Schnellablösetechnologie der Build Platform 2L mussten Teile schräg auf der Konstruktionsplattform gedruckt werden, was ihre Höhe in der Z-Achse vergrößerte und den Druck verlängerte. Mit der Build Platform 2L kann Deutsch nun ohne Stützstrukturen flach auf der Konstruktionsplattform drucken und damit sowohl Druckzeit als auch Materialverbrauch enorm verringern. „Die Build Platform 2L spart uns unvorstellbar viel Zeit“, so Deutsch.
Während das Fertigungsvolumen des Form 3L das Design großer, luftdichter Teile ermöglicht, macht die Build Platform 2L Stützstrukturen überflüssig, sodass die Nachbearbeitung vereinfacht und die Funktion der Druckteile verbessert wird. Vor Kurzem druckte das Team eine Testtülle, die an die Schaufeln von Gasturbinen in einer Luftstrom-Testanlage anschließt. Bei vorherigen Versionen von Teilen wie dieser Tülle waren umfassende Schleifarbeiten nötig gewesen, um Stützspuren zu entfernen und das Teil für eine Dichtung vorzubereiten. Die Tülle dient dazu, einen quadratischen Luftverteiler mit der gesamten Radiusfläche der Schaufel zu verbinden, damit der Luftstrom ungehindert passieren kann.
Zweck des Testverfahrens ist, Probleme mit dem Durchlass und den Merkmalen innerhalb des Schaufelblatts zu erkennen. „Tough 2000 Resin lieferte fantastische Ergebnisse mit hoher Qualität, Festigkeit, Mehrwert und einer leichten Flexibilität zur Kompression. Die Build Platform 2L hat es uns möglich gemacht, diese Teile flach auf der Plattform zu drucken, sodass wir dieselben oder bessere Ergebnisse mit weniger Reinigungsaufwand und in 30 % weniger Zeit erreichen. Außerdem bietet uns die flache Oberfläche der Konstruktionsplattform eine vollkommen glatte Kontaktfläche, die für erstklassige Luftdichtigkeit beim Anschluss an den Luftverteiler sorgt“, erläutert Deutsch.
Druckdaten: Testtüllen
Druckzeit | Nachbearbeitungszeit | Gesamtzeit | Materialverbrauch | |
---|---|---|---|---|
Ohne Build Platform 2L | 14 Stunden | 1 Stunde | 15 Stunden | 295,99 ml |
Mit Build Platform 2L | 9 Stunden | 5 Minuten | 9 Stunden | 259,67 ml |
Grenzen des SLA-3D-Drucks beseitigen
Das Team des Siemens Energy OIC weiß genau, wie es die Grenzen seiner Maschinen voll ausreizt – schließlich ist es seine Mission, neue Prozesse zu entwerfen und Lösungen zu einzigartigen Problemen zu finden. Als Deutsch die Drucker des Typs Form 3L in den Betrieb holte, wurde damit eine völlig neue Palette von Lösungen erschlossen.
Mit der Build Platform 2L reichen ihre Kapazitäten jetzt sogar noch weiter, indem neue Arbeitsprozesse für umfassende Spritzgussverfahren, großformatige Fertigungshilfen und individualisierte Endprodukte umgesetzt werden. „Mit Formlabs kann man die vermeintlichen Grenzen des SLA-3D-Drucks vergessen und Dinge schaffen, die vorher undenkbar waren“, so Deutsch.
Die Build Platform 2L ermöglicht die Produktion von Spritzgussformen in Industriequalität für die Kleinserienfertigung, reduziert Druckzeiten und macht aus dem Entfernen von Stützstrukturen Geschichte. Machen auch Sie sich die Schnellablösetechnologie zunutze und besuchen Sie unsere Produktseite, um mehr zu erfahren.